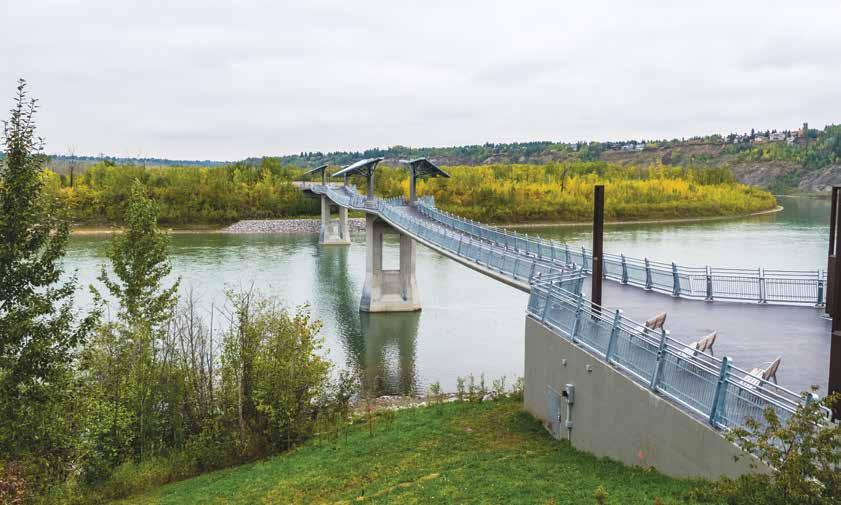
2 minute read
Superior corrosion protection for the steel industry
Simply put, when exposed to the atmosphere all metals corrode. As such, 67 years ago Dick Daam recognized the need for a corrosion protection system that stood the test of time. Founded in 1954, a small kettle in a backyard grew into three employeeowned facilities: two in Alberta and one in Saskatchewan. Our team is technically driven and understands this is essential for success. We’re proud to have implemented a proactive function training program for all employees, to guarantee that we provide the highest quality products and services and that it stays that way. Daam Galvanizing is an environmentally sustainable company that continuously reinvests back into its operations. One example of this is our storm water treatment building, as we were the first galvanizing plant in Canada to build such a facility. Daam’s mission is to deliver expert quality galvanizing, exceptional customer service from start to finish, and timely, cost-effective results that surpass expectations.
Selecting the most effective corrosion protection system requires an evaluation of things like durability, maintenance schedule, service life sustainability, life-cycle costs, and how corrosive the surrounding environment is. Therefore, the answer to steel corrosion is not to use other building materials, rather to adequately protect exposed steel to minimize and delay the process. Fundamentally, hot-dip galvanizing is specified for its corrosion protection as the metallurgical bond between the zinc and the steel creates a barrier that is part of the steel itself. This results in a coating that is tightly bonded and harder than the base steel.
Hot-dip galvanizing provides three levels of resistance: barrier protection, cathodic protection, and the zinc patina. The barrier protection is the first line of defense as it isolates the steel from the environment. That said, barrier protection must remain intact to protect the steel, so the tightly bonded, impervious nature of zinc-metal makes it a very good barrier coating. Second, zinc protects steel cathodically, which means it will preferentially corrode to protect the underlying base steel.
Even if a hot-dip galvanized coating is damaged to the point that bare steel is exposed (up to ¼” diameter), no corrosion will begin until all the surrounding zinc is consumed. The final factor is the zinc patina, which is the formation of zinc corrosion by-products on the surface of the steel. These form when the galvanized coating is exposed to the atmosphere, and once fully developed, slows the corrosion rate of zinc to about 1/30th the rate of steel. It acts as an additional passive, impervious barrier for the hot-dip galvanized coating.
Daam Galvanizing takes great pride in our quality assurance and safety programs. Our team works together with unparalleled diligence to deliver superior products and service while maintaining the safest worksites. We were the second galvanizing plant in North America to be certified by the Quality Management Institute as a corrosion protection coatings company. Our complete range of testing and monitoring equipment, alongside our dedicated quality assurance managers ensure all our products meet the expectations and requirements for any environment. No other corrosion protection system provides the lifelong protection, durability and cost-effective performance of galvanizing while reducing impacts on future generations. For galvanizing expertise delivered with a lifetime of experience, contact Daam Galvanizing for the best DAAM galvanized steel you can get.
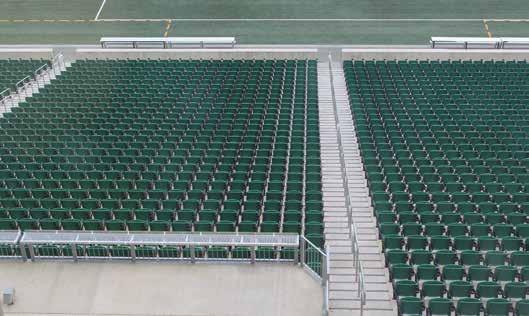

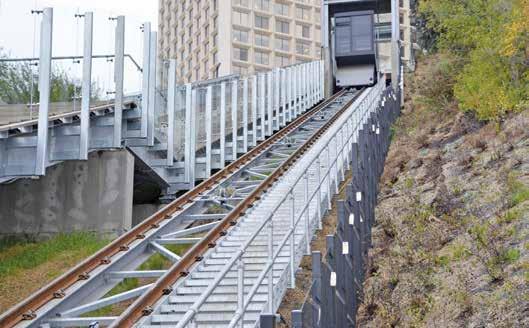