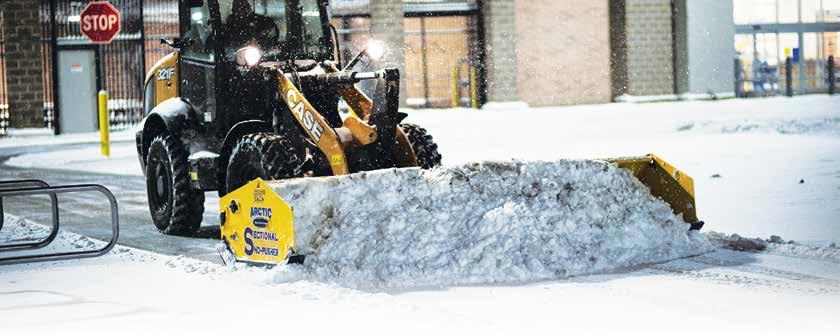
10 minute read
Growing your business with the right equipment
Just about every serious snow contractor remembers what it was like to start out with one pickup truck and a plow. When the snow came, there was good money to be made. More importantly, you found your passion, grabbing every opportunity that came your way. You hired your friends, took on more customers, and dreamed of a bright financial future. By Olivia Roy
However, dreams do not always turn into reality and, at some point, all attempts to further grow the business seem to hit a brick wall. The larger customers that you were attracting were more demanding, the crews were larger but not as reliable, and you found yourself worrying more and more about contracts, liability insurance, and the price of salt. You had more overhead, your equipment was aging, and your margins were being squeezed such that it felt like you were simply treading water. The problem stemmed from the fact that your efficiencies were too low to generate the profits needed to fuel your growth, and you most likely found yourself working day and night during every snowstorm at whatever task was necessary to simply stay afloat.
25 years ago. Having a couple of large steady clients allowed some local growth, but trying to expand much beyond that was extremely challenging, especially in a very competitive market.
Today, however, is a different story. In the last 10 to 15 years, the industry has had a significantly different experience whereby small companies have turned into hugely successful enterprises in a relatively short period of time, running fleets numbering in the hundreds. When recently surveying many of the largest selfperforming U.S. commercial snow contractors, two factors stood out far above the rest as making that possible. The first was the move away from truck fleets to construction equipment. The second was the introduction of a new type of hightech/high-efficiency snow pusher, starting around 2006.
Construction equipment vs. plow trucks
The industry has made a decided shift into heavy iron. Skid steers, compact track loaders, wheel loaders, and even backhoes have taken the place of plow trucks in large commercial retail malls, distribution centres, railyards, hospitals, and corporate parking lots. They have proven to be superior to traditional plow trucks for several reasons, largely coinciding with the advent of the box/containment plow or snow pusher.
Construction machines offer several advantages to trucks. Not only do their power and efficiency dwarf the capabilities of trucks, but the business model requiring machines to be parked on site for the entire season is so attractive to both contractor and customer that the practice is now standard. Today’s largest snow fleets are now dominated by machines, with plow trucks relegated to serving small outlying accounts that require the flexibility of a routed vehicle.
Here are some of the obvious advantages the construction machines offer over trucks with plows when taking on large commercial properties:
1. They are ideally suited to the business model of seasonal contracts whereby equipment remains on a customers’ site for the season and crews start plowing when they get there. This model allows for a natural rotation of operators while it also minimizes the insurance liability of having employees drive to and from their work sites in company vehicles.
3. More creative and efficient snow clearing techniques are possible, such as backdragging and stacking. Large pusher attachments are capable of making long containment runs which clear the snow from the lot rather than simply move it to the side, allowing customers greater overall use of their parking lots.
4. Significant fuel savings are realized as typical pickup trucks run at 250 to 475 HP, but the most common machines range from 74 to 175 HP. Also, there is no fuel spent commuting to and from the site.
5. Licensing, insurance, and other fees are less or non-existent with construction machines.
6. Visibility is significantly greater on all sides, including visibility right to the attachment performing the work. This not only improves efficiency, but significantly reduces the kinds of mistakes that risk operator, equipment, or property damage.
7. Skid steers and track machines can do a 360° pivot, minimizing the need to operate in reverse, another efficiency and safety benefit.
8. Thanks to quick couplers and universal mount designs, machines provide the ability to easily change attachments from pushers to brooms to front-loading salt spreaders.
Added up, the benefits of machines far outweigh plow trucks for large commercial properties. However, their total value increases dramatically depending on the specific attachment they employ.
Selecting the right attachments – How the efficiency of pushers led to the high-tech revolution in snow attachments
With the right attachment, a skid steer can perform the work of three pickup trucks; a wheel loader can do the work of seven.
Once the first plow manufacturer decided to put side panels on a snowplow and create the first box or containment plow, also known as a snow pusher, the industry changed forever. Protech Inc. is credited with launching the first generation of snow pushers and they were designed to be mounted to machines. They required being chained to buckets or, in some cases, welded to boom arms, which then forced the need to cut them off bumps of any surface and miss much of that last inch or so of snow, forcing contractors to re-plow every lot with the narrower plow trucks before salt could be laid down.
Of course, those were not the only frustrations they created. They had problems with heavy wet snow or very large loads since their front-loaded weight would lift the two front tires off the ground and defeat even the largest equipment’s ability to move the snow to the end of a run. Keeping the pusher level to prevent uneven wear was a task that only the most experienced operators could handle, making it difficult to rapidly train new crew members. Their size also presented
The Protech pusher earned its popularity by moving large amounts of snow but left much behind to re-plow.
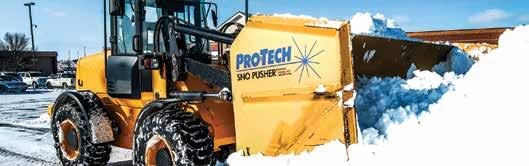
in the spring so that warm weather attachments could take their place. Nevertheless, they became very popular starting in the mid ‘90s and soon became the workhorse of the industry as several other established plow manufacturers, including Boss Snowplows, moved quickly to produce very similar models of their own. Ironically, it was the popularity of the large pushers that created the explosive demand for the construction machines.
The attraction of pushers was that they were quite large and designed to move large amounts of snow at a much faster rate than truck plows, and they could stack the snow as well. However, their length came at a price as they would teeter totter on the rises or another problem in that collisions with manholes, obstructions, or other surface anomalies were far more violent than normal and would risk more serious injuries to the operator, as well as very costly damage to the pusher, often creating a total loss in the thousands of dollars.
When it came to efficiency, snow pushers certainly helped. However, due to their design drawbacks, contractors still spent too much time with too many operators clearing their clients’ properties. Furthermore, losing a critical resource in the middle of a storm due to an impact with a manhole cover, curb, or light pole would likely mean extra overtime or lost revenue that might not be recoverable. Finally, the need to
Product Showcase replow to avoid expensive saltings never went away. In total, this type of pusher simply wasn’t enough to correct the efficiency issues to the level at which growth would soon become unhinged.
The invention that changed the industry
In 2006, a new kind of pusher hit the market and it was unlike anything the world had seen. Randy Strait, the founder and owner of Arctic Snow and Ice Control, Inc., a large Chicago area snow contractor based in Frankfort, IL, and a serious inventor in his own right, had an idea for a new kind of plow that would deal with his frustration over replowing. His idea was to divide the large one-piece moldboard into several moveable sections that could contour to the pavement as if it were being plowed by individual hand shovels.
The result was a revolutionary design that would change the industry forever and eventually lead the industry to rethink their own designs. The highly patented and trademarked Arctic Sectional Sno-Pusher™ literally solved every major issue with pushers. This new design, made up of sections in either 24-, 30-, or 32-inch widths, contoured flawlessly to the rises and depressions in the pavement surface leaving nothing behind, by far the cleanest scrape the industry had ever seen and still has never duplicated.
Strait, however, went several steps
Articulated sections and side panels allow the Sectional Sno-Pusher™ to ride up on sidewalks.

Growing one’s business with construction equipment and Arctic Sectional Sno-Pushers TM .
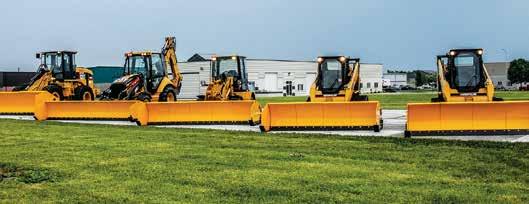
further. He developed a patented two-step obstacle avoidance system that started with individual springoperated trip edges on each section that would flip back over manhole covers and other obstructions up to three inches in height rather than slam the operator and machine to an abrupt stop or destroy the pusher. Then he integrated the trip mechanism with the vertical movement of the sections to allow each section to float harmlessly over curbs, boulders, and other encountered obstructions up to nine inches in height. They could also drop into depressions up to nine inches, into the so called “birdbaths” that would have previously retained countless pockets of ice and snow.
Introducing mechanical side panels that moved in sync with the individual moldboards was Strait’s next innovation that not only protected the fragile side panels from curb impacts on turns, but also allowed the pusher to ride onto sidewalks and clear both roadways and sidewalks at the same time. Unexpectedly, this also allowed the Arctic “Sectional” to expertly back drag sidewalks and gutters right to the edge, something that the others cannot.
He tackled an additional problem with his patented universal Slip Hitch™ mounting system, which quickly became the envy of the industry. It gave the operator the ability to mount his pusher to any machine manufacturer’s built-in coupler without the need for chains or welds, and he could attach and detach without leaving the comfort of his warm cab. It also allowed the attachment to float independently of the machine, keeping all four machine tires on the ground at all times since it transferred no weight to the front of the machine. This not only provided maximum traction, but larger pushers could be put on smaller horsepower machines and more snow could be moved. The traction benefits were only compounded by the fact that tires were not slipping on hardpack or ice any more due to how well the pusher scraped. An added benefit was that the pusher was now self-leveling for immediate drop and go operation, which allowed beginning operators to plow like experts in no time. Finally, the independent action of the Slip Hitch™ provided an additional layer of impact protection.
His final patent was related to his decision to reject the use of springs for vertical movement. Instead, the individual sections were mounted to the frame via flexible polyurethane pads or “polyblocks”. They proved to be superior to springs in several ways. First, they allowed for a superior range of motion when compared to springs, which was necessary for not only clearing curbs and other higher obstacles, but also to give the pusher the ability to get into depressions, something which spring designs could not do. Secondly, they gave the operator the ability to apply as little or as much downward pressure to the cutting edges as he wanted, which meant that this pusher, and this pusher alone, could cut through ice and hardpacked snow like it was powder.
The final benefit of using polyblocks became obvious after Strait had completed his design and began