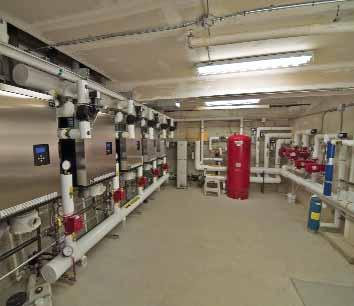
3 minute read
The right structure + creative thinking = a showcase system for efficiency & IAQ
The right structure + creative thinking =
BY ROY COLLVER
Too bad these ideal opportunities don’t come along more often.
When McLeod Road Elementary school in Surrey (SD no. 36) was due for a seismic upgrade, it was also due for an HVAC makeover as well. By the time Robert Cenedese of Rocky Point Engineering finished examining the structure, he knew this job could result in an enhanced heating system that would deliver superior energy savings and comfort, as well as a significant improvement in indoor air quality.
The existing heating system was primarily gas-fired unit ventilation heaters for the classrooms, along with a bit of perimeter baseboard supplied by a small boiler. Ventilation air was supplied through fixed dampers in the unit heaters, resulting in the classic dilemma of how best to set them up. (You are likely to get either extra heat loss when not needed, or inadequate ventilation in heavily occupied classrooms.)
Having experience and expertise in LEED® design, the Rocky Point team was used to thinking about energy savings first and foremost. This project presented some interesting possibilities not often available in school retrofit situations: • The building provided heated crawlspaces so as to allow hydronic distribution piping to be run unobtrusively throughout the structure. • The seismic upgrade process meant the school was going to be literally torn apart inside, so a radical redesign was possible without adding to the disruption. • Replacing all of the worn-out heating equipment meant that new equipment selection could be designed to be compatible with the most efficient type of heating plant
available – multiple-staged, lowtemperature condensing boilers. • There was a local boiler manufacturer, IBC Technologies, that was willing to work with Rocky Point and School
District 36 to provide equipment and control solutions to meet the stringent requirements of the school district. They required high-efficiency boilers to be mounted on a seismically rated, factory-engineered racking system, and the boilers had to be
Native BacNet® capable in order to fit into the district’s operating system. Discussions between the district, Rocky Point and IBC
Technologies resulted in the perfect boiler plant, married with the ideal heating system for this building. • They had the ability to provide an appropriately sized space to house an all-new boiler plant.
McLeod boiler room.
So how do you design the ideal system for this type of building?
Mr. Cenedese made the following decisions: • Use hydronic unit ventilators, with coils sized to be able to heat the spaces at design conditions, with maximum water temperatures of 160°F. • Choke the fluid flow rate to the heaters down so that they operate on a 40°F tee, optimizing condensation (efficiency) in the boilers at design temperatures (by returning 120°F water). BONUS! With a 40°F , the pumps can be smaller, the pipes can be smaller and the power required to drive the water around the building can be less. • Provide variable-volume fresh-air dampers to the unit ventilator heaters – tied to CO2 sensors in the classrooms – to optimize the amount of
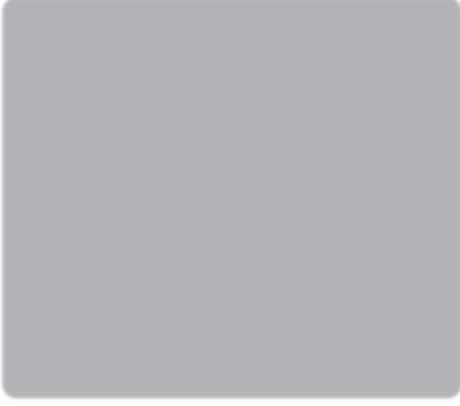
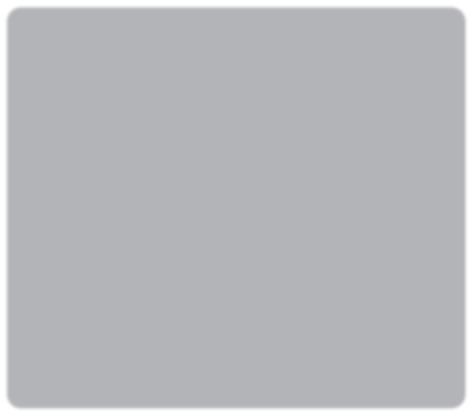

a showcase system for efficiency and IAQ
McLeod rack wall detail. McLeod rack floor detail.
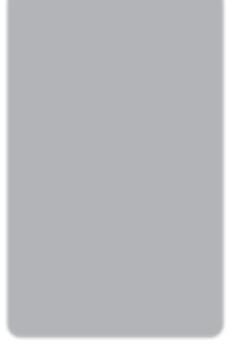
fresh air delivered to the classrooms based on occupancy and need (good duct design could also increase head-space). • Design the perimeter heating radiators to operate at lower operating temperatures, in order to maximize boiler condensation.
• Specify factory designed and supplied boiler-mounting racks that comply with seismic code requirements.
There are many more features to this design that deserve further comment, but I think you get the idea. When the right opportunity presents itself, and the right creative people work in collaboration to come up with creative solutions, “outside the box” then becomes “inside the box”.
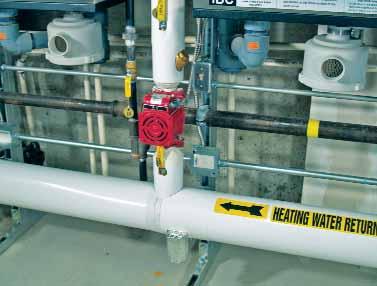

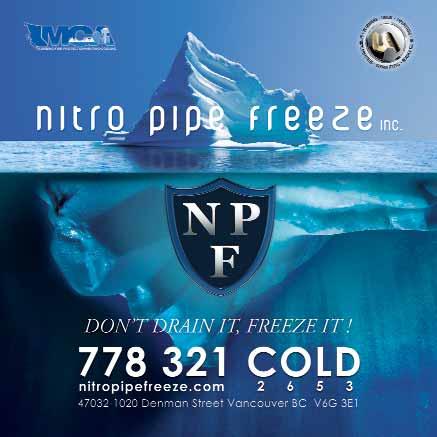