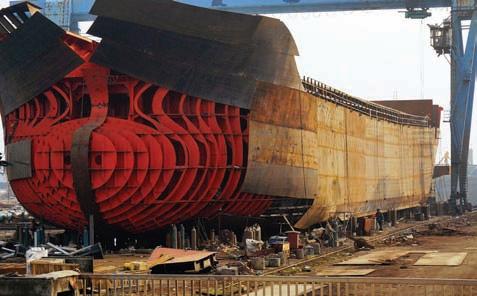
6 minute read
Gemi İnşasında Süreç Geliştirme Yöntemleri Uygulamaları
AYTEK GÜNGÖR Kıdemli Dizayn Planlama Koordinasyon Mühendisi STM Savunma Teknolojileri Mühendislik ve Ticaret AŞ
Gemi imalatı, eş zamanlı yürütülmek durumunda olan karmaşık süreçler ve bunlara bağlı pek çok faaliyet içerir. Dizayn, tedarik ve inşaya ek olarak planlama, yönetim, araştırma geliştirme, satın alma aktiviteleriyle ile bu sanayi kolu, pazar talebinde meydana gelen dalgalanmalardan yoğun şekilde etkilenir. Küresel ve yerel olarak rekabetçi kalabilmek isteyen paydaş; üretkenliği arttırmak, maliyeti düşürmek ve karını maksimize etmek zorundadır.
Advertisement
Gemi inşa projelerindeki düşük verimliliğin öne çıkan sebepleri; üretim hızındaki beklenmedik değişimler, süre aşımları, başarısız bütçe hesapları, ürün ve malzeme akışının aksaması, bekleme zamanları ve makinaların âtıl kalmasıdır. Toplam Kalite Yönetimi, Yalın, Altı Sigma, Kısıtlar Teorisi ve Güvenilirlik Merkezli Bakım gibi müşteri memnuniyetini ve üretkenliği hedef alan yöntemlerin, uygun şekil ve aşamalarda tatbik edilmesi, belirtilen sorunların aşılmasına yardımcı olacaktır.
Çelik Gemi İnşa İnşası
Gemi inşa ürün değer zinciri; tasarım, tedarik, üretim, denetim ve sonrası hizmetlerdir. Bu süreçler ve bağlı faaliyetler, birbiri ile ilişkilidir ve eş zamanlı olarak yürürler.
Modern anlamda gemi inşası, istisnalar dışında seri üretime uygun değildir. Seri üretim nimetlerinin, gemi imalatına uygulanmasının yolu grup teknolojisinden geçer. Grup teknolojisi; benzer işlemlere tabi olan, farklı malzeme ve şekle sahip olabilen, küçük ve orta nicelikteki parçaların aynı yerde konumlanmış ve çizelgelenmiş makine, insan ve teçhizat tarafından işlenmesidir. Sadece imalatı değil aynı zamanda tasarım ve tedarik süreçlerini de yoğun olarak etkiler ve şekillendirir.
Gemi tasarımı, bir optimizasyon sürecidir ve dizayn spirali döngüsü halinde ilerler. Boyutlandırma, gemi yerleşim çalışmaları, yapısal hesap ve analizleri, donatım şematiklerinin oluşturulması ve nihayetinde işçilik resimlerinin elde edilmesi olarak kısaca özetlenebilir. Tasarım dokümantasyonu grup teknolojisine paralel olarak iş paketleri halinde tertip edilir, inşa ve tedariki aksatmayacak şekilde tersaneye gönderilir.
Gemi imalatı, sac kesimiyle başlar ve benzer imalat süreçlerinden geçen parçaların üretilmesiyle devam eder. Bunlar daha karmaşık yapıları oluşturacak şekilde çeşitli kaynak teknolojileri kullanılarak monte edilir ve nihayetinde blok adı verilen ara ürünler ortaya çıkar. Bu yapılar, kızağa konmadan önce belli ölçüde donatılır, ön boya işlemlerine tabi tutulurlar. Kızağa alınan bloklar birbirine monte edilir ve donatım süreçlerine devam edilir. Ana makinenin gemiye alınması, makinaların çalıştırılması ve blok montaj işlerinin tamamlanması sonrası gemi
denize iner, kabul testleri yürütülür ve alıcıya teslim edilir. İnşa, donatım ve boya işleri için uygulanan bu sistematiğe Ürün Merkezli İş Kırılım Yapısı (PWBS) denir.
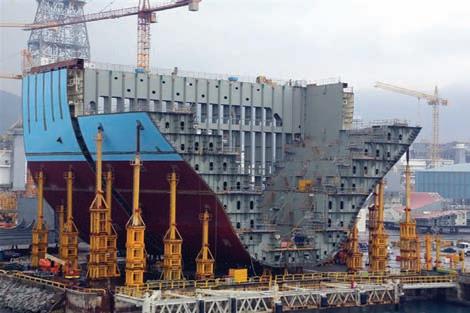
Süreç Geliştirme Yöntemlerinin
Gemi İnşaya Uygulanması
Toplam Kalite Yönetimi; operasyon ve yönetim seviyesinde kaliteyi sürekli bir şekilde yükseltmek amacıyla uygulananı yönetim metodudur. Burada “kalite”; belli bir ürün ya da hizmetin şartnamede belirtilen özelliklere ne kadar uyduğu, amacına ne ölçüde hizmet ettiği, verilen paraya değip değmediği ya da sadece müşterinin kalite veya hizmet ile ilgili öznel değerlendirmesi olarak algılanabilir. Müşteri odaklı yaklaşım, Kaizen, sebep-sonuç diyagramları, akış şemaları, kontrol listeleri, dağılım diyagramları, pareto analizi, histogramlar bazı Toplam Kalite Yöntemi araçlarındandır.
Toplam Kalite Yönetiminin gemi inşasına uygulanması; pek çok bileşeni olan büyük hacimli ürünlerin mevzu bahis olması ve yoğun bir şekilde iç içe geçmiş süreçler sebebiyle büyük çaba ve dönüşüm gerektirir. Bu değişim, sadece teknik değil aynı zamanda yöntemsel, stratejik ve kurumsaldır. Ürün ve faaliyet tanımı ele alınmalıdır. Müşteri memnuniyeti ve verimlilik hedefe oturtularak kapsamlı çalışmalar yürütülmelidir.
Yalın Felsefesi; üretkenliğin arttırılması için kayıpların bertaraf edilmesi doktrinidir. En temel kayıp türleri; hatalar, aşırı üretim, bekleme süresi ile geçen zaman, katma değeri olmayan faaliyetler ve aşırı işlem uygulama olarak özetlenebilir.
Yalın Üretim, panel ve blok montajında kullanılabilir. Kaynak gibi sürekli tekrarlanan faaliyetlerde bileşenlerin döndürülmesi esnasında bolca zaman kaybı yaşanmaktadır. Bu parçaların uygun şekilde boyutlandırılması ve tek taraflı otomatik kaynak teknolojilerinin yaygınlaşması ile yaşanan zaman ve malzeme kayıplarının önüne geçilebilecektir.
Tasarım dokümanlarının, malzeme ve ekipmanların tam ihtiyaç duyulduğu esnada tersanede bulunması; hataların, tekrar işlemlerin ve zaman kaybının önüne geçecektir (Just-in-Time).
Altı Sigma; iş akışının hatalar ve değişkenlerden ayıklanarak iyileştirilmesidir. Burada “Sigma” tabiri istatistiksel bir kavramdır. Hataları yok etmede en başarılı uygulamalar Altı Sigma olarak tabir edilir (milyonda 3,4 adet hata). En başarısız uygulama ise Bir Sigmadır (milyonda 690 bin adet hata). Altı Sigma, bir döngü (DMDAV) halinde iyileştirmeyi hedeflemektedir. Faaliyetler planlanır ve başlatılır (Define), müşteri gereksinimleri belirlenir (Measure), tasarım özellikleri geliştirilir, gereksizler ayıklanır (Analyze), dizayn geliştirilir (Design) ve yürütülür (Verify). Döngü, Altı Sigma seviyesine ulaşana kadar iyileştirilerek devam ettirilir.
Altı Sigma yöntemi, kaynak süreçlerine uygulanabilir. Robotlar ve sensörler; işlem öncesinde parçaların uygun pozisyona alınması, yüzey işlemlerinin yapılması; kaynak sonrası muayene esnasında yetenekli ve tecrübeli personelin gözetiminde kullanılabilir. Böylece insan faktörü azalacak, makineleşme artacak, değişkenlik azalacak ve hata asgariye inecektir.
Yalın Altı Sigma; kayıp ve değişkenliğin dolayısıyla hatanın ayıklanarak süreç iyileştirmesini öngören iş modelidir. Bu döngüde (DMAIC) yine Tanımla (D), Ölç (M) ve Analiz et (A) mevcuttur. Bunun yanında tasarım iyileştirmesini öngören geliştir (Improve) ve yapılan iyileştirmenin kontrol edildiği kontrol et (Control) aşamaları eklenmiştir.
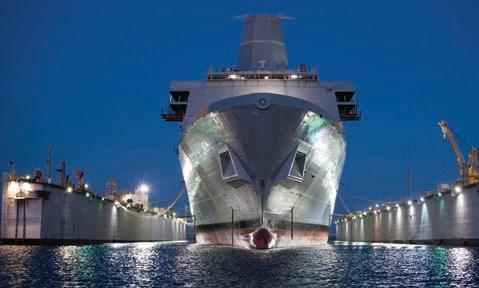
Gemi havuzlama, tamir, kreyn bulunurluğu konularında Yalın Altı Sigma uygulamaları yapılmıştır. Böylece malzeme kaybı azaltılmış, daha az iş gücüne gereksinim duyulmuştur. Kaynak işlemi maliyeti azalmış, tekrar işlem, kurulma zamanı düşürülmüştür.
Kısıtlar Teorisi; bir işin başarısının önünde duran en
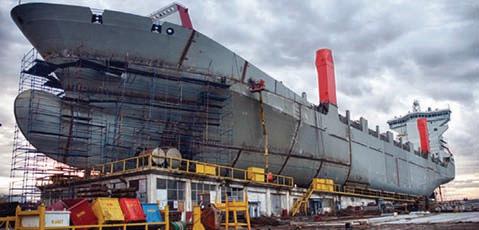
büyük engelin tespit edilip artık bir sıkışıklık teşkil etmeyene kadar geliştirildiği sistemdir. Burada “kısıt” sadece olumsuz bir kavram olarak algılanmamalıdır. Tıpkı bir şişe boğazı gibi akışın kontrol edilmesi için elzemdir. Ancak çok dar olursa akış gerçekleşmez ve genişletilmesi gerekir.
Beş Odaklanma Aşaması adı verilen yaklaşımda; düşünme süreci (The Thinking Process) kullanılarak kısıt (ya da darboğaz) tanımlanır (Identify). Kısıtın istenen miktarda çalışmasını garantilemek için süre ya da malzeme, darboğazın önüne tampon olarak konulur (Exploit). Kritik olmayan faaliyetler darboğaza göre ayarlanır (Subordinate). Kısıtın iş hacmi yükseltilir (Exploit) ve kapasite yükseltmesinden sonra hala kısıt olup olmadığının kontrol edilir.
Düşünme süreçleri kullanılarak yapılan çalışmalarda, çoklu siparişleri olan bir tersanenin ana kısıtının kızak kullanımı olduğu görülmüştür. Burada asıl konu; blok imalat atölyelerinin olabildiğince çabuk şekilde blokları imal ederek gönderme, kızak üstü montaj ekibinin zaman planına uyma eğilimidir. Bu döngü sonunda blok bazında süreç içi iş yığınları (Work-in-Process) oluşur ve odaklanma sorunu yaşanır. Beş odaklanma aşaması ile iş akışı kontrol altına alınabilir.
Gemi İnşasında En Önemli Kısıt
Kızak Kullanımıdır
Güvenilirlik Merkezli Bakım; maliyet göz önüne alınarak bir sistem ya da makinenin ne kadar süre daha güvenli bir şekilde iş görebileceğinin tespiti, gereksiz bakım masraf ve süresinden kaçınma stratejisidir. Arızaların tümüyle engellenmesi yerine muhtemel sonuçları üzerinde durulur. Her ne kadar arızayı göğüslemeye hazır olma gibi algılansa da önce güvenlik prensibini esas alır ve Hata Modu ve Etkileri Analizi (FMEA) gibi metotlar kullanılır.
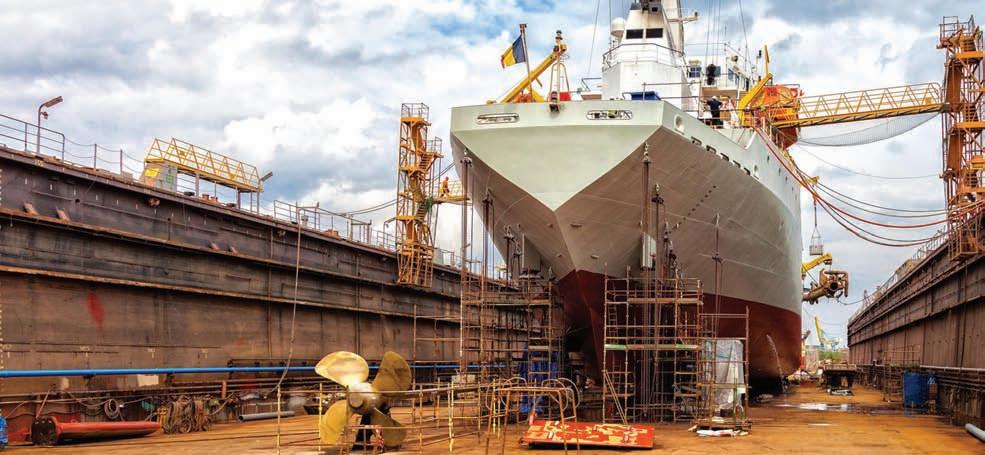
Güvenilirlik Merkezli Bakım; daha çok gemi makinalarının seyir süresince uygun bakım maliyetleri ile kullanılabilir durumda tutulması amacıyla tercih edilir. Kaynak makineleri, kreynler, konveyörler, güç üniteleri, CNC makineleri ve kaldırma ekipmanlarına da uygulanabilir. Fark edilen hatalar, geçmiş deneyimlerden de destek alınarak analiz edilir. Böylece bakım-tutum giderlerinden kayda değer tasarruf sağlanmış olur.
Sonuç
Bir firmanın nihai başarısı; yeni teknolojilerin ve üretkenlik arttırma yöntemlerini benimsemesi ile doğrudan ilişkilidir. Gemi inşa; tasarım, tedarik ve üretim gibi ana süreçler ve bunlara bağlı alt faaliyetlerin yoğun bir şekilde birbirini etkilediği ve eş zamanlı olarak yürütüldüğü karmaşık ve yönetilmesi zor olan bir uğraştır. Sektör paydaşlarının rekabetçi kalabilmek için süreç geliştirme yöntemlerini hayata geçirilmesi zaruridir.
Toplam Kalite Yönetimi; gemi inşa firmalarının politikaları, stratejileri ve yöntemlerinde, müşteri memnuniyeti ve kaliteyi merkeze alarak tüm çalışan ve yöneticilerinin katılımı ile mümkün kılınabilir. Kısıtlar Teorisi; kızak kullanımı gibi darboğazların tespiti, bunlardan faydalanılması, diğer tüm faaliyetlerin bu darboğaza uygun şekilde yürütülmesi ve nihayetinde kısıtın kapasitesinin arttırılması suretiyle uygulanabilir. Yalın ve Altı Sigma ise blok ve panel montajı esnasında, özellikle kaynak süreçlerinde uygulanabilir. Yalın felsefesi ayrıca malzeme, teçhizat, tasarım dokümantasyonu tedarikinde kayda değer başarı sağlayabilir. Güvenilirlik Merkezli Bakım; makinalarının kalan ömrünün takip edilmesi ve bakım faaliyetleri için uygun zaman ve ayrılacak kaynağın miktarının tespiti kapsamında değerlendirilebilir.