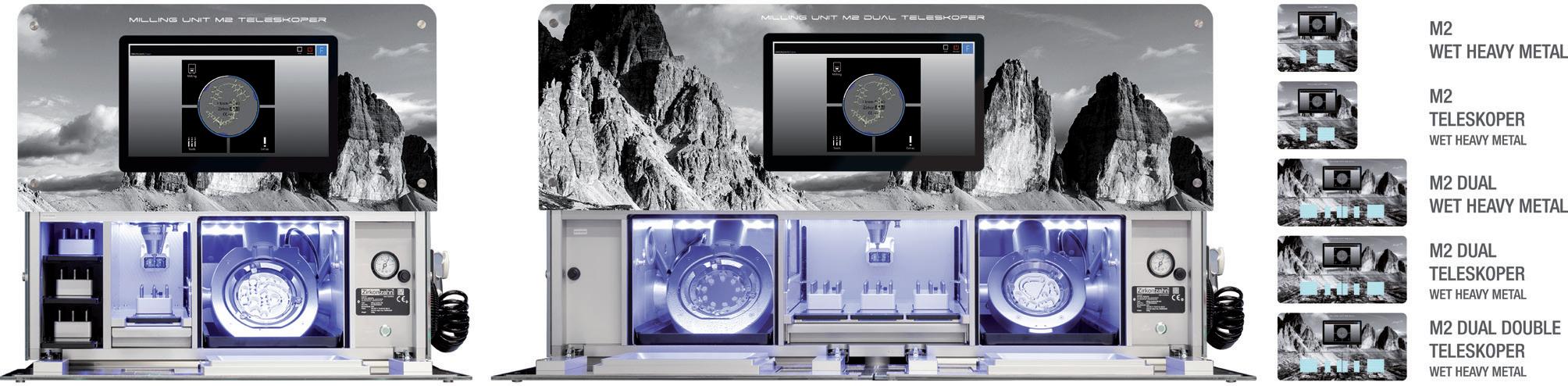
4 minute read
Zirkonzahn worldwide in word and deed!
In the heart of the Italian Alps, with the fundamental values of discipline, innovation, trust and responsibility, the family-run company Zirkonzahn provides innovative solutions for the dental sector. Under the motto “Everything under one roof”, all Zirkonzahn’s milling materials, hardware equipment, software, implant prosthetic components and tools are conceived and developed in-house, in order to guarantee constant controls over the production process and therefore comply with the company’s high-quality standards. In their homeland, South Tyrol, Italy, Zirkonzahn has their headquarters, main education centres, a dental laboratory and operates five production sites, all located within a few kilometres from the head office. Purchasing raw materials only from specially selected suppliers, the company develops new visions and technologies providing dentists and dental technicians with dedicated, simplified instruments for a smooth and reliable workflow, from the implant planning procedures to the final restoration.
From scanning to sinteringEverything for your workflow!
In order to meet the patient’s growing demand for fast and aesthetic solutions without compromising on quality, some of the latest technologies launched in the market greatly simplify the production process of dental restorations. With the new, highly accurate Detection Eye intraoral scanner, the patient’s jaw can be easily digitised in less than 60 seconds, making the impressiontaking more comfortable for the patient and ensuring real-time scan with realistic colours and preparation borders. The scanner has been designed to be lightweight, compact and ergonomic and the scanning areas do not need to be pre-treated with powder, which simplifies the acquisition process. Once the data have been captured, they can be easily and quickly loaded into the Zirkonzahn.Software for the model design. The created model can be then milled in one of the five milling units of the new M2 comfort line or 3D printed using the P4000 Printer.
Fully automatic, flexible and vibration free, the M2 milling unit comfort line exemplifies precision and flexibility. With the M2 Wet Heavy Metal, the M2 Teleskoper, the M2 Dual Wet Heavy Metal, the M2 Dual Teleskoper and the M2 Dual Double Teleskoper, the comfort line comprises five milling machines with fully automatic 5+1 axis simultaneous milling technology.
The highlight is the extra-large Teleskoper Orbit (ø 125 mm): in combination with special interchangeable holders, it allows the processing of all common soft and hard material blanks of ø 95, 98, 106 or even 125 mm. With the Teleskoper Orbit, blanks can be removed and reinserted back into the orbit at the same position with high precision in the micron range.
In addition, the pre-set Ultraspeed programs of the Zirkonofen Turbo, perfectly adapted to each kind of Zirkonzahn zirconia, allow to sinter small zirconia structures in about 1 hour and 30 minutes only, with no variation of flexural strength, colour and fit values. This cuts processing time by 81% and reduces electrical consumption by 73%.


No limitations! With the extra-large Teleskoper Orbit, it is now possible to mill material blanks with Ø 95, 98, 106 or even 125 mm, as well as glass ceramics and Raw-Abutments® blanks. Discs can be removed and reinserted back into the orbit at the same position with high precision in micron range - this is particularly useful for the two-stage fabrication of immediate restorations in case of implant-supported prostheses (Double Milling technique).
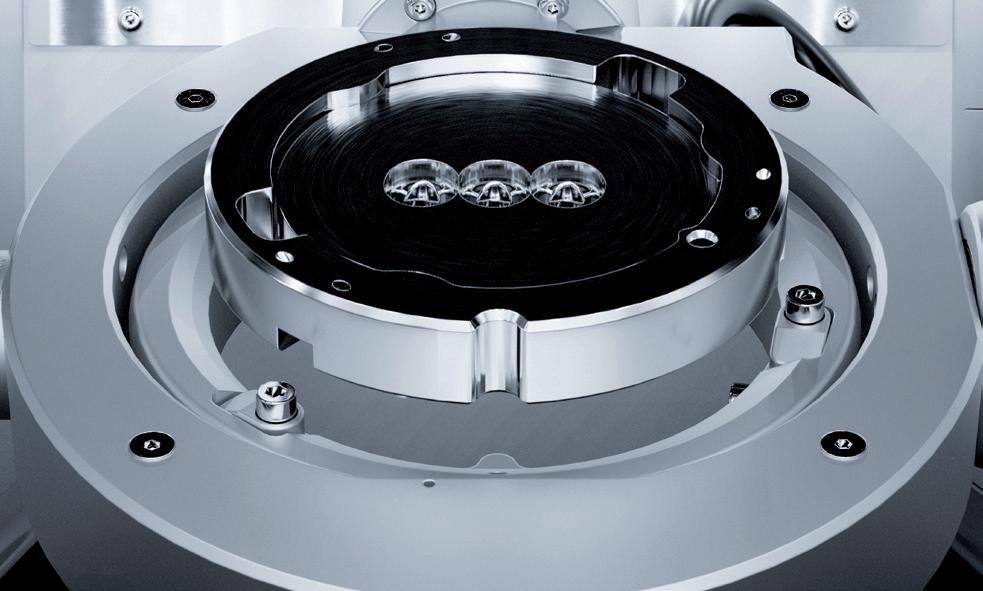
Optimal material and colour selection: monolithic sample teeth available in the shape of upper incisor, upper incisor with minimal cutback for further characterisation, lower incisor and premolar.
Prettau® zirconia – Manufactured with pride
Prettau® zirconia is the material of choice for functional and aesthetical solutions - from single crowns to monolithic full arches. The Prettau line includes different zirconia typologies available as discs (Ø 95 or 98 with step) as well as mini blanks. In the last years, the company’s range of zirconia typologies has recently embarked even more on the path of monolithic design with the new Dispersive® versions. In this case, ceramic layering and manual colouring are not necessary anymore, since materials are already provided with a very smooth, natural colour transition during the manufacturing process. However, for an even more patientspecific result, structures can be further characterised with colouring liquids or, alternatively, a minimal cutback can be applied for the subsequent application of a slight layer of Fresco Ceramics. Developed for both gingival and vestibular regions, these new ceramic pastes do not require staining anymore. Prettau 3 Dispersive is the latest material developed by the company and is characterised by a triple gradient of colour, translucency values and flexural strenght (Gradual-Triplex-Technology).
Monolithic Prettau® zirconia shade guides - Identical to the final restoration
With the new Zirkonzahn Shade Guides, the patient’s tooth colour can be precisely determined on the basis of monolithic zirconia sample teeth.
In this way, it’s possible to determine the most suitable Prettau zirconia material in a safe and quick manner: if the shade guide and the material of the zirconia prosthesis are identical, it is ensured that the colour of the restoration corresponds 1:1 with the natural tooth colour of the patient.
The colour spectrum is inspired by the VITA® Classical shade range and is comprised of 16 dentine colours (A1-D4) and 3 bleach shades.
TGA listed implant prosthetics componentsAvailable for more than 140 implant systems
As one of the world’s largest manufacturers, Zirkonzahn’s implant prosthetics components are made with high-quality medical titanium alloy and meet the strictest quality criteria. The wide portfolio, which includes Scanmarkers, White Scanmarkers, ScanAnalogs (laboratory analogues used as scanmarkers), impression copings, laboratory analogues, Multi Unit Abutments, Raw-Abutments® and healing caps also comprises:
• Zirkonzahn LOC-Connector, a snap attachment system for implants and bars to fix removable dental prostheses on the implant;
• Multi Unit Abutments 17°, characterised by a 17° angle to compensate for any implant inclinations and with two different anti-rotation connection types which allow intermediate positions;
• Titanium Bases K85, with the chimney height adjustable to the individual tooth length;
• Titanium Bases K80 Angled Screw Channel, with a chimney height adjustable to the tooth length and the possibility to tilt the screw access channel from 0° to 30°; and
• White Metal Scanmarkers, reusable scanbodies to acquire the implant position and orientation during intraoral and model scans.
All components - available for more than 140 implant systems - are warrantied up to 30 years, including the implants from other manufacturers used with Zirkonzahn implant abutments.
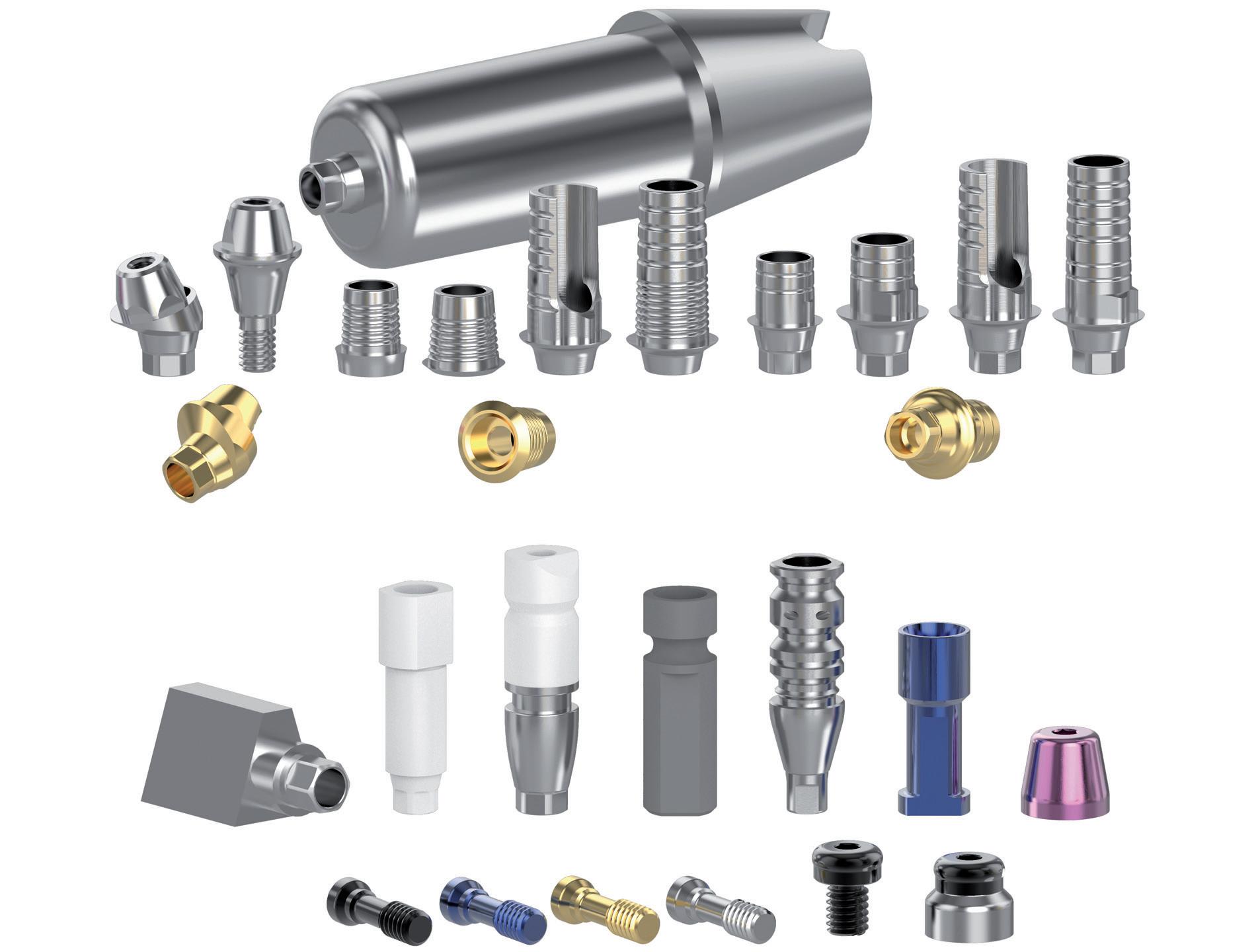
All Zirkonzahn’s innovative products have been conceived to improve the techno-clinical team working process in a smooth and time-efficient manner.
In cooperation with various research institutes, the company constantly develops new and intelligent solutions for creating a 100% patient-oriented, natural-looking restoration.
Find out more about Zirkonzahn by visiting www.zirkonzahn.com or follow the company on social media!