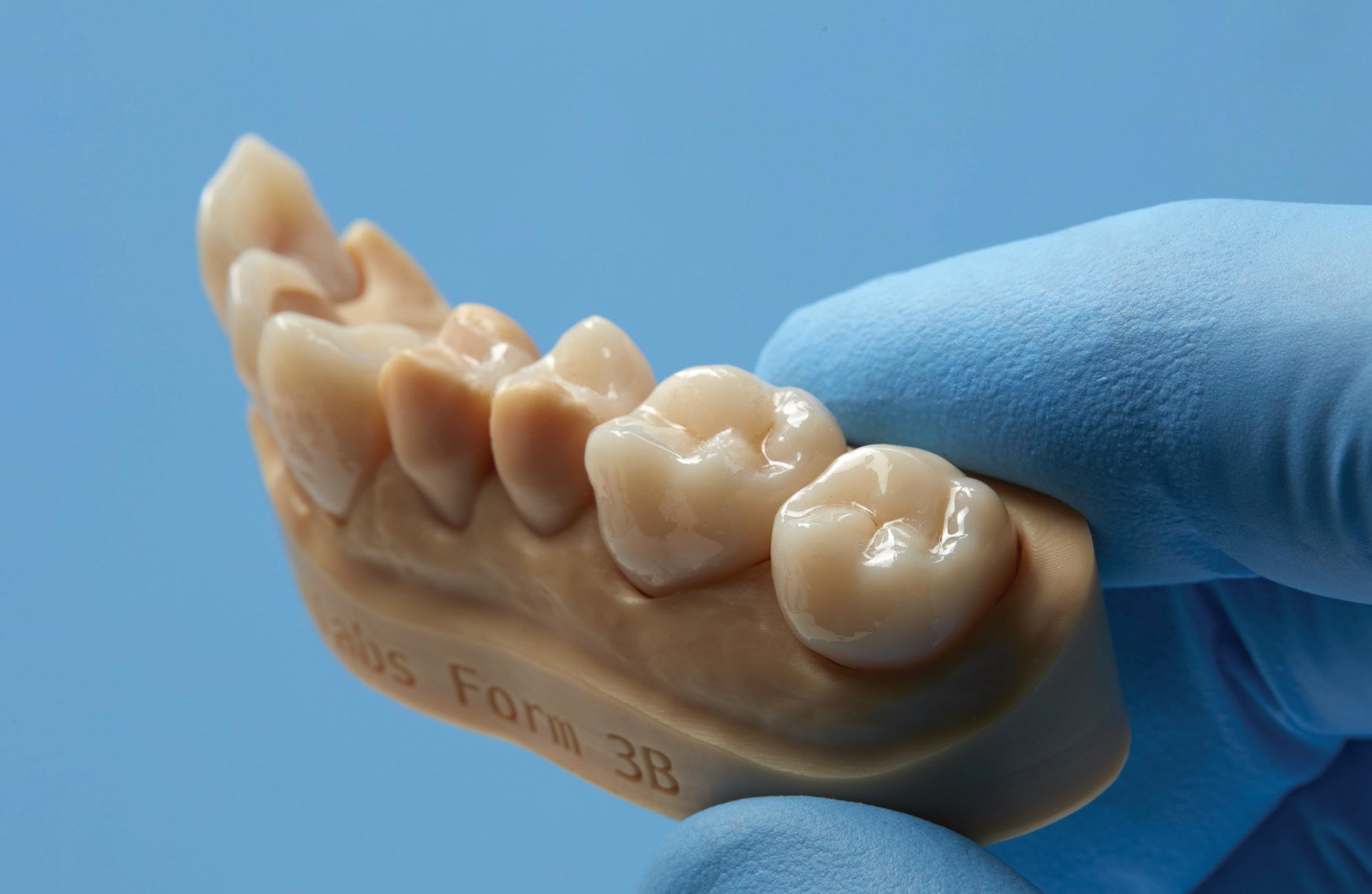
4 minute read
D
entistry as a profession is well-known for adopting new technologies and often well ahead of the curve when it comes to Star Trek-like advancements. Intraoral scanning, CAD/CAM manufacturing, CBCT and digital x-ray just to name a few... and of course the latest and greatest craze, 3D printing.
Although 3D printing has been around since the 1980s, in the last 5 years or so it has really come into its own as the next big thing in manufacturing. The 3D printing option has changed dramatically as newer, progressively lower cost machines have come to market that are physically smaller, more user friendly and designed for dental.
The latest new wave of “additive manufacturing” or desktop 3D printing has the whole of dentistry whipped into a frenzy of amazing expectation. The truth is, 3D printing is a great technology and can be adapted well for some dental applications. However, as with all marketing, it tends to gloss the results and instead of trying to polish a wet cigar, they defiantly roll it in glitter which actually can give people false expectations.
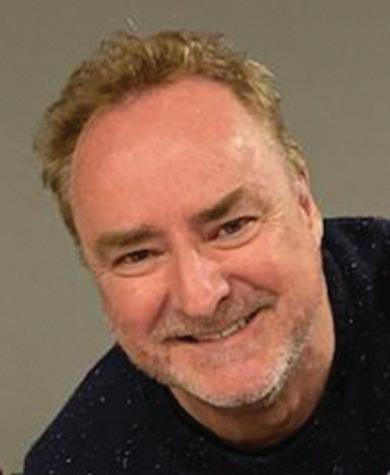
Certainly 3D printing works well for models, surgical guides, splints, sleep appliances, orthodontic aligner manufacturing, dentures and lots of other polymer-based appliances, but what about directly printing crowns and bridges?
To answer that, we would have to ask many questions. What is the case proposed?; What material do we want to use?; Where will we print it (chairside or lab side)?; How long is post-processing and is the resultant crown viable aesthetically?; Are the physical properties up to the level we would expect for a long-term restoration?; and is it economically viable? Phew!
Materials
Firstly, let’s look at dentally-focused materials that can currently be 3D-printed.
Lithium Disilicate is a well-known and loved material. It grew to fame via the e.max brand from Ivoclar. It’s a glass ceramic and aesthetically, some say it cannot be beaten as a monolithic restoration. It has a flexural strength of about 400 MPa and a flexural modulus of approximately 70,000 MPa!

One company of note, LITHOZ from Austria, is investing heavily into creating lithium disilicate 3D printed restorations and are making a big noise about it. The printing of lithium disilicate opens up great possibilities, especially with restorations such as veneers which traditionally can be time consuming and technique and ability dependent, however it could possibly be used for all areas where lithium disilicate is used currently.

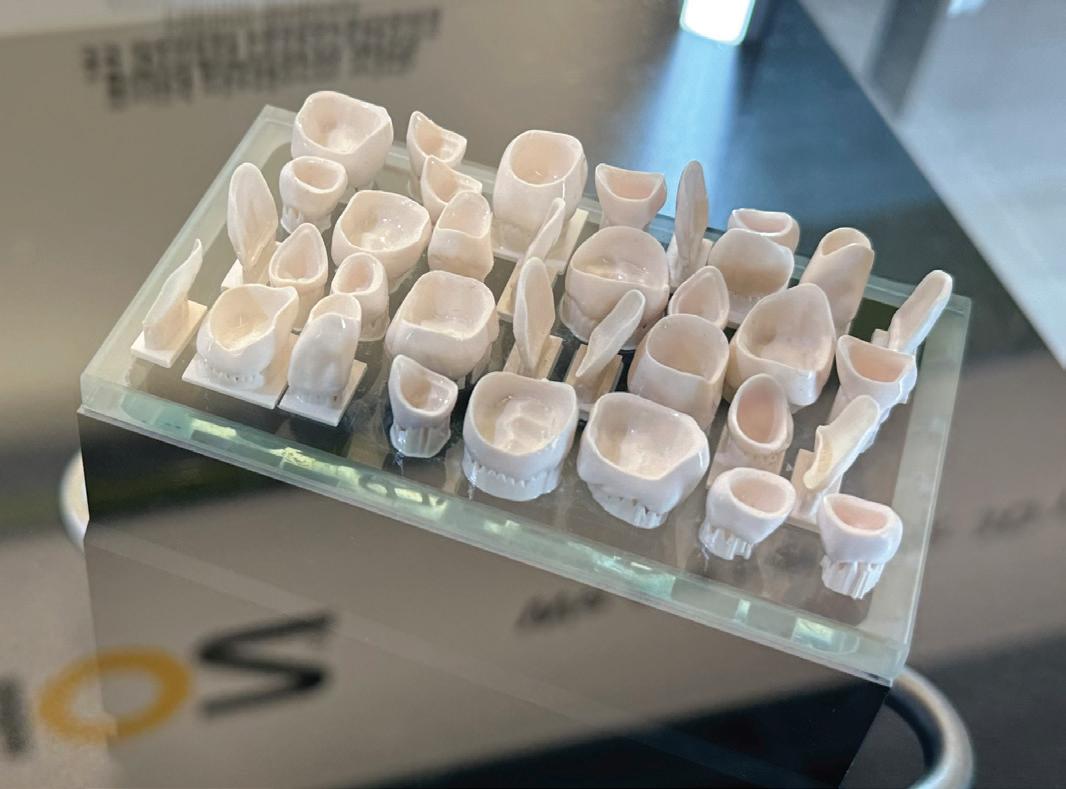
LITHOZ called their printing technology LCM, or Lithography Ceramic Manufacturing and it’s definitely something to watch in the future. However, the current technology to print lithium disilicate comes with a hefty price tag so to get an affordable chairside solution may still be a long way off.
Zirconia is in a similar situation. There are a few companies dabbling in printable zirconia technology and yes, there are printers that can print zirconia. However, the post processing time required currently leaves this technology in a similar bag as lithium disilicate. It’s currently not possible to have a patient sit down, do a quick scan and print an all-ceramic crown in a few minutes; however this will change in the future.
For all glass ceramics, 3D printing materials is the main reason you won’t see a chairside solution for some time as printing and post processing is very time consuming as mentioned before. The ceramic is in a liquified form with a binder holding the ceramic particles together and this “mix” is laid down layer-by-layer.
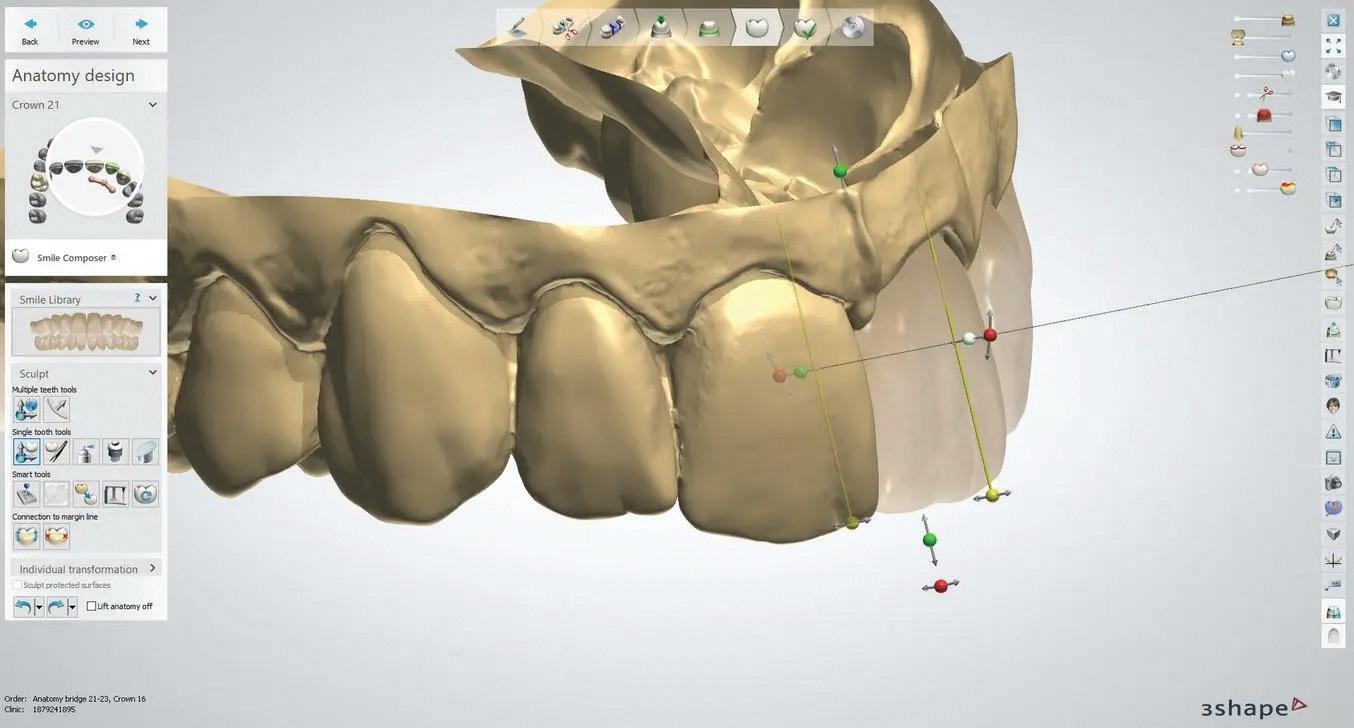
Once the part is printed, the binder needs to be removed, usually by heat over time and the glass ceramic or ceramic also needs to be crystalised or sintered to create the restoration ready for finishing.
At present, this is a fairly long process so it’s not viable to be used chairside. Dental labs are experimenting with this technology and while it’s in its infancy, there may possibly be some advantages to the process. Traditional milling or pressing (which can involve 3D printed models) of ceramics will remain the most viable process for some time yet. In fact, many companies are trying to make chairside milling even more viable.
Hybrid composite 3D printable materials
Probably no material group is as polarising as hybrid composites to create a definitive 3D printed crown. Some people will think it’s a great idea whilst others find themselves running in the opposite direction. Let’s be clear here, we’re talking about a crown at the moment; we’re not including any bridgework here as that will open up a completely different can of worms.
The materials used for 3D printing hybrid composites vary widely from one company to the next, however all are starting to show great promise as a restorative material. Most are nanofilled ceramic composites. Seremco, for example, have a product called Crowntec that has a flexural strength of 135 MPa and an elastic modulus of 4000 MPa which seems to be one of the category leaders. They suggest this product is for permanent crowns, inlays, onlays and temporary bridges. The elastic modulus is key here, notice it is 4000 Mpa.

Formlabs describes their permanent crown material as “a toothcoloured, ceramic-filled resin for 3D printing permanent single crowns, inlays, onlays and veneers. Permanent Crown Resin produces high strength, long term restorations with an accurate and precise fit, available in four VITA Classical* shades. Low water absorption and a smooth finish ensure restorations made from Permanent Crown Resin have a low tendency to age, discolour or accumulate plaque”. They state the flexural strength is 116 MPa and a Flexural modulus of 4090 MPa.
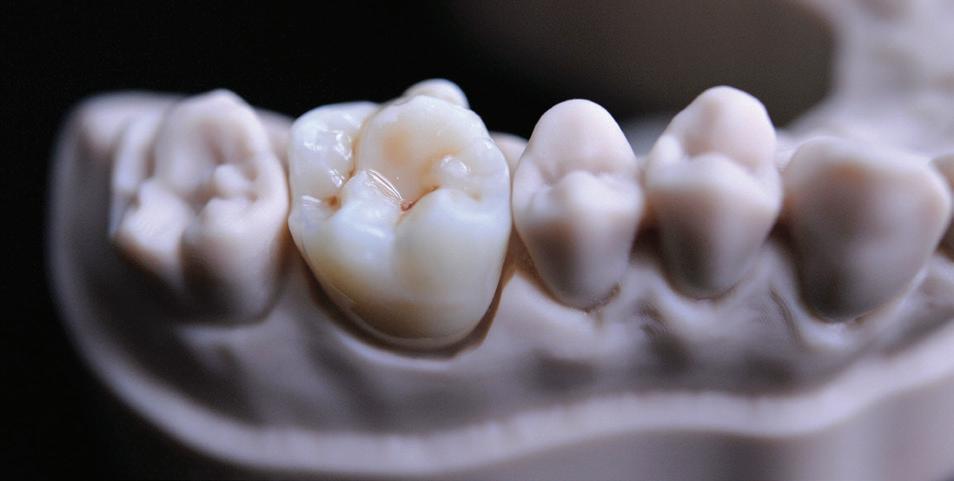
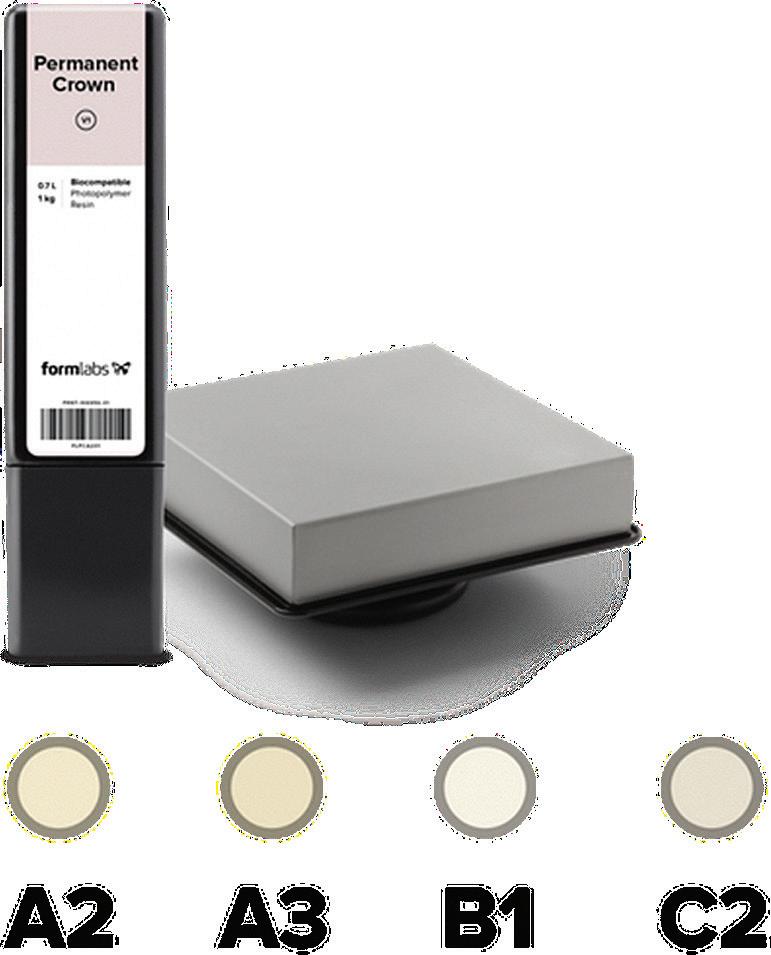
SprintRay describes their new material in partnership with Bego as “a new hybrid nanoceramic, FDA-cleared Class II resin for 3D printed definitive full crowns, partial crowns, and veneers. Ceramic Crown is a ceramic dominant material, with over 50% inorganic ceramic content, for high strength and resistance to wear making SprintRay Ceramic Crown a go-to material for definitive 3D crowns”. Flexural strength of 136 MPa and a Flexural modulus of 7600 MPa.
I think you can see a pattern here regarding the flexural strength and flexural modulus. Remembering a higher flexural modulus indicates a material is more resistant to bending, while a lower flexural modulus indicates a material has a higher tendency to bend when a given amount of bending stress is applied.
Does all this mean the crown will have the mechanical properties to be suitable for long term use? This will no doubt be a point of debate for many, but in the correct circumstances, it could well be the case.
3D printed aesthetics
So what about the aesthetics of these materials? Unfortunately all of these materials are monochromatic as they are usually printed from one shade of resin, for example A2, A3 etc. However, after curing, they can be stained and manipulated in many ways to characterise them, so this is an option. For highly aesthetically demanding cases, however, they may not be suitable.
There are companies working on techniques to improve the printing. Of note is the company DWS with their technique called Photoshade Adaptive Gradient Technology which gives the restoration the appearance of having multiple areas of the shade at differing levels.