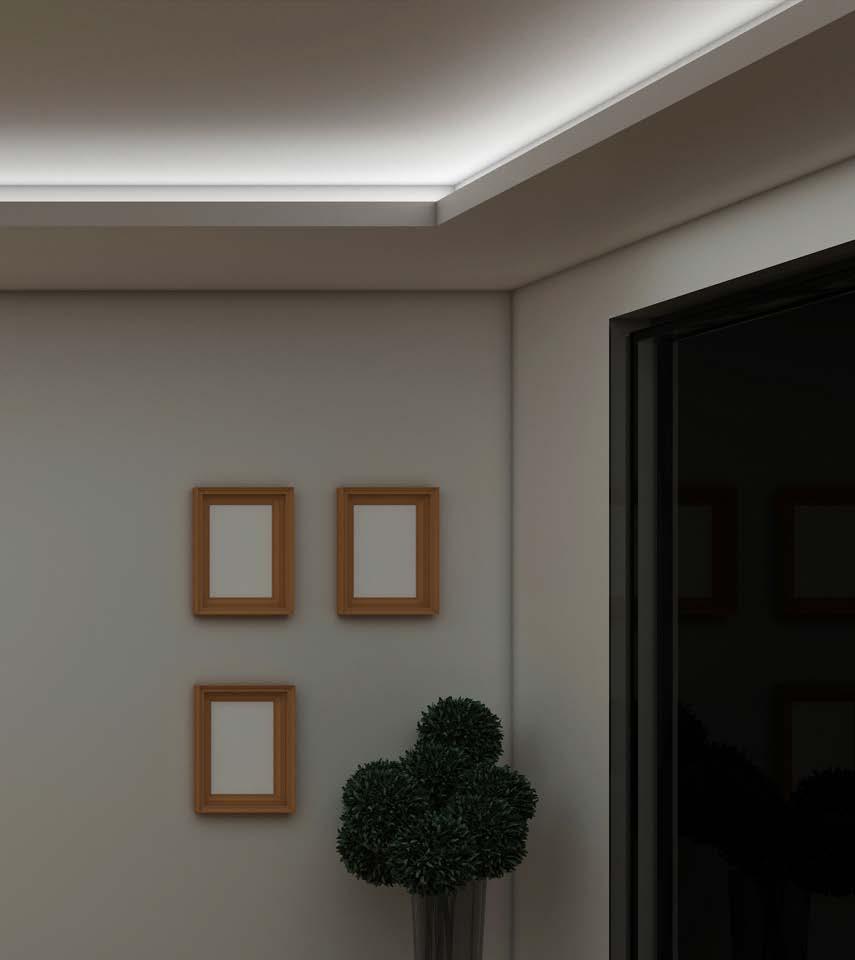
8 minute read
A Line of Light
from DEC 2022
By James R. Benya, PE, FIES, FIALD
Every lighting design specification has its Type “A”, Type “B” and other different luminaires on down the line in the fixture schedule to “Type X’ and sometimes beyond. Type “A” is usually the luminaire used the most and that establishes the overall character of the lighting in the majority of spaces, while other types light the smaller and support spaces. Type “X” is usually the exit signs.
A quick aside - there is no rule or code that says you have to use this “type A” nomenclature on lighting plans. For many reasons lighting specifiers have used other versions, like Type A1 to suggest variations of the same thing, or like types A for incandescent and types F for fluorescent. You can use whatever you want, as long as it is consistent and clear.
Choosing Type “A” is a major milestone on most projects. Because of its quantity and prominence, it is usually the keynote of the lighting design for most commercial, institutional, government, and industrial projects. Not only will it affect the project’s energy code compliance and cost budget, but Type A will also affect the appearance, cost and complexity of other major building systems, especially ceilings. The Type A choice typically plays the most prominent role that lighting itself can in making an architectural quality statement. On major, well-funded projects, Type A has often been used to set the style and tone for the interior architecture and design, because, after all, lighting is usually very bright and prominent.
The most common uses of this kind of fixture schedule nomenclature and the importance of Type “A” are in offices, schools, libraries, laboratories, hospitals, government, and retail buildings. For over 80 years, lighting manufacturers have competed ferociously to produce appealing, energy-efficient, easy-to-maintain, competitively-priced general lighting systems.
In the last 50 years, the ubiquitous 2’ x 4’ recessed box troffer has evolved in every way imaginable, from dozens of different plastic lens types to honeycomb louvers, parabolic louvers, indirect baskets, direct baskets, and most recently, edge lit flat panels. Their evolution was based on the demands of architects, interior designers, and especially, electrical engineers and lighting designers seeking the best possible lighting system for visual comfort, visual performance, or just plain good looks while meeting what is almost always a tight budget. For instance, the parabolic troffer, mainstay lighting for almost 40 years in the marketplace, was invented to reduce reflected glare on computer screens, but because of its upscale appearance and style, it became the dominant type “A” lighting system for over 25 years.
Then there is Type “C” (or some other letter later in the alphabet). It is typically an important luminaire that is used in the better spaces in the building like main lobbies, galleries, executive suites and large meeting rooms. Often, the Type “C” provides the general and/or accent lighting, allowing for a few choice chandeliers or table lamps to add the “jewelry” of lighting to the project.
In the history of architectural lighting, Edison Price is perhaps one of the most important innovators in the design and use of recessed downlights and track lights in architectural lighting. At a time when incandescent lamps could easily consume 250 watts or more and fluorescent lighting was large, heavy, and needed a lot of volume, Price and the lighting designers and architects with whom he worked showed the world the magic of very well-designed lighting. Thus evolved the standard pattern of using point source lighting for a building’s better-finished spaces. The key reason, of course, is drama. The contrast between darkened ceilings and highlighted finished floors, good furniture and artwork are hallmarks of a space that commands attention and respect.
No one could have anticipated the revolution that LED technology would create for the Type “C” choices. Their dramatic impact is first in the small size and weight. Luminaires having small apertures, small or non-existent boxes above the ceiling, and small cross-sections can fit into spaces that older technology overwhelmed. Tiny cove lights, downlights and wallwashers enable classic lighting applications and designs that enjoy a finesse that has been hard to achieve with legacy technology. Today, through apertures of only 1 square inch(!), an LED luminaire can project as much light as the 60-to-75-watt 6” cans of yore. Linear wallwashers only 2” wide replace rows of cans or robust asymmetric-throw semi-recessed luminaires of only a mere decade ago.
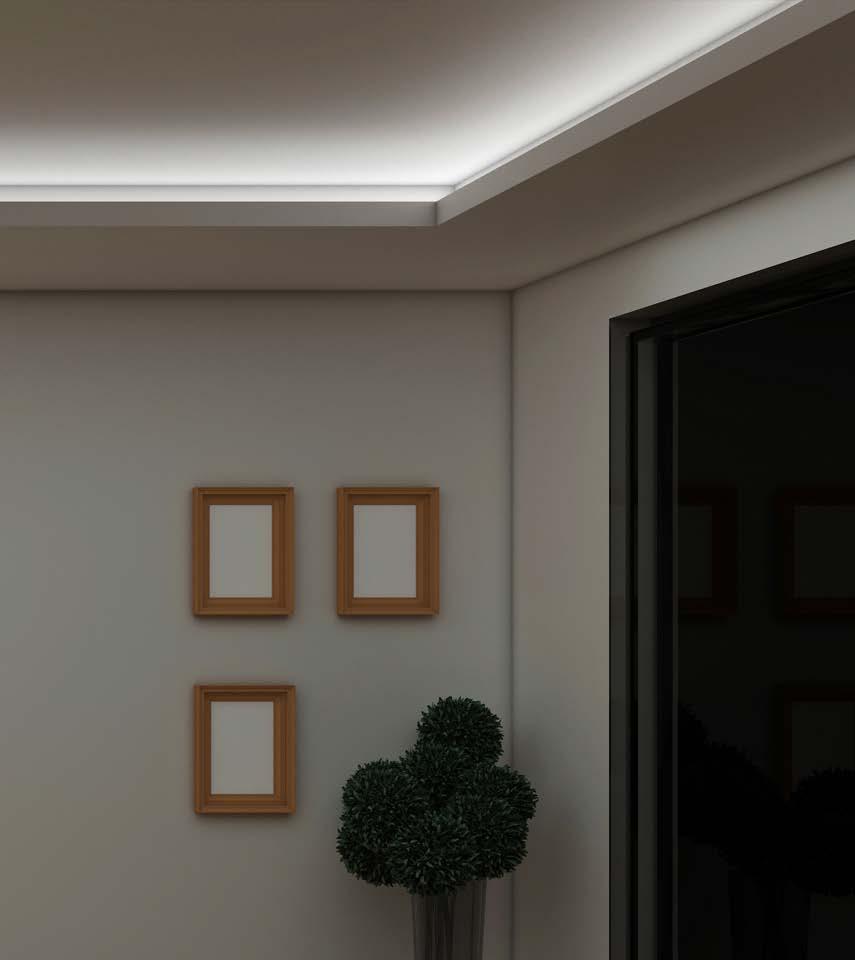
Cove Lighting by GENLED Brands
The late Sylvan R. (Sy) Shemitz, a contemporary of Price and in his own right a legendary lighting designer and inventor of superb wallwash luminaires used in many high-profile projects, would be positively amazed to see what can be done today.
The capabilities of LED lighting have given birth to a new luminaire style, the line of light. Although theoretically possible using legacy light sources like cold cathode or neon, the custom nature of the lighting and the expense and complication of installing large fixtures into a highly finished ceiling made such designs insanely expensive, complicated and fussy.
Combining troffers in-line was hardly acceptable because the line of light was broken every four feet by lamp sockets. And, by adding a parallel fluorescent lamp with offset sockets, luminaires became increasingly large and indelicate. Not to mention expensive.
Instead, the line of light employs a strip of LED chips mounted to a strip that contains electrical circuits and heat-sink materials. The shape of the strip is versatile and can also be round, square or flexible to suit the luminaire being designed. The strip is thermally connected to the housing, which in addition to mounting the luminaire is also the all-important heat sink. Not needing circulating air inside like legacy lighting, the strip can be only as thick as the ceiling itself, and a remote low voltage driver can be placed where convenient.
A number of specialty lighting manufacturers have developed lighting systems of different widths, thicknesses, styles and mounting locations, indoors and outdoors. Among the more amazing developments are wet-label and submersible products that can flushed into walkways, driveways and even swimming pool bottoms. The biggest limitation has generally been trying to stick with linear lines of light because both aluminum extrusions and light strips tend to be linear too.
In staying creative and competitive, once again our industry now offers a variety of products that push the envelope and attract designers’ interest. The impetus for this article is a newly introduced recessed line-of-light product that can be curved in the horizontal place to make patterns in the ceiling.
While the idea is not new, it is a major testament to our industry that I might now employ lighting that is a pattern cut into the ceiling plane, splitting the huge difference between conventional recessed lighting and the impact usually reserved for a chandelier and allowing me to add a pattern to a ceiling with lighting in an artful manner that delivers light in an appealing way.
Welcome to a new lighting tool that changes the way we can light those Type “C” situations in a distinctive and custom manner without the limitations of past generations of lighting or hard-to-work with old technologies like neon or cold cathode lighting!
The Difference Between Sparkle and Glare
One of lighting design’s biggest challenges is to mitigate or prevent glare. Glare is a generally undesirable outcome of direct and directional lighting, usually caused by too much light emitted through too small an aperture. Since the first downlight, controlling the beam so that it operates right on the edge became an art form that decades ago brought great success to a number of companies in our past like Lightolier, Kurt Versen, Edison Price, and Gotham.
With the recessed line of light, glare should be a real concern. Like the downlight, the adjacent ceiling is usually not illuminated except by indirect light or daylight. The resulting scene is dramatic because there is significant contrast between the relatively dark ceiling and the bright volume of the space below. With downlights, the luminaire uses shielding to prevent the viewer from seeing the light source until one must look up to see glare. This can also be accomplished by the recessed line of light, but it will require a lens or louver to concentrate light into the angles nearer to nadir.
From a design standpoint, the purpose of the line of light is to itself be bright, to create a pattern in the ceiling. Most basic products use a diffusing lens, or the LEDs are embedded into diffusing material, but some products employ sophisticated micro-optics to try to capture the shielding of good downlights. In other words, shielding is the key to making line-of-light luminaires work without glare. For general lighting levels in most space types, look for line-of-light luminaires that address this important detail.
However, there will be times when a bright line of light is desired. To keep it from becoming too bright and glaring, consider using a light-colored ceiling that will capture the reflected downlight and reduce the brightness of the luminaire. One might also augment the line of light luminaire with well-shielded downlights to increase the upward reflected light. A bright line of light in a dark ceiling might be dramatic, but hard to enjoy. ■