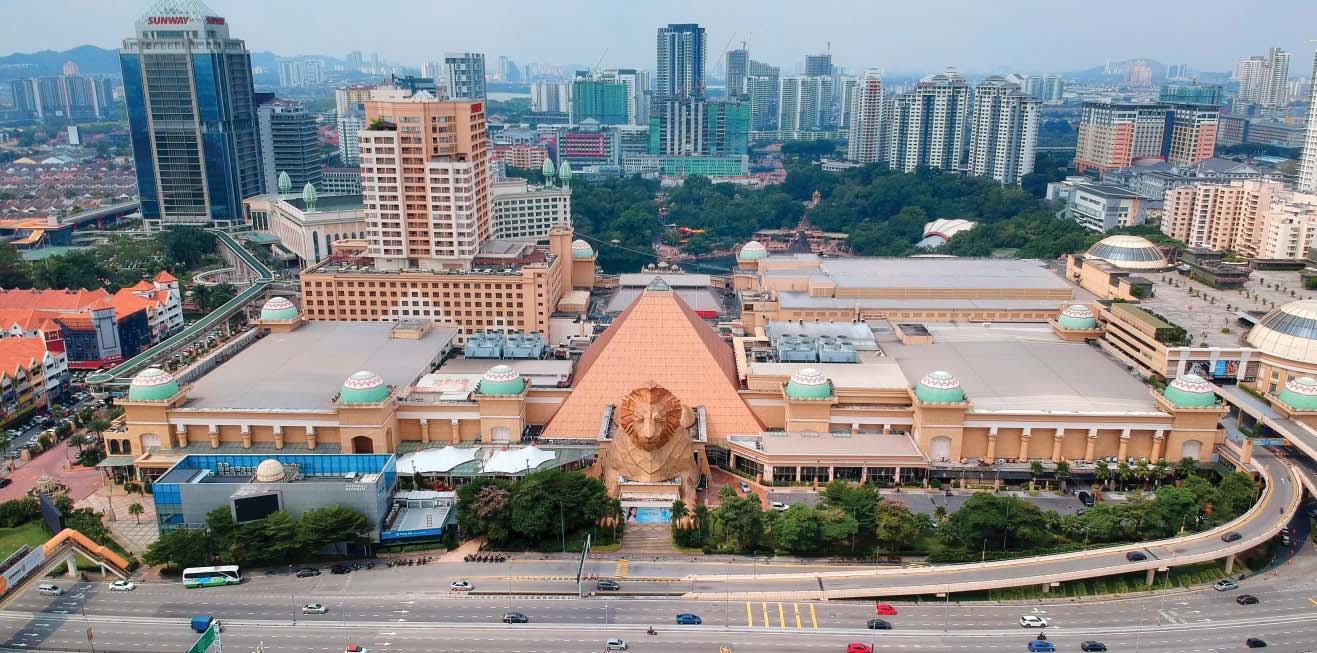
8 minute read
Chiller plant retrofi t helps Malaysia’s mega complex cut annual energy and operaƟ onal costs Rising uƟ liƟ es costs and sustainability issues were key drivers behind the decision to overhaul the original cooling system
ANNUAL ENERGY AND OPERATIONAL COSTS CHILLER PLANT RETROFIT HELPS MALAYSIA’S MEGA COMPLEX CUT
Rising uƟ liƟ es costs and sustainability issues were key drivers behind the decision to overhaul the original cooling system.
An exterior overview of Sunway Pyramid Mall.
Sunway Pyramid Mall is a themed shopping and entertainment mall situated in Sunway City, Selangor, Malaysia. The fi ve-level mega complex houses more than 1000 outlets, with a wide variety of dining, fashion and specialty off erings, in addiƟ on to a 12-screen cineplex, an indoor ice-skaƟ ng rink and a bowling alley. Since its opening in 1997, the mall has gone through two major expansions. It now has a total retail fl oor area of nearly 400,000 m 2 .
ConsisƟ ng of a central chilled water plant with eight units of water-cooled chillers, the exisƟ ng system was designed without adequate buff er and the pumps were over-taxed as a result. An internal energy audit further highlighted the ineffi - ciencies of the poorly designed system. The overall plant room effi ciency registered only in the 1.10 - 1.20 kW/TR range, and the ageing chillers were unable to chill water to the intended temperature effi ciently. IncenƟ ves from the Sustainable Energy Development Authority (SEDA) Malaysia further bolstered the management’s decision to phase out the ineffi cient chillers. Under the SAVE Program, Sunway Pyramid could receive a rebate of about USD 430,000 to off set the purchase of eight new energy-effi cient chillers, each able to achieve
The indoor ice-skaƟ ng rink within the mall.
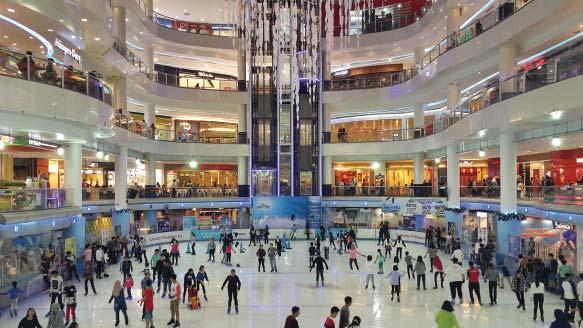
0.54 kW/TR or less. This allowed the management to reduce the project payback period to 4.3 years, instead of 4.8 years.
OpƟ mising the built environment Sunway Pyramid awarded the contract to Johnson Controls, a global technology provider in building technologies and soluƟ ons. In its search for a replacement soluƟ on, Sunway Pyramid had sƟ pulated several criteria:
• EliminaƟ ng the use of HCFC refrigerant gas which will be phased out in 2020 under the Montreal Protocol. • MeeƟ ng the target of 30% savings in energy consumpƟ on annually. • Ensuring no downƟ me and minimal inconvenience to retailers and shoppers during the retrofi t. Against this backdrop, Johnson Controls designed an integrated soluƟ on that included the Metasys soŌ ware and YORK YK centrifugal chillers - a combinaƟ on that opƟ mises and manages the performance of the chillers.
AnalyƟ cs for beƩ er effi ciency The Metasys Central Plant OpƟ misaƟ on (CPO) soŌ ware uses predicƟ ve algorithms to minimise energy use and operaƟ onal cost without sacrifi cing reliability. The technology monitors numerous inputs - from connected chillers, pumps and cooling towers to weather forecasts, uƟ lity rates and maintenance schedules - in real-Ɵ me and the data is updated every 15 minutes. The algorithms automaƟ cally opƟ mise the cooling, heaƟ ng and power generaƟ on in a holisƟ c way. The opƟ misaƟ on soŌ ware is able to predict hourly cooling, heaƟ ng and power loads over a seven-day period. Based on historical loads, weather, day of week, Ɵ me of day, building schedules and special events at the mall, the soŌ ware then adjusts operaƟ ons and makes decisions based on those predicƟ ons. This approach allows the chillers to run at the lowest cost possible, while supplying reliable cooling to the shopping mall.
OpƟ mised chiller plant The YK centrifugal water chiller has a variable-speed drive and an open-drive motor that does not come in contact with the refrigerant. The chiller is also fiƩ ed with a falling-fi lm evaporator that reduces refrigerant charge by up to 40%. Johnson Controls installed a total of seven YORK chillers of 1,200 TR capacity and one YORK chiller of 550 TR capacity, each able to achieve 0.54 kW/TR or less - which were all integrated with the Metasys soŌ ware. These new chillers are using the HFC-134a refrigerant, a chlorine-free refrigerant with zero Ozone DepleƟ on PotenƟ al (ODP) and lower Global Warming PotenƟ al (GWP) than the R-12 refrigerant. With more effi cient technology in place, Sunway Pyramid is running six out of the eight chillers on a daily basis - with beƩ er indoor cooling temperatures. The extra buff er allows the service team to rotate the chillers to minimise equipment stress, in addiƟ on to having extra cooling capacity during fesƟ ve peak periods with heavier fooƞ all. IniƟ ally, the Sunway Pyramid’s service team was scepƟ cal about the eff ecƟ veness of the system. But, they were soon won over by the intuiƟ ve design, touchscreen user interface and powerful analyƟ cs. With the OpƟ View control centre feature, which has a full-colour, interacƟ ve display of setpoints, readouts, alerts and reports, service personnel can fi x any issue quickly, to enhance chiller performance.
Inside the chiller plantroom.
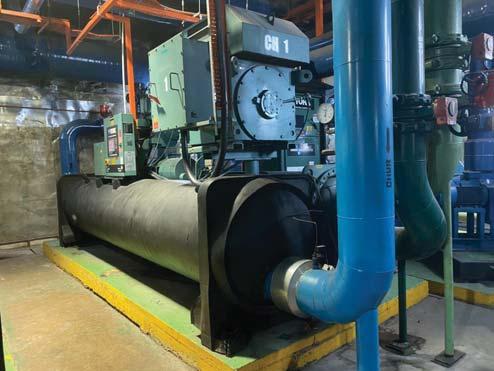
A service technician conducts checks on a York chiller.

CollaboraƟ ve eff orts The engineering teams from both sides relied on meƟ culous planning and resourcefulness to resolve the various challenges they faced during the project. For instance, the worst-performing chiller, which was located in the middle of a linear arrangement of chillers, was to be replaced fi rst, followed by the next worst performer unƟ l all eight units were replaced. This approach added to the level of complexity as it diff ered from the planned sequenƟ al replacement, starƟ ng with the outermost unit. Assembling the new chillers on-site was an intricate undertaking. At Sunway Pyramid, the plinths for the chillers had to be fi rst extended to support the larger-size YORK models. The chillers were delivered to the work site one at a Ɵ me, while a specialised crane operator was brought in to unload the chiller components into the plant room, due to height restricƟ ons of the facility. MulƟ ple teams were engaged to ensure that the components were unloaded quickly and properly posiƟ oned onto the plinth. It took 13 days, from start to fi nish, to replace a chiller at Sunway Pyramid, compared to a typical seven-day period under normal circumstances. Johnson Controls had to re-assemble the components into a fully built-up unit within 24 hours while the Sunway Engineering team saw to the piping rework. AddiƟ onal work on the chiller included pressure tesƟ ng to check for leakage, insulaƟ on, wiring works, charging, test run and observaƟ on for any tripping, before the next chiller was delivered to the site, and the process repeated.
The installaƟ on of the new high tension (HT) switchboard was just as daunƟ ng. The equipment had to be delivered on the day of installaƟ on as there was no storage available on-site. New cables were laid inside the plant room prior to the delivery to facilitate reconnecƟ on works to the chillers. The team had to work within 7 hours of downƟ me to posiƟ on the new switchboard at the existing incoming busbar locaƟ on. This required precise fabricaƟ on of the switchboard, in addiƟ on to having a team of skilled experts with special tools on standby to ensure a smooth transiƟ on. The rewiring work on each chiller had to be completed within the limited Ɵ me-frame, before the mall opened the following day. Work on the one-for-one replacement called for a highly skilled shutdown that allowed the mall to stay open for business throughout the six-month retrofitting project. The tight coordination between Johnson Controls and Sunway Engineering was critical to the process of decommissioning of the old chillers and installing new ones. Johnson Controls also designed a building management system (BMS) for the new chillers. The team held numerous discussions with the management to understand the mall’s operaƟ ng hours and parameters to integrate a soluƟ on that matched the day-to-day operaƟ on of the complex.
Signifi cant cost reducƟ ons Sunway Pyramid exceeded its energy effi ciency targets within a year of project compleƟ on. The soluƟ on delivered plant room effi ciency of 0.7 kW/TR, which was an improvement over the planned 0.75 kW/TR. Energy consumpƟ on and operaƟ onal cost were cut by 30%. The audited savings in electrical consumpƟ on reached about USD 80,000 per month, surpassing the set target of USD 63,000 per month. Prior to the switch to YORK chillers, the average monthly electrical consumpƟ on was a whopping USD 338,000. Reducing carbon emissions is an important corporate social responsibility (CSR) goal for Sunway Pyramid, as the organisaƟ on acƟ vely adopts measures to help miƟ gate climate change. The energy-effi cient chillers reduce some 4,300 tonne/year of CO₂ emissions. In total, these improvements have signifi cantly reduced the energy and operaƟ onal costs for Sunway Pyramid by about USD 900,000 per year - and these savings are sƟ ll conƟ nuing.
New appointments at Johnson Controls
Johnson Controls, a global leader in building technologies and soluƟ ons, is growing its presence in Southeast Asia, with appointments of senior leaders to increase the company’s foothold in the region’s smart buildings market. “Southeast Asia region off ers dynamic growth opportuniƟ es for Johnson Controls. To meet the region’s high demands for infrastructure development, city resilience and appeƟ te for innovaƟ on, Johnson Controls is commiƩ ed to build a strong leadership presence and team to power our customers and business partners for sustainable growth”, said Visal Leng, President, Asia Pacifi c, Johnson Controls. New appointments to the Johnson Controls leadership team in Southeast Asia include Alvin Ng, Vice President, Digital SoluƟ ons, Asia Pacifi c (based in Singapore); David Kirubi, General Manager for TransformaƟ on, Asia Pacifi c (based in Singapore); Adis PeukpaƩ anaruks, General Manager, Thailand, Vietnam, Myanmar, Laos and Cambodia (based in Bangkok); and Jack Yeo, Country General Manager, Philippines. These addiƟ ons complete the Johnson Controls leadership team in Southeast Asia, which also includes Hendrikus Hendra Gozali, Country General Manager, Indonesia and Fam Wee Chean, Country General Manager, Malaysia.
Alvin Ng
Adis PeukpaƩ anaruks
THE SINGAPORE ENGINEER February 2020 David Kirubi
Jack Yeo