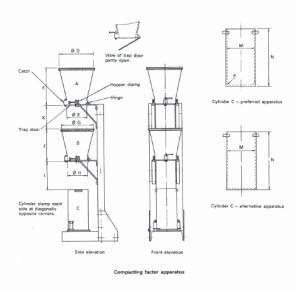
33 minute read
Enhancing standard test approach to beƩ er refl ect applicaƟ on requirements PracƟ cal adjustments to the specifi caƟ ons can lead to beƩ er outcomes
TO BETTER REFLECT APPLICATION REQUIREMENTS ENHANCING STANDARD TEST APPROACH
by C T Tam, Department of Civil & Environmental Engineering, NaƟ onal University of Singapore Standard test methods are intended for assessing conformity requirements. The type of test equipment and procedure are well defi ned for the intended purpose. The materials, relaƟ ve proporƟ ons and method of preparing the test specimens are clearly detailed. The test environment, eg temperature and relaƟ ve humidity are specifi ed, where needed. However, some, if not all of the above, may not be the actual values for pracƟ cal applicaƟ ons on site, parƟ cularly in concrete construcƟ on. This presentaƟ on provides selected examples of how the above factors may be adjusted in the standard test methods for beƩ er correspondence to actual project requirements or a modifi ed test procedure which leads to a beƩ er outcome. These include the consistence in terms of degree of compactability (previously compacƟ ng factor), passing ability of SCC in fresh concrete, the sƟff ening Ɵ mes of concrete (generally in terms of seƫ ng Ɵ mes) and the temperature issues of peak temperature (potenƟ al DEF) and maximum temperature diff erenƟ al (potenƟ al early thermal cracking) in hardened concrete arising from heat of hydraƟ on of cement in the casƟ ng of thick concrete secƟ ons that may take many hours of conƟ nuous casƟ ng. The enhancing of selected standard test methods with appropriate modifi caƟ ons beƩ er relates to the actual applicaƟ on requirements and is presented.
INTRODUCTION Standard test methods are intended for assessing conformity requirements. The type of test equipment and procedure are well defi ned for the intended purpose. The materials, relaƟ ve proporƟ ons and method of preparing the test specimens are clearly detailed. The test environment, eg temperature and relaƟ ve humidity are specifi ed, where needed. However, some, if not all of the above, may not be the actual values for pracƟ cal applicaƟ ons on site, parƟ cularly in concrete construcƟ on. The quanƟ taƟ ve results oŌ en are not directly applicable to the site requirements. In the execuƟ on of concrete structures, the performance of concrete is the actual interest. The principle of performance tesƟ ng should be the same as in conformity tesƟ ng. However, modifi caƟ ons in the test details together with the use of the actual consƟ tuents and composiƟ on of the specifi ed concrete for the project are used to assess the resultant performance. The above factors may be adjusted in the standard test methods for beƩ er correspondence to actual project requirements or modifi ed test procedure which leads to a beƩ er outcome. This presentaƟ on provides some examples selected to illustrate how the standard test procedures and the measurements can be modifi ed to achieve the outcome to beƩ er refl ect applicaƟ on requirements.
DEGREE OF COMPACTABILITY For low level of consistence, the compacƟ on of fresh concrete is formerly assessed by the compacƟ ng factor test to BS 1881: Part 103 [1] which is now replaced by the test on the degree of compactability to BS EN 12350- 4 [2]. In both methods, the principle is to compare the density of parƟ ally compacted concrete with the density of fully compacted concrete. The former test adopted the apparatus shown in Figure 1 to provide the same volume and the new approach is based on the same mass of concrete. The volume of fresh concrete completely fi lling the top hopper is dropped into the lower hopper and then into the cylindrical mould. The mass of the parƟ ally compacted volume of concrete is then compared to the mass of a fully compacted volume of the same concrete. The compacƟ ng factor (CF) is based on the raƟ o of the parƟ ally compacted mass to that of the fully compacted mass of the same volume. A larger value of CF represents a higher degree of compacƟ on. In lieu of comparing by mass, an alternate method to determine CF is by the volumes of the same mass. The volume of the parƟ ally compacted concrete in the cylinder mould is compared to the volume of the same mass of fresh concrete [3,4].
A direct reading device based on the change in height of the mass of concrete aŌ er being fully compacted provides a directly calibrated reading in CF (Figure 2) [3]. The BS EN method adopts the same approach as the alternate volumetric method. The container has a square cross-secƟ on (200 mm x 200 mm) and a height of 400 mm. The container is completely fi lled with fresh concrete and then compacted on a vibraƟ ng table to reach full compacƟ on. The change in height of the concrete within the container is determined by taking the average of four readings, one each at the mid-point of the four sides of the container. The raƟ o of the original height of the concrete to that of the compacted volume is defi ned as the degree of compactability (C0 to C4 classes). A larger value (C0 ≥ 1,46) indicates a lower level of compactability compared to the smallest value (C4 ≤ 1,04). This method diff ers from all the other consistence test methods for which a larger value indicates a beƩ er consistence, eg slump S1 10 to 40 mm and S5 ≥ 220 mm. The new approach requires a volume of concrete about 2.25 Ɵ mes that of the previous method. By changing the container to a cylinder of 225 mm diameter by 200 mm in height, to provide approximately the same volume (0.016 m 3 ), a similar device to that for CF can be designed to give readings calibrated as the value of the degree of compactability directly. It is proposed that the degree of compactability to be redefi ned as the height of the compacted volume to that of the full height of the container as shown in Table 1 whereby a larger value indicates higher compactability.
Table 1: CompacƟ on classes (Table 4, BS EN 206) [5]. Class Degree of compactability tested in accordance with EN 12350-4 Proposed (to nearest 0.005) C0 ≤ 1,46 ≤ 0.685 C1 1,45 to 1,26 0.690 to 0.795 C2 1,25 to 1,11 0.800 to 0.900 C3 1,10 to 1,04 0.905 to 0.960 C4 ≤ 1,04 ≥ 0.960
The adopƟ on of a cylindrical container of the same volume as that of the square secƟ on container in BS EN 12350-4 [2] together with the direct reading device enables the result to be obtained without the need of manual measurement. This is expected to reduce the measurement uncertainty and improve both repeatability and reproducibility of the test method. The main contribuƟ on to uncertainty is the way the mould is fi lled which will aff ect repeatability as well as reproducibility. Furthermore, by introducing a displacement transducer to measure the progressive increase in depth and plotƟ ng the changing values with Ɵ me, the end-point can be further monitored. The fi nal value and the Ɵ me taken to reach the value may be displayed as a depth-Ɵ me plot. In addiƟ on to a beƩ er defi ned fi nal value, the Ɵ me for this provides addiƟ onal indicaƟ on of the ease of achieving full compacƟ on. This test method is oŌ en specifi ed for concrete pavement construcƟ on but may also be useful
with concretes for precast elements where consistence in terms of slump is either S1 or S2 (10 to 90 mm). The former CF test with an intermediate hopper provides a degree of moderaƟ ng the infl uence of the operator factor in fi lling the upper hopper. However, the need to obtain the mass of fully compacted concrete in refi lling the cylinder may introduce variaƟ on in the composiƟ on of the concrete between the two mass determinaƟ ons. The volumetric method avoids this factor. The main contribuƟ on to uncertainty is the way the mould is fi lled which may aff ect repeatability as well as reproducibility. The proposed replacement of the rectangular container with a cylindrical mould minimises possible corner eff ects when vibraƟ ng the concrete to full compacƟ on. The use of a direct indicaƟ ng device also removes the uncertainƟ es in taking the four measurements in the BS EN 12350-4 [2] method.
PASSING ABILITY The passing ability of self-compacƟ ng concrete (also known as self-consolidaƟ ng concrete) is assessed by BS EN 12350-12 [6] using the J-ring (Figure 3) or by ASTM C 1621 [7] with the J-ring but with a diff erent method of reporƟ ng the passing ability. The BS EN test result is reported as the J-ring step. This is defi ned as the diff erence between the height of the concrete at the centre of the J-ring and the average of four readings of the height of concrete located at two perpendicular diameters of the J-ring just outside the bars of the J-ring. The acceptance value of the J-ring step (PJ) for both narrow and wide gap confi guraƟ ons of the J-ring is ≤ 10 mm as stated in BS EN 206 (Table 10) [5]. The values of repeatability as well as reproducibility in BS EN 12350-12 [6] are 4,6 mm and 7,8 mm, respecƟ vely, for the narrow gap (41 mm). Hence, the uncertainƟ es in the J-ring test results are very large for applicaƟ ons. Although BS EN 12350-12 [6] provides values of repeatability and reproducibility for J-ring fl ow spread (SFj in mm) and J-ring fl ow Ɵ me (t500j in s) in the case of narrow gap J-ring, BS EN 206 [5] does not provide any guidance on the acceptance value for either SFj or t500j. ASTM C 1621 [7] is also based on the use of the same J-ring and the narrow as well as the wide gap and narrow gap confi guraƟ ons of the J-ring. However, the result is reported in terms of the reducƟ on in the fl ow spread due to the presence of the J-ring.
Diff erence between slump fl ow and J-ring fl ow 0 to 25mm [0 to 1in.] > 25 to 50mm [> 1 to 2 in.] > 50mm [2 in.] Blocking Assessment
No visible blocking Minimal to noƟ ceable blocking NoƟ ceable to extreme blocking
Table 2: Blocking Assessment (ASTM C1621, Table 1) [7].
This approach was reported in an earlier publicaƟ on [8] prior to ASTM 1621-06 [7] in terms of the raƟ o of J-ring fl ow to that of slump fl ow. This is defi ned as the Passing Ability Index (PAI) with the use of a modifi ed ring diameter of 500 mm (P-ring) [8]. Subsequently, addiƟ onal test results on the usefulness of the P-ring have also been published [9]. Site requirements relate to the size and spacing of steel
reinforcement bars. Their infl uence on the passing ability of SCC is related to the degree of blockage (simulated by the number and bar size in the P-ring) and the clear gap space for the passing ability of SCC. Both factors are simulated by the diameter of the bars and the bar spacing in the P-ring. Only limited combinaƟ ons are provided in the J-ring test [6]. Table 3 shows the clear gap space (spacing less diameter of bar) and blocking raƟ o (sum of the number of bar diameters divided by the circumference of the 500 mm diameter P-ring. The P-ring provides the fl exibility to assess the combined eff ect of actual site requirements which are not available in any of the current test methods. Table 3 shows the clear gap space (bar spacing less one diameter of bar) and blocking raƟ o (sum of the number of bar diameters divided by the circumference of the 500 mm diameter P-ring). Annex A shows the two types of P-ring, Type A with provision for 4 to 24 bars and type B with provision for 4 to 32 bars together with the potenƟ al range of clear gap spacing and blocking raƟ o using 10 mm, 20 mm or 40 mm diameter bars.
Test method
J-ring
P-ring 24 bar locaƟ ons
Example
P-ring 24 bar locaƟ ons c P-ring 16 bar locaƟ ons d
Clear gap space (mm) Blocking raƟ o (%)
narrow gap 16 x 18mm dia. wide gap 12 x 18mm dia. narrow gap 16 x 18mm dia. wide gap 12 x 18mm dia. 41 59 31 23 24 x 20mm dia. 24 x 16mm dia. 24 x 20mm dia. 24 x 16mm dia. 25 a 33 a 31 24 12 x 45mm dia. 12 x 36mm dia. 12 x 45mm dia. 12 x 36mm dia. 41 59 34 b 28 b a values not matching J-ring b values not matching J-ring RaŌ foundaƟ on: 40mm diameter bars at 100mm centres both ways 60 40 8 x 70mm dia. 8 x 70mm dia.
56 36
16 x 40mm dia. 12 x 40mm dia. 58 c 41 c e preferred e preferred c Type A P-ring, d Type B P-ring (Annex A)
Table 3: Clear gap space and blocking raƟ o.
Similarly, the L-box test [10] provides the clear gap space of 59 mm with two numbers of 12 mm diameter bars, and three numbers of 12 mm diameter bars for a clear gap space of 41 mm. The width of the box is 200 mm, providing blocking raƟ os of 12% and 18%, respecƟ vely. These are much less than the blocking raƟ os for the corresponding clear gap spaces in the J-ring [6], of 23% and 32%, respecƟ vely. Table 3 shows that the P-ring does not provide confi guraƟ ons to match both the clear gap space and the blocking raƟ o of the narrow gap or wide gap confi guraƟ on of the J-ring [6] at the same Ɵ me, but for either one of them only. The two clear gap spaces in the P-ring [7] correspond to the two clear gap spaces adopted in the L-box test [10] (established earlier than the J-ring test). However the P-ring [7] with 500 mm diameter and up to 24 equally spaced bars is able to provide a wider range of clear gap spaces and blocking raƟ os that can beƩ er simulate the confi guraƟ on of reinforcement bars for the actual concrete element. For example, a typical raŌ foundaƟ on confi guraƟ on consisƟ ng of 40 mm diameter bars at 100 mm spacing with a clear gap space of 60 mm and blocking raƟ o of 40% is approximated with 8 x 70 diameter bars giving a clear gap space of 56 mm and blocking raƟ o of 36%. On the other hand, the J-ring with a wide gap has a clear gap space of 59 mm but a blocking raƟ o of only 23%. The blocking occurs at 300 mm for the J-ring [6] but at 500 mm for the P-ring [7] at which the fl ow is slower. Combined with the lower blocking raƟ o, the J-ring [6] provides a less criƟ cal assessment of the performance requirement. By repeaƟ ng the P-ring test over a period of Ɵ me since batching and relaƟ ng the fl ow diameter at di ff erent Ɵ me periods to iniƟ al slump fl ow as reference, the reducƟ on in the value of PAI enables assessment of the result of an unintended delay. For iniƟ al slump fl ow of 550 mm (SF1) [5] and J-ring fl ow at a diff erence of 25 mm [7,] the raƟ o, PAI = 525/550 = 0.95. For iniƟ al slump fl ow of 850 mm (SF3) [5], the same diff erence of 25 mm, the raƟ o, PAI = 825/850 = 0.97. When the diff erence becomes 50 mm [7], the corresponding PAI = 0.91 and 0.94 respecƟ vely. Hence, the acceptance range of PAI for SF1 is 0.91 to 0.95 and for SF3, the range is 0.94 to 0.97. The reducƟ on of PAI is in the order of 0.03 to 0.04 which may be considered as their acceptable limit. The PAI approach is likely to be more sensiƟ ve in the assessment of passing ability than ASTM C 1627 [7] and more so than BS EN 12350-12 [6]. The increase in the value of the J-ring fl ow Ɵ me, t500j over a period of Ɵ me using the P-ring compared to t500 of iniƟ al slump fl ow, off ers an addiƟ onal indicaƟ on of the reducƟ on in passing ability. However, as the values of t500 as well as t500j are generally within a few seconds (similar in order as their repeatability and reproducibility [6]), they are not suffi ciently sensiƟ ve to assess diff erences in passing ability. Hence, they have not been included in the requirements for SCC under BS EN 2065. The site requirements for passing ability of SCC are beƩ er assessed based on PAI using the P-rings.
SETTING TIMES OF CONCRETE Although the term ‘seƫ ng Ɵ mes of concrete’ is commonly used, in order to emphasise the diff erence between ‘seƫ ng Ɵ mes of concrete’ from ‘seƫ ng Ɵ mes of cement’, it is preferable to adopt the term ‘sƟff ening Ɵ mes of concrete’ as in BS 5075 [11]. Unlike the seƫ ng Ɵ mes of cement using the Vicat needle apparatus in BS 196-3 [12], the seƫ ng Ɵ mes of concrete are based on the penetraƟ on resistance of wet-sieved mortar from fresh concrete, originally (1957) using the Proctor needles for soil test as stated in the early ediƟ on of ASTM C 403 [13]. PenetraƟ on resistance defi ned as iniƟ al and fi nal seƫ ng Ɵ mes of concrete do not relate to any specifi c change in concrete properƟ es [13]. IniƟ al set is usually considered to indicate the Ɵ me at which the concrete can no longer become monolithic with previously placed concrete and fi nal set when hardening begins [13]. IniƟ al set is defi ned as Ɵ me since adding water for the wetsieved mortar to reach penetraƟ on resistance of 3.5 MPa. Site pracƟ ce has taken this to be the Ɵ me for which a ‘cold joint’ may result between the already placed fresh concrete and the new fresh concrete to be placed over it (even when
vibrated with a poker vibrator). A truly cold joint will show up as a dark line in hardened concrete, eg at a construcƟ on joint. However, unless the already placed concrete has fully hardened, such a line is oŌ en not observed. The parƟ ally set concrete is mixed by vibraƟ ng with the poker vibrator at the interfacial zone of the already placed concrete and the newly placed concrete. Hence potenƟ ally a weakened zone may have been created. However, there is as yet no test method to assess such a situaƟ on when delay occurs even though at the job site this has occurred, eg in casƟ ng of deep secƟ ons such as pilecaps or raŌ foundaƟ ons. The 3.5 MPa penetraƟ on resistance Ɵ me has been adopted as the pracƟ cal criterion to specify required retardaƟ on Ɵ me in the concrete by addiƟ on of set-retarding admixtures. Although this approach has served site pracƟ ce saƟ sfactorily, it does not provide a direct method of assessing the potenƟ al cold joint formaƟ on issues. A more raƟ onal approach is needed to explore the actual situaƟ on and to provide guidance on the way to handle this maƩ er on site, eg a test method to indicate if the already placed concrete has reached a stage that it will lead to an unacceptable zone when new fresh concrete is placed over it, and the use of a vibrator to intermix the new fresh concrete with the already placed concrete. A study [14] on this issue was conducted by considering the delay in casƟ ng of new fresh concrete over a few hours including the Ɵ me when the wet-sieved mortar has reached 3.5 MPa. A specially designed verƟ cal beam mould of 100 mm square secƟ on for casƟ ng the 400 mm length in two halves has been adopted (Figure 3) [14]. The upper 200 mm of concrete was placed with delayed Ɵ me of up to 6 hours aŌ er the placing of the concrete in the lower 200 mm beam mould. The beams were removed from their moulds aŌ er 1 day and moisture-cured Ɵ ll the age of tesƟ ng under the third-point loading system for fl exural strength (modulus of rupture) in accordance with ASTM C78 [15]. Preliminary results from an iniƟ al study (Figure 4) [14] shows that when the interfacial zone is disturbed (by rodding into about 50 mm of concrete placed earlier), there is no clear line to indicate a cold joint. The fl exural strength for an increasing period of Ɵ me to place the second batch of concrete resulted in a gradual reducƟ on of fl exural strength. This is likely to be contributed by the intermixing of the parƟ ally set earlier placed concrete with the new batch of concrete placed over it as shown in Figure 3 [14]. The total period of Ɵ me starts from the placing of the lower half of the beam to beyond the Ɵ me when the wet sieved mortar of the same concrete is placed. The results show a more signifi cant reducƟ on of the fl exural strength when the interfacial zone is not disturbed (by rodding into the already placed concrete of not more than 50 mm in the test programme) compared to the case when no such disturbance is applied. This situaƟ on may be the case for placing with SCC as no vibraƟ on will be applied by simply allowing the new SCC to fl ow over the already placed concrete. Based on the results shown in Figure 4, the expected formaƟ on of a weak cold joint with a sudden large drop in the fl exural strength at the Ɵ me when the wet-sieved mortar reached penetraƟ on resistance of 3.5 MPa did not happen. It has not been established if casƟ ng is repeated to further periods of Ɵ me Ɵ ll the fi nal seƫ ng Ɵ me of concrete at penetraƟ on resistance of 27.4 MPa may lead to the case
THE SINGAPORE ENGINEER January 2020 Figure 3: VerƟ cal casƟ ng beam formwork [4].

Figure 4: ReducƟ on of fl exural strength with Ɵ me [14].
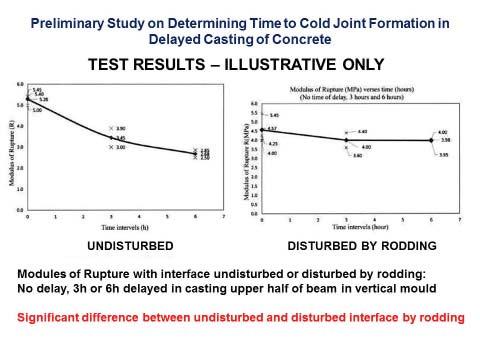
of a sudden large drop in the fl exural strength. This may be expected if the earlier placed concrete has hardened to the extent that the surface cannot be easily broken by rodding. Historically, the seƫ ng Ɵ me test of ASTM C403 [13] was fi rst carried out using the Proctor penetraƟ on needles with a hand-held device in the applied load, by means of a spring of maximum capacity of 110 lbf (approx 50 kgf or 490 N) [16]. Modifi caƟ ons to the method of determining the applied force were later introduced using a pressure gauge or load cell. BS 5075 [11] adopted the use of a self-indicating plaƞ orm scale to measure the applied force. With these modifi ed methods of measuring the applied force, there is potenƟ al to do so directly on the fresh concrete in lieu of its wet-sieved mortar. In the preliminary study [15] for the concrete studied, at the Ɵ me when its wet-sieved mortar reached 3.5 MPa, the penetraƟ on resistance of the concrete was about 10 MPa. Although this is for the specifi c concrete tested, it indicates that the alternaƟ ve of directly conducƟ ng the penetraƟ on resistance on concrete may be applied to the already placed fresh concrete on site. UnƟ l a more detailed study is conducted to determine the criterion for acceptance, the equivalent penetraƟ on resistance of concrete corresponding to that of its wet-sieved mortar at a penetraƟ on resistance of
3.5 MPa may be applied on site pracƟ ce. The specifi c penetraƟ on resistance of the fresh concrete may be established by carrying out penetraƟ on resistance on both the concrete and its wet-sieved mortar for each specifi c concrete for the project. There is potenƟ al to develop a portable loading device for this purpose to assess the concrete on site to decide the penetraƟ on resistance of the already in-place concrete, providing an indicaƟ on of the potenƟ al cold joint formaƟ on.
TEMPERATURE LIMITS ARISING FROM HEAT OF HYDRATION The heat of hydraƟ on of cement leads to a rise in temperature which can be signifi cant in thick secƟ ons. Typically, a thickness above 500 mm will result in a measurable temperature rise even with a low heat cement. When this occurs, at temperatures above 70° C, the potenƟ al for delayed eƩ ringite formaƟ on (DEF) is expected. UnƟ l the mid-1990s, this phenomenon was not generally recognised. On the other hand, early thermal cracking due to temperature diff erence between the warmer interior and the cooler surface zone of a thick secƟ on is well accepted. However the diff erence in temperature (oŌ en referred to as temperature diff erenƟ al) that may result in surface cracks is less appreciated. It is not only the temperature diff erence but also the degree of boundary restraint (restraint factor). The combined eff ect determines the potenƟ al for early thermal cracking. A commonly specifi ed value is 20° C without consideraƟ on of the actual thickness and boundary condiƟ on of the structural element. BS 8110 Part 2 [17] clause 3.8.4 provides guidance on this topic. The following statements are of parƟ cular signifi cance in understanding the issues: • The resulƟ ng expansion of the hot core, if excessive, can stretch the cooler surface zone to the extent that cracking occurs. • In pracƟ ce, however, restraints result in diff erenƟ al thermal strains which depend on the nature of the temperature distribuƟ on, and the raƟ o of the ‘hot’ and ‘cold’ areas. • Experience has shown that by limiƟ ng temperature differenƟ al to 20° C in gravel aggregate concrete, cracking can be avoided. • This represents an equivalent restraint factor R of 0.36. Based on the above statements, a value of 20° C represents the most conservaƟ ve specifi ed value when other types of aggregates and restraint factors apply. Experience in Singapore with raŌ foundaƟ on up to 4000 mm thick and the use of granite aggregate has not shown any surface cracking for temperature diff erenƟ al up to 40° C (equivalent restraint factor R of 0.25) by ensuring boundary restraints are limited to one or two sides of the panel being cast. ReducƟ on of the boundary restraints e ff ect for a thin wall on thick base by adopƟ ng the fi rst liŌ height of not more 1 m has minimised potenƟ al cracking. In temperate climates, where placing temperatures are not above 20° C even in summer, the maximum temperature seldom reaches 70° C, and DEF is less an issue than early thermal cracking arising from temperature diff erenƟ al. Hence, insulaƟ ng the external surface is a common requirement. In tropical climates, it is more diffi cult to keep maximum temperature from reaching over 70° C than avoiding early thermal cracking, as placing temperature is generally above 30° C. Given the complex interplay between restraint factor and the resultant temperature distribuƟ on within any part of diff erent types of structural elements, the simplisƟ c specifi caƟ on of a temperature diff erenƟ al cannot ensure saƟ sfactory results, parƟ cularly in the case of a large pour for a raŌ foundaƟ on, with conƟ nuous placement of concrete over many hours. Even analyƟ cal methods based on data from a ‘hot box’ test as conformity test for an adiabaƟ c temperature test are inadequate, as it is diffi cult to include into the numerical model, the progressively changing element thickness over the long period of placing. The expected performance is best assessed by means of a mock-up simulaƟ ng the actual process of placement and the nature of the structural element (column, transfer beam/slab or raŌ foundaƟ on). For precast elements, the actual formwork may be used with only its criƟ cal zone, by appropriate adaptaƟ on, eg the cross beam of an elevated light rail system.
In the case of a thick foundaƟ on raŌ 4500 mm thick with a panel size 20 m x 60 m, the total volume of concrete is 5,400 m 3 . Placing at the rate of 60 m 3 /h for each pump discharge point and using two such pumps, will take 45 hours. AdopƟ ng the layering technique [18] of placement in nine layers of 500 mm, each layer takes 5 hours. This calls for at least 7 hours of set retardaƟ on Ɵ me based on ASTM C403 [13] penetraƟ on resistance test needles specifi ed. In any specifi c case, opƟ misaƟ on with diff erent placing temperatures for groups of layers (outer zones and central zone) to minimise temperature diff erenƟ al, using diff erent types of cements or addiƟ on of waterproofi ng admixture are possible alternate approaches that have been presented elsewhere [19]. A mock-up to assess the expected performance is adopted to verify if the temperature limits specifi ed are achieved ahead of the actual placement on site. The mock-up is made up of a 2.5 m x 2.5 m secƟ on of the full thickness of the raŌ to represent a central area within the raŌ and insulated on the four sides with 100 mm thick polystyrene foam panel to simulate the eff ect of concrete surrounding the secƟ on. The advantage of the mock-up approach with actual performance data over analyƟ cal methods is a full temperature history record of this representaƟ ve volume of the raŌ , from the start of placing concrete to the fi nal stage when the warmest interior part of the volume has cooled down to less than 20° C diff erenƟ al with the average ambient temperature. Actual examples reported include the case of a 2800 mm raŌ in seven layers (Figure 5) [19] which reached a maximum temperature of 66° C for a high slag cement (PBFC to BS 146) [20] at 350 kg/m 3 plus silica fume of 20 kg/m 2 . Another case of a concrete with a 3700 mm thick mock-up in nine layers (Figure 6) [21] recorded a maximum temperature of 64° C and maximum temperature diff erenƟ al of 22° C with no insulaƟ on at the top surface of the mock-up (Figure 7) [21]. Subsequently for the project, several large volume placements (600 to 1100 m 3 ) recorded maximum temperatures and maximum temperature diff erenƟ als that were within ±3° C of those for the mock-up. These cases provided a confi rmaƟ on of the usefulness of performance tesƟ ng.
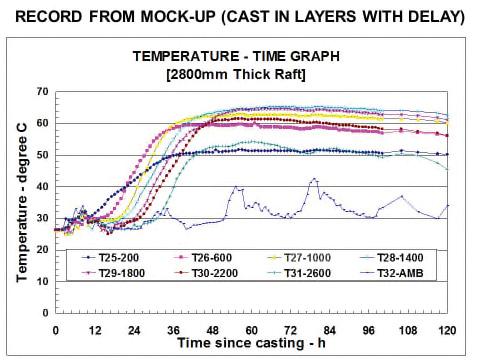
Figure 5: Temperature history of 2800 mm thickness.
Type A: 6 per quarter circle For 4, 8,12 or 24 bars
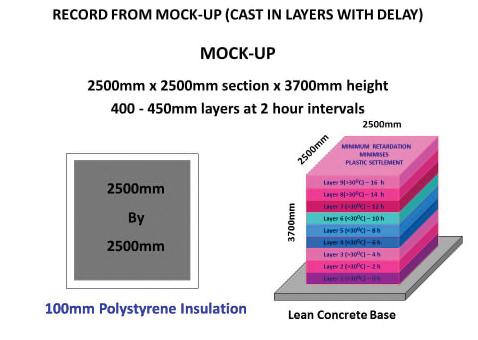
Figure 6: SchemaƟ c illustraƟ on for a nine layer mock-up.
Type B: 8 per quarter circle For 4, 8, 16 or 34 bars
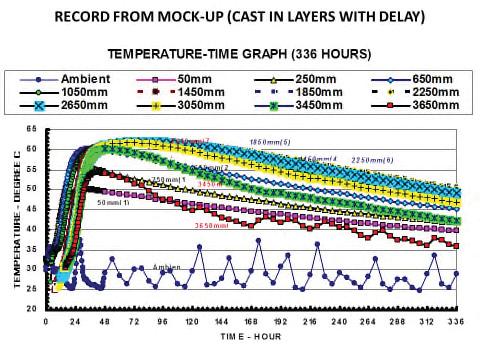
P-ring of 500 mm diameter (circumference = 1571 mm) (Ring A - 24 bars, Ring B - 32 bars with bar diameters of 10 mm, 20 mm and 40 mm) Figure 7: Temperature history of 3700 mm thickness.
Degrees No. of bars Ring A/B Centre to Centre (mm) 5 72 NA 6 60 NA 7.5 48 (4 x12) 32.73 10 36 (4 x 9) 43.64 11.25 32 (4 x 8) 49.09 12 30 (3 x 12) 52.36 15 24 (4 x 6) 65.45 20 18 ( 3 x 6) 87.27 22.5 16 (4 x 4) 98.19 30 12 (4 x 3) 130.92 45 8 (4 x 2)(8 x 3) 196.38 60 6 (3 x 2) 261.83 Gap Space - mm Blocking raƟ o - % 10 mm 20 mm 40 mm 10 mm 20 mm 40 mm NA NA NA NA NA NA NA NA NA NA NA NA 23 13 NA 31 61 NA 34 24 NA 23 46 NA 39 29 NA 20 41 81 42 32 NA 19 38 76 55 45 35 15 31 61 77 67 47 11 23 46 88 78 58 10 20 41 121 111 91 8 16 31 186 176 156 5 10 20 NA NA NA NA NA NA
NA: not applicable (out of range shown in criteria) Criteria: Centre to centre: Maximum 200 mm, 1571/200 = 7.85, select 8 bars x 4 = 32 bars, 11.25 degrees Minimum 40 mm, 1571/40 = 39.27, select 10 x 4 = 40 bars, 9 degrees Gap space: not less than 30 mm and not more than 100 mm (out of range) Blocking raƟ o: not more than 50 % and not less than 15 % (out of range)
CONCLUDING REMARKS Conformity tests are necessary to ensure that the consƟ tuent materials for concrete and the properƟ es specifi ed for the concrete meet the specifi caƟ on for the project. However, the test results of conformity tesƟ ng, in most cases, do not provide adequate informaƟ on for the requirements of the project. Suitable modifi caƟ ons to the procedure and measurements of performance directly related to the project provide beƩ er assurance of achieving the intended design and the in-service performance of the concrete structures. Some examples of this approach are presented to illustrate how such modifi caƟ ons can provide beƩ er assessment of the extent a requirement may be achieved.
ACKNOWLEDGEMENT The author gratefully acknowledges the contribuƟ ons and support of co-authors, colleagues and former research staff and students in the various projects which are quoted in the references from which the data and opinions are derived.
REFERENCES [1] BS 1881: Part 103: 1993, Method for determinaƟ on of compacƟ ng factor, BriƟ sh Standards InsƟ tuƟ on, London (previously BS 1881: Part 2: 1970). [2] BS EN 12350-4: 2000 - TesƟ ng fresh concrete - Part 4: Degree of compactability, BriƟ sh Standards InsƟ tuƟ on, London. [3] Tam C T, CompacƟ ng factor: a new test, Concrete, 10, No. 5, May 1976, pp 27 and 30. [4] DD 90: 1983, Volumetric method for determinaƟ on of compacting factor of fresh concrete, BriƟ sh Standards InsƟ tuƟ on, London. [5] BS EN 206: 2013 + A1: 2016, Concrete - Specifi caƟ on, performance, producƟ on and conformity, BriƟ sh Standards InsƟ tuƟ on, London. [6] BS EN 12350-12: 2010, TesƟ ng fresh concrete - Part 12: Self-compacƟ ng concrete - J-ring test, BriƟ sh Standards InsƟ tuƟ on, London. [7] ASTM C1621/C1621M - 17, Standard test method for passing ability of self-consolidaƟ ng concrete by J-ring, ASTM InternaƟ onal, West Conshohocken, PA, USA. [8] Tam C T, Sheinn A M M, Ong K C G and Chay C Y, Modifi ed J-ring for assessing passing ability of SCC, SCC 2005, Chicago, 31st Oct - 2nd Nov 2005, Session D-3-2, (also Proceedings of First North American Conference on the Design and Use of Self-consolidaƟ ng Concrete, Chicago, USA, Nov 2002). [9] Chan K D, Ong K C G and Tam C T, Passing ability of SCC - Improved method based on the P-ring, Proceedings of 35th ‘Coral’ Anniversary Conference on Our World in Concrete and Structures, ‘Challenge of the Low Carbon Age’, CI-Premier, 26-27 August 2010, Singapore, pp 25-27. [10] BS EN 12350-10: 2010, TesƟ ng fresh concrete - Part 10: Self-compacƟ ng concrete - L-box test, BriƟ sh Standards InsituƟ on, London. [11] BS 5075: Part 1: 1982, Specifi caƟ on for acceleraƟ ng and retarding water reducing admixtures, BriƟ sh Standards InsituƟ ion, London. [12] BS EN 196-3: 2016, Methods of tesƟ ng cement - Part 3: DeterminaƟ on of seƫ ng Ɵ mes and soundness, BriƟ sh Standards InsƟ tuƟ on, London. [13] ASTM C403/C403M - 16, Standard test method for Ɵ me of seƫ ng of concrete mixtures by penetraƟ on resistance, ASTM InternaƟ onal, West Conshohocken, PA, USA. [14] Tam C T, Zhao X Y and Wang N, Preliminary study on determining Ɵ me to cold joint formaƟ on in delayed casƟ ng of concrete, Proceedings 42nd Conference on Our World in Concrete & Structures, 24-25 August, 2017, pp 49-54. [15] ASTM C78/C78-18, Standard test method for fl exural strength of concrete using simple beam with third-point loading, ASTM InternaƟ onal, West Conshohocken, PA, USA. [16] Tam C T, The eff ect of a lignin-based admixture on properƟ es of concrete, PhD Thesis, University of Calgary, Alberta, Canada, 1972, 192 pp. [17] BS 8110: Part 2: 1985, Structural use of concrete, Part 2. Code of pracƟ ce for special circumstances, BriƟ sh Standards InsituƟ on, London. [18] Loo Y H, Paterson J S, Swaddiwudhipong S and Tam C T, ApplicaƟ ons of the layering on large concrete pours, Magazine of Concrete Research, V47, 1995, pp 209-217. [19] Tam C T, Swaddiwudhipong S, Ho D W S and Seow S S, Strategy for casƟ ng of raŌ foundaƟ on in tropical climate, J IES, Singapore, V42, N6, 2002, pp 6-12. [20] BS 146: 1958, Portland blast-furnace cement, BriƟ sh Standards InsƟ tuƟ on, London. [21] Tam C T, InnovaƟ ve approach for casƟ ng of thick foundaƟ on raŌ s - sandwich concept, Proceedings, Twin Coimbra InternaƟ onal Conference, 17-19 June 2009, Coimbra, Portugal, 4th Concrete Future - Recent Advances in Concrete Technology & Concrete in Structures, CI Premier, 2009, pp CF-31 to CF-40. (This arƟ cle is based on a Keynote Paper authored by C T Tam, Department of Civil & Environmental Engineering, NaƟ onal University of Singapore and presented at the 44th Conference on ‘Our World in Concrete & Structures’ held in Singapore, from 29 to 30 August 2019. The conference was organised by CI-Premier Pte Ltd)
Hybrid polymer concrete paving In 2017, the ASCE (American Society of Civil Engineers) gave America’s bridges a Safety and CondiƟ on raƟ ng of C+. Bridges are built to last approximately 50 years. The average age of US bridges is now 42. Of the approximate 610,000 rural and urban bridges in the US, more than 24% are considered funcƟ onally obsolete or structurally defi cient. The stresses aff ecƟ ng the naƟ on’s bridges will only increase as traffi c volumes rise and the demand for heavier semi freight loads grows. One soluƟ on to the problem involves the use of an advanced hybrid polymer concrete overlay that creates a highly durable, fl exible and waterproof surface. The overlay epoxy quickly develops high tensile strength that seals, protects and extends the life of bridge decks in both new construcƟ on and refurbishment work. The epoxy binder is applied evenly to the bridge deck surface. Aggregate is then immediately applied over the binder, increasing the texture depth of the pavement and providing a long-lasƟ ng seal to protect the bridge deck from the eff ects of traffi c and harsh weather condiƟ ons.