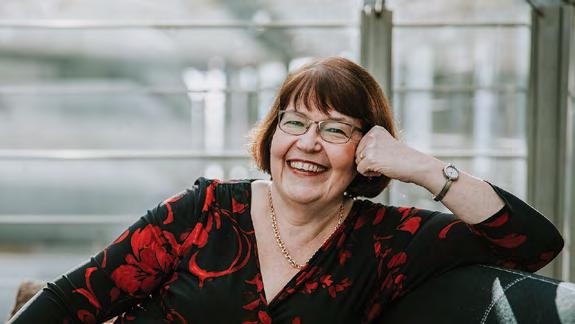
12 minute read
Accelerating transformation of the built environment sector A glimpse of some of the work being done in Helsinki, Finland
Helsinki, the capital of Finland, and Singapore are considered to be two smartest cities in the world. ‘The Singapore Engineer’ obtains a glimpse of some of the work being done in Helsinki, Finland, and the possibilities for collaboration with Singapore, from Ms Irma Ylikangas, Senior Business Advisor, Helsinki Business Hub, and Mr Teemu Lehtinen, CEO, KIRAHub.
Facilitating strategic parnerships
‘The Singapore Engineer’: Could you provide an introductory description of Helsinki Business Hub?
Irma Ylikangas: Established in 2006, Helsinki Business Hub (HBH) is the international trade and investment promotion agency for the capital region of Finland. As a non-profit organisation, its services are free-ofcharge.
TSE: What is the role of HBH and what are some of its achievements?
IY: HBH helps foreign companies to set up their business, grow and develop in Greater Helsinki which offers key business opportunities in (but not limited to) the following fields: • Information and communications technology. • Health: personalised health & med tech. • Smart & clean solutions, especially related to the built environment and sustainability, e.g. smart buildings, smart mobility, smart energy and the circular economy. • Hotel investments. HBH helps companies throughout their journey to Finland and the Greater Helsinki area - from the initial consideration to establishing and expanding their business. Its services include, for example, helping to find the best location for a business, matchmaking and finding co-operation opportunities with Finnish companies and research institutes, and finding deal flow from Finland or opportunities for expansion in Greater Helsinki. HBH can also help organisations looking for specific technological solutions or strategic partnerships including in R&D. In 2019, HBH helped foreign companies to create almost 370 jobs, invest about EUR 78 million and kick-start almost 17 business deals in the Greater Helsinki region. Out of these 17 deals, six were with Singaporean organisations operating in the built environment sector. Solutions around robotics, automation, intelligent data and IoT or data management to improve indoor air quality have been especially successful.
Ms Irma Ylikangas, Senior Business Advisor, Helsinki Business Hub. Image: Petri Mast.
TSE: Could you provide more information on the cooperation between Finland and Singapore?
IY: Helsinki has a long history of close co-operation with Singapore, and since 2017, there has been a special focus on the built environment and smart city topics. Sharing information about new and innovative digital tools to increase information flow and efficiency of the construction process, has been our goal. The digitalisation of the construction industry has been one area which the Finnish government has been supporting, to enable new innovations. HBH has organised several business delegations to Singapore to match innovative Finnish companies with Singaporean organisations. KIRAHub has been a partner in these delegations. HBH is cooperating with multiple leading organisations in Singapore, such as IPI Singapore, Building and Construction Authority (BCA), Enterprise Singapore (ESG) and Housing & Development Board (HDB). Recently, HBH also started to cooperate with the Smart Urban Co-Innovation Lab which is Southeast Asia’s first industry-led lab for smart cities solutions development. The Smart Urban Co-Innovation Lab has been initiated by CapitaLand and is supported by the Infocomm Media Development Authority (IMDA) and Enterprise Singapore (ESG). It is operated by AIRmaker. More information may be obtained from www.hbh.fi
Innovation hub for sustainable digitalisation
‘The Singapore Engineer’: Could you provide a brief description of KIRAHub and its functions and objectives?
Teemu Lehtinen: KIRAHub is a non-profit association and an innovation hub for boosting sustainable digitalisation of the built environment sector. It was founded in 2018 to continue the work that started in the governmental KIRA-digi project (2016-2019). We work closely together with government, municipalities, private sector, research institutions and international networks, to build an open ecosystem for digital transformation. Our aim is to achieve the following: • Create transparent ecosystems. • Connect the right people and organisations. • Promote the adoption of new solutions and flow of data. KIRAHub’s vision is to make Finland a pioneer in the digitalisation of the sustainable built environment - one that can be a global benchmark for successful implementation of infrastructure for balanced and future-oriented lifestyles.
TSE: What is KIRA-digi? What is its scope?
TL: KIRA-digi is a project aimed at boosting digital transformation within the real estate and construction sector in Finland. The project was intended to act as a wake-up call for the sector which has been slow to take advantage of the digital route, in order to achieve productivity improvements through ICT, as other sectors have done. The main objective was to get as many companies and stakeholders as possible, to experiment with new digital solutions within their processes and services. KIRAdigi was a joint effort involving the public and private sectors, that promoted digital experimentation, with 40% of government funding. A total of 139 experimental projects, worth almost EUR 13 million were started during 2017-2018, covering the whole lifecycle of the built environment - from land use planning and zoning, all the way to the project level which includes design, construction, operation and maintenance of the built assets. The project also promoted better information flow with open data and APIs and analysed the needs for legislative changes, in order to achieve true platform economies within the built environment. There were follow-up initiatives, starting with the reform of the land use and building act, and the national data platform RYHTI.
TSE: Could you briefly touch on the KIRA-digi experiments in digital land use planning, wind simulations with a city model, automating design processes, and BIM-based building permits?
TL: The digital land use planning project experimented with a digital platform for land use planning and zoning,
Mr Teemu Lehtinen, CEO, KIRAHub, Helsinki, Finland. Image: Mina Nytorp.
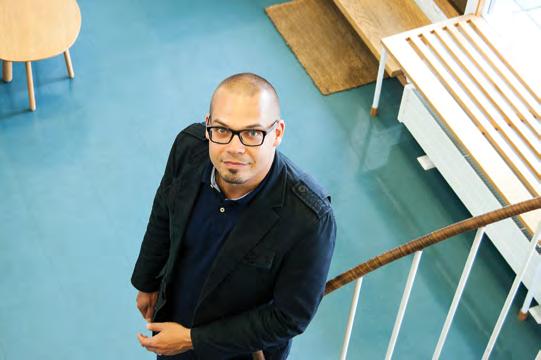
that integrates data from different sources and visualises it for stakeholders. The platform also had a real-time chat function. The objectives were to make the land use planning process faster, to reduce waiting times and to accelerate the shared understanding and decisionmaking. Coming to wind simulations, these are necessary, especially when planning areas for efficient construction close to the sea. Large constructed units and high-rise buildings can increase the negative effects of wind in the city. The wind has a significant impact on the micro climate, comfort and safety of the streets and pedestrian areas. 3D virtual models make it possible to study the effects of the wind in the current scenario and in the future. The wind in the city can be explored with techniques such as computational fluid dynamics. Implementing wind simulations, at the earliest possible stage of planning, provides a good basis for planning a comfortable and safe urban environment. The simulations involved calculations using the ANSYS Discovery Live application which has been used in product development, in the German automotive industry, for example, for designing cars and exploring air flows. In this pilot project, the application was tested, for the very first time, for modelling and analysing airflow behaviour, using information from a city model. The application produced very accurate results regarding information on both large and small areas. It would also be possible to model the wind and air pressure conditions, for example, on a single street. Regarding the automation of design processes, it must be said that the construction process, with its many parties and numerous execution alternatives, is very difficult to manage as a whole. There are not enough resources for performing the calculations for different alternatives, with the selection often falling on the solution that has been used the longest. With machine learning methods, alternative solutions could be generated with computer programs. Modelling a building’s details, according to an image, is a significant part of design, so even a partial boost to efficiency in this work could be immediately applied in practice. The main objective of the project was to
find out how BIM data models of buildings could be applied as starting data for machine learning and what the requirements are for their application in building design. Various AI methods are applied for analysing the material, and tests are conducted to determine whether a proposal for a design solution can be generated on the basis of this material. The subject of a test can be, for instance, the creation of a detail for a joint in a single building. The project on BIM-based building permits was a joint effort by three different municipalities (Vantaa, Järvenpää and Hyvinkää) and four different suppliers (Evolta, Gravicon, Solibri and Sova3D). The project sought to answer how well the targets set in the project description document would be met, and how the process should be changed or how the various software applications and their interoperability should be developed in the future. The project assessed the viability of the process, from the perspective of the authorities, applicants for permits, and designers. More and more sites are designed in a model-based way but, for the processing of the permit, the 3D designs are still saved in the traditional 2D format. This process results in extra work for both designers and building controllers. In future, the majority of buildings will be designed using data models, and their compliance with building regulations will be checked electronically, using artificial intelligence, by the designer, before the application for a building permit is submitted. The authorities’ task concerning the processing of permits will focus on examining the application from the perspective of the cityscape and the local plan and, on a case-by-case basis, approving justified deviations. Permits will be processed in a few weeks or days, instead of months.
TSE: Could you elaborate on two KIRA-digi experiments - ‘The paperless construction site’ and ‘Managing concrete curing conditions with IoT on site’?
TL: The project on ‘The paperless construction site’ experimented with real-time transfer of information to people working on a construction site through augmented reality. The aim was to efficiently provide workers with information that was essential for their work stages and roles during the construction process. The project conducted an experiment in which the workers in a construction project received crucial information, in real-time, for performing their tasks on the construction site, using augmented reality. The information was provided in a digital and easy-tounderstand format and it was shared with the workers at the right time and location. The project also measured the impact of the information on productivity. The project was divided into the following stages: • Generation of a digital 2D work image of the key work stages for each worker. • Extraction of relevant design information, required by each worker, from the data model, in the form of 3D images. Digital transfer of the information, in 3D, to a tablet or smartphone. • Combination of the 3D images based on the data model with augmented reality, i.e. video images of the site, on the tablet. • Enrichment of the information with 3D data that is crucial for the installation and, in combination with augmented reality, communication of the information to the right location. The experiment was limited to a residential flat and a bathroom undergoing plumbing renovation which
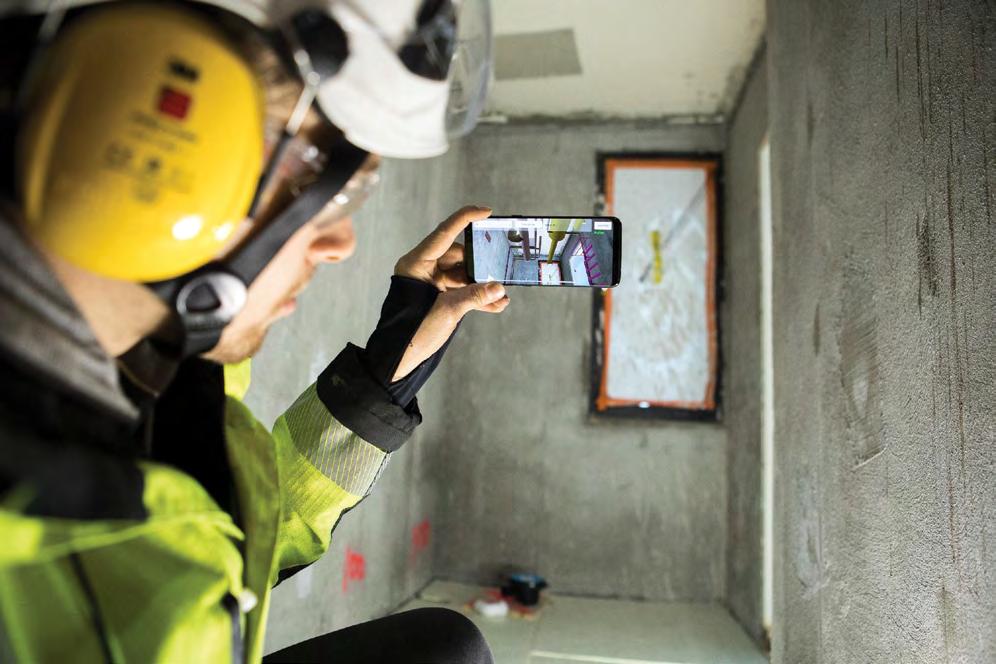
was carried out by Fira, a construction company. The experiment was carried out as a collaboration between Fira, and Sweco, an architecture and engineering consultancy. The augmented reality and location-based service were provided by the VTT Technical Research Centre of Finland. Several key learning points emerged from the project. • The feedback indicated a desire for better measuring accuracy and more specific measuring information directly from the screen. • The experiment showed how challenging it is to execute a practical BIM on a small mobile screen. • Users should be able to add feedback to the BIM, on the go, so there is a need for applications that enable two-way information transfer. • At this stage, the BIM itself does not yet contain all the measurements that need to be shown to the user. The project on ‘Managing concrete curing conditions with IoT on site’ developed a smart method for ensuring that concrete cures within the allotted time at the construction site. The timely drying of concrete on construction sites is important not only from a cost perspective, but also for avoiding structural damage due to dampness. Also, construction work, such as the the laying of carpets cannot proceed until the concrete dries. At the same time, the project was able to map structures at risk and the progress in the curing of concrete placements. A secondary objective was to assess the functioning of wireless data transfer methods (e.g. Wirepas, Lora and Sigfox) in a construction site environment. The project connected IoT (Internet of Things) solutions to dampness management systems used during construction. The IoT network included physical devices and machinery, such as air humidity and temperature sensors, that were connected to the Internet. The project was carried out in a residential building under construction. Air humidity and temperature sensors were installed in the rooms to be monitored, and the measurement data generated by the sensors was transferred wirelessly to a cloud service. Dampness in the drying concrete was measured at critical points. When the conditions were not optimal for the drying process, the system being developed alerted the site management to take action. The measurement data was analysed using machine learning methods. The aim was to find a way to improve the predictability of the drying process. The data collected in this project can also be utilised when planning the execution of future projects.
TSE: How can Finland and Singapore collaborate to further the digitalisation of the built environment industry?
TL: We started a close collaboration with Singapore during the KIRA-digi project and it has been really fruitful. There were delegations from both countries travelling back and forth to learn about solutions and implementation of digital processes. Both Finland and Singapore have a high ‘maturity level’ in the understanding of the possibilities in the digitalisation of the built environment and smart cities solutions. Therefore, it makes sense to keep learning from each other. Going forward, I see a lot of potential for connecting different data platforms, and accessing data in a unified way on a global level, to be used in AI and machine learning solutions and digital tools for the built environment. Finland and Singapore could lead the way in this, globally, and I am really looking forward to a deepening of the collaboration on different levels - between the governments, innovation hubs, companies and data platforms. More information may be obtained from www.kirahub.org
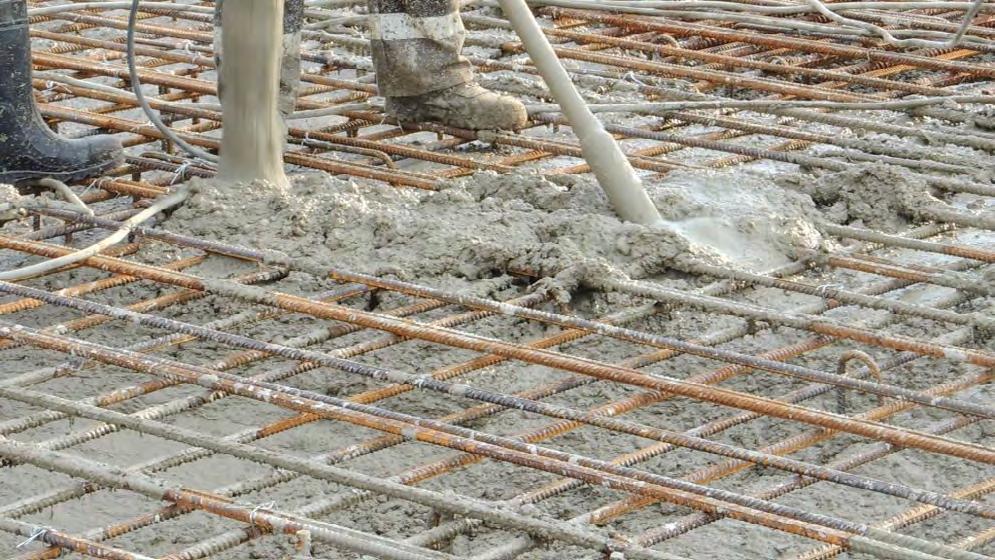