
11 minute read
Cold milling machines solve big challenge They were used to precisely mill the spillway chute of the Oroville Dam, the highest dam in the US
COLD MILLING MACHINES SOLVE BIG CHALLENGE
They were used to precisely mill the spillway chute of the Oroville Dam, the highest dam in the US.
Temporary solution makes milling in two passes necessary
At an altitude of 235 m, the earthfill embankment dam on Lake Oroville holds back the waters of the Feather River. After several weeks of rainfall, the dam reached its maximum water level of around 4.3 billion m³ in the winter after only 50 days. As a result, the owner, the California Department of Water Resources, had to initiate flood control measures at an early stage. The water was discharged in a controlled manner over the top of the dam structure at the level of the dam crown and the adjacent spillway. Due to the large quantities of water and the extremely high water pressure, however, the 55 m wide, main concrete spillway eroded to such an extent that rehabilitation was unavoidable. The damage was initially minimised provisionally by filling the erosion in the surface with rolled concrete, so that the owner could open the overflow system during the winter months, if necessary, explained Chris Anderson, Project Manager at the subcontractor, Anrak, who provided the milling service. This temporary material had to be removed prior to final concrete paving with Portland cement, however, in order to achieve the desired surface quality. To complete this task, the contractor decided to use two cold milling machines from Wirtgen.
Ensuring reliability and precision
Eight days had been scheduled for the removal of the first layer of rolled concrete. The lower section of the spillway was about 300 m long. The milling depth required was approximately 5 cm. This job was performed by the W 2100 equipped with an ECO Cutter milling drum. This milling drum is fitted with up to 50% fewer picks at larger tool spacings (LA) than a standard milling drum. Fewer picks mean a lower cutting resistance, making it possible to mill hard surfaces such as concrete. This process was followed by the W 210i with a standard LA15 milling drum to give the milled surface the finer texture required to pave the new concrete layer. During the job, both machines used the Level Pro leveling system developed by Wirtgen.
Anrak’s CEO, Tom Schmidt, had high praise for the Wirtgen milling machine used together with the Level Pro system. He said, “It is both reliable and extremely precise. The evenness of the surface is perfectly uniform and the machine always has excellent traction. The latter is important when milling rolled or Portland cement concrete. And the vibrations that are unavoidable when milling such a hard surface do not affect the Level Pro system”.
Logistical challenges
After the flat-bed trucks had transported the cold milling machines to the upper end of the spillway, the machines were lifted onto the structure with the aid of lattice boom cranes and driven onto the area in need of rehabilitation via specially constructed ramps. Here they faced the next challenge - milling on a 30° gradient. This challenge was solved by attaching steel cables with a total length of more than 450 m to the blades of a large wheel loader and to the rear of the large milling machines, thus securing the machines while work was being carried out. In the process, the heavy steel cables were attached to several hundred trolleys that are normally used for transporting heavy furniture in order to prevent them from rubbing against the ground. “We used the trolleys to prevent the texture of the freshly milled concrete surface from being damaged”, explained Tom Chastain, Applications Specialist at Wirtgen America.
Application expertise and safety
The machines have a working width of 2.2 m, and it took an average of two hours to remove an entire length. “In order to achieve the desired surface quality, but also for safety reasons, the cold milling machines were operated at a low advance rate of approximately 3 m/ minute”, said Chastain. In the end, the W 2100 and the W 210i had each milled 28 full lengths. The cold milling machines loaded the milled material directly onto tracked vehicles with a capacity of 5 m³. These machines are mainly used in open-cast mining, but their manoeuvrability also made them valuable for steep gradient milling at the Oroville Dam. As soon as the tracked vehicles were filled, they unloaded the milled material at the lower end of the spillway so that it could be transported to a nearby concrete plant. There, the concrete milled material was reprocessed into new concrete for the subsequent construction project. After the ‘milling the spillway’ sub-project had been reliably completed within the scheduled time-frame, the entire rehabilitation project costing USD 1.1 billion was completed on schedule after around two years.
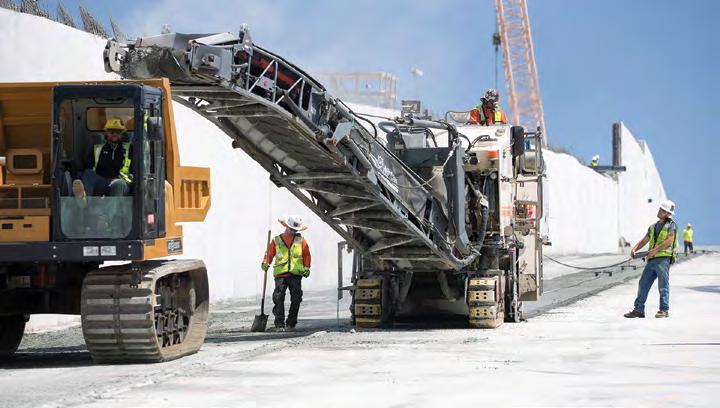
Wirtgen cold milling machines prepared the Oroville Dam’s spillway for the repair project.
All images by California DWR

Steel cables attached to a wheel loader secured the Wirtgen cold milling machines.


MANITOU ASIA INTRODUCES THE 220 TJ-X AND 220 TJ+-X AERIAL WORK PLATFORMS
Manitou Asia has introduced two high-capacity compact aerial work platform (AWP) models - the 220 TJ-X and 220 TJ+-X. Manitou Asia is part of the Manitou Group, a world leader in equipment for operation on rough terrain, material handling, access and earthmoving. Capable of reaching a height of 22 m, the 220 TJ-X is light and compact, and has a basket with a capacity of of 230 kg, while the 220 TJ+-X has a basket which can take up to 350 kg of load. This capacity remains, regardless of the articulated arm’s position or the telescopic extension. The machine’s compact dimensions give operators the desired manoeuvrability, especially on construction sites with a heavy load of machines. With an overall fold-up size of only 8.04 m, the 220 TJ-X is built to facilitate transportation and meet the expectations of rental companies. Powered by a 4-cylinder, 26 kW diesel engine with a variable speed pump, the telescopic booms of the 220 TJ-X and 220 TJ+-X ensure ease and precision when in use. A built-in system also automatically adjusts the engine’s power accordingly, to reduce fuel consumption and total cost of ownership. The machines are also installed with a hydraulic block to provide smooth and rapid movements with complete safety. The jacks taper off before stopping, giving added comfort and eliminating risks arising from jerky movement. A system patented by Manitou automatically adapts the speed according to the degree of extension of the boom, to maintain constant speed regardless of the basket’s position. Designed for use in tough conditions, the machines are ideally suited to handle uneven ground and environments with high salt content and high temperatures. For example, in the San Juan viaduct bridge building project in the Philippines, with a tight working environment and multiple crossings, the default 4-wheel steer of the 220 TJ+-X enabled the operators to manoeuvre it around with ease. Its rough terrain capability also tackled all kinds of crossings on site while its versatility made it possible for the machine to be used on a floating platform during construction as the viaduct was built on a canal. Apart from being highly durable and able to boost productivity, these AWP machines are equipped with IIIA engines to reduce noise during use, to as low as 106 decibels. Like all new Manitou machines, the 220 TJ-X & 220 TJ+-X are connected machines to enable users to optimise usage and maintenance of their machines. This allows Manitou to accurately analyse data to reduce the total cost of ownership for operators.
The new aerial work platform models can help to boost productivity. Image: Manitou Group.
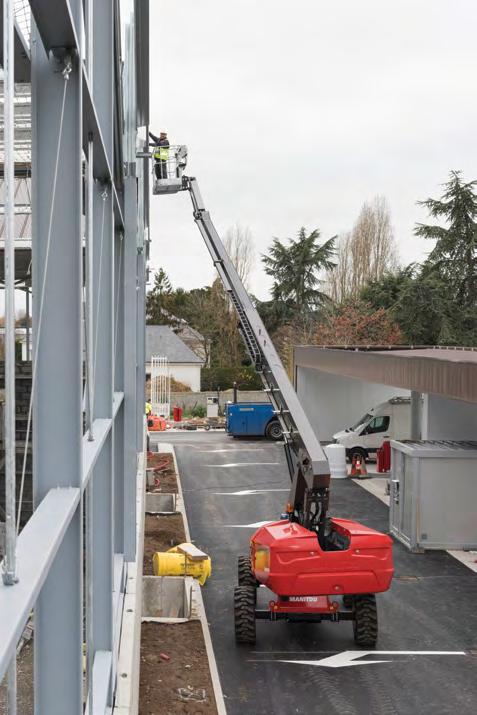
AWP model
Type of wheel drive (WD) / wheel steer (WS)
Capabilities
Basket capacity
Basket dimensions
Working outreach Machine dimensions
Weight
220 TJ-X 4WD / 2WS 220 TJ +-X 4WD / 4WS
Oscillating axle + differential locking 360° continuous rotation 230 kg per 2 persons 350 kg without restriction per 3 persons
2,100 x 800 mm 17.6 m 9.8 x 2.49 x 2.47 m 2,300 x 900 mm 17.8 m 10 x 2.49 x 2.52 m
11,850 kg 13,800 kg
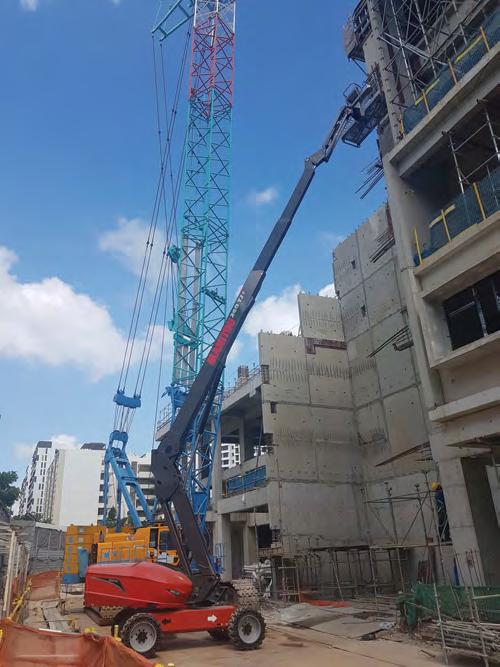
The 260 TJ-X aerial work platform is designed to increase the operational efficiency of worksites. Images: Manitou Group.

The 260 TJ-X aerial work platform (AWP), from Manitou Asia, is equipped with a supersized basket that can lift three operators or 400 kg in load up to a height of 25.9 m. The machine is designed to increase the operational efficiency of any worksite. Targeted at operators requiring a large working area and flexibility of use, the 260 TJ-X is built with an offset of 19.7 m, pendulum travel of +/-70° and capacity for continuous 360° rotation of the turret. Its off-road and four-wheel drive abilities also assure a high-crossing capacity across difficult terrains. Size is not the only advantage of the 260 TJ-X. Its high-precision hydraulic movements ensure maximum operator comfort and its system to reduce noise to 106 decibels effectively moderates noise pollution. In addition, the AWP’s remote control feature gives users a clear view of the entire AWP and the ability to steer the basket to the optimal position. The machine also reduces the Total Cost of Operation (TCO) and is equipped with a diagnostic aid for faster maintenance operations and minimal machine downtime. The 260 TJ-X’s overall unfolded length of 7.88 m makes transporting it a breeze. Optional features of the machine include the Easy MANAGER and the SMS (Safe Man System), an operator protection system that is fully compliant with industry safety standards. The machine’s performance has already benefitted Kwan Yong Construction for its school building project in Singapore. Limitations in the previous machine used had undesirably increased the frequency of transferring raw materials to the specified height, causing delays in the project timeline. After switching to the 260 TJ-X, Kwan Yong was able to lift significantly more raw materials with one transfer, along with tools and other heavy equipment, owing to the 400 kg capacity basket. The time-saving proved crucial in enabling the contractor to complete the project on schedule.
Height Basket capacity
Machine dimensions
26 m 400 kg 2.48 m x 7.88 m
Weight
16,380 kg
NEW CATERPILLAR DOZER LOWERS OWNING AND OPERATING COSTS
The new Cat D9 dozer, from Caterpillar, replaces the D9T model and offers customisable configurations to meet application needs around the world. Built on a legacy of longevity and proven reliability in the field, the new Cat D9 lowers overall costs per unit of material moved by up to 3%. Efficiencies gained through a new torque converter with stator clutch reduce fuel consumption by as much as 5%, and the new dozer reduces maintenance and repair costs by as much as 4%. The new dozer features the proven Cat C18 engine which has a range of exhaust after-treatment solutions available. The D9 also features differential steering for a tight turning radius and the ability to maintain ground speed while turning, to keep productivity high. The suspended undercarriage delivers more track contact with the ground for less slippage and greater productivity. The versatile D9 can be equipped with blades and attachments from a wide range available, enabling it to work efficiently in a variety of applications, including production dozing, site maintenance, fleet support and ripping. For companies engaged in heavy construction, quarry and aggregates, landfill, bulk materials handling and forestry applications, the D9 Dozer is expected to deliver low owning and operating costs while maintaining high productivity.
Reduced maintenance and enhanced safety
Featuring a frame that absorbs and withstands highimpact shock loads encountered in severe applications, the new D9 offers design improvements that reduce maintenance and repair costs. The newly integrated AutoLube system results in fewer grease points to limit daily maintenance procedures. Extended filter change intervals, simple component removal and continuous fluid level monitoring also aid in further lowering operating costs. A new ground-level service centre provides convenient access to the engine shutdown switch, access/egress lighting and optional powered ladder operation. With
ADVERTISERS’ INDEX
Helsinki Business Hub / KIRAHub (Finland) ––––– Page 05 IES Chartered Engineer –––––––––––––––––––– Page 01 IES Membership –––––––––––––––––– Inside Back Cover IES Railway Systems Handbook –––––––––––––– Page 03 standard rear-view mirrors, the new D9 affords the operator clear lines of sight to front and rear working areas. The optional four-camera system offers a 360° view around the machine and ripper to further enhance operating safety. Adding bottom guard retention pins and eliminating lift cylinder grease points also bolster safety. A new design with advanced ergonomics, the cab features intuitive controls that are easy to access and operate. Its cloth air-suspension seat provides operator comfort throughout the entire shift. The suspended undercarriage reduces shock load transfer to the undercarriage by as much as 50%, resulting in a smoother and more comfortable ride. The new operator station comes fully equipped with large, highdefinition touchscreen displays and new electronic architecture that is scalable to meet the customer’s technology needs.
Integrated technology
Sensors integrated into the new Cat D9 provide access to advanced operating technology. Machine management tools provide customers with dozer information. Other features include the Available Automated Blade Assist, the Cat AutoCarry option and the Automatic Ripper Control option.
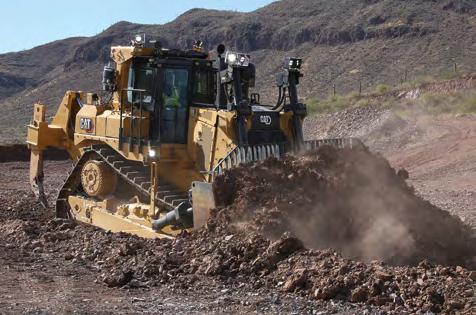
The new Cat D9 dozer. Singapore University ––––––––––––– Inside Front Cover of Social Sciences TW-ASIA Consultants Pte Ltd ––––––––––––––– Page 21 Who’s Who In Engineering, –––––– Outside Back Cover Singapore (3rd Edition)
