
15 minute read
Kristi Montgomery is Vice President, Innovation, Research & Development, at Kenco Group
AHEAD OF THE CURVE
Kristi Montgomery, Vice President, Innovation, Research & Development at Kenco Logistics Services, has identified over 40 million dollars in savings since launching the company’s groundbreaking Innovation Lab.
enco Logistics Services offers customised thirdparty logistics (3PL) management solutions including distribution, transportation, material handling, and solutions engineering services to businesses across North America. Kristi Montgomery is Vice President, Innovation, Research & Development, and responsible for Kenco’s supply chain transformation initiatives utilising emerging and digital technologies.
Having been with the company for over 30 years, she heads up the group’s Innovation Lab, committed to applying innovation in new and existing customer relationships.
“In 2015, the foresight and vision of our leadership to make innovation a priority put us ahead of our competitors, and our customers reaped the benefits,” Kristi says. “Organisations using our services need their providers to look towards the future, identify trends and new technologies, determine how they would impact their business, and decide how best to prepare for it.”
Seven years later, Kenco Innovation Labs have identified over 40 million dollars in savings for customers, and they continue to push that envelope of what is coming next. They provide research, education, and thought leadership to customers. But the biggest benefit of the Innovation Lab lies in its ability to test new technologies in a realworld environment, throwing as much challenge into new solutions as possible and proving their value. In 2019, Kenco expanded their Innovation Lab to include a 10,000 square foot warehouse facility and fully functional distribution centre with the same environmental, space, and technology challenges as any normal warehouse. How does this really play out? Take robotics as an example. It is difficult to find the right solution that will accommodate a customer’s specific needs. This is where Kenco comes in.
“We become the experimentation arm for our customers, testing out solutions before they put them in production,” Kristi explains. “One of the robotic solutions we looked at continued to fail while operating in our test facility for no apparent reason. Working with the vendor, they realised that the extreme pollen count during that time of year in our facility was blocking the LIDAR
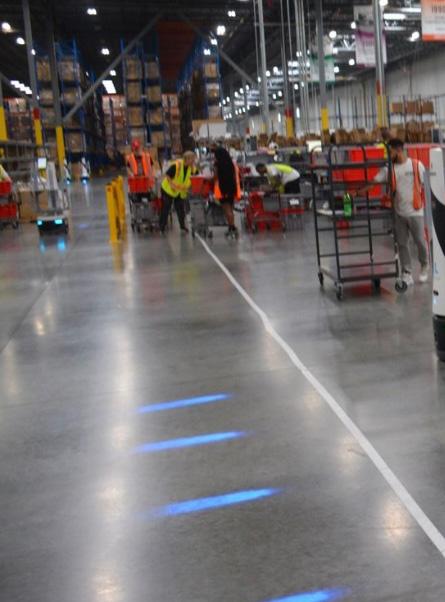
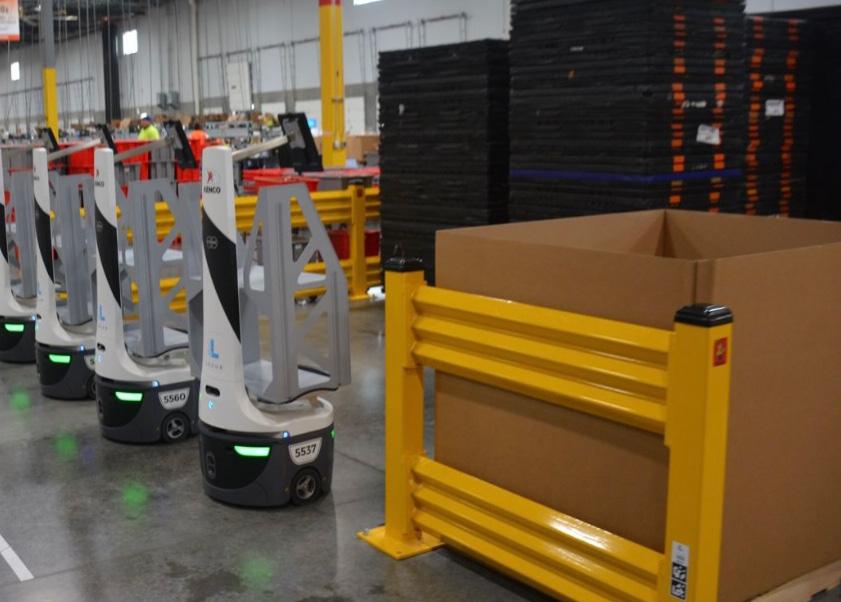
sensors that allowed the robots to navigate the space. The value our customers found in not having to find this out on their own in production was immeasurable.”
INNOVATION EVERYWHERE
Kenco has been an innovator long before the founding of its Innovation Lab in 2015. In its 70+ years of business, Kenco boasts a history of entrepreneurial spirit and innovation including material handling industry attachment inventions, the first contract warehouse agreement, the development and application of the first known warehouse management system, and more.

The innovation never stopped. Kenco is constantly finding new ways to keep a finger on the pulse of new trends. A key to success has been its work with start-up accelerators and entrepreneurs in the space to keep an eye on what is emerging and in development that could be impactful in the future. Kenco continues to participate in logistics pitch days and corporate connection events with supply chain start-ups, which has led to multiple implementations of new technologies for customers.
Though far from exhaustive, below is an exploration of Kenco’s recent innovative endeavours resulting from these efforts.
INNOVATION IN WAREHOUSE SAFETY
Kenco is currently working on several exciting projects in warehouse safety, including in the industrial internet of things (IIoT) space. Soter Analytics’ Soter Spine, for example, is a device that clips onto an associate’s collar and vibrates when they twist or bend improperly. The device also provides analytics around who needs additional coaching or who is improving. “This safety element is so important because employees’ physical safety is a top priority for our organisation,” Kristi says. Additionally, Kenco is currently piloting a project with HeroWear exoskeletons at two of its facilities where heavy lifting or repetitive activities potentially put strain on associates’ backs. HeroWear exoskeletons are wearable, lightweight devices that help reduce back injuries in the workplace. John Barlew, Vice President of Safety at Kenco, notes, “The need for back support in warehousing is undeniable. The exoskeleton has the potential to remove 50 pounds of lift pressure from the lower back. When bending, it will thrust you up into a standing position to help remove the strain.”
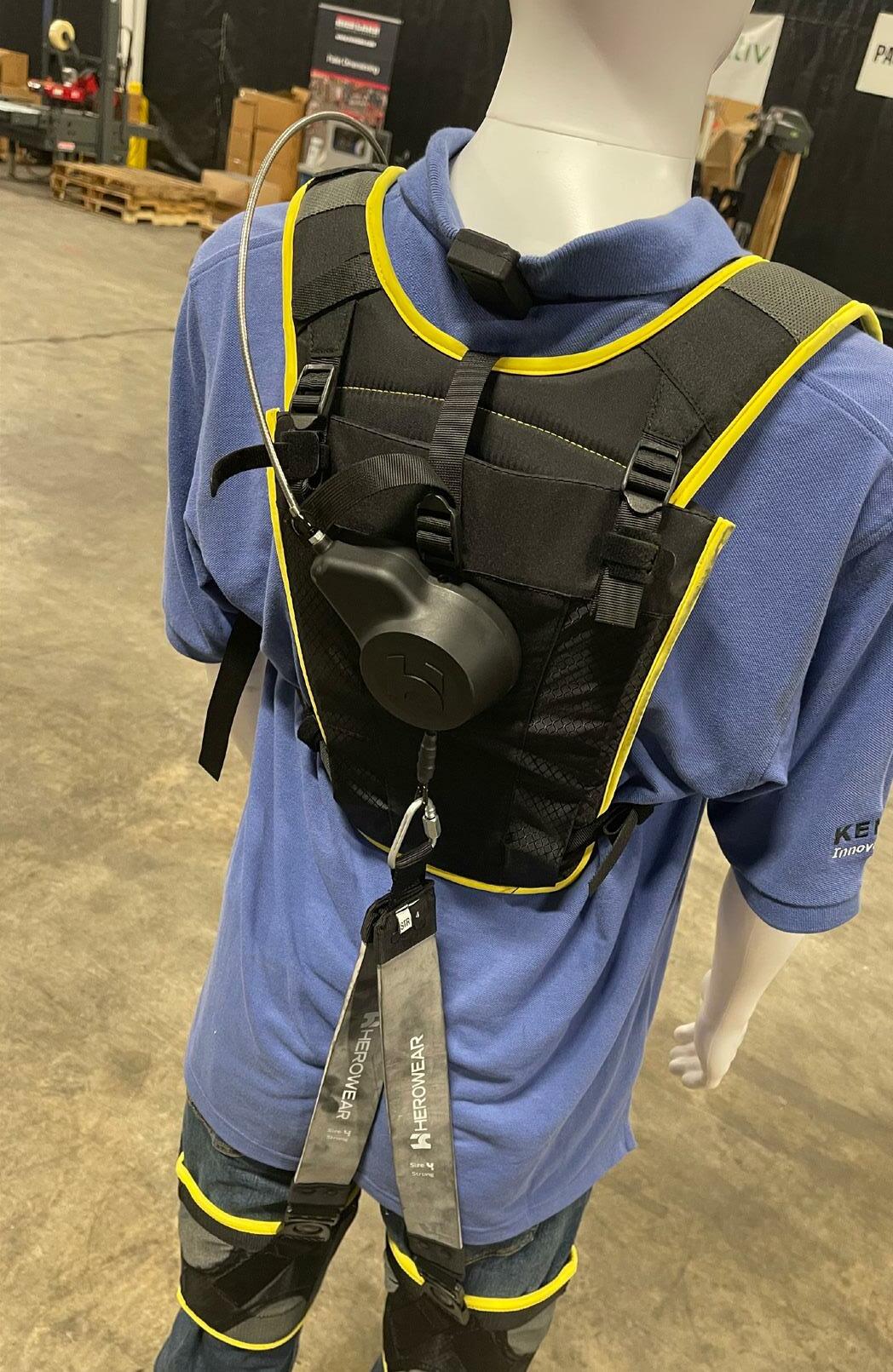

Nothing posed a bigger threat to employee wellbeing in the past 18 months than the pandemic. The company took a strong approach to Covid at the outset, forming a Covid taskforce to look at the data on a regular basis and direct senior leadership. “We implemented safety measures including automatic temperature checks, limited visitors, stricter cleaning, contactless driver interactions, and mask policies,” Kristi says. “Because we took a strong stance early on, we were able to mitigate some of the outages that our competitors experienced. From an innovation perspective, we asked what we could do to make our sites safer, and deployed scrubbing robots that were completely autonomous,” she adds.
FUTURE-LOOKING ROBOTICS AND DRONE SOLUTIONS
Körber assisted Kenco in selecting the right robotics solution – Locus Robotics – for one of its ecommerce facilities, providing assistance throughout the project. “Locus is an autonomous mobile robot that increases your picking productivity,” Kristi explains. “People are kept in the picking aisles and the robots do the travel distance back and forth to the packing station, which increased productivity four-fold, from 30 lines per hour to 120 lines per hour at peak. However, since we were not using the Körber warehouse
Assistance. Comfort. Freedom of Movement.
Suit weighs only 3.5 lbs
Offl oads 75 lbs
Full mobility

MODULAR EXOSUITS STARTING UNDER $1,200 PERFECT FOR SMALL COMPANIES TO GLOBAL ENTERPRISES
Learn More at HeroWearExo.com

management system (WMS), but a specific ecommerce platform, we encountered some difficulties in the way it could integrate with the Locus solution. That’s where we brought in SVT Robotics.”
SVT Robotics built a proprietary SOFTBOT® Platform, which rapidly integrates any enterprise software with any automation, robot, IoT device, or human productivity tool for any task, orchestrating these technologies from disparate companies so they all work in concert. With SVT Robotics, Kenco was able to add connectors to their WMS, with multiple connectors between various types of automation. This helped Kenco to overcome some of the challenges it faced integrating with the Locus solution.
“We see SVT Robotics as transformational technology for the future of allowing rapid deployment, easy experimentation of plugand-play robotics, and execution system augmentation with workflow features,” Kristi adds.
Voodoo Robotics provided a dynamic, pick-to-light device that could be magnetised to stick to racking and relocated easily. Kenco deployed the Voodoo Robotics system to increase efficiency and help with bottleneck issues during peak season.
The solution fills the put wall with high-volume SKUs, Voodoo indicates the tote to pick from on the put wall with a light and text on a screen, the picker picks all of the SKUs for the order, and another Voodoo device indicates that the order is complete, instructing the packer to remove the tote and pack the product into the shipping container. Once this is complete, the tote with container goes onto the conveyor line along with other totes provided by the Locus Robots as they are delivered. The project was completed in phases to be mindful of the production impact on the floor.
With Voodoo Robotics’ flexible design, and intuitive interface, Kenco customers achieve more picking in less time, and with fewer errors.
Kenco also worked with B Garage to develop the world’s first autonomous battery changing drone solution, which is housed in Kenco’s Innovation Lab. They also collaborated on autonomous mobile robots and more traditional AGVs. But can these solutions be deployed successfully and generate the productivity savings they promise?
“The simple answer is yes. We have done it,” Kristi answers. “We have been testing robotic technologies for several years to determine the key capabilities of each one so we can deploy the best fit for our customers. We have also deployed augmented reality, with vision-enhanced picking
VOODOO ROBOTICS
QUICKLY IMPROVE PICKING SPEED & ACCURACY
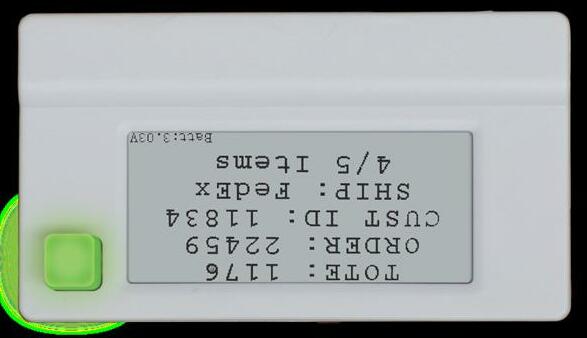
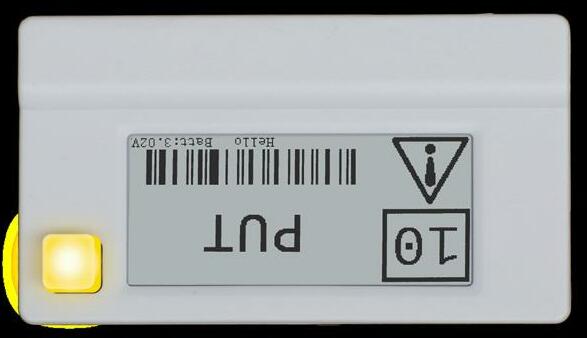
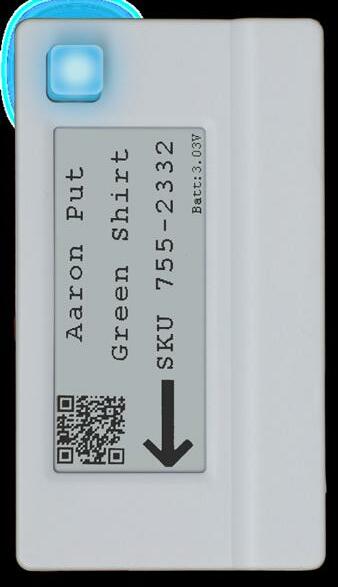

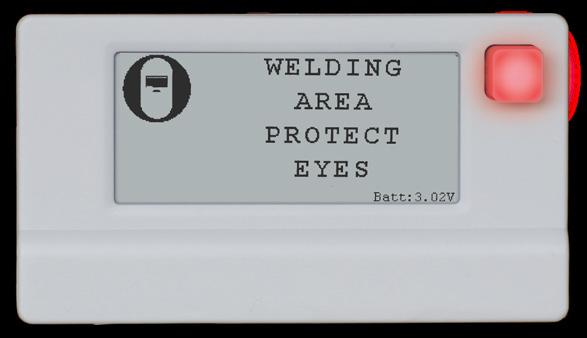
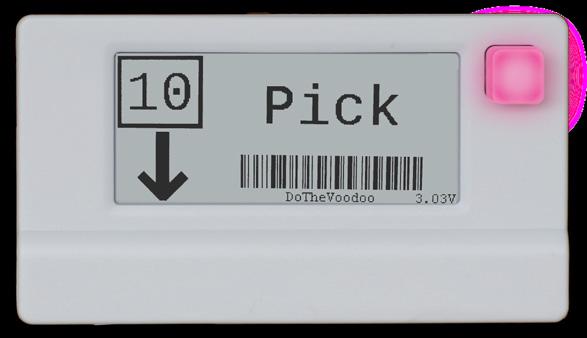
Pick/Put to Light Picking Carts Put Walls
Wireless: Two AAA batteries last for years. Arrows: One device for 2,4, even 8 locations. REST API: Integration is a snap! Call or e-mail to setup an online DEMO today. (972) 914-8758
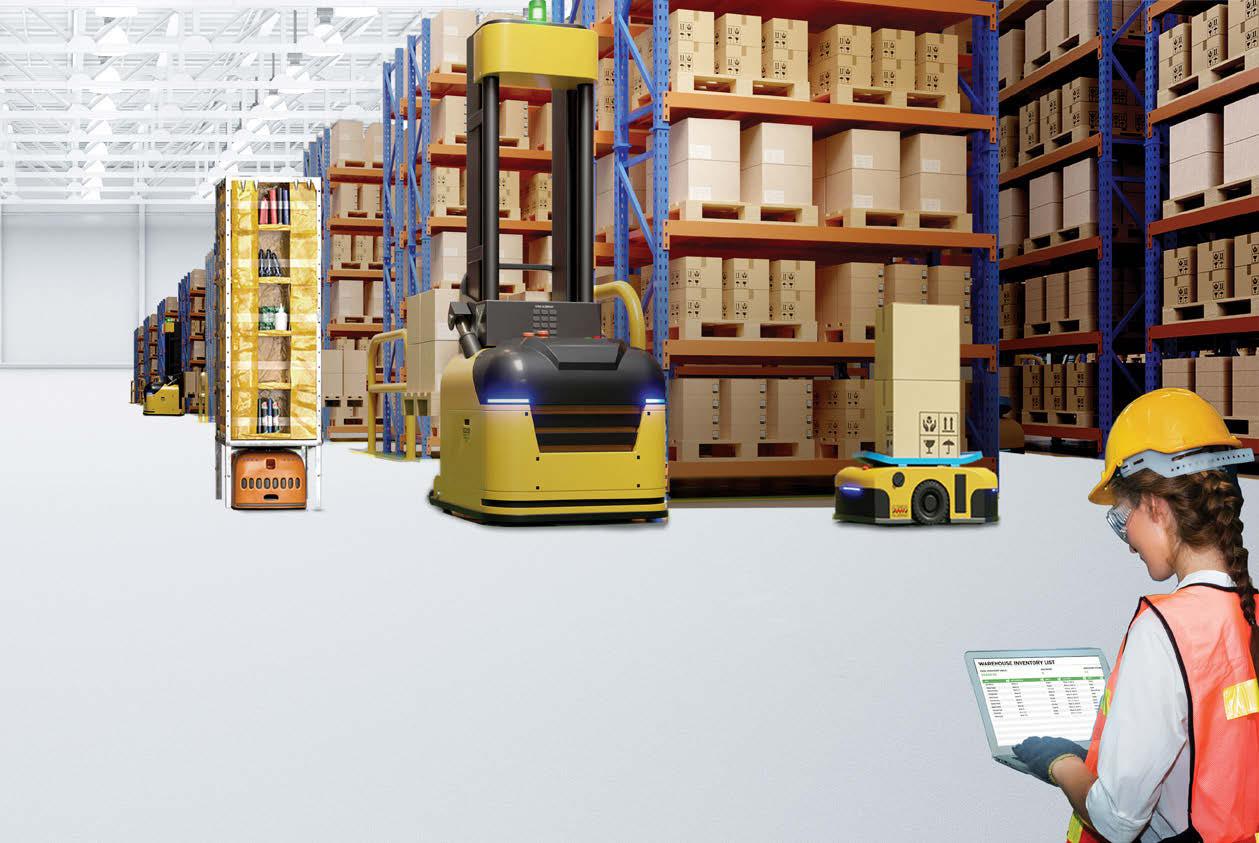
From ZERO to AUTOMATED
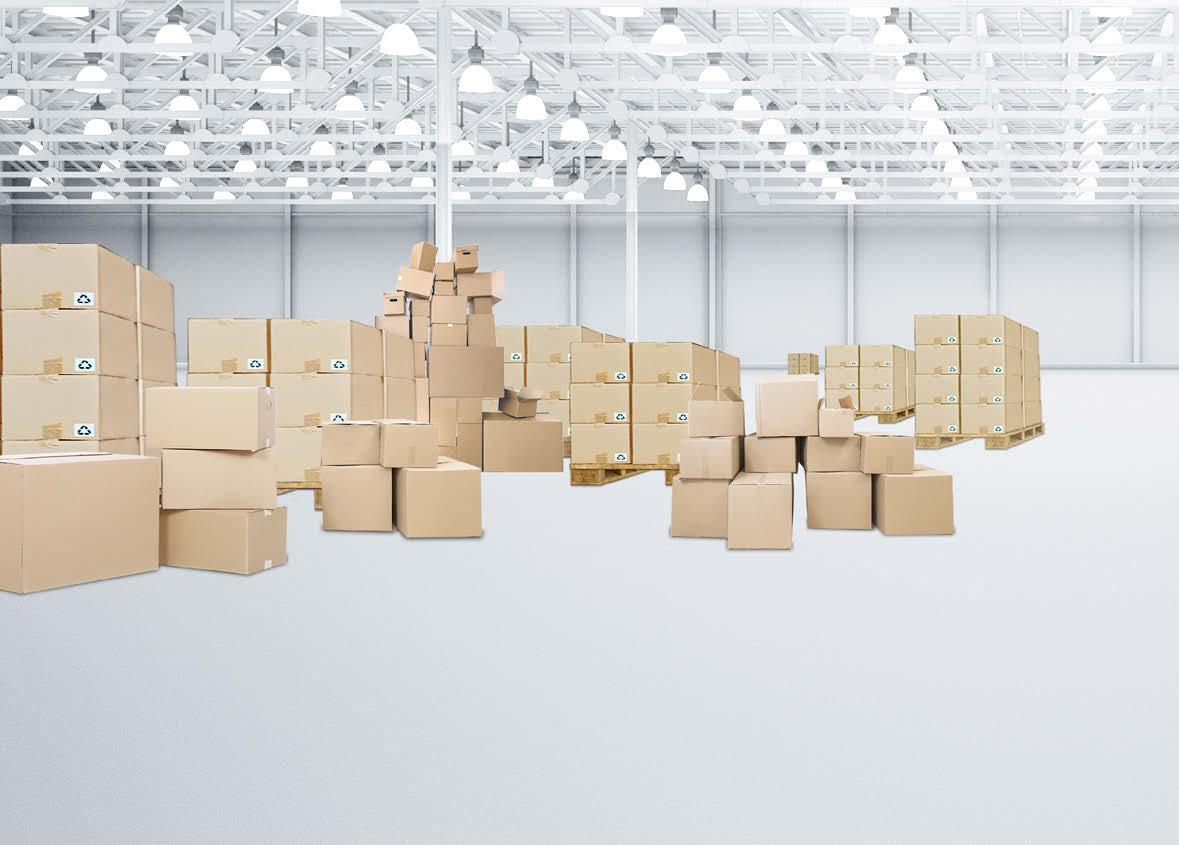
Just like that
SVT Robotics has a singular focus:
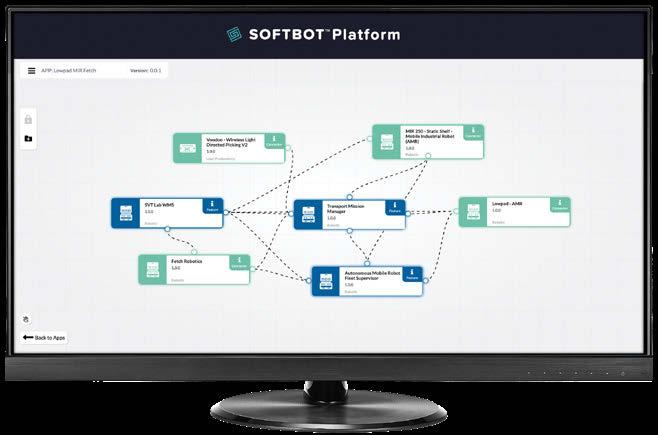
To make integration and deployment of enterprise automation technology quick and easy. Our SOFTBOT® Platform rapidly integrates any enterprise software with any automation, robot, IoT device, or human productivity tool for any task, orchestrating these technologies from disparate companies, so they all work in concert.
That’s insanely powerful.
It speaks to why our platform has received numerous awards, including: • 2021 Gartner® Cool Vendor • 2021 NextGen Supply Chain Award • RILA 2021 Startup Innovation Award • Top Supply Chain Projects Award by
Supply and Demand Chain Executive
The SOFTBOT Platform from SVT Robotics. It’s automation at the speed of your business need.
Meeting Peak Holiday Rush with the SOFTBOT® Platform — a Kenco Logistics Case Study
In July of 2021, third-party logistics company, Kenco Logistics, partnered with SVT Robotics to quickly connect and integrate their WMS with a fleet of Autonomous Mobile Robots (AMRs). The goal was to have system integrations in place and working smoothly in time to meet a Kenco e-commerce client deadline of peak holiday season that begins in November and runs through December.
At the time the project kicked off in July, the WMS platform being utilized by Kenco did not yet have integrations, or “SOFTBOT connectors,” built on SVT’s SOFTBOT Platform. Nonetheless, SVT Robotics was able to quickly build the necessary connector in just over two weeks, with user acceptance testing taking place on August 16th and go-live launch on September 7th.
That fast schedule easily gave Kenco’s client plenty of time to gear up for their busy holiday shopping season.
In fact, the integration between their WMS and the AMR fleet went so smoothly, Kenco was able to accelerate their longer-term plan for staggered ramp up and begin that process on just day two of live operations vs. their original goal of beginning ramp up at one-week post-launch.
The plug-and-play functionality of the SOFTBOT Platform means companies can rapidly integrate the solutions necessary to meet accelerating business needs. Kenco Logistics quickly and easily met their goals - contact us to see what SVT Robotics can do for your company.
See the SOFTBOT Platform in action at svtrobotics.com/Kenco
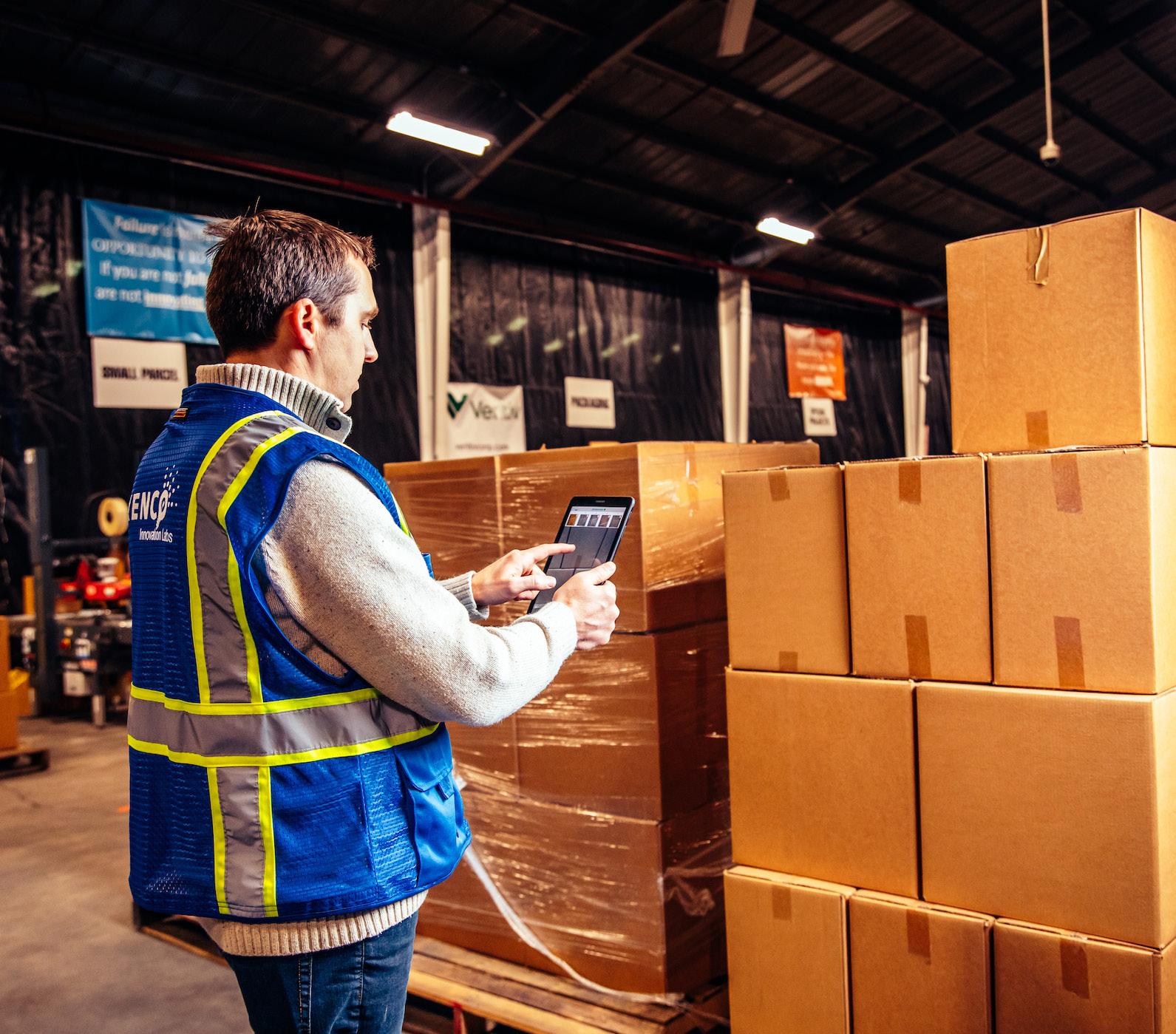
solutions for customers who have retail shipments that are sensitive to chargebacks, as well as wearables, voice-enabled systems, visionenhanced smart packaging, and autonomous tuggers that move eight pallets at a time instead of two. We did not change our focus of being more efficient and effective. We just pushed it to the next level.”
KEEPING AN EYE ON DATA SCIENCE, MACHINE LEARNING, AND AI
Kenco continues to put an emphasis on data science, machine learning, and artificial intelligence.
Kenco’s Director of Data Science and Business Intelligence, Satish Vadlamani, explains, “We developed our own proprietary AI engine called DaVinci AI, and have built several predictive models around volume planning, labour planning and predicting recovery. We are also currently building out a full supply chain end-to-end control tower.”
As a direct response to the supply chain disruptions and recordbreaking labour shortages that the pandemic created, Kenco updated DaVinci AI to generate savings of up to $300,000 in labour costs for some customers and deliver volume predictions at over 90 per cent accuracy. The solution helps improve productivity, efficiency, and ultimately, the customer experience.
“We have put a greater focus on data insights and digital technologies in recent years,” Kristi adds. “We are building a digital supply chain to help both our customers and our employees.”
KENCO’S PROPRIETARY TECH SOLUTIONS
As part of its commitment to digital transformation at every level of the supply chain, Kenco launched Kenco TMS LITE in 2021. The technology empowers small to midsized shippers with the resources they need to effectively manage their transportation networks and drive business success. With integration-free deployment, outof-the-box reporting, and intuitive user experience, Kenco customers can quickly leverage this TMS tool to optimise their transportation networks for greater returns and
customer satisfaction. Kenco TMS LITE also includes access to free training and specialised services through a single, personal point of contact.
“At a time when the freight market is extremely volatile due to the Covid-19 pandemic, mitigating carrier increases and increasing supply chain reliability are paramount for companies of all sizes,” says Mike McClelland, SVP of Transportation at Kenco. “Innovative solutions like Kenco TMS LITE are just one of the ways that we provide value to our customers.” Kenco is also a pioneer of its own telematics solution. Kenco’s FleetCloud is one of the most powerful telematic devices in the industry today. FleetCloud is a telematics solution that automates material handling equipment service processes and monitors equipment performance to drive efficiency, safety, and compliance.
Allen Polk, Vice President of Sales at Kenco says, “For over 70 years, Kenco has maintained its belief that material handling equipment (MHE) is a pillar to every warehousing operation, and having awareness of your MHE fleet is the difference between a successful, profitable operation and an inefficient one. From efficiency and safety to productivity and compliance, we’ve continually emphasised telemetry’s benefits of data-driven fleet awareness across MHE programs. Offering the industry access to a truly brand-agnostic telematics solution in Kenco FleetCloud™ with a customer-centric focus on implementation is just another step towards our goal of creating highly
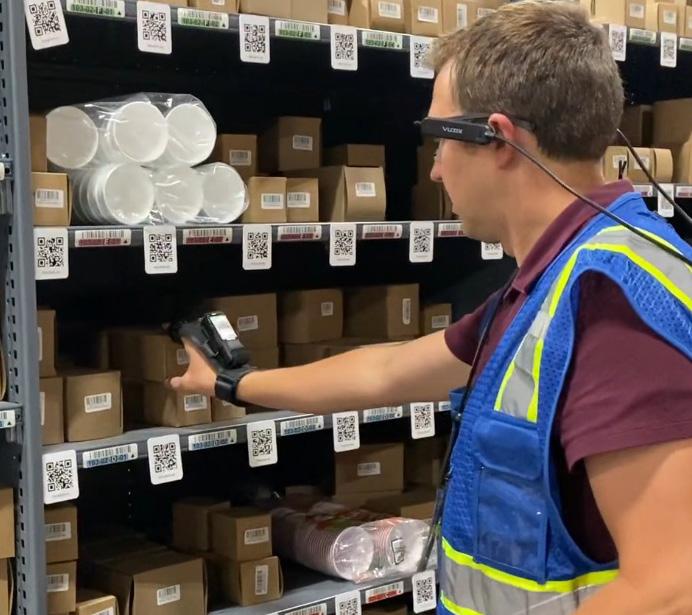
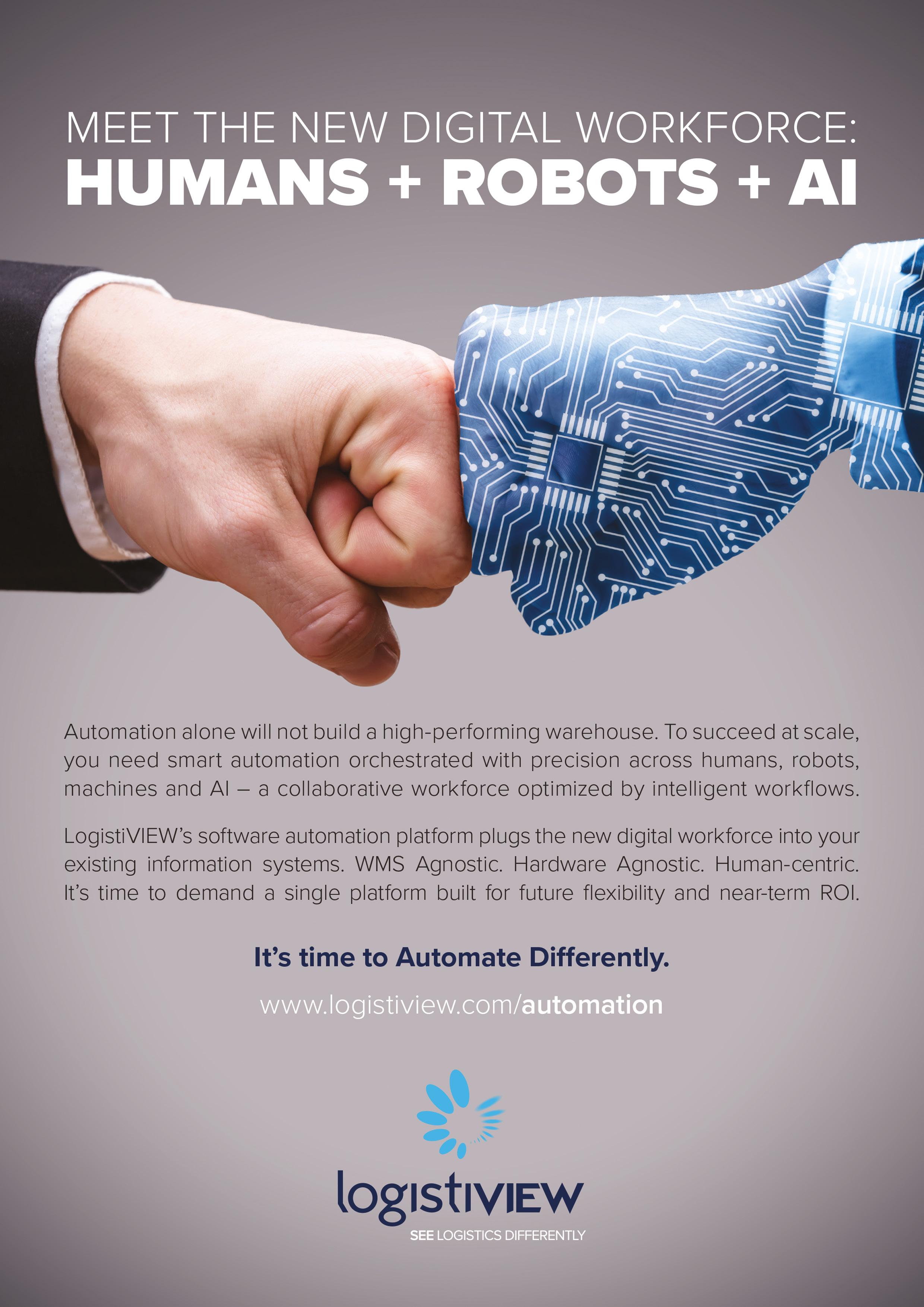
efficient and intelligent supply chains for companies of all sizes.”
ADDITIONAL NOTABLE PARTNERSHIPS THAT DRIVE CUSTOMER SUCCESS
Kenco believes it is critical to form key partnerships with other companies and would not have achieved the 40 million dollars plus in savings without taking this approach.
Logistiview is one example. Kenco partnered with Logistiview to become the first 3PL to use their workflow configurator program for vision. Augmented reality glasses connect to Körber’s WMS to take orders and create picking/puttingaway tasks. When the associate puts on the glasses, they see a picture of what they need to pick. The proper pick location is highlighted in green, thus reducing the error rate. This solution improves picking and shipping accuracy while reducing the need for 100 per cent quality control audits.
To tackle the issue of customer chargebacks (i.e. underpaid invoices in the event of a problem), Kenco developed a solution together with Smart Gladiator for a more organised approach to supply chain accountability.
If you are shipping to retailers and deal with Retail Chargebacks, Damages and Freight claims, you need LoadProof!
Don’t lose sleep over Retail Chargebacks Prove you did your job right Save at least $20K per month per facility resulting in $250K+ in savings in one year Improve Retail Compliance Increase Supply Chain Visibility
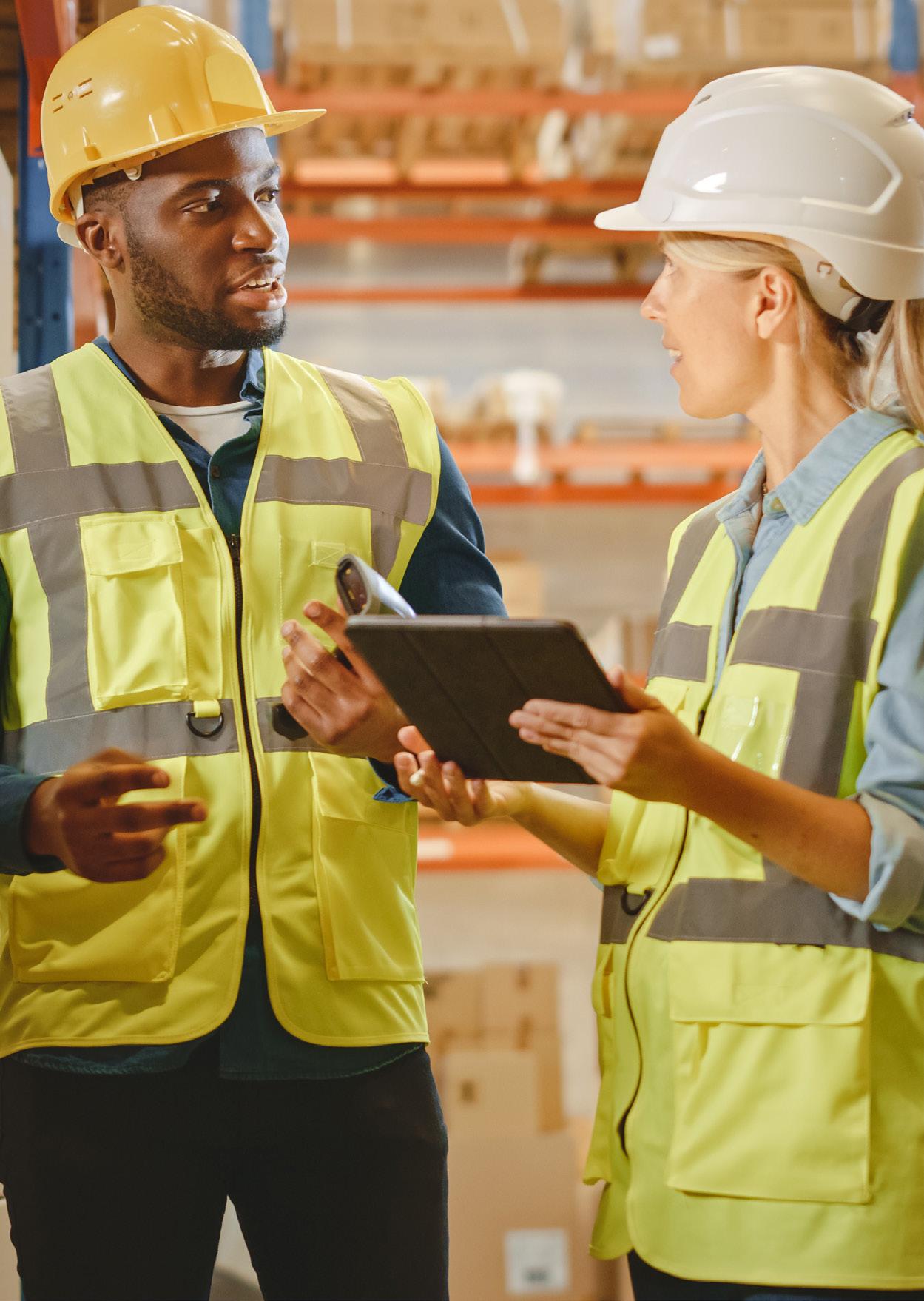
Start saving today on retail chargebacks and freight claims loadproof.com/features
“At the time, every warehouse facility had multiple digital cameras, taking pictures of shipments as they passed through the warehouse,” Kristi shares. “It was almost impossible to locate the right pictures in the event of a chargeback.” Kenco developed a mobile app called Loadproof (patent pending). When it came to commercialising it, Kenco made the choice to go to Smart Gladiator. “The majority of our customers are now using it, as well as other manufacturers and retail distribution centres, so it’s a real win.”
Loadproof provides proof of condition of product/shipment/ packaging through an image capture app, downloadable on any mobile smartphone. Users simply photograph shipments and instantly upload to the cloud, which can then be shared with internal leaders, external vendors, customers, and transportation partners. This solution improves retail compliance, reduces chargebacks, and improves visibility throughout the supply chain.
Kenco also recently became one of the first North American 3PL’s to partner with Phantom Auto to develop a fleet of remotely operated forklifts. Phantom’s interoperable software enables forklifts, tuggers, robots, trucks, and more to be remotely operated by trained operators sitting up to thousands of miles away. The solution helps customers increase labour accessibility, maximise workforce impact, deliver improved workplace safety, and generate greater cost savings.

LOOKING AHEAD: THE FUTURE OF SUPPLY CHAIN INNOVATION
Through dozens of various innovations, Kenco has for decades delivered cost savings to customers and helped move the needle forward in an industry that requires constant optimisation to keep up. It’s a fibre of the company’s being and mission. “We’ll always have our ears to the ground, picking up on industry trends and meeting those challenges with innovation,” Kristi says. “Our vision for what we can accomplish in the future is extremely exciting. We’ve certainly got a lot to look forward to.”