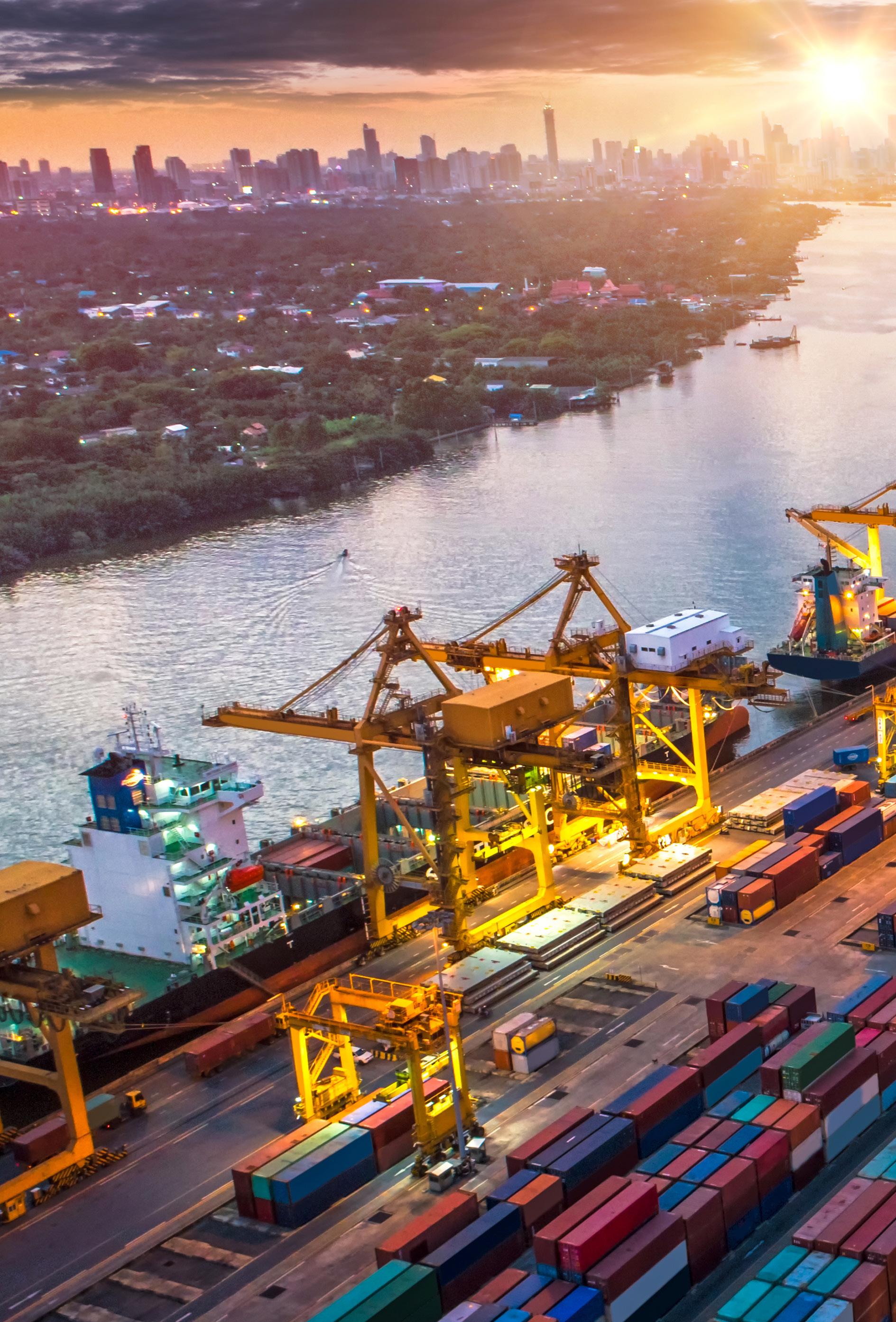
7 minute read
How can businesses best prepare for climate risk?
THE THREAT OF CLIMATE CHANGE IS EVERYWHERE – FROM FLOOD, FIRE AND WIND, TO MIGRATING LABOUR AND DEPLETED RAW MATERIALS – AND THOSE SCENARIOS STAND TO DIRECTLY AFFECT A COMPANY’S BOTTOM LINE.
ccording to recent research from the United Nations
Development Programme, productivity losses related to climate-change-related workplace disruption in the United States could rise to above $2 trillion by 2030.
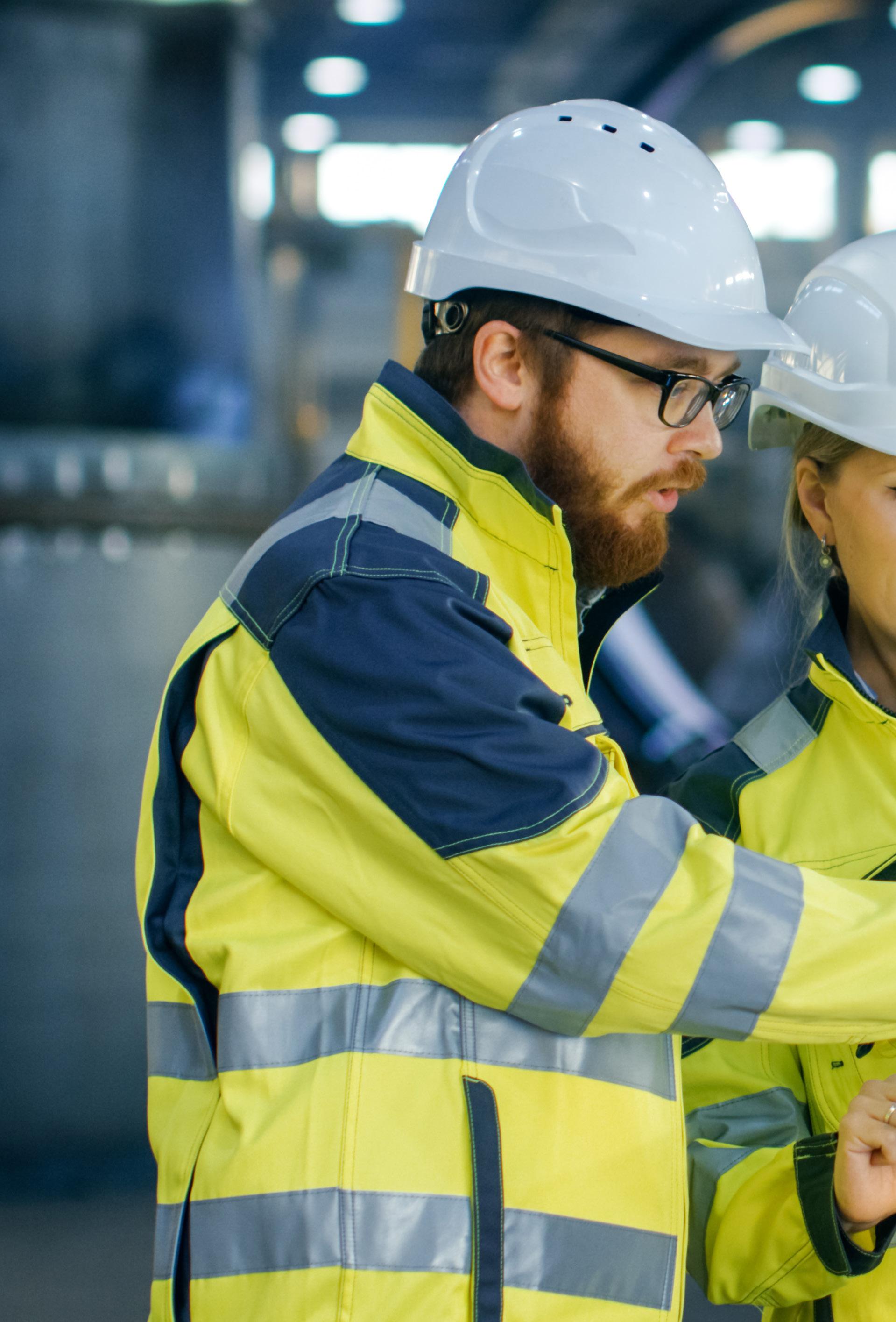
But, it’s only in the last decade that most organisations have even begun to gird against climate impacts. Christopher Knittel, a Professor of Applied Economics at MIT Sloan, said, “Companies that are going to be ahead in the game are hiring risk-management consultants that are tooled up in the impacts of climate change and can give an idea of what portions of their company are more at risk going forward.”

That strategy makes sense to Suzanne Greene, Program Manager of the Sustainable Supply Chains Initiative at the MIT Centre for Transportation and Logistics, who emphasised that it is possible for organisations to take action. She said, “Climate change doesn't just happen to you. You can actively work to fight it.”
So, how do you harden your supply chain and build resilience — the ability to bounce back from disruption — throughout your organisation? Here are five ways to brace for the storms that loom on the horizon:
ENGAGE IN DEEPER, LONG-TERM COLLABORATION WITH SUPPLIERS
A company is only as good – and as protected – as its suppliers.
According to Jason Jay, Director of the Sustainability Initiative at MIT Sloan, forwardlooking companies are already engaging suppliers around health, safety, and environmental issues. With those kinds of relationships in place, it’s not a big leap to suggest changes that improve partners’ climate resilience.


Nike, for example, has adopted a lean manufacturing approach where they say to their suppliers, “We’re going to work with you to improve the productivity of your factory,” as well as suggesting ways to improve worker health and safety, or to reduce environmental footprints. Jay explained, “They say, ‘It’s all going to be rolled into a set of things that are going to increase your output, increase your quality, increase your revenue, and make it a healthier business’.”
It’s a process that requires longer-term relationships built around trust and collaboration. Jay added, “If you want to tell a (supplier) that they need to put air conditioners on their factory roofs so that they’re more resilient to flooding, it’s going to be the same kind of thing. You have to be in a good enough collaboration with them that they’ll be willing to listen to you.”
This may mean committing to longer supply contracts, but it also means you gain influence with your suppliers. Jay noted, “This is how Toyota has always managed its supply chain. Lean manufacturing companies will

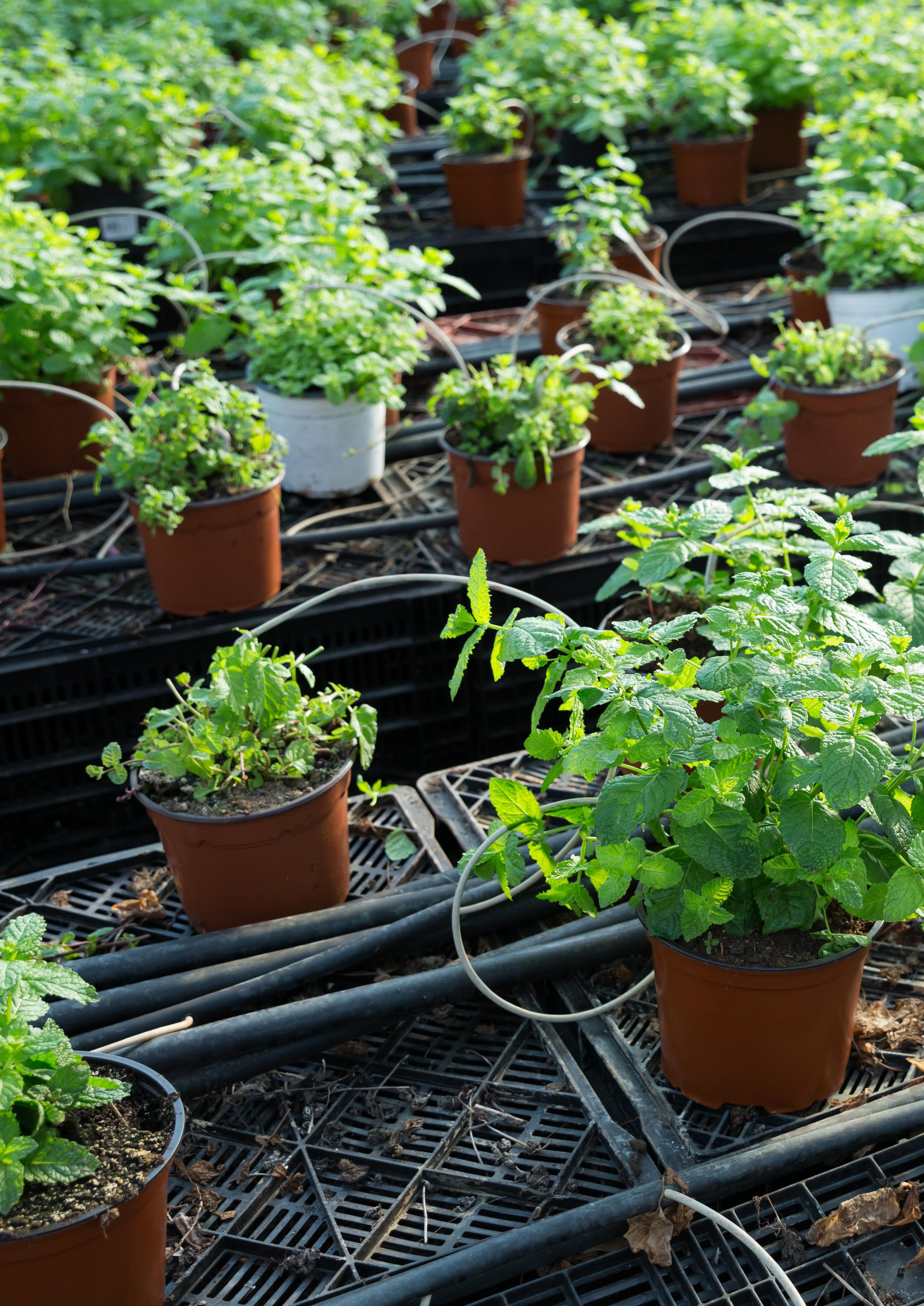
have two, maybe three, suppliers for each category of product, so that they can have those long-term, high-volume relationships.”
However, this tactic can lead to a lack of diversification among suppliers, a downside for companies that seek to protect themselves by retaining multiple connections in various geographic areas.
Jay added, “If one of your strategies for resilience is to spread your bets across different geographies so that you can easily move production from one to the other if there’s a disaster some place, it would tend to decrease the amount that you’re buying from any one organisation. This would make it harder for you to have influence over the local climate resilience of any one particular supplier.”
As such, managers may need to decide between geographical diversification – and potential redundancy – and long-term collaboration and influence.
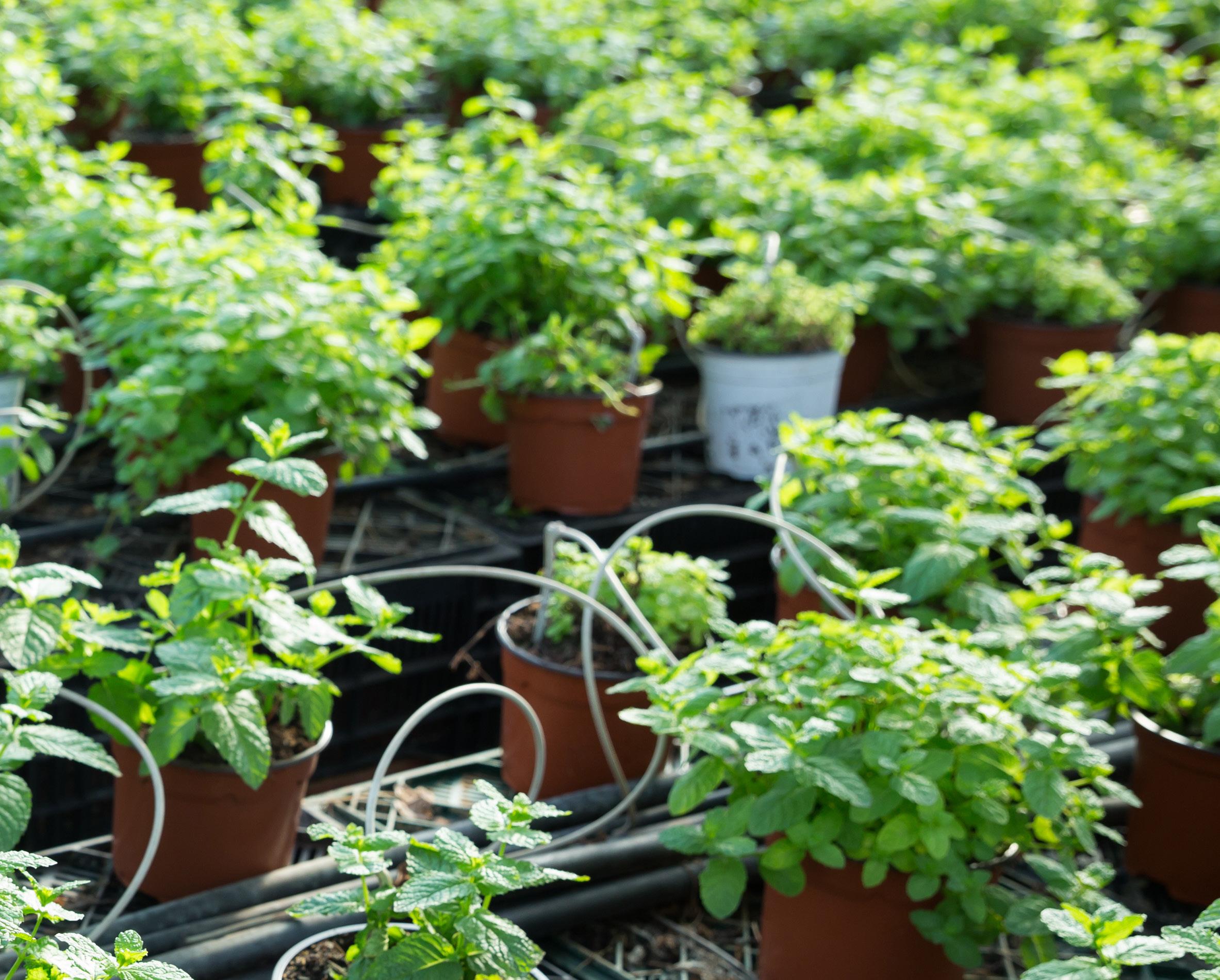

EXTEND YOUR RISK HORIZON TO ADAPT TO LONG-TERM CHANGES
In a 2016 study for ColgatePalmolive, MIT students examined the effect of climate change on the supply of mint.
Oil and compounds derived from mint are used in many of the company’s products, and it relies on its supply from India and North America.
Climate change could affect the crop’s seasons, yield, and quality, leading to supply chain and economic issues. The study urged Colgate-Palmolive to engage in risk mitigation beyond its current fiveyear horizon, moving to a 20-year plan.
Given that not every climate change incident is an extreme, sudden event such as a fire (it could be a long-term combination of droughts, pests, flooding etc), Jay said all companies should add long-term data on climate change to create more robust riskmitigation plans.
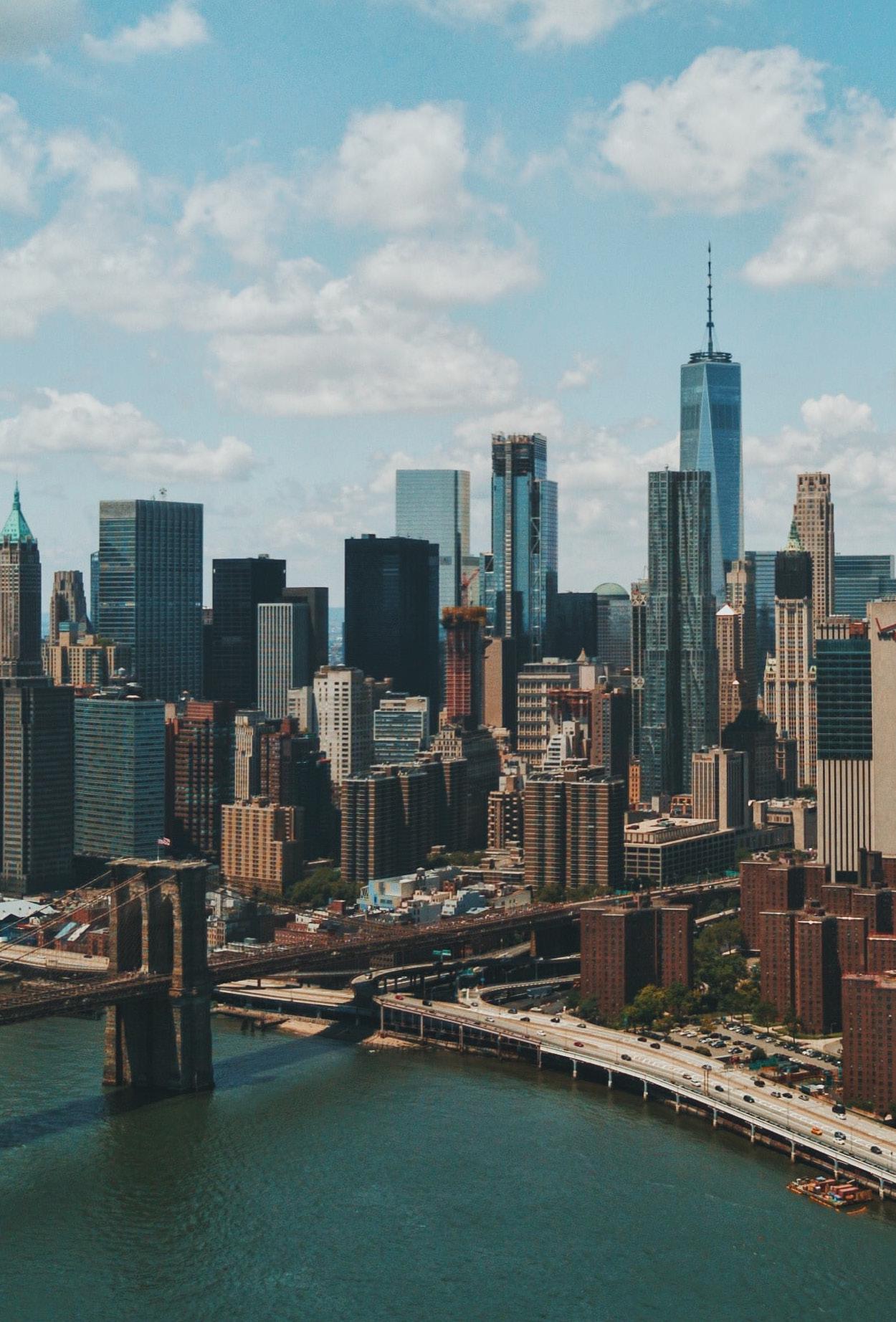
Knittel urged companies to think ahead in terms of geography, possibly retaining existing facilities but also operating other facilities in less disaster-prone areas. He said, “Companies need to take stock of the individual threats to their organisation, because it varies depending on whether there are facilities on the coast versus facilities in hurricane districts.” floods), “The issue with hardening the supply chain is that those are huge investments, such as building a sea wall, which any one organisation can’t do alone.
“A single firm isn’t going to do that, but individual companies can do things. They can raise critical assets that are near coastlines. They can move. They’re not helpless in this. I’ve talked with utilities that have physically moved substations
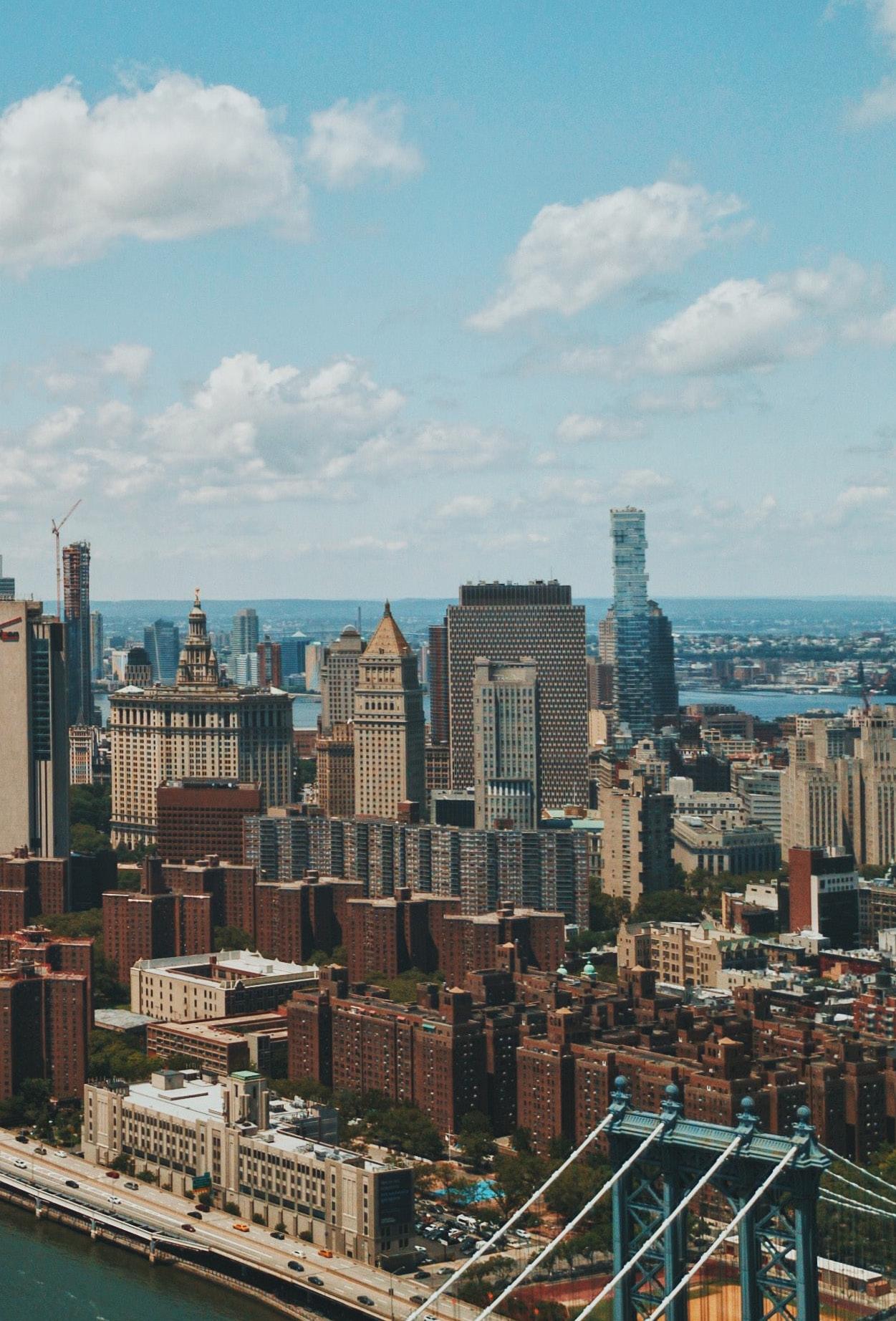
Knittel Christopher Knittel, a Professor of Applied Economics at MIT Sloan, citing New York City’s proposed $119 billion sea wall
While organisations will vary considerably in what those threats are and what they can do about them, one thing that’s clear is that supply chains in the absence of any adaptation by companies are going to be much more volatile and riskier.
So, why wouldn’t a company act? Physically shoring up existing resources is costly. Knittel explained (citing New York City’s proposed $119 billion sea wall to protect against to higher elevations or built existing substations and put them on stilts as a way to adapt to sea-level rise and storm surge.”
Proactive doesn’t mean drastic – there’s no need to shut down a fully functional facility in a precarious location. Knittel added, “But the next time you need to expand production, you build another plant somewhere else, as opposed to expanding that plant.”
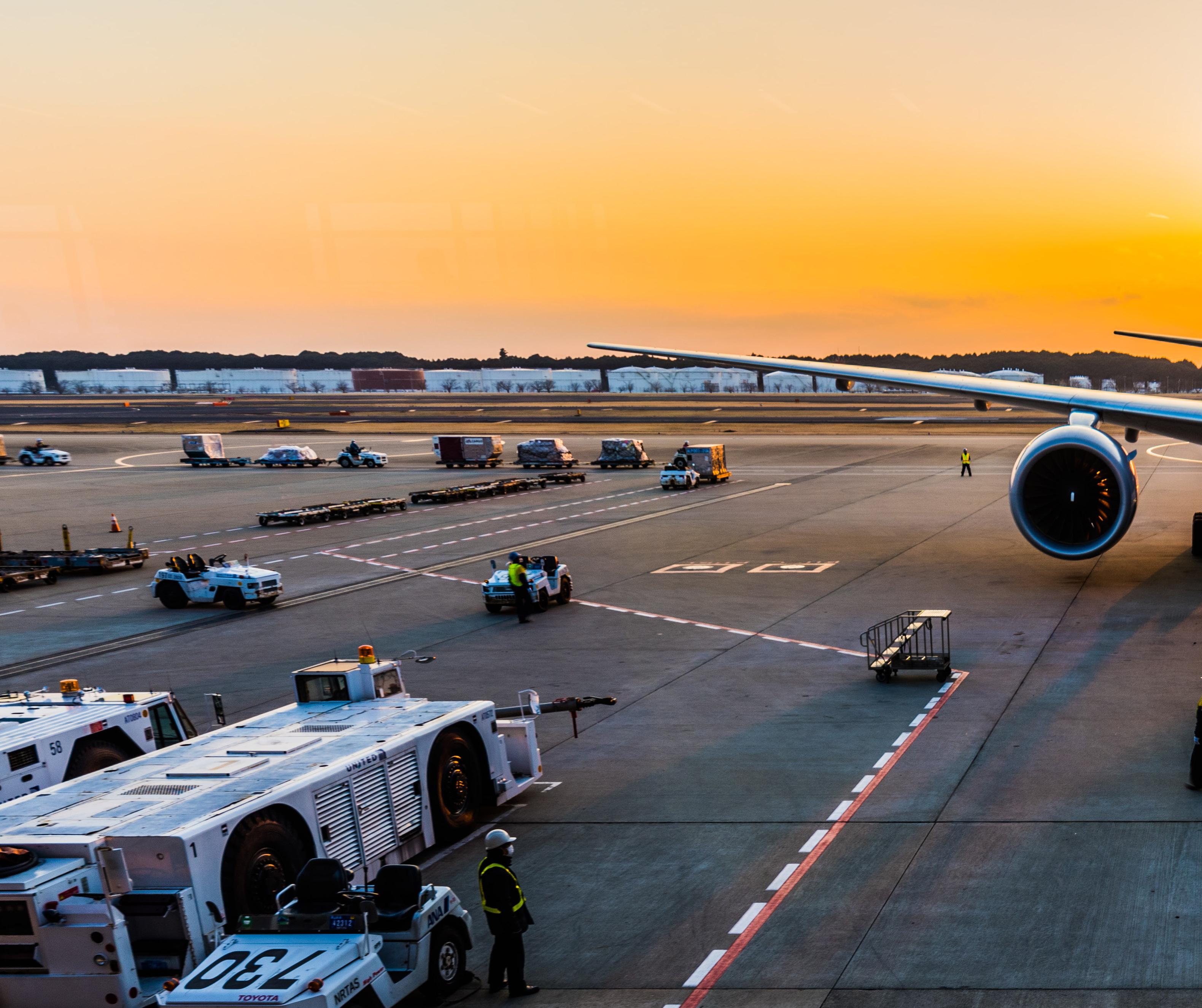
Suzanne Greene, Program Manager of the Sustainable Supply Chains Initiative at the MIT Centre for Transportation and Logistics
START LOBBYING
So what about that sea wall, bridge or fire break that could help protect a geography crucial to your supply chain? Knittel urged companies to lobby policymakers to do their part. He said, “If I were inside a company, I would create a list of what (my organisation) could do, what an industry consortia could do, and what needs to be done by policymakers. Because of the nature of climate change, because it impacts everybody, there’s always going to be some things that just should be done by policymakers.
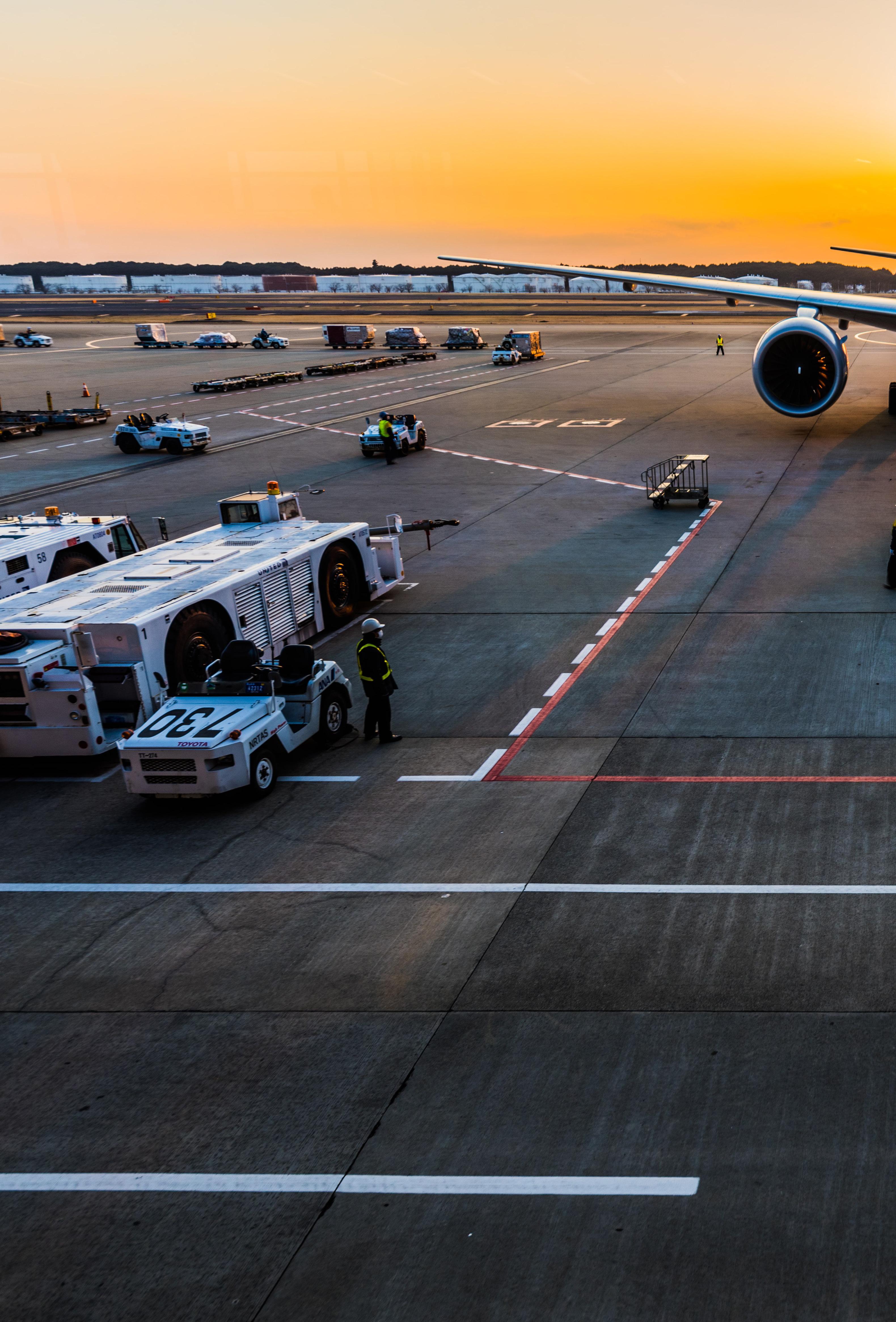
“Companies can play a critical role in lobbying policymakers to do the right thing. I would push on all three fronts, and I would be lobbying policymakers on both sides of the aisle to take climate change more seriously, because, often, it’s the duty of the policymaker to say, ‘Build that sea wall’.”
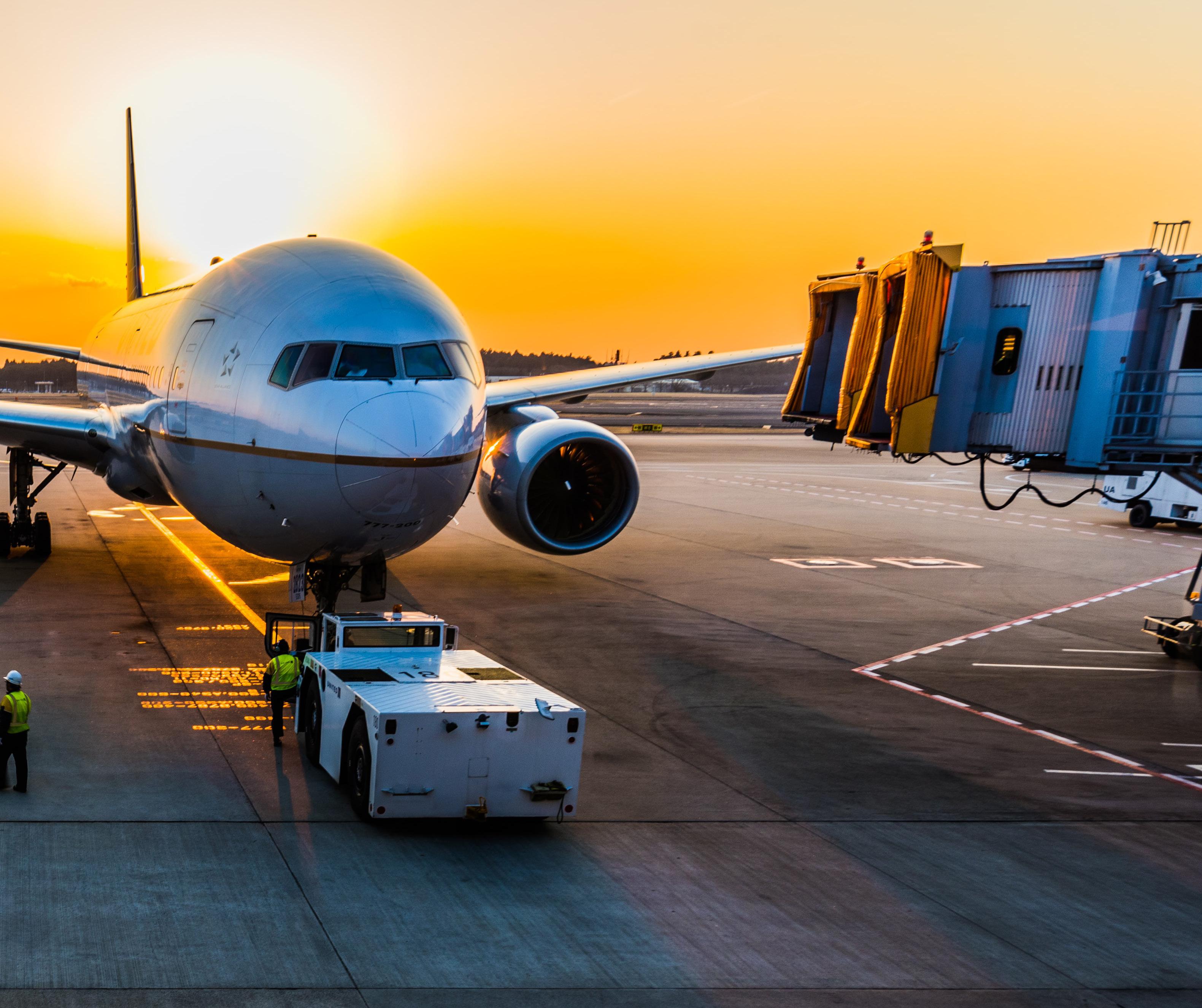
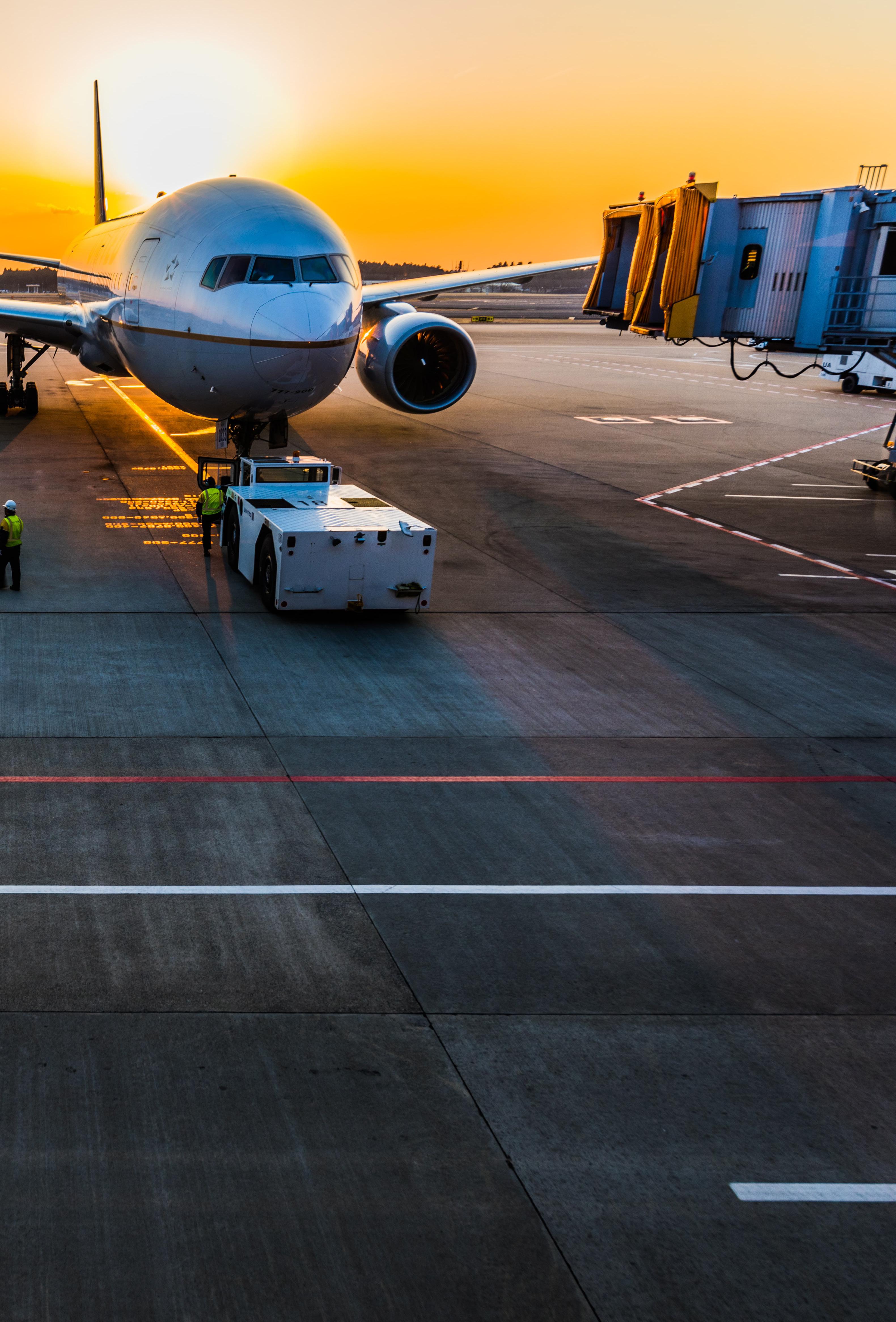
DO YOUR PART TO REDUCE EMISSIONS
While you’re analysing, relocating, and hardening your supply chain, why not decarbonise at the same time? Microsoft, for instance, recently pledged to go carbon negative by 2030. As part of this plan, the company vowed to make carbon reduction an explicit aspect of its procurement processes.
“Companies can leverage their climate goals to support decarbonisation processes throughout the supply chain. For example, a company might choose to buy low carbon steel or aluminum, and put their goods on the hydrogen ship, when these options are available. We’re seeing the action slowly come, and increasing demand for low-carbon goods will accelerate the process.”