
23 minute read
The Mold or Cast
The History of Molding and Casting
The first examples of the production of works of art from clay date back to the Neolithic period.
Advertisement
From the 9th millennium BC, and from the regions of Asia Minor and the Near East, with thediscovery of pottery firing, the first women's idols, symbols of fertility, appeared.
The first useful objects appeared much later (in the 7th millennium) in the Catal Hoyuk region (Asia Minor) and the Sahara.
Many consider Catal Hoyuk, in the Anatolia region (present-day southern Turkey), the oldest and largest Neolithic settlement.
The settlement was discovered in the 1950s and excavations were conducted by archaeologist James Mellaart from 1961 to 1965.
It is also considered the oldest city (from 8000 BC) with a significant number of emerging activities such as systematic agriculture, animal husbandry, and primitive craft production of ceramics and copper products.
Jericho is considered by others to be the oldest city in the world, with the corresponding activities of Catal Hoyuk. Excavation of Jericho was begun in 1911 by the German-Austrian expedition, continued by J. Garstang from 1930–1936, and completed by Kathleen Mary Kenyon in 1952–1956.
In the middle of the 7th millennium, we have the first evidence of gypsum use in the Ain Ghazal area of Jordan.
Ain Ghazal (east of the Jordan River, present-day Jordan) is estimated to have been founded around 7250 BC and abandoned around 5000 BC.
In1983, what are thought to be the oldest plaster statues were discovered. Gary O. Rollefson continued excavations in the 1990s. The motivation for the development of castings throughout the then known world was the cult of the dead.
In an effort to ensure their dead further survival, they resorted tovarious tricks until they reached molding. Initially, they applied light coatings to the skulls of the dead and later tried to make a funerary mask. We have very few plaster funerary portraits because of the corrosiveness of plaster. No beeswax funerary portraits exist although the Romans used beeswax widely (in funerary processions or depictions in atriums). Apparently,due to the organic nature of the wax, it was impossible to preserve over time.
The first attempts to apply coatings were made during the Neolithic period, when the first funerary portraits appeared. After the skin of the dead person had decayed, the skull was coated with a red or brown earth mortar. This symbolic make-up gave the impression of a face. From Susa we have an important find from the 2nd millennium BC.
In a tomb under the floors of the dwellings, a head of unfired clay, painted in a realistic manner, was discovered next to the covered face of the deceased.
The earliest molds were made of stone or baked clay. The use of the mold from the Bronze Age to the present day is the most important patent for the production of multiple artifacts.
Archaeology, in addition to historical research, has for years made extensive use of the mold for documentation, conservation, restoration, and reproduction purposes. In practice, it does no more than reproduce a technique of the utmost antiquity, of which it is now discovering the results. In a way, it conveys to us objects and organic bodies which, without the assistance of congruence with their form, would have disappeared for good.
Catal Hoyuk
Jericho .
Ain Ghazal
The first samples of clay art production are from the Neolithic period in the areas of Catal Hoyuk, Ain Ghazal and Jericho.
The History of Ceramics
The use of ceramic molds in pottery to produce ceramics by slab-casting clay into a ceramic mold first appeared in the Hellenistic period.
The use of plaster molds in ceramics to produce ceramic objects with slab or slip clay occurred much later (for the first time in the mid-18th century in England).
The mold, in addition to boosting the production process, also assisted the potter by finely incising designstransferred to the pottery and filling them with color.
The first imprinting materials used by humanity were clay, plaster, and wax. The first materials used to model and reproduce copies were again clay, plaster, and wax.
It is easy to see, therefore, that model-making and modeling are often combined or confused without distinguishing which came first.
Thus, for example, the relief decoration of an article of pottery requires a mold, whereas the incised decoration of a mortar requires a model.
The art of working clay, from molding to firing, is called ceramics. Ceramic products can range from simple utilitarian objects to highly aesthetic works of art. The development of ceramic technology goes hand in hand with the invention of the wheel and the development of pyrotechnology.
The development of pyrotechnology, in both ceramics and metallurgy, helped to control the temperature of the kilns and to achieve reducing or oxidizing conditions according to the needs of the ancient craftsperson.
In Mesopotamia initially and in Egypt afterward, we see the transition from open fires to kilns.
By firing the ceramics, these civilizations were able to raise temperatures to reduce porosity and to color and glaze the ceramic.
The History of Gypsum
At the same time as the discoveryof fired pottery and in the same region (Asia Minor and the Near East), the first evidence of the use of plaster appears.
The use of gypsum, with the maturation of societies and technology, passed from the Eastern Mediterranean to areas with fewer gypsum deposits.
In Gaul, despite the abundance of deposits, knowledge of its use arrived with Roman occupation.
To discover the properties of fired (baked) gypsum, all that was needed was a hearth that maintained a steady fire in a soil containing mineral gypsum.
The fire imparted the required dehydration to the mineral and all thatwas left was a rain and a tread on it.
Quickly the molded material took the form of a hard and insoluble crust.
Plaster, moreover, having the advantage of whiteness over clay, was also used as a decorative coating in relief. Evidence of this use appears on the plastered walls and raised reliefs in the sanctuary of the temple of Catal Hoyuk.
The region of Jericho was called, in the 7th millennium BC, "the people in the plaster ground."
At Jericho, during an excavation in 1953 by Kathleen Kenyon, a piece of a human skull appeared in the walls of a trench.
The face was coated in plaster, with much realism and with the eyes molded in color.
The first evidence (around 6500 BC) of the use of plaster is found in the sculptures discovered in the Ain Ghazal area of Jordan.
Subsequent excavations (1983) brought to light a total of seven specimens which were dated to around 6500 BC.
These seven heads should be regarded as the first true funerary portraits. The most important achievement of the period was the use of plasteras an imprinting material.
It gave a more realistic rendering of the funerary portraits, differentiating them from the usual funerary masks.
The most important evidence of the event was also located in the same place.
The next find came from Susa and was much younger (2nd millennium BC). It is an independent portrait found in a tomb resting next to the deceased.
Hedi Slim, excavation director at El Jem, Tunisia, found the workshop of a 3rd century AD cast craftsman. In it he found a sufficient number of molds—casts of human faces and animals.
The History of Synthetic Resins
The history of elastomeric resins begins with the arrival of the Spanish conquistadors in America. The Mayans and Aztecs in Southand Central America drilled rubber trees to obtain an emulsion from which they separated the rubber by heatcrystallization. The rubber emulsion (latex) is produced by etching the bark of the tropical tree Hevea brasiliensis.
Similarly, from Southeast Asia (Malaysia) and from the sap of the tree of the Palaquium family, we obtain a type of latex, gutta-percha. The molding of gutta-percha, after its introduction in 1840, was done in molds (like thermoplastics in our time). Gutta-percha as an impression material, in the form of black or brown plates heated in water (50–70 °C), was used by dentists. The collection of latex has been carried out since ancient times by the natives of Central and South America.
Pre-Columbian cultures, unaware of sulfurization (vulcanization), developed organic methods with similar results.
They mixed raw latex with various vine juices, particularly Ipomoea alba.
Rubber balls have been found,especially in areas that were flooded by water.
The Aztecs used these as toys. According to Bernal Diaz del Castillo, the Spanish conquerors were surprised by the bouncing of the rubber balls.
Additionally, the Mayas made a kind of rubber shoe by dipping their feet in a latex mixture.
The indigenous peoples of Brazil were familiar with the use of latex to make waterproof clothing. It is said that the first European to import samples of Brazilian raincoats into Portugal was taken to court on charges of witchcraft. The use of rubber was nonexistent in Europe until 1751, when the French Academy of Sciences' research was published. In 1770, J. Priestey used rubber as a gum rubber (rubber = eraser). The word rubber was coined as the English term for natural and synthetic elastomers.
Latex has been used to produce molds since World War II. Synthetic resins first appeared around 1840 with the conversion of natural products into synthetic resins. An example is the vulcanization of caoutchouc and its conversion into rubber (caoutchouc + sulfur = rubber). In 1838, Christian Friedrich Schonbein produced the first semisynthetic material,nitrocellulose, by applying sulfuric acid to paper (cellulose). In 1839, Charles Goodyear invented vulcanization. In 1843, Thomas Hancock developed the vulcanization process and produced the first solid wheeled tires. In 1888, Dunlop invented the pneumatic tire. In 1862 the first artificial plastic was created by Alexander Parkes (parkesine) by treating cellulose with nitric acid and a solvent, nitrocellulose.
Then, in 1869, John Wesley Hyatt plasticized nitrocellulose by dissolving camphor in alcohol to produce celluloid (billiard balls, piano keys, etc.). In 1887, Hannibal Goodwin filed a patent application for celluloid in the form of a flexible film. Goodwin, who was not a chemist, as a clergyman wanted a way to project slides of Bible stories in his Sunday school classes.
Kodak founder George Eastman filed a patent application in April 1889, also for celluloid. In 1914, after 27 years of litigation, his heirs were successful in obtaining justice and were compensated by Kodak with $5,000,000.
In 1872, Adolf von Baeyer observed that the condensation of phenol and formaldehyde produced a hard resinous material.
This observation was exploited by the Belgian-Canadian chemist Leo Baekeland in 1907, producing the first fully synthetic resin, phenolic resin (Bakelite).
The invention of Bakelite marked the beginning of the plastics era, and Baekeland is considered the father of the plastics industry. Bakelite had excellent electrical insulation and thermal resistance.
Its best-known derivatives were the electrical switches, telephone sets, and radios of the time.
In 1912, Fritz Klatte discovered polyvinyl acetate, which as an emulsion was used as an adhesive in wood, paper, textiles, etc.
One male and one female were found, of particular interest. Themale cast had faithfully reproduced every detail of the face of the deceased (up to behind the ears). It is obvious that the face had been smeared with oil to perfectly capture the beard, moustache, hair and closed eyes due to the deceased's condition and to prevent the fluid plaster from sticking. The other is a female cast whose death mask has not been found. The retouching she has received, the open eyes, and the arranged hair leave room to think that she was ready to receive wax and go for casting. In any case, finds of mortuary portraits in plaster are few, and there are none made of wax (because of its perishability). The ancient Egyptians, as early as the 3rd millennium, knew the process of burning gypsum in open furnaces and pulverizing it. They then mixed it with water and used it as a binding material in the joints of the boulders of their monuments.
Theophrastus (372–287 BC) in his On Stones precisely describes the preparation of gypsum as it was done in his time in the region of Syria and Phoenicia. According to Pliny, Lysistratus was the first to think of pouring wax into the mold (a technique that led to the casting of bronze by the "indirect method of lost wax"). In doing so, he was the first to impose the process of producing brass or bronze sculpture as we know it today: template, mold, wax, bronze.
Our knowledge of antiquity issupplemented by written evidence from Theophrastus and Pliny (23 AD–79 BC). They give us a very clear picture of how, with the assistance of a modelmold, we passed from funerary portraits to sculptures with the molding of the dead and the reproduction of thefunerary mask. From Pliny we have also learned how, in the 4th century BC, the sculptorLysistratus of Sicyon (brother of the more famous sculptor Lysippus) used plaster for direct casting from a human face to achieve greater realism. He was also the first to move from idealized sculpture to realistic portrait.
It is very likely that the use of plaster casts, despite Pliny's evidence, had begun much earlier than the 4th century BC. In Amarna, Egypt, plaster casts were found dating to about a thousand years earlier.
The History of Copper
The use of metals has been integral to the development of humancivilization.
Humanity's first contact with metals dates back to the Stone Age (between the 9th and 7thmillennia). These metals are indigenous, i.e., often found freely on Earth's surface. The real age of metals, however, began when humans succeeded in extracting metals from their ores, melting them, and casting them into molds.
It is no accident, therefore, that their names are used to describe the epochs that followed the Neolithic period. The Bronze Age was from 5000 to 3000 BC, the Craton Age from 3000 to 1000 BC, and the Iron Age from 1000 BC to the present. According to the Roman historian Pliny the Elder, the origin of the word metal is due to the coexistence of similar minerals in gold or silver deposits: The Greek μετ’ άλλων, or met allon, means "with other." The seven known metals ofantiquity are gold (6000 BC), copper (5000BC), silver (4000 BC), lead (3500 BC), tin (1750 BC), iron (1500 BC), and mercury (750 BC). With the exception of lead and tin, they were found in their native state (they exist in nature inan elemental state as minerals). The excellent mechanical properties of these metals helped in the manufacture of tools, hooves, utensils,jewelry, and works of art. The ancients also found that copper could be shaped by forging. They then heated the copper (annealing) to make it even more malleable while giving it an extra hardness, properties important for the manufacture of early tools and weapons. Copper, a highly plastic metal, could even be cold-forged to a satisfactory hardness.
The discovery of copper alloys further improved the properties of the individual elements.
For example, the fusion of tin with copper gave an alloy that had superior properties to copper or tin in both forming and casting. By the time they reached the high levels of the classical period, the craftspeople of the time, over the course of 4000 years, had managed to solve a number of problems related to the discovery of mines, mining, ore dressing, and smelting.
A prerequisite for the development of metallurgy was the development of pyrotechnology, which was facilitated by knowledge of handling fire for use with ceramics.
Already since the Stone Age, humans had been using open and later closed kilns to fire ceramics.
Since the 7th millennium BC andthe first finds in Asia Minor, knowledge of metal processing has been constantly evolving and expanding.
It extends from the Babylonians, Egyptians, Greeks, Romans, Arabs, and European alchemists to the present day.
From the 4th millennium BC onward, the metallurgical knowledge of copper, which began in what is now Iran, spread westward.
In the 3rd millennium, it reached the Aegean Sea, Britain in the 2nd millennium BC, and then eastward via India to China in the 2nd millennium BC.
Prehistoric copper ore mines and processing centers in the Near and Middle East have been identified at Kozlu in Asia Minor, and at Cyprus, Palestine and Timna in the Sinai Peninsula.
Zinc is also found in copper ores. The copper ores of Cyprus and Ireland contain significant zinc.
In the Balkans we have coper in Aibunar and Burgas in Bulgaria and in Rudna Glava in Yugoslavia.
An important mine, especially for the Romans, was that of Rio Tinto in Spain.
From the point of view of ancientwriters, there are no reports of copper mining in Greece, but there are reports, such as those of Herodotus, about the gold and silver mines of Thassos and Skyros and the silver mines of Lavrio. Archaeological research into the mining technology of the ancients has identified and highlighted the way the galleries were opened and the excavation tools that were used (printing presses, axes, etc.).
The dimensions of the galleries were very limited, with steps and slots to facilitate the movement of workers and cavities in the walls for the placement of lamps.
To this day, impressions of the chisels can still be seen on the walls. Obviously, the mines contained more metals than the ancient miners knew or cared about.
In the middle of the 4th millennium, the use of copper in the form of an alloy began. The metals used to alloy copper were arsenic, tin, and zinc.
The reason is to improve the mechanical strength of the metal. The first alloys contained arsenic (1%–5%) and were widespread in Syria, northwest Iran, Cyclades, and Crete.
Arsenic was used mainly in the 3rd millennium BC and was abandoned in the 2nd millennium, when the easily mined arsenic-rich copper deposits began to run out.
Arsenic is commonly found in arsenic -rich copper ores as enargite ortennadite.
According to the relevant literature, most scholars accept that an arsenic concentration of up to 2% is probably due to the use of arsenic-containing ores. Above 2% should be considered intentionalcontamination.
In contrast to arsenic, the use of tin to produce alloys wasintentional since no tin-doped copper ore is found in nature.
The presence of tin in copper alloys, in a proportion of 8%, like arsenic, gives equivalent properties in terms of both hardness and cold- and hotworking. Arsenic content of about 8% gives the alloy maximum workability, which the ancient craftsperson seems to have known very well.
In this proportion, the alloy shows very good ductility and easy shaping by either cold- or hot-forging.
From the beginning of the 2nd millennium, the use of tin in the production of alloys gradually began to prevail.
The reasons for abandonment of arsenic are possibly the transition of mining from arsenic-bearing to nonarsenic-bearing ore deposits and the difficulty of controlling the proportion of arsenic in the alloy due to its volatility and toxicity.
While arsenic-rich copper ores and native arsenic are quite common geologically, cassiterite (tin oxide) is a particularly rare metal.
The world's tin mining areas are few and well known: China, Nigeria, Cornwall, Saxony-Bohemia, and especially Malaysia.
The oldest bronze finds date back to around 3500 BC and come from Thailand (Bann Chiang) in the East and Near East (Tepe Giyan and Navahand of Western Iran).
In the same period, we have finds in the wider Aegean region in parts of present-day Bulgaria(Chernykh).
If, for Thailand or China, the problem of finding tin was solved due to the existence of deposits in their region, for the Near Eastern regions, Egypt and the Eastern Mediterranean, it remains unknown where they obtained tin from.
For the Aegean region, from the Mycenaean period onward, we have the first indications of contacts be- tween Cornwall and Greece. Herodotus refers to the Cassiterides ("Tin Islands").
Although the production of brass objects dates back to the beginning of the first millennium in the Asia Minor region, in Greece it appears from the Roman period onwards. There are references from the 7th century BC by the Greeks to brass not for its use but as an exotic product not produced in Greece. From the 1st century BC onwards, brass was produced, first for coins and then for every object that had previously been made with bronze. The zinc content of the alloys of the period was 10-30% in zinc. Finally, from the 3rd century AD a new copper alloy containing lead, zinc and tin appeared. An alloy that has been widely used ever since. It is still in use today, called red brass, and its proportions are: 85% copper, 5% tin, 5% zinc and 5% lead. Lead was also used in ancient times as a deliberate addition to castings to improve the cast ability of the alloy. The absence of lead in wrought objects indicates that the ancient craftsman knew that even its minimal presence made forging difficult. Since the Archaic period the development of casting technology has been continuous and uninterrupted. Since the 3rd century BC we have the addition of a larger quantity of Pb lead to the statues; Pb significantly improved the ductility of the alloy. From the Hellenistic period and especially after the Roman conquest of the country, the use of brass prevails. The copper-zinc alloy (brass) originated in the region of Lydia (Asia Minor) shortly before 600 BC. The casting techniques during that period, according to the earliest studies of German archaeologists and in particular Kurt Kluge, archaeologist, sculptor and foundry man, the ancient Greeks began casting (6th early 5th century BC) by imprinting their models (made of carved wood) in sand molds. They then moved on to the lost wax technique, first direct (5th-4th century BC) and later indirect (late 4th-2nd century BC). This view was based on the evolutionary theory of the arts of the period. This theory was based on the logic of the continuity of technical progress. According to this theory, sculpture began with the carving of wood before moving on to stone and ending with metal. Correspondingly, metal casting therefore began with sand and ended with lost wax.
Kluge (published 1927-29), in his attempt to substantiate his theory, based it on the well-known sculpture of Heneochos at Delphi (6th century BC) as the most convincing example of a work made by the method of casting in sand. Very quickly, research proved that the only technique used by the ancients was that of the lost wax.
As early as 1955 it was proven that the Heneochos of Delphi was cast using the lost-wax method. The predominant method of the two of lost wax, as both archaeological research and modern technology show, was the direct method until the Hellenistic period. From the 8th century BC there is already evidence of the use of the indirect method for small objects, such as handles, supports and decorations on boilers, tripods, etc. Pliny refers to Roikos from Samos who was an architect and a bronze maker (7th century BC), his son Tilekles and his grandson Theodore. According to Pausanias, Roikos invented the digestion and casting of copper in molds. In this century the artist Glaucus invented the welding of iron. Roikos was also a pioneer in the art of bronze sculpture in Greece The bronze statue of the Night, which stood in the temple of Artemis in Ephesus, was his work. Theodore was also a great architect, sculptor, bronze maker and seal maker.
The sculptors Roikos and Theodoros, from Samos, made statues of bronze that were hollow inside.
Together with his grandson Theodore, they brought about many innovations in the arts, such as the discovery of a new method of casting copper, known as the "lost wax" technique. They were the first to apply bronze casting and the first to use the stationary gnomon, lathe and screw in sculpture and are said to be the first makers of scaling keys. From the middle of the 4th century BC, as can be seen both from finds and from information from ancient writers, the indirect method began to spread. From 410, when Rome was conquered by the Barbarians, Europe went through a period of war and uncertainty. Mines are abandoned, metallurgical know-how is lost, and trade in metallurgy ceases. We have the Dark Ages.
Metallurgy resurfaces in Europe after Charlemagne is crowned Emperor of the Romans in 800.
To ensure that the empire's coinage needs were met, Charlemagne used Saxon captives to mine silver from the old mines of central Europe (Erzgebirge or Mineral Mountains on the Czech-German border), a source of copper, silver, lead, and zinc. With the discovery in 938 of the Rammelsberg mines in Germany came the first major source of silver, lead, and copper. This discovery caused miners to frantically search for new deposits (similar to later U.S. prospectors) and gave the opportunity to regain knowledge lost during the Dark Ages.
By the Renaissance, mining had made little progress since Roman times. Workers were still digging galleries supported by wooden beams and hauling up minerals with hand winches.
From the Renaissance onward, the old methods became inadequate, so miners imported techniques from the Chinese and Mauritanians.
Thus they used water mills to grind minerals, pump water from the galleries, move the bellows for the casting, and heat furnaces for the metals being forged. As far as artistic bronzing is concerned, after the decline of the western Roman Empire, Byzantium continued the tradition of bronze casting until the fall of Constantinople to the Turks.
Thus, from the Crusades onward, Byzantine craftsmen began to transfer their knowledge to Italy. With the fall of Constantinople, their flight to the West was completed. The provision of knowledge mainly concerned the artistic aspect of bronze casting since the Westerners' expertise in casting bells and cannons was more advanced.
Andrea Pisano (1290–1348) in 1330 undertook the construction of the south gate of the Florence Baptistery. This work was the first to be cast exclusively by Italian craftsmen (installed in 1336). Pisano also contributed to the liberation of modern art from Byzantine influence. His successors in the new flowering of bronze sculpture in the West and its reconnection with antiquity were Michelozzo di Bartolommeo, or Michelozzo Michelozzi (1396–1472), Florentine architect and sculptor of the early Renaissance(Brunelleschi's contemporary); Lorenzo Ghiberti (1386–1455); and Donatello (1386–1466). The information we have from that period is due to V. Biringuccio and G. Agricola.
Vanoccio Biringuccio (1480–1539) was an Italian metallurgist born in Siena. In his career, he was in charge of an iron mine near Siena. He also led a cannon foundry in Venice and later in Florence. He is remembered for his book De la Pirottechnia on the treatment of metals. He is considered the father of metal casting technology. Biringuccio was a member of the order Fraternita di Santa Barbara, and the information he gives in his book on metallurgy and military arts was held in complete secrecy. The printing of De la Pirottechnia preceded Agricola Georgius’s publication of De Re Metallica by 14 years. It marks the beginning of the tradition of scientific and technical bibliography. As one of the first technical manuscripts to survive from the Renaissance, it is a valuable source of information on technical practice at the time of writing. It is structured as 10 books dealing with metals, minerals, alloys, the art of brass casting, and so on. It describes in detail how to make molds for casting and gives details about methods of mining and the use of explosives. Agricola Georgius (Georg Bauer, 1494–1555), a German born in Glaushau, Saxony, became known as the father of mineralogy with the publication of De Re Metallica. He studied medical physics and chemistry while working mainly in mineralogy and secondarily in mathematics, history, and theology. In 1530, when he was appointed as a historian by the prince of Saxony, he moved to Chemnitz, the center of the mining industry, where he also worked as a doctor.
He was a prolific writer. His greatest book, De Re Metallica, was published a year after his death (1556) although it had been finished in 1550. It is presumed that the delay was due to his rich iconography (woodcuts took time).
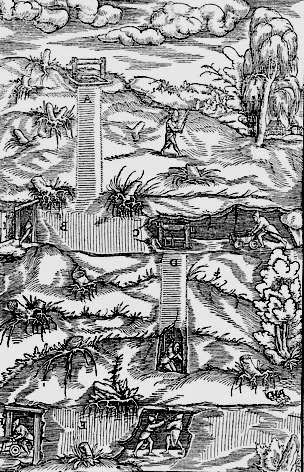
Agricola Georgius (Georg Bauer, 1494–1555), his book “De Re Metallica”.
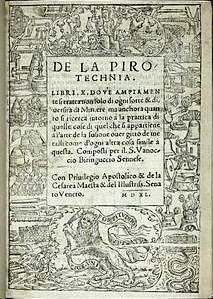
Vanoccio Biringuccio (1480 - 1539) his book 'de la Pirottechnia' on the working of metals.