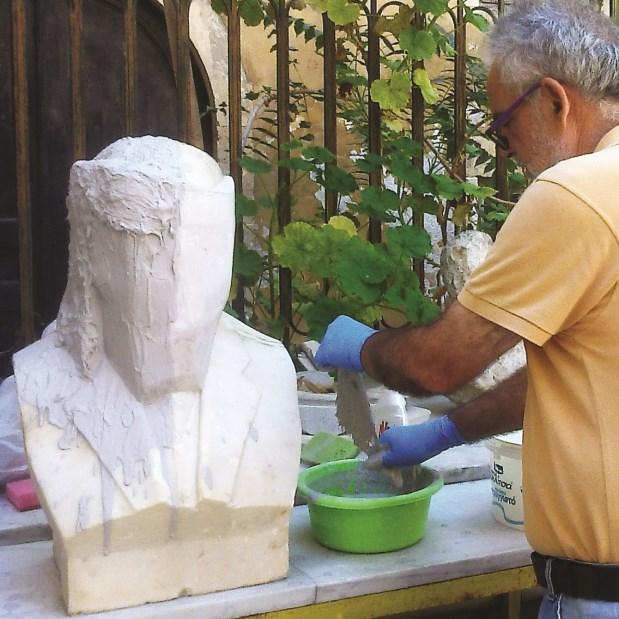
7 minute read
Mold or Matrix or Form or Negative
In 1926, Waldo Semon developed a method for laminating PVC (polyvinyl chloride, now used in sewer pipes, gutters and roofing sheets). From 1928 onward, the technology of synthetics developed rapidly, largely to meet the needs of the coming World War II.
The first synthetic rubbers were introduced (with a polymerization of acetylene-chlorine in 1932 and butadi-styrene shortly afterward) and replaced natural rubber after 1940, when the Japanese occupied the Asian rubber tree plantations. In 1931, industrial production of polystyrene began at the IG-Farben plant in Ludwigshafen am Rhein. Its use as a foam plastic (Styrofoam) was developed in 1949 by Fritz Stastny and his boss Rudolf Gäth at BASF (patented in 1950). In the United States, it was developed as Styrofoam by Ray McIntire at the Dow Chemical Company (patent 1944). Polystyrene (polyphenylethene) is an aromatic hydrocarbon produced from the styrene monomer. It is solid at room temperature but melts when heated and becomes solid again when cooled.
Advertisement
It was accidentally discovered in 1839 by Eduard Simon, who noticed that the resin of the Styrax tree, which he called styrene, polymerized after a few days into a gel form which he called styroloxyd (styrene oxide). The Styrax tree (also called Astyrax, Astrakia, or Wild Cypress) grows in temperate regions (Greece, Asia Minor, and Lebanon). In 1941, researchers at the Dow Chemical Company produced polystyrene foam using Carl Georg Munters's invention. It is used to produce materials such as expanded polystyrene (EPS) and extruded polystyrene (XPS) for insulation, packaging materials and many other applications. (It is known in as Styrofoam®) In 1933, Carlton Ellis invented polyester resins (unsaturated synthetic resins). Acrylic glass (Plexiglas, methyl polymethacrylate) was developed in 1928 in various laboratories by several chemists, including William Chalmers, Otto Röhm, and Walter Bauer.
It was first brought to market in 1933 by the Rohm and Haas Company under the brand name Plexiglas (as well as under the trade names Lucite and Perspex) as a durable substitute for glass. Polyethylene was accidentally manufactured in 1898 by Hans von Pechmann while he was studying diazomethane.
Polypropylene was invented in 1951 when J. P.Hogan and R.L. Banks polymerized propylene. In 1954, Giulio Natta discovered the isotactic polypropylene, which had great commercial application. Teflon was discovered in 1930 by DuPont and has been on the market since 1949.
Polylactic acid is a biodegradable thermoplastic aliphatic polyester made from renewable sources such as corn starch (in the United States), tapioca,or starch (in Asia), or sugarcane (rest of the world). It is one of the materials used in 3D printing. In 1937, Otto Bayer and his colleagues discovered polyurethanes, which were polymerized by polycondensation and had some advantages over existing plastics. They became commerciallyprevalent in 1952, and in 1954 the production of polyurethane foam began. In 1939, Dr. Pierre Castan discovered epoxy resins. The basic raw material for producing epoxy resin is oil.
In 1942, Harry Wesley Coover discovered cyanoacrylates, the application of which he completed in 1951. The best-known trade names for cyanoacrylate adhesives are Loctite, Eastman and Permabond.
F. S. Kipping was a pioneer in the study of organic compounds in silicones. He coined the term silicone in 1901. From 1890 to 1940, he published 51 papers on the subject. In about 1930, J. F. Hyd began to study the chemistry of siliconestructure and compounds. In 1943, Dow Corning began researching and manufacturing organosilicone compounds. In 1946, they begin to gain industrial and commercial value.
The same year, General Electric began producing silicone polymers, and in 1956 Union Carbide began also. In 1953, within a week of each other, Daniel Fox and Hermann Schnell invented polycarbonates. These substances are known by the trade name Lexan and used to manufacture CDs and DVDs.
The Mold or Cast
Terminology
Mold, cast, form, or matrix: the negative imprint of the form of a solid body, produced mainly for the manufacture of faithful likenesses of it.
A structure intended for casting a fluid material which, when set, will take its shape and then be removed.
Synonyms of cast are printing, impression and negative or positive (as a clarification). Negative (cast): the malleable mass upon which a form can be imprinted.
Positive (mold): the most common reference to the faithful likeness of a solid body which has been made by injecting soft matter (which then solidifies) into the cavity of another negative likeness.
Pattern or model: that which serves as an example for reproduction, for making copies of any person or object, used as a specimen to create something new (posed as a model to painters.
Object and Molding Materials
Any three dimensional object can be reproduced through molding.
For artists the cast is the means of producing a work of art, and for conservators it is the means of restoring a work of art, while for decorators it is the means of producing threedimensional decorative elements, and, finally, for technicians and engineers it is used to produce parts, tools, and devices and for many other applications.
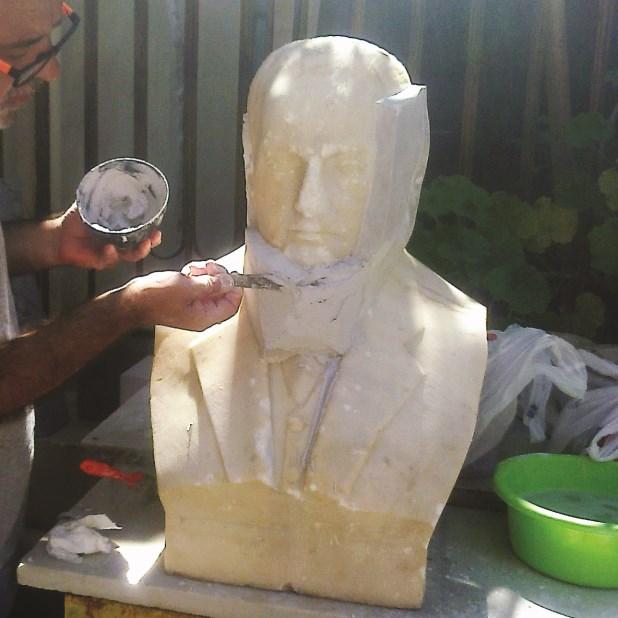
1 2
Marble sculpture molding (fig. 1, 2).
3 4
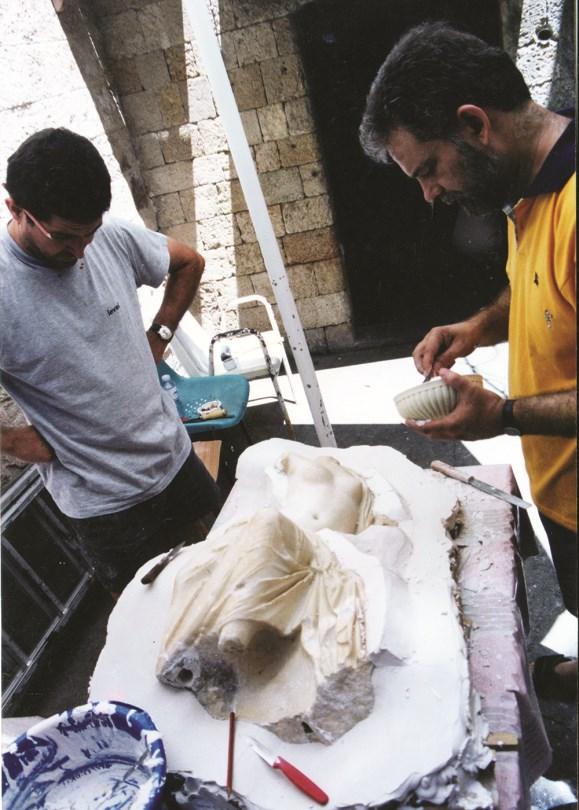
Extraction from ancient artwork (fig. 3-4) for reproduction of copies.
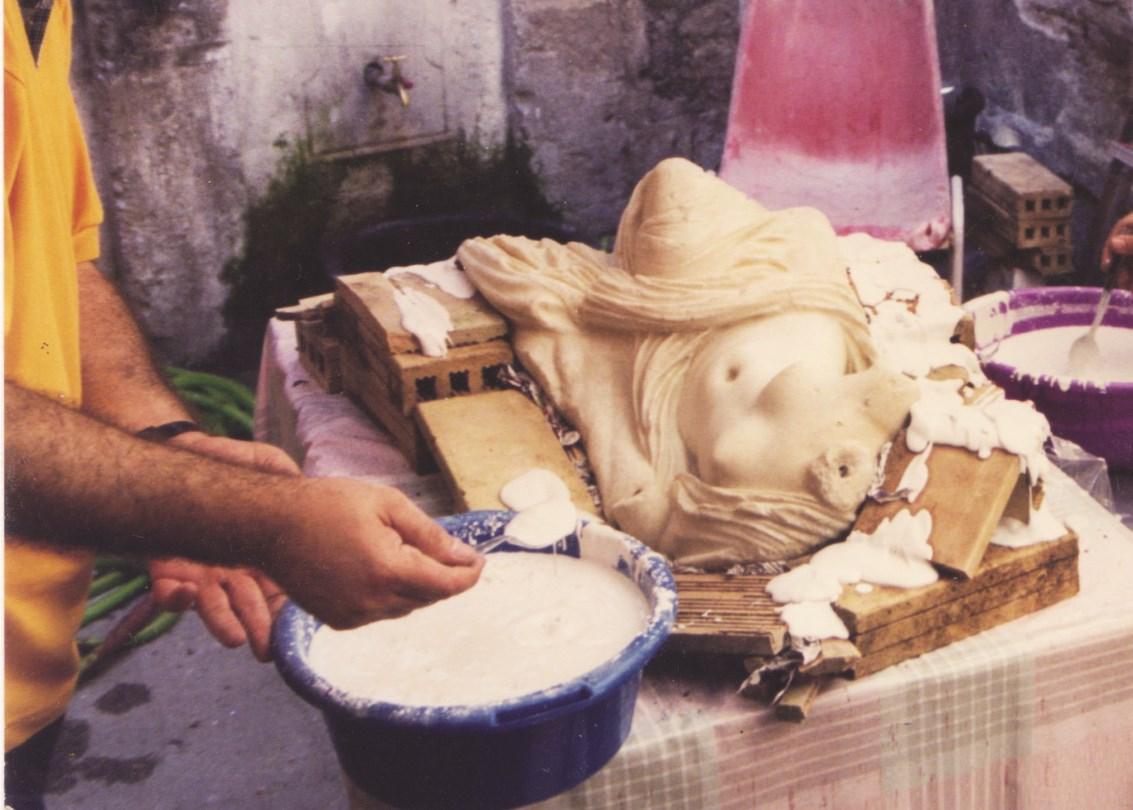
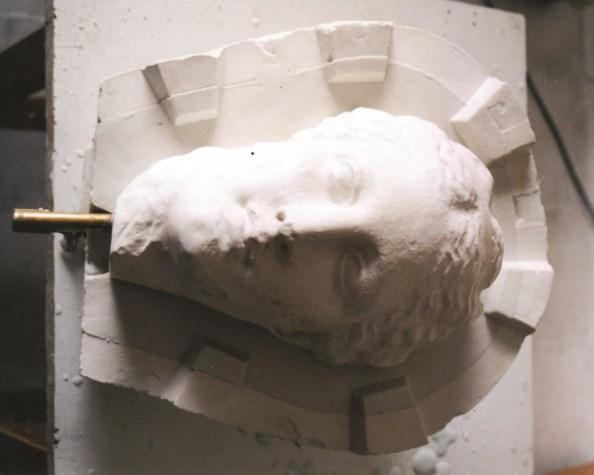
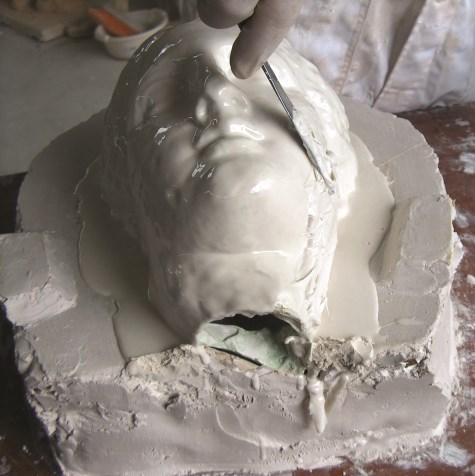
5 6 7
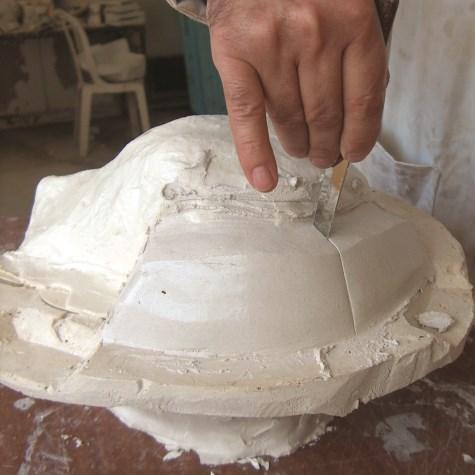
Casting with elastomeric silicone and plaster from a plaster model (plaster replica of an ancient one; figs. 5–7).
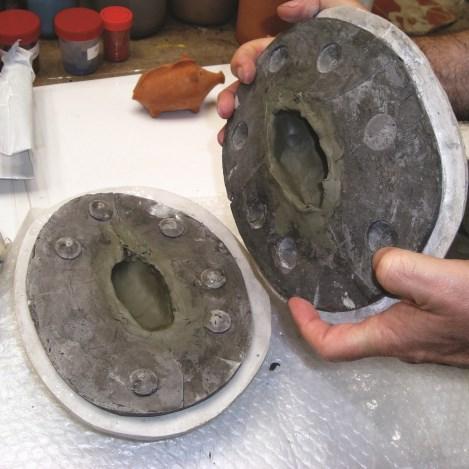
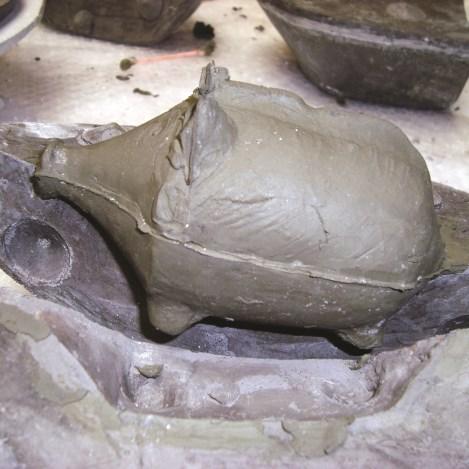
8 9 10
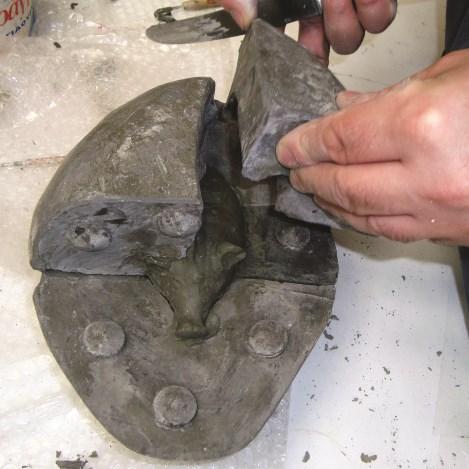

Clay molding of a plaster mold for the reproduction of a ceramic replica (figs. 8–11).
13 11
12
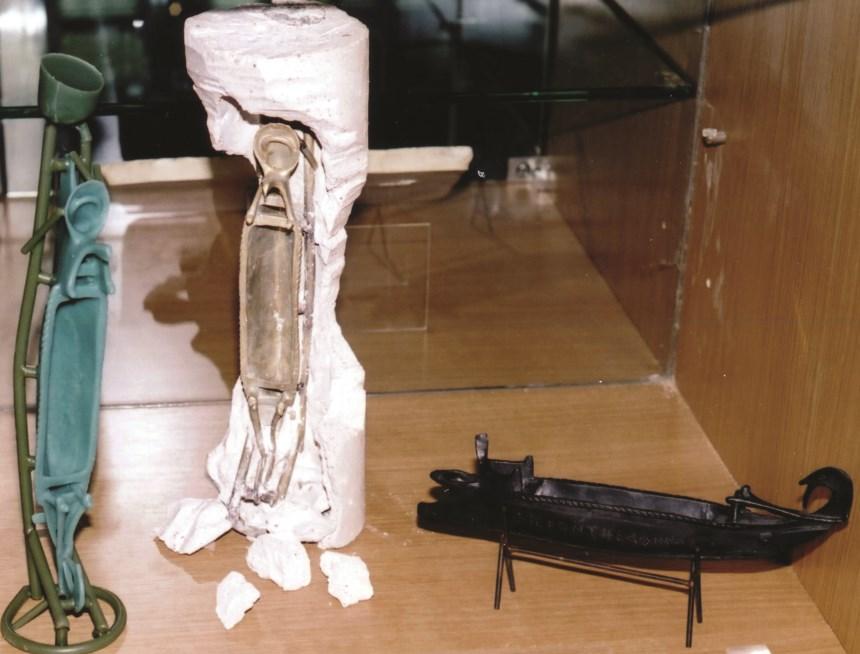
14 α β γ
16
Mold (ceramic shell or investment) for casting brass sculpture (fig. 12). The wax cast (fig. 13a) the ceramic shell (investment), half-opened after casting the metal (fig. 13b ) and the final casting product (fig. 13c).
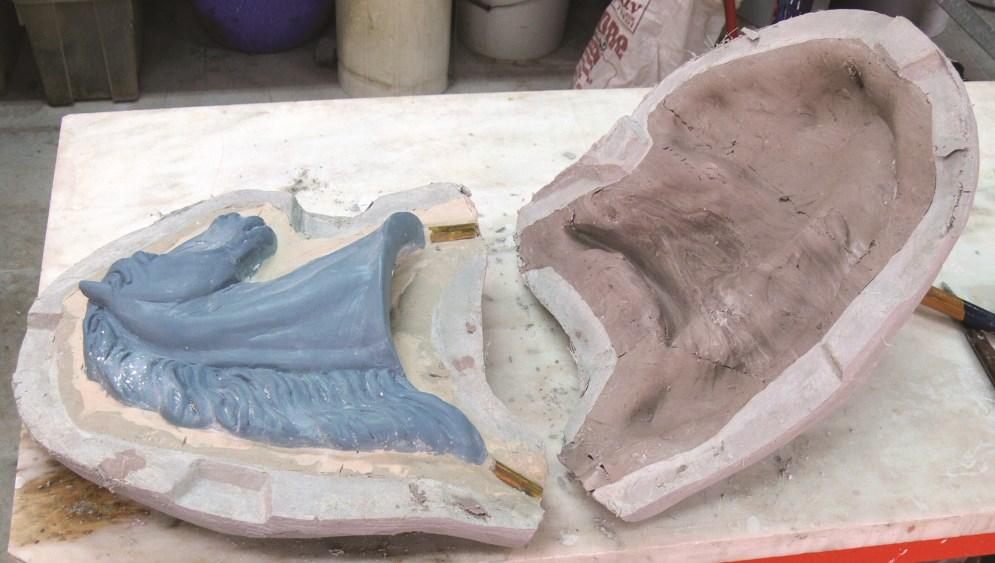
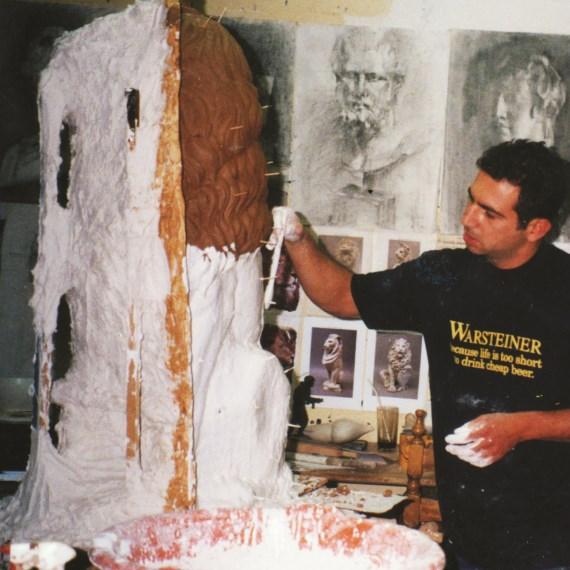
15
Free model construction with clay and its molding with plaster. We consider free model-making to be that which is done on the basis of the image in the artist's mind and not on the basis of what they see in a posed model (figs. 14–15). The model can be made of any material (plaster, Styrofoam, wax, stone, wood, metal, etc.). Fig. 16 shows a hard-material model.
The Prototype or Model as an Object of Molding
The molding processes, media and materials relevant to artists, art conservators, modelers and decorators are the subject matter of this textbook. The process of molding starts with the model and ends with its reproduction in the same or another material. The sculptor has naturally, the comfort and ability, to start from the construction of the model and through molding, to reach the completion of the work, with whatever material he has predetermined. Let's not forget that even carving in marble, passes indirectly through molding, when it is based on a plaster model (preform product). The model is made from either something we see or something we imagine. In either case the preform will act as the model on which the impression or molding, or casting, will be made. The template is in a sense a molding, a combination of mental and manual work.
The sculptor casts the model by eye and impresses it by hand on the model.
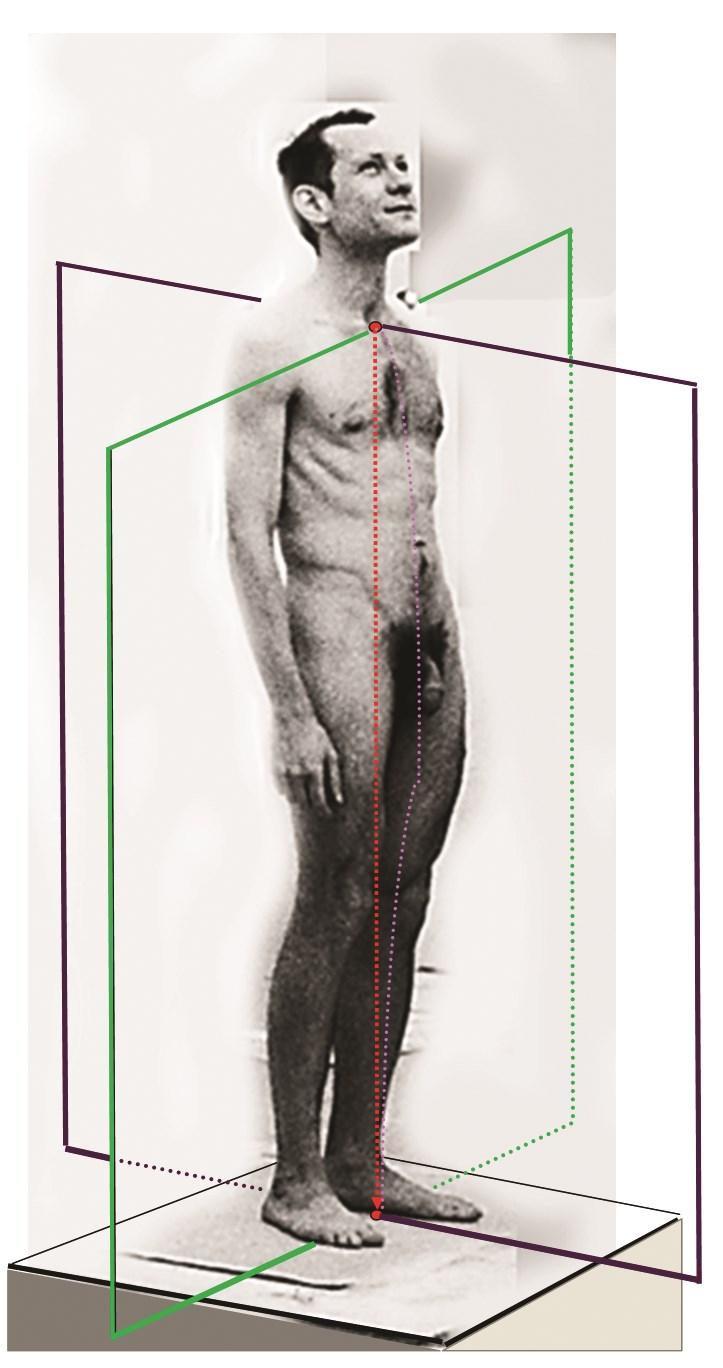
Jugular notch
The central point around which all other points are mentioned
The measurable sizes of the space are occupied by a geometric shape.
In this sense, there is the dimension of length, which is the distance from point to point; of width, which is a perpendicular distance to length (thus giving the concept of a plane); and of height, which is the perpendicular distance to a plane and is identified as the third dimension of solids and space.
From this it follows that space has three dimensions: length, width and height. We use these dimensions to move from the model to the template.