The Eggshell Project Un
proyecto de huevo
Description: Professional project from MANUFACTURA
Authors: Dinorah Schulte (Co-Founder / Project Director), Edurne Morales (Co-Fundador / Computational Designer)
Material Research: Montserrat Ayala
Location: Mexico City, Mexico
Institution: MANUFACTURA
Date: 2023
Collaboration: Maria Pia Assaf (Guest Designer), Santiago Rangel, Aleida Merkel y Natalia Juan
Material Donators: Rosetta Panaderia, Restaurant Rosetta Rancho Rio Blanco, LARDO, BOU
THE EGGSHELL PROJECT / UN PROYECTO DE HUEVO is a research project that seeks to take advantage of and transform our waste to turn it into a buildable material and open up a new possibility to create our living in an environmentally responsible way. In this project we create a bioceramic made from eggshell and combine it with sustainable aggregates, resulting in a new materiality, which seeks to reduce food waste and generate new opportunities.We decided to reevaluate the potentials of ceramics, keeping the connection between materiality and nature, extensive access to raw materials, geometrical freedom and strength. But reducing some of the harmful traits by using a locally sourced largely found lightweight waste product: egg, together with biobinders that allow the mix to solidify without the need of firing.
Our process is based on 3D printing with a KUKA KR-150 robotic arm, an extruder and additive fabrication process, which allows us to shape our blocks with different geometries and project them into different architectural applications. allows efficient use of material (less waste), geometrical freedom, precision and repeatability, project them into different architectural applications.
EGGSHELL bricks
Credits: Arturo Arrieta
EGGSHELL bricks Credits: Arturo Arriet
Assembly Process / EGGSHELL bricks
Credits: Arturo Arrieta
A third of the production of food intended for human consumption is lost or wasted worldwide, which is equivalent to approximately 1,300 million tons per year. An estimated 17% of all food available to consumers in 2019 ended up in landfills at households, retailers, restaurants and other food services, according to new UN research conducted as part of global efforts to reduce waste. of food in half by 2030. The weight is equivalent to approximately 23 million fully loaded 40-ton trucks, enough to circle the Earth seven times (Food and Agriculture Organization of the United Nations, 2019)
Mexico is a hungry country that wastes tons of food. Total waste in Mexico, a country with 53.4 million people in poverty, reaches 20.4 million tons per year (37.98 percent of what is produced in the country) (Do you know how many tons of food Mexico throws away? El Universal, 2018). Mexico is also considered the main consumer of fresh eggs worldwide; the per capita consumption of the Mexican is 28.0 kg per year, considered the fourth largest producer of eggs worldwide and is responsible for 1/27 eggs produced in the world (Sader)
We tend to think of ceramics as an environmentally friendly industry, and a beloved hobby for many of us. But, is this claim real? Robert Harrison in his book Sustainable Ceramics mentions: “Ceramics with all its necessities for manufacturing, materials, firing, fuels and workspace is certainly not a clean/ green environment.”. Gas emissions, waste management, transportation and energy consumption are just a few of the characteristics that turn this process into one that can negatively impact our environment. We decided to reevaluate the potentials of ceramics, keeping the connection between materiality and nature, extensive access to raw materials, geometrical freedom and strength. But reducing some of the harmful traits by using a locally sourced extensively found lightweight waste product: egg, together with bio-binders that allow the mix to solidify without the need of firing and an additive fabrication process based on 3D printing with a robotic arm. Our process allows less waste production, geometrical freedom, precision and repeatability.
3D Printing Process
Credits: Dinorah Martínez Schulte
In this research, we have developed two applications: a wall (Eggshell Bricks, presented in the INÉDITO collection by Design Week Mexico 2022) made up of a total of 105 different blocks that are assembled based on their geometry, and a column (Eggshell Column, presented in the DISEÑO EMERGENTE collection by ZONA MACO 2023) made up of 26 pieces that embrace each other and create stability through their shape. Each brick is made in a 100% sustainable and circular way, as the raw material was obtained through the collection and donation of waste from several restaurants in Mexico City such as Rosetta, Rosetta Panadería, LARDO, and Rancho Rio Blanco, from over 2 months of their production.
From a cultural perspective, this project frames a new material that does not exist in the current market, which generates added value as a construction material, as it cannot be found or produced in any other way. Technology allows us to innovate current construction markets, which has a great economic and cultural impact on society because it opens up new possibilities for construction and materiality in our habitat, generating a circular system from where it is obtained to its use, by giving new life to our waste.
This project was achieved thanks to the combination of computational design and the opportunities given by digital manufacturing, technology, and material innovation to transform our waste and create awareness, questioning our manufacturing methods and creating centuries of circular life, generating new job opportunities from recycling, sanitizing, to their robotic 3D printing fabrication and placement on site, requiring new talents to produce this material and product in series and opening new opportunities in the construction of future architectural spaces, creating a new dialogue between machines and human beings.
EGGSHELL Column Credits: Enrique Aguilar
EGGSHELL Column Credits: Enrique Aguilar
The development of manufacturing strategies based on the material behavior allows an integration early logics of manufacture in the design process and an exploration of new structural typologies.
Enrique Aguilar
Sueños con Earth/Concrete Sueños con Tierra/Concreto
Description: Professional Project from MANUFACTURA
Authors: Digital Structures MIT
Director: Caitlin Mueller, Project Team: Edu Gascón, Mohamed Ismail, Sandy Curth, Kiley Feickert, Tim Cousin, Leslie Norford
MANUFACTURA
Dinorah Schulte (Co-Founder / Project Director), Edurne Morales (Co-Fundador / Computational Designer.
Material Research: ANFORA Studio
Location: Mexico City, Mexico
Institution: MANUFACTURA
Date: 2023
Collaboration: Digital Structures MIT, NEW STORY, ECHALE
Exposition: Festival de Arquitectura Mexicana MEXTROPOLI 2022
sueños (in English, dreams): dreams (of the past or future); a cherished aspiration, ambition, or ideal.
A participatory, architectural installation featured in the Mextrópoli Architecture and City Festival (September 21-25, 2022), Sueños con Fiber/Timber, Earth/Concrete unfolds stories about Mexico City through four materials, their provenance, and their promise for the future. Through its critical adaptation of traditional papercraft, creative reuse of recycled wood, and innovative use of earth and concrete, this siteresponsive installation invites us to recognize the palimpsest of Mexico City’s histories and imagine new possibilities.
Sueños with Earth / Concrete
Credits: Dinorah Schulte
Final Protoype Credits: Arturo Arrieta
Assembly Process
Credits: Dinorah Martínez Schulte
Sueños con Earth/Concrete explores the future of affordable housing in Mexico by minimizing the material impact of existing construction methods. This pavilion has been developed in partnership with New Story, an international non-profit organization that pioneers solutions to end global homelessness, and Échale, a social enterprise based in Mexico that offers housing solutions through the integral development of communities.
The horizontal roof structure takes the existing vigueta y bovedilla system as a starting point, optimizing the shape of the precast reinforced concrete beams to minimize the use of material and its associated environmental impact by 50% compared to conventional systems.
This elegant geometry, sculpted by varying width and depth along the beam’s span, is enabled by recent computational design methods developed in MIT research. 3D-printed clay blocks vault between beams as lost formwork that enables the casting of a topping slab manufactured by MANUFACTURA and ANFORA Studio.The use of tepetate, a local soil with high contents of clay, allows for fabricating compressed, sundried blocks that constitute the pavilion walls.
This affordable, low-carbon solution, which has been successfully applied in the construction of housing communities around Mexico for more than 30 years, is reinterpreted here with a post-tensioning system that allows for assembly and disassembly.
Final Protoype Credits: Walter Shintani
3D Printing Process
Credits: Dinorah Martínez Schulte
Final Protoype
Credits: Walter Shintani
Diagrams and drawings
Credits: Digital Structures MIT
Final Protoype
Credits: Dinorah Schulte
3D Printed Bovedillas / Beams
Credits: Dinorah Schulte
Sueños con Earth/Concrete lies at the intersection of local construction techniques and new digital fabrication technologies, resulting in a collaboration between industry, social enterprise, and academia as a model toward a more sustainable built environment.
The Talavera Project
Un proyecto de talavera
Description: Professional project from MANUFACTURA
Authors:
MANUFACTURA + Uriarte Talavera
Dinorah Schulte (Guest Artist /Co-Founder/ Project Management) / MANUFACTURA
Edurne Morales (Co-Fundador / Computational Designer) / MANUFACTURA
Mariana Muñoz (Partner and CEO / Uriarte Talavera
Arturo Rojas (Production Management) / Uriarte Talavera
Katia Ramirez (Production Management) / Uriarte Talavera
Material Research: Uriarte Talavera
Location: Puebla, México
Institution: MANUFACTURA
Date: 2023
Collaboration: Jared Zarate, Erick Marin
Exposition: PATIO Efimero 2023
THE TALAVERA PROJECT / UN PROYECTO DE TALAVERA, is a research initiative executed by MANUFACTURA in collaboration with Uriarte Talavera, a workshop established in 1824 and recognised as the first producer of talavera in Mexico and to obtain certification according to the Official Mexican Standard, which grants it the Denomination of Origin (DO 4-1). Located in a historic mansion in the heart of the historic centre of the city of Puebla, this workshop fully preserves the process of elaboration of the stanniferous earthenware, introduced in the 16th century in New Spain. As of 2019, this process is part of the Intangible Cultural Heritage of Humanity.
The fundamental purpose of this project lies in making visible the synergy between tradition and innovation, creating a new dialogue between handmade craftsmanship, intrinsic to the country’s cultural heritage, and technological and industrial innovation, represented by digital fabrication: robotic 3D printing. The aim is to forge a conscious evolution that preserves our roots and fosters identity. Throughout the fabrication, the primary role of water is highlighted as a central element in our palette of materials. The project illustrates how water is intertwined with the creation of the signature cobalt blue colour palette. This iconic shade arises from a mineral amalgam of aluminates and cobalt silicates, encapsulating the essence of Talavera.
Final Protoype Credits: Dinorah Schulte
Final Protoype
Credits: Dinorah Schulte
A study by the Midwest Economic Policy Institute predicts that by 2057, robots could replace more than 2.7 million construction jobs, as automation seeks to reduce reliance on human labour by becoming more efficient and outperforming human capabilities (Beatty & Baldwin, 2022; Colomina & Wigley, 2016). Robotic automation is changing the shape and pace of work, offering a new labour supply, and this transition to greater automation has been compared to Frederick Taylor’s vision of replacing craft workers with intellectual engineers. This raises the question of whether we are damaging our human condition by being replaced by robots (Carpo, 2023)
Hannah Arendt, in her book: “The Human Condition”, warns that automation could free us from work, but at the same time threatens to strip us of a fundamental part of the human condition by eliminating labour activity, which could be detrimental (Arendt, 1998). Moreover, regardless of automation, changes in syntax, tectonics and production are already altering the way we create our built environment (Carpo, 2023).
Craft production is based on manual or simple tool manufacturing, without using industrial technologies, which limits customisation and mass production. On the other hand, digital manufacturing combines the customisation of craftsmanship with the cost efficiency of mechanical production, thanks to modern digital technologies. This makes it possible to mass-produce varied products without additional costs, which was previously complicated (Carpo, 2023). Cultural heritage must be continuously reviewed and updated to maintain its relevance in society, promoting peace, social development and community cohesion. This implies relating collective memories of the past and traditional practices to current issues and their significance in the future (Intangible Cultural Heritage, n.d.)
Talavera process waste Credits: Dinorah Schulte
Redesigning the way of making between tradition with innovation, through humanizing automation and robotics fostering economic equity.
In Mexico, artisans occupy population is 12.6M. Their working conditions are limited: having an average salary of 6.09k per month, where 30.1% are women and 69% are men. They are disappearing due to multiple causes: globalization, mass production, climate change, demanding learning, lack of economic support and not transferring innovation. s (Trabajadores Artesanales: Salarios, Diversidad, Industrias E Informalidad Laboral | Data México, n. d.)
Digital fabrication combines the customization of craftsmanship with the cost efficiency of mechanical production, thanks to modern digital technologies. This makes it possible to mass-produce products without additional costs, enriching tradition that not only preserves our cultural identity, fostering new opportunities in the conscious preservation and sustainabilty. The fundamental purpose is to make visible the synergy between tradition and innovation, to create a new sustainable way of making. They have the same technological impact and are not replaced, rather, they dialogue with each other to allow more sustainable manufacturing, where heritage and customs shouldn’t be erased by machines.
This intervention comprises two elements addressing the mentioned issues: an 80-piece column replicated from a mold created through Robotic 3D printing and the second element is a carpet made from the production waste, prompting a reconsideration of recycling strategies to transform it into a higher-quality, ecologically valuable product.
Mexico’s greatest wealth lies in its cultural heritage. We envision echoing this initiative with all indigenous, protected materials and vulnerable artisans societies, reshaping production lines for efficiency, thwarting extinction, fostering employment, and revitalizing the economy for Mexican artisans. Our ambition is to forge a novel economic paradigm, seamlessly blending 3D printing technology and innovation with the artistry of hands, elevating production efficiency, understanding their processes while safeguarding age-old skills. Together, we forge a path toward a vibrant and sustainable tomorrow.
3D Printing Process
Credits: Dinorah Schulte
3D Printing Process
Credits: Dinorah Schulte
The process of this project consisted of the following stages of elaboration:
Stage 01
3D Printing process with local clay.
3D Printign process with a KUKA KR-150 robotic arm in a time of 10:00 min.
03
Creation of plaster moulds
Handmade by a certificate and local craftsman from a 3D Printed piece.
05
oven: Jahuete or sancocho
at low temperature (850ºc). Both words are used to denote that the piece is cooked, biscuit or partially cooked.
07
The paint is obtained from natural minerals, handmade with mule hair brushes.
Smooth Finish
The process of making smooth finish handmade ceramics by hand.
The piece is moulded by hand with clay from the region of Amozoc and white clay from Valsequillo.
Enamelling and glazing
The entire surface of the piece is raised by immersion to apply the paint. The enamel gives the traditional shine and colour of the authentic Puebla Talavera.
Production of the piece with clay Second kiln session and final finish
the pieces are introduced to a burner (1050ºc) so that the enamels and paints react together and we obtain the piece with its final finish.
Stage
Stage
Stage
Stage 02
Stage 04
Stage 08
Stage 06
Cobalt blue paint
First
“Technology should not replace human contact; there can be no community without physical proximity”. - Mario Carpo .
Final Protoype Credits: Dinorah Schulte
The Wood Project Un proyecto de madera
Description: Professional project from MANUFACTURA
Authors:
Dinorah Schulte (Co-Founder / Co-Project Director) / MANUFACTURA) Rodrigo Escobedo (Co-Founder / Co-Project Director) / La Metropolitana
Edurne Morales (Co-Founder / Computational Designer) / MANUFACTURA
Fabricio Vazquez (Colaborator) / La Metropolitana Brando Marín (Colaborator) / La Metropolitana.
Material Research: Montserrat Ayala + La Metropolitana
Location: Mexico City, México
Institution: MANUFACTURA
Date: 2023
Collaboration: Santiago Rangel, Jared Zarate
Material Donators: La Metropolitana
In Mexico, approximately 102,895 tons of trash are generated daily, from which 83.93% get recollected, 83.93% are taken to final disposal sites, and only 9.63% gets recycled, according to Mexico’s Environment and Natural Resources Department.
Annually the volume of timber production in Mexico reaches approximately 9 million cubic metres. From which 70% gets destined to the sawmill industry, and 45 to 65% of this volume becomes sawdust, shavings and bark, becoming waste elements of little or no economic value. (Fragoso-Madueno 2)
THE WOOD PROJECT / UN PROYECTO DE MADERA is a research initiative in collaboration with La Metropolitana, a conscious furniture manufacturing and design workshop with more than 15 years of experience in the search for the link between nature and human beings through creativity and design. The workshop combines traditional woodworking techniques with cutting-edge technology in its furniture manufacturing processes, managing to increase efficiency and offer high-quality and competitive proposals.
Final Protoype
Credits: Enrique Aguilar
The project focuses on using the wood and the development of multiple transformation techniques based on the natural processes of the material. Responding to the current problem faced by the workshop, the daily production of up to 5-6 bags of sawdust of different species, equivalent to approximately 40 kg per bag per day. The overarching goal is the meticulous construction of 3D printed structures, seamlessly manufactured through the precision of a robotic arm, starting a process of circular economy and decarbonization.
During this development a bio-composite has been generated mainly conformed by sawdust. The selected tree species is the Tzalam tree (Lysiloma latisiliquum), native to the southeast of Mexico and highly prized in the Mayan region due to its appearance and high hardness. The wood itself is distinguished by its sober presence, pronounced grains and an attractive reddish colour that adapts to various design styles. The matrix of the composite is based on organic binders and lime to avoid humidity and fungal development.
Several mixing experiments informed of the changes in physical state and binding behaviour during drying, which depended in great measure on the machine used to generate the sawdust, as it modifies the sizing of the particles. After a prototyping process, it was determined that the sawdust coming from the calibrating machines and the CNC router presented the most optimal physical conditions to allow the 3D printing process.
Final Protoype Credits: Sebastian Decasa
Our setup is based on an extruder for semi-liquid materials mounted on a KUKA KR-150 industrial robotic arm. The 3D printing process is based on following a trajectory that allows specific laying of the material coming from the extruder. This process allows the generation of diverse, precise, and intricate geometries based on digitally adjusted parameters, providing an efficient use of material, waste reduction, geometrical freedom, precision and repeatability, opening new possibilities for the design and architecture fields.
The demonstrator for the material developed was based on 3 partition walls of architectonic scale composed of 72 pieces of 20 x 20 cm fabricated during a lapse of 3 weeks between printing and drying. The pieces are easily replicable and assemblable among them, allowing to increase the scale of the elements easily. These bricks are produced sustainably and in a circular manner, utilising raw materials sourced from waste at La Metropolitana and processed to attain their finest sizing.
Most of the sawdust is rich in cellulose, hemicellulose, lignine and other substances of low molecular weight, characteristics usually wanted in the industrial applications. Additionally, the resulting components exhibit remarkable lightness, with each brick weighing an average of 207 grams, leading to a total weight of 15 kg for the entire structure.
The use of these materials and processes opens new possibilities for our current sustainability, culture and economies. The project proposes an innovative focus for the production through circular systems. This strategy covers various stages starting from the extraction of raw materials of recycled origin coming from collaborations with multiple industries, followed by the generation of new materials based on natural additives with biodegradability potential, and the subsequent utilisation of a method based on contemporary technology that optimises the quantity of material and precision granting a new life to the residues and establishing a new circular durability that transcends generations.
Final Protoype Credits: Walter Shintani
With this ongoing research we seek to promote environmental awareness, job generation and efficient use of resources, contributing to a more sustainable and conscious future.
Final Protoype
Credits: Enrique Aguilar
POROUS ASSEMBLIES
Robotic 3D printing of mineral foam for novel lightweight architectures
Description: Individual Thesis
Tutor: Patrick Bedarf
Location: Zurich, Switzerland
Institution: ETH Zurich + Digital Building Technologies
Date: 2020
Collaboration: Ayca Senol (D-MATL ETHZ), Dr. Michele Zanini and Dr. Etienne Jeoffroy (FenX AG)
This project presents the design and fabrication of a lightweight composite facade shading panel using 3D printing (3DP) of mineral foams.
Despite their important role in industrial construction practice as insulating and lightweight materials, few studies have been conducted on the use of foams in 3DP. However, the recent development of highly porous mineral foams that are very suitable for extrusion printing opens a new chapter for the development of lightweight, geometrically complex and novel building components with efficient additive digital manufacturing processes without formwork.
The work documented in this project was based on preliminary material and manufacturing development from a larger research effort, and systematically explored designs for small interlocking foam modules.
Details / Final Prototype Credis: Dinorah Schulte
Details / Final Prototype
Credits: Dinorah Martínez Schulte
Currently, the construction industry is going through two crises: the global warming crisis and the rapid increase in population, giving rise to a housing crisis. Building elements used in architecture can be designed and produced using high-tech materials and digital fabrication, and material research. A particularly interesting group of materials with respect to their strength/weight ratio are foams. Despite their important role in industrial construction practice as carriers and lightweight material, only brief research has been done to use 3D-printed foams in Construction 3D Printing (C3DP) construction (Keating, Oxman, 2013; Lublasser et al., 2018). The recent development of highly porous mineral foams that are particularly suitable for extrusion printing opens a new chapter for experiments and the development of new, lightweight construction components with digital manufacturing processes (Minas et al., 2016).
As part of a 12-week thesis project of the MAS ETH DFAB program at ETH Zurich, this project demonstrated development through design and fabrication of lightweight architectural elements as part of a larger investigation investigating C3DP with mineral foams from recycled waste, which could be customized and optimized for a material reduction in the built environment. Starting from the initial material development and research, several 3D printed block designs were born. The mineral foam was systematically explored through an extensive prototyping exercise.
3D Printing Process Credits: Dinorah Schulte
The fabrication method is robotic 3D-extrusion-printing and the printed elements were sintered in a furnace to achieve their full mechanical strength. As a final demonstrator, an ultralight screen façade was manufactured with mineral foam discrete elements and cast on UHPFRC Ultra-High-Performance Fibre concrete. Due to its geometry, they allow natural lighting and ventilation, highlighting the benefits of using this material to create lightweight, innovative, sustainable, and low-impact architectural elements on the environment.
The main goal of the research is to explore design challenges for 3D printing with mineral foams, promote awareness on the future built environment, and give a conclusive outlook discussing the future avenues of research.
Prototyping
Credits: Dinorah Schulte
Credits: Dinorah Schulte
Description: Academic Group Pavilion
Tutor: Marirena Kladeftira (project lead), Matthias leschok, Eleni Skevaki (Chair of Digital Building Technologies, ETH zurich), Davide Tanadini (Chair of Structural Design, ETH zurich), Yael Ifrah (MAS ETH DFAB coordination, chair of Digital Building Technologies)
Location: Zurich, Switzerland
Institution: ETH Zurich + Digital Building Technologies
Date: 2020
The Digital Bamboo pavilion explores the innovative combination of a bio material with digital fabrication. Bamboo is an excellent sustainable building material, because of its rapid growth and very low weight-to-strength ratio. Customized computational tools were developed to design the ultra-lightweight structure, whose bespoke connections were manufactured using 3D printing technology. The structure covers more than 40 sqm with a total weight of only 200 kgs.
The Digital Bamboo pavilion showcases a filigree and engaging architecture that surpasses the standardized space frame vocabulary.
The bamboo elements are connected via a new system based on 3D printing technology. The generation of the connections was automated thanks to a digital process and developed to fulfil mechanical requirements. Their intricate geometry encapsulates necessary functions such as tolerances for assembly and bamboo inhomogeneities, connections to the shading panels, labelling, and cable fittings. In parallel, their volume is minimized to save time and cost. A hybrid strategy using MultiJet Fusion technology and Direct Metal Laser Sintering was used to manufacture the 380 bespoke connections.
Final Prototype
Photo by: Andrei Jipa / DBT ETH Zurich
Final Prototype
Photo by: Andrei Jipa / DBT ETH Zurich
Final Prototype
Photo by: Andrei Jipa / DBT ETH Zurich
Final Prototype.
Photo by: Andrei Jipa / DBT ETH Zuric
Final Prototype
Photo by: Andrei Jipa / DBT ETH Zurich
Joint Final Prototype
Photo by: Dinorah Martínez Schulte DBT
The shading panels of the pavilion are designed through a custom computational process and fabricated through add-on 3D printing of a recyclable UV resistant thermoplastic on a lightweight lycra textile. 3D printing stiffens and shapes the fabric into flexible bespoke panels.
The construction system developed for the Digital Bamboo pavilion aims to reduce the logistic efforts of construction while exploiting the advantages of digital fabrication for a more sustainable building culture. Following the principle of distributed prefabrication, the complexity of the structure is encapsulated in small parts that can be fabricated all over the world using 3D printing. These custom parts can be used to construct high-performance structures together with local materials. The Digital Bamboo Pavilion is designed by students of the Master in Advanced Studies in Architecture and Digital Fabrication 2019-2020 at the ETH Zurich and is based on research at the chair of Digital Building Technologies
Section Drawing Image by: MASDFAB ETH 19/20
Floor Plan Drawing
Image by: MASDFAB ETH 19/20
Joint Details Drawing
Image by: MASDFAB ETH 19/20
The composite elements are locally reinforced reducing the amount of material used.
Photo by: Mathias Leschok
Description: Project at the Robotic Atelier 2019
Tutors: Xavier De Kestelier and Manuel Jiménez García
Location: Madrid, Spain
Institution: Norman Foster Foundation
Date: 2019
Collaboration: Ramon Weber and Nik Eftekhar
Described by the Workshop Mentor, Xavier De Kestelier, as ‘the inception of the Fourth Industrial Revolution,’ the third edition of the Robotics Atelier, which took place from the 4th to the 8th November of 2019, tested the limits of 3D printing and its potential applications.
The third instalment of the Robotics Atelier we will focus on large scale 3D printing with recycled plastics. One of the advantages of 3D printing with plastics is the inherent freedom of form. With that comes the potential of an integrated approach to design.
The field of application will be building skins. These are often built up out of a series of materials that each have their own shape and function. But what if we can start to blur the lines between these different materials, forms and performances? What if we can design a building skin that can have multiple functionalities embedded within one complex geometrical system?
Can we integrate a variety of functions that respond to specific environments into one 3D-printed element?
Final Prototype
Photo by: Norman Foster Foundation
We are living in a time of change and above all we are facing consequences such as the climate change that we are experiencing today. We are running out of the planet and our nature is demanding a change, a solution. In this workshop, it encourages us to think of new solutions and create initiatives to improve our capacities as designers and architects hand in hand with technology, creating awareness and using recycled materials for their production.
THEMODULAR is a proposal contemplated the ubiquity of prefabricated façade systems used throughout Europe, speculating how these could be transformed using 3D printing and recyclable materials. seeks to create a facade solution from an architectural and ecological perspective and with the support of technology such as 3D Printing tools and robotics, we seek to generate a response to put a grain of sand to this emerging issue that seeks a way out, creating a 3D printed facade using recycled plastic obtained from the oceans (collaboration with Parley parley.tv/#fortheoceans) to create a building skin with the ability of thermal insulation to address and optimize responses to new climate changes.
Firstly, we analyze the function and the meaning of what a facade is from both an architectural and social perspective.
We take as reference the exercise: ‘Façades’ is a series of photographs by French photographer Zacarie Gaudrillot-Roy. The photographer attempts to imagine a world where buildings are stripped of their “buildings” with nothing but their surface left. Zacarie isolates the surfaces of buildings and photographs the hauntingly incomplete images. The facades look like icing if it was removed from its cake.
According to the artist, the facade of a building is “the first thing we see ... it can be impressive, superficial or safe.” The photographs explore a world in which first impressions and surfaces are all there is. There is nothing to discover beneath. Essentially it’s what we’d see if in a holiday photograph, there was only the outside of the building. But why is the outside more important than the inside?
The same can be said about people. We are all more than what is on the surface.
One of our main objectives was to seek to make a prototype of a façade that would allow it to be erected, stable, re-adaptable, standard and that would be light so that it would allow you to transport it easily and its assembly was a fairly simple, flexible and replicable process on any scale.
Prototyope
The basis of the project is a very simple geometry defined by offset sine curves, which could be easily stacked and interlocked in both directions. to give fluidity and dynamism to the project and allow us a fairly simple and rigid assembly between part and part.
One of the objectives was to create a façade that would create a solution to dramatic climatic changes, which is why we focused on how to face solar radiation through a thermal insulation system. Solar radiation directly affects objects that have contact in a range of influence with the heat transfer. A thermal insulation system reduces thermal conductivity and radiation. One solution is to generate an empty structure and fill it inside with some material that generates
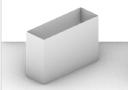
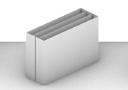
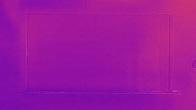
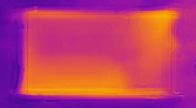
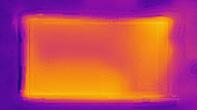
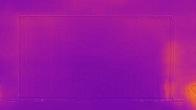
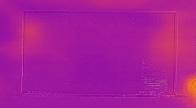
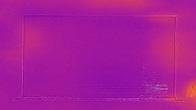
thermal insulation, to address this issue, the group created several prototypes incorporating air gaps, printed infill patterns and recycled PETG pellets, whose energy performance was tested using a thermal camera . Inserting PETG pellets made from plastic waste recovered from the ocean proved to be a satisfactory insulating technique, and the concerns about the weight increase could be resolved by transporting hollow modules which could then be filled with locally available materials. Therefore, we generated 5 different line patterns for each insulation infill and we measured them and with the captured information, we analyzed which were more efficient and which were not so efficient.
Interlocking modular elements defined by offset curves.
According to Jiménez, there are still some important questions that need to be addressed within the world of large-scale 3D printing.
For example, short production chains have yet to be improved and the reduction of building elements is a subject that continues to carry many complexities within the building industry.
However, the ambiguous position between the parametric approach and the fordist production, he said, has opened a new horizon to digital fabrication and its adaptation to the everyday world.
Digital Process.
Photo by: Norman Foster Foundation
Digital Process
Photo by: Norman Foster Foundation
Largely focused on prints made with recycled plastics recovered from the planet’s oceans, the workshop aimed to continue the ground-breaking innovations made possible by 3D printing within the architecture and construction industries.
Its design possibilities were considered by both students and professors alike, reconciling the dimensions of form, material and performance into one complex system capable of responding to the various questions, both ethical and technical, raised by its use.
of the prototype’s design and print.
Development
Final Protoype
Photo by: Norman Foster Foundation
By using only recycled plastics for large-scale 3D printing in construction, we can begin to reuse our planetary surplus of plastic waste, turn it into functional building material and thus, hopefully, begin to reduce the amount of plastic waste in our environment. The design also prioritised optimal insulation properties.
Final 3D prints of the façade’s components.
Final Protoype
Photo by: Dinorah Martínez Schulte
“Technology has the power to create the new vernacular.” - Lord Norman Foster.