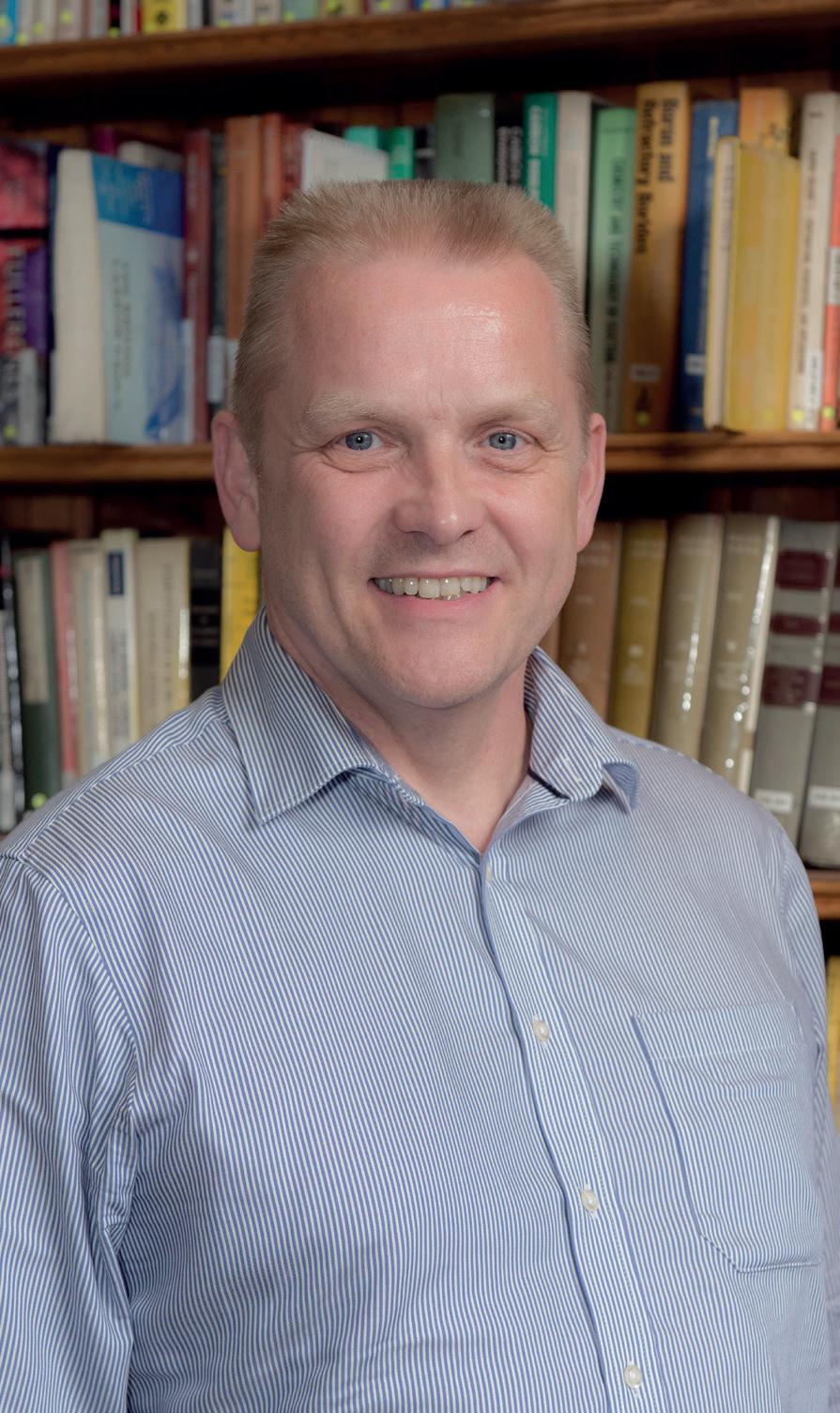
14 minute read
big interview
COVID-19 lockdowns lead to UK tech sales boom and adds to e-waste problem
Following our Precious Elements campaign last year – which raised awareness of the supply risks to elements in our personal devices such as mobile phones – we have conducted further research to quantify how the COVID-19 pandemic may have had an impact on the problem of waste electronic equipment.
Advertisement
By Lizzy Ratcliffe
Last year we discovered that there could be 40 million or more unused devices being hoarded in drawers and cupboards around the UK. Now we’ve found that this problem is growing even more, with 12.8% of the 2,000 UK residents we surveyed saying they had acquired new IT equipment to enable them to work from home during the pandemic. Of these, nearly as many said they had put redundant tech in the bin (10.8%) as said they had recycled it (12.8%). And a further 10% of said they had a stockpile of old IT equipment they didn’t need as a result of changing their working habits. Later this year we will release the full results of our global survey, which looked at technology consumption during the pandemic as well as attitudes towards personal technology and sustainability. Meanwhile, Currys PC World told us that fitness trackers were up 45% year on year, and gaming technology sales were up 121%. With many gyms across the country set to remain closed – the traditional time for making weight loss and fitness resolutions – this is a trend that looks set to continue well into 2021.
The figures are revealed as part of our ongoing Precious Elements campaign, which draws attention to supply risks to some of the precious elements used in consumer technology, such as gold, yttrium and indium. Prof. Tom Welton, President of the Royal Society of Chemistry, said: “Clearly the coronavirus pandemic caused a rapid change to our work and lifestyle patterns, but a significant unintended consequence we are now facing is a rapid increase to the UK’s already growing e-waste crisis. That nearly as many people are binning their old tech as recycling it is a huge concern. “We increasingly think about the sustainability of other items around the home, such as plastics and cardboard packaging. If we’re to have sustainable technology, we need to start thinking in the same way about our old gadgets, or we risk running out of the elements we need to produce these items while continuing to exacerbate the environmental damage caused by the consumer tech industry.” The Royal Society of Chemistry was invited to give evidence to the UK Government’s Environmental Audit Committee report into e-waste following its Precious Elements campaign last year, which found that up to 40 million unused gadgets were stockpiled in people’s homes because they didn’t know how to dispose of them. The recommendations have now been put to the government for possible inclusion in the new Environment Bill in 2021. Meanwhile, as of 1 January 2021, retailers distributing electrical and electronic equipment are now required to offer in-store take back of items equivalent to those sold to consumers in-store.
In addition, retailers with greater than 400 square metres of floor space will be required to accept all items of very small Waste Electrical and Electronic Equipment (WEEE) regardless of whether customers are replacing the item by buying new products or not. Very small WEEE is defined as items with dimensions no greater than 25cm on any side/edge. Prof. Welton said: “We know chemists are working on the tricky problem of how to separate more critical raw
materials from electronic waste for recycling purposes, but we need local recycling infrastructure that enables the waste to be collected first.
“While we welcome the changes coming in to force at the beginning of January to ensure that retailers operate takeback schemes – an issue highlighted in the Environmental Audit Committee’s report to government – it’s only possible to extract some of the more common raw materials on a large scale at the end of life. Many precious metals are never recovered.”
Jason Love, Professor of Molecular Inorganic Chemistry at the University of Edinburgh, whose research group designs new chemical reagents for metal recycling, believes chemistry is key to tackling this problem. “Existing methods of extracting precious metals from technology include smelting which can produce harmful emissions, is energy intensive, and requires further downstream separation processes,” he said. “Chemists are now working on more efficient and sustainable ways to separate these metals. This can involve dissolving the waste materials and then using carefully designed molecules that identify and extract the different metals. Understanding and controlling the interactions that lead to separation are very much fundamental chemistry challenges.” Prof. Welton concluded: “If we’re to successfully tackle the UK’s e-waste crisis, citizens, governments, retailers, manufacturers and scientists need to work together to make technology and our consumption habits more sustainable.” “In the meantime, we are urging everyone to be more conscious about how they use and reuse technology. For example, if a device is not useful to you anymore, try selling it, donating it or giving it to someone else. Recycle it as a last resort – but do not put waste technology in the bin.” The RSC’s survey of 2,000 people across the UK about their tech consumption and recycling habits found more than a quarter (26.9%) of people across the UK started to work from home for the first time as a result of the coronavirus pandemic, but just a third of those (33%) took existing office equipment home. Nearly the same number (29%) said their employer had purchased new tech on their behalf to support the change in working habits, and almost one in five (18.8%) purchased new IT equipment at their own expense to support home working. A further 17% said they used the need to work from home as an opportunity to upgrade their IT equipment when they weren’t previously planning on doing so. This is reinforced by sales figures from tech retailer Currys PC World, which show there was a 41% increase in computing sales between stores first re-opening on 1st May and 22nd August, compared to the same period in 2019. However, the electrical retailer, which also offers a free recycling service for small e-waste such as computers or gadgets, says returns of redundant equipment have dropped. While stores were closed for 13 weeks this year due to restrictions, e-waste returns were down 81% in 2020 when compared to the pre-lockdown period. Kesah Trowell, Head of Sustainable Business for Currys PC World said: “All through the pandemic we have been experiencing unprecedented demand for the technology that has been keeping families fed, clean and entertained as well as helping people to work from home, but it is vital that people don’t stockpile old or unwanted tech. “We already recycle 65,000 tonnes of waste electricals each year, making us the biggest e-waste recycler among UK retailers, but are committed to doing more through our e-waste doorstep recycling scheme and store take-back scheme. Regardless of whether you have bought your tech from us, we will take any unwanted equipment to help declutter households and the environment at the same time.”
Chemical researchers in academia and industry are working to develop solutions and the Royal Society of Chemistry is collaborating with them to communicate recommendations to policy makers.
www.rsc.org/new-perspectives/sustainability/elementsin-danger
Delivering on Training Requirements in a Virtual Setting
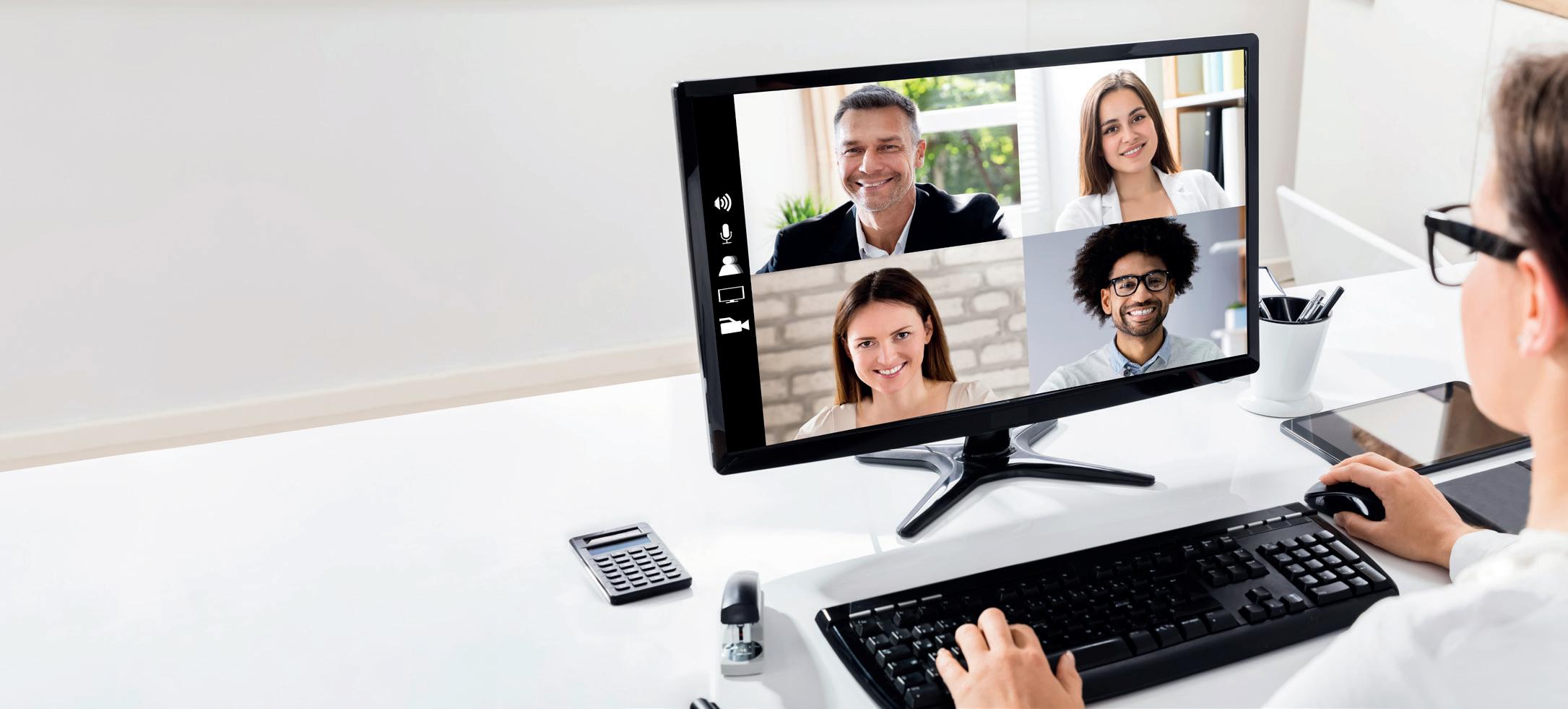
Last year we spoke about managing major accident hazards at high hazard establishments in the face of COVID-19, but at the time we couldn’t have predicted that the “temporary” measures associated with the pandemic would still be in place almost a year on. It has been a firm standpoint of the COMAH Competent Authority that regulatory activities must continue despite the pandemic, with many sites having to carefully think about how to demonstrate that they can maintain safe operations while adapting to reduced manning and other COVID measures.
Overall, it feels like our industry has risen to the challenge and adapted well, even where we thought that some process safety activities would be impossible to achieve. From our perspective, this in particular means HAZOP and other hazard identification studies, ALARP sessions and information gathering for assessments and reports. It was once unthinkable that any of these processes should be carried out remotely, but where needs-must, we have adapted well and managed to maintain the necessary high standards of work. That’s not to say that all work going forward should be carried out remotely; we still recommend that studies are consolidated by an onsite review once things return to normal. On the whole, though, industry has learnt a lot about maintaining the highest standards of major accident hazards in a more virtual world. The same goes for training. It has been great to see our clients embracing online training in favour of delaying faceto-face sessions until more ‘normal’ times. By adopting the most suitable video conferencing platforms, we have been able to adapt our workshop style of training facilitation and feedback has remained positive. There have been some lessons learnt along the way that we look forward to implementing as we widen our training capacity in 2021. Limiting delegate numbers to smaller groups helps greatly in keeping up the energy needed for a productive training session. Facilitation is largely about engaging with delegates to make the most of their experience and make sure that the key messages stay relevant to them. This is easy when speaking face to face with delegates, when you can use body language to gauge feelings and change direction. Technology can become a barrier to communication but working with smaller groups can create a more comfortable atmosphere with more open discussion which ultimately helps delegates get the most from their course. Shorter sessions have also been of great benefit. When the time and expense associated with travel is limited, there is more flexibility in session start and end times, which has worked to the delegates’ advantage. Staying focussed on a video conference all day is tough on anyone, not to mention operators and technicians who would normally spend a lot of their time in the field. By limiting online training sessions to multiple shorter sessions, engagement has been positive and more consistent.
Successful training relies on a balance of delivery techniques that address the different learning styles of the delegates. Online video conferencing platforms no longer limit trainers to Powerpoint presentations and a lecture style of delivery. Using break-out rooms for small groups of delegates helps to engage those with more active learning styles by allowing them to participate in activities and apply what they are learning to practical situations from the outset. For those with more visual and aural learning styles, shared screens, whiteboards and chat functions all help to ensure that information is delivered in a way that benefits the individual, and make it easier for trainers to quickly adapt to the needs of the delegates. Overall, it can be tempting to shy away from online training delivery in favour of delaying courses until they can be delivered in person. However, online methods of delivery can be quickly adapted to suit the organisation and the individual, which can result in positive training outcomes. We will be continuing to implement what we have learnt as we deliver online training to our clients through 2021. By bearing these lessons in mind, we can confidently deliver our bespoke courses in all aspects of process safety, as well as our new offerings of the Cogent Process Safety Management for Operators (PSMO) and Bowtie use and application, ultimately allowing operators to continue to demonstrate that they can maintain safe and efficient operations in this ‘new normal’.
Jenny Hill & Carolyn Nicholls enquiries@ras.ltd.uk
RAS
RISK & HAZARD MANAGEMENT
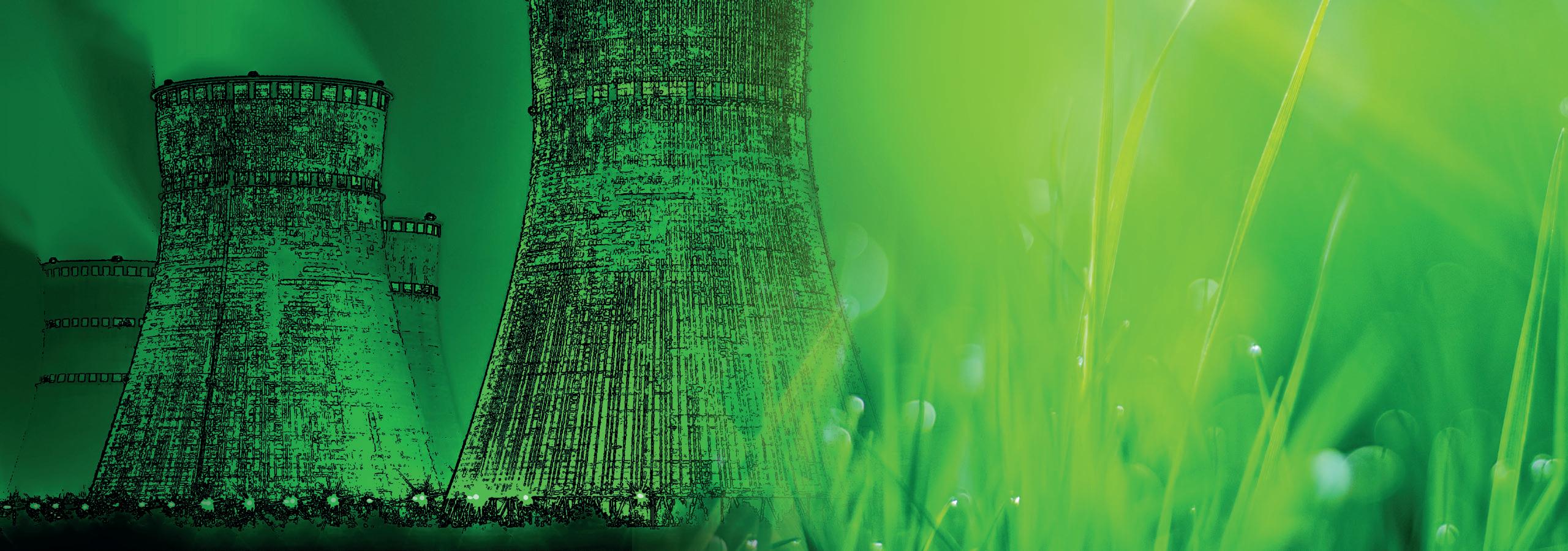
Understanding and facilitating the effective management of risk is our core business. Our expertise covers the full range of risk assessment and management services across:
Safety Risk Business Risk Environment Risk
Only when the risk facing an organisation is well understood can it be effectively managed. Key to the successful identification, assessment and management of risk is engagement with the right people, using the right processes at the right time. We believe we are different to many of our competitors and our approach is distinctive, we don’t always walk the well-trodden path but look at each client’s particular risk context and develop a tailored solution, working in partnership with our client.
We work across all aspects of risk, from Quantitative Risk Assessments and Predictive & Consequence modelling, through to the ‘softer’ risks which may affect an organisation’s reputation.
overFill protection • level measUrement & alarms • volUme & Weight • process control Providing solutions for Liquid Level Management
ISS Projects (UK) Ltd Provide Level Management solutions to various industries throughout the UK. We design, install and upgrade all types of tank gauging systems, providing planned preventative maintenance and annual calibration services. We work on Top Tier COMAH sites and our Compex certified Engineers can provide a complete gauging solution utilizing the most suitable type of sensor for the medium.
CASE STUDY 1
UnaUthorised prodUct movement detectionTask: ISS customer required a complete Tank Gauging and overfill • remote telemetry • FUnctional saFety With many years experience in our field, ISS Projects UK Ltd provide liquid level management solutions to industry throughout the UK. protection system to SIL 2 on a bulk storage tank farm. We design, install and upgrade all types of tank gauging systems, providing planned preventative maintenance and annual calibration Solution: ISS built, installed and commissioned a ISS Tank in Touch services. Working on Top Tier COMAH sites our Engineers are CompEx certified and can work on and install ATEX certified equipment, Gauging system with control interlocks for high and low levels they are also trained the latest edition of wiring regulations. utilizing the latest 80GHz radar level sensors. All levels reading were Providing a complete gauging solution to all types of sensors from Pressure Transmitters, Temperature sensors, Bubbler Probes to then made available to the company network meaning anyone connected with authentication could log on and see real time tank Non-Contact and Guided Wave Radar connected to Local Displays and or a HMI touch screen display capable of providing simultaneous levels and available space in each tank. To meet the SIL 2 requirement real time level, temperature and top pressure readings with used defined alarms all of which can be access via Local area or Wide area Vibrating fork switches were installed on all tanks and connect to networks. an ISS High Level Panel. Our TUV Functional Safety Engineer then provided the documentation and calculations required to meet SIL 2
We can also provide systems that will text or email alerts for preset conditions giving you peace of mind wherever you are. ISS also install remote telemetry systems using GSM and network solutions sourcing the best solutions to meet your needs allowing real time information to be shared to anyone with a web browser and Tel: 01765 606655 access to the internet, these units can send alerts via text or email and can be made accessible Email: info@issprojects.com Web: www.issprojects.com
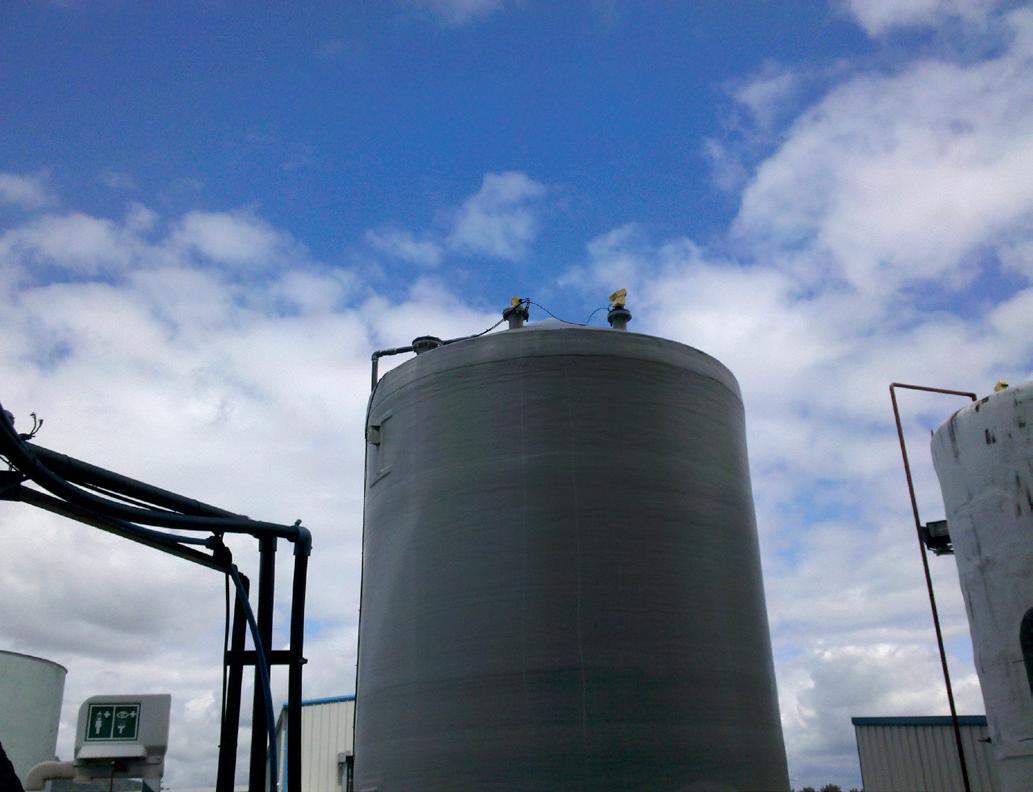
CASE STUDY 2

Task: ISS client wished to support their customer with tank gauging and remote telemetry. Solution: ISS supplied, installed and commissioned 2 tank radars and a Telemetry unit with a display, which could also be accessed via a device connected to the internet. The Telemetry uses a mobile sim so no connection to the sites network was required. The system sends out an email when a delivery is required and a further email if the level passes a lower set point. When a user is logged into the unit trending can be viewed and downloaded. Once installed the reorder setpoints can be configured remotely by ISS. Multiple users can login to the system with their own login. ISS monitor the unit for faults and visit the site once a year for a health check of the system Task: Upgrade an old gauging system with a new system incorporating unauthorized product movement monitoring (leak detection). Solution: The application required fourteen underground tanks containing various solvents to be gauged and monitored for unauthorised product movement. We selected magnetostrictive probes to provide us with a high level of accuracy (accuracy being a fundamental element to the function of the leak detection monitoring). The system uses Pepperl + Fuchs (P+F) field barriers for ATEX conformance and a P+F gateway for the HART variables. Our industry proven Tank-in-Touch gauge was used as the platform to build the leak detection system. The whole package not only monitors for any possible loss of product (which has an environmental as well as a financial cost), it also enables a more efficient stock control and ordering system which ultimately can save costs.
CASE STUDY 3
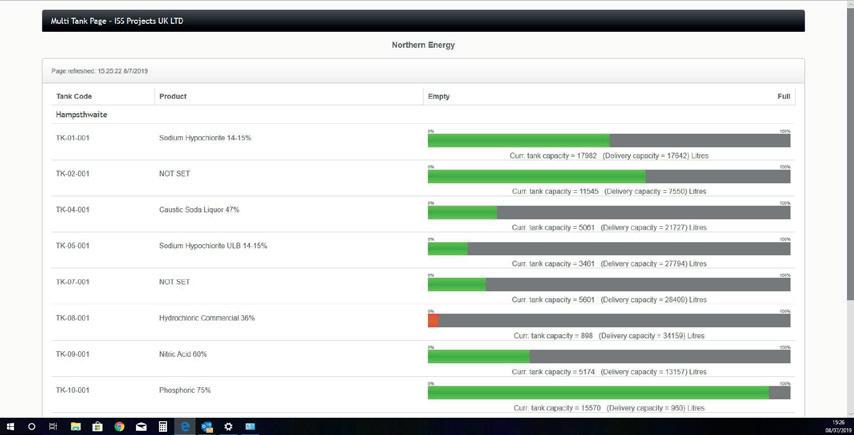