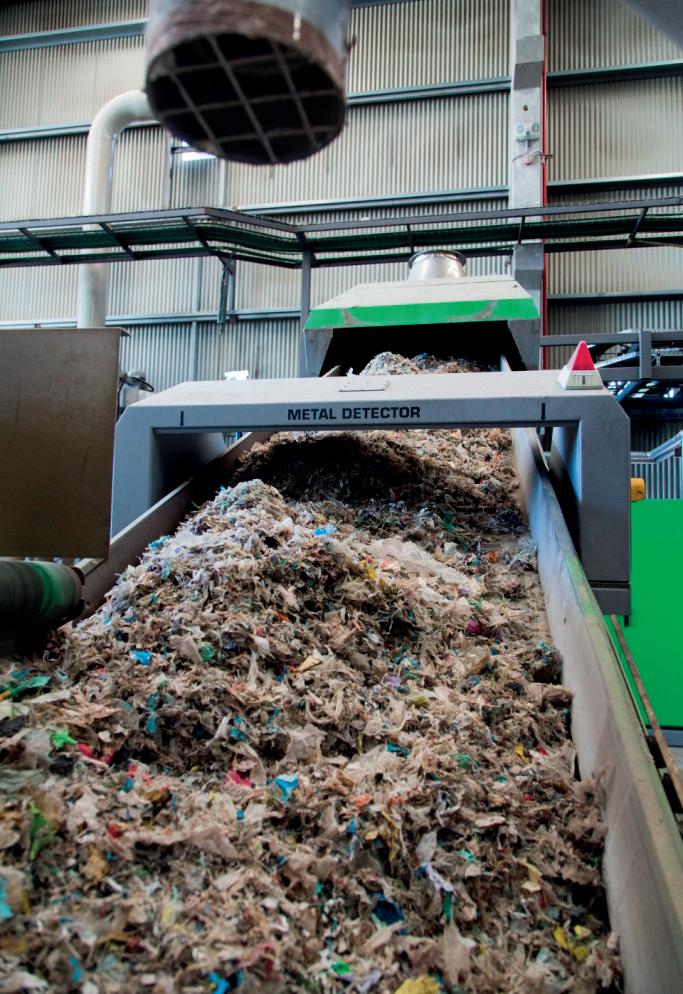
17 minute read
environmental
Europe chemical recycling to keep growing but legislative, infrastructure challenges remain
By Mark Victory
Advertisement
Senior Recycling Editor at ICIS
Chemical recycling continues to attract a wealth of investment in Europe and is still seen by many as the only potential way to meet mass-scale food-contact recycled material content targets for most polymers.
As a result, new pilot plants are expected to continue to emerge in 2022. Nevertheless, a number of legislative and infrastructure challenges continue to face the industry. The EU Commission stated in late 2020 that it would take a decision in 2021 on the legal status of chemical recycling based on its cradle-to-grave life-cycle impact. This has failed to emerge. Current EU regulations typically use the definition of recycling set out in Directive 2008/98/EC, in which recycling is “any recovery operation by which waste materials are reprocessed into products, materials or substances whether for the original or other purposes. It includes the reprocessing of organic material but does not include energy recovery and the reprocessing into materials that are to be used as fuels or for backfilling operations.” This leaves the regulatory status of chemical recycling under the proposals uncertain. EU definitions on the legal status of chemical recycling are becoming increasingly pressing for the industry following the EU Commission’s proposals in November to overhaul current rules surrounding the export of waste. Several players have said that the new proposals would make it more difficult to export waste, particularly for chemical recyclers. Of particular concern to some waste managers is the EU allowing modification of waste measure to be up to individual countries, which they fear would lead to significant regulatory divergence. The Commission is proposing an EU-wide system to electronically exchange documents and information, which would allow authorities to better monitor waste streams.
Materials not listed on the EU’s green list and destined for recovery operations will require prior written consent and approval from relevant authorities in both the sending and receiving countries. Shipments of waste for disposal in other member states will be broadly restricted under the proposals. Mixing waste streams during shipment will also be prohibited under the proposals.
CONSULTATION BEGINS
In December, the Commission issued new draft legislation for consultation on changes to food-contact recycled
material regulations, which would encompass both mechanical and chemical recycling. Along with restrictions on the type of input waste used for recycling to food contact, the legislation would mandate the use of “suitable technologies” for recycling waste, which currently only include mechanical polyethylene terephthalate (PET) recycling, and closed-loop recycling originating from a food distribution chain or catering service in a closed and controlled chain.
The legislation would cover both mechanical and chemical recycling processes. Nevertheless, there is an exemption from the regulation for plastic waste used to manufacture substances under Article 5 of Regulation (EU) No 10/2011, as long as they are intended for subsequent use in accordance with that Regulation. This would appear to potentially exempt chemical recyclers reverting material back to monomers. The consultation period was open until 10 January 2022. There is currently 364,000 tonnes/year of operational chemical recycling capacity in Europe, of which 218,000 tonnes/year (or 60%) is pyrolysis based, data from the ICIS Chemical Recycling Supply tracker shows. With new chemical recycling plant volumes frequently being announced, this volume is expected to increase in the coming years, even as the majority of plants remain at pilot or lab scale.
One challenge facing pyrolysis-based chemical recycling start-ups is the sheer number of different input waste types that can potentially be used in the process, which typically requires extensive testing of different types of input waste to see which will deliver within specification at the lowest cost. 70% mixed-polyolefin, 90% mixed-polyolefin, or RDF-reject bales are commonly used, depending on what sorting facilities chemical recyclers have on site. Prices of mixed-polyolefin bales suitable for mechanical recycling have increased sharply during 2021, as a result of high prices of mono-sorted material making the use of mixed-polyolefins increasingly economically viable for mechanical recyclers. With pyrolysis-based chemical recyclers not wanting to compete with mechanical recycling on ideological grounds, and process costs expensive before the variable cost of bales is accounted for, pyrolysis-based chemical recyclers are increasingly shifting away from the use of mixed-polyolefin waste.
Process costs from plant to plant remain too variable to give estimated production costs and are highly dependent on factors such as yield, technology and logistics. Nevertheless, some players spoke of costs in triple figures due to rising electricity costs – with pyrolysis typically an energy-intensive industry. This has also led to differences in costs from country to country, with energy prices in France, for example, typically lower than other parts of Europe due to the prevalence of nuclear energy.
COSTS SET TO FALL
It is expected that pyrolysis-based chemical recycling costs will fall as technology and economies of scale develop and the market matures.
Historically, mixed polyolefins have been the feedstock of choice for pyrolysis-based chemical recyclers because of the need to limit PET (which oxidises and does not depolymerise via pyrolysis), chlorine (which is corrosive), nylon and flame retardants content in its input material. At the same time, high energy costs are making burn for energy more attractive and the RDF market is growing, particularly from the cement industry. While most pyrolysis-based chemical recyclers are eager to avoid competition with mechanical recyclers for ideological reasons, this is placing them in direct competition with the RDF sector due to a lack of sufficient infrastructure to meet expected future demand. ICIS has launched a new mixed plastic waste pricing service. Details at clientsuccess@icis.com.
INEOS, Petroineos and Plastic Energy in plastic recycling breakthrough
INEOS Olefins & Polymers Europe and Plastic Energy are working together on a trial to convert ‘hard to recycle plastic material’, such as flexible packaging, back into ‘food-grade’ quality plastic for use in food packaging, and other high hygiene standard applications.
The companies have come together to launch a preliminary trial in Q1-2022 at the INEOS Grangemouth facility in Scotland. This preliminary trial and the evolution of the policy environment in the UK will inform the development of a large-scale advanced recycling plant, which aims to be the first of its kind in the UK.
Advanced Recycling creates a closed-loop system for plastics management, helps reduce landfill, prevents plastic from ending up in the environment, and reduces the use of fossil derived raw materials. The circular re-use of ‘end of life’ plastic is a further step to reduce total emissions. INEOS Olefins & Polymers Europe and Plastic Energy have a shared goal to create a world class circular economy value chain in advanced recycling, driving circularity to create the next generation of food-grade recycled content packaging. Plastic Energy uses its advanced recycling process to convert post-consumer plastic, otherwise destined for landfill or incineration, through a pyrolysis process, into a liquid raw material (called TACOIL) for re-use in the next generation of plastic production. TACOIL is used as a replacement for fossil derived materials, to make foodgrade and/or medical grade plastics. The trial will take place in partnership with Petroineos at Grangemouth. It will use the existing refinery operations to process the TACOIL supplied by Plastic Energy, which already operate two recycling plants in Spain. Plastic Energy’s technology allows for the improvement in circularity of highly demanding labelling, and packaging applications, such as chocolate bars, snacks and biscuits, pet and dry food. The new project is complementary to the existing use of mechanically recycled plastic in INEOS Recycl-IN range of products. Petroineos will supply the recycled raw material to INEOS Olefins & Polymers Europe to be transformed into Certified Circular plastic with the identical properties expected of conventional plastics made from oil and gas. The partners recognise the need for collaboration to make such innovations sustainable at scale – in the spirit of “SDG#17 Partnerships for the Goals”, each partner contributes complementary skills and expertise that together create the circular value chain. Plastic being recycled and compressed
“We are pleased to announce this trial in Scotland, which exemplifies a strong partnership between companies working together to take big strides to reduce plastic waste in the UK. Working with INEOS, we are pleased to see our advanced recycling technology being used as a core component to improve the circularity of packaging.”
Carlos Monreal, Founder and CEO of Plastic Energy
Rubber holds key to long-lasting, safer EV batteries
For electric vehicles (EVs) to become mainstream, they need cost-effective, safer, longer-lasting batteries that won’t explode during use or harm the environment. Researchers at the Georgia Institute of Technology may have found a promising alternative to conventional lithium-ion batteries made from a common material: rubber.
Elastomers, or synthetic rubbers, are widely used in consumer products and advanced technologies such as wearable electronics and soft robotics because of their superior mechanical properties. The researchers found that the material, when formulated into a 3D structure, acted as a superhighway for fast lithium-ion transport with superior mechanical toughness, resulting in longer charging batteries that can go farther. The research, conducted in collaboration with the Korea Advanced Institute of Science and Technology, was published recently in the journal Nature.
In conventional lithium-ion batteries, ions are moved by a liquid electrolyte. However, the battery is inherently unstable: even the slightest damage can leak into the electrolyte, leading to explosion or fire. The safety issues have forced the industry to look at solid-state batteries, which can be made using inorganic ceramic material or organic polymers. “Most of the industry is focusing on building inorganic solid-state electrolytes. But they are hard to make, expensive and are not environmentally friendly,” said Seung Woo Lee, associate professor in the George W. Woodruff School of Mechanical Engineering, who is part of a team of researchers who have uncovered a rubber-based organic polymer superior to other materials. Solid polymer electrolytes continue to attract great interest because of their low manufacturing cost, non-toxicity and soft nature. However, conventional polymer electrolytes do not have sufficient ionic conductivity and mechanical stability for reliable operation of solid-state batteries.
NOVEL 3D DESIGN LEADS TO JUMP IN ENERGY DENSITY AND PERFORMANCE
Georgia Tech engineers have solved common problems (slow lithium-ion transport and poor mechanical properties) using the rubber electrolytes. The key breakthrough was allowing the material to form a threedimensional (3D) interconnected plastic crystal phase within the robust rubber matrix. This unique structure has resulted in high ionic conductivity, superior mechanical properties and electrochemical stability. This rubber electrolyte can be made using a simple polymerization process at low temperature conditions, generating robust and smooth interfaces on the surface of electrodes. These unique characteristics of the rubber electrolytes prevent lithium dendrite growth and allow for faster moving ions, enabling reliable operation of solid-state batteries even at room temperature. “Rubber has been used everywhere because of its high mechanical properties, and it will allow us to make cheap, more reliable and safer batteries,” said Lee. “Higher ionic conductivity means you can move more ions at the same time,” said Michael Lee, a mechanical engineering graduate researcher. “By increasing specific energy and energy density of these batteries, you can increase the mileage of the EV.” The researchers are now looking at ways to improve the battery performance by increasing its cycle time and decreasing the charging time through even better ionic conductivity. So far, their efforts have seen a two-time improvement in the battery’s performance / cycle time. SK Innovation, a global energy and petrochemical company, is funding additional research of the electrolyte material as part of its ongoing collaboration with the Institute to build next-generation solid-state batteries that are safer and more energy dense than conventional LI-ion batteries. SK Innovation is building a new EV battery plant in Georgia, expected to produce an annual volume of lithium-ion batteries equal to 21.5 Gigawatt-hours by 2023. “All-solid-state batteries can dramatically increase the mileage and safety of electric vehicles. Fast-growing battery companies, including SK Innovation, believe that commercializing all-solid-state batteries will become a game changer in the electric vehicle market,” said Kyounghwan Choi, director of SK Innovation’s nextgeneration battery research centre.
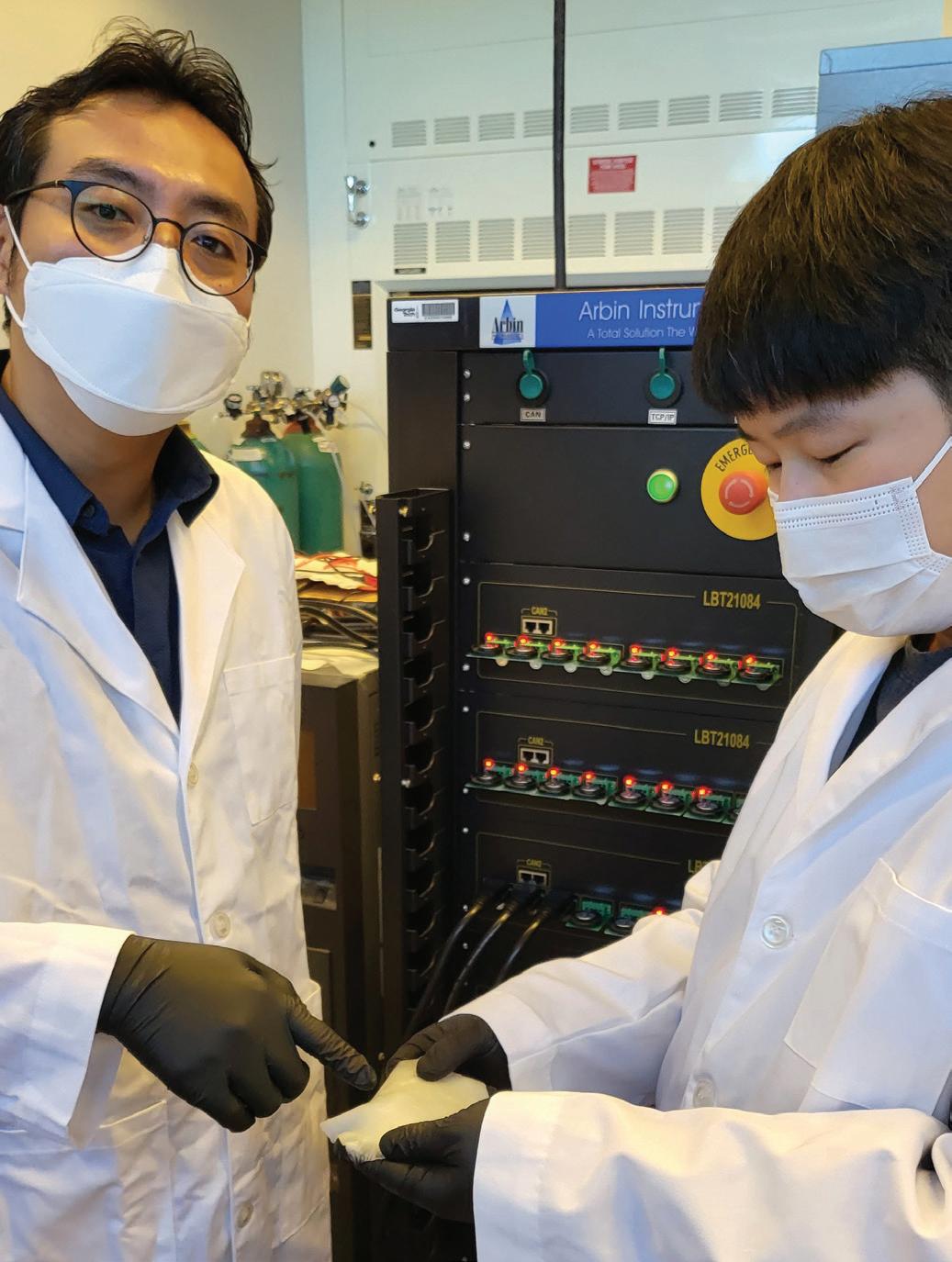
Prof. Seung Woo Lee (left) and Michael J. Lee (right) have demonstrated a more cost-effective, safer solid polymer electrolyte (rubber material) for allsolid-state batteries. (Photo credit: Georgia Tech)
Scientists develop novel strategy for sustainable post-lithium-ion batteries
Bristol University scientists are celebrating the performance of sustainable batteries with far-reaching implications for e-vehicles and devices.
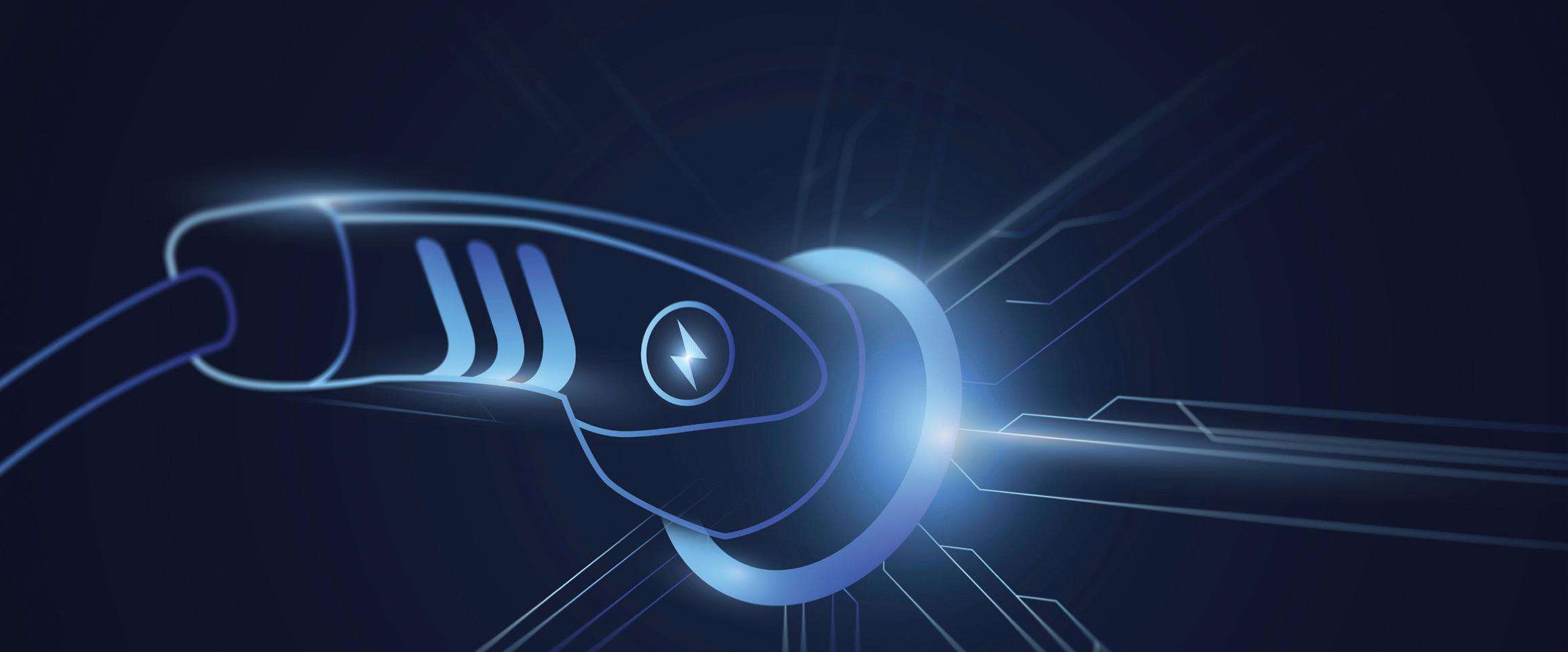
High-performance sodium and potassium ion batteries have been developed using sustainably sourced cellulose. Scientists at the Bristol Composites Institute developed a novel controllable unidirectional ice-templating strategy which can tailor the electrochemical performances of nextgeneration post-lithium-ion batteries with sustainability and large-scale availability. The paper is published in the journal Advanced Functional Materials. There is a rapidly increasing demand for sustainable, ethical and low-cost energy-storage. This is due in part to the drive towards developing battery-powered transport systems – mostly replacing petrol and diesel-based engines with electric vehicles – but also for hand-held devices such as mobile phones. Currently these technologies largely rely on lithium-ion batteries.
Batteries have two electrodes and a separator, with what is called an electrolyte between them which carries the charge. There are several problems associated with using lithium for these batteries, including build-up of the metal inside the devices which can lead to short circuits and overheating. Alternatives to lithium, such as sodium and potassium batteries have not historically performed as well in terms of their rate performance and the ability to use them lots of times. This inferior performance is due to the larger sizes of sodium and potassium ions, and their ability to move through the porous carbon electrodes in the batteries. Another issue associated with these batteries is they cannot be easily disposed of at end-of-life, as they use materials that are not sustainable. The cost of the materials is also a factor and there is a need to provide cheaper sources of stored energy. Additionally, lithium is mined in countries such as Chile, Bolivia and Argentina. This mining is very destructive and there are poor human rights records associated with it. Work at the University of Bristol in the Bristol Composites Institute, published in Advanced Functional Materials, and in collaboration with Imperial College, has developed some new carbon electrode materials based on an ice-templating system. These materials are called aerogels, where cellulose nanocrystals (a nano-sized form of cellulose) are formed into a porous structure using ice crystals that are grown and then sublimated. This leaves large channels within the structure that can carry the large sodium and potassium ions.
The performance of these new sodium and potassium ion batteries has been shown to outperform many other comparable systems, and it uses a sustainably sourced material – cellulose.
Corresponding author, Steve Eichhorn, Professor of Materials Science and Engineering at the University of Bristol and a world-leader in cellulose-based technologies, said: “We were astounded with the performance of these new batteries. There is great potential to develop these further and to produce larger scaled devices with the technology.” Jing Wang, lead author and a PhD student in the Bristol Composites Institute, said: “We proposed a novel controllable ice-templating strategy to fabricate low-cost cellulose nanocrystals/polyethylene oxide-derived carbon aerogels with hierarchically tailored and vertically-aligned channels as electrode materials, which can be utilized to well-tuning the rate capability and cycling stability of sodium and potassium-ion batteries. “Benefiting from the renewability of the precursor and scalability at relatively low cost in the environmentally benign synthesis process, this work could offer an appealing route to promote large-scale applications of sustainable electric vehicles and large-scale energy storage grids in the near future.”
Professor Eichhorn said: “In light of these findings, we now hope to collaborate with industries to develop this strategy on an industrial scale and to explore whether this unique technology can be easily extended to a variety of other energy storage systems such as zinc, calcium, aluminium and magnesium-ion batteries, thus demonstrating its universal potential in next-generation energy storage systems.”
UK scientists apply pressure to develop sustainable and affordable catalysis for production of biorenewable chemicals
Dr Zongyuan Zhu from the Process Intensification Group, University of Newcastle
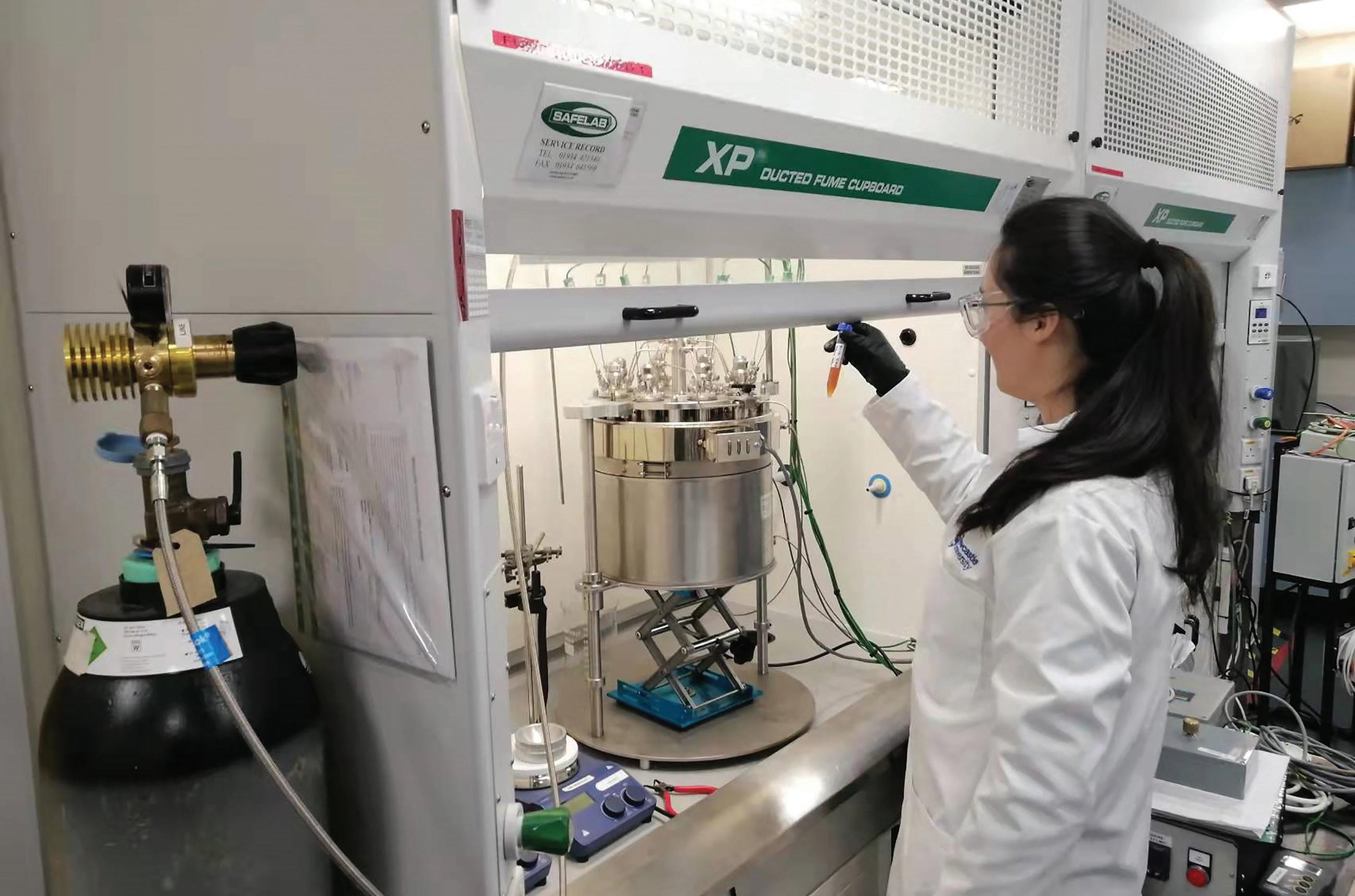
The Process Intensification Group at the School of Engineering, Newcastle University, is using the MultiCell-PLUS High-Pressure Reactor as part of their program of ongoing research to create a new environmentally-friendly generation of catalysts for production of biorenewable chemicals.
Many industrial processes rely on catalysts containing expensive precious and metals, or metals sourced from areas of conflict. A key objective for the Process Intensification Group has been to develop affordable, less hazardous catalysts to achieve similar function and performance to those currently available, keeping synthesis simple and easy to scale up. Dr Fernando Russo Abegão, a Lecturer from the Process Intensification Group, said: “In order to develop our new generation of catalysts we needed to be able to screen a high number of samples, often at high pressure and temperature. In the past we only had isolated autoclaves in the lab.
“These weren’t ideal for screening as they required large amounts of catalysts for testing, and we could only perform one reaction at a time. To be effective we required an instrumental set-up that could provide a fast turnaround, allowing us to quickly test, rationalise, and identify optimal catalyst formulations”. Dr Kamelia Boodhoo, a Reader in Sustainable Process Technology, added: “For screening of heterogeneous catalysts, mass transfer can play a big role in the process. We wanted to ensure that we selected a high-pressure reactor system that was well stirred to keep the particles in suspension at all times, reducing mass transfer limitations. “By doing this, it enabled us to screen the catalyst intrinsic activity, rather than having the results masked by mass transfer limitations. For some of the reactions we investigate, accurate temperature control is also very important – a few degrees under the desired temperature and the reaction won’t progress fast enough, a few degrees above, and we experience unwanted side reactions. “It is therefore important to stay within the correct temperature ranges to ensure optimal catalyst and reaction performance. We looked at various commercially available high-pressure reactors and chose the MultiCell-PLUS system from Asynt as it incorporated parallel agitated reactors with automatic temperature and pressure control. Using this versatile, high-performance system we have already successfully developed a new generation of ‘greener’ catalysts for dehydration of C5 and C6 sugars into furans. Looking to the future, our plan is also to use the MultiCellPLUS for screening of solvents and process conditions”. The Multicell-PLUS was developed by Asynt to provide scientists with a flexible and customisable device for high throughput screening of chemical reactions under high pressure. The reactor allows users to set up a multitude of experimental conditions in each of its 8 reaction cells, ideal for optimisation and screening investigations. Details at asynt.com/product/multicell-plus

Collaboration on bio-based acrylonitrile for carbon fibre applications
The new agreement with Trillium Renewable Chemicals will enable Solvay’s development of sustainable, bio-carbon fibre for use in various applications.
Solvay and Trillium Renewable Chemicals have signed a letter of intent to develop the supply chain for bio-based acrylonitrile (bio-ACN). Trillium will supply Solvay with bioACN from Trillium’s planned commercial asset, and Solvay will evaluate bio-ACN for carbon fibre manufacturing as part of its long-term commitment to developing sustainable solutions from bio-based or recycled sources. The aim of this partnership is to produce carbon fibre for use in various applications such as aerospace, automotive, energy, and consumer goods. Acrylonitrile is a chemical intermediate typically made from petroleum-based feedstocks like propylene and is the primary raw material used in the production of carbon fibre. Trillium’s Bio-ACN™ process delivers acrylonitrile from plant-based feedstocks like glycerol with a lower carbon footprint. “We are thrilled to be partnering with Trillium which aligns well with our Solvay One Planet commitment to more than double our revenue based on renewable or recycled materials by 2030,” said Stephen Heinz, head of composite research and innovation, Solvay. “Innovation partnerships such as this are driven by a desire to make a real-world sustainability impact. Bio-based feedstocks are a key part of Solvay’s sustainability strategy, and we look forward to being a consumer of bio-ACN from Trillium’s first bio-based acrylonitrile plant.” “Trillium’s bio-ACN process technology enables biocarbon fibre,” added Corey Tyree, CEO of Trillium. “We are excited to continue our partnership with Solvay, who have supported the bio-ACN process technology development since 2014. Solvay is a leader in the most rapidly-growing acrylonitrile segment (carbon fibre) and are market leaders in bio-carbon fibre and sustainable development.” Bio-ACN™ is a registered trademark of Trillium.