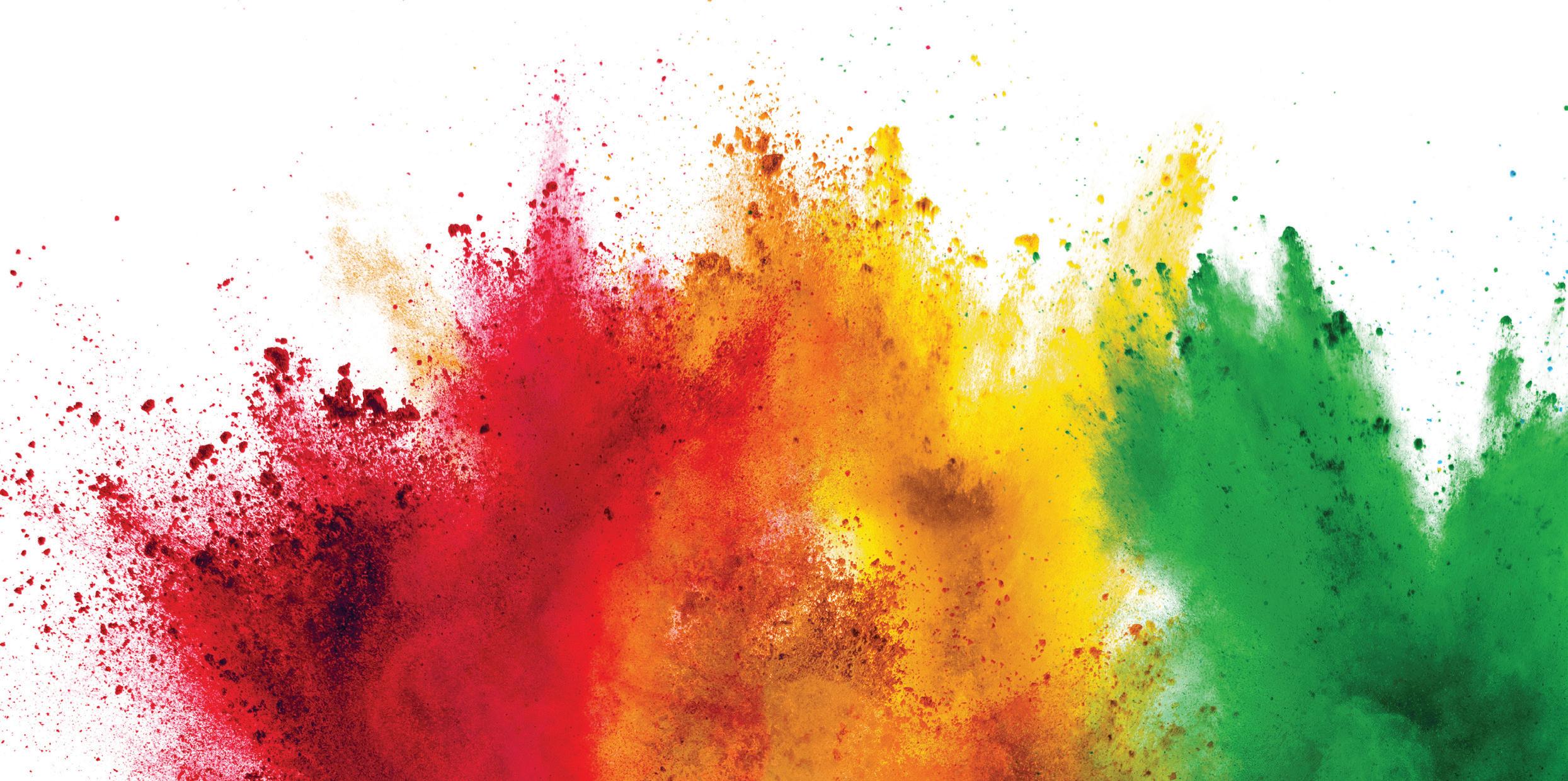
10 minute read
ingredients and blending
Daniel Brown, Biotechnology Lead, at James Robinson Specialty Ingredients, examines the benefits and challenges of using natural chemistry in sustainable production.
Advertisement
Natural chemistry is gaining serious attention given the perceived benefits it could have for sustainability efforts. Major companies are looking to formulate products with ingredients derived from natural chemistry to reduce their carbon footprint and bring more environmentallyfriendly products to shelves. Now, the onus is on ingredient companies to deliver these products, to stay relevant in fast moving markets and meet rising consumer and client demand for sustainable goods. Natural chemistry includes the production of products using micro-organisms. Compared to traditional synthetic chemistry, the use of micro-organisms presents unique challenges, specifically product recovery from the microorganism biomass. Smart thinking early on in a project can help overcome these challenges.
‘ONE-POT’ REACTIONS
Micro-organisms are able to convert simple substrate molecules into complex final products, transforming the substrate through a series of intermediates. Microorganisms can accomplish this with a speed and stereoselectivity impossible for synthetic chemistry to replicate. This can be done in a single vessel, or a ‘one-pot’ reaction.
Honed through billions of years of evolution, a microorganism can accomplish 20 or 30 reaction steps in ‘onepot’ at ambient temperature and pressure in a matter of hours. Development work typically focuses on optimising these ‘one-pot’ reactions to achieve the highest possible yields of product. This however, is only half of the story; the challenge is then to recover the product from the pot.
COMPLEX MATRIX
A relatively high yielding process by the standards of a biotechnologist would be considered a low yielding process by the standards of a synthetic chemist. The nature of micro-organisms means that the final product is not the only molecule that is produced. The micro-organism must also make every other molecule necessary for growth and survival; to do so, it must be surrounded by nutrient rich liquid media. This means the final product will represent only a small fraction of the end process mixture, and is contained within an incredibly complex matrix of large and small organic and inorganic molecules that comprise a biological process. This complexity presents immense challenges for economic product recovery.
A LIVING REACTION
Recovery steps begin the moment that optimal yield of final product is reached, at this point the micro-organism is harvested. However, we must remember that microorganisms are living things and the reaction doesn’t stop there.
Even after harvesting begins, the micro-organism will continue to be biologically active, and reactions will continue, ultimately leading to undesirable degradation or conversion of the end product. These processes can quickly reduce yields and continue to occur even after cell death. As a result, once harvesting begins, the final product must be separated from the biomass as quickly as possible. It is vital to assess just how quickly a product degrades during harvest, especially at scale. It can take a long time to process a large volume of biological material at scale. Something which may take minutes in a laboratory, may take hours on a plant. If the processing time at scale results in excess product degradation, then the process cannot be considered economically viable.
At harvest, the product to be recovered is either contained within the micro-organism itself, or will have been secreted out of the micro-organism into the surrounding liquid media.
Products contained within the micro-organism are more challenging for several reasons. This includes spending time and energy bursting or rupturing the micro-organism, which represents an additional process step. This leads to the release of a cocktail of biologically active molecules and enzymes, contributing further to degradation of the final product. It presents difficulties for further processing, as certain molecules may contribute to undesirable outcomes such as discoloration or skin sensitization.
Products that have been secreted outside of the microorganism are easier to recover than those retained within. In this case, the liquid media containing the product is separated from remaining biomass. Great care must be taken during separation to minimize the accidental rupture of micro-organisms through process-shear. After separation, the products from an extracellular process will be contained within simple media largely composed of inorganic salts or small organic molecules. This makes subsequent isolation of the final product much easier compared to an intracellular product. When selecting projects and processes to pursue, special attention should be paid to whether a final product is contained inside or outside of the micro-organism. A target product may seem desirable but if it can only be produced inside the micro-organism, and the cost of the additional processing steps do not match what a customer is willing to pay, then the process will not be viable.
CURRENT DEVELOPMENTS
Plenty of research and investment has been funneled into optimising product yields by micro-organisms. In recent years there has been a greater appreciation of the importance of product recovery. Reducing time, energy and the number of process steps will make the difference as to whether a product is sustainable from an economic, but also an environmental, point of view. It is not simply the case that bigger and better processing technology will improve product recovery. Product recovery requires a holistic approach, with smart decisions early in a project often making the largest difference:
Smart selection of product producing micro-organisms and smart process development. Consider not just product yields, but parameters such as the strength of cell walls or impact of by-products on viscosity as well. Likewise, some liquid media components may be beneficial for growth or yield, but may impact on separation steps.
Novel techniques such as cell immobilization or magnetic separation may improve product recovery and reduce the impact of shear.
Modification of micro-organisms is an area of active research, and may be done to encourage secretion of a product outside the micro-organism. Modification may also be conducted to move the reaction steps from difficult micro-organisms into benign and well characterized host micro-organisms. This is important when the host micro-organism contains toxic or undesirable by-products.
SMART THINKING
The ability to carefully plan and adapt to challenges is vital when it comes to sustainable product recovery from micro-organisms. Process development is never a linear process, though smart thinking early on can impact product recovery down the line. This can make the difference between a sustainable and unsustainable product and meeting your client’s product requirements and budgets. More details at jrsi.com
ABOUT JAMES ROBINSON SPECIALITY INGREDIENTS
James Robinson Speciality Ingredients is a global supplier of speciality ingredients for the personal care and photochromics industries, backed by over 180 years of heritage and supported by a dynamic team of experts. Founded in 1840, the company underwent a 2019 management buyout that saw it return to the James Robinson brand, with sites in Manchester, Huddersfield, Amsterdam and India.
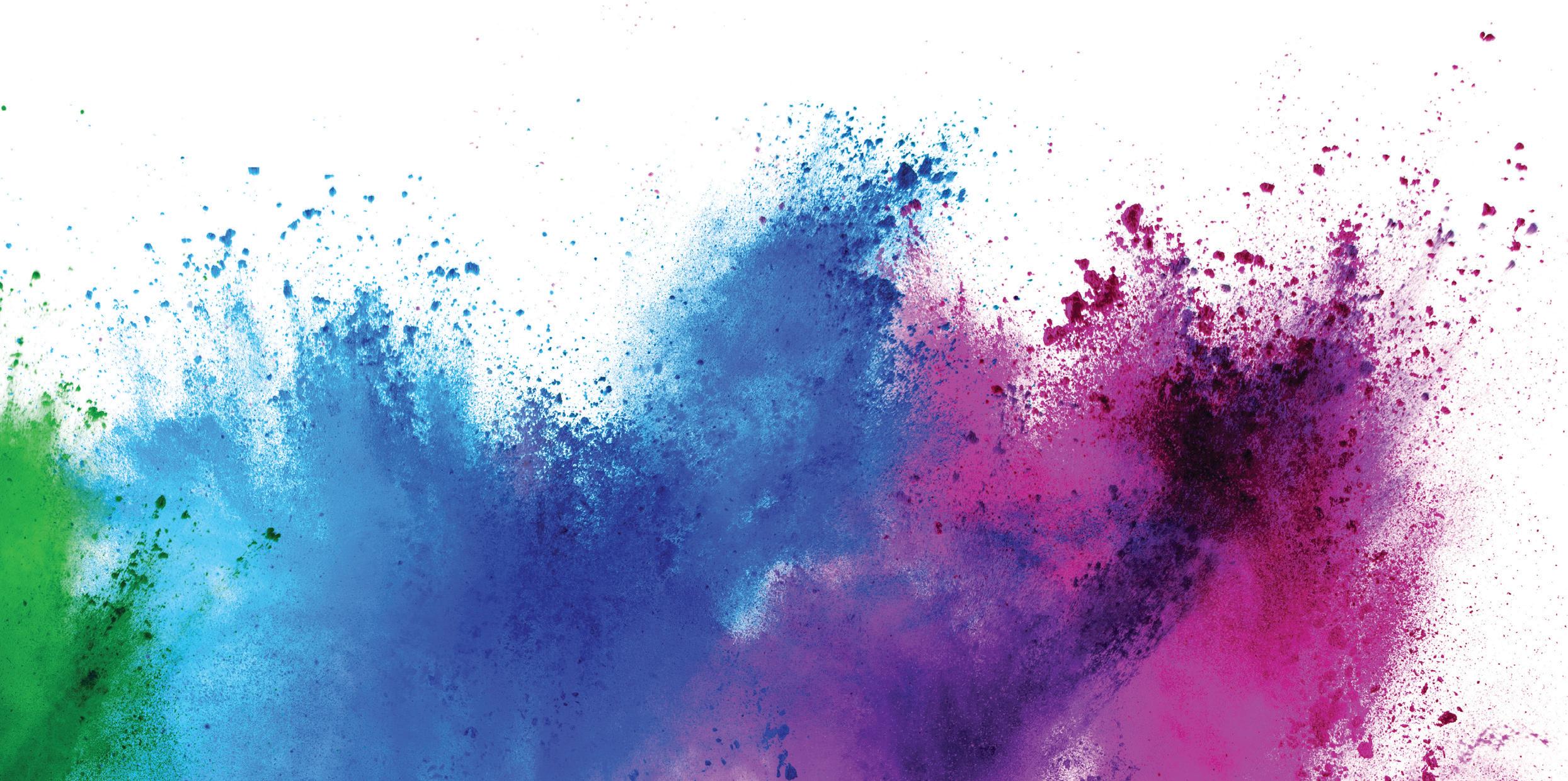
Mini grinding mill closes in on details of ‘green’ chemical reactions
Scientists at the University of Cambridge have developed a new approach for observing mechanochemical reactions – where simple ingredients are ground up to make new chemical compounds and materials that can be used in anything from the pharmaceutical to the metallurgical, cement and mineral industries.

The study, published in Nature Communications and led by Cambridge Earth Sciences’ Dr Giulio Lampronti, observed reactions as materials were pulverised inside a miniaturised grinding mill – providing new detail on the structure and formation of crystals. Knowledge of the structure of these newly-formed materials, which have been subjected to considerable pressures, helps scientists unravel the kinetics involved in mechanochemistry. But they are rarely able to observe it at the level of detail seen in this new work.
The study also involved Dr Ana Belenguer and Professor Jeremy Sanders from Cambridge’s Yusuf Hamied Department of Chemistry. Mechanochemistry is touted as a ‘green’ tool because it can make new materials without using bulk solvents that are harmful to the environment. Despite decades of research, the process behind these reactions remains poorly understood. To learn more about mechanochemical reactions, scientists usually observe chemical transformations in real time, as ingredients are churned and ground in a mill – like mixing a cake – to create complex chemical components and materials. Once milling has stopped, however, the material can keep morphing into something completely different, so scientists need to record the reaction with as little disturbance as possible – using an imaging technique called time-resolved in-situ analysis to essentially capture a movie of the reactions. But, until now, this method has only offered a grainy picture of the unfolding reactions.
By shrinking the mills and taking the sample size down from several hundred milligrams to less than ten milligrams, Lampronti and the team were able to more accurately capture the size and microscopic structure of crystals using a technique called X-ray diffraction. The down-scaled analysis could also allow scientists to study smaller, safer, quantities of toxic or expensive materials. “We realised that this miniaturised setup had several other important advantages, aside from better structural analysis,” said Lampronti. “The smaller sample size also means that more challenging analyses of scarce and toxic materials becomes possible, and it’s also exciting because it opens up the study of mechanochemistry to all areas of chemistry and materials science.”
“The combination of new miniature jars designed by Ana, and the experimental and analytical techniques introduced by Giulio, promise to transform our ability to follow and understand solid-state reactions as they happen,” said Sanders. The team observed a range of reactions with their new miniaturised setup, covering organic and inorganic materials as well as metal-organic materials – proving their technique could be applied to a wide range of industry problems. One of the materials they studied, ZIF-8, could be used for carbon capture and storage, because of its ability to capture large amounts of CO2. The new view on these materials meant they were able to uncover previously undetected structural details, including distortion of the crystal lattice in the ZIF-8 framework.
Lampronti says their new developments could not only become routine practice for the study of mechanochemistry, but also offer up completely new directions for research in this influential field, “Our method allows for much faster kinetics, and will open up doors for previously inaccessible reactions – this could really change the playing field of mechanochemistry as we know it.”
Giulio Lampronti
European biogas offers huge potential for digestate
By Matt Hale
International Sales and Marketing Director, HRS Heat Exchangers
As much as 40 per cent of Europe’s total gas consumption could come from sustainable biomethane by 2050, according to the European Biogas Association (EBA). Their new statistical report highlights the importance of creating sustainable uses and markets for digestate, without which such ambitions will not be realised.

The report analyses the current availability of renewable gases in Europe, notably biogas and biomethane, and concludes that combined production of these energy sources in 2020 was 191 TWh, a figure which is expected to double in the next nine years. In particular the report predicts that biomethane, which saw its biggest year-on-year increase across the bloc in 2020, with an additional 6.4 TWh of production – a figure which is itself predicted to be eclipsed in 2021 as a record number of new biomethane plants become fully operational. The EBA report is the latest in a series of national and international reports which highlight the important role that anaerobic digestion has to play meeting greenhouse gas reduction targets, as well as providing renewable green energy and improving soil health and agricultural productivity. Unlike some other reports, the EBA also provides an assessment of the use of digestate from anaerobic digestion in each country, highlighting the importance that digestate plays in delivering the circular economy benefits of biogas and biomethane generation. The uptake and use of digestate as a sustainable biological fertiliser can be improved with appropriate treatment, such as pasteurisation, to prevent the spread of pathogens, as well as weed seeds and crop diseases. For example, the HRS Digestate Pasteurisation System (DPS) is based on heat exchangers rather than tanks with heating jackets. Using heat exchangers means that effective digestate pasteurisation is possible using surplus heat while allowing additional thermal regeneration levels of up to 60 per cent. This saved heat can then be used for other processes, such as evaporation of the digestate to remove water. The standard 3-tank DPS provides continuous pasteurisation, with one tank being pasteurised while one is filling, and another being emptied. The DPS uses a double tube heat exchanger to heat the digestate to 75°C above the required pasteurisation temperature. This allows for variation in the sludge consistency and its incoming temperature, making sure that the digestate is always properly pasteurised. The tanks can also be used individually, for example to allow for routine maintenance. Details at hrs-heatexchangers.com
Matt Hale
Pasteurising digestate can increase its value and prevent the spread of pathogens and viable weed seeds
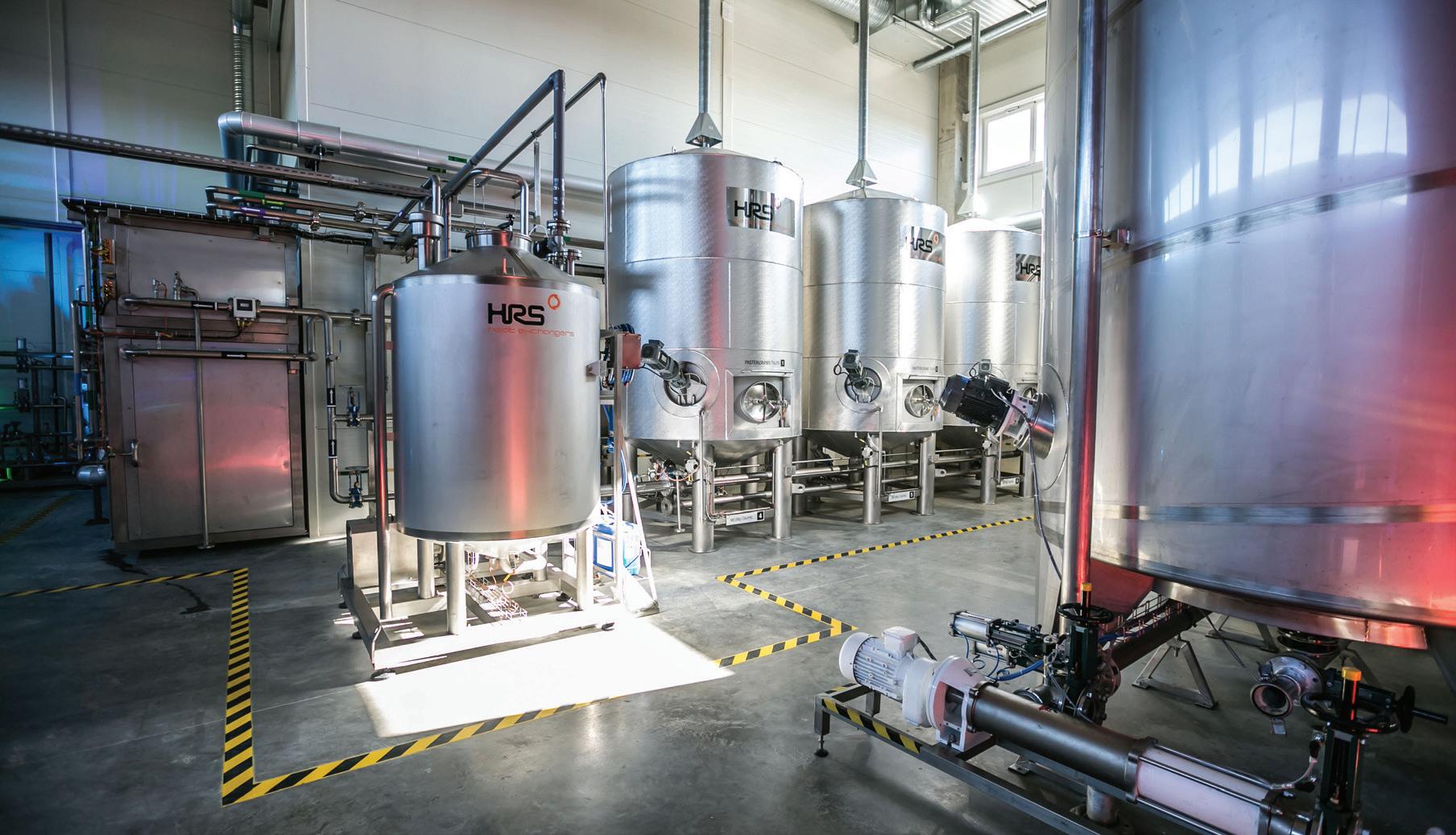