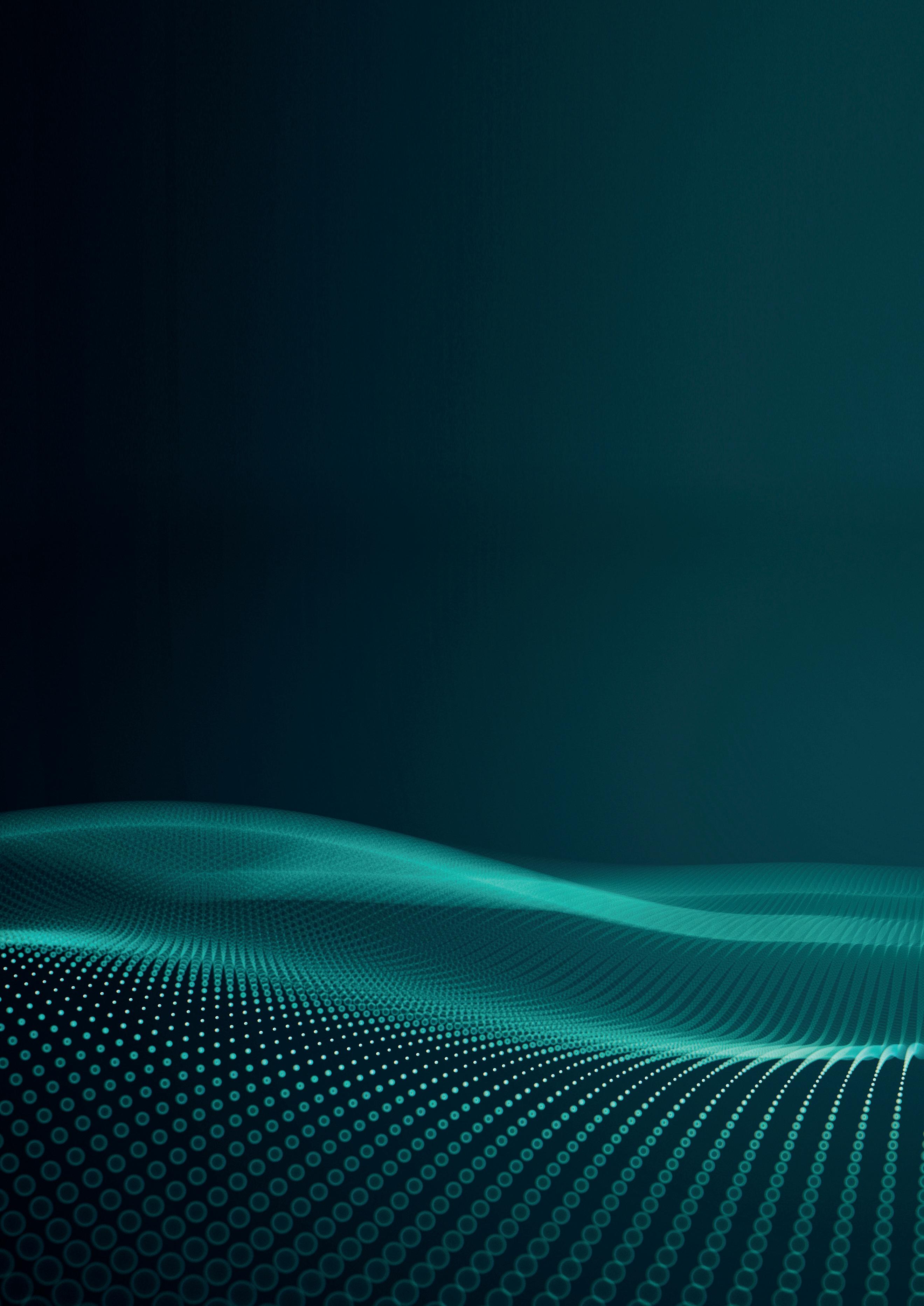
5 minute read
green chemicals
HydRegen’s proprietary enzyme platform implemented into sustainable chemical processes
Bioscience company HydRegen focuses on sustainable chemical manufacturing using their proprietary enzyme based redox platform.
Advertisement
The company has received £385,000 in new funding from the UK Innovation & Science Seed Fund (UKI2S), alongside private investors, to work in collaboration with pharmaceutical and fine chemical companies that want to reduce their costs and environmental impact.
Development of greener and less wasteful processes is at the forefront for many companies who are under increasing regulatory, policy and financial pressures to improve their sustainability. HydRegen is addressing unmet needs in the chemical sector, most specifically around the challenges associated with redox reactions*, their waste generation and use of toxic metals.
The newly raised funds will enable HydRegen to invest in the people and resources required to develop and scale up its platform and subsequent implementation into new chemical processes. HydRegen will work alongside UK-based pharmaceutical and chemical company Almac Sciences, part of the Almac Group, to evaluate a joint technology development project for large-scale manufacture of a commodity chemical.
The project will use enzyme technologies from both companies in a multi-enzyme system to develop a low-cost manufacturing process, producing cost effective green alternatives to commodities.
Since spinning out from the University of Oxford in 2021, HydRegen has focused on implementation of their new strategies for reducing the environmental impact of active pharmaceutical ingredient (API) manufacturing, by switching the power source for biocatalysis from glucose to hydrogen gas. With a vision to replace finite resources,
like metals, with environmentally and economically sustainable alternatives, HydRegen believes it must focus on lowering the barrier to entry for evaluation and scale up of redox bioprocesses. This is something that Governments around the world are also pushing for as they encourage energy intensive businesses to share expertise and come up with radical new innovations to help reduce their carbon footprint.
Contributing £300,000, UKI2S is a national seed investment fund that nurtures innovative businesses, providing the patient, long-term committed capital and strategic advice they need to flourish.
Dr Holly Reeve, CEO at HydRegen said: “We are very excited to have received the funds required for us to take our enzyme platform to the next stage and move another step closer to commercialising our technology in applications that will help our clients meet their Net Zero goals. This additional funding provides us with a huge opportunity to work with world leading speciality chemical companies on scaling up the production of our biocatalysts and ultimately, licensing our technology across a wide range of applications. This research and testing could help HydRegen to become part of the ‘advanced manufacturing tool-box’ across the chemical industry.”
Prof. Tom Moody, VP Technology Development and Commercialisation at Almac, added:
“We look forward to working with HydRegen towards the implementation of a sustainable multi-enzyme system for the manufacture of a commodity chemical and demonstration of the process at scale.”
Andy Muir, Investment Director at UKI2S, said: “Backing companies with sustainability at their core is a major priority that will help shape the economy and human lives in a positive way. We are delighted to support HydRegen’s innovative platform that aims to catalyse the much-needed transition to net-zero chemical manufacturing and improve the pharmaceutical industry’s impact on the environment.”
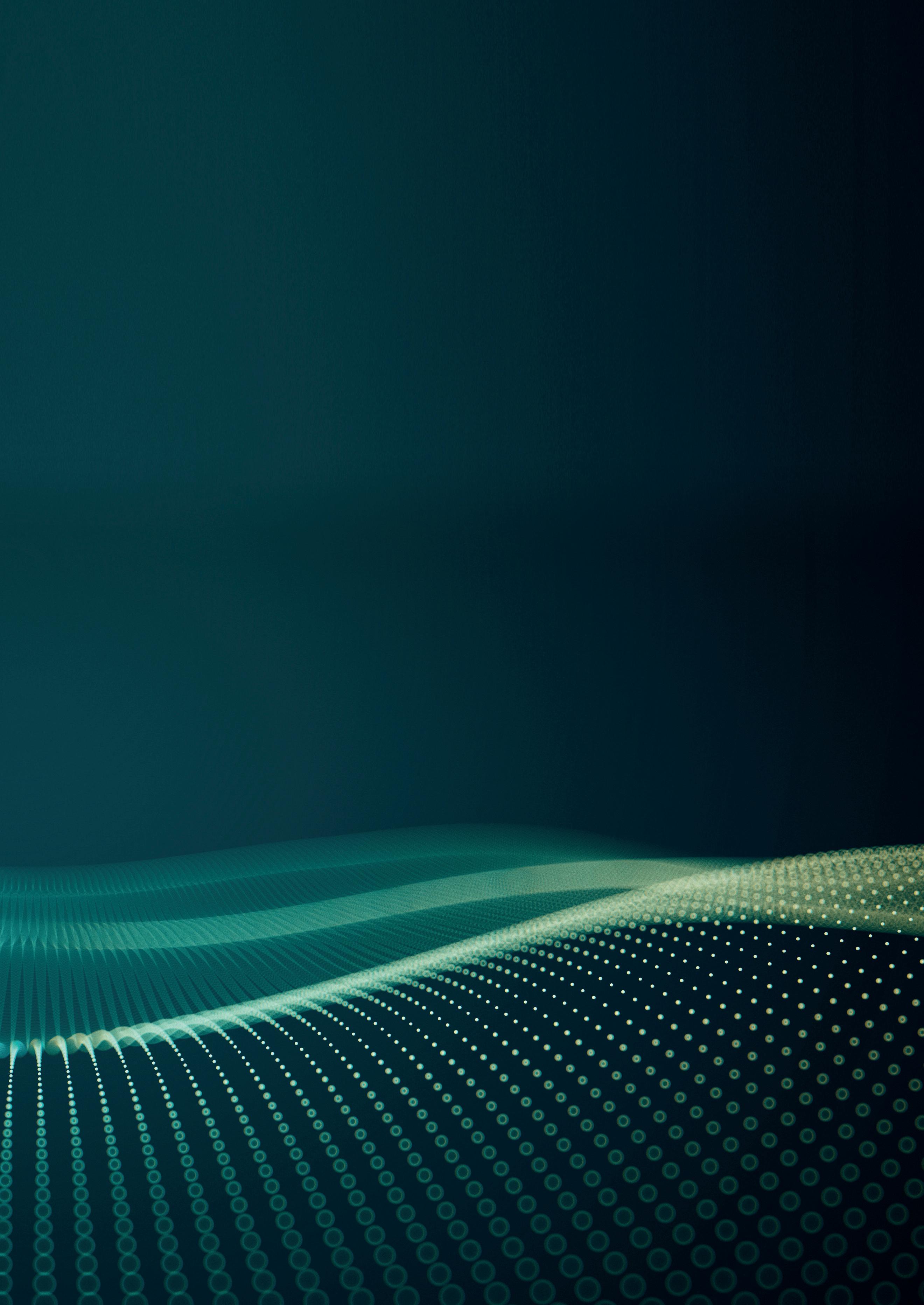
PROF. TOM MOODY, VP TECHNOLOGY DEVELOPMENT & COMMERCIALISATION, ALMAC *Redox reactions are a type of chemical reaction characterised by the transfer of electrons between chemical substances. Redox (reduction-oxidisation) is the gain of electrons, or decrease in the oxidation state, of a chemical substance.
Lithium plant seeks to lower ‘eco’ impact
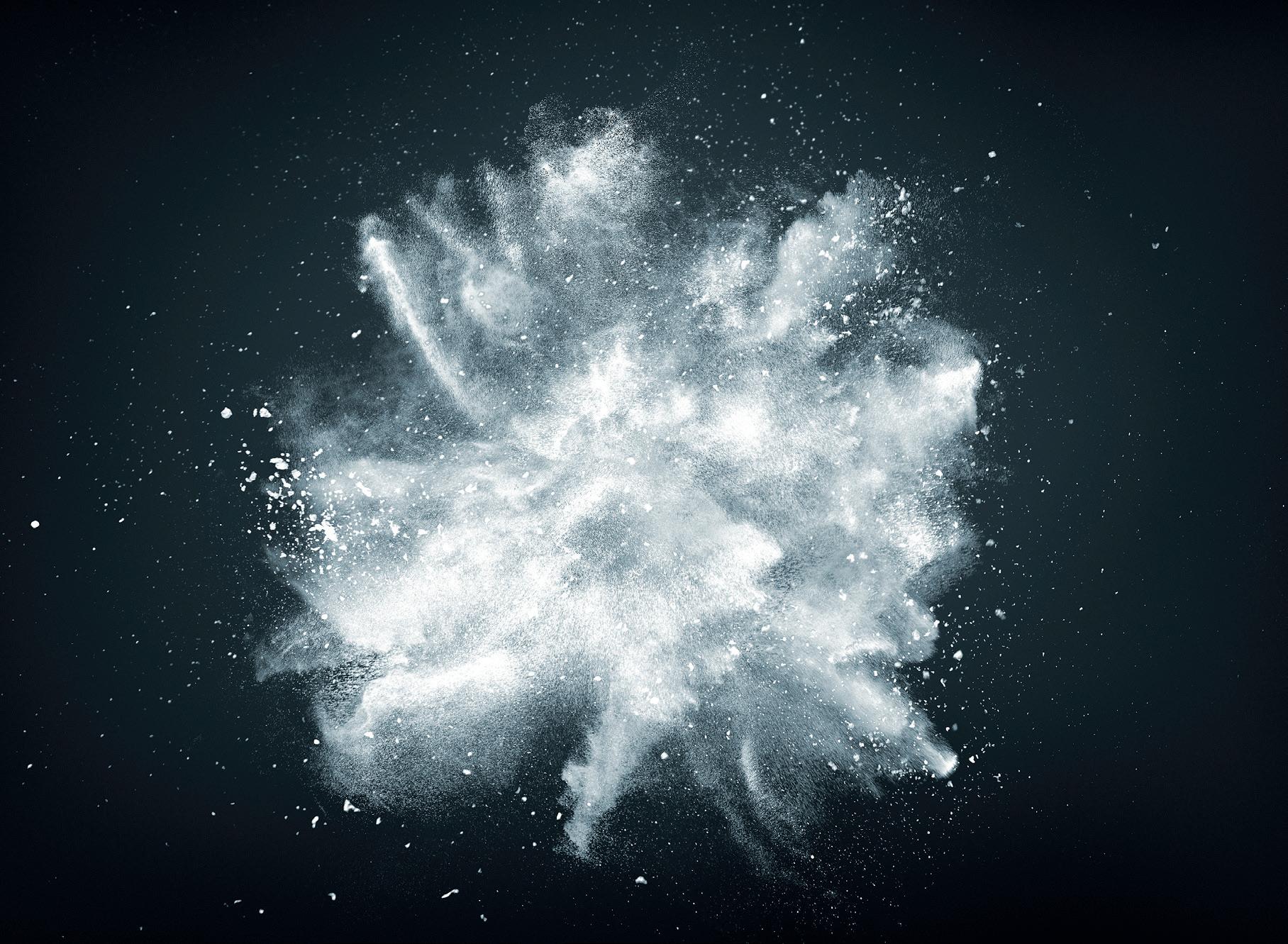
Europe’s first lithium refinery is aiming for production of lithium hydroxide with the lowest possible environmental impact.
The partnership between sustainable supply chain provider Circulor and cleantech company Rock Tech Lithium will provide supply chain provenance and emissions traceability for the plant in Brandenburg, which is expected to produce 24,000 metric tons of lithium hydroxide a year – enough for the batteries of half a million electric vehicles.
Circulor’s work will precede the EU’s battery regulation, which takes effect as early as 2024. “A sustainable and resilient raw material supply chain is increasingly important to our automotive customers, and we are proud to work with Rock Tech to deliver their product with clear proof of origin and embedded CO2 emissions,” said CEO and founder Douglas Johnson-Poensgen. “As the automotive industry prepares for the EU Battery Directive and battery passport provisions, we’re very pleased to support Rock Tech in pioneering low-carbon, European-produced lithium hydroxide.” Rock Tech Lithium CEO Markus Brügmann added: “With the holistic documentation of our value chain, we create a decisive added value for our customers.
“Customers have information about the origin and life cycle assessment of our lithium hydroxide at all times. Based on the work of Circulor and Fraunhofer UMSICHT, Rock Tech will create a material passport for its product.”
Dr Ilka Gehrke, of Fraunhofer UMSICHT which is also collaborating on the project, explained: “We will carry out the life cycle assessment (LCA) of Rock Tech’s production processes. Extensive collection and analysis of their data not only allows Rock Tech to make the production of lithium hydroxide more sustainable, but also supports them in implementing subsequent process optimizations in the most energy and environmentally friendly way possible.”
Fraunhofer UMSICHT specialises in climate neutral energy systems and circular products, and is part of FraunhoferGesellschaft, Europe’s largest organization for applied research and development services.
The Rock Tech and Circulor partnership also entails traceability and CO2 tracking for Rock Tech’s planned recycling at the facility, aiming to become Europe’s first closed loop supplier of lithium hydroxide. Currently, only one percent of lithium from batteries is recycled worldwide. By 2030, Rock Tech Lithium aims to achieve 50 percent of its materials to come from recycled batteries.