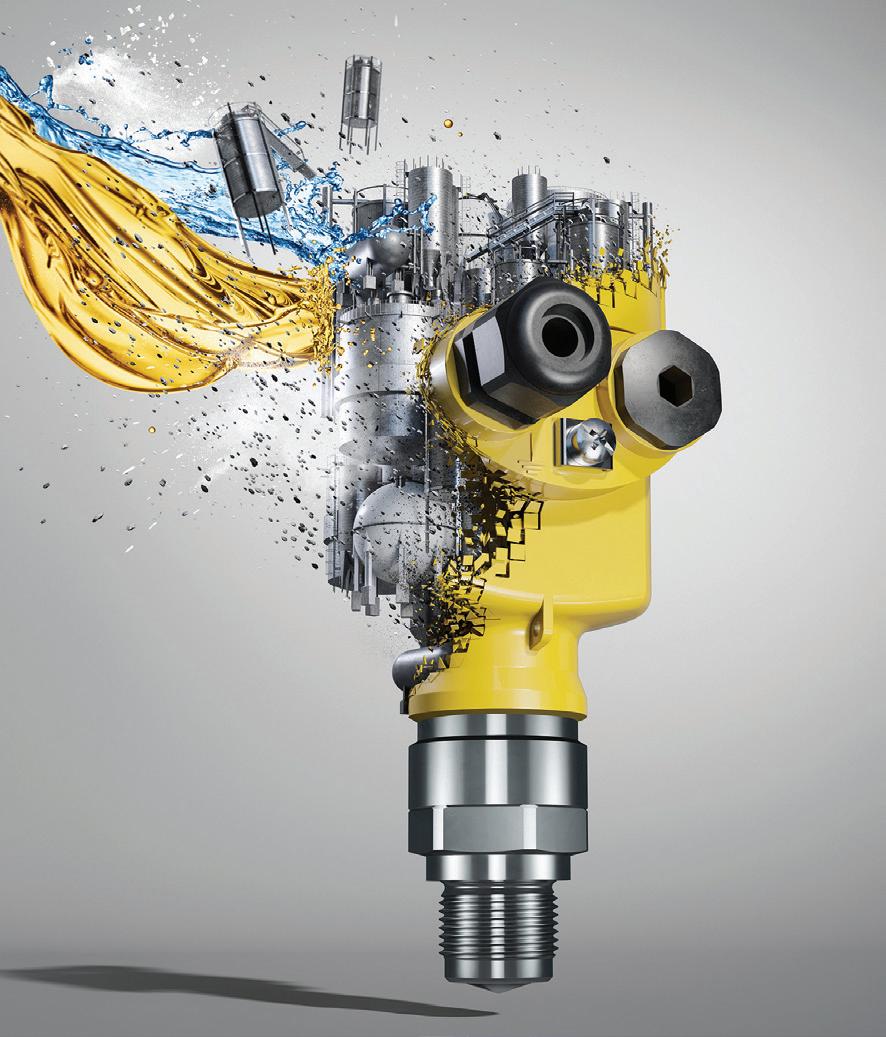
18 minute read
www.chemicalindustryjournal.co.uk / issue
A new choice for radar level sensors: VEGAPULS 6X
Traditionally, the search for a suitable level sensor begins by thinking about things like: what solution would be best for my application? How can I ensure I choose the correct and most reliable device for a successful outcome on my project? Of course non-contact radar offers great answers for all of these questions.
Advertisement
This is often followed by thoughts and investigations about the properties of the product to be measured, could it influence a sensor, as well as the installation and operating environment. Furthermore, process conditions like: temperature, pressure, the presence of abrasive, aggressive materials, corrosive chemicals, or dusty conditions and build up in bulk solids, may also give cause for concern. Many of these details are often well known to the user. What they can be less sure about is, “Which model is best?”. Sometimes differences can be subtle. Would the highest specification option, perhaps with exotic materials, be the right choice to be on the safe side? Or a basic design, that seems to fit the job, but what if it’s not up to the performance needed? These and other questions make one thing clear: with such wide ranges, selecting the right one can be difficult. Customers have to match up their application conditions to the large variety of radar sensors, models, antennas and frequencies on offer. A user needs a good understanding of the market, but they are often the first to admit they are not experts. It takes know-how, experience and time, to avoid making bad investments and get a reliable measuring system.
So its time to challenge this laborious, stressful and timeconsuming process. It’s being turned on its head with a new radar sensor generation. Florian Burgert, one of the closely involved radar product managers says. “We now offer one radar level sensor for all applications, regardless of liquids or bulk solids: it’s called a VEGAPULS 6X. The sensor selection is simpler than ever, in a few mouse clicks and key strokes, your selection is selected and tailored to suit. Of course a radar specialist is on hand for advice and consultation; online, by phone or in person.” This new way of selection makes it easier for the customer and specialist to collaborate, too. At the heart is not just the first, but a second-generation in-house radar chip designed specifically for level measurement. “The result consolidates three decades of radar experience”, says VEGA product manager Jürgen Skowaisa, “In scope and functionality, this chip is unique. With low energy consumption, super-high sensitivity, universal applicability, as well as a direct connection of chip and antenna system, this delivers maximum performance.”
ALL-ROUND PROTECTION
For safety, VEGAPULS 6X offers SIL 2/3 with class-leading functional safety characteristics to IEC 61511. It also offers a first in “cybersecurity”, meeting IEC 62443-4-2 standard for system security, but at the sensor level. The continuous, internal self-diagnosis system is one of the most comprehensive in the market, delivering higher plant availability, and also better sensor performance.
FOCUSING ON THE APPLICATION
Jürgen sums up: “It’s about maximum simplification. Until now, there were many different sensor models for an application. With the VEGAPULS 6X, there is just one sensor for all.” Even setup and commissioning, is reduced to a minimum. “Our customers can even order a sensor ready calibrated and pre-set for the application. Which means it just needs installing and connection.” adds Skowaisa. “It doesn’t get any easier than that.” With VEGAPULS 6X there is now only one radar sensor – but it is suitable for all applications
A PROVEN PLATFORM
This brand new radar still maintains its roots in the well-established plics® platform, with compatibility and close affinity to all existing process devices from the manufacturer. This offers benefits of familiarity and commonality, and future cross-platform developments, perfectly demonstrated with the Bluetooth option brought out in 2018, which was instantly compatible to all plics® transmitters from 2002.
A RADAR MADE FOR PEOPLE
This latest radar level technology features five main innovations: higher (cyber and process) safety, better self-diagnosis, new dedicated radar chip technology with wider application capabilities for simpler selection and adjustment. Jürgen Skowaisa summarises; “Our technology has reached such a high level today that reliable measurement is no longer the issue. With VEGAPULS 6X, you get the right sensor for the application, but we still pride ourselves that our engineers are always there for customer support, partnership and collaboration.” Jurgen concludes, “Now, the user no longer has to worry about model numbers or technology – with 6X the measurement will simply work.” More information available at www.vega.com/radar
info.uk@vega.com OVER 1 MILLION INSTRUMENTS IN USE WORLDWIDE
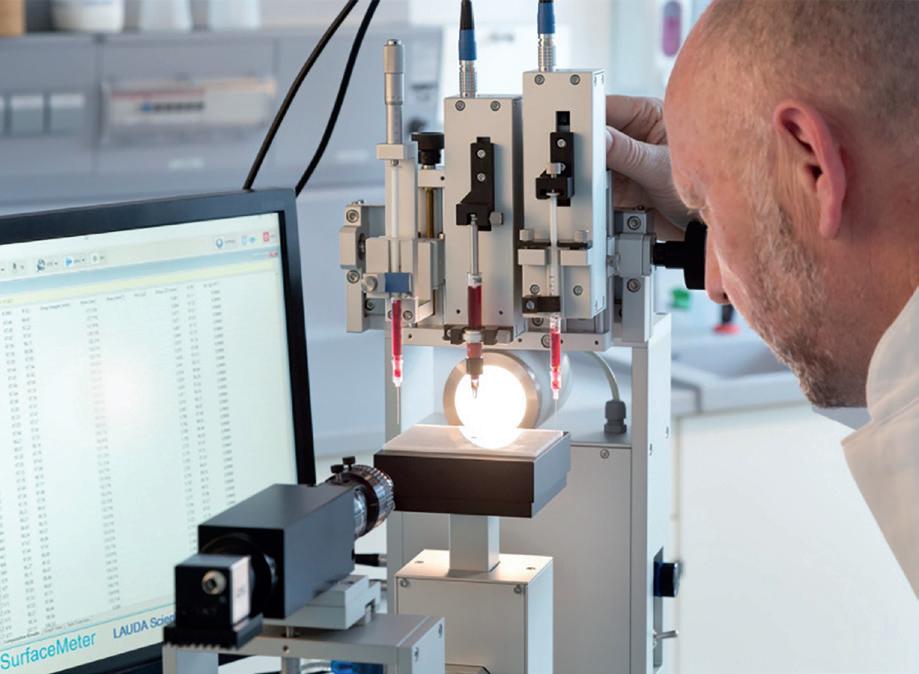
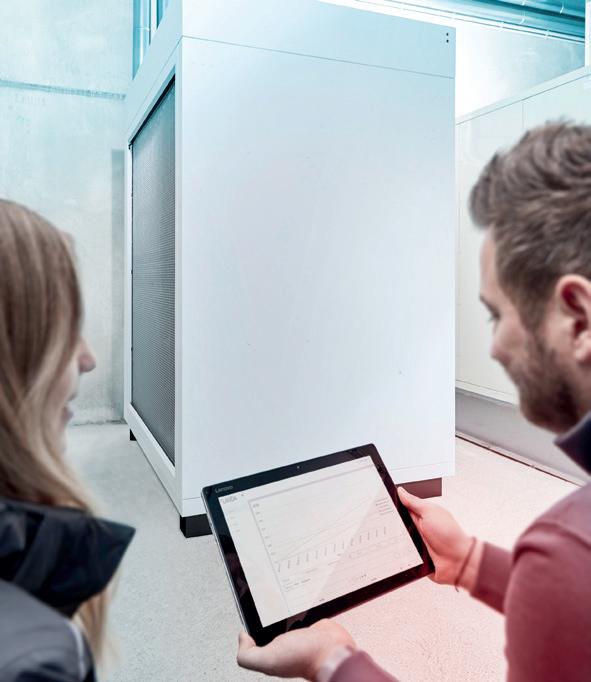
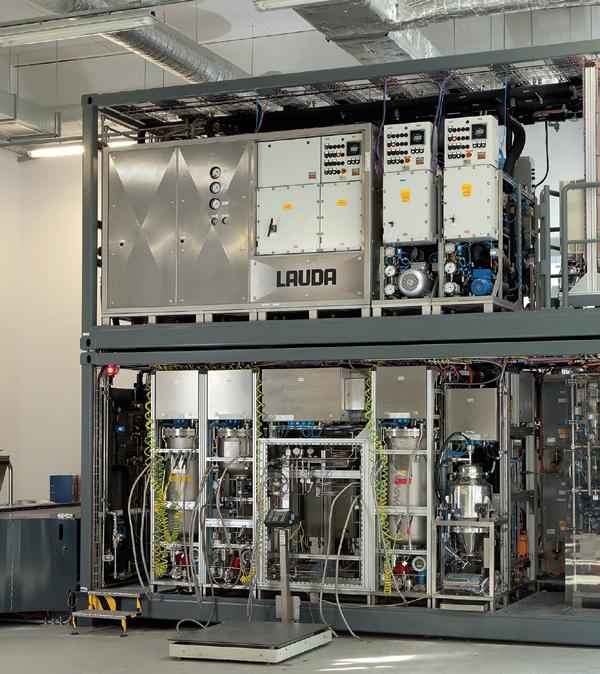
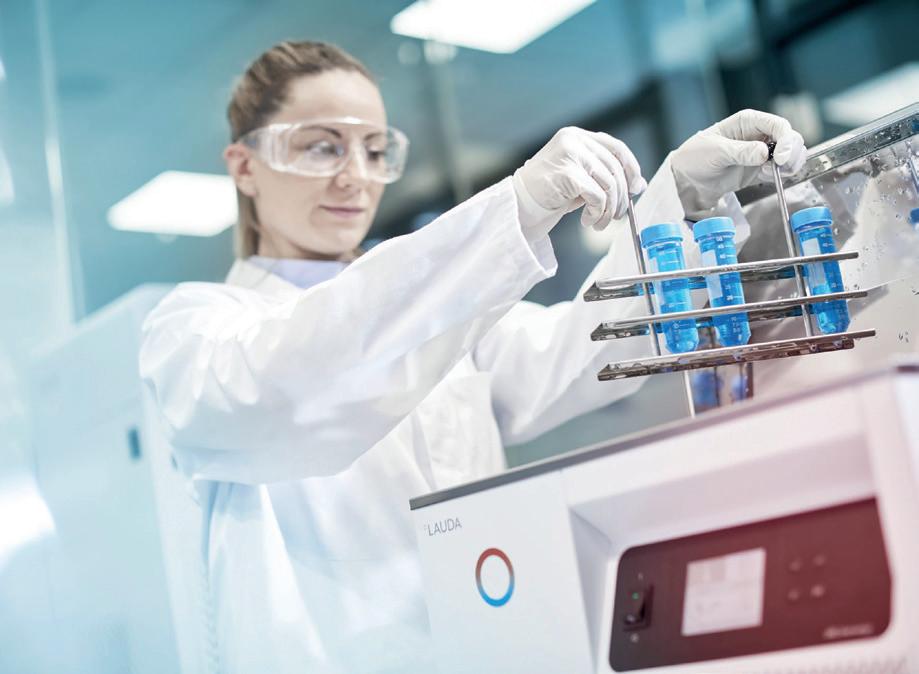
LAUDA – Experts In Thermal Control And Measurement Providing Innovative Solutions For Thermal Process Control, Chilled Water Applications, Water Baths, Freezers, Incubators, Shakers, Stills, Tensiometers, Viscometers And Contact Angle Measurement.
LAUDA continues to provide an expanding range of feature-rich, future proof solutions with energy efficiency and connectivity front of mind, serving a diverse range of industries including chemical, pharmaceutical, biotechnology, oil and gas, composites, automotive, aerospace food & beverage, brewing, digital printing, laser and beyond. LAUDA’s new range of water chillers has been designed not only to comply with the new Eco-design directive, but to surpass it through the innovative use of variable speed modules that automatically reduce their duty cycle in line with the cooling demand hence reducing energy consumption and running costs, giving a tangible return on investment for the user, whilst ensuring full compliance with the latest regulations on refrigerant (fluorinated) gases. Further portfolio expansion delivers the new LAUDA ‘Versafreeze’ ultra-freezers, (deep-freeze storage down to -85°), and higher power ‘Integral’ process circulators, (process control from -90 to 320°C with >25kW of cooling @20°C), with pressure overlay options to increase the working range of water / glycol up to 140°C. Furthermore, for applications requiring customised solutions tailored to individual requirements, we offer a made-to-measure design service using a long-established and highly skilled team. Project engineering is a core competence of LAUDA and using the modular engineering approach we can design and scale a system specifically matched to the application needs. With the capability to provide accurate heating and cooling in the range -150 to +550 °C using a variety of proven modules including heat transfer systems, process cooling systems, secondary circuit systems, fired heaters and molten salt plants, we are able to provide unique, costeffective solutions unparalleled by others. Beyond temperature control, LAUDA has a well-established suite of solutions for measuring viscosity and surface/ interfacial tension aimed at the development of polymers, oils, and surfactants. We look forward to hearing from you. Contact details:
T: +44 (0)1780 243118 E: info@lauda-technology.co.uk
www.lauda-technology.co.uk www.linkedin.com/company/lauda-technology-ltd www.facebook.com/LAUDA.UK/ https://twitter.com/lauda_uk
At Blended, we have been supplying specialist chemicals and gases for almost 20 years. The company prides itself on offering the optimal ‘blend’ of speciality chemical expertise, exceptional service, and positive attitude that customers can rely on.
From Anhydrous Ammonia and Carbon dioxide to a line a glycol-based heat transfer fluids, a team of industry experts and a full-service testing laboratory, Blended are the ideal partner to supply your chemicals and gases. We have developed strong relationships with our clients and endeavour to provide the best, ongoing service with the food and drink industry, heating, and cooling sector and even wastewater treatment plants. Whatever the challenge, we have the equipment, resources, and people to meet your project needs. Coolblend, by Blended, is a complete range of highperformance heat transfer fluids that can be used in a wide variety of applications requiring the need for glycol based heating and cooling liquids. Our new line of cleanings solutions: Serviceblend includes pre-cleaner, biocide, and online cleaner as a highly effective biocidal flush. This product works optimally with our glycol-based products but also as a stand-alone product for servicing and maintenance of equipment. As part of our ongoing service to our customers, we provide glycol testing for prevention, protection and catching any issues as early as possible, resulting in significant cost saving benefits. Maintenance is minimised as the threat of a costly shutdown that would be necessary if a problem escalated into a system failure is vastly reduced. An example is testing on shipments before they leave the premises to allow for benchmark figures to be given and, if anything is detected in the tests, it means low-cost preventative maintenance can be undertaken now.
OUR RIGOROUS TESTING INCLUDES:
pH levels check
The most common route of glycol decay is oxidation, this route causes the formation of acidic chemicals which are corrosive. Under normal circumstances corrosion inhibitors will prevent corrosion from small amounts of acidic compounds. Many corrosion inhibitors are most effective at basic pH levels and if the formation of these acidic compounds lowers the pH it can reduce the effectiveness of the corrosion inhibitor or in some cases stop it working entirely. Measurement of the glycol pH allows the monitoring of the situation so preventative action can be taken if needed.
Determination of iron content
If corrosion is occurring inside your system, then this can be accurately monitored via the iron content of the glycol. Most systems are built with steel and if the metal begins to corrode this can be readily detected by increasing iron content in the glycol mixture. Our spectroscopic method allows for very accurate determination of the iron content in samples.
Review of conductivity
This measurement allows for determination for dissolved salts in the glycol mixture. These dissolved solids promote corrosion and can indicate that incorrect water is being used for the loading or top up of the system.

Undertake refractometry
This provides an accurate measurement of glycol within the system. With this information it should be possible to determine if a leak has formed on your system somewhere. As water is used to top up the system as per usual (due to water loss) the glycol content will decrease. It is key to maintain glycol levels to keep the frost protection for your system.
Assess Turbidity
This is a measure of how cloudy the glycol is. Most problems that can occur in your system be it corrosion or otherwise will cause the glycol mixture to go cloudy. Turbidity measurements allow you to measure this and determine if your glycol is becoming contaminated with suspended solids.
Ammonia Presence Testing
Using our advanced spectroscopic equipment, it is possible to determine if the glycol has been contaminated with ammonia.
This would be indicative of cross contamination between primary and secondary refrigerant. There is no doubt that pre-emptive testing should be a core part of any maintenance plan as it saves suppliers and companies both time and money. Blended Products is delighted to offer this service free to its customers but if you are not yet a customer and would like to know more, Blended is still happy to help. Keep an our out for technical manager, Ben France, upcoming whitepaper explaining more on this subject at
www.BlendedProducts.com
What triggers a review of Hazardous Area Classification and DSEAR Risk Assessment?
The Dangerous Substances and Explosive Atmospheres Regulations 2002 (DSEAR) is a set of rules and regulations which must be followed by employers to ensure risks from fire, explosion and similar events are sufficiently reduced.
DSEAR applies to all workplaces where dangerous substances are present, used, or produced. A dangerous substance can be any substance that has the capacity to create a fire or explosion or result in the corrosion of metal. These substances are inclusive of flammable liquids, gases and dusts. DSEAR assessments are required to be carried out by not only large corporations, but also medium and small sized businesses. Employers must reduce the risks associated with the dangerous substances by:
Identifying all dangerous substances produced, used or stored onsite, including potential mixtures of incompatible substances.
Assessing the risk in the workplace due to dangerous substances.
Classifying those areas where explosive atmospheres may be present. Introducing control measures to eliminate or reduce the risks.
Ensuring control measures are in place to mitigate the effects of any incident.
Ensuring procedures/training are in place to deal with incidents involving dangerous substances. In order to ensure that the site in question continues to manage their risks appropriately, it is important that the risk assessment and supporting documentation is routinely reviewed. There is no legal requirement in terms of how often a DSEAR assessment should be reviewed, however, it is recommended that at least every 3-5 years is a sensible timeframe to ensure any changes in the work environment which could increase the likelihood of a serious accident are properly considered and do not go unnoticed. It is important that this happens, as over the years lots of small insignificant changes, can creep into being cumulatively substantial ones.
There are many possible reasons which can stimulate the need for a review, one of which is changes to the plant or processes which are carried out on a plant. Not all changes are obvious, consider changes to the team, old equipment being replaced, changes to materials stored, changes to process conditions and changes outside of your control in the surrounding areas. A change to process equipment or process conditions has the potential to impact hazardous area zoning and therefore have a knock-on impact for required ignition controls. Changes to raw materials could lead to the introduction of a substance with a lower flashpoint and therefore impact zoning requirements. Changes near an establishment such as industrial developments beyond the site boundary may affect the potential consequences or frequency of ignition. Other changes which may result in the need to review your DSEAR assessment may include a change in knowledge and understanding. This may come from wider industry research, publications or learning from incidents. Industry research may impact the extent of hazardous area zoning which has specifically been the case recently for high flashpoint liquids following research around flammability of mists.
Ensuring that effective management of change (MOC) processes are in place at the site may be an important first step in triggering the need to review DSEAR documentation. But question your process, would wider industry changes trigger a review of your DSEAR assessment? How do you keep up to date with industry news and learnings from incidents?
It is important that any DSEAR assessment is reviewed at regular intervals, to ensure it remains fit for purpose. Only when hazards are properly understood are they effectively managed. The review process should go beyond a paper exercise. Reviews are a great opportunity for continued risk reduction. Technology is always improving, meaning that since your last review there may be better measures available to you.
James Park and Carolyn Nicholls enquiries@ras.ltd.uk
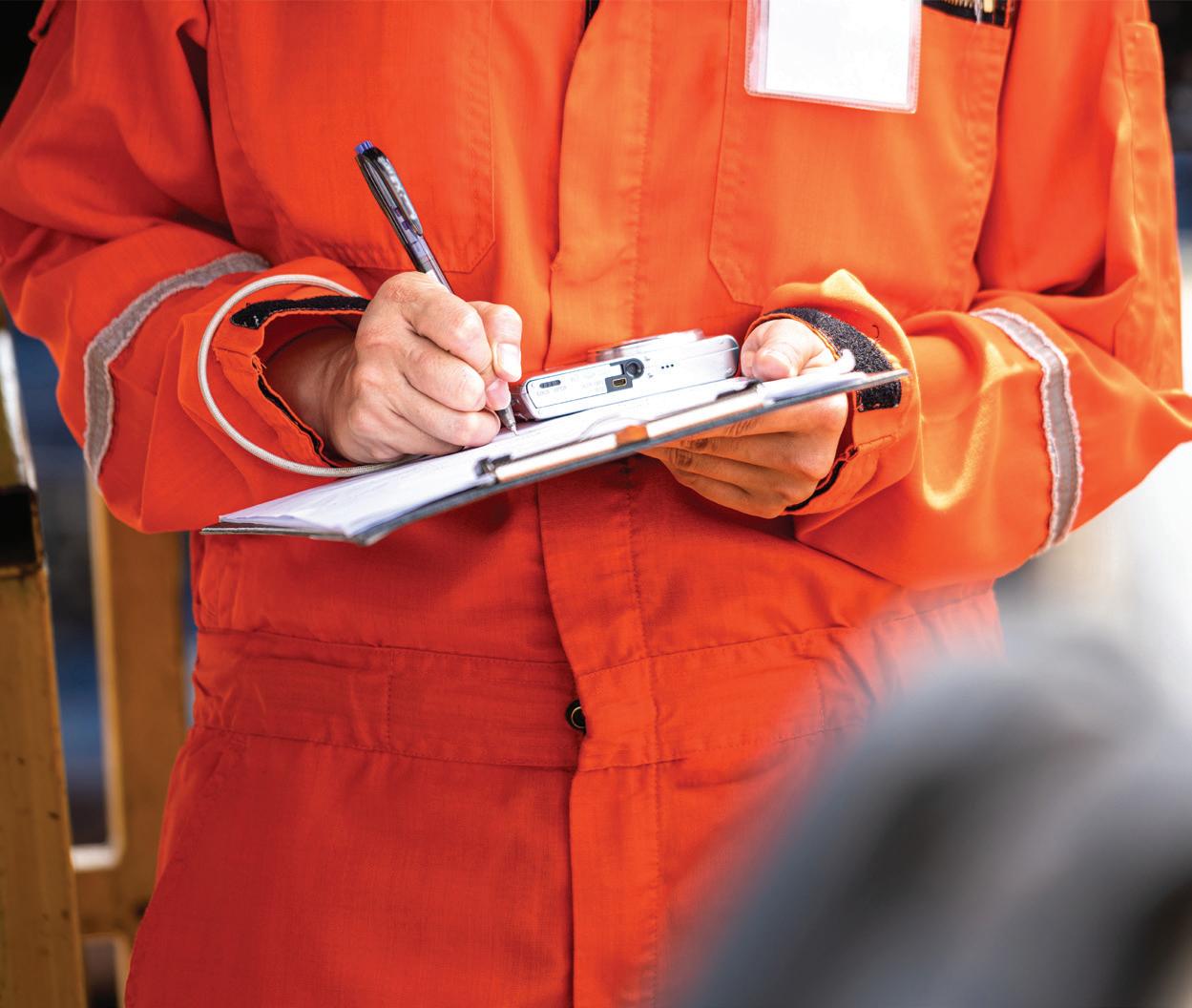
RAS
RISK & HAZARD MANAGEMENT
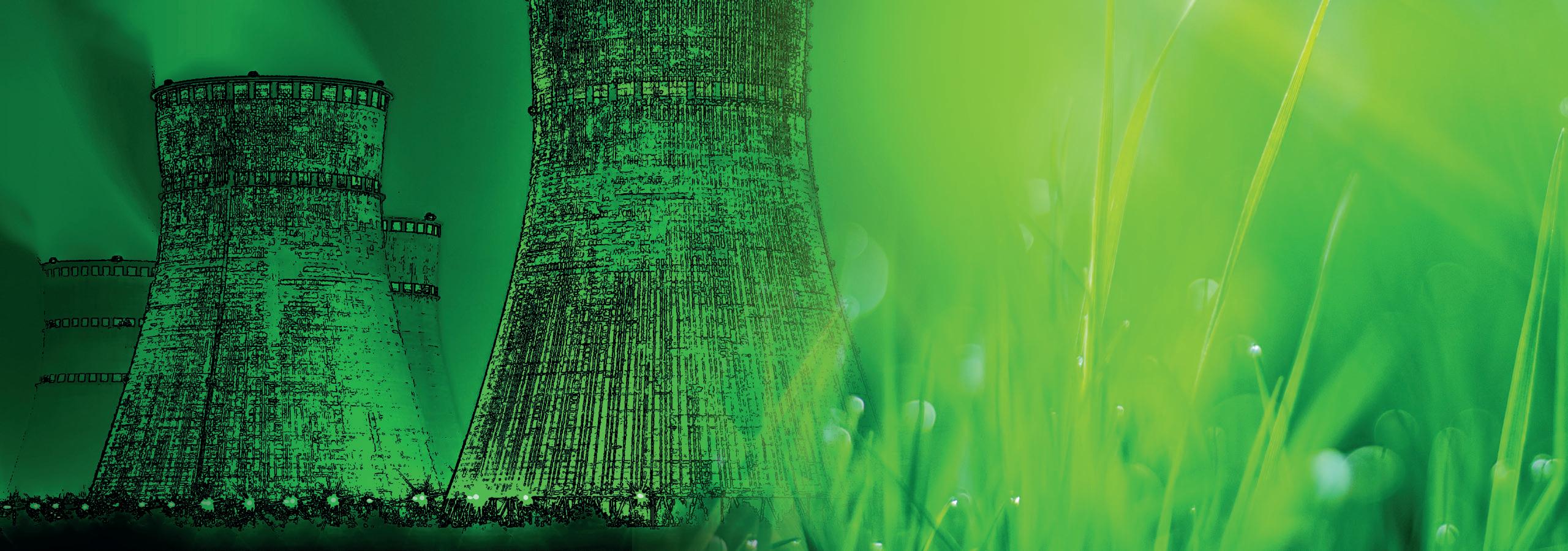
Understanding and facilitating the effective management of risk is our core business. Our expertise covers the full range of risk assessment and management services across:
Safety Risk Business Risk Environment Risk
Only when the risk facing an organisation is well understood can it be effectively managed. Key to the successful identification, assessment and management of risk is engagement with the right people, using the right processes at the right time. We believe we are different to many of our competitors and our approach is distinctive, we don’t always walk the well-trodden path but look at each client’s particular risk context and develop a tailored solution, working in partnership with our client.
We work across all aspects of risk, from Quantitative Risk Assessments and Predictive & Consequence modelling, through to the ‘softer’ risks which may affect an organisation’s reputation.
Upramolecular chemistry breakthough for more efficient perovskite-based solar cells
Supramolecular chemistry which deals with multimolecular systems, (in particular halogen bonding, ie the intermolecular interaction involving halogen atoms (I, Br and Cl) in organic molecules) can help improve the performance of perovskite-based solar cells, enabling them to achieve high levels of efficiency and high stability.
This is the conclusion of researchers at the Politecnico di Milano who have published in Angewandte Chemie
International Edition.
Organic-inorganic hybrid perovskites - ionic compounds consisting of small organic cations and metal halides - have been known about since the 19th century, but they have only recently been used in optoelectronics for the construction of lasers, diodes, photodetectors and solar cells. In particular, the first perovskite-based photovoltaic cell was produced in 2009 and since then there has been intensive research into achieving an efficiency of more than 25%, which would surpass even the silicon that currently dominates the photovoltaic market. The low cost and excellent performance of perovskites make them very attractive for photovoltaic applications, but there are still a number of problems that prevent these materials from entering the market. First of all, there is their low stability when it comes to air and humidity. In addition, the presence of defects, i.e., imperfections in the crystal lattice, can generate ‘trap states’ that interfere with the movement of charge carriers (electrons and holes) generated by light within the material, trapping them and causing electrical energy losses. Generally, these trap states are unbound halide ions that can move under the effect of an electric field and recombine with holes.
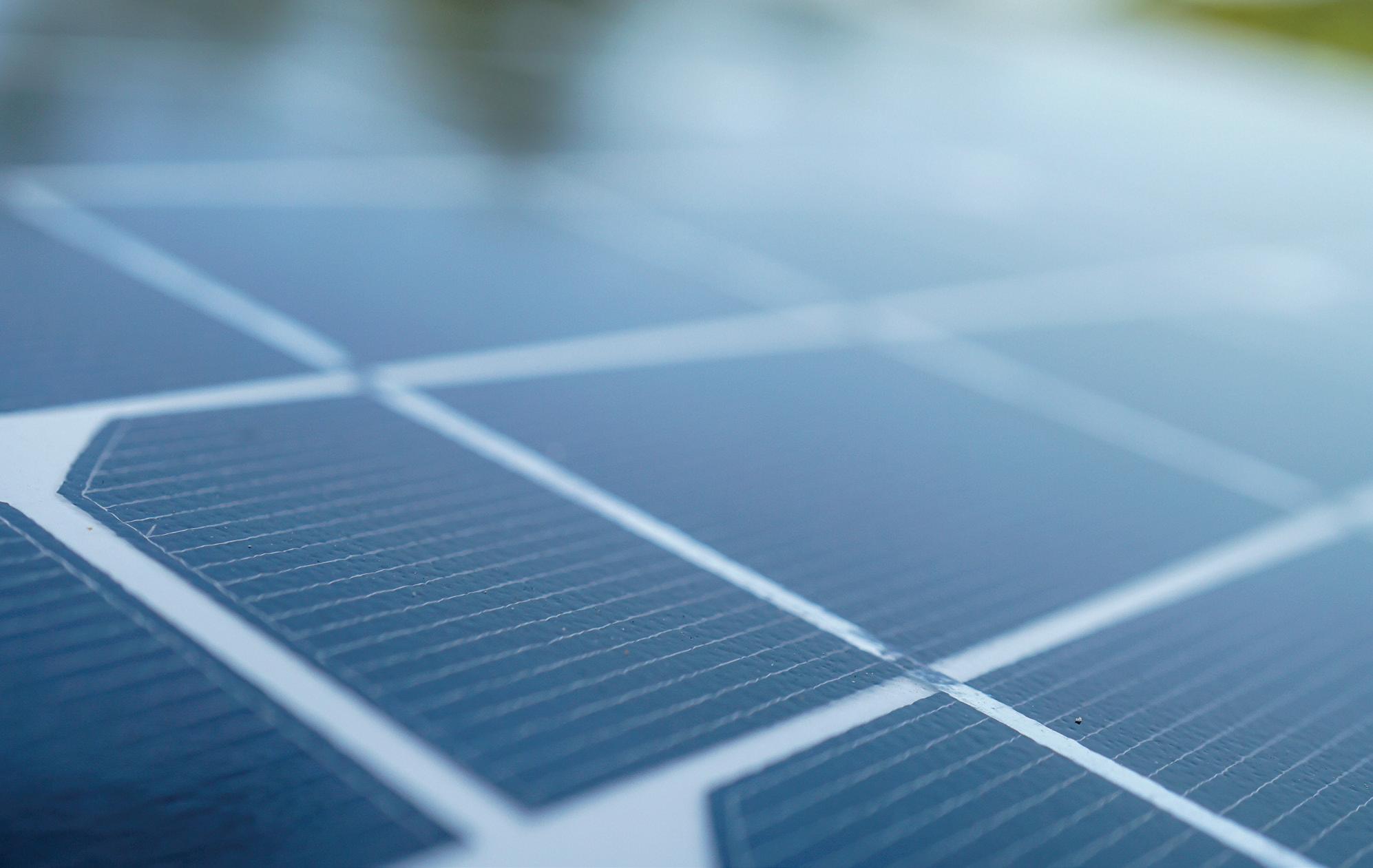
The study conducted at the Politecnico showed that the use of additives capable of forming halogen bonds with the halide ions present in perovskites provides significant advantages for the development of solar cells with better crystallinity and greater stability. Halogen bonding enables fluorinated molecules to be introduced, which passivate the surface halides to produce hydrophobic and waterrepellent perovskites. In this way, trap states are blocked and efficiency is increased. In addition, the surface modification of perovskite with bifunctional molecules capable of forming halogen bonds enables better integration of the perovskite within the solar cell, facilitating the generation of electrical current. From the data reported, it appears that halogen bonding has considerable potential for the development of a new generation of solar cells based on perovskites. However, a better atomic/molecular understanding of these materials is needed to fully exploit the advantages of halogen bonding. The paper was written by Gabriella Cavallo, Giancarlo Terraneo and Pierangelo Metrangolo of the Department of Chemistry, Materials and Chemical Engineering ‘Giulio Natta’ of the Politecnico di Milano in collaboration with Laura Canil and Antonio Abate (an alumnus of the Politecnico di Milano) of the Helmholtz Zentrum Berlin fur Materialen und Energie.
Michael Kriegel
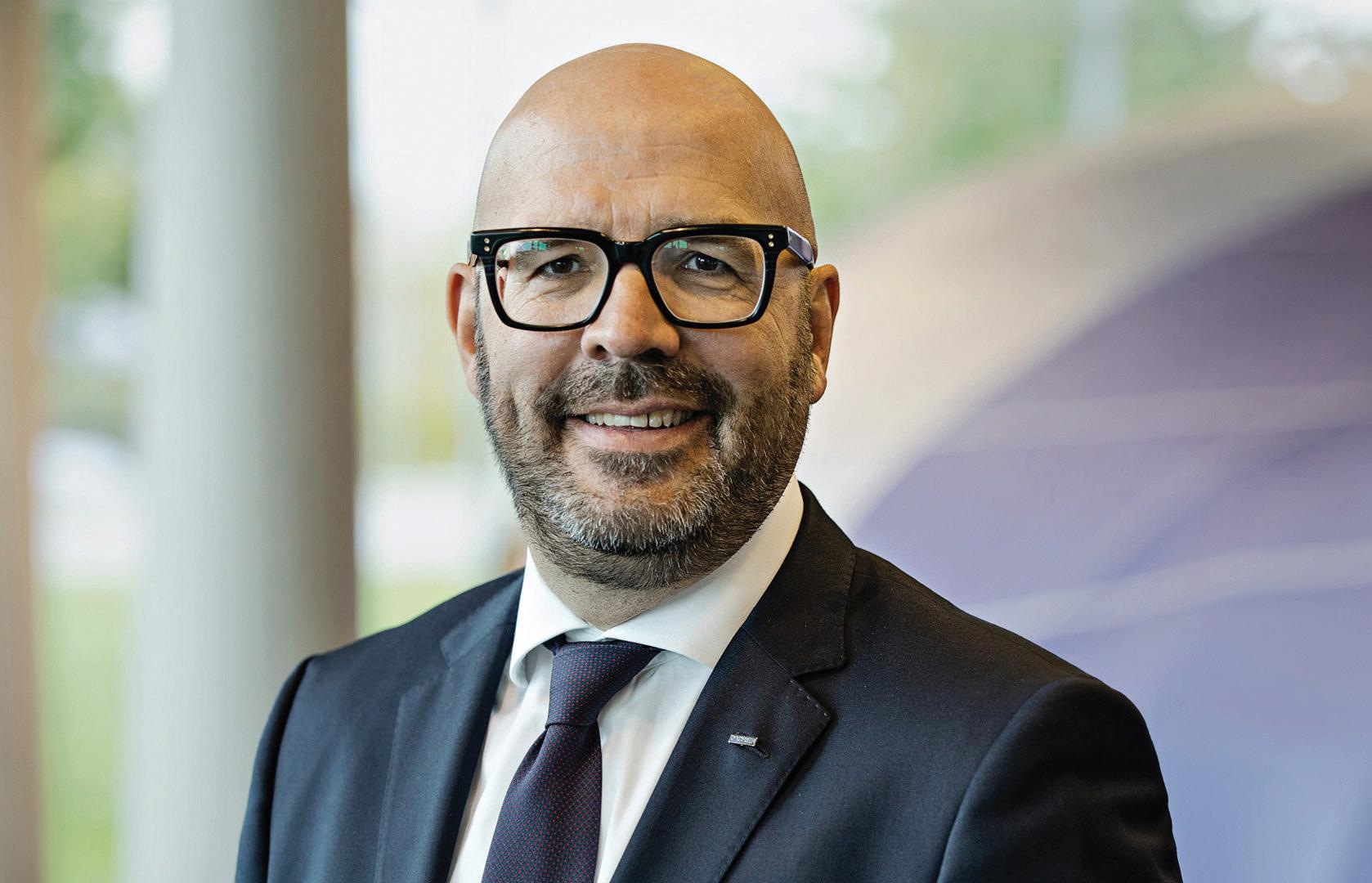
Chemical logistics in challenging times
Chemical logistics face the challenges of changing supply chains, digitalisation, and growing sustainability requirements. Challenges accelerated by the pandemic have made a stable network a critical success factor. Michael Kriegel, Department Head DACHSER Chem Logistics, provides an expert opinion on the implications the current global supply chain problems are causing for the sector.
The chemical industry is known as one of the most successful and competitive industries, and its growth trend is consistent.
Despite the industry growth, logistics services have been under considerable strain over the past two years due to disruptions to supply chains, shortages of materials, and capacity bottlenecks. It is now necessary to use predictive planning to manage these difficulties so that supply chains can run without interruption. Companies are currently in crisis mode, focussing entirely on procuring capacity at affordable rates and working with their logistics partners to find solutions for maintaining their supply chains. But, the medium to long term plans include companies planning structural changes to their sourcing patterns. Last summer, Dachser conducted an internal survey that revealed that 70 percent of customers polled were considering regionalising their supply chains. Generally, the pattern is that the first chemical companies relocate production to the region with their largest sales markets; however, this will take some time and in no way heralds the end of globalisation. Reshoring or regionalising the supply chain completely would be suboptimal, not to mention risky. However, this is about more than just regionalism; ensuring the stability of logistics networks and uninterrupted supply chains calls for logistics networks with flexible structures. Our job as a logistics provider is to respond with alternatives while also expanding our own transport capacity, a crucial factor in avoiding or dealing with bottlenecks. A robust and balanced transport network, one remaining effective and controllable, even under the stress conditions caused by pandemics or other infrastructure capacity constraints, is vital.
Environmental sustainability is another timely consideration. Currently, Dachser is investing significantly in research and development in this field. While we have several electric vehicles deployed in city centres, there are still only a handful of zero-emission heavy trucks available on the market; and are required to distribute groupage shipments of chemical goods in the main carriage. So the main leverage we have to make chemical logistics more climate-friendly is still to optimise transport capacity. Ultimately, there’s nothing worse for the climate than empty runs.
Additional issues we foresee in the future, over and above those we’ve already touched, will be driver recruitment, digitalisation and supply chain resilience and the corresponding network mindset. The current bottlenecks are giving many companies a wake-up call. They want to and must position themselves to be more resilient if they want to improve the protection of their supply chains against potential dangers. IT security and IT resilience will also be among the top priorities because secure data, and the exchange of that data, keep the physical supply chain moving.
dachser.co.uk

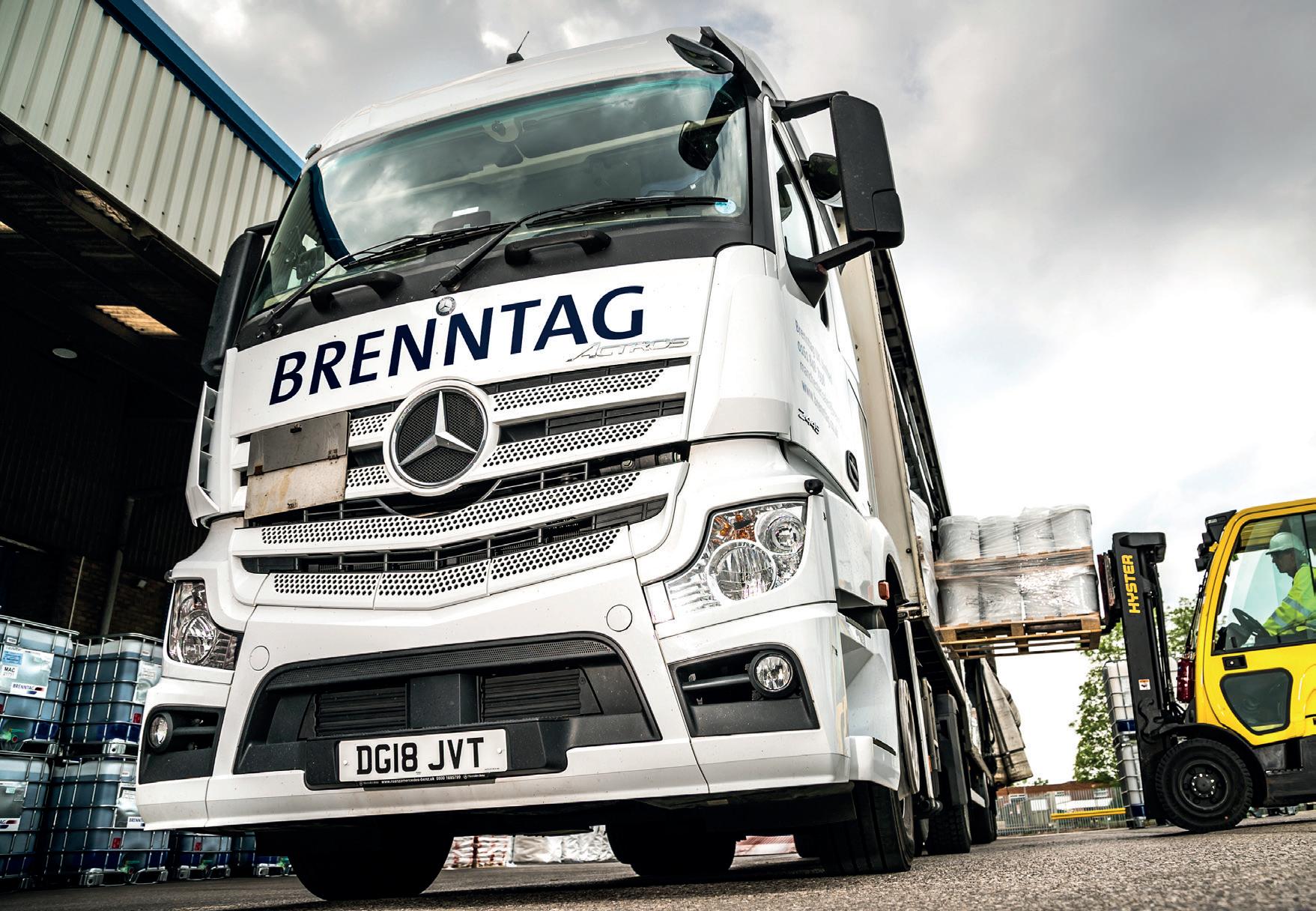
