
17 minute read
Pipeline Rehabilitation
The future is trenchless
Concern about the state of the United Kingdom’s underground pipe networks emerged in the 1970s with the reorganisation of the Water Industry and the publication of the NWC’s National Assessment’ in 1977.
Advertisement
It became clear that a substantial proportion of the UKs 234,278 km of sewers and 318,415 km of water mains were more than 50 years of age and in need of attention. Annual renewal costs for sewer and water mains estimated at £215.3M sent shock waves through government and ultimately triggered discussions leading to privatisation. NWC urged accurate determination of the scale of problems underground and development of new methods for repair and maintenance prompting investment in CCTV inspection and rehabilitation techniques. Thames Water’s Graham Cox, at the 1981 ICE Conference ‘Restoration of the Sewerage Systems’, spoke of ‘making use of the hole’ describing new techniques for sewer renovation including slip lining, cured in place lining and GRP panel lining. In 1985 the institution of Public Health Engineers, now CIWEM, hosted ‘Trenchless Construction for Utilities’. The event, styled ‘No Dig 85’, attracted 378 delegates from 21 countries and 66 exhibitors, was a signal moment for pipeline rehabilitation. Speaker James Thompson of Jason Consultants detailed the scale of opportunities for renovation and renewal in the UK and overseas. He introduced the notion that the costs of the social and economic disruption associated with open cut construction would be many times the direct engineering cost of renewal and replacement and should drive innovation towards more and better trenchless methods. No Dig 85 prompted establishment of an International Society for Trenchless Technology, a series of annual awards for trenchless innovation, various trenchless publications and a succession of international No Dig conferences; the 38th International No Dig will be held in Helsinki in October 2022. There are now 27 affiliated national or regional trenchless societies affiliated to ISTT, providing representation for more than 3000 corporate and individual members. Pipeline condition assessment and rehabilitation are the primary focus for at least half of the current membership. Cured in place pipe, originally pioneered in the UK in 1971 by Eric Wood, developer of the Insituform method, is unquestionably the primary process for renovating sewer pipe. Wood’s company and its contracting partners have subsequently lined more than 65,000kms of gravity sewer. The annual worldwide investment in cured in place pipe in all its forms is thought to be running close

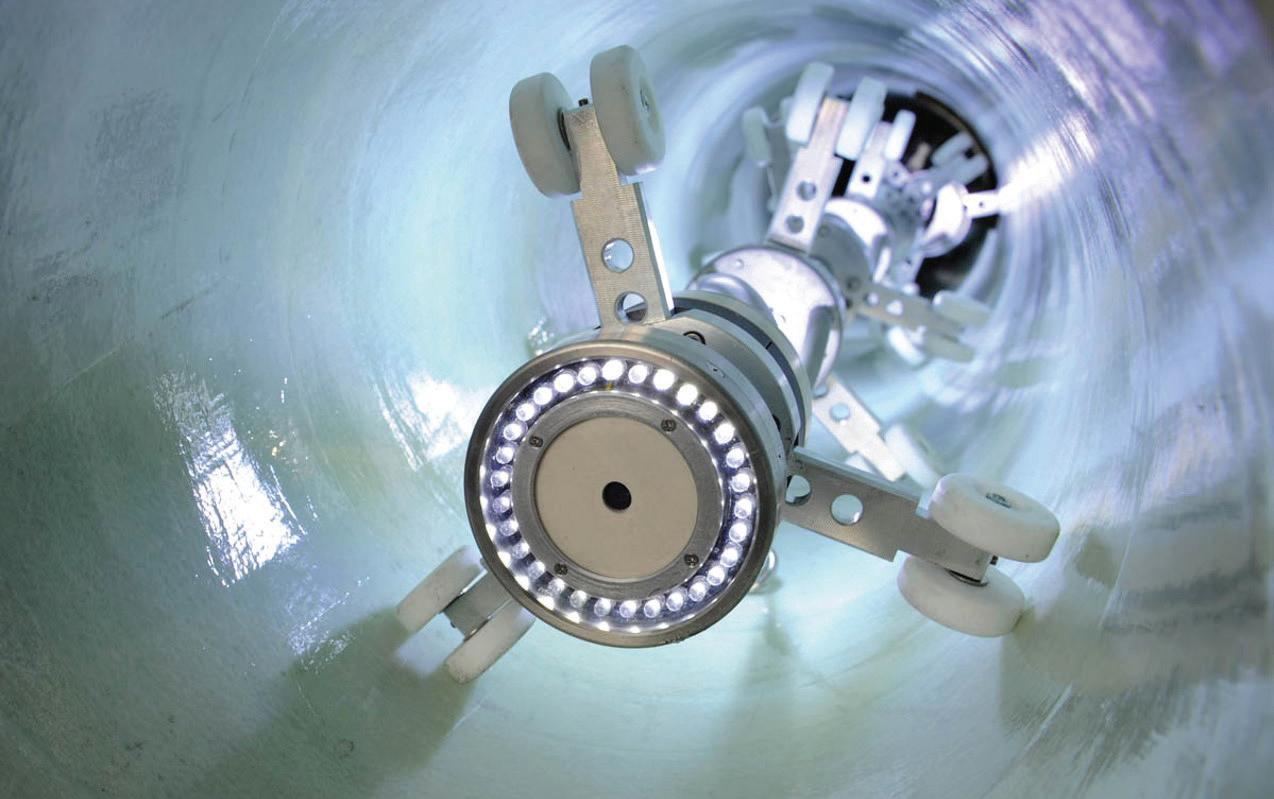
to £2Billion, about 55% of expenditure on pipe renovation. The method continues to evolve with UV light curing of glass reinforced linings pushing boundaries and growing in popularity. Other methods such as close fit lining, spiral wound lining, slip-lining with PE and PVC pipe and lining with GRP panels and segments account make up the balance, altogether perhaps half of the rehabilitation market.
We should recognise that rehabilitation is a catch-all phrase, defined by WRc, for repair, renovation and replacement. Use of trenchless methods for installation of new or replacement pipe is also well established. In 2001 the United Nations Environment Programme declared renovation and trenchless installation to be environmentally sustainable. Since that time numerous academic studies have calculated that greenhouse gas emissions are substantially reduced wherever trenchless methods are preferred to open cut construction. GHG’s for trenchless technologies can be as low as 10% of those estimated for open cut. UK Legislation such as the New Roads and Street Works and the Traffic Management Act has been crafted to regulate the disruption caused by street-works. These provisions generally support the use of trenchless technologies and benefit urban dwellers wherever underground utilities need attention. In many cities around the world regulations favour trenchless methodologies for the public benefit by restricting utility works to night working and limiting on-street storage of materials and construction traffic movements.
There remain barriers to wholesale adoption of trenchless technologies. Such methods can be more costly when considered solely in terms of direct costs. They often require specialist materials and skills. The trenchless industry has much work to do promoting awareness of its benefits and providing in service training to engineers and managers. No Dig Live, to be held at the Peterborough Arena, September 14-16th includes a 1st European No Dig Conference on Pipe Rehabilitation and related short courses. The technologies must be regulated with detailed specifications and quality management systems which recognise that a manufacturing process is being undertaken at the worksite. Adequate provision must be made for continuity of consumer services such as maintaining water supply during preparation and timely completion of siteworks including essential quality assessment. It could be said that over the past 50 years the industry has harvested some of the low hanging fruit, gravity sewer renovation is undoubtedly simpler than similar works on pressurised water or sewer mains. However there remains much to do in gravity and pressurised mains network, our buried pipelines have grown in length from 550,000 to 700,000 km over this period, many are aged, the process of wear and tear is relentless. More than half of our pipes are pressurised and inevitably more challenging. The condition assessment and rehabilitation procedures are more complex; but dig up and replace, with the attendant impact on the environment and the economy, should not be the go-to solution. We must explore better ways to solve the challenges and speedily install high strength linings without impact on water quality or loss of hydraulic capacity. In the United States, the Environmental Protection Agency’s (EPA’s) sixth national assessment of public water system infrastructure needs shows a total 20-year capital improvement need of $472.6 billion for water systems to continue to provide safe drinking water to the public. The picture must be very similar in Europe. This is the real challenge to materials suppliers, process developers and contractors worldwide, some of whom are now submitting products and processes to regulators and utility owners for trial and approval. We live in interesting times and maintaining our water and sewerage infrastructure is a priority. In the 1970’s we often used to say “out of sight and out of mind”, but 50 years on environmental awareness is more acute and there are no excuses for kicking the problem into the long grass, the future is trenchless.
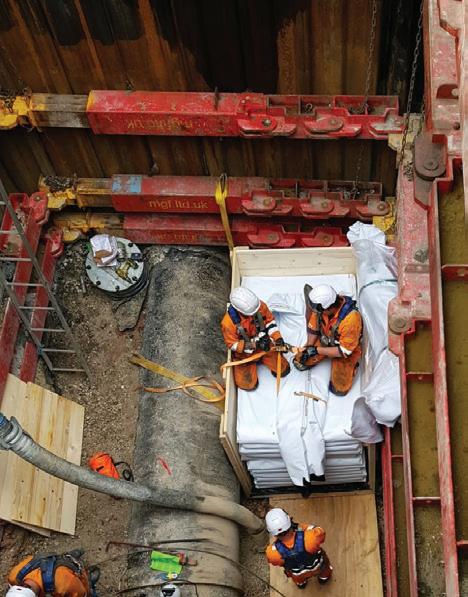

By Dec Downey Ph.D. C.Eng MIMMM Honorary President ISTT Dec Downey is a Chartered Engineer, he graduated from the University of Bath in 1970 and obtained his PhD in Materials Science in 1975. He spent fifteen years working in the concrete pipe industry before joining Insituform Technologies in 1987. Since 2002 he has worked as an independent consultant specialising in pipeline rehabilitation providing services to water and sewerage undertakings and their contractors in many countries around the world. He has been involved with the International Society for Trenchless Technology since its formation in 1986, he served as ISTT Chairman in 2007-2010, a Trustee since 2002 and is presently Honorary President. Together with Prof Sam Ariaratnam, Dr Downey developed the successful ISTT Masterclass Programme, teaching a variety of courses on trenchless technologies around the world. He is a co-author of the NASTT’s Cured in Place Pipe (CIPP) Good Practices Guidelines. His efforts have been recognised with the Japan Microtunnelling Association’s Kurose Award, the UKSTT’s Lifetime Achievement Award and the ISTT Gold Medal. He is an ISTT Fellow.
Race-against-the-clock Kendal water project scoops top award
A major race-against-time project to connect four huge water pipes into the even huger Haweswater Aqueduct in Cumbria has scooped the pipeline industry’s most prestigious award.
The Hallbank project, near Kendal, was completed within a tight eight day deadline, in a storm AND during the second COVID lockdown, last November – with three hours to spare. Now the team of 180 people from United Utilities and its framework contractor Mott Macdonald Bentley have been named Utility Project of the Year, by the Pipeline Industries Guild, one of the world’s most respected pipeline associations. They beat off stiff competition from pipeline projects across the UK in varied disciplines, including power, gas, both onshore and offshore.
Principal construction manager John Dawson said he was ‘tickled pink’ on behalf of everyone who made it happen and helped boost the resilience of water supplies across the North West as a result.
“This is a fantastic achievement. We were up against some very impressive competition. I think what made us stand out was the scale, the use of future technology like 4D modelling and digital assurance and the fact that we were really just one team, working collaboratively for a common goal – to build that pipeline safely, on price and on time. Everyone, from the cabin cleaner to the project director, had their own unique part to play. It’s was the best I have ever witnessed in my career,” he said.
Connecting the four new 1.6m diameter pipes meant shutting down the aqueduct for the shortest period possible and marked its first major repair in the 65 years since it was built.
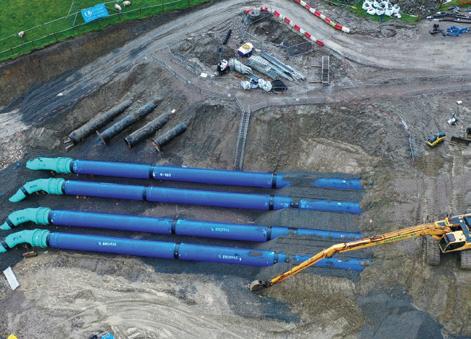
North connection complete: An aerial view of the four new pipes showing the old section of Haweswater Aqueduct which has been replaced Project director John Hilton with some of the new blue pipes which were connected into the Haweswater Aqueduct this month. The old pipes can be seen behind him to the left
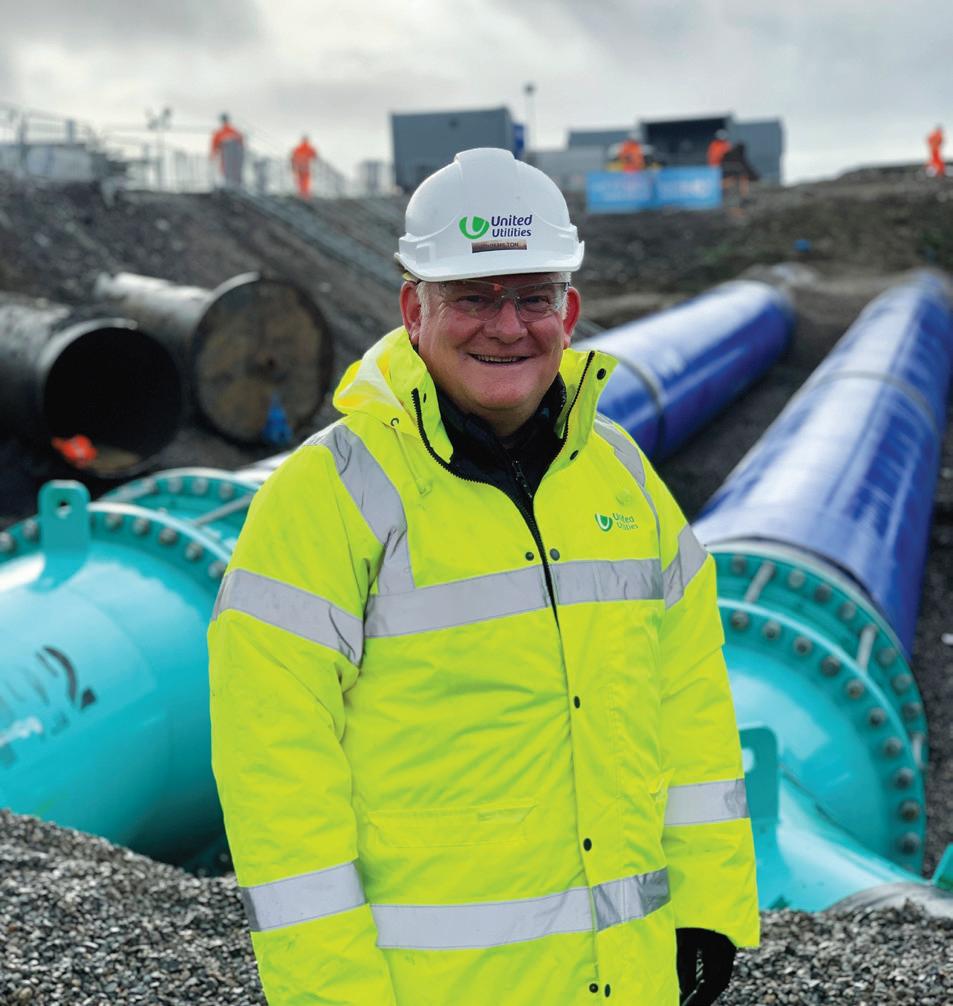
Project Director John Hilton said every hour of every day had been planned in meticulous detail to make sure it went smoothly. “This is only the third time in its life that the aqueduct has ever been drained and I’ve been there every time. You’d think it would get easier but it doesn’t. This time we were working during a pandemic and we had biblical rain like you wouldn’t believe. When you’re planning something on this scale it’s right to be sensibly paranoid,” he said. “The other big issue we faced was COVID. As well as rigorous round-the-clock cleaning, team distancing and testing, almost 100 extra trained staff had to be put on stand-by in case an entire work team had to self-isolate. We had hot and cold food brought in and we took over two hotels- one for the night shift, one for the day shift, to reduce the risk of contamination,” said John.
The impressive feat of engineering completed at Hallbank is the first milestone in a much bigger project which will see the replacement of six more tunnel sections along the 109km Haweswater Aqueduct. This £1bn Haweswater Aqueduct Resilience Programme is due to begin in 2023. The success of the first section at Hallbank will be the blueprint for that future resilience work.
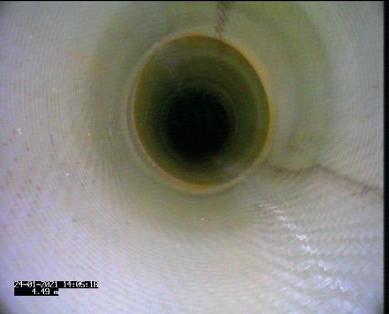


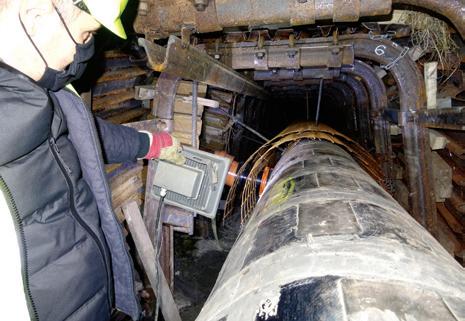
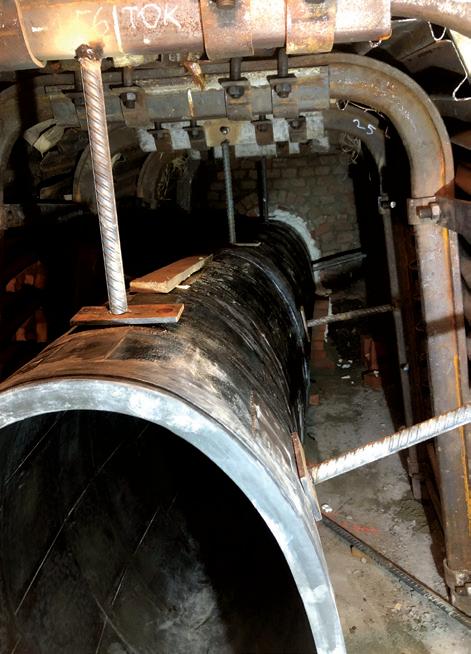
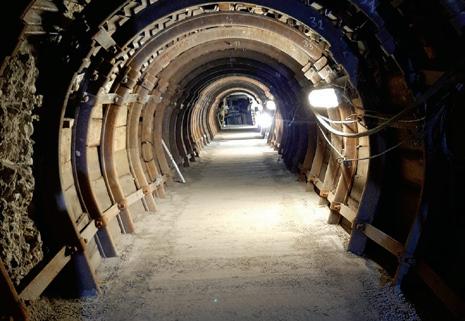
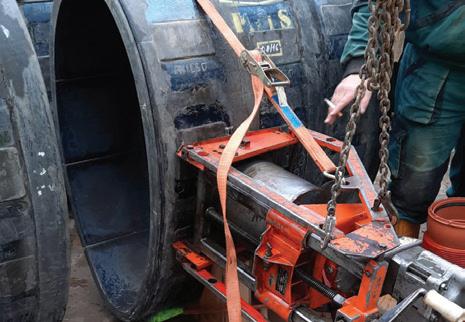
Ovoid-shaped basalt pipework developed for sewer renewal
By Robert Kostolány, Eutit Czech Republic and Ray Moorehead, Greenbank UK UK-based engineering company, the Greenbank Group, is drawing on the experience of its partner in the Czech Republic to provide a unique solution for the reconstruction UK sewer systems in the UK and Ireland. Over the last 25 years Greenbank’s partner Eutit has successfully developed and applied basalt tiling systems to the extent that they are now the preferred choice for many European utility companies looking to build new sewers or refurbish or repair existing ones.
Key to this success has been the development of oval or egg-shaped pipes made from basalt, one of the most resilient natural materials that offers a wide range of benefits when compared to more traditional materials such as concrete.
Development timeline
With a service life exceeding 100 years, basalt has been widely used in European sewer systems, but only for the bottom sections of ovoid ducts. The sides and tops were either bricks or specially cast concrete sections.This began to change in 1995, with the signing of the first contact between Eutit and Central European contractors and designers in wastewater handling. After consultations and design reviews in early 1996, the first basalt moulds were produced and the initial pieces were delivered for the construction of Slavojova street in Prague. The following year, the functionality of the fitted troughs was verified, evaluated and approved for use on future projects. Basalt designs now come in a range of shapes such as full oval, round and rectangular or specials produced to suit the given operating conditions. Prague’s sewers are mainly constructed using an ovoid profile and today the bottom sections are fitted with basalt and the upper arch with materials that can withstand strong chemical stresses (chemically resistant bricks). Therefore, any new sewer designs in this profile must be equally resistant. Thanks to further research and development by Eutit, one piece ovoid’s fully cast in basalt have become an attractive alternative to the labour-intensive brick laying method. Basalt can be cast in thinner more handleable sections, reducing installation times with significantly lower overall project costs. Other materials used for construction of ovoidprofile sewers lack abrasion resistance and time-tested durability of basalt rather than the theoretical claims made for alternatives.
From 1996, Eutit improved on the original 600/1100 designs from 1996 to produce full basalt lining systems and manufactured the shaped tiles within a tolerance to enable watertight bonding of the required pipe.
Ovoid-shaped pipe production technology
To produce the 600/1100 basalt pipes, 35 mm thick tiles are used and designed so that there are no continuous longitudinal joints in the entire profile. After casting, the tiles are ground with modern diamond tools to a precise shape then bonded together on a template to form a 360° profile, with each row being 330 mm long. These are then bonded together to the required length, with the joints between individual segments sealed using fiberglass tape with epoxy. The connection of the individual pipes is anchored to one end of the pipe with a rubber seal at the other end. Bends are made by bonding segments shortened to the required angle. All that remained was to verify the functionality of basalt in practice. The first project to utilise basalt segments was the renovation of the sewer in Rásnovka street Prague. The Project leader was PVK and the design company Ko-ka, with Eutit supplying the basalt.
Conclusion
The final construction of this project is due for completion at the end of 2021, however, it can confidently be said that the development from part use to full-profile cast basalt pipework is already proving a success. Due to the basalt pipes being easier to handle the project has resulted in real cost savings during the installation process and their abrasive resistant properties will significantly extend the effective lifespan of the sewer. The moulds for other profiles of the Prague Standard ovoid shapes, e.g. PN V, are already set for use on other projects across central Europe and can easily be adapted for UK clients.
The combination of correct material choice, a well-prepared project and, most importantly, an experienced installation company produced a finished result that complements the legacy left to the city of Prague by an English genius named William H Lindley who designed the city of Prague’s original sewers in the late 1800’s and early 1900’s. www.greenbankgroup.com
Preventing water loss from water networks
Damaged pipelines are a major cause of water loss in the UK and this is compounded by an out-of-date network infrastructure. Billions of pounds in investment annually by the water companies aims to dramatically reduce leakage and improve water quality.
Trenchless technology provides exceptional potential to support utility companies in their quest to renovate and renew the UK’s ageing water pipe network and help prevent water loss through damaged and burst pipes. Methods such as pipe bursting offer a cost-effective and time-efficient solution for contractors tasked with pipe repair and renewal. A sustainable and ecologically-sound technology, it minimises the need for open trenching and saves the purchase of raw materials. The pipe bursting technique is as simple as it is ingenious; old pipeline is broken up underground and radially displaced into the surrounding soil, whilst new pipe is pulled into the existing bore path. It is particularly suited to outdated pipelines with damage such as cracks, joint gaps, root growth and misalignment that are no longer repairable. New pipe with the same, smaller or larger diameters can be pulled in to the same space, including cross-section enlargements which are often necessary due to increasing demand for water. Once installed the new pipes have a service life of another 80-100 years. TRACTO has been pioneering trenchless technology for over three decades and offers a comprehensive range of equipment; whatever the task. Dynamic pipe bursting with the GRUNDOCRACK is an optimum solution for replacing pipes made of brittle material and is particularly suitable for applications from pit to pit. The versatile GRUNDOBURST can be used for renewal of pipes up to 120” in diameter made of cast iron, UPVC, asbestos cement, clay, concrete, ductile iron and steel. Anglian Water is one utility company that has recognised the benefits of this technique and recently used a GRUNDOBURST 400G to replace 900m of old 3” pipe with 125mm MDPE for a mains replacement scheme at Eye Green in Peterborough. This included 68 properties that were transferred onto the new mains during the replacement programme. One of the fundamental factors in the success of the scheme was the use of pre-chlorinated coils which allowed for the immediate commissioning of the main. It also facilitated a process where service transfers could be carried out almost immediately after installation of the main pipe. This enabled continuous progress of the scheme and adherence to installation targets. Backfill and reinstatement teams followed the bursting team to minimise time and inconvenience in the locality and the job was completed over a 7-week period in early 2021. As the smallest GRUNDOBURST in the range, the 400G has compact dimensions of just 1420 x 560 x 520mm and pulls up to 40t. It can install pipes up to 6” in diameter. This meant that only small pits were required on site yet the rapid work cycles and high performance of the unit ensured disruption was minimised. Other advantages of the GRUNDOBURST included:
No road damages, very little traffic disruption Shorter construction times; saving costs of manpower and materials Minimal dust and noise emissions
No follow-on costs due to ground subsidence or groundwater impact Minimal civil engineering work Intelligent technology; uncomplicated to operate and quick to handle Low weight for ease of transportation and easy manoeuvrability on-site Supplied as standard with 100M of rods Fast rod pushing through of the old pipe length and fast pulling in of new pipes Exceptional installation quality and high conformity to regulations Safe working – one man operation with remote control
The 400G is just one machine in the range. Other models include the 800G, 1250G, 1900G and 2500G for the replacement and renewal of larger pipes. GRUNDOBURST technology from TRACTO is a sustainable solution for water companies that are looking to improve the speed of water pipe repairs and replacements whilst considering the local environment and saving time and resources. Full specifications can be found on the TRACTO website: www.tracto.com/en
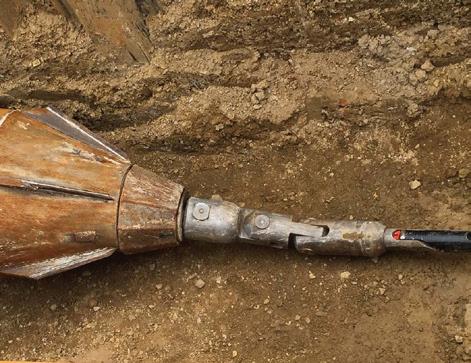

GRUNDOBURST - PIPE BURSTING SYSTEMS THE RENOVATORS
Trenchless pipe renewal using pipe-bursting technology is a costeffective solution for the rehabilitation of water supply networks. It also requires fewer raw materials.
With the proven GRUNDOBURST hydraulic bursting rigs, damaged pipes up to 1200mm can be repla-
ced or renewed underground within the existing pipe. This includes adapting the network capacity, if required, by installing new pipes of smaller, equal or larger diameter.
For more information please email customerservices@tt-uk.com or phone +44 1234 342 566
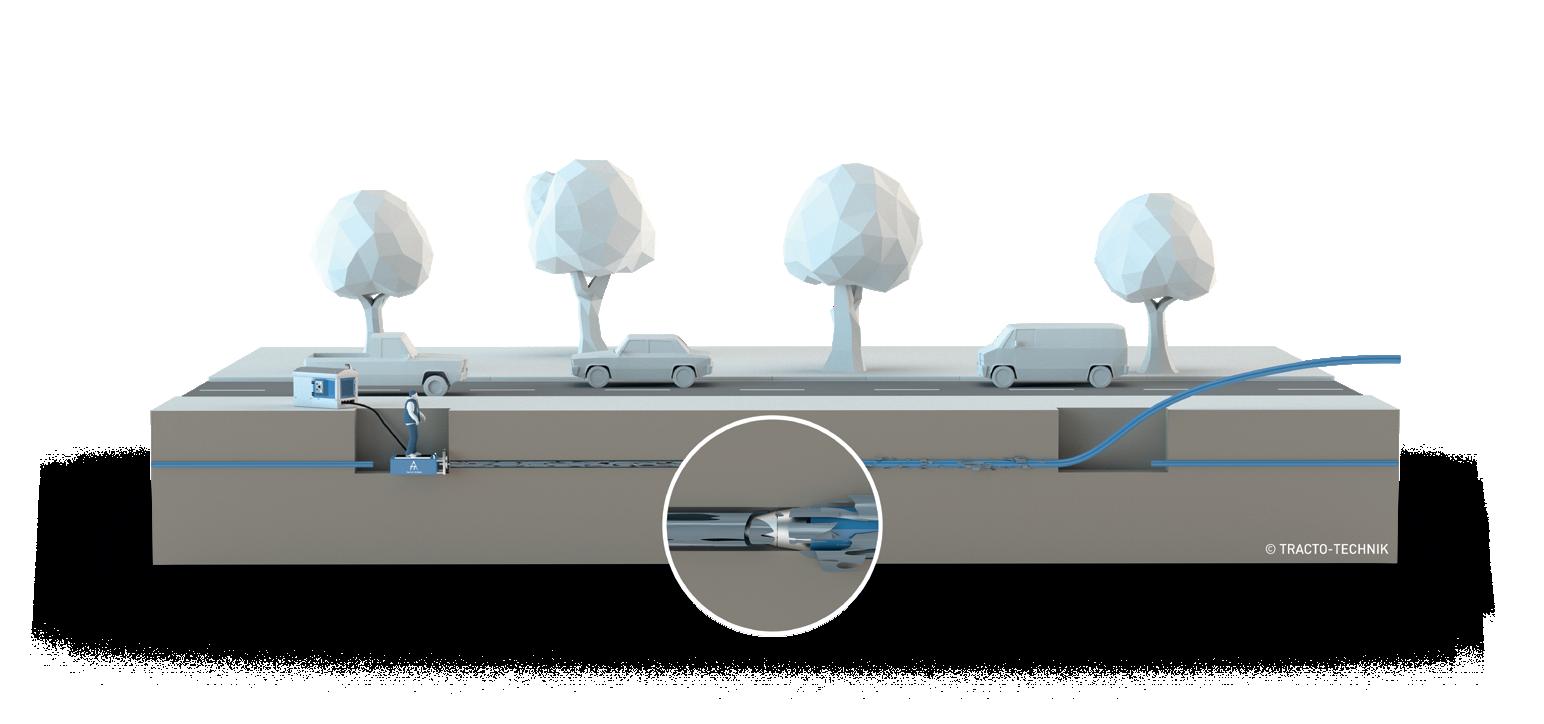
