
11 minute read
Pump Technology and Innovation
Energy efficient system delivers optimum savings
With energy consumption accounting for nearly 90% of the lifecycle of a pumping system, it makes sense to take advantage of the latest technology to achieve significant savings.
Advertisement
Graphs show energy savings that can be achieved with the High Efficiency System. Images: credit Franklin Electric
Franklin Electric, renowned worldwide for excellence and innovation, is helping customers do exactly that with its High Efficiency System (HES), which cuts energy costs by up to 21%. The system comprises of a synchronous submersible NEMA permanent magnet high efficiency motor, a submersible E-Tech pump and a frequency converter, as well as a matching output filter for systems higher than 230 V. It uses pre-written software to ensure greater efficiency with higher power density. The permanent magnet motor is critical to the system’s high efficiency abilities, as Mike Deed, managing director of Geoquip Water Solutions, Franklin Electric’s UK strategic partner for groundwater products, explains. “This sets it apart from current asynchronous technology as it means the windings are permanently magnetised, therefore using less energy when starting and running, delivering both a smoother and faster solution and improving the efficiency of the motor,” he says. “The permanent magnet motor also has less temperature heat rise and requires lower amps to run at the same pump load, while utilising the frequency converter further optimises energy efficiency.” A solar-powered option is also available, further increasing energy savings by carefully calculating how much energy can be provided by each day’s sunlight. It uses an algorithm to maximise motor and pump performance based on the number of solar panels in place, and its clever advanced voltage boost function makes it possible to size systems up to 2.2kW based on power rather than voltage, saving up to 50% on solar panels compared to a standard system. Among those to benefit from investing in an HES has been one of London’s major teaching hospitals, which estimates it has saved around £2.5k a month on running costs. After encountering problems with its existing borehole water supply, St George’s Hospital in Tooting, called in borehole and well drilling specialist Darren Hughes, who determined that a replacement pumping system was needed.
His team worked with Geoquip to install the Franklin Electric HES and Darren explains: “The original 8” pump was pumping 140 cubic litres an hour and would be switched on and off every time the tanks needed filling. The new 6” pump now runs for longer to match peak demand but because it has the permanent magnet system in place, it uses less energy when starting and running, is much more energy efficient and there is no detriment to supply.” Customers can estimate their likely financial savings and see how long the payback period is likely to be by using Franklin’s online calculator www.fehighefficiency. franklinwater.eu A further key advantage of the HES is its easy set up, a step-by-step guide takes users through the drive settings, and once in place, monitoring can take place either manually via a board panel or remotely through Bluetooth and the Franklin Smartphone App ‘FE Connect Drivetech’ (Android and IOS). Mike Deed continues: “The ability to access information via your phone or tablet makes a huge difference as you can instantly check usage and data at the touch of a button. You can monitor pump performance and quickly identify any issues, such as reduced water pressure, and take remedial action before the problem accelerates.” In addition to enabling operator monitoring, it also provides access to the Franklin Electric support team in order to help solve any issues. Always at the forefront of innovation, Franklin Electric continually works to develop new products, including the constant-pressure system DriveTech and DriveTech Mini and various controls for submersible and surface pumping systems. As a strategic partner, the Geoquip team works closely with Franklin Electric and has direct access to its European manufacturing facilities, enabling Geoquip’s experts to provide tailored solutions to meet customer requirements. For more information, visit www.geoquipwatersolutions.com or call 01473 462046.
For the latest Water Industry news...
www.waterindustryjournal.co.uk
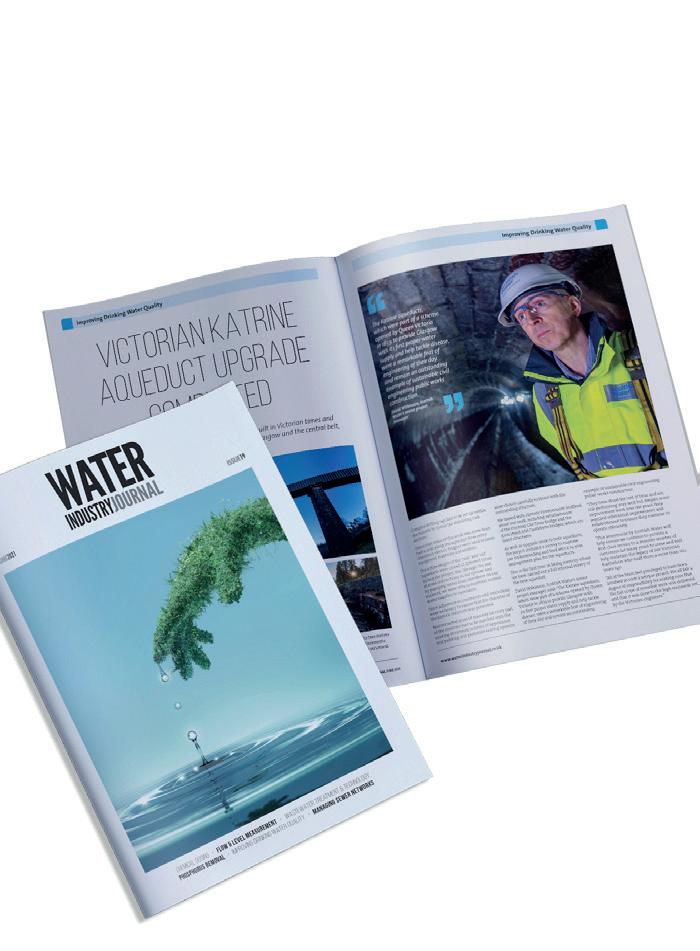
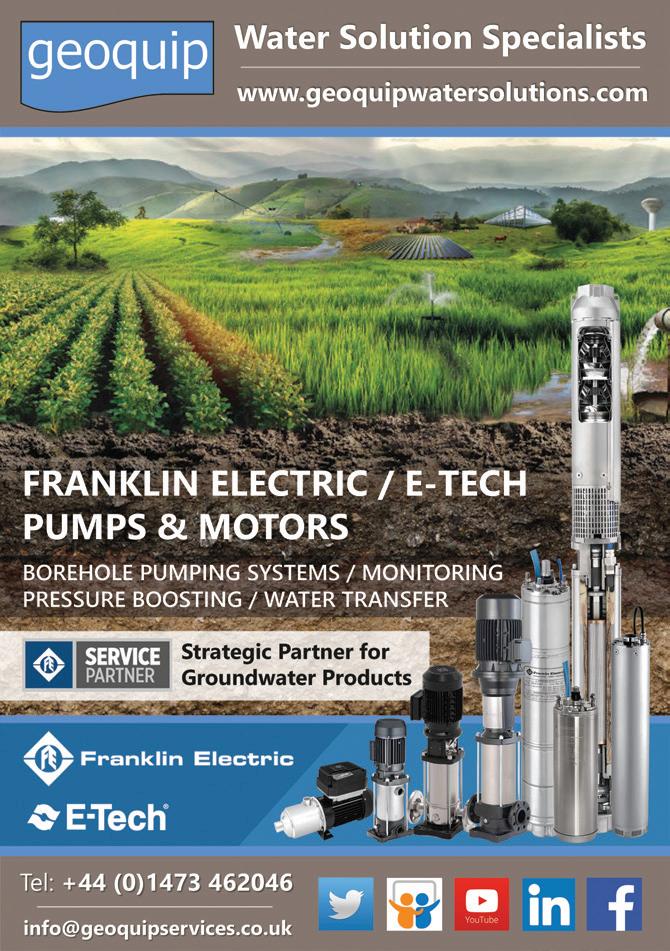
Anglian Water announces route map to reach net zero by 2030
Company’s comprehensive carbon plan aligned to raising of £300 million bond investment
Anglian Water has published a route map which sets out how the company will reach net zero carbon by 2030. The net zero target will cover all of the company’s operational activities and those of its supply chain, as well as a commitment to cut capital carbon by 70 per cent against a 2010 baseline.
Last month, the water company made financial history when it became the first utility in the world to launch a sustainability-linked bond connected directly to achieving its interim carbon targets. By 2025, Anglian has committed to reduce capital carbon by 65 per cent from a 2010 baseline, and operational carbon by 30% from 2018/19 levels as part of its journey to reach net zero.
In 2020, the water industry of England and Wales became the first sector worldwide to work collaboratively on a route map to reach net zero within the decade, with each company expected to publish their individual plans this month. Anglian’s route map is centred around several key areas of work and outlines the targets the company will reach by 2030. Each year the company will reduce its carbon emissions, and by 2030 its operational emissions will have reduced by over 70 per cent against a 2018/19 baseline – a reduction of over 250,000 tonnes, or the equivalent of filling 55,000 hot air balloons. CEO Peter Simpson said: “We are accelerating our progress to net zero and setting out the pathway that will get us there by 2030, based on our three-step hierarchy of reducing emissions, decarbonising our electricity supply and removing or offsetting our residual emissions.
“It won’t be easy – in fact it will be incredibly challenging and we don’t have all the answers. Finding and delivering them is going to take sustained and genuinely collaborative efforts throughout the coming years, not just from us but from our supply chain, our peers, from government and from regulators too.”
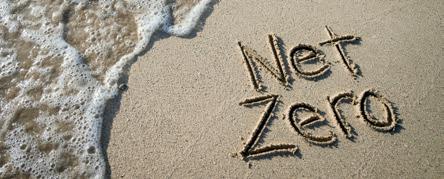
Look – no pumps! Selwood turns to siphons for major canal project
Selwood is renowned as the UK’s leading provider of pumping solutions – but one of its most ingenious engineering solutions involved no pumps at all.
Using nothing more than pipes, gravity and specialist technical knowledge, Selwood developed an environmentally-friendly siphoning system to assist with crucial works to replace canal gates in Scotland.
The task
The Caledonian Canal is one of the most popular visitor attractions in the Scottish Highlands, carrying more than 1,400 boats each year. The Gairlochy top gates at its Lock 17 are the largest on the canal and serve as a crucial flood defence, separating Loch Lochy from the canal and the communities to the west. As the gates were 30 years old, they were made a priority for replacement based on age, condition, and risk.
Amco Giffen, carrying out the replacement works on behalf of Scottish Canals, called upon Selwood’s solutions team for support with water bypass of the lock to enable the replacement gates to be installed.

The challenge
In the lock there is a bypass channel which allows the flow to be diverted from Loch Lochy, through the lock gates and into the canal. This is in place to maintain the required water level in the canal and is controlled by a pen stock located on the lock system. Almost 2,000 litres per second has to be forwarded into the canal system to maintain the water levels needed downstream.
A marina below the lock also has to be fed to avoid the damage a drop in water level would cause to boats moored there. Noise was a key concern to avoid disruption to nearby residents, and there was a need to avoid the risk of fuel spillage and minimise the overall environmental impact.
The solution
Using pumps to drain the lock would have been a conventional solution – but the commitment of the Selwood teams to innovation and sustainability resulted in a more environmentally and cost-effective idea. Siphon systems on this scale are rare – especially with such a low head difference between the top and bottom water level. However, Selwood’s specialists carefully studied and modelled the location, even building a scale model to demonstrate the concept was viable. With the case proven, Selwood ran two 800mm pipes from the top of the lock to the downstream canal system. A Selwood-designed priming system filled the siphon to get the water flowing. The siphon was also fitted with an 800mm gate valve on each set-up to regulate flow rates, measured by two 800mm digital flow meters. The vacuum pressure was continually monitored by two Selwood pressure monitoring panels that enabled the system to start automatically if the vacuum started to drop below the required levels. Once the siphon was up and running, it required very little maintenance with only occasional checks on the priming system. 13,000,000m3 of water was moved from Loch Lochy during the operation.
The result
The cost of operating a traditional pump set-up flows required would have been more than £10,000 a week to run. By comparison, the siphon system cost around £200 per week, saving around £156,000 in total for the duration of the project. Additionally, 424,883kg of CO2 was saved when compared with a diesel pump set. Noise levels were kept low, which ensured that the local residents were not disturbed.
Amco Giffen said: “Removing and replacing the largest lock gates in Scotland was challenging in so many ways, but with continued support from Selwood, we were able to deliver the works as planned. We were pleased with the level of support from Selwood throughout the project.” www.selwood.co.uk Gairlochy lock syphoning
How pump selection can affect total cost of ownership
While considerations should be made on the total cost of ownership (TCO) when specifying a pump, the most important criteria should be that it is fit for purpose, to ensure optimal productivity. Selecting the wrong pump can prevent the pump from performing to its full potential and lead to unnecessary downtime, wear, maintenance and energy consumption, product damage or reduced uptime of the process.

Before: Build-up in the pumps affected the flow, requiring 2-3 hours to clean each pump and equipment being replaced every 6 months After: SEEPEX transfer pumps offer reliable performance, and ease of maintenance due to their simple pump design

When selecting a pump, factors such as the viscosity of the product being conveyed, flow rate or the operating temperature should also be considered. Not all pump technologies are equal. Some are designed to handle low viscosity, others for highly viscous and high solids content products. Shear-sensitive media, for example, requires a pump with low shear action.
In wastewater treatment processes, polymers are used to thicken sludge by attracting all suspended fine particles to produce larger groups of solid materials through a process called flocculation. These flocculants are often extremely viscous and shear-sensitive once hydrated. Incorrect pump selection can affect the metering accuracy, damage the polymer structure and potentially the efficiency of the thickening process.
Wrong selection affects process performance
A Water Company was using two multistage vertical centrifugal pumps to handle polyelectrolyte for use as a flocculant agent and transfer it from a ‘make-up’ tank where the powdered polymer was mixed with water to their daily service tank. However, build-up around the volute casing and impellers in the pumps severely affected the flow which required the pumps to be dismantled and cleaned – a process which took 2-3 hours per pump, and the pumps being replaced every 6 months. The use of centrifugal pumps to transfer viscous media reduces their performance due to factors such as the effect of viscosity on the impeller, reduction in flow and the increase in horsepower required. But also their pumping action generates high shear, making them unsuitable to handle shear-sensitive products. To address these challenges, SEEPEX was engaged to offer a cost-effective pumping solution.
The right pump for the duty
To meet the application’s requirements, SEEPEX selected progressive cavity pumps from their BW range for transferring the viscous polymer. Simple and compact for quick and straight forward maintenance. Progressive cavity pumps have a low shear pumping action. Their flow rate is directly related to pump speed and have minimal pulsation, producing the lowest mechanical stress and minimising product shear damage. Additionally, in a PC pump the stator is cleaned by the action of the rotor, eliminating any chance of product build-up and subsequent blockages which would otherwise affect pump performance.
No onward cost since installation
SEEPEX’s intervention has resulted in costsavings for the customer as the new PC pumps have not suffered from blockages, used any spare parts or required maintenance since they were installed in 2018.
www.seepex.com
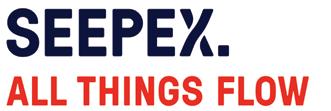