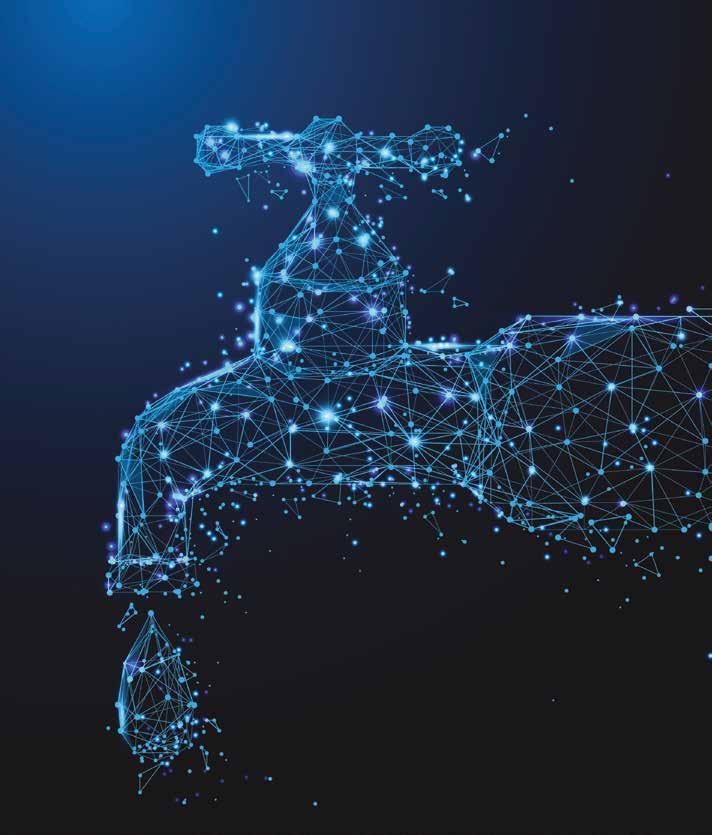
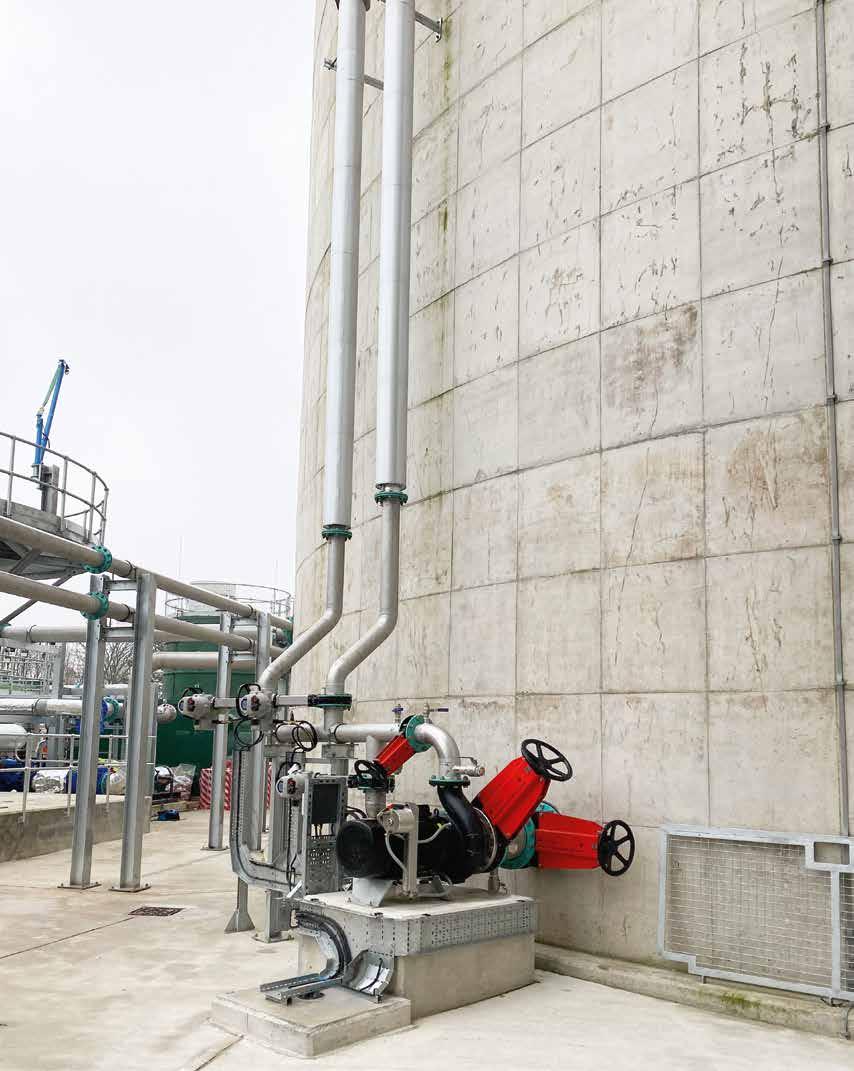
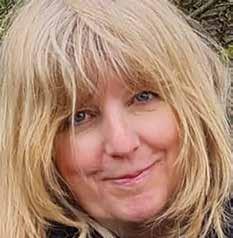
Is the UK water sector ready for AMP8?
As Lila Thompson of British Water discusses in this issue, it certainly won’t be an easy task.
But, with external expenditure on goods and services currently amounting to around 55% of water company revenues, it’s high time for pragmatic decisions to be made… and Lila believes the supply chain will play a central role.
She argues that the complex dynamic between water companies and suppliers is ripe and ready for improvement, and a successful outcome could just prove to be the sector’s next watershed moment.
Lila also touches on the need to move away from asset-intensive processes to services based on environmental solutions, demand management, and digital technology.
Which brings us to innovation. It’s most definitely an over-used buzzword in industry circles, but Scottish Water’s new biogas production facility is showing the way.
Since upgrading the existing thermal hydrolysis process and installing a new
digester mixing system, the Nigg Wastewater Treatment Works has become the first in the UK to successfully co-digest.
But as operations director Simon Wrigglesworth points out, “sometimes it’s not just about new technology, it can be about doing something differently.” Could this be the start of a move to a more circular, sustainable economy? Nigg certainly looks like an exciting breakthrough.
Ageing water systems present a massive challenge for operational management as Canadian utility Halifax Water (HW) was all too aware, after hitting a static level of breaks and non-revenue water loss.
Having already tried several approaches to advanced pressure management, including flow modulation, HW were open to a new trial and comparing the results. They eventually partnered with Mueller for a performance trial of an advanced pressure management and control platform using the Internet of Things (IoT). The results have been extremely positive, as detailed in this issue.
YTL Wessex Water has joined the Hydrogen South West (HSW) partnership.
Wessex Water, which serves 2.8 million customers in the region, has plans to optimise hydrogen usage for future operations by collaborating in the development of hydrogen infrastructure and technology across SouthWest England.
With water management expected to undergo significant changes through climate change, Wessex Water wants to provide reliable, affordable services for customers and communities, and deliver a better environment for nature and people.
HSW’s cross-sector partnerships will generate investment for projects beyond heavy industrial clusters. Not only are these ambitions set to assist the journey to Net Zero by 2050, but also to enhance skills and deliver new job opportunities for a sustainable future.
Wessex Water Chief Operating Officer, John Thompson, said: “Wessex Water is committed to achieving net zero operational carbon emissions by 2030 and full de-carbonisation of all aspects of our work by 2040, a decade ahead of the UK government’s 2050 target.
“It is absolutely essential that we all work together across the South West to achieve these aims and therefore we are very keen to be part of Hydrogen SW and to be collaborating with some of the other large infrastructure and transport organisations in the region.”
Simon Earles, Chair of Hydrogen South West added: “HSW continues to bring together organisations, covering aerospace, shipping, high-tech engineering and public utilities to create an infrastructure ecosystem. We welcome Wessex Water as the newest member to help us fulfil this ambition.”
The supply chain has a critical role to play in the complex challenges facing the UK water sector in AMP8, and its successful delivery, says Lila Thompson, the chief executive of British Water.
“There is no time to waste. Now is the time to get serious about water as an imperative for climate action,” said a joint statement from an eminent panel of water and climate leaders at the UN COP27 negotiations in Egypt, in November 2022. The statement urges heads of state and governments to take a more integrated approach to water to replace the existing fragmented management across the world.
Closer to home the water industry is facing a challenging backdrop of supply chain disruptions, energy price increases, skills shortages, and the need to address sectorwide carbon targets and environmental and performance issues.
We believe failure to address these challenges could lead to further difficulties for the whole sector, including and perhaps most dramatically of all, suppliers leaving the UK water sector to explore other markets including those overseas.
In today’s resource-constrained market, this will severely limit utilities’ ability to meet customers’ expectations and could result in water companies failing to meet Ofwat’s required regulatory outcomes in AMP8 – the regulatory asset management period 2020-25. The supply chain is critical in the delivery of these outcomes, with external expenditure on goods and services amounting to around 55% of water company revenues, according to the Institute of Civil Engineers.
The water industry is the most capital intensive of all major sectors and its supply chain is complex, and will become increasingly so as the industry shifts focus away from asset intensive processes to services such as nature-based solutions, digital technologies and demand management.
That is why pragmatic decisions need to be made urgently, and communicated properly, within the water industry to keep it moving forward, with fully engaged suppliers playing a leading role.
The relationship between the regulators’ requirements and inputs from the supply chain is indirect. It functions in a complex dynamic via water companies’ planning and procurement, and the need to deliver services to customers and protect the environment.
It is heavily dependent on the management of water companies’ relationships with the supply community, and British Water believes this indirect linkage is ripe and ready for improvement - with substantial benefits for customers, the environment, the companies, and their shareholders.
Earlier this year, British Water’s Supply Chain Taskforce surveyed supply chain companies
on their experiences of working with water companies in three key areas - innovation, procurement, and cyclicality.
Using the valuable findings in our submission to Ofwat for the 2024 price review, British Water recommended that the regulator measure supply chain satisfaction with water companies, and water company satisfaction with their supply chains. This would build on the work of British Water’s annual Water Company Performance Survey, and further the understanding of resilience in the sector at a time when supply chain connectivity is of paramount importance.
In responding to Ofwat, British Water explained that the supply chain is a community, which can bring important markets to water if enabled properly. To achieve this, joint working initiatives that provide opportunities for supply chain companies to participate and up their contribution to tackling these big issues will be key.
The sector will be better able to tackle its joint problems by bringing together individual companies, across utilities and the supply chain, along with sector organisations such as Water UK, UKWIR, WRc, Spring - as well as British Water’s UK, technical and international forums and the Water Industry Forum.
What is clear from the conversations taking place at COP27 is that the world is finally starting to understand the value of water and the ongoing importance of protecting, conserving and restoring water and waterrelated ecosystems. Closer to home, it is clear that here in the UK there is an urgent need for change across the industry to meet these pressing challenges too.
British Water and its supply chain members are ready and willing to be an integral part of the discussions and help drive action. We are committed to work with regulators, water companies and other stakeholder to drive these matters forward as we move closer to AMP8.
If COP27 can be considered to be a watershed moment for climate action, then with the right relationships, policies, knowledge and tools, AMP8 could prove be a watershed for the UK water sector too.
British Water represents the interests of UK water and wastewater supply chain companies together with wider stakeholders across the sector, through its UK, Technical and International forums, connecting them to contacts to raise their profile, grow their business and promote best practice. Our Water Industry Forum provides challenge-led, independent thought leadership, to tackle the challenges facing the sector.
Electric motors account for a significant proportion of the water industry’s energy consumption. Against the backdrop of rising prices, putting in place an effective motor purchasing policy can help to reduce bills, and meet PR24 goals, as James Thomas, UK Water Industry Manager, ABB, explains.
A significant amount of electricity consumption within UK water industry is consumed through the use of electric motors, which drive much of the rotating equipment needed to transfer and treat the water network (e.g., pumps, blowers, centrifuges, etc). The introduction of an electric motor policy can reduce energy usage and improve efficiency.
Electricity usage accounts for a significant proportion of a motor’s overall lifecycle costs, whereas initial purchase costs only represent a small fraction of this expenditure. High efficiency motors therefore provide an opportunity to lower lifecycle electricity costs. The extra cost of a high efficiency motor is often quickly recouped in reduced energy usage.
To reduce energy consumption, water companies should adopt a total cost-ofownership approach (TOTEX) and consider implementing an electric motor purchasing policy. Additionally, this course of action will assist water company’s efforts to meet Ofwat PR24 strategic goals to:
Increase focus on long term cost savings Drive improvements through efficiency and innovation Deliver greater environmental and social value Ensure customer expectations of service and maintain affordability Create working partnerships with innovative organisations Embrace new thinking by collaborating with others inside and outside of the sector Support Green Recovery initiatives Achieve Net Zero carbon targets
IE4/IE5 options are already widely available and should be considered the preferred option.
Use a minimum IE4 motor or IE5 where possible. IE5 synchronous reluctance motors are the most efficient and resilient but must be used with a variable speed drive (VSD). It may be possible to use existing VSDs if compatible.
Given the expected total expenditure benefits, all motors purchased for new installations, including package plants, should be energy efficient and exceed the minimum standard set in WIMES, i.e. IE4 or IE5 synchronous reluctance and compatible VSD if the option is available. This specification must be shared and specified with project teams, contractors and plant OEMs such as pump manufacturers.
on LCC with a new energy efficient motor i.e. IE4 or IE5, if option is available/possible.
Upon motor failure for motors over > 75 kW:
• Total cost-of-ownership assessments must be undertaken for failed motors over 75kW to determine whether replacement with or rewind/repair is most appropriate. It’s the supplier’s responsibility to provide a quote for an energy efficient alternative (incl. required mechanical & electrical modifications to allow installation) and the potential energy savings that can be achieved. If simple payback is less than 5/7 years, the motor must be replaced rather than rewound. Typically, IE5 synchronous reluctance motors will offer the fastest payback period and should be considered before all other options.
For use within the water industry, all motors purchased need to meet the most recent WIMES standard), which states that all motors between 0.75 kW – 1,000 kW need to meet the IE3 energy efficiency standard as a minimum. From the 1st of July 2023 all new motors in the range of 75 kW to 200 kW need to meet the IE4 efficiency standard per the EU ecodesign regulations for electric motors.
When an electric motor fails and is rewound, its efficiency is more often than not reduced, resulting in increased energy costs. Therefore, it is often more cost effective (based on lifecycle costs) to replace the failed motor with a new high efficiency motor, rather than rewinding a failed motor. Furthermore, a repaired IE2 motor is still an IE2 motor.
Upon motor failure for motors less ≤ 75 kW:
• Repair if due to a bearing failure and no other failure has occurred.
• Rewind required – Consider replacing based
Successful implementation of an effective motor purchasing policy can contribute towards a reduction in energy consumption and related CO2 emissions, along with improved resilience and fewer motor failures. This in turn can help to meet Ofwat’s PR24 strategic goals to increase focus on long-term cost savings, drive improvements through efficiency and innovation.
If you have any questions about SynRM, or ABB’s wider motor and drive offering for the water industry, contact me at james.thomas@gb.abb.com.
Work is due to begin in Ilkley to lay a new sewer under the A65 to help reduce the frequency and volume of storm discharges into the river Wharfe during periods of heavy or prolonged rainfall.
Yorkshire Water’s partner Ward and Burke began work in mid-November, setting up site working areas ahead of construction. Trenchless technology will be used with underground boring machinery controlled remotely throughout the project to keep disruption to a minimum while laying 800m of new sewer under the A65 to the Sewage Treatment Works.
This reduces the need to close the road as it lays pipework behind it and sends the earth back to the staging site where it is cleaned and recycled for use in other projects in the area.
The sewer will operate as additional storage during periods of heavy rainfall or prolonged rainfall to reduce the frequency of discharges from Rivadale storm overflow by 40% and halve the volume of wastewater discharged during those events.
The initial stage of the work will include laying the sewer between Yorkshire Water’s Ilkley wastewater treatment works and Ashlands playing fields. The second stage of the project is to lay the sewer under the A65. Remotecontrolled tunnelling equipment will be used at depths of 5-8 metres below the ground, to bore the hole for the new sewer.
The equipment will be recovered at the Ilkley Wharfe View car park once the sewer has been laid.
Ben Roche, director of wastewater at Yorkshire Water, said: “This project forms a major part of our investment in Ilkley following the creation of an inland bathing water on the Wharfe in the town. Laying a new sewer to accommodate higher flows of wastewater during periods of heavy and prolonged rainfall will ultimately reduce the number
and volume of discharges from Rivadale CSO, helping to improve water quality in the Wharfe.
“We’ve worked very closely with Bradford Council highways teams to keep the disruption for our customers to a minimum. As a result, we’re making use of trenchless technology, with equipment boring the hole and laying the sewer remotely, preventing the need to dig up the A65 to complete this work. For the majority of the project, there will be limited signs of our activity underground.
“We completely understand the increased public interest in river quality in our region and it’s an issue that must be addressed by a range of agencies working together. We continue to invest over and above existing investment plans in Ilkley and the surrounding area to make improvements on our network to reduce its impact on water quality. Water companies have a key role to play, but coordinated action is needed by farmers, the local authority, businesses and local people with the ultimate aim of improving the bathing water classification.”
Laying a new sewer to accommodate higher flows of wastewater during periods of heavy and prolonged rainfall will ultimately reduce the number and volume of discharges from Rivadale CSO, helping to improve water quality in the Wharfe.
Ben Roche, director of wastewater at Yorkshire Water
To allow the equipment to be controlled and recovered from underground, part of a Ashlands playing fields will be turned into a working compound and the Ilkley Wharfe View car park will be closed. Yorkshire Water is working with Bradford Council to develop alternative parking arrangements.
The project is expected to be completed in January 2024.
Careful management of service reservoirs is essential to safeguard drinking water quality, requiring accurate and reliable monitoring for a detailed understanding of supply configuration, asset condition, along with and the expertise of a multi-disciplined team. ATi discusses how the data provided from analytical sensor technology can provide vital insights into reservoir performance, allowing the optimisation of systems and the early identification of issues to prevent the deterioration in water quality, compliance breaches and regulatory sanction.
Service reservoirs are a fundamental component of water distribution networks, providing vital reserves of treated water to supply system shortfalls during peak demands. Over recent years, the water industry has become far more knowledgeable about the need for optimisation of service reservoirs, recognising the significant role they play in delivering clean, safe water and regulatory compliance is now more important than ever.
The storage of water within service reservoirs can represent a risk to the quality of drinking water if not closely monitored, resulting in the reduction in chlorine concentrations due to long water age leading to bacterial growth, ebb and flow supplying mains may be present, poor mixing characteristics and the potential for ingress following structural failure when residence times are excessive. It is therefore essential to perform regular inspections and monitoring to ensure they operate in a manner that maintains necessary disinfection levels.
Historically, the quality of water within service reservoirs was monitored through the collection and analysis of grab-samples on a weekly basis. Such a monitoring regime, however, is unable to rapidly identify any sudden deterioration or variation in water quality. As a result, it is now widely acknowledged that weekly sampling is no longer adequate to appropriately manage water quality for the optimisation of asset operation.
Continuous, smart sensor technology monitoring of critical water quality parameters, including chlorine residual, conductivity, turbidity and pH, plus BOD, COD, TOC & DOC organics, at even the most remote locations is now possible. Smart water quality monitoring solutions, such as ATi’s MetriNet for the critical water quality parameters and s::can’s spectro::lyser for organics, provide water companies with industry-leading, tried and trusted methods for providing data points from as little as one minute apart onto any chosen platform.
The installation of such proven, continuous monitoring solutions, both on the inlet and outlet of service reservoirs, is enabling water companies to meet compliance while understanding the operation, performance and management.
The installation of continuous monitoring instrumentation allows detailed understanding of the reasons for low chlorine levels eg is it due to the incoming supply at certain times of the day or residence within the reservoir? Such insight allows operational modifications to be made, including changes to supply routes or forced turnover of water within the reservoir in order to improve chlorine concentrations and protect against statutory sample breaches. Often, forced turnover is the natural response to low chlorine levels, however, if the issue is actually
upstream then this could jeopardise resilience without addressing the root cause.
Ingress into service reservoirs following heavy rainfall is one of the most common reasons for microbiological sample failures and this can result in a loss of chlorine residual or changes in other parameters, such as conductivity. Where monitoring of water quality relies upon infrequent grab sampling, it could be sometime before issues are identified and, in many cases, after the water has reached the tap. Through proactive online monitoring, unexpected changes in water quality can be swiftly identified, and when aligned with information such as rainfall, allows for urgent investigation, intervention and mitigating action.
Service reservoirs are essential for the effective operation of water supply systems and for ensuring customer taps keep flowing. By their very nature, they pose a risk to drinking water quality, therefore effective monitoring is vital to optimise usage and to forewarn of any issues. Advances in smart sensor technology, battery-powered units and mobile communications means that accurate, reliable and continuous monitoring is helping water utilities to make informed decisions on management and optimisation, not only ensuring that supply demands are met, but crucially that safe water is being delivered.
For more information visit analyticaltechnology.com
The MetriNet telemetry bollard provides street level water quality monitoring for distribution networks.
Our ultra low powered, multi-parameter, MetriNet smart water quality monitor delivers a modular solution for generating reliable and continuous data within distribution networks. With 16 parameters to choose from, the MetriNet telemetry bollard offers a secure and serviceable street level monitoring solution with less hostile environmental conditions, prolonging the life of the monitoring asset.
Creating intelligent, optimised, smart water networks of the future with MetriNet. analyticaltechnology.com
Water is key to a wide range of industrial processes, chemicals and materials production, and agriculture. There are few industrial sectors that do not rely on water in their value chain. Yet many of these processes create polluted wastewater which harms human health and the environment.
Water pollution is a challenge in need of a collaborative solution IN-PART regularly surveys and consults our network of 6,000 science, engineering and technology companies to understand the unmet R&D needs they are seeking solutions to.
Recent conversations with our industry network – including with water technology companies like De Nora, Evoqua, Hach and Puraffinity, and companies involved in water R&D such as Suez, Veolia, Southern Water,
Beko, and AkzoNobel – zeroed in on the fact that water monitoring and treatment was a major unsolved challenge across sectors.
These conversations, which included a series of webinars, uncovered a range of priorities.
The overarching message was a widespread need for new, more accurate, easy-to-use, rapid, continuous flow sensors, and new materials and techniques to remove a wide range of pollutants.
Much talk was about more accurate detection and removal of existing pollutants including particulates, heavy metals, and bacteria. Microplastics, PFAS, and organic pesticides and their derivatives, were also flagged as having a serious unmet need for detection and removal. Concerns were raised about nanoparticles –used in products such as hard-wearing paints and coatings, sunscreens, and self-cleaning
windows – where little is known about the health and environmental implications. What underpinned all of these commercial problems was that the solutions will require finely tuned devices developed by people with a deep understanding of the physical and chemical properties of these pollutants, and advanced analytical techniques. In other words, people in academia.
Our Global Challenge campaign was a vindication of this. Having broadly defined the scope of the challenge by surveying the research from academia already uploaded on our matchmaking platform, Connect, we invited the global research community to submit water monitoring and treatment solutions.
Despite widespread interest in finding innovative ways to monitor and remove pollutants and pathogens from wastewater, a significant unmet challenge remains, as Dr Robin Knight, of IN-PART, discusses.
In just six weeks we surfaced over 100 innovations from around the world previously unknown to our water industry network. Half (43%) related to the treatment of water for pollutants, 20% to the treatment of water for natural particulates and pathogens (20%) and 17% to the detection of pollutants in water.
Solutions we surfaced included a portable, low-cost, reusable sensor to detect and quantify up to 10 different PFAS molecules (New Jersey Institute of Technology); and robust, inexpensive sorbents to remove PFAS contaminants from water (Suny Research Foundation, NY).
Others included reusable smart filters based on polymeric compounds capable of trapping five of the UK’s most common pesticides, and a plant growth regulator (University of Lincoln). And a technique to capture silver nanoparticles – found in a variety of modern technology, from nanomedical imaging to toothpaste – in replaceable, easy-to-use capsules using a novel ion-exchange method (University of Massachusetts Dartmouth).
These and others have attracted considerable interest from companies looking for water treatment and monitoring solutions (here is a
summary of the top 20 water innovations by industry engagement).
We did not create any of these innovations –they have been developed by leading academic researchers in universities across the world. But thanks to the Challenge, we were able to connect those developing the solutions to those who need them. This matchmaking is important if we are to make progress towards solving global problems like water pollution.
Academic researchers all over the world are creating solutions to combat the greatest challenges we face today. But their work sometimes stays locked up in labs or on small local trials, and does not always make it into the hands of the right people working in industry who need the solutions. Similarly, people with the expertise and the research often do not appreciate its full range of potential applications around the world.
Partnerships between academia and industry are not a new thing, but their profile has grown in recent years, and the pandemic
in particular showed just how powerful academia-industry collaboration is, through the rapid development of life-saving vaccines.
A partnership between academia and industry is particularly advantageous when there is a problem in need of a complex scientific solution – especially one that involves advanced physical, chemical or biological analyses and an understanding of materials. Researchers bring specialist scientific expertise, industry brings an understanding of real-world need.
This Global Challenge campaign is a testament to this. Through this challenge, we’ve initiated 100 new conversations between industry and academia that otherwise would not have happened. Soon, some of these will turn into collaborations that make a real impact on reducing water pollution and improving water quality worldwide.
Dr Robin Knight is a co-founder of IN-PART, a service that matches research pioneers from academia with decision-makers in industry. The full results of the Challenge are detailed in a white paper published on the campaign alongside a full list of water treatment innovations.
The importance of industryacademic partnerships in solving global challenges
Partnerships between academia and industry are not a new thing, but their profile has grown in recent years, and the pandemic in particular showed just how powerful academia-industry collaboration is, through the rapid development of lifesaving vaccines.
According to government sources, there are 7,078 sewage treatment works (STW) in England and Wales, and 10,814 STW in Scotland and Northern Ireland. Pumping and storing sludge cake during the wastewater treatment process can be costly, driving water companies to technologies that reduce their volume to minimise such costs.
This can be achieved through conventional Anaerobic Digestion (AD) or through Advanced Anaerobic Digestion (ADD) processes, such as Thermal Hydrolysis Process (THP). ADD can reduce the volume of solids and increase the yield of biogas used to power engines. This can make plants energy self-sufficient or generate income by exporting power to the National Grid.
At Cotton Valley Sludge Treatment Centre (STC), one of Anglian Water’s ten main STCs, competitor’s progressive cavity pumps were installed to back mix the dewatered sludge and pump it into the THP. The two pumps were costing overall circa £100K per annum due to rotor and stator changes every 3-6 months.
Their inability to transfer no more than 3.5m3/h (bottleneck and limiting biogas production) meant the site was not able to meet the design criteria limiting the amount of imported raw cake being handled to only 120 tonnes per day. Additionally, before pump maintenance could be carried out, the silo had to be emptied. This also meant cake imports from satellite sites had to be diverted, which resulted in substantial logistical costs.
SEEPEX supplied and installed two custom-made open hopper pumps with a dimensionally identical hopper to fit within the same footprint of the original pumps whilst delivering over 55% increased throughput capacity from 3.5m3/hr to 5.5m3/ hr.
Prior to the installation of the new pumps, Anglian Water was processing approx. 120 tonnes per day of imported sludge cake with both pumps running. With the new pumps installed, the customer is now able to exceed this by 50% (from 120 tonnes up to 180 tonnes) whilst maintaining the same footprint and motor size.
“Due to the reliability and performance of the new SEEPEX pumps there is an increase in uptime of the cake import facility at Cotton Valley,” explains Luke Fish, Production Manager at Anglian Water. “This has not only allowed us to increase the sludge throughput on site and therefore generate more biogas but has also given us significant savings in logistics and raw cake storage costs.”
Existing competitor’s progressive cavity (PC) pumps at a large AD plant were unreliable,
causing downtime to the thermal hydrolysis streams. When the THP feed pumps were offline, this affected production and biogas generation. To address this, SEEPEX delivered a custom-made open hopper PC pump fitted with Maintain-In-Place technology to replace the original pump, incorporating condition monitoring and digital solutions.
SEEPEX Maintain-In-Place technology includes Rotor Joint Access (RJA) and Drive Joint Access (DJA) which simplifies maintenance and improves availability of equipment. To complement these features, the pump’s baseplate is manufactured in three pieces (on wheels) which enables individual sections of the pump to be removed for maintenance or major overhaul.
SEEPEX Digital Solutions facilitate preventative maintenance, equipment availability and process optimisation, which has a direct impact on reactive costs and biogas production – contributing to net zero objectives and increased sustainability.
Since installation, there has been zero downtime and no drop off in performance, and the sludge handling process has gained resilience.
SEEPEX open hopper pumps were used to replace unreliable chain conveyor systems. These pumps are used in two applications. Firstly, to transport the imported dewatered sludge from the imported belt facilities at
a capacity of up to 75 m3/h with dry solids up to 32% to either of the two pre-THP silos, enabling a 20-minute turnaround time for the trucks to unload and prevent backlog of vehicles. Secondly, to transport the indigenous dewatered sludge from the four decanting centrifuges to a third pre-THP silo.
Pump maintenance is carried out at ground level, improving health and safety issues associated with working at height with the previous conveyor installation. In addition, with the new SEEPEX pumps, the site now benefits from increased availability of their THP streams with subsequent improvements in gas yield.
To achieve the full benefits of advanced digestion by thermal hydrolysis requires reliable and efficient delivery of feedstock to the process. SEEPEX solutions combine back mixing expertise with open hopper PC pump technology to both transfer and blend imported and indigenous dewatered sludges to the precise DS % content. This ensures optimum digestion and maximises biogas production, reducing carbon footprint.
seepex.com
Wastewater treatment is 24-hour a day process, with domestic and industrial waste produced at all times of the day. Wastewater treatment is complex multi-stage process, but to meet these requirements many additional processes are needed to treat inflows, dose process chemicals, force particle sedimentation and remove contaminants to make water potable and waste safe for storage.
After waste has been screened for large objects such as wood, metal and plastics, flocculants are added so the solids precipitate in the bottom of the tank as sludge. Depending on the incoming liquid stream, additional chemicals may be added to neutralise contaminants or optimise pH levels. Lime, or milk of lime is one of the most widely used chemicals with excellent pH adjustment properties. Unfortunately, it is not an easy product to pump. It requires high line velocities and is highly abrasive, resulting in high rotor and stator wear rates on conventional pumps e.g., progressive cavity pumps. Traditional methods of lime dosing may prove tricky with frequent downtime.
Once the liquid has been through primary treatment, the treated sludge is transported to farms for use as fertiliser, or anaerobically digested to produce biogas which can be sold into national grid networks. A proportion of the sludge is filter pressed and shipped to landfill. Ferric sludge is produced after flocculation and is deposited at the bottom of settling tanks forming a sludge blanket. This sludge can be extremely abrasive, causing stator wear on a traditional progressive cavity pump. This results in needing to increase the pump speed to maintain the flow rate. This increased speed increases suction pressure and reduces the amount of settled sludge content as more water is pulled into the lines, ultimately contaminating the already treated liquid.
Waste water processes also need to verify the quality of the incoming waste stream and use analysers to detect the presence of contaminants or monitor key parameters that impact on downstream operations. Analysers need to be fed with consistent liquid volumes for optimum reporting and subsequent process control. Some pumps used in this application are not able to provide this reliability, so process control is less precise.
The Verderflex range of Dura peristaltic pumps are easy to install and maintain, significantly reducing downtime and minimising disruption. The pumps are extremely accurate and reliable, giving complete control over the treatment process. In the Dura pumps, the product is totally contained within the hose, eliminating the
possibility that any moving parts can clog or corrode. This makes a peristaltic pump the perfect choice for pumping high solid content slurries such as lime. In filter press applications, consistent suction reduces water content for drier sludge and lower waste disposal costs. Verder pumps are ideal for this type of application.
In testing scenarios, there are several pumps which could be used to improve the process. The new Verderflex Ds500 is ideal for metering and dosing and can give accurate quantities of liquid time and time again. As standard, the Ds500 is IoT enabled and can be monitored via the Remote Assistant app to provide process reports and updates for auditing purposes. The easy-to-change click and go cartridge can
be swapped in a matter of seconds, meaning nasty chemicals are contained.
Pumping wastewater sounds very easy, but often fluid contains long fibres and other abrasive solids. For water treatment a lot of different aggressive or abrasive chemicals are necessary. As a specialist for the water and wastewater industry, we can offer you a lot of different pumps which are designed with treatment works in mind and can handle most of the difficult fluids.
www.verder.co.uk
The perfect pumps: Verder provides pumps for every stage of the
If we took a short trip forward in time to 2040, and then looked back at how some organisations in the water industry successfully achieved Carbon Net Zero, it’s likely you’ll see a large four-letter word: NIGG.
This Scottish Water treatment centre in Aberdeen is currently leading the way as a centre of excellence for biogas production (from sludge), with its dedicated team tirelessly focused on improving efficiencies. This is a place that believes in ‘better’. It is also the first wastewater treatment plant in the United Kingdom to successfully co-digest.
The Nigg Wastewater Treatment Works, which was built in 2002, has made some significant steps forward since Scottish Water took over ownership and operation in December, 2018; working with Cambi to upgrade the existing THP (thermal hydrolysis process) and importantly, installing a new digester mixing system, from Landia.
From initially producing 250 cubic metres of gas per tonne of dry solids, levels have increased; first to 350, and has now climbed to an impressive 400 – 420.
The 400-plus figure is also being achieved without unlimited, costly power. Typically, if standard propellers were in use, around 17 watts per cubic metre would be required, but with the Landia system running at what amounts to less than 12 hours in a 24-hour period, only 7 watts per cubic metre are needed for the anaerobic digester mixing.
These latest numbers (at a site that has a small footprint for its energy output), are very much the result of fine-tuning and regular dialogue, as Nigg’s Operation Team Lead, Ewan Dickie, explains: “It is imperative that we understand the equipment and processes in front of us,” he said.
“And two years on since the latest improvements began at Nigg, Landia are always there to answer any questions we have about enhancing the mixing of our digesters.”
Prior to the upgrade, the facility had switched off the old compressor mixing system that had all too regularly caused problematical pipe blockages. The clean-out of the digesters for the upgrade revealed that 45% of the volume had been lost to grit and heavily compacted sludge.
“Now,” added Ewan, “we have an extremely robust mixing system that comprehensively mixes our two 4000m3 digesters. We don’t get any problems. The mixers just sit in the background, working away. The equipment is also so much easier to maintain, because it’s externally-mounted”.
Further evidence of Nigg proving how much energy from sludge can be produced at a wastewater treatment facility is its use of the biogas and heat from the Combined Heat & Power units (CHPs) for the site’s new boiler. £0.5M pa is now being saved on fuel oil. Two years ago, the original target set for utilising the CHPs (supplied by Clarke Energy) was 56%. It now stands at 73%. The CHPs were producing around 80% of the power required to run the site at Nigg. That figure has improved to the point where most of the time, Nigg is now exporting surplus energy to the National Grid. In addition to the intake from a local population of around 300,000, Nigg imports
sludge cake from a further six Scottish Water wastewater treatment centres, and has commercial waste delivered from approximately 30 tankers per day.
Since the introduction of the Landia digester mixing system and the upgrade of the Cambi THP, CO2 emissions have more than halved. The amount of biogas being produced has risen by more than 30%. In the first stage of the digester mixing process, the liquid (or sludge) is injected into the upper half of the tank, whilst biogas is aspirated from the top of the tank and mixed into the liquid. This not only has the benefit of reducing buoyancy at the surface of the liquid, but also sees the rising gas bubbles continue to mix after the pumps are switched off.
Cambi’s proven Thermal Hydrolysis Process (THP) exposes sewage sludge at Nigg to high temperatures (160oC to 180oC) and pressures (about 6 bar), typically for 20 to 30 minutes for each batch to ensure pathogen kill. Sterilised and hydrolysed sludge is passed to the flash tank, which operates at atmospheric pressure. The sudden pressure-drop leads to substantial cell destruction of the organic matter in the sewage sludge, which is then cooled to its optimum temperature before it is fed to the digesters.
Based on the proven ongoing success of Nigg’s biogas production, Scottish Water is considering the development of a further six sludge-to-energy facilities, which would represent a giant leap towards achieving the net zero target by 2040; five years earlier than the goal set by the Scottish Government.
We’re all for genuine innovation, but sometimes it’s not just about new technology; it can be about doing something differently. Cambi’s THP has been around for over 20 years, and the chopper pump, which is a key part of the digester mixing system, was invented by Landia back in 1950.
Simon Wrigglesworth, Operations Director for Scottish Water GrampianOne shouldn’t be blasé about hearing the word ‘innovation’ in the water industry, but some would argue that it has become so overused that it has begun to lose its real meaning due to static purchasing habits. Nigg though is full of innovation, with constant, gradual progress, according to Simon Wrigglesworth, Operations Director for Scottish Water Grampian.
“We’re all for genuine innovation”, he said, “but sometimes it’s not just about new technology; it can be about doing something differently. Cambi’s THP has been around for over 20 years, and the chopper pump, which is a key part of the digester mixing system, was invented by Landia back in 1950.”
He added: “It’s fair to say that at first, investing in the Landia mixing system seemed a bold move, because others were seen as a much ‘cheaper’ capital cost. But in an industry that promotes TOTEX, Landia were unmatched in providing meaningful numbers for the total cost of ownership, which showed that in the long term, they were in fact the least expensive option. We believe in what Henry Ford once said, that ‘If you do what you always
do, you’ll always get what you’ve always had’. For us, ‘average’, and ‘same old, same old’, won’t do. We are adding resilience. The performance potential of the Landia digester mixing system is massive.”
Part of Nigg’s genuine innovation has also been its willingness to undertake a 3-month trial to co-digest residues from local distilleries and breweries with its domestic sewage. Not only were 58 tonnes of carbon saved, but the plant saw methane levels increased from 60% to 64%. This first for the industry in the UK, which was led by the publicly owned water company’s commercial subsidiary, Scottish Water Horizons, could be just the start of a move that could have a major positive impact to a more circular and sustainable economy.
Keeping an ever-keen eye on all the production figures at Nigg is Process Engineer, Relina Dusa. During the past two years, she has worked on optimising the mixing with different run times, from 45 minutes per hour, down to 15. Operation now rests at 28 minutes per hour; not half an hour or thereabouts, but a very specific 28 minutes.
“We had a need for proper mixing and now we
1 4
2 3
Since introducing Landia’s digester mixing system and upgrading Cambi’s THP, CO2 emissions at Nigg have more than halved
Nigg’s Operation Team Lead, Ewan Dickie (left) with Paul Davies from Landia
Easy to service outside the digester, the Landia Chopper Pump that forms part of the mixing system at Nigg
Landia’s digester mixing system at Nigg now produces a consistent 400 - 420 cubic metres of gas per tonne of dry solids
have it”, said Relina. “It is important that we have experimented with different run times –and now I’m very happy with the gas yield of between 400 and 420 (cubes of gas per tonne of dry solids) that we’ve now reached. Over the past two years I have worked closely with Tony Challinor at Landia. We never have to wait for answers and feedback. There haven’t been any issues with the mixing system- and though it might sound like a small point, the Landia service engineers always clean up properly after themselves and leave everything tidy. We work well together.”
From what has been learned and continues to be learned at Nigg, the prospect of Scottish Water developing six additional similar sites will be a landmark for the water industry in what can be achieved with sludge when optimising biogas production.
Simon Wrigglesworth added: “We’ve come a long way with Nigg already. The water industry rightly has to focus on achieving regulatory compliance, but we’re always looking at how we can maximise the generation of green energy, in order to meet our commitment to reducing and ultimately eliminating carbon.”
www.landiaworld.com
For the plant to function, the first area to look at is ensuring the biology is “happy”. Keeping the biology in working condition enables the plant to work, so this should usually be the first point to check on any site managers checklist. If the biology isn’t getting all the necessary elements it needs, such as adequate food, aeration and nutrition, the plant will subsequently fail and lose performance, this can in turn lead to wastewater being discharged with certain measured parameters being out of consent.
The best way to assess the biology in the plant is to analyse it. OMEX offer full technical support and provide facilities to assess the performance of the bacteria in the plant. The fully accredited OMEX labs can offer an in-depth analysis and treatment of all the possible problems which can occur within the wastewater treatment industry. OMEX technical staff will collect a set of samples to establish the status of the biological process.
Once a full nutritional analysis of the plant has been undertaken, results should be analysed and discussed with a technical expert, who is able to advise on the best course of action to improve and
optimise the process. The OMEX technical sales team are able to assess the plant via lab analysis and in-depth discussion with the site operator/manager to gain a thorough understanding of any issues the plant is experiencing. Once this process is completed a tailored product programme is put together, along with recommendations and appropriate dosing rates to achieve the desired outcome.
OMEX offer a full range of products to help with the optimisation of the wastewater treatment process, including:
Magmex - an environmentally friendly pH neutraliser. In addition, Magmex contains certain compounds that are beneficial nutrients needed by the biology within the plant
Nutromex N&P (Plus) - strengthens the biology, stabilises performance and enables a more effective breakdown of the organic content in the raw wastewater
Micromex - when the plant is lacking in the number of microorganisms needed to process, Micromex augments the biology cultures, effectively breaking down the unwanted organics
Anomex - in activated sludge processes there is a risk of hydrogen sulphide in the sludge storage tank, Anomex is used to minimise the risk of sludge becoming septic.
At OMEX we understand the importance of keeping the wastewater treatment facility at optimum performance. Below our operations manager, Dimitris Theodoridis, highlights the key points to achieve the best performance from your WWT plant:
Achieve the best performance from your WWT plant
Scottish Water’s Kinneil Kerse WwTW produces an estimated 4,701 tds of dewatered sludge which is conditioned with lime for use as fertiliser on land. The sludge operation at this site has been funded and is operated by Veolia who are contracted by Scottish Water. In 2021, as part of a modernisation project delivered by Veolia, two competitor’s progressive cavity (PC) pumps were installed to feed dewatered sludge into a SEEPEX lime mixing pump.
After commissioning the new pumps, the site began to experience regular blockages in the discharge pipework which affected feeding the lime mixing process and sludge disposal. To clear the blockages the pipework had to be dismantled and the site incurred additional costs associated with the hire of a mobile lime dewatering unit. Veolia approached SEEPEX for a solution.
After assessing the installation, it was clear that the high friction losses generated when pumping 22-25 % DS sludge through 55m pipe length with a 3m. elevation including 3x 45° and 5x 90° bends were affecting the pumps’ performance.
To address this, SEEPEX offered a trial for their Smart Air Injection (SAI). SAI is an energy efficient system that combines a SEEPEX open hopper progressive cavity pump with pneumatic dense phase conveying technology. The system is able to transport 16-40% DS dewatered sludge up to 1,000m. with a lower operating pressure requirement than conventional technology.
We were very happy to work with SEEPEX to get this SAI system installed. It has given our site a solution to a difficult issue and resolved it. We use this system daily and it is beneficial to our day to day working environment.
Veolia
SEEPEX UK installed and commissioned the trial SAI system to demonstrate its effectiveness. Within the first 30 minutes of operation, SAI had cleared out all existing blockages and continued to perform.
SEEPEX retrofitted the SAI system to the competitor’s equipment. This included: SEEPEX SAI controls and MB Air Systems’ compressor and air receiver, both companies being part of Ingersoll Rand.
The SAI system has proven to be robust and reliable overcoming the existing pumps’ performance issues, enabling the sludge to be processed for land disposal. In addition, SAI enables the discharge pipework to be emptied when idle, removing the risk of blockages, thus reducing downtime and maintenance costs.
Commenting on this project, Veolia said: “We were very happy to work with SEEPEX to get this SAI system installed. It has given our site a
solution to a difficult issue and resolved it. We use this system daily and it is beneficial to our day to day working environment.”
SEEPEX and MB Air Systems have joined forces to deliver mission-critical, energy-efficient and market-leading technology for conveying applications. Our conveying systems are fully supported by a trained team of Field Service Engineers for service, installation and aftermarket support. Together we offer our customers our combined experience and technical expertise, providing one interaction point and one contract – for a streamlined project.
seepex.com
experts Logan
East Lothian-based Logan Energy are supplying and installing an electrolyser at a wastewater treatment plant in Cambridgeshire as part of an initiative led by Anglian Water, geographically the largest water company in England and Wales.
The project is being watched closely by water companies across the UK as it has significant potential to be scaled up.
Anglian Water says that Logan Energy were chosen to take part due to their ability to install as well as supply the type of electrolyser that meets the projects’ requirements, and because of Logan’s reputation for delivering support for innovative energy projects.
As part of the Ofwat Water Breakthrough Challenge, the Triple Carbon Reduction project, led by Anglian Water, aims to develop, and demonstrate a novel integrated solution. The plan is to investigate using treated wastewater through an electrolyser to create hydrogen and oxygen. The oxygen will then be used within a novel wastewater treatment process (Membrane Aerated Biofilm Reactor/MABR), targeting the reduction of nitrous oxide which is a source of greenhouse gas emissions.
The hydrogen could be used for different uses, in fuel cells, to displace diesel generators, or for local transport application. Also, by investigating using treated wastewater, the project aims to tackle resource recovery, without additional demand for drinking water resources and without compromising the water resilience needed to face climate change. The project will run for the until June 24.
Process emissions are a key priority for the water sector, as they are among the most difficult to tackle. It is hoped that by using an electrolyser to generate oxygen, wastewater treatment processes will see a reduction in energy consumption of up to 85% and a reduction in nitrous oxide process emissions.
And by using renewable energy at the treatment works, the hydrogen created by the electrolyser will be classed as green hydrogen, indicating it has not been made using fossil fuels.
If successful, there are industry-wide implications as the solution could be rolled out more widely and at a larger scale.
Other utilities partnering in the project and
We are excited about this innovative project, which will greatly support the delivery of the water sector’s drive to Net Zero by 2030, by aiming to reduce nitrous oxide emissions, increase the energy efficiency of wastewater treatment processes and generate a new renewable energy source via electrolysis.
Giulia Pizzagalli, Innovation Projects Manager at Anglian Waterexpected to share the learnings include Northern Ireland Water, Severn Trent, Scottish Water and United Utilities.
Bill Ireland, Chief Executive of Logan Energy, said: “Logan Energy is driven by the desire to help other businesses meet their net zero ambitions and provide intelligent energy solutions. So many of today’s carbon challenges can be met with innovative ideas involving hydrogen.
“Unusually for electrolysis projects, this project will use both the oxygen and hydrogen produced, further increasing the efficiency of the overall process. We’re excited to be chosen to take part in this important project with Anglian Water, which has huge scale-up potential, and look forward to seeing the results.”
Giulia Pizzagalli, Innovation Projects Manager at Anglian Water, said: “We are excited about this innovative project, which will greatly support the delivery of the water sector’s drive to Net Zero by 2030, by aiming to reduce nitrous oxide emissions, increase the energy efficiency of wastewater treatment processes and generate a new renewable energy source via electrolysis.
“This is a valuable opportunity to collaborate with Logan Energy. Their extensive expertise in the hydrogen sector will help our project advance the water sector’s position within the developing hydrogen landscape.”
In what is thought to be an industry first, hydrogen
Energy have been chosen to play a key role in a ground-breaking project designed to cut the carbon emissions associated with wastewater treatment processes.
A £50 million investment at Macclesfield Wastewater Treatment Works (WwTW) will use innovative technology to help improve water quality in the River Bollin.
The project, being undertaken by United Utilities at its site in Prestbury, will mean lower phosphorous and ammonia levels in the treated water that is released from the works back into the environment. The stricter targets, being introduced from the end of 2024, are driven by the Water Framework Directive (WFD).
To meet these lower nutrient limits, innovative Nuvoda Mobile Organic Biofilm (MOB) technology is being introduced for the first time at a United Utilities wastewater treatment works. This biological approach uses a highly renewable plant material to digest the sludge produced in the treatment process. It has a number of benefits, helping to optimise the wastewater treatment process, increase capacity, and improve nutrient removal, as well as being friendlier for the environment.
The investment at Macclesfield WwTW will also provide additional treatment capacity to meet the needs of a growing population and ensure monitoring of flows and stormwater discharges continues.
Alison Byrne, Project Manager at United Utilities, said: “At United Utilities we don’t just supply high quality water and treat wastewater – we also want to make our region greener, healthier, and stronger.
“Investing in our wastewater treatment works is a vital part of that goal, and the project at Macclesfield will ensure we can continue to treat wastewater to the highest standards and help protect our local waterways.
“It’s a challenging project as we have to ensure the new processes are installed offline while continuing to run the existing treatment works, but it’ll all be done within the current site footprint and with minimal impact to local residents.”
The water company recently showed Macclesfield MP David Rutley and representatives from Mottram St Andrews Fly Fishing Club around the wastewater treatment works and highlighted how the site’s facilities are going to be upgraded. During the visit
United Utilities also explained how a broad range of sectors with expertise and influence are working together to help continue to improve the health of the wider River Bollin catchment area.
Using innovative new technology the project will help ensure that the water is treated to high standards and improve the water quality in the River Bollin. I welcome this important investment and will continue to work with United Utilities on this and other initiatives to help improve the environment in our area and beyond.
David Rutley MPAsked about what he thought of the investment work, David Rutley MP said: “It is positive to see United Utilities making a significant £50 million investment to upgrade Macclesfield’s Wastewater Treatment Works. Using innovative new technology the project will help ensure that the water is treated to high standards and improve the water quality in the River Bollin. I welcome this important investment and will continue to work with United Utilities on this and other initiatives to help improve the environment in our area and beyond.”
Earlier this year United Utilities published its ‘Better Rivers, Better North West’ programme, outlining a £230 million investment plan to improve 184km of the region’s rivers..
United Utilities begins £50m investment to improve River Bollin through innovative wastewater treatment process
Yorkshire Water has partnered with Saveco to add a new sludge screen to its Woodhouse Mill wastewater treatment works – an industry first in the UK.
Known affectionately as ‘The Beast’, the new screen enables tankers to connect and pump sludge into it, rather than offloading sludge to a holding tank that is then fed into traditional screens by gravity.
The technology has been used successfully in the US and will be introduced to treatment process at Woodhouse Mill. ‘The Beast’ is fully automated and can quickly remove debris, plastics and other solids from sludge.
Ed Sutherland, project sponsor at Yorkshire Water, said: “We’re always looking at innovative ways to improve the operations of our wastewater treatment works. The Beast has been tried and tested in the US and will deliver significant benefits to the operation of Woodhouse Mill.
“Ultimately, it enables sludge to be pumped directly into the screen, rather than the traditional method of using an upstream storage tank that feeds sludge through screens via gravity. Removing the need for an upstream feed tank will result in significant capital savings, which ultimately leads to a reduction in costs and benefits for our customers.”
‘The Beast’ is equipped with an integrated perforated plate VSA Drum Screen which washes, conveys, and dewaters wastewater screenings, as well as a self-cleaning screen basket and self-cleaning dewatering zone to deliver maximum efficiency.
Comprising a dual motor drive powered by independent drum and auger speeds, max flow rates of up to 200 m3/h, a drum screen 5 to 6mm perforation and incline angle of 25 degrees designed to increase solids capacity, the “Beast” can also be connected through a Perrot joint to tankers or pipes. Designed without a lower drum support
arm, the Beast can be used to eliminate rag accumulation.
Rotating around its axis, the cylindrical filter conveys the screenings into a loading hopper placed in the centre. A set of spray nozzles washes the filter during operation. A screw placed inside the conveying pipe (with its top inside the discharge hopper), conveys the screenings towards the next treatment stage where organic substances are washed out. Subsequently, solids are compacted and dewatered in the compacting and drainage area and finally, solids are discharged
through a discharge chute.
The Beast will be trialled at Woodhouse Mill and, if successful, will be installed at other treatment works around the region.
Saveco’s municipal wastewater sector Manager Craig Webb said: “Achieving unprecedented success in the US market, the Beast is a game changer for how we will treat sludge going forward in the UK.
“We are delighted to have earned Yorkshire Water’s trust and confidence to remedy the complex challenge of sludge treatment.”
We’re always looking at innovative ways to improve the operations of our wastewater treatment works. The Beast has been tried and tested in the US and will deliver significant benefits to the operation of Woodhouse Mill.
Ed Sutherland, project sponsor at Yorkshire Water
When Portsmouth Water needed an emergency Cryptosporidium inactivation treatment process at one of their water treatment works, they turned to their AMP7 and NonInfrastructure Framework Contractor, Trant Engineering, to design, build, install and commission a suitable system and return the works to full operation within 13 weeks.
Trant set up a multidisciplinary client and contractor project team which identified Ultra Violet disinfection as the preferred solution. Sourcing the required UV treatment process within the short time frame was a difficult ask, however UV treatment’s simple configuration naturally lends itself to containerisation and Trant managed to identify and purchase a portable containerised UV treatment unit, which had been in use at another site, and this enabled the project to stay on programme.
Integrating the additional treatment process into the existing works operation and within the limited site space was a significant challenge. Te-Tech Process Solutions, who are part of the Trant Group, have a specialist team of controls engineers, and it was their expertise that helped deliver the integration.
The containerised UV system had its own local Compact Logic PLC and motor control centre (MCC), controlling duty and standby UV reactor streams, and this had to be integrated into the existing WTW control system which utilised an Allen Bradley PLC, providing overall control of the abstraction, treatment and water quality monitoring systems. The maximum works flow was too high for a single UV reactor, so the control system had to be changed from duty/standby to duty/ assist configuration. This alteration enabled a single UV reactor to operate within a defined flow and water quality range. If the single reactor failed the second reactor would resume control allowing the continuous compliant production of wholesome water. At high flow rate or if water quality deteriorates the system automatically reverts to duty/duty
mode, allowing both UV reactors to operate in parallel splitting the load equally between the two.
Integrating the signals from the UV treatment control system with that of the existing works was the next challenge for the Te-Tech team. The integration of the network architecture of the two control systems could be designed, tested and proven. The solution integrated the two PLC control system via Ethernet/IP as shown in the system architecture schematic (Figure 1, left).
As part of the integration package, Te-Tech modified the human machine interface (HMI) to allow key parameter and asset performance to be monitored easily. Operational flexibility was provided by allowing Operators to log in and change some parameters, such as setpoints and alarm limits. However, changes to parameters outside of the designed work and operating window were protected, ensuring that there were no water quality or treatment breaches. Key operational and performance data was retransmitted to Portsmouth Water’s remote telemetry system. This activity utilised the same communications network, by the
programming and configuration of a remote telemetry outstation and user terminals, via a Schneider GeoSCADA platform.
Te-Tech’s wide range of experienced electromechanical engineering and software programming talents, enabled all the required cabling, integration hardware and ancillaries to be designed, installed and tested in an efficient and professional manner. Their involvement in the project ensured that the implemented solution achieved the project’s objective, and Portsmouth Water was able to return the works to operation with a validated Cryptosporidium treatment process within the project period and before the increased summer demand.
Contact Te-Tech now on: 023 8235 1600 or email: enquiries@te-tech.co.uk
The report is a milestone for Thames Water’s Smarter Water Catchment (SWC) programme, and The Crane is the first urban river system in the Thames Region to be supported in this way.
Positive outcomes so far include the launch of the SWC Community Fund which offers small grants of up to £2,000 for capacity building of community groups. The SWC Large Project Fund offers grants up to £100,000 for projects delivering benefits across multiple themesboth launched in June 2022.
The programme has already supported the creation of a major new wetland at Headstone Manor in Harrow, and a rain garden in Pinkwell Green in Hillingdon, and has identified over 20 wetlands and sustainable drainage schemes across the catchment.
However, several challenges for river health are also highlighted in the report, including issues with habitat, water quality, river access and flooding. The SWC programme and joint report has identified the following five key themes to be addressed:
Promote public awareness, access, and participation
Enhance flood resilience
Improve water quality
Improve the river form
Enhance biodiversity – for wildlife and their habitats
Challenges to the natural environment of the river have been caused by concrete linings built into the river over 100 years ago. Improvements are already underway starting with the removal of a 30-metre length of concrete wall in the lower Crane in Twickenham, with further restoration planned along different parts of the river in 2023.
The report also reveals that access to the river is a significant challenge for some local residents and community groups: for example,
in places, there are a number of physical barriers to the river corridor where there is no through access from one section to another; in others, residents don’t use areas because of anti-social behaviour. This report will improve understanding of such issues so that they can be addressed going forward.
Richard Aylard, Thames Water sustainability director, said: “We’re committed to meeting our environmental responsibilities and that includes improving and protecting our rivers and streams. Whilst our partnership work and joint report for the Crane catchment shows a clear step in the right direction, we know we have a long way to go.
“Our five-step plan clearly outlines our ambitious strategy which will enable us to engage with more organisations and volunteers, whilst improving water quality and boosting biodiversity.
“As part of our turnaround plan, we’ve invested into the environment and launched our river health commitments. This includes a 50% reduction in the total annual duration of spills across London and the Thames Valley by 2030, and within that an 80% reduction in sensitive catchments.”
John Waxman, Crane Valley Partnership’s development manager, added: “The Crane Valley Partnership is delighted to have co-hosted the River Crane Catchment Conference with Thames Water as part of the on-going Smarter Water Catchment initiative.
“This was the first opportunity for a wide range of stakeholders, all sharing an interest in the protection and enhancement of the watercourses and open spaces of the Crane Valley, to consider the information presented in the brand-new State of the Crane Environment Report and collectively identify ways to respond to the challenges and opportunities highlighted in this landmark document.”
Thames Water’s wider £9 million Smarter Water Catchment programme covers the River Crane, River Chess and River Evenlode. The plans set out a 10-year commitment to boost biodiversity and help address water quality issues, as well as providing wider benefits for local communities through better access, improved amenities, schools programmes, volunteering opportunities and health and wellbeing benefits.
Thames Water and The Crane Valley Partnership have launched their State of the Environment Report for the River Crane, providing insights into the current health of the river and the challenges ahead.
We’re committed to meeting our environmental responsibilities and that includes improving and protecting our rivers and streams. Whilst our partnership work and joint report for the Crane catchment shows a clear step in the right direction, we know we have a long way to go.
Richard Aylard, Thames Water sustainability directorRichard Aylard
Water conservation is the key to reducing energy bills. Heating water accounts for nearly 1/5th of energy use in UK homes.
Reducing hot water demand is an effective way to help occupants conserve energy and reduce bills. Some uses are fixed, e.g. the washing machine or dishwasher, here education about full loads and eco settings can have an impact. However, many are not.
Showers account for a quarter of UK domestic water usage. To reduce this hot water usage there are three options:
Cold showers, not ideal on a cold winter morning
Shorter showers, using egg timers or a ‘favourite song’ to cut shower time
Flow reduction, less water is used while the shower is running.
The first two options require active engagement by all members of the household. The last is a fit and forget method of permanently reducing water use.
‘Eco’ or water saving shower heads are designed to restrict the water flow to a single outlet. They are highly effective but retrofits like these come at a price, especially larger properties with multiple bathrooms. They also do nothing for running taps, whether they’re in the bathroom or kitchen.
A second 1/5th of water usage is the taps in the house, e.g. rinsing the coffee cup, or washing hands. Again, flow restrictors can be fitted to each of these outlets.
For households on an increasingly tight budget, or developers trying to minimise costs, multiple fittings for each tap or shower might not be an investment they are able to make.
Household flow restriction for just £20 per property.
The alternative is whole site flow reduction. Fitting a device such as Groundbreaker’s NRv2 LoFlo®, at the meter regulates the level of flow entering customer premises – regardless of network pressure. As the flow of water into the premises is limited, then the amount used in ‘time controlled’ activities is also limited – but without providing a degradation of service. More importantly not requiring any intervention or behavioural change on the part of the customer, so leading to ‘natural’ reduction in consumption.
Our water companies are regulated to provide a minimum level of water supply, but in many areas, due to network structure and gravity fed systems, supply is much greater. Households in high pressure areas could be receiving up to three times the required minimum levels. So, run a hose for five minutes at the bottom of the hill, and your lawn will be greener that the gardener that does the same at the top. ‘Time controlled’ uses could be reduced if all households received the same acceptable, ‘standardised’ supply.
Independent research carried out by WRc, showed a theoretical reduction of 2-4% of typical water usage when devices such as LoFlo® are installed. However, recent field trials by a major UK water company have showing savings of 5%.
As part of UK Net Zero Carbon targets water companies have been targeted to reduce the water householders are using, Per Capita Consumption (PCC). PCC reduction targets average just under 6% in the UK, so utilising property flow restriction could achieve just 1% off the average PPC reduction targets!
However, water companies are also tied to customer performance commitment levels (C-Mex), and some seem to be concerned that a reduction in the supply levels to properties will prompt customer complaints, offsetting the financial rewards of achieving PCC targets.
Field trials of devices such as LoFlo®, have shown that most customers are not aware of supply levels in their property, within certain limits. Especially when moving into a new property, customers accept the levels as ‘being what it is’ and fears of an increase in customer complaints impacting C-Mex values are overrated. In recent trials in England, where occupants did notice the change in supply, it was the positive impact of reduced flow that was cited, e.g. reduced splashing at the kitchen sink.
Not a single occupant wanted the LoFLo® to be removed after the trial period.
The NRv2 LoFlo® can be easily and simply retrofitted to any meter installation, or meter exchange when upgrading or remediating underground meter chambers. Thus, allowing Water Companies to manage demand, with little or no impact on consumers, at the minimal cost of approximately £20 per household.
As the LoFlo® is fitted at the water meter, it is the water companies fitting. Therefore, developers must be proactive in challenging water companies to provide a standardised supply to help UK housing stock to achieve water consumption targets.
For further information www.groundbreaker.co.uk
As digitisation spreads across sectors and industries, technology is rapidly changing the customer experience landscape. The digital transformation underway across many organisations in the water sector is enabling smoother interactions that remove friction for the customer and improve efficiency for the business. However, there’s also a risk in trying to digitise too much too fast. The key to unlocking the promise of innovative technology lies in how it combines with the level of personal interaction to ensure an empathetic connection with customers. This is the equation that water companies should strive to balance on both sides.
By Jo Causon CEO, Institute of Customer ServiceDigitisation and how it applies to customer service is a theme we explored in depth at The Institute in our recent research called A Connected World?. This found that many customers are embracing technology and welcome many of the advancements it is bringing. In particular, customers are using apps and also enjoy being able to self-serve for transactional requirements like checking bills, browsing options and finding essential information.
However, when it comes to more complex and personalised matters – and especially when there is a problem – most customers still want and expect to be able to talk to a real person and receive direct, human attention.
While nearly three-quarters (73%) of the 1,000 customers we surveyed described themselves as confident users of technology, this still leaves a significant proportion who are less assured. In addition, 23% of respondents said they currently help a friend or family member to deal with an organisation online or digitally.
This is a reminder that there remain significant sections of organisations’ customer bases who are not well-adapted to
We asked customers to identify a channel or technology they used to contact an organisation which resulted in a particularly positive or annoying experience. The findings suggests that experiences with artificial intelligence-enabled chatbots are more likely than experiences in other channels to cause annoyance, rather than satisfaction. Indeed, most of the digitally active customers we interviewed recounted (unprompted) a frustrating experience with a chatbot. Email and phone calls were associated with the highest number of positive customer experiences, perhaps reflecting the widespread use of these channels to deal with organisations.
Thinking of your interactions with large organisations like banks, retailers, utilities or travel companies, which technologies have had the biggest impact of your customer experience?
the technology environment. This can be for many reasons. Some simply prefer traditional ways of interacting with organisations; others are wary of data privacy and confidentiality; while others – often for financial reasonsmay not have the equipment or broadband access to engage digitally. In addition, there are vulnerable customers who may straddle any of the above categories or have special needs when interacting online.
Organisations such as water companies that provide essential services have a duty to cater for all of these diverse needs and preferences. In assessing the risk of digital exclusion, they need to consider how they will enable communication both with vulnerable customers who have challenges in using technology, and customers who prefer not to engage through digital channels. As essential service providers, achieving the right blend
Artificial intelligence-enabled chatbots are more likely than experiences in other channels to cause annoyance
of technology and in-person service becomes even more important.
Regulators and government have a key role in monitoring customer service outcomes for vulnerable people, setting minimum standards and encouraging organisations to share practice. As technology develops and organisations seek to offer differentiated customer experiences to digitally confident customers, it will be increasingly relevant to assess fairness of customer service outcomes for all customers.
But what are the benefits that organisations introducing greater levels of technology into their service delivery are unlocking? Our research finds that many are using technology to improve workflow processes, bolster analytics for better decision-making, and to achieve better integration of data.
Some of the most impactful applications empower employees to deliver better service experiences: real-time prompts based on analytics of similar customer interactions, increased visibility of relevant data, and analysis of interactions with customers to identify training needs. One striking example is the role of customer service advisers as “digital coaches” – helping customers to use digital channels, stepping in where they are experiencing a problem, but doing this with the customer and, therefore, improving customer knowledge and capability as well.
One lesson we see clearly in our research is that it is vital to provide a variety of channels through which customers can contact and interact with the organisation – because individuals have a range of preferences and experiences.
Overall, email, apps and phone remain the most positively rated channels, with webchat not far behind. It is notable, however, that automated chatbots emerge as amongst the least satisfying and most annoying experiences for many customers – frequently because they take people on a ‘circular loop’ and don’t provide satisfactory solutions. AI capabilities are moving very rapidly, and the transformational potential it offers may be just around the corner. However, it’s clear that successful deployment of chatbots requires excellent design and structuring of customer journeys, thorough testing – and quick human intervention when it is needed.
Source: A Connected World?, Ensuring the right blend of people and technology for customer service, The Institute of Customer Service, 2022
The best service approaches will see a blend of the technological and the human – working in combination to support and complement each other.
We also see successful organisations using technology and customer data to help predict likely spikes in contact from customers. In the
water industry, this might mean identifying the early signs of a significant leak for example. Preventative action can then be taken – protecting the customer experience and alleviating the pressure on the contact centre before it happens. Ensuring that there are good communication flows between operations and customer service is therefore essential.
It is also crucial that the implementation of technology is not seen solely through a cost saving lens. With the cost of living crisis that is upon us, I am concerned that more organisations may look for cost efficiencies by increasing their use of technology and automated service, at the expense of their human customer service teams. This would be a mistake. If Covid taught us anything, it was the importance of human support
and interaction through difficult times –something that the water and utilities sectors were right at the forefront of.
Without doubt, many water companies and utility providers have further to go in their digital transformation journey and how they weave new technology into the service model. This can in fact be a strength, because it enables them to learn from the experience of others and take a considered approach.
I am sure that we will see increasing advances in the sector moving forward. The key to success will be to achieve the right balance of human and tech that covers the needs, expectations and priorities of all sections of the varied customer base that relies on them to provide one of the very essentials of life.
More than ever before, today’s customers have high expectations and water utilities’ customers are no different: their provider should be able to deliver a seamless service, with little or no inconvenience to them or their day-to-day activities
Echo Managed Services, the experts behind Aptumo, provide specialist customer service and billing solutions to the water industry. Decades of sector-specific experience and direct engagement with customers confirms that their needs and, more importantly their expectations, are changing.
One of the top five recommendations for businesses in all sectors, according to the latest UKCSI report from the Institute of Customer Service, is to develop strategies to tackle or prevent problems before they affect the customer. In the water sector specifically, implementing smart tech could be the best way to achieve this goal.
From infrastructure to customer service systems in contact centres, implementing smart tech should be a collaborative, one team effort, with the objective being to detect any issues before they can impact the customer experience.
A full end-to-end review of existing customer journeys and touchpoints will inform the introduction of suitable smart technology that will give the provider full visibility of the water system, enabling them to better understand what their customers truly want and need.
Every partner involved in the review, design, and implementation process will share their knowledge and skills to improve the overall customer experience. It’s paramount in any smart tech project that this remains at the heart of the collaboration, and customer benefit is the objective.
Introducing smart tech that enables a water company to detect issues which may cause problems helps to reduce customer complaints and ensure that customers don’t get a surprise either with their water supply or bill. Embracing smart tech enables all elements of the water supply journey to work together to benefit the customer.
Water companies should be able to identify any potential issues themselves; relying on customers to report problems means reputational damage could already have been done. Introducing smart tech gives providers the tools they need to pre-empt issues with water supply or billing to minimise any impact on the customer.
By constantly monitoring systems to detect any changes in performance, water companies can rectify issues before they become a problem for consumers. There’s no one-sizefits-all approach but, following a full review of existing customer experience, first steps should include introducing tech that gathers performance data such as changes in water pressure, for example. By noticing faults promptly, teams can be notified to carry out repairs before the customer becomes aware.
If an issue is likely to take a little longer to fix or there may be an impact on water supply, service teams can contact customers to prepare them for any disruption. They can also direct customers to any support they may need if their water supply is disturbed.
Introducing smart tech can also improve the customer experience by helping to ensure that a higher than usual bill doesn’t come as a surprise. Having a system that monitors supply, considers any change in household circumstances, and continually monitors usage, means customer service teams are well-equipped to have conversations with customers about billing and affordability.
Ideally, any changes to billing should be due to something the customer is aware of; it should never be because of a system fault or increased consumption that was beyond the customer’s control. Having a proactive system that identifies leaks quickly, before they develop into serious incidents, should help to reduce any impact on customer bills.
Being able to constantly monitor usage gives water utilities intel that allows them to contact
a customer if, for example, there’s a noticeable change in household consumption. Customers don’t always realise the impact that changes to the number of people in the household or introducing new water dependent appliances can have on their water bill. If the customer service team identifies an unusually high bill before it’s sent to the customer, they can make contact in advance to ensure that the customer understands why their bill has increased and provide any support they may need to help pay it.
Proactive systems are key to maintaining and further improving satisfaction ratings among water customers. In the July UKCSI report, the average customer satisfaction for water companies was up 1.5 points since July 2021, with satisfaction settling at a respectable 76.1 points. The research showed that 42.7% of respondents said any complaints were dealt with immediately, and 38% said that the resolution time was quicker than expected.
Whilst this data largely reflects very well on the water sector, there’s clearly still room for improvement which can be achieved by taking steps to both reduce the number of complaints and manage them quickly. Proactive customer service that works with the right tech and involves real collaboration between the partners involved in managing the customer experience means that satisfaction could be greatly improved. It removes the frustration of unexpected issues with supply or bills and allows people time to seek out support if they face any financial or practical challenges. If water providers are to keep up with ever changing consumer demands, implementing smart tech really is the future.
Digital sustainability, a key concept in today’s world, stems from the far-reaching digital transformation that companies have to tackle and the need for them to exploit their data to add value. Understanding this concept and how to be digitally sustainable in the water sector is also essential in terms of flexibility, operability and cost savings.
Digital sustainability is a must in this day and age. Although we have lived through different industrial revolutions, none of them is comparable to the so-called Industrial Revolution 4.0, which entails the profound digital transformation of companies. It involves technological changes, as well as shifts in company culture, in the way we communicate, organizational flexibility and even in the different strategies required. Yet data exploitation is always the driving force behind all these changes.
In the face of these developments, water utilities have to implement changes so that they can offer a better service, making the most of the characteristics of this new industrial transformation such as 5G, greater operational agility, interconnectivity, more data, and greater access to information. However, these changes must be preceded by a comprehensive assessment of all the areas that make up a utility, pinpointing the ones which require improvement.
However, it is important to highlight the difference between sustainable digital transformation and digital sustainability. While the former refers to the use of technology in an environmentally friendly way, digital sustainability in the water sector can be defined as the process by which companies access and exploit their data thanks to intelligent solutions and applications to integrate this data, regardless of the vendors. In this regard, digital sustainability means the entire company speaks the same language, and is able to create improvement indicators (KPIs) and dashboards to enable it to make the best decisions.
Digital sustainability means companies can improve communication, standardizing language and avoiding information silos. However, there are other advantages that should also be taken into account:
The digital sustainability of water utilities guarantees the smooth operation of the system regardless of the number of users. In this case, we are talking about horizontal scalability. There is also vertical scalability in which more resources are added to meet the needs of a larger number of users.
In any of its forms, it guarantees that the system responds despite the increase in users and data.
Digital sustainability guarantees longer system life cycles thanks, in part, to the digital transformation process, which does away with the need to have several suppliers, or the implementation of solutions such as GoAigua, a tool that offers a holistic overview of operational digital infrastructure components, bringing all the systems into one, standardizing language and avoiding the need to constantly change parts of the systems to achieve this coordination.
As previously mentioned, digital sustainability means the company speaks the same language. This will lead to improvements in operational management, greater control over situations, real-time alerts about possible incidents, shorter response times, and improved functions in general, thanks to automation.
Companies can reduce costs thanks to greater durability and improved operational management, since there will be no need to replace infrastructures, delay processes or involve more stakeholders in them.
One of the main advantages is the ability to interconnect systems to break down
information silos, bring data together and make recommendations for action based on real-time information.
Digital transformation is key to the conservation of water resources, to decisionmaking and to the improvement of demand management. It can take place via a bottomup process, where it is carried out as specific problems arise, or via a top-down process, where a well thought-out roadmap is followed. The latter of course requires greater effort but also offers further-reaching results.
In any case, it is a must for water utilities, which have no choice but to redefine their processes and organizational culture to keep pace with current circumstances. Digital sustainability must be factored into this process if utilities are to become more efficient in terms of water management, offer a better service to consumers and reduce their carbon footprint.
idrica.com
The event took place at the Royal College of Pathology in London, but the body of water infrastructure was the one under examination on this occasion, not least, the health of the instrumentation monitoring some 375,000 combined sewage and stormwater overflows (CSOs) in the UK wastewater network.
“A lot of that data we know is false,” Grieveson said, “because of the quality of what we’re doing with instrumentation.” He also reflected on the “sheer volume of data about the hit the water industry” as new instrumentation comes online in the next few years, and the challenge to the people tasked with making sense of it.
The conference gave delegates the opportunity to hear updates from a number of winners of Ofwat’s innovation competitions first hand. The projects led by Yorkshire Water, Anglian Water, Severn Trent Water, South West Water and United Utilities are funded by the £200 million Innovation Fund set up by the regulator to help grow the water sector’s capacity to innovate.
First up was Yorkshire Water’s Blockage Predictor Project set up to identify sites at risk of pollution. With sensors deployed across the utility’s CSO asset base, Heather Sheffield, the utility’s integrated planning & central control manager (wastewater), said 24% more blockages had been found and 65% were detected earlier than previously.
Speaking of the value of finding the right partners to collaborate with, in this instance German technology company Siemens, she said, “One of the challenges we have
is that concept, culturally, that we can do everything ourselves – and we just can’t. This partnership has helped accelerate some of this thinking and the implementation of AI [artificial intelligence] across our asset base to help us manage service risk.”
Next was Anglian Water’s £8 million Safe Smart Systems Project (SSSP), which involves 26 partners, and focuses on the first steps to achieve autonomous control of UK water systems. Presenter George Schley, consultant business architect/analyst at US engineering company Jacobs, explained that digital solutions need to be scalable and adoptable by other water utilities.
“Defining the common language” is one of the most important things in the SSSP project, he said, promising that an information management framework (IMF) was an output of the project that would be “shareable with everyone”.
Schley also spoke of the challenges of getting data from operatives in the field who are sometimes working under the most difficult circumstances, at night and in bad weather: “People are one of our most important sensors.” he said.
His thoughts on the importance of people were echoed by South West Water data scientist James-Pascal Mercer, who is involved in another Ofwat funded project examining the effect of tourism on arealevel water demand in Devon and Cornwall and how it can be used to make predictions.
After sharing results showing greater correlation of visitor numbers and demand in coastal areas, he said, “The operators
already knew intuitively what the data revealed from their years of experience. We wanted to verify it.”
Gigi Karmous-Edwards, founder and cochair of the Smart Water Networks Forum (SWAN) work group for digital twins, said that setting best practice on these advanced digital tools is an important next step. Building on the theme of a shared language, she proposed that everyone adopt a common definition of a digital twin as: “A dynamic digital representation of real-world entities and their behaviours using models with static and dynamic data that enable insights and interactions to drive actionable and improved outcomes.”
The meaning of open data given consideration by a number of speakers, with Adam Cartwright, head of IoT applications at Siemens asking, “Data open to who? Interoperability is more important than openness. The public don’t need to know the efficiency of a pump, they need to know the outcome.”
Thanking delegates at the end of the packed day, Tracy Britton, chair of British Water’s Data & Analytics Focus Group, and smart water solutions director at Jacobs, came back to the theme of collaboration: “We have to get better at not just talking about collaboration, but enabling it,” she said, highlighting the Ofwat projects and the need to take them out of silos and “bring everything together”.
The event was sponsored by Innovyze, an Autodesk company, which provides digital software for water professionals.
Transformation of Anglian Water’s treatment and recycling processes is being made possible by trials of artificial intelligence (AI) driven software developed by Norwegian technology company InfoTiles.
The digital analytics company is collaborating with the UK utility on a 12-month pilot project focusing on biofilters and anaerobic digestion. Both types of biological processes and assets are integral to the treatment of wastewater and a key aim of the collaboration is to enhance operational visibility and decisionmaking around asset management.
The initial trial of the InfoTiles software will monitor the rotating arms of biofilters at 15 sites to assess whether they are rotating when needed. It will also involve measuring sludge blanket levels in primary settlement tanks at a further 15 sites, to ensure they stay within optimal ranges for effective operation.
The data, collected from a mix of new and existing sensors through Anglian’s existing supervisory control & data acquisition (SCADA) systems, will be combined with flow rates and publicly available weather data to build a rich contextual overview of what is happening at the water recycling plants in real-time.
InfoTiles can also combine Anglian Water’s existing SCADA systems into one event streaming platform that can aggregate, compare and visualise reliability of the equipment. This same platform allows Anglian Water to trial different sensor technology and compare the reliability and accuracy of the different sensors undergoing testing.
InfoTiles’ strength lies in the ability to visualise and model process data through machine learning to show the likelihood of critical failures in wastewater treatment, such as potential stoppages and breakdowns.
This will give Anglian Water, one of the UK’s largest water utilities, the ability to anticipate, detect and resolve potential problems. By continually assessing the health and
effectiveness of assets, maintenance teams can be deployed much more efficiently.
The two companies were brought together through WaterStart, a US-based membership platform which seeks to remove common barriers to the adoption of innovative technologies and connects utilities and municipalities with solution providers globally.
“We are so proud to be involved in this pilot programme, which will transform the way we manage our water recycling sites,” said Adam Jessop, optimisation technologist at Anglian Water. “Collaborating with international companies through WaterStart has helped the team to work at pace to find solutions and ways to improve the service provided.”
The overall aim of the collaboration is to enhance operational visibility, create more informed decision-making, and understand
where and how to prioritise maintenance of the water company’s assets.
Adam Wood, chief product officer at InfoTiles said, “Our Nordic customers use InfoTiles to guide their maintenance decisions with real-time data. Our team is enthusiastic to collaborate with the technicians and analysts at Anglian Water to tailor the InfoTiles platform to enable better, data-driven, maintenance at this major UK utility.”
Nathan Allen, executive director at WaterStart, said, “InfoTiles have proven the technology works in the Nordics, and WaterStart is thrilled to support the company’s expansion into the UK market. Effective data management is a global challenge for water utilities and it is exciting to see the outcomes of the pilot as the technology is expected to be broadly scalable among our global membership base.”
Our Nordic customers use InfoTiles to guide their maintenance decisions with realtime data. Our team is enthusiastic to collaborate with the technicians and analysts at Anglian Water to tailor the InfoTiles platform to enable better, data-driven, maintenance at this major UK utility.
Adam Wood, chief product officer at InfoTiles
Illegal work such as dredging, realigning and gravel removal on watercourses continues to have a negative impact on the animals, fish and plants that make their home in and around Welsh rivers and streams.
These types of modification cause long-term damage, potentially lasting many decades with harm to habitats and species often extending miles downstream from where the modification work occurred.
Oliver Lowe, Geomorphology Specialist Advisor for NRW, said: “During lockdown, Wales experienced an unprecedented increase in unconsented physical modifications to its watercourses, including dredging, removing shoals, realignment of water courses and inappropriate bank protection.
“We set up a Physical Harm to Rivers task force to improve our response to such incidents and we have delivered more than 30 regulatory notices on unconsented work.
“Our improved response is changing landowner behaviours as word of our action spreads. We also have the option of pursuing prosecution if the incident is particularly
severe. Should a notice not be complied with then this can result in a fine and criminal prosecution.”
Regulatory notices are legal documents that can be issued to a landowner or contractor to stop unconsented work and restore the harm caused.
Oliver added: “Protecting our rivers and the wildlife that depend on them is a priority for us and we are using these notices to great effect.
“For example, in 2021, works were undertaken on a river to install a gabion basket wall which resulted in the narrowing of the channel, increased water velocity, erosion, flood risk and destruction of river habitats.
“Our officers visited the site to stop the work and then issued a formal notice to restore the river channel.
“Today, the landowner has restored the bank profile, reseeded the ground with native wetland grasses and wildflowers and willow and alder trees are being planted on the bank to improve stability. Once the plants have established, this site will
resemble a natural riverbank bursting with native species and supporting the riverine environment.”
Hilary Foster, Specialist Advisor for Freshwater Habitats and Species for NRW said: “This work is part of our Wales-wide River Restoration Programme which also includes the delivery of ambitious river restoration projects.
“Our improved response to these incidents is successfully protecting our rivers from harm and supporting our goal of ecosystem resilience. This work has generated interest from the regulatory authorities in England, Scotland and as far afield in Norway.
“Anyone considering undertaking any work on a watercourse should contact NRW for advice. We will provide information on any necessary permissions and measures to avoid environmental harm.
“If you do not consult NRW prior to undertaking works on a river or stream, you are at risk of committing an offence. Enforcement measures may include the requirement to restore the damaged habitat.”
A task force set up by Natural Resources Wales (NRW) to tackle illegal physical modifications to rivers and streams across the country has resulted in more than 30 legal notices to stop and remediate served on landowners.
Ageing water systems face a number of well-documented challenges such as growing urbanisation, water scarcity and extreme weather events. This is why water utilities worldwide are moving to more advanced operational management solutions using the Internet of Things (IoT), says Harold Mosley, Product Engineering Manager for i2O and Hydro-Guard, Mueller Water Products and David Kenny, International Sales Director, Water Management Solutions.
IoT devices can provide valuable insight into the operational efficiency of a water system and give utility operators the analysis and intelligence necessary to help make informed decisions for performance improvement. In some cases, advanced technology uses algorithms to automatically adjust system, or device, operations to improve the overall performance of the distribution network.
For Halifax Water (HW), after hitting a static level of breaks and nonrevenue water (NRW) loss, the challenge is increasing leak awareness to reduce run time. Headquartered in Halifax, Nova Scotia, in Atlantic Canada, the integrated water utility serves a population of over 430,000
and supplies high-quality drinking water to more than 85,000 service connections.
As part of its commitment to customers, the utility is continually focused on innovation and has been internationally recognised as a ‘leader’ in NRW management. This includes finding new solutions to reduce water leakage and manage system pressure to extend the life of its assets while meeting customer expectations.
As part of its 2021-22 Annual Business Plan Halifax Water is developing recommendations to reduce NRW loss. HW had already tried several
approaches to advanced pressure management, including flow modulation, but were open to a new trial and comparing the results.
To help support these plans, HW partnered with Mueller for a performance trial of an advanced pressure management and control platform. This solution has been successfully deployed by Mueller in many water utilities across the globe and is being introduced to North American utilities.
Kevin Healy, Operations Engineer with HW said, “We’ve worked with Mueller in the past, so we were eager to start the trial. Additionally, from a deployment perspective because our system already had district metered areas (DMAs) with pressure reducing valves, and access to an enabled LTE-M cellular network.”
While sub-division of the network into DMAs enables closer management of pressure and leakage, pressure monitoring and control solutions can also be effective in open networks.
The pilot program included three phases of implementation.
Phase one of the pilot program served to evaluate the communication and reporting functionality of the pressure loggers as well as the data analytics, notification alarms, and data visualisation of the Sentryx™ Intelligent Network cloud-based software service. A total of three pressure loggers were installed – two single-port pressure recorders within existing air release valve chambers, and one triple-port pressure logger to record inlet, outlet, and control chamber pressure of an existing pressure reducing valve (PRV) station. (see figure 1)
Sentryx Intelligent Network is a highly available, highly secure software service that stores data and maximises the value available from it by applying machine learning algorithms and visualises it in the most actionable formats -- including maps, graphs, and tables.
Figure 4 – APV and Controller Installed on a 4" Singer 106-PR Pressure Reducing Valve in Halifax
During phase 1 of the pilot program, HW was able to derive valuable insights about its network that it did not have before and see these using the software service’s maps and graphs. Some of the most interesting insights included the detection of pressure surges and transients at one of its air valve installations as seen in figure 2. It is a standard feature of the loggers that they collect statistical data that enables transients to be detected. In addition, a routine fire flow test could easily be identified as seen in figure 3. While HW previously had pressure sensors reporting to SCADA, the i2O data loggers, by Mueller enabled the utility to monitor pressure and flow at air release valves (ARVs) and other locations without existing power and communications, without the expense of adding power or communications in an existing chamber.
The ‘Zinck PRV station’ seen in figure 4 has a 4" PRV main supply and 10" PRV fire flow back-up. It is the only primary feed into the Mowatt Intermediate DMA, as seen in Figure 5. The PRV was retrofitted with the Advanced Pilot Valve (APV) with the existing PRV pilot system still installed but valved off to allow for back-up control during routine maintenance. A control logger was also connected to the PRV. Utilizing the APV and control logger, the PRV can now be controlled remotely with the new advanced pressure management system.
The Mowatt Intermediate DMA characteristics are as follows: Number of connections: 479 (476 residential & 3 non-residential)
Total length of water main: 4.0 miles (6.4 km) (mainly 8" cast iron)
Number of fire hydrants: 37
Number of mainline valves: 52
Figure 8 – Optimised PRV Control - Mowatt Intermediate DMA
As the first proof of concept to HW, the APV pilot was locally set and programmed to operate as a normal fixed outlet PRV. The current PRV pilot system on the 4" PRV was set to a constant 71 psi, and the APV was programmed to regulate the PRV output to the same 71 psi outlet pressure. Figure 6 shows how smoothly the APV unit kept the PRV outlet to 71 psi.
Healy said, “I was impressed with how well the PRV outlet pressure was maintained – particularly in low-flow scenarios. The Sentryx software allowed us to change the PRV setpoint remotely and even adjust the opening/closing speeds of the PRV to offer an even smoother outlet pressure.”
Once the new pilot proved its ability to regulate and keep a constant outlet pressure, HW moved on to test control using ‘flow-modulation’. In flow modulation, the PRV outlet pressure is varied based on the actual demand in the DMA. This allows a lower pressure set point at night when demand is low and system head-loss is at its minimum. During peak demands, pressure is increased to overcome system head-loss and ensure sufficient pressure within the DMA. Flow modulation is ideal for lowering pressure in off-peak demands to reduce leakage flows and the occurrence of water main breaks. It also responds quickly to increase pressure at peak demands or for fire flow requirements. Figure 7 illustrates the performance of the APV pilot and pressure controller in flow modulation mode for the Mowatt Intermediate DMA.
Rather than setting fixed or timed outlet pressure from the PRV, in Automatic Optimisation mode, the system takes in data from the PRV and from a logger placed deeper in the network at which the water utility wants to deliver fixed pressure levels. That position is called the ‘Control Point’. All the user needs to do is set the target
pressure levels required at the control point by time of day and day of the week. The Sentryx Intelligent Network software service does the rest: it receives data from the PRV control logger and the Control Point logger and calculates the optimal control curve to achieve the target pressure. It then makes adjustments to the PRV outlet pressure continuously. The profile is created in the software service, then sent down to the Control Logger. It takes just 1 week to be confident in its first curve. The curve is automatically re-calculated regularly to account for changes in demand. These may be seasonal or may result from changes in customer usage in that area of the network over time (e.g., the building of new housing). The system ensures that pressures are maintained at the minimum viable level at all times. This in turn reduces leakage and the likelihood of pipe bursts. This method of optimised pressure management gives HW the highest level of security of supply while reducing NRW loss.
Figure 8 shows how the Mowatt Intermediate DMA performed under the Optimised PRV Control Mode.
Although the DMA flow profile and ‘night flow’ for the Mowatt Intermediate zone shows that there is very little leakage in this zone, HW was still able to obtain savings from the optimised PRV control mode. Under fixed outlet control, the average daily DMA demand was 55 kGal/day (210 m3/day). In optimised PRV control mode, the daily DMA demand was 54 kGal/day (204 m3/day) – a savings of 1000 gal/ day (6 m3/day) or 2.8% of the average daily demand. In a pressure zone or DMA where leakage levels are 10, 20, or even 30% the savings would be significantly higher.
Mueller’s off-the-shelf advanced pressure management solution can be installed quickly and is supported by an intuitive dashboard. Additionally, the combination of mechanical and control logic fail-safes provides the security redundancy needed for such devices.
The initial emergency response before the arrival of the Selwood team had been to use a fleet of 29 tankers to take the water away – a noisy and costly operation with a significant environmental impact.
The job at hand was to install an efficient over pumping solution that would bypass the damaged sewer, covering 550 metres from the pump station to the next gravity manhole.
The site was a difficult one due to its location on the public highway and close to the active tram network. Because of this the local authority had to approve all movements.
Works around the tram lines could only happen during a limited time when the tram service was shut down, and equipment could not be lifted to a height above three metres to avoid disrupting the overhead tram power cables. In total the tram was shut for 31 hours across a weekend
After assessing the site, Selwood’s team specified a set of eight-inch suction pumps, pumping into a 300mm discharge line. Due to the wet well being too small submersible pumps were not an option for this project.
Instead, three electric-powered S200 75kw Selwood Super Silent sewage handling pumps were installed in a Duty/ Assist/ Standby configuration to ensure uninterrupted operation. These were chosen for their reliability and ability to lift water out from the wet well even more capably than submersibles could.
To minimise disruption to residents and traffic, four road ramps were used to allow access to local businesses, including a nearby timber yard which was the source of regular HGV movements, and a private boat yard.
A 12-inch mag flow meter was used to monitor flow from the pump station. This helped indicate when the road ramps were starting to rag up and would need cleaning. Tankering points were added along the drain line to enable regular inspection and cleaning.
For the works around the tram lines, a height-restricted crawler crane and low loader trucks were used to keep works clear of the overhead cables.
Despite the challenges, the job was installed in less than a week. The use of electric pumps as specified by Selwood saved a huge amount of time and cost along with significantly reducing the environmental impact of the works.
Continuing to tanker away the water would have cost well over £400,000 for the duration of the works, with the Selwood alternative
www.selwood.co.uk
Selwood’s pumping solutions specialists were able to greatly reduce the financial and environmental cost of works to repair a leaking sewer in Nottingham for Severn Trent Water. The leaking 600mm rising main gravity sewer had the potential to cause serious disruption, as it was on a main road crossing within a few metres of tram tracks and could have burst or created a sink hole.
As explained in the recent ‘Customer Experiences of Sewer Flooding’ report published by Ofwat and CCW; “being flooded with sewage is one of the most distressing things that can happen to you in your home. The lasting effects it leaves behind are not just limited to damaged property, but can extend to psychological and emotional damage, often leaving people in vulnerable circumstances”.
Cleaning up these incidents can be expensive in financial terms, but customer-side incidents can also incur additional costs. News travels fast via both traditional and social media, and when these instances occur, a water company can very quickly experience expensive reputational damage both locally and nationally.
Additionally, every time a customer calls in to report an overspill (either CSO or SSO) it has an impact on the water company’s Output Delivery Incentives (ODIs), which if not achieved, will lead to strict financial penalties.
With all of this to consider, when a UK water company was looking to be proactive in identifying problem areas in their network and deal with blockages before they spill, they turned to HWM.
Driven by a desire to identify spillages before they happen, the water company approached HWM, as a trusted long-term partner, for a simple but effective solution; and we recommended SpillSens.
SpillSens is our multi-alarm digital float sensor that uses digital positioning technology to monitor sewer levels constantly and effectively.
Installed hanging in the chamber, rising sewer contents affect the position of the sensor and should the tilt of the SpillSens sensor reach a specific angle then an alarm is sent to the water company. The sewer can then be investigated and any necessary action to negate the cause of the level rise can be taken.
Programmed with three alert levels, SpillSens indicates green when conditions are normal, amber when levels are rising and red when critical levels are reached. This level of information is helpful in supporting water companies to make resource allocation decisions.
The water company chose SpillSens over more traditional level sensors because they were specifically concerned with picking up blockages quickly, especially in small and shallow customer-side inspection chambers, where level sensors could suffer from deadband issues.
SpillSens was seen as a more definitive solution as opposed to regular level sensors. If, after a rainfall event, a SpillSens sensor angle does not return to 0o then there is a problem, whereas in contrast, level sensor data will not be anywhere near as clear cut, and requires analysis at every site, every time.
The water company has benefitted in numerous ways from the deployment of SpillSens in problem areas of their network. Significantly, a much lower customer incident rate is being reported, which has reduced the ‘reactive’ cleaning, jetting and rodding being undertaken. This is contributing to a marked improvement in ODI performance, which is delivering a sizeable financial benefit.
The use of SpillSens is providing vital data to help identify additional problem areas
in the network, highlighting locations that could require development or upgrades and supporting decision making throughout the wider network.
www.hwmglobal.com
The spillages and pollution incidents that result from sewer blockages can have devastating consequences, particularly when these incidents happen customer-side.
A wastewater intelligence solution is helping improve community health in a partnership first between Scottish Water and Kando. Water Industry Journal spoke to Dr Andrew Engeli, CSO at Kando, about the shared vision for a smart networked wastewater system.
Wastewater treatment is a priority for the UK government.
Raw sewage from storm overflows and harmful wastewater emissions are an escalating problem, with water utilities often under-equipped to respond to the resulting public health challenges.
Effective wastewater analysis can have a game-changing impact on community health, using technology to monitor the spread of viral diseases or measure the impact of specific community health initiatives.
Kando is implementing its cutting-edge wastewater management technology across hundreds of assets for Scottish Water, using a real-time alert system capable of unlocking a range of actionable insights.
As Steven Boon, Wastewater Treatment Area Manager for Scottish Water, says, “We were impressed by the offering, experience, and professionalism from Kando which should enable us to bring this wastewater treatment works back into compliance.”
Kando is an Israeli-based company with a proven track record in the field of wastewater intelligence, having spearheaded Israel’s efforts to track COVID-19 and its variants in collaboration with Israel’s Ministry of Health. So just how novel is its approach?
Andrew explains, “We’re at the forefront of AI and IoT innovation in the field of wastewater analysis providing software that, through automation, can generate instant insights into what’s really going on inside urban sewage systems, helping municipal
authorities pinpoint how and where they need to intervene to manage water networks most effectively, to improve public health and protect the environment.
He adds, “With wastewater quality a growing health and environmental concern, we help government authorities accurately detect and pinpoint the sources of reduced wastewater quality thanks to a first-of-its-kind hyperlocalised comparative wastewater quality analysis, helping them track down entities and organisations violating hygiene regulations.
“We are working with partners, investors, and clients to improve public and environmental health all over the world. We also support water utilities, which bear the ultimate responsibility for the quality of the wastewater that their networks emit, in bringing their technology up to date and
fitting it for purpose through AI-powered big data analytics and predictions, reducing risk and mitigating legal and compliance concerns.”
Kando’s solution will provide Scottish Water - for the first time - with the ability to know when and where contamination is accumulating in their assets, helping them ensure that all assets are working properly.
Andrew says, “This will have a multifaceted effect increasing levels of regulation compliance, policy observance, and cost reduction.
With wastewater quality a growing health and environmental concern, we help government authorities accurately detect and pinpoint the sources of reduced wastewater quality thanks to a first-of-its-kind hyper-localised comparative wastewater quality analysis, helping them track down entities and organisations violating hygiene regulations.
Steven Boon, Wastewater Treatment Area Manager for Scottish Water“In the UK today, there is no other technology that provides such a holistic solution to water utilities, implementing state-of-the-art AI technology in wastewater and subsequently providing unique value and visibility into what is happening in a water network. Once a water utility has access to this invaluable information and insights, they can manage their assets and networks more efficiently and save costs.”
In December 2021, Kando and Israel’s Ministry of Health (MoH) combined in a unique project using wastewater analysis to track COVID-19 throughout Israel’s sewage system, the first time a single technology provider has provided such instant insights uniformly across an entire country. The partnership used data drawn from within the collection network to support accurate COVID-19 outbreak mapping across service areas.
Andrew explains, “Kando’s solution uses real-time, in-network condition monitoring and cloud-based data analysis to ensure findings represent viral loads accurately. Live data inputs from in-sewer IoT units are used to determine when effluent contamination might compromise results, preventing automated sampling when conditions are not ideal. Working with lab and deployment partners, Kando provided the MoH with geographically defined outbreak data, pinpointing infection hotspots via a live online dashboard.
“The partnership enabled officials to aggregate data from every population centre with more than 20,000 residents (85% of Israel’s population), gaining a full picture of COVID-19 rates without requiring individual tests. This method indicated outbreaks and their locations up to 6 days ahead of conventional testing, providing an early warning system
to anticipate outbreak waves and detect variants.”
In short, using wastewater intelligence helped authorities monitor spread of the disease without relying on the population to come forward and get tested.
Scottish Water’s system will ‘hit the ground running’, collecting raw data from strategic locations on the network. Together with historical data, it will create a unique base line of predicted behaviour and identify abnormalities, correlating them to types of industrial effluent and “pinpointing the source of the exact location of each behaviour that impacts the asset”.
Andrew adds, “Our system can provide insights into the source of the events in the network, the severity of the event, its timespan, and eventually, after characterising it, the type. Most of all, it will allow the water utility to identify the source and take the relevant actions to stop it from occurring or re-occurring.”
Turnaround time on testing depends on the nature of the event being analysed and its findings. Some insights can be shown instantly through a real-time online dashboard, while lab-analysed results are typically turned around within several days, and within 36 hours at a minimum.
Andrew points out that further down the line, Scottish Water can leverage Kando’s technology and its expertise to tackle a range of questions whose answers might be found in water systems: detecting future pandemics, overcoming high levels of drug use, reflecting the quality of the population’s diets, monitoring wastewater being reused for agricultural needs, and more.
He says, “Using the Kando system will allow Scottish Water to manage their assets differently, as by harnessing the data, they will know 24/7 what, when, and where every abnormality is accruing, and prevent it from happening. This will allow the asset to perform in compliance with regulation and also optimise its efficiency and reduce the overall costs of operation.”
Looking forward, it’s hoped that Kando’s network intelligence can mitigate problems like pollution, water waste and climate change and boost real-time decision-making. Andrew concludes, “These capabilities are only scratching the surface. As investment into the industry increases, more capabilities will be discovered to further support healthy communities and environments.”
Dr. Engeli was previously Deputy Director for Innovation at the Joint Biosecurity Centre (JBC) and Deputy Director for EMHP at the UK Health Security Agency.
Just like humans, wastewater treatment plants can get sick through viral attacks. Research from Chalmers University of Technology, Sweden, reveals the implications for the local environment if a plant gets ‘sick’.
In the sewage industry, the ‘work’ of wastewater plants is often executed by microscopic bacteria. Biological processes carried out by these bacteria turn the wastewater into cleaned water that is safe to discharge into the environment. Essentially the bacteria break down the pollutants and purify the water, keeping the plant running efficiently.
“A large treatment plant has billions of bacteria that work in a treatment process called ‘activated sludge’,” says Oskar Modin, Professor at the Department of Architecture and Civil Engineering at Chalmers.
“The bacterial communities are constantly exposed to viruses that infect them, so the question we asked ourselves was whether the process can periodically be more exposed and what happens then.”
Researchers measured the concentration of virus particles released from four different wastewater treatment plants in Sweden and compared this with how much organic carbon was released at the same time. This relationship between virus and effluent quality is a first step in understanding the impact of a viral infection on a treatment plant.
The study showed a clear relationship between virus concentration and the amount of dissolved organic carbon present in the effluent water. This is because viruses could affect the concentration in two ways, firstly because they themselves contain
The activated sludge process at a wastewater treatment plant and virus particles visualised using nanoparticle tracking analysis - Chalmers University of Technology
carbon and secondly because they rupture host bacteria cells, causing carbon to be released.
“When we measured virus particles in the water, we found a connection between viruses and organic carbon – when there was more of one there was also more of the other,” says Oskar Modin.
More dissolved organic carbon in the effluent water means that more oxygen is consumed by microorganisms in the surrounding bodies of water where the effluent is discharged.
Oskar adds, “Viruses are often specialised in a certain species, which means that humans and bacteria cannot be infected by the same virus. So, the viruses ‘generated’ in a wastewater treatment plant do not infect humans, but only affect microbial communities. One possible way to influence the number of viruses in treatment plants could be to adjust the way the treatment plant is operated. We saw differences between the treatment plants in the study, which we believe may be related to the design or control of the biological treatment processes.”
When we measured virus particles in the water, we found a connection between viruses and organic carbon – when there was more of one there was also more of the other.
Oskar Modin, Professor at the Department of Architecture and Civil Engineering at Chalmers
This could have potential negative impacts on nearby aquatic ecosystems. Therefore, tough regulations are in place for wastewater treatment plants to reach low concentrations of biodegradable organic carbon in their effluent. A small increase of organic carbon in the plant can also lead to increased resource consumption, including money, energy and materials in processes for disinfection and pharmaceuticals removal, which are implemented at wastewater treatment plants in some parts of the world. Organic carbon in the water affects the efficiency of these processes.
Viruses are dependent on a host to replicate. Since biological wastewater treatment processes have a high concentration of active bacteria that can serve as hosts, there will be a lot of viruses capable of infecting those bacteria. This leads to a net increase in virus particles as the wastewater moves through a plant.
The scientific article “A relationship between phages and organic carbon in wastewater treatment plant effluents” published in Water Research X was written by Oskar Modin, Nafis Fuad, Marie Abadikhah, David l’Ons, Elin Ossiansson, David J. I. Gustavsson, Ellen Edefell, Carolina Suarez, Frank Persson, Britt-Marie Wilén
The researchers are active at Chalmers University of Technology, University of Connecticut, Gryaab AB, VA SYD, and Lund University
The study behind the paper was financed by Svenskt Vatten through VA Teknik Södra, and involved wastewater treatment plants in the Swedish municipalities of Lund, Malmö, Kalmar and Gothenburg. Funding was also provided by the Swedish Research Council for Sustainable Development (FORMAS).
The world’s aviation industry urgently needs low-carbon liquid fuels — now seen as the only practical means of meeting its targets for reducing carbon emissions by 2050. These kinds of Sustainable Aviation Fuels (SAFs) emit 80% less carbon over their life cycle compared with conventional jet fuels. There’s no need for expensive investment in new aircraft or new infrastructure, SAFs are a plug-and-play solution for the industry.
The global market for SAFs is huge, due to be worth $6.2 billion by 2028. The problem for the moment is solely production capacity. Like all other types of biofuels, SAFs need feedstocks, and these are either in short supply or come loaded with other environmental issues.
Levels of interest in SAFs are growing exponentially. Last year saw the first commercial flight with a full load of passengers using 100% SAF for one of its two engines. Rolls-Royce has confirmed that all its engines will be SAF-ready by 2023. The US government has taken a lead on incentivising the use of SAFs through its Inflation Reduction Act (IRA) 2022 and has a goal of enabling the production of 3 billion gallons of SAF by 2030, with a trajectory of growing production facilities to deliver 35 billion gallons a year by 2050.
In 2020, the industry was reporting $7bn worth of SAF offtake agreements (arrangements where buyers agree to purchase goods that will be available in the future). This figure has increased to $25bn and rising.
Current production rates of approved SAF technologies, however, only meet a small fraction (less than 1%) of the actual fuel demand from commercial airlines.
Biofuels in general are in demand. The UK government and many others have signalled their support for the increased use of biofuels as a stepping stone technology until electric and hydrogen alternatives for transport become viable. This just means a constantly growing pressure on supplies of feedstocks — and higher unit costs — which make transition to low carbon transport a challenge.
The UK continues to be a net importer of biofuels, with most of its supply (traditionally at least) coming from Ukraine, China, the US and the EU. With government plans to increase the mandate for ‘biofuel blending’ in transport fuels to 14.6% by 2032, there is only
going to be more competition over land use internationally: more land being turned over to bioenergy crops rather than food; weakening food security; damage to local economies; and higher prices for biofuels.
The Intergovernmental Panel on Climate Change (IPCC) has warned that the shift to using land for bioenergy crops is leading to deforestation, land degradation, increased use of chemicals, water pollution, and is a serious threat to wildlife and biodiversity. A controversial crop like palm oil — with its significant contribution to carbon emissions — is increasingly being grown as a biofuel. It will be critical for the aviation industry not to simply shift its carbon impact onto agricultural businesses that are growing palms for example.
Using municipal sewage sludge to produce SAFs will be a genuinely sustainable foundation, addressing both waste management and low-carbon energy demand. As a feedstock, the scale of supply more than works. It is estimated that around 53m tonnes of sewage sludge are produced every year that require to be treated in the network of around 200 sludge treatment centres in the UK.
The UK’s wastewater system is heavily over capacity, meaning storm events (or even, in some locations, just a light rain) regularly lead to raw sewage ending up in rivers and seas.
According to Environment Agency figures, there has been a 37% increase year-on-year in incidents: meaning 9 million hours of sewage
being pumped into rivers and seas since 2016. Finding alternative uses for sewage sludge will be a huge benefit to businesses, to the environment and society as a whole.
The FIREFLY project, funded by Department for Transport as part of its Green Fuels, Green Skies competition, has shown how this can work; it has proved that the quality of the resulting biofuel will meet strict industry standards; and led to the engineering design and construction of a demonstrator plant for production. With further industry investment, the project is due to lead to a first-of-a-kind commercial refinery and the development of a network of UK sites close to airports, pipeline terminals and wastewater treatment works. The integrated processes involved will also reduce the processing costs involved and help keep unit costs low. Alongside other development pathways, the FIREFLY technology is expected to become a strategic asset for the UK as part of the broader national SAF portfolio.
Costs for SAFs will remain relatively high, at least for the short-term. Which is why the huge potential for SAFs — and the opportunity for a circular economy approach to their production — will only be realised with a clear mandate from governments, stimulating mass uptake of SAFs, more investment from finance institutions and a rolling cycle of lower costs for every stakeholder involved.
Dr Ying Jian is Senior Lecturer in Bioenergy, Centre for Renewable and Low Carbon Energy, Cranfield University, cranfield.ac.uk
What if sewage sludge from wastewater treatment could be used as a feedstock? A solution to waste disposal issues and a means of providing an additional revenue stream for water companies? Cranfield University - academic partner to Green Fuels Research and energy services company Petrofac -- has already proven its viability as Dr Ying Jiang reports.Dr Ying Jiang
In the September issue of WIJ, we made extensive responses to government consultations underpinned by Position Statements, and set out some general principles:
A more ‘connected approach’ is needed for initiatives, including a ‘road map’ and overarching strategy
To meet many of the aspirations for a better water environment, it can’t all be left to the water companies. They must provide excellence in operational delivery but changing societal practices is not their sole responsibility. There must be a greater role for Citizen Science coupled with Citizen Delivery.
To meet aspiration, practical experience needs to be blended with academic insight and innovation. An understanding of societal psychology is also required (anything to do with sewage is dominated by the ‘faecal aversion barrier’, an essential part of public health hygiene).
Relatively straightforward practical policy changes could include:
Removing the automatic right to connect to the public sewer network
Making water companies a statutory consultee in planning processes
Tighter product regulation and customer information on packaging to reduce sewer blockages and reduce water consumption
New developments should have a legal requirement to deliver SUDS (with exemptions in prescribed conditions)
Improve the processes for dealing with disruption to roads and access when water infrastructure is being put in place or repaired.
As mentioned in September’s article, a broader approach generates innovative thinking. For example, the Consultation on Environmental Targets proposes that phosphorus loadings from treated wastewater are reduced by 80% by 2037 (against a 2020 baseline).
Defra wants water companies to explore innovative, nature-based, and catchmentbased approaches. The Consultation also set demanding targets for agriculture.
But as an example of the ‘jigsaw approach’, the government issued further instructions on 20 July 2022 requiring treatment of sewage discharges in nutrient neutrality areas to be upgraded to the highest technically achievable limits by 2030. The statutory duty to do this will be incorporated into forthcoming Levelling Up and Regeneration legislation.
Nutrient neutrality is already causing debate about delayed housing development; and fuller sewage treatment is promoted as a major solution. These are still end of pipe solutions.
We have suggested that reducing phosphate in diets could be one way to help achieve targets. Half is added artificially and the NHS already issues advice on reduction for patients with renal problems.
The government also wants to reduce water demand long term (see the consultation on Environmental Targets), but consumers will have to play a role in dealing with water leaks. The complexity of delivering this is already defined in Ofwat’s consumption targets (but not yet Defra’s) and leakage management has gone well beyond the old ‘watershed’ of economic levels.
A return to river quality objectives is needed to achieve local delivery using a set of national principles. We need an overarching National River Strategy based on existing Basin and
Catchment Plans, which should include quality criteria for recognisable uses, with public consultations on uses within defined stretches of rivers.
This could then be combined into a quality specification for each stretch to decide:
discharge consents (including separated surface waters)
river flow regimes, using models such as SIMCAT, under the future Regulations of the Environment Act.
Getting this right will be essential for a robust regulatory framework, including Ofwat’s role.
Including nutrient neutrality could create a very different programme for overall phosphate reduction. By linking to 25year Environment Plan targets and other environmental initiatives, integrated decisions can be made to best manage the phosphate cycle, whilst recognising that phosphate is an increasingly scarce resource.
We believe the designation of bathing waters should be part of this strategy, but also part of a wider consultation. Expectations may be raised which can’t be delivered in practice and won’t be the best course of action within the context of storm overflows - a major, but not sole, factor in healthy bathing waters.
We back a review of national committees, even a revival of Royal Commissions. The impact of demographic change on the environment should also be revisited as it overshadows issues addressed in the consultations.
The Environment Act provides an excellent framework, but the Environment Plan has lost its focus. An overarching water strategy is needed urgently which sits within, or informs, the Plan, so that water targets fit together better.
‘End
In the second part of his comment on water quality management, Peter Matthews of The Worshipful Company of Water Conservators, discusses strategic issues and practical examples of change which can bring immediate benefits.
Selwood’s reputation as the UK’s number one pump rental solutions provider is built on the quality, reliability and longevity of our products and our ability to provide a solution for your pumping needs.
Providing efficient, suitable, safe, integrated solutions using both surface mounted and submersible pumps.
Available from our comprehensive network of UK branches, all our pumps and solutions come with the Selwood guarantee of specialist support and outstanding service. www.selwood.co.uk