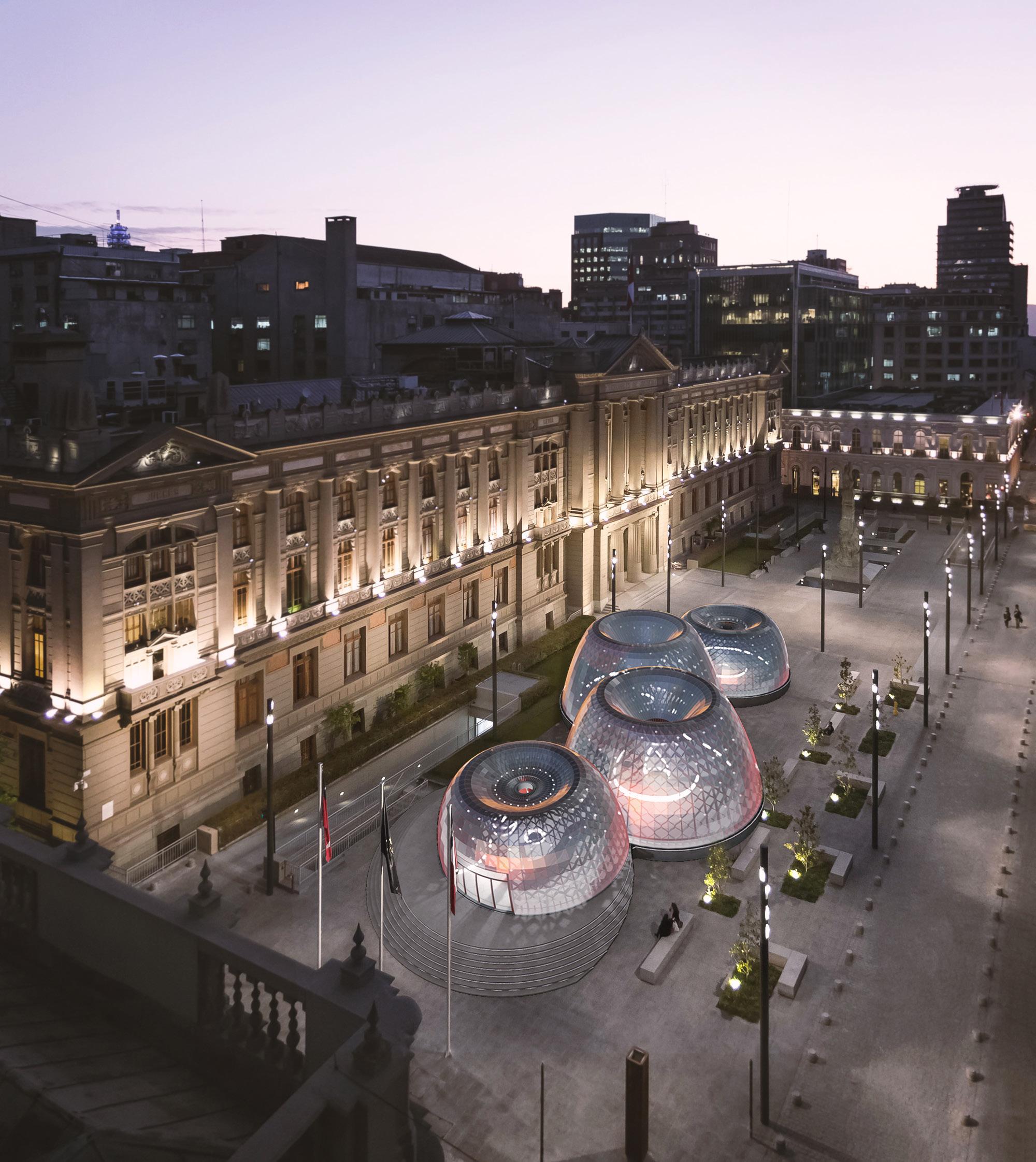
5 minute read
Audi showroom
- portable showroom -
Type: Showroom
Advertisement
Year: 2019
Location: Tehran
Area: 1020 m²
Status: Concept & Reasearch
Architects: DNA Groups
Brief:
The purpose of this project was to design a mobile car exhibition, which according to the choice of Audi company, the final form of the exhibition was chosen and designed inspired by the logo of this factory. Since this exhibition should be able to be moved, at the end of the research, the construction method was chosen using the active bending method. Bending-active structures are structural systems that include curved beam or shell elements that base their geometry on the elastic deformation from an initially straight or planar configuration. In this project, all the facilities, including sanitary facilities, ventilation systems, and light and water supply, were selected using mobile facilities and according to the final goal of the project. In fact, all these facilities can be off-grid.
Contributation to the project:
Idea Development
Modeling: Rhinoceros 6.0 & Grasshopper & Sketchup
Rendering: Lumion 8
Presentation: Photoshop 2020
Structural design
In a dynamic context of rapidly evolving user needs, transformable structures anticipate and respond to changing demands in minimal time, with minimal effort. Innovative structural concepts should supplement the design of transformable structures to increase their structural and functional efficiency. Therefore, we defined transformable active bending as a combination of the principles of mobility and rapid assembly of transformable structures, and the utilisation of bending deformations in bending-active structures. Although it is the availability of state-of-the-art design modelling techniques and structural modelling tools that facilitate design exploration and form-finding of bending-active structures, accurate modelling of the complex relation between their geometry and bending behaviour remains challenging
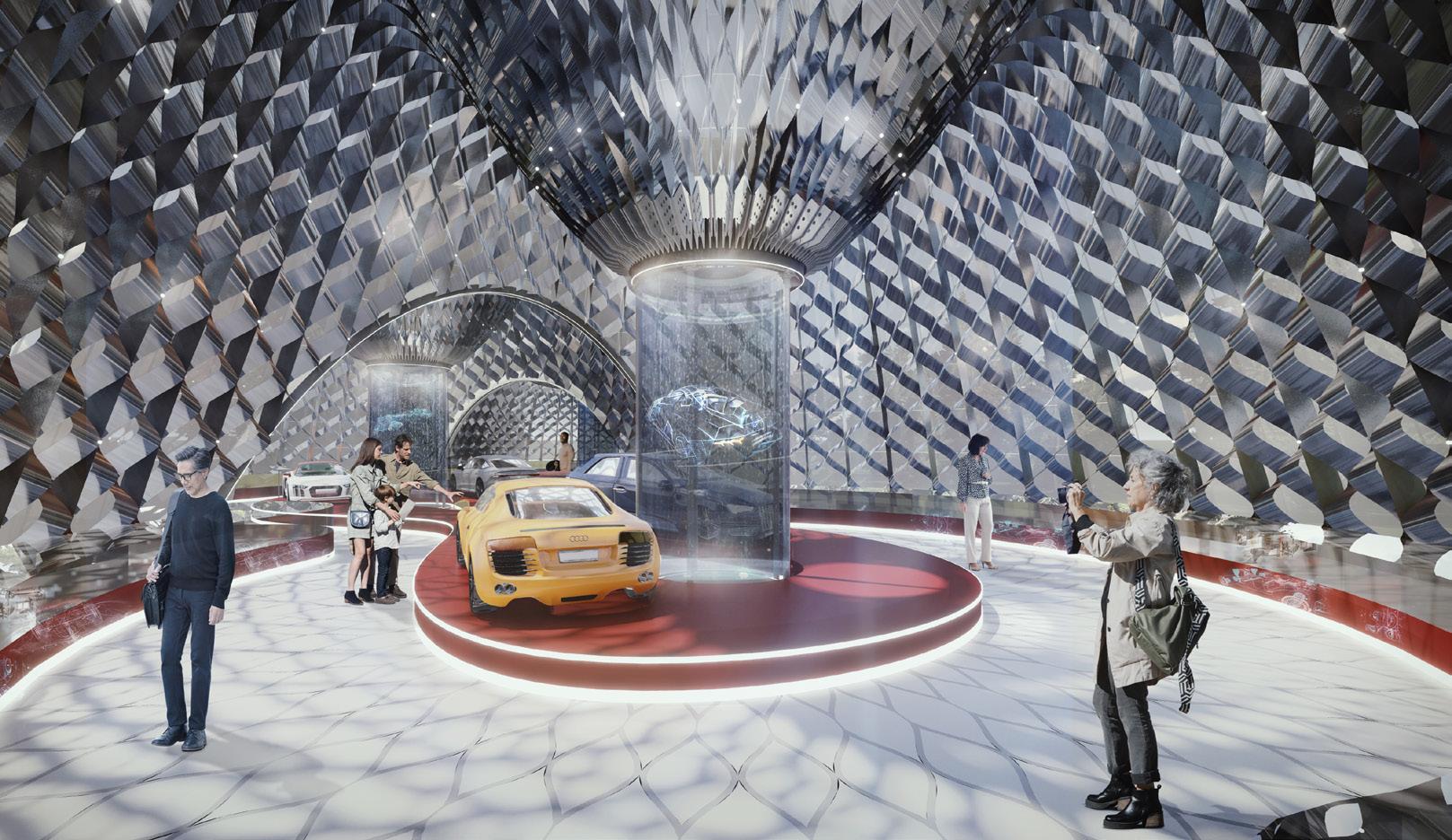
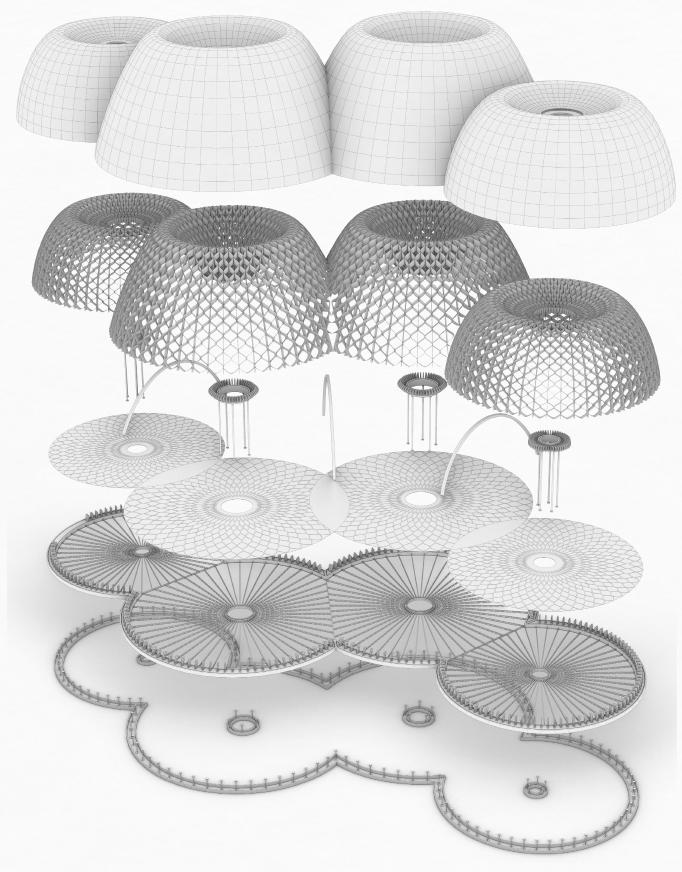
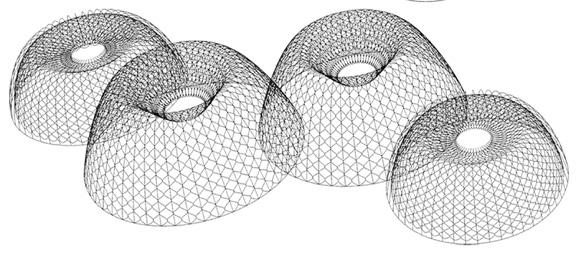
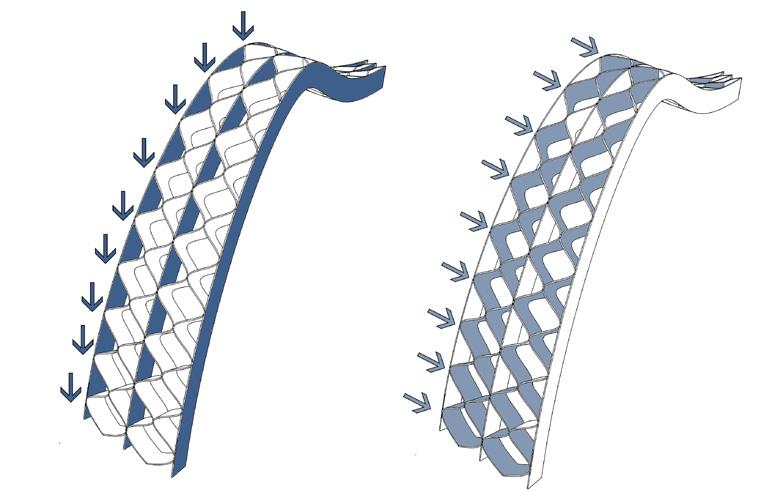
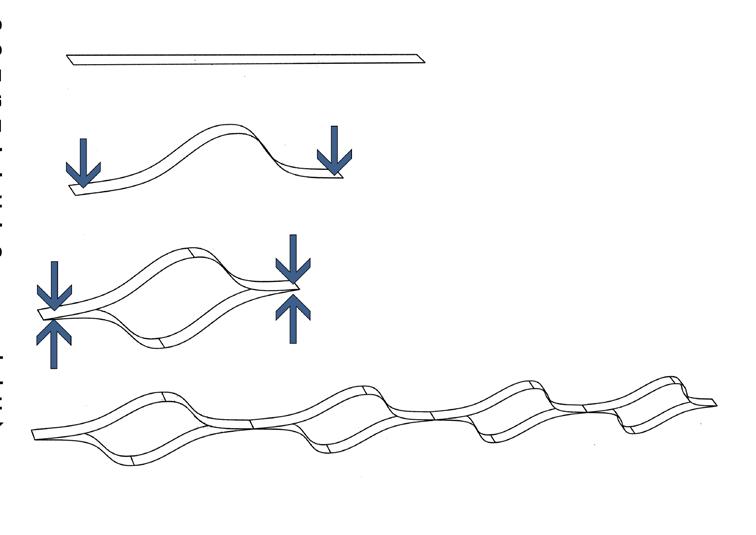
Design consept the design concept started with the Audi logo and four rings. this formation has a linear orientation that is appropriate for exhibition circirculation. then these rings repeated and scaled and in the following, they moved in z axis to make the considered shapes.
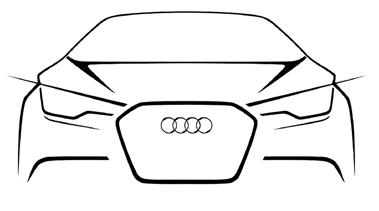
Semi-transparent panels
Main structure
Complementary structure
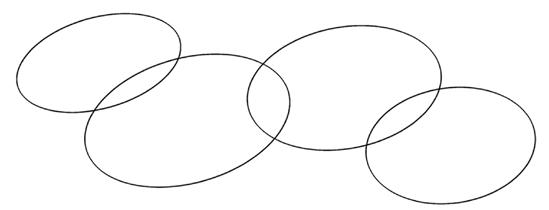
Floor panels
Substructure
Foundation
Watercurtain system
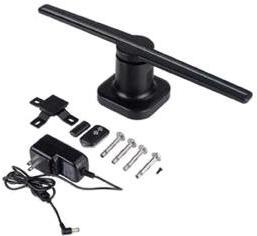
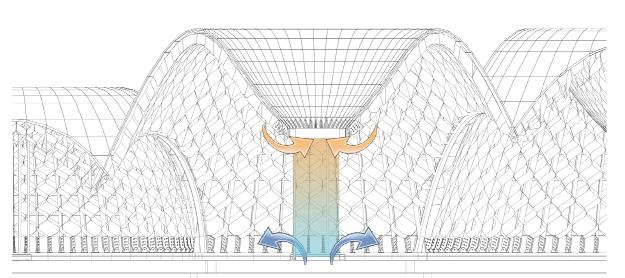
A water curtain is defined as a line of closely spaced sprinklers (or a single sprinkler) in combination with draft stops that are intended to retard the passage of fire through an opening
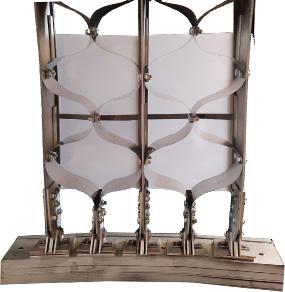
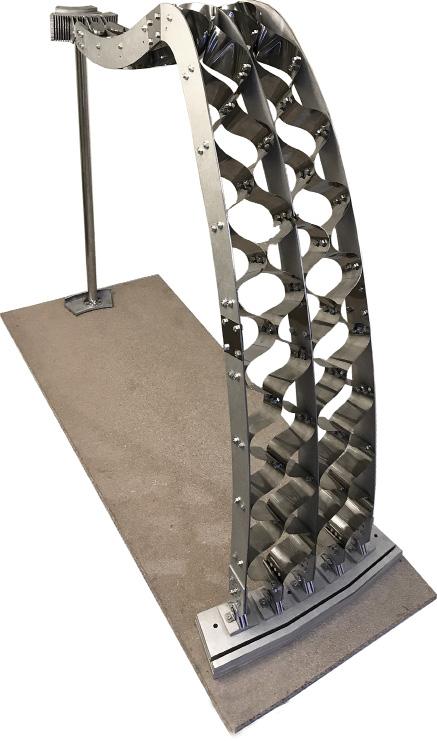
Holographic system
A holographic display is a type of display that utilizes light diffraction to create a virtual three-dimensional image of an object. Holographic displays are distinguished from other forms of 3D imaging in that they do not require the aid of any special glasses or external equipment for a viewer to see the image.
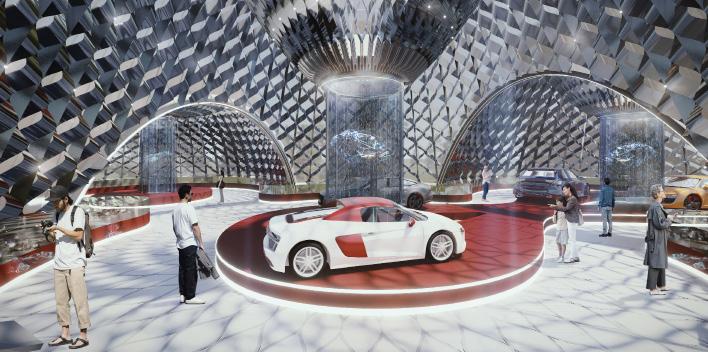
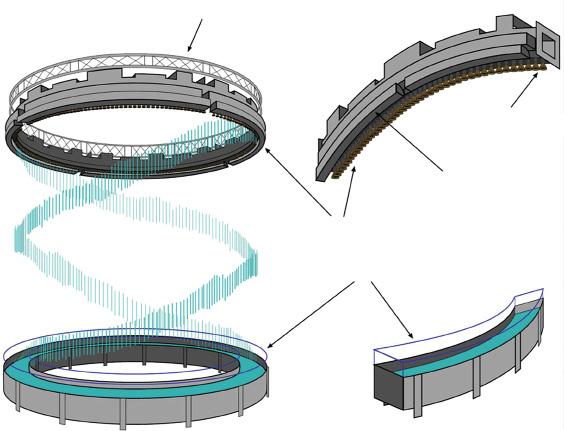
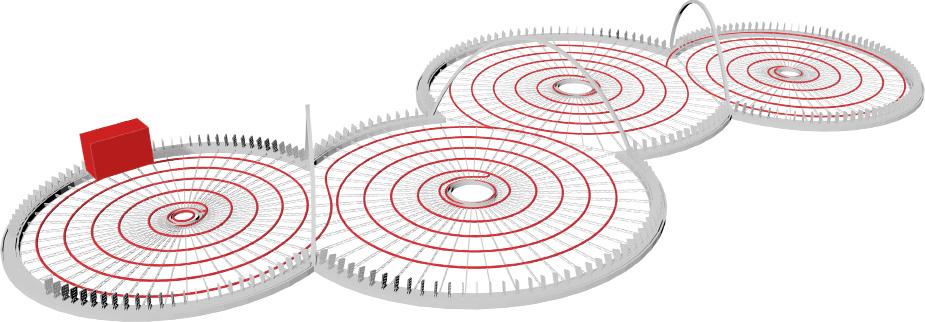
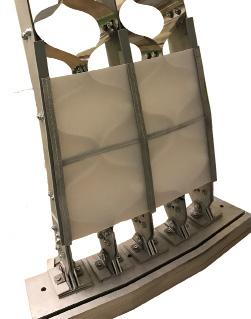
CHP
Cogeneration or combined heat and power (CHP) is the use of a heat engine or power station to generate electricity and useful heat at the same time. Trigeneration or combined cooling, heat, and power (CCHP) refers to the simultaneous generation of electricity and useful heating and cooling from the combustion of a fuel or a solar heat collector. The terms cogeneration and trigeneration can be also applied to the power systems generating simultaneously electricity, heat, and industrial chemicals – e.g., syngas or pure hydrogen (article: combined cycles, chapter: natural gas integrated power & syngas (hydrogen) generation cycle)...
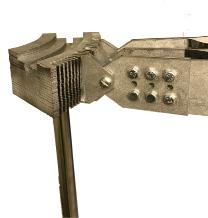
Ipogami
- compliant kinetic panel -
Type: Facade Panel
Year: Autumn 2020
Location: University of Tehran - Tehran
Status: Constructed
Supervisor: Dr Mohammad Reza Matini
Brief:
In this project, the goal was to design a kinetic panel that responses due to intense sunlight or rain, to provide comfort conditio. In this regard, inspired by the structure of the Ipomea flower -how it blooms- and using the origami method, the final panel was designed. This origami, which is known as NASA origami, used in various NASA projects. Prototyping this structure in different ways using different materials and construction methods, considering proper response and efficiency, in the end, a combination method was chosen. The final structure was made using a flexible part and a rigid part. The rigid part is used to provide strength and the flexible part is used to provide opening and closing ability. Using cable and spring steel is also to integrate the main part to the stepper motor. This compliant kinetic panel is equipped with a water and light sensor and provides the final goal by using an Arduino Uno and a stepper motor.
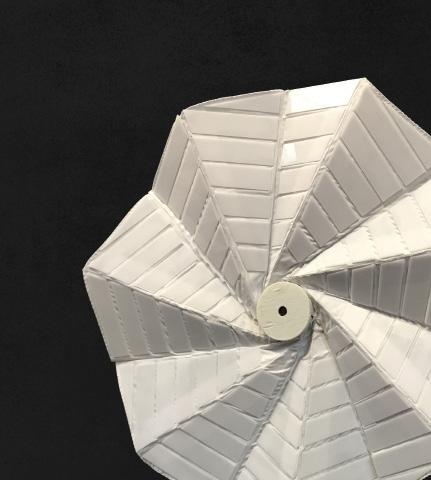
Contributation to the project:
Idea Development
Construction
Modeling: Rhinoceros 6.0 & Grasshopper
Presentation: Adobe premier
The purpose of designing panel:
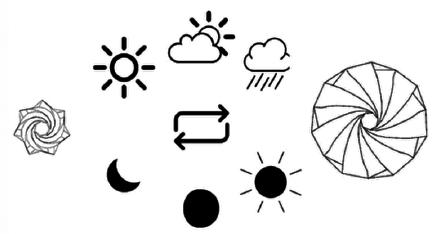
Tested fabrication methods:
1: PP (PolyPoropylene)
2: PVC (polyvinylChloride)
The movement in many biological kinetic structures is often based on compliant mechanisms that are integrated into larger flexible organs. Compliant mechanisms where technical devices obtain their motion by the flexibility of their members and functionalize large elastic deformations. In this flower configuration, all five petals are fused together to one continuous corolla surface. While other flowers can change their shape by sliding or overlapping their petals individually, Ipomea has to adjust its shape by means of folding and bending its entire corolla surface. It combines a soft and thin lamina on the one hand and five leathery mid-petaline bands on the other. A spiral movement of the bands begins with a sudden burst of the bud shell. Once the thin lamina that connects the bands is torn apart, the five bands start to separate from each other and bend outwards in a slower helical movement.
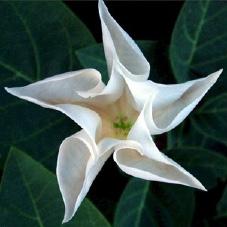
Since origami relies on the deflection of flexible materials it is a compliant mechanism. The origami mechanisms examined herein are flat-folding in their final-folded state, and so they are part of a subgroup of compliant mechanisms called lamina emergent mechanisms. The chosen origami for this research is Starshade, Flasher( Jeremy shafer)
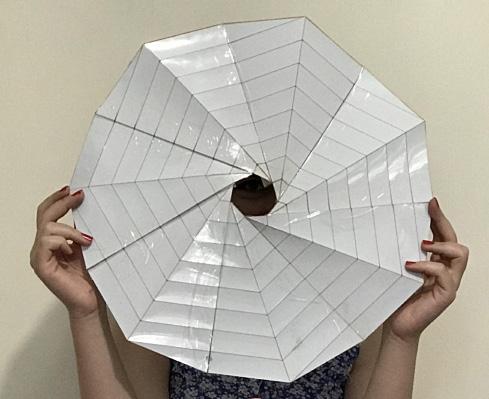
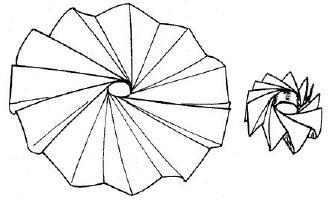
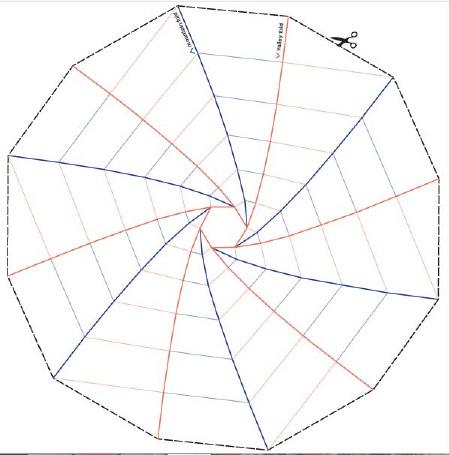
Tested fabrication methods:
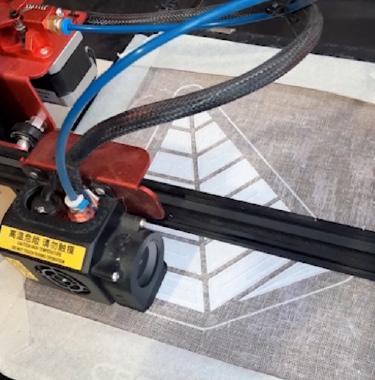
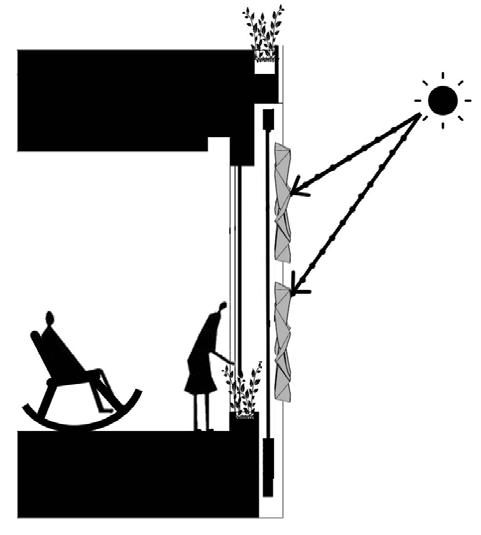
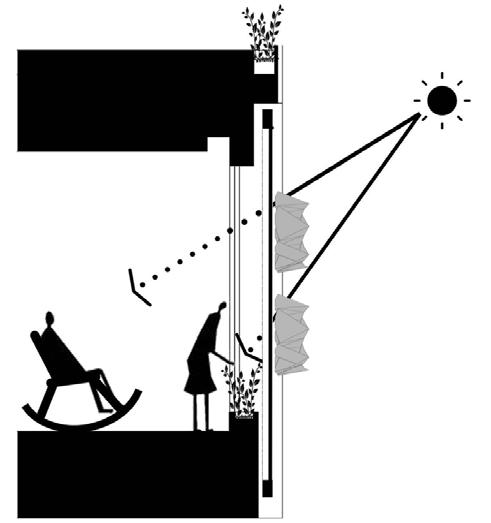
1 : Integrated
3: High impact Polystyrene
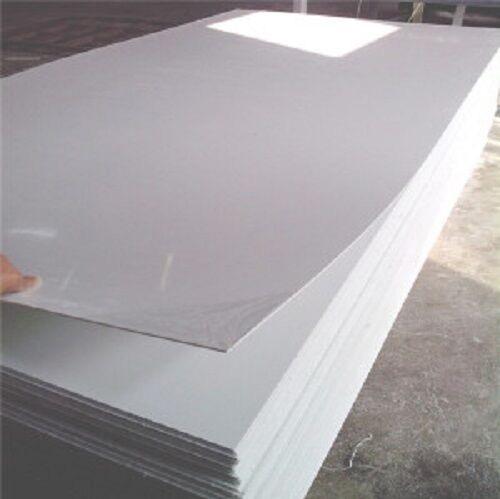
4: PES-PVDF
3 : Stiff & flexible
1: Fabric + 3D print
2:
3:
In the process of panel design and construction, some of the possible methods and materials given in the previous section have been used and each has been tested. But due to various reasons such as lack of flexibility, being heavy, difficult to make, high cost, etc., they were finally removed. The final design is actually a combination of these methods, especially the use of fabric and plexiglass to provide flexibility and strength at the same time.
7 strands

Tensile strength
Digital techniques
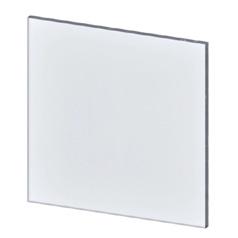
Abrasion Resistance
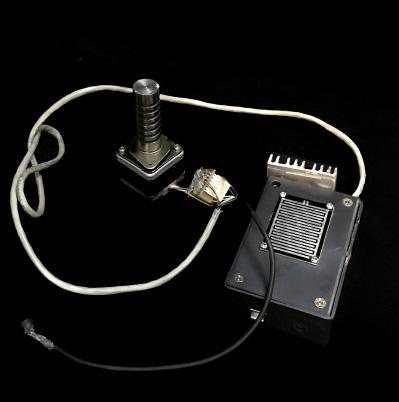
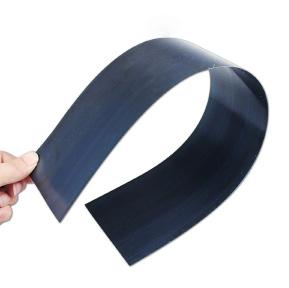
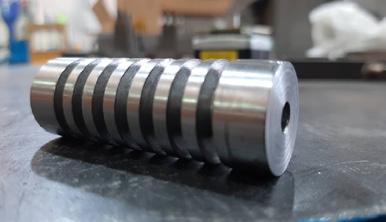
What is Arduino Uno?
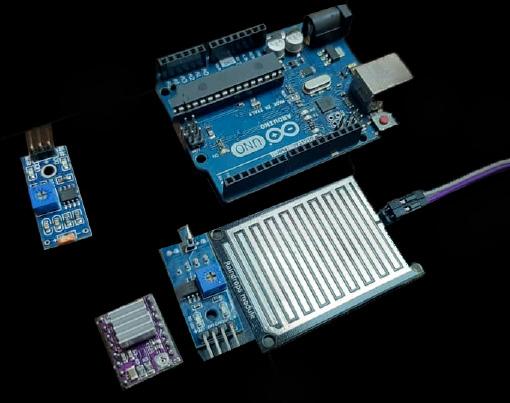
Arduino Uno is a microcontroller board based on the ATmega328P (datasheet). It has 14 digital input/output pins (of which 6 can be used as PWM outputs), 6 analog inputs, a 16 MHz ceramic resonator (CSTCE16M0V53-R0), a USB connection, a power jack, an ICSP header, a reset button. It contains everything needed to support the microcontroller; simply connect it to a computer with a USB cable or power it with an AC-to-DC adapter or battery to get started.
“Uno” means one in Italian and was chosen to mark the release of Arduino Software (IDE) 1.0. The Uno board and version 1.0 of Arduino Software (IDE) were the reference versions of Arduino, which now evolved to newer releases. The Uno board is the first in a series of USB Arduino boards, and the reference model for the Arduino platform; for an extensive list of current, past, or outdated boards see the Arduino index of boards.
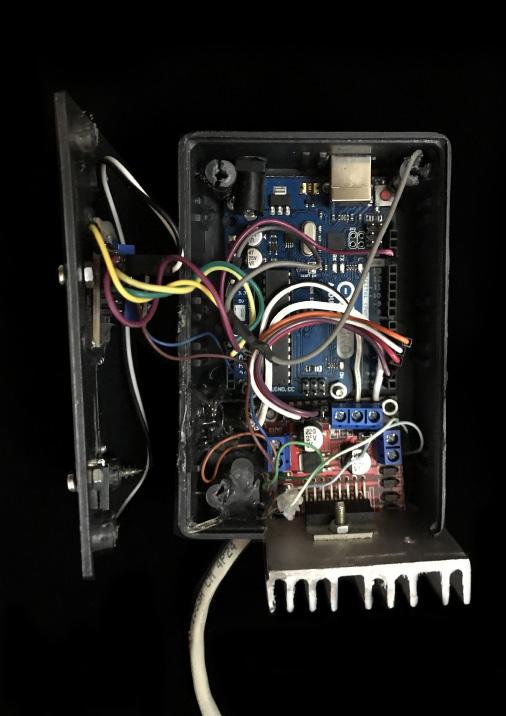
The spring are not allowed to have motion in their place in fabric.
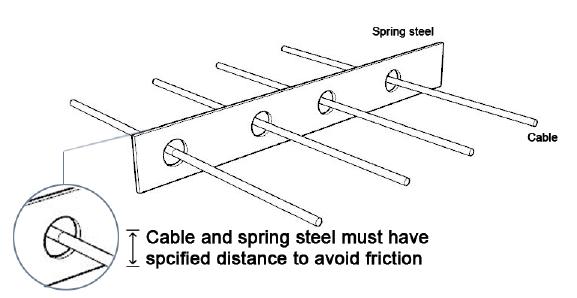
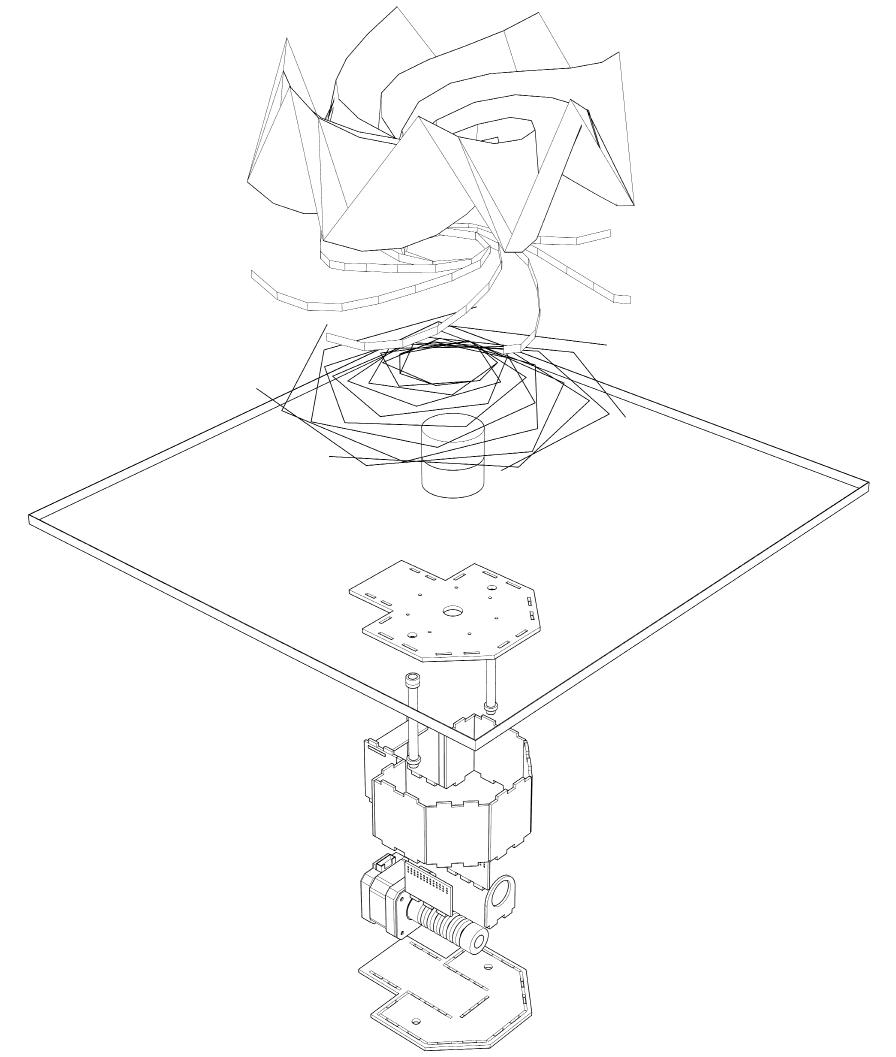
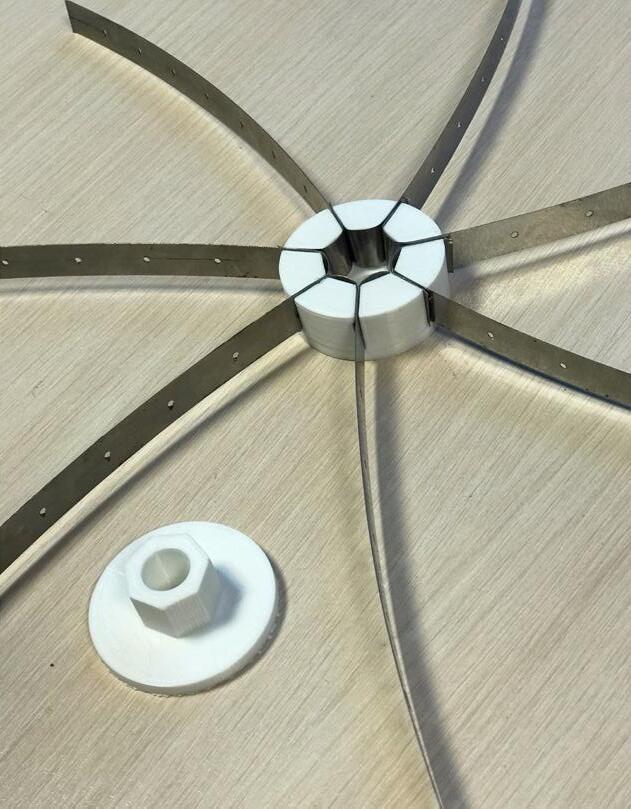
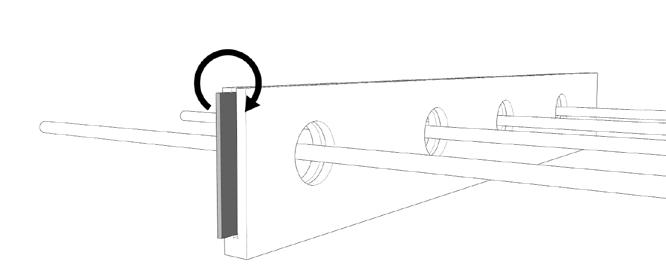