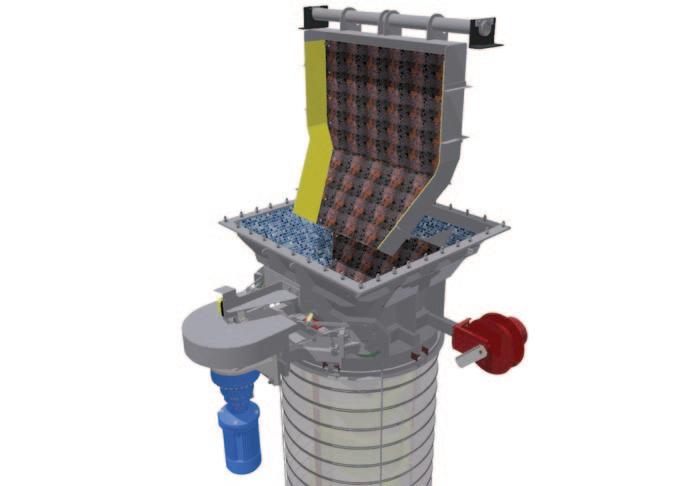
12 minute read
Cleveland Cascades to supply shiploading system to Cuba
Cleveland Cascades is to supply its cascade loading system to Cuba where it will load cement and clinker. The project is focused on supporting the elimination of dust generation during loading operations for which the materials are known to be problematic.
The system is to be supplied with a fixed head chute and an independent upper deflector which has the capability to pivot –5°. This feature allows for greater optimization of material control before the product enters the head chute.
The 950 sized Cleveland Cascades cones are to be utilized on the project; these have the capability of loading up to 750m3 per hour.
The extended length of the system will be 22.0m measuring from the interface flange to the base of the skirted outlet with an operational retracted length of 6m.
Due to the abrasive nature of the materials being loaded, the head chute will feature chromium carbide liners as this is the initial point of impact following the deflector meaning improved abrasion resistance is required. The cones will have ceramic tiling installed as opposed to chromium carbide liners, this reduces the static load of the system whilst still providing sufficient wear resistance.
A full suite of electrical components is to be included to allow for system automation and safety.
At the customer’s request this system will have the option to easily retrofit a hatch charger if deemed necessary for future loading operations. This requires careful design consideration when producing the specification for the hoist unit to ensure there are no complications with regards to the additional weight which would be introduced to the system. CC960 GA. CC960 head chute.
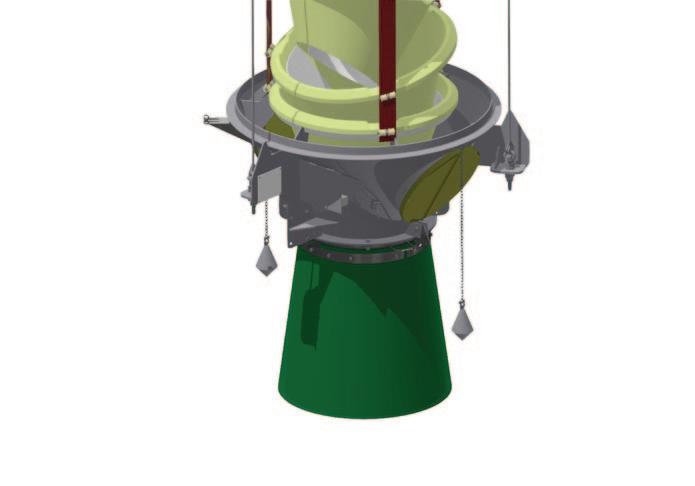

CC960 carrier and skirt outlet.
CC960 carrier and bellows hatch charger.
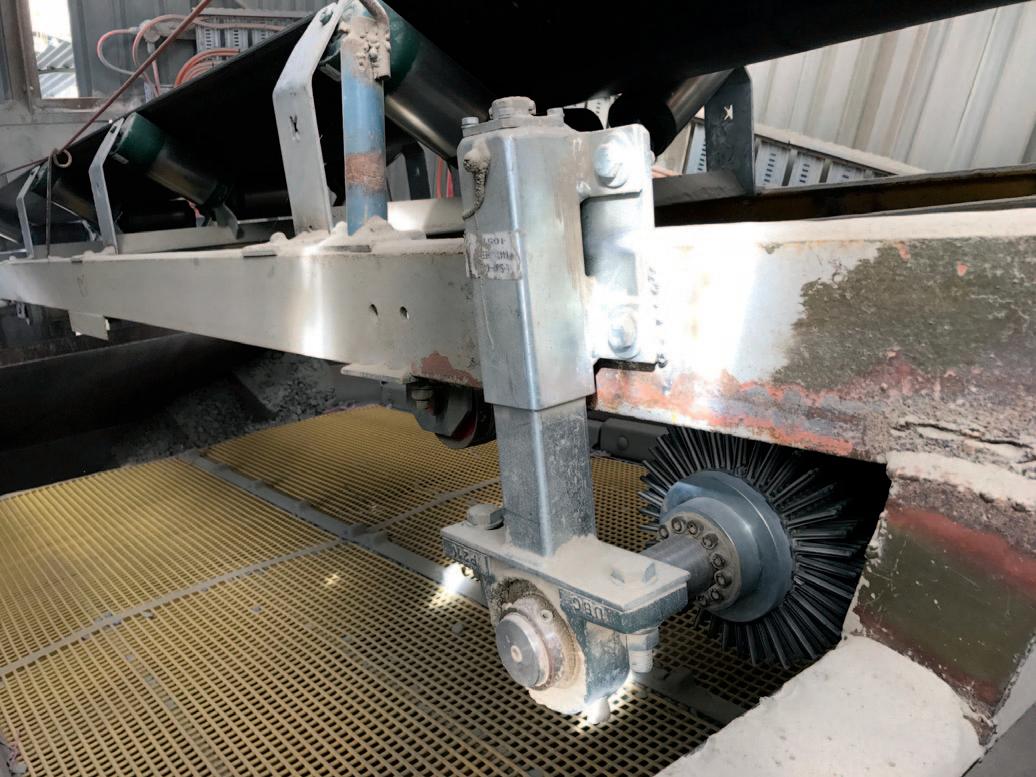
Kinder Australia Pty Ltd’s solutions have eliminated problem with conveyor systems at a basalt quarry.
A long-standing quarry customer needed to find a solution that would: v eliminate belt cleaning and carryback issues; v address conveyor belt mistracking; v address the issue of increased maintenance and cleaning-up costs; and v minimize production downtime.
Located in North Western Victoria, the quarry customer has been a long time vocal advocate for Kinder Australia conveyor componentry solutions. Major productivity and operational improvements at the quarry have been realized in recent years with the installation of K-Commander® Self Centring Idler to address the on-site belt tracking and excessive material spillage issues.
K-MotorShield Motor Covers were also recently installed to the site. Cost savings due to reduced maintenance and extension of motor life were achieved. K-Sure® Support Belt Support Systems installed also delivered on its promise of consistent and stable support at the quarry’s main transfer points.
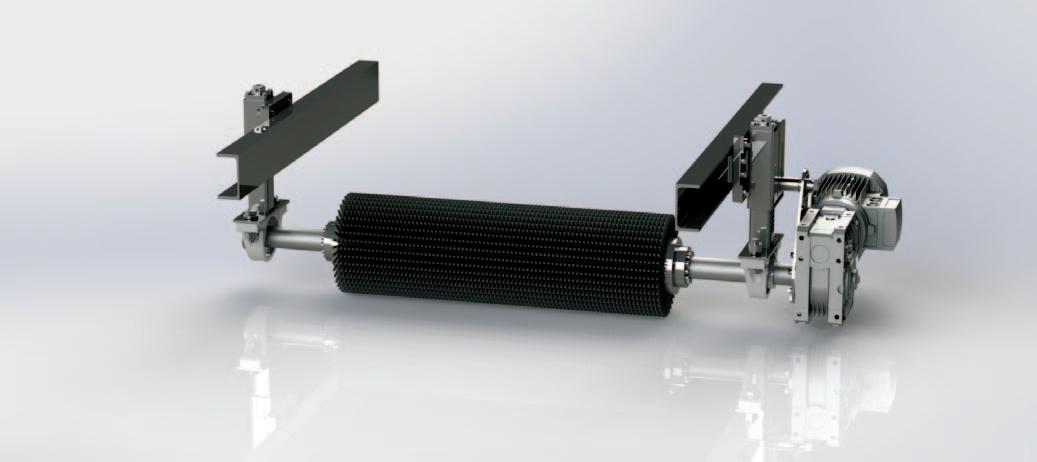

The quarry was utilizing a primary belt cleaner and it was observed by Maintenance Teams particularly during the Winter months that material fines were travelling down the conveyor belt. This residual material or carryback had the tendency to cling onto the belt and accumulate on the return rollers. This common scenario was a leading contributor of potential belt mistracking issues and increased power usage on site.
In-depth consultations with quarry and Kinder Technical Applications Team were aimed at addressing the important belt cleaning challenges as this greatly impacts the site’s continuous productivity goal. Reducing maintenance and cleaning costs associated with time and resources required to clear/shovel away the material fines on a regular basis was also targeted.
For many years, the quarry was operating an incline conveyor system. To implement a reliable and effective cleaning system and overcome the sites ongoing challenges, key factors needed to be taken into consideration, including the hard to reach tail pulley location and tilting nature of the incline conveyor.
Maintenance Team were unanimously in favour of installing K-Rotabrush® conveyor belt cleaner, that has the capacity to provide excellent cleaning performance primarily where space limitations apply.
K-Rotabrush® conveyor belt cleaners installed at the quarry, consisted of a rubber brush design and featured a high performance, uniform rotatory action successfully sweeping excessive fines off the belt. This greatly reduced the instances of carry back on the return rollers and helped to stabilize belt tracking, improved conveyor operation and plant efficiency. K-Rotabrush® effectively per formed the cleaning action without compro mising belt wear and extending its wear life. An external contractor was involved in this simple belt cleaner installation and to date minimal maintenance and virtually no adjustments have been necessary.
As well as resolving the ongo ing belt cleaning challenges, the quarry was also successful in achieving a multi tude of improve ments and plant efficiencies due to the K-Rotabrush® conveyor belt cleaner installation. Including the imme diate eliminat ion of carryback issues and the extension of belt wear life — all thanks to correct conveyor belt tracking.
Costly cleaning up expenses and the risk of injury has also been signif icantly reduced.
Quarry Mainte nance Teams continue to report less production down-time with operators being more efficient, less time involved with manual shovelling of material fines has meant more time to focus on other daily duties.
Part of a National building and construction materials group, Kinder is pleased that the Maintenance Team continues to spread its successes achieved to date with other members of the group at training sessions and operational improvement meetings.
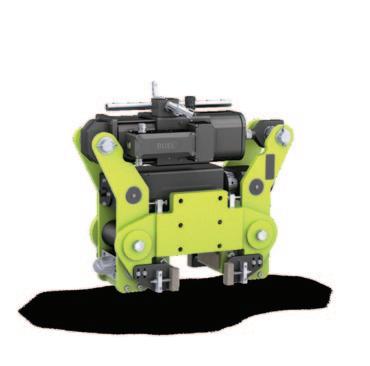
RESULTS: v improved belt cleaning and carry back issues; v improved conveyor belt tracking; v reduction in maintenance cleaning up costs; v daily continuous productivity maintained; and v sharing of successes with group members.
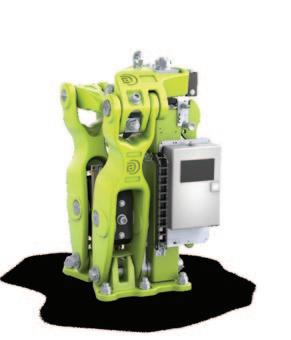
LEADING THE WORLD IN BRAKING SYSTEM DESIGN & MANUFACTURING
SB SERVICE BRAKES WITH BUEL® H BRBe ELECTRIC WHEEL BRAKES WITH BUEL® S SF SAFETY BRAKES WITH BUEL® G
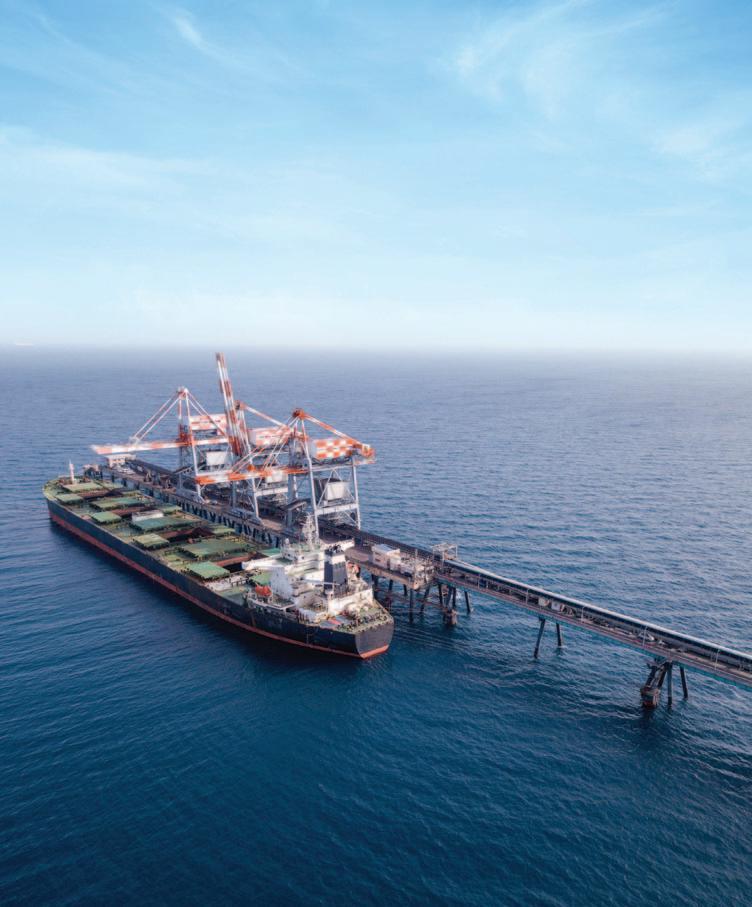
Breston opts for wireless controls of Tele Radio

Tele Radio BV in The Hague, subsidiary of Tele Radio in the Benelux, has been the proud supplier of radio controls to Breston in the Netherlands, which has been a manufacturer of mobile transport systems for almost 20 years. Breston mainly applies wireless remote controls to its shiploaders and store loaders.
Tele Radio, founded in 1955 in Lysekil, Sweden, specializes in the development and production of safe, radiographic remote controls for industrial use. “The robustly and durable built remote controls are characterized by a very high reliability and an ergonomic design,” says Jerry Bredewoud, salesman at Tele Radio BV and account manager for Breston. “The transmitters and receivers meet the highest possible safety standards and have independent certification.”
INNOVATIVE SOLUTIONS The globally operating Tele Radio Group currently has set up more than 20 branches and dozens of dealers and agents spread across Europe, the United States, and Asia.
Tele Radio Group serves a range of industrial sectors with innovative solutions for the realization of wireless remote control of lifting equipment, cranes, heavy machinery, winches, hydraulic tail lifts, gates, and doors, to name just a few. “Where necessary, we can adjust our remote controls for specific applications.”
STORE LOADERS An example of a demanding application is the wireless remote control used by the telescoping store loaders and shiploaders of Breston BV, a manufacturer of mobile transport systems. The top-notch Tiger series remote control is used for this. Jan Abresch, sales manager at Breston notes: “The Tiger remote control meets all our requirements; in terms of safety as well as functionality and reliability.”
FUNCTIONALITY The remote control’s functionality is highly programmable and customizable.
Proportional operating buttons or joysticks guarantee precise control. The connection between transmitter and receiver is checked every 40 milliseconds. The remote controls have standard relays, analogue, and digital inputs and outputs, and various fieldbus communication protocols. These protocols include an emergency stop function and relays that meet SIL 3 and PLe classifications. The Tiger also shows machine feedback via LED lights. Says Bredewoud: “This way the operator can easily see whether a function is active, without having to see the machine. The control has an adjustable range of up to 1,000 metres, depending on the environment.
PERSONALIZED The transmitter and receiver are protected against moisture and dust (IP65). Depending on the model, the control has a rechargeable, replaceable battery or a rechargeable internal battery.
The Tiger can be personalized with a front foil. Says Abresch: “We can therefore supply our machines utilizing a Tiger remote control that has the Breston look. The clear function indication of the buttons on the transmitter contributes to an efficient and safe operation of our store loaders and shiploaders.”
ABOUT BRESTON Breston BV in Nieuwe Tonge (the Netherlands) is dedicated to the design, manufacture, installation, and maintenance of fixed and mobile transport systems for the agriculture and bulk processing industry. In addition to warehouse loaders and shiploaders, the company also supplies verifiable weighing bunkers and loading systems for trucks, even far beyond national borders.
To accelerate its push to become a net-zero operator by 2050, BHP will become a founding member of Komatsu’s GHG Alliance, which aims to develop commercially viable zerogreenhouse gas emissions haul trucks. As a founding partner of the Alliance, BHP plans to operate one of the first batches of zero-emission trucks upon commercial release.
BHP will provide engineering and technical resources to Komatsu to support the development phase as required. These activities will provide BHP with real-time access to technology in development, with Komatsu drawing upon BHP’s mining expertise to accelerate its path to market. Additionally, BHP and Komatsu will collaborate through the BHP FutureFit Academy to develop the future facing skills in our teams to operate and maintain this pioneering equipment.
BHP’s Chief Commercial Officer, Vandita Pant, said: “Tackling climate change requires strong collaboration and collective effort across the supply chain. Reducing vehicle emissions is key to our climate strategy, and we are thrilled to join with Komatsu and our peers in the global mining sector on real, tangible action to help accelerate our transition to a low carbon future. Extending the FutureFit Academy partnership to equip our workforce to operate zero emissions technology is an exciting addition to our collaboration with Komatsu.”
BHP’s Group Procurement Officer, James Agar, said: “We are excited by the opportunity to work with the Komatsu GHG Alliance to drive new technology and innovation that can benefit the mining industry globally. This collaboration is a great example of the partnership approach we are taking in our supply chain as we work towards BHP’s goal of net zero operational emissions by 2050.” Komatsu Ltd.’s President Mining Business Division, Max Moriyama, said: “We are thrilled to welcome BHP to this exciting new customer alliance and ready to see how we can all work together towards a more sustainable future and rapid development of zero-emission equipment solutions.”
The Alliance framework will support BHP’s broader Zero Emissions Material Movement (ZEMM) programme, which also includes founding patron membership of the global Charge On Innovation Challenge announced in May 2021, which is seeking solutions from technology innovators for large-scale haul truck electrification and charging systems.
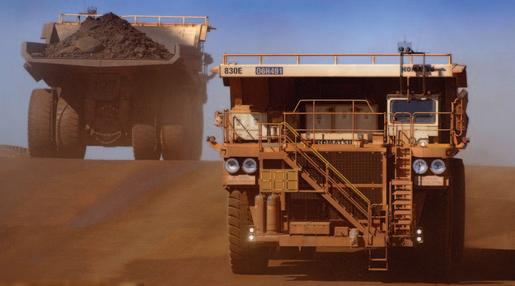
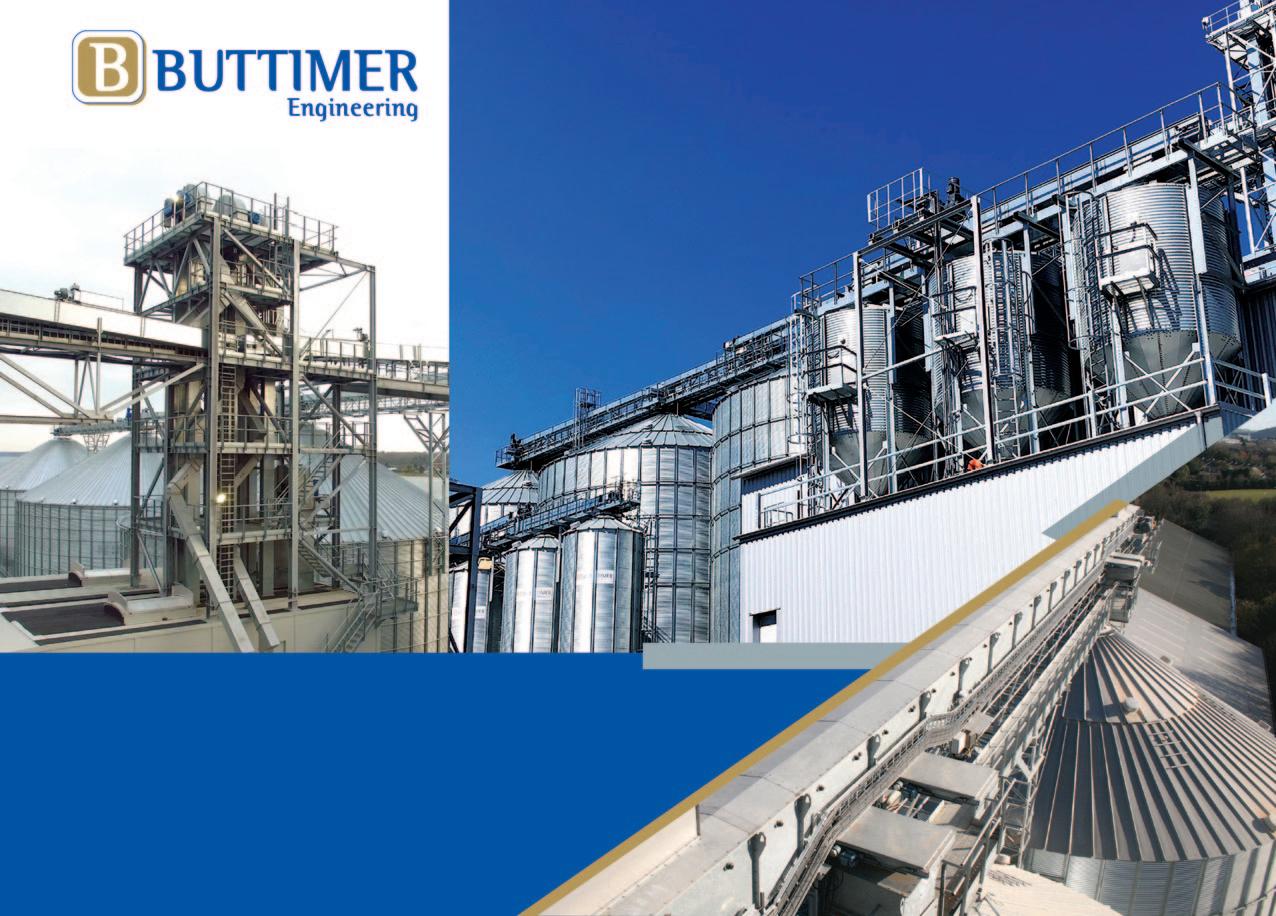


NORDAC FLEX frequency inverters from NORD DRIVESYSTEMS are true all-rounders: they not only offer a wide power range, but also work very economically. The NORDAC FLEX SK 205E series has been specially designed for conveyor systems that handle parcels, as well as baggage handling systems in airports.
The large power range, up to 22kW, is characteristic for the frequency inverter. In addition, the NORDAC FLEX SK 205E is compact and enables high precision in synchronous and positioning applications via the integrated POSICON control Another advantage is the precise and rapid current vector control: It ensures constant speeds in case of fluctuating loads. The NORDAC FLEX SK 205E also offers maximum flexibility and due to its high energy efficiency enables energy savings, especially during partial load operation. This even applies to applications that technically do not require an inverter.
Users are provided with complete flexibility when it comes to installation: Inverters can be both installed close to the drive in the field and integrated into the motor. Power and data cable connections are available as plug-in versions. The decentralized system enables short motor and encoder cables as well as short supply cables to sensors.
The inverters can be used to control standard asynchronous motors, highefficiency synchronous motors and brake motors. Encoder feedback can be realized, for example position-controlled transport systems. The large operational overload characteristics of the NORDAC FLEX SK 205E makes dynamic movements with short start and stop times or cyclic operation possible.
NORDAC FLEX SK 205E series frequency inverters feature four digital inputs and one digital output (e.g. for error messages). The inverter can be monitored via an optional Bluetooth interface using the NORDCON APP software. This way, possible errors can be quickly diagnosed and remedied. Drive parameterization is possible as standard via the integrated diagnostic interface with the free NORDCON software tool.
The inverter features a total of six digital and two analogue interfaces, two encoder interfaces and one integrated PLC for programming of functions close to the drive. A wide range of extensions through option modules are possible as accessories, for example a communication interface that supports commercially available Ethernet dialects as well as extensions for functional safety such as PROFIsafe and STO.
ABOUT NORD DRIVESYSTEMS
With more than 4,100 employees, NORD DRIVESYSTEMS has developed, produced and sold drive technology since 1965, and is a highly respected global full-service provider in the industry. In addition to standard drives, NORD delivers application-specific concepts and solutions for special requirements such as energysaving drives or explosion-protected systems. In the 2020 financial year, annual sales amounted to €735 million. NORD has 48 subsidiaries in 36 countries and further sales partners in more than 50 countries. These provide technical support, local stocks, assembly centres and customer service. NORD develops and produces a wide range of drive solutions for more than 100 industries, gear units for torques from 10Nm up to over 282kNm, supplies electric motors in the power range of 0.12kW to 1,000kW, and supplies the required power electronics with frequency inverters of up to 160kW. Inverter solutions are available for conventional control cabinet installations as well as for decentralized, fully integrated drive units.
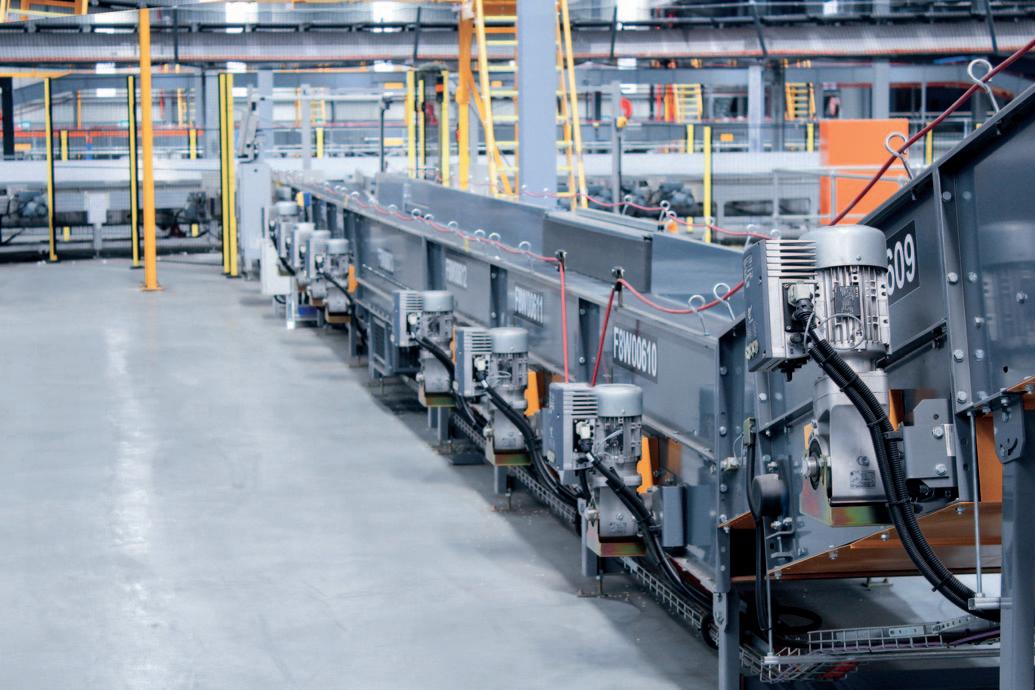

NORDAC FLEX SK 200E series frequency inverters have been especially developed for use in extensive conveyor technology systems. The NORDAC FLEX SK 205E features extremely high positioning accuracy and enables exceptional energy-efficient system operation (images: NORD DRIVESYSTEMS).