
28 minute read
READY FOR ACTION: CRANES AND GRABS — ONBOARD AND IN PORT
Ready for action
Cranes and grabs — onboard and in port
The Calypso with two CBG 360 from Liebherr, which is in operation in North Vietnam to supply energy to the region.
Jay Venter
Liebherr floating cranes supply North Vietnam with energy
Liebherr has delivered four transshipment cranes, type CBG 360, to its long-term customer Oldendorff Carriers for a major project in North Vietnam. In the coming years, the cranes, which excel through their reliability and high operating speeds, will be used for power generation in the region. A further three cranes of the same type will be commissioned in West Africa for handling bauxite.
Handling and transporting 100 million tonnes of cargo in 25 years: that is the goal of the NS2 project of Oldendorff Carriers, Germany’s largest bulk shipping company. To achieve this, Oldendorff Carriers’ fleet will work with Liebherr floating cranes. The core of the North Vietnamese project are the power plant’s 2 x 600 megawatt power generation units, which supply the region with energy.
The CBG-series ensures a continuous turnover of material for the power plant’s operation. The deployed cranes are characterized by their long service life and low maintenance requirements, which is a decisive advantage especially on the open seas and in remote areas.
LONG-TERM PARTNERSHIP Liebherr and Oldendorff Carriers can look back on decades of co-operation based on partnership and trust. Like Liebherr, Oldendorff Carriers is a family-owned company that has been operating successfully on the market for many years. For the large-scale project to supply energy to North Vietnam, it was looking for a low-maintenance handling solution. “Oldendorff Carriers values the reliability of Liebherr products and is therefore also counting on high-performance Liebherr four-rope grab cranes, type CBG 360, for this major project,” said Jan Breckling, Senior Sales Manager for transshipment and ship cranes at Liebherr Maritime Cranes.
“The CBG is a heavy-duty crane designed for continuous operation. The new equipment will therefore play a crucial and at the same time permanent role in our customer’s long-term transshipment project.”
EXTENDED ACTION RADIUS Each of the four CBG 360 floating cranes is installed on a 10-metre-long eccentric platform. This allows an extended operating radius of 46 metres for a lifting capacity of 30 tonnes. The maximum lifting capacity of 36 tonnes can be utilized at up to 40 metres. The improved positioning and outreach creates more operational flexibility and makes the unloading of the cargo holds even more efficient.
Captain Johannes van Dijk, Technical Director Projects at Oldendorff Carriers, said: “We needed a robust, reliable cargo handling system for our project in North Vietnam. For that reason we chose Liebherr CBG 360 cranes which are highperformance cranes designed for continuous operation.”
The first transloader, Calypso, with two CBG 360 cranes went into service at the beginning of 2021 and start of work coincides with Oldendorff Carriers’ 100th company anniversary. Like its sister vessel, it has a length of 145 metres and a deadweight capacity of 18,000 tonnes. In
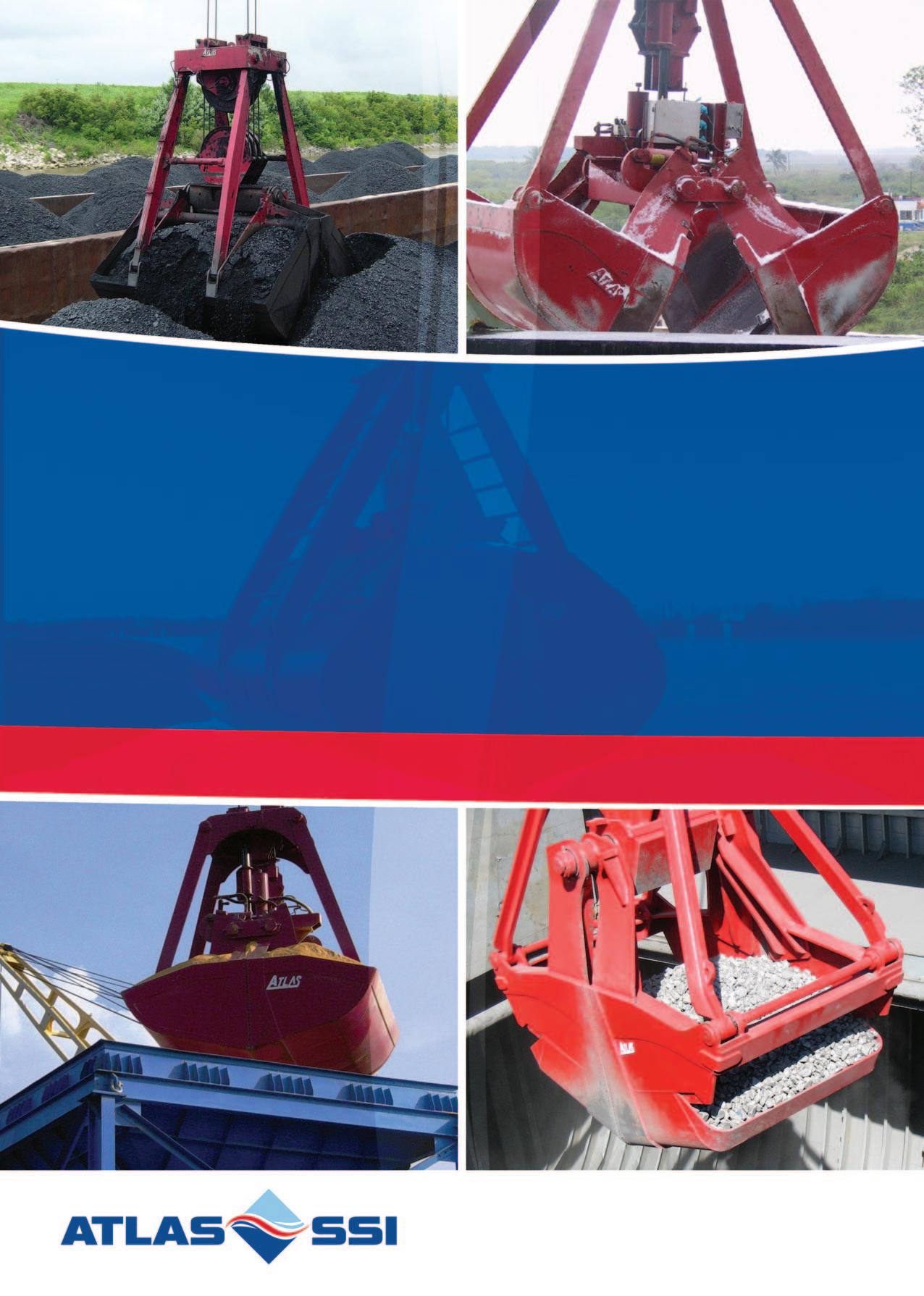
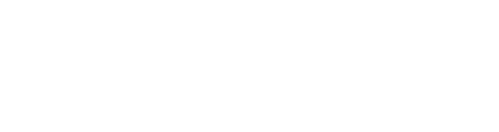

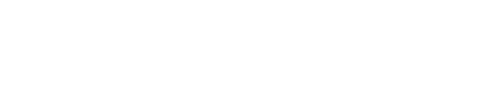
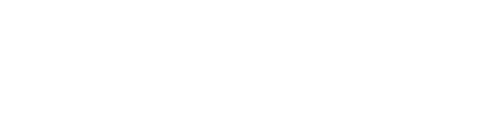
West Africa, the Albert Oldendorff with three CBG 360 is in operation for bauxite handling.
This transshipment vessel is equipped with hoppers and a conveyor system, which leads to a faster turnover of the material. The cranes are installed sidemounted and directly discharge into the hopper conveyer belt system.
ABOUT OLDENDORFF CARRIERS Oldendorff Carriers is a 100-year-old family owned shipping company operating a fleet of about 700 bulk carriers and 50 transshipment vessels. The company is represented by 20 offices around the world with 10 bulk transshipment projects and has a workforce over 4,500 people from 60 countries.
ABOUT LIEBHERR-MCCTEC ROSTOCK GMBH Liebherr-MCCtec Rostock GmbH is one of the leading European manufacturers of maritime material handling solutions. The product range includes ship, mobile harbour and offshore cranes. Reach stackers and components for container cranes are also included in the product portfolio.
The Albert Oldendorff is equipped with three CBG 360s, which are currently handling bauxite. ENGINEERING & EQUIPMENT
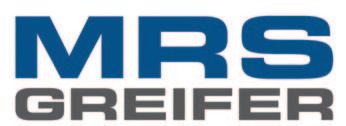
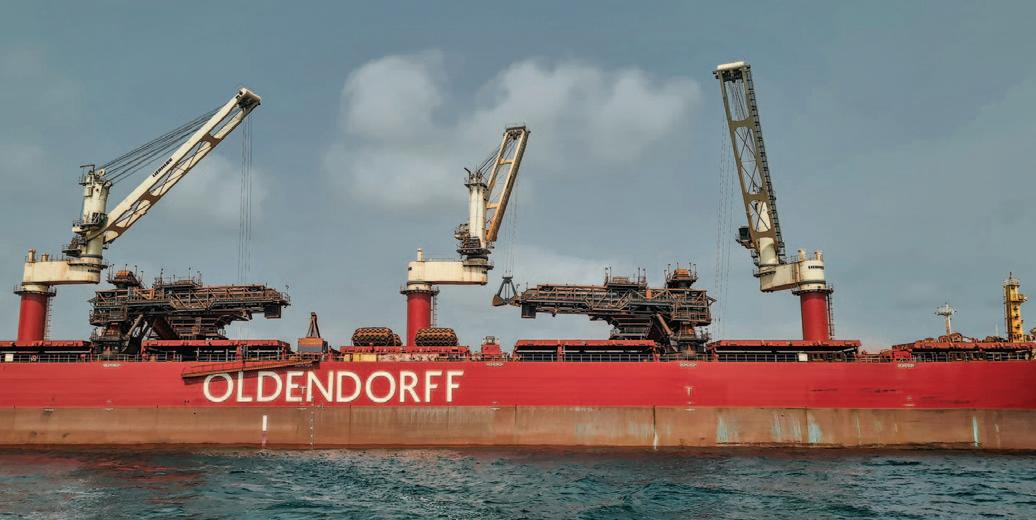
OUR EXPERIENCE –YOUR ADVANTAGE
The perfect grabs with unbeatable reliability, leading in efficiency and quality, expedient and economical.
Rope-, Motor-, Hydraulic-Grabs
MRS GREIFER GmbH
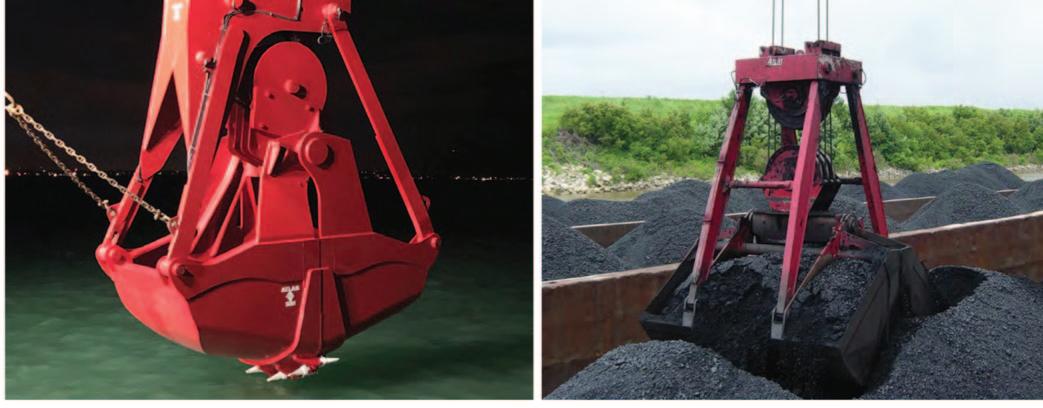
Atlas-SSI is a major manufacturer in the bucker and grapple market. The company prides itself on product excellence. Its high-performance buckets and grapples are built for the toughest jobs, setting the standards for quality engineering and craftsmanship.
As a full-service manufacturer, Atlas-SSI offers comprehensive engineering, manufac turing and servicing capabilities for new and rebuilt equipment. Outstanding customer support results in a winning combination. The company’s core values are simple — it emphasizes safety and superior customer service. Atlas-SSI understands the importance of equipment quality and has the capabilities to rapidly respond to virtually any bucket or grapple challenge that may arise on site, no matter the manufacturer or type of equipment.
Atlas-SSI manufactures single-, two-, three- and four-rope cable-operated buckets and grapples as well as radio remote control, hydraulic and continuous unloader buckets used for all types of materials and applications. Using the latest manufacturing methods and highest quality materials, its buckets and grapples carry with them the quality and reliability that customers have come to know and expect from Atlas-SSI.
Atlas-SSI also maintains an inventory of buckets and grapples that are available for short- or long-term rental. Whether it’s for project cost control or an unplanned equipment breakdown, the rental fleet is well maintained and is ready to ship from the company’s strategically located facility near the Mississippi River. To avoid downtime, many customers leverage this rental programme while their bucket or grapple is being rebuilt at our facility.
In addition to manufacturing new equipment, Atlas-SSI has also made its mark on the industry with top-quality rebuilds. It has the expertise to rebuild all styles, makes and models of buckets and grapples from any manufacturer. The quality of the rebuilds often exceed their original manufacturers’ performance specifications. This not only makes the equipment work like new, but saves the customer time and money, improving your bottom line.
With extensive engineering and manufacturing experience, Atlas-SSI has the specialized knowledge to service all makes and models of buckets and grapples and make best practice recommendations on equipment maintenance and operation to help maximize the life of the customer’s bucket or grapple. Because it manufactures the equipment, it also has an inventory of parts that can be quickly shipped to the jobsite.
Atlas-SSI is proud to be a trusted extension of its clients’ in-house engineering and maintenance teams. As the most experienced provider in North America, Atlas-SSI operates with an uncompromising commitment to health and safety at its facilities and on the jobsite. Safety starts with the leadership team and touches every employee through daily hazard assessments, safety training and ensuring that all essential industry safety certifications are in place.
Atlas-SSI’s state-of-the-art manufactur ing sites feature over 250,000ft2 of combined space and produce a wide range of buckets and grapples. Atlas-SSI engineers use the latest CAD software programs in combination with high-tech equipment and experienced welders and machinists to ensure that each bucket and grapple is produced to the highest standards. Its buckets and grapples are manufactured using a combination of A-514 (T-1) and AR-400 steel, heated treated pins, rollers and bushings to maximize structural strength and durability in the field. This helps to ensure long and trouble-free operation.
The quality of the buckets and grapples is a top priority and Atlas-SSI conducts detailed inspections in every step of the manufacturing process. When its engineers provide the final sign-off for equipment to leave our facility, customers can rest assured that Atlas-SSI buckets and grapples will exceed all expectations.
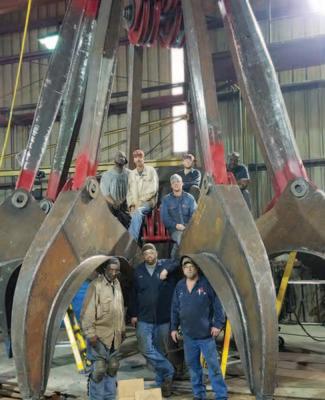


STEMM GRABS OF 40M3 FOR GRAIN HANDLING STEMM has reached an international agreement with shipowners and stevedores from the main European ports to manufacture clamshell grabs for cereal handling in the unloading of bulk carriers.
The manufacture of this type of grabs requires highly qualified personnel and technical equipment, especially boiler makers and welders duly approved, according to ASME and ISO standards.
PHYSICAL CHARACTERISTICS OF THE GRAIN HANDLING CLAMSHELL GRABS Clamshell grabs are ideal for use with cranes from companies such as Italgru, Liebherr, Konecranes Gottwald. These STEMM models have a capacity of 55 tonnes at maximum boom outreach.
A clamshell grab of this type is an indispensable tool with an own weight of about 18 tonnes and an installed electric motor with a power of 55kW. It is driven by four robust, special high-pressure hydraulic cylinders with a diameter of 160mm, which are fitted with shock absorbers.
The mechanically welded construction uses high strength steels (TRENX 700) and anti-abrasive steels (HARDOX 500), both in the central body as well as in the shells and in the sealing and penetration lips.
METHOD OF OPERATION These grabs are operated by a powerful and well-designed electro-hydraulic unit with an internally installed manifold block.
This manifold block concentrates all the components and valves inserted in a single piece or steel block. It is quickly dismountable, allowing easy interchange ability for control and maintenance operations.
GRAB CONNECT REMOTE CONTROL SYSTEM The GRAB CONNECT system designed by STEMM engineers is a highly developed and highly experienced system that allows remote control of a grab located at any port in the world.
The control of the grab is displayed either on a computer, a tablet or a Smartphone providing all kinds of parameters and technical data, such as pressures, temperatures, current consumption, number of manoeuvres carried out, etc.
In addition to its control, it allows diagnostics and preventive maintenance treatment by carrying out a check of the machine’s condition. Thus, before the arrival of ships at the port, all corrective or updating operations can be established, so that when unloading operations begin everything is totally controlled and there is no possibility of unforeseen events,, ensuring that ships are unloaded without stoppages or incidents.


QUALITY SYSTEMS THAT ATTEST THE RESULT The entire clamshell grab manufacturing process at STEMM’s facilities is subject to continuous and intensive quality controls: v Laser, plasma or water jet cutting of laminated sheet metal. v Full surface treatment of all surfaces, with maximum shot blasting level
SVENSK grade SA 2.5 v Primer treatment before 4 hours have elapsed. v Subsequent C5 marine treated paint finish in RAL 1007, with a minimum dry

film thickness of 300 microns.
During the manufacturing process, in order to ensure the excellent quality required, continuous and constant technical controls are carried out, both by STEMM’s internal personnel and by the duly approved technicians who are contracted by Bureau Veritas engineering.
All the final tests, control and supervision were carried out with the support and intervention of the technical specialists of the company Lloyds, which issued a Final Certificate of Tests and
HOW STEMM WAS AWARDED THE CONTRACT The buyer was a maritime consortium of international shipowners and stevedores, operating in various European and Indian Ocean ports.
The technical committee in charge of the selection of the most suitable option, 11 engineers and doctors of great prestige and experience, was appointed by the consortium’s top management.
This Committee appreciated almost unanimously the high technical performance of great value and design offered in the technical report presented by STEMM engineers, who in addition to providing technical reports with designs and profile calculations by means of finite elements of the profile of the shells, enriched the presentation with 3D designs.
This optimum filling degree was fully corroborated and confirmed in the highly anticipated unloading operations of the first 300,000 tonne bulk carrier that arrived in port.
Ships cranes turn a quayside with no cranes into a bulk copper loading port
North Parks mine in western NSW Australia loads its copper in bulk ships in Port Kembla on a quay side with no cranes or conveyor belts using the ISG containerized Bulk Handling System
In 2014 the first ship was loaded in Port Kembla with copper concentrate using ships cranes and ISG Pit To Ship solutions™ containers.
At the mine site, the ISG containers have their lids removed by the ISG mine site lid lifter. The ISG containers are then loaded with copper at the mine site using a front-end loader, the lids are then replaced by the ISG lid lifter.
Each container is placed onto trucks and taken to the railhead where they are loaded onto the train. The copper is then delivered by rail from North Parkes mine. The train arrives into the Patrick terminal in Wollongong where the loaded containers are swapped for the unloaded containers, the train then returns to Parkes.
The loaded containers are taken around to the quayside and using the ships crane and a tippler the containers are placed into the ship’s hull. Using the patented ISG lid lifter the containers are rotated 360° and the copper is placed into the ship’s hull making this a dust-free solution.
The following photos show the loading process using ships crane, tippler and the ISG containers, note the ISG patented lid lifter in operation.
INTERMODAL SOLUTIONS GROUP PIT TO SHIP SOLUTIONS™ Intermodal Solutions Group (ISG) is a global company. Its container designs are all FEA tested and have gone through a rigorous testing programme. ISG designed the first ever bulk container certified BK2 compliant and these containers currently move copper concentrate in Australia.

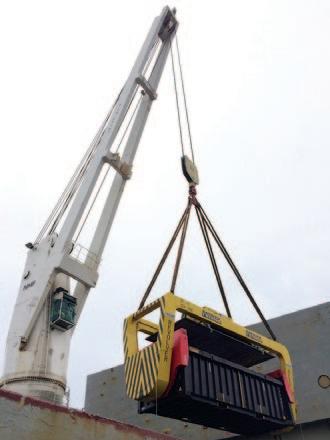
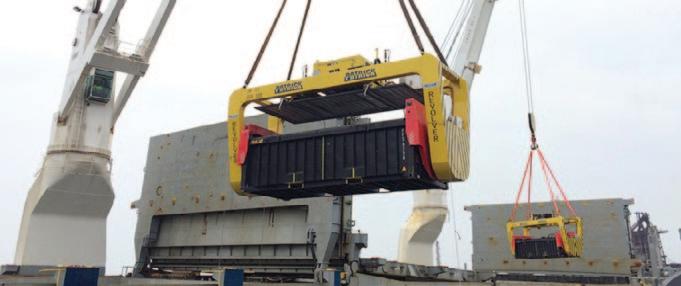


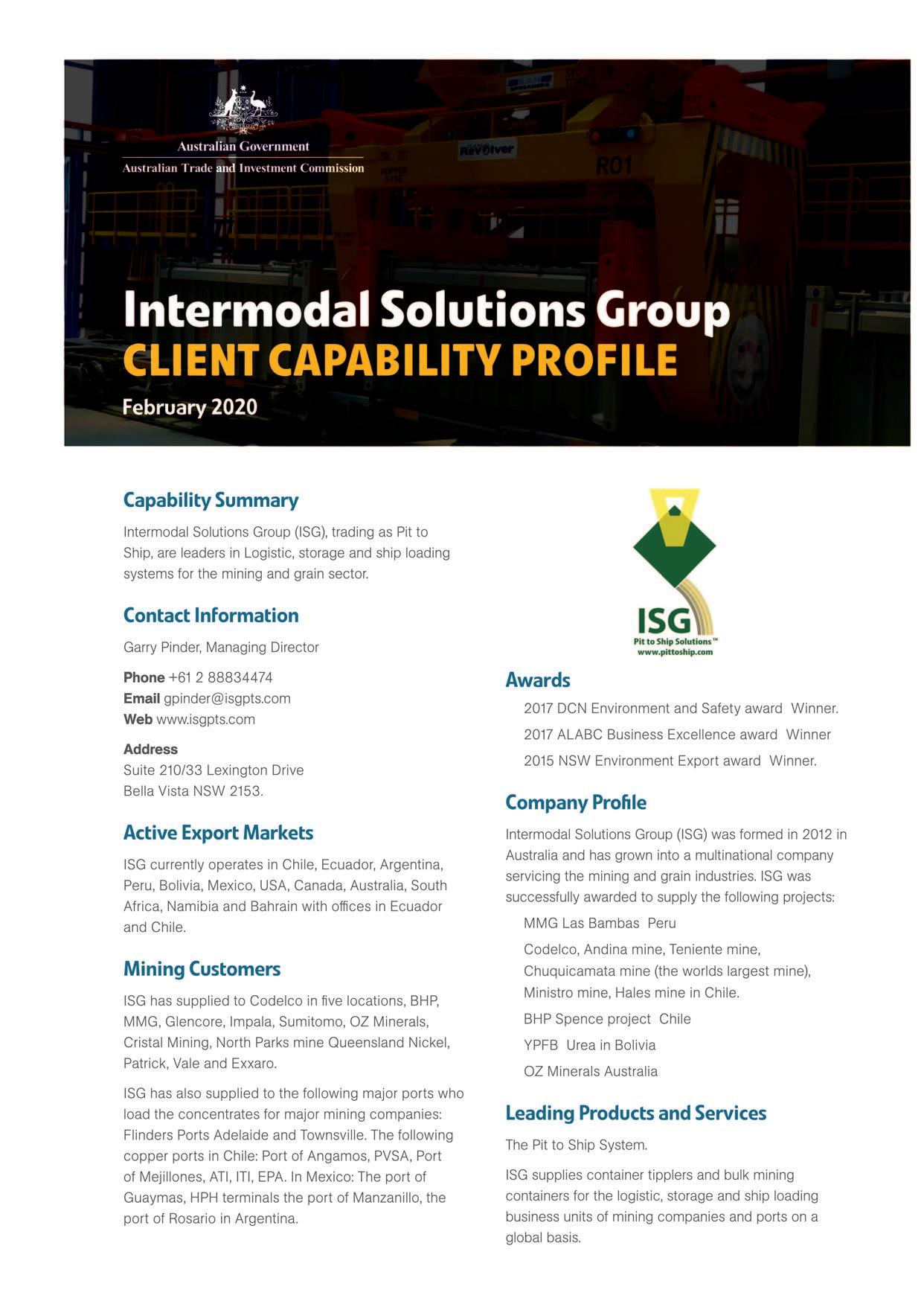
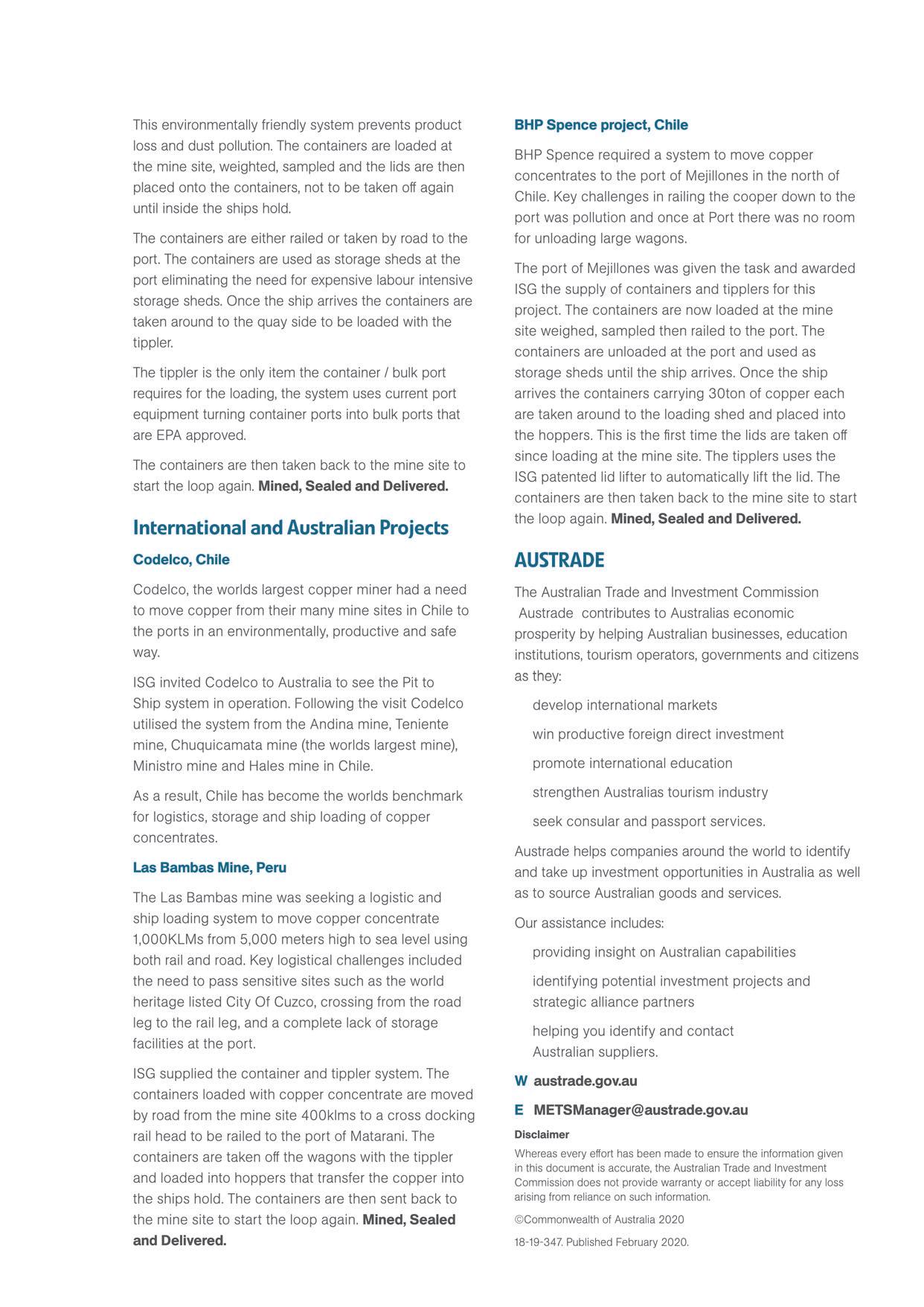
ENGINEERING & EQUIPMENT Negrini’s electro hydraulic equipment now with Remote Control Industria 4.0
Negrini has introduced a new tool, Remote Control Industria 4.0, which further enhances the company’s electro hydraulic grabs.
The tool is ideal for routine maintenance and to improve the efficiency of customers’ production processes.
FEATURES OF REMOTE CONTROL INDUSTRIA 4.0: v monitoring and control of processes in electrohydraulic equipment; v real time scans and diagnostics; v system communication via Wi-Fi or data sim; v notifications via email, sms or smartphone, tablet and PC; v preliminary production analysis; v routine maintenance alert; v failure prediction; and v immediate alarm in case of failure or malfunction.
THE SMART GRAB With Remote Control Industria 4.0 installed, the grab parameters automatically adapt to the type of material being handled without the need for human intervention, thus maximizing production and reducing costs.
In the presence of high-density materials such as mineral, the grab speed is reduced and the hydraulic pressure is increased, parameters otherwise not suited to lighter materials such as coal or cereals, where we see a change in speed and reduction in hydraulic pressure which would otherwise be unnecessarily high, causing energy wastage and wear.
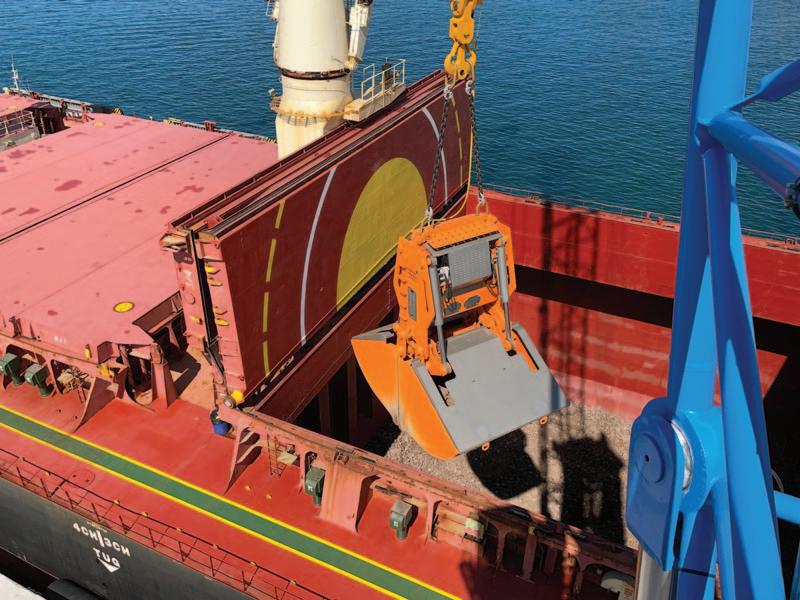
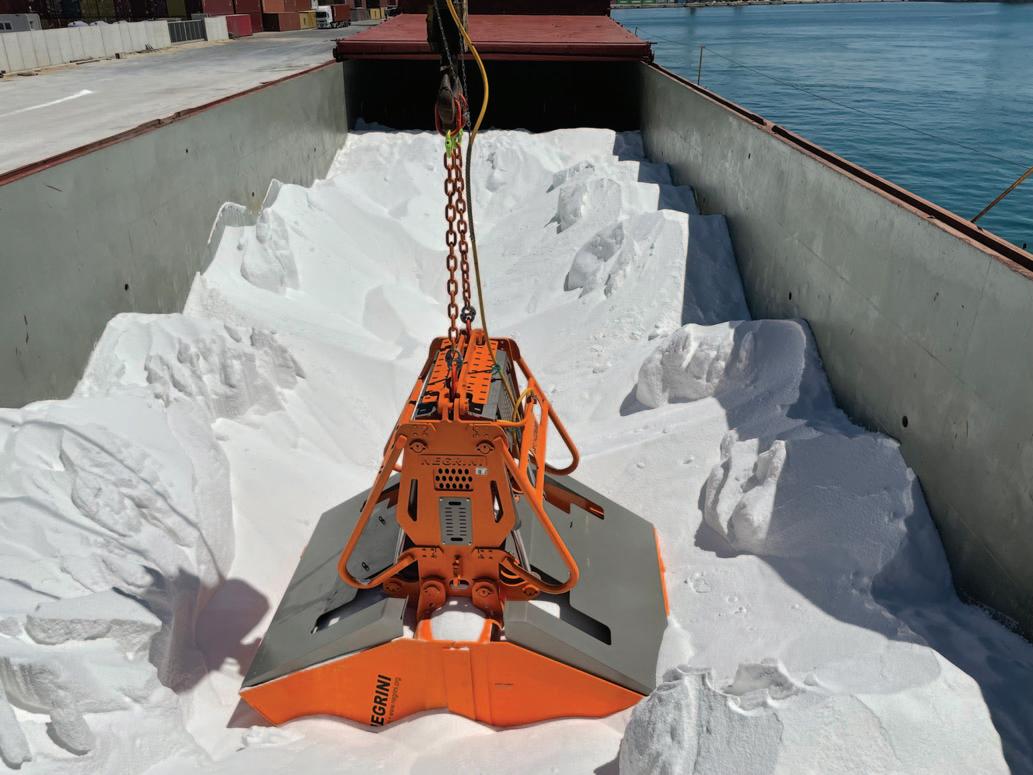
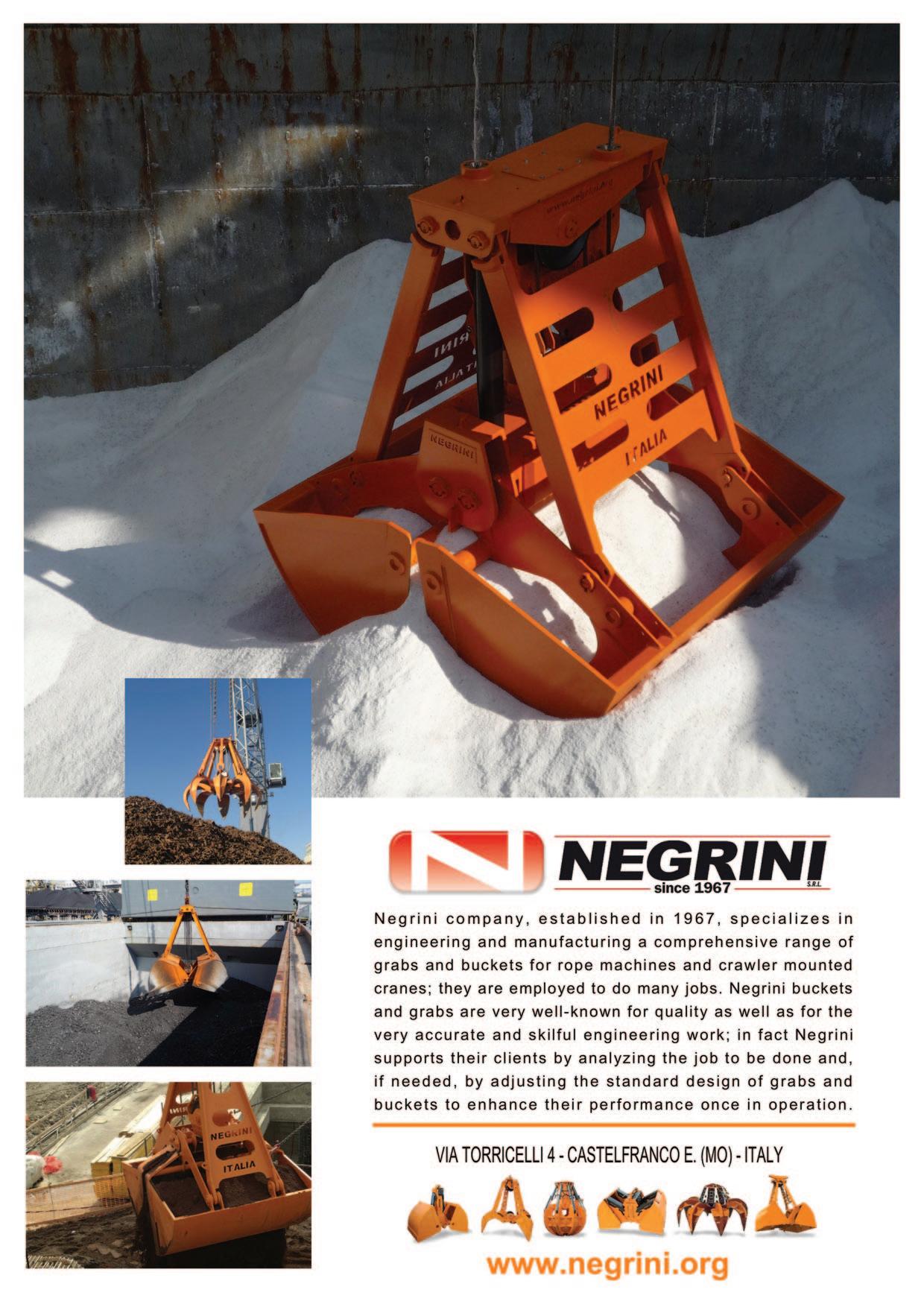
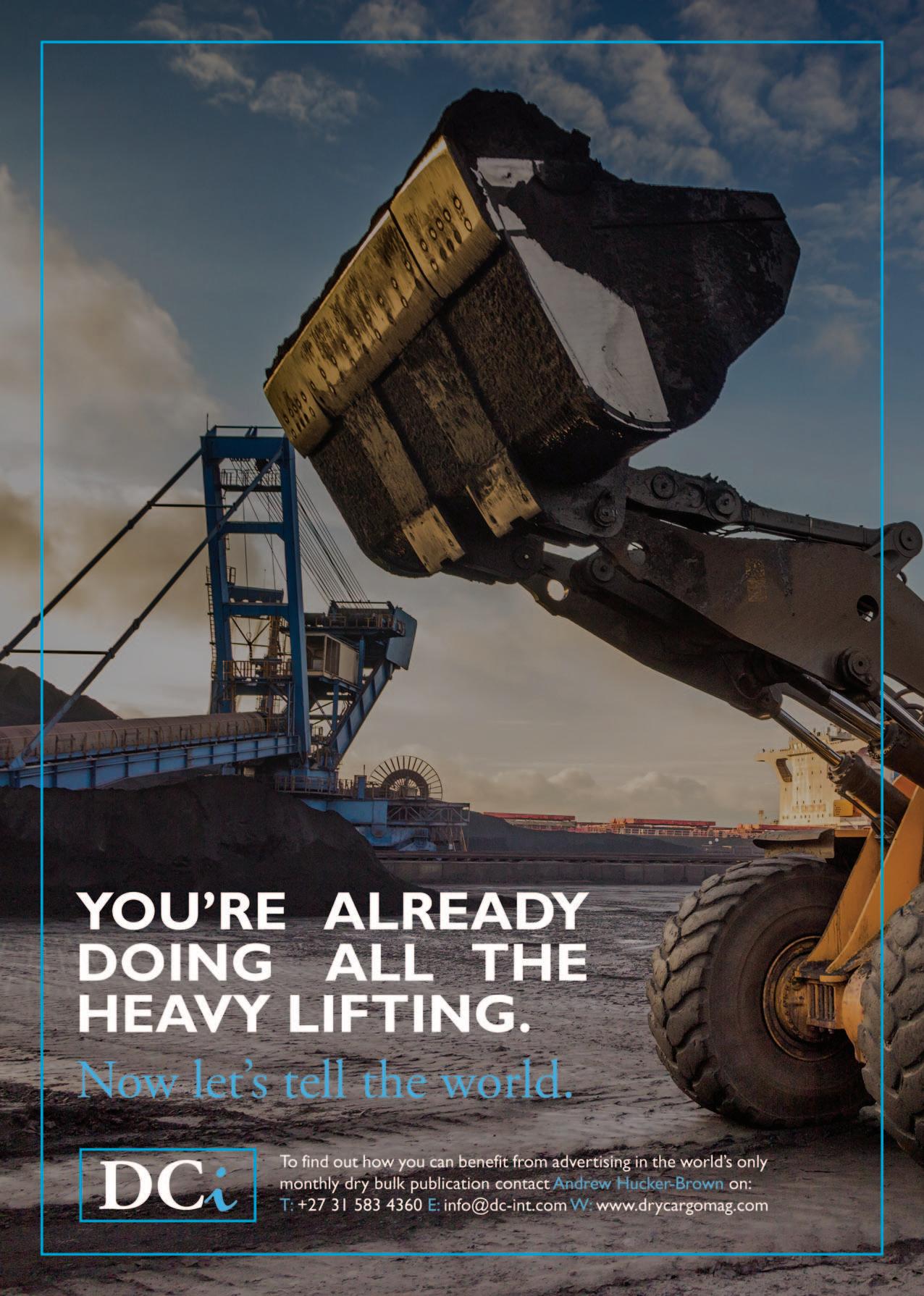

The most important advantage offered by the Remote Control Industria 4.0 device installed on Negrini’s equipment concerns the processing of data, thus allowing preliminary production analysis and failure prediction. Notifications are sent via email and sms and each time an event occurs, either an incident, arrest or maintenance request is recorded.
Costly machine downtime is therefore avoided while maximiz ing production, reducing periods of non-activity and minimizing expenses normally incurred by corrective maintenance works.
The client and Negrini S.r.l. will have total control over the condition of the equipment via Wi-Fi or a data sim, using a smartphone, tablet or PC, and will receive all notifications sent by the system so as to always be informed on machine requests and events.

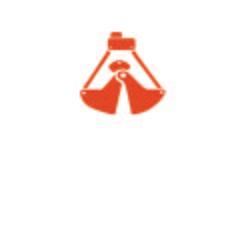
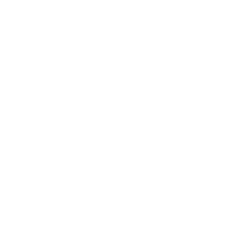

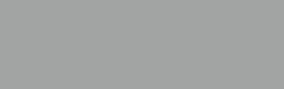
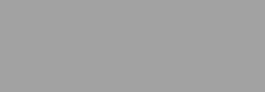
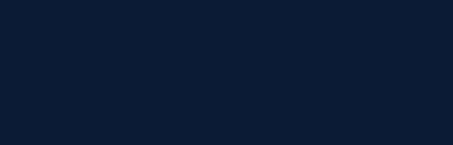
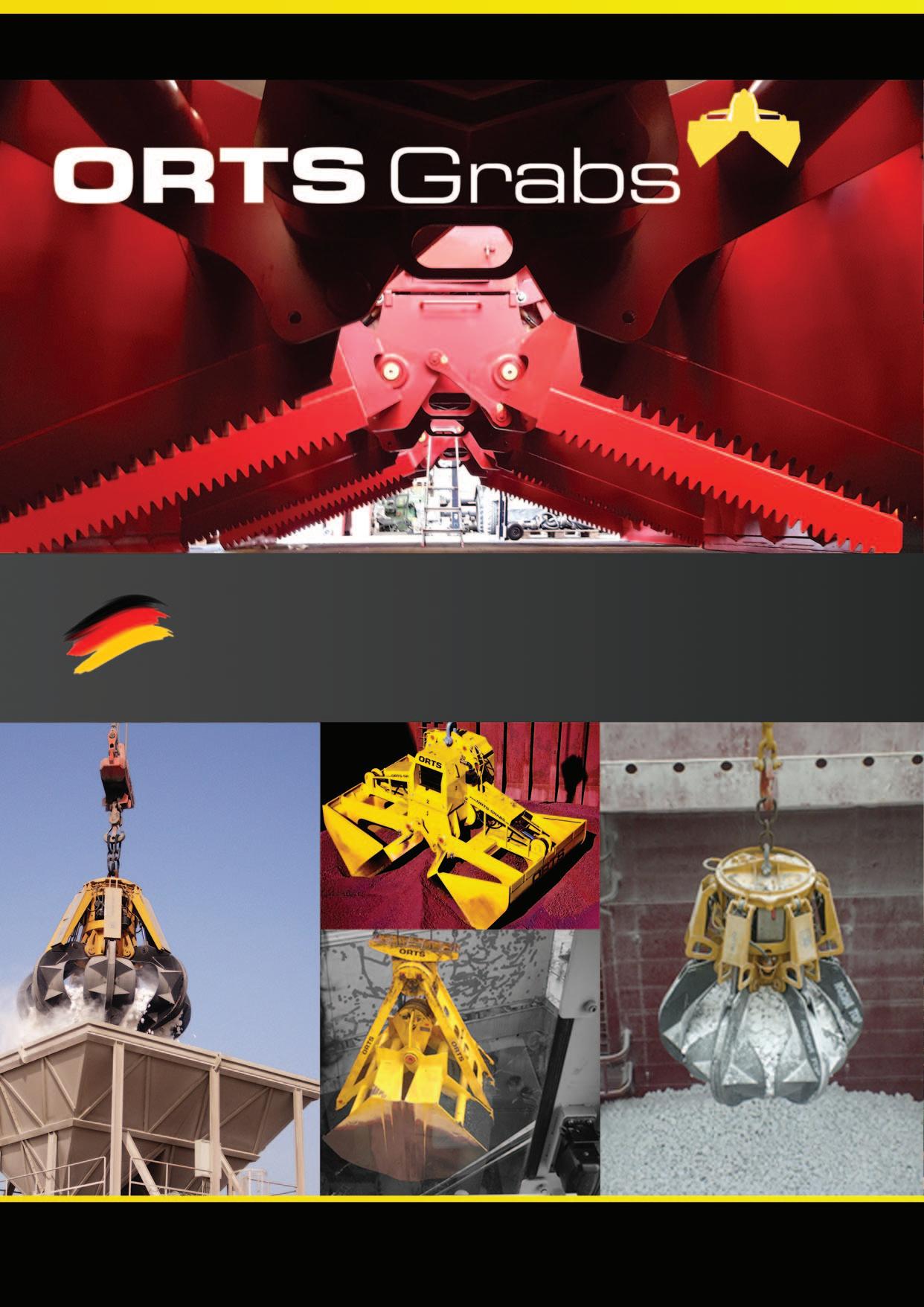
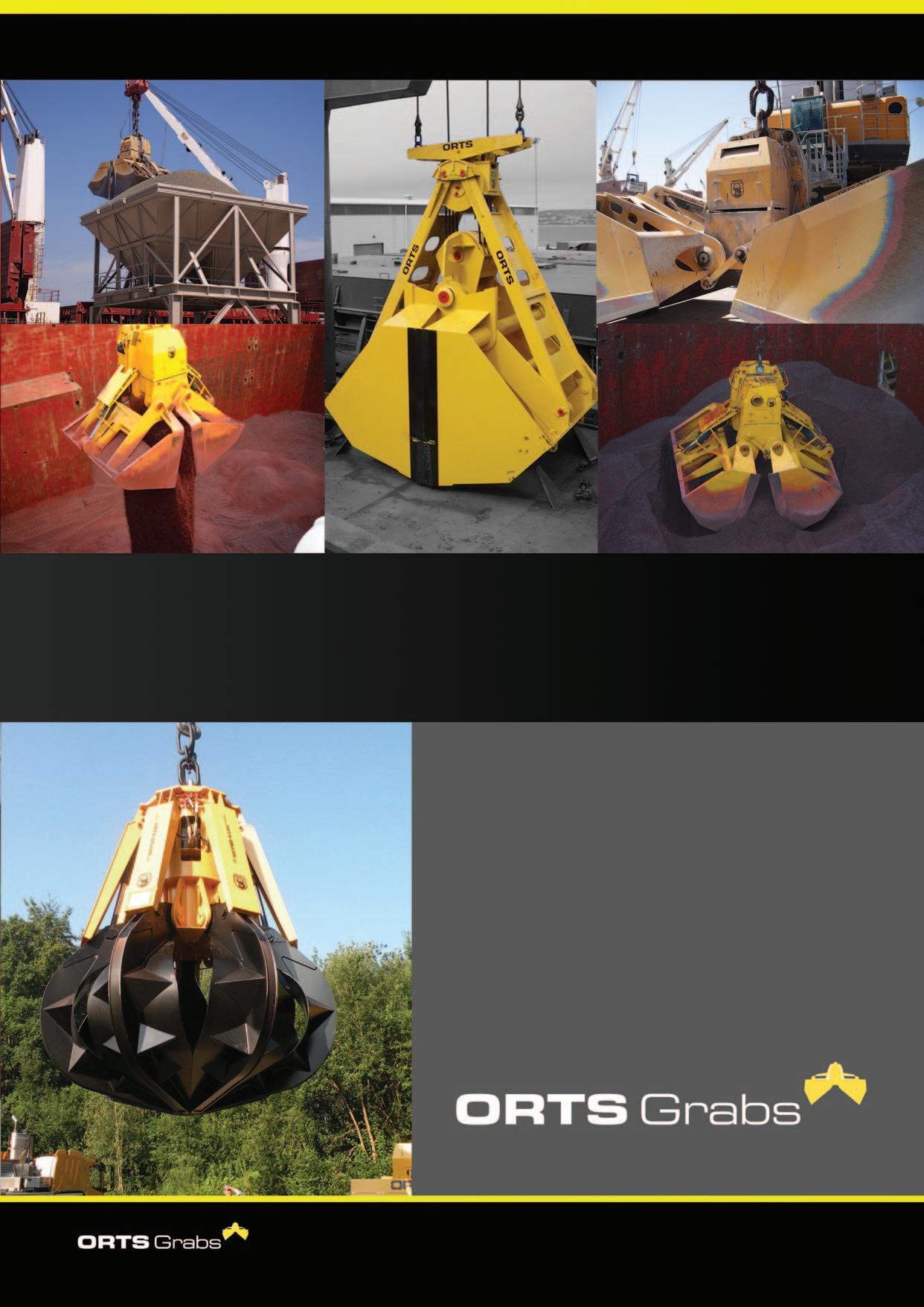
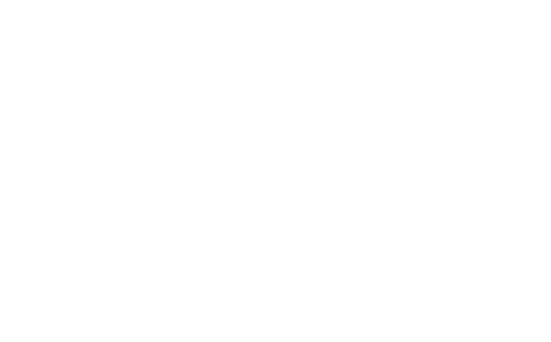
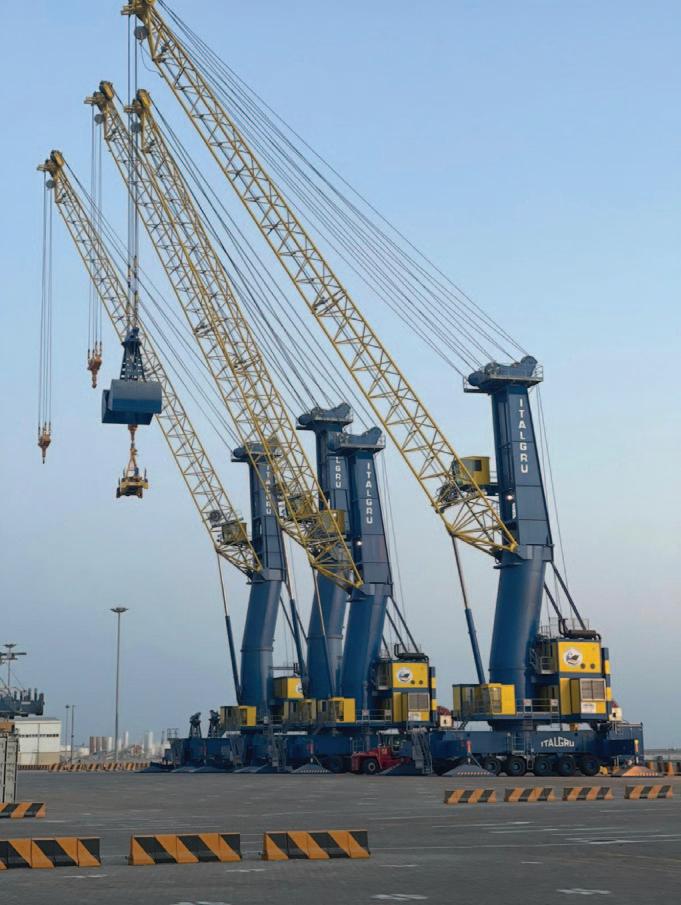
Italgru S.r.l. has proven experience in providing specific operational solutions in the cargo handling industry. These solutions cater to the most important logistic segments such as harbour, offshore, shipyard, and steel mills businesses. Competence and innovation are the pillars behind the Italgru brand, designs and developments.
TK OFFSHORE CRANE SERIES With the recently introduced knuckle boom crane design, Italgru has once again revolutionized the standard in crane design solutions and concepts. The TK series caters to a growing market that requires more efficient technical handling solutions with a view of saving space on customers’ offshore projects.
The TK knuckle boom offshore pedestal cranes are the right choice for applications with limited space available. The modular design allows the cranes to be equipped with a machinery house on the rear side of it or alternatively a compact version is available where the crane’s prime mover is situated within the interior of the slewing column.
The TS offshore cranes are available with either electric or diesel prime movers that can be customized for operation in both safe and hazardous areas. The unique design of the TK crane allows for adequate access for maintenance and inspections.
The key characteristics of the TK type cranes are: v compact design based on modular systems with or without machinery house; v Italgru electronic-type crane manage ment system; v power output regulator to avoid power pack overloading and to ensure excellent operating efficiency; v closed hydraulic system; v auxiliary winch; v all winches are mounted on the main frame for easy access and safe maintenance; v emergency load-lowering system; v three-ways roller slew bearing; v gross overload protection; v constant tension; and v man-riding application.
PORT CRANES With over 60 years of experience in the cargo handling industry, Italgru’s mobile harbour cranes are the result of careful studies of technological developments and the application of the necessary technologies to modern harbour equipment in order to handle every type of goods.
Both diesel-hydraulic and electric drive system are available, controlled by Italgru’s state-of-the-art electronic crane management system, ensuring the crane’s performance is optimized. Safe, smooth and precise crane handling is a result of innovative engineering and constant customer feedback and implementation of the latest technologies available.
Efficient, mobile and versatile, Italgru’s mobile harbour cranes can be used in any port for the handling of: bulk materials, steel or scrap metal, general cargo and heavy loads, containers.
Italgru’s crane designs, in compliance with F.E.M. 1.001 Design Rules, allow for classifications from A3 to A8 based on client’s requirements.
Recent orders for Italgru’s mobile harbour cranes include two IMHC 2120s for India. These units have a maximum capacity of 100 tonnes under hook; double winch; diesel-hydraulic and electric motor and cable reel to plug-in from berth. This delivery forms part of a project related to the manufacture and delivery of six cranes in total, two with a maximum capacity of 100 tonnes, with four cranes already delivered.
The IMHC 2120 is a true all-rounder, the flagship within Italgru’s range. It offers great flexibility and fast handling of all sorts of cargoes on vessels up to Post-Panamax size. For bulk cargoes, it is suitable for use with mechanical or four-rope grabs, or with attachments to handle coils and containers (telescopic 20ft and 40ft spreader).
The crane is built in two variants: a single winch with two ropes; and a double winch with four ropes (four-rope grab crane).
Italgru has also manufactured one IMHC 2120 E, diesel-electric crane, for delivery to Volos Port in Greece. This unit has a maximum capacity of 125 tonnes, a single
The four IMHC 2120s that are already in operation with the client in India — these units form part of the sixcrane delivery package.
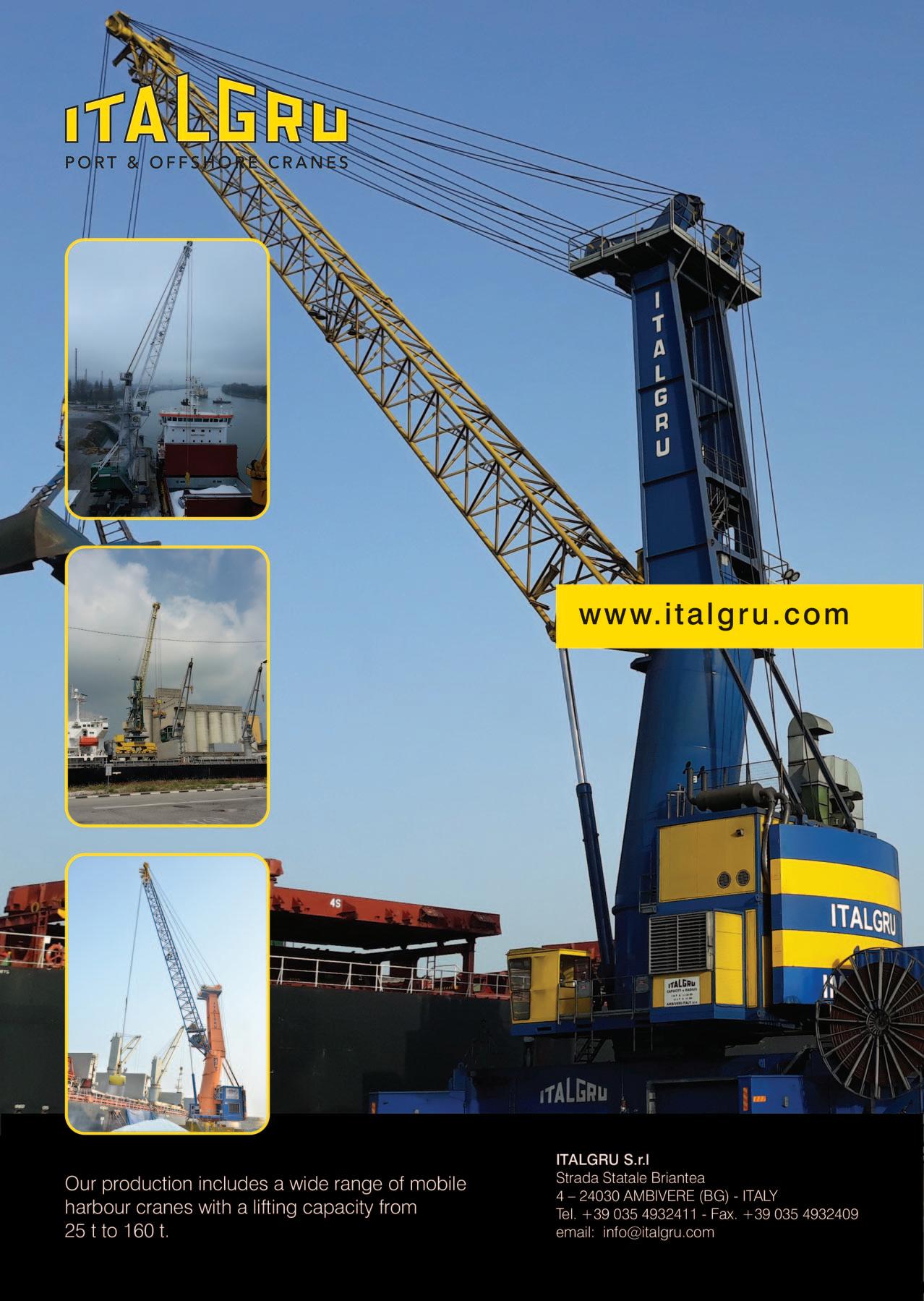

winch, and a cable reel to plug-in from the berth.
Italgru has also received an order from Russia (Azov Port), for one diesel-hydraulic IMHC 1580 crane, with a maximum capacity of 80 tonnes under hook. The IMHC 1580 is ideally suitable for feeder and medium-sized vessels. It is built for fast and efficient handling of bulk, coils and containers (telescopic 20' or 40' spreader). The crane is built in two variants: a single winch with two ropes; and a double winch with four ropes (four-rope grab crane).
Orders in Italy include: one IMHC 2120, with a maximum capacity of 125 tonnes, for Barletta Port; two diesel-hydraulic IMHC 1580s, with maximum capacities of 80 tonnes, for the ports of Ravenna and Oristano — deliveries are scheduled to take place by the end of this year.
GREEN SOLUTIONS Italgru is working ever harder to develop solutions that are environmentally friendly. As part of the company’s ‘green drive’, it has now designed all its IMHC models so that they are all available with electric drives. This option is now offered in addition to the traditional Italgru hydraulic drive configuration, and is already very popular with those customers which are focused on environmentally friendly solutions.
COVID-19 AND DELIVERIES IN 2020 The Covid-19 outbreak has dramatically impacted the global environment. Due to travel restrictions, after-sales and mainte nance was a major issue that Italgru has been able to solve through tele maintenance, an effective tool that allowed it to oversee operations from its HQ.
All of Italgru’s cranes can be monitored through telemaintenance: the crane is connected, through the internet, to the Italgru HQ or the local maintenance station, for realtime monitoring and troubleshooting.
Remote support has always been a tool used by Italgru to help its customers. The global pandemic and the restrictions imposed on travelling have certainly increased the number of requests to operate directly from Italgru headquarters.
These tools allowed the company to keep in contact with its customers and with potential ones, providing the opportunity to connect from employees’ homes and avoiding a slowdown in negotiations or project management.
A direct approach to the customers to carry out training and commissioning is the way to operate for equipment of high complexity and technological content like Italgru cranes. Italgru is aware that, during these times, it is important to exploit all the tools available in order to support customers in the most optimal way.
Despite the pandemic — which, from March to May 2020, shut down all Italian companies for over two months, causing delays in delivery of cranes and materials procurement — during 2020, Italgru was able to supply 11 cranes. Between September 2019 and June 2020, Italgru delivered three cranes to Stukwerkers Havenbedrijf, a private customer located in Gent Port. In September, the client received model IMHC 2120, with a maximum capacity of 125 tonnes, powered by a diesel engine; in June, two IMHC 3160 cranes, with a maximum capacity of 140 tonnes were delivered.
As for cranes with electric drives, in February 2020, Italgru delivered two IMHC 2120E cranes to Dar Es Salaam Port, in Tanzania, and two IMHC 2120Es were delivered to Gangavaram Port in India. These units are entirely powered by a cable reel in order to operate the crane using power supply from the quay.
ITALGRU CRANE SERVICE Italgru has built a network of sales & service partners present in all continents with a proven track records in providing our clients with qualified expertise and know how.
OPEN ARCHITECTURE The open architecture of Italgru’s IMHC foresees a wide use of components from primary brands in the world market, for which it releases all information (OEM part numbers, model, data sheet, etc). This provides easy availability of spare parts on the market; over 80 % of Italgru’s suppliers have their own branch office located in the major areas of the world.
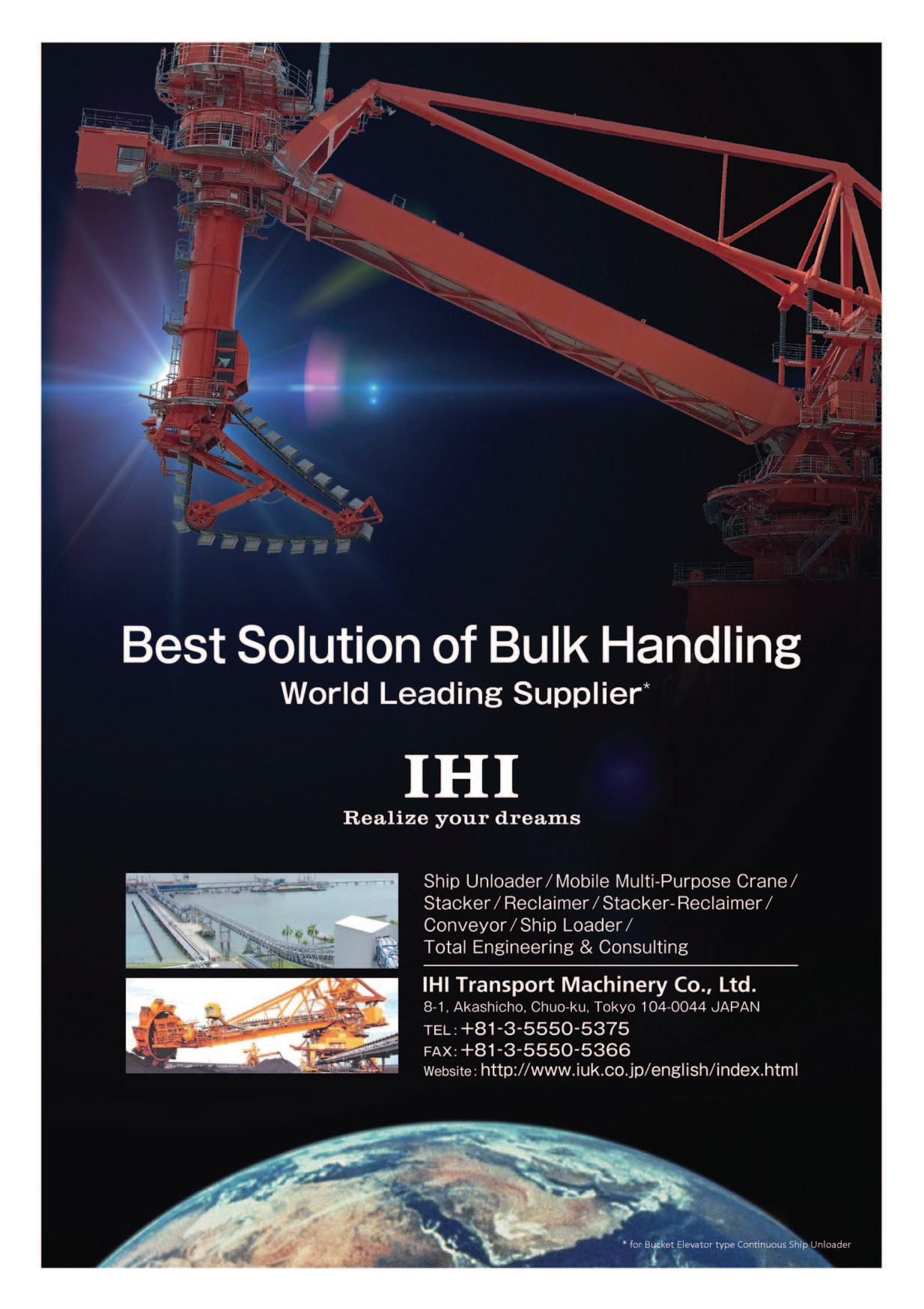


‘AAL KEMBLA’ CARRIES THEM ALL AND MORE, ON LINER SERVICE VOYAGE FROM EUROPE TO ASIA
Dredger being loaded onto AAL Kembla. Baskets discharge in Taichung.
On Valentine’s Day 2021, the AAL Kembla set sail from Rotterdam on a voyage from Europe, through the Persian Gulf and onto Shanghai — as one of six 31,000dwt A-Class heavy lift multipurpose vessels employed on AAL Shipping’s (AAL) ‘Europe, Middle East / India – Asia Monthly Liner Service’. On the journey eastwards, she loaded close to 37,000m3/15,000 metric tonnes of project heavy lift, breakbulk and steel commodity cargoes. These included multiple private yachts, the longest of which was 23m; a 33m tall mobile harbour crane weighting 370 tonnes; 16 power transformers with a total weight of 1,583 tonnes; a 41m-long dredger and components weighing 584 tonnes; and four giant circular baskets with an average circumference of just under 52m. The smallest parcel she carried was 1.8 tonnes and 2.5m3 .
Eike Muentz, General Manager Europe, commented; “The cargo carried on this particular voyage serviced over 30 shippers and upwards of 10 multiple industry projects along the route, including wind energy, infrastructure, oil and gas and mining. The volume and wide range of cargo types featured on this voyage illustrates the supreme flexibility of the A-Class and the growing dependency upon a breakbulk-style of shipping from global shippers. These customers would normally put their smaller breakbulk and steel commodity cargoes into containers, but cannot due to the current climate of increased costs and limited capacity.
He added; “Even with significant Covid restrictions, unparalleled port delays and cargo readiness issues, AAL’s monthly liner service between Europe and Asia has thrown a lifeline to all types of shippers and all sizes of parcel. It is credit to our crews, engineers and operations teams who worked tirelessly on the front line throughout the pandemic and keep these voyages on schedule and our customer cargoes moving.”
AAL’s owned fleet of heavy lift multipurpose vessels has grown by 117,600dwt in three months. This brings the carrier’s operating fleet to a total of 711,200dwt and comprises multiple vessel sizes, with 14 of these featuring a maximum lifting capacity of 700 tonnes and many of the larger ‘mega-size’ vessels offering up to 40,000m3 cargo intake volumes. The fleet serves AAL’s growing portfolio of multipurpose cargo services, which includes monthly sailings on the ‘Asia –Americas’, ‘Asia – Europe’ and ‘Atlantic’ trade routes, scheduled liner services ‘Asia – Australia’, and ‘Europe – Middle East / India – Asia’ and additional tramp solutions around the world.
ABOUT AAL SHIPPING AAL Shipping (AAL) is a highly awarded breakbulk and project heavy lift carrier with over 25 years’ experience creating and delivering competitive solutions for the world’s most dynamic industry sectors including oil & gas, mining, energy, construction, and agriculture. It is one of the multipurpose shipping sector’s top carriers by total fleet DWT and has a sterling reputation for safety, trust, and customer service.
AAL operates regular sailings on key trade lanes, comprising scheduled monthly liner services connecting Europe, Middle East, Asia and Oceania, frequent sailings through the Americas and tramp chartering solutions to any compass point. It carries all cargo types including project heavy lift, breakbulk, steel, containers and dry bulk commodities – large and small.
AAL operates one of the sector’s youngest and largest fleets of modern MPP heavy lift vessels. These are designed to load and carry any cargo and at the same time. The fleet comprises a variety of size classes that combine strong heavy-lift capability (700 tonnes maximum and significant cargo intake volumes (40,000m3 maximum). AAL spearheads the ‘megasize’ MPV segment, with a range of 30,000dwt + tonnage that offer its shippers highly competitive economies of scale on each sailing.
With 11 representative offices on four continents, AAL’s team comprises over 25 different nationalities and 35 spoken languages, ensuring a local 24/7 service in key trading hubs and in support of major trade lanes globally.
One of the Jumbo Kinetic’s latest voyages demonstrates more than Jumbo’s height of engineering, it also shows its highly flexible shipping solutions for complex projects that require the best engineered heavy transport solutions worldwide.
v The cargo challenge: three fully erected single boom shipyard cranes, manufactured by Haixi Heavy Machinery
Company in China for the Italian shipbuilding group Fincantieri. v The client: charterer LiHua Logistics
Company. v The voyage: from Qingdao, China to three different Fincantieri shipyards in
Italy.
THE HEIGHT OF ENGINEERING EXCELLENCE The most notable aspect of this voyage becomes clear as soon as you look at the accompanying photo below: these shipyards cranes were fully erected. The alternative was to transport them in pieces (pedestal, crane house and boom) and then erect them at their destinations. However, considering the overall project costs, the client preferred the cost-effective, specialized and safe Jumbo-SAL-Alliance transport solution.
The challenge of transporting shipyard cranes like this is that they are not only tall; they are also extremely narrow and have a small footprint. This means that, compared to other types of cranes, their centre of gravity is relatively high. The highest two cranes, for instance, were 137 metres high during loading (with boom raised fully) and 81 metres high during transport.
INCREASING STABILITY The team engineered this shipping solution in less than three months. “These cranes were particularly narrow; one of them was only nine metres wide at its base. Therefore, stability of the cranes was critical during the lift. We added 100 tonnes of ballast to the base of one of the cranes to increase stability during the lift and the voyage,” says Jumbo Senior Project Engineer Otto Savenije, whose job focuses on the lifting and stability calculations, seafastening and engineering of the project.
The Jumbo Kinetic, only one of three vessels in the world capable of this project, loaded the cargo with its own deck cranes — each lift as a dual-lift — into its cargo hold. “We lifted the first and second cranes one by one to the middle of the ship, driving them aft and forward on temporary rails that we built at two different heights. The third crane stayed in the middle of the ship,” explains Savenije.
A CLOSE EYE ON THE WEATHER With its cargo safely loaded, the Jumbo Kinetic departed Qingdao, China on 10 February. The dimensions of the cargo impacted the route options for Jumbo’s Vessel Manager Jeroen Herders. “The cranes were too high to pass under the Mubarak Bridge in the Suez Canal. So, we had to go round the Cape [of Good Hope], have a bunker stop in Durban, and then going up the west coast of Africa to the Mediterranean.”
To guarantee that the maximum allowed acceleration forces on the cargo where not exceeded throughout the entire voyage, the Jumbo Kinetic sailed with a maximum wave height restriction of 5.4 metres. Anything higher than that, the vessel had to slow down. “But as it happened, the ship had favourable weather en route, resulting in a smooth passage around the Cape and no delays during the transit.
SPIDER IN THE WEB Herders’ role continued on arrival at the three ports of call in Italy: Trieste on 1 April, Sestri on 18 April, and La Spezia on 26 April. He describes his function as being the “spider in the web”. This means that in addition to making sure that everything on the ship is working well, monitoring the voyage and organizing bunker stops, he also coordinates contact with the offloading ports. “This includes communicating with the agencies, the stevedores, the terminals and the client. At the end of the day, though, this is a team effort on the part of the Jumbo Kinetic’s crew, our engineers, and the Port Captains — Mike Ma in Qingdao and Andrea Chitto in the Italian ports — they did the real work!”
No project is completed successfully without great communication and a cooperative spirit from all involved, and these factors were key to engineering the lifts and designing the seafastening approach for this project.
With the completion of this complex highly-engineered shipping solution, another heavy transport challenge awaits the dependable Jumbo-SAL-Alliance team. It’s time to engineer the next shipping solution.
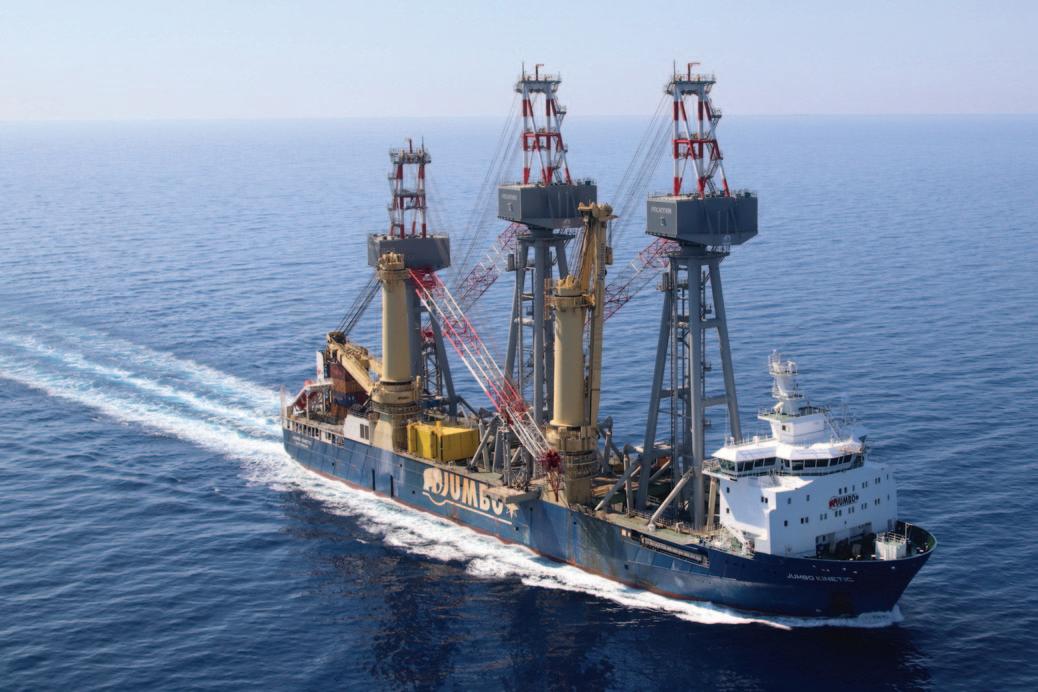
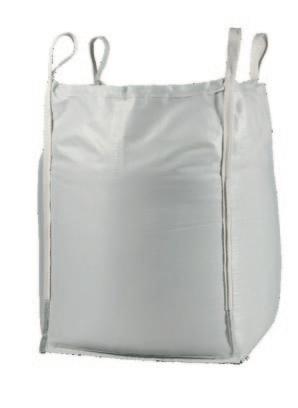