
4 minute read
Multi-commodity portal scraper reclaimers successfully commissioned in Japan
TAKRAF portal scraper reclaimer, multi-commodity, 1,100tph, Japan.
At the end of 2021, TAKRAF completed the hot commissioning of four portal reclaimers in Japan. The reclaimers form an integral part of the materials handling feeding system for a new multi-commodity power plant.
This advanced new plant will be fired by a combination of thermal coal and woodchips/biomass with TAKRAF scraper reclaimers located within the multicommodity warehouse, which is divided into two sites (North and South). The reclaiming system is able to convey material from one warehouse to the other, which means that with this flexibility, the system can be used to restore or, if required, mix material. Due to the redundancy required — two reclaimers are required to work on the same rail in the same warehouse — a dedicated safety and anti-collision system was implemented and extensively tested.
Each reclaimer is designed to scrape up to 1,100tph (tonnes per hour). With a rail gauge of 52m and a double-boom system (main and auxiliary boom in line), TAKRAF’s reclaimers are state-of-the-art machines and some of the largest built.
An interesting feature of each reclaimer is that each machine has a dedicated platform to carry a small bulldozer, which it can drop off at any location along the stockpile for cleaning purposes.
During the complex commissioning process, the TAKRAF team had to overcome multiple challenges and obstacles including travel and entry conditions into Japan as a result of the pandemic.
Wolfgang Schilling, Senior Project Manager – TAKRAF Germany, had this to say from site upon successful commissioning, “During commissioning, the close co-operation between all parties involved was essential to ensure success. These commissioning circumstances and conditions were indeed extraordinary and very challenging. The efficiency and teamwork shown by all stakeholders under these arduous conditions was something to behold and I would like to personally thank the entire project team, particularly the site team, for their continuous contribution, patience and support. Successful commissioning of this project only serves to entrench TAKRAF scraper reclaimer solutions as the best in the business!”
Maritime electrification plant Echandia opens branch in Norway
Swedish company Echandia, a major developer of battery systems for maritime electrification, expands in the Norwegian market through the appointment of industry veteran Roy Storeng to lead the business development for Echandia in Norway. Storeng has an extensive background from the maritime and transport industry in Norway and abroad.
Norway is a front-runner in maritime electrification. Of the total number of fully electrified vessels globally, as much as 36% operate in Norwegian waterways with no other countries coming close. As such, Norway is an important market and will continue to lead the way on the path to a zero-emission global fleet.
Echandia is a respected developer of zero-emission energy solutions for heavy-duty maritime electrification.
Crane manufacturer Seram has been in business for over 40 years, during which time its customers have benefited from the profitability and efficiency of its machines. The company is now responding to today’s environmental concerns by offering an electrically driven crane.
The benefits of a Seram solution include:
INCREASED PRODUCTIVITY: v electric-driven prime motor; v reduced downtime due to no internal combustion engine maintenance; and v balanced boom reduces structural stress and fatigue, greatly increasing the life cycle while reducing operational downtime.
WIDE SELECTION OF SUPPORTS FOR THE CRANE:
ANSWERING ENVIRONMENTAL CONCERNS WITH AN ELECTRIC DRIVEN CRANE: v no exhaust released into the atmosphere; v no internal combustion engine oils, lubricants or coolants to manage; v lower energy consumption through the equilibrium design (balanced boom); and v noise reduction.
LOWERING COST OF OWNERSHIP WITH ELECTRIC DRIVEN & BALANCED BOOM OPERATION: v electric vs. diesel results in a lower cost of energy; v balanced boom leads to reduction in structural stress; v balanced boom requires only enough
energy to lift the load, not the boom/load combination; v up to 50% of a conventional electric crane; v up to 80% of a diesel conventional crane; and v hydraulic cylinders are identical and interchangeable with rod design cast of one piece.
INCREASING LIFE CYCLE WITH EXCEPTIONAL LIFETIME AND RELIABILITY OF COMPONENTS: v balanced booms result in a major portion of the weight being directly over the centre of the crane, reducing structural stress; v high-pressure hydraulic system operates at a reduced operational pressure (420 bar design operating at an average of 180 bar); v hydraulic unit equipped with load sensing distributor & variable flow pumps; v increased service life of hydraulic system components; v low noise level; and v reduction in hydraulic oil temperature rise. v fixed pedestal — where the base is anchored to a concrete foundation; v free standing — which has no anchoring at the base, facilitating relocation; v trolley — which is rail-mounted for lateral movement; v gantry — which is rail-mounted for lateral movement while allowing transportation equipment to pass under the crane; v crawler — providing total autonomy of the crane through diesel power while operating under electric power; and v barge — offering marine mobility and an economical alternative to construction of a dock.
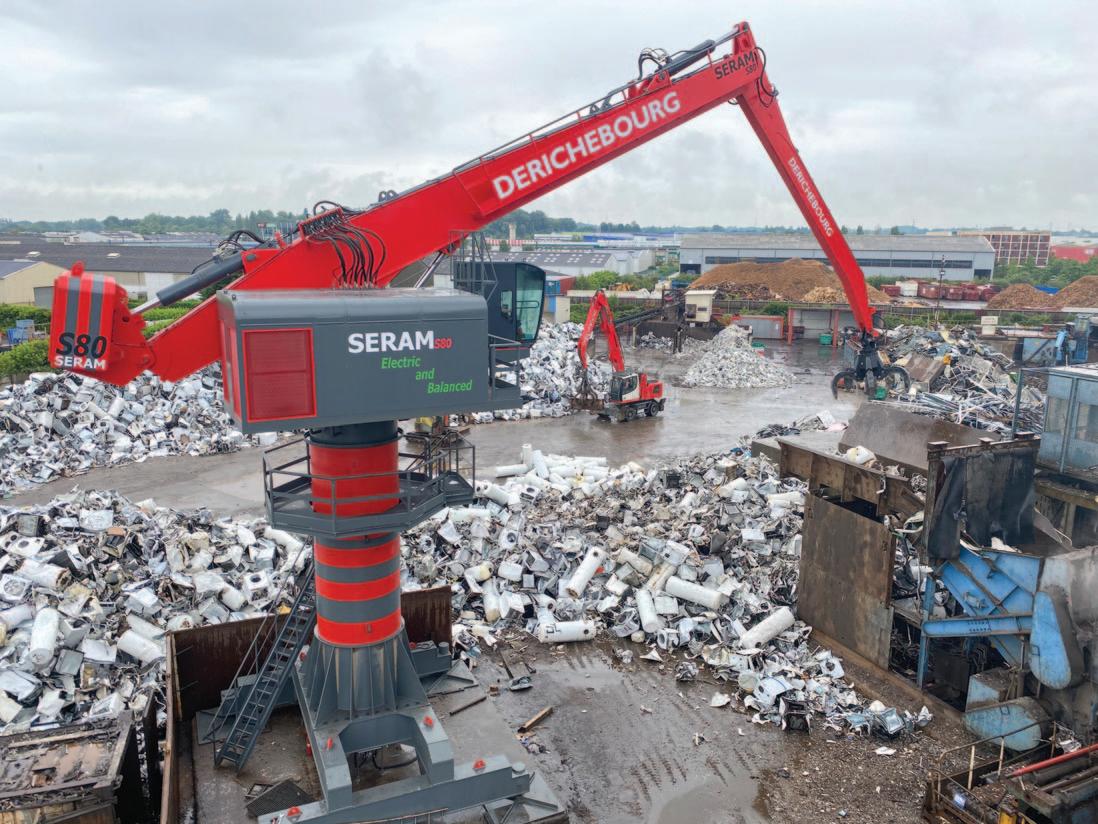