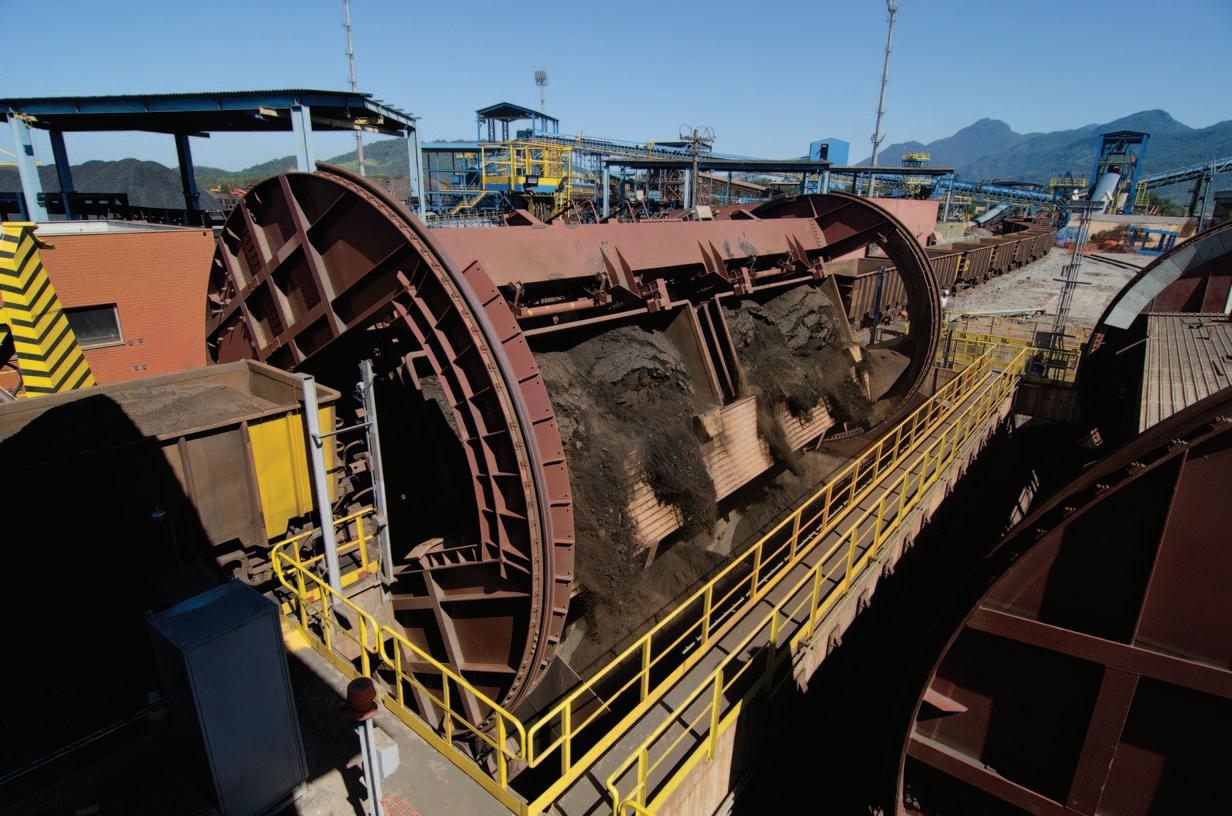
29 minute read
ALL SYSTEMS GO: COAL HANDLING EQUIPMENT AND TECHNOLOGY IN THE SPOTLIGHT
All systems go
coal handling equipment and technology in the spotlight
High-performance thyssenkrupp rotary car tippler.
Louise Dodds-Ely
thyssenkrupp: efficient equipment for entire coal handling process
Coal represents a major portion of dry bulk which is transported around the globe today. Alongside other fossil fuels such as natural gas and oil, it remains an important source of energy in many parts of the world. The production of steel still depends on coke, which is one of the most important products derived from hard coal. Coal tar, a by-product of the coking process, is an important raw material for the chemical industry. The aromatics and carbolic acid which are derived from it, are used for the manufacture of a variety of plastics and dyes. Both ammonia and methanol can be synthesized from brown or hard coal, while fuels are produced with coal-to-liquid processes. These industrial processes rely on a reliable logistics network that links the mine with the plant. The need for long-distance transport has led to the development of specialized rail and port infrastructure for import/export terminals. Coal deposits are often located in more remote areas and transport by train or ship becomes necessary to feed the plants and power stations. Countries which do not have their own coal deposits, or where the coal demand exceeds national supply, need to import the coal they require by sea. The vessels bringing the coal are loaded at export terminals which are equipped to receive the bulk material from open pit mines and transfer it onto ships. Import terminals have to be developed to unload the coal and direct it onwards to the industrial user. thyssenkrupp Mining Technologies is one of only a few companies in the world
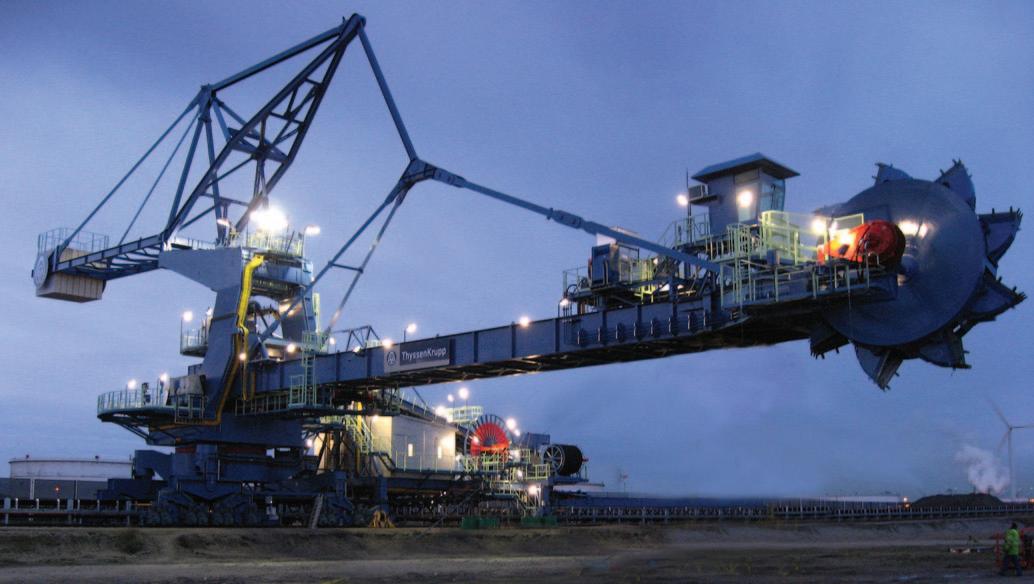
Bucketwheel stacker/reclaimer at an import terminal.
able to supply the plant and handling equipment covering the entire logistical network from mining, to the transportation and handling of coal. In the mine this encompasses bucketwheel excavator systems, in-pit crushing systems and belt conveyors. Further down the line there are train loading and unloading stations, stockyard equipment, blending beds, shiploaders and ship-unloaders as well as conveyor systems within power plants, steel mills and other industrial plants.
At various nodes, stockyards function as a temporary storage facility for the material and also act as a buffer between different modes of transport and plant processes. Specialized machines perform the task of stacking the material onto stockpiles, and Shiploader at an export terminal.
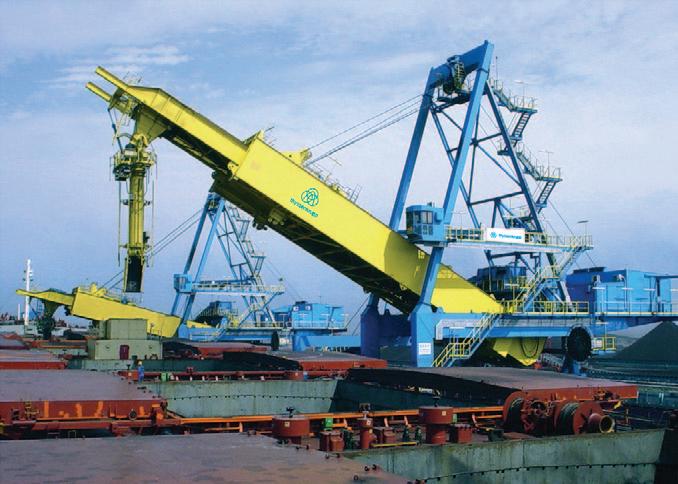
MY DRIVE IS FROM NORD!
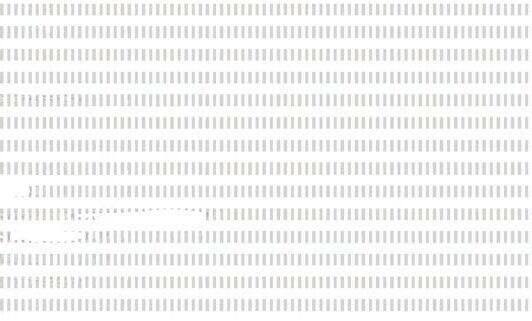
MAXXDRIVE® – Powerful drives for heavy-duty applications
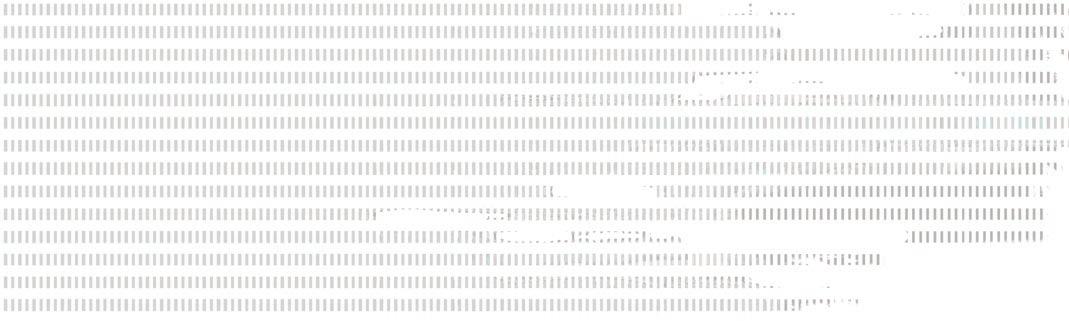
Variety of options for tailor-made application concepts High output torques and drive powers Comprehensive configuration and mounting options allow for standardised as well as customised drive solutions


Grab ship-unloader at import terminal.
reclaiming it again when required.
The design of the stockyard and the machine types which are selected depend upon the process and function of each particular facility and its unique local requirements, climatic conditions and restrictions. Stockyard layouts at harbours, for example, are generally subject to tight spatial constraints and are required, from an operational perspective, to minimize the time required for loading a ship. For this reason, they tend to use high-capacity bucketwheel stacker-reclaimer combinat ion machines. By contrast, a power station requiring lower throughputs and subject to strict environmental constraints due to its proximity to urban areas, may opt for a circular stockyard which is completely covered with a roof to minimize noise and dust emissions. Strict regulations may also motivate the selection of pipe-conveyors inside such a power plant because the material is not exposed to the environment. At mines or chemical plants, where the composition of the material must be controlled according to the requirements of the end user, stockyards are used for homogenization or blending different grades of material. In such cases machines such as bridge or drum reclaimers are employed because their mode of operation yields the best results. In each case, the stockpile design and stacking method must be selected to suit the particular application.
The rail network functions as an efficient link between mine, harbour and
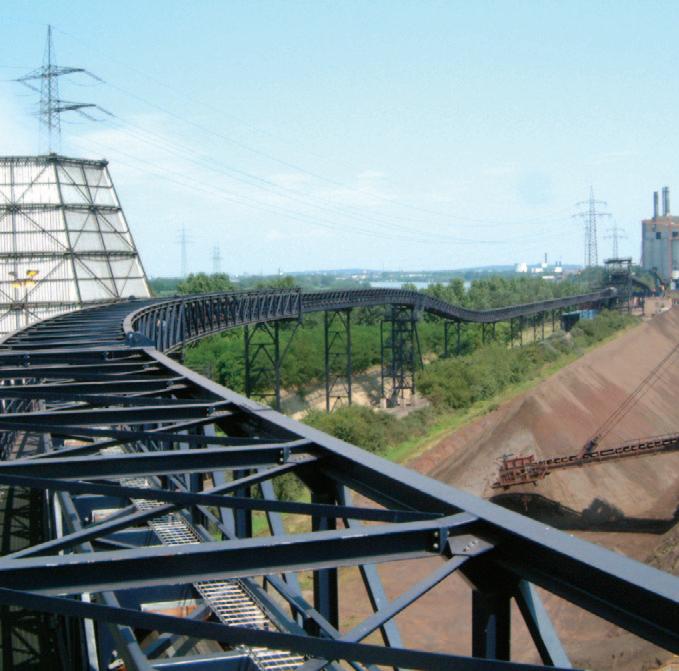
Steel bridge of pipe conveyor for inplant transport with, inset, pipe conveyor system inside the steel bridge.
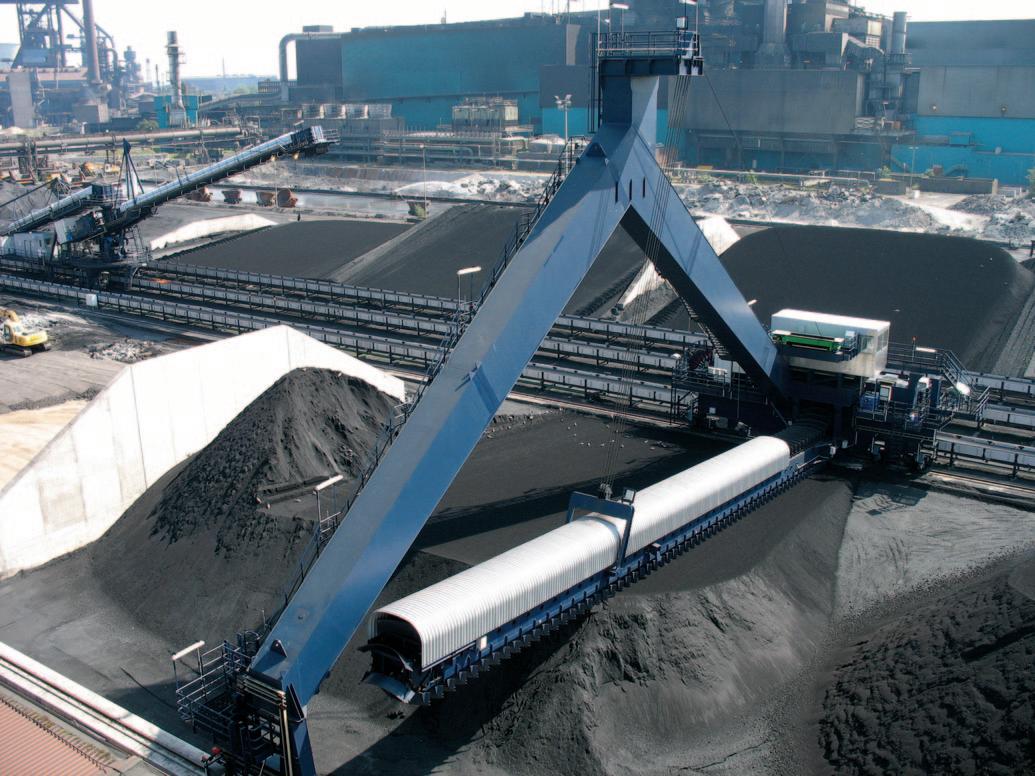
plant. Rail loading stations transfer the material onto trains for outward transport, while ensuring the optimal filling of individual wagons. At the destination, the unloading of the train is done by tippler systems which tip and discharge the material from the wagons. The design of the installation and choice of a suitable tippler depends on the specifics of the application. Tipplers are constructed in a number of different geometries, with implications in terms of cycle time, plant infrastructure and compatibility with rolling stock. Side-tipplers are generally less costly to install, while rotary tipplers are selected for high-performance applications requiring higher throughputs. At terminals for transshipment, the latest rotary tippler installations can unload four wagons simultaneously without the units being uncoupled from the train. With such machines, the whole unloading process can be automated to a high degree if the appropriate logistical arrangements are made.
At the export terminal, the material supplied by the mine is temporarily stored
Stacker and full portal scraper at a stockyard of a steel plant.
Stockyard machines at a power station.
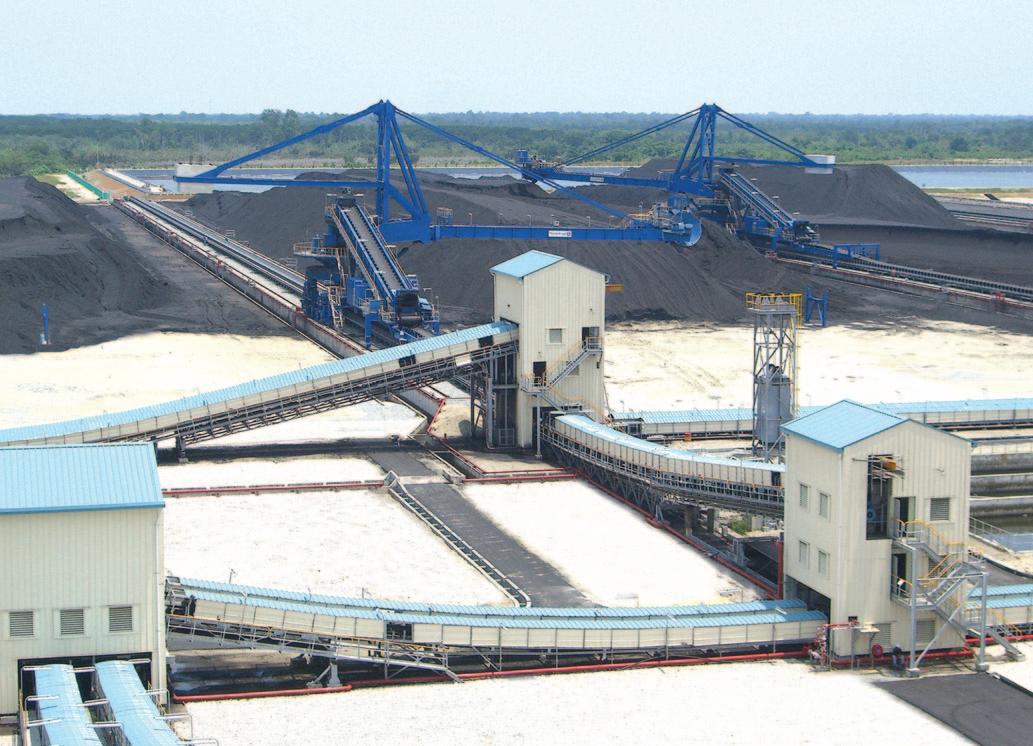
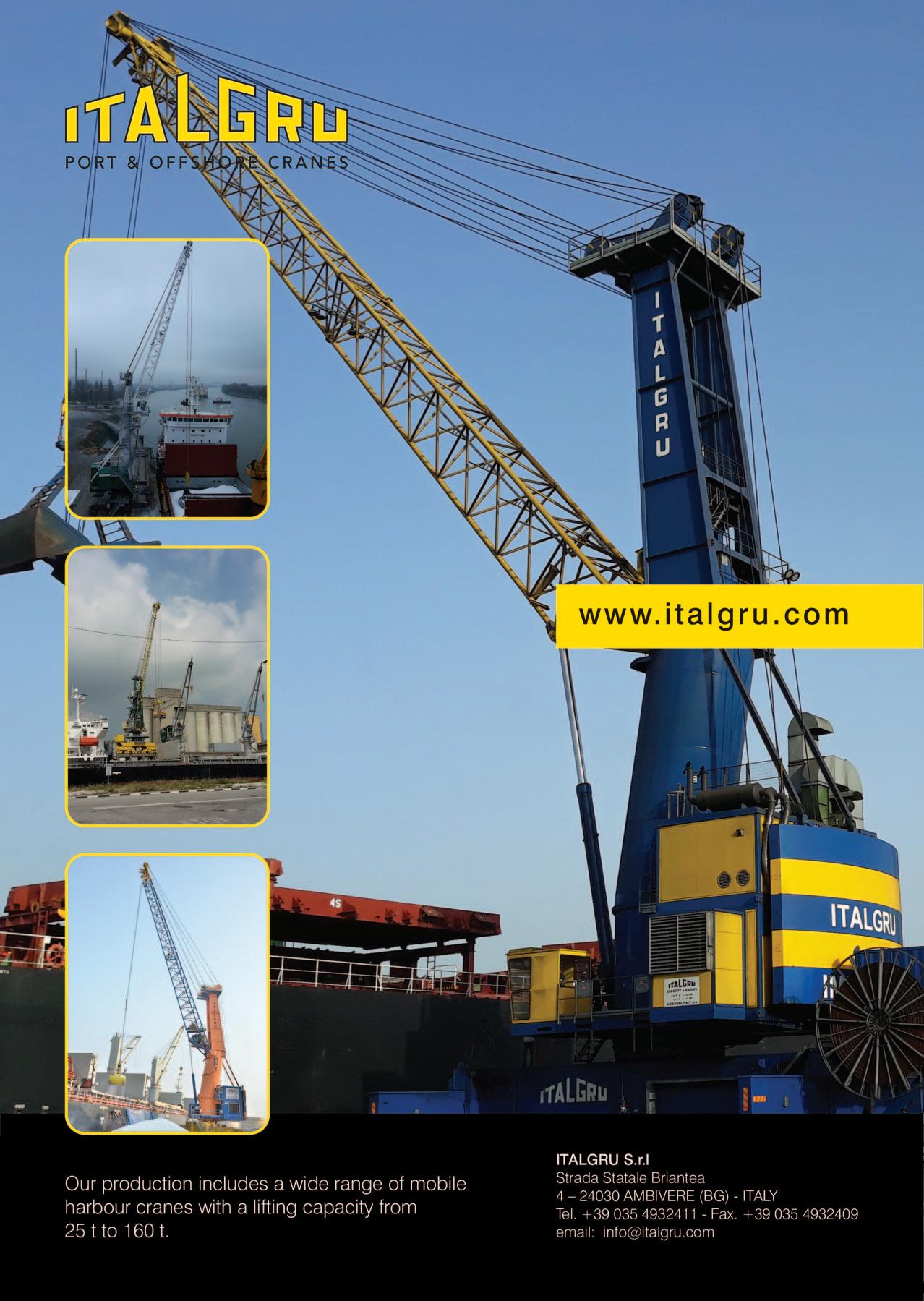
Train loading station. ENGINEERING & EQUIPMENT
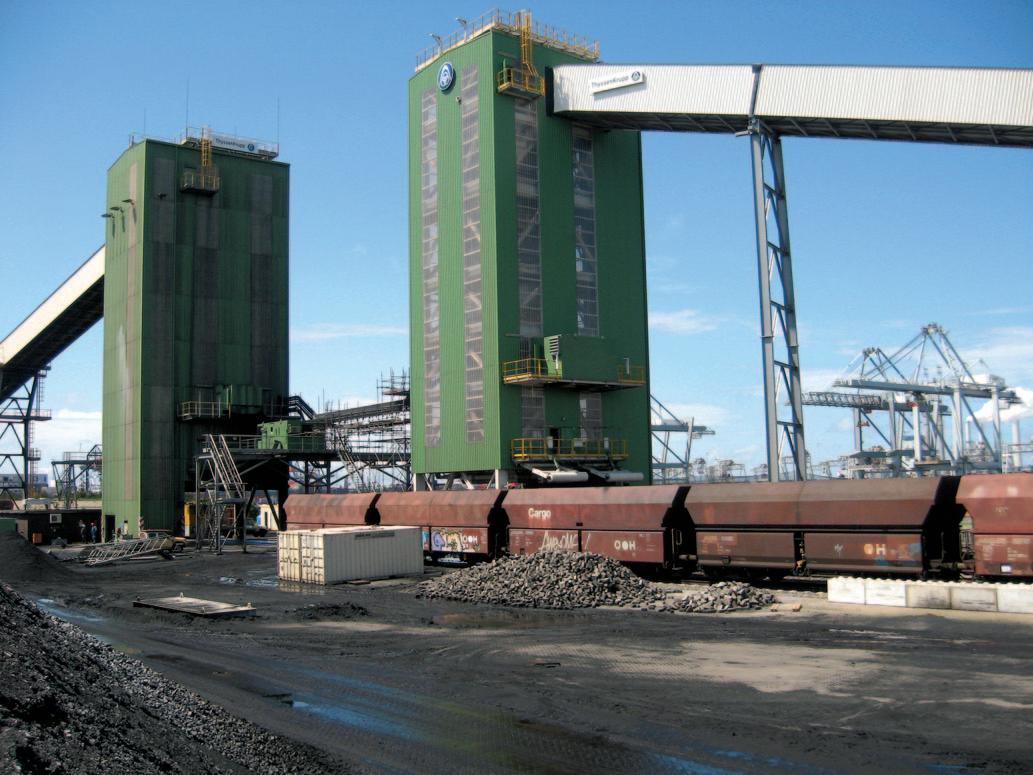
in the stockyard. The stockpiles are generally segregated on the basis of origin and grade of material, a procedure which allows the product of a particular supplier to be dispatched to the correct customer, or for the mixing and homogenization of different qualities according to customer requirements. When a ship arrives at the harbour, the material earmarked for that shipment is transferred from the stockyard and loaded onto the waiting vessel by means of a shiploader. thyssenkrupp offers the full range of shiploader configurations to cater for most customer requirements; this includes radial, slewing, co-ordinate, linear and stationary type machines. Port handling equipment must be designed to perform a range of motions and adjustable reach to ensure sufficient flexibility for each particular application. This is important because the machine must cope with the full range of shipping that can be expected, both in terms of size and configuration. For coal, the ship size tends to vary from 35,000dwt to 250,000dwt. High capacity machines are required for coal export to minimize the time vessels spend in the harbour and the resulting costs.
The function of the import terminal is to unload the incoming cargo vessels and dispatch the product to the next destination, whether by road, rail or ship. Various types of specialized machines can be used for the unloading of ships, with the choice of suitable equipment depending on factors such as material properties, product variety and throughput that must be handled. Continuous unloaders, equipped with bucket elevators, are excellent for handling coal and operate at a high level of efficiency. The time lost in the manual cleaning of the hold is kept to a minimum through careful optimization of the unloading procedure. Where a greater variety of materials must be handled, grab unloaders offer greater flexibility; in some cases, the machines may even be used for loading vessels. The unloading process of grab unloaders is more time consuming, however, due to its cyclical nature.
In conclusion, it must be restated that coal remains an important raw material for a large number of industries globally. This generates a continued demand for logistical infrastructure to transport coal from the mine and deliver it to the end user. thyssenkrupp offers its customers a complete service, relying both on its vast experience in this field whilst also remaining committed to innovation and the optimization of its products; a partner that forms a vital link in the path from pit to plant.
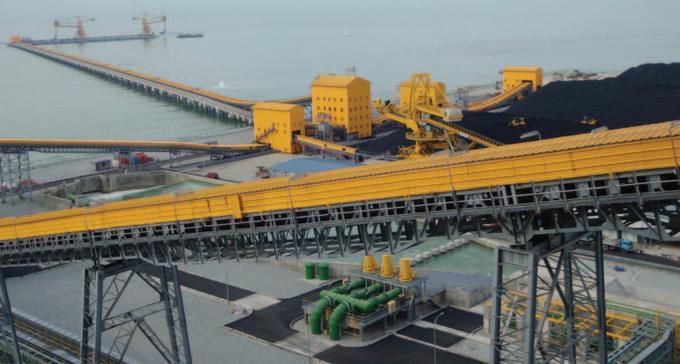
Two continuous ship-unloaders at an import terminal. www.drycargomag.com
One-stop-shop for energy and data management systems for coal handling equipment along the process and transport chain

Today, coal still represents a major proportion of all dry bulk. It is extracted from either an open surface cutting or through underground mining and is typically processed prior to be stockpiled. Millions of tonnes of coal are handled yearby-year and Conductix-Wampfler, with its prominent position into the world market for energy supply and data transmission systems to mobile machinery and equipment, is the ideal choice for engineering, design, manufacturing and installation of customized solutions to suit a wide range of applications.
Conductix-Wampfler’s extensive range of solutions, including motor-driven cable and hose reels, cable festoon systems, conductor rail systems, slip ring assemblies and rotary joints or energy storage systems, data transmission solutions and radio remote controls is present at all stages of bulk materials handling and storage processes contributing to safe, efficient and trouble-free operations.
Machinery and equipment in longwall mining, open pit mining or drill & blast applications reliably perform their service due to proven and robust power supply and data transmission systems.
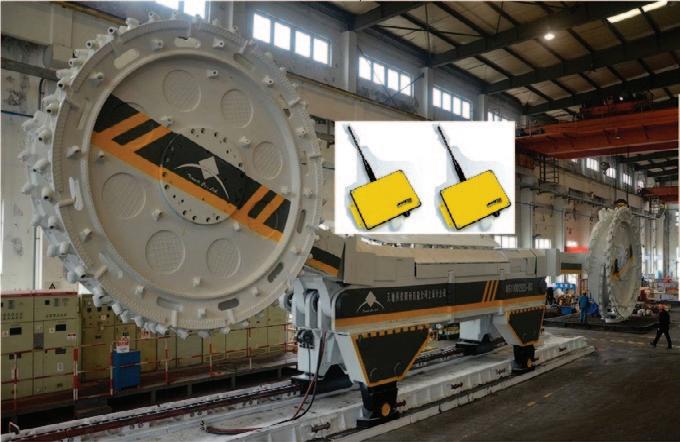
Jay Radio Remote Controls enable a safe work environment for operators of a coal shearer at Tiandi Shanghai Mining.
COAL IS TRANSPORTED BY TRAIN FOR PROCESSING AND TRANSFER TO STOCKYARDS IN BULK PORT TERMINALS. Coal is transported in rail wagons that are moved by ‘wagon pushers’ moving the wagons under hoppers to load material or to wagon dumpers for unloading. So far, those pushers were diesel powered, but in this area, too, a reconsideration of solution approaches is taking place.
Conductix-Wampfler is strengthening partnership with OEMs and end-users
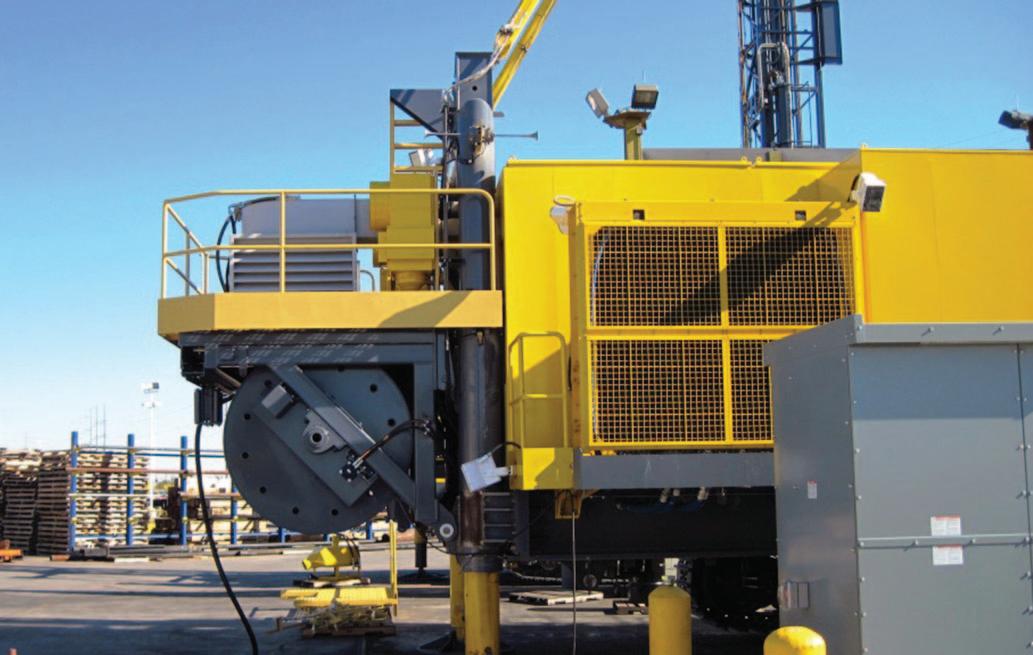
supporting a conversion to electrically driven machines by means of cable reeling systems, conductor rails or energy storage devices like batteries including efficient charging solutions.
Fastening device EPIROC VIPER series 270 used on drill and blast applications to mount trailing cable reeling system

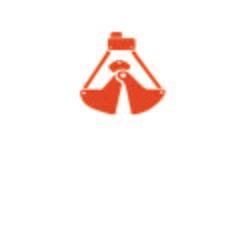
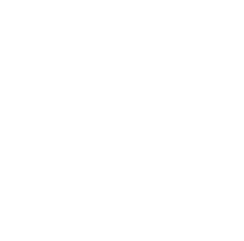
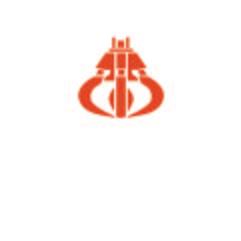
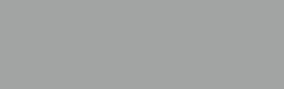


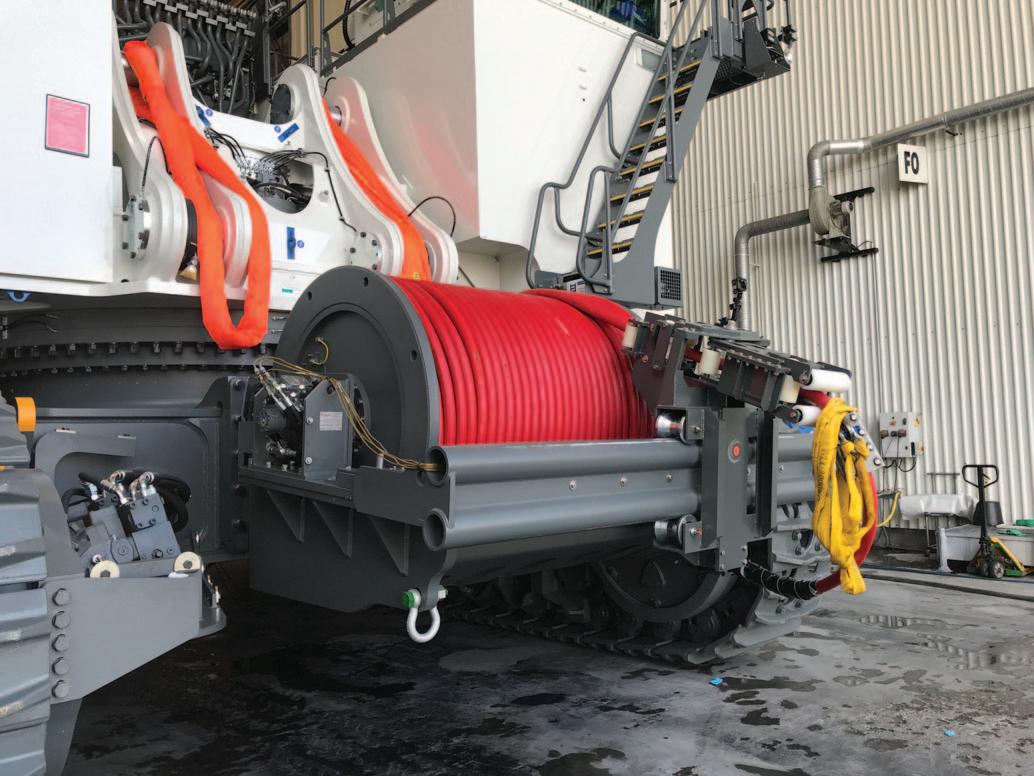
Brand new solution to electrify shovels that is already successfully tested at various shovel types and deployed into the market.
Customer trustworthiness and preference for Conductix-Wampfler products is proven along the years. Recently, the company received an order for the complete refurbishment (new equipment and services) of two existing Level Wind Reeling Systems in Australia on Anglo Coal’s Stacker Reclaimers at Lake Lindsay, replacing them with the new ARGO solution developed at ConductixWampfler’s Center of Excellence in Italy.
WITH THE USE OF SHIPLOADERS TO BULK PORTS AROUND THE WORLD On belt conveyor systems coal moves from stockyards and reaches shiploaders that load it onto vessels for shipment to various port locations all around the globe.
In bulk port terminals reached, coal will be unloaded and will be transferred to various plants for transformation. Coke oven plants are one of the important segments in coal transformation and Conductix-Wampfler has built strong partnerships with big OEMs like Paul
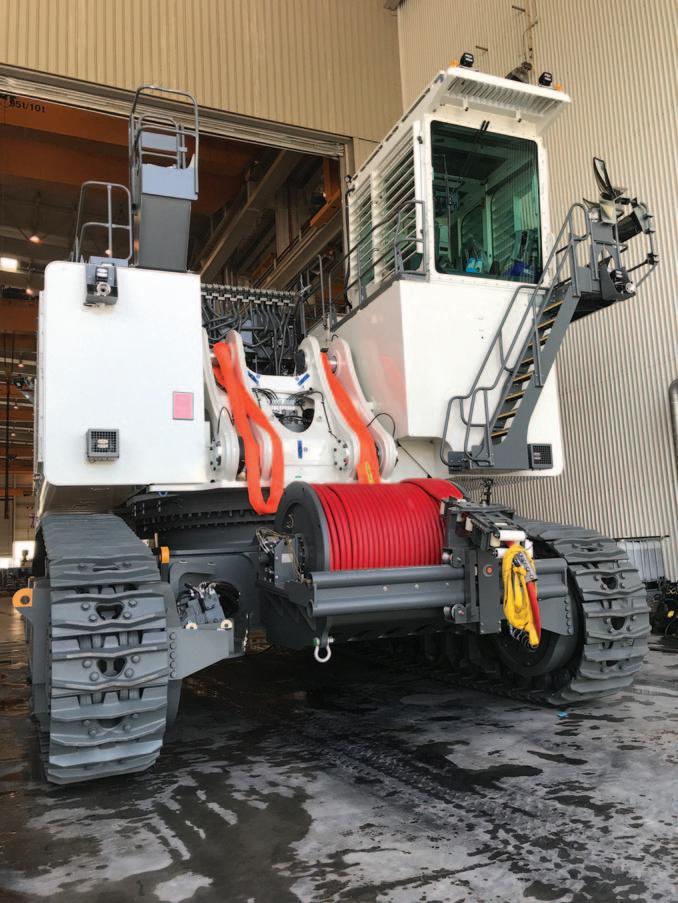
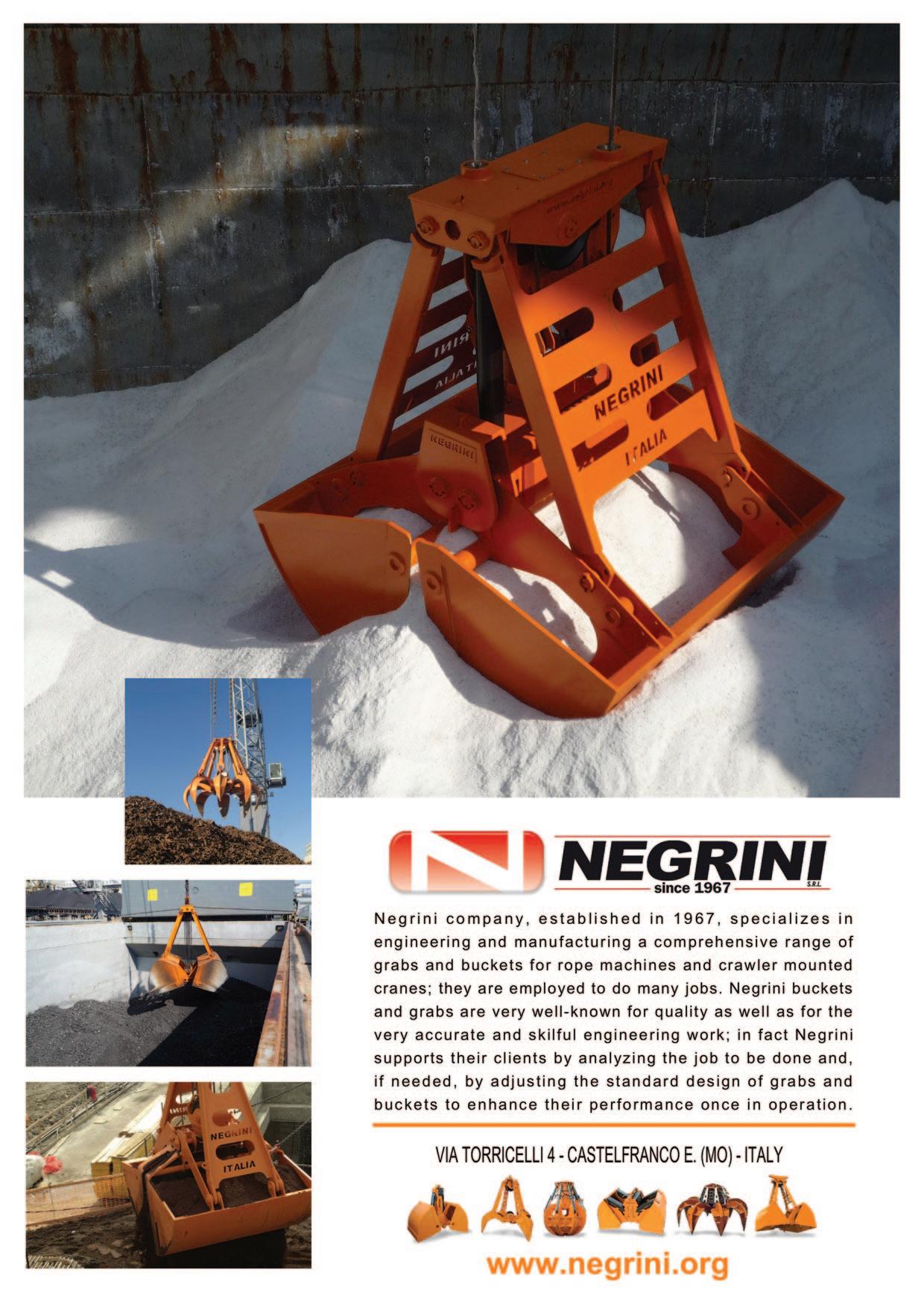
Material processing through coal crushers ‘crushing’ material in rail wagons. wagon pusher reliably supplied with energy via motor-driven cable reel.
Conductor rail systems for power supply of wagon pushers
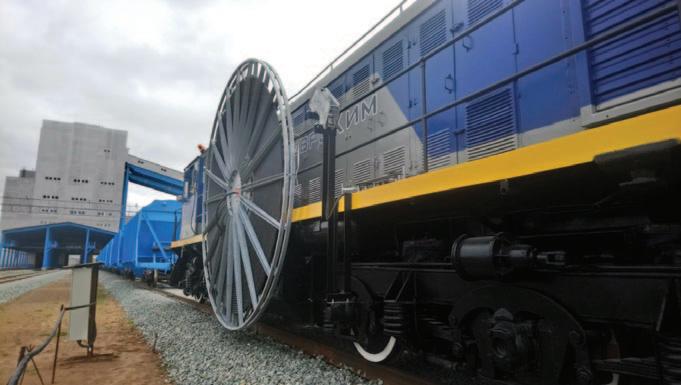
Wurth, Thyssen Krupp Industrial Solutions, SMS Group (just to name a few) with regular supply and continuous service of cable reeling systems among other solutions.
Experienced people can customize solutions according to individual requirements and adapt standard

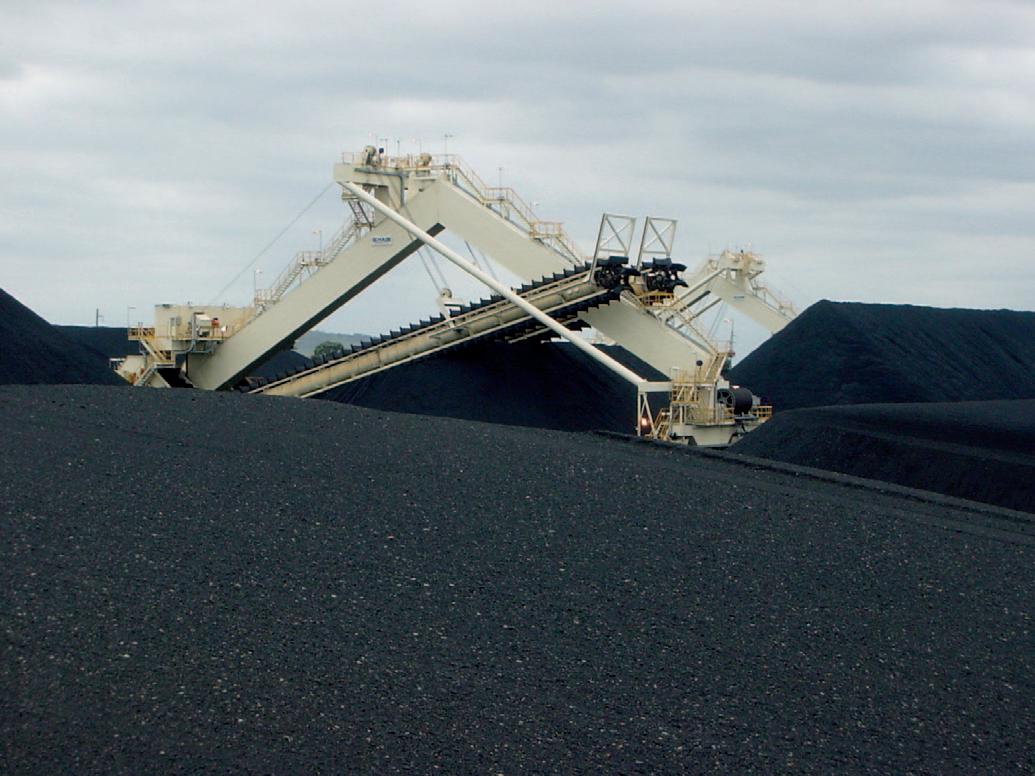
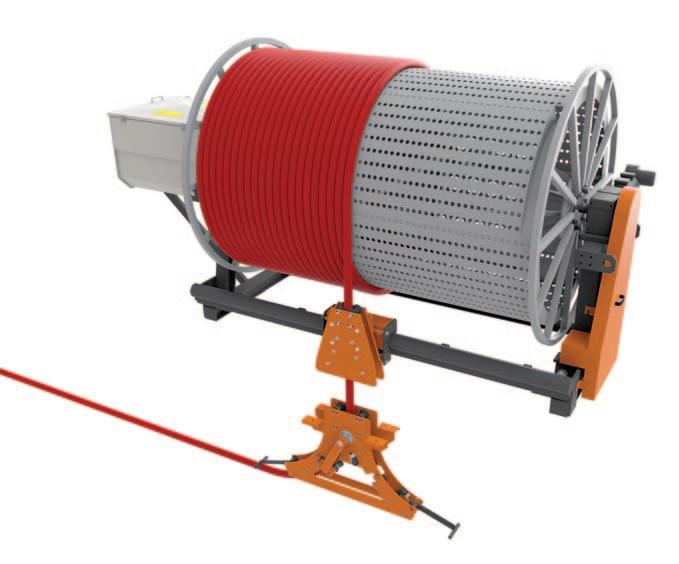
solutions to any further needs with advanced designs and efficient, highquality manufacturing at ConductixWampfler’s specialized facilities. Thanks to a global presence and experienced sales and service network the company is the partner of choice for OEMs as well as endusers to support their production maximization and improve material transportation’s efficiency.
Motor-driven cable reeling systems ensure a reliable operation of shiploaders at Ha Tinh plant in Vietnam. Conductix-Wampfler’s new ARGO level wind reeling system with rigid chassis and drum, guiding devices, anchoring devices, HV+LV+FO connection boxes and a wide choice of drives.

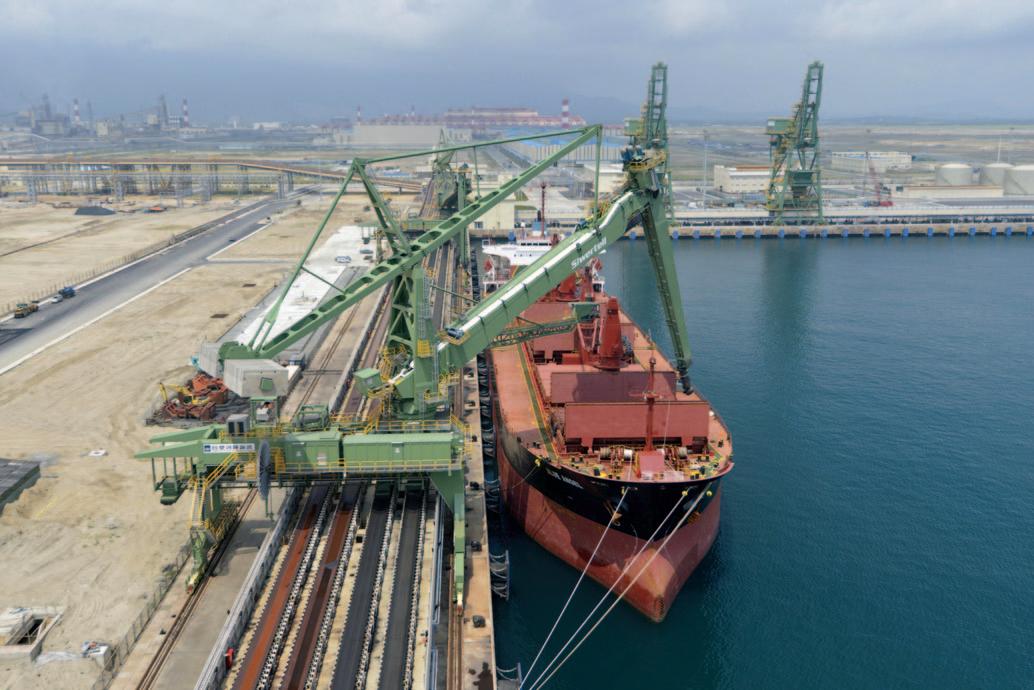

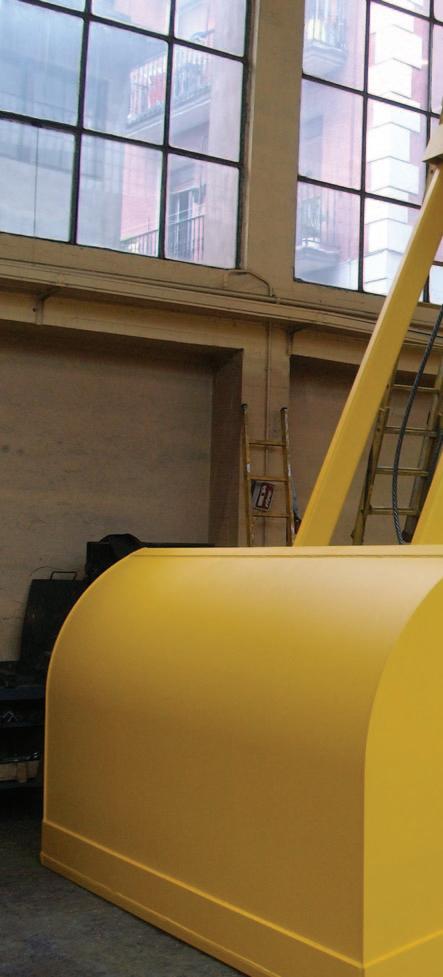
Since it started operating in 1965, BLUG has been a world-renowned for the design and manufacture of industrial handling equipment — such as orange peel grabs, clamshell grabs and tongs with their different working mechanisms, hydraulics, electro-hydraulics and mechanics.
BLUG machines are designed to guarantee a long useful life and low maintenance costs, being able to work in the most adverse and repetitive conditions.
The company offers an excellent aftersales service of repair and maintenance of the machines both nationally and internationally. In addition, it offers spare parts in a very short period of time.
MARKET CONSOLIDATION As mentioned above, BLUG is known not only for its longevity in the industry, it is also renowned for the quality of its R&D activity, which has been a key part of its work. Its focus on R&D has enabled it to remain up-to-date with all the latest developments relating to new technologies, new designs, improvements in manufacturing materials, etc.
All this and the experience gained by the company itself over the years has made the end-user bet on BLUG products during all these years.
WHO ARE BLUG’S PRODUCTS FOR? BLUG’s products are focused on sectors such as coal handling, agriculture, construction, recycling, iron and steel, cement and port, with customers ranging from a small engineering company to a manufacturer of overhead cranes, logistics services, end customers, etc...
RECENT TECHNOLOGICAL DEVELOPMENTS: GIITS SYSTEM The wireless GIITS system (Grab Intelligent Interface and Transmission System) enables secure, real-time communication between the orange peel grab/clamshell grab and the crane’s PLC. It consists of a transmitter/receiver assembly to simplify wiring and improve the quality of operating information, opening the door to possible automation.
The main advantage of GIITS technology is that automation of manipulators is made much simpler and cheaper. It even opens the door to the modernization of equipment that does not have the necessary electrical wiring in the reel.
FUNCTIONALITIES v orange peel grab/clamshell grab and/or crane signal collection; v configuration and basic display of signals; v interconnection of signals from different equipment wirelessly (Master-Slave); and v interconnection with DIGITAL BLUG.
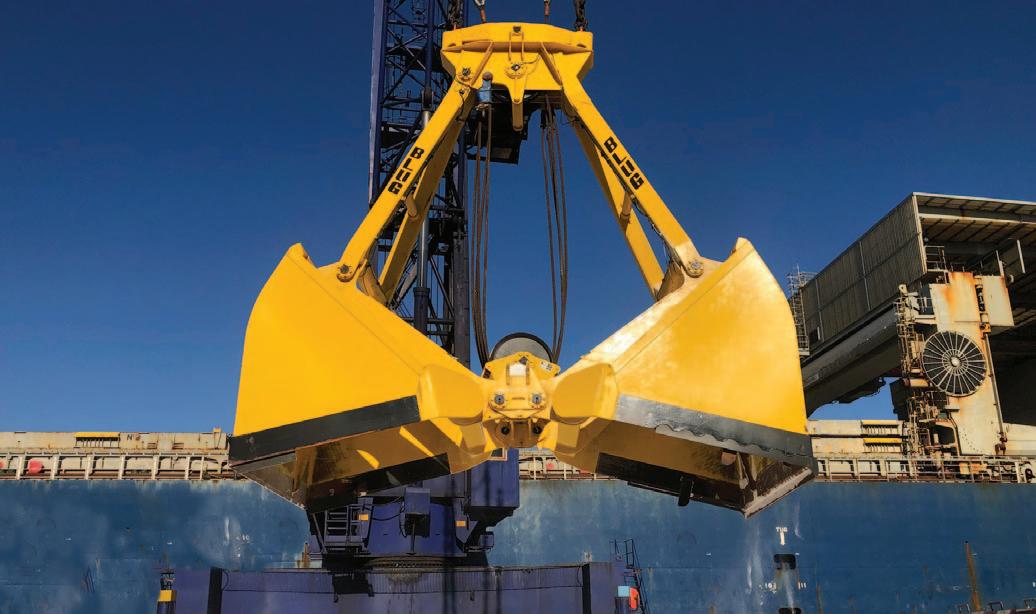
SPECIALIZED IN COAL HANDLING Coal represents a significant volume of the bulk product handled in ports; historically, it’s been one of the star materials more usually handled by grabs and therefore, grab solutions have suffered a continuous evolution and specialization to improve this material’s loading cycles.
Based on a 0.8–0.9 T/m3 average density, the Blug range for coal handling offers a wide variety of options depending on the crane and capacity requirements. The key factor to obtain a fast return of investment for this kind of applications is to optimize grab’s capacity/self weight ratio and offer the highest lifetime versus purchase, start-up and maintenance costs.
The C4, CV2 and CM4 grabs are the most representative models of Blug clamshell grabs for coal and bulk handling applications.
RECENT COAL HANDLING PROJECTS In terms of coal handling deliveries during 2021, BLUG supplied a 13m3-capacity rope-operated clamshell grab for a Romanian port and two 20m3-capacity rope-operated clamshell grabs for the Spanish market.
Currently, ten more four rope grabs are being tendered for different international ports.

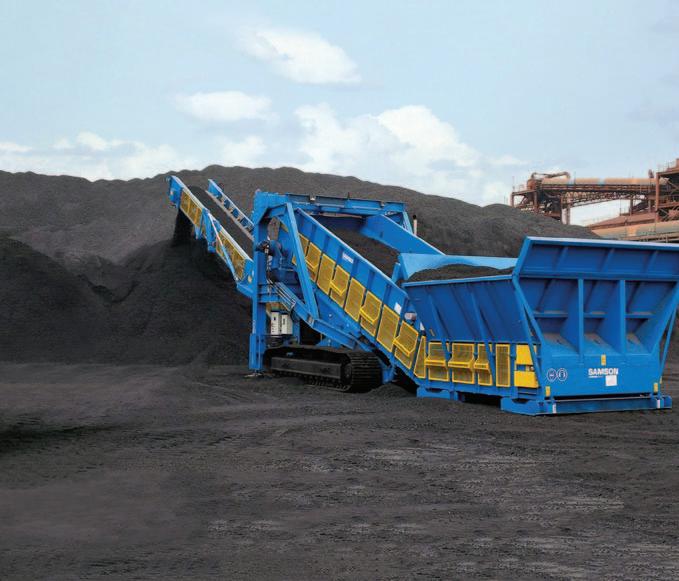
STORMAJOR® application prevents spontaneous combustion in coal stockyards
In cooperation with AUMUND Asia (H.K.) Ltd (China), responsible for the Asian Sales Area, SAMSON Materials Handling (AUMUND Group) has recently supplied a STORMAJOR® 2.0 to a Japanese company for the handling of coal at its chemical plant in Indonesia. The site, located in Banten province, is a specialist manufacturing facility producing various chemicals for the global supply chain. Coal is delivered by seagoing vessel, then it is offloaded and stored in the facility directly. During storage, the coal can spontaneously combust due to its quality. The STORMAJOR® designed and delivered by SAMSON manages the continuous in- and out-loading of the coal, whereby the coal is cooling down and hot spots will be avoided.
The situation before: in 2018, a coal fired power plant was opened to support the chemical manufacturing operations. This 2 x 151 MW facility is located on the periphery of the production plant with its own covered coal stockyard. The environmental conditions, if not ideal, can cause hot spots of burning fuel. These hot spots, if left untreated, can spread, resulting in a potentially dangerous situation and a loss of usable product. To combat this, the operating company has been using a combination of excavators and dump trucks to move the coal out from the covered storage area to an external uncovered stockpile. Once the coal has cooled down, the reverse process occurs and the excavator loads a dump truck to take the material back into the covered area before another excavator manoeuvres the material back onto the covered stockpile. This movement, along with manipulation from an excavator on the external pile allows any hot spots to be dealt with.
Prior to the purchase of the SAMSON STORMAJOR® 2.0, a number of excavators and dump trucks were being used to move the material, this double handling was time consuming and tied up a lot of resources. They identified a need to simplify this process and worked with AUMUND Asia and SAMSON on providing a simple, cost effective and reliable solution, a STORMAJOR® 2.0.
The situation today: after detailed review by SAMSON product specialists, a track-mounted, self-powered, 450 series STORMAJOR® with a 27m boom was selected. The STORMAJOR® could be positioned with the reception feeder inside the facility and the boom outside allowing the excavator to load the material transported outside directly onto the coal pile. Keeping the STORMAJOR® in place and turning the machine around, it could subsequently feed cooled coal back inside onto the covered stockpile. The versatility of this machine allows the company to reduce the number of truck movements and the number of personnel needed in the coal facility, thus reducing operating costs, increasing material yield and improving operator safety.
The STORMAJOR® is the Samson® Material Feeder combined with an outloading boom conveyor, which can slew and luff. The feeder and boom are combined into a single mobile machine. Mobility is achieved via self-powered tracks for uneven terrain or wheeled units designed to be towed. Three different types are available on the feeder section to enable the handling of light to heavy bulk materials. The modular outloading boom can be up to 27m long and achieves stockpile heights of over 11m.
Dust control can be achieved by fully enclosing the material feeder and belt conveyors then employing integral filter units mounted on the feeder and boom. In addition, for certain applications a telescopic discharge chute can also be fitted to the boom to allow dust free loading.
The feeder is able to accept material delivered by numerous methods such as a front end loader, tipping truck, mining dump truck, grab and excavator. This makes the STORMAJOR® a truly versatile machine with various applications including stockpiling, barge or ship loading, rail wagon loading, transfer or emergency material feeding.
ABOUT THE AUMUND GROUP The AUMUND Group is active worldwide. The conveying and storage specialist has special expertise at its disposal when dealing with bulk materials. With their high degree of individuality, both its technically sophisticated as well as innovative products have contributed to the AUMUND Group today being a market leader in many areas of conveying and storage technology. The manufacturing companies AUMUND Fördertechnik GmbH (Rheinberg, Germany), SCHADE Lagertechnik GmbH (Gelsenkirchen, Germany), SAMSON Materials Handling Ltd. (Ely, Great Britain), TILEMANN GmbH Chains & Components (Essen, Germany) as well as AUMUND Group Field Service GmbH and AUMUND Logistic GmbH (Rheinberg, Germany) are consolidated under the umbrella of the AUMUND Group. The global conveying and storage technology business is spearheaded through a total of 19 locations in Asia, Europe, North and South America and a total of five warehouses in Germany, USA, Brazil, Hong Kong and Saudi Arabia.
Example of a STORMAJOR® 2.0 operating in an outdoor stockyard for coal (photo: SAMSON Materials Handling).
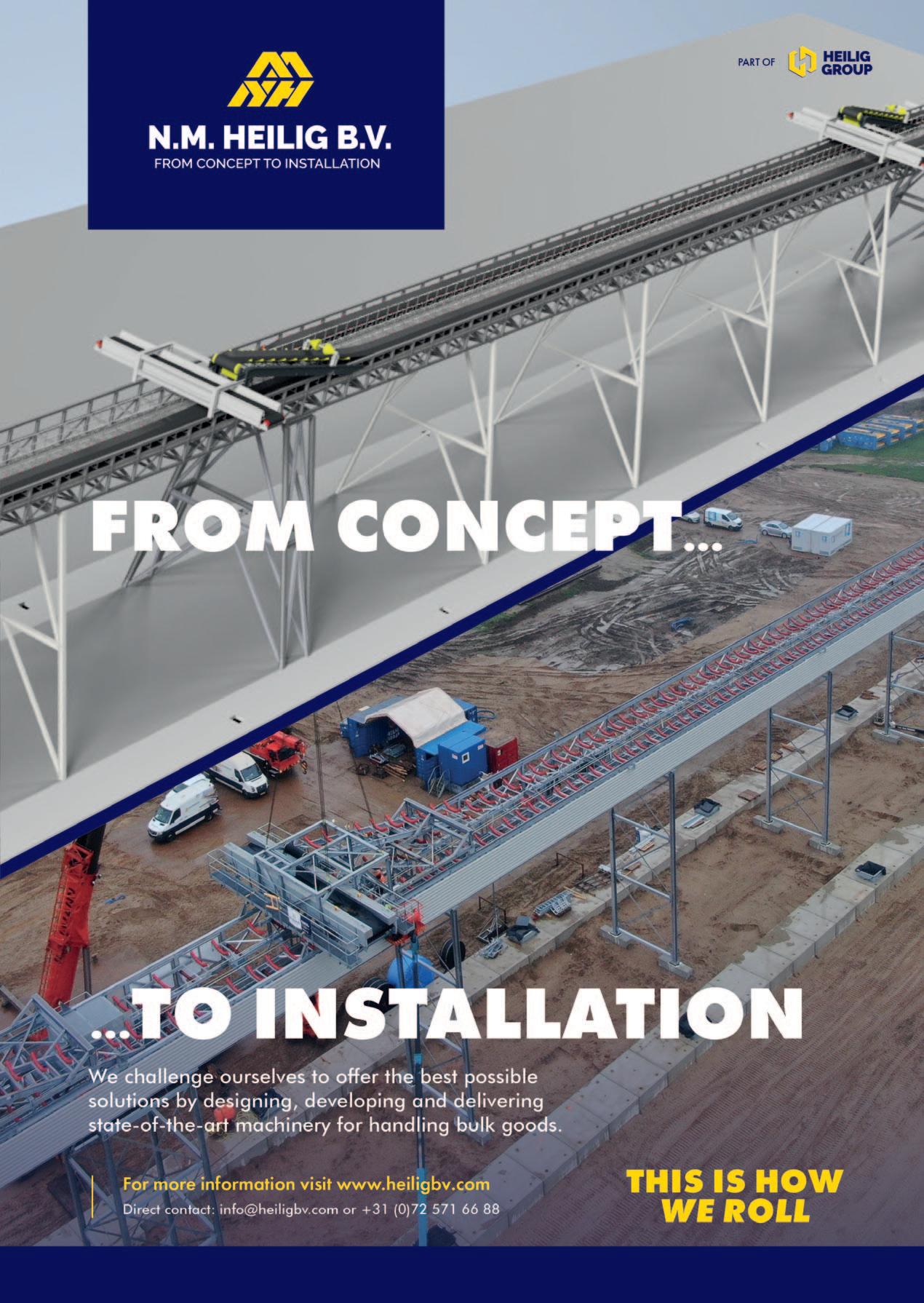
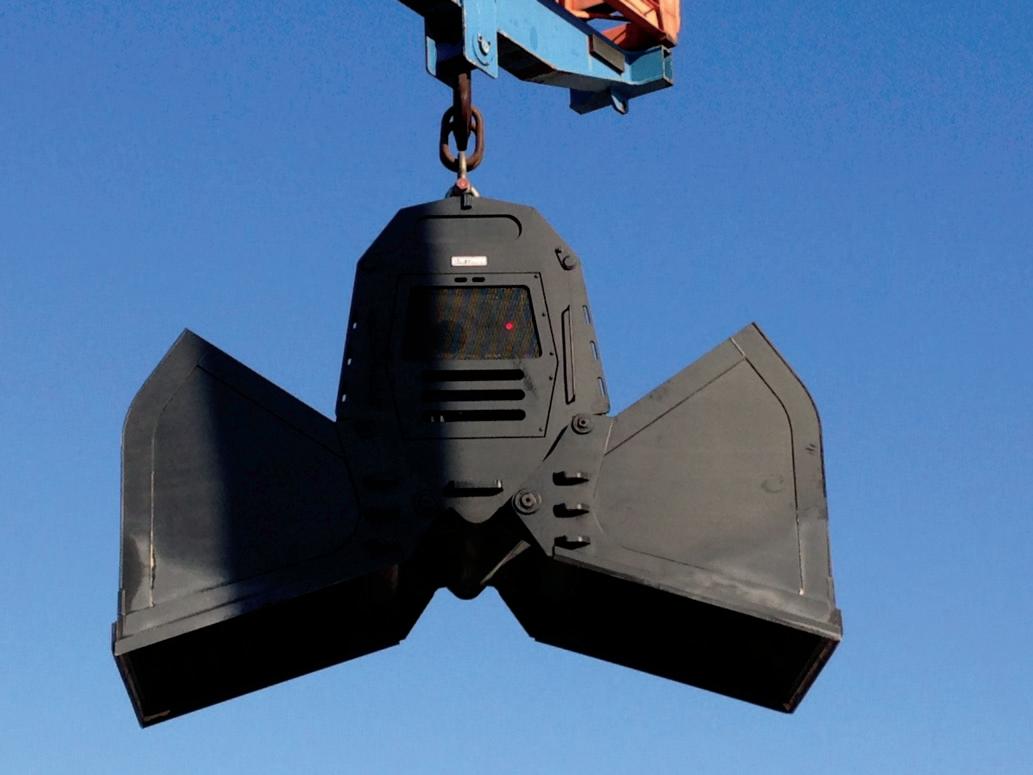
Bateman Manufacturing was established in 1989 Barrie, Ontario. Since then, Bateman has become renowned within the industry for material handling attachments both domestically and internationally.
“Coal is the second largest, in terms of trade volume, dry bulk commodity, behind iron ore, transported by sea accounting for about the 25% of the world dry bulk trade” — Open Sea Blog. Coal is one of the most important resources as it supplies approximately 36% of global electricity worldwide, it’s of the utmost importance to secure coal without delay to prevent costly problems. That is where Bateman Manufacturing comes in; its large clamshell bucket is able to effectively and efficiently load coal at cargo ports.
Bateman clamshell buckets provide an ideal solution for re-handling, digging, and loading. Its hydraulic clamshell buckets come in light, medium, and heavy-duty models with either open or closed back designs. All of its clamshell buckets come equipped with severe-duty rotator with continuous 360° rotation and internal hydraulic relief. All these enhancements allow for an increase in productivity and efficiency when used for port applications
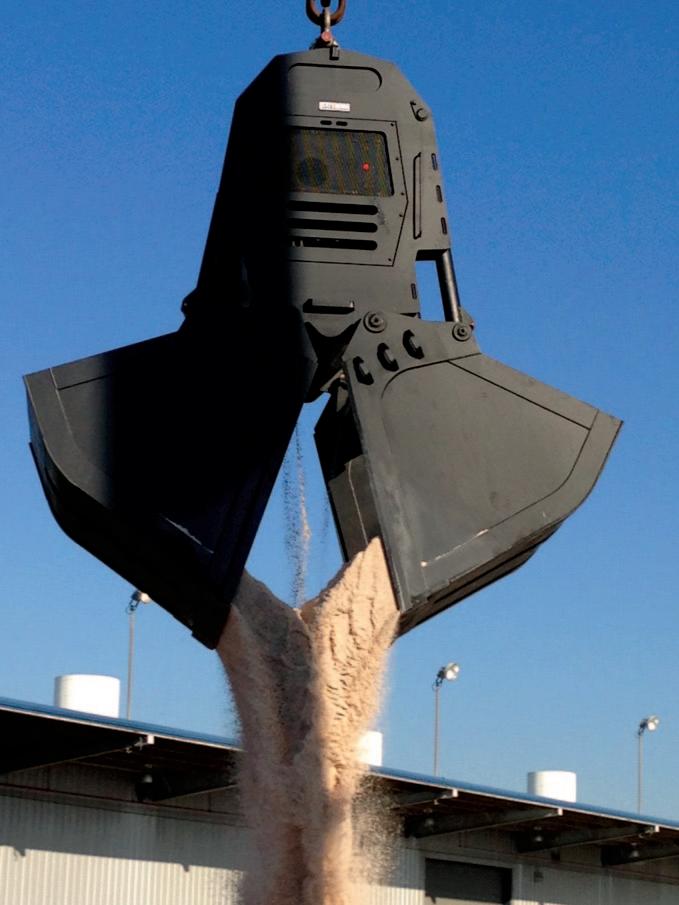
such as loading coal.
Bateman uses a range of strategies to remain competitive, including: offering a client-oriented experience; increasing its brand awareness; and continuing to innovate its products. Bateman aims to fundamentally transform the material handling industry into a customer-driven experience, fuelled through the needs and challenges of the global market.
Increasing Bateman’s brand awareness by staying relevant in the physical and digital world is an essential part of its business model. By attending the biggest tradeshow events and continuing to appeal to its audience with content of its products on social media, Bateman hopes to attract customers all over the world. It believes that it is imperative to be known and seen worldwide as a trusted brand and manufacturer of high-quality products. Finally, Bateman strives to innovate. With the help of its expert engineer team, it continues to optimize its product line to stay up to date on new technologies being developed. Bateman’s goal is to keep up with trends in the industry and stay at the peak of innovation to provide the best products to its clients and customers.
Bateman works towards developing technologies to simplify material handling for its clients. Its large hydraulic clamshell bucket is self-contained, remote-operated, and diesel driven. By continuing to enhance its products, it hopes to not only simplify its clients’ jobs but save them time and money by increasing machine productivity. Bateman supplies material handling attachments to large stevedore port companies all over the world. Its latest project is manufacturing a large 25-yard clamshell for shiploading.
While Bateman offers material handling for port applications, it also manufactures a range of other attachments that are vital to many industry sectors. Whether it’s a contractor grapples for demolition; orange peel grapples for recycling, log grapples for forestry, and rail grapples for railway, Bateman covers what is needed in all sectors. It does so because it wants to provide its 30+ years of experience manufacturing top quality products to its customers in whichever industry they specialize in.
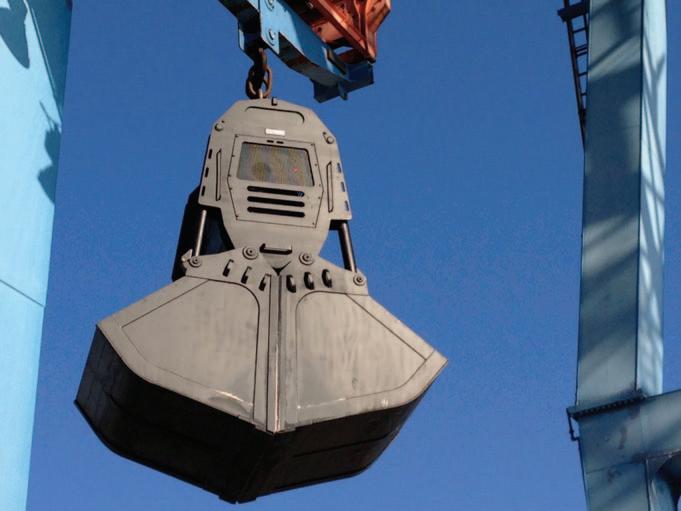
RELIABLE INTERNATIONAL TRADE - OIML CLASS 0.2 (+/- 0.1%)
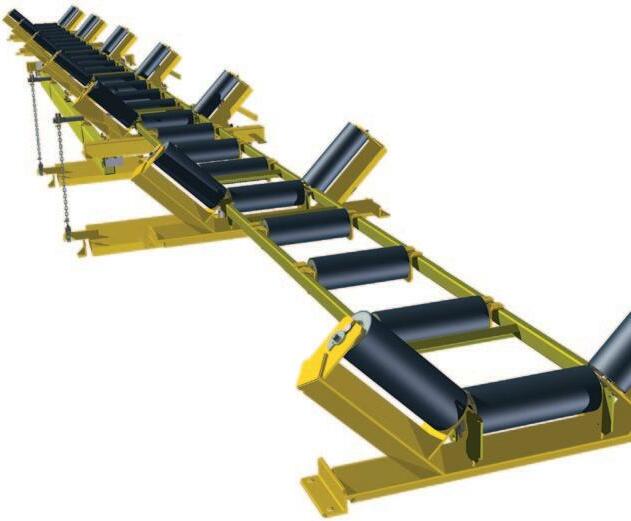
Features
High precision fully suspended weigh frame
Direct force measurement (no lever arms, pivots or bearings)
Strong rigid beams
Low deflection design 4 load cells 3 or more idler weigh length
Extended Idler Spacing for improved performance
Close Spaced Roller Rack (CSRR) for reduced belt sag and reduced belt dynamic effects (Protected by International Patents)

E: sales@controlsystems.com.au T: +61 1 300 784 449
+ Subscribe to Newsletter
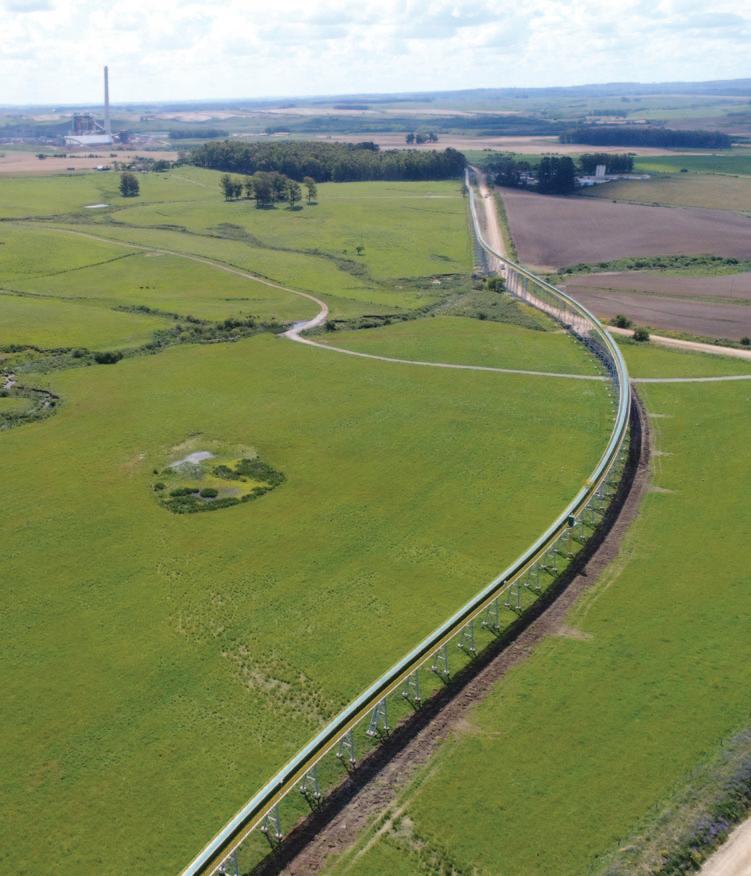
TMSA - Moving Technology was founded in 1966 with 100% state capital. The company has consolidated itself in recent years as one of the main MERCOSUR suppliers for port terminals and equipment for long-distance bulk and solid handling. Defying the crisis, TMSA was selected by Amanhã magazine as one of the 50 most innovative companies in southern Brazil. TMSA has a highly capable team of professionals, which means it is able to develop unique solutions to provide quality equipment and show its expertise and competency in different markets.
One of its recent developments is its innovative system for handling and transporting coal in Brazil at the Pampa Sul Thermoelectric Plant in the city of Candiota/RS. This is considered one of the largest tubular conveyor belts in Brazil, at 4.17km long and offering a coal transport capacity of 550 tonnes per hour.
This turnkey project includes: the design; civil engineering; manufacturing; testing and environmental management; environmental recovery required for the IBAMA system operation licence; and control of the drive system by means of state-of-theart medium voltage inverters with load sharing and automation. The project has a lighting system that uses autonomous LED lighting fed by integrated photovoltaic solar panels, ensuring pollution-free, silent energy from renewable sources, easy installation and low maintenance. In an increasingly competitive mining market, where the pressure to reduce costs and increase productivity is ever more decisive, TMSA’s team has the expertise to seek and create the most costeffective and innovative solutions for customers. Fifty-four years after its creation, TMSA has gained vast experience and a strategic will to focus on improving the profitability of its customers and, in addition to greenfield projects, has also started to provide support and modern solutions. Its customers already have industrial facilities (so-called ‘brownfields’) through the assignment of its highly specialized engineering teams. TMSA remains at the forefront of bulk solids handling and long-distance equipment.
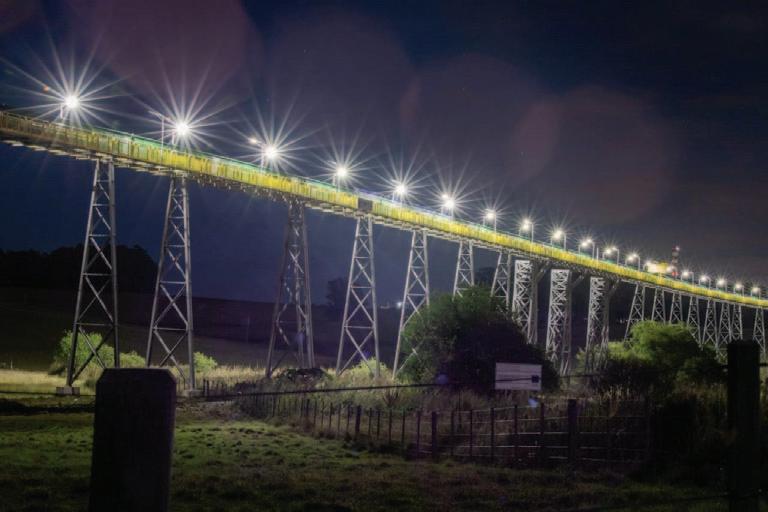
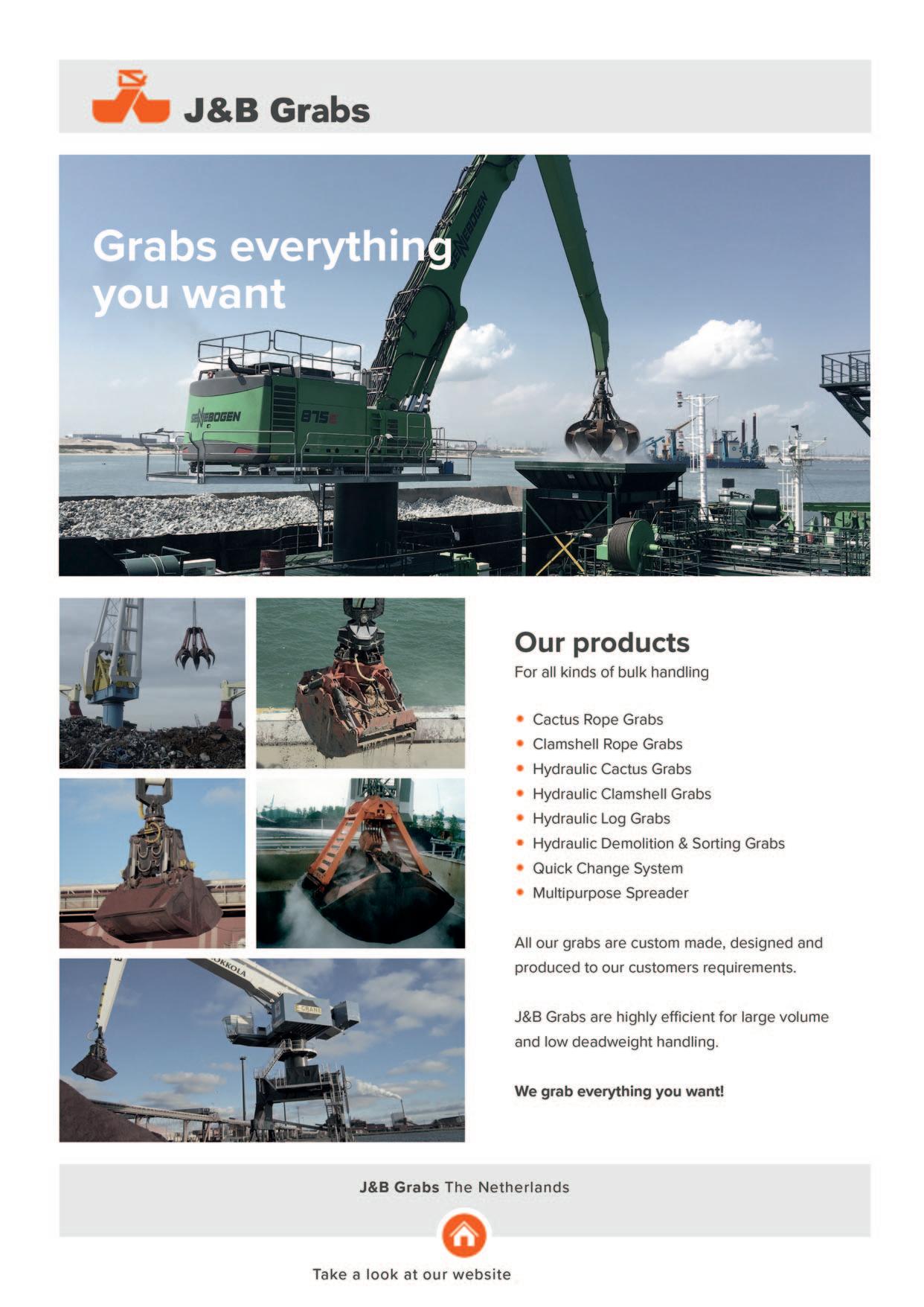
ABOUT DELLNER BUBENZER
DELLNER BUBENZER is globally renowned for the design and manufacture of braking systems. Its high-quality braking equipment offers customized stop-action solutions for a wide variety of industries from sea to sky, and everything in between. For decades DELLNER BUBENZER products have been recognized worldwide as innovative braking solutions that are precision engineered to meet the highest quality standards.
As a multinational global company, DELLNER BUBENZER is also a local partner with manufacturing facilities located in Sweden, Germany, Poland, Italy, Denmark, Czech Republic, India, USA and China, as well as sales and service divisions in Holland, Singapore, Malaysia, Dubai, Brazil and Argentina.
DELLNER BUBENZER manufactures a range of industrial brakes and brake-related products like storm brakes (rail clamps and rail brakes, wheel brakes), monitoring systems, couplings, brake discs, hydraulic power units and safety systems to protect the steel structure of the machine against overload and snags.
DELLNER BUBENZER’s multinational manufacturing capabilities across the world, paired with local impact under one united front, strengthens DB’s loyal customer base. Furthermore, due to the continuous development of the product line and the service network, the customer base is continuously growing.
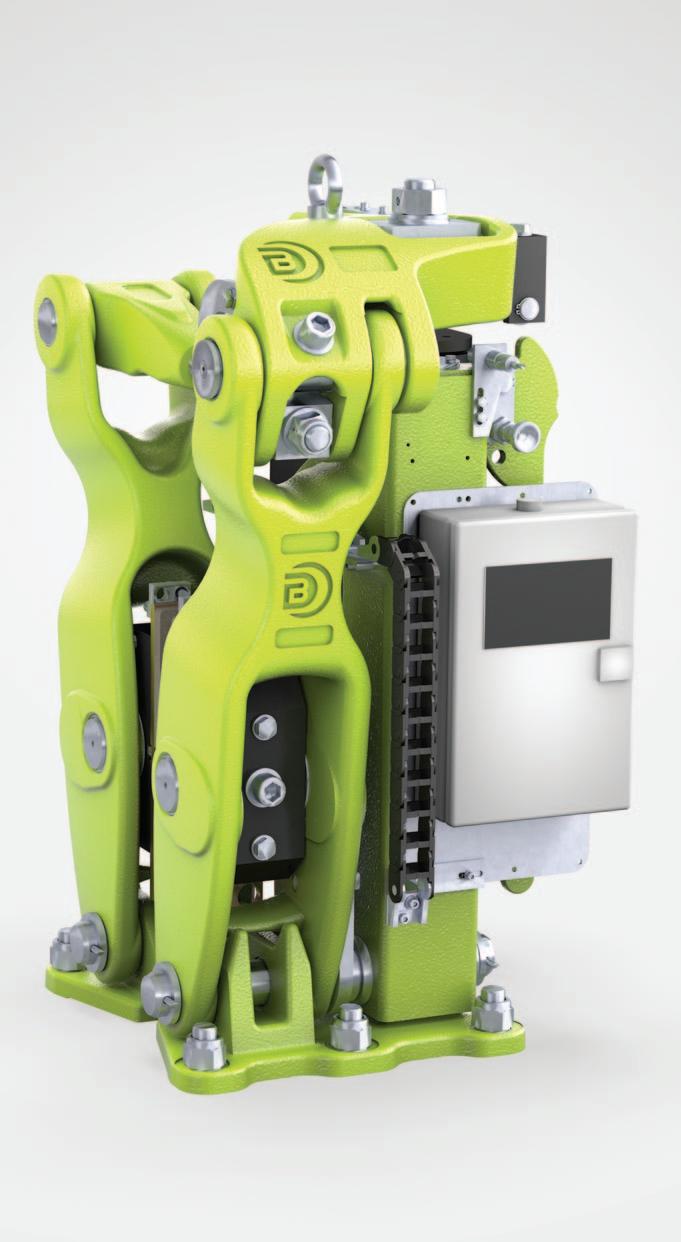
QUALITY PRODUCTS Most of the parts are made in-house on new CNC machines, with production in the company’s different facilities. Furthermore DB runs one of the biggest dyno stands for industrial brakes in Europe. All brakes are put through their paces before they are released to the market. When it comes to quality standards DB runs a final check with every brake leaving the factory. In addition, the company works with its quality assurance and development team to constantly optimize its products. In its own development centre, DB has one of the largest test benches in Europe, where it puts the existing product range and all new developments through their paces. Compliance with its own quality requirements has the highest priority, which is reflected in the longevity of the products.
DB’s Torque scales are exactly calibrated. DB is one of the very few companies that is able to provide both brakes and thrusters. This means that the set-up of the brake matches the thruster’s capabilities exactly and vice versa. Since DB has the ‘strongest thruster’ in the market, brake performance is far better than with conventional technology.
DB is not only a brake manufacturer, but also a system supplier, for example safety systems to protect huge steel structures against overload, monitoring systems and more.
The company’s internal global service team also receives regular training. In addition, DB also offers external training at its customers’ sites, so that employees learn how to use its products in the best possible way. Throughout the new DB has continued to maintain sales and service in the challenging environment of the Covid-19 pandemic. To help support customers remotely, DB has been making use of VR glasses. These are connected
CMB box mounted on a thruster disc brake. ENGINEERING & EQUIPMENT
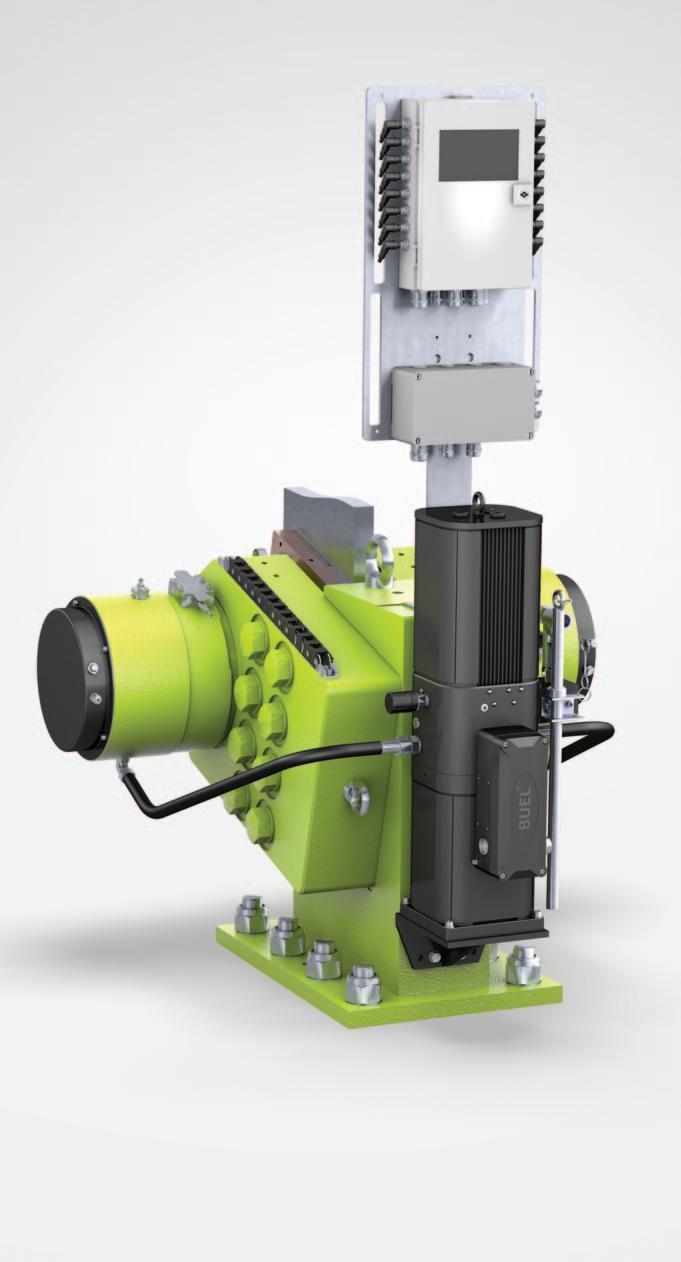
glasses that link personnel to DELLNER BUBENZER experts over the internet. The DB service team can look at the application, its monitoring system and the brakes directly and guide staff through the necessary maintenance and repair steps.
CUSTOMERS DB’s customers include all well-known OEM for huge equipment like conveyors, ship- (un-) loaders, stacker, stackerreclaimer, bucket wheel excavators, ball-, SAG and AG mills, process equipment etc., but also end-users like huge mines and bulk terminals worldwide. Coal is just one of the many commodities kept in control by systems from DB.
DELLNER BUBENZER CASE STUDY
In this case study, DELLNER BUBENZER recently supplied brakes for three gearless conveyor systems with an installed capacity of 2 x 5,500kW each for 7,100 tonnes per hour for a copper mine in Mongolia.
The scope of supply was including floating calliper brakes SFR50, brake discs, hydraulic power units, UPS, BCC3000 closed loop control systems as well as the complete encoder technology. The main parameters of the brake like pad wear, stroke (air gap) and brake pad temperature are continuously monitored.
The brakes stop the conveyor within 10s in loaded or unloaded condition. Depending on the parameters, like load, speed etc., the HPU and control unit provide different braking levels and scenarios. The controlled braking process minimizes the conveyor belt tension and reduces stresses in the connected equipment. The system is also able to perform the pre-programmed ramps and stopping curves after a power outage.
Redundant controls and HPUs guarantee highest system availability. The environmental conditions need a compact set-up of the brake units. The spring applied, hydraulically released, fail-safe brakes are able to equalize axial movement of the connected shafts.
VISUALIZING AND MONITORING OPTIONS Communication between main PLC and BCC3000 goes via PROFIsafe protocol integrating the relevant safety features while also monitoring the subfunctions.
In summary, DELLNER BUBENZER’s products offer a safe and durable braking solution.
NEW PRODUCTS In January DB launched its new disc brake SB28.5. This brake is one of DB’s first brakes, which it has been building since 1980, and which is constantly technically developed.
With this model, DB has also set new market standards in combination with its own thruster, the BUEL. Sustainability is a driving force in development for DB, with the combination of the SB 28.5 with the BUEL® thruster.
This is an important development for braking systems that consumes less energy with a fast-closing time. Beyond sustainability and energy saving, the SB 28.5 brake presents the significant advantage of less maintenance.
This new braking system underscores DELLNER BUBENZER’s commitment to uphold our pioneering reputation and deploy the latest in technology to mirror what market needs, and its clients deserve. And DB’s customers can look forward to great new developments this year.
CMB3 box mounted on a SF brake.
PSB Inspection was established by Peter Bagchus, CEO and owner, in 2017. Since that time, the company has grown organically and is now financially healthy and very successful.
The company operates from its head office in Vlaardingen (Rotterdam port area). It has highly qualified and experienced senior surveyors and an experienced sampling preparation team. PSB Inspection runs its own laboratory with highly qualified and experienced laboratory technicians which is all managed by the operational team in close conjunction with the management team members, who have been active in this type of business for decades.
Currently, PSB Inspection focuses primarily on coal and coal-related products. However, bearing in mind that the world — and the energy market — is changing vastly and rapidly, it is also working hard to expand into markets such as biomass, alternative fuels, minerals, metals, slag, flyash and fertilizer, which are under development in different phases.
This all takes place with a clear eye on high quality services in the field of inspection, sampling, sample preparation, analytical services and weight ascertainment required by PSB Inspection’s customer base. Recently, the company expanded its service portfolio with gas/toxin measurement (four qualified and certified gas/toxin measurement experts including high quality, certified equipment. More expansion is in the planning.
Other than Europe, PSB Inspection is able to offer its services in various other countries (Russian Federation, Turkey, UK, LATAM) as well and expanding its country portfolio. All is being coordinated from its head office, obviously under the applicable ISO standards 9001 and 17025. Certifications to 17020 and GAFTA are on the way. DCi
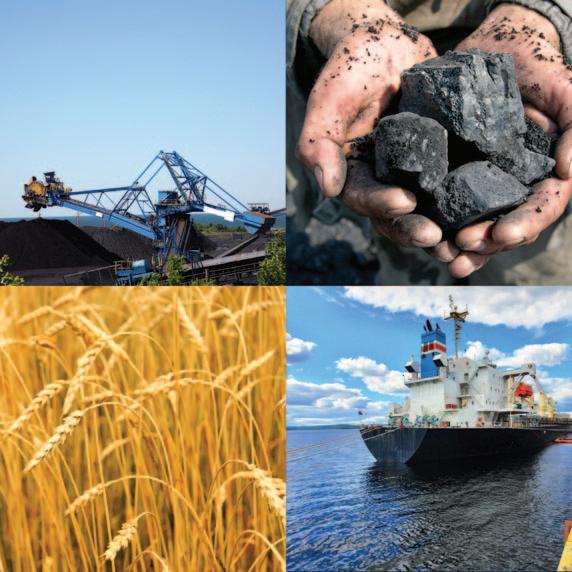
EVOLUTION STARTS WITH A PIONEER
INTRODUCING THE SB 28.5 DISC BRAKE

As a result of decades of engineering, evolution, and innovation, the world’s leading supplier of brakes and related power transmission debuts the SB 28.5. Distinguishing features include:
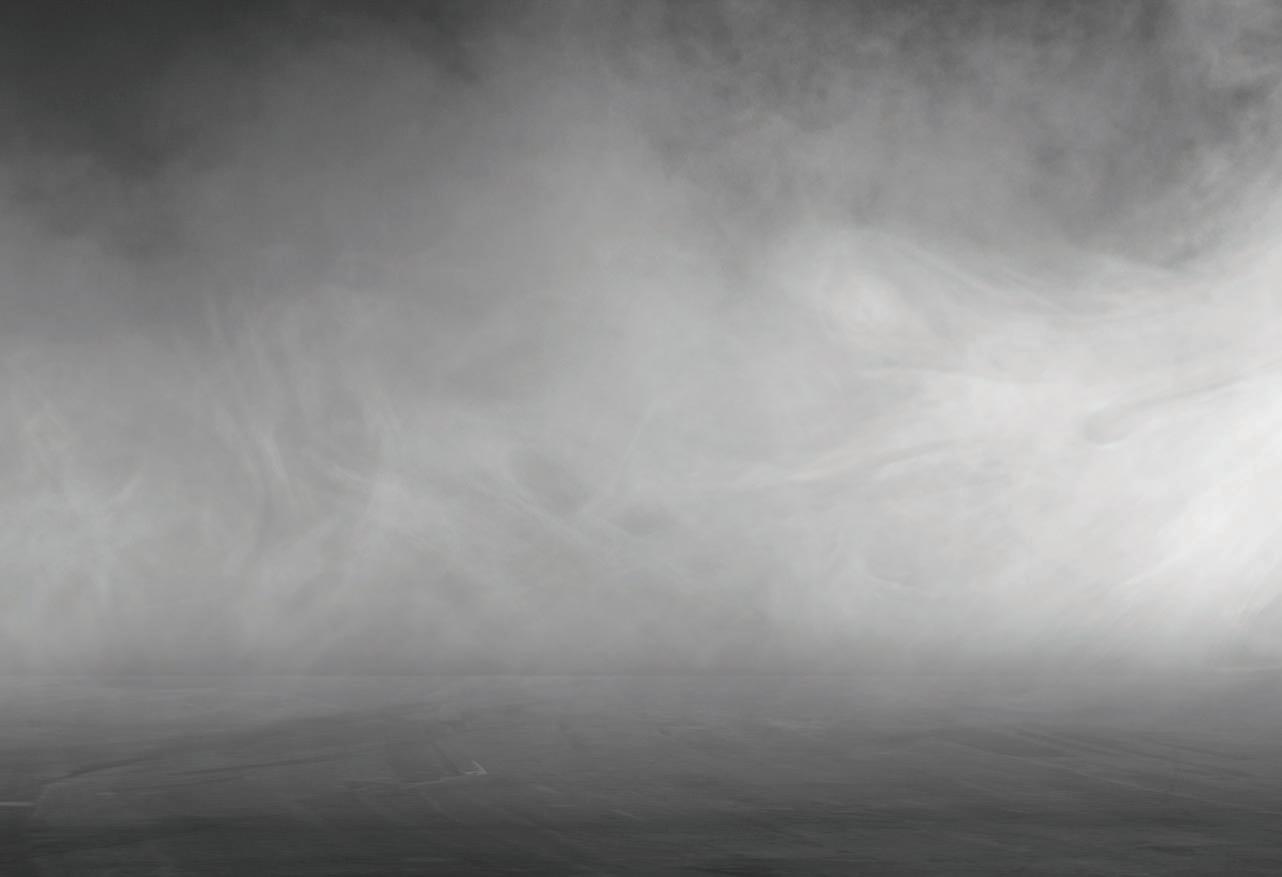
Increased Sustainability Enhanced Design Automated Wear Compensation Improved Self-Centering System Enhanced Parallel Alignment System
Powered By
