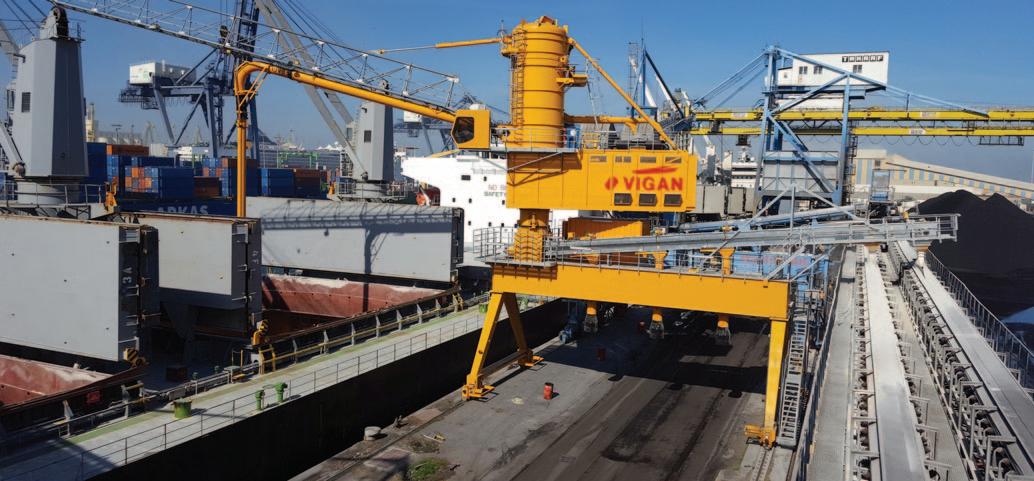
3 minute read
The enduring benefits
of continuous ship-unloaders
Pneumatic unloaders respond to greater cargo demands: Vigan explains
Growing demand for grain storage solutions and silos with larger storage capacities is translating into bigger demand for pneumatic unloaders.
Increased capacity and speed are the main reasons why larger-sized equipment is required for unloading increasingly large vessels. At the same time, minimizing dust emissions, grain spillage and noise pollution are important considerations in the design of the unloaders.
Progress in design is occurring rapidly, giving ports and terminals wider choice for handling free-flowing agribulk cargoes such as grains and meals, animal food pellets, chemicals and wood pellets.
For other cargoes, both mechanical and pneumatic unloaders can be fitted with optional devices to ‘fluidize’ the cargo before being lifted, such as cutting nozzle or screw accessory equipment.
Mechanical unloaders may have the edge in terms of speed, perhaps 200tph (tonnes per hour) up to 1,200tph, compared to 200tph up to 800tph per pipe for pneumatic unloaders. However, the pneumatic types have versatility — they can work on most quays and handle ship-tobarge transfers etc.
With a ship-unloader’s lifetime of about 30 years, it is essential for the customer to make the right choice of equipment. Vigan’s Commercial Director, Dirk Janssens, confirms progress in pneumatic technology has been so great that ten pneumatics are now sold for every mechanical unit. “This is the case for Vigan, but it must also be true for the whole market — for grain and agribulk at least. It is different for cement, iron ore and coal,” he states.
The three most critically important features to compare pneumatic and mechanical unloaders are efficiency, power consumption and investment cost. Pneumatic unloaders have a higher efficiency which means a higher ratio between the average capacity (which really matters to the operator), divided by the peak or nominal capacity.
Nicolas Dechamps, Managing Director of Vigan explains further: “The main reason for such higher efficiency is that the pneumatic unloader is sucking everything up to the bottom of ship. No grain remains in the suction nozzle. As a result, the total time to discharge the vessel ‘berth in –berth out’ is shorter compared to the same situation with a mechanical unloader of the same capacity.”
He further explains that for any type of mechanical unloader (chain, screw, doublebelt type, or even grab cranes), it is necessary to have the bottom of the vertical leg and its feeder buried in at least one metre of product to keep a high unloading capacity. “The last layer of cargo in the bottom of the hatch needs much more time to be discharged with a mechanical unloader, making its efficiency lower than the pneumatic unloader.”
In terms of power consumption, he says mechanical unloaders (chain, screw, doublebelt) have a lower nominal energy consumption at full capacity ranging from 0.3kWh/t to 0.8kWh/t.
Pneumatic unloaders have managed to reduce their consumption to lows of about 0.7kWh/t due to reducing the number of elbows in their pneumatic lines, using a multi-stage turbo blower instead of an oldfashioned roots-type blower and the use of inverters for the drive of the turbo blower unit (allowing power consumption to be regulated automatically according to power required).
However, the higher efficiency of the pneumatic unloader outweighs its higher electric consumption by a factor of ten in terms of costs.
With respect to investment cost, Dechamps says the pneumatic unloader is significantly cheaper to buy. “Other factors have to be taken into consideration: extra cost of quay construction or quay refurbishment due to higher weight of mechanical unloader compared to pneumatic unloader. Transport costs are notably high as mechanical unloaders are usually made in Far-East countries and transported on expensive heavy-lift vessels, with all downstream equipment (conveyors, elevators) having to be sized according to the nominal capacity of the unloaders.”

Financial analysis shows that the pneumatic unloader remains globally the most economical solution and that the extra small power consumption is largely compensated by lower investment costs and its higher efficiency.
Pneumatic unloaders also appeal due to easier maintenance (a pneumatic unloader is an enclosed machine room with pumps and suction pipes and barely any moving parts), machine weight (less need for new quay construction or refurbishment) and simple controls meaning quicker training for operators.
In terms of costs of operation and power consumption, Mr Dechamps says that based on US$0.1/kWh, the difference in power consumption is ±0.2kWh/t which represents approximately US$0.02 or as little as US$1,200 in total for a Panamaxsize vessel.
However, thanks to higher efficiency, a pneumatic unloader of 600tph will unload a Panamax vessel faster than a mechanical of 600tph. Saving one day on average for the discharge of each vessel means a saving of one day of demurrage on each vessel.
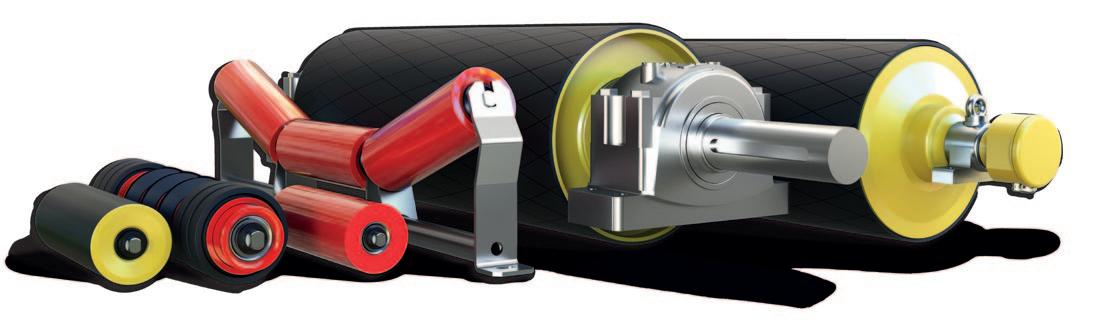