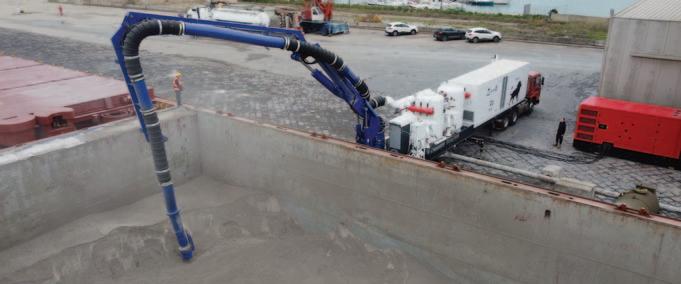
3 minute read
Lion Bulk Handling delivers pneumatic ship-to-silo unloader to Italian import terminal
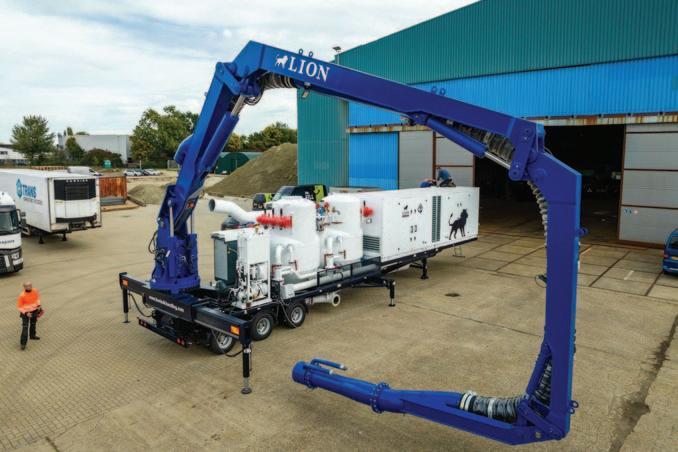
Lion Bulk Handling, a division of Lion Marine Group B.V., has recently delivered a pneumatic ship-to-silo unloader to an import terminal in Italy.
This highly technological machine is specially designed to unload dry bulk materials at a rate of 205tph (tonnes per hour). The features of this ship-unloader make it the first of its kind for unloading dry bulk materials such as cement, fly ash, alumina, etc.
v fully electrically driven;
The ship-unloaders features include: Industry 4.0 approved; v remote access — global remote v assistance possible; v Kinematic tested manipulator arm; wireless-controlled manipulator arm;
Finite Element Analysis (FEA)/ v highly advanced PLC control system; v dock-mobile configuration; v can be used to unload vessels of up to operation of its trusted partners.
Lion Bulk Handling offers products for: floating terminals; v v 7,600dwt; unloading capacity of 205tph.
Lion was able to engineer, deliver and commission this ship-unloader with the co-
ABOUT LION BULK HANDLING v self-discharging ships; v offshore rigs; v offshore vessels; v shiploading; v ship-to-truck unloading; v ship-to-silo unloading; v conveying; v storage and reclaim; and v v truck loading.
Lion Bulk Handling is a respected expert in the field of bulk handling equipment. The company designs, manufactures and commissions bulk handling systems for the marine, offshore and onshore industries.
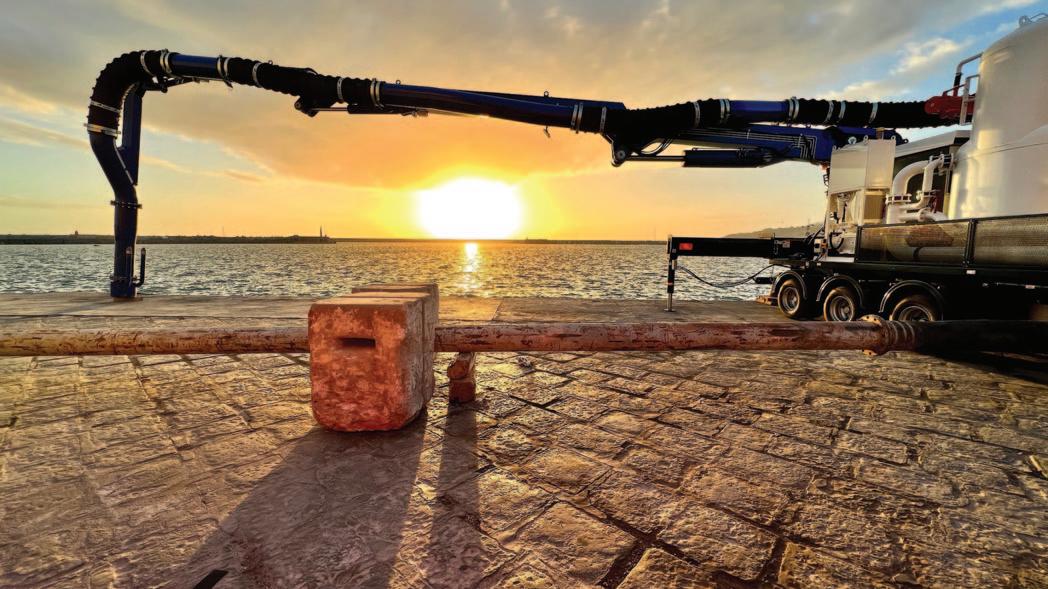
SHIP-TO-SILO UNLOADERS
The ship-to-silo unloaders only require a pipeline connection to handle the entire conveying process from ship to store. All configurations are available with a manipulator arm for open hatch (option 1) unloading or delivered with a flexible hose connection for closed hatch (option 2) unloading. The closed hatch unloading option can only be used with a fluidized floor vessel and can be operational in any weather condition. road mobile ship-unloader; v dock mobile ship-unloader; v gantry mobile ship-unloader; v barge-mounted ship-unloader; and v stationary ship-unloader. v
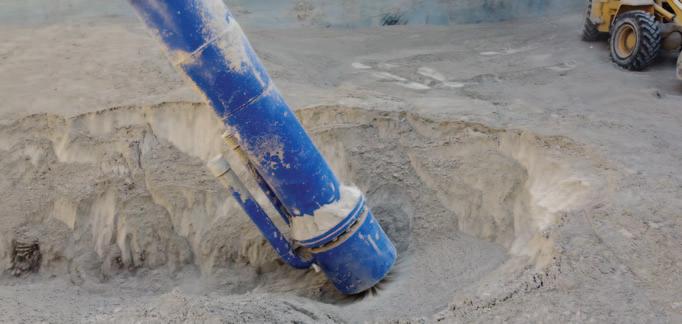

Road mobile ship-unloader
The ship-to-silo road mobile unloader is designed as a road legal unit and can be easily transported to various ports and terminals. One unloader can be used to service multiple ports and terminals for unloading (open hatch) barges and ships up to 7,000dwt. Due to its road mobility, the utilization rate of the road mobile unloader can be very high, driving the investment costs per tonne to a minimum. A permit may be required for movement over public roads, per local law.
The key benefits of the road mobile ship-unloader include that it is a compact unit for easy movement, it can service multiple terminals for unloading operations, it is automated, and it offers continuous material flow. The unit can serve vessels of up to 7,000dwt, with a maximum capacity of 205tph.
Dock mobile ship-unloader
The ship-to-silo unloader dock mobile type only requires a pipeline connection to handle the entire conveying process from ship to storage. This ship unloader configuration can easily move on the dock site or stored when not in use. Tyres are used to move the unloader, so no obstacles are located on the dock. This enables it to work in practically any type of dock environment. The pipeline may run below at or above ground level. The unloader also functions with removable pipeline sections.
The key benefits of the dock mobile ship-unloader include shared dock space, the dock remains free of obstacles such as rails or conveyor belts, it is automated, and it offers continuous material flow. It can work with vessels of up to 40,000dwt, and offers a maximum capacity of 360tph.
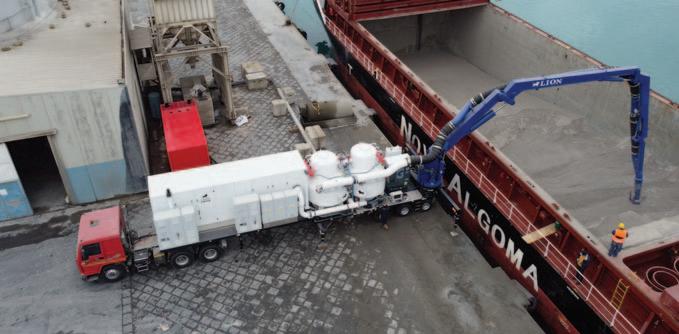
Gantry mobile ship-unloader
The ship-to-silo unloader gantry mobile type only requires a pipeline connection to handle the entire conveying process from ship to storage. This ship-unloader configuration is ideal for dedicated operations with available shore power. Especially with an existing infrastructure (rails) will save investment costs. The pipeline may run below at or above ground level. The unloader also functions with removable pipeline sections.
Key benefits include a dedicated jetty, existing rails, it is automated, and it offers continuous material flow. The unit works with vessels of up to 40,000dwt, with a maximum capacity of 360tph.
Barge-mounted ship-unloader
The ship-to-silo unloader barge-mounted type is ideal for unloading locations with large tidal differences, as this requires a minimum required length of the manipulator arm when unloading open hatch (option 1) ships or barges. When ships cannot reach the dockside, unloading closed hatch (option 2) ships or barges with integrated fluidized floor system through a flexible (floating) hose connection, would be a solution. The closed hatch option can be operational in any weather condition and is advisable for high humidity or monsoons regions. The barge-mounted ship unloader can also be used at multiple terminals, as the complete unit can be towed to another unloading location.
The key benefits of the barge-mounted ship-unloader include the ability to cope with large tidal difference, the ability to be used at multiple unloading terminals, it is automated, and it offers continuous material flow. The unit can be used with vessels of up to 10,000dwt, with a maximum capacity of 200tph.
Stationary ship-unloader
The stationary ship-to-silo unloader is a cost-effective configuration, as no propulsion system is required. This type of unloader only requires a pipeline connection to handle the entire the conveying process from ship to storage. This enables it to work on a dock with limited space. The key benefits of the stationary ship-unloader include that it is suitable when there is limited space on the dock, barges and ships can easily move alongside the dock, it is automated, and it offers continuous material flow. The unit can be used on vessels of up to 40,000dwt, with a maximum capacity of 360tph.