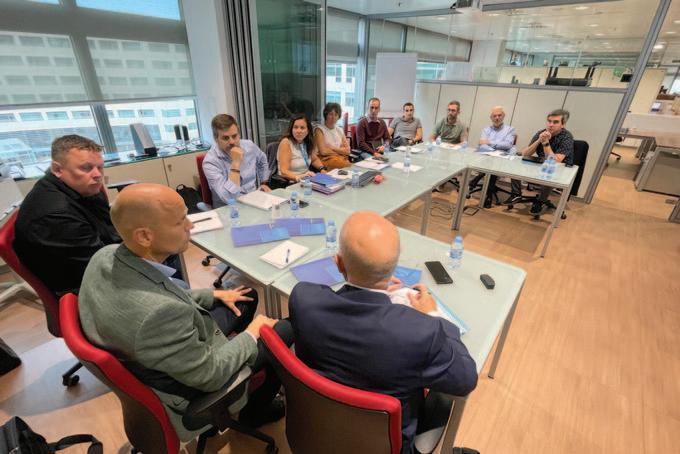
26 minute read
Port of Barcelona and PowerCon: electrical power to ships at the BEST terminal
The Port of Barcelona and PowerCon start building the pilot project to provide electrical power to ships at the BEST terminal
The Port of Barcelona and Denmark’s PowerCon A/S have started building the pilot project to provide electrical power to ships at the BEST terminal. The company has been awarded the contract for this project, which is part of Phase Zero of the Wharf Electrification Plan developed by the Port of Barcelona and includes the drafting and performance of the project as well as the ships’ connection and disconnection service and the maintenance of the installation. The contract has been awarded for €4,978,640.
The first meeting was held between the Port of Barcelona team that heads the pilot project (Ana Arévalo, Energy Transition Manager; Gemma Peñalver, Site Manager, and José Manuel Hernández, electrical engineer) and the team from PowerCon A/S, led by Peter Castberg Knudsen, Team Manager and founding partner of PowerCon; Soren Munch, Site Manager, and Javier San Miguel, coordinator.
During the meeting, the Port of Barcelona and PowerCon teams established the ground rules for the performance of the construction project in accordance with the tender and visited the Hutchison Ports BEST terminal to inspect the facilities where the electrification equipment will be located. Ana Arévalo stated “we hope to have the construction project approved in six months, at most, so that we can start the building work”.
NEXIGEN With a planned overall investment of nearly €110 million, the Wharf Electrification Plan is among the key projects promoted by the Port of Barcelona to halve CO2 emissions from port operations by 2030 and become a carbon neutral port by 2050. This plan, known as Nexigen, will make it possible to connect ships to the general electricity grid while they are berthed, using clean energy that is generated at the port itself or that is certified 100% renewable.
Awarding the pilot project at the BEST terminal marks a decisive step towards realising the first OPS (onshore power supply) supply points, which will work at the port’s commercial docks. It should be remembered that the port’s first OPS points are already working at the MB92 Barcelona facilities.
Once the BEST pilot project is underway, the Port of Barcelona will have real and useful experience-based information about the performance of OPS on container ships and will be able to draw conclusions regarding best practices and identify future needs and developments.
The Port of Barcelona Dock Electrification Plan is fully aligned with the United Nations Sustainable Development Goals (SDGs) and one of the keys to its success lies in connecting the Port directly to the high-capacity electricity grid to respond to expected demand for electricity from ships.
THE SUCCESSFUL TENDERER PowerCon is a Danish engineering and manufacturing company specialising in electrical energy conversion solutions for various applications. With its roots in the Danish wind power sector, PowerCon is not only involved in the wind turbine industry but also operates in the maritime sector, where the company ranks among the leaders in power supply equipment.
PowerCon offers high- and low-voltage power supply solutions from land to all types of vessels, ranging from cruise ships to container ships, ferries and fishing vessels. All of its flexible and innovative systems are built according to international standards.
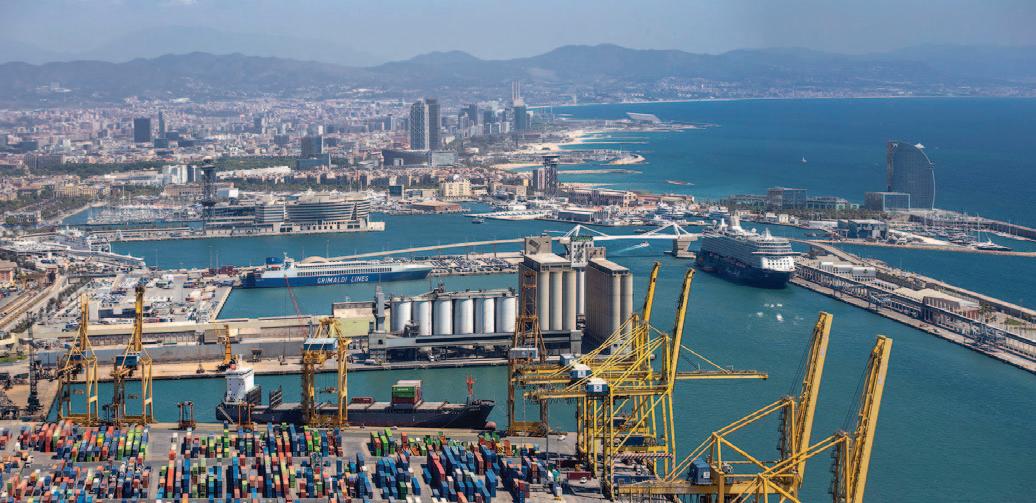
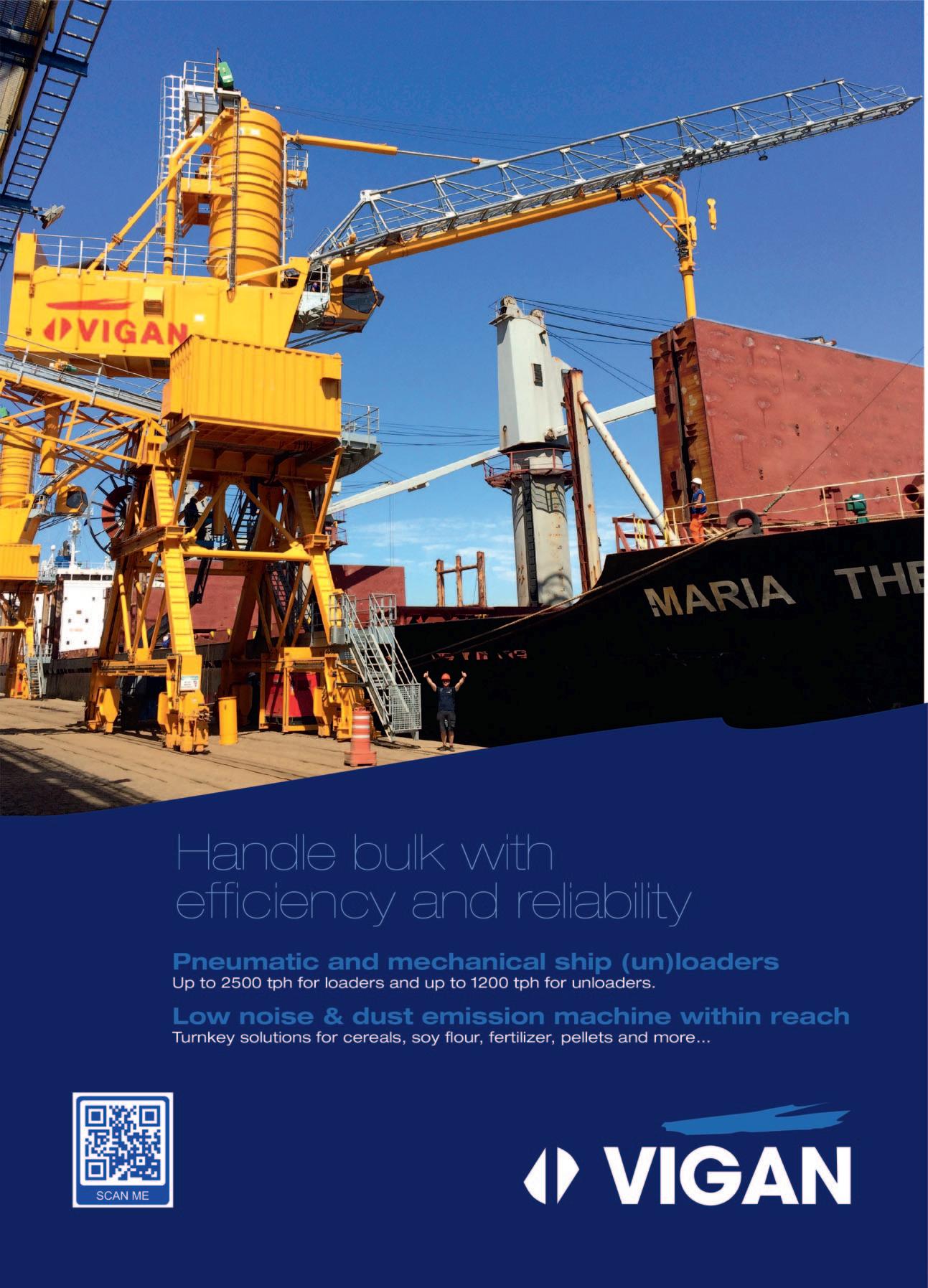
Bulk in BelgiumBulk in Belgium
Belgian Regional Report
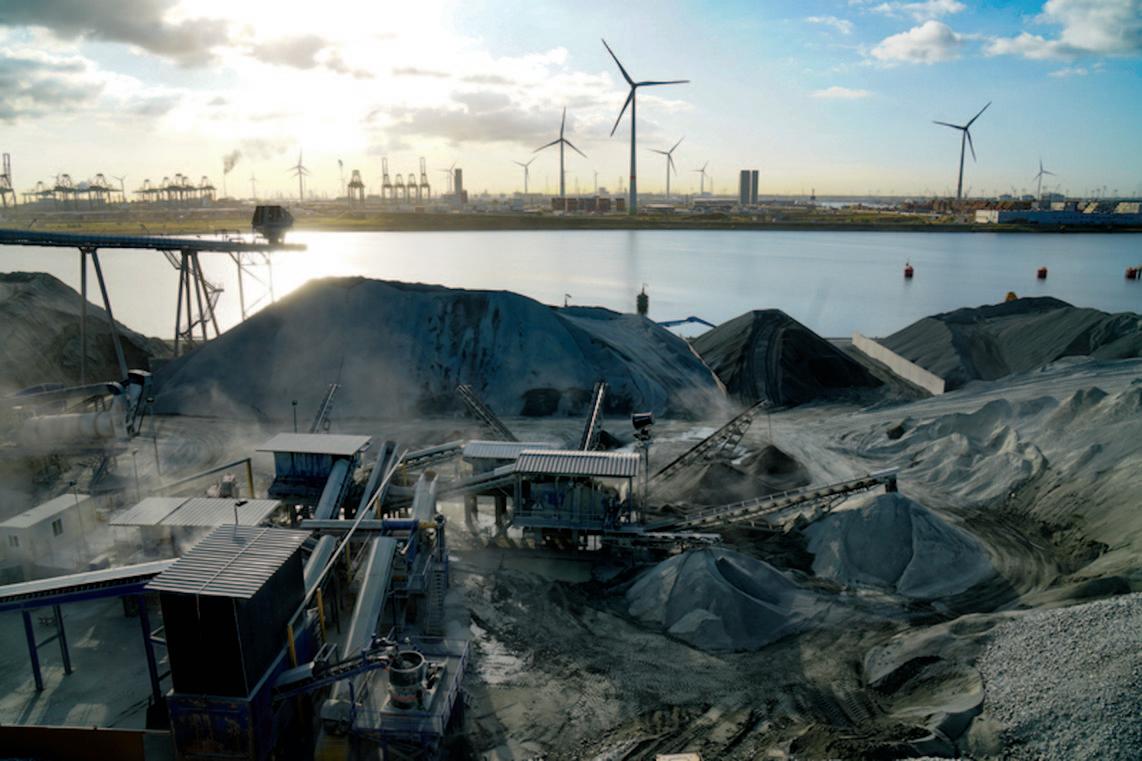
Jay Venter
After nine months, the total throughput of Port of Antwerp-Bruges was 217.4mt (million tonnes), a slight increase of 0.8% compared to the same period last year. Despite the negative impact of the geopolitical and macroeconomic context, all cargo flows are recording growth, with the exception of the container segment, which remains under pressure. Together with a series of announcements of new investments in the port platforms of Antwerp and Zeebrugge, this confirms the attractiveness and resilience of the unified port.
After nine months, container through put is down 8.8% in tonnes and 5% in TEUs compared to the same period last year.
Conventional breakbulk grew by 9.7%. While steel outflows are holding up well, steel supply volumes are showing a downward trend as a result of high inventories and falling demand. Despite a declining trend in the throughput of wood and building materials, these product groups, like fruit, are still recording growth.
Roll-on/roll- off traffic saw an increase of 8.1%.
Growth in the dry bulk segment (+21.5%) is primarily fuelled by growth in the transport of coal. The increased demand for coal for power generation translated into throughput of 2.43mt compared to 364,000 tonnes in the same period last year. Throughput of iron ore is showing growth, while scrap metal, sand and gravel show a decline and other building materials remain status quo. Although both fertilizer inflows and outflows have picked up compared to the second quarter, there is still a decline from the 2021 record year (–11.8%).
The liquid bulk segment recorded an increase of 13.3%.
After nine months, Zeebrugge has welcomed 102 cruise ships with 325,406 passenger movements, up from last year when cruise shipping was largely at a standstill due to Covid-19.
UNIFIED PORT ATTRACTS INVESTMENT Since the official launch of merged port Port of Antwerp-Bruges six months ago, several investors and new projects have already found their way to both the Antwerp and Zeebrugge port platforms. Conti Seafrigo Antwerp, for example, will construct a new frozen food warehouse, Antwerp Euroterminal (AET) will commission Belgium’s largest unit parking lot and Fluxys will build an ammonia terminal in partnership with Advario. Meanwhile, Covestro has begun construction of an aniline plant, ITC Rubis is expanding with an additional tank pit and Lanxess is installing a new climate protection system. Ineos has also chosen to set up a pilot for Carbon Capture and Storage (CCS) from Antwerp. In www.drycargomag.com
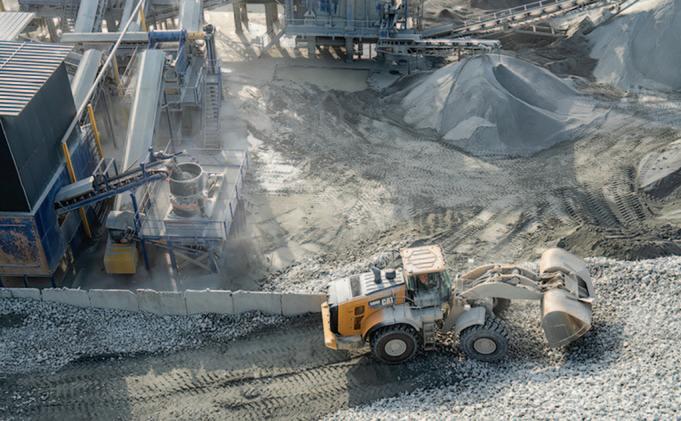
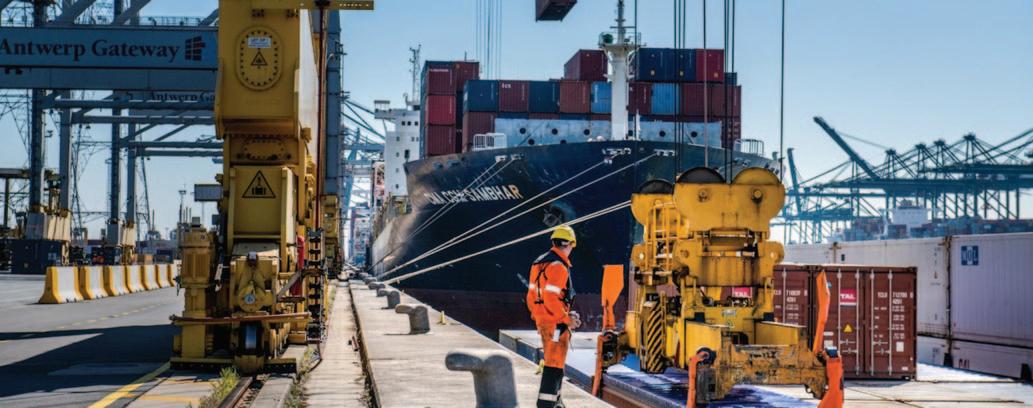
Zeebrugge, Ziegler Group is opening a branch for unaccompanied ro-ro freight to Ireland and the United Kingdom, and real estate group Intervest this week officially opened the logistics complex acquired in April from Chinese developer Lingang.
Jacques Vandermeiren, CEO Port of Antwerp-Bruges commented “Despite the ongoing challenges due to the current geopolitical and macroeconomic context, we stand as a unified port. The negative trend in the container segment, rectified by growth in the other segments, is likely to continue towards the end of the year. But the flood of substantial, forward-looking and sustainable investments and new projects, especially in a climate of closures and production cuts due to high energy prices, is a confirmation of our strong position and attractiveness as a world port.”
Annick De Ridder, Port Alderwoman of the City of Antwerp and Chairwoman of the Board of Directors of Port of AntwerpBruges, added, “In these particularly challenging times, our unified port is demonstrating its resilience. This is proven by the slight increase of 0.8% compared to the same period last year. In addition, some major investments were announced this month.
“The modernization of the Europa Terminal (investment by Port of AntwerpBruges of €335 million and €500 million by PSA Antwerp), the inauguration of the Lanxess climate protection installation (€13 million) and the start of construction work on Covestro’s aniline production unit (€300 million) are the most notable examples. There will also be a net addition of 750 port workers this year and next. Together with the innovative companies that believe in a sustainable future and are anchoring their presence through investment, the port is and can continue to function as the engine of the Flemish economy.”
Dirk De fauw, Mayor of the City of Bruges and Vice-Chairman of Port of Antwerp-Bruges said, “The fact that we can achieve this result in the current context makes me hopeful for the future, even though we will certainly need to be resilient. The growth in LNG throughput confirms the important position of Port of Antwerp-Bruges in that segment. In addition, we recently received two new Far East services and were included as the first port of discharge in Europe on MSC’s ‘NWC – USA – SAWC Service’. Together with the new investments, this will continue to strengthen our international position.”
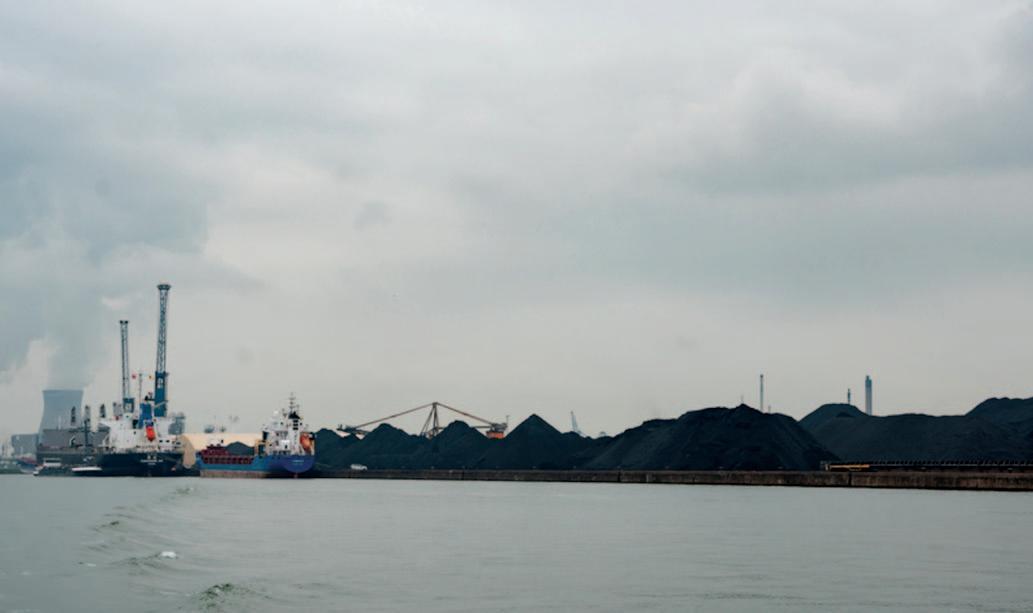
During the first nine months of this year, the North Sea Port companies recorded transhipment of goods by sea of nearly 57mt (million tonnes). This is a 9.3% increase. Transshipment of dry bulk, general cargo, ro-ro and liquid bulk all improved significantly.
In 2020, during the first nine months — in the middle of the coronavirus crisis — North Sea Port was faced with a 13% drop in cargo traffic by sea compared to the previous year. A 9% growth was recorded for the first nine months of 2021. Again, a 9.3% increase can be recorded for the same period, mainly in the second quarter.
DRY BULK, GENERAL CARGO, RO-RO AND LIQUID BULK ON THE UP Transshipment by sea increased by 4.8mt (+9.3%) during the first nine months of this year to 56.9mt compared to the same period in 2021.
Dry bulk experienced a 13% growth (3.6mt) and reached 31.4mt. Here, solid fuels account for almost half of this increase (+1.6mt). Transshipment of oilseeds, iron and ores also increased.
General cargo recovered strongly with an 11% growth (+0.8mt) and clocks in at 7.7mt. More than half of this increase was achieved by trade in steel plates.
Ro-ro continued to grow by +8.4% (0.2mt), clocking in at 2.8mt.
Total liquid bulk transshipment recorded 13.3mt, an increase of 3.1% (0.4mt).
Container transhipment declined 8.9% in the first three quarters of 2022, reaching 1.7mt compared to the same period in 2021. This mainly concerns a decrease in the transshipment of fruit and vegetables not transported by container but as break bulk.
INLAND NAVIGATION TRANSHIPMENT ALSO ON THE UP For the first nine months of this year, transhipment via inland navigation also recorded an increase, plus 8.4% (3.7mt) to 48mt. This increase was, to a large extent, due to an increase in cargo traffic during the second quarter.
IMPACT RUSSIA-UKRAINE During the five months, March to July this year, immediately following the start of the war in Ukraine, many companies stockpiled large amounts of goods. This was because of limited exports from Ukraine and EU embargoes on goods from Russia such as coal and wood.
Daan Schalck, CEO North Sea Port: “Uncertainties on the geopolitical stage therefore cause (temporary) spikes in supply streams in certain segments. The drop in trade with Russia will be compensated by additional transhipment from mainly the United States, Canada and Finland. Russia may then cease to be the first trading partner by the end of this year.”
Ukraine also logically drops further down the list of trading partners despite the supply of grain since early September through the grain corridors set up by the United Nations. A total of 0.4mt were traded, well below the 1mt in the same period in 2021. The declines are in maize, animal feed and iron ore.
OUTLOOK Growth in cargo traffic by sea and inland waterway occurred strongly during the second quarter of this year. During the third quarter, growth slowed down. It is expected to continue like this in the months to come.
Zoutman to build the world’s most advanced salt tower at North Sea Port
Zoutman is to erect the world’s tallest and most modern production tower for sea salt at its Ghent Kluizendok site in North Sea Port. The €30 million investment features high sustainability as well as creating 40 new jobs and enhancing the port’s position as a food port.
The new 64.5 metre tower will provide an additional capacity of 150,000 tonnes per year. High-tech production may start as early as the middle of next year. The site will include five unique optical cleaners to remove impurities from the salt. To Zoutman this investment is an important landmark. The family-owned company specializing in sea salt aims to double its sales by 2030.
GROWING DEMAND FOR SUSTAINABLE SALT The process in the new tower will focus on producing salt without additives in order to combat salt clumping and hardening. “We find that food companies want to switch to table salt without artificial additives as soon as possible. Because of substantial investments in research, we are the only sea salt producer in the world that can offer a quality product for this growing demand,” underlines co-CEO Bert Lamote. On top of that, natural and sustainably sourced sea salt is by far the most environmentally friendly type of salt. When extracting salt from the sea, CO2 emissions are up to 31 times lower than salt extracted from mines, the company said.
The new production tower will rank highly in terms of sustainability. Its high-rise reduces space requirements, doubles production efficiency per square meter and allows the use of gravity to reduce energy consumption. The plant that is selfsufficient in energy and heat will purify and reuse its process water.
FOOD PORT WITH THE LARGEST COVERED SALT TERMINAL IN EUROPE The new installation is no chance occurrence for North Sea Port. The West Flanders salt producer has had a storage, production and distribution hub at the Kluizendok in Ghent for years. This has developed into the largest covered salt terminal in Europe and the main hub in Zoutman’s logistics. The storage capacity is 300,000 tonnes of sea salt. Each year, the group ships 450,000 tonnes of salt to more than 60 countries.
This new Zoutman investment will enhance one of North Sea Port’s strategic pillars, CEO Daan Schalck pointed out. “The expansion of the Zoutman Ghent facility fits into our efforts to develop North Sea Port as a food port. The 40 additional jobs as well as the increasing cargo throughput of 150,000 tonnes of sea salt per year will further establish this development. It is good to see that this company of international standing has an eye for sustainability in the extraction of sea salt, the economical use of space with the very innovative building and its operation. A perfect example of how growth and sustainability can go together.”
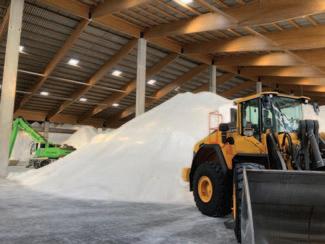
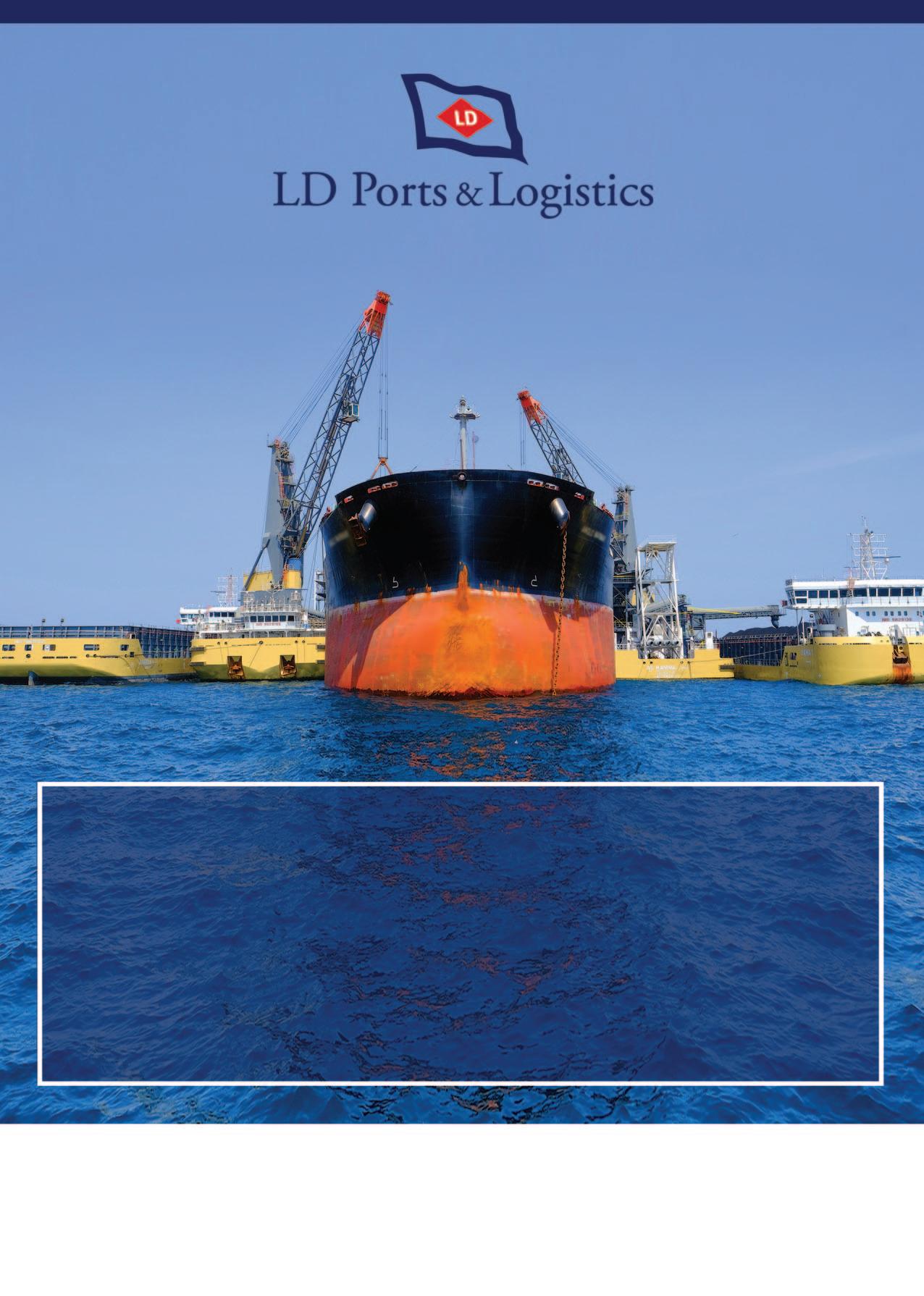

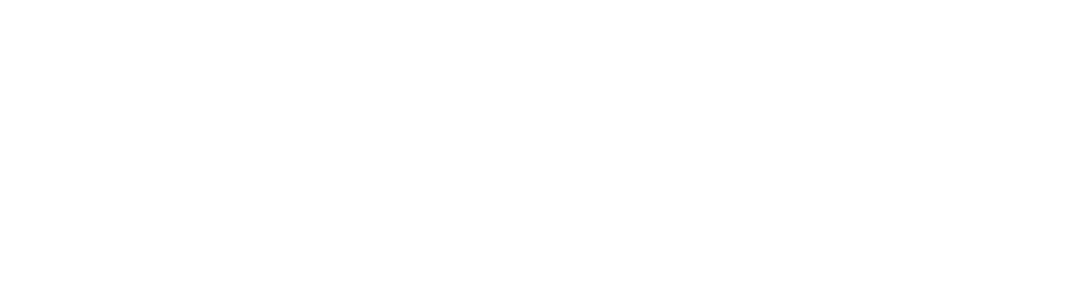
In the Region of France
Traffic, equipment, upgrades and environmental commitments
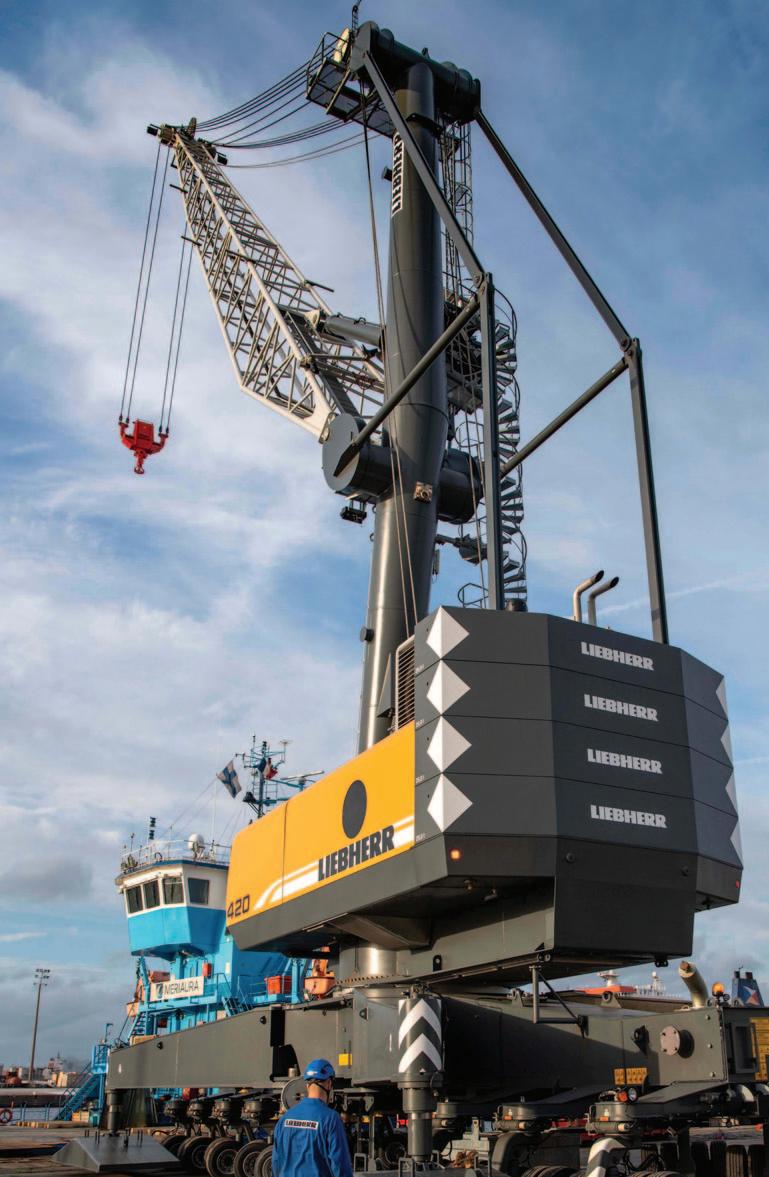
Jay Venter
A new crane at BARRA SNM in Dunkerque-Port
The BARRA SNM company has installed a new Liebherr 420 mobile crane at its terminals in the port of Dunkerque in Dock 6.
This new multi-purpose crane with a maximum hoisting capacity of 125 tonnes completes the current fleet. It allows the company to meet the needs of its customers to consolidate existing traffic and develop new activities in breakbulk, heavy loads and small agricultural and industrial bulk.
In addition to the operational advantage that this new tool will bring, it will also improve the environmental footprint of port operations with reduced energy consumption, the possibility of operating with bio-fuels and, in the long term, of switching to all-electric systems.
The BARRA SNM teams are happy to be able to continue to offer their customers the best possible services backed by their recognized human operational skills and by latest-generation tools.
ABOUT DUNKERQUE-PORT Major French port complex (Calais–Dunkerque); ninth-largest port on the Channel and North Sea Ranges, thirdlargest port in France, the port of Dunkerque stands out in many segments. It is the leading passenger port in Europe (Calais–Dunkerque corridor); the largest energy hub in France; largest LNG terminal; top French port for containerized imports of fruit and vegetables; top French port for mineral and coal imports; largest rail port in France; largest regional river port; third-largest port in France for grain traffic.
Dunkerque-Port is also a sustainable port. It is the trading port of the new Hauts-de-France Region, the largest agricultural region of France, the leading region for the rail industry, and the leading region for the car industry. In 2021, traffic totalled 48.6 million tonnes.
Atlantic Port La Rochelle, Groupe Sica Atlantique: committed to sustainable soy
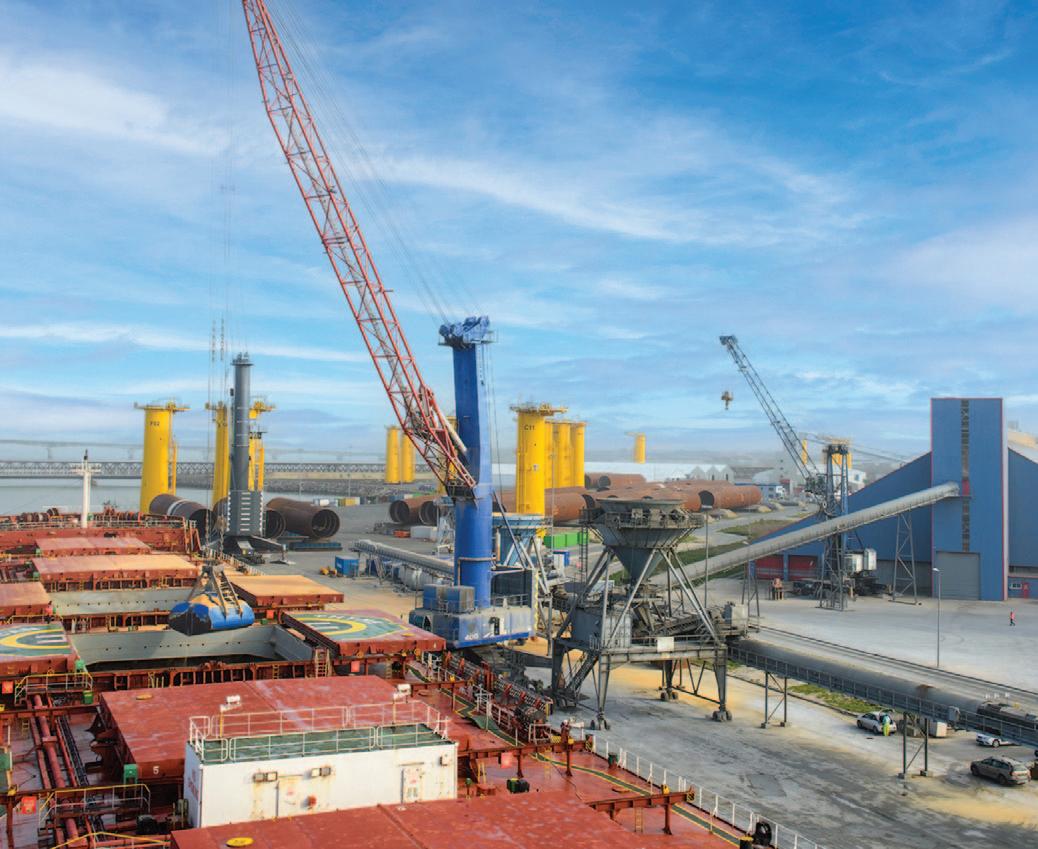
Solteam (importer), EVA (stockman) and Atlantic Port La Rochelle (located on the coastline of the west French Atlantic coast), have signed a tripartite agreement validating their collective commitment: now only sustainable soybeans, from nondeforested and non-converted areas, are being transited to La Rochelle.
During the recent stopover of the Ultra Leopard chartered by Solteam, at the EVA terminal of Anse Saint-Marc in La Rochelle, EVA unloaded 30,000 tonnes of sustainable soybeans from Brazil.
While on 13 September 2022, MEPs adopted a text prohibiting on European territory a number of products* whose importers could not prove that they come from unforested or unconverted land,
Solteam says it has not waited for European regulations to embark on a virtuous approach. Guillaume Bettinger explains “We work in partnership with the non-governmental organization Earthworm Foundation, which describes our goods as coming from non-deforested and unconverted areas. Our suppliers in Brazil carry out geolocation and satellite monitoring of the plots as well as the verification of the origins of the seeds. This is our guarantee of transparency, our commitment to non-deforestation and the preservation of sensitive biotopes such as those of the Cerrado or the Amazon.”
Sustainable soybeans will become the norm of the market, excellent news in terms of social responsibility in the face of climate issues.
EVA and the Grand Port Maritime wanted to support Solteam in this approach by placing social responsibility at the same level as health responsibility, which itself led to the construction of the new Saint Marin building in 2019.
The Groupe Sica ATLANTIQUE was born at the end of the 50s from the strong will of a few pioneers in the grain export sector. Around 80 grain operators decided to gather their strengths to build the first port silo dedicated to export. port silo dedicated to export.
“Since then we always have nurtured our commitment to the regional agricultural sector; our shareholders and board members are all local grain market actors.” says Louis Tercinier, Président of the Board. “Our vocation is to design and implement innovative, integrated, global solutions to optimize and massify logistics flows for players in the agricultural and agro-industrial sectors, who represent our core businesses. We are their main port logistic operator. We also develop services for other sectors working towards our strategic objectives.
Since 1992, we have developed and organized our activities into six complementary divisions.
We have become the leading port operator in La Rochelle-Pallice.
*Soy is one of them, such as palm oil, coffee, cocoa, wood, rubber, corn, livestock (pork, sheep, goats, poultry).
Bruks Siwertell road-mobile unloader in Marseille. REGIONAL REPORT
Handling alumina, the valuable, powdery bulk commodity used in the production of the endlessly recyclable metal, aluminum, is a Trímet France speciality. At the end of 2021, Bruks Siwertell enhanced these capabilities further with the delivery of a new Siwertell 10,000 S next-generation road-mobile unloader to the company’s alumina import facilities in France’s largest port, Marseille.
SPEEDING UP AT THE BERTH Trímet France, part of Germanyheadquartered, Trimet Aluminum SE, principally receives vessels from Greece and Ireland, with the largest standing at around 14,000gt and the smallest close to 6,000gt. Shipments of alumina are discharged to silos, ready to be sent in rail wagons to a long-established aluminumproducing factory in Saint-Jean-deMaurienne, south-east France.
“One of the biggest challenges for us has been to reduce the time that a vessel stays at the berth,” explains a spokesperson for Trímet France. The faster vessels can be turned around the higher the utilization rate of the jetty, delivering better profitability for the terminal. With an expected alumina intake of around 50,000 metric tonnes into the port in 2022, the majority of which will now be handled with the new road-mobile unloader.
Siwertell unloaders are based on screwconveying technology and offer high, continuous through-ship efficiencies. They can reach into the corners of a vessel’s hold, including under the hatch coamings, because of the range of movement in the horizontal conveyor and the pendulum capability of the vertical arm, which also means that assistance from payloaders is kept to a minimum.
“The mobility of the equipment’s conveying arm is definitely an advantage for achieving faster vessel turnarounds, and allows us to operate everywhere in the holds,” says Trímet France.
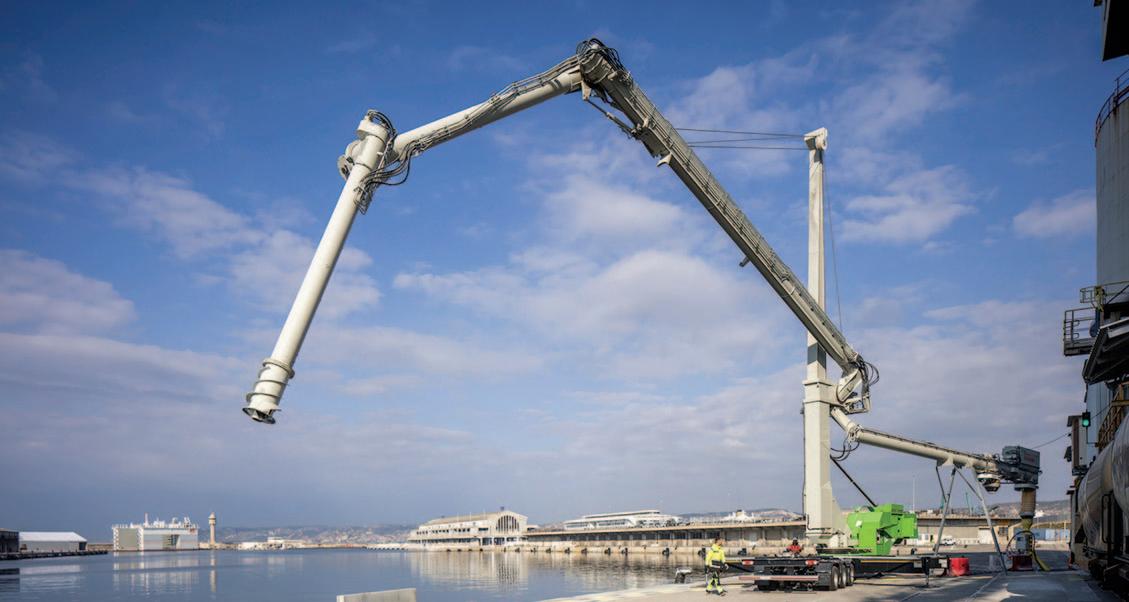
EXCEEDING UNLOADING EXPECTATIONS For around a year and a half, Trímet France leased an older Siwertell 10,000 S unloader from another Bruks Siwertell customer. “We did this before deciding to buy a new, next-generation electric-drive model,” says the company. “Environmental issues have an important place in our mind. So, we are happy to reduce emissions, and the noise of the engine, with this electric Siwertell version.”
The new unloader has a designed rated capacity of 130tph (tonnes per hour) for discharging vessels up to 10,000dwt, it also features advanced digital capabilities. Fitted with the Industrial Internet of things (IIoT) device, CompuLab, owners of nextgeneration models have safe, remote access to extensive monitoring, follow-up support, diagnostics and troubleshooting.
Trímet France highlights the additional performance capabilities of its nextgeneration road-mobile unloader. “The remote control is particularly useful,” says the company. “Operators are able to see precisely if the unloading is efficient, so we can reach a discharge capacity of 150tph. This is over what we expected. Also, the digital capabilities mean that Bruks Siwertell is able to check any problem that occurs on this Siwertell unloader in real time.”
During commissioning Trímet France noted that the remote control needed further attention. “We were grateful to Bruks Siwertell for its reactivity to solve the issue, and are continuing to work together to find a solution to reduce noise from the screw because we are situated very close to neighbours,” it adds.
ENCLOSING THE DUST Environmental protection legislation is often a driver for the adoption of enclosed dry bulk handling equipment, and prior to the Siwertell unloader installation, Marseille’s port administration had requested that Trímet France reduce its dust emissions.
All Siwertell ship-unloaders have a totally enclosed conveying line from the hold, where the inlet feeder draws material into the vertical screw conveyor from beneath the surface, to the receiving facility, offering close-to-zero dust emissions and eliminating any wasteful spillage.
They also operate with a layer-by-layer unloading process, which minimizes the
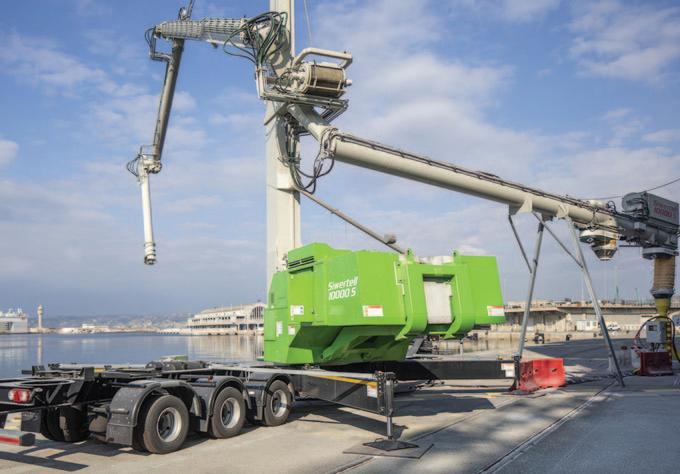
chance of airborne emissions from avalanches in the cargo hold. This is further reduced because of the equipment’s excellent hold reach.
For road-mobile unloaders, a dust filter is installed at the top of the loading conveyor. It creates negative pressure and minimizes the risk of dust emissions at the transfer point where material leaves the unloader and enters the receiving equipment. It automatically returns the collected dust to the conveying system.
MINIMIZING DEGRADATION MAXIMIZES PROFITS In addition to offering efficient, environment-friendly alumina handling, with no spillage and very low energy consumption, the Siwertell unloader minimizes material degradation, which delivers a particular benefit to the alumina industry that goes further than the port.
Alumina is sensitive to degradation and therefore has a high propensity for the production of powdery fines. These have a significant impact on a smelting plant’s energy consumption; the lower the percentage of fines, the lower the temperature required in the process.
“In the midst of soaring energy prices, any reduction in fines has a huge economic impact, and offers better cost control for the plant,” explains Jörgen Ojeda, Sales Director Mobile Unloaders, Bruks Siwertell. “We are not only keen for more port operators to benefit directly from our market-leading alumina handling capabilities, but in addition to this, for these advantages to extend to substantial savings for the global alumina industry as a whole.”
SUPPORT BEYOND DELIVERIES Siwertell road-mobile unloaders provide a flexible, efficient solution for customers that have operations at more than one location. They can be folded down and relocated in under an hour. In the future, Trímet France plans to trial these capabilities, and transfer the equipment to its other sites to test if this solution could be successfully transposed elsewhere.
“We have really had a chance to get to know Trímet France and its operations, initially over its leasing of the older roadmobile,” continues Ojeda. “This was a valuable experience and over this time, we supported the company with any servicing needs.
“We hope that Trímet France will continue to benefit from the enhanced capabilities of its new road-mobile unloader for many years to come, and we look forward to helping the company with its plans for the future,” he concludes.
ALUMINA: A BILLION DOLLAR POINT Bruks Siwertell’s ship loaders and conveyors are well-established as preferred bulk material handling systems for alumina across the world, but it has even more to offer.
Bruks Siwertell can demonstrate that Siwertell screw-type unloaders outperform established alumina unloading methods, including grab cranes and pneumatics, to such a degree that across the global alumina industry, savings could reach the billion US dollar mark.
Alumina is an expensive dry bulk commodity, and its spillage costs the industry millions of dollars every year. During alumina unloading, some grab cranes can spill up to one and a half percent of a shipment. In contrast, independently-observed tests with Siwertell road-mobile unloaders showed no loss of bulk material. Eliminating spillage and minimizing dust creation deliver additional savings in clean-up costs as well.
Pneumatic systems do not incur spillage on the scale of grab cranes, but they are less efficient, demand more energy and cause significantly higher material degradation than Siwertell unloading systems. Alumina degradation, and the presence of powdery fines, has a major impact on energy costs in the smelting process; reducing fines, reduces production costs. Siwertell road mobile unloader.
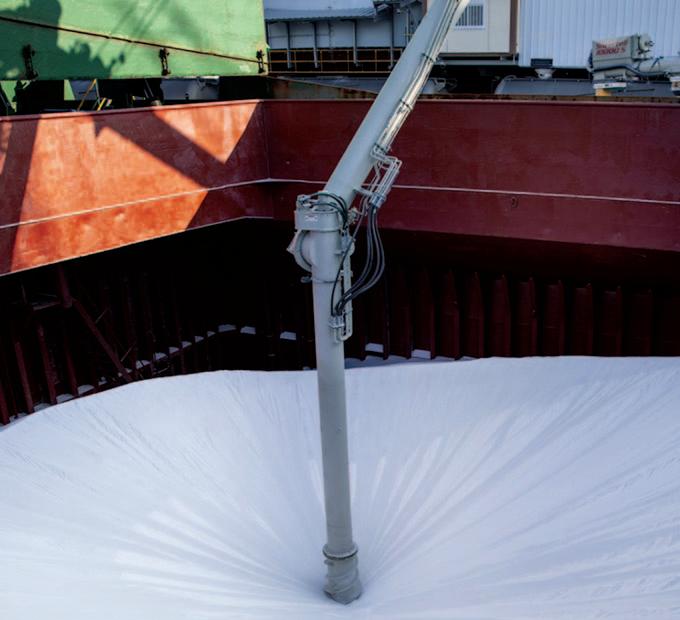
Rouen-Sénalia Grand-Couronne Grain terminal.
A major player in the development and protection of the Seine estuary, HAROPA PORT | Rouen, the Western European cereal exporting port, receives 3,000 vessels and 6,000 river convoys each year. At the heart of the HAROPA PORT, Rouen bases its uniqueness on its ability to handle all types of traffic, particularly industrial, thanks to the know-how of its operators and the diversity of its terminals, which range from Honfleur to the Rouen Normandy Metropolis.
2022 TRAFFIC UPDATE In the first two quarters of 2022 dry bulk traffic at Port of HAROPA PORT | Rouen declined by 4.2%, despite a positive trend in the cereals segment (+2%) and a 2022/23 marketing year judged to be as good as 2021/2022.
Aggregates traffic going to the construction market registered a fall of –22%, down by 260,000 tonnes, as of the end of June, but up by +8% on average and remaining generally at historically high levels, underpinned by an positive trend in construction projects. This weakening can be put down to unfavourable weather in the early months of the year, which had an impact on worksites and logistics conditions for materials.
Wood pellets used for heating’s flow consists entirely of imports and accounted for 110,000 tonnes, an increase of 9%. This sector is likely to continue to progress. Last year, French consumption stood at 2.4mt (million tonnes) with domestic production of 1.9mt.
In addition to the commodities mentioned above: v Solid fertilizers are up (+84% at end of
June [417,000 tonnes]). v Coal is about to disappear, replaced by biomass (including wood pellets).
INFRASTRUCTURE AND INVESTMENTS During the past campaign, the Rouen silos continued their investments. The BZ Group undertook several maintenance operations on its installations and equipment. Sénalia renovated the gantries of the Elie peninsula terminal for an amount of €7.3 million and finalized the construction of its new head office for the same amount of €7.3 million. Two wheel loaders were also acquired by the company. On its side, Simarex has built a new car park to make it easier for heavy goods vehicles to enter. The silo has also installed a new footbridge for access to ships. Finally, the Socomac silo of the new Invivo – Soufflet group has completed the refurbishment of one of its gantries and extended the tread of the gantries by 2m, This has resulted in a new 145m-long quay.
HAROPA PORT accompanies private investments by modernizing the terminals (extended Radicatel, dredging, etc.)
For the transport of cereals, the typical vessel used is the Panamax (229 x 32m). The deepening of the port of Rouen channel, which has been operational since July 2019, makes it possible to receive large-tonnage vessels, and more and more Panamax.
For example, the Bregaglia charged 59,400 tonnes of barley in June 2020, the Andros charged 57,000 tonnes of feed barley in January 2021 (record draught at Rouen exit: 11.40m)
HAROPA PORT is working to develop its mass transit modes with freight and rail, this is an important point of its Strategic Project. Already committed, HAROPA PORT plans to increase its efforts to achieve a 30% modal shift by 2025, mainly: 1) by continuing the development of combined rail transport; 2) the development of inland waterway combined transport; and 3) by enlarging the rail and river hinterland of the cereals sector.
In 2021, which was a year marked not only by a strong recovery in global activity but also disruption in maritime calls and a shortage of empty containers, multimodal inland container traffic was maintained at 12%, reaching 270,000 TEU.
In order to cope with the constraints generated by this massive upturn in activity, shipping lines prioritized road transport due to its advantages for rapid container throughput. However, modal transfer has progressed marginally by 2% since 2017, a year in which the port achieved 2.2 million TEU, not including transhipments, as in 2021. Efforts do however still need to be made in 2022 on the use of mass transport modes both for hinterland full container flows and empties.
VALUE ADDED SERVICES An agro-industrial cluster is located directly on the quays of the port sites that allows the following: v Packaging or sorting on demand for agricultural products (skills and tools to handle all types of requests). v Some companies are involved in the processing of agricultural products
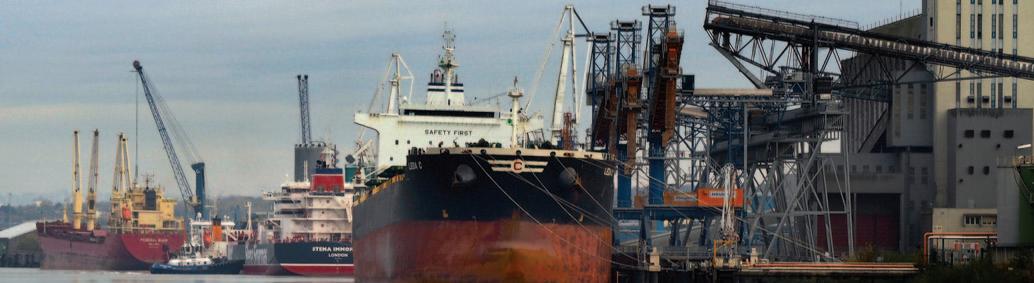
IMPACT OF WAR IN UKRAINE The war in Ukraine has had a substantial impact on trade in agricultural products globally, and specifically on exports of wheat, maize and oilseeds, these being largely carried by sea, which means that stocks have been blocked in the Black Sea ports and forthcoming harvests are also compromised. Notwithstanding this, the situation highlights the key role played by France as a supplier of wheat and barley to countries with a structural need for imports, thus opening up new market opportunities.
France imports very few agricultural products from Ukraine and Russia (fertilizers, wood but in small quantities).
Some countries have returned to French cereals after having started to buy from Russia or Ukraine: Algeria, Tunisia, Egypt and a few new countries have placed some orders this year.
Thanks to its experience, the Port of HAROPA PORT | Rouen is competitive and well organized. The operators have the equipment and the commodities to respond quickly to new demands.