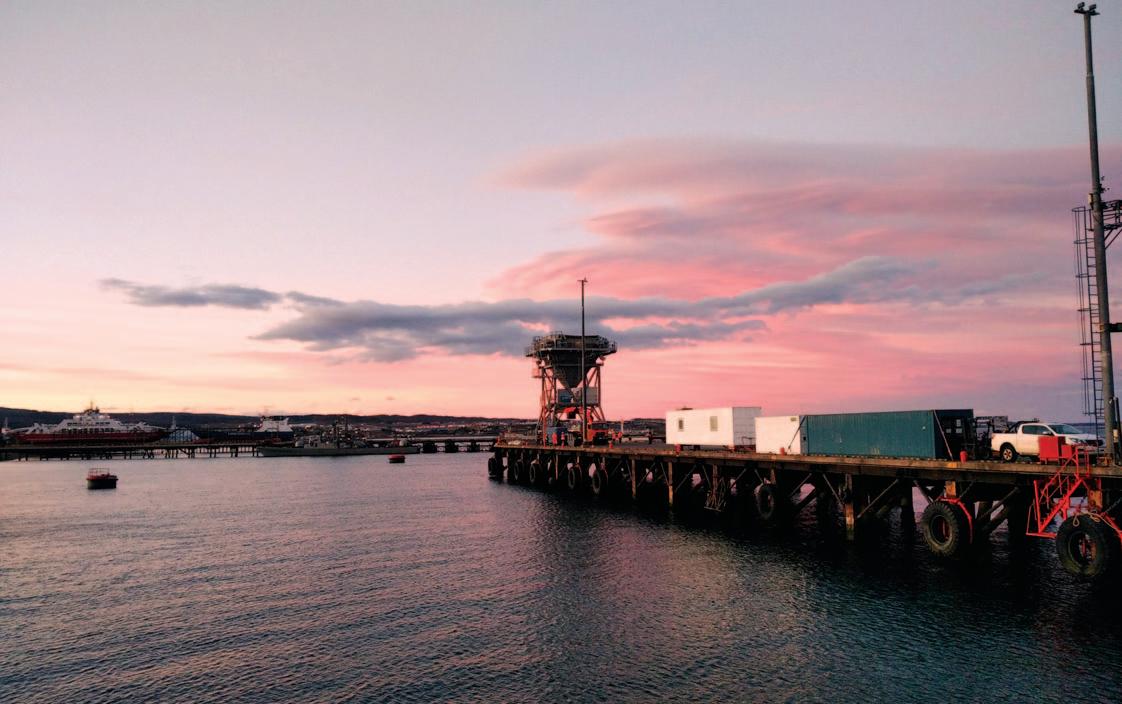
44 minute read
WHY THE RIGHT TOOLS MATTER WHEN HANDLING AND STORING CEMENT
Bedeschi eco-hopper in Punta Arenas, Chile. Why the right tools matter...
... when handling and storing cement
Green applications in the cement industry
The cement industry is increasing every year, due to the continuing growth in industrialized and urbanized areas with consequent construction of new buildings, roads and infrastructures. Most of this new development is taking place in emerging countries.
At the same time, cement factories are major contributors to global CO2 emissions and dust emissions, both of which have high environmental impact.
Recently, the common goal has been set from keeping the temperature rise below 2° Celsius at 1.5° Celsius. More than 77 countries are committed to controlling and reducing the impact of the cement industry on environment by 2050.
Reducing the emissions of the cement industry will play a pivotal role in addressing the climate challenge. Companies will need to identify the best paths through technological innovation, eco-friendly equipment, and modern technology in order to ensure the highest environmental standards.
Bedeschi is committed to help reaching this global goal thanks to its 110 years of experience and the wide variety of solutions that it can offer. The R&D Department of the company is constantly working to improve the capability of all systems, focusing on environmental protection, energy efficiency, investments into eco-friendly and innovative equipment and pollution prevention.
The solutions Bedeschi is improving in its machines to reduce dust emissions and material spillage during bulk material operations are several: a careful selection of belt width and speed according to the handled cargo; the installation of belt conveyors and trippers in enclosed galleries; the use of pipe conveyors and enclosed conveyors; the use of gas cleaning and water spray for dust suppression, telescopic or spiral chutes; implementation of eco-hoppers; and the use of different conveying systems, like screw conveyors and chain conveyors.
Besides avoiding spillage and dust emissions, the use of a pipe conveyor makes it possible to get rid of several transfer points between straight conveyors. This solution reduces the consumption of energy need to handle the material, not to mention the energy used for the filters and other suppression systems to lower dust emissions. Fewer transfer point in a plant means fewer chutes, cables and other auxiliary equipment installed, with a positive payback in terms of erection timeline and related environmental cost. Without transfer towers a lot of steel fabrication is saved, as well as foundation works, and erection activities, thus reducing the overall carbon footprint of the plant and its environmental impact.
Moreover, Bedeschi is extremely proud to work closely with its clients in projects that aim to use alternative fuels to limit the use of fossil-type fuels, as well as cutting plant power consumption.
Below are some of Bedeschi’s latest applications to guarantee environmental safeguard and avoid dust pollution:
MELON – CHILE Bedeschi supplied a new eco-hopper to Melon S.A. The unit will operate on the austral port of Punta Arenas, Chile.
The eco-hopper is designed for direct unloading of clinker to trucks at a rate of 600tph (tonnes per hour) and is designed to work with 12m3 grabs. The machine is equipped with pulse-jet bag filters with high filtration capacity and performance and with low compressed air consumption: an economical and flexible solution to satisfy the stringent environmental standards required.
“The eco hopper has been a crucial part of the project, and the results in environmental matters are very satisfactory” confirmed Pedro Pinto, Corporate Technical Manager of Melon.
A set of four bag filters are mounted in the volume between the upper receiving hopper and the hopper main body. The bags are automatically cleaned with a pulse jet system and all the particles removed from the bags simply fall inside the hopper itself. Access platforms are provided for an ergonomic and safe replacing of the bags. A fan outlet with silencer provides noise reduction.
Louise Dodds-Ely
The eco-hopper is equipped with a fully covered feeder conveyor to avoid dust dispersion due to wind action and it maximizes the efficiency of the dedusting filters.
For clinker loading inside the truck, there is a dust controlled telescoping spout. The automatic lifting control keeps the skirt in constant contact with the forming pile, to avoid fugitive dust. An aspiration system keeps the inside of the chute depressurized. Bedeschi’s ecohopper can guarantee to contain and minimize emission during every unloading phase, both from ship to hopper and from hopper to truck, and as a result, the company “has been able to fulfill and exceed the environmental regulations” says Pinto. “The teamwork between Melon and Bedeschi has developed a creative tailormade solution that allows it to operate in a multipurpose port,” he added.
In fact, the eco-hopper is designed with a special support structure that allows a solid anchoring of the hopper to the pier structures during unloading operations, but at the same time it allows the machine to be moved by means of SPMT (selfpropelled modular transporter) when not in use.
This configuration is made necessary by the multi-purpose nature of the Punta Arenas port and due to structural limitations of the existing pier. These operational constraints have forced our engineers to find a winning solution in terms of flexibility of use, weight limitation and structural strength.
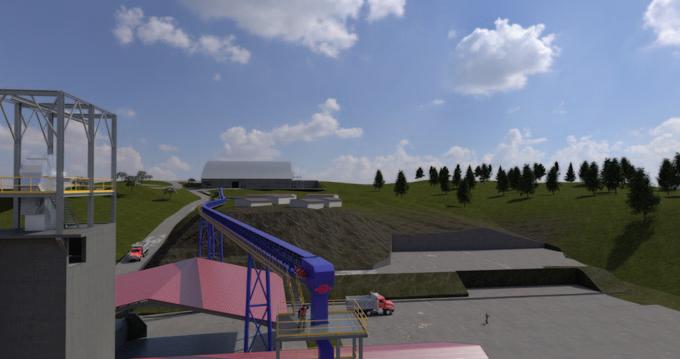
SECIL – PORTUGAL
Incorporating alternative fuels such as waste and biomass to replace fossil fuels, a multi-decade trend in the industry, could reduce emissions by nearly 10% by 2050.
SECIL Group has awarded Bedeschi a contract for the supply of a new pipe conveyor to handle different kinds of alternative fuels at Outão Cement Plant in Portugal.
This project further strengthens the co-operation started with SECIL more than 20 years ago and it is part of the major R&D Clean Cement Line (CCL) project.
The CCL project, aims to bring the Outão cement plant to the forefront of energy efficiency and lowest CO2 emissions among the European cement producers. The project is partly funded by the Portugal 2020 Government incentives programme, and it aims to develop a new concept of cement production. Bedeschi’s supply to SECIL Group will contribute to the elimination of dependence on fossil fuels. The concept of Industry 4.0 will become essential for the plant’s management for improving efficiency and optimizing the processes, therefore a digitalized system will be integrated into the whole plant.
Bedeschi engagement in this project is among the activities implemented by the Italian company to contribute reaching some of the sustainable development objectives, especially environment protection, as established in the Agenda 2030 by the United Nations. For many years, Bedeschi has been working hard in this direction for achieving these goals.
The pipe conveyor with a diameter of 250mm and conveying length of 350m will grant a safe and clean transport ation of alternative fuels at a rate of 300m3/h. Bedeschi will design and supply the complete pipe conveyor system, delivering the structure in pre assembled trans portable modules to allow a smooth and trouble-free erection.
The pipe conveyor solution has been selected for this application as it is a modern and environ mentally friendly transport system solving numerous problems that are associated with conventional conveyor systems (i.e. spillage of materials, limit ations with regard to steep incline and curve layout, etc.) and transportation of difficult materials.
There isn’t one global solution that fits all the stake holders of cement industry, and it will be a long journey to turn it into a green industry. Bedeschi is finding its own solutions to make a positive impact in this process.
Thanks to research and development in green technology, Bedeschi is able to design and produce machines and turnkey installations reaching the highest environmental standards. The company is fully committed to the fundamental aim: guarantying a sustainable model for the future.
3D design of SECIL pipe conveyor.
WE MANUFACTURE IN ITALY TO SUPPLY ALL AROUND THE WORLD CONVEYOR & ELEVATOR BELTS
STEEL CORD & TEXTILE
Via A. Colombo, 144 www.sig.it E-mail: sig@sig.it
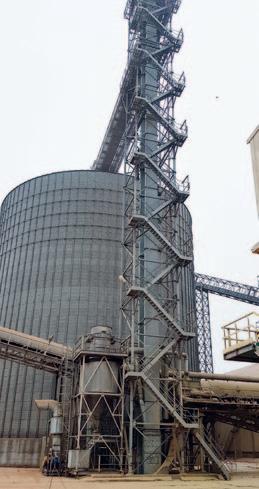
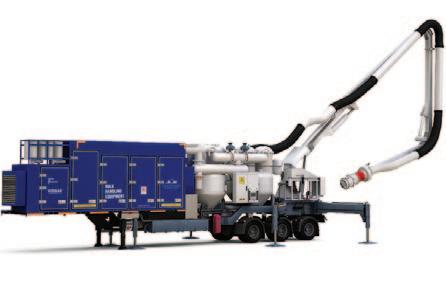
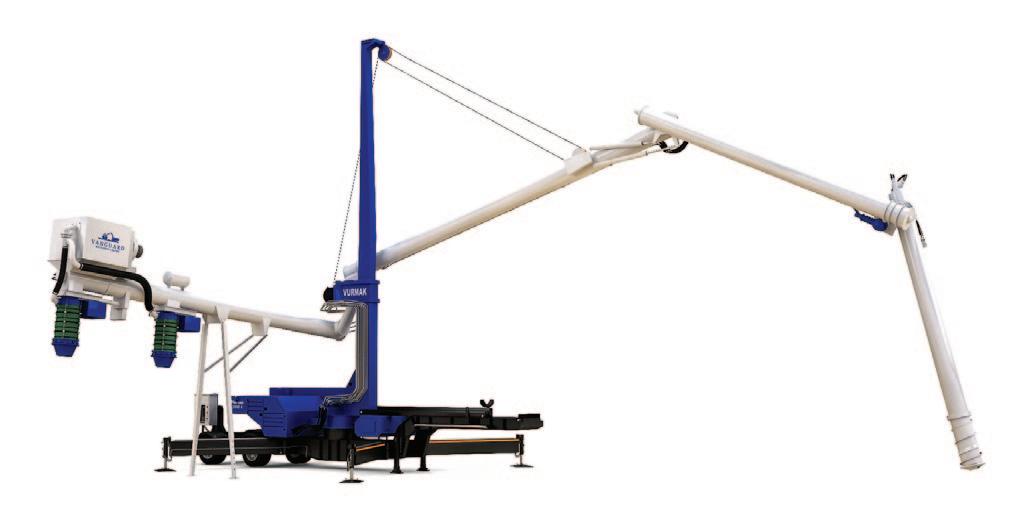
Founded in 1997, Vurmak is a brand that provides cost-efficient, up-todate technological solutions, mainly to the concrete and cement industries. The company boasts a team of 250 personnel, a number that is growing day by day.
Vurmak’s initial product range was confined to batching plant equipment. However, today, the company offers a wider range of equipment, and works as a serial manufacturer for concrete batching plant equipment and a solution provider for cement companies with tailor-made equipment, specifically designed for their needs.
The latest project to be developed by Vurmak’s research and development team is bulk ship-unloaders. These are now operating all around the world, and have become a global success. They aim to minimize the cost of importing bulk material. Vurmak’s vision is to minimize the previously huge burden of initial investment required for such equipment by keeping the same quality of technology and thus not only increasing the profitability of the company’s customers but also, consequently, minimizing the price of products for end-users, especially in third world countries.
As Vurmak Machinery, the company’s product range includes, but it not limited to: a wide variety of concrete batching plants; batching plant equipment; pneumatic conveying systems; mechanical conveying systems; cement packing machines; shiploaders and unloaders; automation and software systems related to cement and concrete production; and storage facilities.
However, a major part of the company’s business is tailor-made systems for cement terminals or terminals themselves. The wide variety of products that Vurmak manufactures, and its expertise in conveying systems, enables it to mix and match different equipment to create complete systems with a central automation system for its partners.
Vurmak also focuses on customers’ needs and limitations to design a system rather than providing rigid, standard machinery. In this way, it creates a relationship with customers that is based on providing solutions and creating win-win situations. This partnership-based model with clients enables Vurmak to select its customers accordingly and lets it focus on the technological advancement of the cement and concrete industry, rather than focusing on short-term profitability. This is why its concrete batching plant automation system is the market leader in Turkey and is enjoying a rapid expansion all around the world. As the global trend for companies shifts to lean manufacturing methodologies, Vurmak is aware that any establishment unable to keep up with this trend is inevitably doomed to fail. However, from the day it was established, Vurmak’s working principle was to provide lean manufacturing methods with its machinery and automation systems to its partners and adapt them itself as well. That is the reason why Vurmak and its partners are thriving in these times of hyper-competitive business environment. The mix of lean manufacturing methods and manufacturing custom equipment, differing from product to product that Vurmak inevitably embraced have created a flexible structure to the company that can adapt to the needs of the contemporary. Also, its expertise in central automation systems — ranging from ERP integrations to CRM services — have created a base that it can adapt to any system. Furthermore, the thorough field experience of its team, matched with its expertise in automation systems, creates an environment of constant product develop ment, with mixer washing machines, cement packing machines, telescopic belts being the newest equipment that Vurmak has developed in the past two years.
However, being able to develop both mechanical and pneumatic ship-unloaders, being able to produce them in sizes that can handle ship sizes up to 50,000dwt, and which are also suitable for any mobility (road mobile, dock mobile, on rails), with
the same level of quality of European competitors, have been Vurmak’s biggest success so far and moved the company recognition to another level.
Finally, the technological and monetary competition with European competitors, especially in the field of handling bulk materials, have created a great competitive environment that Vurmak thrives on.
There is a world-wide shift to accessibility and affordability to these machineries, which aligns with the company vision, and Vurmak takes pride being a vanguard to this shift.
Just as it is with its other equipment, Vurmak has embraced a mix of standard products, such as unloaders that suit all required regulations to travel on road, have a capacity of 150tph (tonnes per hour) and can service 5,000dwt ships, with customtailored products — such as implementing the unloading systems into the cargo carriers themselves with capacities such as 450tph.
In conclusion, the team of Vurmak embraces competition and views it a means of technological advancement, and increased affordability to all its customers, and even, ultimately, the end-user. With its expert team of engineers and developers, Vurmak challenges all its competitors to upmost advancement and it believes that this is the root of its and its partners’ success.
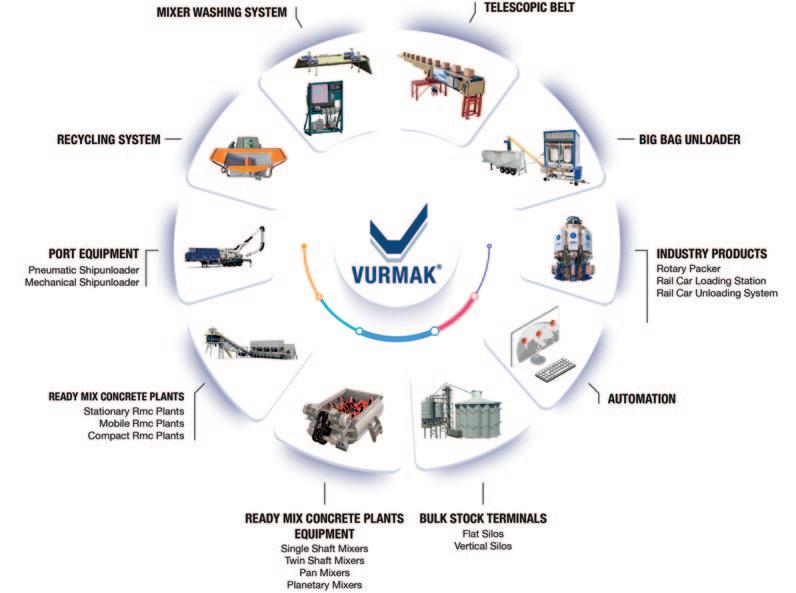
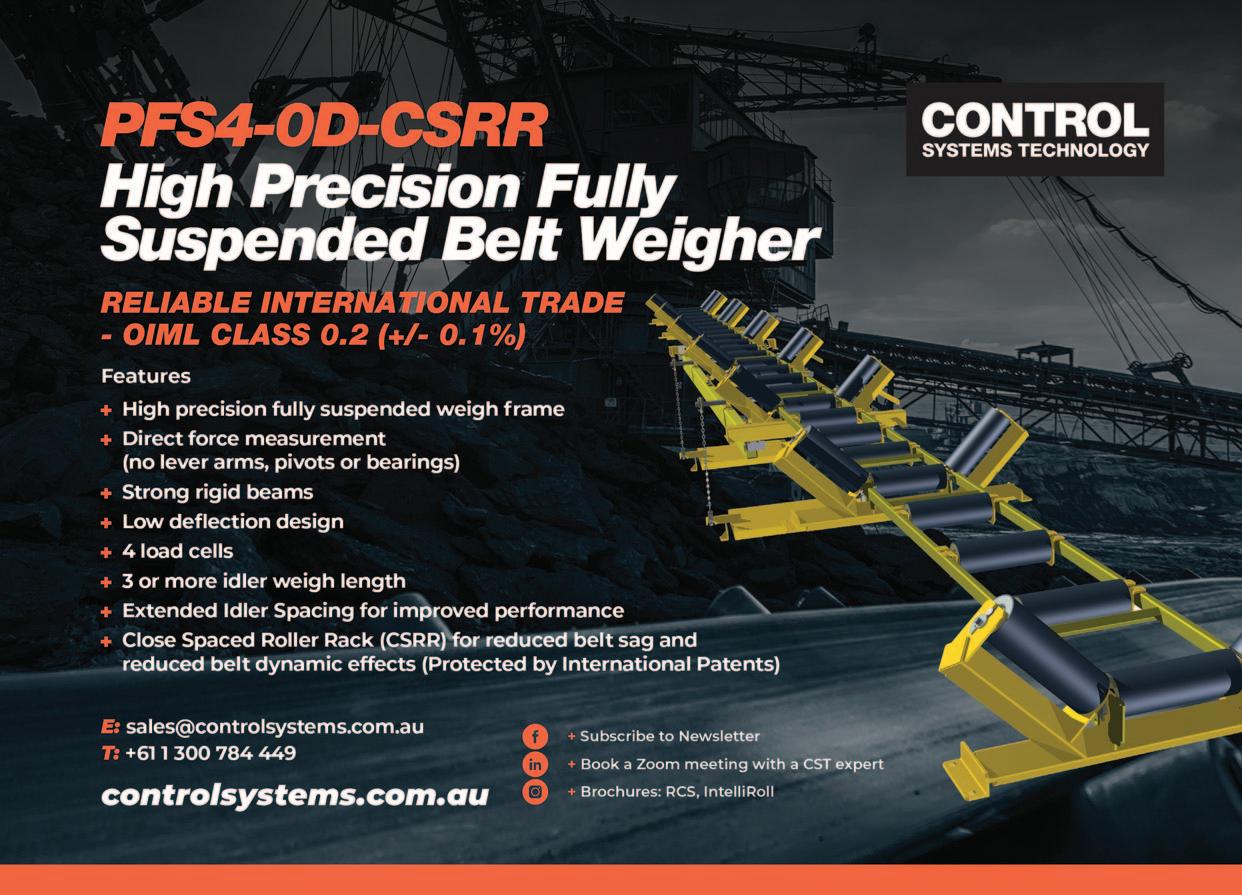
There is no shortage of options for different kinds of screen media available today, writes Lars Bräunling, MAJOR director of product technology. From woven wire to polyurethane and perforated plate, it is possible to equip a screen box with a variety of different types of media. Highvibration screen media has grown in popularity as a way to improve efficiency and virtually eliminate issues like blinding, pegging and clogging. Users must decide if this type of screen media is right for their operations.
Here are a few things to consider:
COST Traditional screen media options — for fertilizer, as well as other commodities — such as woven wire, offer a lower up-front cost. Price alone has historically made woven wire a more popular option. Many mining and aggregates operations are realizing, however, that investing in a more advanced option like high-vibration media, actually saves money in the long-term. This can be achieved through longer wear life, reduced downtime for cleaning and changeouts, increased efficiency and capacity or extended uptime. Often it is a combination of several of these effects.
WEAR LIFE High-vibration screen media and other specialized designs tend to offer a much longer wear life than traditional options like woven wire. Woven wire and some types of self-cleaning media have cross wires that are subject to high-wear spots, leading to a shorter wear life. Alternatively, highvibration screen media uses highly engineered wires held together with polyurethane strips, eliminating the need for cross wires. The design extends wear life by as much as five times longer than traditional screen media, while also optimizing open area.
BLINDING, PEGGING & CLOGGING Issues like blinding, pegging and clogging hamper an operation’s profitability potential. While some screen media is tapered to try to mitigate these problems, their design often limits the extent to which they can resolve severe issues. The independent wires in FLEX-MAT cause high frequency vibrations from hook to hook that magnify those produced by the screen box. This virtually eliminates pegging, blinding and clogging, and reduces risk of material contamination.
Better screening performance often depends on open area — a factor limited with traditional screen media. Highvibration screen media offers as much as 30% more open area than woven wire, and 50% more than polyurethane or rubber panels, enabling more material to be sized accurately in less time.
EFFICIENCY Screen machines are a vital contributor to a plant’s productivity when they are operating efficiently. However, poor screening creates challenging bottlenecks that hold back the entire operation and reduce production volume. Certain screen media options actually amplify the screening process to offer unparalleled efficiency.
High-vibration screen media, for example, operates at an intense frequency— up to 8,000 to 10,000 cycles per minute. That’s 13 times the vibration frequency of a standard screen box. This enhanced vibration accelerates the material stratification process, sending fines to the screen surface quicker and maximizing contact with the screen surface to improve throughput and eliminate carryover. So not only is material moving through the plant faster, the result is also a cleaner product with less risk of material contamination.
FINDING THE RIGHT FIT When it comes to screen media selection, there is a lot to choose from, but more and more aggregate and mining operations are finding that high-vibration screen can take their production to the next level.
Screen manufacturer MAJOR has all the information on FLEX-MAT high-vibration screen media, and where it can fit in an operation.
ABOUT MAJOR
MAJOR is an innovative global manufac turer of wire screens for the aggregate, mining and recycling industries. FLEX-MAT®, the company’s renowned line of distinctive lime-green high vibration screens made with OPTIMUMWIRE® ‘The longest-lasting wire’ sets a high standard in lowering the cost of production per tonne by dramatically increasing throughput and wear life while eliminating blinding and pegging. MAJOR masters wire quality, screen manufacturing and the screening process, and provides onsite screening performance assessment and training seminars on screen maintenance and screening efficiency to help producers increase their screening performance and profitability. MAJOR is a Haver & Boecker company.
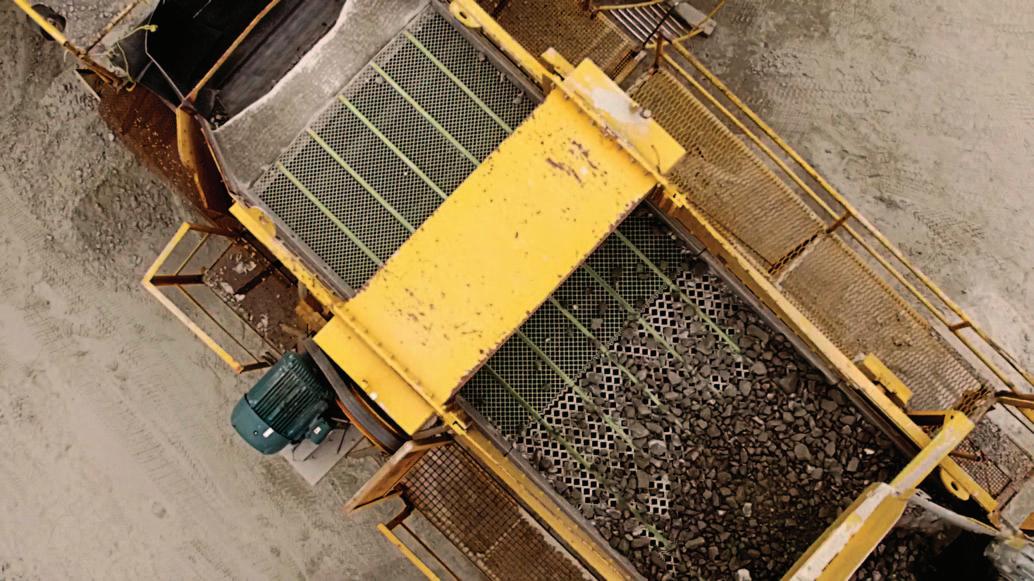
ENGINEERING & EQUIPMENT Declogging inside silos: the Airchoc® 6 solution simplifies maintenance and spare parts costs
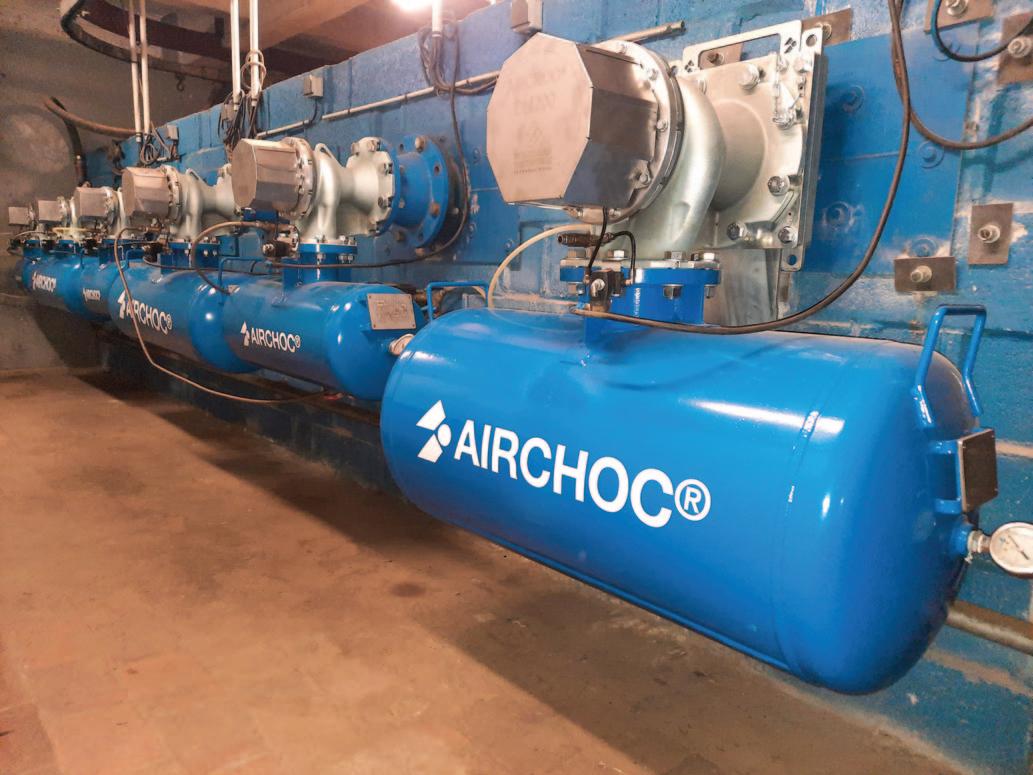
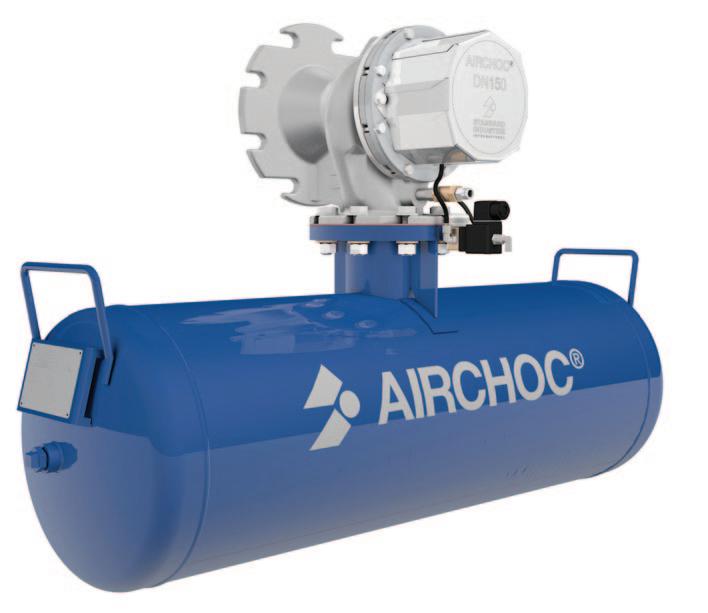
AIRCHOC 6 new range on the test bench at STANDARD INDUSTRIE.
Created in 1978 by the French company STANDARD INDUSTRIE International, the AIRCHOC® is an air cannon that is placed preventively on raw material storage units. Thanks to regular shots, it makes it possible to avoid production stops due to material accumulation. The unit is particularly appropriate in cement handling operations. The AIRCHOC® is a cost-effective maintenance solution that uses 6 bar compressed air only when the shots are activated. It is suitable for use with many bulk commodities, including cement.
STANDARD INDUSTRIE International’s technical teams study an optimal installation recommendation according to the clogging factors and the environment of use (risks, high heat zone, corrosiveness, humidity).
Particularly attentive to its customers’ requirements, the design office team spent nearly three years testing modifications to its legendary
AIRCHOC® air cannon, with the following results: v the quick exhaust valve was replaced with a pneumatic valve system that improves impact force; v the silencers have been replaced by a protective cap which, in addition to protecting the new valve system, absorbs the noise caused by the shots.
The main advantage is that there is no risk of clogging in the exhaust system; and v as these two wearing parts (quick exhaust valve + silencer) are removed
AIRCHOC®AC615 + Solenoid valve.
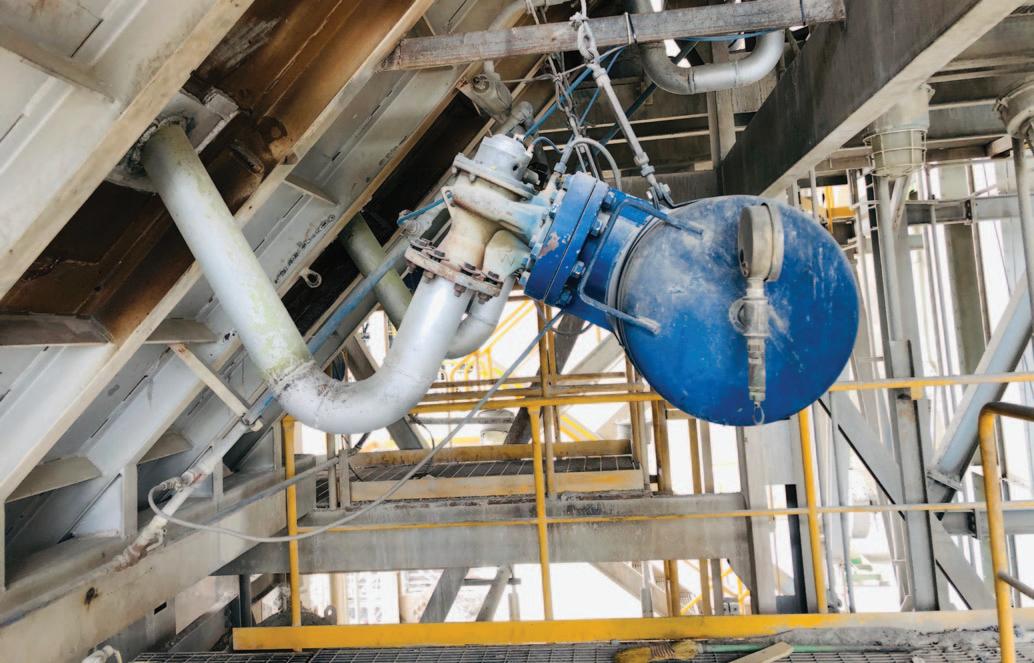
from the design, maintenance is simplified and less expensive for the user.
THE BENEFITS OF THE NEW VERSION OF THE AIRCHOC® AIR CANNON The AIRCHOC has always had the performance, profitability and safety characteristics expected by user customers. The latest innovations of the AIRCHOC® version 6 are focused on: v Compressed air savings: thanks to a better sealing of the piston and to a better impact force on the clogging (10% higher than the old version).
Indeed, the air pressure can be reduced for an equivalent result. The version 6 of The AIRCHOC® meets the challenges of the global energy saving policy. v Reliability: particularly due to an improvement of the impact force of the shots coming from the cannon. (No quick exhaust valve): No air passes through the piston seal, thus no wear and tear on the seal. This means that the air cannons are always available for preventive shots and thus maintain the production flow. The tests guarantee three years of shooting cycles without replacement of the triggering system. v Spare parts: these have been streamlined and selected for their durability.
The new design of the AIRCHOC® with fewer wearing parts and components ensuring good resistance, allows for reduced and simplified maintenance. This is a considerable advantage when maintenance operations require access at height and important safety precautions.
In this regard, STANDARD INDUSTRIE has also created an AIRCHOC® maintenance kit that avoids operators and foremen from having to perform lengthy and costly interventions.
Here again, STANDARD INDUSTRIE is responding to the need to save on maintenance and spare parts for large consumers such as cement plants.
In summary, the AIRCHOC® is the solution for plants that want to reduce maintenance and spare parts replacement on their cleaning system, and reduce their compressed air consumption.
The first few customers already benefiting from the AIRCHOC® improve ments are very satisfied, as testified by Abraham Campos Figema, Maintenance Manager of the cement plant Cementos Fortaleza in Mexico.
Since 2020, this customer agreed to test the prototype of the new AIRCHOC® 6 air cannon head created by STANDARD INDUSTRIE International and placed in the plant on the kiln inlet.
After two years of use in the research and development of this product, the customer has answered the following questions: Q: How much maintenance time do you save with this new AIRCHOC® head compared to the previous version 5 over one year of operation? A: 24 working hours per year and less risk of intervention on the hot equipment. Air cannon installed for a test on the kiln inlet of Cementos Fortaleza.
Q: How many maintenance kits for the quick exhaust valve have been saved in one year? A: 24 maintenance kits. Q: What do you think about the reliability of this new development (ACCMECBRD610) for the future? A: The reliability is very good because there was no maintenance for one year. Q: Have you noticed a difference between version 5 and the new prototype, what do you think about the power (impact force) of this head compared to the previous one? A: Of course, the head is much stronger than the previous one. The impact force is good for the area where we placed it, which is the hottest area of our system. Q: Do you need a more powerful conical head to reduce the pressure level of the compressed air and save energy and money? A: Of course, saving compressed air means saving energy and therefore money. Q: Do you have any other comments on your experience? A: Yes, it is good that there are developments to increase the reliability of this equipment because it mitigates the risk of having personnel working on hot equipment. Congratulations!”
STANDARD INDUSTRIE International has succeeded in offering a solution that is both efficient and economical. Relying on its proven expertise with many bulk manufacturers around the world, the company is committed to offering reliable and durable ‘made in France’ equipment to ensure that its customers maintain their productivity.
Keeping cement conveyors clean with K-Rotabrush® Conveyor Belt Cleaner from Kinder Australia
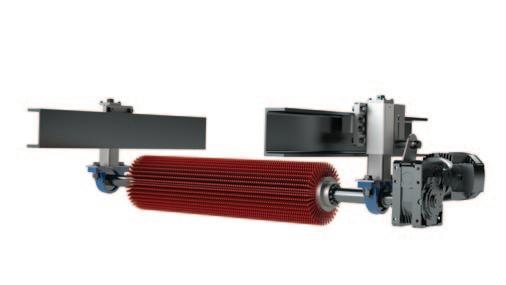
For stubborn material carryback, the K-Rotabrush® conveyor belt cleaner is an ideal solution to ensure excess fugitive material will be effectively removed from the underside of the return belt.
Carryback build up on conveyor hardware — especially during cement handling operations — can cause belt mistracking, as well as conveyor belt and structural damage. Material spillage may occur, which presents a potential slipping and tripping hazard. Fugitive material can also bury idlers, conveyor components, or structural supports — this requires expensive clean-up labour and replacement parts.
K-Rotabrush® will provide thorough cleaning, without compromising belt wear.
The rotary action of nylon, rubber or polyurethane bristles, sweeps wet, dry, sticky, hydroscopic, statically charged and abrasive conveyed materials off the conveyor belt. It is suitable for difficult applications such as salt, sugar, fertilizer, timber as well as cement/clinker.
The K-Rotabrush® conveyor belt cleaner is well suited to areas where space limitations apply. Often carryback occurs in awkward spaces that are difficult to safely reach; any manual labour allocated to remove the carryback is at risk of injury. The compact K-Rotabrush® will take care of the cleaning safely and effectively. It is simple to install, and maintenance is minimal.
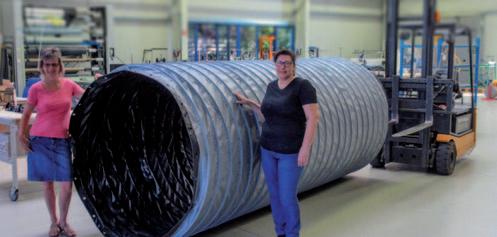
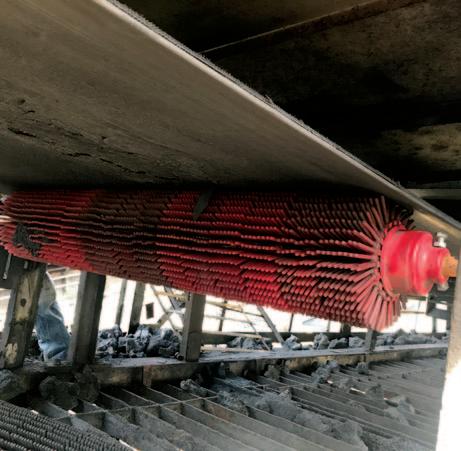
VERLADESYSTEME FÜR SCHÜTTGÜTER
We make sure that nothing gets lost!
For over 50 years, our loading systems for bulk materials have been synonymous around the world with long-lasting and reliable technology.
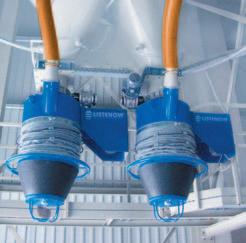


Replacement loading hoses +49 7152 50900
› Bulk loading systems for open and closed loading › Loading with no segregation e.g. with FLOW-stop technology › Dust-free loading › High quality loading hoses e.g. made in wear-resistant PU-flex › Positioning System LIS-pos › First-class service:
Start-up and installation
Revision and repair services
System maintenance, modernisation and upgrading › more informationen at www.listenow.com
LISTENOW GmbH & Co
Dieselstrasse 21 71277 Rutesheim / Germany +49 7152 50900 listenow@listenow.com www.listenow.com
ENGINEERING & EQUIPMENT
Medcem Madencilik: 41 AUMUND machines for the second kiln line
Medcem, which will increase its capacity by 90% in the first quarter of 2023, will be among the largest cement factories in the world (photo: Medcem Madencilik).
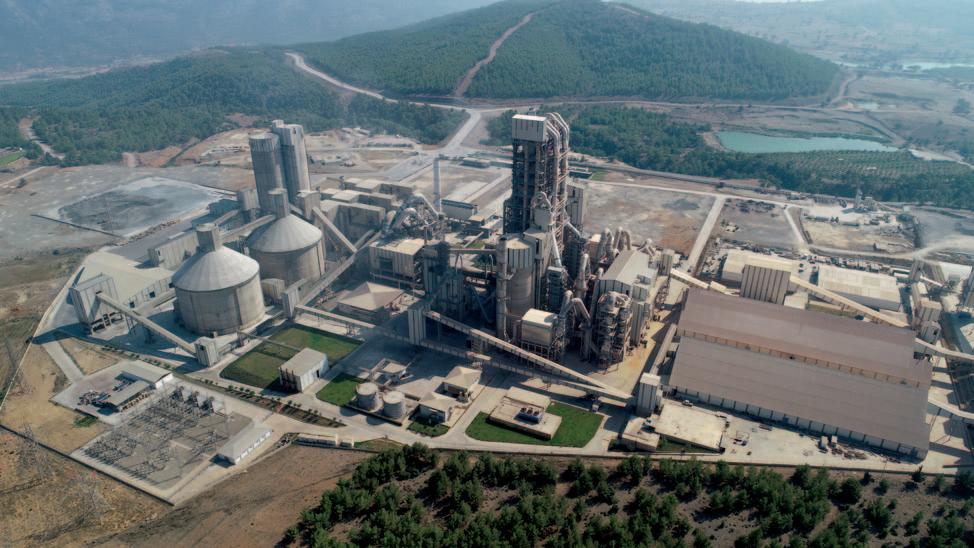
Before the end of the year AUMUND Fördertechnik GmbH, Rheinberg, Germany, will supply 41 machines for a new kiln line at the Medcem Madencilik cement plant in Silifke in the Turkish province Mersin.
The AUMUND supply package comprises six belt bucket elevators, two bucket elevators with central chain, four pan conveyors and eleven drag chain conveyors. The conveying capacities range from 50 to 900tph (tonnes per hour). The machines will be used for feeding material to the raw mill, the raw mill silo, the coal mill, the heat exchanger and the cement silo. The order also includes 13 silo discharge gates for belt conveyors and five telescopic chutes for truck loading.
Commissioning is expected to be carried out in January 2023.
AUMUND had also equipped the first kiln line at the Medcem Cement plant with various machines, commissioned in 2015. Medcem Madencilik ve Yapı Malzemeleri San. Tic. A.S. started construction on the second kiln line in August 2021, and when completed it will increase annual clinker production capacity from 3.5 to 6.5 million tonnes. According to Medcem, this makes it one of the largest cement plants in the world.
ABOUT THE AUMUND GROUP The AUMUND Group is active worldwide. The conveying and storage specialists has special expertise at its disposal when dealing with bulk materials. With their high degree of individuality, both its technically sophisticated as well as innovative products have contributed to the AUMUND Group today being a market leader in many areas of conveying and storage technology. The manufacturing companies AUMUND Fördertechnik GmbH (Rheinberg, Germany), SCHADE Lagertechnik GmbH (Gelsenkirchen, Germany), SAMSON Materials Handling Ltd (Ely, Great Britain), TILEMANN GmbH Chains & Components (Essen, Germany) as well as AUMUND Group Field Service GmbH and AUMUND Logistic GmbH (Rheinberg, Germany) are consolidated under the umbrella of the AUMUND Group. The global conveying and storage technology business is spearheaded through a total of 20 locations in Asia, Europe, North and South America and a total of five warehouses in Germany, USA, Brazil, Hong Kong and Saudi Arabia.
Advertising is important!
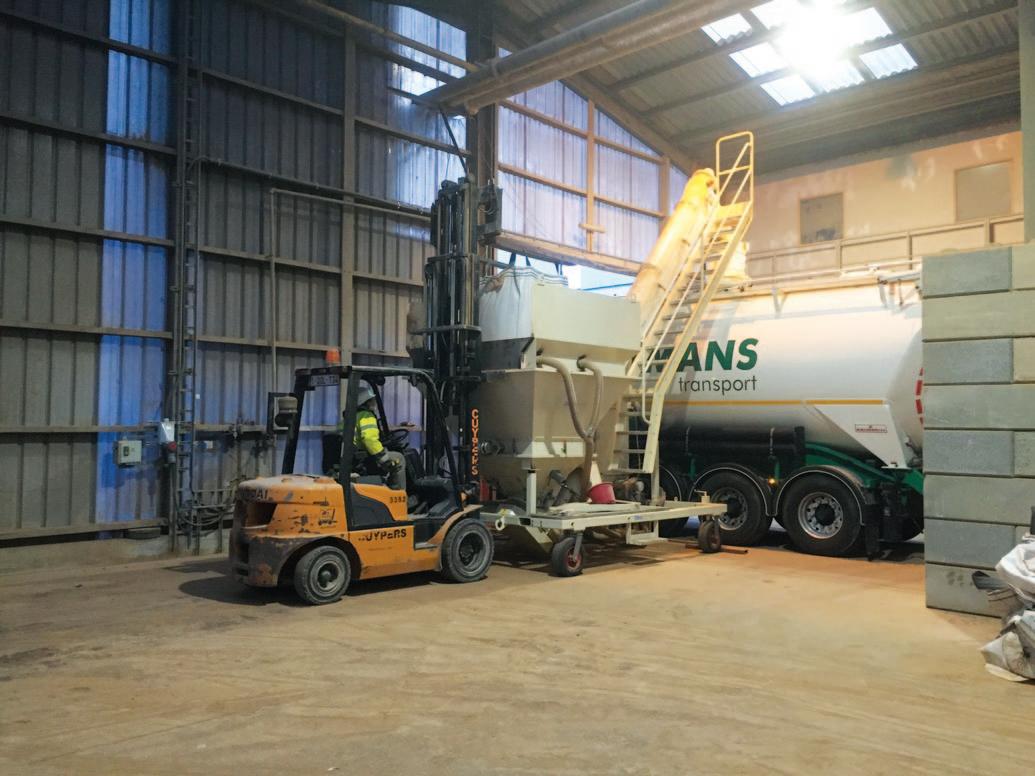
The Dino DS400 Cement from Van Beek has been adapted for loading big bags of cement and cement-like products such as limestone, soda ash and bentonite into bulk trucks.
The Dino Cement has a capacity of 80m3/hour, where the capacity of a standard Dino is 40m3/hour. The inlet hopper is fitted with a crossor U-shaped blade so that a forklift truck driver can pour in the bags quickly, safely and easily. He does not have to get out to cut the big bag open and can immediately fetch the next big bag. This means a bulk truck can be filled within 30 minutes.
On the inlet hopper is a screening deck with vibrator. This separates the large chunks and lumps from the cement powder. The vibrator breaks down the chunks so that they can flow freely. The inlet hopper itself is fitted with fluidizing pads. These spray air into the product and create an ‘air film’ on the inside of the inlet hopper so that the product can flow into the screw more easily.
Van Beek’s standard models offer an immediate solution to suit most situations. Many decades of experience have shown that a specific challenge often requires a customized Dino, something Van Beek understands better than most. Its sales engineer works together with the customer to assemble a bespoke Dino, configured to meet specific loading operations.
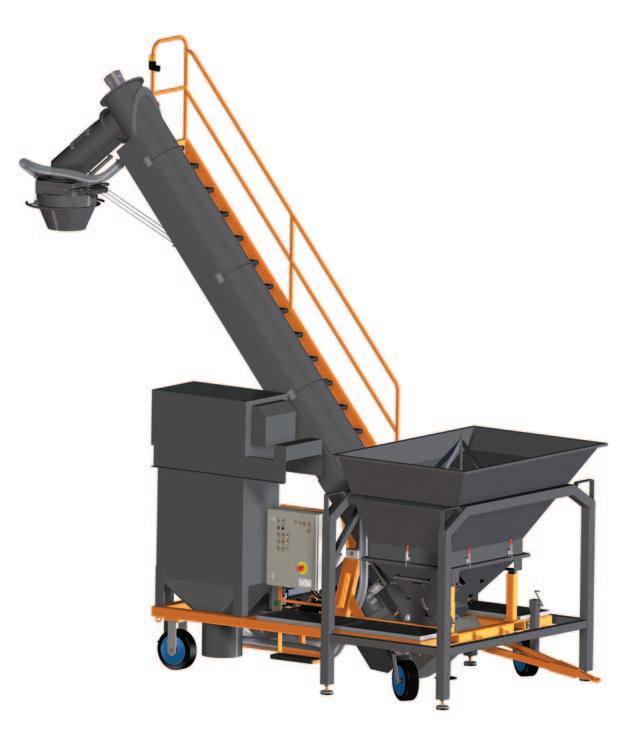
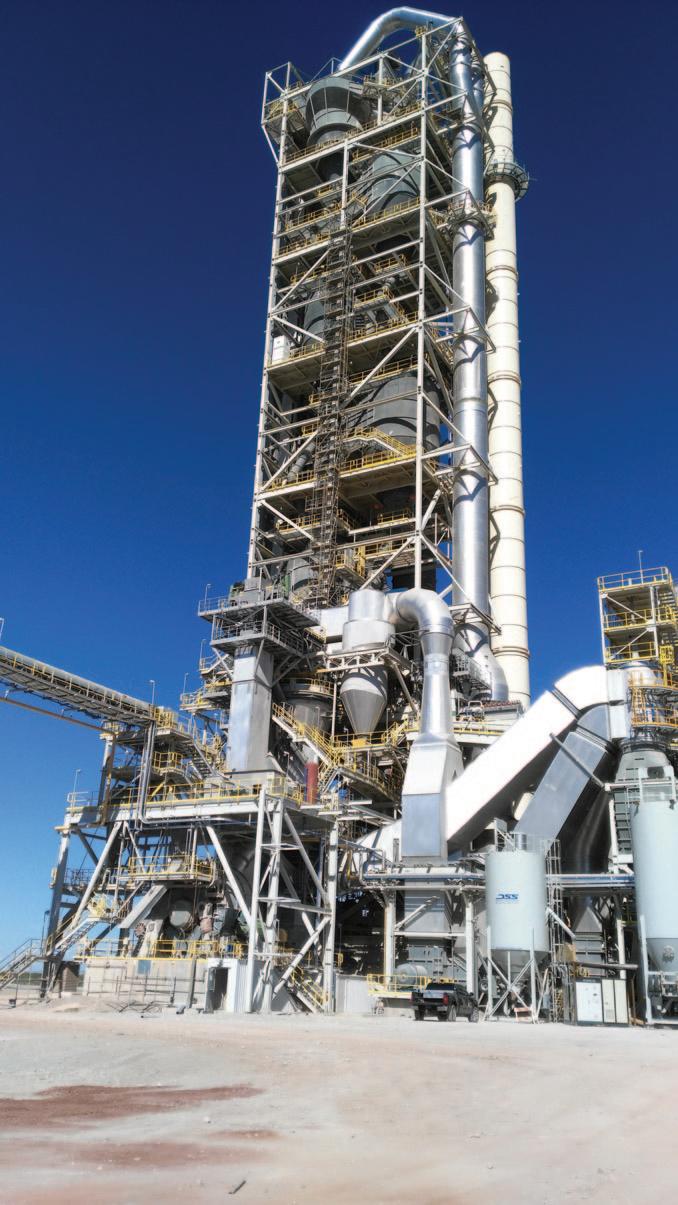
GAMBAROTTA GSCHWENDT: the state of art for super-capacity chain bucket elevators
Since 1919 GAMBAROTTA GSCHWENDT has been developing and manufacturing loads of bucket elevators for lifting a wide range of bulk solid materials.
Thanks to its continuous research and development effort and to the quality of its equipment, addressed to their maximum reliability, GAMBAROTTA GSCHWENDT maintains a good position among the leading manufacturers of this sector.
This article focuses on one of GAMBAROTTA GSCHWENDT’s bucket elevators — the ESPLV.
The ESPLV is a double-chain bucket elevator that can be considered one of the most modern among heavy-duty elevators providing the highest flow rate: 2,000m3/h and higher.
The large-sized buckets are one of the main features, with a capacity up to 290 litres each on the largest elevators.
Mechanical chains have pin and bush, also designed for very high breaking loads (up to 4,000kN).
Thanks to the continuous buckets, these GAMBAROTTA GSCHWENDT bucket elevators have great flexibility allowing both slow and high speeds. They are perfect when a low speed is required (less than 0.7m/s), as in the case of lifting granular fertilizer material or for lifting mediumsized materials (50–100 mm). Never theless high speed is possible too (>1.5m/s) in order to minimize the size — and therefore the cost — of the bucket elevator required.
When speeds lower than 0.8–0.9m/s are required, the material discharge, although external to the trajectory of the buckets, occurs due to the combined effect of centrifugal force and gravity, with the material flowing on the back of the preceding bucket, thanks to the continuous bucket system. Therefore, when the material is being discharged, the back of each bucket acts as a ‘slide’ for that part of the material that is forced to follow a less effective expulsion trajectory due to insufficient centrifugal force.
This allows an easy discharge through the outlet chute.
When lifting granular fertilizer, low speed is used to minimize the crushing of the granules and the level of powdering, which is essential to guarantee a good product quality.
Low speed also allows the buckets to load (partly with dredging) and lift materials with larger grain sizes, up to 80–120mm.
When speeds exceeding 1m/s are allowed (the most frequent case) — usually up to 1.5-1.6 m/s — it is possible for the highest flow rate of material to be lifted. In this case the material is usually discharged centrifugally. A hydraulic tensioning system is frequently used for tensioning the chains, thus allowing for high loads (if necessary) as well as easy and uniform adjustment of the chains.
The larger GAMBAROTTA GSCHWENDT bucket elevators are equipped with double drive unit (see pictures 2 & 3).
CASE STUDY In the cement industry this type of GAMBAROTTA GSCHWENDT supercapacity bucket elevator is used to lift a wide range of bulk materials such as clinker,
Picture 1: ESPLV in Maryneal, Texas, USA.
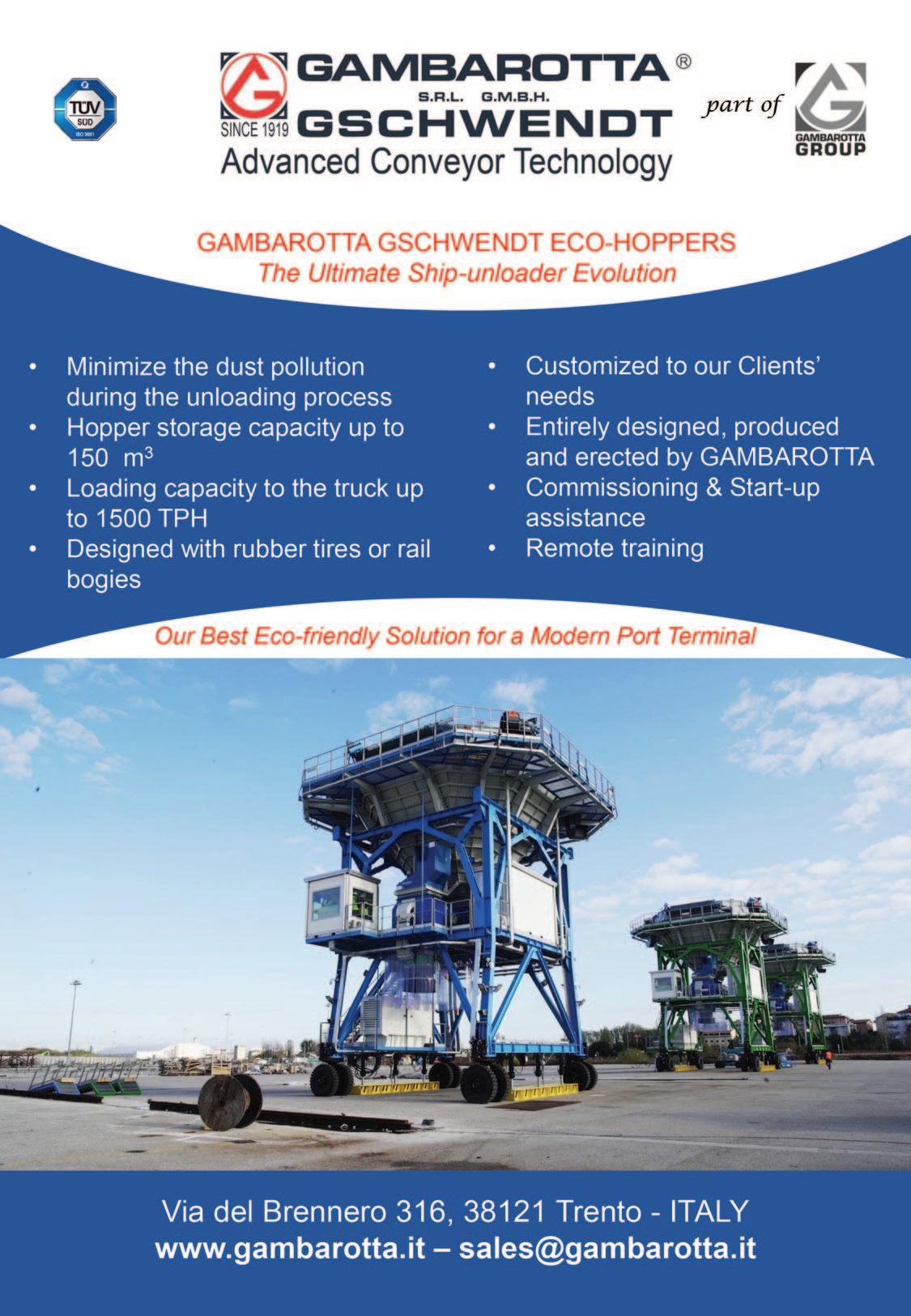
Ship unloaders
Road mobile ship unloaders
Storage & reclaim
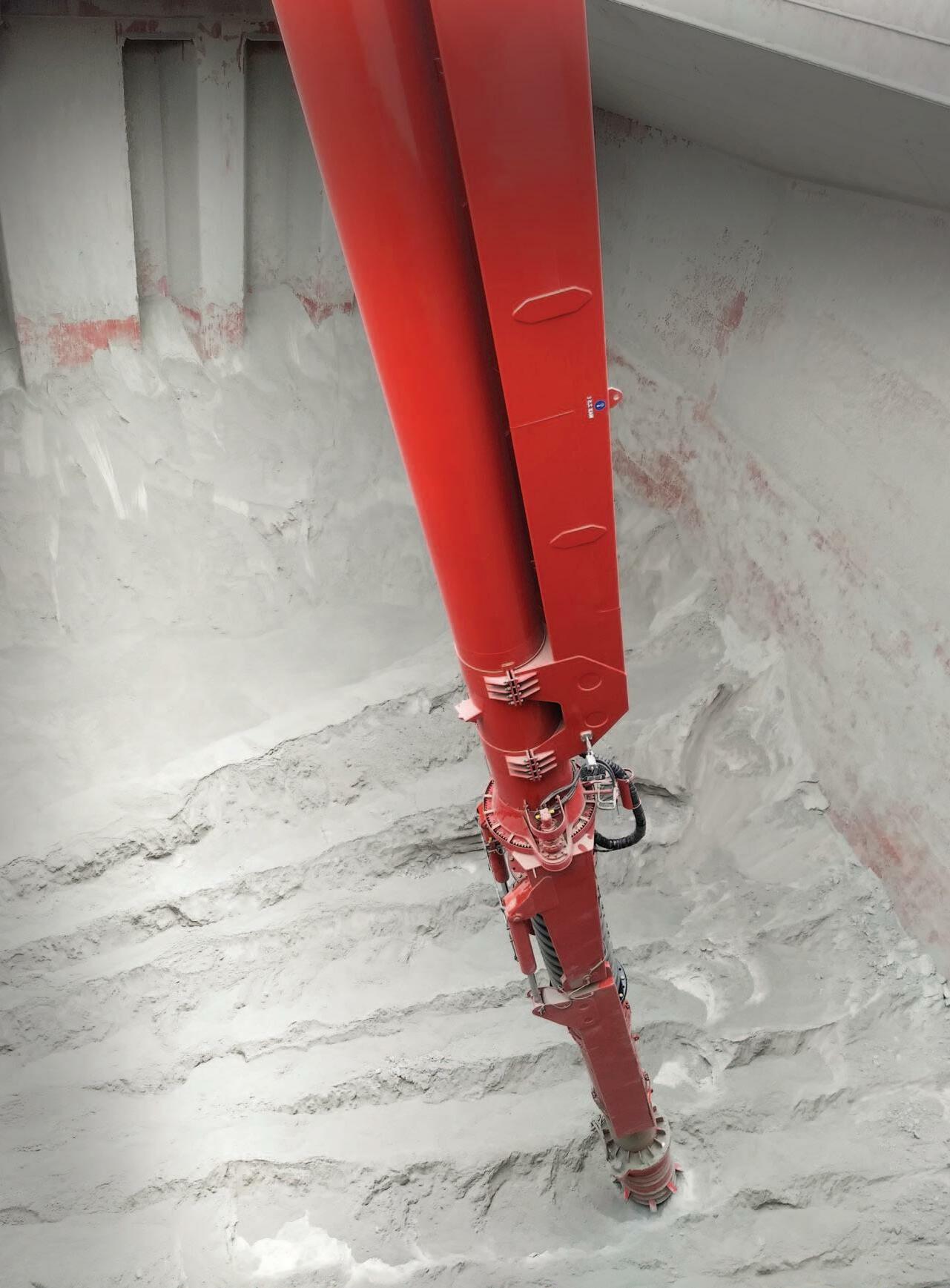
Convey units
Truck loading
Ship loaders
The answer to your bulk handling questions
raw meal, raw mix, limestone, cement, coal, to name a few.
Recently GAMBAROTTA GSCHWENDT was awarded an order from DYPNF, South Korea, for the supply of a super-capacity bucket elevator, with a length of 50.6m.
This GAMBAROTTA GSCHWENDT elevator lifts petroleum coke (100mm max) at a speed of 1.3m/s and thanks to its two lateral bushed chains, which have a breaking load of 1,500kN each, is the best GAMBAROTTA GSCHWENDT solution to serve this purpose. Pictures 2 & 3: GAMBAROTTA GSCHWENDT ESPLV head stations equipped with double drive.

Picture 3.
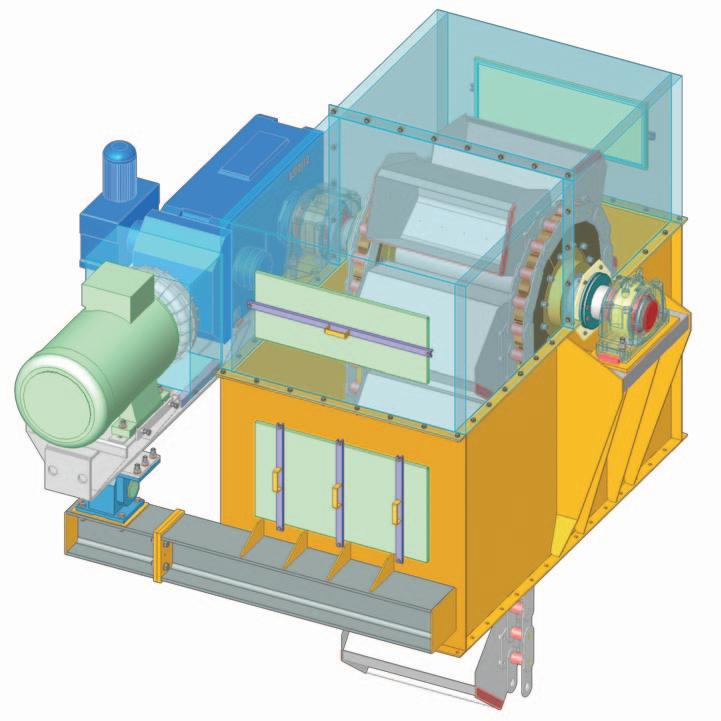
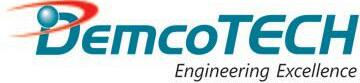
Picture 4: ESPLV wheels.
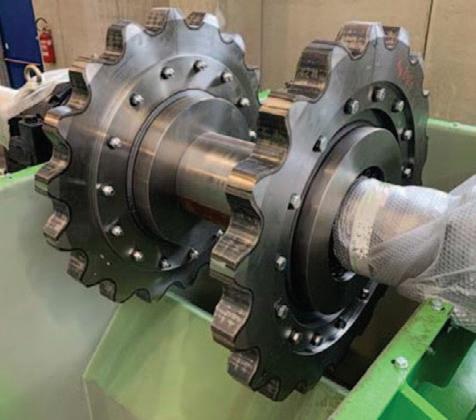
Picture 5: ESPLV chains.

Engineering Excellence
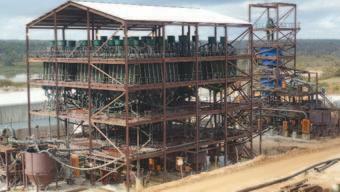

Leading Specialists in Bulk Materials Handling, Niche Process Plants, and Conveyor and Stockyard Design Servicing the Power Generation, Mining, Metallurgical, Cement, Manufacturing and Port Handling Industries Strong reference list in Africa, SE Asia and South America, and in India, having partnered with M/s METHODS India From Concept Design to Project Completion
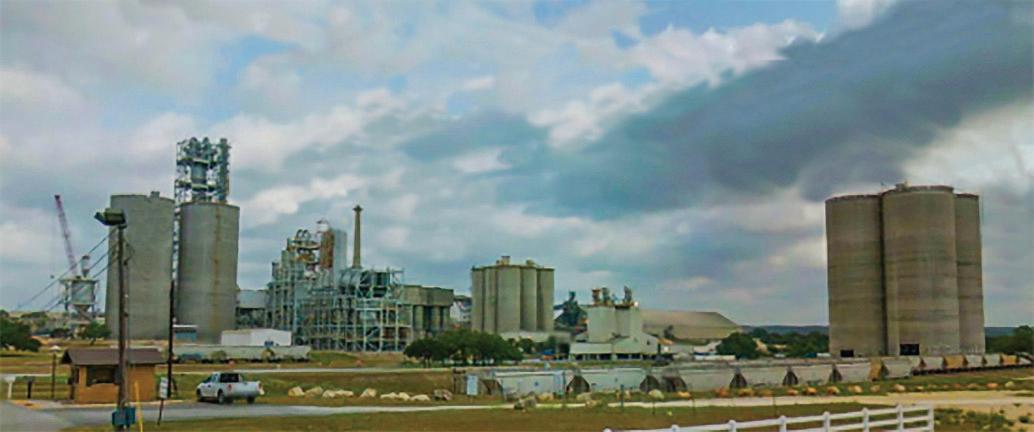
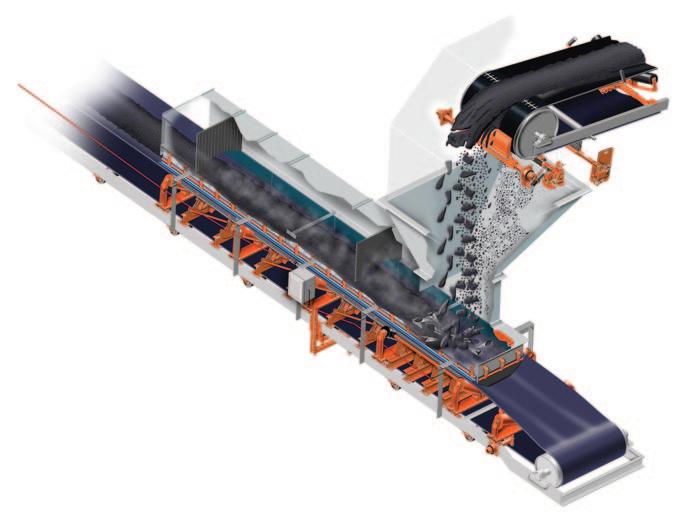
Texas cement plant.
For thousands of years, cement production has heated the constituents used in the mix to the highest temperatures possible to remove impurities, writes Byron Allen, Service Technician/Martin Engineering. Today, meal or raw material for Portland cement is calcined in a ~2000°F (~1,000°C) degree kiln, akin to dropping it into the centre of an active volcano. Although the material is run through a cooling process afterward, the light friable aggregate is still hot enough to burn through regular conveyor belting, high heat personal protective equipment (PPE), or pretty much anything else it encounters.
The presence of hot material has long made safety a priority for cement plant operators. However, regardless of the safety measures protecting individual workers, mitigating buildup and spillage in the hottest parts of the production process to avoid clogging and downtime is largely considered the least desirable job in the entire plant.
Safety personnel at a cement plant in Texas raised attention to a transfer point leading from the cooling process to the tripper conveyor in the clinker barn. The transfer point struggled with excessive spillage of hot material and posed a potential risk to workers.
TEXAS CEMENT PLANT “The transfer point in the clinker barn was an issue we’d been trying to address for a while,” said a source close to the project. “Our goal was to reduce the amount of maintenance needed for repairs and cleanup in the area. Unscheduled downtime, increased labour and product loss were raising the cost of operation. By making the system more efficient, we would also improve safety around the transfer point.”
FROM KILN TO STORAGE Processing approximately 200tph (imperial tons per hour) [181.4 metric tph] of raw meal, when the molten clinker rolls out of the kiln, it is loaded onto a pan conveyor consisting of several high heat metal pans pulled by a chain. Cold air cools the cargo quickly, reducing it from nearly 1,400°F (760°C) degrees to a temperature range of between 350–800°F (176–426°C).
Once the clinker is cooled, it’s dropped through a 5ft (1.5m)-long sloped chute onto a high-heat belt attached to a tripper conveyor that is suspended 80ft above the massive piles along the length of the airplane hangar-sized clinker barn. With a length of 1,100ft (335m) and a width of 24 inches (610mm), the belt conveys material at 260ft/m (1.32m/s) toward the tripper discharge chute.
Moving slowly back and forth along the entire length of the barn, the tracked tripper system discharges chalky clinker through a chute onto tall piles for storage. However, the stored material does not stay long, being constantly moved by front loaders to different sections of the plant as needed.
“This is a 24-hour operation to meet the demand of our customers,” said the source. “When there’s a problem with the clinker tripper conveyor, it needs to be addressed right away or it could hamper production.”
FEELING THE HEAT Several issues contributed to safety concerns. The original transfer point from the pan conveyor to the tripper had some problems with sealing. Hot fines would spill out the sides and collect on the walkway around it. In addition, backups in the transfer chute often stopped production until they could be cleared.
Access was also a challenge. The outdoor staircase goes up eight storeys to an operations platform, which can be a daunting climb, especially in the Texas
The original transfer point had serious spillage issues (© 2022 Martin Engineering).
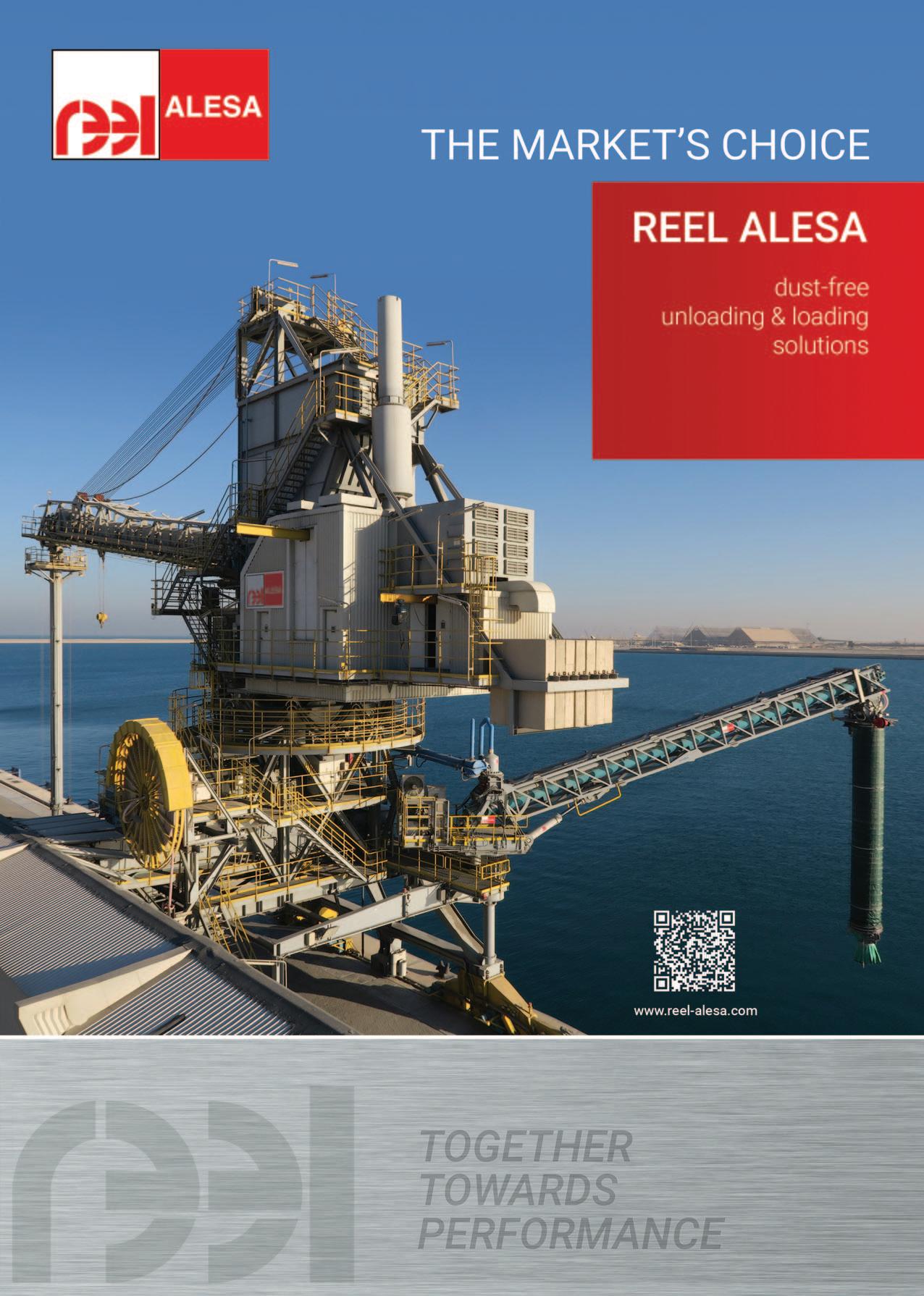
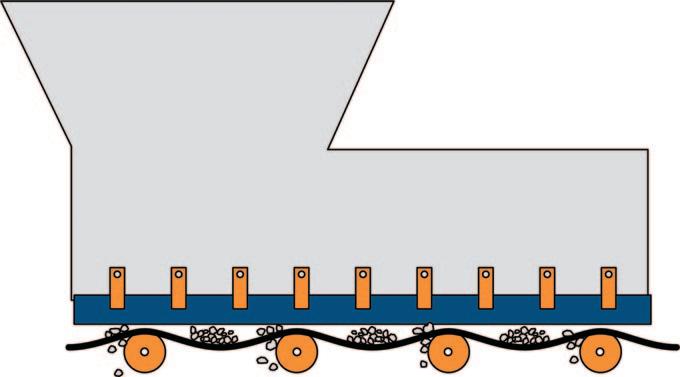
summer. Once staff has reached the transfer point, the temperature rises due to the clinker. Manually clearing the transfer chute carries the possibility of direct contact with the hot material, so it’s important that a trained employee with an air lance or CO2 blasting device perform the cleaning while wearing high-heat PPE.
To capture some of the spillage, there was a 3x5ft (0.9 by 1.5m) grated shaft installed on the platform under the transfer point. It leads down a chute and adds the product to the storage pile below. This was intended to mitigate worker contact with the material and shore up some production losses associated with the spillage. However, excessive fugitive material still piled around the platform, creating a potential hazard that needed to be removed often.
Even scheduled maintenance imposed both safety and cost concerns. Contractors were brought in approximately twice per month to clean the area. A crew of four to five workers with a vacuum truck would remove the debris. This cost the plant as much as US$15k to $20k per month, depending on the scope of the job and the number of times the crew needed to come in.
EQUIPMENT STRUGGLES The punishing environment of this transfer point had a profound effect on the equipment. Idlers would regularly seize or break due to warping from the heat, the weight of the cargo, or fines getting into rolling components such as bearings. The belt would also wear quickly, forming holes or even breaking at the splice.
When an idler seizes, it causes friction and excessive heat on the return side (bottom) of the belt. Friction can cause the belt to quickly degrade and fray at the edges. If left unnoticed long enough, it can erode mechanical splice attachments, causing the splice to break. Although the belt might be high heat graded on the cargo side, the return side is likely more vulnerable, which can potentially lead to fires.
The impact idlers were of particular concern, because they were the most likely to freeze from impact damage and warping due to constant heat exposure. The gaps between idlers would often allow dents and cracks to form on the protected side of the belt. These damaged spots would succumb to the heat and quickly become holes. Due to the high cost of belt replacement, operators would leave the holes, adding to
Poor belt support allowed fugitive material to collect on idlers, causing premature failure (© 2022 Martin Engineering).
The large hole and the warped grate indicate the extreme heat emitted by the system.
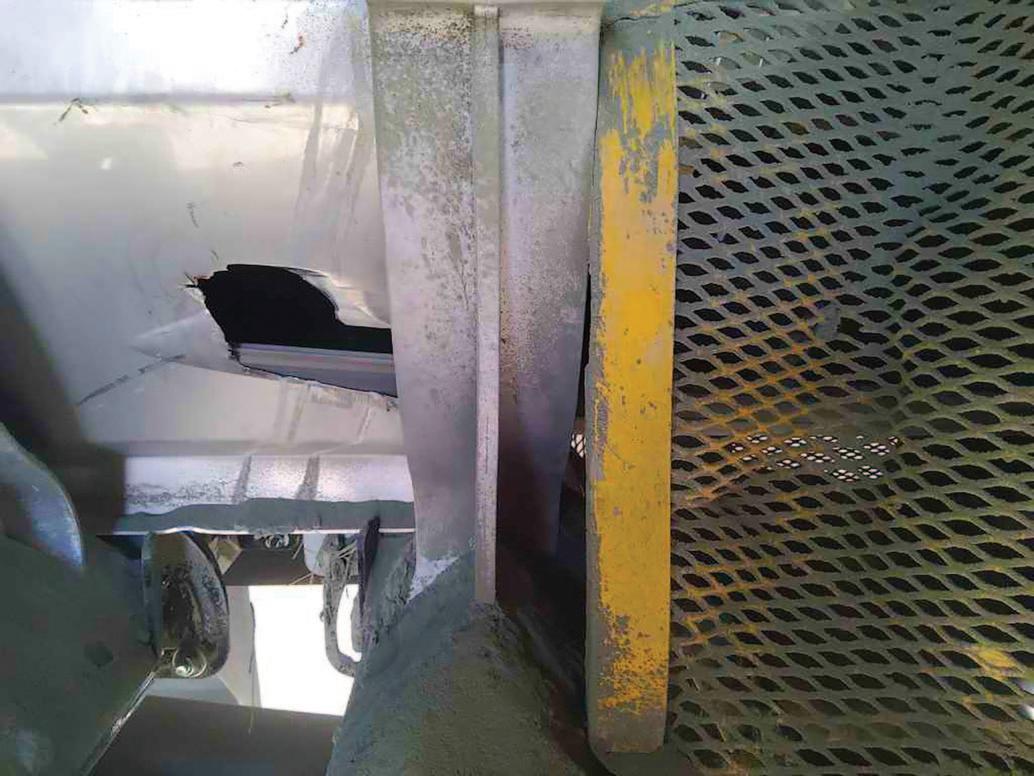

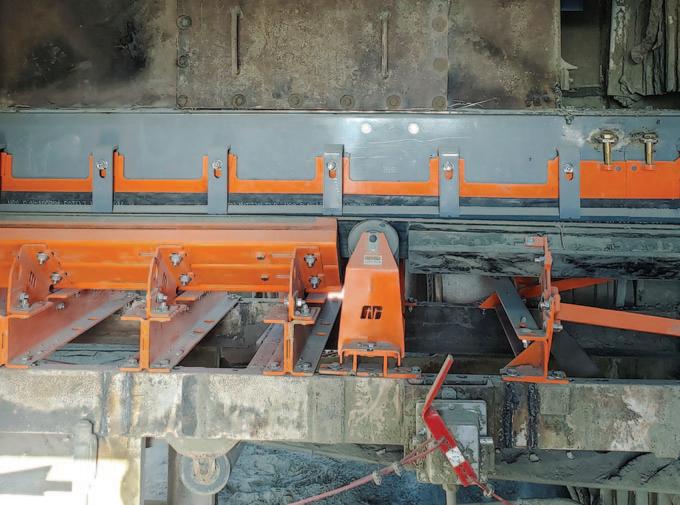
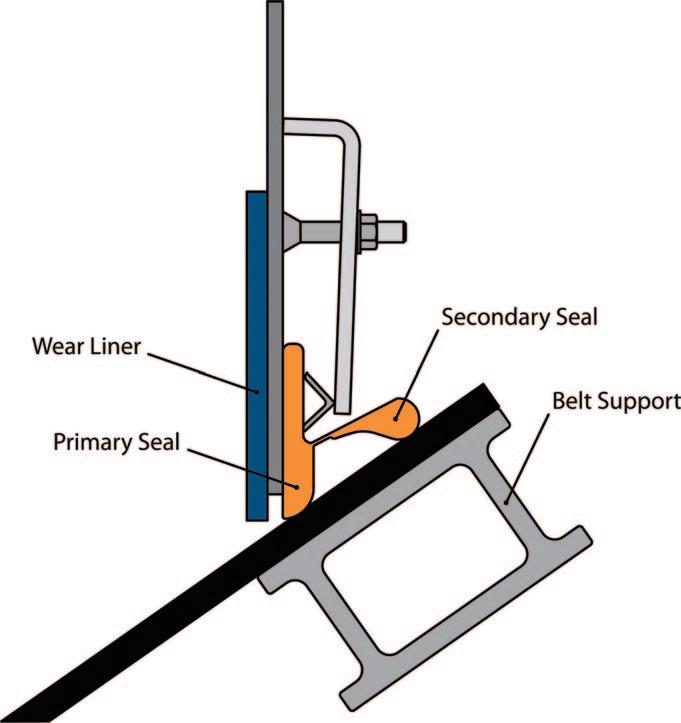
the spillage until it became unmanageable.
The belt seal in the loading and settling zones was an issue that contributed to spillage, as well. Wear liners along the chute wall were not adequate for handling the high heat environment and would warp or tear, creating escape points for fines. The skirting would wear quickly and leave large gaps between idlers where the belt would sag, allowing more fugitive material to escape.
ONE SIZE DOES NOT FIT ALL Managers did not immediately approach Martin Engineering, instead choosing what, on the surface, seemed like a logical solution. The company installed a prefabricated interlocking tube system that offered a sealed environment with good access for maintenance and idler replacement. Unfortunately, the system’s construction materials were unable to endure the punishing environment and the demands of the application. This caused excessive spillage, unscheduled downtime, product loss and a higher cost of operation. Due to failures and serious concerns over fires and safety, the tube system required premature replacement.
Having a long-time relationship, several service contracts and many successful projects throughout the plant, Martin Engineering was brought in to inspect the transfer point and offer solutions. Trained technicians who were familiar with the issues in the clinker barn executed a Walk the Belt™ procedure that allowed them to complete a full checklist and identify issues throughout the transfer process.
Technicians proposed a fully modular heavy-duty Total Transfer Point Solution™ that would be better suited for the application. This included raising and shortening the transfer point enclosure, drastically improving the seal, adding belt support and controlling airflow through the settling zone.
“We liked the plan and the fact it could be done in only a few days during scheduled downtime,” the source continued. “Martin equipment in other parts of the plant had held up well, so we trusted that they would be able to offer a long-term solution.”
HIGH FLYING INSTALLATION Using a crane to lift the components to the high work platform, five contractors and a Martin Engineering supervisor were able to dismantle the old system, install the new components and clean up the area in fewer than four days. This quick turnaround allowed improved testing of the system prior to the end of downtime.
The team installed a new enclosure with an impact cradle, external wear liner, apron seal skirting, track-mounted idlers, support cradles and dust curtains. These components work together as a total solution to improve belt loading, reduce spillage and dust, and minimize impact damage to the belt.
The previous enclosure was 20ft (6m) long. The idea is to give cargo and dust as much time to settle in a sealed environment as possible. To accomplish roughly the same goal in a shorter length, Martin Engineering technicians raised the height of the enclosure slightly and reduced the length to 12ft (3.6m).
The impact cradle eases the cargo’s collision with the belt, reducing the chances of serious belt damage. The unit features troughed low-friction UMHW bars that support belt edges and stabilize the belt line. This eliminates belt sag and bounce associated with impact idlers and minimizes the need to replace broken rolling
Integrated modular components work together for maximum performance.
Wear liner, skirting and apron seal.
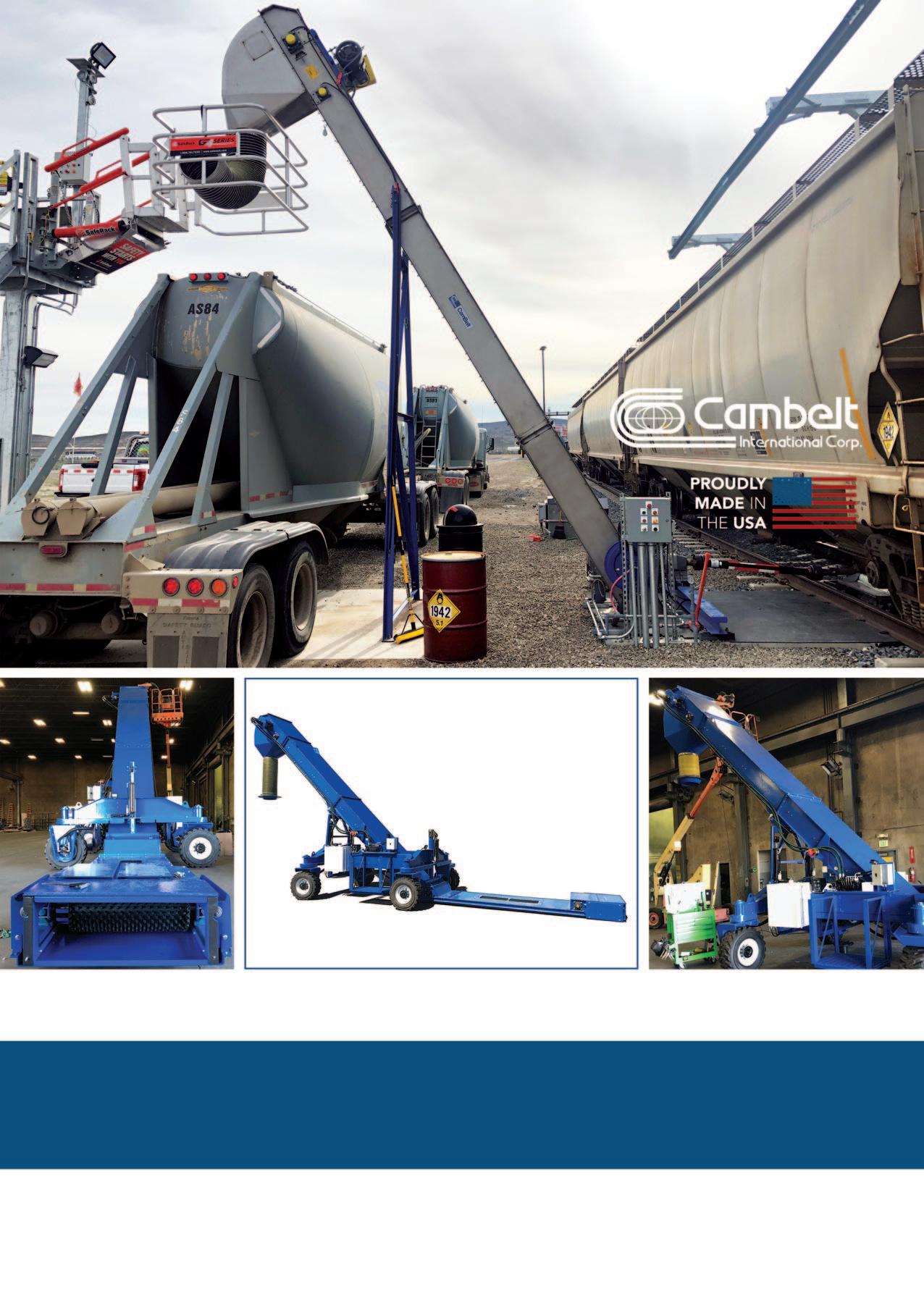

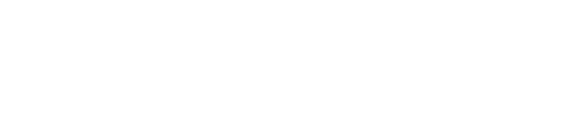
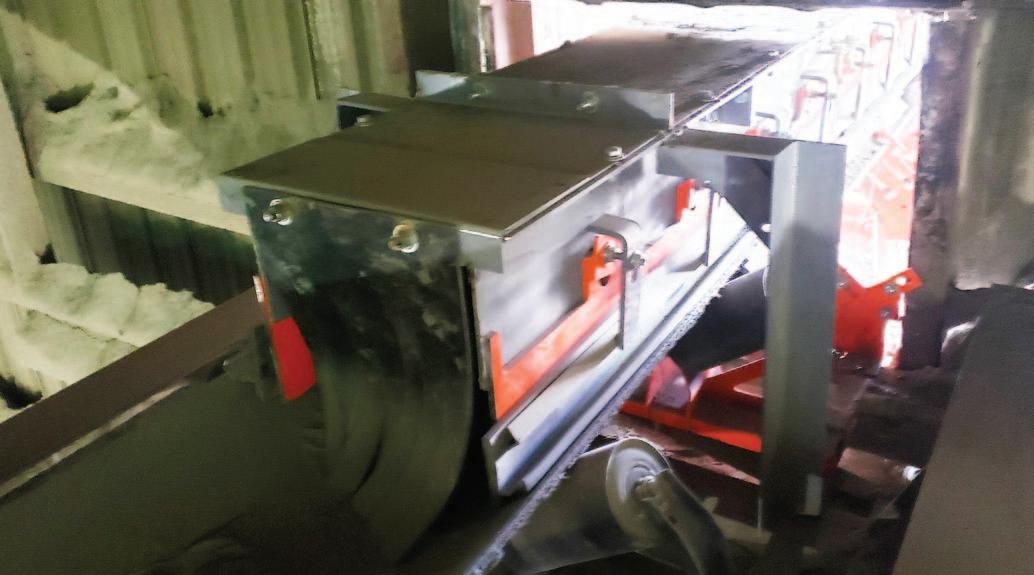
Dust curtains at the front and back of the chute keep emissions down.
components that can increase friction on the belt. The ‘box’ design allows each bar to be turned over to provide a second wear life.
When loaded at a high speed, hot material hitting the enclosure wall can quickly erode the metal and create holes where spillage can escape. The external wear liner adds an extra layer of protection and can be replaced from outside the chute. Previous designs required confined space entry by a certified worker to remove the liner using a blow torch. Now it can be done safely with simple tools from outside the enclosure.
Accompanying the wear liner on the outside of the enclosure is the apron seal skirting. This innovative dual sealing system made from EPDM (ethylene propylene diene monomer) 70 durometer rubber composite prevents spillage by maintaining an effective dust barrier. The primary seal is clamped to the chute wall, with a selfadjusting secondary flap laying outward for extra protection.
Following the tail pulley leading into the impact cradle are track-mounted idlers, which also support the belt in between cradles. Idler replacement is easy, since the units slide out from the stringer for external maintenance. Preventing belt sag is key to creating a tight seal and controlling spillage. Well-placed idlers between cradles help retain a smooth belt path throughout the loading and settling zones.
Two slider cradles smoothly direct the cargo through the settling zone, helping center the material. A similar concept to impact cradles, these feature wider troughed bars that prevent the bumping and jostling associated with idlers. Placed sequentially with track-mounted idlers in between, they promote a tight seal with the skirting to prevent spillage.
Dust curtains at both ends of the chute control the turbulent airflow created by the loading process, minimizing the escape of fugitive material at either end of the chute. By controlling airflow, material settles faster on the belt and more product is retained.
SUSTAINABLE RESULTS Nearly a year following installation, operators report improved efficiency and a drastic reduction in spillage. “Clinker is dusty stuff being dropped into open piles, so completely preventing dust from collecting anywhere in the clinker barn was virtually impossible,” said the source. “However, material piling on the walkway has been drastically reduced, and there’s less dust in the immediate area, so this project made working around the transfer point much safer.”
Belt damage such as holes and splice detachment have not been a problem since installation, reducing the cost of operation significantly since the belting is the most expensive and time-consuming component to replace. The enclosure has remained intact and sealed, continuing to control spillage. Removing most of the idlers from the entire transfer point reduced the chance of roller seizure and friction damage on the return side of the belt.
“We no longer need the crew with the vacuum truck, so that has definitely cut down on man hours and the significant expense for maintenance and cleaning,” the source concluded.
“Overall, we’re happy with the results. The Martin equipment has made the area safer and more productive.”
ABOUT BYRON ALLEN, TERRITORY MANAGER, MARTIN ENGINEERING Byron Allen is the Martin Engineering Territory Manager in Texas, specializing in air cannons, transfer points and conveyor belt cleaning, primarily serving customers in the cement industry. He has been instrumental in training service technicians and managing the company’s Mr. Blade programme in the region, helping customers optimize belt cleaner performance and longevity. Byron’s work experience includes ironworking and boiler construction, failure analysis, preventive maintenance and reliability engineering.
ABOUT MARTIN ENGINEERING Martin Engineering has been a global innovator in the bulk material handling industry for more than 75 years, developing new solutions to common problems and participating in industry organizations to improve safety and productivity. The company’s series of Foundations books is an internationally recognized resource for safety, maintenance and operations training — with more than 22,000 print copies in circulation around the world. The 500+ page reference books are available in several languages and have been downloaded thousands of times as free PDFs from the Martin website. Martin Engineering products, sales, service and training are available from 17 factoryowned facilities worldwide, with whollyowned business units in Australia, Brazil, China, Colombia, France, Germany, India, Indonesia, Italy, Mexico, Peru, Spain, South Africa, Turkey, the USA and UK. The firm employs more than 1,000 people, approximately 400 of whom hold advanced degrees.
SRON company provides customers with high-quality bulk materials storage and transportation system solutions
Henan SRON Silo Engineering Co., Ltd. is a leading and reputable EPC Contractor in China — article written by Wang Leipeng and Wen Peng. The company provides safe and reliable and technically advanced steel silo project system, closed material yard systems, terminal bulk material loading and unloading systems and other bulk materials storage and transportation complete equipment systems solutions and EPC contracting services for bulk materials storage and transportation field.
SRON is engaged in equipment research and development, manufacturing, system process design, general contracting, technical transformation and after-sales service of the following sections, as well as import and export business of related equipment.
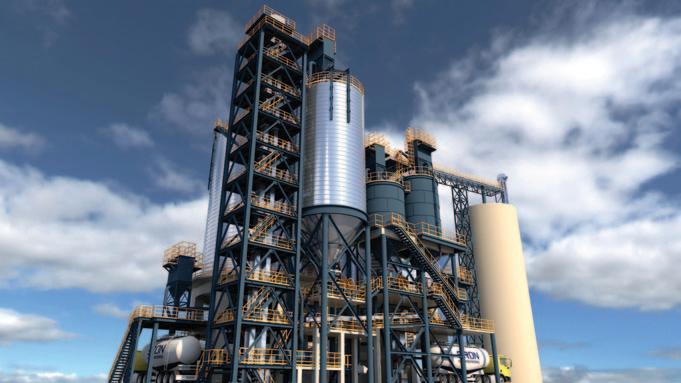
ADVANCED BULK MATERIAL STORAGE AND TRANSPORTATION SYSTEM
RAW MATERIAL HOMOGENIZATION SILO SYSTEM The raw material homogenization silo system includes silo, bucket elevator, air chute, silo roof raw material distributor, dust collector, silo bottom aerated fluidization system, buffer bin, solid flow meter and other equipment.
The homogenizing mechanism of raw material homogenization silo is that feed material through the silo roof raw material distributor, so that raw material in the silo at different periods is transverse distribution; through the silo bottom annular fluidization aeration system, the silo is aerated every five minutes. Raw material is vertically cut by air flow and feed into silo to achieve homogenization; after raw material entering into the mixing silo, mix and homogenize it again so as to achieve the ideal homogenization.
SRON special cement homogenization system for POSCO.
CEMENT SILO SYSTEM Cement storage system includes steel silo, bucket elevator, air chute, dust collector, silo bottom aerated fluidization system, silo bottom discharging device, bulk loading machine, tonne bag packaging machine,
SRON 4* 10,000-tonne cement storage system.
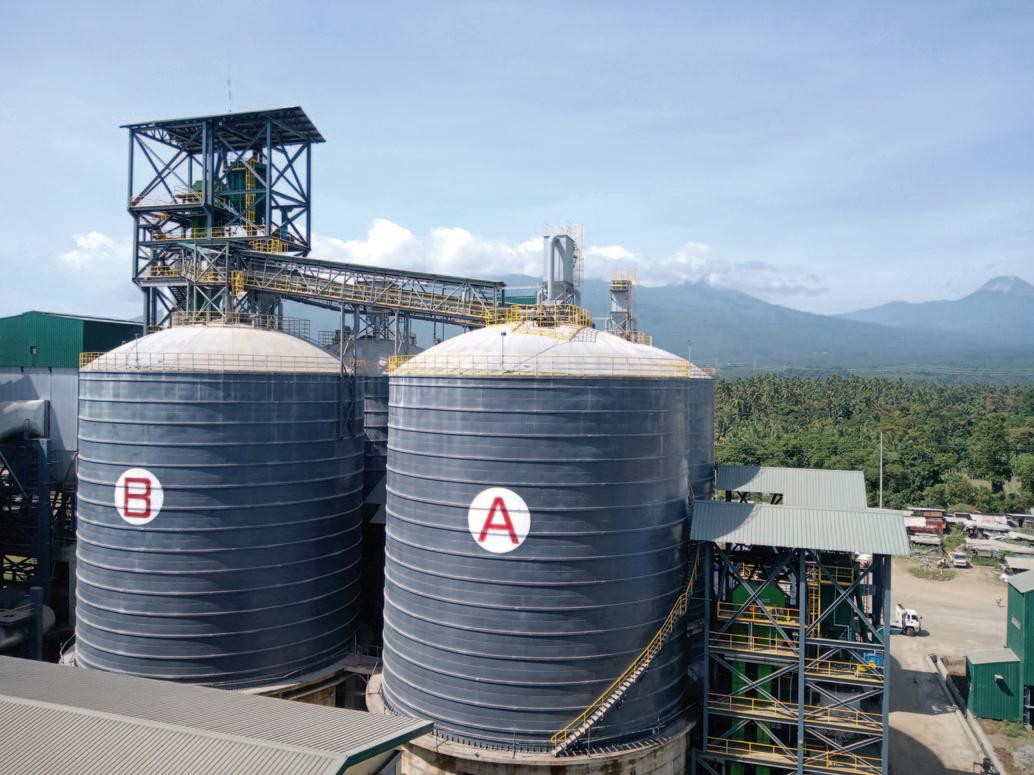
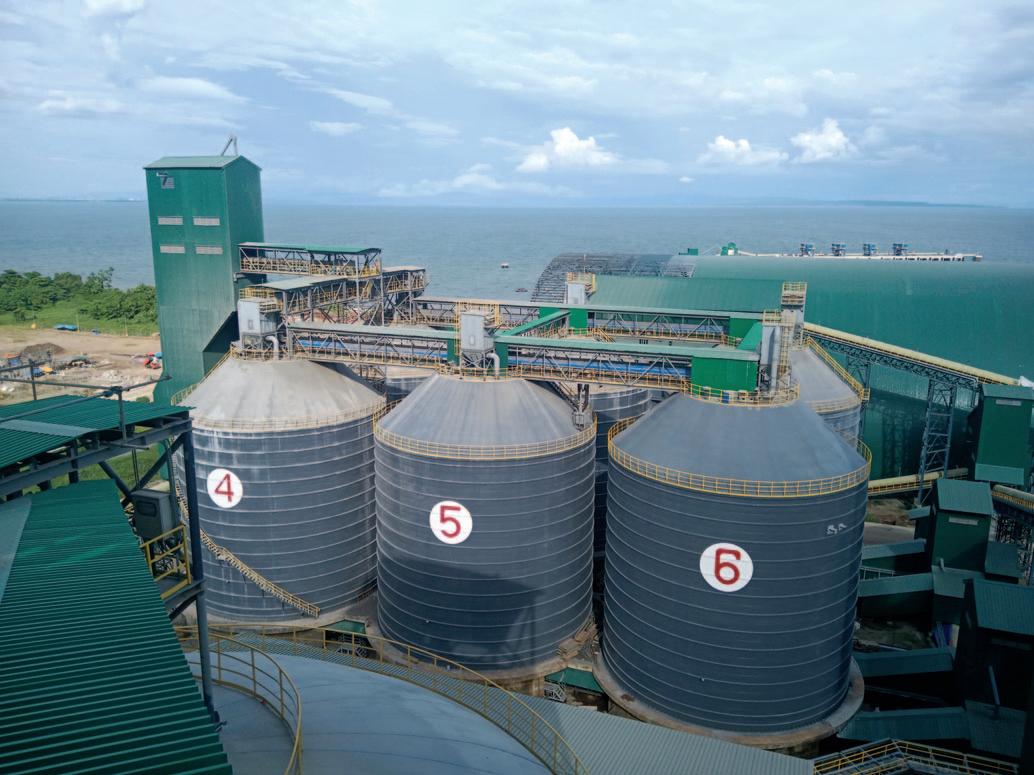
pneumatic conveying system, complete sets of equipment for cement packaging line, etc.
SRON can provide welded steel silo, spiral silo, bolted steel silo and other types of steel silos, of which the reserve is100–50,000 tonnes. According to the specific situation of customers’ projects, SRON’s experienced engineer team will provide professional solutions. SRON’s cement silo system has the characteristics of high unloading rate, long service life, high reliability, almost no maintenance and repair work, low energy consumption, automatic control and so on.
CLINKER SILO SYSTEM The clinker silo system includes steel silo, belt conveyor (chain bucket conveyor), bucket elevator, dust collector, silo bottom discharge valve and other equipment.
LARGE CLOSED MATERIAL YARD AND STACKING AND RECLAIMING SYSTEM SRON can provide large closed material sheds and stacking and reclaiming systems to achieve the purpose of prehomogenization of raw materials in the production of cement plants. According to the different situations of customers’
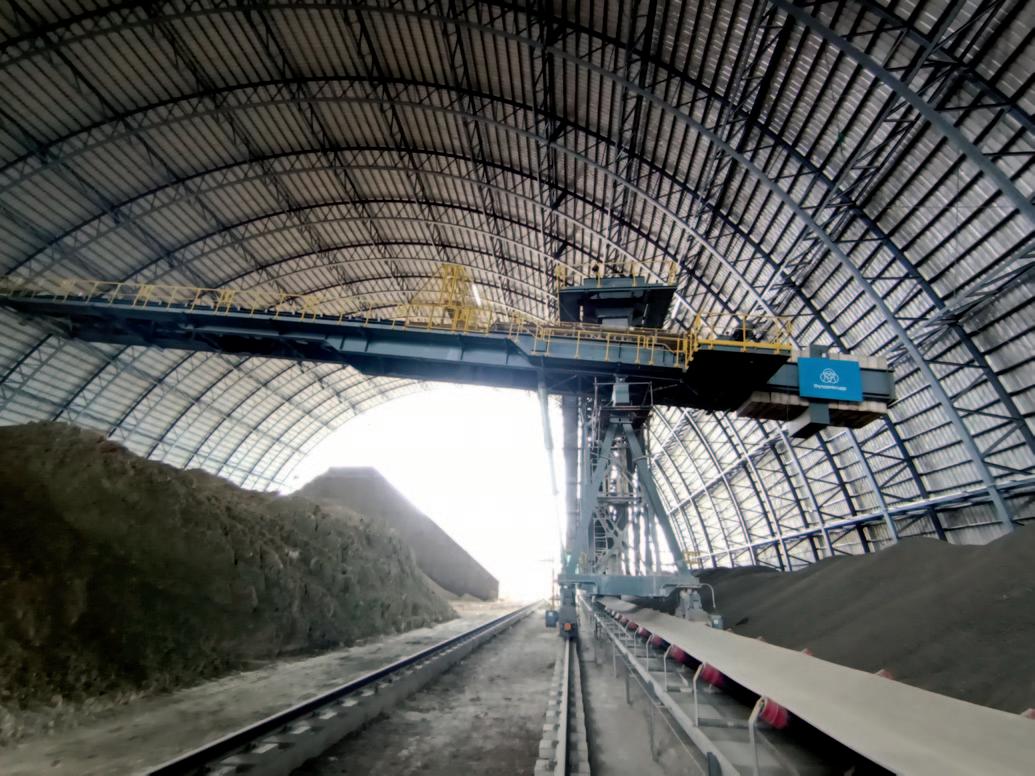
SRON pre-homogenization stockyard system for cement plant.

projects, the structure of the material shed is arched or ball shell shaped grid, and the material shed has advantages of a large span (50m~120m), high degree of factory, high degree of factory components (80%), fast installation, short construction period, low cost, wind and snow resistance, good antiseismic performance, high stiffness, and high structural safety.
SRON can configure various types of stacking and reclaiming equipment according to the customer’s project requirements.
WHARF TRANSIT SYSTEM The wharf transit system from SRON mainly transfers bulk materials from silos to the wharf for loading, or transfers bulk materials from bulk carriers to silos for storage after ship-unloading. The wharf transit system includes silos, shiploading (unloading) machines, air chutes, belt conveyors, bucket elevators, dust collectors, and so forth.
MAIN CUSTOMERS SRON provides systems engineering and services for building materials, metallurgy, mines, terminals and other enterprises. Through years of unremitting efforts, the company is the supplier of Sinoma, Lafarge, Loesche GmbH, San Miguel Corporation, POSCO and other well-known group enterprises at home and abroad. These include: San Miguel Corporation; SIG; Lafarge; CUCC; Primecement; Posco; CHD; Loesche; Baowu; and SECMC.
TECHNOLOGICAL INNOVATION AND PROGRESS Automation and intelligence: with the development of society, the distributed control system of centralized management has been widely used in the cement industry in the world. By using this system, the motor group programme control, process quantity collection, processing, display and regulation can be realized. SRON continues to explore unattended production, and through remote instrumentation, monitoring and other means to reduce staffing, enhance plant management level, and improve labour productivity.
SRON organizes and utilizes domestic and foreign technical and intellectual resources, carries out a wide range of international technical exchanges and cooperation in various forms, constantly develops and innovates, and has established long-term and stable co-operative relations with universities, research institutes and peer enterprises.
The company collects and analyses relevant global technology and market information, studies industry development trends, and provides advice and suggestions for product and technology development decisions. DCi
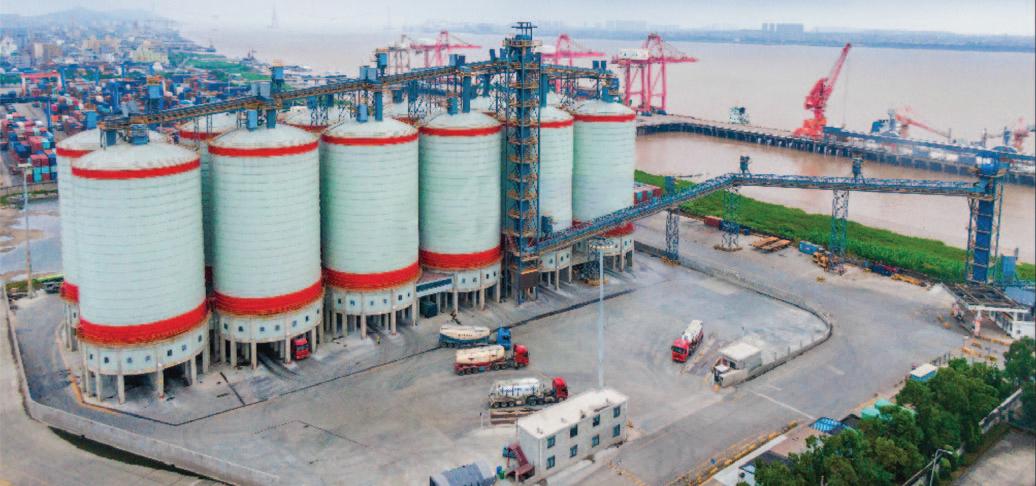