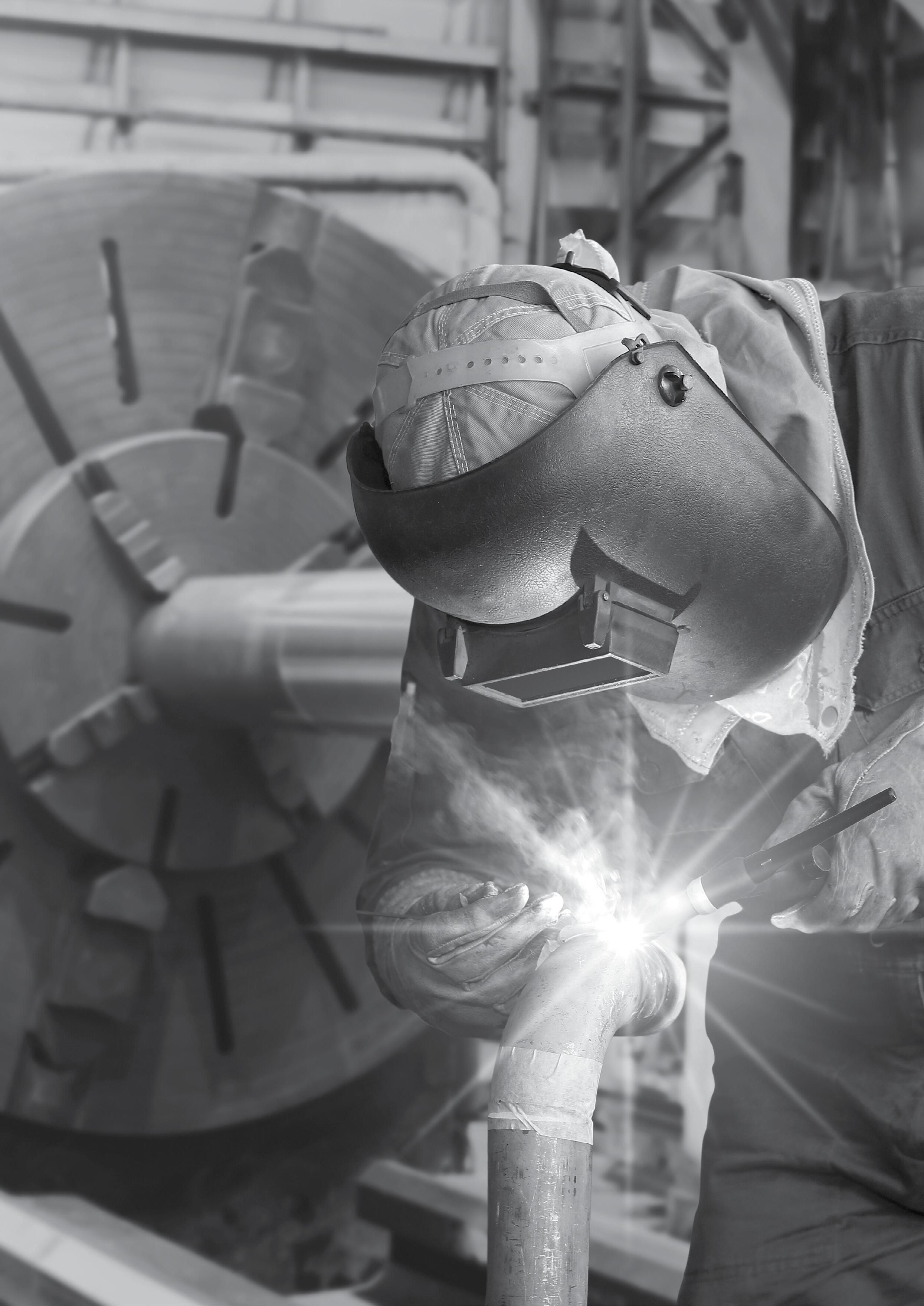
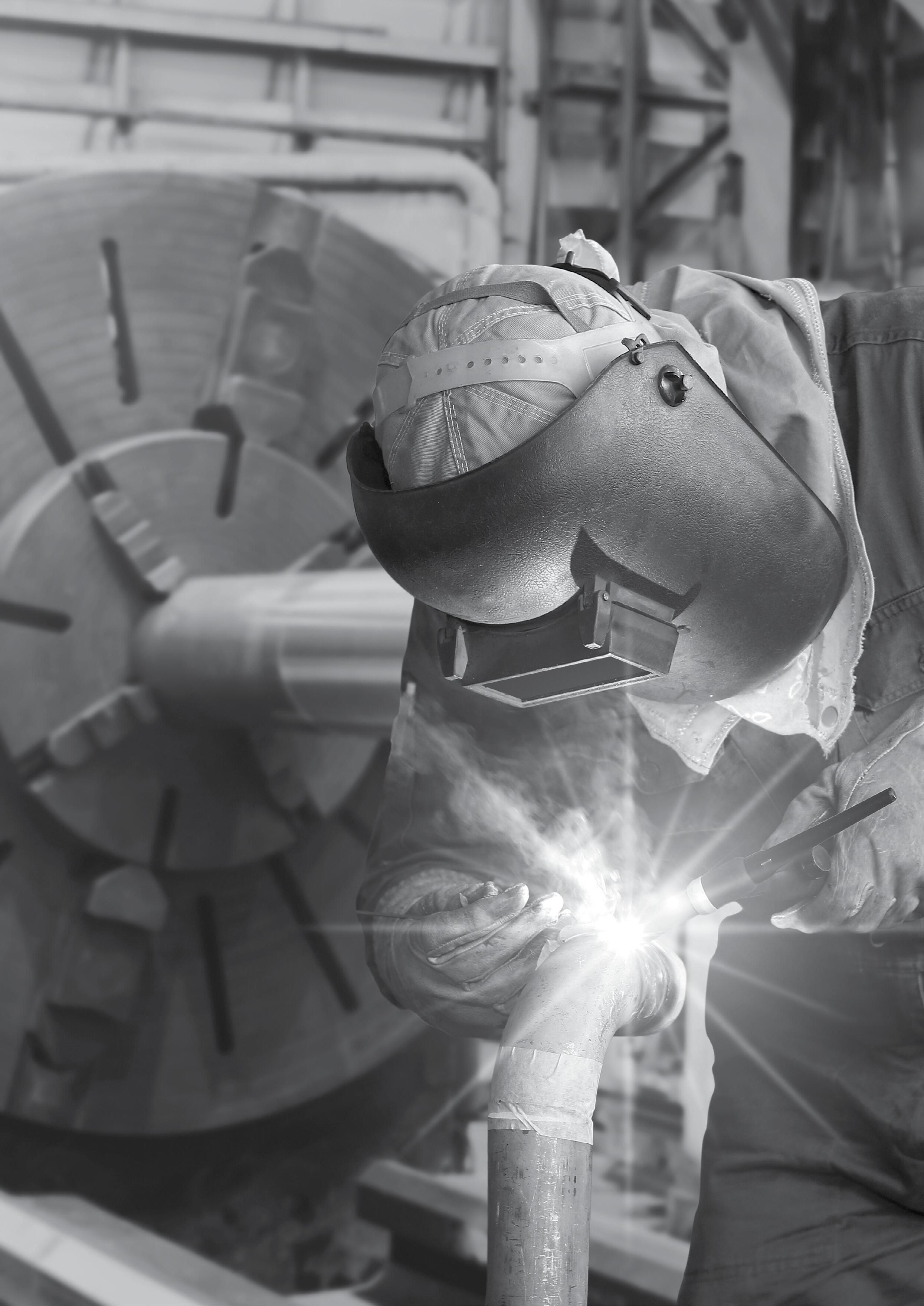
WELDING & CUTTING MACHINES
FRENCH MANUFACTURER SINCE 1964
Created in 1964, GYS is a French industrial group with 900 employees around the world. Built around continuous investment in Research & Development and in the acquisition of knowledge, the company is now a major player in the design and manufacture of welding machines, battery chargers and car body repair equipment.
"The market realities are constantly changing and the size of our family business requires us to quickly adapt to new contexts and new challenges.
We are convinced that our future is closely linked to the future of our partners. This is why we do everything in our power to understand what distributors and users expect from us and what challenges they face every day. To support them in facing these challenges, we wish to become and remain their privileged partner on the path we will travel together."
Bruno Bouygues, C.E.O.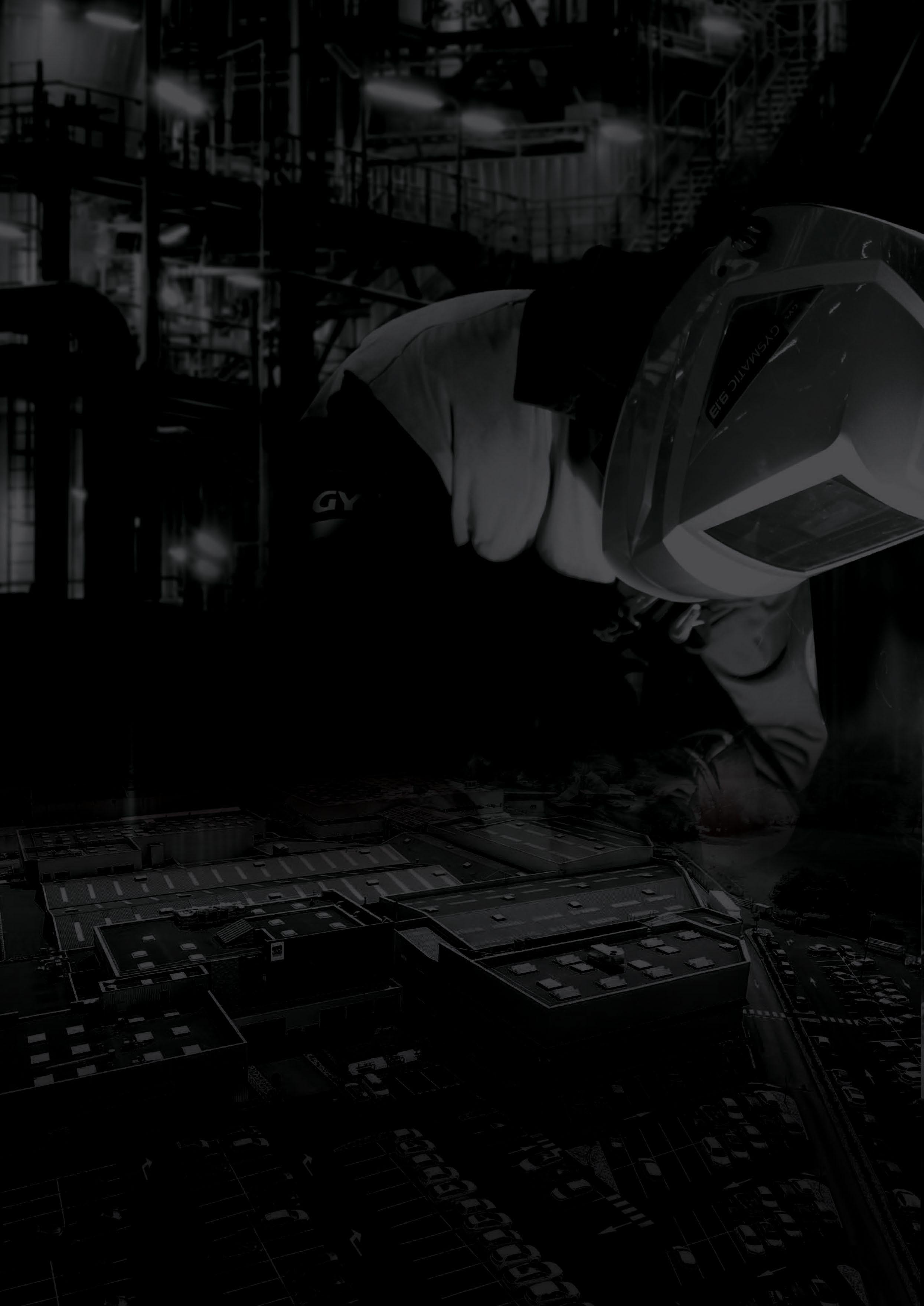
FLEXIBLE VOLTAGE
The device works on a simple 230V-16A or 110V-32A plug, even in intensive use and on site extensions (100m).
PFC technology suppresses peaks and regulates the supply current. Also allows the use of extension cords or generators and contributes to a better current stability during the welding phase.
Can withstand occasional or permanent voltage variations on the electrical network up to 400V (lightning, generator, load shedding loads).
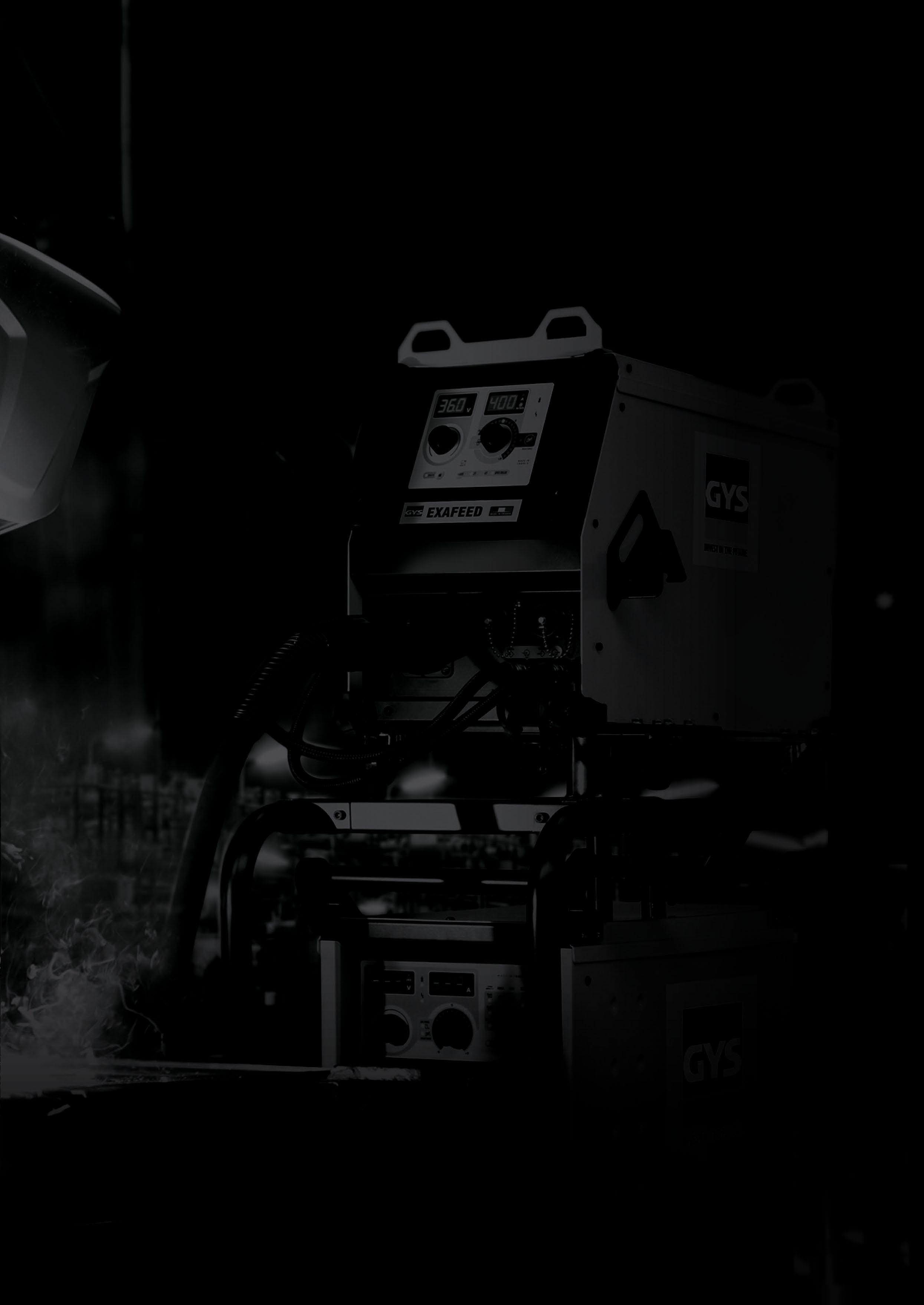
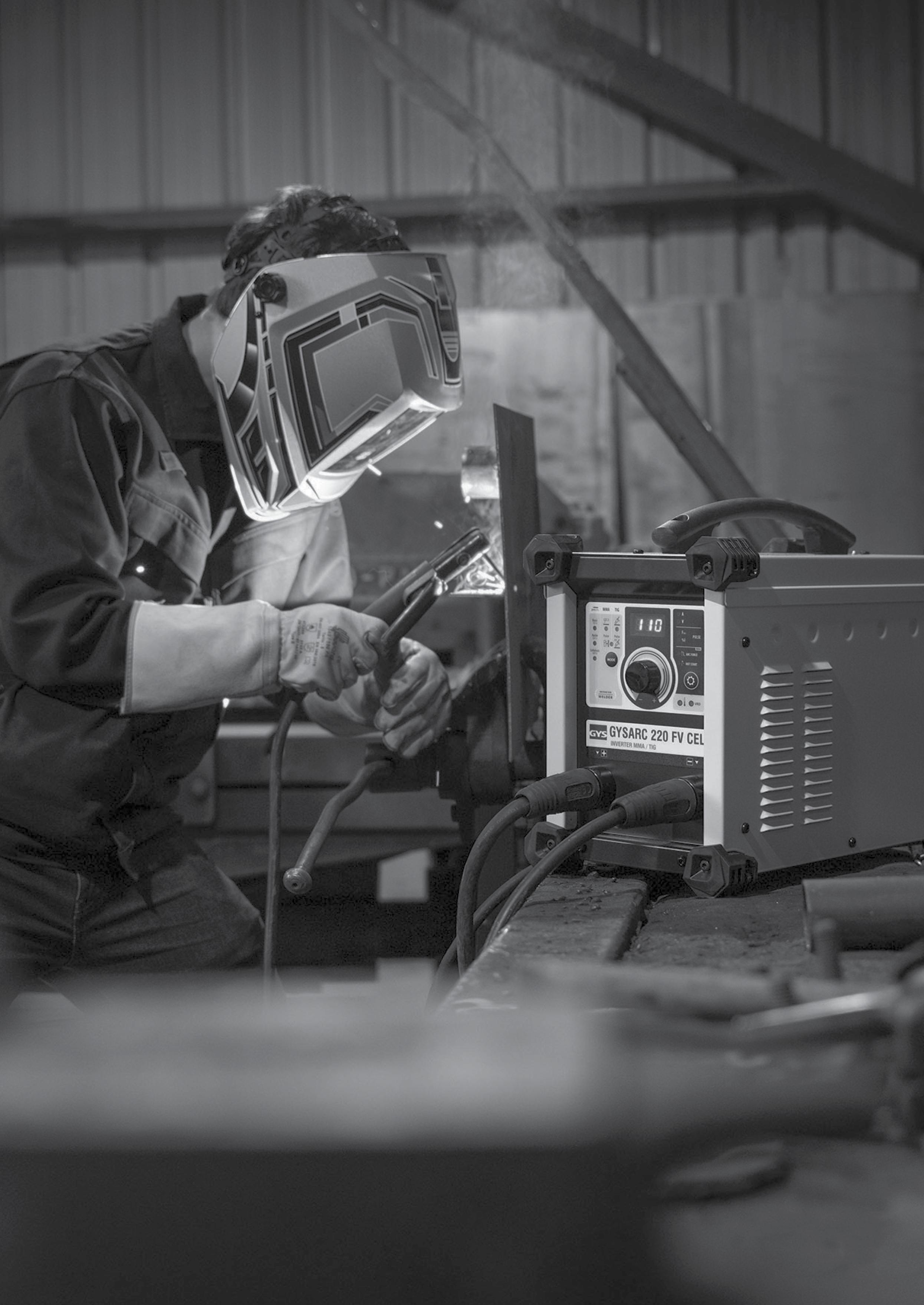
MMA/ARC WELDERS
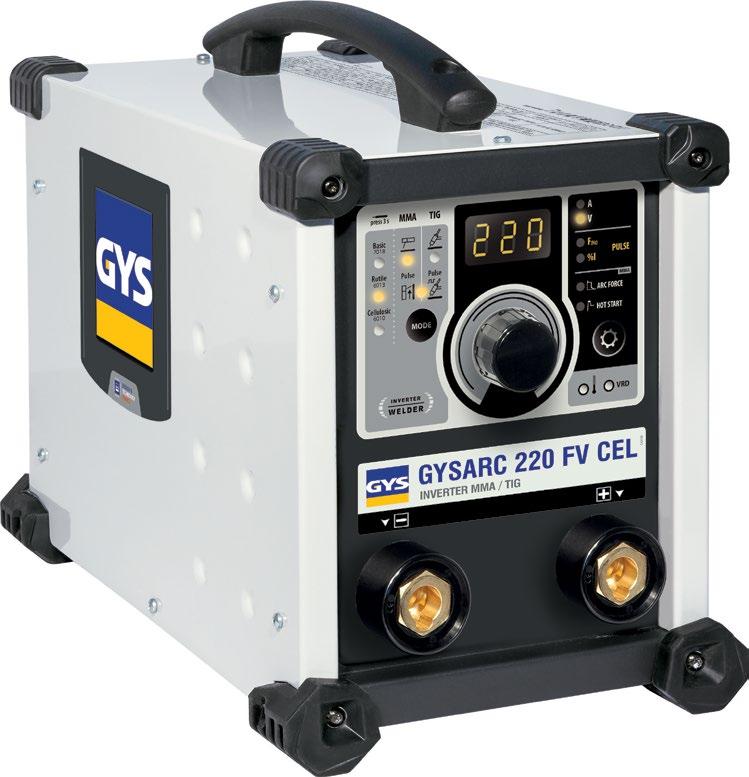
FOUR
WELDING MODES (MMA & TIG DC)
Welds basic, rutile and cellulosic electrodes up to Ø 5 mm thanks to two MMA modes:
• MMA Standard
• Adjustable Pulse MMA: Ideal for welding in the vertical upright position.
TIG Lift: Ignition by simply touching the workpiece.
TIG Welding Help: Automatic arc fading.
• Adjustable TIG Pulse: Facilitates the welding of very thin sheets (0.3 mm) and increases bead penetration.
INTEGRATED WELDING HELPS IN MMA
• Adjustable Hot Start: Generates an over current at start-up to facilitate ignition and reduce welding defects.
• Adjustable Arc Force: Regulates arc length deviations and offers comfort to the welder.
• Anti-Sticking: Prevents the electrode from sticking if it comes into contact with the workpiece.
REINFORCED SECURITY
• VRD (Voltage Reduction Device): Lowers the no-load voltage (<30V) to secure welders in specific environments (mines, chemical plants, shipyards, etc.)
• Protection Class IP23: Ideal for outdoor and indoor environments (subject to dust or light rain).
• Anti-Dust (AD): Ventilation tunnel against external pollution.
With inverter technology, the ARC 220 FV CEL is a singlephase 220A MMA power source that meets the professionals’ requirements. Designed around reinforced electronics, this workstation can easily weld cellulosic, rutile or basic electrodes. It is also equipped with the TIG lift (DC) process which ensures high quality weld beads, even on thin sheets. Robust and versatile, the ARC 220 FV CEL offers the user great welding comfort and maximum productivity.
ACCESSORIES:
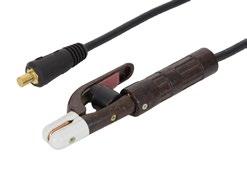
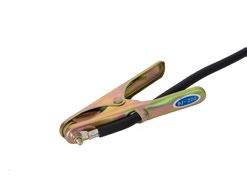
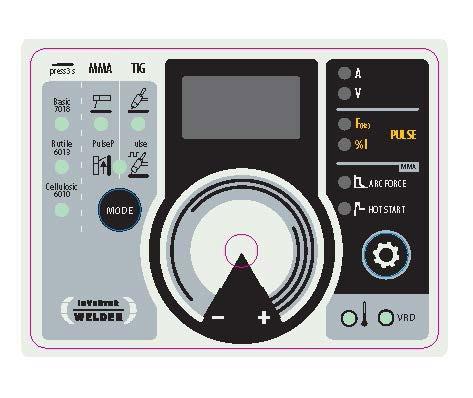
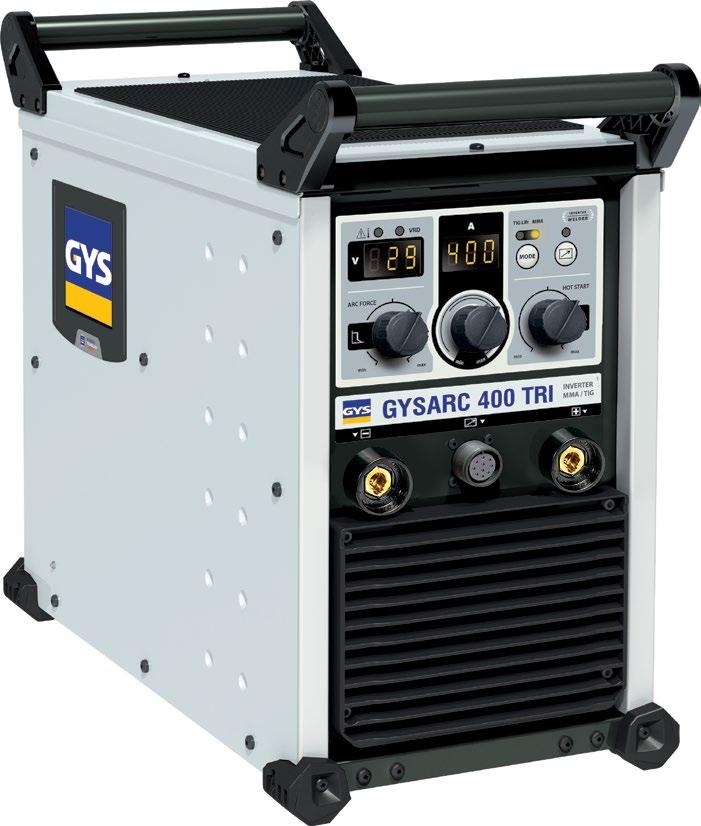
MMA (SMAW) / TIG LIFT (GTAW)
• MMA (SMAW): Rutile (6013), basic (7018) and cellulosic (6010) electrodes (up to Ø 6 mm).
• Arc Gouging: With carbon electrodes (up to Ø 6.4 mm).
• TIG (GTAW): Process with LIFT arc ignition (Ø1.0 to 3.2 mm).
WELDING AIDS
• Adjustable Hot Start: For a better arc ignition.
• Adjustable Arc Force: Temporary current increase when welding in difficult situations.
Anti-Sticking: Reduce the risk of the electrode sticking to the metal when in contact.
HEAVY DUTY
• High Duty Cycle: 400A @ 60%.
• High No-load Voltage (84V): For a good arc dynamic and to facilitate the arc ignition for cellulosic (6010) electrodes.
Voltage Display (when welding) No-load Voltage Display (after welding)
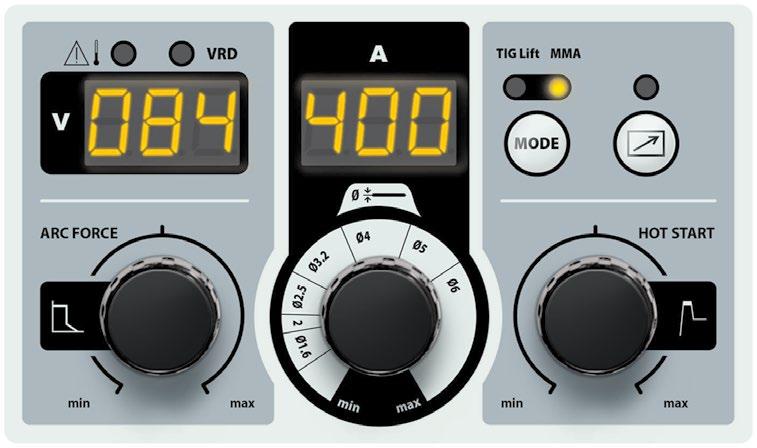
With inverter technology, the ARC 400 TRI is a 3-phase MMA (SMAW) / TIG (GTAW) welding power source with exceptional welding performance. Featuring advanced electronics, this product guarantees maximum productivity, even in harsh environments. Its switchable Voltage Reduction Device (VRD) protects the welder in hazardous areas (mines, chemical and petrochemical installations, shipyards, etc.).
TECHNICAL DATA:
ACCESSORIES:
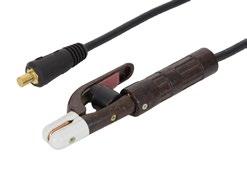
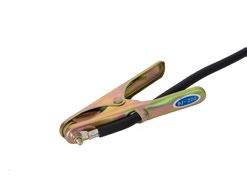
OPTIONAL ACCESSORIES:
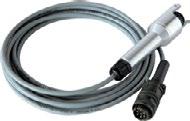
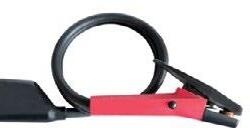
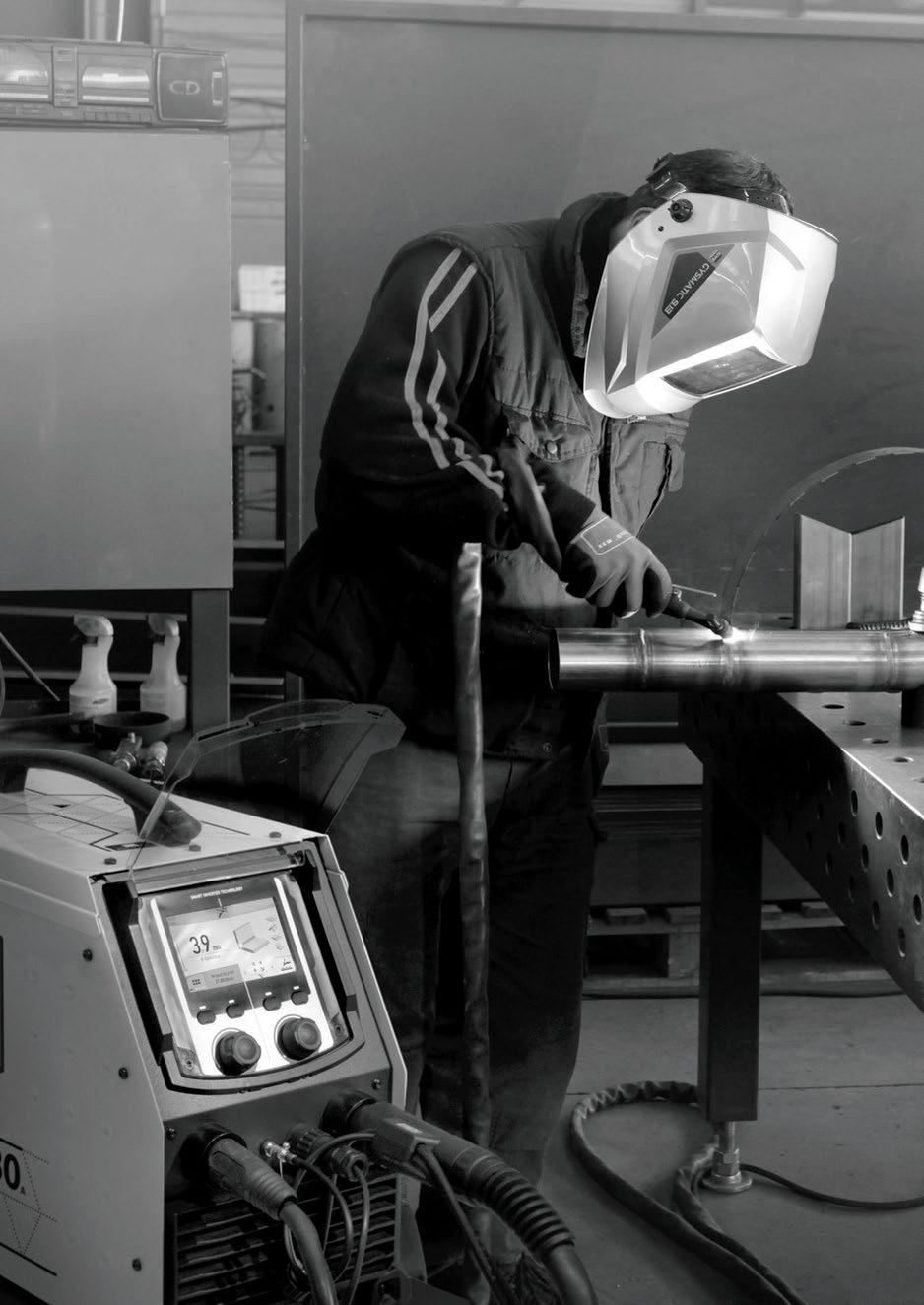
TIG WELDERS
PROTIG 221 DC FV
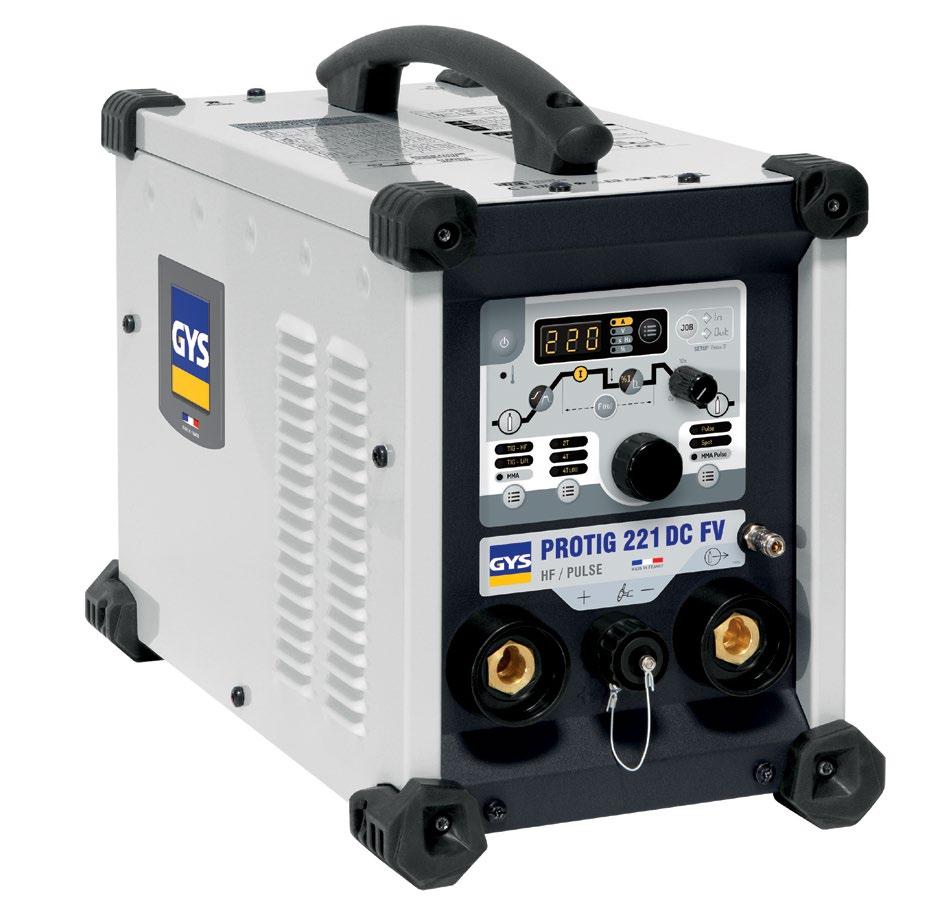
OPTIMISED DC WELDING
• Its secondary regulation system ensures optimal arc stability as well as a constant current in all welding positions.
• The DC TIG-welding mode ensures high-quality welding on all ferrous materials, such as steel, stainless steel, copper and its alloys.
DC Pulsed TIG welding up to 2 kHz means users can control the temperature of the weld pool, limit deformations and join sheet metal as thin as 0.3 mm.
Its spot-welding feature can be set anywhere between 0.1 - 25 sec offering fast and precise spot-welding on thin sheet metal.
• The machine is equipped with two different ignition types: contactless HF (High Frequency) ignition or Arc-Lift ignition with contact for electro-sensitive environments.
• Users can also enjoy three separate trigger managements systems: 2T, 4T and 4T LOG.
• An automatic torch-detection feature means that this device is compatible with trigger, double-button and potentiometer torches.
MMA WELDING
MMA welding uses basic and rutile electrodes (up to Ø 5 mm).
Pulsed MMA welding enables users to weld in a vertical-up position (ideal for tubing and pipelines, etc.).
The PROTIG 221 DC FV has three integrated welding aids: Anti-Stick: Minimises the risk of the electrode sticking to the workpiece.
Hot Start: Facilitates ignition and can be quickly adjusted depending on the type of metal.
Arc Force: Automatically increases the current in difficult welding situations.
MAXIMUM PRODUCTIVITY
• Stores up to 10 welding programs per process. The advanced menu settings offer optimal welding control.
• The current and voltage are displayed during and after the welding process (DMOS/QMOS).
Remote control connections (manual or pedal).
• Reinforced bodywork and anti-shock pads.
• Compact and easy to move around the work site.
The versatile PROTIG 221 DC FV (220 A) is a compact, portable, dual-process appliance for DC TIG and MMA welding processes. This machine is fitted with PFC technology which has numerous advantages; it is very energy efficient and can work reliably with very long power cables, even ones over 100 metres long.
TECHNICAL DATA:
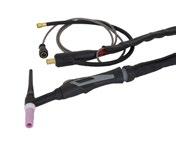
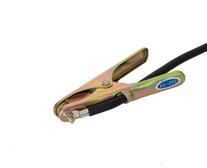
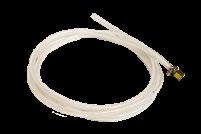
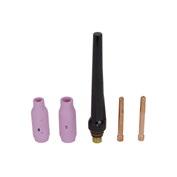
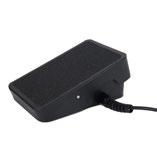
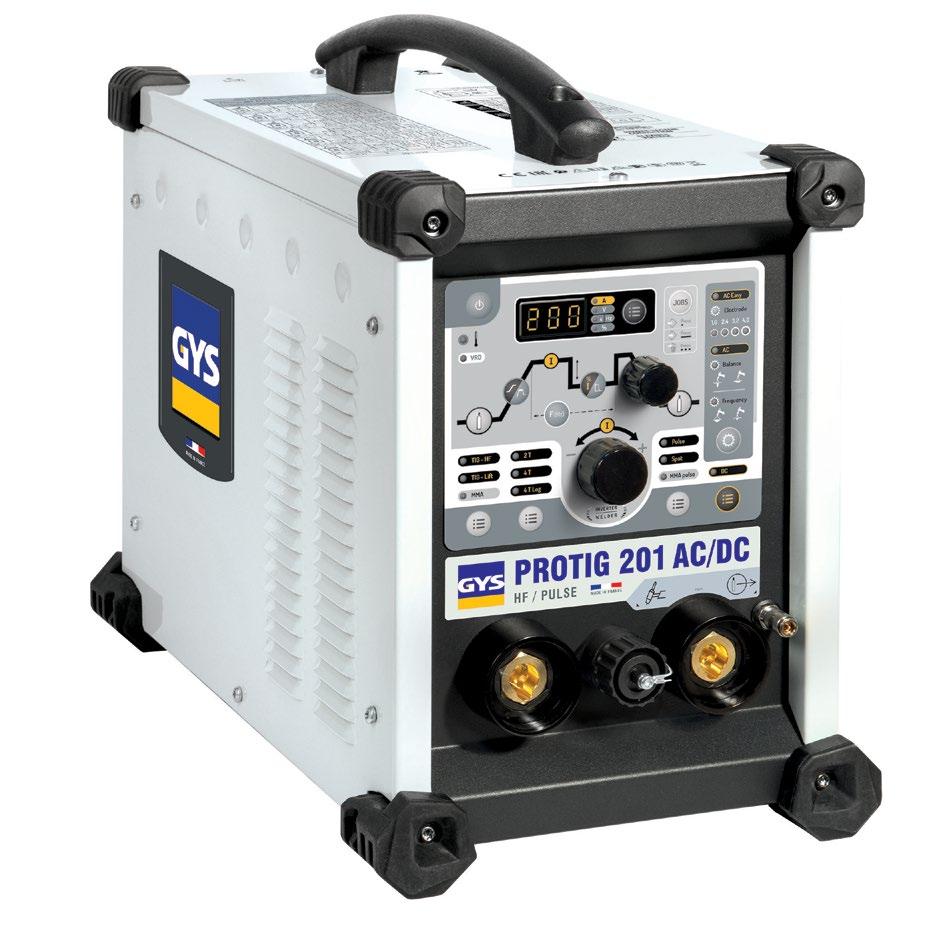
SIX AC/DC TIG PROCESSES
• STANDARD DC TIG: Ensures high-quality welding on all ferrous materials, such as steel, stainless steel as well as copper, its alloys and titanium, etc.
• PULSED DC TIG: Controls the melting temperature, limits deformation and allows sheet metal from 0.3 mm thick to be assembled effectively.
• SPOT DC TIG: Pre-assemble ferrous metals by spot welding them together.
• EASY AC TIG: Makes using the welding machine even easier thanks to predefined user settings. The operator only has to select the tungsten electrode’s diameter on the machine’s control panel.
• STANDARD AC TIG: Designed for welding aluminium and its alloys (Al, AlSi, AlMg and AlMn, etc.). An alternating current effectively cleans the aluminium for perfect welds.
• SPOT AC TIG: Pre-assemble aluminium parts and accessories by spot welding them together.
TWO COATED-ELECTRODE WELDING
MODES
• STANDARD MMA: Uses basic and rutile electrodes up to Ø 4 mm.
• PULSED MMA: Makes it easier to weld in a vertical-upright position (nozzles/pipelines).
DESIGNED FOR USER COMFORT
• Two Ignition Types: HF (without contact) or ARC-LIFT (with contact) for electro-sensitive environments.
• Three Trigger Management Modes:
2T: Maintains pressure on the trigger throughout the welding process.
4T: To start welding, press the trigger once and then press the trigger again to stop the welding process.
4T «LOG»: The operator can switch between two separate welding currents by quickly pressing the trigger (hot and cold current).
• MMA Welding Aids:
Anti-Stick: Reduces the risks of the electrode sticking to the workpiece if it comes into contact with it.
Hot Start: Assists in igniting the arc and can be adjusted according to the type of metal being welded.
Arc Force: This fully adjustable feature regulates the arc length deviations.
• VRD (Voltage Reduction Device): The welding current is only delivered when the electrode is in contact with the workpiece (not originally activated). Save 10 programs for each process, for repetitive tasks.
The PROTIG 201 AC/DC is a professional TIG welding solution for welding all metal types up to 4 mm thick (steel, stainless steel, aluminium, copper and titanium). It ensures a very high level of precision in many areas such as production, maintenance or pipe work.
ROBUST DESIGN FOR ALL ENVIRONMENTS
• Compact and lightweight design. Current/voltage displayed after welding (DMOS/QMOS).
• Stores up to 50 welding programs per process.
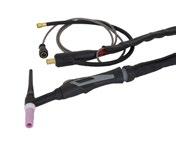
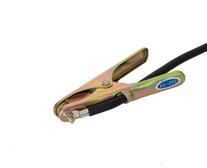
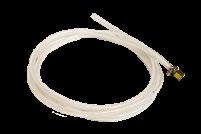
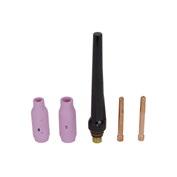
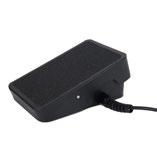
TITANIUM 230 AC/DC FV
WM-061996
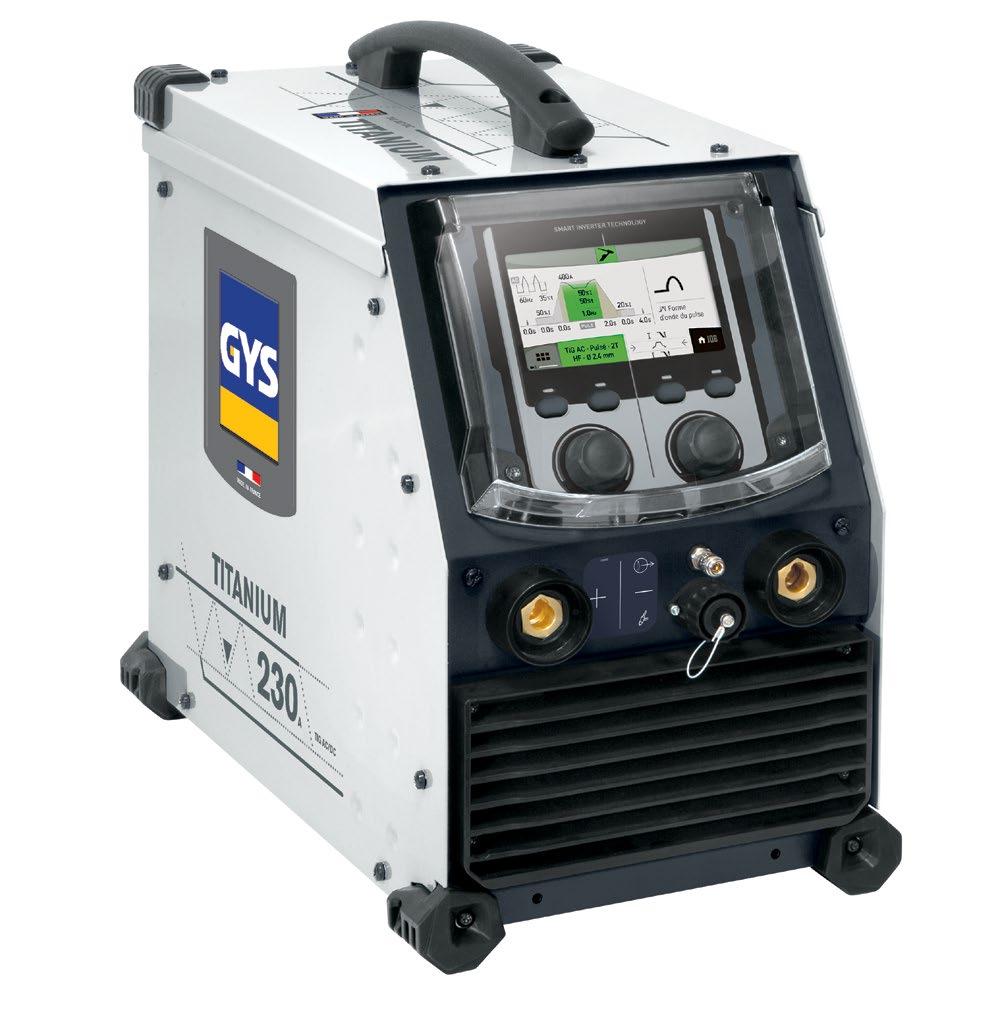
SIX TIG WELDING MODES
DC Standard: Smooth welding on the majority of ferrous materials.
DC Pulse: Allows welding while minimizing heat input (up to 2.5 kHz).
Fast Pulse: Pulses up to 20 kHz for specialised steel applications
AC Standard: Welding of aluminum and its alloys (Al, AlSi, AlMg, AlMn, etc).
AC Pulse: Precise penetration regulation, controllable by adjusting the AC pulse frequency (up to 500 Hz).
AC Mix: Alternates between AC and DC currents to increase welding speed.
TIG WIZARD SOLUTION
Patented synergic mode for maximum productivity with welding and tacking of Aluminum, Steel, Stainless Steel and Copper parts, with or without the need for filler material.
Five types of assembly: End to end (BW), Lap (FW), Interior angle (BP), Exterior angle and wire fusion.
Wizard Lab for the creation of bespoke welding cycles.
OPTIMIZED SETTINGS
Four Tacking Modes:
Spot/Multi Spot: Traditional spotting before welding thin sheets. Tack/Multi Tack: Ultra-precise pointing without oxidation, reducing the risk of workpiece deformation.
Three Types of Arc Ignition: Standard Lift, High-Frequency (HF) and Touch. HF (timed high-frequency ignition).
Three Trigger Modes: 2T, 4T and 4T LOG Configuration of AC waveforms enabling closer arc control and penetration.
E-TIG mode guarantees the machine to respect the selected welding perimeters, regardless of the position of the torch in relation to the workpiece (welding energy control).
MAXIMUM CONNECTIVITY
• Accurately measures energy usage.
• Traceability of all welding seams, conforming to EN 3834 standard. Welding accessory calibration mode (improves the calculation of energy usage).
• Connectable for use with Robots via an optional kit (037960).
• User mode allows the option to share the product with several different operators.
• Free tool for interface customization is available online.
• Backup of user Jobs via USB key (500 max.) as well as machine configuration.
The TITANIUM 230 AC/DC FV is a single-phase AC/DC TIG welding Power Source. Intelligent and connected, it offers extremely precise arc control and industrial welding performance up to 230 A (16 A fuse) thanks to integrated power factor correction. It combines excellent ergonomic design and user experience, with advanced welding functionality.
• Compatible with latch, double button, potentiometer (remove and push pull torches.)
New and revised welding synergies and software updates available by USB key.
Remote control (pedal or remote option) connectable without tools. Liquid cooling unit optional (070820).
• MMA, MMA AC and Pulsed MMA modes (electrodes up to Ø 5 mm).
• VRD (Voltage Reduction Device) can be activated to lower the no-load output voltage to under 35 V.
• «FV» technology guarantees a welding arc that is always stable, even in the event of mains voltage variations (85 to 265 V). It also means that the machine is suitable for use on a generator, or with a very long power cable.
TECHNICAL DATA:
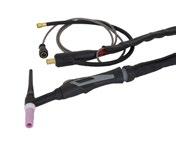
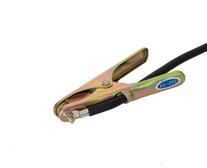
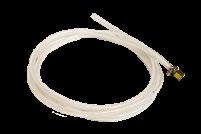
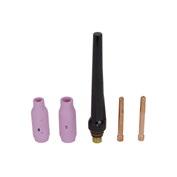
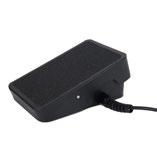
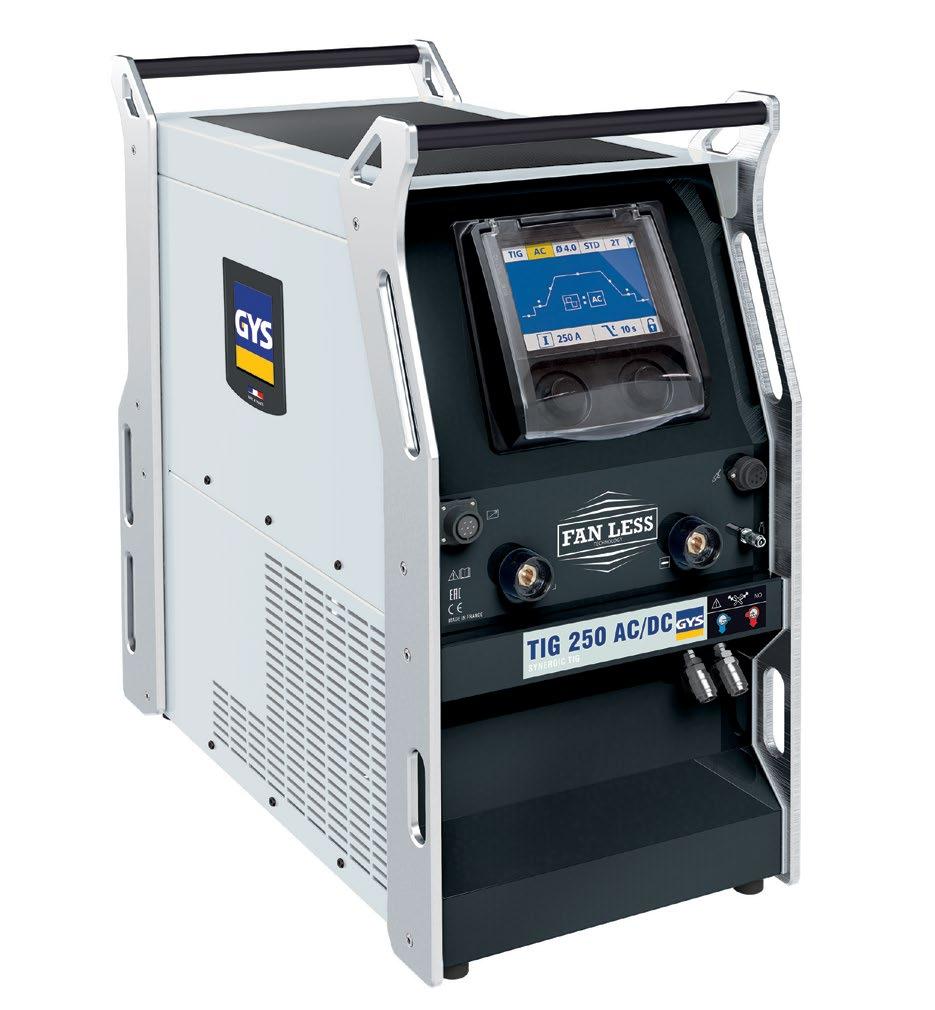
PROFESSIONAL INTERFACE
• 5.7” TFT display screen offering large information readabilitycurrent, thickness, welding mode, etc. Two control knobs to easily navigate through the different menus.
SYNERGIC MODE
Simplified mode which offers automatic configuration of welding parameters tailored to the users’ requirements. Simply enter four settings:
• metal assembly type
• electrode diameter
• thickness of the metal to weld
MANUAL MODE
The operator has full control of all the TIG settings to suit the welding requirements. 250 user selected parameters can be saved in the machine for future recall.
EXCEPTIONAL LIQUID COOLING SYSTEM
The internal electronics are cooled by an advanced system with no fan required giving the added advantage of protection from dust ingress «Fanless».
This industrial TIG, with a high duty cycle, is designed to weld steel, stainless steel, copper and aluminium alloys. Its reinforced steel casing is ideal for on-site work and its advanced cooling mode gives the highest duty cycle and protects it against dust.
ROBUST DESIGN (HORS MARINE)
The casing is reinforced by an external aluminium structure to allow safe lifting without damaging the machine. An easy to set up trolley enables conversion into a transportable unit with a 10m³ gas bottle support.
TWO MMA MODES
Easy mode or PRO mode with access to every parameter.
TECHNICAL DATA:
ACCESSORIES:
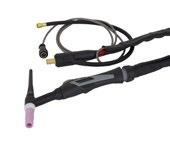
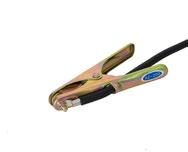
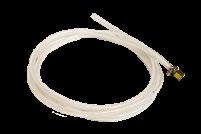
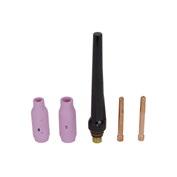
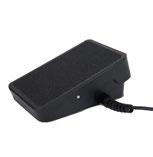
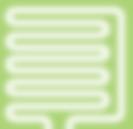

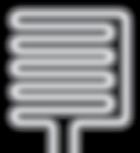

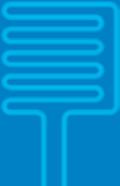


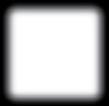


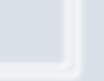

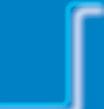
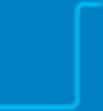
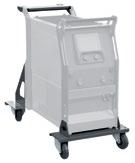
TITANIUM 400 AC/DC
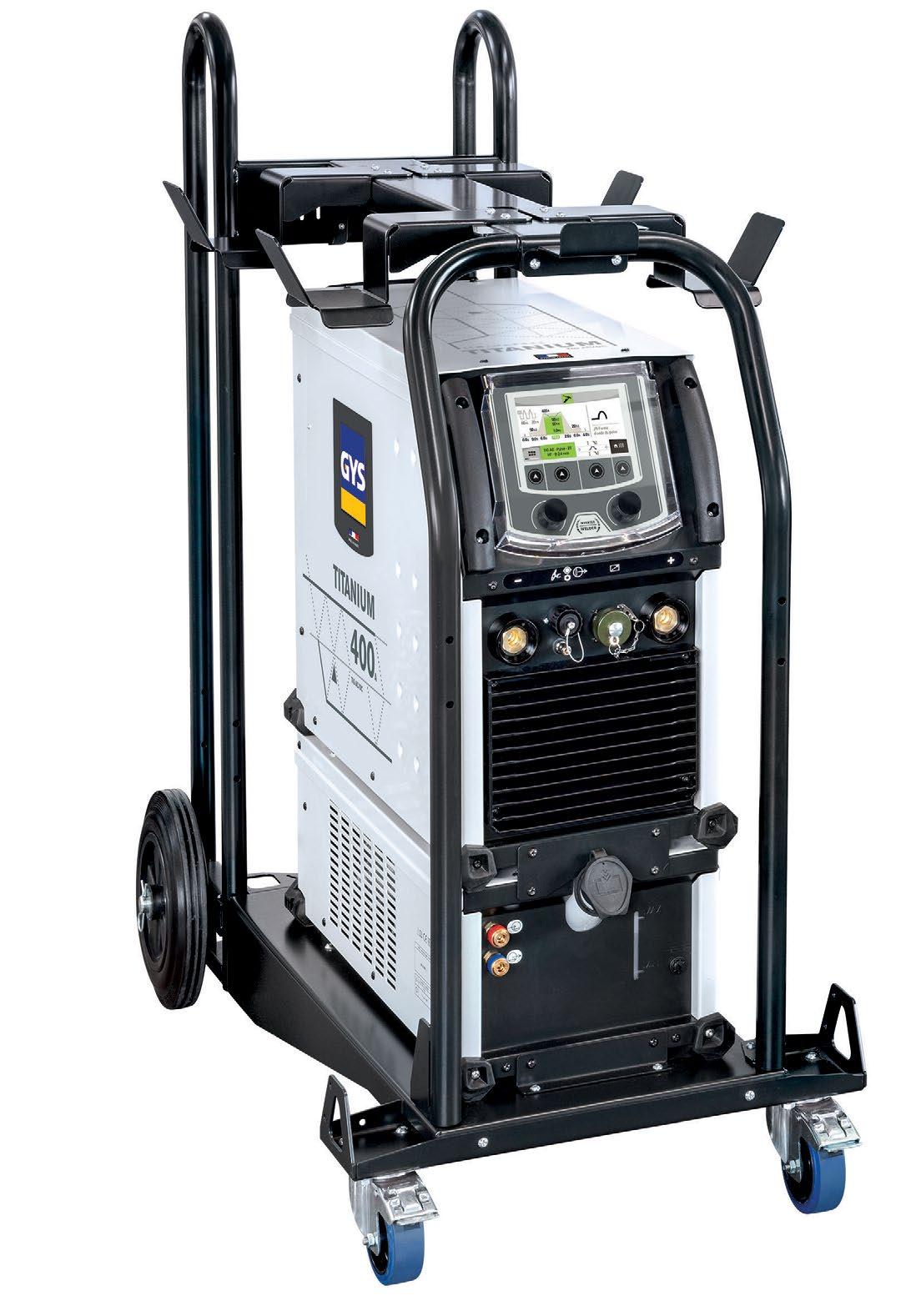
The TITANIUM 400 AC/DC is a high-performance TIG AC/DC generator (400 A to 60%) designed to offer a wide choice of welding processes (TIG AC, DC, MMA). It can be used to weld all types of materials; mild steel, stainless steel, aluminium, copper, titanium. Also ideal for welding thin gauge, its Pulse mode reduces heat input and provides better arc control. Intuitive and highly functional, its digital interface allows you to change welding parameters with ease.
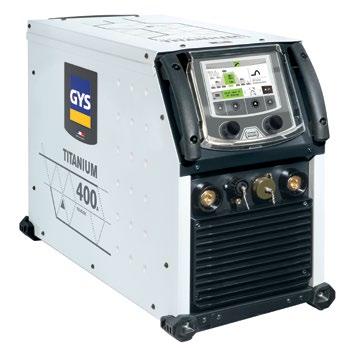
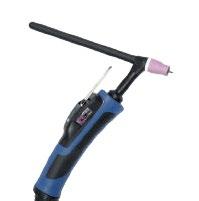

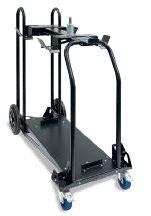
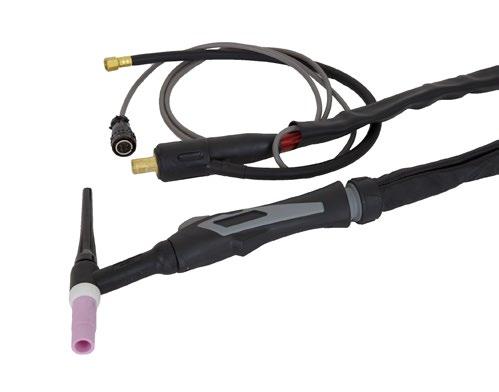
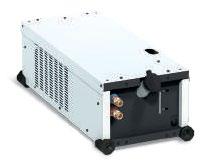
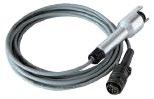
FIVE TIG/GTAW WELDING MODES
DC Standard: DC welding on most ferrous materials.
DC Pulse: Limits the heat input of the parts to be welded. Ideal for very thin sheets.
AC Standard: Welding of aluminium and its alloys (Al, AlSi, AlMg, AlMn...).
AC Pulse: Limits the heat input rise of the parts to be welded. Ideal for very thin sheets.
AC Mix: AC and DC current alternation accelerates productivity on aluminum assemblies.
AUTOMATION & ROBOTICS
• Connect five mode to control the generator from a console or PLC. Connectable via an optional bridge for robot use.
OPTIMIZED SETTINGS
Four Tacking Modes:
Spot/Multi Spot: Traditional tacking before welding thin sheet metal.
Tack/Multi Tack: Ultra-precise tacking and without oxidation reducing the risk of heat input. The points are invisible in the final weld bead.
Two Types of Start-Up: HF (without contact) or LIFT (with contact) for electro-sensitive environments.
Three Trigger Modes: 2T, 4T and 4T LOG
Parameter setting of AC and Pulse waveforms, facilitating arc control and penetration while reducing noise level.
Automatic detection of the torch: compatible with trigger, double button and potentiometer torches.
SMART
SYNERGIC Mode: Offers a configuration adapted to the type of welding after entering three data - type of material, thickness to be welded and welding position.
E-TIG Mode: Ensures a constant bead width and penetration, regardless of the torch’s position in relation to the part (welding energy control).
ADVANCED INTUITIVITY
New simplified HMI focused on the navigation habits of TIG welders (EASY).
• Ideal for compliance with WPQR and WPS (EXPERT and ADVANCED). Updatable machine and synergies via USB key.
• Cooling unit (ref. 013537) and trolley (ref. 037328) optional. Recording of 100 programs/jobs per process for repetitive tasks (can be saved on USB stick).
• Remote control (optional pedal or manual) connectable without tools. Intelligent ventilation management to reduce power consumption, dust extraction and substation noise.
SMAW/MMA WELDING
MMA: Coated, rutile, basic and cellulosic electrodes (up to Ø 8 mm).
MMA AC: Allows welding without magnetic disturbance of the arc.
MMA Pulse: Developed for welding in an upright vertical position.
ACCURATE
Calibration mode of welding accessories, to adjust the measurement of the voltage and improves the calculation of the energy.
ENERGY mode, display and calculation energy after welding according to the standards EN1011-1, ISO/TR 18491 and QW-409.
Portability - Load/backup user JOBs and machine configuration from a USB key.
Traceability - Trace/record all welding steps, bead by bead, during industrial manufacturing according to EN 3834.
TECHNICAL DATA:
Power Supply (V) 400V 3~
Rated Input Current | 1 eff’ (A)
(V)
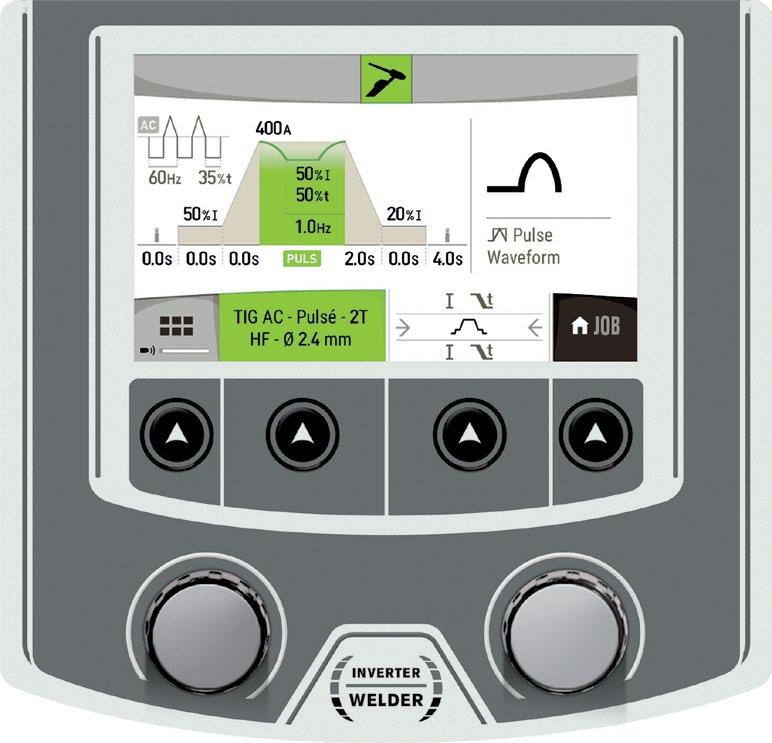
3 interface levels for the user:
• EASY (simplified display)
• EXPERT (full display) ADVANCED (specific applications)
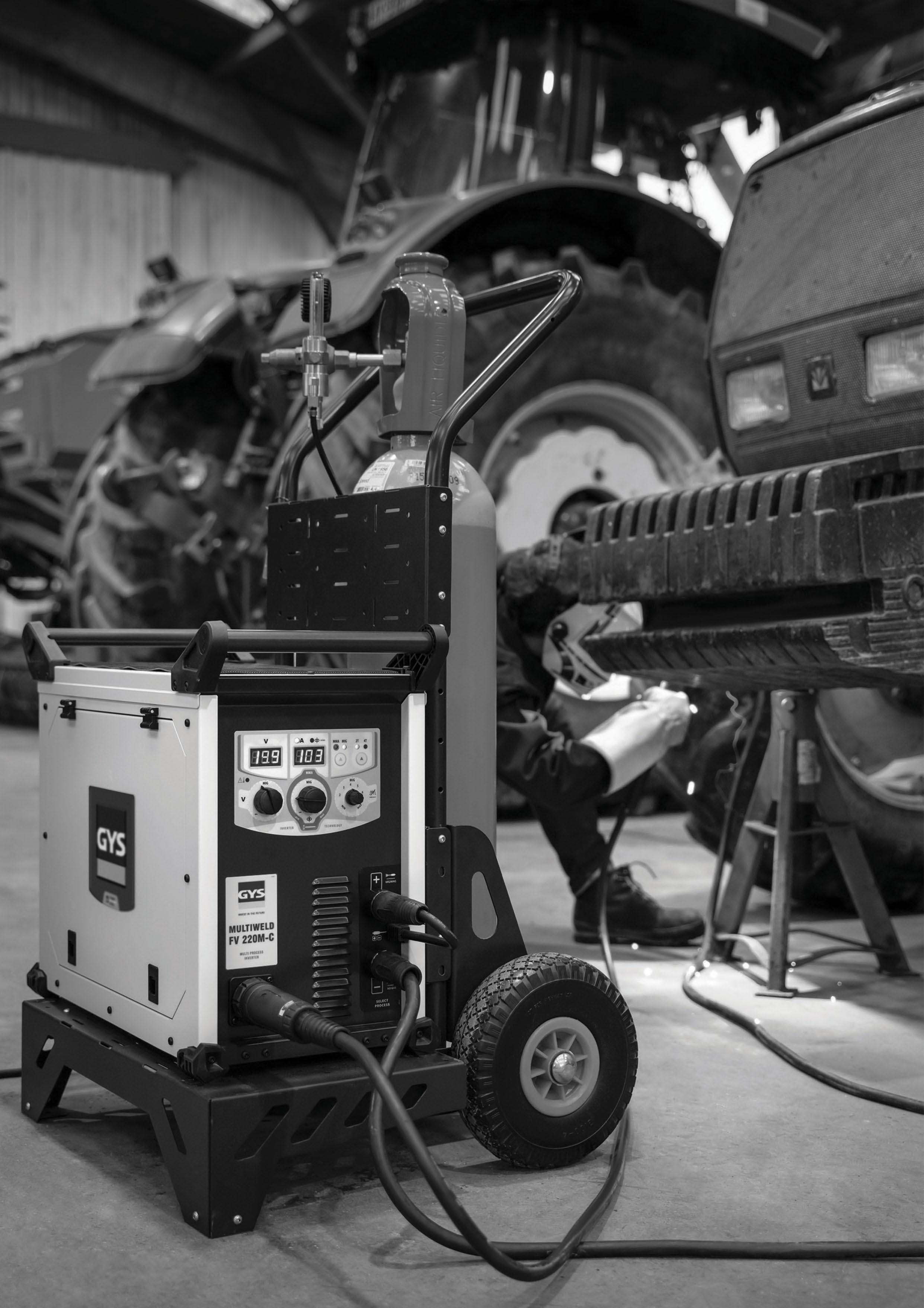
MIG/MAG WELDERS
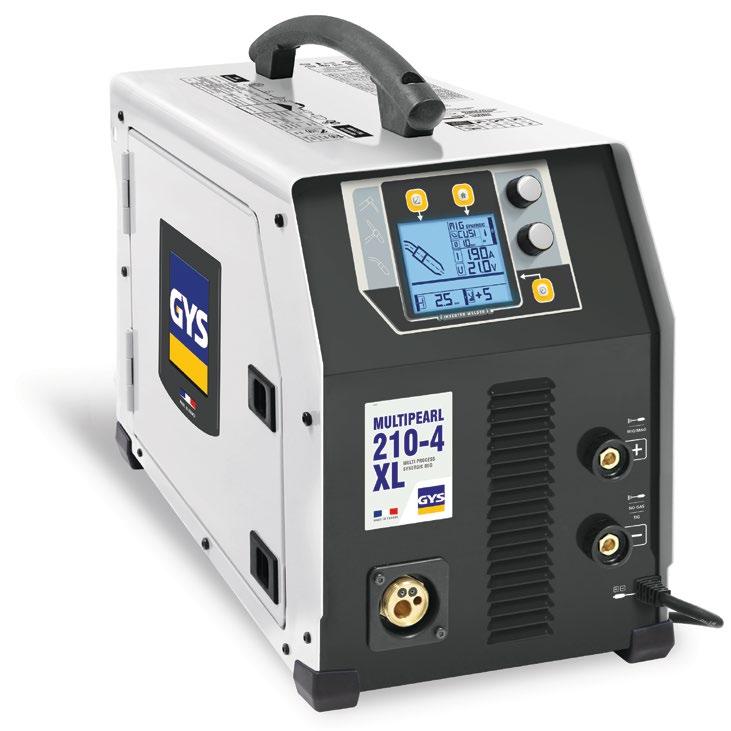
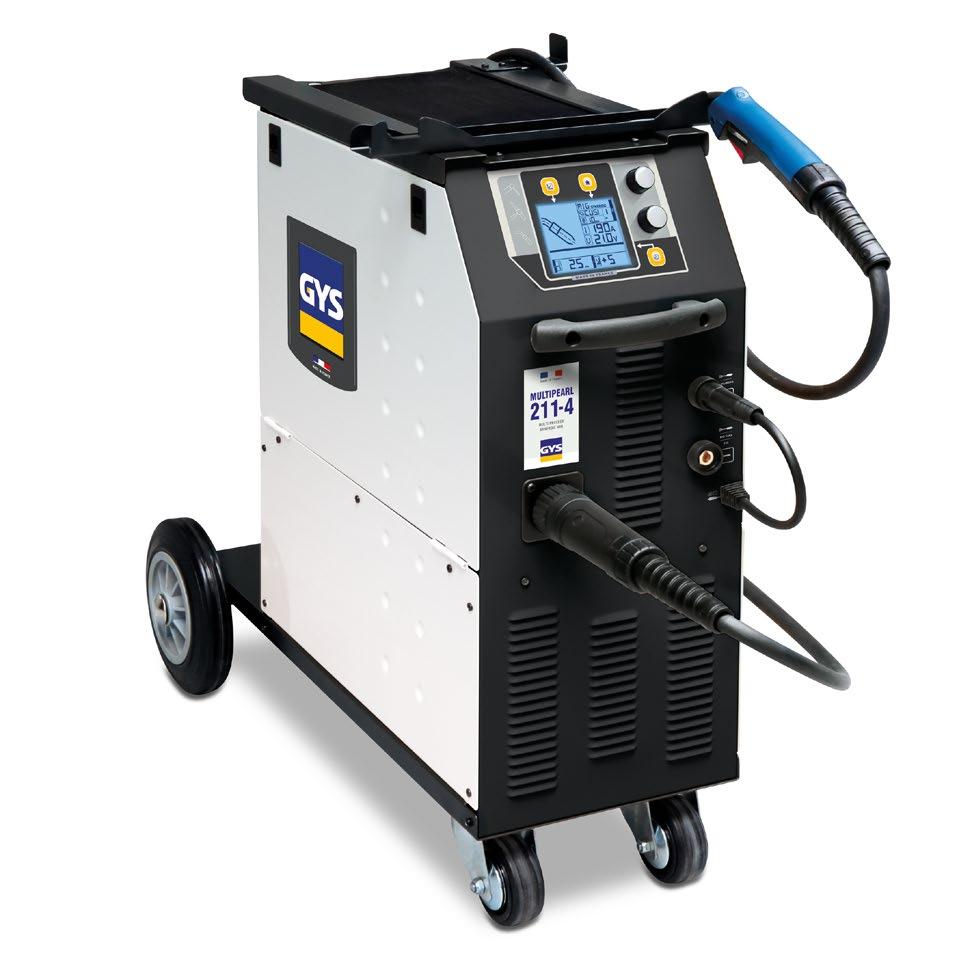
4 in 1, the MULTIPEARL 210-4 XL & 211-4, is a multi-process power source capable of performing MIG/MAG (with or without gas), TIG DC and MMA welding with high precision It features 9 welding synergies to enable welding in all positions. Versatile, but also equipped with a single-phase power supply with PFC/ FV technology, it is the perfect tool in the workshop or on site.
3 WELDING PROCESSES
MIG-MAG
Four roller motor: Ø 200 and Ø 300 mm reels.
• Adjustable manually or synergistically.
• SPOT and DELAY functions available. Can weld sheets from 0.6 to 6 mm thick.
TIG
• TIG DC welding and TIG Lift ignition with the TIG EURO torch.
• Adjustable Post Gas and Downslope (arc downslope).
MMA
• Welds different types of coated electrodes up to Ø 5mm (rutile, basic, stainless steel, steel, cast iron). Adjustable Hot Start (0 to 100%): facilitates ignition and can be adjusted according to the type of metal.
• Arc Force adjustable (0 to 100%): regulates the arc length deviations.
• Anti-Sticking: reduces the risks of the electrode sticking if it comes into contact with the workpiece.
MIG-MAG SYNERGIES
Automatic calculation of wire speed and tension according to:
• the type and diameter of the wire; the thickness to be welded;
• the gas used;
• the welding position.
Manual setting possible: wire speed and arc length.
ACCESSORIES:
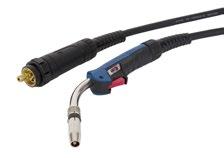
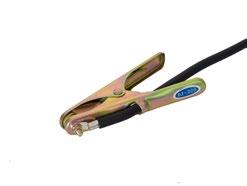
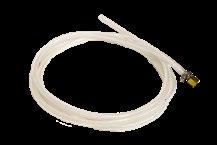
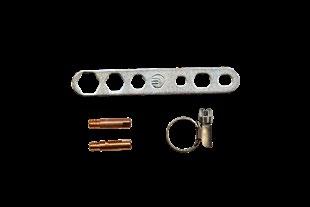
MULTIWELD FV 220M-C & 220M
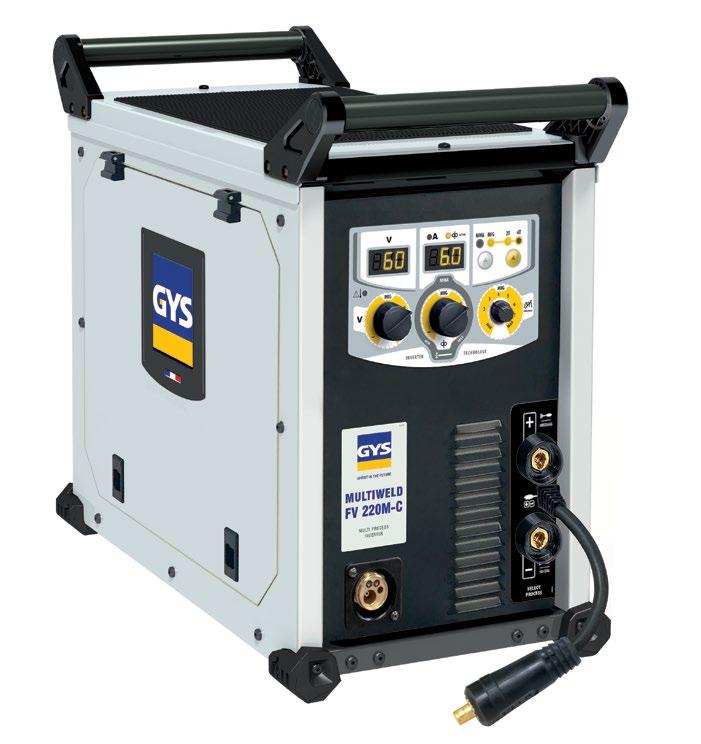
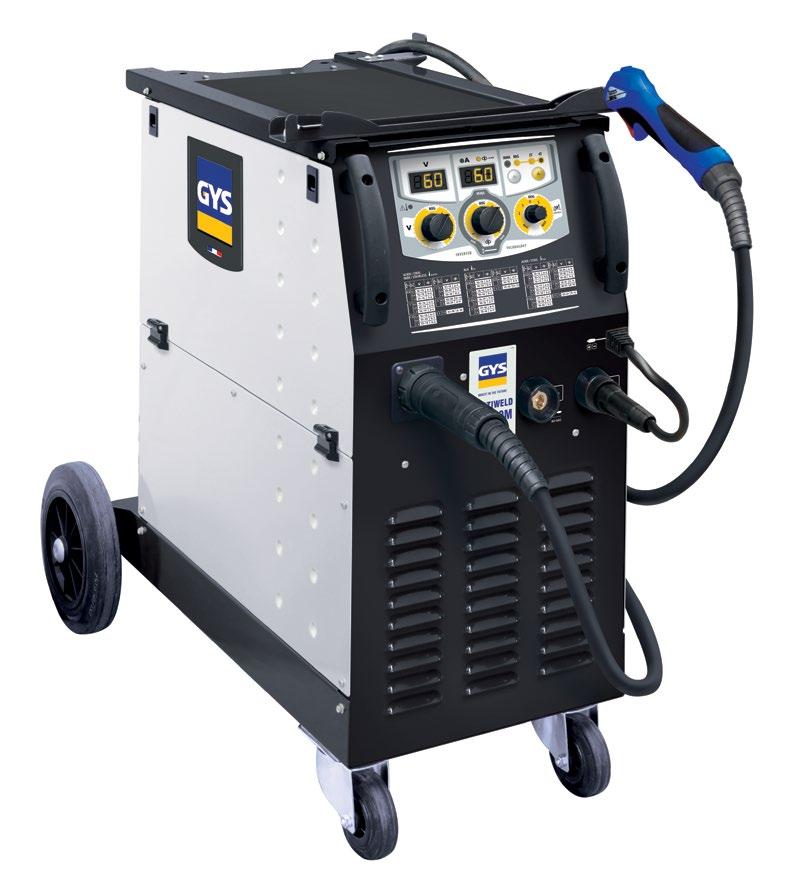
The MULTIWELD 220M-C & 220M is a single-phase welding machine, combining MIG/MAG, cored wire and MMA welding processes. It operates on a supply voltage between 85 and 265 V thanks to its FV (Flexible Voltage) power supply. Equipped with an accurate 4-roller wire feeder system and a reinforced structure with 2 handles for lifting and slinging, it is ideal for welding in the workshop and for quick troubleshooting on site.
MULTIPROCESS
MIG/MAG welding:
• Steel wire: Ø 0.6 to 1.0 mm
• Stainless steel wire: Ø 0.8 to 1.0 mm
Aluminium wire: Ø 0.8 and 1.0 mm
Cored wire (reverse polarity): Ø 0.9 to 1.2 mm
MMA welding: basic and rutile electrodes (up to Ø 5 mm).
OPTIMISED MIG/MAG SETTINGS
Choice of the trigger mode: 2T or 4T.
Welding guide: tables assist the user to adjust and fine tune the voltage and the diameter of the filler wire according to the thickness of material being welded.
INTEGRATED WIRE FEEDER
Wire feeder with four rollers for an efficient wire feeding.
PRE-HEATING, PURE CO2
Pre-installed socket (36 V - 4.2 A) for gas heater in pure CO2 welding (heater not included).
ROBUST
IP 23 classification for outside use.
• Accepts very long extension cords (100 m).
• Protected against overvoltage up to 400 V (PROTEC 400).
P400 PROTEC 400
TECHNICAL
ACCESSORIES:
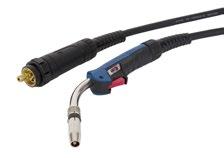
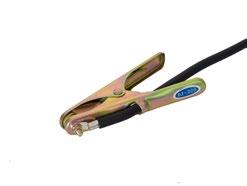
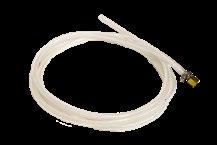
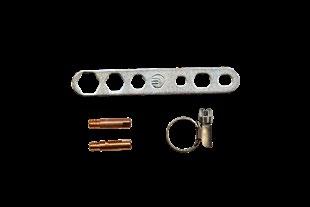
MULTIWELD 320T-C & 320T
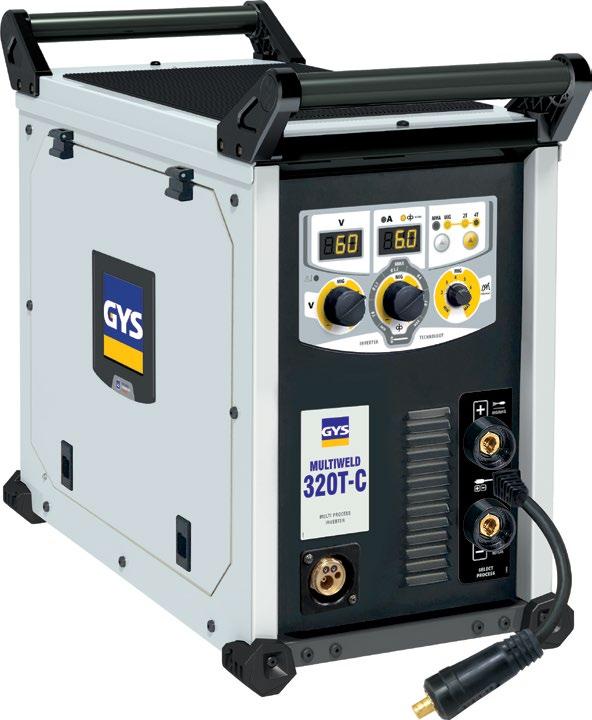
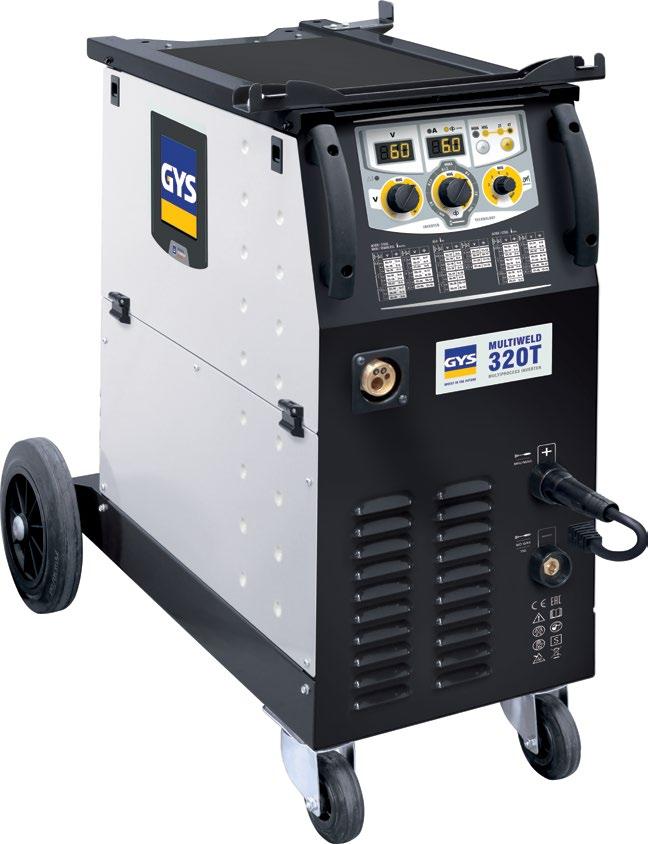
MULTIPROCESS
MIG/MAG Welding:
Steel wire: Ø 0.6 - 1.2 mm
• Stainless-steel wire: Ø 0.8 - 1.2 mm
• Aluminium wire: Ø 0.8 and 1.0 mm
Flux-cored wire (polarity inversion): Ø 0.9 - 1.2 mm
MMA Welding: Basic and rutile electrodes (up to Ø 6 mm).
ADVANCED MIG/MAG SETTINGS
Choice of trigger performance: 2T or 4T
Welding support chart: a chart on the machine’s side helps the user adjust the tension and diameter of the filler wire according to the thickness of the material being welded.
BUILT-IN WIRE-FEED REEL
Powerful, four-roller, motorised wire-feed rollers for efficient unwinding.
PURE CO2-GAS PREHEATING
Pre-installed socket (36 V / 4.2 A) for heating gas in pure CO2 welding (heater not included).
The MULTIWELD 320T-C & 320T is a three-phase welding machine that combines MIG/MAG, flux-cored wire and MMA welding processes. Its intuitive interface integrates digital displays for easy and precise adjustment. Equipped with a precise and powerful four-roller wire-feed system, the MULTIWELD 320T- C can weld Ø1.2 mm wire effortlessly. Its reinforced structure, with two handles for lifting and carrying, is perfectly suited for workshops and quick on-site repairs.
TECHNICAL
ACCESSORIES:
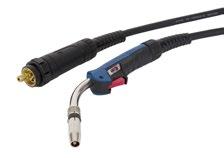
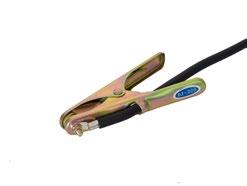
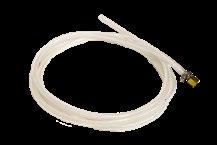
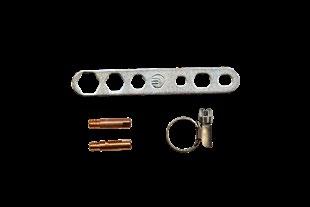
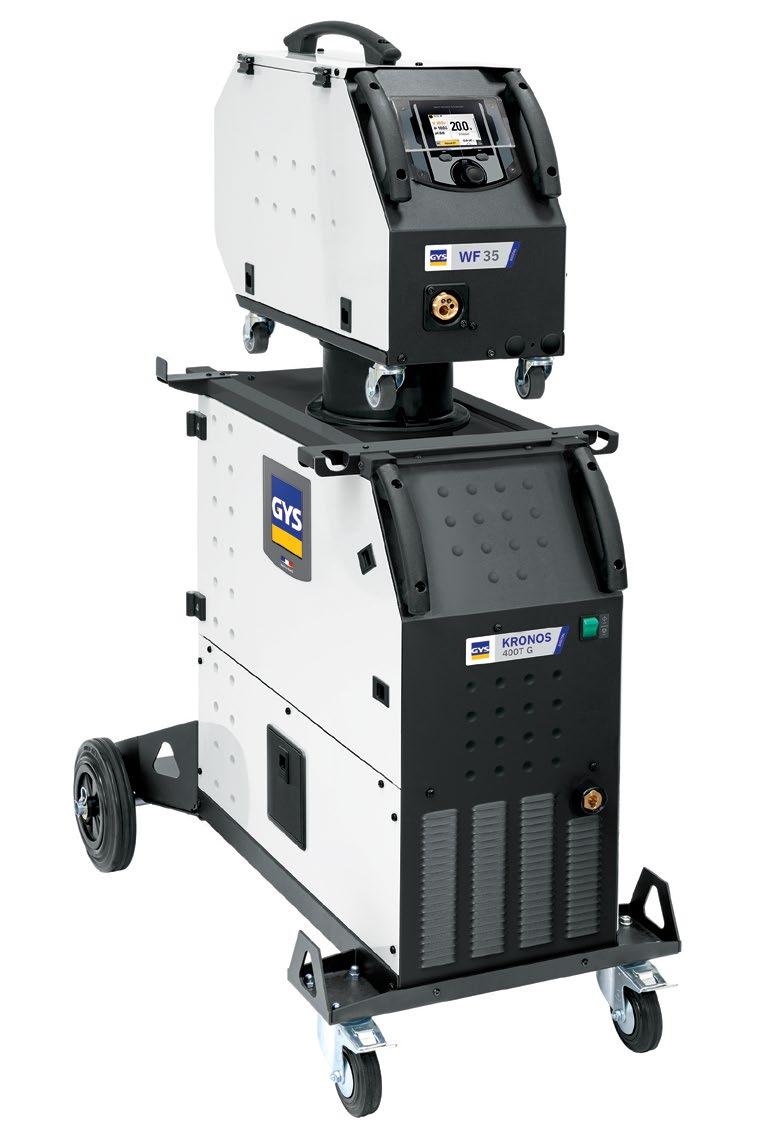
MULTIPROCESS
MIG/MAG Welding:
Steel and stainless steel wire: Ø 0.6 to 1.2 mm
• Aluminium wire: Ø 0.8 to 1.2 mm
• Flux-cored wire (inverted polarity): Ø 0.9 to 1.6 mm
MMA DC/Pulse: Basic and rutile electrodes.
TIG DC Lift/Pulse.
INTELLIGENT
Specific synergies for: Steel, AlMg, AlSi, CrNi, CuSi.
• After entering three pieces of data: Wire diameter, material/gas and thickness, the product automatically determines the optimal welding parameters.
• New bright and user-friendly 3.5’’ HMI. Full machine software and synergy updates available via USB stick.
• Storage of up to 200 welding programs (Job) for recurring tasks. Portability function, the ability to load/save/transport user JOBS and machine configuration via USB stick. On-demand ventilation system to reduce dust ingress, and increase energy efficiency.
PREMIUM WELDING
Digital arc control with instantaneous ignition. Very stable arc which reduces welding spatter. Four-roller wire feeder with digital encoder for smooth operation.
TWO DISPLAY MODES
Easy - Streamlined interface suitable for the vast majority of users to achieve the best possible weld quality.
Expert - Dedicated interface for the most experienced welders, allows the user to adjust all the parameters of the welding cycle.
ERGONOMIC
Reinforced wheels for stability and manoeuvrability.
• Gas bottle support up to 10 m3 (50 L).
• IP 23S rated to withstand difficult environments. Large storage compartment.
• Four lifting points for easy handling and safe transport.
The KRONOS 400T G is a three-phase, multi-process power source, with separate wire feeder. Its innovative technology ensures excellent arc characteristics for the most demanding MIG/MAG applications. The integrated synergies make set-up much easier, and reduce spatter during welding. In combination with the optional WF 35 wire feeder, it allows precise adjustment of welding parameters to help achieve excellent results.
TECHNICAL DATA:
ACCESSORIES:
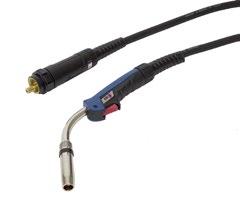
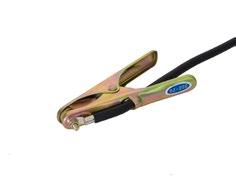
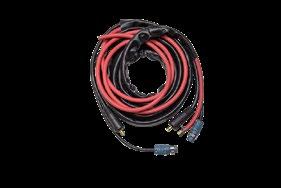
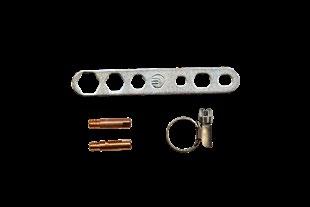
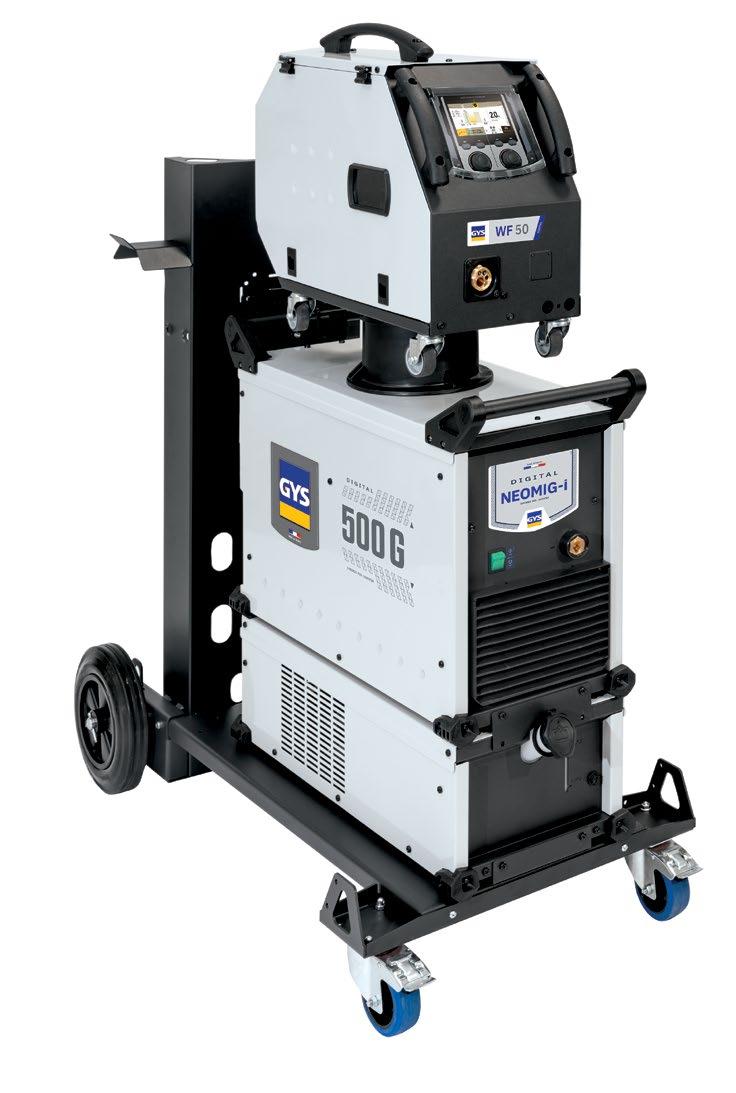
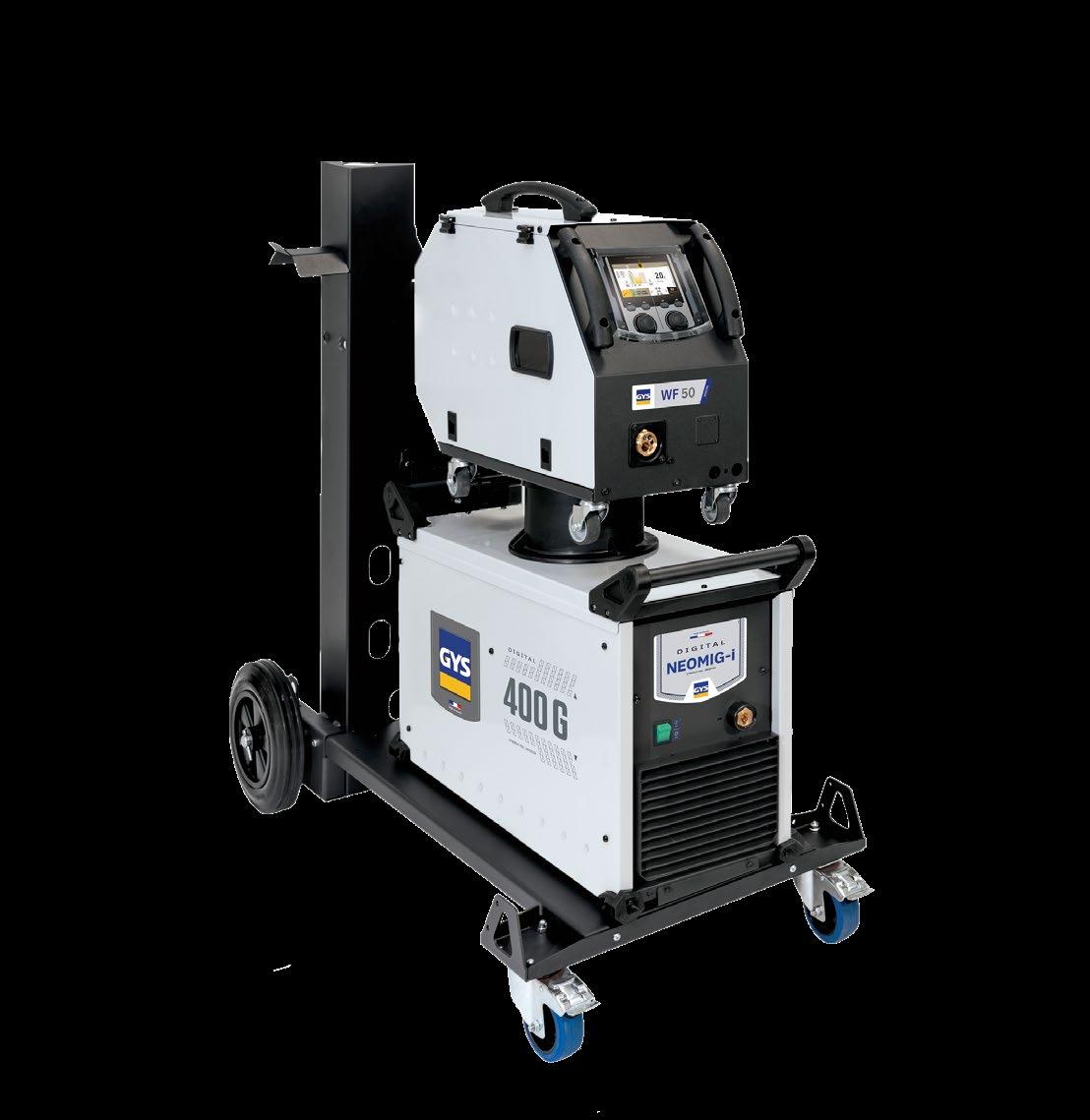
MULTIPROCESS
MIG/MAG:
Steel and stainless steel wire: Ø 0.6 to 1.6mm
• Aluminium wire: Ø 0.8 to 1.6mm
• CuSi and CuAl wire: Ø 0.8 to 1.6mm Cored wire (polarity reversal) : Ø 0.9 to 2.4mm MMA DC/Pulse: Basic, rutile and cellulosic electrodes. TIG DC Lift/Pulse. Air-Arc Gouging.
INTELLIGENT
• Specific synergies for: Steel, AlMg, AlSi, CrNi, CuSi. After entering three pieces of data: Wire diameter, material/gas and thickness, the product automatically determines the optimal welding parameters.
• Full machine software and synergy updates available via USB stick. Storage of up to 200 welding programs (Jobs) for recurring tasks.
PREMIUM WELDING High duty cycle of 100% at 400A and 60% at 500A
• Digital arc control with instantaneous ignition. Very stable arc which helps to reduce welding spatter.
• Compatible with WF 35 and WF 50 wire feeders.
MAXIMUM CONNECTIVITY
• Traceability of all weld beads according to EN 3834. Calibration mode for welding accessories in order to amend the voltage displayed.
• Connectable via an optional kit (062993) for use with robotic systems.
• User mode to share the product between multiple operators. Free online tool to customise the interface.
• Compatible with KOOLWELD 2 cooling unit (075115).
• Optional Push-Pull torch connection (078741) for WF 50 wire feeder.
INDUSTRIAL DESIGN
IP 23 protection rating.
• On-demand ventilation system to reduce dust ingress and power consumption. Ideal height to view settings conveniently.
• Reinforced housing for demanding environments. Easy disassembly for maintenance.
• Optional dust filter (046580).
• Interconnection cables up to 10m for an extended working area.
The NEOMIG-i 400 G and 500 G is a three-phase, multi-process power source with separate wire feeder. Its advanced digital technology and duty cycle ensure excellent arc characteristics for industrial MIG/MAG applications. The integrated synergies make set-up considerably easier, and reduce spatter during welding. When equipped with the WF wire feeder, the machine offers precise control of the welding parameters in order to deliver the best possible results.
ACCESSORIES:
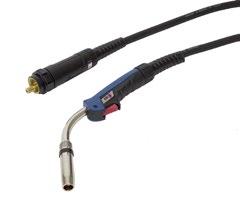
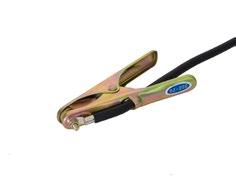
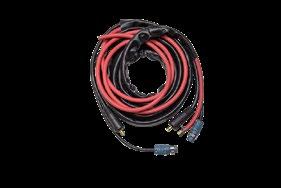
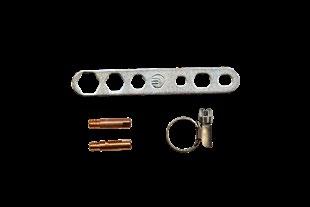
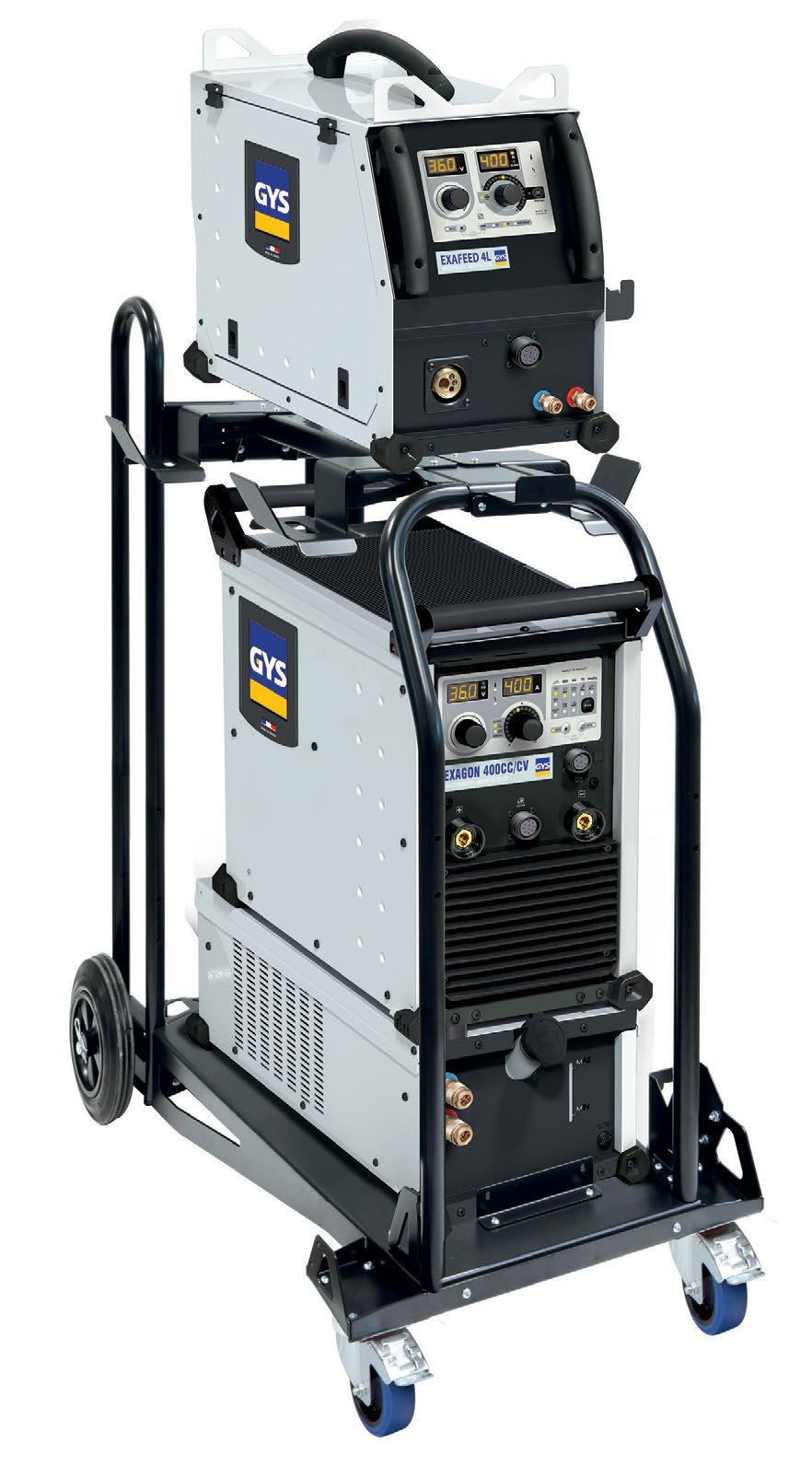
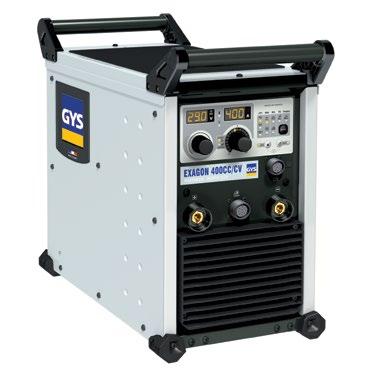
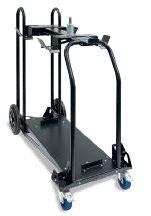
Powered by inverter technology, the EXAGON 400 combines MMA, MIG-MAG & TIG in a single machine, offering exceptional welding performance. Featuring advanced electronics and a reinforced structure, this station guarantees maximum productivity, even in the most hostile environments. Powerful, sturdy and versatile, the EXAGON 400 takes welding to the next level.
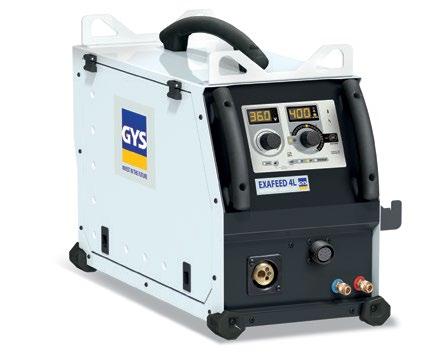
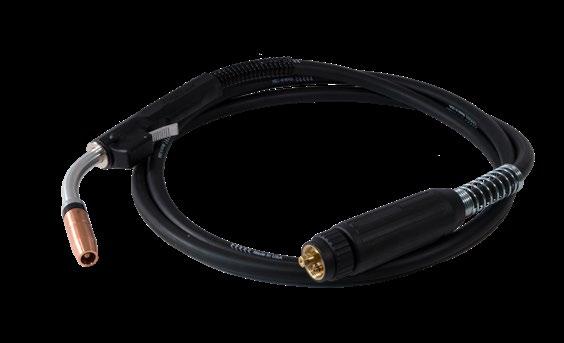
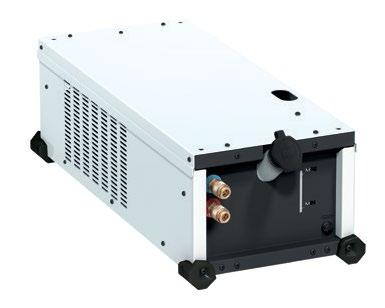
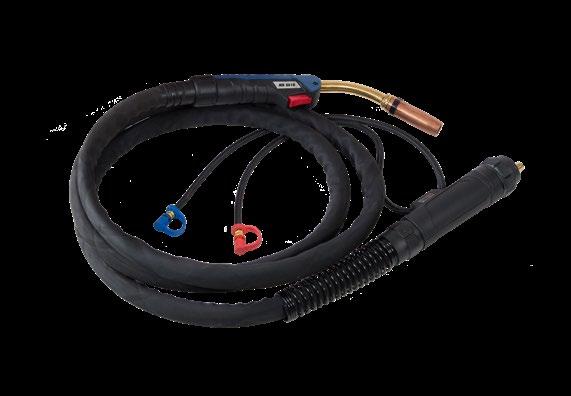
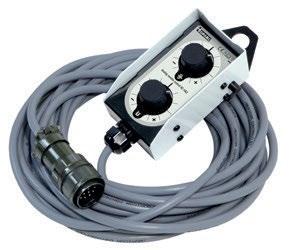
3 WELDING PROCESSES
Versatile thanks to its six modes:
Interconnection Cables Air
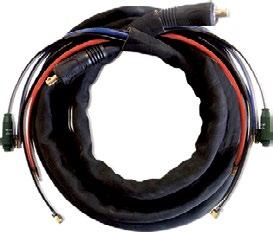
WA-047587 5m - 70mm2
WA-047594 10m - 70mm2
WA-047617 5m - 70mm2
WA-047624 10m - 70mm2
MMA: Basic, rutile and cellulosic electrodes (up to Ø 6 mm).
MMA Pulse: Ideal for rising vertical welding.
MIG/MAG: Solid wire (Ø 0.6/1.6 mm) and cored wire (Ø 2.4 mm).
• Workshop water cooled wire feeder (optional EXAFEED 4L). Construction site wire feeder (optional NOMADFEED).
Arc Gouging with carbon electrode (up to Ø 6.4 mm).
TIG DC with TIG lift start.
INTENSIVE USE
Suited for offshore, naval and railway construction and metal works:
• Increased productivity thanks to its strong duty cycle (400A @ 60%).
Optimised cooling thanks to the air-tight ventilation corridor that helps insulate the electronic components from the dust.
INTUITIVE Visible display, even when exposed to the sunlight.
• Simple interface with easily adjustable buttons and knobs, adapted to gloved hands. Stores 50 presets for each process.
• Remote control (optional).
USER PROTECTION
VRD (Voltage Reduction Device) to lower no load voltage < 35V. Lockable keyboard to protect against misuse.
TECHNICAL DATA:
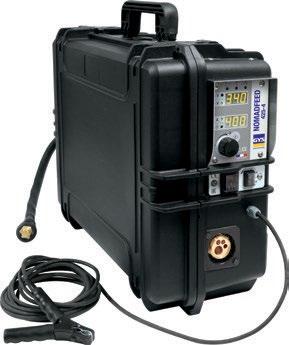
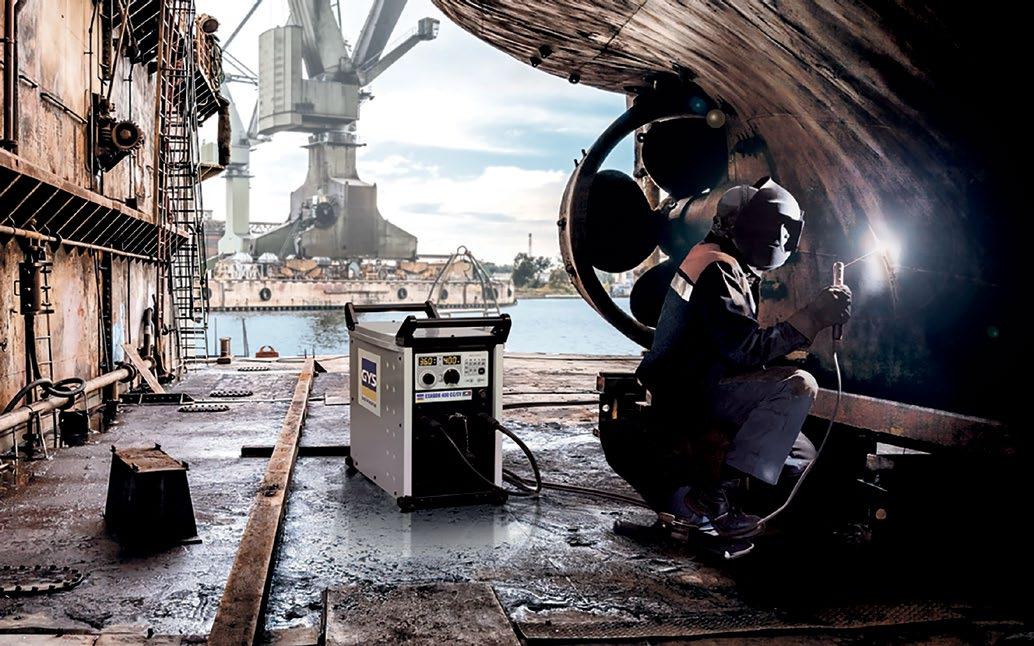
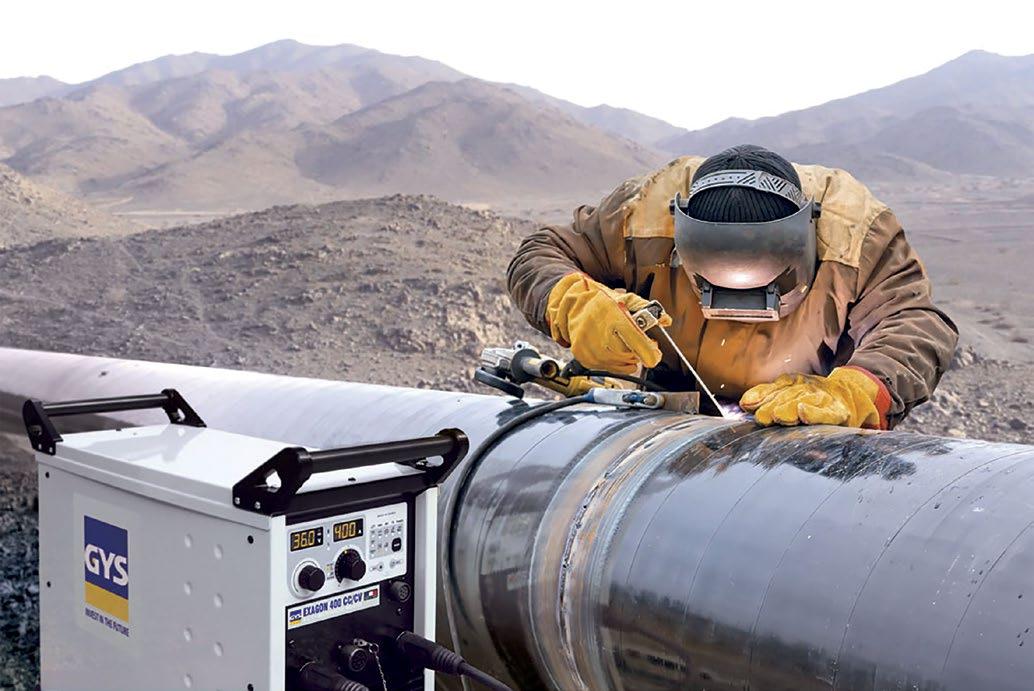
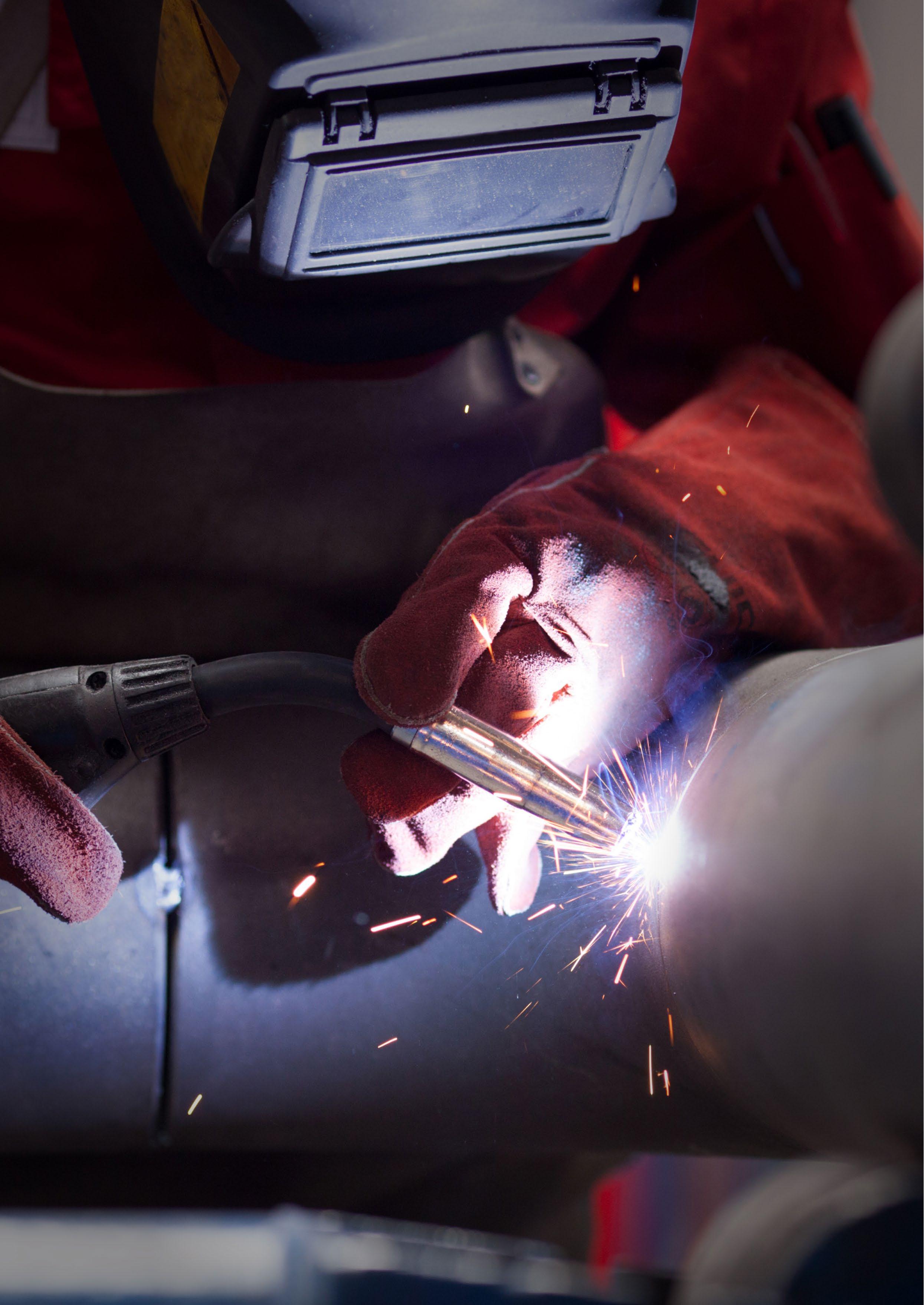
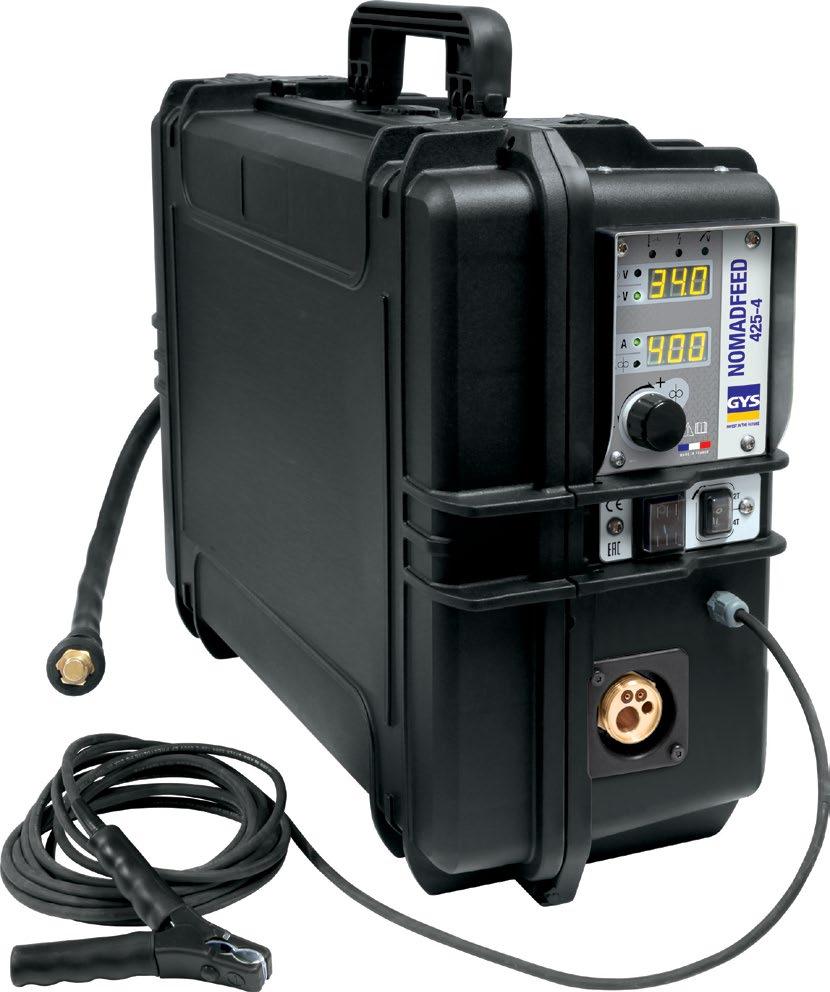
OPTIMUM MIG/MAG SETTINGS
Electronically controlled wire speed adjustable using the potentiometer at the front of the machine.
Choice of two torch trigger modes: 2T or 4T.
• Wire speed regulation modes: CC (current source) or CV (voltage source).
Soft start function - easier first contact with the metal.
• Precise wire pressure adjustment.
Choice of information displayed on screen.
HEAVY DUTY
Heavy duty cycle for enhanced productivity (425A @ 60%).
• Compatible with air cooled torches and water cooled torches connected to an external cooling unit.
Powerful electronically regulated wire feed motor (100W).
The four drive rolls ensure a smooth feed on all types of wire.
ERGONOMIC
• Display of current/voltage/wire speed (for DMOS).
• Display screen is readable even in very bright situation. Straightforward interface with buttons designed to be
• operated while wearing gloves.
EURO torch connection.
• Easy wire feed.
Quick torch air purge.
TECHNICAL DATA:
The NOMADFEED 425-4 is a wire feed case that takes its power directly from the welding circuit. . Ideal for MIG/MAG, the feed case is recommended for site work and is compatible with most welding generators in the market.
NEOPULSE 220 C XL
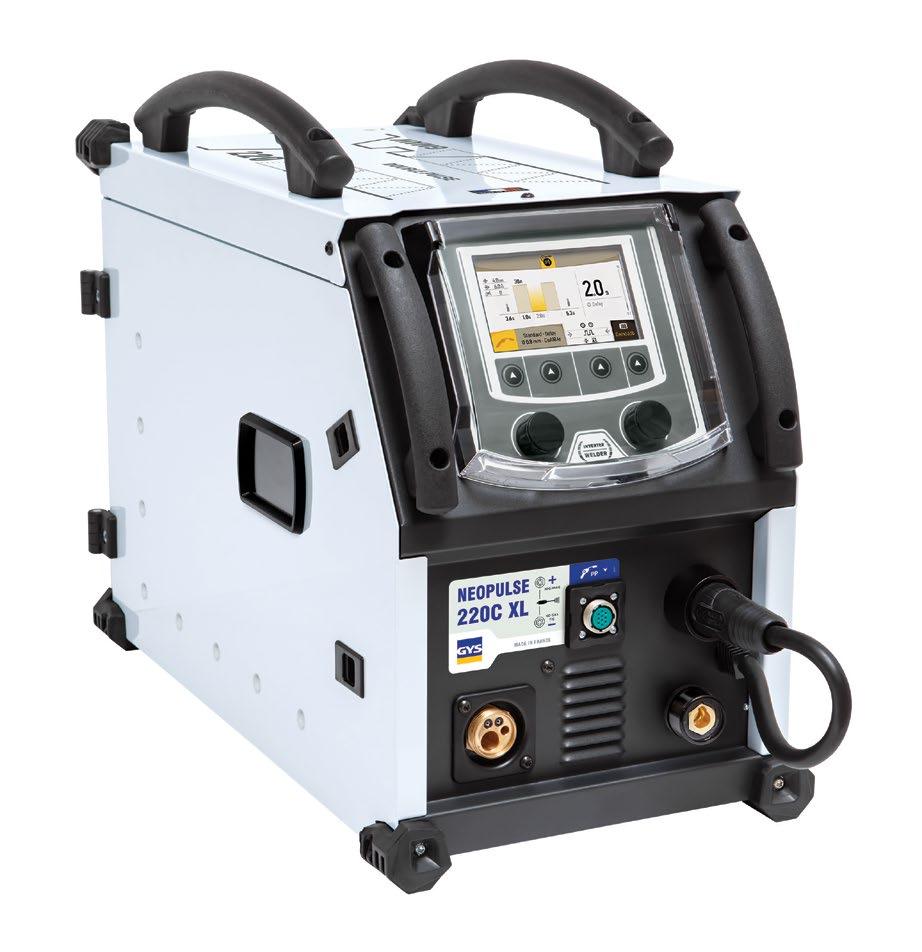
MULTI-PROCESS WELDING
MIG/MAG:
• Steel and stainless steel wire: Ø 0.6 to 1.0 mm
Aluminium wire: Ø 0.8 to 1.2 mm
• CuSi and CuAl wire: Ø 0.8 to 1.0 mm
MMA DC/Pulse: Basic, rutile and cellulosic electrodes (up to Ø 5 mm).
TIG DC/Pulse.
SMART
SYNERGIC Mode: After selecting two criteria (material/gas combination and the wire diameter), NEOPULSE automatically works out the optimal welding conditions while still allowing you to adjust the settings (wire feed rate, voltage, current, arc length).
ACCURATE
Calibration of the wire feed speed to adjust the displayed voltage measurement and refine the energy calculation.
Energy display and energy calculation after welding based on standards EN1011-1, ISO / TR 18491 and QW-409.
Portability - Load/backup user JOBS and machine configuration from a USB key.
Traceability - Trace/record all welding steps, cord by cord, during industrial manufacturing in line with standard EN ISO 3834.
OPTIMISED MIG/MAG
SETTINGS
Welding processes: Manual, Standard, Pulsed, Arc Module (variation of hot/cold current)
TACK modes: SPOT and DELAY.
Trigger options supported: 2T and 4T.
Precise control over the welding cycle: CreepSpeed, Softstart, Hotstart, Upslope, Downslope, Crater Fill, Postgas, etc.
MAXIMUM PRODUCTIVITY
Four microprocessors giving four times the processing power.
• High productivity thanks to high duty cycle (150A @ 60%).
Compatible wire reels: Ø 200/300 mm.
• Powerful four roller wire-feeder for efficient wire feeding.
• Very high arc voltage for easier ignition and exceptional arc dynamic.
The NEOPULSE 220 C XL is a single-phase pulsed MIG/MAG generator with digital technology. Designed for the highest performance level using the latest technology, it features numerous synergic curves and exceptional arc quality/ performance. Intuitive and highly functional, the digital interface allows for quick and easy modifications of the welding parameters. Fitted with an accurate and powerful 4 drive roll feeding system, the NEOPULSE 220 C XL offers manufacturers maximum productivity.
INTUITIVE
New user friendly interface focused on welders’ navigation habits.
• Update of the machine and synergies using a USB key.
Storage of 500 welding programs (can be saved on USB stick).
• Displays current/voltage during and after welding (WPS/PQR).
• Choice of the main parameter to display on the screen (wire speed, average welding current, etc.).
• Internal lighting of the wire feed motor and wire reel. Viewing window on wire door to check the state of wire.
• Intelligent ventilation management to reduce power consumption, dust intake and noise.
Compatible torch Push Pull (24 V).
TECHNICAL DATA:
| 1 eff’ (A)
ACCESSORIES:
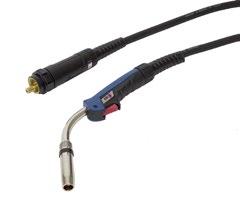
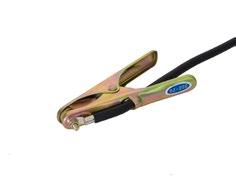
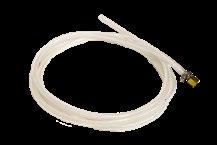
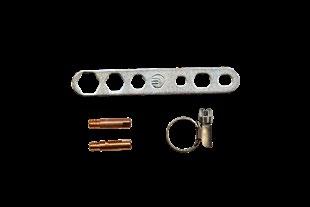
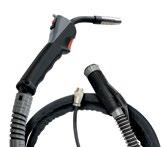
NEOPULSE 320 C
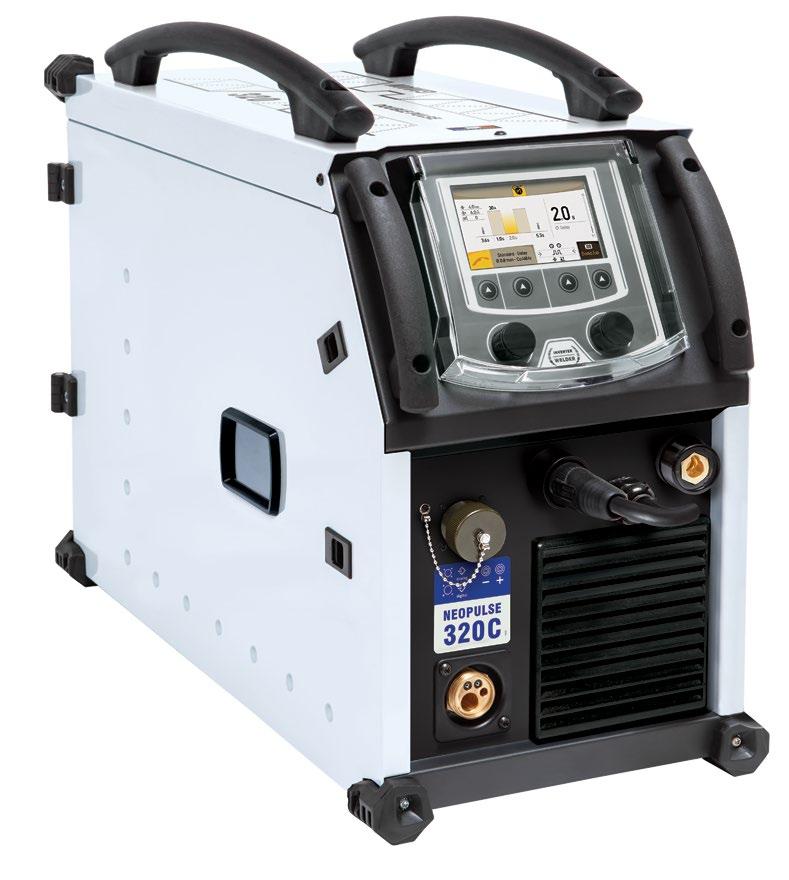
MULTI-PROCESS WELDING
MIG/MAG:
• Steel wire: Ø 0.6 to 1.2 mm Stainless steel wire: Ø 0.8 to 1.2 mm
• Aluminium wire: Ø 0.8 to 1.2 mm
• CuSi and CuAl wire: Ø 0.8 to 1.2 mm
MMA DC/Pulse: Basic, rutile and cellulosic electrodes (up to Ø 5 mm).
TIG DC Lift/Pulse.
SMART
SYNERGIC Mode: After selecting the material/gas combination and the wire diameter the NEOPULSE 320 C will automatically work out the optimal welding settings whilst still allowing you to adjust the settings (wire-feed speed, voltage, current and arc length).
ACCURATE
Calibrate the welding cables and motor speed to adjust the displayed voltage and refine the energy calculation. Energy consumption, displays and calculates the energy consumption after welding in accordance with standards EN1011-1, ISO/TR 18491 and QW-409. Portable - Load/save user JOBS and machine settings using a USB key.
Traceability - Track/record all welding stages, weld by weld, during industrial manufacturing in accordance with standard EN ISO 3834.
OPTIMISED MIG/MAG SETTINGS
Welding processes: Manual, Standard Dynamic, Pulsed, Arc Module (a variation of hot/cold current).
TACK modes: SPOT and DELAY. Trigger options: 2T and 4T.
Precise control of the entire welding cycle: CreepSpeed, Softstart, Hotstart, Upslope, Downslope, Crater Fill and Post-Gas, etc.
MAXIMUM PRODUCTIVITY
Intended for heavy and demanding industrial applications:
• Four microprocessors increase the communication speed and optimise the machine’s efficiency. High productivity thanks to its high duty cycle (300 A @ 60%).
• Compatible wire-feed reels: Ø 200/300 mm.
Can be connected to a SAM control interface for automated or robotic applications (optional).
• Robust design to withstand shocks and vibrations. Powerful, motorised wire-feed system (100 W) with four active drive rolls.
• Very high arc voltage for easier ignition and exceptional arc dynamics.
The NEOPULSE 320 C is a digital, three-phase, pulsed, MIG/ MAG welding machine. Designed to operate at the highest performance level using the latest technology, it features various synergy curves as well as exceptional arc quality and performance. User friendly and highly practical, its digital interface is designed to allow the welding settings to be quickly and easily adjusted. Equipped with a precise, four-reel, wire-feeding system, this power source provides unparalleled productivity and welding quality on all types of materials.
EASY TO USE
New user friendly interface focused on the welders’ navigation habits.
• Machine and synergy updates using a USB key. Optional cooling unit (P.N. 013537) and trolley (P.N. 037328).
• Stores up to 500 welding programs (can be saved to a USB key).
• Displays the current/voltage during and after the welding process (WPS/PQR).
• Choose which key parameter setting to display on the screen (wire-feed speed, average welding current, etc.).
• Internal lighting system for the wire-feed motor and reel.
• Viewing window on wire-compartment’s door for easily wire monitoring. Smart ventilation management system to reduce power consumption, dust intake and noise. Compatible with Push-Pull torch (24 V / 42 V).
TECHNICAL DATA:
Power Supply (V)
ACCESSORIES:
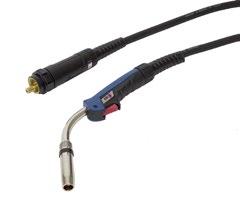
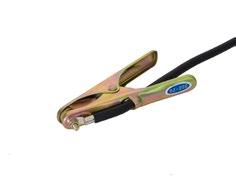
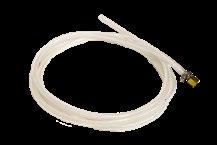
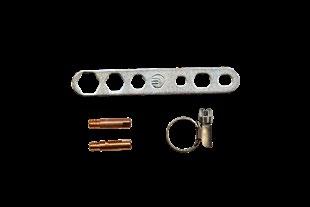
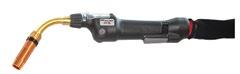
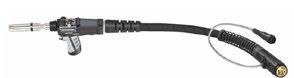
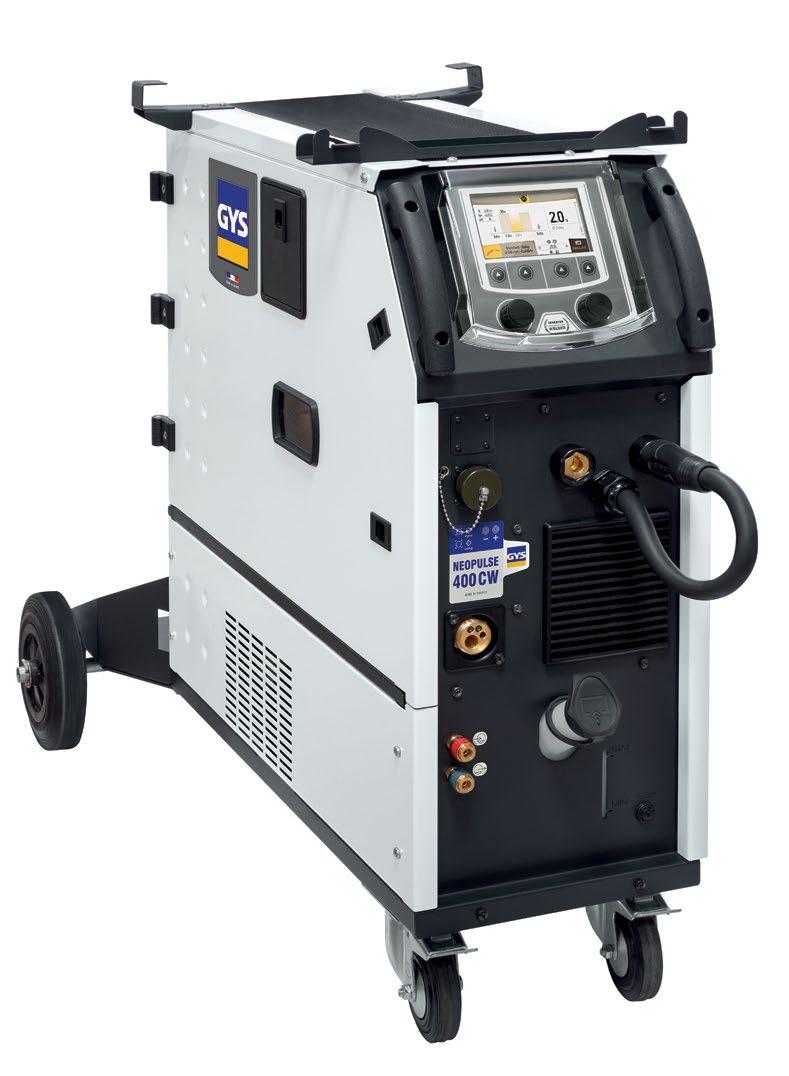
MULTI-PROCESS WELDING
MIG/MAG:
• Steel and stainless-steel wire: Ø 0.6 to 1.6 mm Aluminium wire: Ø 0.8 to 1.6 mm
• CuSi and CuAl wire: Ø 0.8 to 1.6 mm
• Flux-cored wire: Ø 0.9 to 2.4 mm
MMA DC/Pulse: Basic, rutile and cellulosic electrodes (up to Ø 6 mm).
TIG DC Lift/Pulse.
Gouging (up to Ø 6.5 mm).
SMART
SYNERGIC Mode: After entering two data (material/gas torque or wire diameter), the NEOPULSE automatically determines the optimal welding conditions and automatically adjusts the settings (wire feed speed, voltage, current and arc length).
ACCURATE
Calibration of welding accessories and motor reel speed, to adjust the displayed voltage measurement and improve energy data.
Energy data display and post-welding energy data is available according to standards EN1011-1, ISO/TR 18491 and QW-409.
Portability - Download/backup/transfer user JOBS and machine configuration information from a USB stick.
Tracking - Trace/record all welding stages, bead by bead, during industrial processing within the framework of standard EN ISO 3834.
OPTIMISED MIG/MAG SETTINGS
5 MIG-MAG welding modes: Standard Dynamic, Standard Impact, Pulsed, Modularc and Manual.
MAXIMUM PRODUCTIVITY
• Four microprocessors increase calculation speeds and optimise the machine’s efficiency.
• High productivity thanks to its high duty cycle (400 A @ 60%). Compatible wire spools: Ø 200 / 300 mm.
• Can be connected to a robot/PLC through a SAM control interface (optional).
Dip coating of the entire power block for increased resistance.
• Powerful, electronically-controlled motor reel (100 W) with four driven rollers.
• High arc voltage for easy ignition and outstanding arc dynamics.
The NEOPULSE 400 CW is a three-phase, pulsed, MIG/MAG generator developed for heavy industry. The NEOPULSE 400 CW is mobile and equipped with a cooling unit and a powerful reeling system, making it ideal for handling demanding pulsed applications. Both intuitive and highly practical, its digital interface makes adjusting the welding settings very easy.
ERGONOMIC
New, simplified interface focused on welders’ browsing habits.
• Full machine updates and pre-installed user setting updates by USB key.
• Up to 500 welding programmes saved on the machine (can also be saved on USB stick).
Current/voltage display during and after welding (DMOS/QMOS).
• User mode facilitates the shared use of the product with multiple users.
• A selection of main settings can be displayed on the screen (wire speed, average welding current, etc.).
Smart ventilation management to reduce power consumption, dust extraction and machine noise. Compatible Push-Pull torch (24 V / 42 V).
TECHNICAL DATA:
Power Supply (V)
Duty Cycle
3 x 400V +/- 15%
60% @ 400A
100% @ 360A
No Load Voltage (V) 85
Weight (kg) 78
ACCESSORIES:
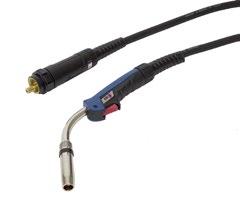
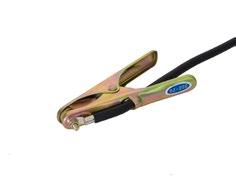
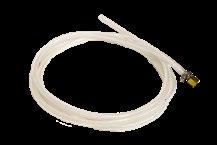
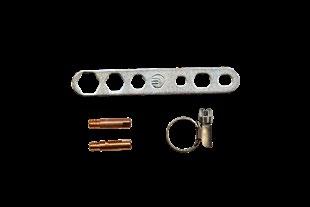
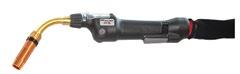
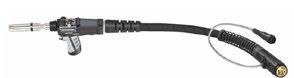
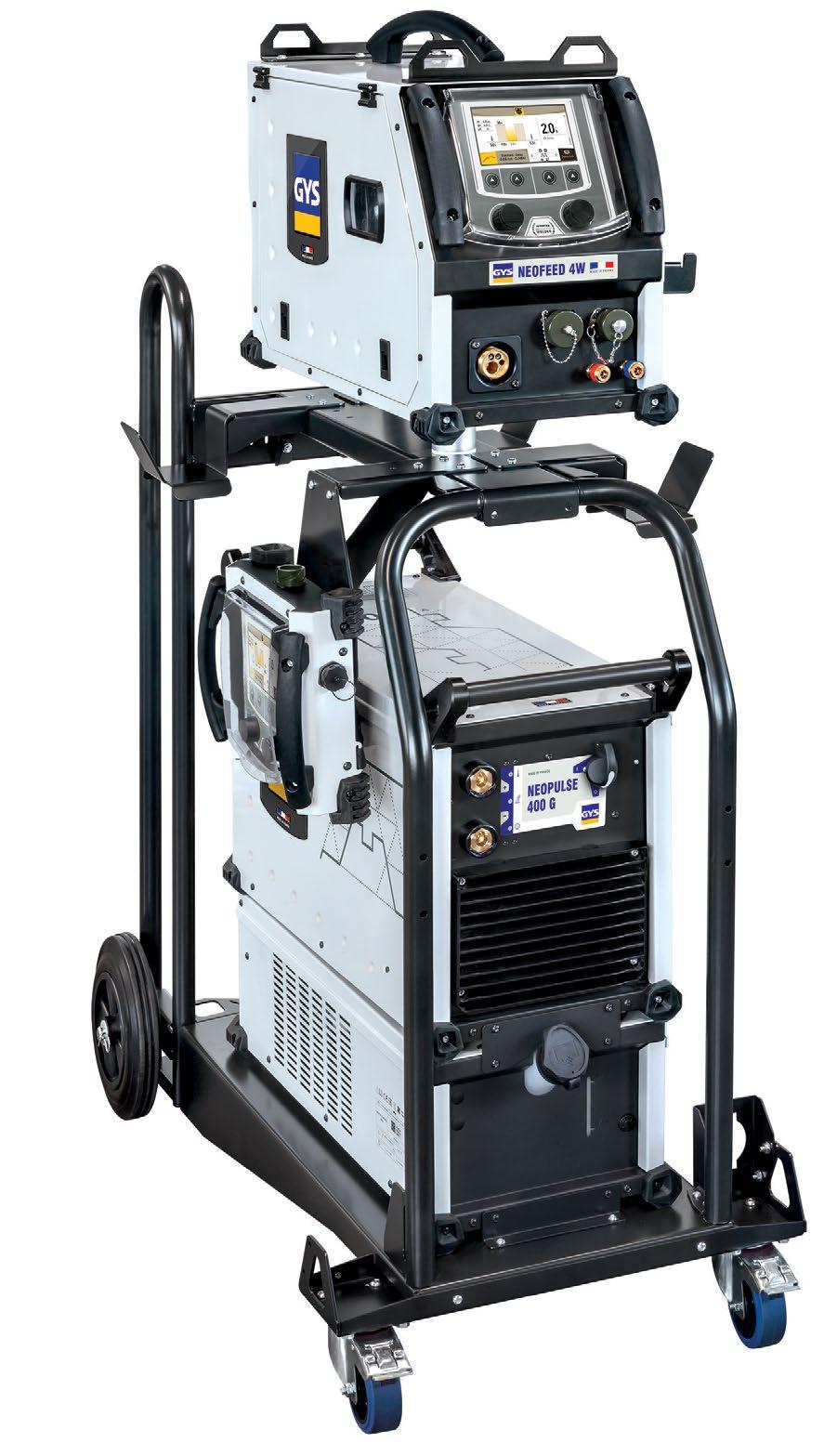
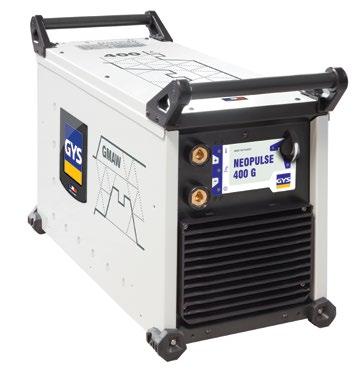
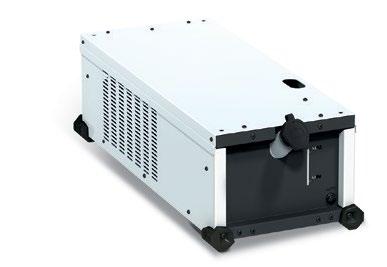
Digital technology, the NEOPULSE 400 G is a pulsed MIG/MAG welding power source with a separate wire feeder. Ultra high performance and designed for the highest performance level using the latest technology, it features +100 synergic curves and exceptional arc quality/performances. Intuitive and highly functional, its digital interface allows you to change welding parameters with ease. Equipped with its NEOFEED-4W reel (optional), this welding power source provides productivity and quality of unmatched welding on all types of alloys.
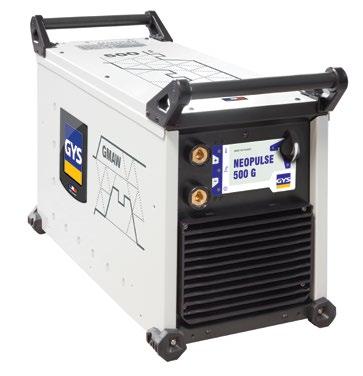
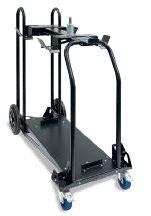
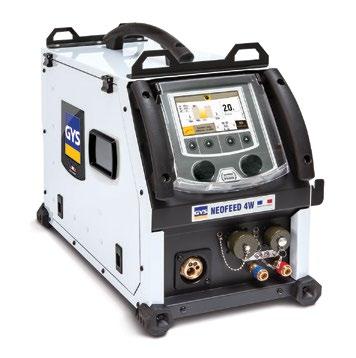
Interconnection Cables
Air
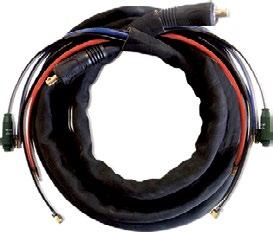
WA-047587 5m - 70mm2
WA-047594 10m - 70mm2
Water
WA-047617 5m - 70mm2
WA-047624 10m - 70mm2
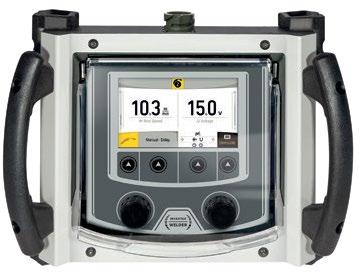
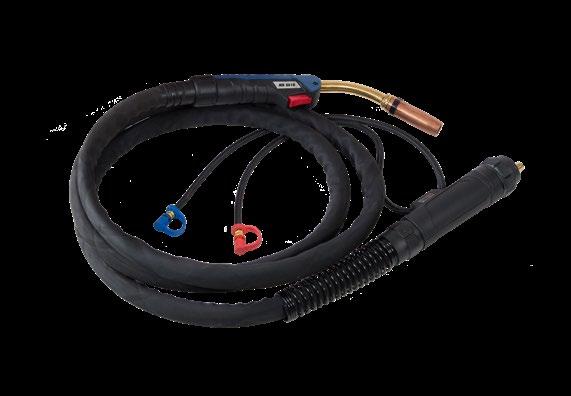
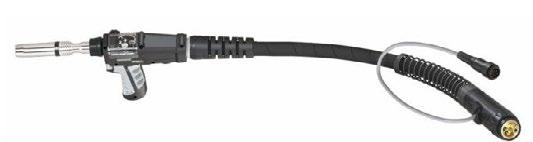
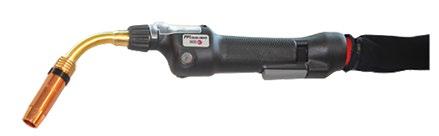
M-UGP3600 Push Pull Gun M-072992 Push Pull Gun
MULTI-PROCESS WELDING
MIG/MAG:
• Steel and stainless steel wire: Ø 0.6 to 1.6 mm
Aluminium wire: Ø 0.8 to 1.6 mm
• CuSi and CuAl wire: Ø 0.8 to 1.2 mm
MMA DC/Pulse: Basic, rutile and cellulosic electrodes (up to Ø 6 mm)
TIG DC Lift/Pulse.
SMART
SYNERGIC Mode: Select the material/gas type and wire diameter, now the NEOPULSE automatically determines the optimal welding conditions and allows you to adjust the settings (wire feed speed, voltage, current, arc length).
ACCURATE
Calibration of welding accessories, to adjust the displayed voltage measurement and the energy calculation.
Energy display and energy calculation after welding according to EN1011-1, ISO / TR 18491 and QW-409.
Portability: Load/save as, JOBS from a USB key as well as the machine configuration.
Traceability: Trace/record all welding steps, weld by weld, during industrial manufacturing according to EN ISO 3834.
OPTIMISED MIG/MAG SETTINGS
Welding processes: Manual, Dynamic STD, Pulsed, Modul Arc (variation of hot/cold current)
TACK modes: SPOT and DELAY.
Trigger management: 2T and 4T.
Precise control over the welding cycle: CreepSpeed, Softstart, Hotstart, Upslope, Downslope, Crater Filler, Postgas, etc.
MAXIMUM PRODUCTIVITY
Intended for heavy and demanding industrial applications:
• Four microprocessors increase the speed of communication and optimize the efficiency of the product.
• High productivity thanks to its high duty cycle (400A @ 60%). Connectable via a SAM control interface for use on robot/ automaton (optional).
• Higher resistance and robustness of the electronics. Powerful electronically controlled wire feed motor (100 W) with four active drive rolls.
High arc voltage for easier ignition and exceptional arc dynamic.
ADVANCED INTUITIVITY
• New user friendly interface focused on welders’ navigation habits.
• Complete update of the machine and synergies by USB key. Cooling unit (ref. 032750) and trolley (ref. 037328) optional.
• Storage of 500 welding programs (can be saved on USB stick). Displays current/voltage during and after welding (WPS/PQR).
• Choice of the main parameter to display on the screen (wire speed, average welding current, etc.).
Internal lighting of the motorized roll and wire reel.
• Viewing window on trapdoor to check the consumption of the filler wire.
• Intelligent ventilation management to reduce power consumption, dust extraction and substation noise.
DATA:
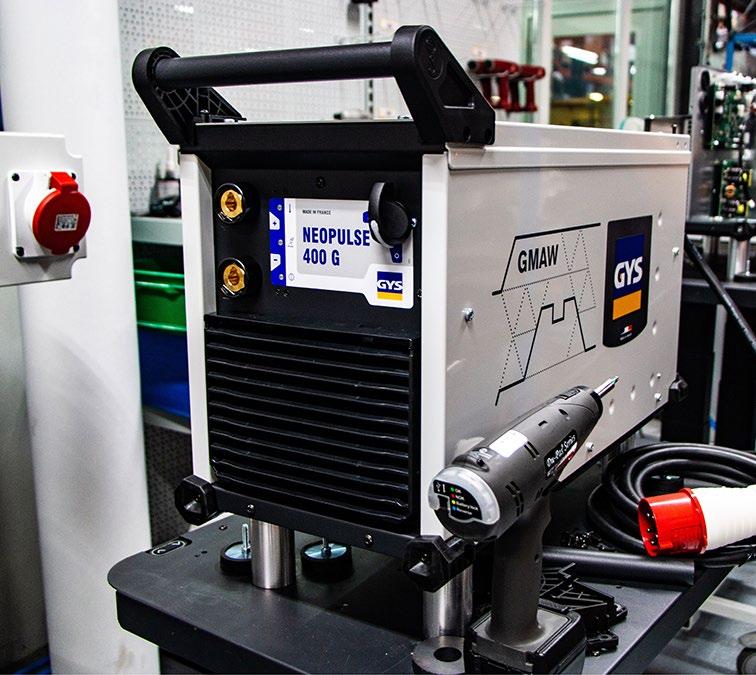
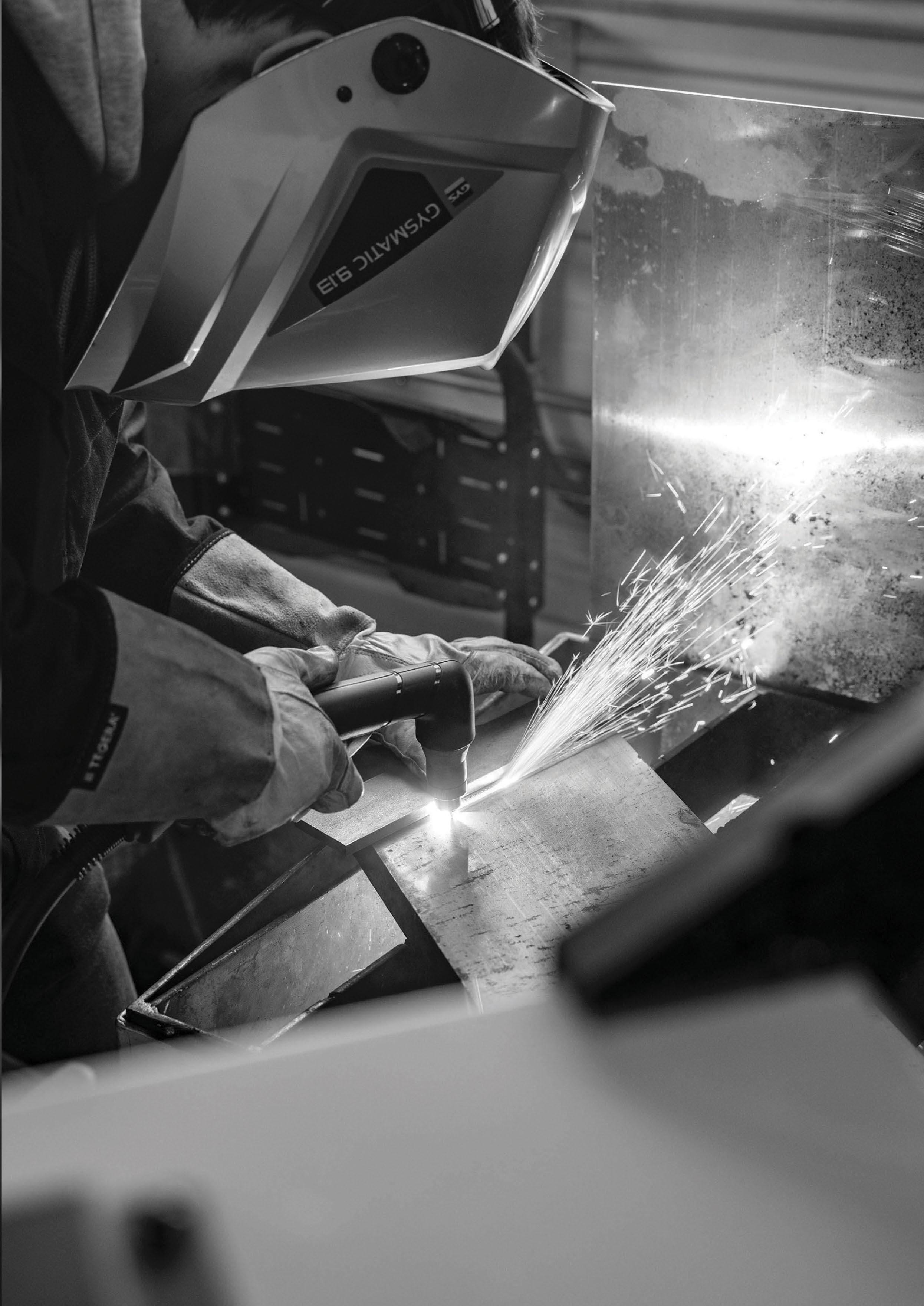
PLASMA CUTTERS
CUTTER 30 FV
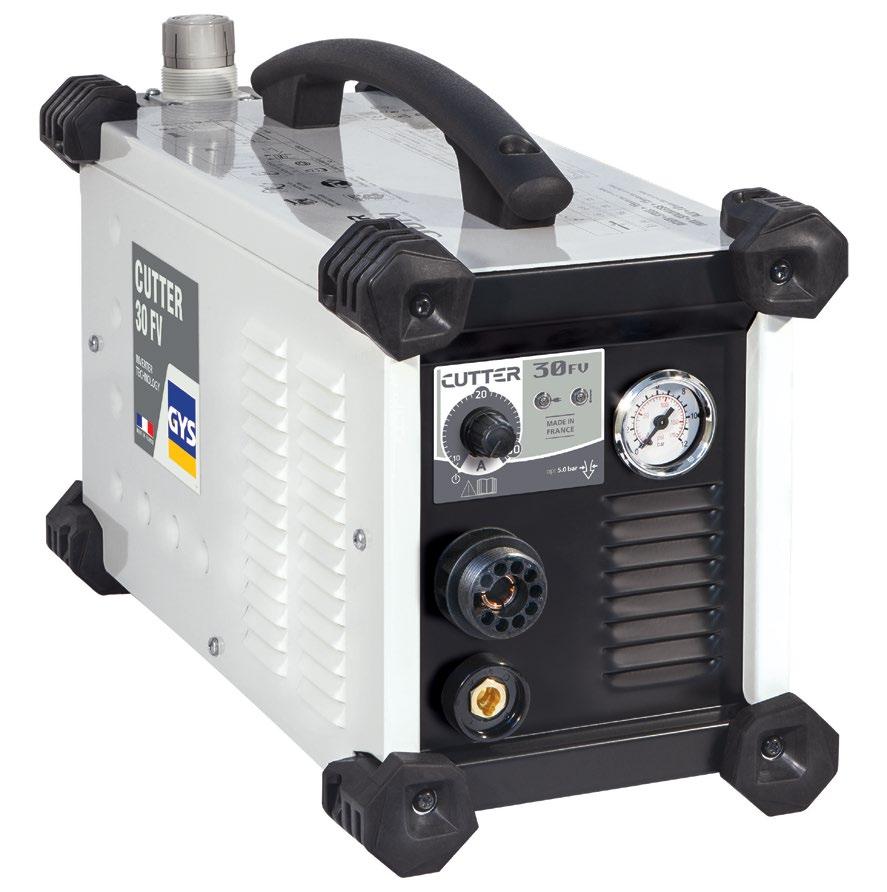
EFFECTIVE IN ANY ENVIRONMENT
Inverter technology to ensure quality cut on all types of steel (mild, stainless, tempered, HSS), aluminium, copper, etc. Consumables replacement is fast and easy for a maximum productivity.
• Intuitive display: Potentiometer to adjust the output current according to the thickness and material to cut. Manual adjustment of the air pressure (2.5 to 9 bars) with flow meter on the front panel.
• HF-free ignition to prevent disturbances that could damage nearby electrical equipment.
The CUTTER 30FV is a 30A plasma cutter with a cutting capacity of 10mm thick for steel (severance cut up to 15mm). The HFfree arcing system preserves and increases the consumables life span. Designed for maintenance jobs and car body repairs, it integrates robust mechanical parts along with an intuitive interface and flow meter on the front panel.
ACCESSORIES:
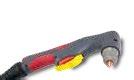
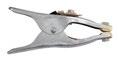
CUTTER 45 CT
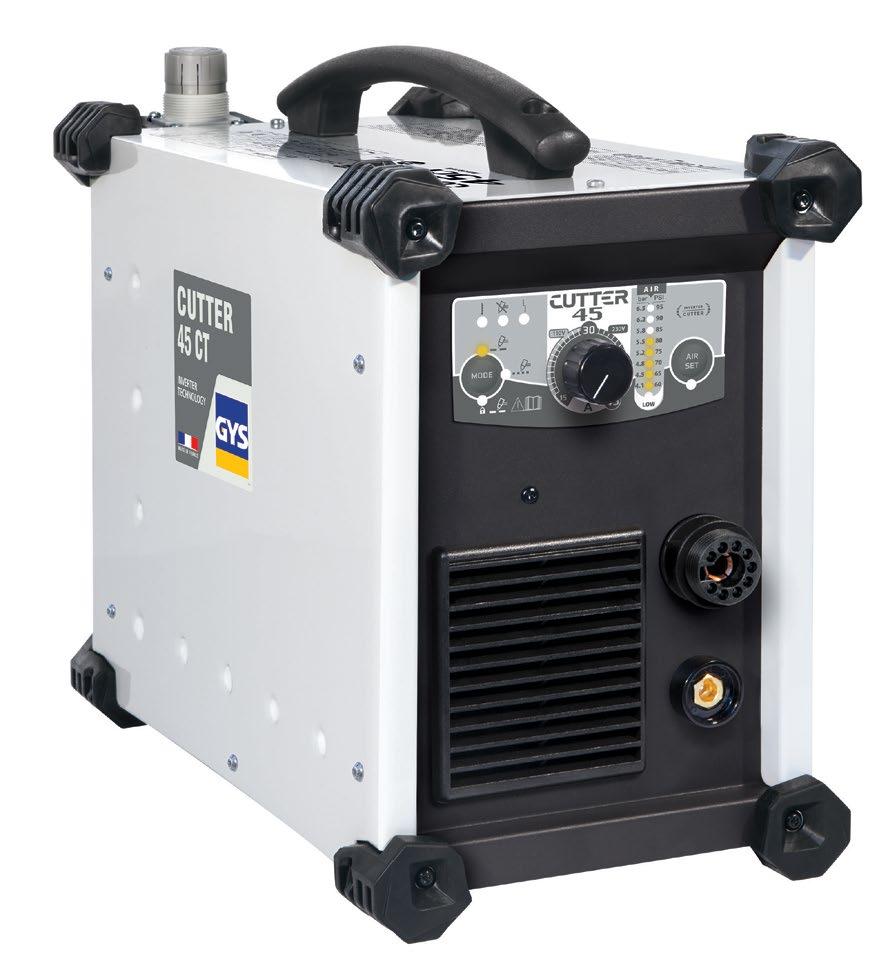
MAXIMUM PRODUCTIVITY
Faster cutting speed than using oxygas.
• Cuts all types of steel (mild, stainless, tempered, HLE), aluminium, copper, etc.
• Optimised cooling using the ventilation corridor that helps insulating the electronic components from the dust. Consumables setting up is easy for maximum productivity.
• Duty cycle 41 A at 60 % (40°C).
EFFECTIVE IN EVERY WORKPLACE
• User friendly interface with three working modes: Plain metal sheet / Open metal sheet / Locked. Manual setting of the air pressure using front screen chart.
• HF-free ignition to prevent disturbances that could damage nearby electronic equipment.
• Compatible with CNC kit for automatic cutting tables. Disconnectable earth cable for easy storage and simple replacement.
The CUTTER 45 CT is a 45 A plasma cutter with a clean cutting capacity of 20 mm thick on a wide range of materials thanks to the MT/AT 40 torch range. The HF-free arcing system preserves and increases the lifetime of consumables. Designed to be used in difficult environments, it has a very robust mechanics and a user friendly control panel. It is pre-wired for use on automatic cutting tables.
TECHNICAL DATA:
PERFORMANCES:
ACCESSORIES:
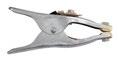
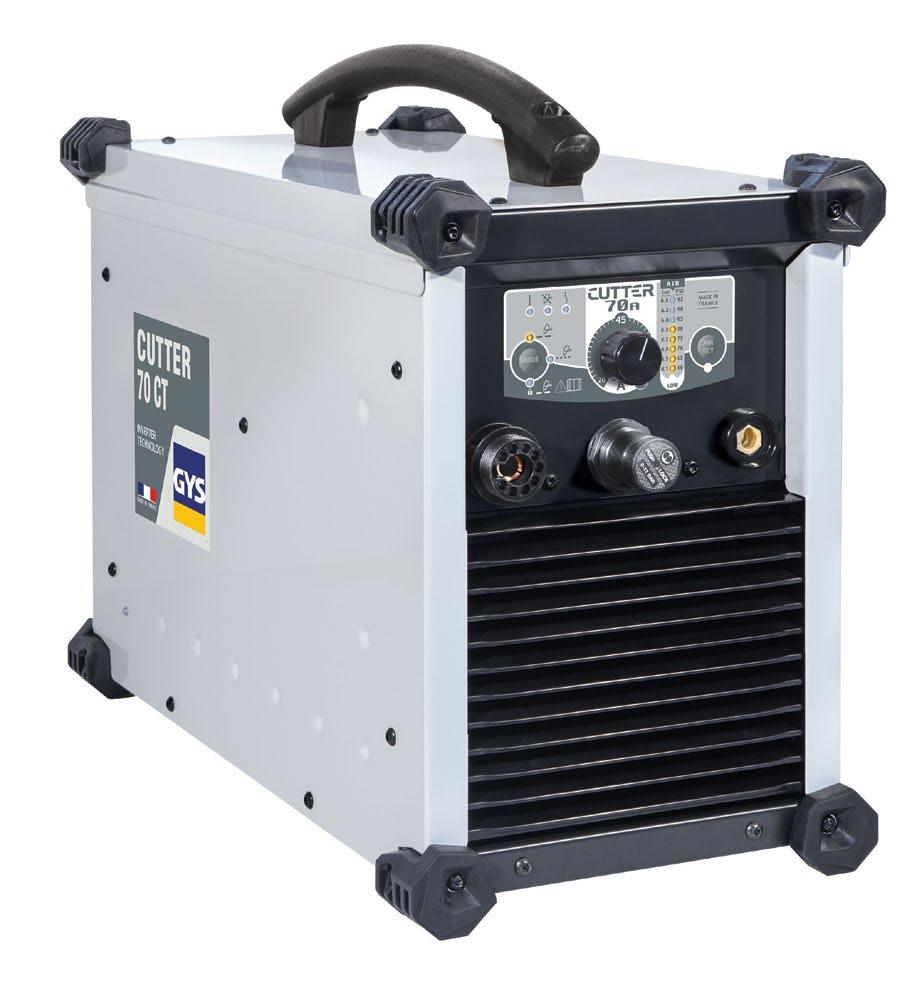
MAXIMUM PRODUCTIVITY
Faster cutting speed using oxygas.
• Cuts all types of steel (mild, stainless, tempered, HLE), aluminium, copper, etc.
• Optimised cooling using the ventilation corridor that helps isolate the electronic components from the dust. Replacement of consumables is fast & easy for maximum productivity.
Duty cycle 70 A at 60 % (40°C).
EFFECTIVE IN EVERY WORKPLACE
User friendly interface with three working modes: Cutting, Mesh & Locked. Manual setting of the air pressure (4.1 < 6.5 bars) using front LED indicator.
HF-free ignition to prevent disturbances that could interfere with nearby electronic equipment.
Compatible with CNC kit for automatic cutting tables.
The CUTTER 70 CT is a 70 A plasma cutter with a cutting capacity of 35 mm thick on a multitude of materials. The HFfree arcing system preserves and increases the lifetime of consumables. Designed to be used in difficult environments, it has very robust mechanics and a user friendly control panel. It is pre-wired for use on automatic cutting tables.
TECHNICAL DATA:
PERFORMANCES:
ACCESSORIES:
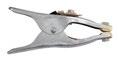
WM-063044 125 WM-067431
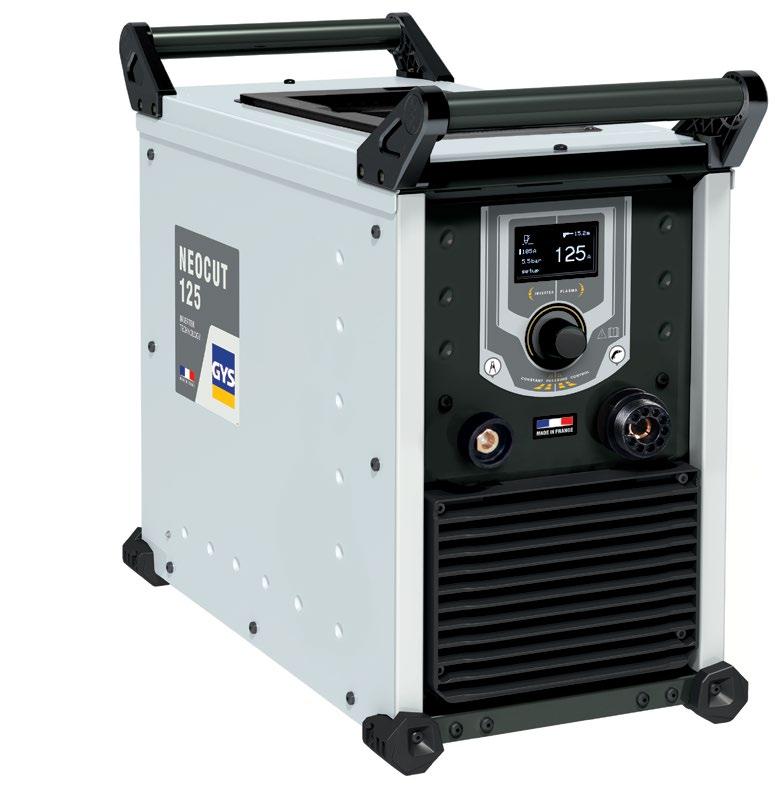
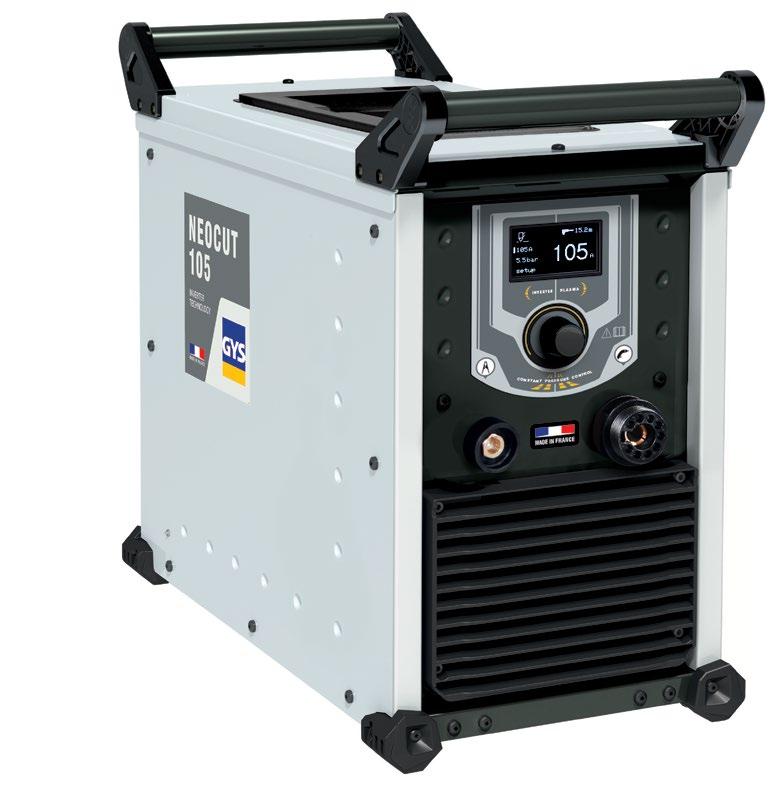
SYNERGISTIC AIR PRESSURE
Automatic management of pressure and air flow rate whatever the torch length and the operating mode (cutting, gouging and marking).
• Optimised consumable lifespan.
MAXIMUM PRODUCTIVITY
Duty cycle 100% A at 105 A (40°C) and 100% at 125 A (40°C).
• Marking mode, ideal for tracing and identifying parts. Cuts all material types (mild, stainless, tempered, HLE), aluminium, copper, etc.
Optimized cooling design to operate in an industrial environment.
• Connectable via an optional CNC kit for use on an automated cutting table.
Reinforced structure IP 23.
SIMPLE TO USE
Ergonomic interface with OLED screen (7 languages).
• Six working modes: Cutting, Cutting with locked trigger, Gouging, Gouging with locked trigger, Cutting of perforated sheets, Marking. Counter to follow the wear of the consumables (nozzle and electrode).
Pneumatic diagnosis (moisture presence test and air pressure control).
• HF-free arc ignition to prevent disturbances that could damage nearby electronic equipment.
• Simplified software update via USB cable without any tools or disassembly.
HIGH-PERFORMANCE TORCH
• Premium torches available in two lengths (6 m/12 m), 2 types (manual/automatic) and two powers for automated cutting (125 A /160 A).
Large choice of consumables adapted to all metal thicknesses.
• Designed to be shock and heat resistant.
• Quick connection/disconnection of the torch, without tools required for transport or maintenance.
• Easy to use trigger mechanism for more comfort.
The NEOCUT 105 & 125 is a plasma cutter with a duty cycle of 100% at 105 A for cutting work up to 50 mm thick and duty cycle of 100% at 125 A for cutting work up to 57 mm thick in industrial environments. It is equipped with automatic air pressure management, in all modes, offering optimum cutting quality throughout the lifespan of the consumables. Can also be connected to a cutting table, its «Marking» mode is perfect for tracing and identifying parts.
ACCESSORIES:
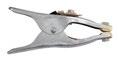
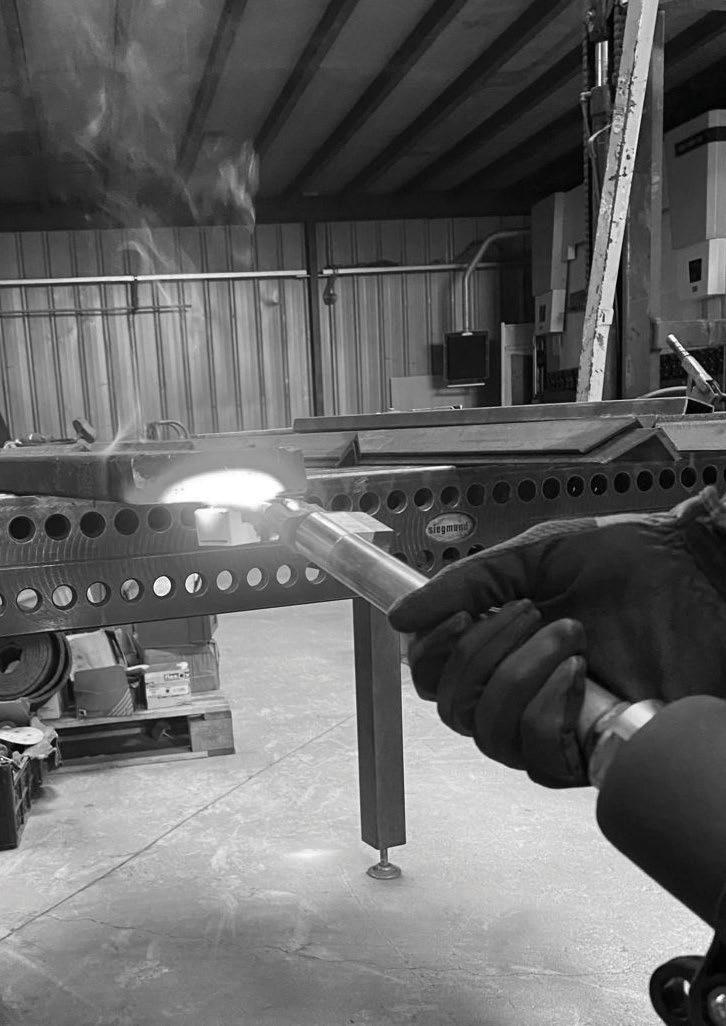
INDUCTION
POWERDUCTION 10R
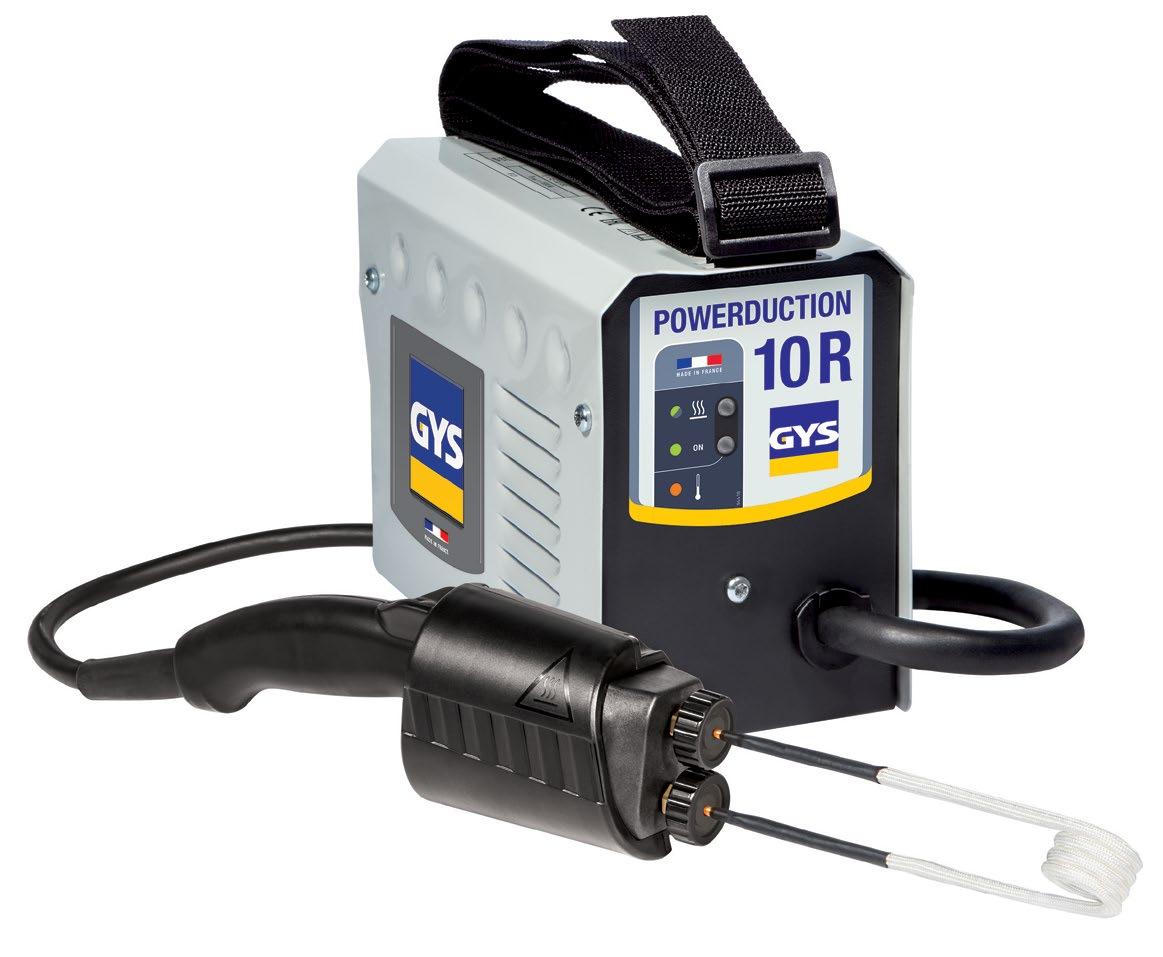
The Powerduction 10R is designed to heat, unlock to enable removal of mechanical parts such as worn nuts and bolts in seconds. It is especially recommended in the automotive, agricultural, maintenance and metal construction.
AN ERGONOMIC MULTI-APPLICATION TOOL
Instant heat without flame applied to a specific area, it can be used close to cables, pipes, or other heat sensitive objects avoiding the need to disassemble/remove them.
• Light weight, just 3.5 kg - 1.3 kg for the inductor alone.
• Ergonomic shoulder strap provided. Easy to use: uses a standard 230V single phase supply.
• Quick start: select and install the inductor, connect and go. 1200W output power with high duty cycle.
Heating Speed
A WIDE RANGE OF INDUCTORS
• The range of five inductors allows to vary the heating applications for all types of shapes and access constraints.
• Changing the inductor is very easy by virtue of the simple wheel clamping system.
TECHNICAL DATA:
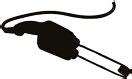

CONSUMABLES INCLUDED
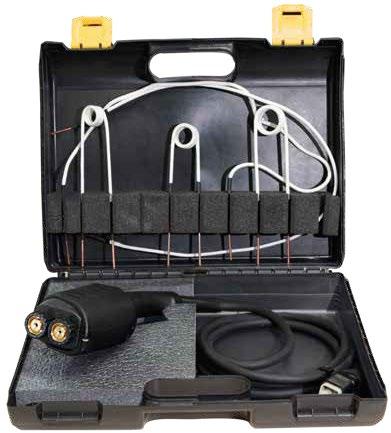
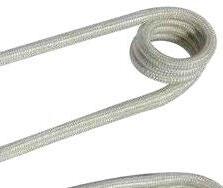
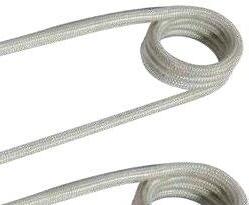
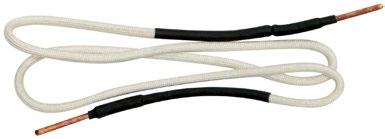
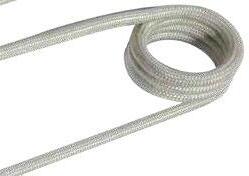
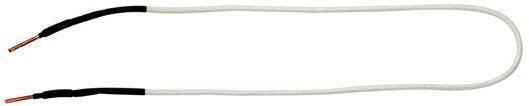
POWERDUCTION 37LG
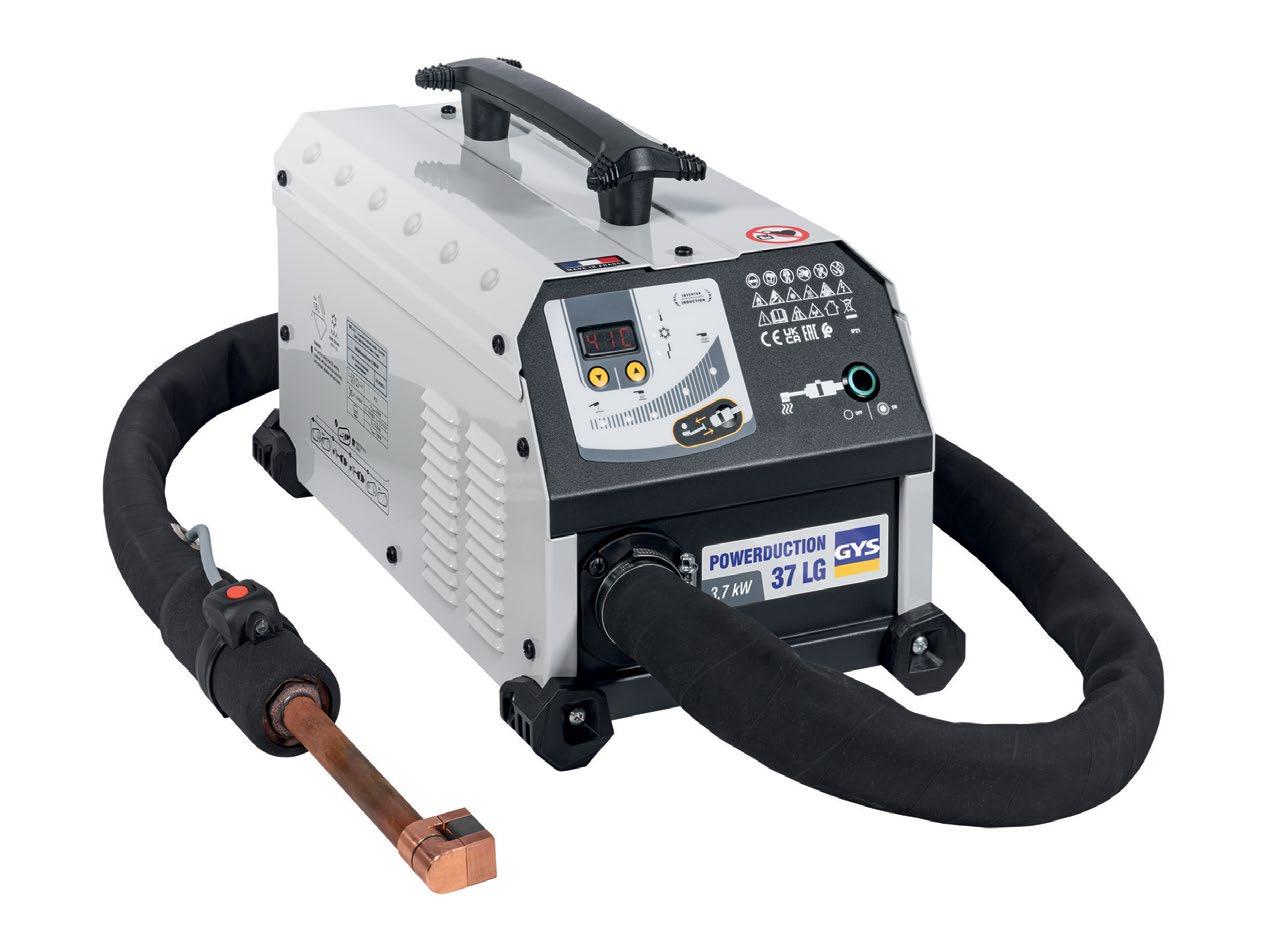
The POWERDUCTION 37LG provides instant and powerful heating to release, or simply heat, steel or aluminium.
Light and portable, this device can also heat metallic parts continously for several minutes without interruption thanks to its water-cooling system.

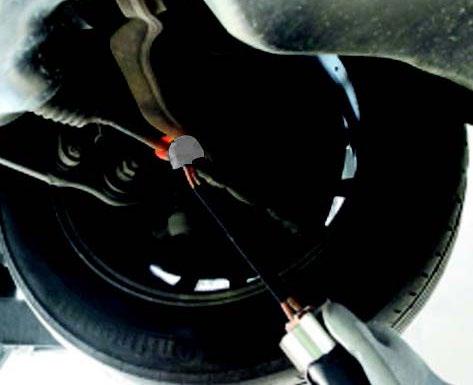
THE IDEAL TOOL FOR MECHANICAL AND MAINTENANCE WORK
• Essential for releasing the steering linkage (wheel alignment) Removes glow plugs, seized-up wipers and spare wheel compartments
• Releases seized up bolts Releases steering ball joints without damaging the bellows
• Releases shaft drives seized up in the hub Removes automotive or HGV exhaust lines
• Removes glued-on, steel or aluminium parts
FEATURES
High Heating Performance: 3,700 W of power that can be easily adjusted in 250 W increments. Directly heats up the heart of the metallic part at a depth of 6 mm. This device is capable of heating steel until it is red hot (around 1,000°C).
Secure and Time Saving: Immediate, flameless heating in a specific area, allows work to be carried out close to cables, pipes or any other heat-sensitive part without having to be dismantled.
Portable Machine: Used to reach difficult-to-reach areas. Supplied with a two meter inductor cable.
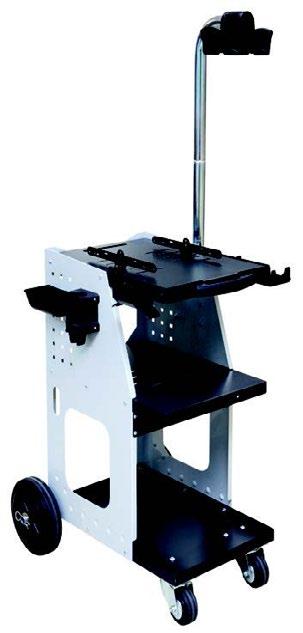
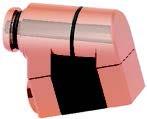
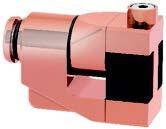
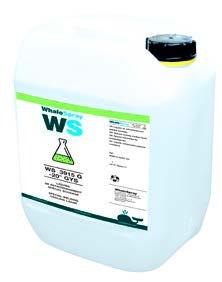
POWERDUCTION 110LG
WM-058590
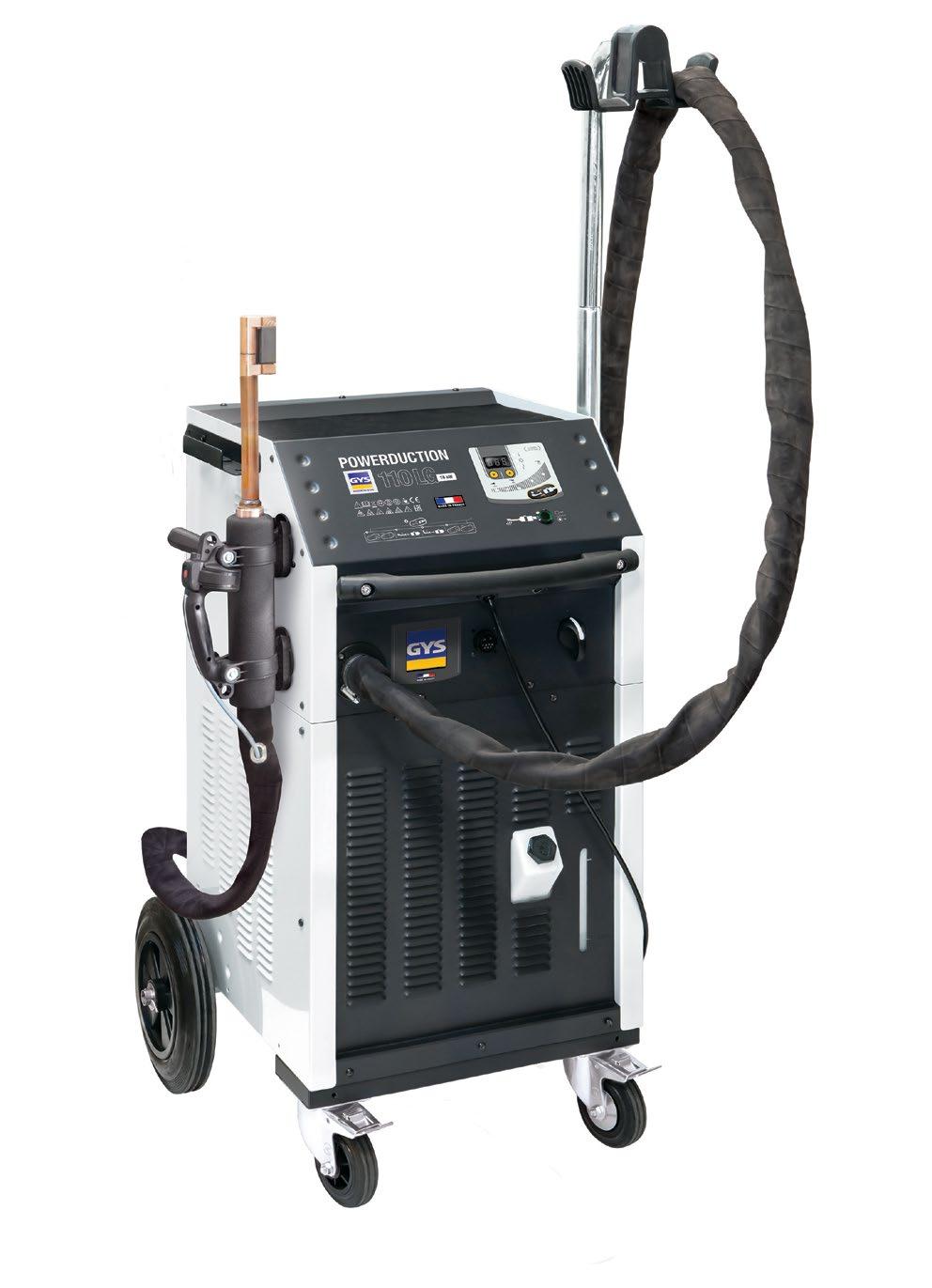
A WIDE RANGE OF APPLICATIONS
• Straightening out bent chassis (not HLE steel) Releasing bolts and steering ball joints without damaging the rubber pads
Removing seized hub bearings
• Removing the exhaust system
• Annealing metal parts
Heating for bending
• Brazing
GUARANTEED TO SAVE POWER & TIME SAVING
Heating Power: 11 kW of power that can be selected in increments of 1,000 W. Directly heats the centre of the metal down to a depth of 6 mm. Heats until red hot (800°C).
The POWERDUCTION 110LG supplies an instant heating power to unseizing metal parts as well as heating up steel or aluminium. Featuring flame-less technology, its heating is accurate, instantaneous and safe for the working environment. Thanks to its liquid-cooling system, this machine can work continuously at its maximum power (11 kW). Designed for use on a three-phase, 16 A socket, it is particularly effective for HGV mechanical work, public works vehicles and agricultural machinery.
ADAPTATION TO ALL SECTORS
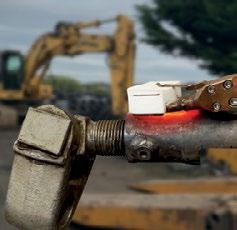
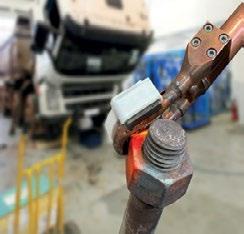
Mechanical work, car maintenance, HGVs and the construction industry.
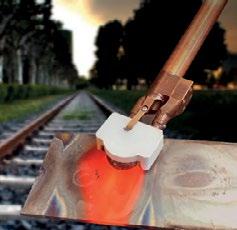
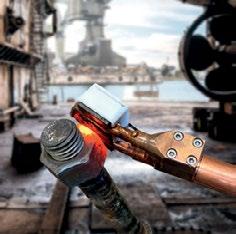
Industrial, maritime, railway and maintenance applications
Safe and Time Saving: Immediate, flameless heating on a specific area; it can be used to close cables, pipes or other heat-sensitive parts whilst avoiding the need to disassemble them.
User Comfort: Equipped with a four metre induction cable, which allows the operator to work at height or in places where the machine cannot fit.
TOTAL HEAT CONTROL
The POWERDUCTION 110LG has an integrated, heating time management system and can be used to operate a temperature control unit (optional extra: POWERDUCTION Heat Controller, P.N. 061644). It is fitted with indispensable technologies that are essential for precisely controlling the heating process in order to obtain a result that meets all requirements.
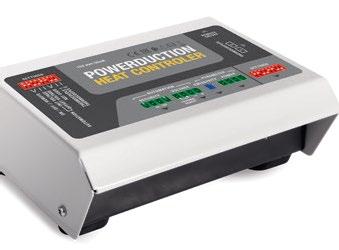
TECHNICAL DATA:
Power Supply (V)
Rated Input Current | 1 eff’ (A)
Weight (kg)
INDUCTION HEATING HEADS
Spiral Ø 18 mm 054806
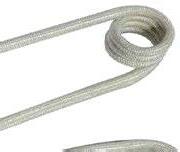
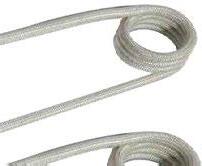
054813

054868 Spiral Ø 24 mm 054790
400V 3~
16
80
Spiral Ø 30 mm 055469
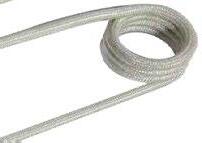
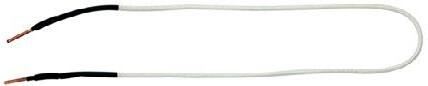
POWERDUCTION 220LG
WM-066861 WM-074576
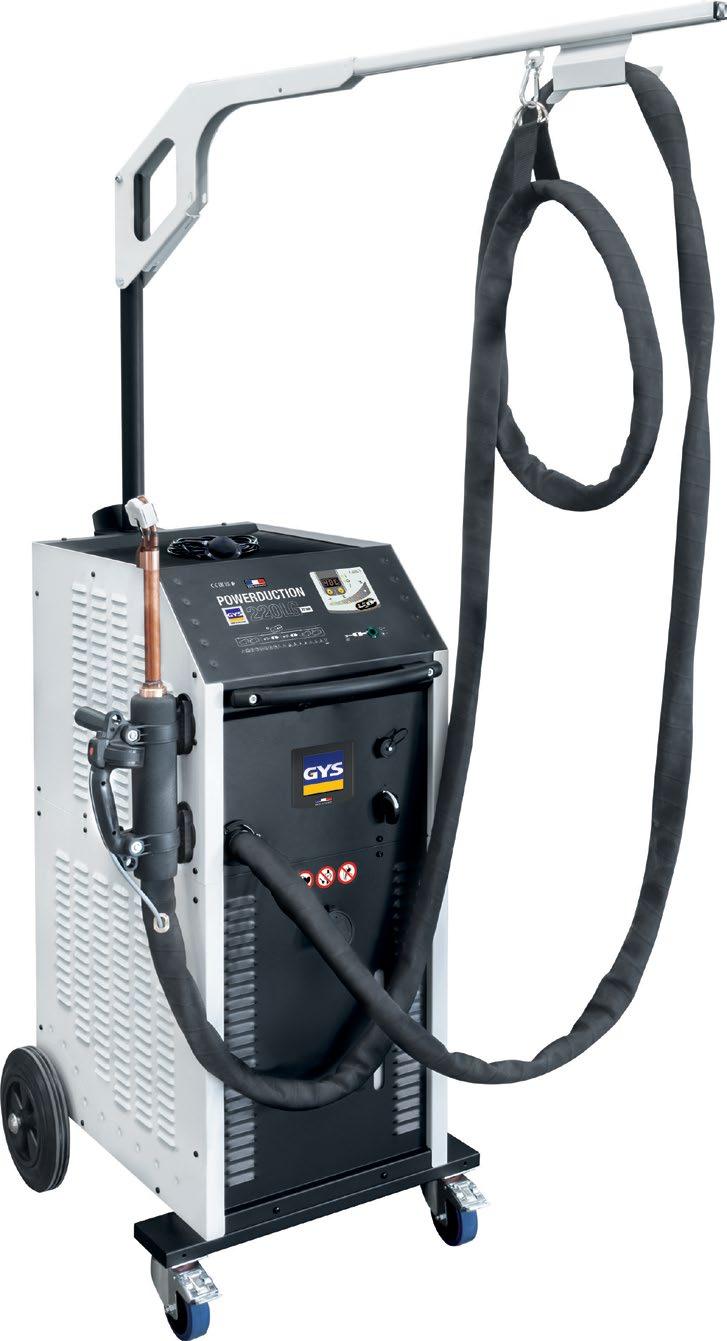
A WIDE RANGE OF APPLICATIONS
• Heating and straightening of bent frames (except HLE steel)
Releasing of bolts, steering ball joints without damaging the bellows
Removing seized cardans in the hub
• Removal of exhaust lines
• Annealing of metal parts
Heating for bending
• Brazing Shrinkage
GUARANTEED TO SAVE POWER & TIME SAVING
Heating Power: 22 kW, selectable in 2200 W steps. Heats up the core of the metal and turns red (approx. 800°C).
POWERDUCTION 220LG supplies an instant heating power to unseize, and to heat up steel or aluminium. Flameless, its heating is accurate, instantaneous and safe for the working environment. Thanks to its liquid cooling, it can work continuously at its maximum power of 22kW. Designed for intensive use on 32 A sockets, its productivity and heating quality make it an indispensable ally in industrial environments.
ADAPTATION TO ALL SECTORS
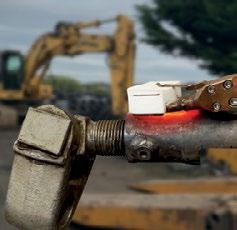
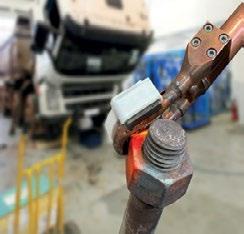
Mechanics and maintenance agricultural, heavy goods vehicles & construction.
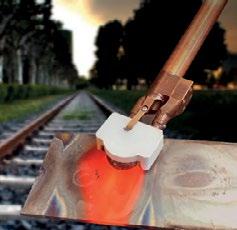
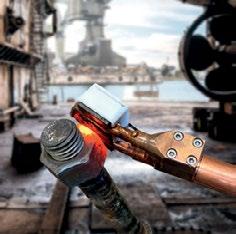
Sectors: Industry, maritime, railways, maintenance.
TOTAL CONTROL OF THE HEATING
The POWERDUCTION 220LG has an integrated heating time management and can control an intelligent temperature control unit (Option: Powerduction Heat Controller - ref. 061644). Technologies that are indispensable for the precise control of the heating in order to obtain a result that meets all requirements.
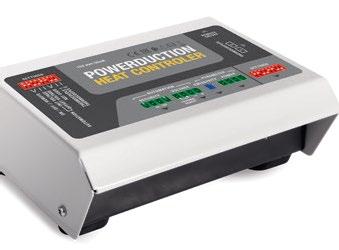
TECHNICAL DATA:
Power Supply (V)
400V 3~
Rated Input Current | 1 eff’ (A) ≥32
Weight (kg) 141
INDUCTION HEATING HEADS
Spiral Ø 18 mm 054806
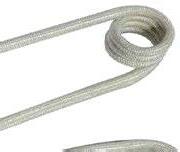
Safety and Time Saving: Immediate heating without flame on a specific area, it can be used close to cables, pipes, or other heat sensitive part avoiding the need to disassemble them.
Easy to Use: 6 metre induction cable which allows to work at height or in any places the powerduction cannot fit.
Spiral Ø 24 mm 054790
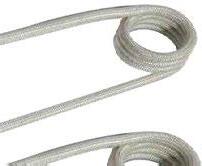
Spiral Ø 30 mm 055469
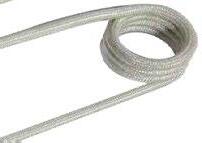
Flexible braided wire 80 cm 054813 Straight rigid wire 80 cm 054868

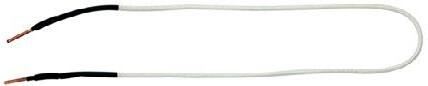
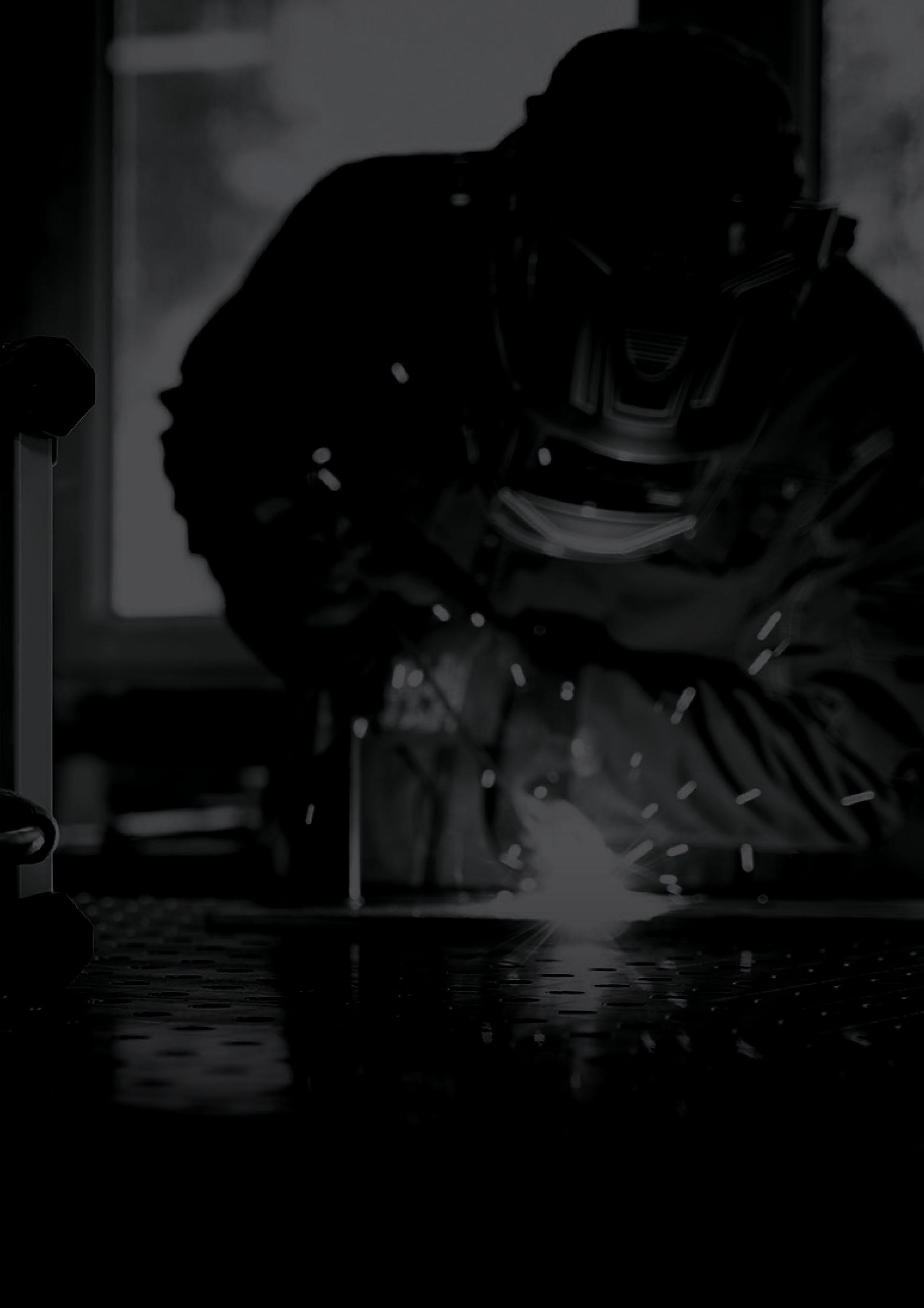
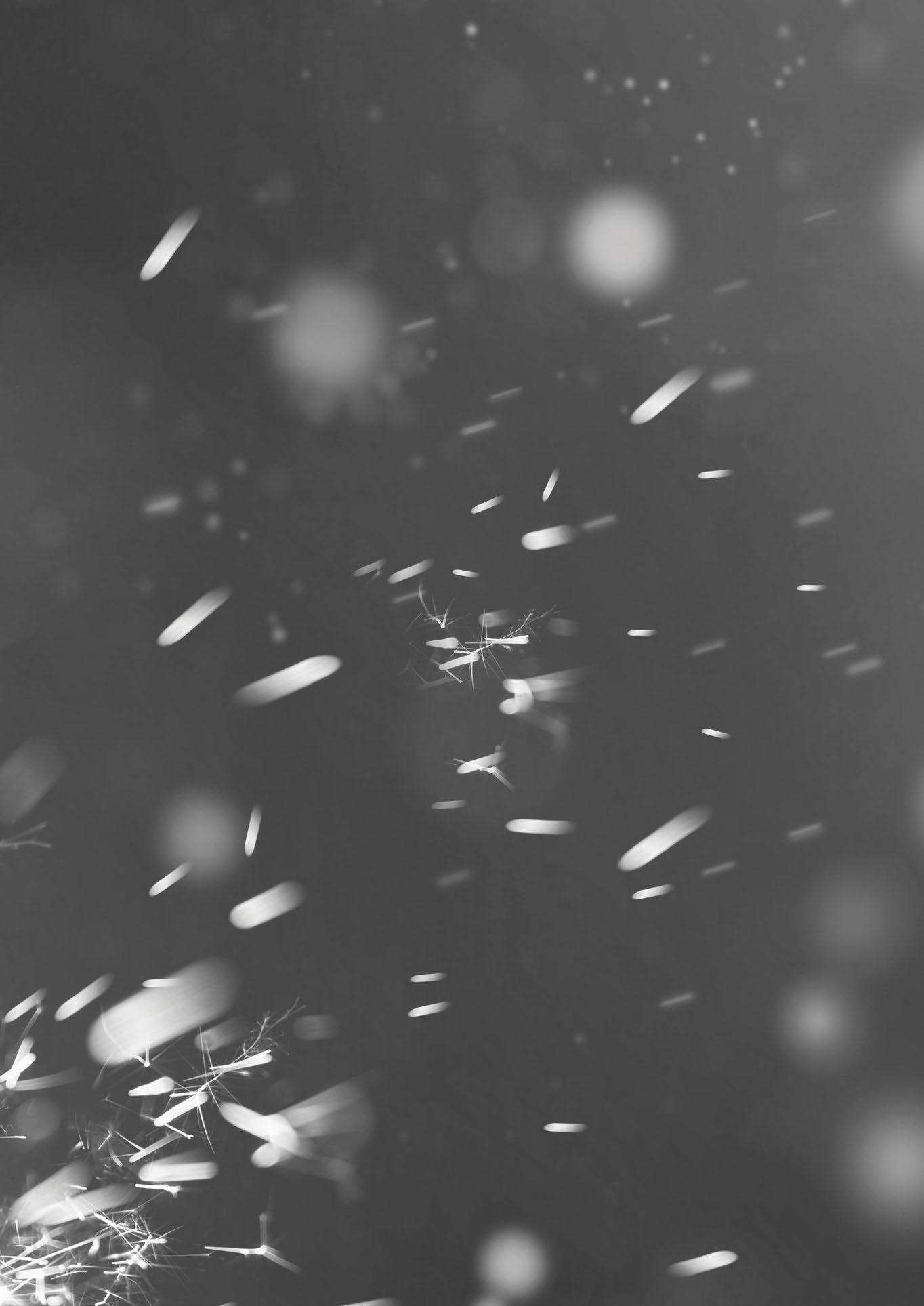