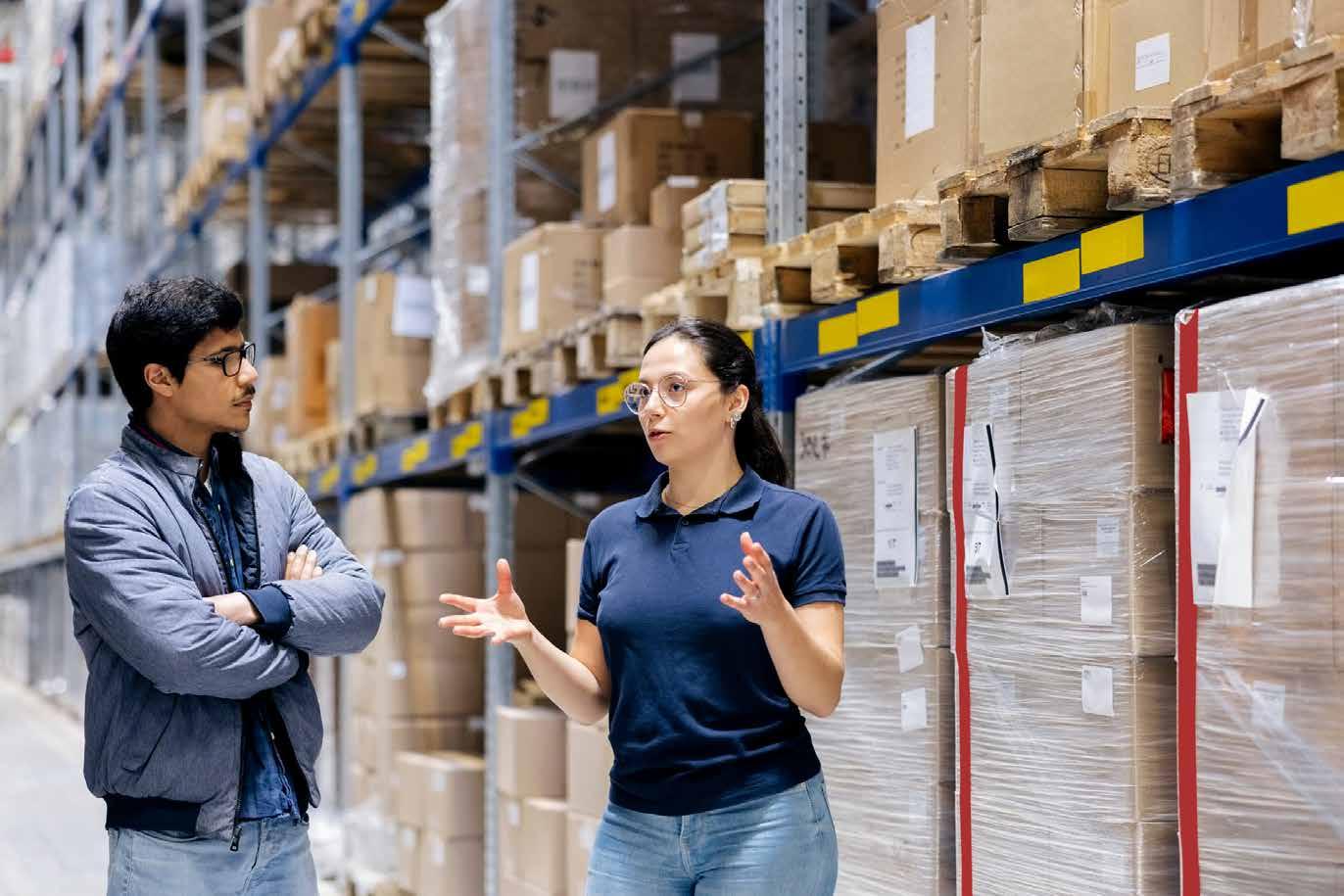
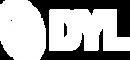
Looking Ahead: 2025 Construction Ebook
Looking Ahead: 2025 Construction Ebook
endeavors to serve as an indispensable resource in negotiating the complexities of this volatile environment as we look toward 2025.
Material costs represent a critical component of overall construction expenses, as they significantly influence project budgets and bidding strategies. These costs encompass a wide range of elements, including raw materials like wood, steel, and concrete, as well as associated processing, transportation, and storage.
As major determinants of a project's financial feasibility, understanding these costs is crucial for industry professionals who must maintain competitiveness in a cost-sensitive market.
Project managers, estimators, and procurement specialists consistently analyze these expenses to ensure that projects remain within budget and on schedule, prioritizing efficient resource allocation and purchasing.
Lumber has long been an essential commodity in the construction industry, but the past few years have witnessed unprecedented fluctuations in its pricing. In 2019, lumber prices were relatively stable, averaging around $350 per thousand board feet.
However, as the COVID-19 pandemic took hold, supply chain disruptions and heightened demand for home renovations and new builds led to a sharp increase in prices.
By May 2021, the price soared to nearly $1,500, marking a dramatic escalation that placed significant financial strain on construction companies. While these prices have since moderated, projections for 2024 suggest a potential settling at approximately $600 per thousand board feet as supply chains stabilize and demand evens out.
The volatility in lumber prices has had profound implications for construction companies, impacting their project timelines, budgeting, and overall financial health. The spike in 2021 forced many companies to alter their procurement strategies, delay projects, or even halt new undertakings due to prohibitive material costs. According to industry reports, these disruptions contributed to an estimated 10% increase in overall project costs and delayed completion times by approximately 15%, as firms struggled to adapt to the rapidly evolving market conditions.
In today's volatile market, adaptive procurement strategies have become essential for construction companies seeking to manage rising costs and ensure timely completion of projects.
One effective approach includes the implementation of flexible contracting models that allow for price adjustments based on market conditions.
According to a recent survey by Deloitte, 62% of construction firms reported adopting flexible contracts to better handle price fluctuations, achieving cost savings of up to 10% compared to fixed-rate contracts.
Another strategy involves establishing strategic partnerships with suppliers, which not only secures favorable terms but also enhances supply chain predictability.