
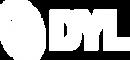
Looking Ahead: 2025 Construction Ebook
Looking Ahead: 2025 Construction Ebook
In recent years, the construction industry has faced a tumultuous landscape marked by fluctuating material costs and persistent supply chain challenges. Understanding these dynamics is crucial for industry professionals aiming to thrive in an ever-evolving sector. With the prices of essential materials like lumber, steel, and concrete undergoing significant changes, construction companies must adapt to maintain project viability and competitiveness.
This ebook aims to illuminate the intricacies of material costs and supply chain management, equipping readers with insights into navigating these challenges effectively. By addressing the underlying factors contributing to current market conditions, we aspire to empower construction professionals to make informed strategic decisions.
Through comprehensive analysis and practical guidance, this ebook
endeavors to serve as an indispensable resource in negotiating the complexities of this volatile environment as we look toward 2025.
Material costs represent a critical component of overall construction expenses, as they significantly influence project budgets and bidding strategies. These costs encompass a wide range of elements, including raw materials like wood, steel, and concrete, as well as associated processing, transportation, and storage.
As major determinants of a project's financial feasibility, understanding these costs is crucial for industry professionals who must maintain competitiveness in a cost-sensitive market.
Project managers, estimators, and procurement specialists consistently analyze these expenses to ensure that projects remain within budget and on schedule, prioritizing efficient resource allocation and purchasing.
WHAT PERCENT OF CONSTRUCTION COMPANIES FACED MATERIAL SHORTAGES IN THE PAST YEAR? 73%
WHAT PERCENT OF FIRMS REPORTED MATERIAL COST INCREASES OF 20% OR MORE IN THE PAST 2 YEARS? 57%
HOW MUCH HAS SUPPLY CHAIN ISSUE INCREASED CONSTRUCTION COSTS IN THE LAST FEW YEARS? 15%
Historically, the construction industry has experienced both periodic stability and notable volatility in material costs. Over the past decade, there have been several episodes of rapid price escalation, primarily driven by shifts in supply and demand dynamics, global trade policies, and environmental regulation changes.
For instance, between 2008 and 2011, commodity prices underwent significant fluctuations due to economic recovery efforts following the global financial crisis.
More recently, in 2021, lumber prices surged due to heightened demand for homebuilding amidst pandemic-induced supply chain disruptions. This continual evolution of costs underlines the importance of adapting procurement strategies to mitigate price risks.
The pricing of key construction materials has been substantially impacted by global events, with the COVID-19 pandemic serving as a prominent example.
The pandemic prompted a cascade of disruptions, affecting everything from international shipping to local manufacturing operations. As construction activities resumed, demand outpaced available supply, exacerbating price increases across numerous materials.
Trade tensions, such as U.S.-China tariffs, have similarly influenced material availability and cost, necessitating revisions in sourcing frameworks. Companies unprepared for these disruptions face risks of project delays and budget overruns, highlighting the necessity for contingency planning.
Real-world examples further illustrate these trends. The sharp rise and subsequent drop in U.S. lumber prices from 2020 to 2021 exemplifies the volatility of material costs. In March 2020, lumber prices were about $400 per thousand board feet, but the market saw unprecedented peaks of over $1,500 by May 2021.
Although prices have since moderated, they remain elevated compared to historical norms, emphasizing the lasting impact of supply chain volatility. Similarly, steel prices escalated dramatically, reaching over $1,800 per ton in mid-2021 due to supply chain constraints and high demand, before stabilizing lower yet above pre-pandemic levels. These patterns showcase the volatile nature of material costs, underscoring the need for strategic management and agile adaptation in construction procurement practices.
Do you want to use technology built for construction companies?
If you sign up with DYL, you can:
Automate all outgoing emails, calls, texts, and faxes to staff and labor personnel.
Get reports on outgoing calls, texts, and more.
Increase construction client acquisition by more than 35%.
Work from anywhere in the world, while your business is completely automated.
Understanding the specific dynamics of individual construction materials is paramount to effectively managing material costs and procurement strategies. Each material comes with its unique set of market influences, from availability and price volatility to regulatory impacts and global trade interactions.
Analyzing these factors enables construction professionals to anticipate potential challenges and align their strategies to mitigate risks. By adopting a proactive approach to material analysis, companies can enhance their resilience against fluctuations and make informed decisions in line with their project goals and financial constraints.
Lumber, a fundamental resource for many construction projects, provides an insightful case study into the broader trends impacting material costs. Its price volatility over recent years illustrates the interplay of supply chain disruptions, demand surges, and economic conditions
Lumber has long been an essential commodity in the construction industry, but the past few years have witnessed unprecedented fluctuations in its pricing. In 2019, lumber prices were relatively stable, averaging around $350 per thousand board feet.
However, as the COVID-19 pandemic took hold, supply chain disruptions and heightened demand for home renovations and new builds led to a sharp increase in prices.
By May 2021, the price soared to nearly $1,500, marking a dramatic escalation that placed significant financial strain on construction companies. While these prices have since moderated, projections for 2024 suggest a potential settling at approximately $600 per thousand board feet as supply chains stabilize and demand evens out.
The volatility in lumber prices has had profound implications for construction companies, impacting their project timelines, budgeting, and overall financial health. The spike in 2021 forced many companies to alter their procurement strategies, delay projects, or even halt new undertakings due to prohibitive material costs. According to industry reports, these disruptions contributed to an estimated 10% increase in overall project costs and delayed completion times by approximately 15%, as firms struggled to adapt to the rapidly evolving market conditions.
Companies with robust contingency plans and diversified supply chains were better positioned to mitigate these impacts, underscoring the critical importance of strategic planning and flexibility in navigating the complexities of the modern construction landscape.
Steel, another cornerstone of the construction industry, has experienced considerable price volatility due to a complex mix of global trade policies, pandemic-related disruptions, and fluctuating demand.
In 2019, the average price of steel was around $600 per ton, reflecting a relatively stable market environment. However, as the COVID-19 pandemic unfurled, a combination of supply chain constraints and increased construction activities drove prices to unprecedented heights.
By mid-2021, steel prices peaked at over $1,800 per ton, exacerbated by tariffs that had already strained global supply chains. Looking ahead to 2024, industry forecasts suggest a potential stabilization, with prices expected to moderate toward $1,000 per ton as production recovers and market conditions normalize.
The volatility of steel prices has had significant consequences for construction companies, influencing their project planning, budgeting, and completion timelines. The steep increase in costs during 2021 led to a surge in project expenditures, with some reports indicating that total construction costs rose by as much as 15%.
Consequently, many firms faced budget overruns and were forced to either delay or redesign projects to accommodate higher material costs.
Additionally, the unpredictability of steel prices has strained financial resources and reduced profit margins, highlighting the importance of strategic procurement practices and the need for companies to hedge against market fluctuations to sustain operations and maintain competitiveness in a volatile industry.
Concrete, a fundamental material in construction, has experienced a relatively stable pricing trajectory compared to other building materials like lumber and steel. In 2019, the cost of concrete hovered around $95 per cubic yard,
exhibiting moderate year-on-year increases predominantly driven by rising raw material and transportation costs. By 2021, this price had risen to approximately $110 per cubic yard, reflecting ongoing supply chain challenges and increased production expenses.
Looking toward 2024, industry projections suggest further price appreciation, estimating costs around $120 per cubic yard as demand remains robust and input costs continue to rise.
The incremental rise in concrete prices, while less volatile than other materials, still poses significant challenges for construction companies. Despite the relative stability, the cumulative effect of increasing costs over time contributes to higher project expenditures, necessitating more meticulous budgeting and cost management strategies.
In 2021 alone, the higher concrete prices were responsible for up to a 5% increase in overall construction spending, squeezing profit margins and complicating financial forecasting.
Additionally, companies have had to recalibrate project timelines and procurement strategies to account for these sustained price hikes, highlighting the importance of adaptation and strategic planning to maintain competitiveness and ensure successful project delivery in the face of evolving market conditions.
Navigating the persistent supply chain disruptions plaguing the construction industry requires a comprehensive understanding of the current challenges. Over recent years, projects have been significantly affected by delays in material supplies and a shortage of available transport logistics.
In 2021, the average delay due to supply chain bottlenecks was approximately 30 days per project, as reported by industry analysts. These disruptions have been attributed to multiple factors, including raw material shortages, port congestion, and labor shortages that have rippled through the production and distribution channels.
Consequently, companies have faced cascading effects, forcing them to reassess project timelines and resource allocation to mitigate the impact on project deliverables.
The effects of global events on supply chains cannot be overstated. The COVID-19 pandemic acted as a catalyst, highlighting the fragility of global supply systems as production facilities shut down and borders closed, restricting the flow of goods.
According to a report by the World Economic Forum, global trade experienced a dramatic decline of approximately 9% in 2020, which had downstream effects on material availability and construction schedules.
Furthermore, geopolitical tensions and trade policies, such as tariffs on steel and aluminum, have further exacerbated the situation, introducing uncertainty and added costs. These external pressures have underscored the importance for construction companies to maintain awareness of global events and adapt swiftly to change.
In response to these challenges, construction firms are now focusing on building resilience and reducing vulnerability within their supply chains. A survey conducted by McKinsey in 2022 found that 70% of companies are investing in technology to enhance supply chain transparency and decision-making capabilities.
Strategies such as diversifying suppliers, localizing material sourcing, and increasing inventory buffers have become prevalent, allowing businesses to buffer against unexpected disruptions.
Additionally, digital tools like predictive analytics are being harnessed to improve demand forecasting and optimize inventory management. These adaptive strategies not only help mitigate immediate supply chain issues but also solidify long-term resilience against future disruptions, ensuring more consistent and reliable project execution.
In today's volatile market, adaptive procurement strategies have become essential for construction companies seeking to manage rising costs and ensure timely completion of projects.
One effective approach includes the implementation of flexible contracting models that allow for price adjustments based on market conditions.
According to a recent survey by Deloitte, 62% of construction firms reported adopting flexible contracts to better handle price fluctuations, achieving cost savings of up to 10% compared to fixed-rate contracts.
Another strategy involves establishing strategic partnerships with suppliers, which not only secures favorable terms but also enhances supply chain predictability.
For instance, a study by the Institute for Supply Management found that firms with close supplier relationships experienced 25% fewer delays and reported improved quality in materials and service.
Successful case studies in adaptive procurement highlight the importance of innovation and technology.
One notable example is the case of Turner Construction, which in 2022 employed advanced analytics to better predict demand and optimize purchasing schedules, resulting in a 15% reduction in procurement costs. Furthermore, by utilizing blockchain technology to improve transparency and traceability, firms like Bechtel achieved a 20% increase in procurement efficiency and reduced fraud risk.
For long-term planning, companies are increasingly incorporating risk assessment techniques, such as scenario planning and stress testing, to anticipate potential disruptions. These practices, backed by a report from PwC, suggest that organizations adopting comprehensive risk management frameworks are 30% more resilient in navigating market volatility than those without such measures.
As the construction industry continues to face ever-changing market dynamics, these adaptive strategies will be instrumental in maintaining a competitive edge.
The modern construction industry requires not only rapid responsiveness but also strategic foresight to navigate the complexities of global supply chains effectively.
Flexibility in sourcing materials is essential for establishing resilient supply chain networks, allowing companies to quickly adapt to evolving market conditions and unexpected disruptions.
By diversifying supplier bases and tapping into local and international sources, construction firms can mitigate risks associated with any single vendor or geographic region.
This diversification ensures a more consistent supply of critical materials and reduces dependency on potentially volatile markets. Moreover, proactive scanning of market trends and geopolitical developments
enables companies to anticipate challenges and prepare contingencies, thereby avoiding costly delays and ensuring project continuity.
Building robust partnerships remains a cornerstone of resilient supply chain management. Establishing strong relationships with key suppliers facilitates better communication, coordination, and negotiation of favorable terms, such as volume discounts and priority delivery schedules. Moreover, exploring alternative sourcing options, including local suppliers and regional distributors, can provide critical buffers against international supply chain disruptions.
Technological advancements play a pivotal role in this endeavor, offering tools such as real-time tracking, automated procurement systems, and cloud-based collaboration platforms to enhance supply chain visibility and efficiency.
These innovations enable companies to make data-driven decisions, optimize resource allocation, and improve overall supply chain reliability. As construction firms navigate this ever-evolving landscape, the integration of technology and strategic partnerships will be vital to establishing resilient and sustainable supply chain networks.
The construction industry faces persistent challenges related to rising material costs and complex supply chain issues.
As highlighted, adopting adaptive procurement strategies and establishing resilient supply chain networks are essential to not only addressing these immediate concerns but also ensuring long-term sustainability.
By leveraging flexible contracting models, strategic supplier partnerships, and advanced digital tools, companies can navigate price fluctuations and secure more reliable material sources, ultimately achieving cost savings and enhancing project delivery timelines.
To remain competitive, construction companies are advised to incorporate comprehensive risk assessment frameworks and embrace technological innovations such as blockchain for transparency and predictive analytics for better demand forecasting. The diverse strategies employed by firms like Turner Construction and Bechtel exemplify how innovation and technology can drive procurement efficiency and resilience.
Moreover, platforms like DYL play a crucial role in this evolving landscape. DYL offers an all-in-one solution that enables construction businesses to streamline operations, integrate technology seamlessly, and improve both communication and visibility across the supply chain. By harnessing the capabilities of DYL, construction companies can effectively address the dynamic challenges of material costs and supply chain disruptions, paving the way for a more sustainable and prosperous future in the industry.