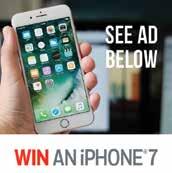
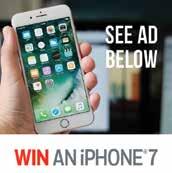
IN DEFENCE OF MANUFACTURING
As Australia’s automotive assembly operations continue their planned run-down, one sector that is putting itself forward to soften the blow is the defence manufacturing sector.
In his keynote address to the recent Australian Business Defence Industry Sovereignty Forum, Defence Industry Minister Christopher Pyne said: “This Government is putting Australian industry and Australian workers front and foremost in our defence procurement plans.



“There will be opportunities for Australian industry involvement and Australian jobs far broader than those covered by sovereign industrial capabilities.

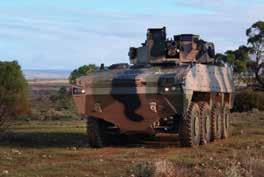
Industry Update has been promising a revolution in manufacturing media, and now it’s here. Industry Update Video is now live on our website at www.industryupdate. com.au.
While many companies have already embraced the medium of video to promote their products and to demonstrate them in action, until now, no Australian manufacturing media organisation has taken this approach to


OSAKA TO SYDNEY



“The Government’s forthcoming Defence Industrial Capability Plan, our Defence Export Strategy and the range of initiatives we have already put in place – not to mention the size, scope and scale of our Naval Shipbuilding Plan – will provide unprecedented
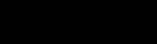
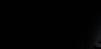


























Tsubaki celebrates 100 years P 10 Test and Measurement feature P 16


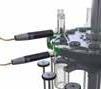


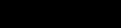


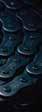






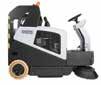
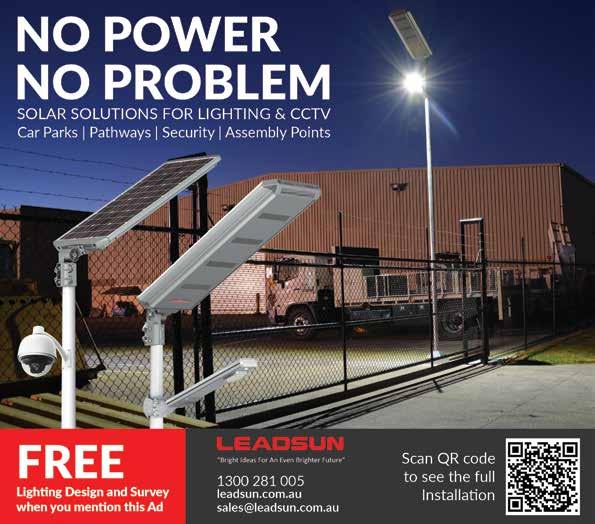

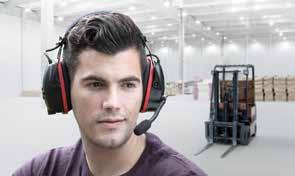

BAE's AMV35 combat reconnaissance vehicle is one of two contenders for the
SMALLER ISN'T SAFER
By Tony Pearce
It seems to be common wisdom that the larger a business is, the more it has to worry about cyber security. The converse of this is assumed to be true: the smaller a business, the safer they are. Who's going to want to hack into the friendly neighbourhood machining house when multi-million dollar companies are waving their online data tantalisingly in the digital breeze?
The answer, unfortunately, is quite a lot of people. Small businesses all over Australia, and even in rural locations, are just as vulnerable as anyone else and they can present a very attractive target to those with ill-intent looking to hone their trade.
Small businesses are juicy targets for up-and-coming hackers who are looking to test their skills or make small, unobtrusive hacks that are unlikely to be traced back to them. SMEs often lax security means it's easier to get in, and harder to get caught. They often have less strict information storage policies, meaning personal data is more likely to be stored on company computers (making it easier for an intruder to do more damage, or steal more information).
Anyone who's able to guess a company password or exploit an unmatched application can gain access to company information, personal details,
and additional passwords which could enable them to get into bank accounts, or any application or account that you move money through (like Paypal, Ebay, or Amazon).
But surely we're too small to be targeted?
Some people consider themselves safe because hacking their small business would be "too much work for a very small chance of a very small reward", but this isn't so.
Hacking at this smaller scale is less "typing code into a glowing screen" and more "running down a checklist of possibilities". Much of the work has been done long before someone sits down to breach a system, so it's not much work at all to attempt a hack. Software is coded and compiled, and vulnerabilities are located in old software builds well in advance, and all someone needs to do is try as many approaches as possible, rather than code a custom solution for every company.
All takes for a successful hack is one weak password, or one out-ofdate program. Recent ransomware like Wannacry or NotPetya crippled companies around the world, and attackers didn't compile a custom program for every company; they created a program that exploited a single vulnerability in old
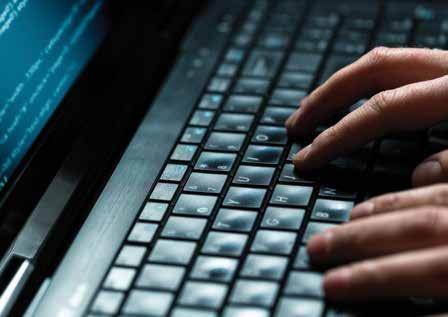
operating systems, and tried to find as many instances of that vulnerability as possible.
How do we stay safe?
Luckily, laying the groundwork for staying safe as a small business is simple and free.
We've covered common approaches to business security before, and the core rules always apply: keep your software updated, have strong passwords that are
not reused for different accounts, check what files are before you open them, and don't connect unknown devices to your computer or internal network.
Other rules, such as having a separate device for work and for personal use (so that if one is infected, hacked, or in any way compromised, the threat doesn't spread to a different network) can help small businesses stay safe and prevent the cross-contamination of business and personal data.
PUBLISHER SCOTT FILBY scott@industryupdate.com.au
ADVERTISING SALES DIRECTOR SCOTT FILBY scott@industryupdate.com.au
ADVERTISING SALES REP GLYN SMITH glyn@industryupdate.com.au
EDITOR LAURENCE MARCHINI editor@industryupdate.com.au
CREATIVE DIRECTOR DEB ZOROTHEOS production@industryupdate.com.au
SUB EDITOR TONY PEARCE tony@industryupdate.com.au
ADVERTISING COORDINATOR & WEB CONTENT ASSISTANT KEVIN NGUYEN kevin@industryupdate.com.au
VIDEO EDITOR RHYS MCGOWAN rhys@industryupdate.com.au
WEB DEVELOPER JINI M R
FINANCE & ACCOUNTS MICHELLE ALCOCK michelle@industryupdate.com.au
ACCOUNTS RECEIVABLE LYN SLIGAR lyn@industryupdate.com.au
ADMINISTRATION NICOLE CHARLES nicole@industryupdate.com.au
SUBSCRIPTION ASSISTANT MARK ZAKOSHANSKI info@industryupdate.com.au
SUBSCRIPTION ASSISTANT NICHOLAS TSE nicholas@industryupdate.com.au
PRINTER NEWSTYLE PRINT
INDUSTRY UPDATE MEDIA PTY LTD Suite 403, Level 4, 116-118 Christie Street, St. Leonards NSW 2065 Phone: 02 9439 1288 Fax: 02 9439 3233 Email: sales@industryupdate.com.au ww.industryupdate.com.au
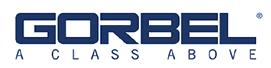

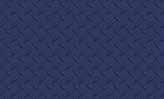
IN DEFENCE OF MANUFACTURING
Continued from cover
Among projects already started, the $50 billion investment in Australia’s Future Submarine Programme will directly create and sustain around 1100 jobs and a further 1700 jobs through the supply chain. And the Future Frigate Programme will directly create more than 2500 jobs and, according to Minister Pyne, “will form the backbone of Australia’s future surface shipbuilding industry.”
With the Federal Government committed to investments that will increase Australia’s defence manufacturing capabilities to the extent that the industry can become an export earner, such is the potential for on-going business that the states are finding themselves pitted against each other.
Take, for example, the impending $5 billion contract to replace the Army's Australian Light Armoured Vehicle. The two leading contenders are the BAE Systems AMV35 and the Rheinmetall Defence Boxer CRV, and each bid has the backing of a state government.
Rheinmetall intends to build its vehicles in Queensland, and is receiving support both from the state government and local federal politicians. But it is the Victoria-backed BAE Systems bid that is receiving more publicity – and financial support.
Importantly, the plan is to build a new assembly works at Fishermans Bend, the 37-hectare former Holden manufacturing site, purchased last year by the Victorian
Government for $130 million with plans to turn it into a hub for highend industries.
And Victoria's Industry and Employment Minister Wade Noonan claims the contract could lead to the creation of up to 2000 jobs, thereby helping at least some of those who have lost employment in the car manufacturing sector.
Shadow Minister for Innovation, Industry, Science and Research, Senator Kim Carr, reckons that defence manufacturing is an ideal growth area: “Australia has a long history of quality defence manufacturing,” he says.
“The Bushmaster is a notable example. It has served Australia’s soldiers well in the conflicts of the past 20 years as one of the world’s best-protected mobility vehicles. But the Bushmaster is approaching the end of its useful life and the ADF must choose a successor.”
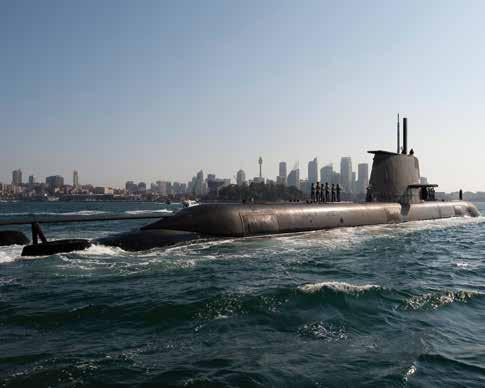
However, government sponsored expansion of the Australian defence industry is not universally welcome.
“It is in the national interest that the new armoured vehicles will be built in Australia too, “ he adds. “Australia needs a defence industry plan to ensure that this is done properly.” But Carr warns: “These strategically vital industries should not be used as bargaining chips to buy votes.”
Australian Greens industry spokesperson Senator Lee Rhiannon says: “The defence sector compensating for depressed activity elsewhere demonstrates that the government can intervene to support jobs and investment.
“The question is then what sort of activity the government should be
supporting; should it be the development and export of machines of war?
“Surely it would be better to support jobs and investment in productive, socially useful areas like renewable energy and public transport.
“An innovative manufacturing sector providing thousands of secure, well-paid jobs will go a long way to overcoming the challenges our country faces,” says Senator Rhiannon.
INTELLIGENCE IS KEY TO POWER MARKET DEMAND MANAGEMENT
With dire warnings of impending electricity supply shortfalls in the eastern states during the coming months, attention is turning to effective demand management as a tool to balance supply and demand. And while electricity retailers are offering financial incentives for both individuals companies to switch off large loads at projected times of shortfall, this simplistic approach can have only limited benefits.
Flow Power, the electricity retailer that gives its clients access to the wholesale power market, has a rather more sophisticated approach to demand management. And it needs to.
“As a wholesale customer, you can respond to market signals to save on energy costs. In fact, the more businesses that buy wholesale, the better the market
will cope when supply and demand are out of sync,” said Flow Power Managing Director, Matthew van der Linden in a recent Ai Group webinar on energy management.
Because Flow Power allows its customers to take advantage of the lower but variable wholesale rate (rather than the arbitrarily averaged rate charged by the big three retailers), they are potentially exposed to the wilder fluctuations that can occur in the wholesale market, with rates potentially multiplying tenfold from one half-hour period to the next.
The key to avoiding these market peaks is intelligence: to have advance knowledge of when the market is about to change for the worse. Generally, these events will be known in advance –especially when they involve something
like a generator being taken out of service for routine maintenance. But there are also occasions where there is only a short warning period.
The key for Flow Power’s customers is the kWatch Intelligent Controller, a “black box” that is wired into each of the company’s clients’ sites.
At the simplest level, the controller monitors the site’s loads, providing realtime data on consumption and rates via the Flow Power Portal. But it can also be programmed to manage the site’s energy use when prices change with automatic responses to market signals. And, ultimately, it can be used to interactively manage supply and demand.
As a result, having the advance knowledge of the impending rate rise, the
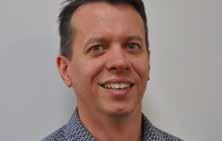
user can elect to switch off large loads for the duration of the higher rate, or to switch in their own generating resources, whether that be an on-site diesel generator or solar with storage, thereby reducing their demand on the grid.
The Collins Class submarine is a diesel sub built and operated by the Australian Navy, and were the first subs to be built in Australia.
Matthew van der Linden
CAPACITOR REFORMING SERVICE KEEPS DRIVES READY FOR SERVICE
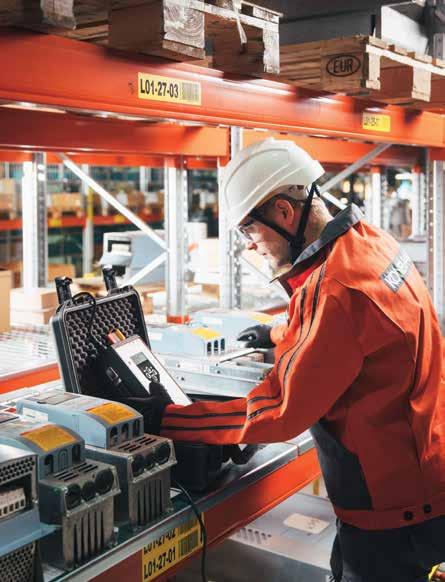
The latest productivity enhancing service from Konecranes addresses the problem of keeping spare motor drives in shape so they can be relied on to enter service if required. The company’s new variable frequency drive capacitor reforming service uses a proprietary DC power source to reform stored VFDs onsite, ensuring that they are in top condition when they are needed in service.
According to Konecranes’ Australia and New Zealand Consultation Services Manager, Joseph Cefai: “Companies that use VFDs almost always keep spare units on-site in case one breaks down. These spares can remain dormant for years before being put into service. These dormant VFDs require reforming at least once a year to ensure their capacitors stay charged and in top condition. Failing to do so creates a risk of a catastrophic failure during a time when the spare VFD is needed the most,” he says.
Konecranes’ VFD capacitor reforming service is designed to reform spare drives
without ever removing them from the facility. A certified/qualified electrician will reform the capacitors in the DC bus of a VFD using a fully automated portable DC power source.
The service also includes a full visual inspection to identify faulty devices and recommendations for corrective actions.
“After the drive has been reformed, the electrician will issue a certificate of inspection and label the VFD. The certificate includes the date of the next recommended reform, should the VFD remain idle for another year,” adds Cefai.
“Spare VFDs are there to minimise downtime, when the main VFD isn’t working. The last thing you want is for your spare part to also fail, causing additional unnecessary downtime,” he said.
Konecranes
1300 937637 www.konecranes.com.au



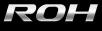
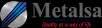
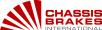




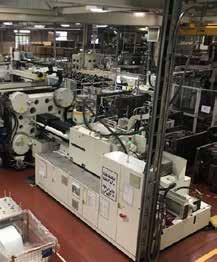
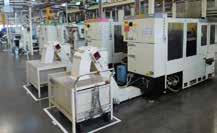

THE ESSENCE OF SMARTER MANUFACTURING IS CLEVER IDEAS
By Senator Arthur Sinodinos
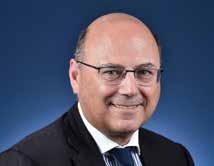
Manufacturing in Australia and around the world is turning the corner. It’s turning the corner in a smart, advanced way, creating opportunities that the nation must grasp.
The tide of change occurring in the sector—and the opportunities arising from this change—was a central theme of my address to the National Manufacturing Summit in Canberra in June.
The summit was a great chance to speak to key stakeholders from across the sector and outline the Government’s
vision for manufacturing in Australia.
The summit was also an important opportunity to hear experts from a range of sectors—industry, education and government—discuss the state of Australian manufacturing and share ideas about how manufacturing in this country can innovate and prosper.
As the Minister for Industry, Innovation and Science, I’m acutely aware of the important role manufacturing plays in the nation’s economy. Manufacturing is an indispensable part of the innovation ecosystem that we are trying to build in this country. We can’t hold back the tide of change that’s gathering pace—what we have to do is adapt.
I made it clear at the summit that we have to adopt an innovation mindset and a global outlook. We recognise that we need to embrace advanced technologies and innovative business processes to be globally competitive. In essence it’s about being smarter in the way we do things.
The opportunities presented by Industry 4.0, the Internet of things, artificial intelligence and robotics were all discussed at the summit. They’re all incredibly exciting developments and will all play a role in smarter manufacturing for the future.
But the essence of smarter manufacturing is clever ideas—and one thing I know about this country is that we really punch above our weight when it comes to knowledge creation. The challenge, however, is how we translate this knowledge creation into more commercial outcomes.
No sector of the economy invests more, relative to its output, in new research and experimental development than manufacturing. But we can do more—and we are. It all revolves around collaboration.
We have the Industry Growth Centres, Cooperative Research Centres and Entrepreneurs’ Programme all working to help Australian businesses and researchers
to collaborate, innovate and succeed. And we have just rolled out the first two tranches of our additional $100 million investment in advanced manufacturing. This includes the $47.5 million Advanced Manufacturing Growth Fund, which has grants to encourage new capital investments in advanced manufacturing in South Australia and Victoria, where car assembly will cease later this year. And $20 million has been dedicated to advanced manufacturing research projects under the Cooperative Research Centre Projects initiative.
Manufacturing is seizing opportunities by playing to their competitive strengths to build dynamic and globally focused businesses. But to make the most it, we must continue to invest in knowledge and draw on our reputation as a nation of innovators.
Senator Arthur Sinodinos is the Minister for Industry, Innovation & Science.
AUSTRALIA SHOULD HEED THE GERMAN EXAMPLE
By Senator Kim Carr

The IMF and OECD have drawn attention to the fact that, for the first time since the industrial revolution, the rate of technological change is increasing faster than new job opportunities are being created.
Unfortunately, when these warnings are distilled into media commentary they too easily become predictions of catastrophic job losses, especially in manufacturing. We should heed instead the example set by democracies where policymakers are intent on unleashing the opportunities in technological change while containing the risks.
Automation does not have to mean that the future will be a sci-fi nightmare in which robots perform most of the work while humans are reduced to precarious casual employment in sweatshops. Avoiding that will require action by governments, and it will require workers being properly engaged in deciding the future of work.
This is increasingly widely recognised. Even Elon Musk has made the extraordinary assertion – for him – that
to avoid disaster governments need to regulate effectively.
In deciding how to shape the future, we must rely on fact rather than the predictions of doomsayers. We must challenge the notion that most jobs will disappear at the rate than some people have been predicting. The evidence to sustain such claims just is not there.
We frequently hear that more than 40% of existing jobs will be gone by 2030. Sometimes it is nearly 50%, depending on who is doing the doomsaying.
The source of all this gloom is a much-cited paper published in 2013 by two Oxford University researchers, Carl Frey and Michael Osborne. They argued that “about 47%” of jobs were at risk from computerisation. Their estimate went global, and was picked up in a CEDA report that has fuelled the media commentary here in Australia.
The disruption predicted by Frey and Osborne is real enough. But citing a bald figure, whether 40, 47 or 50%, can be seriously misleading.
David Autor of the Massachusetts Institute of Technology has argued that although automation may reduce average employment (the number of jobs per unit of output) it does not necessarily reduce aggregate employment (the total number of jobs).
According to Autor, robots and computers substitute for human workers in repetitive tasks while increasing the
value of tasks that workers uniquely perform – tasks involving problem-solving, adaptability and creativity.
That is also the view of the International Federation of Robotics, which argues that in future manufacturing robots will complement and augment labour. Robots will perform routine or dangerous tasks while raising the demand for higher-skilled forms of human labour. New lower-skilled jobs may also be created, through spillover effects in other sectors.
This is not wishful thinking. It is already happening in some advanced economies. The Centre of European Economic Research has reported that between 1999 and 2010 the replacement of routine work by new technology actually raised labour demand across the 27 EU economies by 1.9 million jobs.
It is essential that this bigger picture be kept in mind each time the Frey and Osborne research, or some garbled media version of it, is mentioned.
The European Union argues that with the correct policy settings opportunities can actually be expanded in the new age of automation. The EU has set a target: by 2020, it wants 20% of total economic value to come from manufacturing. That is a 25% increase on present levels.
This is no rosy-eyed optimism. EU planners accept that there are difficult problems to be overcome, such as deciding the amount of investment needed to attain the target.
Questions about legal liabilities, intellectual property and the harmonisation of standards will have to be resolved. Above all, there are questions about the transfer of skills that will be required in the transition to the smart factories of the future. That includes questions about how people at the bottom end of the labour market can be reskilled.
But, even with these acknowledged difficulties, EU policymakers are still talking to the public about opportunities. The Germans, in particular, estimate that there will be a 6% increase in manufacturing jobs in the next decade.
The Germans are already demonstrating that smart factories can be compatible with lower unemployment. The unemployment rate in Germany is 3.9%, and the number of robots per 10,000 workers is 300.
Compare that with Germany’s neighbour, France, where the number of robots per 10,000 workers, 126, is much lower but the unemployment rate, 9.5%, is much higher.
Australia should heed the German example. We cannot be luddites, rejecting new technology. But nor should we assume that technological change means an insecure future for manufacturing and those who work in it.
Senator Kim Carr is the Shadow Minister for Innovation, Industry, Science and Research. This article is adapted from his speech to the Australia Institute’s Future of Manufacturing Summit, held in Canberra in June.
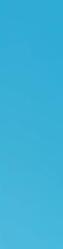

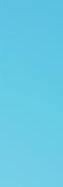







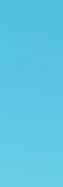

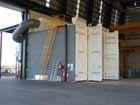


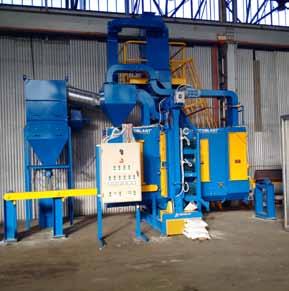
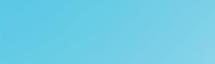


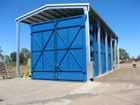
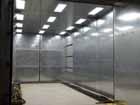


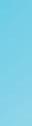
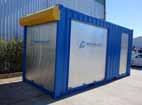
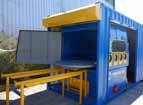


Protoblast has been designing and manufacturing to suit customers’ individuals needs since 1975.

ABRASIVE RECOVERY SYSTEM





The best way to prepare a surface for a coating is by using the abrasive blasting process. Whether you need to blast earthmoving equipment, turbines, structural steel or railway lines...
AIRLESS BLAST MACHINES
DUST COLLECTORS



SECTION BLAST MACHINES




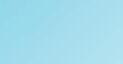



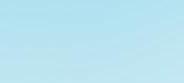
We have successfully completed projects for Bechtel, BHP Billiton, ThyssenKrupp and BAE Systems just to mention a few.

Protoblast has the experience to design and supply equipment that is fast, efficient, improves your product and saves you money ... year after year

TSUBAKI CENTENARY CELEBRATIONS MOVE FROM TO SYDNEY
This year marks the 100th anniversary of the foundation of the Tsubakimoto Chain Co at Osaka, Japan, and the milestone is being celebrated at the company’s subsidiaries around the globe.
Shortly after the first event in the centenary celebrations in June, Tsubaki Australia hosted a training seminar followed by a cocktail reception for almost a hundred guests at Sydney’s Darling Harbour. The audience, which included customers and distributors from both Australia and New Zealand, were honoured to be welcomed to the event by Yasushi “Eddy” Ohara, the President and
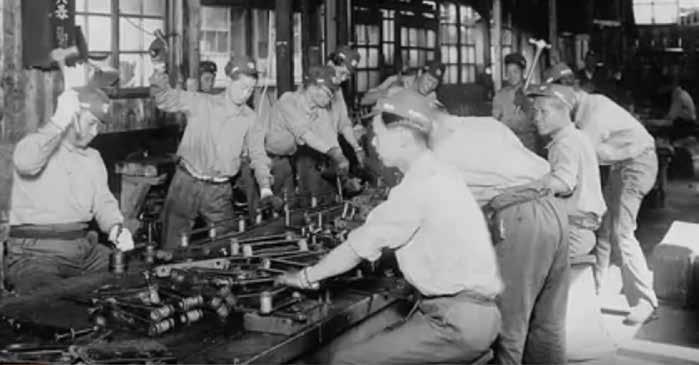
COO of the global Tsubakimoto Chain Co.
In his welcome, Ohara gave the assembled guests a brief tour through the preceding 100 years, which had seen the company grow from a small operation manufacturing bicycle chains to the global chain specialist it is today, serving markets from auto engines to materials handling.
Said Ohara: “Today, if something’s moving, you should see our products underneath!”.
The formal presentations concluded with a traditional toast, raised by Brendan McConnell, Sales Director of Tsubaki Australia.
WOOD PROCESSORS USE COUNTLESS KILOMETRES OF CHAIN
One of the largest users of Tsubaki chain products on both sides of the Tasman is CarterHoltHarvey Woodproducts, represented here by Peter Neal from the company’s New Zealand operation and Gary Monshing from Australia.
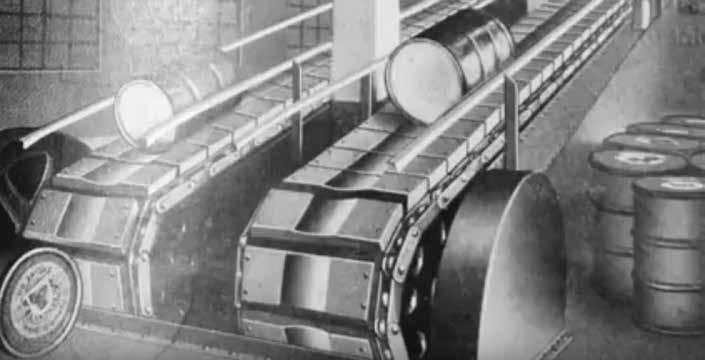
The company operates 14 sawmills around Australia and four in New Zealand, and has been using Tsubaki chain exclusively for the past 11 years –amounting to “countless kilometres of chain, “ according to Gary Monshing.
Peter Neal describes Tsubaki as “an integral part of our operations” and
his company’s “preferred supplier that offers added value and the lowest TCO in the business.”
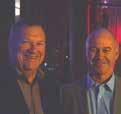
In toasting the next century for Tsubaki, the two colleagues expressed their confidence that the company would continue to deliver premium products and service and would continue to innovate to add value to customers such as CarterHoltHarvey Woodproducts.

NEW ZEALAND FRUIT PACKERS ARE RECENT CONVERTS
One company that is a relatively recent convert to the benefits of Tsubaki chain products is Compac, the New Zealand based leader in high-speed packhouse technology for the produce industry.
The company produces its fruit sorting systems both in New Zealand and China and exports them worldwide, with significant sales throughout the Americas, notably in California. And those systems are now built using Tsubaki chain.
According to Compac’s Joshua Schoombie, this amounts to many kilometres of chain a year: “Not enough to go to the moon yet,” he quipped, “but
we’re getting there!”
“There is so much to admire about Tsubaki,” says Josh: “the Japanese philosophy, the quality, the workmanship and the capacity to support the products.”
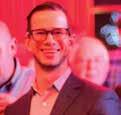
“I’m sure Tsubaki will continue its trajectory into its second hundred years with its spirit that there can be no second best.”
Yasushi “Eddy” Ohara, President and COO of Tsubakimoto Chain Co, welcomed the guests
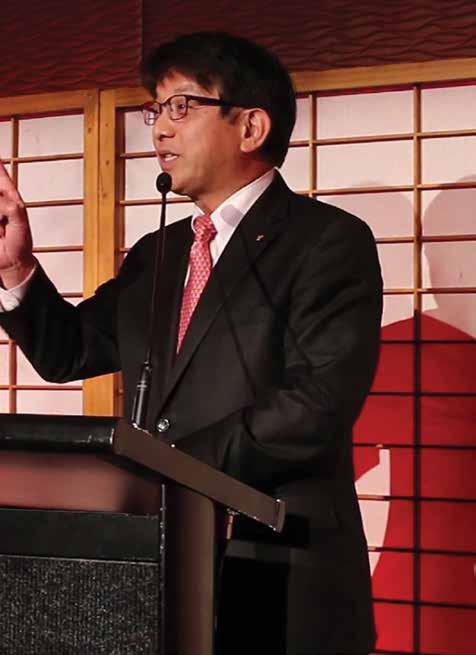
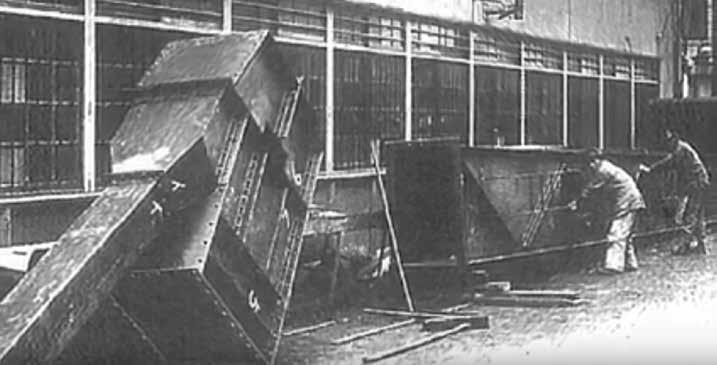
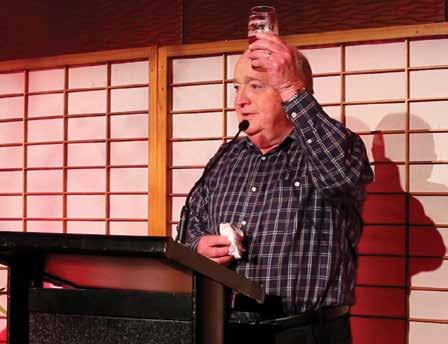
PRESIDENT REGARDS AUSTRALIA AS HIS SECOND HOME
The reason why the Tsubaki centenary celebrations moved direct from the company’s headquarters in Osaka, Japan, to Sydney is due in no small part to the company’s President and COO, Yasushi “Eddy” Ohara.
Ohara is a 35-year veteran of the company, and is proud of its history, pointing out that 10 presidents had preceded his appointment.
NEW ZEALAND DISTRIBUTOR RATES NUMBER ONE SUPPLIER
Robin Russell is Director of Russet Holdings, Tsubaki’s major distributor in New Zealand, and reckons that the company is his number one supplier.
“We feel privileged to be a distributor,” says Russell, who has been representing Tsubaki on the New Zealand market since 2009. “We did try before to get the agency, but Tsubaki stuck with its incumbent distributors, and we admired them for their loyalty. Now they are loyal to us and we are loyal to them,” he added.
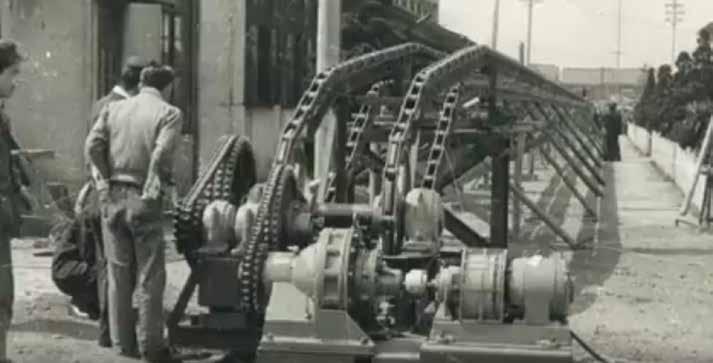
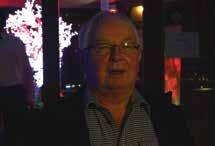
Russell has been in the materials handling business for almost 32 years, and knows a thing or two about quality equipment. So when he describes Tsubaki as his number one supplier it’s clearly an informed statement.
“It’s not just the excellence of the products,” he says, “it’s the continuous innovation, the helpfulness, and the support is absolutely A1.”
He has strong ties with Australia, having first visited the country some 40 years ago, and having spent five years during the 1990s based at Tsubaki Australia in Sydney. “My son grew up here,” he said “and he still calls Sydney home!” Ohara added that his son is now carving out a career in politics in Japan.
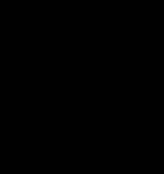
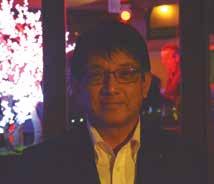
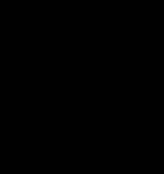
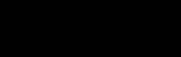

Having formally kicked off the centenary celebrations at the company’s Osaka headquarters, it was Ohara that insisted that Australia should be next on the list. “I cannot attend all the celebrations around the world,” he admitted, “but I wanted to make sure that I could be here to celebrate with my Australian friends and colleagues.”

some form or other (and continue to use Tsubaki chains). “Who else is going to manufacture a ute?” quipped Sakai. “I’m worried about that too,” added Ohara. And Ohara’s ties with Australia continue to get stronger. His secretary was recently married… to an Australian!
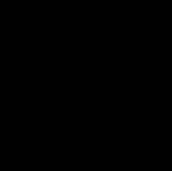
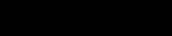
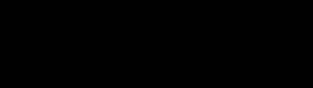

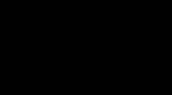


Both Eddy Ohara and Taku Sakai, Managing Director of Tsubaki Australia, expressed regret at the demise of volume car manufacturing in Australia, with the impending closures of the Ford, Holden and Toyota plants.
However, they both expressed hope that the industry would continue in


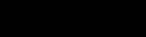



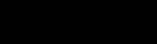
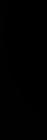





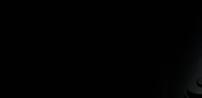
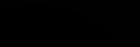


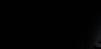








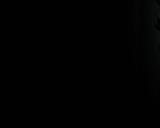


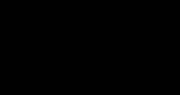







Sales Director Brendan McConnell raises a traditional toast
EXPRESS ACCESS TO INDUSTRIAL ELECTRICAL AND NETWORKING PRODUCTS
LAPP Express Australia offers instant access to thousands of stocked industrial electrical and networking products. Operated by ECS (Engineering Computer Services), a business serving engineers and purchasing specialists for more than with 30 years with extensive experience as a leading authorised supplier of electrical and automation products across Oceania, the company has now extended its online offer to customers in Australia.
Employing only trained electricians and automation engineers who understand customer needs, LAPP Express stocks more than 5000 high-quality parts and over 1 million metres of the world’s best
cable from renowned manufacturers such as LAPP Group, Wieland Electric, Moxa Networking and LS.
Lapp Express offers cut-to-length cable with no cutting charges from its huge stocked cable range with over 1000 different options to choose from. And with fast free delivery to any location in Australia in 1-4 days on all orders over $100 the company reckons it can reduce downtime for Australian clients.
The company’s website makes it easy for users to quickly find and buy what they need using the intuitive search and find functionalities, rich technical product data, real time stock availability and online and telephone technical support.
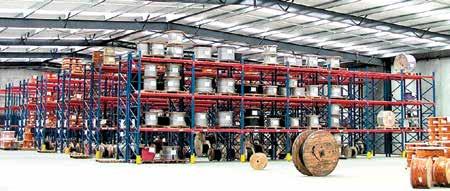
In addition, customers can track their orders as they are dispatched and delivered, download invoices online and receive updates via email on the latest new products, technologies and promotions.
ICONIC STORAGE BRAND SET FOR AUSTRALIAN LAUNCH
An iconic Taiwanese brand in storage solutions is on its way to Australia. Shuter Enterprise Co will introduce itself to the Australian market with a series of conferences during October.
Shuter was founded in 1969, and over the years has developed a strong reputation for high-quality engineering and manufacturing, combined with aesthetic design. These attributes have seen the company’s storage solutions find global acceptance in applications from the factory floor to the front office. And now the range extends to stationery and the home, with the Livinbox brand of domestic storage products.
The product is broad, and includes
industrial sorting containers, tool storage, workstations, office furniture and cabinets and stationery organisers. All the company’s products are designed from the user’s point of view, by finding the simplest way to build an ideal home for objects.
Shuter has been particularly successful in developing high quality products that combine its manufacturing expertise in both metals and plastics. For example, the ST series of professional steel cabinets are constructed using high-quality galvanised steel, high impact PP or ABS drawers, along with its innovative multi-material combinations.
With more than 100 different cabinet designs combined with no fewer than 27

different types of drawers, the company reckons it can cover every user’s needs.
All Shuter storage solutions have the strength to carry heavy-duty repair tools or auto parts, and lockable casters make transportation safe and easy. And the modular design ensures that cabinets can be stacked as required to help users manage their workspaces efficiently.
The Shuter range will be introduced to the Australian market with a series of
Shuter Enterprise Co +886 4 2335 8800
info@theshuter.com www.theshuter.com



conferences, beginning in Parramatta on 13th October 2017, then in Melbourne on 16th October, and concluding in Brisbane on 19th October.
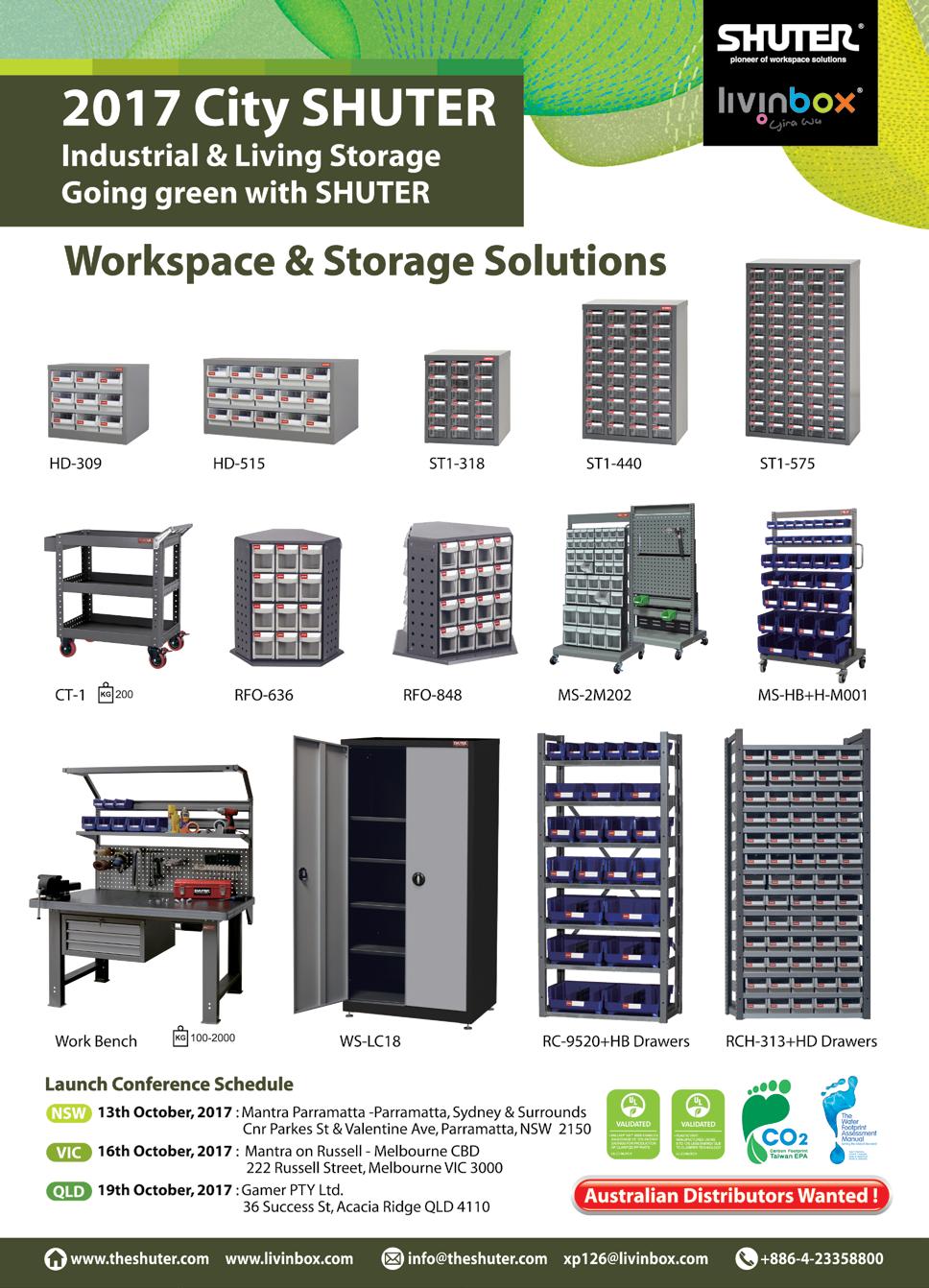
AUSTRALIAN EXPORTERS ARE GROWING IN CONFIDENCE
The last six months have seen Australia’s small- to medium-sized exporting businesses growing in confidence and looking forward to increased sales, profits and growth.
The latest exporter sentiment index from Australia’s export credit agency, Efic, paints a bright future from its survey of more than 1200 SME exporters, reporting on perceptions about current and future economic conditions and the international business outlook.
Expectations for future economic conditions over the next 12 months increased by 10 basis points since the last survey in November 2016. There is also a much stronger expectation of international business profitability with 58% of all respondents expecting increased profitability over the next year. And around half of the surveyed businesses expect to increase employee numbers - an increase of 6 basis points on the previous survey.
Two thirds of all respondents are expecting future sales revenue to increase.
According to Swati Dave, CEO and Managing Director of Efic: “We have found that confidence among respondents is strong in terms of economic conditions, their financial position and perceived future profitability from international revenue and employee growth.”
“The increased confidence is driven by an increased demand in export markets and due to improved sales strategies,” she added.
Although positive sentiment is significantly higher since the last survey, competition in international markets has increased. 27% of respondents that expected declining sales cited increased competition in international markets - a significant increase from November 2016 when 12% of respondents felt constrained by international competition.
Access to finance appears to be easing
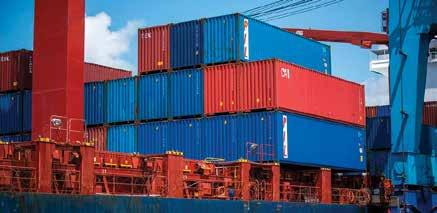
slightly with 34% saying that borrowing money for an overseas venture will be easier in the year ahead.
“However one in five respondents surveyed are expecting finance access to become more difficult – primarily due to the cost of credit increasing and working with financiers that do not understand the complexities of managing working capital through the export cycle,” said Swati Dave.
“It is in cases like these where Efic is able to help with expertise in exporting and the ability to support businesses when their bank may not be able to assist,” she concluded.
Efic 1800 093 724
www.efic.gov.au
SYDNEY SHOWCASE FOR SUCCESS OF AUSTRALIAN FOOD MANUFACTURING

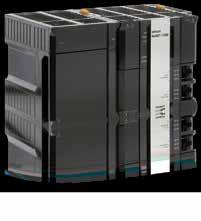



If anyone needed convincing of the buoyancy of the Australian food processing industry, a visit to foodpro 2017 in Sydney would have done the trick. As one of the top performing areas of the country’s manufacturing industry, the food manufacturing business now accounts for 4% of Australia’s GDP, employs hundreds of thousands of people and contributes significantly to Australia’s exports.
In the words of Federal Minister for Small Business, the Hon Michael McCormack, who visited the show on opening day, it “is a fantastic example of the importance of food manufacturing in Australia. There’s never been a better time to produce food. There’s never been a better time to market it overseas.”
Marking the show’s 50th anniversary, the 2017 foodpro was the largest show ever, both in terms of numbers of exhibitors and floorspace occupied, and was the best attended ever in Sydney.
Split over two floors of the new Sydney International Convention Centre
at Darling Harbour, the show saw some impressive displays from exhibitors, with the organisers awarding a tie between both Multivac and Sealed Air for the best stand at the show. Best shell scheme went to Wilmar BioEthanol, and best stand under 100m2 was Columbit Foods.
Event Director Peter Petherick is enthusiastic about the event: “foodpro 2017 was the best we’ve had, absolutely. It was marvellous seeing the show floors so busy, with visitors so engaged in what was on offer. From demonstrations of the larger equipment to ingredients exhibitors showing new additives – there was no shortage of interesting and valuable opportunities available. I can’t wait to see what advancements, partnerships and products come from this show.”
foodpro
03 9261 4500
www.foodproexh.com
Rugged, reliable industrial automation products from Turck are built to perform in the toughest conditions, and our engineered solutions are customised to meet your application challenges. Cheap knock-offs can’t compare. Turck works!
Manages complex data, with seamless PLC integration, in RFID environments. Measures just 1.25 x 5.6 inches. Not suitable for managing complex data (or your reputation).
Call 1300 132 566 or visit www.turck.com.au
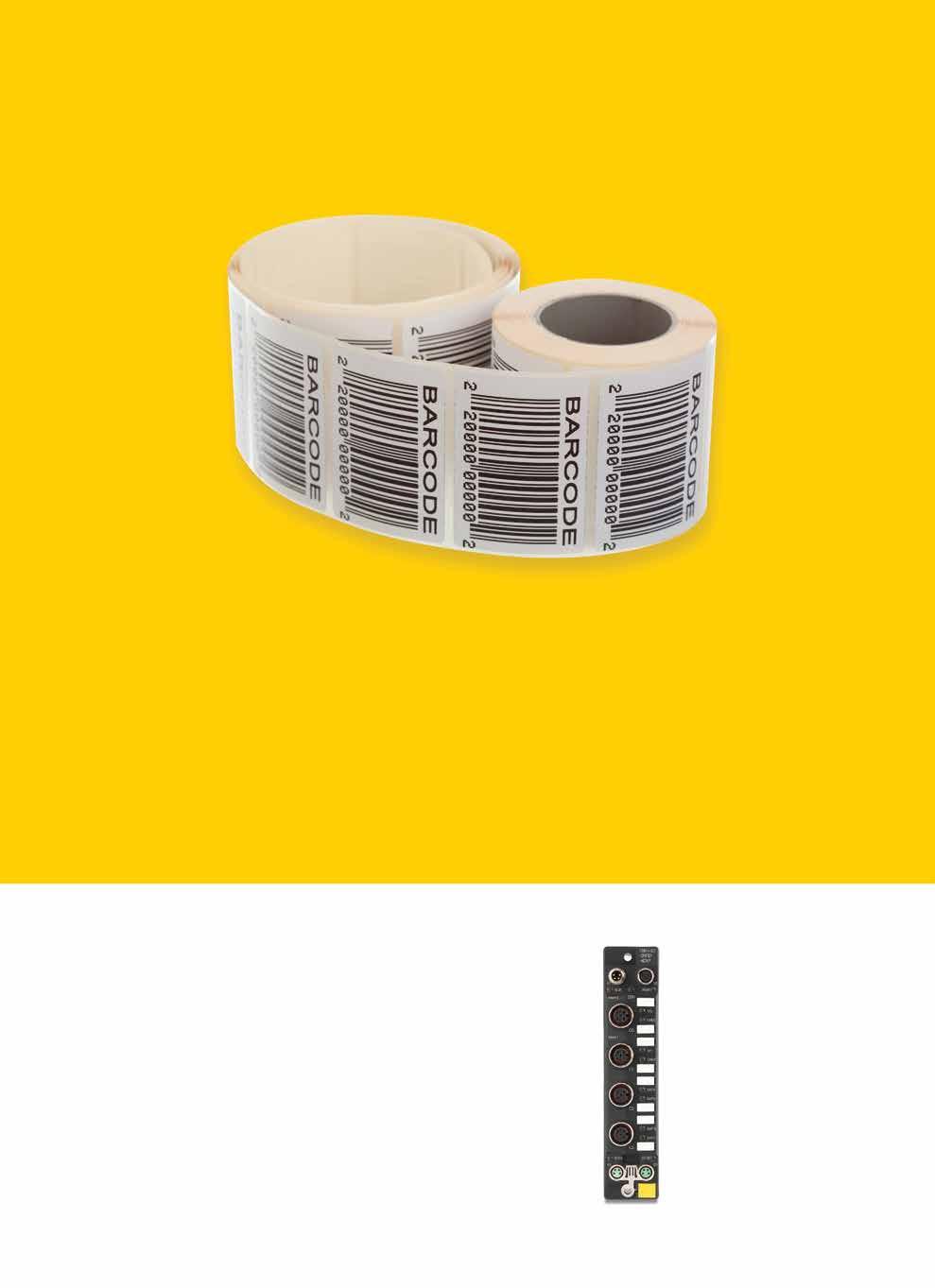
TBEN-S-RFID Ultra-Compact I/O Modules
DISPLACEMENT MEASUREMENT
– ARE YOU USING THE
RIGHT SENSORS?
The measurement of distance (or displacement) has become an essential part of automated manufacturing, as Sam Bhasin explains.
In a world of Industry 4.0, sensors must perform high-speed measurements and provide high-precision results to ensure reliable quality assurance. Optical measurement techniques play an essential role in the increasing automation of manufacturing and inspection processes. Noncontact sensor technology is responsible for wear-free, fast, highprecision and reliable measurements of manufactured components and their measuring points. This is a decisive advantage in online measurement, particularly if the target is in a difficult-toaccess area.
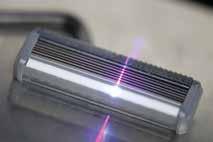
Measurement data are generally available in real time and so can be used to automatically correct and control the production process. Process automation can improve product quality and reduce raw materials and energy usage, which minimises production costs.
A wide range of displacement sensors are available to suit different applications based on parameters such as measuring range, frequency response and accuracy.
The manufacture of laminated glass, solar cells, flat screens and smartphone displays are challenging as they consist of several layers and different transparent materials. When manufacturing multilayer, laminated and curved glass for aeroplanes, automotive and architectural applications, precise thickness measurement of each layer is important. If the curvature of the adjacent layers does not comply with the specifications, there is a risk of increased stress, which might lead to deficiencies or delamination of the glass.
CONFOCAL SENSORS
The exact thickness of each layer and the air gap between those layers must be determined to ensure high quality. Due to the high cycle rates involved, the measurements must be performed quickly and precisely. Confocal sensors master these tasks. They are compact, high speed and easy to integrate and ensure highest reliability in almost any area where high precision is expected - from machine monitoring to fully automatic quality control of the final product.
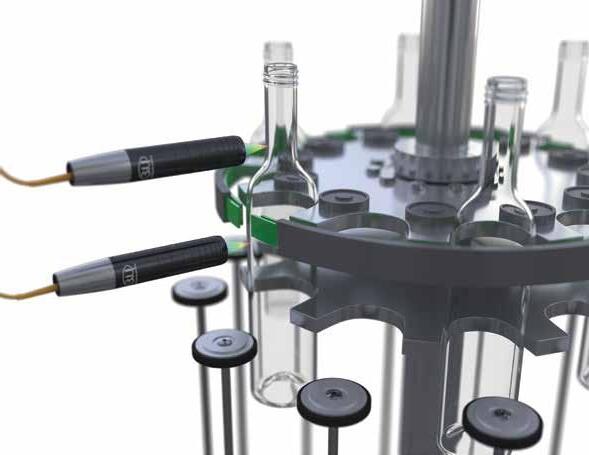
Large plants and machinery such as stone mills or telescopic installations often work with hydrostatic bearings, which are continuously supplied with liquid lubricant via an external pressure supply. In this case, eddy-current displacement sensors are used as they can ‘see through’ the lubricant and provide submicron position control. Eddy current sensors can be used under high pressures and temperatures, in high radiation and in dirty and dusty harsh environments. Built-in temperature compensation also ensures high measurement accuracies can be achieved even in fluctuating temperatures.
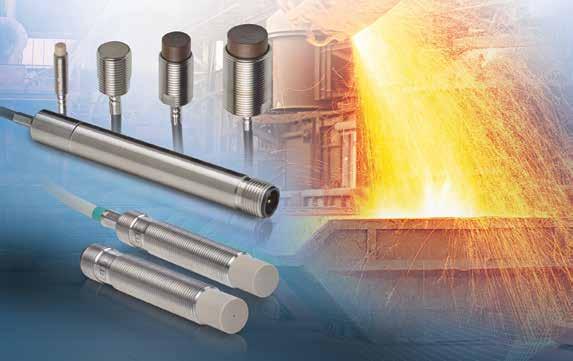
Laser triangulation sensors with their small spot size, large standoff, fast measuring rate and very high precision find numerous applications in industry. One example
is in pick-and-place machines, where laser triangulation sensors are used to monitor the position of tiny components. They ensure that the components are positioned the correct side up, at the correct location and at the correct height.
The requirements on the measurement technology are enormous; not only because the parts are extremely small, but also primarily due to the rapid change from shiny to matt surfaces. The pins consist of a shiny metal, whereas the circuit board presents a matt surface. Therefore, the receiver element in the sensor is at frequent intervals alternately exposed to strong and then weak reflections. A laser sensor technology with automatic target compensation (ATC) provides fast control of different reflections and enables a smooth signal frequency of the distance signal ensuring high measurement precision at all times.
Laser sensors are not only bound to one-dimensional measurements, as there is demand for multidimensional quality control in industrial production. Laser profile scanners are increasingly used for 2D and 3D profile and contour measurement applications. Their operating principle is based on the laser triangulation technique for twodimensional profile detection. They detect, measure and evaluate the profiles on different object surfaces. While the
Eddy current sensor for harsh environment >
Razor profile measurement
Single sided glass thickness measurement >

laser scanners are giving 2D information, you can obtain the third dimension by moving the laser scanner or the target object relative to each other.
QUALITY CONTROL
One such application that can benefit from laser scanners is the inspection of adhesive beading in a smartphone housing. A challenge here is the very fine contours inside the smartphone and extremely thin, partially semi-transparent adhesive beading. To ensure the product passes quality control, perfect control of the completeness of the beading and the exact height and width of the applied adhesive are required.
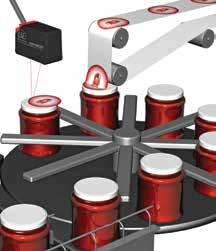
This also applies to the logos on tablets and laptops: grooves are milled into the aluminium housing, in which the logo elements are glued afterwards. The latter must be flush with the housing. Haptic (touch) feedback is a critical factor, as the customer would immediately feel any protruding logo or depression. Using laser line scanners, these depressions are measured to determine the planarity as well as the depth. The parts being glued are also measured to ensure a perfect fit. Other applications include welding seams,
profile and gap measurement.
Research equipment also benefits from capacitive displacement sensors, including the particle accelerator at one of the largest research facilities in the world - CERN (European Organisation for Nuclear Research). Here, a capacitive hydrostatic levelling system is used to ensure that the pipes through which the particles are sent are at the same height, even when the concrete foundations of the pillars on which the pipes are mounted change their height due to natural soil movements. High-performance capacitive sensors have outputs that are very linear, stable with temperature, and able to resolve incredibly small changes in distance, resulting in high-resolution measurements of less than 1nm.
With its high precision, measurement speed, compact size and fast data processing, noncontact measurement technology offers many benefits. The user can choose from a variety of different measurement systems. Each principle comes with its own advantages and limitations that all need to be carefully considered.
Because demanding applications can require things like higher resolution, robustness, temperature stability, linearity or special mounting and installation conditions, Bestech Australia offers Micro-Epsilon sensors for special solutions and custom designs that are adapted to the customer’s specifications. Contacttype sensors such as potentiometers, LVDTs and draw wires are also available. Factory trained application engineers with specialised product knowledge will work with you to understand your requirements and recommend the right sensors for your application.
Bestech Australia 03 9540 5100
enquiry@bestech.com.au
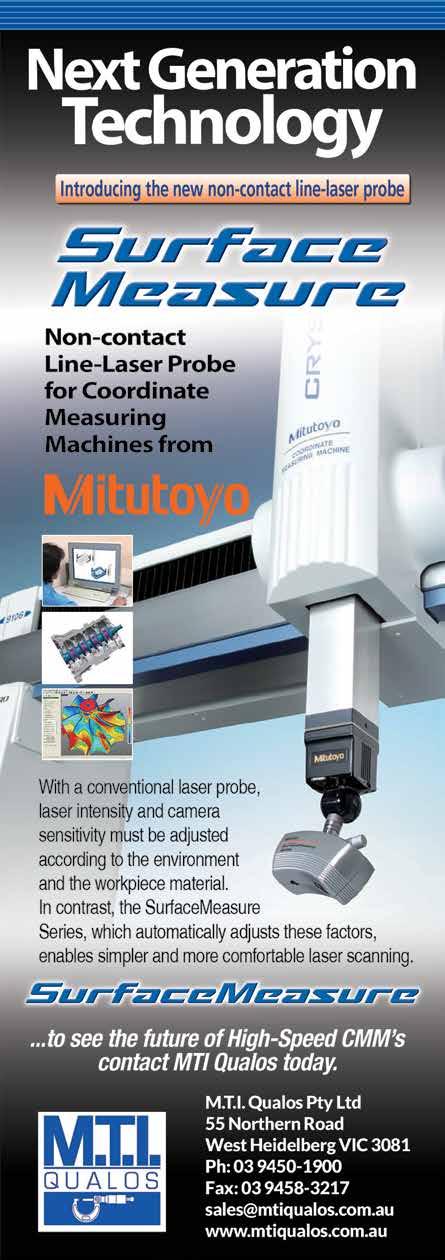
Compact high-precision laser sensor
Online faulty label inspection >
LASER TRACKERS CLAIM BREAKTHROUGH IN 3D MEASUREMENT PRODUCTIVITY
The latest generation of laser trackers from 3D measurement specialist FARO are claimed to set a new price/performance standards for large-scale metrology. The high-performance FARO Vantage family are well suited to applications in assembly alignment, part and assembly inspection, machine installation and alignment, and reverse engineering.
There are two distinct models, the VantageE with an operating range of 25m and the VantageS with an operating range of 80m. Both models are fully selfcontained, incorporating hot-swap batteries and industrialgrade Wi-Fi. This means they are easily portable both between job sites and within the factory by a single user.
The Vantage uses the all-new FARO RemoteControls system for advanced control using a mobile phone or tablet. The mobile device not only controls the movements of the laser tracker but also incorporates live video feed from targeting cameras so that a single operator can control the tracker from anywhere in the measurement area.
It also includes novel workflow management features
such as remote accuracy checks and programmable remote warm-up so the user can schedule the device to turn on in advance and make it ready for immediate operation.
FARO RemoteControls has been designed to be easy to learn and use to maximise productivity. It also includes advanced productivity enhancing functionality, such as the ability for the laser beam to be automatically re-established with a simple set of gestures, indoors or outdoors, with no need to manually reacquire the target.
Both VantageS and VantageE fully support FARO’s patented Super 6DoF TrackArm, which enables a Vantage Tracker to work with one or more FARO ScanArms, to create an integrated 3D measurement solution across a single coordinate system. Super 6DoF eliminates line-of sight challenges and greatly increases the measurement range while maintaining high accuracy.
According to FARO President and CEO Simon Raab: “The new Vantage laser tracker series provides a combination of innovation in usability along with value driven pricing that sets a new, highly accessible price/
ULTRASONIC FLAW DETECTOR
SINGLE-HANDED INSPECTION
The Olympus Epoch 6LT flaw detector is designed for challenging ultrasonic inspection applications. The compact and highly portable instrument is optimised for single-handed operation in hard-to reach locations, such as offshore oil platforms, in-service wind turbines, aviation, bridges, large-scale machinery and structural steel.
Weighing just 890g with the weight evenly distributed around the grip, the Epoch 6LT can be securely attached to a user’s leg or harness with the display rotating so users can properly view the A-scan and readings.
Simple rotary knob and button controls make it easy to navigate through the user interface, even wearing gloves.
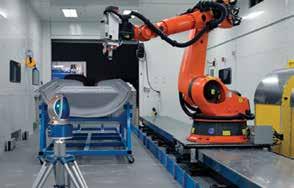
performance standard for laser trackers in large-scale precision measurement. We are confident that the breakthroughs offered in the FARO Vantage platform will make it the go-to option for a variety of demanding factory metrology applications.”
FARO Technologies 07 3029 6000 www.faro.com
EASES
Simple user software featuring a two-screen, icon based interface makes navigation quick and easy.
The ruggedly built unit is engineered to IP65/67 for dust and water resistance and drop tested to protect against the hazards found in challenging inspection applications.
Optional Wi-Fi connectivity enables ‘on the go’ backups, downloads of setups, and access to cloud applications on the Olympus Scientific Cloud. It can also be specified with optional corrosion software, thereby combining the ease of use of a thickness gauge with the flexibility of a flaw detector.

Olympus Australia 1300 132 992 www.olympusaustralia.com.au
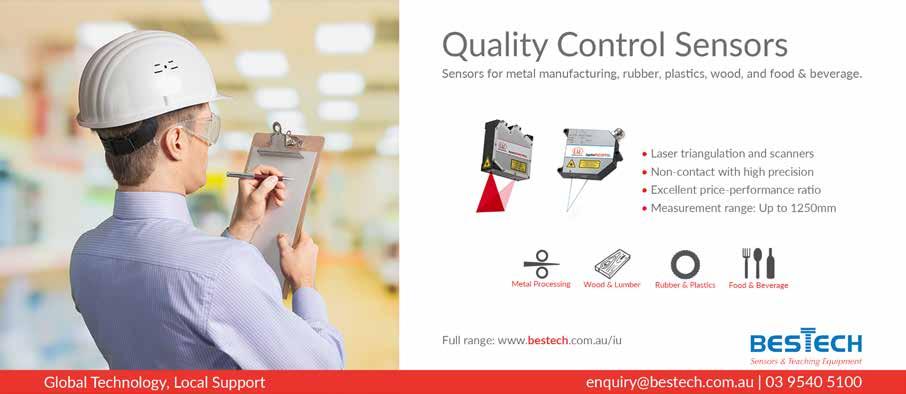
D ES IGNED TO CU T
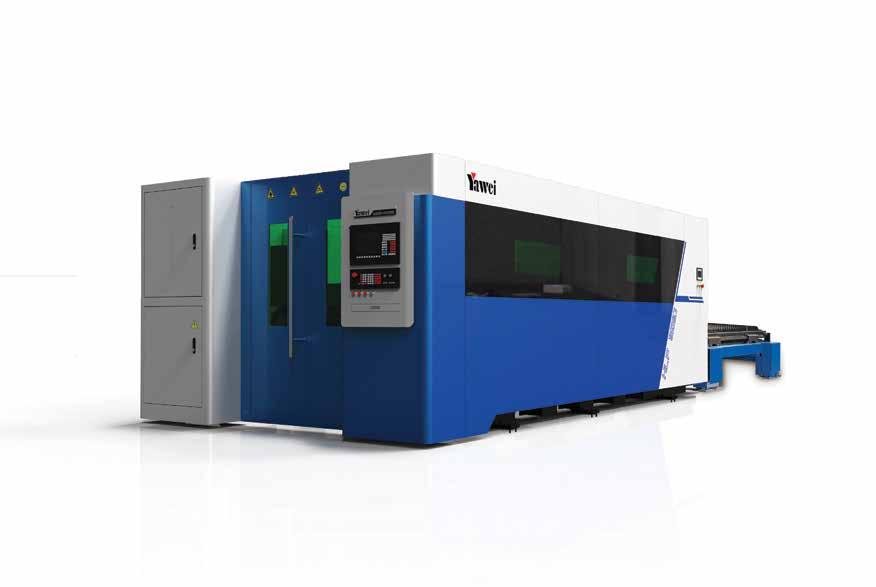
With its extreme accuracy, speed and consistency of cut, combined with very low operating costs, the new Yawei HLF fiber laser is the perfect way to take your business to the next level.
Dollar for dollar, the new HLF is in a league of its own, opening up possibilities for companies all across the laser cutting sector; from start-ups through to full production, 3-shift environments.
With a quality German built Precitec auto-focus cutting head, IPG laser source, Siemens 840DSL controller and a fabricated, stress-relieved fully annealed frame it really is a cut above the rest.



For more information:
Call: 03 9706 8066
Email: sales@appliedmachinery.com.au
Visit: www.appliedmachinery.com.au
TIME TO SWITCH TO CNC SYNCHRONISED BENDING
Daniel Fisher of Applied Machinery reckons that the transition to CNC synchronised bending has never been easier.
If you are new to the bending game, or have been running torsion bar pressbrakes for years, you might want to consider how a CNC synchronised pressbrake could be the perfect machine for your company.
Advantages
All of the hydraulic rams (Y1 and Y2 axis) are synchronised via the CNC controller to allow for absolute precise delivery of pressure for your bending job –regardless of where you are bending across the bed. Your bending performance will be equally as good at each end of your bed, as it will be for dead centre, allowing for tooling setups along the bed for more efficient processing of your multi-bend, multi-angle work.
Furthermore, because of the greater accuracy in the delivery of the bending force, the CNC machine is inherently much more power efficient than the “always 100% on” force delivery from a torsion bar pressbrake. And with skyrocketing energy costs in Australia, this can
significantly impact your bottom line.
More PBA production, lower prices for our customers
At Applied Machinery, we have been providing high-level CNC synchronised pressbrakes into the Australia market for well over 10 years in the shape of the Yawei PBH series.
And while Yawei has always produced an entry-level CNC synchronised pressbrake – the PBA Series - the economics of the machine have never really allowed us to present a competitive entry-level offering to our Australian customers - until now. The reduction in the price of steel, along with increased production at Yawei have seen the emergence of the PBA series machine as a legitimate option for companies looking to enter the market.

similar spec torsion bar machine, the difference may only be as little as 15%. However, when you take running and maintenance costs into account, the switch to the PBA could actually save you money over the payback period.
With a PBA machine, you can be sure that you are getting years of product refinement from the PBH range, passed down to its little brother.
When comparing the prices of these machines, to a
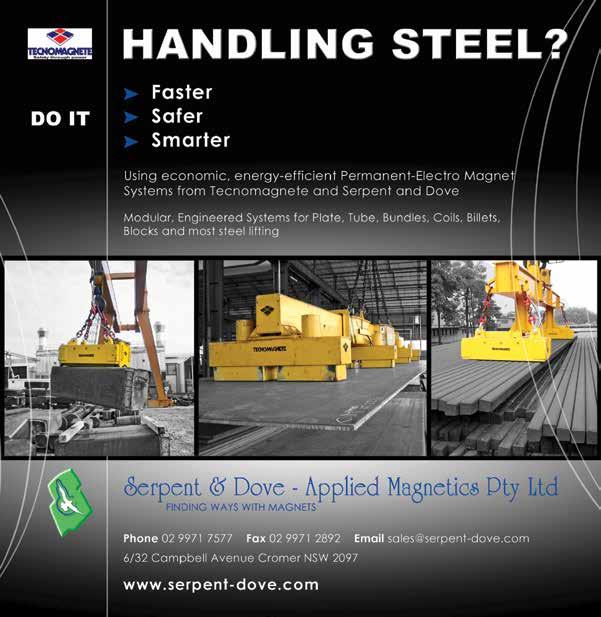
Let’s take a closer look at the Yawei PBA series CNC pressbrake from a technical standpoint.
The CNC controller is a Delem DA-52S, which is capable of CNC control of 4 axes as standard. A USB interface enables quick and easy memory stick backup of product and tool information and a 7-inch colour display gives quick visual access to the critical bending information that you require. Speedy single-page programming, tool/material/product library and hotkey navigation really make this control a fantastic option for entering the CNC market.
The machines feature CNC control of 3 axes as standard: Y1, Y2 and X (backgauge). To keep costs down, we offer this machine without the CNC R-axis as standard, but it is available as an optional upgrade. All machines featuring Hoerbiger hydraulics, Heidenhain linear scales and Voith oil pumps. Lazersafe light guards, along with Rolleri tooling really add icing to the cake and finish this machine perfectly.
What about crowning compensation?
For the vast majority of customers looking at either 2050 or 2550mm machines deflection in the main beam will barely be a consideration. However for 3100mm machines, crowning compensation is usually included with the machine as standard.
What next?
We see the PBA series of CNC pressbrakes offering customers with far more choice. A high spec torsion bar machine will be priced not too far below a PBA, and when you consider the features that you will be getting in the CNC control, in the machine build quality and componentry, along with the associated power savings, then it becomes really easy to justify the upgrade.
These machines will never replace the CNC5 and CNC7 available in the PBH series. However, they offer a legitimate entry point into CNC controlled synchronised sheet-metal bending, and we would welcome an opportunity to explain this further.
Applied Machinery
03 9706 8066
www.appliedmachinery.com.au
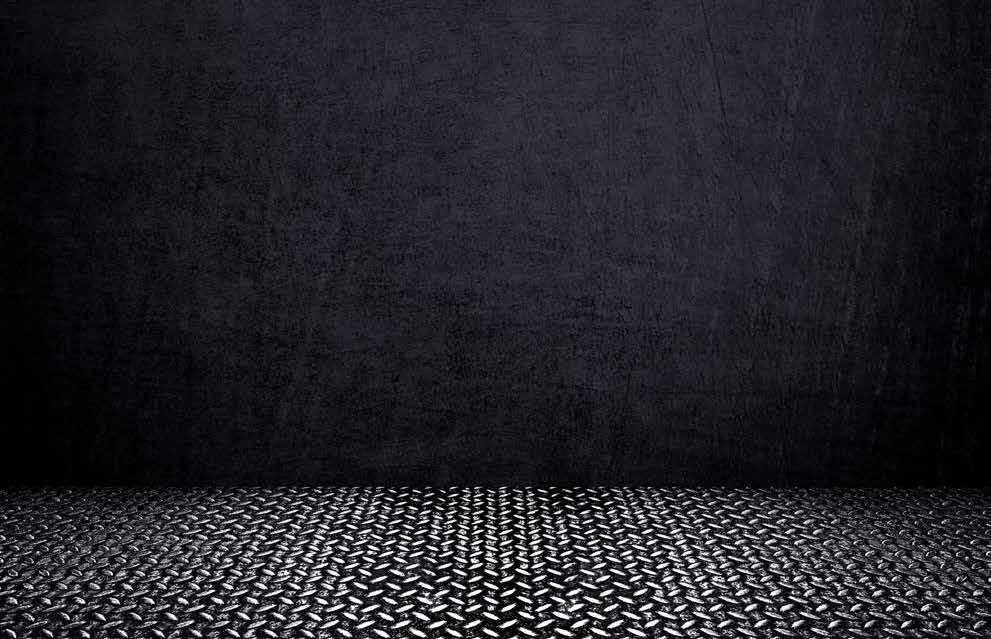
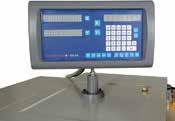
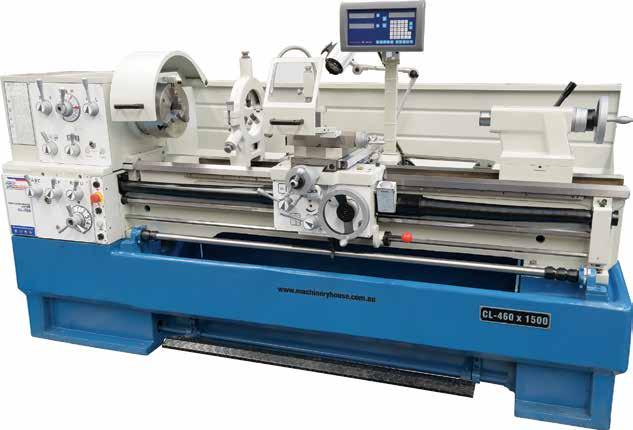
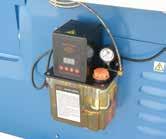

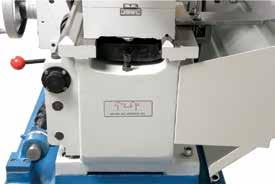

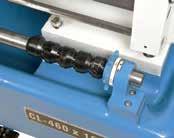
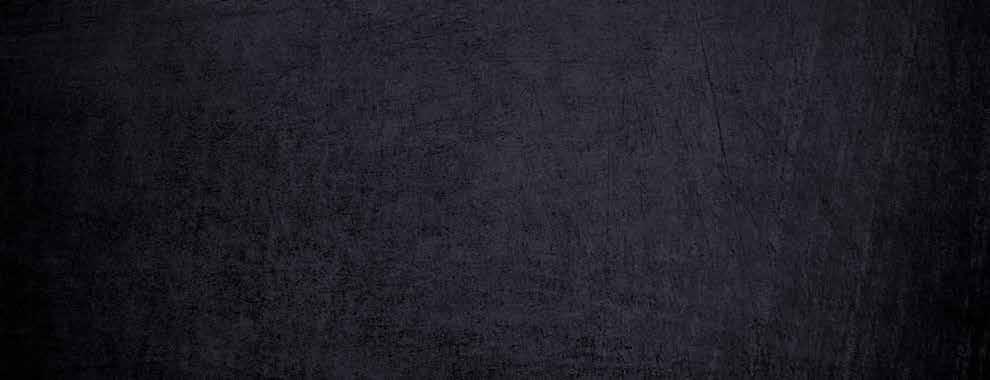
DECADE-LONG RELATIONSHIP ENABLES MACHINING EVOLUTION
If there's one thing Alsop Engineering is, it's ambitious. When Jarrod Vinen bought the business in 2008, it wasn't much more than a few manual machines and a rented space. Now, just under a decade later, it's a thriving business with CNC machines, a big workshop, separate fabrication and machining sections, and absolutely no signs of slowing down.
"[The previous owner] was winding down the business and looking to retire. So when I took over the business, I had to start building it up; there was a small client base but I needed to ramp up [production].
“I didn't even have a computer, didn't have an email address, I basically started flicking through the yellow pages and looking for people that potentially needed machining services," Vinen says.
"I had a manual lathe, and a manual milling machine and drill press, they were my three little machines."
With those machines, Vinen built a business almost from scratch. Taking jobs from those initial leads he dug up, he soon found that he needed quality CNC machinery to remain competitive. Borrowing against his Melbourne apartment he purchased a Lynx 220LC with a bar feeder from Hare & Forbes, and a decade-long business relationship was born.
"I'd done my homework," Vinen says. "We did look at other suppliers, but we'd have been paying a lot more money and when I looked at the figures it wasn't quite worth it… looking at bang for your buck it was a no brainer really."
Over the years he's had accidents and issues, but without fail Hare and Forbes have been able to help out, usually with
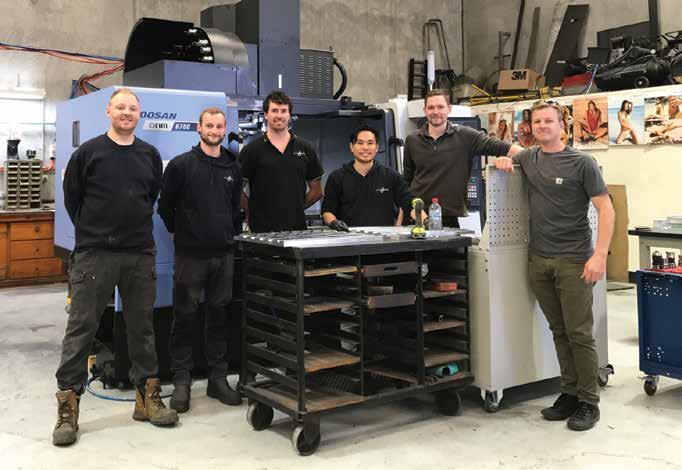
a next-day response for spare parts and machine failures.
"I have been very happy with what they've provided me with over the years. It's even little things like… very small minor problems where some companies might think "we'll get to it when we get to it because the machine's running but it's just a little warning light", but they're more proactive about that, actioning that and getting it sorted."
This quick response for repairs allows
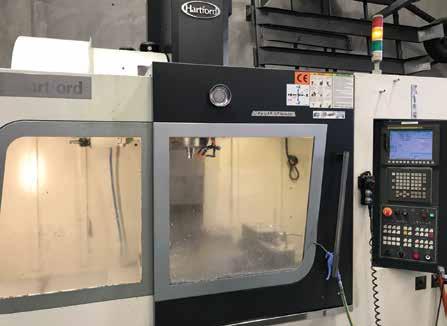
Alsop to remain flexible and provide a quick turnaround for its clients, which has been one of the leading factors doing business with local Australian companies.
Like many other service providers and goods producers, Alsop Engineering is seeing an uptick in the number of clients dissatisfied with the long wait times, inflexible payment plans, and communication difficulties that come part and parcel of ordering from overseas manufacturers. As part of an 'onshoring' trend, more and more companies are bringing their orders back to Australia and reaping the benefits of a close, local supplier (and the prestige of an Australia Made certification).
As Alsop's business prospects kept growing, and clients ordered so much work that Alsop had to outsource some of the overflow, Vinen had to take on a production manager to keep track of the business. His manager's first recommendation was to keep expanding, and get a new CNC machine.
"That was when we bit the bullet and jumped into the Doosan DNM650. And that machine really was a gamechanger," says Vinen.
"Not only does it have a lot more spindle speed, it was a lot faster and had a bigger table capacity, having the two machining centres helped us ramp up
production. Then [our clients] were very happy with what they were getting and started giving us more work."
With every new machine, and every move to a larger property, Vinen has been able to add more and more capabilities and employees to his business. What was once a one-man operation has expanded to a bustling company with ongoing contracts for 3D printer parts, clothing rack fabrication, and more.
"But we couldn't do any of that without investing in the next machine, and obviously a bigger factory space," Vinen says, outlining the constant upwards momentum of his company. He has no plans to stand still, either, and is already planning the next upgrade to his workshop.
"Moving forward our next purchase will be a Puma Y axis lathe because our current machines don’t have Y axis twin spindle facilities.."
Alsop Engineering: www.alsopengineering.com.au (02) 9521 4412
Hare & Forbes
www.machineryhouse.com.au (02) 9890 9111
The Alsop team, standing in front of their latest CNC machine: the Doosan DNM6700
The Hartford LG1000 was the second CNC machine Vinen purchased, just after he moved Alsop to a bigger facility.
MAGNETIC LIFTING HEADS FOR PALLETISATION AND DEPALLETISATION
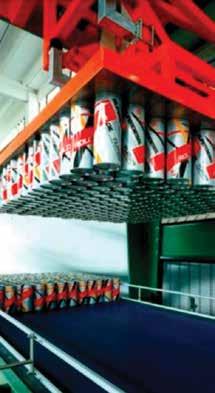
Steel cans and steel capped jars and bottles can be quickly palletised or depalletised with the use of automated magnetic lifting heads.
Magnetic equipment specialist
Serpent & Dove - Applied Magnetics has teamed up with Unimac-Gherri of Italy to offer this magnetic equipment as well Unimac’s complete range of cleaning, washing, drying, filling and capping equipment for food processors and other industries.
These magnetic palletisers/ depalletisers are capable of lifting a complete layer of cans or capped jars to or from a pallet. In cases where layers are interleaved with layer pads an integrated pneumatic pickup system can be used to handle the pads.
Serpent & Dove - Applied Magnetics 02 9971 7577 www.serpent-dove.com
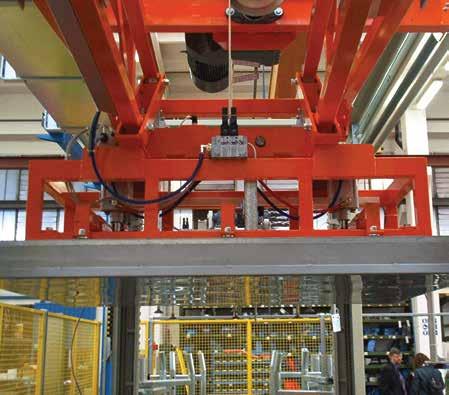
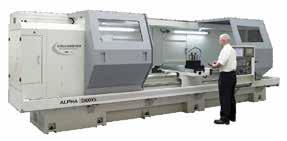
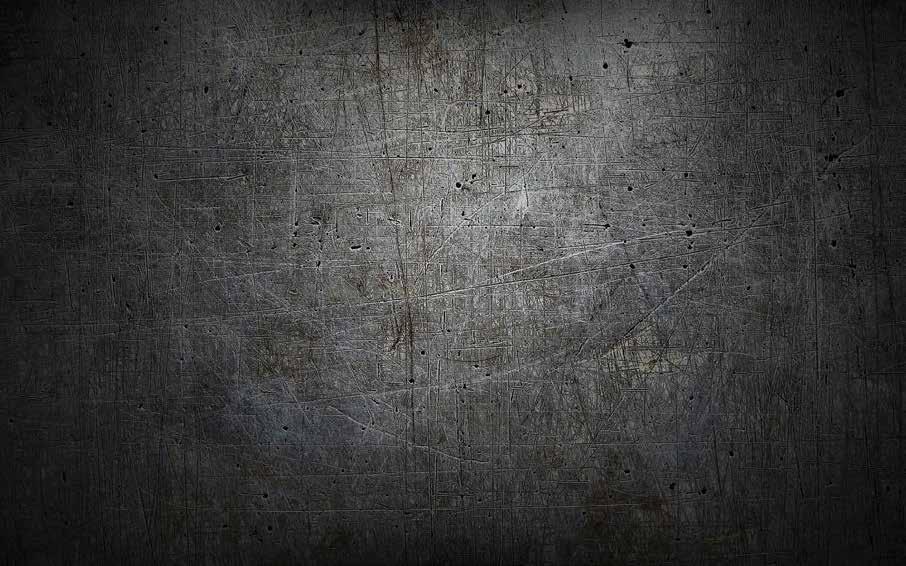
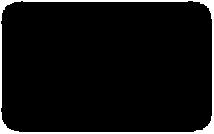
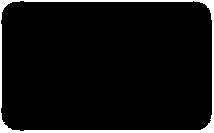
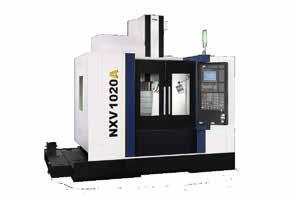
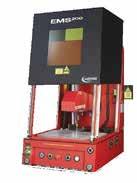

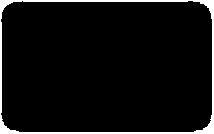
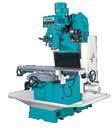
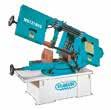
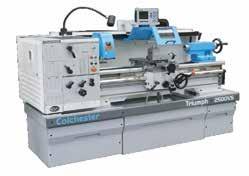
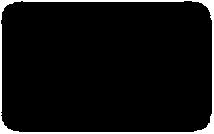




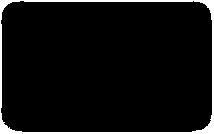
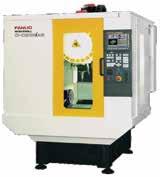
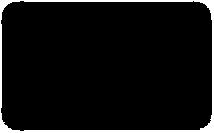




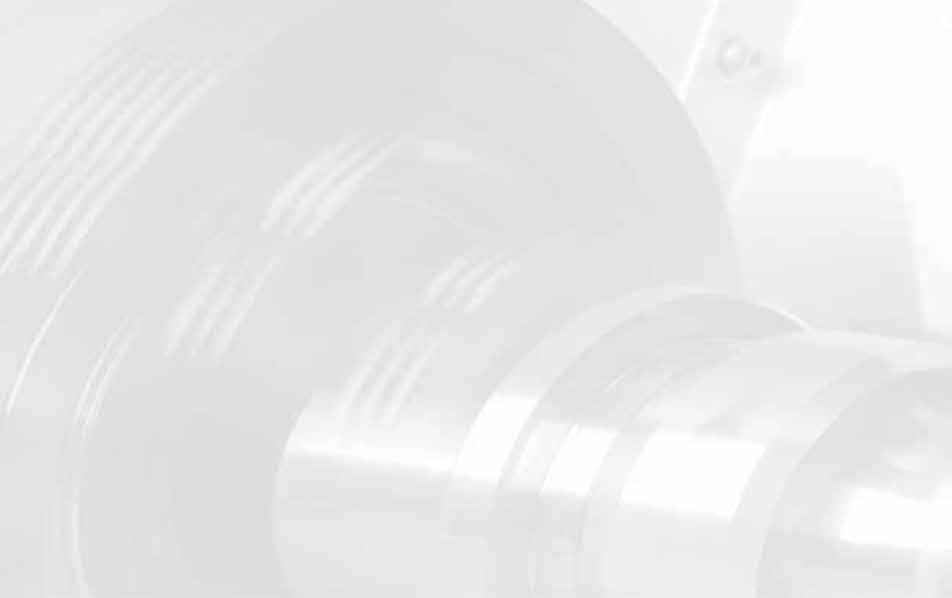
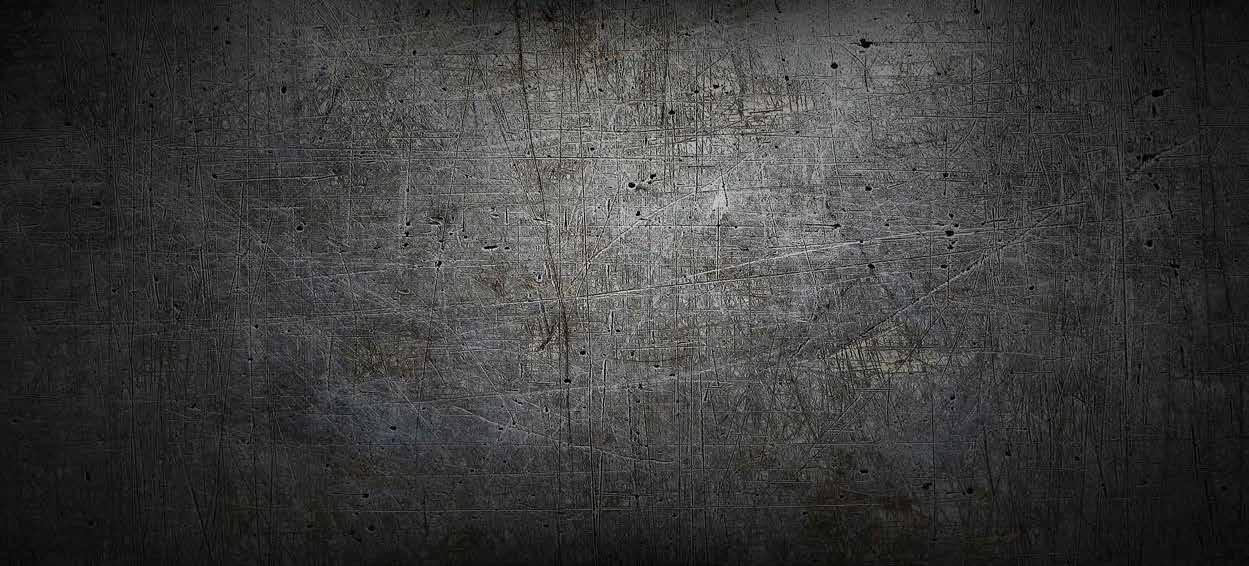
Fanuc Robodrill
Colchester & Harrison
ADDITIVE MANUFACTURING TO ACCELERATE SUPERSONIC TRAVEL
Stratasys has signed a three-year collaboration deal with Boom Supersonic that aims to help reintroduce supersonic travel to the commercial airline industry. The 3D printing and additive manufacturing specialist will help Boom accelerate the production of advanced tooling and production-grade aircraft parts using Stratasys FDM 3D printing technology.
By taking advantage of the design freedom, production speed, and cost efficiencies of additive manufacturing, Boom is planning the first flight of its XB-1 supersonic demonstrator for 2018.
Boom is using Stratasys FDM-based Fortus 450mc and F370 3D printers. Both machines are designed to produce on-demand parts using production-grade thermoplastics, as well as advanced manufacturing tools that perform even under aviation's most challenging environments.
Boom's supersonic airliner will fly 2.6
times faster than any other aircraft on the market today. Accelerating to 2335km/h, the planes could reduce typical New York to London flight times to just over three hours.
"Today's significant advances in aerodynamics, engine design, additive manufacturing, and carbon fibre composite materials are transforming the industry at all levels. Additive manufacturing helps accelerate development of a new generation of aircraft," says Blake Scholl, Founder and CEO of Boom. "With a proven trackrecord of success across aviation and aerospace, Stratasys now becomes a key catalyst in our design and production processes - helping to transform the future of aviation through the power of 3D printing."
Stratasys +852 3944 8888 www.stratasys.com
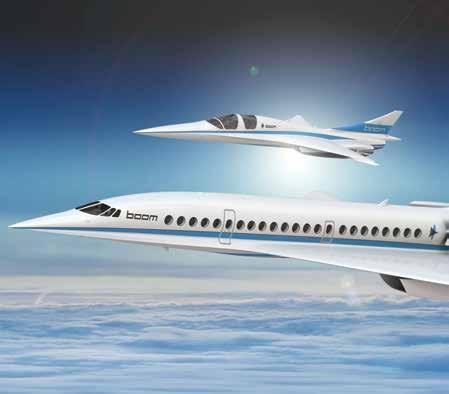

SPECIALIST HIGH SPEED DOORS
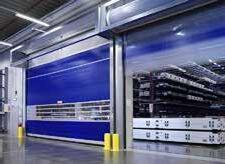
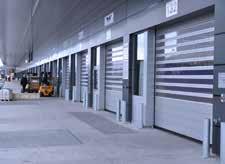


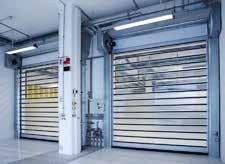
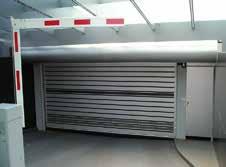


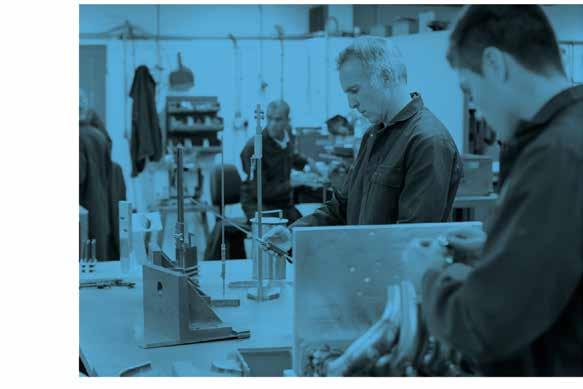
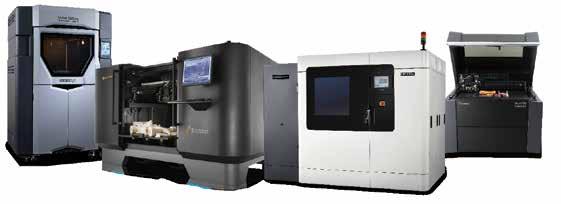
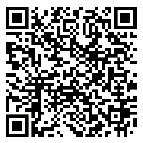
STEREOLITHOGRAPHY DRIVES F1 DEVELOPMENT RACE
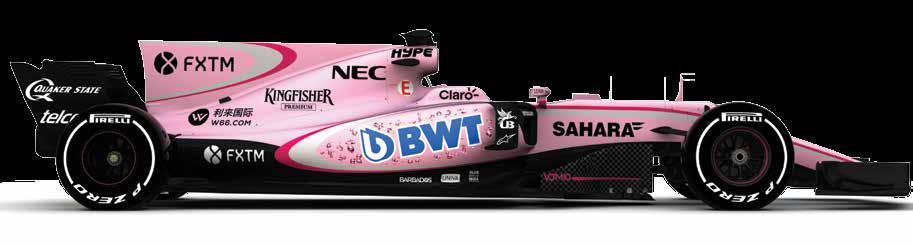

The pace of Formula One (F1) development is rivalled only by the speeds achieved on the racetrack. Each time the Sahara Force India F1 Team brings its car to a circuit, it represents the team’s top engineering; every time the team leaves, the car is just a baseline. Between races it must be reoptimised to outperform the last, best version.
“F1 is essentially a development race,” says Patrick Hawtin, Rapid Manufacturing Leader, Sahara Force India F1 Team. “Once the cars are on the track, that’s one thing, but every single week we’re trying to bring more performance to the car.”
Sahara Force India F1 is based at Silverstone and Brackley in the UK, and has relied on 3D printing as a crucial component of its development process for more than 17 years.
Particularly useful for wind tunnel testing, 3D printing has saved Sahara Force India F1 considerable time and money in the development and testing of new designs. Before 3D printing, not only was manufacturing more labour intensive, with pattern and composite shops providing tooling, carbon layering, curing, trimming and finishing, but the design process was also slower and more involved to accommodate these extra steps.
Using the previous workflow, it took 5-7 days to produce one testable design. From a development standpoint where 20 or more iterations of a design are needed for testing, these traditional methods simply were not scalable.
Sahara Force India F1 has relied on 3D printing as a crucial component of its development process for over 17 years.
“The benefits of using 3D printing in our design and development come down to cost, leadtime and quality,” says Patrick Hawtin, Rapid Manufacturing Leader, Sahara Force India F1 Team. “3D printing gives us the capacity to make hundreds of parts in a week, and when we go through the wind tunnel testing we do, there’s no way we could develop parts at the same rate without 3D printing unless we quadrupled the size of our more traditional manufacturing
departments.”
Sahara Force India F1 predominately uses 3D Systems Stereolithography (SLA) for its wind tunnel tests. Hawtin says it is not just the throughput of the 3D Systems SLA printers that make them an asset, but also the accuracy and resolution of the systems to meet their target requirements.
“3D Systems’ SLA systems deliver accuracy within a tenth of a millimetre,” Hawtin says.
Sahara Force India F1 Team’s Rapid Manufacturing Department works closely with the team’s design, aerodynamic and other manufacturing departments to devise new designs in multiple iterations.
The team’s engineers use 3D Systems’ stereolithography machines with a range of 3D Systems materials selected to meet
their application requirements, including Accura Bluestone, Accura Greystone and Accura 60. These applications include windtunnel model parts, full-size parts, moulds, cores and jigs.
“We use SLA printing for airfoil sections and downforce testing, which require extremely smooth surfaces,” says Hawtin, adding that the temperature resistance of Accura Bluestone also makes it good for carbon moulding.
“3D Systems’ SLA systems allow us to survey more and benefit from the sensitivity we can achieve with many iterations,” says Hawtin. “The amount of finesse we’re looking for would be lost if we did it any other way.”
Hawtin concludes: “The current pace of F1 development would be pretty much nonexistent without 3D printing.”
3D Systems, On Demand Manufacturing - Asia Pacific 03 9819 4422
au.3dsystems.com
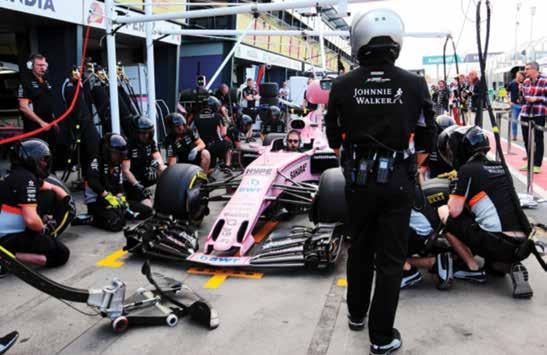
Empowering Engineers to Bring Ideas to Reality
The Tools of Modern Manufacturing
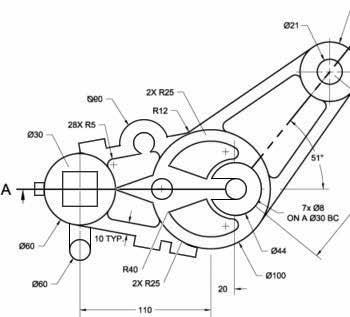
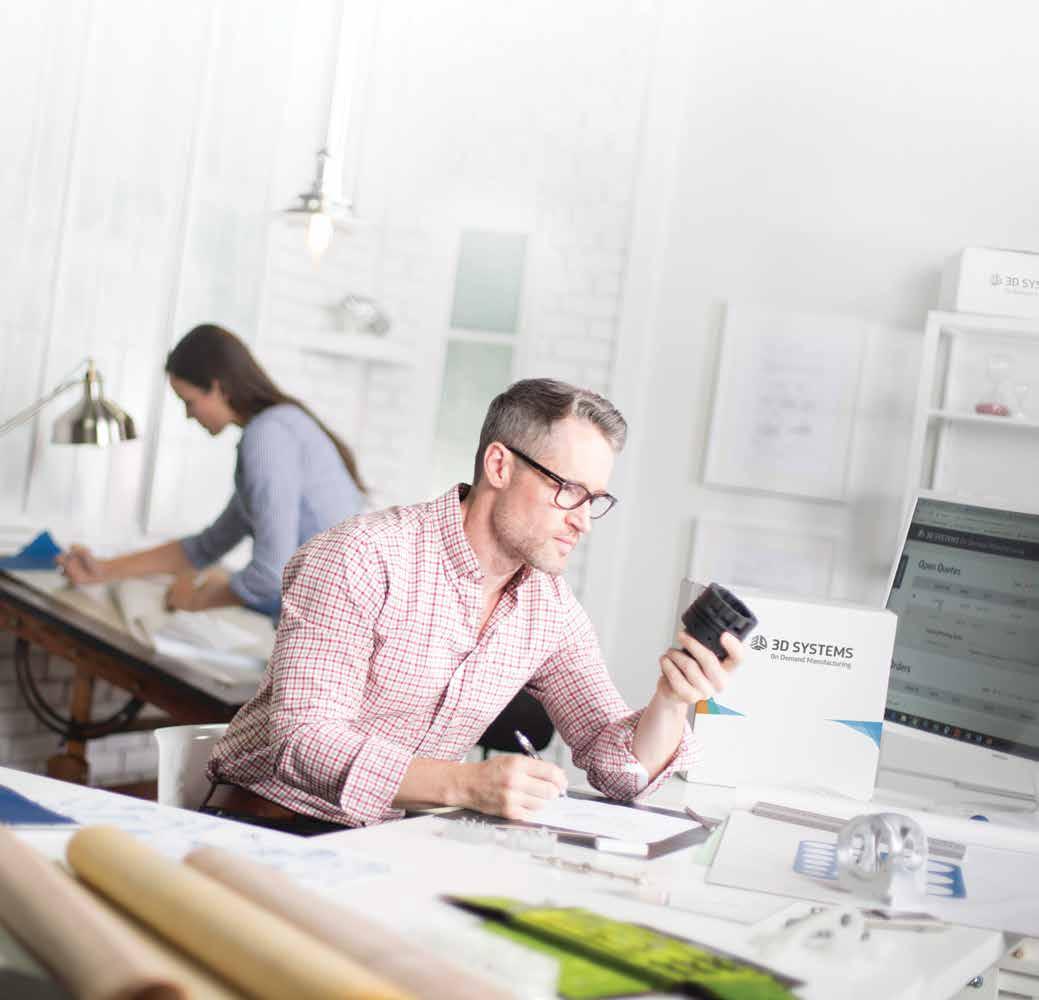
Providing designers and engineers on-demand access to the tools to bring concepts to reality. From 3D-printed prototypes to CNC machining and low-volume injection molding, we provide free online quoting, material, and technology selection. We’re the industry leader in delivering ideas. To learn more, visit au.3DSystems.com
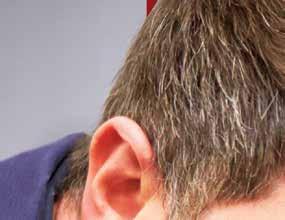

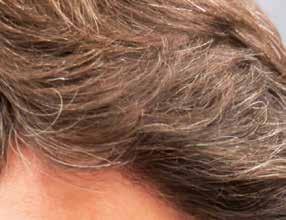
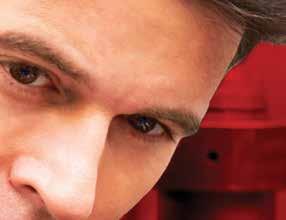
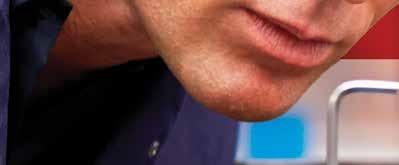
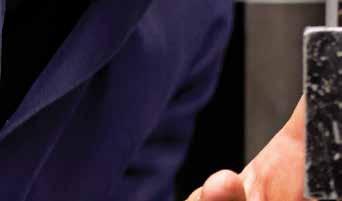
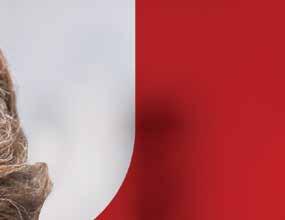
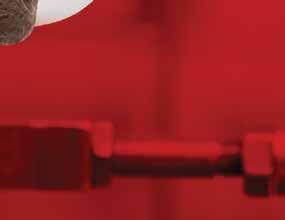
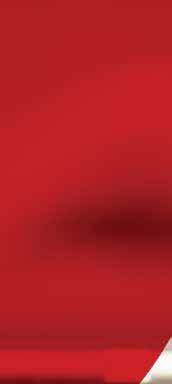
FROM IDEA TO IMPLEMENTATION, EVERY PART MATTERS.
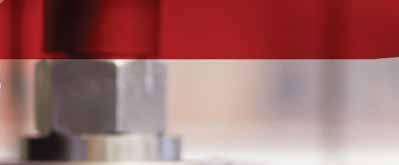
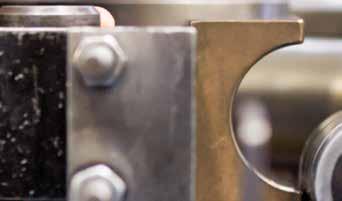
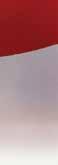
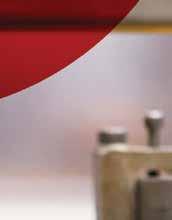
Choose quality, performance and value without compromise.
Decisions have consequences. Making the right choices can improve the efficiency and productivity of your entire organisation.
Because every decision matters, every part matters. That’s why RS Pro gives you everything that matters – quality, performance, choice and exceptional value for money.
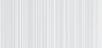
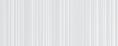
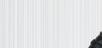



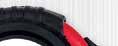
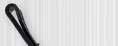
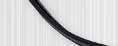

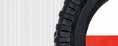
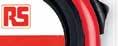
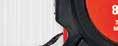
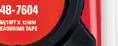
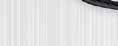
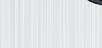

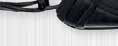
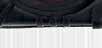

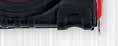
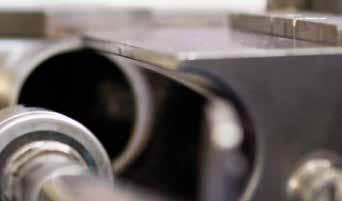
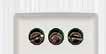
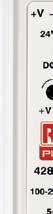
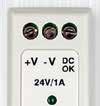
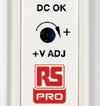
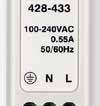
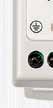

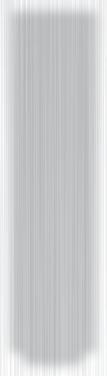
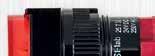
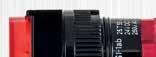

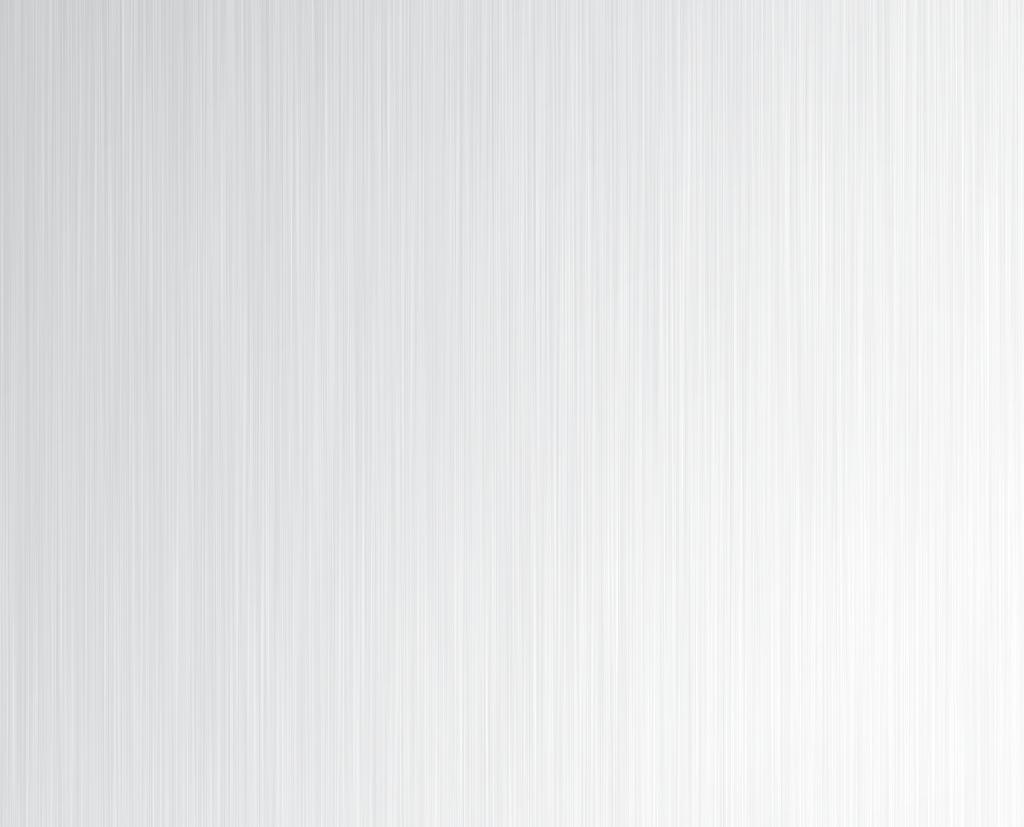

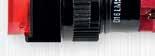
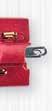
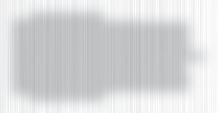
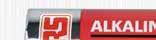



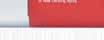


