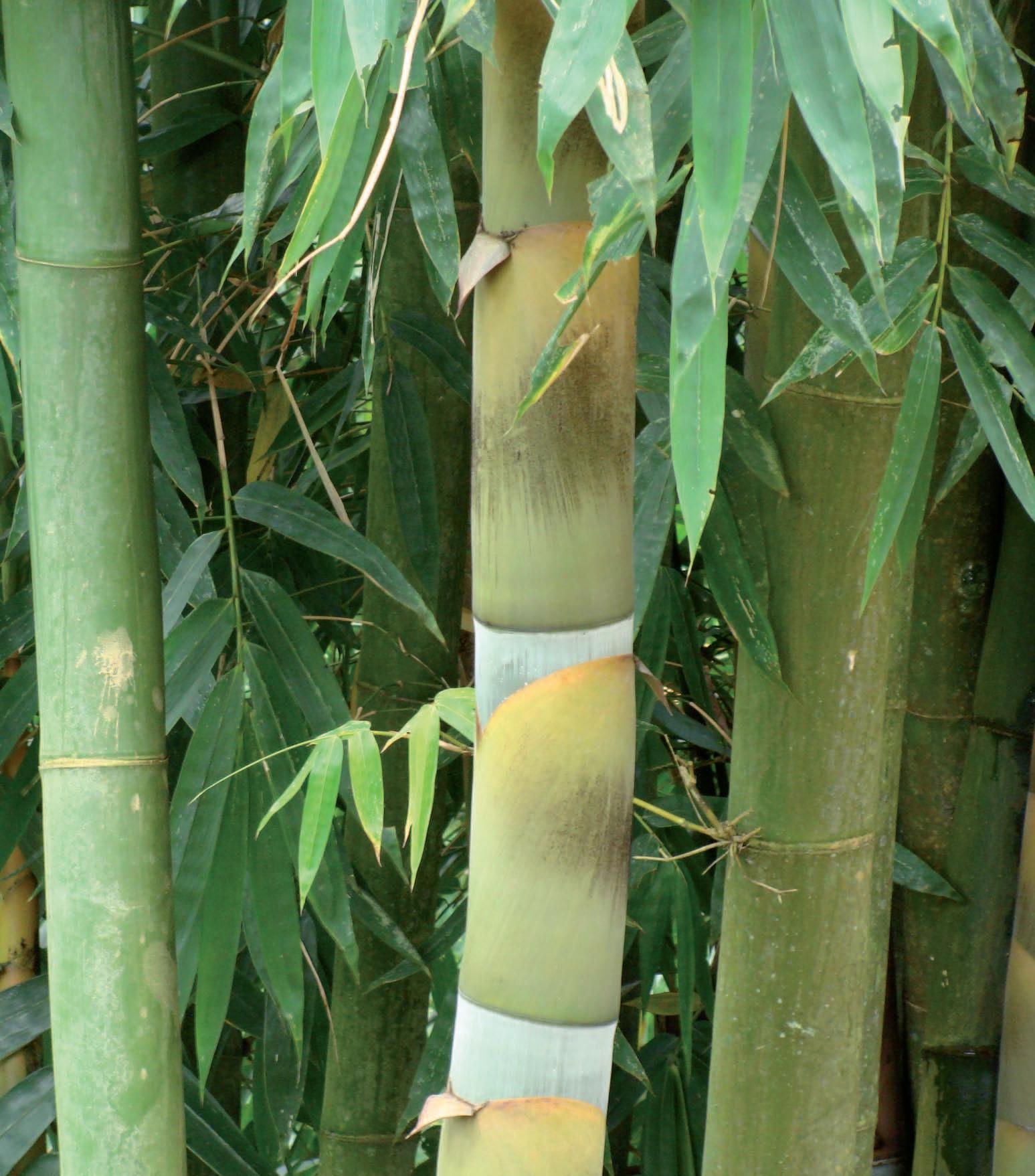
11 minute read
REPORT
Bamboo
AS A BUILDING MATERIAL
Advertisement
BY CHRISTIAN GAUSS, PH.D
First of all, what is bamboo? In a few words, bamboo is a giant woody grass of the Poaceae family (subfamily Bambusoideae), with around 1450 species found worldwide [1–3]. The bamboo forests are mainly found in the southern hemisphere, widely distributed in Asia (67%), Americas (30%) and Africa (3%), in regions with tropical, subtropical and temperate climate zones [4]. There are no native bamboos in New Zealand, but a few species with commercial value have been introduced throughout the years, including Bambusa oldhamii, Phyllostachys edulis (moso bamboo), Phyllostachys aurea, and others.
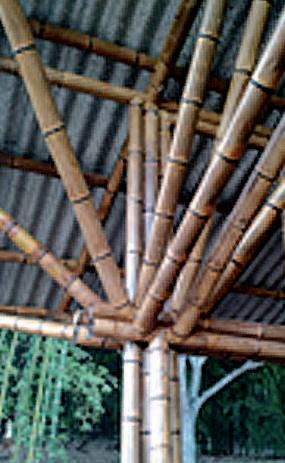
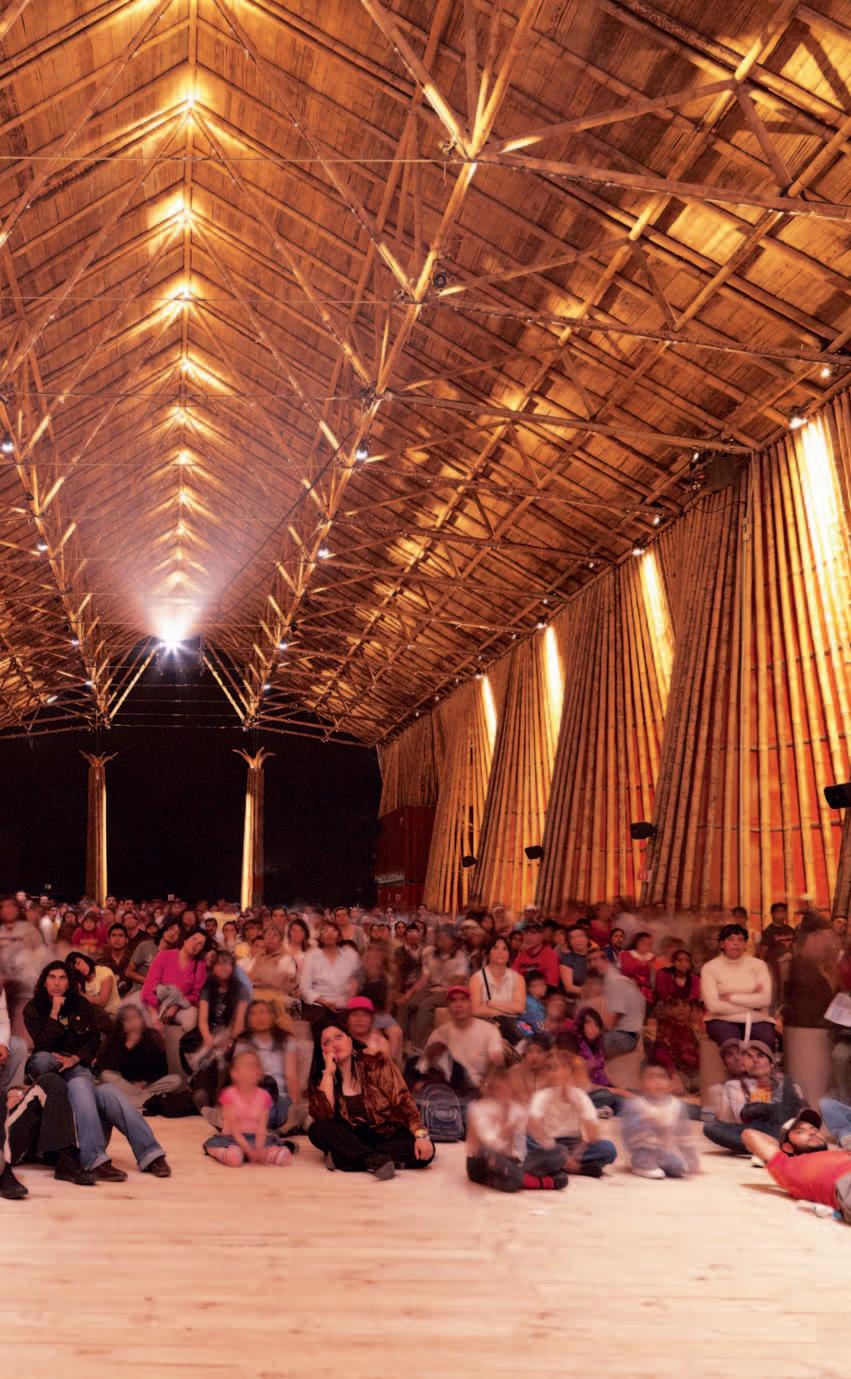
PHOTOS - EXAMPLES OF BUILDING USING BAMBOO IN ITS NATURAL FORM
THIS PAGE - TOP: Inside the Nomadic Museum in Mexico.
Photo thanks to Simón Vélez / Flickr
OPPOSITE PAGE - TOP LEFT: Bamboo road toll station in Columbia.
Photo thanks to Forgemind Archimedia / Flickr
RIGHT, TOP AND BOTTOM: Green School classroom in Bali.
Photo thanks to Forgemind Archimedia / Flickr Bamboo is an example of a naturally abundant resource that presents an enviable versatility in relation to other humanmade materials. Bamboo can be used in a wide range of applications, e.g. construction sector, composite materials, chemicals, pharmaceuticals, and food, mainly using the culms/ poles or shoots. In civil construction, the culms can be used in their natural form (Figure 1) or as engineered materials such as bamboo particleboards, bamboo scrimber, laminated bamboo lumber, plybamboo, and oriented strand board (OSB) (Figure 2) [5–10]. Additionally, in the perspective of climate change mitigation, bamboo also works as an efficient carbon sink, storing approximately 5.7 kg of CO2 per kg of dry biomass above the ground [11,12]. In its natural state, bamboo is characterised by its excellent specific mechanical strength (strength divided by density / weight) compared to traditional building materials such as steel, cement, and wood [14]. Bamboo buildings have demonstrated great seismic resistance, as observed in the maintenance of structural integrity of several houses built with bamboo in Colombia and India after the occurrence of earthquakes [15]. Bamboo can also be used for minimally processed materials, such as esterillas (Figure 3). This building component is traditionally produced in Colombia cracking the bamboo cane in the nodes and then opening it as a mat. The obtained “board” is very versatile and can be used for bahareque style walls and as structural element in roofs. It is commonly thought is that bamboo can be a steel replacement for reinforced concrete, as strips or small diameter whole-culm. Despite the excellent mechanical properties of bamboo, it has low modulus of elasticity compared to steel, which is an important property for reinforcing concrete. Therefore, for the same load-bearing structure, much more bamboo would be necessary than steel for the same reinforcing effect. Another main issue is that bamboo is a hygroscopic material, and it swells and shrinks during wet and dry cycles, which cause gaps (and potential cracks) between the bamboo element and the concrete. In the end, in terms of life cycle perspective, bamboo is not considered a proper replacement in situations where steel can be used. Archilla et al. (2018) published a comprehensive review on this topic [16]. If bamboo has to be used because of lack of alternatives, some waterproof coating with additives to improve the adhesion between bamboo and concrete should be applied. The maturity of bamboo culms is an important aspect for most parts of products and applications. Bamboo culms achieve maturity in 3-5 years and, similarly to wood, are composed mainly of 50-80% of holocellulose (cellulose + hemicellulose), 30% of pentosan and 20-28% of lignin, depending on the species and culm age [17–19]. Additionally, the lack of toxic constituents in bamboo makes it a ready food source for xylophagous organisms compromising its structural integrity and durability [20]. Without proper treatment, bamboo is decomposed and has a durability of 4 to 6 years in covered
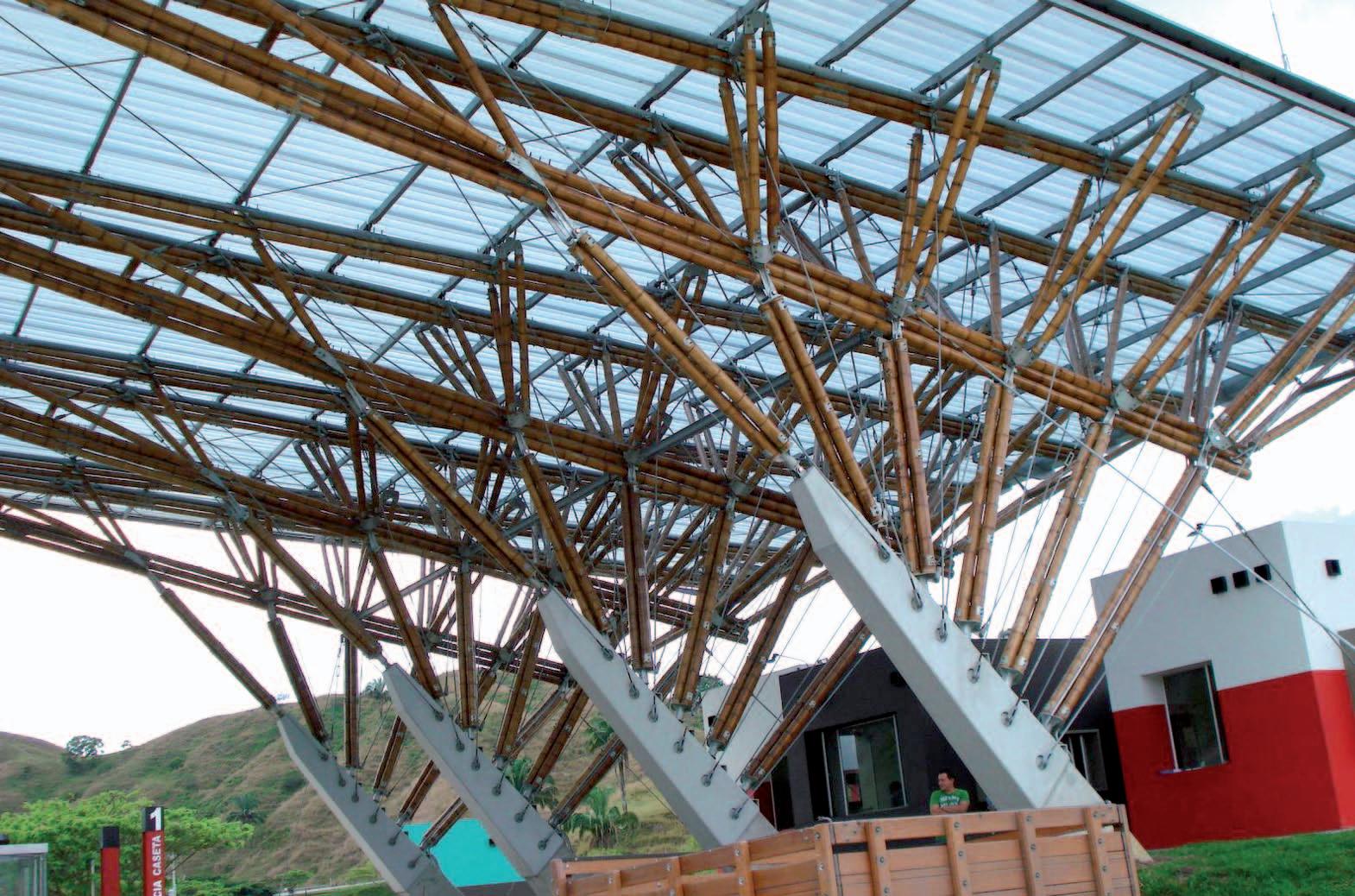
places and up to 15 years in regions with a not very humid climate. However, a decrease in mechanical strength is already observed in a short time, especially if attacked by insects. Therefore, its use is only recommended after a preservative treatment process that can guarantee long term protection. Regardless of treatment, loadcarrying (i.e. structural) bamboo should never be placed in direct contact with soil or water and should be protected, to the extent possible, from intermittent wetting (see Figure 4). In such environments, bamboo demonstrates little durability [21] Although international standards for structural design and laboratory tests are available (e.g. ISO 22156:2004, ISO 22157:2019, IS 9096:2006, IS 1902:2006, and others), testing and designing with natural materials is still challenging [23]. A summary of international bamboo standards available is given in Table 1 [24]. In general, the standards complement each other and address structural design and physicalmechanical characterisation.
Specific standards for treatment are only found in India and Colombia, although other standards describe this subject briefly. The main bamboo standard used in recent publications is the ISO 221571:2004, recently substituted by the ISO 22157:2019 for mechanical and physical characterisation and ISO 22156:2004 for structural design. From a general perspective, bamboo is a wonderful and versatile material for civil construction. There are many successful examples of how this abundant material can be used and explored in a variety of ways to create incredible and resilient structures (Green School in Bali, for example). Bamboo connects sustainability, design, and performance, which can revolutionise the built environment. Nevertheless, protocols and recommendations should be followed carefully to avoid bamboo misuse and guarantee safe and reliable structures. There are many reports, manuals, and publications on the Inbar (International Network for Bamboo and Rattan) website. Inbar is the leading international organisation working towards the development of a worldwide bamboo economy and collaboration network.
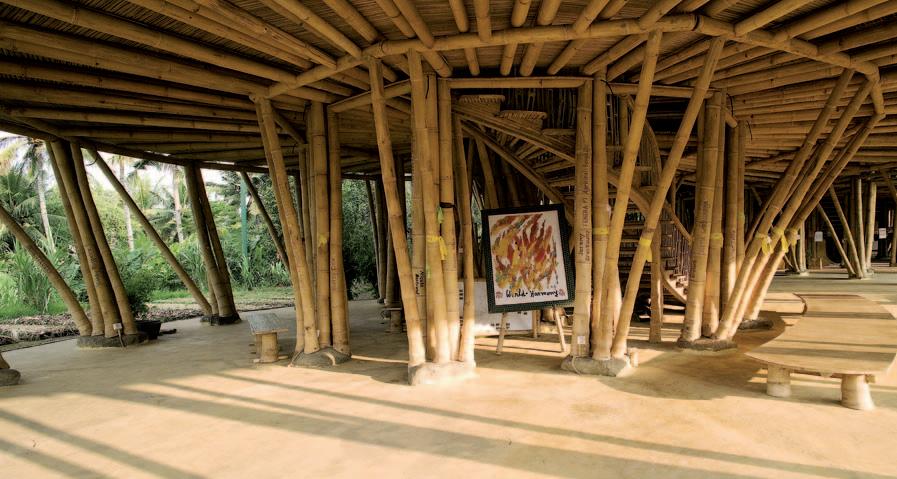
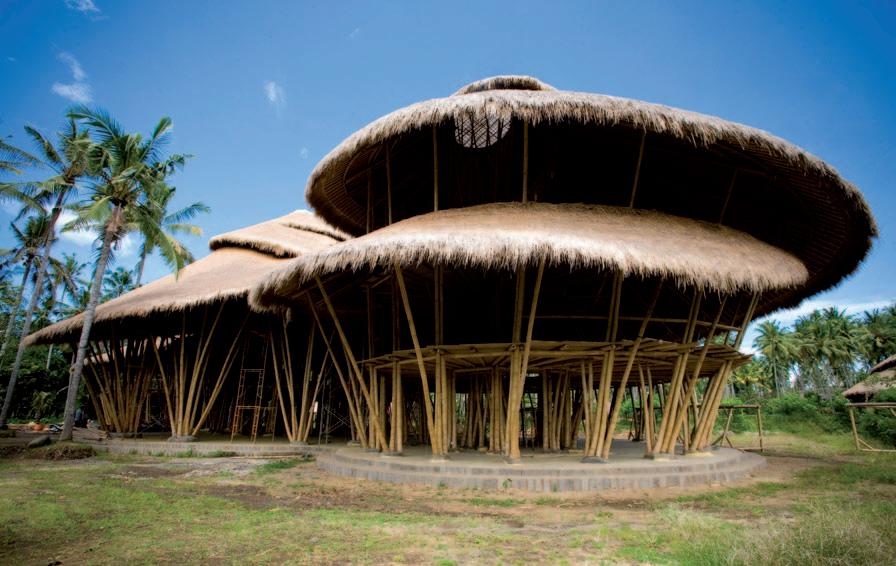
PHOTOS - (FIGURE 2.) Figure 2. Summary of bamboobased engineered materials. (a) Flattened bamboo panel, (b) Bamboo laminated lumber, (c) Plybamboo, (d) Bamboo scrimber, (e) Bamboo oriented strand board, (f) Bamboo particleboard. [13]
Reference
[1] L.G. Clark, X. Londoño, E. Ruiz-
Sanchez, Bamboo Taxonomy and
Habitat, in: W. Liese, M. Köhl (Eds.), Bamboo Plant Its Uses, 1st ed.,
Springer, 2015: pp. 1–30. doi:DOI 10.1007/978-3-319-14133-6. [2] W. Liese, The Anatomy of Bamboo Culms, Brill, Leiden, 1998. [3] Y. Goh, S.P. Yap, T.Y. Tong, Bamboo: The Emerging Renewable Material for Sustainable Construction, in: Ref.
Modul. Mater. Sci. Mater. Eng., Elsevier, 2019: pp. 1–14. doi:10.1016/b978-0-12803581-8.10748-9. [4] Z. Huang, Y. Sun, F. Musso, Assessment of bamboo application in building envelope by comparison with reference timber, Constr. Build. Mater. 156 (2017) 844–860. doi:10.1016/j. conbuildmat.2017.09.026. [5] S. SUMARDI, I.; ONO, K.; SUZUKI, Effect of board density and layer structure on the mechanical properties of bamboo oriented strandboard., J. Wood Sci. 53 (2007) 510–515. [6] M.A. Anwar, U.; Hiziroglu, S.; Hamdan,
H.; Latif, Effect of outdoor exposure on some properties of resin-treated plybamboo, Crop Prod. 33 (2011) 140–145. [7] D. Biswas, S.K. Bose, M.M. Hossain, Physical and mechanical properties of urea formaldehyde-
bonded particleboard made from bamboo waste Daisy, Int. J. Adhes. 31 (2011) 84–87. doi:10.1016/j. ijadhadh.2010.11.006. [8] M. Mahdavi1, P.L. Clouston, S.R.
Arwade, Development of Laminated
Bamboo Lumber: Review of Processing, Performance, and
Economical Considerations, J.
Mater. Civ. Eng. 23 (2011) 1036–1042. doi:10.1061/(ASCE)MT.1943-5533. [9] P. Malanit, M.C. Barbu, A. Frühwald,
Physical and mechanical properties of oriented strand lumber made from an
Asian bamboo (Dendrocalamus asper
Backer), Eur. J. Wood Wood Prod. 69 (2011) 27–36. doi:10.1007/s00107-0090394-1. [10] C. Gauss, V. De Araujo, M. Gava, J.
Cortez-Barbosa, H. Savastano Junior,
Bamboo particleboards: recent developments, Pesqui. Agropecuária
Trop. 49 (2019) 1–9. doi:10.1590/198340632019v4955081. [11] P. van der Lugt, J.G. Vogtländer,
J.H. Van Der Vegte, J.C. Brezet, Environmental Assessment of Industrial Bamboo Products - Life Cycle Assessment and Carbon
Sequestration, in: 10th World Bamboo Congr. Korea, 2015. [12] J.G. Vogtländer, N.M. van der Velden,
P. van der Lugt, Carbon sequestration in LCA, a proposal for a new approach based on the global carbon cycle;

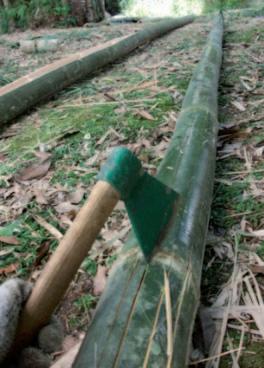

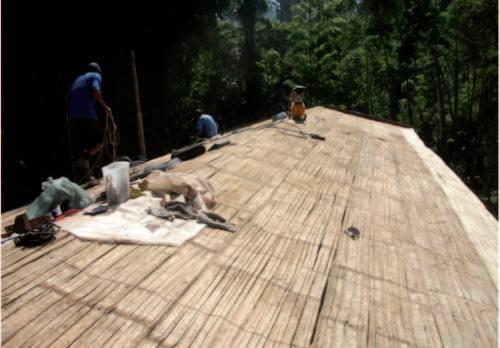

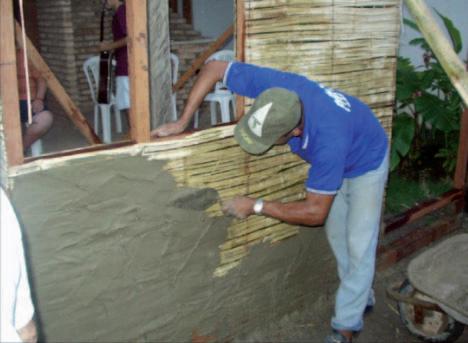
cases on wood and on bamboo, Int.
J. Life Cycle Assess. 19 (2014) 13–23. doi:10.1007/s11367-013-0629-6. [13] M. Kadivar, C. Gauss, K. Ghavami, H.
Savastano, Densification of bamboo:
State of the art, Materials (Basel). 13 (2020). doi:10.3390/ma13194346. [14] K. Ghavami, Bambu, um material alternativo na engenharia, Rev. Eng.
Construção Civil. Pesqui. Eng. 492 (1992) 23–27. [15] B. Sharma, Performance Based Design of Bamboo Structures, Univeristy of Pittsburgh, 2010. [16] H. Archila, S. Kaminski, D. Trujillo, E. Zea Escamilla, K.A. Harries, Bamboo reinforced concrete: a critical review, Mater. Struct. 51 (2018) 1–18. doi:10.1617/s11527-018-1228-6. [17] F. Nogata, H. Takahashi, Intelligent functionally graded material: Bamboo,
Compos. Eng. 5 (1995) 743–751. doi:10.1016/0961-9526(95)00037-N. [18] K. Ghavami, A.B. Marinho,
Propriedades físicas e mecânicas do colmo inteiro do bambu da espécie Guadua angustifolia, Rev.
Bras. Eng. Agrícola e Ambient. 9 (2005) 107–114. doi:10.1590/S141543662005000100016. [19] T. Tan, N. Rahbar, S.M. Allameh, S.
Kwofie, D. Dissmore, K. Ghavami,
W.O. Soboyejo, Mechanical properties of functionally graded hierarchical bamboo structures, Acta Biomater.
7 (2011) 3796–3803. doi:10.1016/j. actbio.2011.06.008. [20] S. Kumar, K. Shukla, T. Dev, P. Dobriyal,
Bamboo preservation techniques: a review, INBAR publication, 1994. [21] S. Kaminski, A. Laurence, D. Trujillo, C.
King, Structural use of bamboo. Part 2: Durability and preservation, Struct.
Eng. 94 (2016) 38–43. [22] C. Gauss, Preservative treatment and chemical modification of bamboo for structural purposes, University of São Paulo, 2020. [23] K.A. Harries, B. Sharma, M. Richard,
Structural Use of Full Culm Bamboo:
The Path to Standardization, Int. J.
Archit. Eng. Constr. 1 (2012) 66–75. doi:10.7492/IJAEC.2012.008. [24] A. Gatóo, B. Sharma, M. Bock, H.
Mulligan, M.H. Ramage, Sustainable structures: bamboo standards and building codes, Proc. ICE -Engineering
Sustain. 167 (2014) 189–196. doi:10.1680/ensu.14.00009. PHOTOS - (FIGURE 3.) Esterilla, an example of a minimally processed bamboo material that can be used in walls and roofs.
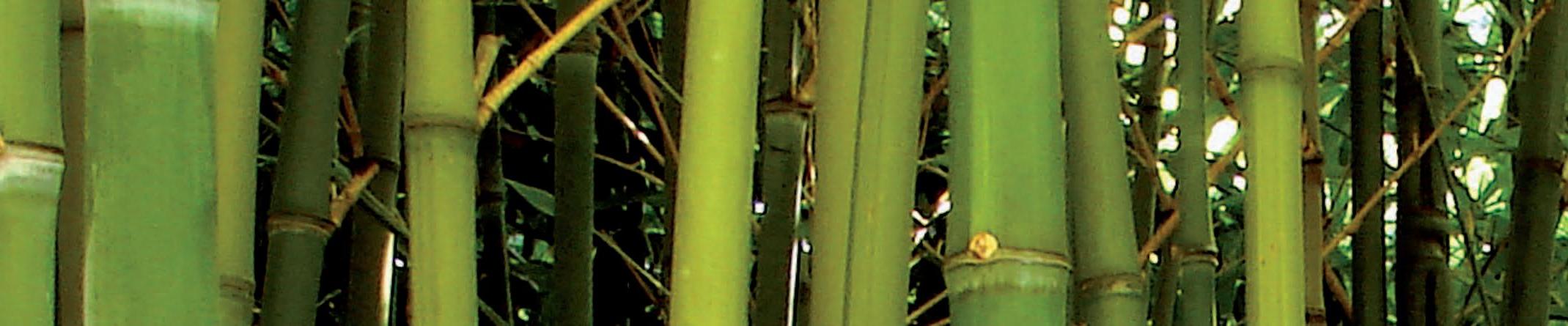
I Table 1 – Present international Standards for bamboo use.
COUNTRY CODE
China -
Colombia Reglamento Colombiano de Construcción Sismoresistente – chapter G12 Estructuras de Guadua (Guadua structures)
Ecuador Norma Ecuatoriana de la Construcción – Estructuras de Guadúa (Guadua structures)
India National Building Code of India, section 3 Timber and bamboo: 3B
Peru
Reglamento Nacional de Edificaciones, Section III International -
STANDARD
JG/T 199:2007 - Testing method for physical and mechanical properties of bamboo used in building NTC 5407:2006 - Uniones de Estructuras con Guadua angustifolia Kunth (Structural unions with Guadua angustifolia Kunth) NTC 5525:2007 - Métodos de Ensayo para Determinar las Propiedades Físicas y Mecánicas de la Guadua angustifolia Kunth (Methods and tests to determine the physical and mechanical properties of Guadua angustifolia Kunth) NTC 5301:2007 - Preservación y secado del culmo de Guadua angustifolia Kunth (Preservation and drying of Guadua angustifolia Kunth culm) NEC-SE-GUADÚA:2017 – Estructuras de Guadúa (GaK) (Guadua structures)
IS 6874:2008 - Method of tests for bamboo IS 15912:2012 - Structural design using bamboo – code of practice IS 1902:2006 - Preservation of bamboo and cane for non-structural proposes - code of practice IS 9096:2006 - Preservation of bamboo and cane for structural proposes - code of practice E100:2012 – Diseño y Construcción con Bambú (Design and Building with Bamboo) ISO 22156:2004 - Bamboo – structural design ISO 22157:2019 - Bamboo – determination of physical and mechanical properties. Substitutes the former ISO 22157:2004 parts 1 and 2. Source: Adapted from [24].

PHOTOS - (FIGURE 3.) Protection by design is one of the most important tools for long-lasting bamboo structures.
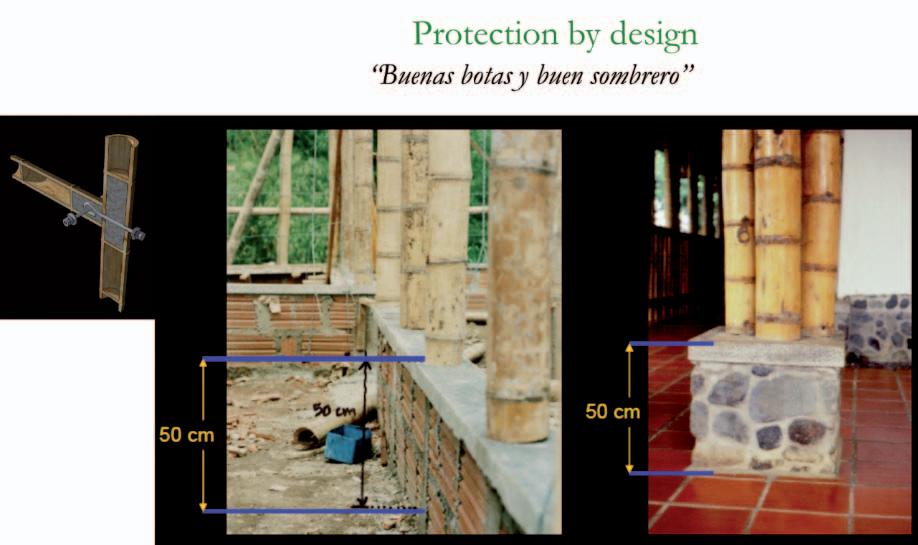
AUTHOR BIO Christian is a postdoc researcher at the University of Waikato, Hamilton. Before coming to New Zealand, he obtained his Bachelor (Eng), Master, and Doctorate degrees in Materials Science and Engineering at the University of São Paulo, Brazil. He has been working with bamboo for the last 6 years, mainly for the development of bamboo as a structural material and assessing its potential in products with high added value. His doctorate thesis was focused on the treatment and chemical modification of bamboo (mainly Dendrocalamus asper). He has authored and co-authored around 12 scientific publications about bamboo. He is a founding member and ex-secretary of the Brazilian Association of Bamboo (BambuBR), a non-profit organisation with more 40 active members (www.bambubr.com). He is organising and planning a project proposal for possible funding to start bamboo related research in New Zealand. As always, collaborations are welcome. Research gate: https://www.researchgate.net/profile/Christian_Gauss Google Scholar: https://scholar.google.com/citations?hl=en&user=sj5g5zAAAAAJ