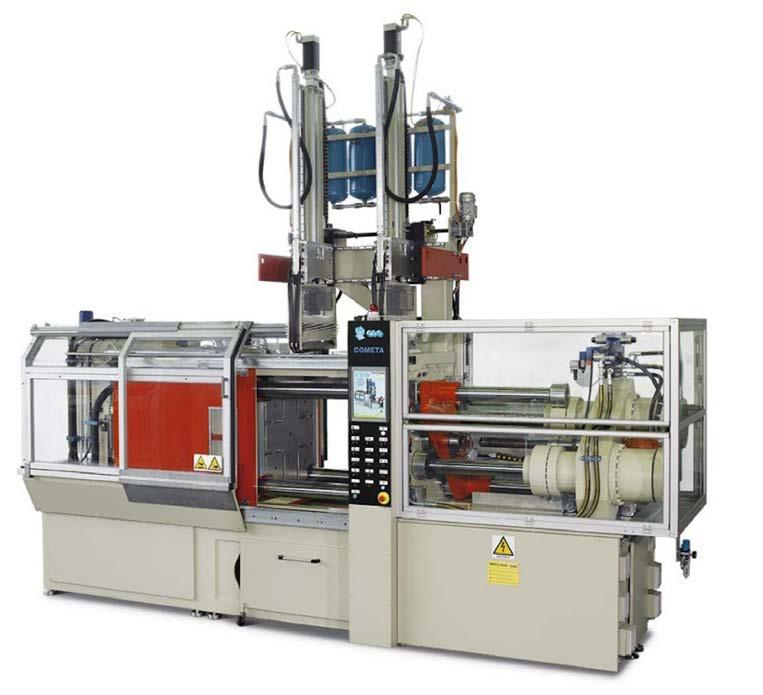
7 minute read
VUOTO INTEGRALE PER UNO STAMPAGGIO DI ALTA QUALITÀ
Nata nel 1971 e con una lunga esperienza nello sviluppo di macchinari per l’industria calzaturiera, CDG si è avvicinata al mondo degli elastomeri nel 1997 con lo sviluppo di una pressa a compressione. È passata poi alle macchine a iniezione sulle quali adotta la tecnologia del vuoto con campana integrale, estesa a tutta la superficie dello stampo, cornici comprese, e non solo alla zona della stampata. Una soluzione che presenta numerosi vantaggi in termini di qualità, riduzione di tempi e di qualità dell’ambiente di lavoro
La capacità di innovare delle piccole e medie aziende del manifatturiero italiano è proverbiale, legata all’indubbia creatività e inventiva di tanti nostri imprenditori e alla preparazione dei nostri tecnici in fatto di progettazione meccanica. Un esempio che conferma questa propensione anche per il settore della trasformazione della gomma arriva da CDG, un’azienda di Carrè, in provincia di Vicenza, nota soprattutto per i suoi macchinari per l’industria delle calzature, ma che ha anche sviluppato una linea di presse per la gomma dotata di una particolare tecnologia del vuoto.
CINQUANT’ANNI DI ESPERIENZA Ci siamo fatti spiegare di che cosa si tratta da Mauro Feracin, responsabile della progettazione dell’azienda che ci ha parlato delle particolarità di questa soluzione e di come CDG l’abbia sviluppata. «Siamo nati nel 1971 come Electromodul, marchio tuttora esistente e di nostra proprietà, per il quale forniamo assistenza tecnica. Nel tempo ci siamo costruiti un nome ben conosciuto nel settore delle calzature, per il quale produciamo, tra l’altro presse per suole in termoplastici e in gomma. La conoscenza degli elastomeri ci ha spinto, a partire dal 1997, a concepire una presLa pressa orizzontale Cometa IF/V di CDG. Si distingue per l’ingombro contenuto e la camera a vuoto integrale di serie. Base, testata pressa e piano mobile sono stati progettati seguendo concetti originali e procedimenti elettronici per offrire la massima rigidezza sotto carico e utilizzare al meglio la superficie degli stampi.
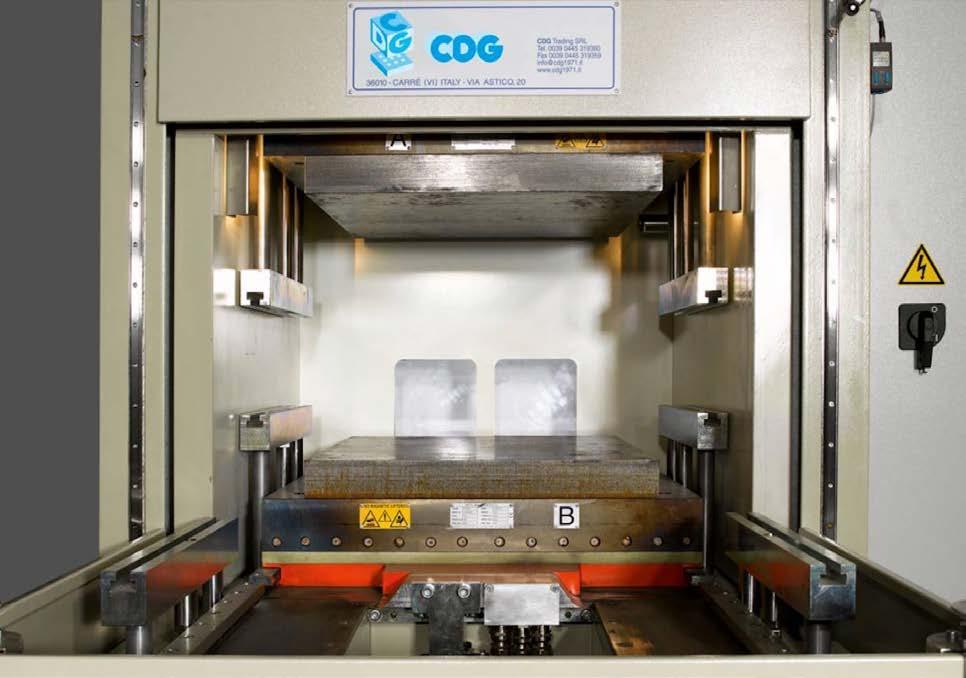
Un particolare della pressa verticale Cometa IV/V di CDG, con camera a vuoto integrale. Si notano in particolare testata pressa e piano mobile, progettato per avere la massima planarità e parallelismo dei piani portastampo.
sa a compressione verticale per la gomma con campana a vuoto a cui è seguita, intorno al 1999, una nuova pressa a iniezione orizzontale, in cui la tecnologia della campana a vuoto è applicata integralmente su tutta la superficie del piano di chiusura».
LA TECNOLOGIA DEL VUOTO INTEGRALE La tecnologia del vuoto comporta molti vantaggi nello stampaggio, ed è adottata in molte presse limitatamente all’area della stampata. La soluzione adottata da CDG, però, fin dall’inizio ha scelto un’altra strada, quella cioè di applicare il vuoto a tutta l’area dello stampo, comprese cornici ed estrattori, centrali o laterali. Con una serie di vantaggi, che lo stesso Feracin ci illustra. «Innanzi tutto la nostra tecnologia è molto semplice e consente di eliminare progressivamente l’aria nella zona di stampaggio anche con lo stampo aperto, ottenendo quindi un vuoto reale e non quello approssimativo che caratterizza le soluzioni basate sull’impiego di guarnizioni. La nostra campana a vuoto agisce anche su cornici e piani intermedi e questo consente di avere effetti positivi sul risultato finale, perché in assenza d’aria si abbreviano i tempi di vulcanizzazione e si riducono drasticamente gli scarti, con vantaggi tangibili soprattutto quando si impiegano mescole costose o per articoli complessi. Inoltre si riducono i degasaggi, e quindi si abbreviano i tempi ciclo, e si aspirano meglio i fumi di processo, contribuendo a rendere migliore l’ambiente di lavoro». Un altro vantaggio di questa soluzione è che si può utilizzare anche con stampi a più piastre senza la necessità di adattamenti, semplificando enormemente il lavoro dell’attrezzista, con ulteriori risparmi di tempo.
MIGLIORAMENTO DEL PROCESSO Lo stampaggio con camera a vuoto integrale, spiegano in CDG, «non si limita solo a evitare i difetti di produzione dovuti alla permanenza dell’aria negli stampi, ma migliora e rivoluziona in maniera positiva tutto il procedimento di stampaggio, ricreando tra l’altro un rapporto decisamente migliore tra uomo e macchina a tutto vantaggio della produttività. Questo succede perché proponiamo non semplicemente una camera a vuoto, ma un vero e proprio sistema dove pressa e campana sono state progettate, integrate e finalizzate a produ-
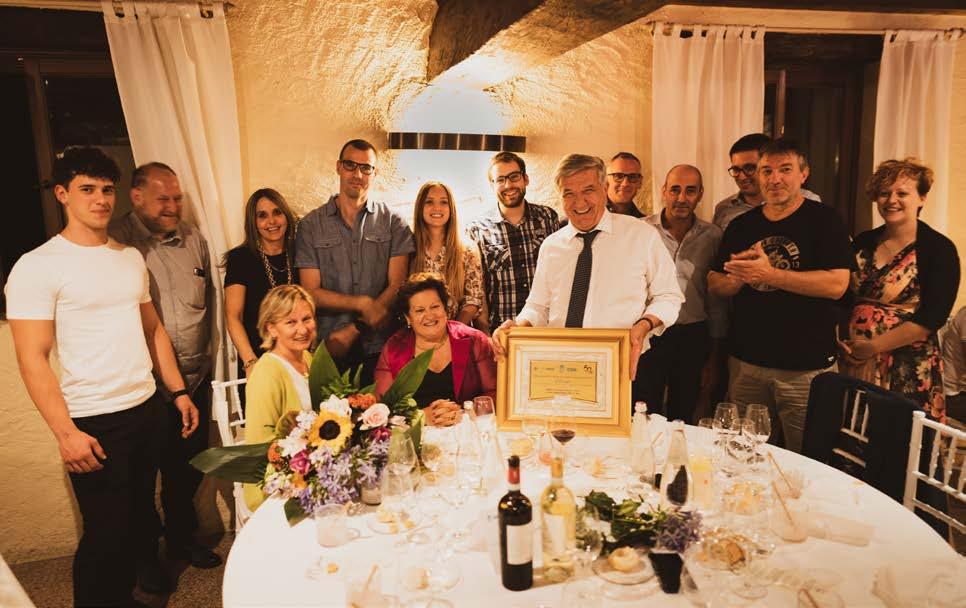
Un momento della festa con cui CDG ha celebrato i 50 anni di attività. Al centro, attorniato dallo staff, il fondatore dell’azienda, Corrado Dalla Guarda.
zioni di qualità e alla massima produttività».
UNA GAMMA AMPIA Le presse dell’azienda vicentina hanno adottato fin dall’inizio la campana a vuoto integrale. Hanno subito però nel tempo una notevole evoluzione concettuale. «All’inizio», dice Feracin, «le nostre macchine avevano una struttura a colonne. Intorno al 2010 abbiamo cominciato a progettarle con una struttura a spalle fisse, anche in questo caso con tutta una serie di vantaggi, in particolare legati a una maggiore rigidità, che si traduce in maggiore precisione della stampata e alla riduzione dell’ingombro e alla possibilità di realizzare presse di tonnellaggio inferiore. Oggi produciamo presse a compressione verticali e a iniezione orizzontali e verticali, in una gamma che spazia dalle 150 alle 1.200 tonnellate di forza di chiusura. Di recente abbiamo introdotto anche una pressa orizzontale da 80 tonnellate che utilizza una tipologia costruttiva che avevamo temporaneamente smesso di utilizzare e che abbiamo rivisto per applicarla su un basso tonnellaggio». In sostanza questa macchina, a iniezione FIFO e campana del vuoto, utilizza quattro cilindri per attuare la chiusura dello stampo in modo molto preciso. La testata pressa ha una particolare geometria high-tech.
SU MISURA E COMPATIBILI 4.0 Nella produzione delle sue macchine CDG prevede una configurazione di base, che poi può essere integrata con accessori come piani caldi, piani magnetici, estrattori, carrelli, e altro. Il cliente può così scegliere la soluzione che più si confà alle sue necessità. Si tratta di macchine connesse, compatibili con le tecnologie digitali e che quindi possono essere acquisite con gli incentivi del piano Transizione 4.0. «Già da parecchi anni le nostre macchine possono essere controllate con assistenza da remoto ed è stato quindi molto semplice per noi aggiornarle ai requisiti 4.0».
FACILI DA INSTALLARE E PROGRAMMARE Anche se la maggior parte delle vendite riguarda il settore delle calzature, negli anni CDG si è creata un buon numero di clienti e di estimatori che operano nel settore gomma, concentrati nel distretto del Sebino ma anche in altri comprensori, come quello del Trevigiano, dove operano aziende manifatturiere che hanno la necessità di produrre componenti in gomma di alta qualità. Le presse prodotte dall’azienda vicentina sono anche molto semplici come concezione. «Sono macchine plug & play, che una volta collegate all’alimentazione di rete sono praticamente pronte per funzionare. Durante il periodo più difficile del Covid-19, in cui non potevamo nemmeno uscire per effettuare il collaudo sul posto, un nostro cliente ha potuto perfino installare alcune nostre macchine in totale autonomia. An-
che dal punto di vista di programmazione e di interfaccia utente cerchiamo di fornire soluzioni semplici e user friendly, che anche dopo un brevissimo training sono utilizzabili in autonomia».
RICORRENZA DA FESTEGGIARE L’azienda ha festeggiato quest’anno i suoi 50 anni di attività, celebrando anche una festa in azienda. La ricorrenza coincide anche con un momento delicato e importante, il passaggio generazionale tra colui che fondò l’azienda nel 1971, Corrado Dalla Guarda, e suo figlio Marco, l’attuale amministratore delegato. Corrado è colui che partendo da Electromodul, ha costruito l’esperienza dell’azienda nello sviluppo, produzione e commercializzazione di macchinari, inizialmente per il settore delle calzature, per cui CDG realizza un’ampia gamma di presse per suole in termoplastici e per gomma. Da questo know-how sono poi nate anche le macchine per lo stampaggio di articoli tecnici in elastomero. Marco Dalla Guarda oggi prosegue il suo lavoro, con particolare attenzione a coordinare e ottimizzare tutte le attività amministrative, logistiche e operative dell’azienda, per renderle ancora più efficaci e funzionali alle richieste dei clienti e agli obiettivi aziendali. u
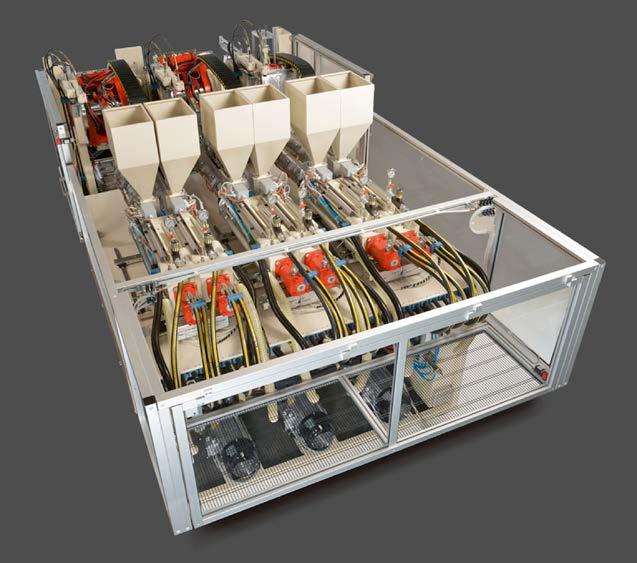
CDG è nota anche per le sue macchine per l’industria delle calzature. Nella foto la pressa Beta, per suole in elastomeri termoplastici. Può essere prodotta in tre versioni, a 2, 3 o 4 stazioni.
IMCD Italia distribuisce LANXESS Urethane Systems
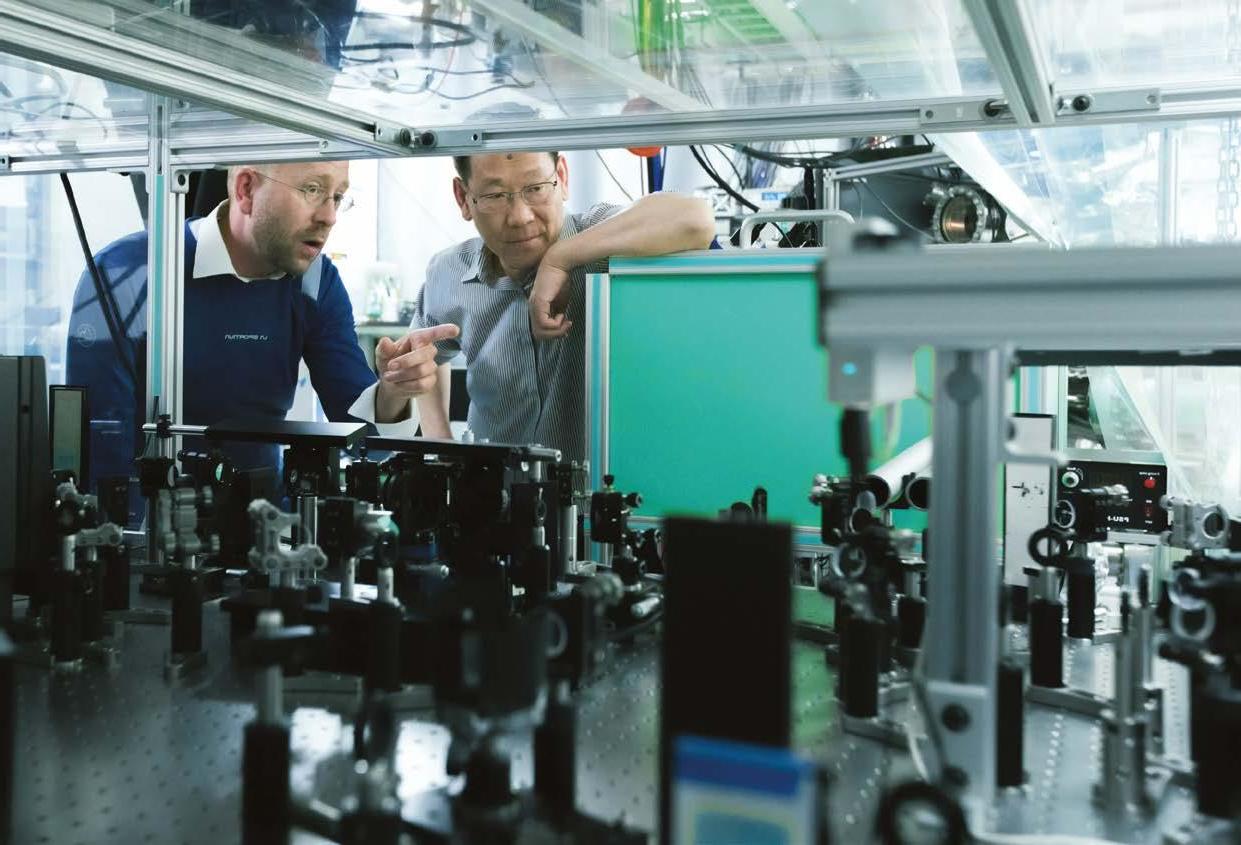
I sistemi Poliuretanici delle linee Adiprene® LF Vibrathane® Adiprene® Vibracure® Duracure® Vibracat ® Ultralast® coprono un’ampia gamma di applicazioni: • gomma e pneumatici • attività estrattiva di petrolio e gas • carta e stampa industriale Progettiamo soluzioni innovative con i nostri partner per accompagnarvi nella realizzazione delle vostre migliori creazioni.
Contattaci per scoprire le nostre proposte formulative! IMCD Italia Spa
T +39 02 557091 E info@imcd.it