Mirror a year in REview WINTER 2022
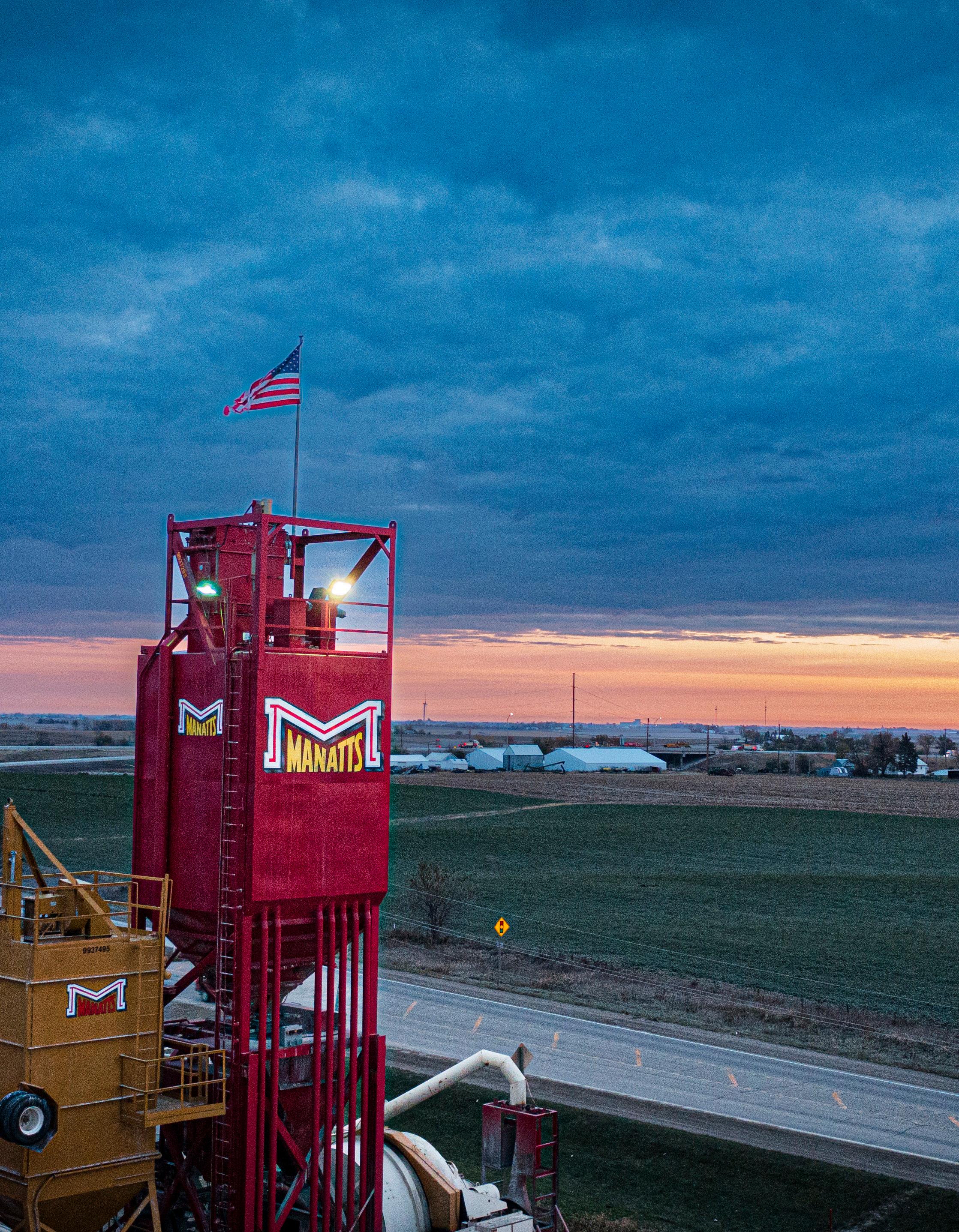
Brian Manatt | President, Manatt’s
We don’t just build for the gratification of a finished project; we build for the long-lasting legacy of hard work and commitment that we leave behind. We build our employees up and leave our mark of excellence everywhere we go. At Manatt’s, every material is vital to the whole project– that’s exactly how our team functions.
With 2022 fresh in our rearview mirror, it is easy to look back and reflect on the numerous challenges that occurred over the past year. Labor shortages, supply chain issues, and product allocations, to name a few, compounded the hard-working nature of our day-to-day work and project initiatives. However, we enjoyed success across many areas of the business in setting Manatt’s apart as an industry leader— striving for continuous process improvements, levering technology tools that increase safety and communication initiatives, all while putting our customers and employees first.
2022 also marked the 75th Anniversary of our company, an incredible milestone. Junie founded the business with one truck, a vision, and probably had no idea what it would become. Whether it was ever spoken or not, the first generation set the foundation for the mission, vision, and values that are present today. This organization’s leaders and talented employees have made our company successful and profitable, staying on the path to excellence and ongoing success.
As I reflect on the business journey, I cannot overlook the personal experiences that have impacted my perspective on the company’s vision and the challenges faced. The commitment to staying true to one’s mission, vision, and values can lead to creating something bigger than yourself, proving that anything is possible. For those who don’t know me personally, I recently participated in and completed my first Ironman competition earlier this year in Cambridge, Maryland. The Ironman competition is a triathlon, an athletic event that challenges competitors to complete three consecutive legs of a race: a 2.4-mile swim, a 112-mile bike ride, and a 26.2-mile run. But more than that, Ironman is about excellence, passion, and commitment— showing the heights you can achieve when you push beyond your boundaries.
The first question people always ask me is, “Why did you want to do this?” Followed by the second and seemingly more obvious question, “Wasn’t it hard?” I offer this explanation: I’m competitive. It was an idea that continued to build as my fitness journey progressed from playing football in college, to a simple 5K in my neighborhood to get back into shape, and then to longer rides and longer runs as I became stronger and more engaged in the community of athletes that supported me. And, yes, it was hard. However, here’s where I think this experience applies to anyone working through something challenging and how it applies to business objectives and our daily lives. To accomplish something extraordinary, one must have an extraordinary dream with a goal that may seem impossible to most. Below are three simple practices I used through my training program and are themes that I believe we can all use to better ourselves personally and professionally.
COMMIT TO THE GOAL. Do something worth doing. If it were easy, everyone would do it. My goal was to finish the race in twelve hours. I didn’t set that goal alone. I relied on my training partners, my coach, and my family. An incredible community of people supported me through this event. It’s true for athletes or businesses of any discipline. I’d say it’s also true for our work at Manatt’s. It’s hard work and long hours in various demanding conditions. What we do matters, who we do it with matters, and to be successful we must stay focused on our aligned goals, shared commitment, and a shared vision for the future. We are leaving our mark, and it’s been that way for 75 years. As I look to our future, we must keep that mindset at the forefront and work as one united team.
BE FEARLESS. As simple as my goal sounds, I would not have finished if I had let self-doubt and fear drive my decision to compete. The more I trained and focused on being the best version of myself, the more strength and discipline I developed to help me complete my goal. I relied heavily on my training plan. It helped me stay accountable, taught me how to manage failures, and prepared me for when things didn’t go as planned. We do the same thing in our businesses. We set goals to help focus on key initiatives. We learn from our mistakes and are not afraid to fail forward – that is, we don’t quit when it gets tough, we adjust the plan and keep on moving. Sometimes you have to go slow to go fast. We cannot stand still; the world will pass us by. At Manatt’s, we do more than expected and embrace opportunities to innovate our processes. These are tough challenges with often no clear path forward. We must be fearless as we welcome the path ahead for a future that will benefit us all.
ACHIEVE SUCCESS. I didn’t start my fitness journey with an Ironman competition in mind. Initially, I found a group of people that challenged me, showed me a different path, and demonstrated how important it is not to quit. I remember my first 100-mile training day on my bike. I was off my bike, standing in the middle of the road, 50 miles from home, climbing Madera Canyon in Arizona, and experienced a fullbody cramp. I could not pedal. I could not move. I could hardly stand. “What do I do now?” I asked myself. I felt the panic and shame in my chest grow as I thought about calling for a ride. I heard my coach in my head saying, “Ironman training is crisis management. You need to learn how to overcome when you’re faced with failure, including your equipment, body, and mind.” I took a breath and decided to keep going. At first it was a walk, then a slow ride, and slowly I felt the power return to my legs. I did make it to the top and completed the 50-mile ride home for my first successful 100-mile bike ride. This describes our journey at Manatt’s. We have faced difficult and hard times and persevered. We have made the most of our opportunities and excelled while enjoying the ride. We have always done things the right way, the Manatt’s way. This means looking forward, learning from our mistakes, and supporting our fellow employees. We started
with one truck and a vision. Over time, we built on our experiences, took pride in our values, and demonstrated what it means to be an industry-leading company. The community of people we have at the company is unique and is the reason for our 75 years of success. Anything is possible if we stay true to our mission, vision, and values to believe in ourselves. I am confident we are on the path to excellence and achieving success.
Since our beginnings and today, we have operated with three core values, “Family,” “Excellence,” and “Human Potential” as our founding principles. We see ourselves as an extended work family. At the end of the day, it’s all about the people. I’m thankful to everyone that contributes time and talent to this organization because you have proven that anything is possible.
Welcome to the race.
As I reflect on the business journey, I cannot overlook the personal experiences that have impacted my perspective on the company’s vision and the challenges faced. The commitment to staying true to one’s mission, vision, and values can lead to creating something bigger than yourself, proving that anything is possible.
2022 has been a unique and exciting year. Two key trends have threaded through the last construction season, creating challenges and forcing us to reevaluate our daily processes and business plans. These are both labor shortages and material fluctuation.
The ongoing battle for labor is not new to us and we continue to look for opportunities to recruit new employees. In addition, we continue to reinvest in our training and onboarding experiences to empower and develop current team members. We believe in the power of human potential, which means that we believe each of our team members is worth investing in and supporting.
For the first time, we were able to hire CDL drivers through the H2B Visa Program. I want to recognize Arturo Gutierrez, Christian Neria, Joe Guillen, and Mike Sanchez for their work onboarding and welcoming four H2b visa drivers. At Manatt’s, joining our team means joining our family. We are proud of these gentlemen who have stepped up to help coach, train, and translate. Welcome Jose “Sr” Rojas Saucedo, Jose “Jr” Rojas Benavides, Humberto “Berto” Sanchez Pinales, and Valentin “Val” Rojas Saucedo to our Manatt’s Ready Mix family. We know that every person matters when delivering and creating excellence for our customers. Christian, Mike, Art, and Joe have helped build communication aids and worked to ensure that our H2B drivers meet Manatt’s Ready Mix standards of Excellence. Also, thank you to Sue Esther, Adela Fragoso, and everyone in HR for all the work to make the H2b program possible. We work hard because we believe in what we’re doing. I’m confident in this direction. With the support and alignment of the business, I know we will continue to build on successful Manatt’s legacies.
Material and product availability has been a unique challenge this year. We have seen product shortages, allocation challenges, multiple price increases, and distribution disruption throughout 2022 on our input materials. The most significant impact has been on cement. Cement is a material we cannot make concrete without. In response to this challenge, we are incorporating a new, more sustainable type of cement called Portland Limestone Cement (PLC or type 1L). Our quality control team has been leading the efforts on this
initiative, but the error tolerances are much smaller with this product. It has been challenging to make the needed adjustments, but we are confident in the go-forward plan to resolve product shortages. This year, the drastic price increase on powder, aggregates, and labor costs led us to experience our first mid-year price increase on ready mixed concrete in over three decades. This will likely be an ongoing challenge in the year to come.
More significant issues in 2022 have been associated with the operation of cement mills and logistical problems with product distribution. Almost every midwest cement plant experienced maintenance issues with their kiln, grinding facilities, or both. Cement plants are built to run 24 hours a day, seven days a week, so any downtime impacts the amount of product available.
Distribution and transportation options have continued to evolve over the 2022 season. Low water levels on the Mississippi River have impacted the ability to barge materials up and down the river. Most of our eastern Iowa plants are fed from river terminals and depend on this transportation. Rail has also been inconsistent, and the mid-summer strike threat created significant rail delays. Most of our central Iowa plants are served by terminals dependent on rail delivery.
Additionally, there is a trucking capacity shortage which impacts direct plant hauling. Even more, the trucking shortage affects us when we must go to terminals at further distances to supply plants with cement, fly ash, or slag—often with little or no notice. It has taken coordination and communication between all our plant managers and the dispatch group in Brooklyn to allow us to find success this year. Mike Novelli, Tim Morrison, and their teams have demonstrated dedication and passion that enabled Ready Mix’s success this year. It is a testament to our ability to work together and support each other to overcome challenges.
2022 is also notable as our 75th year in business. A milestone like our 75th anniversary is a great time to reflect on what has made the company great. Our people, processes, and willingness to continuously pursue excellence have made us successful. The commitment to training, communication, and overall people and process development will be essential in our continued industry.
Whether you have been at Manatt’s for one month or 50 years, you have heard the phrase, “that’s just how we’ve always done it here.” It is a true statement, to a point. Still, I would argue that the statement is more rooted in the idea of delivering excellence, investing in our people, and providing quality products and services for our customers, versus our unwillingness to embrace change. As I reflected on the past year, it struck me how much we focus on process improvements in our daily activities. For example, over my 15-year tenure, we have changed and adapted our training programs which now include CPD (Concrete Delivery Professional) training and plant manager training. We have greatly improved our processes over the years; it’s exciting. But first, I’d like to share a little of my story and “how we’ve always done it…” shaped my experiences in the early years of my career with Manatt’s’.
July 2007 - I was hired to drive a mixer out of our Products Shop based in Brooklyn, IA. When Denny hired me on a Friday, he gave me two days to obtain my CDL learner’s permit. He said, “if you don’t have a CDL permit in hand on Monday morning, don’t even come here because you won’t have a job.” Thank goodness the DMV was open on Saturday, because I failed the test Friday afternoon!
The following Monday started my journey with Ready Mix. Orientation at that time was sitting in the upstairs break room watching old VHS movies of different training seminars - 8 solid hours of videos. The next day, Tom Shaull, Products Manager, introduced me to my “trainer,” and away we went. I asked the trainer how long the training process should take, and he said, “hopefully, a while; once I train you, I lose my job because I am losing my CDL.” On my way home after my first day, I remember Tom asking me if I had any concerns. I told him, “Only one; I don’t know how to downshift!” He told me, “Don’t worry; you will figure it out going down the road!”
Aug 2011 - We had a manager who needed surgery during the season, so I was asked to run the Belle Plaine plant. To be clear, the plant everyone sees in Belle Plaine now is NOT the same plant that was there in 2011. We used to have an old pull-lever plant with a 3-cy batcher. You tasted every cubic yard you produced. We scheduled time for me to be onsite in Belle Plaine on a Monday to complete a “crash course” with the plant manager the day before he was taking leave. Well, just my luck, we got three” of rain, and everything was canceled for the day. Luckily, we talked a contractor into doing a 1-cy footing pour inside so that I could see how the plant operates at the bare minimum.
Alone the next day, I received a phone call from a customer wanting to do a 300-cy cattle project. Freaking out, I called our trucking division. Luckily, Dwight and Elmer, long-tenured dispatchers for the aggregates and cement powder, were available. We started talking, and they asked me what I needed for materials.I said, “hell, if I know,
that’s why I called you!” I owe a lot to those guys for teaching me about ordering materials and saving my butt that day.
We currently have 12 NRMCA-certified professional CDP Elite trainers throughout Iowa to help onboard our CDPs and show them the Manatt’s way (aka the right way)! Every new employee must complete the CDP Elite Training program BEFORE they are allowed to operate a mixer on their own.
During the training process, which may take a few days for someone with previous experience or up to several weeks for a new CDP operator, the CDP-to-be must show their trainer they can safely operate the equipment along with the ability to pass a 41-point proficiency checklist. In addition to that, we also spend time training on customer interactions and how to deliver the “Manatt’s Customer Experience.” Once the CDP Elite trainer is confident with output and performance, a trainee completes a “check ride” with an eligible person that will sign off and release the new CDP for independent work.
Due to the success of the CDP Elite training program, we started a new program in 2022 called the “Plant Manager Elite Program.” Gone are the days of handing someone a set of keys and saying, “good luck, call if you have any problems.” Four plant managers were selected and trained through our pilot program. They are called Plant Manager Elites and are available to help onboard and support new plant
managers. Similar to our CDP Elite Program, when we bring on a new manager, we pair that person with a PM Elite and spend at least one week with them at the Elite’s plant.
During this time, the new plant manager will go through a 39-point proficiency checklist for running and operating a ready-mix plant. New plant managers will also meet with office and shared services staff to learn more about back-of-house support services, billing, and other critical processes. Throughout the year, the PM Elites will have scheduled visits with the new Manager to ensure they understand how to run a plant the right way, the Manatt’s way.
It is amazing to see how we have matured and progressed during these last 15 years regarding our training programs. I know they would have benefited me as I was starting my career. I’m excited and grateful to be part of a team that can continue to develop and execute programs that help our employees and the company. Thank you to everyone who participates in implementing these programs and continues to progress and improve over time.
Our people here at Manatt’s truly make a difference. We are only as great as our people, which is why we continue to invest in helping each of us become the best version of ourselves.
In February, I went to a funeral visitation for Lyle Davis, a plant manager in New Sharon, before his retirement in 2006. As I talked to his family and watched the video montage of Lyle’s life, it caused me to reflect and examine my feelings about life, our work lives, Manatt’s, Value Based Leadership (VBL), and how they all relate to one another.
Lyle started at Manatt’s in 1971, delivering Manatt’s precast concrete products in Brooklyn to farmers and septic installers. He advanced to managing our precast operations in Brooklyn. Then, in 1979 returned to his hometown of New Sharon to manage our concrete plant until he retired in 2006. 27 years at the helm leading in New Sharon. 35 years as an employee of Manatt’s Inc.
I first met Lyle in 1973 when I started employment with Manatt’s. Initially, I was intimidated by Lyle. He was bigger than life, confident, gruff, and had a tough reputation. But as I got to know him, that was all fluff. He was a very down-to-earth, humble guy with a lot of pride. While conversing with his family and watching videos of his life, it struck me how much of a simple, ordinary family guy Lyle was, and that was his life. He was honest, had pride, lived by his word, and led his family with a steady hand. He strived to do things the right way. He never strayed far from his roots in managing our plant, raising feeder calves on his small farm outside of town, and building his own rustic log cabin getaway on the back forty. The countless stories he told over the years backed up the impression of a steady, uncomplicated, great
guy. Around the country, we hear great feedback about “midwestern values,” and that was Lyle. He was one of us.
Lyle was the type of guy that Manatt’s was built on by Junie and Merlin. For 27 years, he was “Mr. Manatt” in New Sharon. In those days, he was sent there with the direction: “You are in charge. Run it like you know we want it run. Call if you need anything; otherwise, we will assume all is ok.”
Lyle was well-equipped for that mission. He was in his hometown, had pride in himself, and had pride in Manatt’s. He showed up every day and operated his business based on his dignity, sense of duty, and the commitment he felt to himself, Manatt’s, and his customers. Lyle felt obligated to do it the Manatt’s way with limited oversight. There were lots of “Lyles” in the early decades.
Lyle managed the New Sharon plant to the best of his ability. He did it by living his ingrained values, which served all parties well. But Lyle didn’t change a single thing in how he ran that plant for the 27 years he was there. New Sharon was a time warp; there was still a rotary dial phone on the desk in 2006. This isn’t a criticism of Lyle or Manatt’s. That is just the way we did things back then. He did an excellent job as “Mr. Manatt.” As we look to the future, we must remain diligent in our pursuit of excellence— looking for opportunities to challenge existing perspectives and processes.
Looking back today, with my journey and the company’s journeys in mind, I feel that we let Lyle down. He performed to the best of his abilities and did ok. What did we do to help him grow and improve? What support did we offer to “ditch the rotary phone?” We did
nothing. But that’s the way we operated back then. Hire a person with good qualities, put them in place, and stand back. Contrast that with today’s realities of fierce competition, complex technology, required communication, and the need for continual improvement. All of these require the best version of ourselves. When we started our VBL journey, Brian Manatt said, “We have a history of putting people in jobs and accepting the results even if the outcome is mediocre. In today’s environment, we can’t accept mediocre results anymore, and we won’t.” This statement stuck with me. We must ask ourselves: “Am I, in my position, challenging mediocrity both up and down the chain of command?”
Our success comes from working together. We must challenge, support, and communicate with each other for any of us to succeed. The business has grown and times have changed. Company pride and dedication, like Lyle demonstrated throughout his life and career, are not a given, nor should they be today. I challenge you to help earn that. Manatt’s asks you to be accountable to your job; you have every right to hold them accountable to you. Manatt’s is making a great effort to be your employer of choice. Use opportunities available for feedback, both good or bad. It’s our opportunity to help the company be better, help others to be their best selves, and don’t forget to hold yourself accountable to those same standards. If we genuinely care about one another, express that through words and actions. This is how Manatt’s can be a great company for each of us, as it was for Lyle.
Let’s begin by nurturing the pride in being a Manatt employee. Foster continuous growth and earn dedication by living our core values every day. In my opinion, some ways we can all focus on living our values:
Believe in Yourself. Lyle believed in himself. Nurture your belief in yourself into continuous improvement and help others do the same. Do your homework, be prepared, and fail forward – learning from every lesson both good and bad.
Live in Service to Others. For Lyle, living in service to others meant taking care of his customers. Help the current Lyles of Manatt’s feel part of the team by highlighting the positive traits others possess, and leveraging those traits to benefit all.
Be Great on Purpose. Lyle was successful in doing what was expected of him. Hold yourself accountable for being great and expect the same from others. Constantly ask if there is a better way. Do more than what is expected.
Lead Fearlessly. Lyle led fearlessly in a style suited for his times. Commit to leading fearlessly in today’s world. Ask for help when you need it and challenge the convention. Show support for your brothers and sisters around you through love and accountability.
Leave a Legacy. Lyle was extremely proud of his career at Manatt’s. He left a legacy at Manatt’s; without a doubt, I am a part of it. We must be accountable and put in the effort. We cannot wait for our legacy to simply show up. It is up to each of us to do the work and create them. We must put in the work, have fun, celebrate the wins, and share with our teams.
It’s the fun days and the “not-so-fun” days that add up to make the journey we call life. Enjoy the Ride.
2022 concluded with a lot of decent projects in Ready Mix this year. We have been faced with a change in cement material and challenges in supply. We are also making a new kind of concrete this year: a mash-up of both concrete and asphalt.
Starting off the season was the transition to Type IL (10) cement, known as Portland Limestone Cement (PLC) which replaced the Portland Cement Type I/II we have used for years. What is PLC? PLC is a cement engineered with higher limestone content than Portland Cement to reduce the carbon footprint of concrete by about 10%. Portland Cement is manufactured with up to 5% limestone vs. PLC, which has 5% to 15% limestone. With more limestone mixed in, it cuts down on the manufacturing process, causing less CO2 emissions.
The Portland Cement Association (PCA) estimates that if all cement used in the USA in 2019 had been PLC, it would have reduced the CO2 emissions by 8.1 million metric tons. That is the equivalent of taking 1.75 million cars off the road for the entire year!
PLC performs very similarly to Portland Cement, causing minimal change to mix design performances, and is compatible with other materials in concrete. With the increasing importance of sustainability and reducing the carbon footprint, this mix of more environmentally
friendly cement can make a difference and meet specs driven by these demands.
Have you ever heard of Roller Compacted Concrete (RCC)? If not, let me explain, it’s basically like asphalt but better--it’s concrete! We have been supplying it for the Tama Premium Beef Project. RCC has the same basic components as conventional concrete but in different proportions. With only 10-15 gallons of water per yard, it is a dry mix of concrete mixed in a twin shaft plant or pug mill. The mixture is hauled in a dump or belly truck and then placed at zero slump—looking similarly to damp gravel with an asphalt paver and is compacted with a roller. Once rolled, it is finished with power trowels and broomed to look more like conventional concrete.
RCC is also unique because we sell it by the ton (like asphalt) rather than by cubic yard (like concrete). Testing such a dry mix has some interesting differences as well. There is a separate ASTM standard (C1435) for testing RCC. It uses a 6 x 12 cylinder that must be filled in four lifts and compacted with a hammer drill between each lift. This will give compressive strength and unit weights to determine yield. Air is not a factor as most, if not all, is beaten out in the rolling process.
With many projects this year, we have had to delegate the QC team to all Ready Mix locations, including many outside of their home bases, to get the job done all while keeping safety a top priority.
Manatt’s 75th year has been good for the South Area team. We experienced some bumps in the road, but I believe this team is better because of that. Our core values are more prevalent than ever before in this company’s 75-year history. I was present during Manatt’s 50th Anniversary and at that point in time, everything seemed great, we simply “got things done.” Today, we have procedures and techniques, but we have opportunities to discuss them, to share learnings with peers, and opportunities to enhance best practices to accomplish more – together. We learn from our mistakes and are open to changing our behaviors, with the goal of becoming the best version of ourselves.
The 2022 season brought new and challenging work. Thank you to the South Area team members for striving for EXCELLENCE, living your HUMAN POTENTIAL, and coming together as a FAMILY to deliver our customers the greatest, most versatile construction materials. I am very proud to work alongside you and am grateful to have you as a member of this team. We reached our yearly target for production despite the many roadblocks. The unity, strength, and support the team demonstrated allowed us to accomplish every task we set out to complete.
We supplied 16,000 CY of RCC material for the Roller Compacted Concrete (RCC) parking lot project in Tama, IA. This project is unique for several reasons. First, the RCC product itself. We are producing the mix, not delivering it. We are utilizing someone else’s plant to make the RCC mix. It is a very different style of plant than we normally operate. This project challenged our thought process, from setting up the plant site, and providing raw materials, to how we measure, sell, bill, and invoice for the product provided. Special thank you to Tim Niedermann who spent his fall working outside in the elements and running the plant. And, thank you to the entire team that has driven this project from inception.
Matt McDonald accepted the challenge to produce as much as he could from two plants this season. Batching at both plants on the same day but also utilizing others, including Cristian Neria, to step in as needed. There were many challenging times at the Blairstown plant itself. The team took those operational challenges in stride. Through all the daily challenges, Matt went on to produce over 10,000 cy from the Belle Plaine plant. This is a single-season production record for a stationary plant in Belle Plaine!
Cement allocations came early this season, with Justin Bridgewater and AJ Douglas being the first affected. Many phone calls with uncomfortable conversations became difficult and stressful, but both
team members faced it head-on and made it through. The subsequent allocations impacted Todd Eckles, Jose Gonzalez, and Zac Schott. They faced the challenge with great attitudes and willingness to adapt. The team was able to call some audibles, utilize some split silo space, and muster up enough supply to never entirely run out of cement. Zac, remember, you are not out of cement if you are beating on the cone and a loaded tanker pulls in the yard! Yes, we can laugh about it now, but again, difficult and stressful. However, everyone persevered.
The last challenge we faced was with our fly ash source running out of supply, and the adaptations we made with a percentage of replacements or no ash mixes. Again, uncomfortable conversations were had, but everyone has done great with those, including Nick Gallagher, Jeff Upah, and the sales team.
We have great opportunities for improvement, especially in our safety and incident rates. If we can continue to learn from our mistakes, change our behaviors, and control outcomes, we will improve and stay on this journey to EXCELLENCE! I hope everyone has a SAFE, HAPPY, and HEALTHY “off-season”. I look forward to seeing everyone in the spring!
Thank you to the South Area team members for striving for EXCELLENCE, living your HUMAN POTENTIAL, and coming together as a FAMILY to deliver our customers the greatest, most versatile construction materials.
The days seem long, and the years go fast. It’s hard to believe the 2022 season is coming to an end. Christmas décor is going up and the cold weather has arrived. It’s been a season marked by celebratio, but filled with fuel surcharges and price increases punctuated by material supply issues that have impacted the entire business. Not knowing where our cement would come from, or if it would come at all, is a stressful way to go about your days. This year also marked the first year in my 16 years at Manatt’s that the ready mix has passed on a mid-year increase to our customers. With the constant changes and difficult daily conversations, one may assume we had a rough season. However, we always do what we do at Manatt’s. We adapted, persevered, and came together. It wasn’t always easy, but we all fought hard to achieve a successful year. To me, it is fitting that this season happened to fall on our 75th Anniversary. Over the last 75 years, Manatt’s has always found ways to succeed in even the most challenging times. You aren’t successful in business for 75 years without teamwork, innovation, and strong leadership: Family, Excellence, and Human Potential. Speaking on behalf of Ready Mix, I am proud of the season we have had and the way we have gone about our business.
In the South area, we are finishing the season tackling a unique type of project that, to my knowledge, Manatt’s has never been involved with. We are renting a rapid twin-shaft continuous mixing plant to produce Roller Compacted Concrete (RCC). We have set the plant in the Wendling-Tama yard and are producing 17,000 cy of RCC over five weeks. We are on schedule to finish the project by the end of November, but this project has created many challenges that have required a lot of effort, creative thinking, and teamwork.
Tim Niedermann, Josh Beaderstadt, Kris Seitz, and Kevin Matteson continue to put in long hours in harsh conditions to make the project a success, and it certainly does not go unnoticed. The Wendling team has been a pleasure to work with. Todd Miller and Ellen Graff have been extremely accommodating and have gone above and beyond to ensure we operate successfully. I am proud of the working relationship both Wendling and Manatt’s have had on this job. This project mirrors our company’s history of not being afraid to take risks, being great on purpose (Excellence), people pushing themselves (Human Potential), and coming together in difficult times to accomplish great things (Family). Cheers to a great season and an incredible 75 years!
The rural plants (Maquoketa, Dewitt, and Tipton) have had a great season regarding the yards produced. The metro has also done very well this year, with the help of the R+L Carriers project, which we anticipated conclusion in the 2022 season but will carry over work to the 2023 Spring season.
We hired 12 new CDPs in the Spring, which helped manage the dayto-day workload and keep projects on time and on schedule. The individuals we hired did a great job onboarding and learning their new positions. We were also fortunate to add a new mechanic to our team. He is doing a great job learning the “Manatt’s Way of doing things and keeping our equipment operational. I am very proud of the team we have in the East division. They live our core values, strive for excellence, and manage projects and customer needs courteously and professionally.
With their first dome built in 1976, Dome Technology is a leader in industry and innovation. Now over 45 years later, they have constructed over 750 domes, with 36 of these in foreign countries. They are working on seven cement domes, one of which is located at Continental Cement in Davenport, IA.
The Continental Dome project started in early 2022 and is 2.8 miles from Manatt’s Ready Mix Davenport plant, making it an excellent location to support Dome Technology. The dome was inflated on March 28, 2022, standing 171.5 feet high. Long days of spraying shotcrete
Dome Technology provided steady work for several Concrete Delivery Professionals. While the Dome is not finished, to date, Manatt’s has supplied nearly 6,800cy of materials to this project and almost 7,000lbs of structural fiber provided by DE Fiberworks. Once completed, the Continental Dome will be the largest cement storage facility in the USA. It will store 125,000 tons of finished product, reclaim speed with top out at 350 short tons per hour.
The 2022 construction year was very demanding, with significant price increases, material, and labor shortages. It started at the beginning of May when we went on cement allocations. Typically, we may see an allocation in October, but never has it been in May. Our cement supplier initially indicated we would be cut back to 13 loads a week when we were used to approximately 30 loads to meet our project demands. With a few phone calls and special requests, we were able to increase that total to 20 loads. This wasn’t enough on an average week, so with leadership’s support, we supplemented our shortage with a second cement source to procure the last ten loads. At one time, we were contemplating a third source, but by luck, we were not forced to use that option. While on cement allocation we were hit with two more allocations simultaneously on fly ash and limestone aggregate. We shared our allocation with the Metro plants, and we were able to make aggregate abundant for all plants involved. The fly ash shortage was short-lived but still a problem. For a period, we went straight to Portland for the COD customers and changed our mix designs by reducing our fly ash content to 10% for our regular customers. I’m not going to say it made an abundance of carryover, but it did get us through the shortfall.
At the close of the 2022 season, we are bidding on work and trying to secure projects for the 2023 construction year. We have always known our prices for the coming season in previous years. Several suppliers have decided to raise their pricing by almost double per ton this year, beginning with January 1 and not April 1. In the past, our suppliers would let us give them our carry yardage from the previous season, and they would carry our price on signed quotes. This year
they said, “no carryovers.” After we thought the dust had settled, we were informed of a July increase by two major material suppliers on top of their January increases. As we close the 2022 season, we know approximately what we will be paying for most of our materials this year, so we feel a little more comfortable. However, no one can confirm another midyear price increase on products with certainty. Looking into our crystal ball, we can likely cover our costs enough and keep our contractors competitive.
As we conclude the 2022 season, let’s reflect on all the positives we have accomplished this year. Thank you to our employees for their hard work and commitment to the company. Especially this past season, when there’s such a shortage of qualified employees to fill our empty spaces. Keeping the bench full was a daily task. Thank you for your contribution. You are appreciated and essential to Manatt’s. We all have many blessings to count in our lives. For this Christmas season, step back, take a breath, and smile.
I want to spotlight three projects we were part of in the metro. These three projects all show sustainability and long-term solutions. Just like Manatt’s being around for 75 years, this project will stand the test of time and be there for 75 years.
NICK RIPLEY METRO, AREA MANAGERManatt’s poured 15 total pedestal rings forming the main tower structure of the water tower. The pedestal sits on a 300 CY footing that will support the tower. The bowl of the tower will be constructed from steel and will rest on the final pedestal/dome slab. One of the main challenges of this pour was the mix consistency. The mix had to be an exact duplicate of the previous one to ensure a uniform color between the rings. All concrete placed had Super Plasticizer added on site to limit water and increase strength. Our CDPs enjoyed being part of this project and watching it grow into the sky. It is now visible from I80 as you drive through Altoona and brings a sense of pride to all who were part of this water tower project.
The metro was fortunate to have a big project at the IA state fair that will stand the test of time and will express our family values. Our employees, parents, kids, grandkids, or other family members will sit in the bleachers to watch a tractor pull, demolition derby, concert, or event in the new bleachers. Manatt’s poured this complex project with KRW construction over a period of 2 seasons. Each phase had to be completed by the fair opening deadlines and came down to the wire. We poured a high-strength chip mix on the exterior foundations to support the new press box and bleacher overhang. These footings required forms that had to be hand-made to the angles for the new supports. The mix needed to be high-strength and have an astatic uniform appearance.
The West Des Moines Manatt’s plant took on a challenging and rewarding project this spring. We installed 12 drilled shafts, roughly 70 cubic yards each. The shafts were drilled over 60’ into the ground. Without these foundations, the structure above would fail. As these shafts were placed, we had to access the job from both sides of the river along with areas built out onto the river. All loads had very tight specifications to follow, in addition to having Super Plasticizers added onsite to increase slumps of 8” + at placement. At Manatt’s, we take pride in working as a team to succeed; like these shafts, we must have a strong foundation and be grounded to support the weight. This project received a lot of help and support from the Brooklyn Quality Control team to ensure we stayed on track with the IDOT requirements.
These projects will last long beyond our time and will encompass the legacy we have left at Manatt’s. Projects like these are why Manatt’s has succeeded for 75 years and will push Manatt’s into another 75 successful years. Next time you sit in your car or a ready-mix truck, look north in Altoona and smile, knowing your name is on that water tower. If you’re sitting in the bleachers or standing at the railing, cheering your favorite race or at the Iowa State Fair, know all the concrete around you is bringing all those families together. With all the uncertainty today, from out-of-control prices and shortages in everything from eggs and fuel, to rock and cement. We all may feel overwhelmed but find comfort knowing Manatt’s has seen many moments that have felt like this over the last 75 years and survived to prosper. Finally, no need to hold your breath while driving south over the Racoon River in West Des Moines. That bridge is sitting on one solid, long-lasting foundation.
We are having a good year in the North Division. We have experienced wonderful fall weather. Warm temperatures and very little rain have allowed us time to complete more projects than we anticipated. Typically, the north plants close 3-4 weeks before the other areas due to cold weather, but in 2022, we were able to operate well into November.
CHANGE is an excellent word to summarize the opportunities and challenges the North Ready Mix division has faced this year. From staffing challenges and employee promotions, to product shortage and supply chain challenges, compounded with exciting but demanding project schedules, the team has managed to navigate many hurdles over the 2022 season.
The North Division experienced employee changes in every plant manager location this year. As we conclude the 2022 season, three plant manager positions remain open - Waterloo Elk Run, Waterloo Airline, and the Readlyn plant. Hank Schares was promoted from Truck Coordinator to Waterloo Metro Manager. He now oversees four Waterloo plant locations, management staff, and all CDPs in his area. It’s an understatement to say that Hank has had a busy year, but he was able to strategize and prioritize which plants to operate each day to hit targets and project deadlines. Mike Holt was promoted to Truck Coordinator and has done a great job. Mike works with plant managers and other area truck coordinators to ensure everyone has the trucks they need to accommodate their customer requests. Nick Lake has had a good first year as Plant Manager of Independence after previously managing the plant in Oelwein. Les Allwood accepted
management responsibilities for the Oelwein plant location. Les is a CDP Elite. He uses the leadership skills he gained from training our CDPs to lead the Oelwein team. Aaron Robbins joined our north leadership team as Traer Plant Manager and was a CDP in Vinton before joining our team. Justin Damm started the year as plant manager of the Waterloo Airline plant, but this summer transferred to Grundy Center.
While there have been some growing pains with these changes as new leaders learn their new roles, it has been an awesome opportunity to see the growth in each person as they’ve developed over the 2022 season. It has been challenging to be short-handed and balance conflicting priorities, but the team has done a great job being there for each other, having each other’s back, and growing as a family to get the work done. This is a testament to what it means to live our core values here at Manatt’s. Every day we have an opportunity to demonstrate the power of our potential, our human potential. We have so much talent within our Manatt’s work family I’m confident we’ll be able to fill our open positions soon.
Another challenge that has forced us to be flexible and change our processes relates to supply issues with cement and fly ash. Unfortunately, this has hit every area of the Ready Mix division but significantly impacted the North Division through the fall of 2022. While we typically encounter cement supply shortages each fall in the north, it started much earlier this year. This, along with the shortage of fly ash, changed how we planned and coordinated load deliveries and plant operations. We focused on product availability, even if the plant was closed, and transferred fly ash to open plants to keep us in supply where we needed product to deliver to customers.
We have many projects to highlight and feature for the 2022 season. The larger projects we have completed or will continue to work on into next season include the following:
In Waterloo, our projects include two bridges over the Cedar River, the new Cedar Falls high school, Warren Transport, an assisted living in Cedar Falls, a Hydrite addition, and a new addition to Colwell Ford. In Grundy Center, a walking trail along the Iowa River and paving in Eldora. From the Traer Plant, paving in both Dysart and Traer. In Oelwein, a Kwik Star, trail paving and patching. Independence projects included airport paving and patching.
Over the summer, we hosted a special memorial project in downtown Waterloo— commemorating the work of the USS Juneau and the sailors who served on her. It was held at our Waterloo plant and consisted of old mixer drums used on cement trucks that were taken off when the drums got too old and needed to be replaced. The memorial pays homage to the Five Sullivan Brothers, the USS Juneau, and the branches of the U.S. military. The Army, Navy, Air Force, and Marine Corps. We poured pads and mounted Sullivan and Navy mixer drums on either side of a Manatt’s drum. The sailors from the current USS Sullivan, the original USS Sullivan, and the USS Iowa were in attendance for the ribbon-cutting ceremony. The memorial was an excellent way for Manatt’s and the community of Waterloo to show their support to the brothers and military veterans everywhere. It was a great event and an honor to visit with so many heroes. The memorial will honor veterans who live and visit Waterloo for years.
Thank you to everyone on the North Ready Mix team for a great year. The work you do is noticed and valued. I appreciate everything you do to ensure we provide excellent service to our customers, as we have for 75 years.
At Manatt’s, we measure everything we do against our core values of Family, Excellence, and Human Potential. Our mission states, “Safely do everything we do better than anyone else.” Our culture has been building on this concept for generations. It started with a purchase of a Studebaker truck in 1947 and has continued to grow by working together towards a common goal. This has been true for 2022, as cross-functional teams work together to hit our organizational goals and targets. Our Transportation and Shops teams have been focused on two strategic initiatives: empowering people and technology enhancements. In my opinion, these are two strategies we are doing better than anyone else in the industry. Our investment in people, along with our investment in tools and technology, is what defines us as a company today.
We want to be the employer of choice. We want to take care of our people as our founding leaders established 75 years ago. People empowerment is focused on creating and implementing trucking-focused training and development programs.
As of 2023, employees within the Trucking division will be called “Professional Drivers.” We believe that our employees do more than drive a CMV. They are our front-line customer service representatives— delivering products on time and on schedule. Their vehicles are mobile billboards that promote our great company and represent our values. We want to show that we value their contributions. Over the last several months, six previous job descriptions have been evaluated and updated to align with our core values, highlighting the unique skill sets of these employees. Training will be provided to all employees during the 2023 spring meetings to review and discuss these exciting updates.
Brian Schulz, Director of Equipment & Shops, and Mike Novelli, Director of Transportation, along with their teams, have been laser focused on implementing new training and development programs. Their efforts have transformed our culture in Brooklyn. People are our biggest differentiator; equipment does not do us any good without good people to operate it.
Technology enhancements continue to challenge and change our daily business practices with the introduction of Lytx and XBE. The Lytx program aims to increase our professional drivers’ operating awareness by identifying risky driving behavior via the Lytx DriveCams. A rewards program will be developed to promote those professional drivers who increasingly improve their driving skills. A pilot program was launched in 2022, with complete program execution planned for 2023.
XBE provides the broadest, deepest, and most ambitious solution to transform how we plan, execute, analyze, and improve our operations. As we continue to grow and evolve the business, this platform will help us make informed, data-driven decisions for our company.
Each of you and your contributions has made this company successful. Thank you for your efforts and dedication to these and many other organizational initiatives. Thank you for choosing to build your legacies at Manatt’s.
We want to be the employer of choice. We want to take care of our people as our founding leaders established 75 years ago.
New tools, processes, and procedures must be developed and implemented to keep pace with our competition in today’s changing environment. The leadership team’s’ challenge was bringing an entrepreneurial mindset to the rest of the workforce. The biggest challenge was motivating and cultivating the family values that have defined this organization and making it resonate with all employees in the business. The adoption of Value Based Leadership principles has been a solution to that challenge. Creating a positive work environment inspired by trust, open communication, and accountability is the roadmap to a successful future. People, pride, and purpose distinguishes us in this market and motivates the team to succeed. The Manatt’s vision and commitment to Family, Excellence, and Human Potential have evolved over the past 75 years. The desire to be the safest and best producer is on every employee’s mind. The history of a proud company is the cornerstone of future growth. When history meets technology, we should expect good things to happen.
For the Trucking Division, the next pivotal journey will be focused on implementing on XBE, an operating platform that will allow for increased transparency and real-time access to information. The trucking division has experience with transportation management systems like Command Alkon, Dauber, and GEOTAB. It made sense that they were identified to support the initial implementation of the new system. The project soon proved to be a challenge due to the complexity of our business. Our customers, vendors, and business models are complicated and unique, and those unique attributes became apparent within the confines of the platform. The Manatt’s
team, led by Brandie Flathers, identified challenges and created opportunities to tailor the XBE Platform to our business. Order flow, fleet activity tracking, communication processes, and training and development programs are all great examples of existing processes and procedures that are being evaluated through these critical updates.
The benefits of planning and forecasting using XBE have become evident and will help reduce costs and streamline asset allocation. As more divisions begin using the tool, data will become more accurate. Accurate data will lead to better planning and allow us to identify constraints before project execution. XBE will enable supervisors to communicate with the carrier base, monitor carrier activity, and influence carrier settlements like never before. Challenges may continue to present themselves, but we have the tools to set us up for success for 2023 and beyond.
The Lytx System is another technology improvement introduced in 2022. The Trucking Division realized the success of the Lytx program in our Ready-Mix fleet, which implemented the Lytx program in 2020. The program aims to increase the company’s overall safety awareness and protect our professional drivers. Our professional drivers are the touch points for our customers and are our safety ambassadors. New trucks with predictive cruise control, lane departure, anti-rollover warning systems, and cameras will be standard equipment on all Manatt’s power units. We expect the Lytx Program to enhance the skill sets of our professional drivers and reward them as Lytx training and coaching unfolds. The Lytx program is a significant investment in our overall safety program but the decision to continue to roll out the project was easy. We recently launched a pilot program to determine the unique adjustments that need to be made for the Trucking Division, with the full implementation slated for spring 2023.
On Saturday, August 27th, 2022, the Shops and Equipment teams contributed, alongside many others, to prepare a special day of celebration where employees, families, friends, and vendors could celebrate the legacy of this great company. There was fun for families with face painting, bounce houses, yard games, excavator challenges, and equipment displays. A new Manatt mini-concrete-mixer truck was also unveiled at the event. It is a fully-functional mini concrete mixer truck. It drives under its power, the drum turns, and the chutes fully function and are very realistic; it was the star of the day. The Minimixer truck was named Truck #47 in tribute to the year that Manatt’s was founded, 1947. It has already been featured in community parades and events all across the state of Iowa, as seen in the BGM Homecoming Parade and Ottumwa Octoberfest Parade. It also made an appearance at the Kirkwood Community College Diesel Technology Career Fair.
Our weld shop team conceived the mini-mixer truck concept. The goal was to build a miniature model to represent Manatt’s at local events. Various options were considered through discussions with Greg Manatt and the team, from remote-controlled trucks to push-carts. The mini-mixer truck concept was adopted and approved in April, and the team got to work. The truck is hand-made from flat steel and aluminum and 100% born from the talented teams in our Brooklyn facilities. Rodney Christy, Cory Wirth, Dale Frascht, Todd Kriegel, James Weiermann, Curtis Klein, Jeremiah Eggert, Rick Hurst, Josh Schnebbe, and many others contributed time and talent to complete this unique project. A special shout-out goes to Rodney Christy the welder/ fabricator, Jeremiah Eggert our painter, and Todd Kriegel from the parts team, for their talents and hard work to make this project come to life.
As we wrap up 2022 amidst continued economic uncertainty, we are celebrating 2022 as a landmark year of growth and improvement for our Shops and Equipment teams.
At Manatt’s, we believe in human potential. We believe each team member is worth investing in and supporting. We work hard because we believe in what we’re doing, we are committed to excellence, and we are committed to each other. Our shop’s team has put intense focus and energy into training and developing new technicians. Brandon Slaubaugh, Corporate Shops Manager, joined Manatt’s in 2021. His work on developing training and apprenticeship programs have been crucial to our initial success. Tyler Vermace was promoted to Training and Technical Support Specialist in January 2022, and his responsibilities are focused on training and development initiatives. Tyler and Brandon worked many hours together in creating technician training and developing process standards that engage both of the seasoned and apprentice-level technicians. The range of training content is extensive.
From expert lead classroom-style training, to hands-on PM and inspection training, the programs benefit tenured employees to apprentice-level technicians. With support from our Human Resources team, Brandon fortified Manatt’s Apprenticeship programs, which now include seven apprenticeships. All individuals with high character
that desire a future in our field. Jill Kienzle, a workforce program representative from South Tama High school, said this about a student who participated: “Once he had someone believe in him and had an employer willing to take a chance on him, his life changed for the better. He is so much happier and more enjoyable to be around. I can never thank you enough for what Manatt’s has provided for him. This opportunity has changed his life and future.”
We are very proud of our apprentices and the effort they are giving to themselves and to us to build a brighter future. Apprenticeship programs are a proven and industry-driven training model that provide a critical talent pipeline in addressing some of our pressing workforce challenges. These programs have been successful and the lives being impacted are evident.
As we wrap up 2022 amidst continued economic uncertainty, we are celebrating 2022 as a landmark year of growth and improvement for our Shops and Equipment teams. There have been many struggles, including supply chain challenges, materials and equipment pricing fluctuation, and Midwest weather. However, we are poised to have an even stronger year in 2023. We welcome the new year and the challenges it will bring.
Heavy construction means work. It’s defined as construction activities on or below the earth’s surface, including excavation, building foundations, grading, filling, demolition, structures, roads, and appurtenances. But I don’t need to define work to this audience. It’s a day in your life. It’s a day in July under the relentless, unforgiving sun. It’s a day away from home on a bitterly cold morning, with the wind whipping across harvested cornfields. Day after day, you bring your skills, expertise, and experience to the job to deliver excellence for our customers in an ever-changing and demanding industry.
Over the last several years, we’ve faced many challenges, the weather being a common underlying theme. The industry has changed, and that in itself is a challenge. Change is hard. It forces us out of our comfort zone. The industry has changed. It’s faster; it’s more competitive. Even our business in heavy construction is impacted by the macro trends other non-construction industries face – i.e., the increased need for dynamic communication, upgraded technology, and digital tools. Adjustments in how we recruit and retain talent need to be addressed thoughtfully and with patience; otherwise not been practiced until recently.
It’s easy to be overwhelmed and disheartened by the challenges we faced this year. Almost every department struggled to fill open positions and faced supply chain issues and pricing fluctuations. However, as we close the 2022 season, I am excited and hopeful for 2023. At Manatt’s, we have history, we have industry expertise, and we have amazing people to that support each other. These are unique attributes, especially in our industry.
From my perspective, it was a strong year. Measurements and metrics don’t lie; construction volumes for the 2022 season reflect a very productive season. And in the spirit of thinking about things differently, I’ve offered equivalents to add perspective to our work’s staggering impact.
The numbers are impressive. They tell the story of our lives. They demonstrate the excellence and the skillsets we bring to the table every day. We did this together.
We overcame our challenges to work and collaborate as a cross-functional team. Teams helping teams. Division leaders stepping in to work together to help adjust where needed—solving our day-to-day problems while building longer-lasting strategies for the future. And when we change how we think about ourselves, we open ourselves up to new ways of thinking about how the jobs can be completed. Thank you for your fantastic work and contribution. Your talents are seen and appreciated.
And, as always, safety comes first.
454,000 hours worked. This is equivalent to 1 person working 10 hrs./day, 365 days a year, for 124 years.
240,500 CY of concrete placed. This is equivalent to overlaying a county road at 6” for 103 miles or Des Moines to Iowa City. Talk about a road trip! 194,000 LF Subdrain (36.7 miles)
194,000 LF Subdrain installed (36.7 miles). This is equivalent to driving from Brooklyn to Grinnell 3 times on Old 6 road.
276,000 SY Sealcoat applied. This is equivalent to approx. 550 basketball courts.
206,000 SY Stabilization installations. This is equivalent to approx. 410 basketball courts.
1163 CY Concrete pours onto bridges. This is equivalent to 116 10CY mixer trucks.
433,831 Tons of product overlaid. A 2” thick overlay is equivalent to overlaying 740 Football Fields.
Greetings from PCC Paving! As 2022 comes to an end and we close the book on another construction season, I cannot help but view this year in a positive light. Some things seem to click, and although there are always challenges, the differences from year to year can be noticeable. 2022 will set a high bar for what a good year looks like in many respects. This year started with a very successful bidding season that led to a full workload. Fast forward to December, and we were able to substantially complete all of the work that was available to us. PCC Paving took advantage of a dry season and placed more than 840,000 square yards of pavement that required over 240,000 cubic yards of concrete. Thanks largely to our management team’s leadership, coordination, and all our employees’ hard work and commitment.
Some of the highlight projects that come to mind are as follows—two projects on Interstate 80 in Jasper County and Poweshiek County. Roy Piper III’s crew paved Jasper County, and Kenny Alexander’s crew paved Poweshiek County. Both projects were complete reconstructions that had Manatt’s Inc as the prime contractor, therefore leaving the coordination between bridge contractors, dirt contractors, and all of Manatt’s’ crews in the hands of our Project Management team of Craig Kalinay, Jon Puls, and Reece McGrew. Brett Strong’s dirt crew placed all the subbase on both projects. This crew continues to impress; I would put them up against anyone in
the industry at efficiently placing subbase for new pavement. Other projects of note include two more projects on Hwy 30 in Tama and Benton Counties, another year on the Interstate 80 to 380 interchange in Johnson County, and relocation of Hwy 17 in Boone County. Our portable plant crews did excellent work of having plants moved and ready to go job after job, to keep our paving crews paving day after day.
2022 could not have been successful without the support this division receives from the company. The amount of work behind the scenes to get to the finished product of a new highway is sometimes unrecognized, but it’s substantial. From aggregate producers like Wendling Quarries to Manatt’s trucking division, which is the lifeblood of any of our projects, to shops and back-office support. None of it works alone, and I take solace in the fact that we, as a company, have a lot of good people working hard to make our paving projects as successful as possible. We are now in the middle of the 2023 bidding season, looking forward to the opportunities and challenges of the coming year. Merry Christmas and Happy New Year to all!
Like any year, 2022 could not have been successful without the support this division receives from the company. The amount of work behind the scenes to get to the finished product of a new highway is sometimes unrecognized, but it’s substantial.
Despite material and labor shortages, the Metro Paving crew has had a productive 2022. Thankfully, we have not had much wet weather to contend with and have been able to keep projects moving along. Metro Paving has completed 23 projects for approximately 180,000 sq/yds of subdivision and municipal streets using around 44,000 cu/yds of concrete.
A couple of notable jobs for the year include the City of Altoona’s First Avenue reconstruction and the new Costco Store in Ankeny, Iowa.
Altoona 1st Ave consisted of approximately 17,800 sq/yds of 9” PCC with CD baskets. It included a new roundabout and side streets. It is now open to the public, and residents are pleased.
Costco in Ankeny consisted of approximately 19,000 sq/yds of 8” PCC paving with CD baskets with four side streets, a large number of sidewalks, trails, handicap ramps, and a paved median. Manatt’s completed their portion of the project approximately a month ahead of schedule. Costco appears to open its store on its original schedule, as there were 160 days from the groundbreaking until the grand opening in the contract.
Our crew is still paving, and we hope to finish several more subdivisions before “Old Man Winter” catches up with us.
As a November cold spell moves in, I am wrapping up my first full season with the awesome people at Cunningham-Reis. It has been a fun and challenging season. I want to thank everyone at CunninghamReis for making this year successful. It’s the people that make us successful and able to take on any challenging tasks ahead.
We were excited to make significant additions to our equipment fleet in 2022. At the end of June, we purchased a low-hour Terex HC80 crane. This is an 80-ton crawler crane, a significant jump from the 50-ton machines that were our largest cranes previously. The bigger machine will open the door for us to tackle projects differently and allow us to look at some different types of bridge projects. It is also a safer and smoother operation than the old friction-style American cranes that make up the bulk of our existing fleet. It looks nice, and it didn’t take long for our operators to fall in love with it. We hope to add another to the mix soon.
Along with the new crane, we purchased a Diesel Pile Hammer. Again, we were looking for improvements to safety and efficiency, and this D-19 Diesel Hammer was a big improvement in both aspects. The Polk County project we used it on required 55-foot-long HP14x89 piling, which is the most extensive piling IDOT specifies on projects. It was impressive to watch the diesel hammer drive those 55’ piles into the ground in less than 8 minutes. Previous methods would’ve taken over an hour per pile! We are incredibly proud of this addition as well.
The one project that stands out the most from our 2022 list, is the Second Avenue project in Des Moines, IA, with Jasper Construction. There are two bridges on the project, one is a partial deck reconstruction with a deck overlay, and the other is a complete reconstruction. We’re doing the bridge over Birdland Drive, which is the full reconstruction of the CCS bridge. What’s unique about this project is that it is to be done in two stages. The whole Birdland Bridge is 120’ x 70,’ and the stages are broken into 120’ x 32’ and 120’ x 38’, including a sidewalk on one side and a bike trail on the other. It was a different work environment in Des Moines compared to the county road bridges we were accustomed to building. James’ crew did a great job adjusting to this. They completed our portion of the Stage 1 at the beginning of October, and both James’ and Kody’s crews will be moving back in December to work through the winter. Our season’s biggest challenge was recruiting a full labor force for both crews. Thankfully, we could lean on other divisions to help when we needed it most. Thank you to everyone involved in making this season a success!
As we wrap up the 2022 season, we are already looking forward to jumping into 2023. As noted, we will work on Stage 2 of the Second Avenue project in Des Moines, as winter weather allows. We were awarded a 130’ slab bridge in Decatur County in the November IDOT letting for 2023. There continues to be plenty of work to do at the bidding table to finish filling out our 2023 season, but there is a lot of work coming. I know you’re ready for the challenge and I look forward to another successful year. Have a happy new year!
The close of the 2022 season marks the close of my 28th season with Manatt’s. It’s hard to remember the details of those first days, but I remember the ride out of the first jobsite I worked – driving in an old putter truck on a dirt road on a spring day in May. A few things have changed since that day, and I am grateful for my time and the experiences I’ve had along the way. I’d like to think I’m wiser with age and the knowledge that I’m only successful because of the people I have surrounded myself with over the last 28 years. When I started, I didn’t know anything, but I had the opportunity to learn from and alongside some great people.
At Newton Asphalt & Milling, we have a unique opportunity to learn and work alongside a great team of people and work on a variety of projects. It takes a unique individual to do our work and do it well. Our crews are versatile, flexible, and portable. Our Milling division is, by far, the largest in the state, allowing us to take care of our customers timely. The past season was tough; the team compensated for being short-staffed, especially on the asphalt side of the business. However, the team rallied and we completed some great projects this past season.
Tama Co. Hwy 63 MPN 7624 -A collaboration between Newton Asphalt & Milling and Brooklyn PCC Division Grade Crew. The project objective was to mill 5” off the road, rubble existing pavement, process 18,000 tons of millings, place for choke stone base and place 6” of asphalt in three lifts. 45,255 tons of asphalt was produced, hauled, and placed
The Milling crew removed 36,000 tons of asphalt. Half of this tonnage was placed in a windrow on the shoulder of the road, and the other half was hauled to Wendling’s Montour Quarry to be used in the new asphalt mixtures. The material placed in the windrow was crushed in a moving operation and placed on the rubblized grade by Brett Strong’s grading crew.
Mike McDonald and Josh Sadler’s paving crew placed 45,225 tons of asphalt produced by Eric Doty’s portable plant operating at Wendling’s Montour Quarry.
Tama Co. Hwy T-47 MPN 7623 – A collaboration between Newton Asphalt & Milling and Brooklyn PCC Division Grade Crew and Crushing Crew. The project consisted of removal-milling at each end of the project and multiple areas of full-depth patching and placement of
three lifts of asphalt. Once removal was completed, grading and rock placement was provided by Brett Strong’s grade crew. They also placed 16,550 tons of crushed asphalt shoulders. In total, the asphalt and plant crews produced, hauled, and placed 26,835 tons of asphalt.
Tom Dvorak’s Crushing Crew crushed 17,000 tons of asphalt at Wendling Quarries for the rock shoulder. Asphalt was produced by Eric Doty’s portable plant at Wendling’s Montour Quarry.
Marshall Co. Hwy S 52 & E 63 MPN 7629 – Another collaboration between Newton Asphalt & Milling and Brooklyn PCC Division Grade Crew. This project consisted of milling 2” and placing 4” of asphalt. 9,500 tons milled and hauled to Wendling’s Montour Quarry to be used in future asphalt projects. 18,235 tons of asphalt was produced and hauled by Eric Doty’s portable plant operating out of Wendling’s Montour Quarry. Rock shoulders were placed by Brett Strong’s grade crew.
Jasper Co. Ramps Iowa Speedway Drive and Hwy 224 MPN 7619 - Newton Asphalt and Milling project. Night work was required for this project, consisting of milling 3” of asphalt and placing 3” of asphalt. 6,545 tons of milling and asphalt were produced and placed. Milling would start by removing 3” of asphalt, followed by the Asphalt Crew covering it back up the same night. Millings from the Iowa Speedway Drive exit were hauled to a permanent asphalt plant in Newton for future projects. Millings from Hwy 224 exit were hauled to the Kellogg portable plant site for future asphalt projects when the portable plant was in that location.
Jasper Co. Hwy 117 from Colfax to Prairie City MPN 7620 –A Newton Asphalt & Milling project consisting of milling 3”, Cold-inPlace-Recycling, widening the existing road by three feet on each side, and placing 3” of new asphalt. The Milling Division removed 3,225 CY of rock for the pavement widening and millings were hauled to the portable plant site to be used in future projects. Asphalt is produced by Eric Doty’s portable plant sitting at Exit 159. 15,285 tons of product were milled and hauled for this project. 24,1555 tons of asphalt were produced, hauled, and placed when the project wrapped up.
At the end of the 2022 season, 149,125 tons of asphalt were produced by plants 304 and 309. This is just an example of how the Newton Asphalt & Milling division works together as a team to deliver for our clients. It also shows how we can come together as a cross-functional team—working with various divisions of our business. PCC, Wendling, it takes us all working together as one company to be successful. Thank you to the incredible teams that accomplished these projects in 2022. We have a lot of good people with a lot of knowledge about our business. This sets us apart from others and continues to make Manatt’s an industry leader. Keep on crushing.
The team is racing to finish up subdrain work behind the PCC Division on the Boone project and they should finish around the first of December. Even though it may be in the 40’s, it is still cold, starting and finishing the day in the dark. Your efforts are appreciated and it has been a good season for our division this year. The year started slowly with cooler temps and high moisture events earlier in the year- causing a delay in our normal seal-coating start time. 2022 was the first season to combine our two crews into one. Due to some retirements, health issues, and crews trading people, we felt we could be more competitive as one aligned unit. Crew members rose to meet the challenge and highlight true talents in our division. The team demonstrated their tenacity and ability to multitask to get the job done. Reviewing the 2022 season, we had several small projects that added up to a strong year. Looking forward to 2023, we are positioned well with the schedule board with close to 50% of the year already booked. It takes us executing our projects in the most efficient way possible to a standard of excellence we pride ourselves on, which will keep us at the forefront of the industry.
Manatt’s celebrated its 75th Anniversary of being in business this year— a true milestone that many companies have not made. I have had the pleasure of working with all three generations of the Manatt family leadership teams. My parents farmed, so I grew up running farm equipment and knew a hard day’s work and what it meant not to walk away until the job was done. One Sunday after church, Merlin
asked me what I would do with my life. At that time, I wasn’t sure, but he said he had a place for hard-working farm kids in the company and offered me a job. At that time, Merlin and Junie were still very involved in the company’s daily management. The second generation of ownership was taking the reins in the coming years. I started on Curt Manatt’s crew, running equipment on the dirt crew. I did this for three summers before I was hired for full-time employment. The Iowa DOT wanted contractors to provide quality control on their projects, opening a new area within the company. Brad placed me as the manager of the Quality Control Division. That was probably the best exposure I had to the true heart of the company. I worked with crews and plants from both sides of the company, from asphalt paving to PCC paving. Over the years, Manatt’s expanded with the purchases of additional ready-mix plants, quarries, and asphalt companies.
One expansion that sticks in my memory was the purchase of Aggrecon, now Wendling Quarries. The acquisition was to be finalized on December 31st of that year. With a disagreement on rock inventory at the quarries, Brad called and said we need to go and measure all the stockpiles at several locations in Eastern Iowa and Western Illinois before the December 31st deadline. Howard Stewart, Joe Edmundson, and I took off to complete the measurements! This was when you physically measured the stone piles with tapes and survey equipment. We had two days to travel several miles and then compute the data. What I recall most about this adventure was the weather. That week, a cold snap settled into our area, and temperatures plunged to -25/-30. We would leave the hotel room at 5:00 AM and return around 9:00 PM. Once we got back to our rooms, we’d go out and remove the battery
from our pickup and bring it to the room for the night to keep it warm, then put it back the following morning so our trucks would start.
Another project that stands out was when we paved the Keokuk Airport. I was the Quality Control manager on that project. I would start the day around 4:00 AM to get moisture readings run for the batch weights, then move out to make concrete test beams on the grade. Once we were done paving, I had to take the previous day’s test beams to Clapsaddle-Garber’s office in Cedar Rapids. I would strip them out of the form boxes and place them in their water tanks, put the form boxes back together, and get back to Keokuk by midnight to start the process over again.This project ran into November to complete. With rainy and cold weather, I ended up catching a bad cold. That was the last project of the year, so I was able to get promptly laid off. The next day I went to my doctor, who put me in the hospital in intensive care for a week with walking pneumonia for my first week of layoff. Never give up until the job is done! Times have changed, so I don’t recommend anyone doing this, but it was a testament to our “get-it-done” focus.
I am completing my 35th year of full-time employment, with an additional three years of part-time summer work. I started on the Dirt crew, managed the Quality Control Division, and then moved into estimating and managing the Subdrain & Sealcoat Division. We expanded our department to include the Stabilization Division on top of that. Over the years, I have seen many changes in both the company and the people. We have lost some dear friends and gained many.
The first generation were strong, respectful leaders who built the foundation for this company. The second generation were visionaries and could see that it would require growth in quarries, plants, and facilities to expand the company’s reach. The third generation has come from all of this with the most important vision for the next generation. They realized that it wasn’t just equipment and property that built this company; it was the people that have built this company. The old saying is, “You can’t see the tree from the forest.” This may apply to those who have been here for ten years or less. I can genuinely say that this generation of leaders is taking this company forward and doing it with their employees at the forefront of their minds. Please don’t misunderstand me; both generations also valued their people, but it was a silent, strong appreciation and was not a common topic. Our core values of Family, Excellence, and Human Potential are in place and growing. Most people will never witness the changes. But for me, for my journey, I have been blessed with the best leaders and crew members I could ask for.
I truly know that we wouldn’t be where we are today without you putting in the time and hard work, watching the radar at 2:00 AM for the weather and enduring freezing wind chills. Thank you. This run is far from over, and I can’t wait to see what the upcoming years will bring. Hug your kids, kiss your wife or husband, and don’t forget to pet the dog or cat. Thank you.
Synergy is a method in which individuals or organizations pool their resources and efforts to enhance value, productivity, efficacy, and performance more than they could individually. By promoting a diversified yet cooperative workforce, we can maximize our productivity, effectiveness, and performance to increase profits. One of our biggest strengths here at Manatt’s is our diversity among divisions. For example, when we run into an obstacle that we haven’t seen before in Ames, we don’t have to go farther than Manatt’s directory to find a solution. Through our values, we tell each other to be open to opportunity and to maintain an entrepreneurial spirit. We have the opportunity almost every day to collaborate with other divisions to find the most efficient ways to complete tasks and projects.
The Ames division started and ended the year under synergy, albeit a forced proposal at times. The labor market seems to be the last to shake off the pandemic, and we still felt those constraints in 2022. With a shortened dump truck roster, we worked closely with the Brooklyn trucking division to share assets to meet demand. It’s been beneficial for us to have Brooklyn PCC working on Highway 17 in Boone
this year, as they were able to keep our trucks busy on occasion. With the changes to unemployment benefits this year, we were nervous about laying drivers off early. The extra week of material hauls in mid-November to and from Boone’s portable sit and Jeremy Rucker’s sub-drain crew were momentous to our morale. Our concrete guys spent several weeks supporting Todd Nuckolls in the Metro division, where the workload was more abounding and proved valuable to both parties.
We started the year with a substantial amount of work. January 19, 2022 was the single most pivotal letting day I’ve seen in my time with Manatt’s. We took eight jobs between the city of Ames and IDOT lettings for approximately 90,000 tons of asphalt. In the days following, I recall conversations with people concerned about how we could complete the work we had just picked up and still have the capacity to take on the commercial and small city work our other customers have come to expect from us. At the beginning of June, we started our mainline paving work on a small stretch of county road in Story County. Our paving crew would bounce from one mainline project to the next, with a few days between catching up with the city and commercial work. By mid-October, we had knocked out all our mainline work, and everyone could step back and take a deep breath. Our grade, intake, and concrete crews spent most of their time
prepping jobs for the paving crew to come back into town. Iowa State University lots B1 & F took up most of the summer for all three crews. By October, they were all picking away at the bread and butter of our division – city street rehab in Ames. None of us would have guessed we’d have such a lightened load by the middle of November, but that, paired with a couple of inches of snow that fall, made it an easy decision to lay off for the season at the end of the week.
2022 has foreshadowed plenty of challenges we will face in the upcoming months. We are constantly looking to hire – as is everyone in the industry – so hopefully, this offseason, we can hire help and provide everyone some relief. While completing our Story County R38 project this fall, we did a soft rollout on the XBE platform. The software showed its strengths in the first couple of days. It does a great job of pointing out any spots in the paving plan where we are over or under-leveraged in real time so adjustments can be made before the next paving day. It was a soft rollout, so we all used it to watch the production plan. We’re interested to see what challenges and benefits it will present when we decide to use it for subcontractor truck procurement, timecards, and paying subcontracted truckers. The Ready Mix team in Ames has been using electronic timecards for several months. We recently onboarded a couple of our construction crews too. We hit a few snags in the first week, but we believe we’ve
gotten past them and look forward to integrating all of our construction crews this coming spring. While this will no doubt make it easier for the office, we understand there may be some initial frustration with the foreperson and crews entering and coding timecards. Stay optimistic – we’re confident it will become a practical and helpful system once everyone gets used to it.
I want to wrap this up by showing appreciation for everyone working on our job sites every day. We understand the commitment you make to help us have a safe and successful season, and we don’t take that for granted. We want to see everyone return in 2023. Bring a few new faces with you too. Manatt’s recognizes the position we all might be in given the shortened unemployment benefits. I am always here to help, so feel free to stop by my office or call, and we can discuss any questions.
Through our values, we tell each other to be open to opportunity and to maintain an entrepreneurial spirit. We have the opportunity almost every day to collaborate with other divisions to find the most efficient ways to complete tasks and projects.
By the time you are reading this, hopefully, you have had a great holiday season in spending some quality time with friends and family. It is an added bonus that our construction season ends with the beginning of the holidays. I know after a hard year I am always looking to breathe a sigh of relief and spending some extra time with family.
Things were busy for the Eastern Iowa Asphalt Division this year. We had a wide variety of work such as; small parking lots (Plasti Paint & Palmer College), large parking Lots (Love’s Travel Center & Clinton Community College), pickleball courts, Rec Trails (Muscatine & DeWitt), city streets (Clinton, Low Moor, DeWitt & Davenport), county roads (Clinton, Cedar, Muscatine, Scott & Louisa), state highways (Hwy 62, Hwy 64 & Hwy 61), chip seal (City of Clinton & Clinton County), crack-fill / crack-seal, and tennissurfacing (various work in 10 counties). On any given day we were producing mix from three plants, supplying jobs with three different QC/QA requirements, and dispatching trucks across six counties. These are just a few examples. It is really a testament to the skill and versatility of the crews and people in EIA. Thanks, everyone, for your hard work!
As always, thanks for working safely. Enjoy the winter relief and I hope to see everyone for another busy year in the spring of 2023.
It is an honor to write to this audience as a part of Manatt’s Family of Businesses. As I write this, it is hard to believe that I have been with the company for over 90 days. For those I have met, thank you for such a warm welcome. For those I have yet to meet, I look forward to that opportunity in the future. In the meantime, please reach out if I can help you, if you have something to share, or want to say hello.
In the first 90 days of my time with the company, the most common question I received was, “Why Manatt’s?”
For those who do not know, I spent the last 20 years in the sport’s medical world, first as a provider, then in operations, and then on the leadership side. Not exactly something that would scream a move from a Chicago-based large business, to an Iowa-based family construction business.
The reason is simple: the Manatt’s family. A family business where legacy and people are more important than next quarter’s profits, and all of the amazing people and work family that exists in this organization. That statement does not mean we benefit from ignoring elements of the business necessary to provide opportunities for growth and success, as those successes will be shared with our teams. It does mean we will not sacrifice our future and our people to hit a mark tomorrow. This has shown up in two distinct ways in my first 90 days with the company.
First, a continued commitment to taking care of the employees and their families through best-in-class benefits. While inflation and costs have increased, the family decided not to pass any health premium cost increases onto employees. In addition, there were enhancements to plans, such as preventative dental costs no longer being a reduction in the benefit
cap allowed. With the industry expecting 5+% cost increases, this was offset by a desire to assist Manatt’s employees with no “inflation” to their costs in providing health and wellness for those they love.
Secondly, the responsiveness to the changes in unemployment laws in the state of Iowa. In July 2022, a law was signed that reduced the unemployment benefit duration from 26 weeks to 16 weeks. Unfortunately, we believe this change did not consider the seasonality of our work and the DOT restrictions on winter work for the safety of our employees and the people on the roads. Manatt’s owners and leadership teams are committing their time and resources to educate lawmakers on the impact on the industry, the company, and the people. Hopefully, the lack of seasonality is temporary. The next step is to explore opportunities for work out of the state of Iowa and develop partnerships outside our normal local operations. The Human Resources team is ready to help employees with information and support services. If you have questions on these things, please do not hesitate to contact HR.
So “Why Manatt’s?” I met the family, like many of you, in my youth. The move to join the company was not about a particular job title, compensation, or typical reasons for employment. It was an opportunity to be a part of something more; a family. In this case, a work family, where those relationships are more than co-workers. It means that even my kids build life-long next-generation friendships, such as at the 75th anniversary.
As seen here: Lucy Manatt, Brian and Laura Manatt’s youngest daughter, and Harper Sels, Nathan and Lauren Sels, youngest daughter, are enjoying festivities at the 75th Anniversary Celebration in Brooklyn, IA, on August 27th, 2022.
Exciting progress was made in 2022 to lay the foundation for a successful digital transformation. It was a very busy year that included significant change and our team embraced the challenges associated with this journey. In no particular order, the highlights of these changes are:
Transitioned from our on-premises Vista by Viewpoint environment to the Viewpoint/Trimble Construction One Cloud platform. This will allow us to leverage many more tools, continue to see improvements and enhancements to many of our core processes, and provide a foundation for the source of truth for much of our data.
Implemented XBE for logistics and construction operations. This technology will allow us to explore what is possible when it comes to more efficiently moving our trucks and completing construction projects on time, and within budget.
Completed a project with Preferred Strategies to create data models that will serve as foundations for dashboarding and reporting across multiple sources. This will allow us to provide better and more accurate information to those that need it and, most importantly, when they need it.
Completed two foundational projects for both the SD Wan and VoIP, bringing us up to date with our network and connectivity to better communicate between locations. The efforts illustrated above were a heavy lift for many people in the organization. While we still have a long way to go, I am confident that we are building a solid foundation aligned with our core values of Family, Human Potential, and Excellence.
The COVID-19 pandemic was an eye-opener for our industry and company. First and foremost, it revealed to us the incredible resilience of our workforce. In a time when economies were shutting down, and no one knew exactly what would happen next, our people rallied around one another and pushed through. The pandemic also showed us how fragile our supply chain is and how interdependent our industry’s producers, suppliers, and manufacturers truly are. Finally, this global crisis gave us the opportunity to reflect on how rapidly change can happen and how much better off we are when we take a strategic, long-term approach to business. Thus, toward the end of 2021, we formed a Wendling Strategic Planning Team consisting of John Ahlberg, Steve Bohlken, Kaleb DiRico, Drew Frey, Rob Manatt, Tony Manatt, Ande Miller, and Marc Whitman. Over the last 12 months, this team has studied strategic planning, gathered and analyzed data, built models and forecasts, and ultimately put in a lot of hard work. The fruits of this labor are a new purpose, vision, and strategy intended to guide Wendling through the next five years.
Our purpose at Wendling is to support people in their pursuit of a life well-lived. Our visionary goal is to earn a national reputation as a construction aggregates company that is doing things right. What do we mean by “doing things right?”
“Doing things right” means more than providing high-quality products and services. It requires a world-class commitment to human potential, building economic prosperity for employees and the company, and continuing to leave a legacy of
social good. Our core values of family, excellence, and human potential will guide us on this journey as we double down on our belief that putting people over profits is the most responsible way to run a company. Having great people on board will power operational excellence, and others from around the country will want to engage and learn from us about how we operationalize values-based leadership to win on the business side without compromising on the human side. People who never considered working in the mining industry will seek us out for employment because they will be inspired by the stories they hear about the way we work. The Wendling name will be trusted and respected in the communities we serve and the industries we compete in.
I am excited and energized by this vision, and I hope you are too. Our goals may seem lofty, but if we all pull together as a team, we can make our vision a reality. I look forward to sharing more information about our strategy and how each of us plays an essential role in our collective future successes. Thank you, as always, for your hard work and dedication to Wendling!
Our purpose at Wendling is to support people in their pursuit of a life well-lived. Our visionary goal is to earn a national reputation as a construction aggregates company that is doing things right.
At the Blairsferry Specialty Products facility, the team is processing a gravel product and making high-angle sand. The team is using conveyors, a crusher, and a screen to produce the product.
In 2022, our Wendling Cushing Crews found ways to help each other and create synergy as a team. Throughout the year, there were times when our portability teams met for an opportunity to have each other’s back. Several of the portable crews collaborated on a job site with another team to help meet customer needs. They came without hesitation, and the crew’s superintendents had no focus other than to help a coworker of Wendling. Howard Fruehling joined Bill Cohenour at Montour. Travis Galloway and Brian Paup joined forces in Cedar Rapids, and Ryan Feller and Gene Ehlers worked together north of Cedar Rapids.This is one of many examples the Wendling team found an opportunity to help one another succeed and, without fail, have a little fun along the way. There were some tight fits, but the team worked together to find a safe, productive layout and setup. Thanks to all the departments that helped this process operate safely and successfully.
As the year progressed, a customer requested a new high-performing product concept that required some “out-of-the-box” thinking. Redline, a specialty products division, received a request from a golf
course to produce “high-angle sand.” It’s a process that requires crushed river gravel to be washed until it becomes sand-like. Golfers desire this product’s consistency as it provides excellent golf shots out of sand traps where golf balls lie on the surface of the sand versus being buried in the sand. It sounds like a simple product but was quite complex due to the uniqueness of the product. We had to combine crushing and washing equipment to achieve the outcome, along with the help of the Wendling sand, gravel, and shops teams. It was a collaboration of the best minds in the company. The product was produced and sits in a happy customer’s sand bunker. This is just one example where the team found an opportunity to deliver greatness and exceeded expectations in delivering for a customer. Thanks to all involved that allowed this product to be made.
The Wendling leadership team has decided to invest in a customdesigned learning management system (LMS) for our employees. It’s an ongoing project that has now spanned over two years. We aspire to be the best version of ourselves, and this system significantly helps jump-start that process by offering classes tailored to Wendling. It is incredible how much effort and time has been dedicated to this project, with the confidence that it will pay seven-fold for our people and culture. Subject matter experts create learning models alongside
internal resources, our employees, and consultants. Kaleb DiRico, Vice President of Operations, was personally involved in developing classes with two Superintendents, Travis Galloway and Howard Fruehling, and our Safety Director, Mike Miller. Every page was personalized with content directly from our team—including insights and knowledge from their years of experience. These contributors truly live in service to others with their countless hour investment, all while knowing they are positioning Wendling for future success. Thanks to everyone that has participated in helping our current and next generation drive their continuous growth.
We had to combine crushing and washing equipment to achieve the outcome along with the help of the Wendling sand, gravel, and shops teams. It was a collaboration of the best minds in the company.
My original forecast for the 2022 season was robust. At the start of the year, there was plenty of uncertainty. Would Covid be an issue again this season? Would our economy stay stable? What about the supply chain and fuel prices? These are just a few concerns that could move our success needle.
While the rest of the world may swing great distances toward success or failure, I am confident that we, the Manatt Family of Business (MFB), remain steady and sure of ourselves. Here are a few reasons I feel this way:
We are very good at what we do Our vertical integration The history of our company
Let’s look at these one at a time, keeping in mind that this is a year in review article.
We are good at what we do. Our reputation speaks for itself. Our goals for our quality of work are high. When you have the employees we have, you can’t go backward in standards. Our long-standing reputation is always moving up and forward, never down and back. Understanding all the ‘human potential’ we possess within our companies is powerful. If we foster the privilege of teaching, learning, and leading this very talented work pool, we can’t lose.
We support each other. Our diversification in our MFB, as well as the types of work we do; asphalt (and asphalt paving), ready mix, concrete paving, bridges, stone, sand, and gravel help us take the highs and, more importantly, the lows out of our construction season. When one area is slow, another is booming! That’s a good thing, and it is by design.
Our company history: Let’s talk about that briefly. My review of 2022 would be remiss if I didn’t mention the 75th anniversary of our company’s history. I couldn’t be prouder and more humbled by an event full of festivities for families and historical memorabilia, topped off with an evening concert, food, and fun. At dinner Friday, I talked about what family means to our companies. I could bring up the last names of past, present, and future employees with parents, siblings, cousins, in-laws, and out-laws working at the same company. The defining moment for me was when I looked out and saw 230 employees, customers, and suppliers, some of whom have been with us for thirty years or more. My past years’ peers, mentors, teachers, advisors, but most of all ‘friends’ in front of me. I was humbled to tears. What a great feeling – BLESSED! I felt Merlin’s, Junie’s, and Clair’s presence in the room.
Other events throughout the year were primarily good progress for our company. We had a Manatt’s Family of Businesses strategic planning retreat in October. The presidents of our teams were in attendance, and I am very proud of the work they and some of our best visionaries did during this time away from family and friends. Thank you, team! I just wanted to acknowledge this effort to move our company forward and say how proud I am of them.
The light at the end of the tunnel is obvious. My original forecast for the 2022 season was robust, and I remain focused on the future of our entire group.
Thank you to everyone who helped us celebrate— especially those who stayed and braved the weather in Brooklyn on August 27. Even more, I would like to thank everyone who has helped contribute to 75 years of success. That includes many current and former employees, their families, and those who have supported them while building their legacies and careers with Manatt’s. We could not have done any of this without ALL of you!
There was fun for families with face painting, bounce houses, yard games, excavator challenges, equipment displays, and even a brand new Manatt mini-concrete-mixer truck. There were burgers and brats, soda pop, beer, and fun, with plenty to share with over 1,500 people—a performance by Tyler Rich & JT Hodges from Nashville, TN book ended an exciting evening.
Severe Iowa weather and three inches of rain did its best to thwart the event. But our people and spirit continued to make it happen, and we had fun! A BIG FAMILY THANK YOU to all who put in much effort to make this celebration happen!
75 years is a milestone. It is an occasion to celebrate and an opportunity to look back momentarily and honor those that laid the foundation, but also to look forward as we plan and build a brighter future. Junie founded the business with one truck and a vision. We will continue to build on the mission and vision set forth by our founders while continuing to stay on our path to excellence and ongoing success for the future.
On our 50th Anniversary, Junie Manatt, founder of the company, was quoted as saying, “We’ve done real well. There could have been no way that we could have ever envisioned we’d be where we are today. That’s a pretty good feeling.” Indeed, we have. I like to think about what he’d say today as we celebrate our 75th – I know he’d be proud. Thank you to the great people and families that have made this a reality.
Con el 2022 fresco en el espejo retrovisor, es fácil mirar hacia atrás y reflexionar sobre los numerosos desafíos que enfrentamos el año pasado. La escasez de mano de obra, los problemas con la cadena de suministro y la asignación de productos, por nombrar algunos, agravaron la naturaleza ardua de nuestro trabajo diario y las iniciativas de proyectos. Sin embargo, tuvimos éxito en muchas áreas del negocio, lo que distinguió a Manatt’s como un líder del sector que lucha por las mejoras continuas de procesos, aprovecha las herramientas tecnológicas que aumentan la seguridad y las iniciativas de comunicación, todo esto al mismo tiempo que pone a nuestros clientes y empleados en primer lugar.
El 2022 también marcó el 75to aniversario de nuestra compañía: ¡qué gran hito! Junie fundó la empresa con un camión y una visión y, probablemente, no tenía idea de en qué se convertiría. Ya sea que lo hayan dicho o no, la primera generación sentó las bases de la misión, la visión y los valores que están presentes en la actualidad. Los líderes y empleados talentosos de esta organización han hecho que nuestra compañía sea exitosa y rentable, manteniendo el camino de la excelencia y el éxito continuo.
Cuando reflexiono sobre el camino de la empresa, no puedo pasar por alto las experiencias personales que tuvieron impacto en mi perspectiva de la visión de la compañía y los desafíos que enfrentó. El compromiso de mantenernos fieles a nuestra misión, nuestra visión y nuestros valores puede llevar a crear algo más grande que nosotros mismos, y demostrar que nada es imposible. Para quienes no me conocen en persona, recientemente participé en mi primera competencia Ironman y la completé a principios de este año en Cambridge, Maryland. La competencia Ironman es un triatlón, un evento deportivo que desafía a los competidores a completar tres partes consecutivas de una carrera: nadar 2.4 millas, pedalear 112 millas y correr 26.2 millas. Pero más que eso, Ironman se trata de la excelencia, la pasión y el compromiso, y muestra lo que uno puede lograr si supera sus límites.
Lo primero que las personas me preguntan es: “¿Por qué quería hacerlo?” Seguido de la segunda pregunta, más obvia: “¿No fue difícil?” Yo les explico: “Soy competitivo”. Fue una idea que continuó desarrollándose a medida que mi camino de acondicionamiento físico avanzaba de jugar fútbol americano en la universidad a una simple carrera de 5K en mi vecindario para volver a ponerme en forma y luego a trayectos en bicicleta más largos y carreras más largas a medida que me fortalecía y me comprometía más con la comunidad de atletas que me brindaban apoyo. Y sí, fue difícil. Pero este es el motivo por el cual creo que esta experiencia se aplica a cualquier persona que trabaja en algo que representa un desafío y de
qué manera se aplica a los objetivos comerciales y a nuestras vidas diarias. Para lograr algo extraordinario, uno debe tener un sueño extraordinario con una meta que a la mayoría de las personas pueda parecerle imposible. A continuación, encontrarán tres prácticas simples que usé durante mi programa de entrenamiento y que son temas que creo que todos podemos usar para mejorar a nivel personal y profesional.
COMPROMETERSE CON LA META. Haz algo que valga la pena. Si fuese fácil, todos lo harían. Mi meta era terminar la carrera en doce horas. No me puse yo solo esa meta. Conté con mis compañeros de entrenamiento, con mi entrenador y con mi familia. Una comunidad increíble de personas me apoyó durante este evento. Es verdad para los atletas o para las empresas de cualquier disciplina. Diría que también es cierto para nuestro trabajo en Manatt’s. Es un trabajo arduo, lleva muchas horas, en condiciones muy exigentes. Lo que hacemos es importante, con quién lo hacemos es importante, y para tener éxito, debemos mantenernos concentrados en nuestras metas alineadas, en el compromiso compartido y en una visión compartida para el futuro. Estamos dejando huellas, y ha sido así durante 75 años. Cuando miro hacia el futuro, debemos mantener esa mentalidad en primer plano y trabajar como un equipo unido.
NO TENER MIEDO. A pesar de que mi meta suene simple, no podría haber terminado la competencia si hubiera dejado que la falta de confianza en mí mismo y el miedo impulsaran mi decisión de competir. Cuanto más entrenaba y más me concentraba en convertirme en la mejor versión de mí mismo, más fuerza y disciplina desarrollaba para ayudarme a alcanzar mi meta. Confié plenamente en mi plan de entrenamiento. Me ayudó a seguir asumiendo la responsabilidad, me enseñó como manejar los fracasos y me preparó para los momentos en que las cosas no salieron como estaba planeado. Hacemos lo mismo en nuestra empresa. Establecemos metas para ayudar a centrarnos en iniciativas clave. Aprendemos de nuestros errores y no tenemos miedo de cometer errores en el futuro. Esto significa que no nos damos por vencidos cuando las cosas son difíciles. Ajustamos el plan y seguimos avanzando. A veces hay que avanzar lento para avanzar rápido. No podemos quedarnos quietos; el mundo seguirá su camino. En Manatt’s, hacemos más que lo esperado y aprovechamos las oportunidades de innovar en nuestros procesos. Estos son desafíos complicados y con frecuencia no hay un camino claro hacia el futuro. No debemos tener miedo cuando le damos la bienvenida al camino que surge para un futuro en el que todos nos beneficiaremos.
ALCANZAR EL ÉXITO. No comencé mi camino de acondicionamiento físico con una competencia Ironman en mente. Al principio, encontré un grupo de personas que me presentaron un desafío, que me mostraron un camino diferente y que me demostraron lo importante que es no darse por vencido. Recuerdo el primer día de entrenamiento de 100 millas en mi bicicleta. Me había bajado de la bicicleta, estaba de pie en medio del camino, a 50 millas de casa, subiendo el Madera
Canyon en Arizona, y me dio un calambre en todo el cuerpo. No podía pedalear. No me podía mover. Casi no podía mantenerme en pie. “¿Y ahora qué hago?”, me pregunté. Sentí que me invadían el pánico y la vergüenza cuando pensé en pedir que me fueran a buscar. Escuché la voz de mi entrenador en mi cabeza que decía: “El entrenamiento para la competencia Ironman es gestión de crisis. Debes aprender a sobreponerte cuando te enfrentas al fracaso, incluidos tu equipo, tu cuerpo y tu mente”. Respiré hondo y decidí seguir adelante. Al principio, caminé, luego pedaleé lentamente y, de a poco, sentí que las piernas recuperaban fuerzas. Llegué a la cima, completé el camino de 50 millas hasta casa y logré mi primer recorrido exitoso de 100 millas en bicicleta. Esto describe nuestro camino en Manatt’s. Hemos enfrentado momentos arduos y difíciles y perseveramos. Hemos aprovechado al máximo nuestras oportunidades y nos destacamos a la vez que disfrutamos el recorrido. Siempre hemos hecho las cosas de la manera correcta, a la manera de Manatt’s. Esto significa mirar hacia adelante, aprender de nuestros errores y apoyar a nuestros compañeros empleados. Empezamos con un camión y una visión. Con el tiempo, construimos a partir de nuestras experiencias, nos enorgullecimos de nuestros valores y demostramos lo que significa ser una compañía líder del sector. La comunidad de personas que son parte de la compañía es única y es el motivo de nuestros 75 años de éxito. Todo es posible si nos mantenemos fieles a nuestra misión, nuestra visión, nuestros valores y creemos en nosotros mismos. No me caben dudas de que estamos en el camino de la excelencia y de que lograremos tener éxito.
Desde nuestros comienzos y hasta la actualidad, hemos operado de acuerdo con tres valores centrales: “Familia”, “Excelencia” y “Potencial humano” como nuestros principios fundacionales. Nos vemos a nosotros mismos como una familia de trabajo extendida. Al final del día, todo se resume en las personas. Quiero agradecer a todos los que contribuyen con su tiempo y talento a esta organización porque han demostrado que nada es imposible.
Bienvenidos a la carrera.
El 2022 ha sido un año único y emocionante. Dos tendencias clave que se han desarrollado durante la última temporada de construcción han creado desafíos y nos han forzado a reevaluar nuestros procesos diarios y nuestros planes comerciales: la escasez de mano de obra y la fluctuación de materiales.
La batalla continua por conseguir mano de obra no es nueva para nosotros, y seguimos buscando oportunidades de reclutar empleados nuevos. Además, continuamos reinvirtiendo en nuestras experiencias de capacitación e incorporación para empoderar y desarrollar a los miembros de los equipos actuales. Creemos en el poder del potencial humano, lo que significa que creemos que vale la pena invertir en cada uno de los miembros de nuestro equipo y apoyarlo.
Por primera vez, pudimos contratar conductores comerciales a través del programa de visas H2B. Quiero brindar un reconocimiento a Arturo Gutierrez, Christian Neria, Joe Guillen y Mike Sanchez por su trabajo para incorporar y para dar la bienvenida a cuatro conductores con visa H2b. En Manatt’s, unirse a nuestro equipo significa unirse a nuestra familia. Estamos orgullosos de estos caballeros que han dado un paso al frente para ayudar a orientar, capacitar y traducir. Demos la bienvenida a Jose “Sr” Rojas Saucedo, Jose “Jr” Rojas Benavides, Humberto “Berto” Sanchez Pinales, y Valentin “Val” Rojas Saucedo a nuestra familia de Ready Mix de Manatt’s. Sabemos que cada persona cuenta cuando brindamos y creamos excelencia para nuestros clientes. Christian, Mike, Art, y Joe han ayudado a desarrollar ayudas de comunicación y han trabajado para garantizar que nuestros conductores H2B cumplen los estándares de excelencia de Ready Mix de Manatt’s. Además, gracias a Sue Esther y Adela Fragoso, y a todo el personal de recursos humanos por todo el trabajo que realizaron para que el programa H2b fuera posible. Trabajamos arduamente porque creemos en lo que estamos haciendo. Tengo confianza en que esta es la dirección correcta. Con el apoyo y la alineación del negocio, sé que continuaremos desarrollando legados exitosos de Manatt’s. La disponibilidad de productos y materiales ha representado un desafío único este año. Hemos visto escasez de productos, cambios de asignación, múltiples incrementos de precios e interrupciones de distribución durante el 2022 en nuestros materiales de entrada. El impacto más significativo ha sido en el cemento. El cemento es un material imprescindible para hacer hormigón. En respuesta a este desafío, estamos incorporando un nuevo tipo de cemento más sustentable llamado Portland Limestone Cement (PLC o tipo 1L). Nuestro equipo de control de calidad ha estado liderando los esfuerzos de esta iniciativa, pero las tolerancias de error son mucho más bajas con este producto. Ha representado un desafío hacer los ajustes necesarios, pero tenemos confianza en el plan a futuro para
resolver la escasez de productos. Este año, el drástico incremento de precios del talco, los áridos y los costos de mano de obra nos llevaron a tener nuestro primer incremento de precios de mitad de año en el hormigón premezclado en más de tres décadas. Probablemente, esto siga siendo un desafío durante el próximo año.
Los problemas más significativos en 2022 han estado relacionados con la operación de la molienda de cemento y problemas logísticos con la distribución del producto. Casi todas las fábricas de cemento del oeste medio tuvieron problemas con los hornos, las instalaciones de molienda, o ambos. Las fábricas de cemento están diseñadas para funcionar las 24 horas, los siete días de la semana, por lo cual cualquier tiempo de inactividad afecta la cantidad de producto disponible.
Las opciones de distribución y transporte han seguido evolucionando durante la temporada 2022. Los bajos niveles de agua en el río Mississippi han afectado la capacidad de transportar materiales a través del río. La mayoría de nuestras plantas de Iowa se alimentan de terminales fluviales y dependen de este transporte. El ferrocarril también ha sido inconstante y la amenaza de huelga a mediados del verano creó retrasos ferroviarios significativos. La mayoría de nuestras plantas del centro de Iowa funcionan con terminales que dependen de las entregas del ferrocarril.
Además, hay una escasez de capacidad de transporte con camiones que afecta de manera directa el transporte en las plantas. Más aún, la escasez de transporte por camión nos afecta cuando debemos acudir a terminales a mayores distancias de plantas de suministro con cemento, cenizas volátiles o escoria, con frecuencia con poco preaviso o sin aviso alguno. Ha requerido coordinación y comunicación entre todos los gerentes de nuestras plantas y el grupo de reparto de Brooklyn para permitirnos tener éxito este año. Mike Novelli, Tim Morrison y sus equipos han mostrado dedicación y pasión que permitieron que Ready Mix tuviera éxito este año. Es un ejemplo de nuestra capacidad de trabajar juntos y apoyarnos unos a otros para superar los desafíos.
El 2022 también es importante dado que marca nuestro 75to año como empresa. Un hito como nuestro 75to aniversario es un momento excelente para reflexionar sobre lo que ha hecho que seamos una gran compañía. Nuestros empleados, nuestros procesos y la voluntad de buscar continuamente la excelencia han logrado que seamos exitosos. El compromiso con la capacitación, la comunicación y el desarrollo general de las personas y los procesos será esencial para la continuidad de nuestro sector.
En Manatt’s, medimos todo lo que hacemos según nuestros valores centrales de Familia, Excelencia y Potencial humano. Nuestra misión afirma: “Hacer todo lo que hacemos de manera segura y mejor que nadie”. Nuestra cultura se ha basado en este concepto durante generaciones. Comenzó en 1947 con la compra de un camión Studebaker y ha seguido creciendo a través del trabajo conjunto hacia un objetivo en común. Esto ha sido verdad para 2022, a medida que equipos interdisciplinarios trabajan juntos para alcanzar nuestras metas y objetivos institucionales. Nuestros equipos de Transporte y Tiendas se han centrado en dos iniciativas estratégicas: empoderar a las personas y las mejoras tecnológicas. En mi opinión, estas son dos estrategias en las que estamos teniendo mejores resultados que nadie en el sector. La inversión en las personas y nuestra inversión en herramientas y tecnología es lo que nos define hoy como compañía. Queremos ser el empleador predilecto. Queremos cuidar a nuestros empleados tal y como establecieron nuestros líderes fundadores hace 75 años. El empoderamiento de las personas se centra en desarrollar e implementar capacitación focalizada en los transportes y programas de desarrollo.
A partir de 2023, los empleados de la división de transportes se denominarán “Conductores profesionales”. Creemos que nuestros empleados hacen más que conducir un vehículo comercial.Son nuestros representantes de atención al cliente de la primera línea al entregar productos a tiempo y según lo acordado. Sus vehículos son carteleras móviles que promueven a nuestra excelente compañía y representan nuestros valores. Queremos mostrar que valoramos sus contribuciones. Durante los últimos seis meses, seis anteriores descripciones de trabajo se han evaluado y actualizado para que se alineen con nuestros valores centrales y destaquen el conjunto de habilidades exclusivas de estos empleados. Durante las reuniones de primavera de 2023, se proporcionará capacitación a todos los empleados para revisar y analizar estas emocionantes actualizaciones.
Brian Schulz, director de Equipos y Tiendas, y Mike Novelli, director de Transporte, y sus equipos han estado completamente centrados en implementar nuevos programas de capacitación y desarrollo.
Sus esfuerzos han transformado nuestra cultura en Brooklyn. Nuestra mayor diferencia son las personas; de nada sirven los equipos sin buenas personas para operarlos.
Las mejoras tecnológicas continúan representando un desafío y un cambio respecto de nuestras prácticas comerciales diarias con la introducción de Lytx y XBE. El programa Lytx tiene como objetivo aumentar la conciencia operativa de nuestros conductores profesionales mediante la identificación de comportamiento riesgoso al conducir a través de Lytx DriveCams. Se desarrollará un programa de recompensas para promover a aquellos conductores que mejoren cada vez más sus habilidades de conducción. Se presentó un programa piloto en 2022, y la ejecución completa del programa está planificada para 2023.
XBE proporciona la solución más amplia, profunda y ambiciosa para transformar la manera en que planificamos, ejecutamos, analizamos y mejoramos nuestras operaciones. A medida que continuamos haciendo crecer y evolucionar la empresa, esta plataforma nos ayuda a tomar decisiones informadas e impulsadas por datos para nuestra compañía.
Cada uno de ustedes y sus contribuciones han hecho que esta compañía sea exitosa. Gracias por sus esfuerzos y dedicación respecto de estas y muchas otras iniciativas institucionales. Gracias por elegir desarrollar sus legados en Manatt’s.
Queremos ser el empleador predilecto. Queremos cuidar a nuestros empleados tal y como establecieron nuestros líderes fundadores hace 75 años.
La construcción pesada significa trabajo. Se define como las actividades de construcción por encima o por debajo de la tierra, incluidas la excavación, la construcción de cimientos, los proyectos de construcción que requieren maquinaria o equipos de movimiento de tierra y cualquier trabajo relacionado con puentes. Pero no es necesario que defina el trabajo para este público. Es un día en sus vidas. Es un día de julio bajo los rayos implacables y abrasadores del sol. Es un día lejos de casa en una mañana gélida, con el viento azotando los campos de maíz cosechado. Día tras día, traen su experiencia, sus habilidades y su experiencia al trabajo para brindarles excelencia a nuestros clientes en un sector exigente y en cambio constante.
Durante varios de los últimos años, hemos enfrentado muchos desafíos, y el clima ha sido un tema subyacente común. El sector ha cambiado, y eso en sí mismo representa un desafío. Los cambios son difíciles. Nos sacan de nuestra zona de bienestar. La industria ha cambiado. Es más rápida; es más competitiva. Aún nuestra empresa de construcción pesada se ve afectada por las macrotendencias que enfrentan otros sectores que no pertenecen a la construcción, esto es, la mayor necesidad de comunicación dinámica, tecnología actualizada y herramientas digitales. Los ajustes en cómo reclutamos y retenemos el talento deben abordarse seriamente y con paciencia; cosa que hasta muy recientemente no se practicaba.
Es fácil sentirse abrumado y descorazonado por los desafíos que enfrentamos este año. Casi todos los departamentos lucharon por contratar personal para los puestos vacantes y enfrentaron problemas con la cadena de suministro y con las fluctuaciones de precios. Sin embargo, con el cierre de la temporada 2022, estoy emocionado y esperanzado de cara al 2023. En Manatt’s, tenemos historia, tenemos experiencia en el sector y tenemos empleados maravillosos que se apoyan unos a otros. Estos son atributos únicos, en especial en nuestro sector.
Desde mi punto de vista, fue un año fuerte. Las mediciones y las métricas no mienten; los volúmenes de construcción de la temporada 2022 reflejan una temporada muy productiva. Y con el objetivo de ver las cosas desde otro punto de vista, estoy ofreciendo equivalencias para poner en perspectiva el impacto significativo de nuestro trabajo. Las cifras son impresionantes. Cuentan la historia de nuestras vidas. Muestran la excelencia y las habilidades que aportamos cada día. Lo logramos juntos. Superamos nuestros desafíos de trabajar y colaborar como un equipo multidisciplinario. Equipos ayudando a
otros equipos. Los líderes de división trabajando juntos para ayudar a hacer ajustes donde son necesarios, resolviendo nuestros problemas del día a día, a la vez que desarrollan estrategias duraderas para el futuro. Y cuando modificamos la manera en que pensamos en nosotros mismos, nos abrimos a nuevas formas de pensar acerca de cómo se pueden completar los trabajos. Gracias por su grandioso trabajo y su contribución. Reconocemos y apreciamos su talento. Y, como siempre, la seguridad es lo principal.
454,000 horas trabajadas. Esto equivale a 1 persona trabajando 10 horas por día, 365 días al año, durante 124 años.
240,500 yardas cúbicas de hormigón colocadas. Esto equivale a recubrir un camino de condado con 6” a lo largo de 103 millas o desde Des Moines hasta la ciudad de Iowa. ¡Todo un viaje!
194,000 pies lineales de desagües subterráneos instalados (36.7 millas). Esto equivale a conducir desde Brooklyn hasta Grinnell 3 veces por el Antiguo camino 6.
276,000 yardas cuadradas de sellador aplicadas. Esto equivale aproximadamente a 550 canchas de baloncesto.
206,000 yardas cuadradas de instalaciones de estabilización. Esto equivale aproximadamente a 410 canchas de baloncesto.
1163 yardas cúbicas de hormigón vertidas en puentes. Esto equivale a 116 camiones mezcladores de 10 yardas cúbicas.
433,831 toneladas de producto colocado. Un recubrimiento grueso de 2” es equivalente a recubrir 740 campos de fútbol americano.