
5 minute read
YACHT
SEA CHANGE
CAN 3D PRINTING TAKE THE HELM IN SUPERYACHT CONSTRUCTION?
BY JAKE POINIER
he promise of faster, less-expensive, and more-precise manufacturing offers obvious appeal for boatbuilders around the world who are incorporating 3D printing into various designs and processes. A first glimpse into the technology’s potential came in 2019, T when the University of Maine’s Advanced Structures and Composites Center
E g
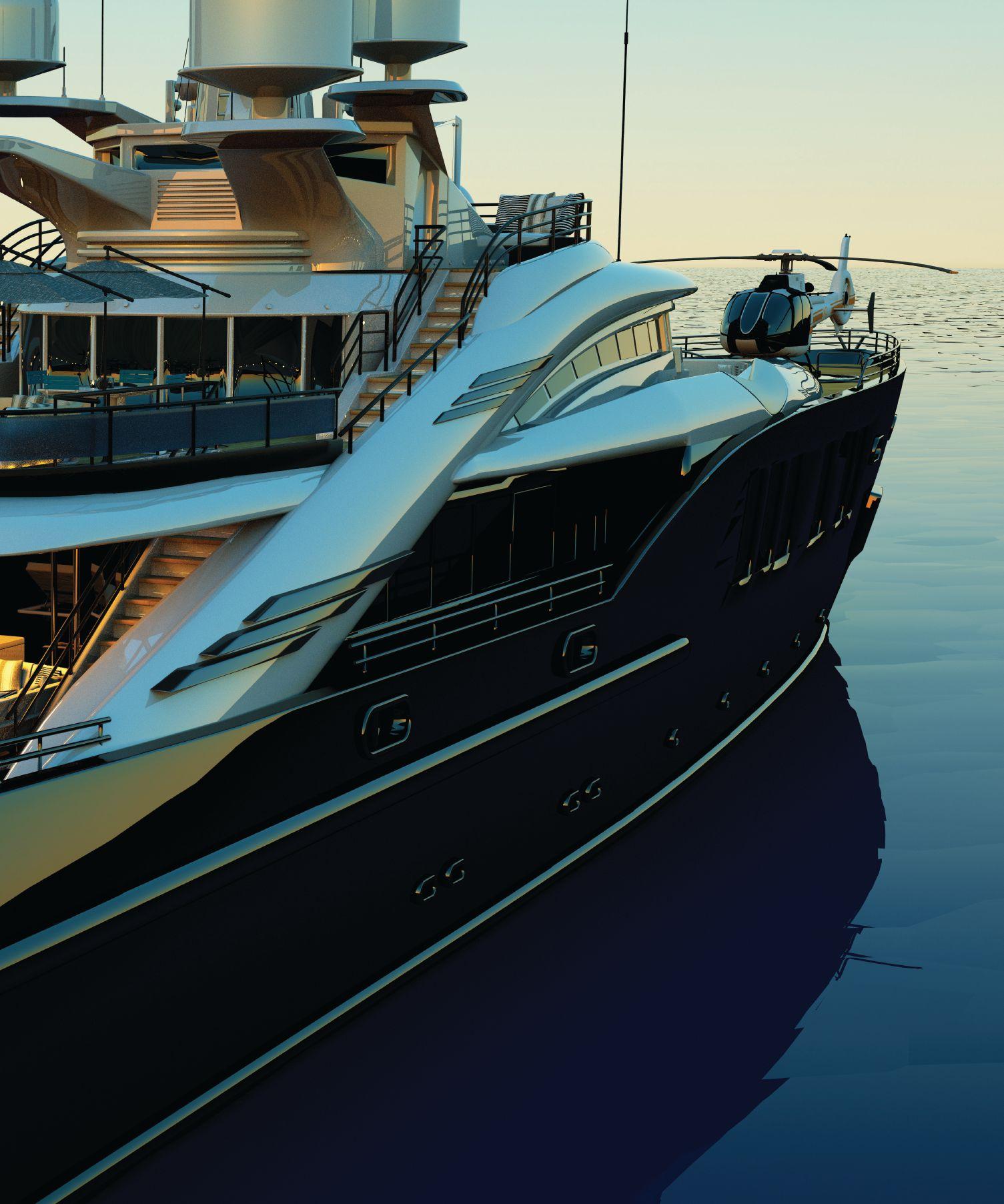
INSIGHT
(ASCC) built 3Dirigo. The 25-foot, 5,000-pound boat was 3D printed in 72 hours, earning Guinness World Records as the largest 3D-printed boat and largest 3D-printed object.
More recently, the university’s mission expanded to work for the U.S. Department of Defense. “It’s under lock and key,” says Dr. Habib Dagher, P.E., founding executive director of ASCC. “But let’s put it this way. We’ve 3D printed vessels quite a bit bigger than the 3Dirigo already, and some of those vessels have made it into an ocean somewhere.”
PLOTTING THE COURSE
While wood, steel or aluminum boats are built using a structure that is sheathed with a hull, fiberglass boats require molds to form the hull, with the structural components added afterwards. With 3D printing, sometimes called additive manufacturing, the equation changes: You can either print the hull, like 3Dirigo, or you can print the mold — and boatbuilders are pursuing both courses.
Tanaruz is among the early entrants aiming at the small boat market, using 3D printing to manufacture hulls out of reclaimed polypropylene and 30% glass fiber. “With my background as a naval engineer, it’s sometimes difficult to transcend seeing things in a traditional way,” says co-owner Alexey Shifman. “Using a 3D printer gives you the possibility of making all sorts of crazy forms. Since the technology is in its infancy, every boat, we learn something new.” 3D printing also offers advantages in manufacturing a wide range of component parts. Hinckley Yachts, which has provided financial and advisory support for ASCC since 2017, used the university’s team to 3D print parts for its Dasher 28-foot all-electric concept powerboat. “The console is a very complex geometrical shape, so we leveraged their capabilities for 3D-printed tooling,” says Scott Bryant, vice president of sales and marketing. “All of the hardware was 3D-printed titanium, as well, which is a nice way to make a custom piece versus traditional casting of stainless.”
Hinckley chief engineer Burr Shaw also cites the example of the transom door on a powerboat. “Using 3D printing allows you to make it much lighter, and the sky’s the limit on customizing the aesthetic,” he says. “Fiberglass molds really dictate a lot of the geometry, and that goes out the window with 3D printed parts.”
Rapid prototyping is yet another benefit of 3-D printing. Michele Tonizzo, CTO and co-founder of Moi Composites, was part of a team that built the MAMBO concept boat, which was billed as the world’s first fiberglass 3-D printed boat and debuted at the Genoa Boat Show in 2020. The boat was designed to be unique rather than mass produced, and helped lead to additional engagements in the maritime space, including a collaboration with Sanlorenzo Yachts. “They were testing parts for a new boat,” Tonizzo says. “When a new iteration was needed, it was possible to develop it in a matter of days.”
OVER THE HORIZON
After printing an entire hull in one go, the next step for ASCC has been to develop materials that meet end-use application requirements for strength, durability and fatigue — essential steps to deliver on the promise of ever-larger boats. The university’s current research and development includes testing high-performance resins, monitoring dozens of manufacturing parameters and crunching the numbers with HighPerformance Computing (HPC) and AI. “If a fly goes across the manufacturing floor, you know exactly what time it went in and what flight path it took,” Dagher says. “A customer wants to be assured the data you collect during the printing process are enough to guarantee the material properties at the end.”
The eventual sea change in the industry is going to be producing usable large parts without the need for molds, an advance for which Shaw projects a fiveyear horizon. “That reduces your capi-
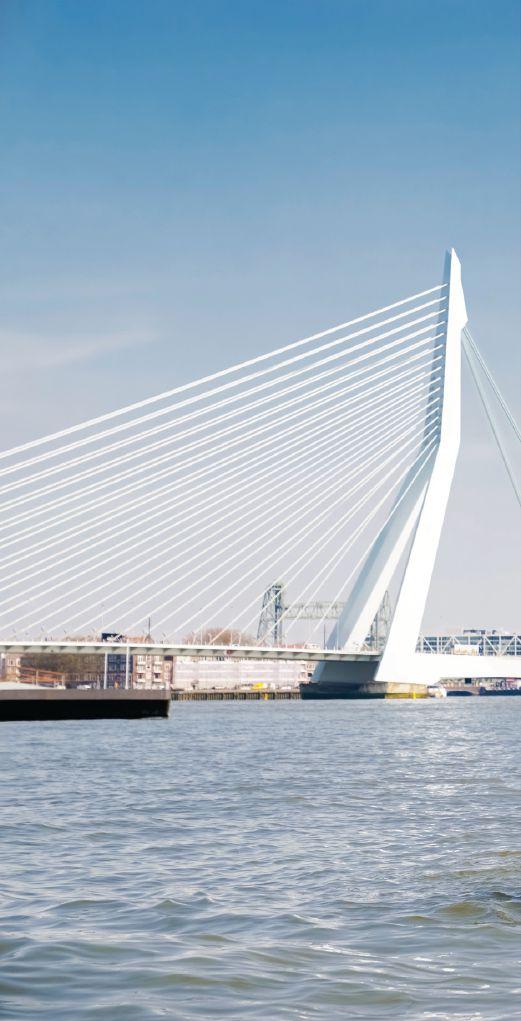
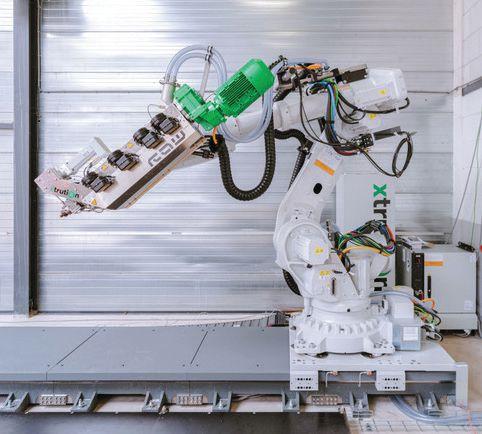
Depending on size and complexity, Tanaruz (photos top and left) can print boats in about 40 to 60 continuous hours, with another 40 hours required for outfitting.
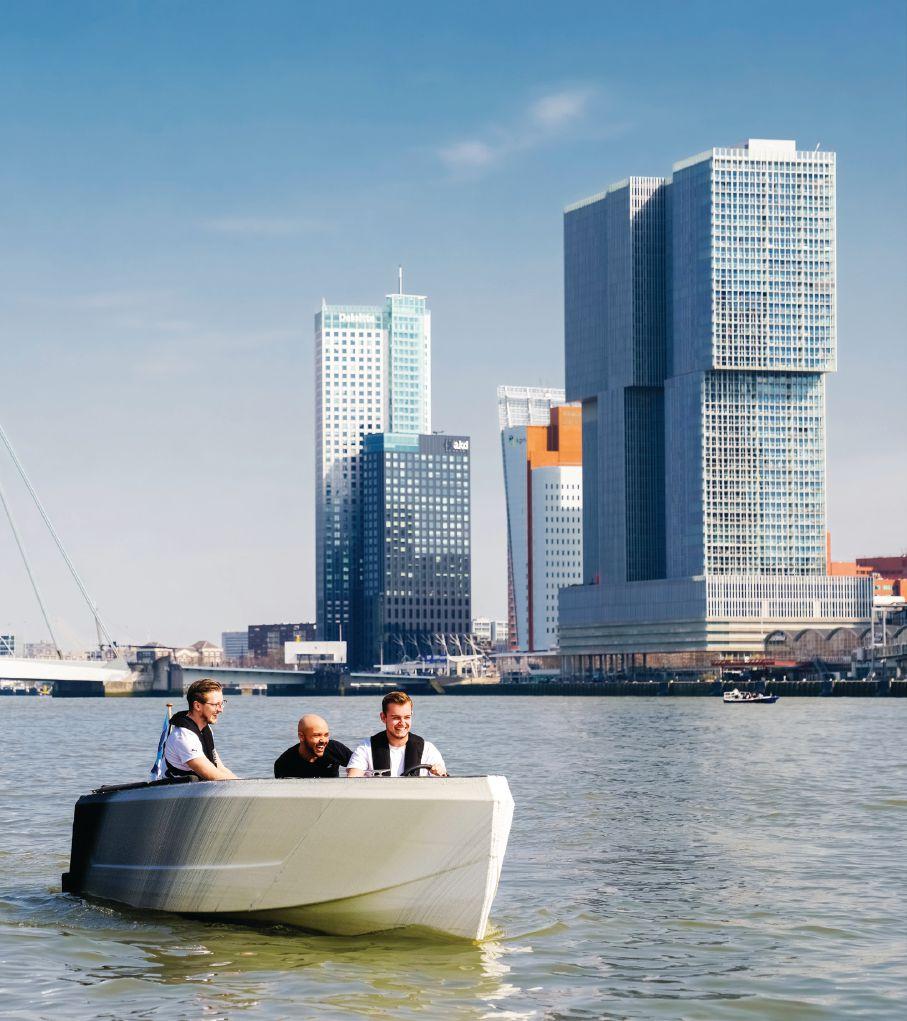

tal cost by a lot, but more importantly, it makes the time to market incredibly quick,” he says. “Instead of taking five or six months to design and build fiberglass tooling, you take that right out of the schedule.”
One of the unknowns, however, is how the 3D printing industry itself develops. “They’re going to go where they see the most growth potential, whether it’s automotive, residential or other products,” says Bryant. “Until there’s something that the marine industry can really leverage to build both cost effectively and at a price that our market will bear, we will probably continue to use molds. 3D printing a hull and deck with a structure that’s comparable in cost, weight and strength to fiberglass would be revolutionary.”
How soon could a fully 3D-printed 40-meter superyacht be cruising the azure waters of the Caribbean? Ultimately, it will depend on advances in materials and increasingly large printers. In the meantime, 3D printing of hardware and smaller parts will continue doing the yeoman’s job of adding flexibility and shaving time off design and construction.
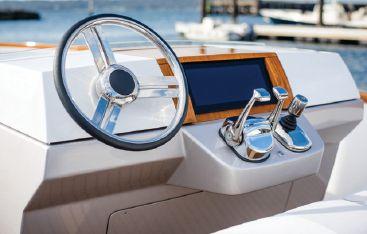
In addition to a 3D-printed console and custom hardware, Hinckley’s Dasher concept boat (photo left and video) includes twin Torqeedo 80-horsepower electric motors and a completely intuitive automatic interface.