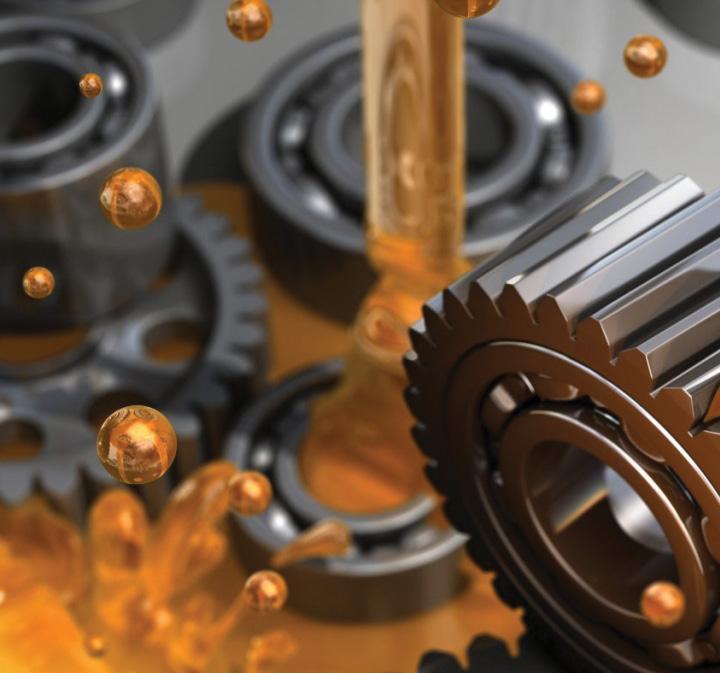
11 minute read
Lubrication Failure and Preventive Ways of Oiling and Greasing
Lubricant

Advertisement
luBrication failure anD preventive ways of oiling anD greasing
Many industries are encountering difficult operating conditions and a variety of business constraints in today's adverse economic climate. The expectation in the construction business is that operations maintain high levels of reliability, efficiency, and safety while also cutting costs and remaining competitive. Fuel is one of the largest operational expenditures for heavy equipment fleet managers; in the long term, even small improvements in fuel efficiency can make a significant impact to a company's bottom line. So, how can operators of construction equipment take advantage of the new oils? The function of lubricants in lowering upfront expenses has sparked a lot of discussion. Lubricants can help you save money on gas while also improving engine performance and protection. This is accomplished by lowering pumping and spinning losses while minimising metalto-metal contact between moving components. Because the oil has a reduced viscosity, it takes less effort to go through the engine and hence flows more quickly. Newer engine types, which operate at greater temperatures, can put conventional lubricants under stress, speeding up the oxidation and degradation of the oil. When it comes to keeping your construction equipment running smoothly, the lubricants you use are crucial. Premium lubricants may cost a little more up front if your dealer or OEM advises them, but the benefits to your machines over time can actually save your operating costs. Lubricant Failure A failure occurs when an objective or expectation is not met. As a result, describing the lubrication goals that were not met is critical in defining a lubricant failure. These objectives are frequently attributed to the lubricant, but
ricants B u l
they are backed up by the lubrication method, system, and procedures. Providing a lubricant film to separate moving parts to minimise friction, wear, and excessive heat generation; acting as a heat-transfer fluid to cool machine components; transferring force/executing work in hydraulic/hydrostatic applications; and allowing the removal of contaminants from the lubricant and lubrication system through a separation method are just a few examples. In addition, the lubricant should prevent varnish and sludge buildup in the system, stay in place even with certain clearances in the lubricated components, simplify/extend relubrication activities and inspections, and protect against rust and corrosion. Achieving these objectives will result in longer machine life and more reliable operation. However, if only one of these objectives is not met, you could call it a lubrication failure. This could refer to a number of different failure modes caused by a single cause or a combination of causes. The lubricant's characteristics and performance, the lubrication system, lubricant handling and application methods, the machine's operation, or pollutants in the environment can all contribute to these issues. Remember that if the lubrication fails, the machine will fail as well. When there is a catastrophic issue, machine failures caused by lubricant failure are usually straightforward to spot. The connection to the lubrication failure may not be obvious in other cases, such as when it is combined with other mechanical/operational factors, when the lubrication failure has affected the machine's performance or efficiency but has not caused a catastrophic problem, or when maintenance practises mask ongoing lubrication problems, such as scheduling more frequent bearing changes to avoid catastrophic failures. A lubrication failure can be defined as a breakdown that occurs when attempting to meet your lubrication objectives. Any lubricationrelated malfunction that jeopardises the machine's reliability or longevity is a more practical definition. Remember that owing to excessive scheduled practises, inaccurate failure mode classification, or a lack of appropriate information to assess the issue, these sorts of failures may not always be tracked to their core causes. Common Lubricant Suffering Points for Construction Operations Heat-sensitive greases can melt and run out of bearings, resulting in bearing failure. Contaminants can enter through grease that does not make a good seal. Some brands make greases that are very sticky and practically immune to water washout, and they can easily carry large loads. They also offers automatic lubrication systems that ensure the proper amount of grease is applied in the right place at the right time. If you're searching for extended oil life while still preserving your engine from the stresses of the job, superior, long-lasting engine oils and LEAP oil analysis will help you safely lengthen oil drain intervals. Water can get into the fuel of diesel equipment that is left outside, causing it to lose power. Soot builds up in injectors, making them unclean. Furthermore, due to environmental concerns, lower-performance diesel fuel is now used in on-road and off-road mobile equipment. Some brands sell diesel fuel improvers to help with these issues. They can clean your fuel pumps, injectors, and combustion chambers, restoring fuel economy, lowering pollutants, and lowering your overall cost per mile or hours of operation.
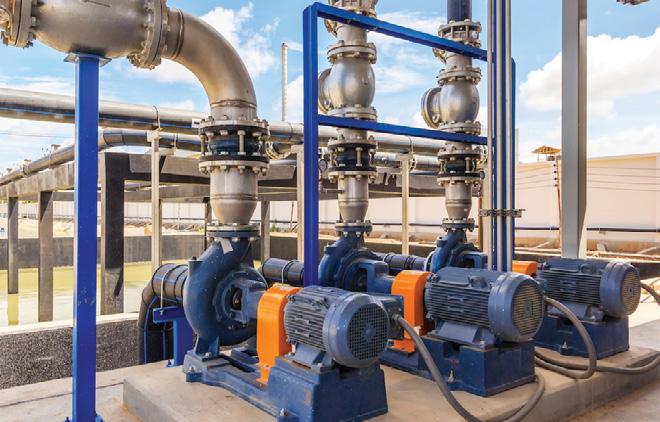
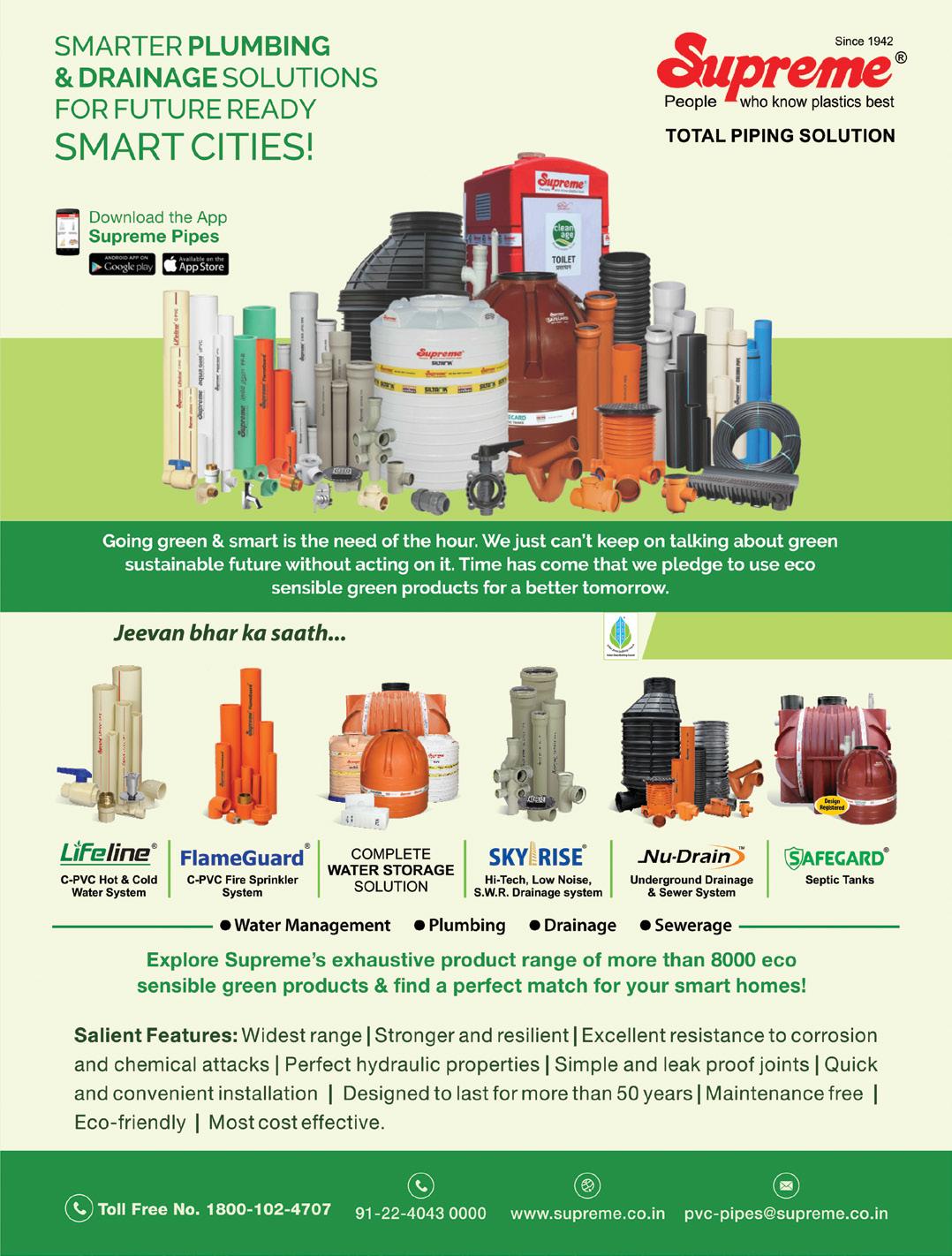
ricants B u l
Do you have rusty, corroded, or frayed wire ropes, cables, or draglines? With LE's entire spectrum of penetrating and coating wire rope lubricants, you can protect your wire rope and cable from high stress loading, shock loading, jerking, and heavy loads. Brands offer a wide range of protective lubrication solutions, including wire rope lubricant applicators to decrease labour costs and assure safe, reliable operation, whether you want lubricant to penetrate to the core or coat and seal. Different Greasing and Oiling Activities There are tasks in a lubrication programme for applying lubricants, analysing their state, and eventually disposing of them once their useful life have expired. Management actions are carried out in addition to these front-line jobs to guarantee that work is executed correctly. The usage of a grease gun is perhaps the most basic lubricating task. However, in recent years, these devices have developed and now include modern technology. Consider the task in respect to the various maintenance philosophies outlined earlier before using a grease gun. Reactive Greasing: "The squeaky wheel gets the grease," you've probably heard. When performing reactive lubrication, you wait until a problem occurs before applying grease to a bearing or machine. Greasing in response to a noise or a raised head, on the other hand, is quite reactive. Damage has already happened by the time these symptoms appear. Preventive Greasing: Greasing a machine according to a calendar date or number of operating hours is common in the industry, although doing so might result in the unit being overgreased or undergreased. Although it can help prevent some failures, maintaining the preventive maintenance (PM) programme will take a lot of work. Predictive Greasing: Greasing prediction systems have grown in popularity in recent years as a result of their ability to pinpoint accurate intervals and grease levels to add. Ultrasound is commonly used to listen to a bearing and determine whether or not lubrication is required. This sort of greasing necessitates a trained crew and the appropriate gear, but it can drastically decrease, if not completely eliminate, the risk of overgreasing a machine. Grease sample and analysis are also becoming increasingly popular for determining the grease's and machine's health, as well as the best relubrication frequency. Proactive Greasing: You may be more proactive with your greasing by balancing all of the best practises. This starts with choosing the appropriate grease for the job. It may also include sampling the grease before to use to ensure its cleanliness in essential applications. Carry out the necessary bearing calculations to ensure the proper grease volume and to direct your future activities. Oil applications follow the same procedure. While you may rely on a machine's rotational motion to supply oil to various internal components, you have influence over a number of other parameters that can indicate success. The burden will vary significantly based on the individual's or organization's perspective. Reactive Oiling: An atypical inspection result, such as a sight glass displaying a low oil level or a chain that appears dry, typically necessitates manually applying oil from a top-up container or spray can. In these situations, fast action is required to guarantee that no long-term damage is caused. A low oil level in splash-lubricated devices might have disastrous consequences. This also would apply to changing the oil only after it has long exceeded its service life. Preventive Oiling: For most non-critical or low-volume equipment, changing oil based on a time period or operational interval is normal, but it can lead to replacing oil that is still excellent or going far too long between oil changes. This is inefficient in terms of both personnel and lubrication. Predictive Oiling: For big oil quantities and essential devices, using oil analysis to determine the optimum oil change interval is the ideal technique. When an oil sample is examined, many of its properties may be identified,
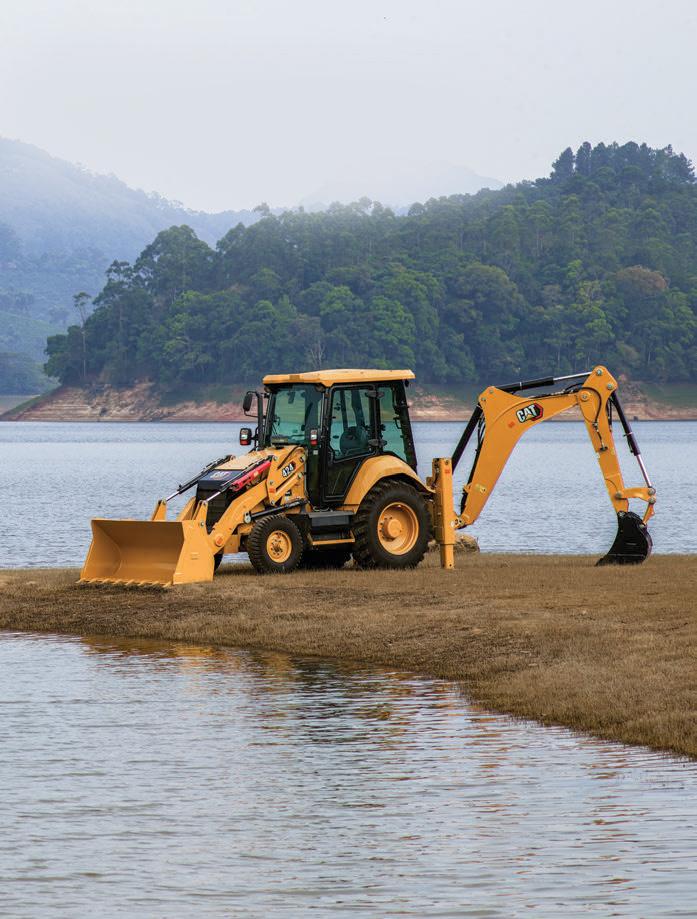
ricants B u l
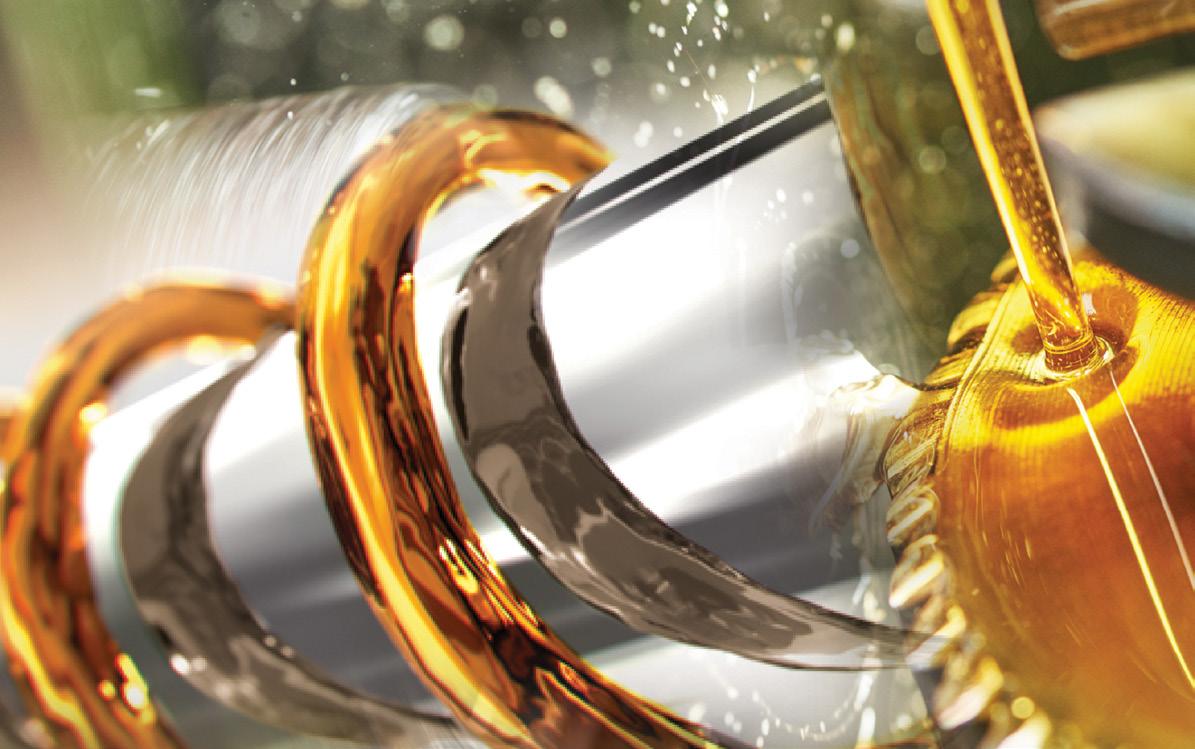
allowing you to evaluate whether it should be kept in service and how much longer it may have. By planning for a shutdown or transferring to an auxiliary machine, you can substantially increase your decision-making abilities and reduce the impact of a lubricant failure. Proactive Oiling: You must eliminate the root reasons of failure to be proactive while oiling a machine. This is performed by ensuring that the correct oil is used, as well as that it is clean and free of defects. To ensure that lubricants are as clean as possible when they reach the machine, you should analyse and enhance your storage and handling processes. This includes purifying the oil prior to use and utilising hermetically sealed transfer containers. The number of failures at your plant will be reduced as a result of these procedures. Inspections are frequently disregarded as a critical component of a world-class lubrication programme. Employees that are exposed to machines on a daily basis are the best source of information for moving your programme forward. While I've discussed how to use the results of inspections to make better lubrication decisions, the inspections themselves must be given more attention. It's not enough to have a checklist or do simple rounds. Examine what you notice about the machine, sight glass, or breather in further detail. Regardless of the ideology used, this will be a very beneficial activity that will bear fruit in all aspects of maintenance. How Lubricant Helps in Lowering the Equipment Cost? Improved fuel economy: When it comes to engines, friction is one of the most crucial factors to consider. You want to reduce friction in the cylinders, bearings, and other moving parts, but you also want the oil to maintain its lubricating properties over time. Older oils have a tendency to degrade – they change quickly when exposed to heat, water, or air. As a result, you'll have to change the oil more frequently. Modern lubricants are far more durable and maintain their properties for a much longer time. They're also made to keep dirt in suspension so it can be absorbed by the filter, which keeps your engine cleaner. All of this means that the machine's overall performance can be maintained for the

duration of the drain interval. The machine's better performance translates to fewer gallons burned per day. For example, corporations frequently utilise 15W-40 viscosity grade oils in their engines. It is conceivable, however, to utilise a lower viscosity engine oil while retaining engine protection and potentially reducing fuel consumption by 0.5 percent. You might enhance your fuel efficiency by switching from a 15W-40 to a 10W-30 oil, for example. Less Maintenance: The majority of premium lubricants are made expressly for the machinery they're meant to be utilised in. For example, Volvo lubricants are designed exclusively for Volvo machines. They're designed for the equipment's specific temperatures, loads, and speeds. Because they're matched, they lubricate better and last longer, resulting in fewer trips to the shop for routine maintenance and repairs. Less Machine Loss: Premium lubricants aid in the reduction of machine losses. When it comes to fuel consumption, it's not simply the amount of friction in your engine or the weight you're carrying that matters. It also refers to the quantity of energy used by the equipment itself. Only 20% of the energy from the fuel is converted into meaningful mechanical work in the hydraulic system and wheels, resulting in total energy losses of around 80% for a typical construction machine. Lower viscosity fluids are easier to pump around, and you can reduce overall losses by lowering friction and heat by using them. Even minor improvements in each system can have a significant impact on total machine efficiency. Friction Optimization: Most lubricants are designed to reduce friction, but there are instances when you want to maximise it. In some circumstances, especially with clutches or a wet brake system, you may want to enhance friction. Obviously, you don't want to reduce friction in a brake system. You want the machine to come to a complete stop, but you also don't want any braking noise. Brake noise is a friction characteristic, and premium lubricants are designed to decrease or eliminate it by optimising friction. Understanding what lubricants are and how they work is critical for improving performance and lowering costs. A prevalent misconception is that an oil is simply something purchased off the market that is required to keep a machine working. Premium oils, on the other hand, go through a development phase with machine development – the two go hand in hand. They're built to operate together to provide superior performance, lower maintenance, and higher trade-in values in the end.
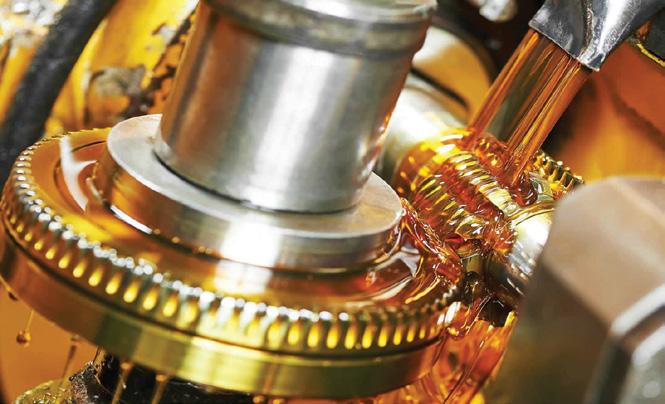