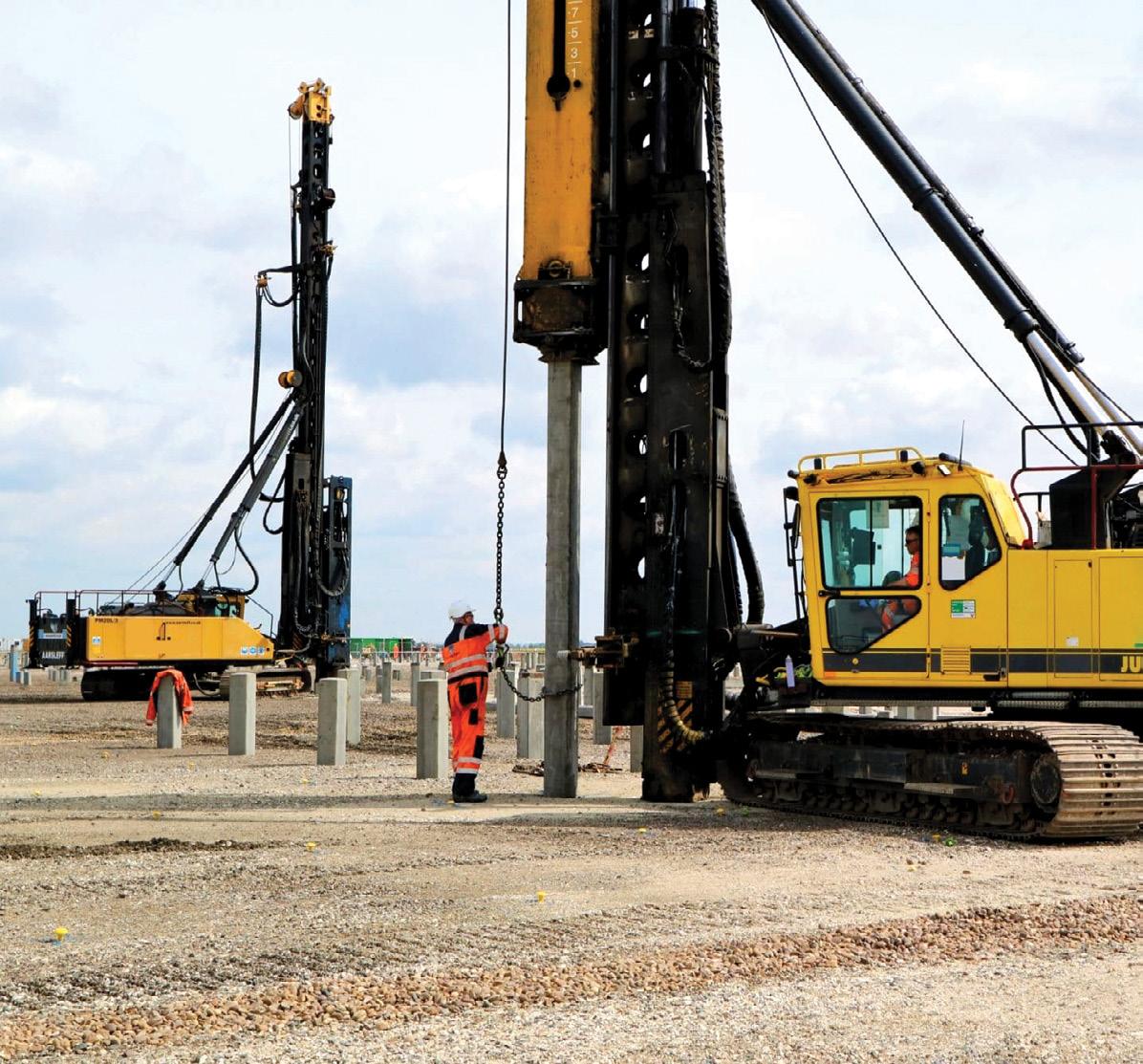
11 minute read
All You Need to Know About the Drilling and Piling Machines
Driling & Piling Machines

Advertisement
all you neeD to Know aBout the Drilling anD piling Machines
A drilling rig is a kind of construction equipment that is used to drill holes in the ground. They can range in size from huge constructions to lightweight structures that can be handled manually by a single person. Drilling rigs can examine the physical qualities of rocks, soil, and groundwater as well as take samples from mineral deposits. They can also be used to construct underground structures such as tunnels, shafts, and pipes. Choosing a Right Drilling Rig A drilling rig could be used for a variety of tasks, such as drilling a well to access a natural resource (water, oil, geothermal energy, etc.), laying foundations, blasting holes in a mine, taking samples from the earth, and so on. It's important to figure out what the drilling rig will be utilised for and what kind of terrain it'll be working in. Different types of drilling rigs are available depending on the terrain: rotary drilling rigs, percussion drilling rigs, down-the-hole drilling rigs, top hammer drilling rigs (with high hammer), and so on. To make the best decision, you must first determine whether the drilling rig will be used for your core business or for occasional operations, and whether you want to take advantage of the most recent innovations or if a machine that has proven its worth over several decades would be more appropriate for you. Safety, dependability, and convenience of use are all critical factors to consider, and they are all intertwined. When operated according to the manufacturer's guidelines, a machine that is reliable and simple to operate promotes user safety. Different Types of Drilling Technology
Rolling Drilling: Rotary drilling digs a hole by grinding the rock with a tool under the weight and rotation of the drill bit. It is mostly utilised in the oil industry. Under the pressure of a drilling fluid pushed into the drill string, the cuttings are brought to the surface.
riling & Piling d
Drilling fluid also aids in the consolidation of the borehole's walls, removing the need to case it as the operation advances. Down-the-hole drilling (also known as rotary percussion drilling or rotary hammer drilling) involves using drilling rigs that use a rotary cutter (drill head) to drill the hole and a pneumatic hammer to hammer the bottom of the hole. Under the pressure of the compressed air used for the hammer, the excavated material rises to the surface. These drilling rigs are powerful and can drill at a rapid rate, particularly in rock. An air injection at the end of the drill pipe propels the water up the borehole for artesian wells (wells where water naturally rises to the surface under groundwater pressure) or geothermal drilling, allowing the operator to immediately evaluate the water flow encountered. This drilling method is utilised for hard and broken ground up to a depth of 4,000 metres. Top hammer drilling employs drilling rigs that use a percussion system as well, but one that is located outside the borehole. They're primarily utilised for small-diameter drilling, such as mineral exploration or tie rod installation in rock. Because the structure of the ground bored through might cause significant deviation, this technique is employed for shallow boreholes. These drilling rigs, on the other hand, can work in any direction. Auger boring is a rotary drilling technique that uses a worm screw (the auger). Unconsolidated clay or sand terrain is best suited for this type of drilling. The worm screw transports the excavated material directly to the surface. Deep drilling may necessitate raising the auger on a regular basis to empty it of the excavated material. Percussion drilling entails shattering the rock with a tool, the drill bit, which is dropped by gravity. Vertical drilling is the only way to employ this sort of drilling. It is required to protect the borehole as it is drilled to keep it from collapsing. When the cuttings obstruct drilling, the drill bit is replaced with a flap valve bailer, and the cuttings are reassembled. The flap valve bailer is a tube that has a tilting flap at the lower half. This tilting flap allows excavated material to be loaded into the tube, which is then delivered to the surface. Pipe jacking is mostly utilised for horizontal pipe installation. The tube is progressively pushed by percussion, with the excavated material being removed either by water injection or an auger at the end of the drilling operation. This method is particularly useful for avoiding vibrations being transmitted to nearby structures while digging a trench. Different types of Drilling Machines and Tools
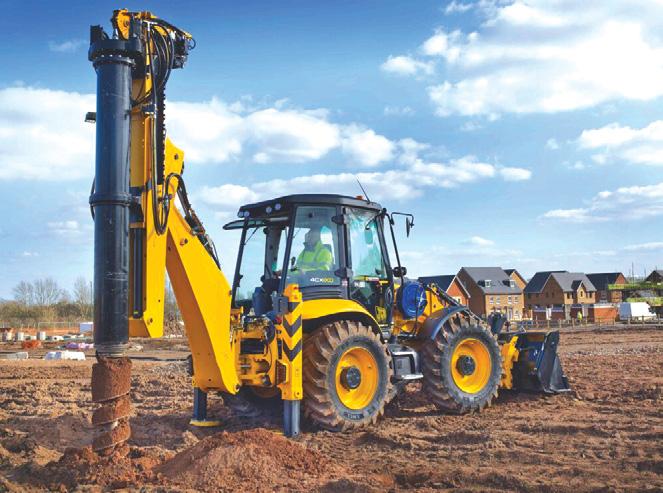
Drilling rigs are divided into two categories: autonomous crawlers and truck or trailer-mounted drilling rigs. Crawler Drills: If it needs to move at a low speed through uneven terrain or on very loose ground, you'll need to go for a crawler. The surface area of the tracks determines the drilling rig's stability. As a result, the drilling rig will be more stable if the tracks are broader. Wide tracks, on the other hand, will wear down and break down the ground more quickly when going, especially when turning. A crawler drilling rig travels at a pace of around 4 km/h. They are therefore better adapted for work that requires little travel. Truck Drills: Drilling rigs installed on trucks or trailers are not self-contained in terms of
25 26 27 AUGUST 2022
PRAGATI MAIDAN, NEW DELHI, INDIA

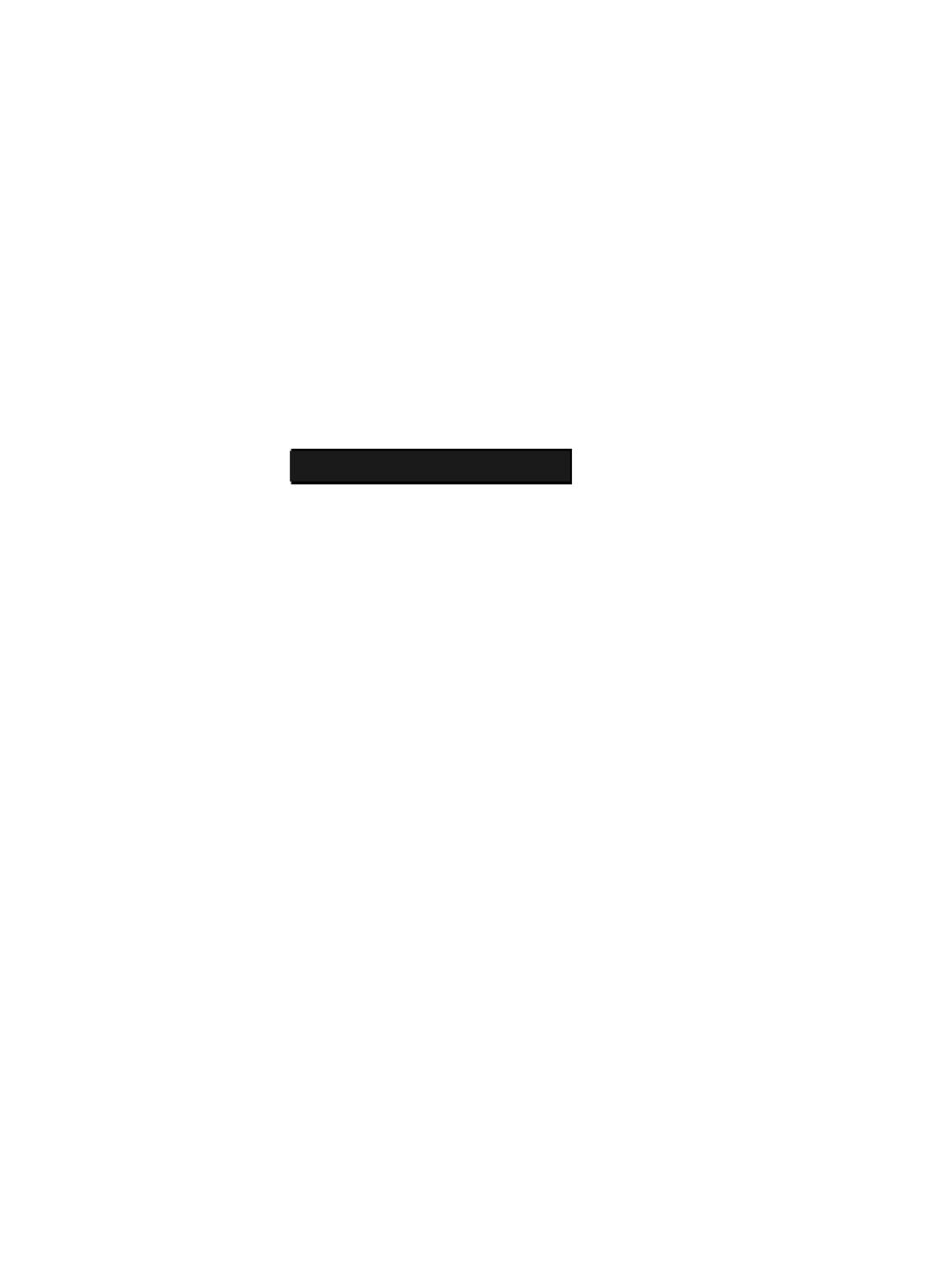
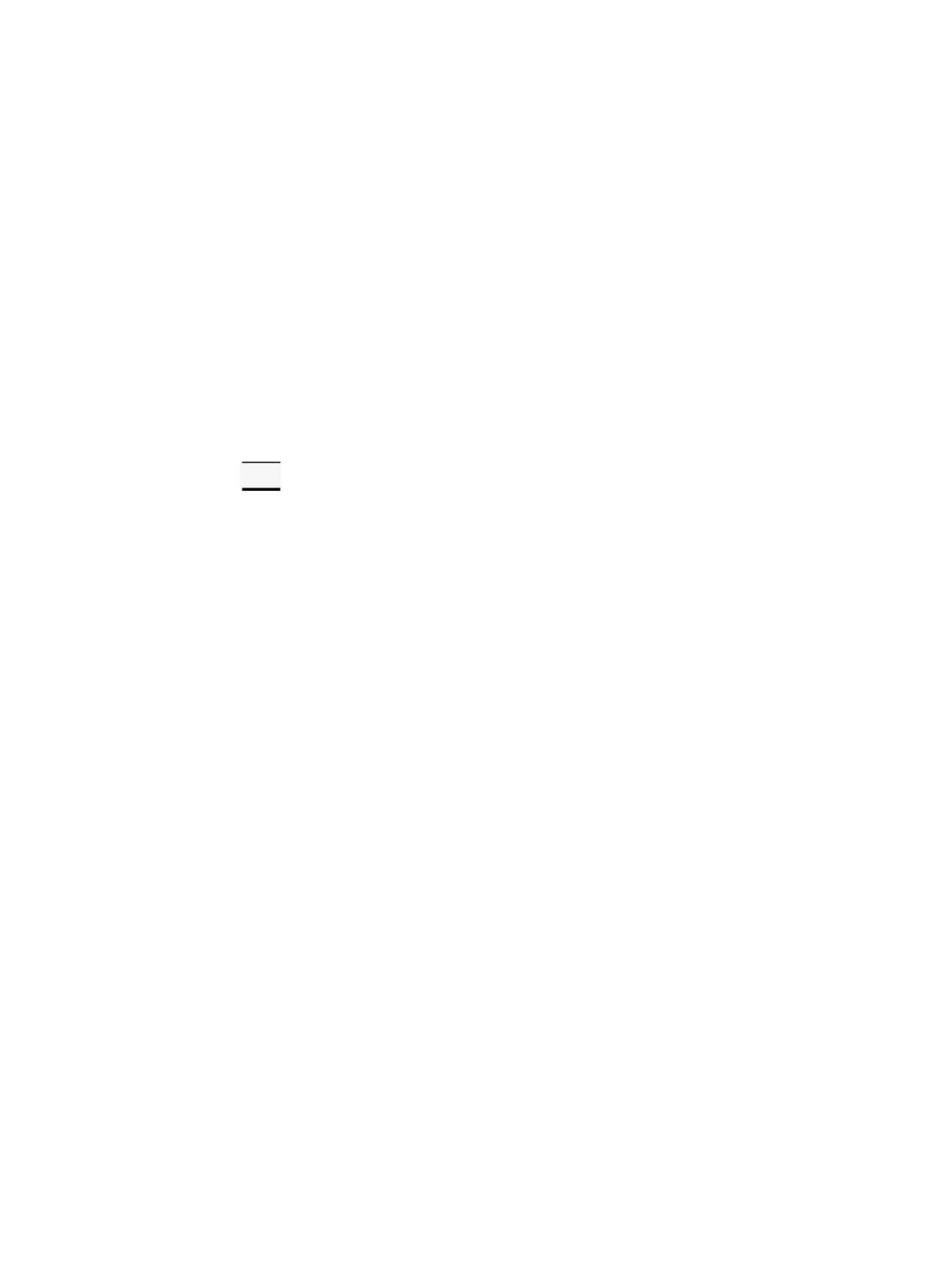

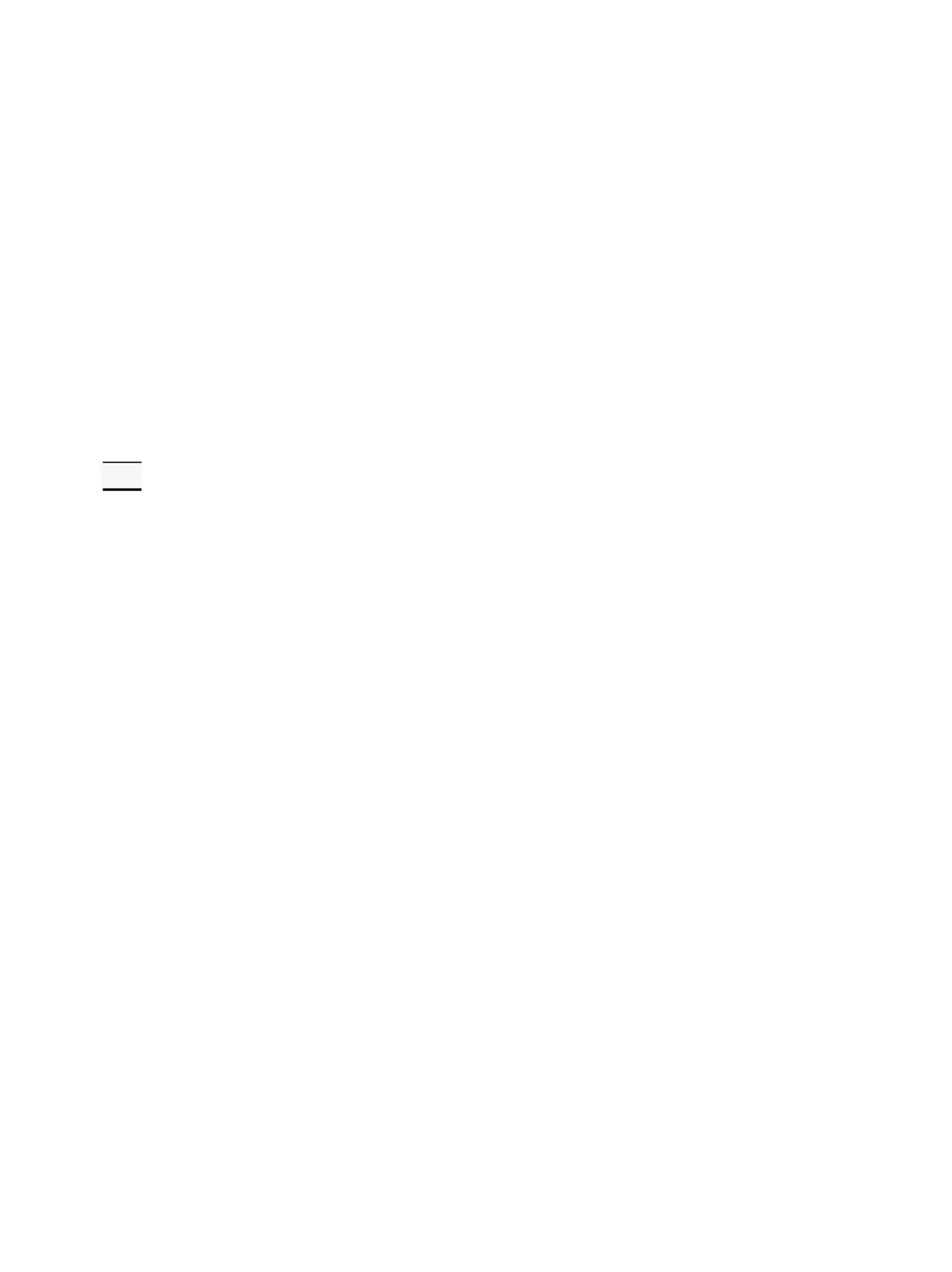


Media Planner
riling & Piling d
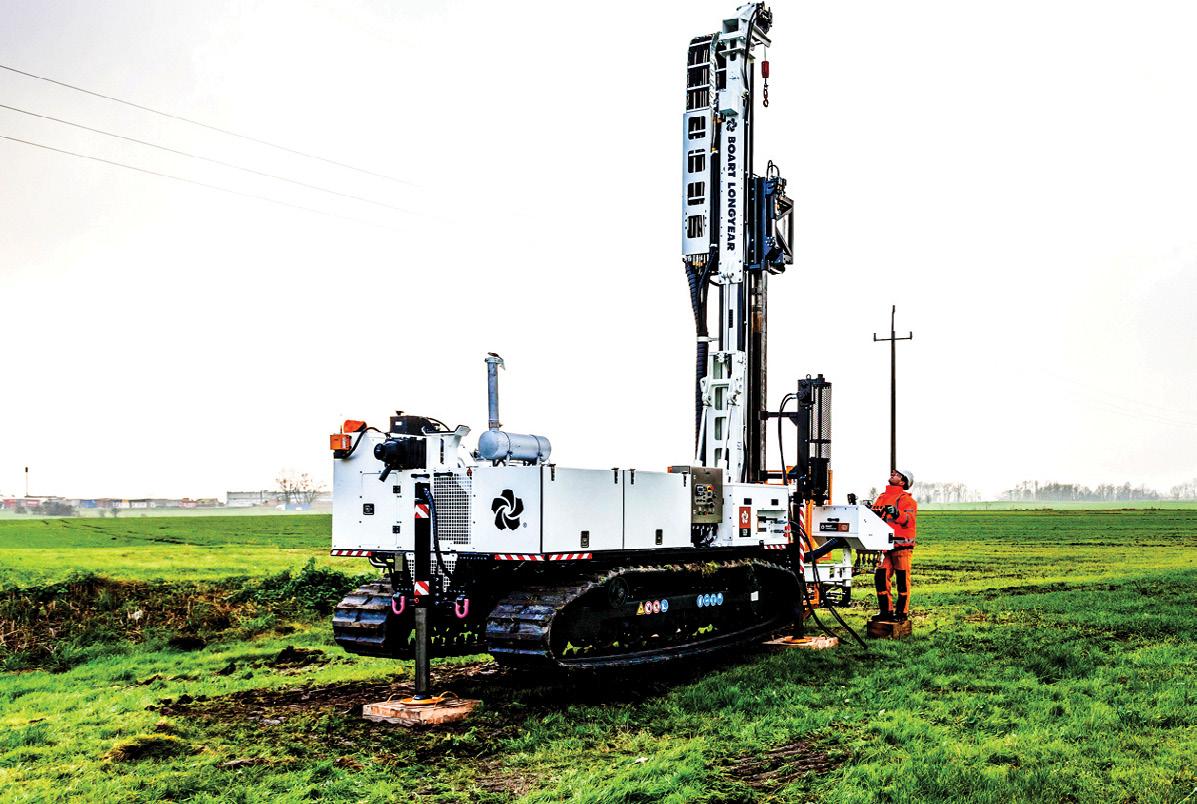
movement or power, which can come from the transport vehicle or a separate generator. They are, nevertheless, far less expensive than crawler drilling rigs. Drilling Buckets: Drilling buckets are used to drill below groundwater level in both cohesive and non-cohesive soil. Drilling buckets can be used to shatter and shred hard soil as well as medium-hard rock. For drill rigs with striker plate, its design enables for a manual or automatic opening mechanism to be installed (for emptying). Soil Bucket: A bucket consists of a hollow, cylindrical part with a hatch on the bottom and a slit joined to one end of the cylinder by a hinge. Cutting teeth are welded to the slit's edge to assist in loading the soil into the cylindrical bucket and to keep it from spilling out when the tool is removed. The hatch is unhooked from the bucket body and the soil is evacuated once the drilling tool has been raised to the surface. The bucket is perfect for excavating loose, cohesion-less soil or soft clay below the water table because it is a closed drilling equipment. Rock Drilling Bucket: Rock Drilling buckets are most commonly used to drill water-bearing sandy soil, sludge, clay, muddy sub clay, sandy gravel, cobble, and worn soft formations. According to bucket diameter, drilling rig type, and soil conditions, the bucket can be constructed as a cylindrical or conical type. The device for opening and shutting can be operated manually, mechanically, or in a combination of ways. Bucket teeth can be welded at various angles depending on formation conditions. The bottom cover is composed of high-strength plate, and the cutting edge is available in single-layer and double-layer configurations; the soil inlet is available in singlebottom and double-bottom configurations as well. Post Hole Driller: Digger for Postholes The Earth Auger is ideal for punching on land, frozen soil, and ice layers, and is frequently used in gardening, tree planting, geophysical research, and road construction, among other things. The drill is composed of synthetic manganese steel and is tougher, allowing it to perform on hard soil, extremely hard soil, clay, frozen soil, and
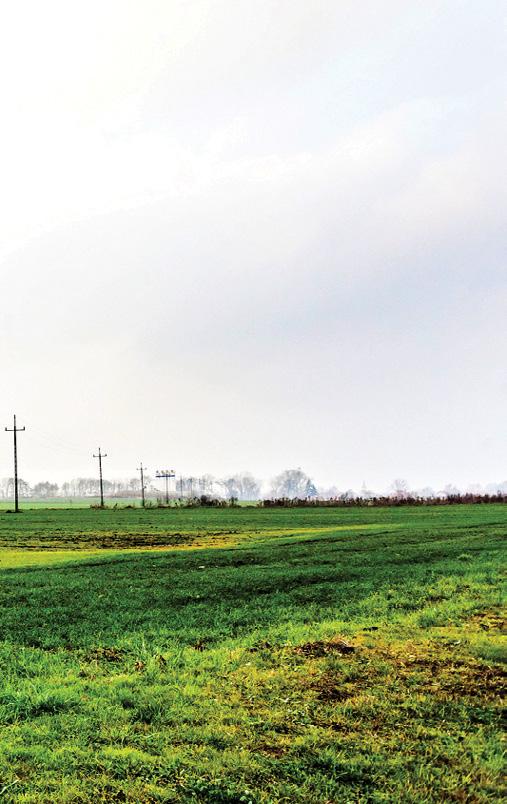
other conditions. It can choose drills with various specifications based on tree species to satisfy the user's requirements. It relieves people of heavy manual labour, is widely used in tree planting, fruit forest planting, fence construction, and fruit tree fertilisation in the autumn, and is suited for all types of terrain. It is also high in efficiency, convenient to transport, and operate in the field. It can be run by a single person or two people, and it is cost-effective.
The major trends in drilling equipment are consistent, whether it's a massive quarry rig or a hand-held diamond coring tool: energy efficiency, autonomy, and ease of use. Because the end goal is the same: maximum output with a shrinking pool of skilled workers, this is the case. Electric drills are quieter than pneumatic drills, and the goal of decreasing noise on the construction site isn't new. While the sounds involved with real drilling cannot be completely eradicated, they can be decreased, as can the noise associated with the rig's motor. Drilling, like all other aspects of construction, is changing as a result of growing digitisation and the data it provides. Surface models are increasingly being used in quarry or building site planning, as well as drill rig communication with third-party cloud services. Piling Rigs
Piling rigs, which feature an impact hammer and a long, columnar, and extendable component, or pile, are often used for drilling in silty clay and sandy soil. Auger boring, drilled percussion, impact-driven, and rotary drilling piling are all options. It has a wide range of uses, including foundation strengthening, cast-in piles, and diaphragm wall installation. Piling rigs in India are available with a variety of features that can be used to dig deep into the earth's subsurface, construct water, oil, or natural gas extraction wells, or install sub-surface fabrications. It is multifunctional in design and can be outfitted with appropriate kits for various foundation and geotechnical building approaches. The piling rig in India is anticipating increased demand for roads, metro railways, and other infrastructure projects. Manufacturers and distributors provide more durable machines that can pile to larger depths with more precision. Piling Rigs with Retractable Crawler: In the primary winch of the most recent machines, single-layer rope winding is used. This prolongs the life of the rope. The model comes with a dedicated chassis that provides exceptional stability. A heavy-duty hydraulic retractable crawler is used on the chassis to provide transport convenience and good travel performance. An adjustable chair, air conditioner, internal and exterior lights, and a windshield wiper are included in the noise-proof operator cabin with FOPS capability (with water injection). The console containing numerous instruments and operation handles make it simple to operate. It also comes with a colour LCD display. The parallelogram articulation construction allows for a greater range of work. The mast's heavily reinforced box-type steel construction design makes it extremely rigid, which improves drilling precision. Maintenance is simplified with a
www.constructionmirror.com
riling & Piling d
standard centralised lubrication system. Piling Rigs for Hard or Soft Soil: Modern piling rigs are capable of working in a variety of soil and hard surface situations. They can bore to a diameter of 3500mm and a depth of 135m. The retractable undercarriage for piling applications is being conceived and developed. The undercarriage provides support and stability. The main and auxiliary winches are mounted on the back of the rotating platform, reducing tipping loads and ensuring great stability when drilling 360 degrees around the rig. The winches use unique rollers that reduce the number of winding layers. Kelly bar is self-assembly and disassembly friendly. It works with a variety of drilling equipment. The spacious cabin improves operator comfort and allows them to work for longer periods of time with less weariness. Operational efficiency is improved because to the innovative intelligent control system. Static pile drivers, dual-purpose drilling rigs, hydraulic crawler drills, and tunnel boring machines are among the models that can be used in underground foundations. They can be used in segments such as urban infrastructure, metro and rapid rail connectivity, bridges and flyovers, and general construction. Piling Rig For Drilling Large Diameter Boreholes: A Pull-down Cylinder is used on piling rigs to exert force on the rotary and is mostly used for drilling big diameter boreholes. The model's articulation system is based on a parallelogram. The control system aids in the monitoring of all working functions, diagnostics of working systems to ensure constant monitoring of sensor and component status, easy conversion in any drilling configuration, and friendly customization of working functions. Drilling with augers or buckets, drilling casings directly with rotary and via casing oscillator, Continuous Flight Auger (CFA), Diaphragm Walls, and Double Head drilling are all done with these sorts of piling rigs. For diverse piling and drilling procedures, the crane control system provides a variety of programme and control possibilities. On colour monitors, service and machine data are also displayed. As a result, the rig is easier to handle for the operator. For autonomous piling, Cruise Control is available, allowing settings such as pull-down speed and rotational speed to be programmed in advance. Demand Drivers
With renewed activity in the foundation and piling equipment industry spurred by projects in roads, metro rails, and other infrastructure developments, manufacturers and distributors are offering more robustly built machines for undertaking piling at deeper depths with greater precision and flexibility in application, and for working in all types of soil and hard subsoil. To accommodate more complicated constructions, the industry is also shifting away from old truck/ tractor mounted rigs and tripod methods and toward modern technology such as hydraulic rotary piling rigs. According to the industry, the modification will result in faster execution, more precise boring, better handling of larger diameters, and deeper bores. CM

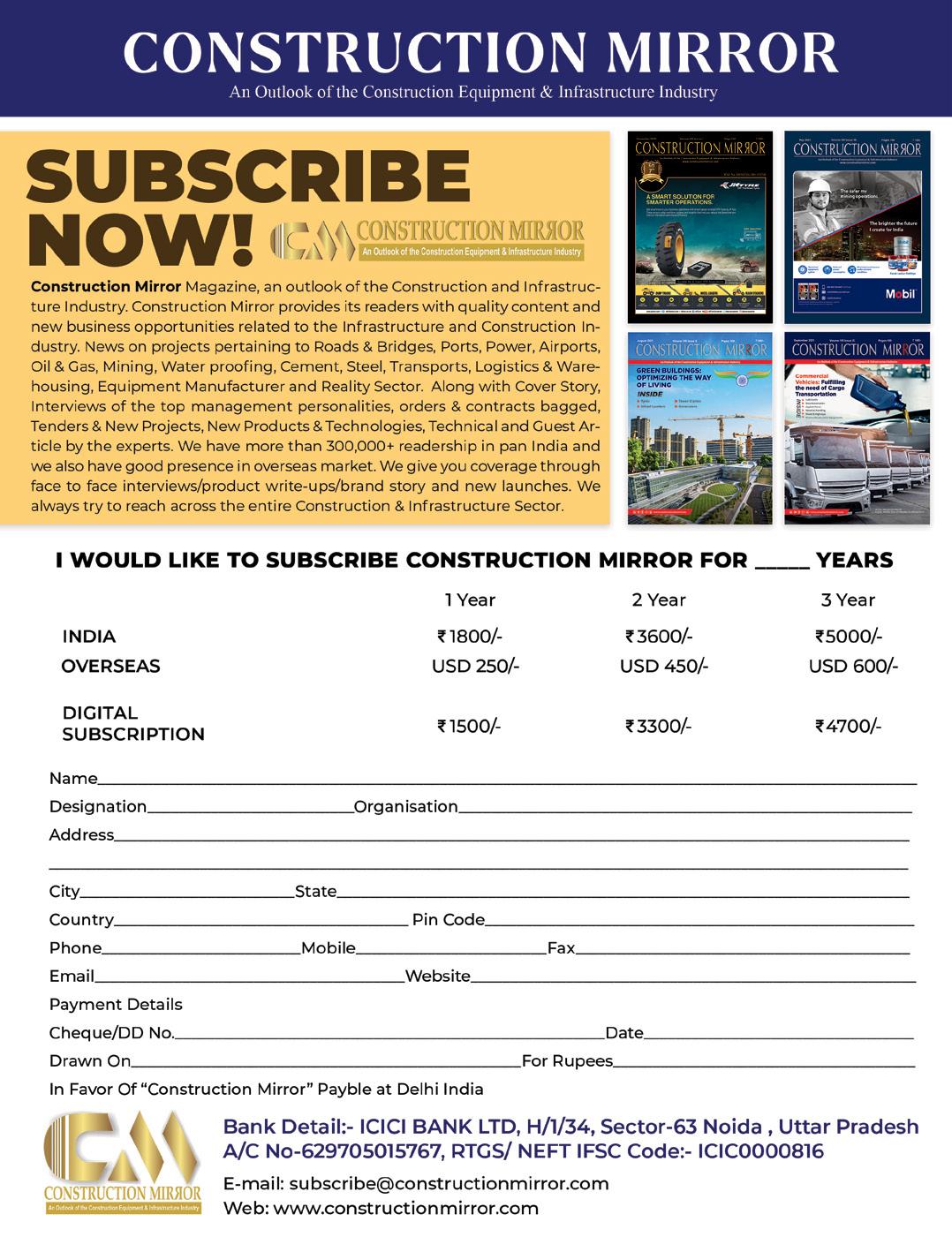