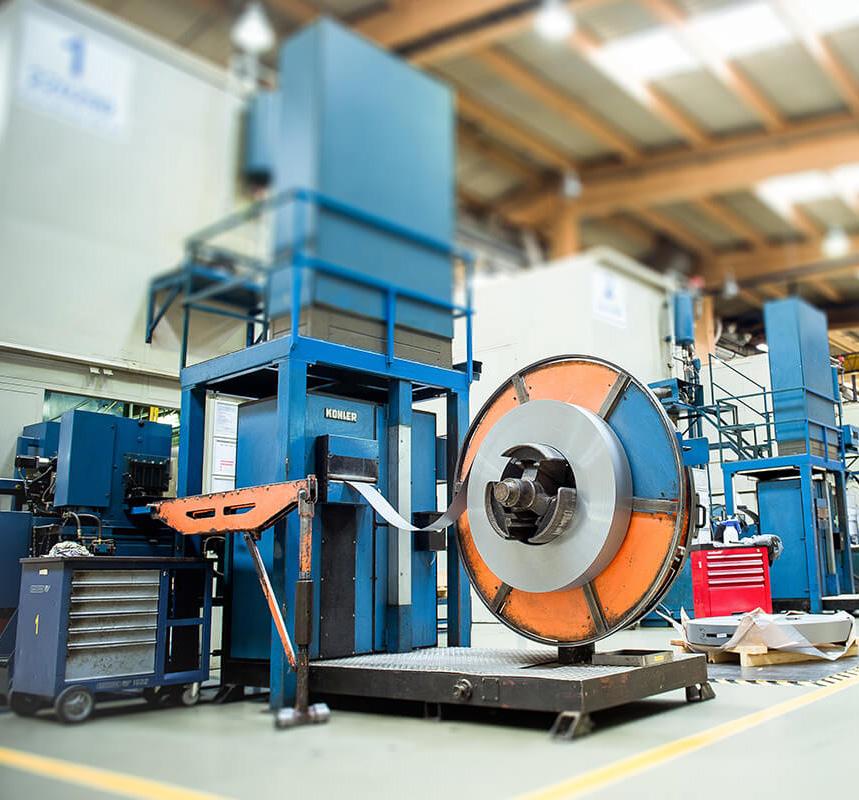
15 minute read
Industry Theme: Stamping & Lamination
Stamping & Lamination

Advertisement
IndIA ARe LookIng FoRWARd to MAkIng tHeIR setuPs As MAnuFACtuRIng bAse FoR suPPLyIng to otHeR CountRIes
Fibre metal laminates (FMLs), as a class of hybrid material taking advantages of both metals and composites, have shown great promise as lightweight structural materials in the transportation industry. Accordingly, manufacturing technologies of FMLs are attracting increasing research interests. This review emphasises the developing technologies of forming FML components, with other aspects related to FML materials being briefly introduced. First, we provide an overall review of the historical background and recent developments of FMLs, their classifications, sheet fabrication processes, and their advantages and disadvantages. Then, various forming technologies are introduced in detail, with a particular focus on stamp forming, which is considered to be the most promising approach for the high-volume production of complexshaped FML components. Furthermore, the deformation modes and defects in forming FMLs are analysed and the challenges encountered in the existing research are thoroughly discussed. Finally, studies on modelling and process simulation of forming FMLs are reviewed and discussed. Based on the comprehensive appraisal of various aspects, current research progress and challenges related to FMLs and their forming technologies are summarised and an outlook of further developments is discussed. Market Drivers & Challenges Spending on Power T&D infra. is expected to boost demand for T/R’s. RGGVY scheme to improve rural electricity infra. & rural household electrification. The electrification drive is expected to provide impetus to demand for distribution T/Rs. Increasing focus on Rural Electrification APDRP 1-2 in order to minimize AT&C losses at the distribution level & improve the financial health of the SEBs. Industrial sector growth, replacement of ageing equips. These reforms are expected to sig. affect demand for T/Rs over the next 4-5 years. Inadequate supply of prime quality CRGO steel is the biggest challenge in the country. CRGO req. is completely met through imports; it is in fact challenging to assess true quality of the material that is used by the
ion T ina M a l ing & MP a sT
T/R manufacturers. India needs 2.5 lakh T of CRGO every year & an appalling 70% of this is scrap grade material. Failure rate of T/Rs – High failure rate of DTs, is a big concern for the T/R industry in India. Avg. operational life of a T/R is b/w 25-30 years; Yet, T/Rs are known to be recalled for repair in as early as 3 years. Failure rate of DTs in India is est. at 10-15%. This is due to the low entry barriers in the DTs market leading to unorganized players entering the market, & competing on the price factor. SEBs historically follows L1 vendor selection criteria, which has led to proliferation of many small players that compromise on quality of T/Rs manufactured. Poor financial Condition of SEBs has restricted pvt. invest. in the power T&D sector, thereby reducing the quality of service from SEBs. Which, in turn, is affecting the capacity building program & transmission of power? The growth in testing infra. has not kept pace with that of production, both, quantitatively & qualitatively. Testing infra. available at India's premier agency, the CPRI is proving short of demand. Manufacturers of large power T/ Rs at times need to send their equip. for testing to overseas facilities like KERI & KEMA which is expensive. Apart from this, huge logistical costs & lead times are also involved. Development, Physical properties & Application of CRGO & CRNGO In recent years, as an aspect of global trend towards energy consumption & preservation of the environment, reduction of electrical consumption has become an extremely essential affair. Due to such global movement of environmental protection, energy saving & noise reduction have been req. for T/Rs, leading to a demand for lower core loss & lower magnetostriction material. Si steel is a soft magnetic material mainly used for T/R cores. It is a material of prime importance in the electrical industry & is been consumed in hundreds of thousands of tons every year. Pure iron has exceptional magnetic properties. One of the properties is its very high saturation magnetization. Pure Iron is, yet not used for electrical applications, instead electrical steels are used in many engineering applications. Electrical steels are also absolutely needed for the electrical power industry, as there are no obvious cost-effective alternative materials available. Most electrical steels are Fe alloys with characteristic alloying additions. Most important alloying elements are Si & Al. Both are strong ferrite-stabilizing elements & their addition may limit the austenite phase stability to the extent that is not present during heat treatment. Currently, India consumes about 2.5 lakh MT PA of CRGO electrical steel & with the growth in demand of transformation capacity the consumption is est. to be 11.5 &13.5 Lakh MT resp. during the XIIth & XIIIth plan period. Against this demand, only SAIL-RSP & Raymond steel has CRGO Production facilities. SAIL produced a small quantity in early 1990s&thereafter discontinued CRGO production. Only 5 global steel makers have the tech. to produce such steel, which India imports around USD 2 bn annually. Plan to produce CRGO has been with steel ministry for quite some time. NML & Tata Steel's proposal for development of CRGO steel in the country through a pilot plant setup at a cost of Rs 500 Cr. is set to take off soon. NML & Tata Steel would set up a pilot plant having a capacity of 3-5 T in Jamshedpur. The 2 will give Rs 170 Cr. each to the project & balance is likely to be funded by the Steel Ministry for procuring plant equip. The Working Group on Steel Industry for XIIth FYP in its report had recommended inclusion of development of CRGO steel as a high value project of national importance. It had also suggested a budgetary allocation of Rs 150 Cr. for research on CRGO development during the XIIth FYP period. There are a couple of public sector CoS including JSW Steel, that have already announced plans to produce CRGO through JV mode, but production from them will take some time to start. Public sector units – SAIL & RINL - have also evinced interest to venture into the area. Yet, Steel Ministry's Empowered Committee (EC) for R&D, said the JVs undertaken by Indian steel firms cannot ensure total tech. transfer. Even if they do, it will cover only normal grades. Steel firms having the tech. to develop CRGO are very reluctant to transfer that to India. Hence, felt that dev of the tech. through indigenous sources through a pilot plant was a necessity. According to CEA, T/R industry of the country has grown to a manufacturing capacity of 800-1000 GVA. Given these daunting req’s, the need for higher capacity T/ Rs is imminent. India's CRGO steel consumption thus would sig. increase from the current level of $ 2 bn. In 2010, around 400 MTs of electric steel were produced globally, making around 29% of total steel production. The share is close to about 50% in Europe & to some extent even sig. higher in North America, Africa, India & the Near East. In total production of GO steel, % of high grade GO steel, HI-B is still around 20%, which is a very small when compared to the benefits of HI-B. This is due to many metallurgical problems observed in production of HI-B such as high slab reheating temp (>1300 OC) for the formation of Austenite phase in desired %, restriction in
increment of Si % & restriction in decreasing the gauge of product. But new developments are also taking place like acquired inhibitor method, in which N2 gas is injected by using NH3 gas after decarburization. This method decreases reheating temp. of slab & hence ensures better performance of electrical machines. Such inferior material causes T/Rs to fail faster debilitating the country's power distribution infra. Thus, CRGO is going to play an imp. role in sustaining India’s economic development. Hence, focus should be given in R&Ds of high grade GO in India. Grain oriented Electrical Steel CRGO is undoubtedly most imp. soft magnetic material in use today. Whether in small T/R, DT or in large T/R& generator, CRGO is a must for the production of energy saving electrical machines. Grain oriented Electrical Steels are iron-Si alloys that provide low core loss & high permeability needed for more efficient & economical electrical T/Rs. CRGO Grain oriented grades of electrical steel are typically used for T/R cores & large generators. Non-oriented Electrical steel CRNGO fully processed steels are iron-Si alloys with varying Si contents & have similar magnetic properties in all directions in plan of the sheet. Non-oriented Electrical steel are principally used for motors, generators, alternators, ballasts, small T/Rs & a variety of other electromagnetic applications. The earliest soft magnetic material was iron, which contained many impurities. Research found that the addition of Si increased resistivity, decreased hysteresis loss, increased permeability & virtually eliminated aging. Substantial quantities of CRGO are used, mainly in power & DTs. Yet, it has not supplanted non-oriented Electrical steel, which is used extensively where a low-cost, low-loss material is needed, particularly in rotating equip. Mention should also be made of the relay steels, used widely in relays, armatures & solenoids. Relay steels contain 1.25-2.5% Si, & are used in DC applications because of better permeability, lower coercive force and freedom from aging. Resistivity, which is quite low in iron, increases markedly with addition of Si. Higher resistivity lessens the core loss by reducing the eddy current component. Raising Si content will lower magnetostriction, but processing becomes more difficult. High Curie temp. of iron will be lowered by alloying elements, but decrease is of little importance to user of CRGO Electrical steels. Magnetization process is influenced by impurities, grain orientation, grain size, strain, strip thickness & surface smoothness. One most important ways to improve soft magnetic materials is to remove impurities, which interfere with domain-wall movement; they are least harmful if present in solid solution. Compared with other commercial steels, Electrical steel is exceptionally pure. Because carbon, an interstitial impurity, can harm low induction permeability, it must be removed before the steel is annealed to develop the final texture. Mechanism for the growth of grains with cube-on-edge orientation during the final anneal is not completely understood. Process involves secondary recrystallization, which, by def, is characterized by accelerated growth of one set of grains in an already recrystallized matrix. For secondary recrystallization, normal grain growth must be inhibited in some manner. As temp. is raised, certain grains break loose from inhibiting forces &

www.electricalmirror.net
ion T ina M a l ing & MP a sT
grow extensively at the expense of their neighbors. Producers know that, on a practical basis, appropriate cold rolling & recrystallization sequences must be carefully followed to obtain the desired secondary recrystallization nuclei & the correct texture. Imports of CRGO steel increased in double-digits for the years 2014 & 2015. On a YoY basis, it grew by 29.9% to USD 433 mn in 2014 & by 18.2% to USD 511.6 mn in 2015. Following this, the imports declined by 5.5% to USD 483.5 mn in 2016. The imports of CRGO steel are mainly made from Japan. Of the total imports (in value terms) of CRGO steel made by India in 2016, 25.6% of the imports were from Japan followed by22.9% from Russian Federation, 14% from Republic of Korea, 10.7% from China, 6.7% from USA. GoI gave nod for policy that provides preference to domestically produced steel to be procured by govt. for its projects. Import duty cut on input products for CRGO steel will reduce cost of its manufacturing. Such move will encourage domestic producers to produce CRGO steel that is otherwise imported, which in turn would mean reduced costs for electrical & power T/R& lamination CoS. What is T/R Lamination You may be wondering as to how the primary & secondary windings are wound around these laminated iron/ steel cores for T/R constructions. The coils are firstly wound on a former which has a cylindrical, rectangular/ oval type cross section to suit the construction of the laminated core. In both the shell & core type T/R constructions, in order to mount the coil windings, the individual laminations are stamped/ punched out from larger steel sheets & formed into strips of thin steel resembling the letters E’s, L’s, U’s & I’s. These lamination stampings when connected together form the req. core shape. For e.g., two E stampings plus 2 enclosing I stampings to give an E-I core forming one element of a standard shell-type T/R core. These individual laminations are tightly butted together during the T/Rs construction to reduce the reluctance of the air gap at the joints producing a highly saturated magnetic flux density. T/R core laminations are usually stacked alternately to each other to produce an overlapping joint with more lamination pairs being added to make up the correct core thickness. Such alternate stacking of laminations also gives T/R the advantage of reduced flux leakage & iron losses. E-I core laminated T/R construction is mostly used in isolation T/Rs, step-up & step-down T/Rs as well as auto T/Rs. Insulation used to prevent the conductors shorting together in a T/R
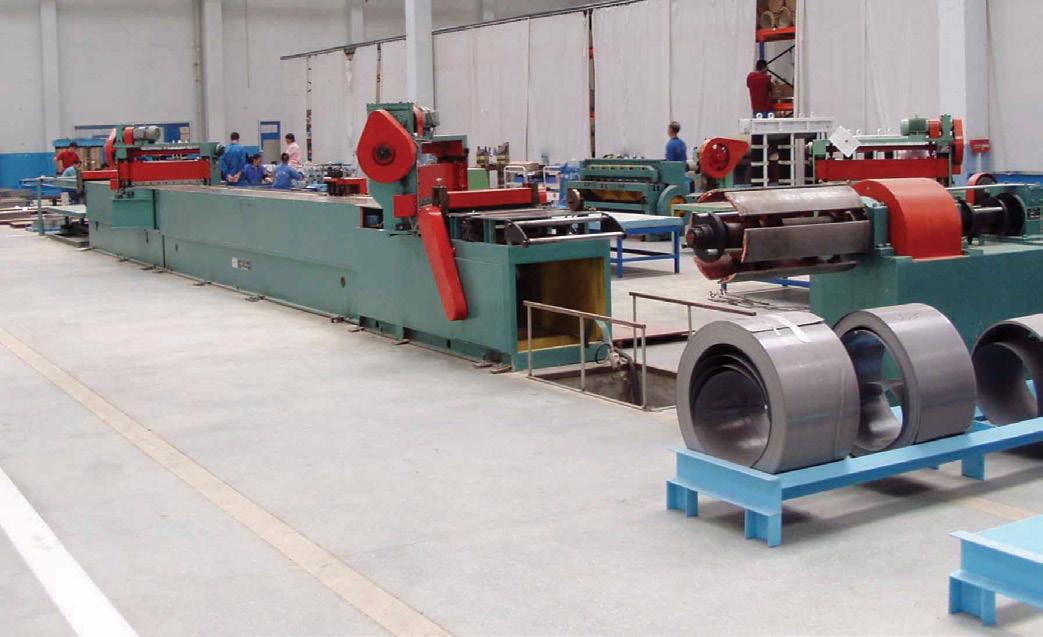
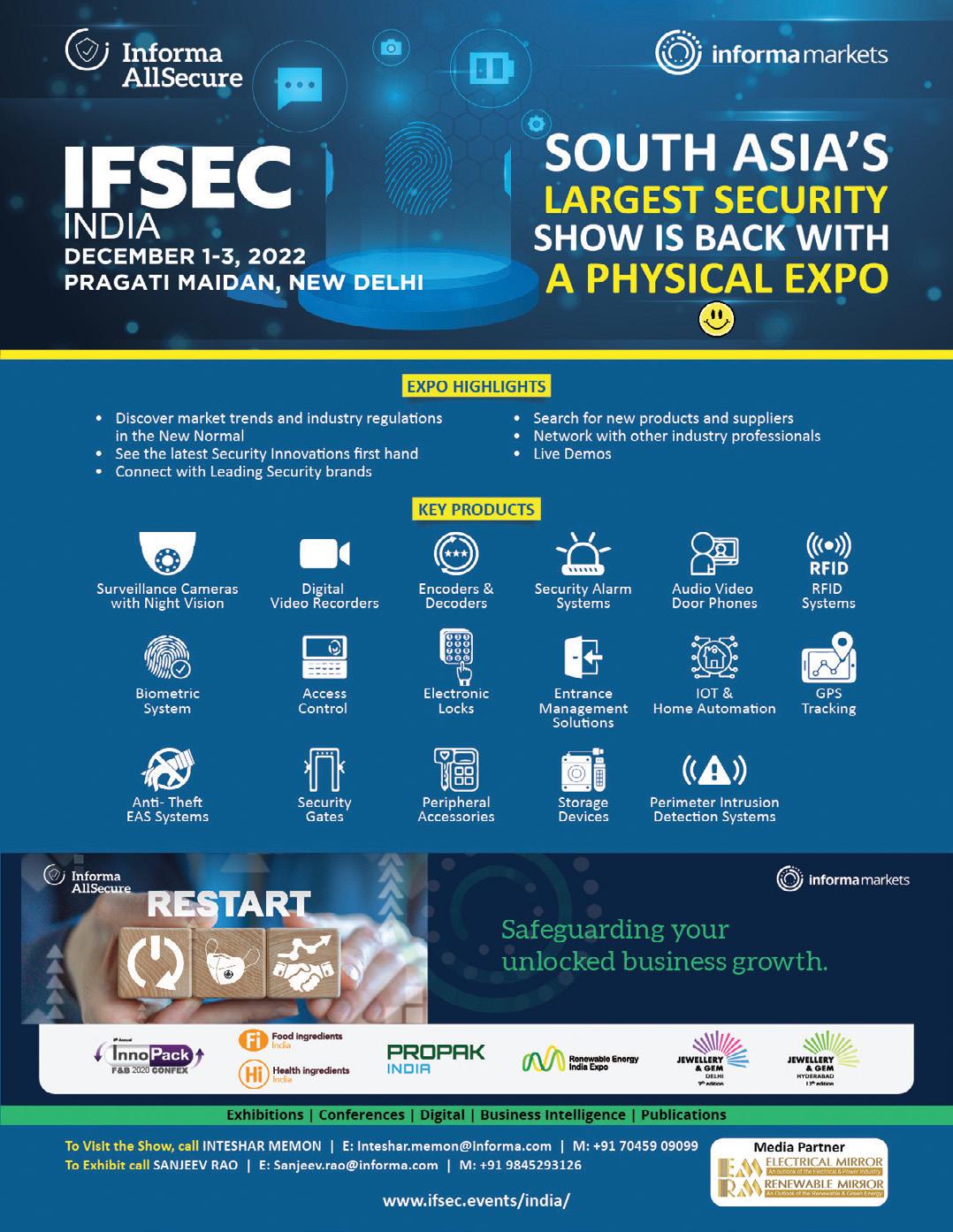
ion T ina M a l ing & MP a sT
is usually a thin layer of varnish/ enamel in air cooled T/Rs. This thin varnish/ enamel paint is painted onto the wire before it is wound around the core. In larger power & DTs conductors are insulated from each other using oil impregnated paper/ cloth. Whole core & windings is immersed & sealed in a protective tank containing T/R oil. T/R oil acts as an insulator & also as a coolant. Eddy current losses within a T/R core cannot be eliminated completely, but they can be greatly reduced & controlled by reducing the thickness of the steel core. Instead of having one big solid iron core as the magnetic core material of the T/R/ coil, the magnetic path is split up into many thin pressed steel shapes called “laminations”. The laminations used in a T/R construction are very thin strips of insulated metal joined together to produce a solid but laminated core. These laminations are insulated from each other by a coat of varnish/ paper to increase effective resistivity of core hence increasing overall resistance to limit flow of eddy currents. The result of all this insulation is that unwanted induced eddy current power-loss in the core is greatly reduced, & it is for this reason why the magnetic iron circuit of every T/R & other electro-magnetic machines are all laminated. Using laminations in a T/R reduces eddy current losses. Losses of energy, which appears as heat due both to hysteresis & to eddy currents in the magnetic path, is known commonly as T/R core losses. Since these losses occur in all magnetic materials as a result of alternating magnetic fields. T/R core losses are always present in a T/R whenever primary is energized, even if no load is connected to secondary winding. Also, these hysteresis & eddy current losses are sometimes referred to as T/R iron losses, since the magnetic flux causing these losses is constant at all loads. Bottlenecks Long overdue demand of T/R Industry to govt. is to pursue CoS like SAIL/ Tata to set up manufacturing plant in India which would save considerable FOREX outflow. Indian power T/R market is set to grow at a CAGR of 14% b/w 2013-18. Yet, challenges are many. Indian steel producers should be forced to set up CRGO plant to meet the demand. India is known to be an active supplier of T/Rs globally. India has always been an exporter of T/Rs & this avenue is set to become even more lucrative in the coming years. Exports from India are diverse including PTs, DTs & even special purpose T/Rs. It is est. that around 15% of India’s production of PTs is destined for int’l markets. With India proving its technological edge by producing even 1200kV T/Rs, surpassing global standards, the country has a very bright future. It is not only developing African & Central Asian economies that are importing from India; India-made T/Rs are even finding their way in developed markets like USA, UK, Canada, South Africa etc. India has been net exporter of T/Rs till now. Several of int’l players who already have base in India are looking forward to making their Indian setups as manufacturing base for supplying to other countries. Indian T/R industry is gradually gaining prominence in developed markets on the basis of its quality & pricing. Domestic T/R industry has potential of becoming manufacturing/ sourcing hub for supply of T/Rs in foreign markets. This market is highly fragmented with a large no. of small & medium enterprises involved in manufacturing processes, & is dominated by organized players. Domestic manufacturing industry is fairly well established with manufacturers having capabilities to develop all type of T/Rs up to the 800 kV & 1,200 kV levels. The industry also exports to several countries including the US, South Africa, Cyprus, Syria & Iraq, apart from Europe. Way Forward India is on the verge of becoming an emerging power nation among developing economies. Availability of electricity is directly linked to the GDP growth of developing economies, India being no exception. Growth of Indian electrical industry & its invests appeal primarily depends on govt. policies. Timely capacity additions to electricity generation, T&D are necessary to improve & sustain GDP growth & reduce demand-supply gap. Indian PT & DT markets are highly dependent on invest’s planned by the GoI for T&D segment &reform programs like RAPDRP & RGGVY. These programs, when fully implemented as scheduled, are expected to drive demand for both PTs & DTs. GoI currently plans to strengthen transmission lines & create a National Grid interconnecting the 5 regions (NR, SR, ER, WR,NER) through creation of Transmission Super Highways & is expected to drive demand for higher-rated PTs. With T&D CoS actively striving to reduce AT&C losses, demand for energy-efficient T/Rs would get a boost. With huge invest’s proposed across sectors such as power, infra., T/Rs market in India is slated for strong growth. Excess capacity in T/R industry in India & entry of new players will increase market competitiveness. Market consolidation over next few years is inevitable. RM
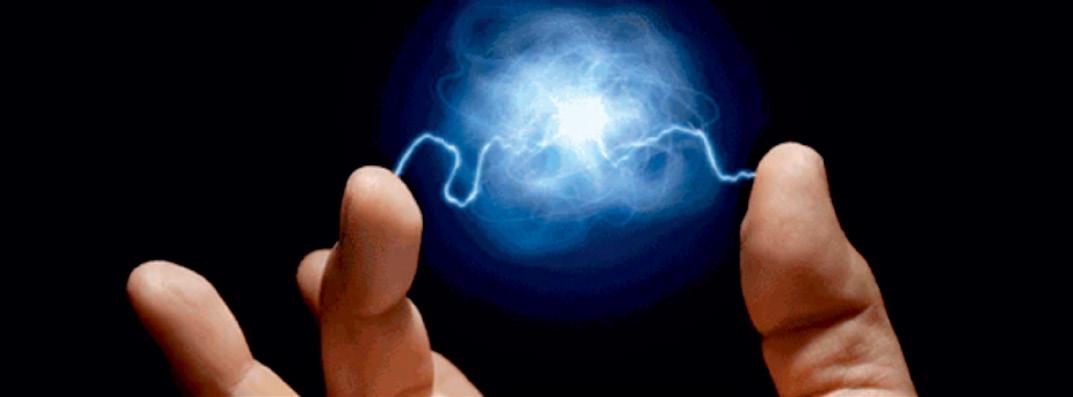