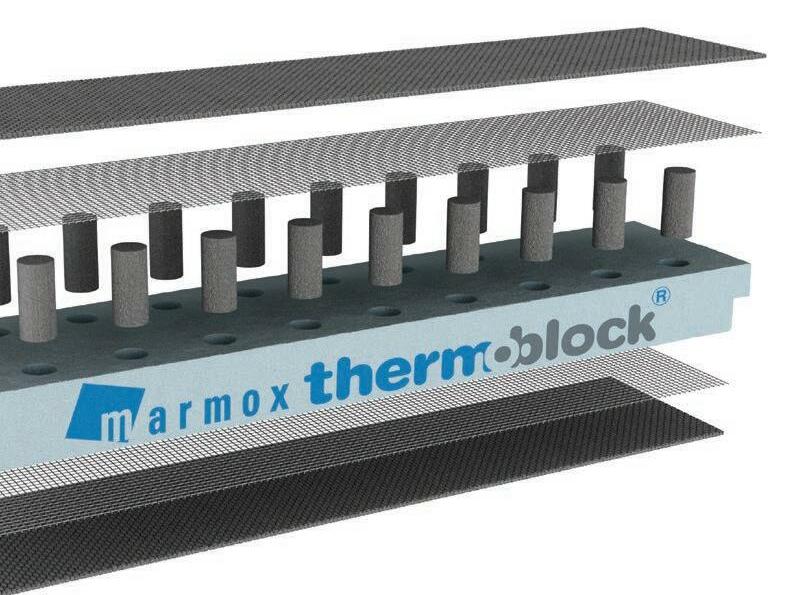
3 minute read
Buildability critical to tackling thermal bridging
18 TECHNICAL CORNER
www.elmhurstenergy.co.uk
Advertisement
Mark Bowman, UK Technical Manager for Marmox
The recent surge in wholesale gas prices has added another dimension to the regulatory and environmental pressures on developers and their consultants to reduce energy losses with the UK’s pace-setting commitments to achieving Net Zero emissions now looming large on the political horizon.
While the plans to end the installation of new natural gas central heating systems by 2035 in favour of heat pumps - are viewed by many commentators as over ambitious, revisions to the Building Regulations have already brought modern properties up to a standard where their use is viable in terms of properties’ thermodynamic characteristics. But although improving the performance of roofs, walls and floors has happened incrementally and with relatively little pain, achieving Part L compliance for the fabric of the building remains a challenge for specifiers, especially in respect of the junction details.
Thermal imaging cameras have become a favourite tool for both building surveyors and those involved in building product research. Offering as they do a spectrum of colours from dark blues to bright red, the technology can show up the troublesome floor/wall junction around the building perimeter for performing almost as badly as an early aluminium window frame or a steel lintel. Such issues were originally highlighted three decades ago by the BRE in a document entitled “Avoiding Risks” and have since been the subject of much research across both industry and academia, though the fundamental problem remains that most good insulating materials are of low density and low strength, making them unsuitable for supporting structural loads. Thus maintaining the overall continuity of performance at the base of the
inner leaf or around some upper floors and parapet walls requires special solutions.
In the case of many PassivHaus projects - the zero-energy benchmark for the majority of environmentally conscious clients, from school boards to self-builders - the problem of the primary floor/wall junction has been addressed by casting a reinforced concrete slab on a raft of medium density foam and then continuing the insulation up the outer face to a level above the junction. This, unfortunately, is not only costly, but can add significant time to the build programme, meaning it is not favoured in the mass market. There is, however, a hybrid solution which has proved successful in applications from home extensions to the construction of municipal swimming pools and which has most recently been adopted for the construction of oversites onto which multi-storey modular homes are craned into position.
Thermoblocks are available in widths of 100, 140 or 215mm and are formed from sections of XPS (extruded polystyrene) encapsulating two rows of high strength, epoxy concrete minicolumns. These are attached at either end to the top and bottom layers of glass-fibre reinforced polymer concrete, to ensure a good bond with the rest of the structure. Importantly, the columns themselves offer a very low thermal conductivity so do not create a cold bridge, while being able to support a loading of 9N, which is higher than the typical dense or aerated concrete block.
Set within the highly insulating XPS section, the units achieve a combined thermal conductivity of 0.047 W/mK. and crucially being able to deliver a very low transmittance, derived by thermal modelling and actual measurement, offers a far more advantageous option than adopting the default figure available under SAP and other assessment methods.
From the perspective of buildability, the blocks are light to handle and are laid in the manner of a continuous course of bricks, while at 600mm in length, progress is rapid. The only difference to bedding a brick is the use of Marmox multi-purpose adhesive to secure the stepped end joint, but this interlock provides far greater stability than a standard perp joint and therefore helps the layer of Thermoblocks to stand firm when a volumetric unit is being positioned over them.
Other recent projects have also seen the very versatile Thermoblocks incorporated into a wall construction featuring traditional dressed stonework by a self-builder creating a family home, while 800 of the widest 215mm units were used in erecting a series of parapet walls where the floorplates stepped back on a nine-storey “Student Castle” built in Brighton.
Overall, the Marmox Thermoblock offers a practical, economic and fully accredited answer to combating cold bridging for different types of development across the UK from social housing to schools and commercial properties.
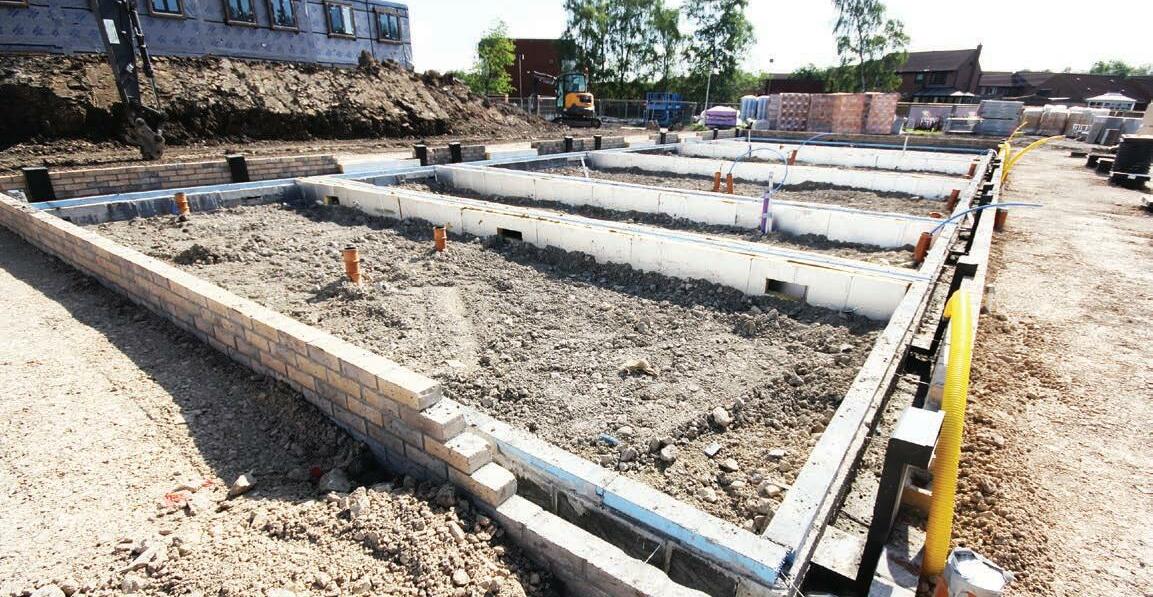