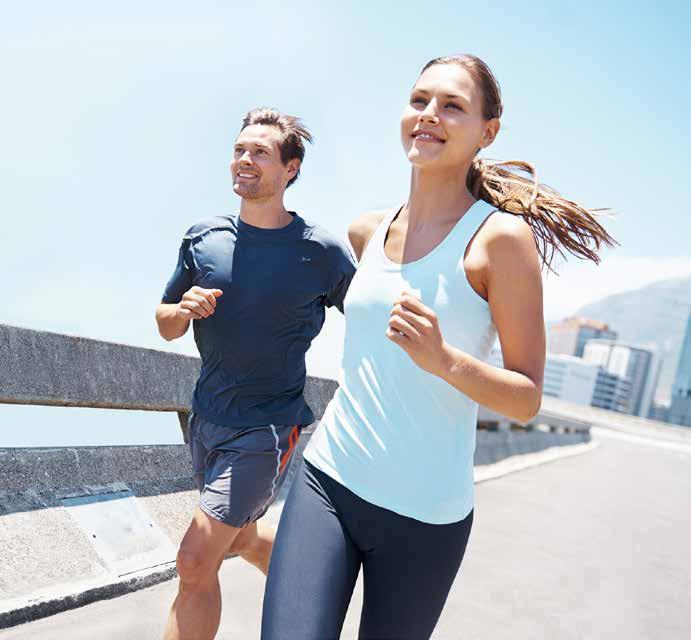
34 minute read
Latest in wool technology from Saurer, Tecnomeccanica, Coppa, Sant Andrea, AUTEFA, Prosino, Tomsic
from Wool2Yarn Global
by Ely Torres
Worsted spinning yarn as you need it
In recent years the range of application for worsted yarns has increased enormously. Beyond traditional applications, the versatile properties of wool are also increasingly used in functional clothing for sports and outdoor activities, seat covers, and more widely in interior textiles for vehicles and aircraft. As such worsted wool yarns are well suited to products that require high thermal retention, good moisture absorption, low density and low
Advertisement
flammability, to name just a few special characteristics. Saurer Group is a market leader in worsted spinning machinery. It includes Saurer Spinning Solutions and Saurer Technologies. Saurer Spinning Solutions offers high quality, technologically advanced and customer-specific, automatic spinning solutions for processing staple fibre from bale to yarn. The worsted sector is very different from cotton or synthetic short staple fibres. Spinning chemical fibres simply involves running at high-speed to produce as much as possible as quickly as possible. The parameters of wool and speciality fibres is different in each fibre, therefore spinning machines must be adaptable. Worsted spinners, in particular, require consistent quality output. They also need the flexibility to be able to change production quickly to accommodate constantly changing fashion. The cost of raw fibre such as fine wools, cashmere, and vicuña has increased, and any mistakes at the spinning stage could be costly. Spinning needs to be perfect every time. Saurer’s worsted spinning and winding machines are ideal partners for intelligent machine and data communication. New Energy Monitoring ensures that power consumption is monitored at all times, so that operators have maximum transparency for easy resource optimization. The latest RFID technology, various sensors for data collection/analysis, and self-optimising control loops are the basis for more intensive integration of the processes, and high productivity and quality. The material flow is tracked all the way, capacity variations can be equalized, and bobbins and tubes go directly to the right processing aggregates.

Online quality monitoring systems (SPID, Q-Package) with numerous functions on Autoconer winding machines ensure that the high quality standards demanded by the worsted yarn industry is met, and supplements the optimisation and control systems on the ringspinning machine Z 451.
The self-optimisation tool OptiSpeed is used in combination with individual spindle monitoring (ISM) making the spinning machines intelligent. ISM leads the operator to spindles where a manual intervention is needed. At the same time, the roving stop system ensures that no valuable raw materials are wasted
while the operator attends to the spindle. OptiSpeed ensures automatic speed maximisation. The operator can set the limits for yarn breakage per 1000 Sph. With better roving quality, OptiSpeed increases the speed until the yarn break limit is reached or, conversely, slows down if there are more breaks. This means it optimises productivity according to roving quality. The system reacts quickly and automatically, which means fewer staff members are needed. Fit for more flexibility, the Z 451 produces ring and compact yarns as well as fancy, core and siro yarns. The unique self-cleaning compact system Impact FX is proficient in dealing with wool grease, textile lubricants, and finishing agents. The walk effect at the deflection point of the apron prevents trash particles and fibre fragments from becoming lodged. The linear air flow creates optimum aerodynamics, so that no accumulations of dirt or blockages can arise. The step less adjustable over delivery and the independent Impact FX vacuum unit supply enable its use in wool processing. However, it is not only its flexibility with regard to yarn counts and raw materials that distinguish the Saurer worsted spinning process. This is also true for its winding machine Autoconer. An individual software-controlled package build, PreciFX delivers package formats optimally and flexibly adapted to the requirements of the respective downstream processing, e.g. 3”-packages for twisting, dye packages with round edge design for uniform dyeing. The Thermosplicer is a market benchmark in terms of appearance and strength, delivering yarn-like spliced joints. For rapid, effective lot changes, all spinning, winding and process parameters can be adapted at the push of a button. Spinnfinity ensures underwind-free doffing on the worsted spinning machine and Q-Package - (intelligent feed material changing strategies on the Autoconer) reduces the manual setup effort to a minimum.

Senses is the new mill management system. It is the ideal completion to the machine park for profitably optimising the use of raw materials, time, personnel, energy and capital. Saurer is ideally equipped to fulfil any request from the worsted yarn industry.
Before each machine is sold Saurer undertakes a detailed study of how the spinner will produce a particular yarn count from a particular micron. Saurer technicians also assess the type of processes that will follow, such as weaving, or knitting or twisting. All information is analysed and the right machine, fit for purpose, will be offered. Additional components could be added to the machine at the beginning or at later stages to make the production even more versatile.
Saurer Components for a perfect yarn
Wool is no longer only found in home textiles and everyday clothing. The renewable raw material is also becoming increasingly popular a much wider variety of applications. Saurer’s Competence Centre for Elastomer Components is investing a lot of time in research and development, particularly in compounds for Accotex spinning cots and aprons. Today there is already a wide range of cot qualities for long staple applications in the hardness range from 60 to 83 shore and suitable apron qualities available for all kinds of coarse to superfine yarns made of pure wool or wool blends.
At the heart of the Ring spinning machine lies the weighting arm, which together with Accotex Cots is essential for evenly drafted yarn. The end result depends on the flawless combination of the small components inside the large machinery. The cots should provide the right grip, enabling sufficient draft. Weighting arms need to give uniform pressure at a constant level, from position to position, to ensure homogenous yarn from the whole mill. And the top roller needs to run evenly to ensure even results. All these small things ensure that your suit is flawless. CS1S spindles provide for quieter working environment.
The quality of the top rollers used in the drafting system is of vital importance for the quality of the produced yarn. The smooth running of the top roller, with its direct contact to the roving, influences the drafting result and, as a consequence, the yarn quality achieved. Texparts top rollers LP 1000 series are used as rear and front top rollers as well as top apron rollers in drafting systems for worsted ring spinning. In terms of an optimized spinning process, Texparts top apron cradles with individual apron tensioning concept offer decisive advantages compared to other types. With the use of OH 2402 and OH 6022 the lowest possible stress on fibres during drafting and a gentle fibre guidance for the worsted ring spinning process will be achieved.
PK 1660 weighting arms are mainly intended for 3-roller double-apron drafting systems on worsted ring spinning machines. They are suitable for spinning wool or man-made fibres or blends of both types up to approximately 200 mm length quality yarn. A recessed roller is used as apron top roller. Thus the drafting system works according to the slip-draft method, having a single draft-field. Depending on the respective preparation method, twisted or french-type rovings can be processed on the drafting system. The 3-roller double apron drafting system works according to the slip-draft principle, with a recessed roller as the top apron roller. Depending on the type of preparation, twisted roving or french-type roving can be fed to the drafting system. The weighting pressures on the top rollers are set infinitely and centrally using a non-oiled compressed air supply system. The latter is installed on the ring spinning machine in form of a ring main to which the weighting arms are connected. The ring main is supplied with controlled air pressure via a pneumatic unit. The saddle load of the top rollers depends on the pressure in the ring main and on the size of the pressure plates of the weighting elements. The PK 6000 weighting arm permits a central partial load relieve when the compressed air system is turned off.
Saurer Accotex NO-79201 new generation aprons designed to meet today’s increasing market demands Texparts PK 1660, the mechanical weighting arm and Texparts PK 6000, the pneumatic weighting arm



Turning an idea into a solution
The international textile machinery industry depends on innovation. But what is innovation? Each of us may have our own definition of how we see innovation but in the end it comes down to turning a novel idea into a solution that adds value to a product and for a customer. Providing solutions for customers around the world is what the Beppe Ploner Group companies have been doing for over 50 years. An Italian based company, with its head office in Biella, encompasses Tecnomeccanica Biellese, Sant’Andrea Textile Machines, and Coppa. The Group supplies machinery for woolen and semi-worsted spinning plants; non-woven products; spinning lines; filtration and recycling systems, and more. The Group also works on individual designs for the specific customer requirements.
‘We provide manufacturers with the latest technology options to achieve their processing and spinning objectives’, says Mario Ploner. ‘It is a commercial necessity for them to operate in the most competitive level and still retain environmental compliance. This sensitivity to the environment has created new design challenges but today the end result is that our machinery produce better quality products. And we are proud to play our part toward this objective’. ‘We have seen the industry adapting and changing to meet market conditions. During this time we have been evolving as a company to provide innovative solutions to our customers’, Mario Ploner commented. ‘We base our designs on the available space that each client has and the specific requirements that their production needs. We are providing faster and better outcomes, both regarding new machinery, plants and for maintenance and spare parts supply. We also care about safety and we keep increasing new solutions to guarantee a better technology for our customer also for these aspects’. ‘Our Automatic Filtering system is the culmination of the accumulated experience in the field of suction of dust, waste and fabric clippings from different types of processing machines’, says Mario Ploner. ‘Using our experience we have developed a new automatic filtering and cleaning system with significant advantages in automation and efficiency’.
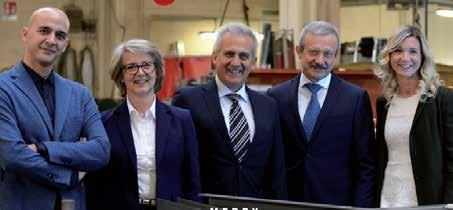
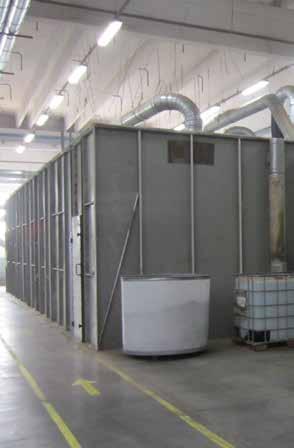
New de-dusting equipment and filtration system installed by Tecnomeccanica Bielleseat Lempriere Wool EOOD in Bulgaria
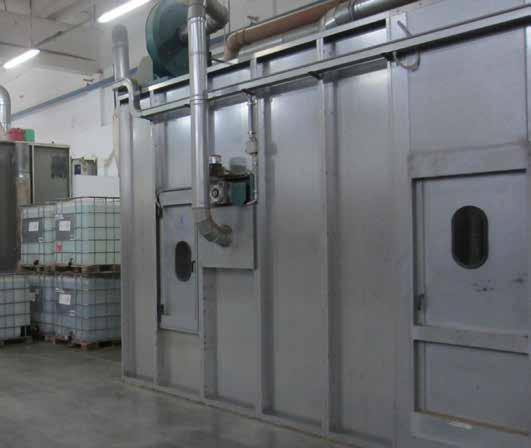
It consists of a monobloc unit optionally fitted in galvanised sheet iron panels containing a pre-filtering system with fibre separation and a drum filter to collect the particles. Because of the action of the unique automatic cleaning systems the efficiency of the unit is guaranteed. The clean air can either be recycled directly in the room or expelled externally. ‘The quality of any finished product made from natural fibers will be influenced by the many processes that it must go through. Early stage processing is no exception. It is important to get this right to ensure that further processing can achieve optimum quality. The main objective of our machinery is to achieve this, and today’s consumers recognize and appreciate this’, says Mario Ploner. Tecnomeccanica’s automatic Bale Plucker is used to mechanically strip fibresfrom pressed bales and automatically drop the fibre on to the feed table of the opening machinery at the beginning of spinning lines. This system also provides a good first blending operation of the fibres. It is mainly composed of a metal bridge moving on rails, providing vertical movement to the plucker head. The different functions of taking, discharging and cleaning are controlled by a computerised digital panel with touch-screen. Photo electric sensor beams provide complete protection against accident, in line with European legislation relating to Health & Safety. Tecnomeccanica has representatives in most countries around the world. ‘We provide excellent machinery service assistance and are able to provide spare parts when needed’. For more information contact www.tbsrl.it

SRL
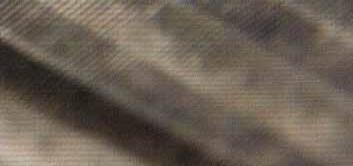
Reaching customers in China
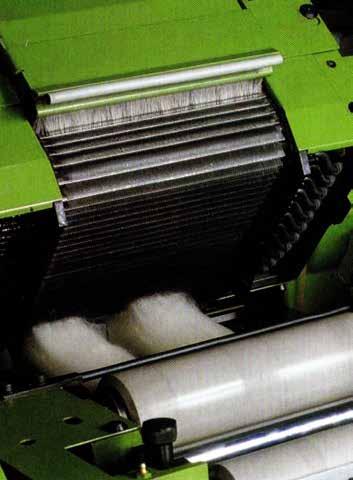
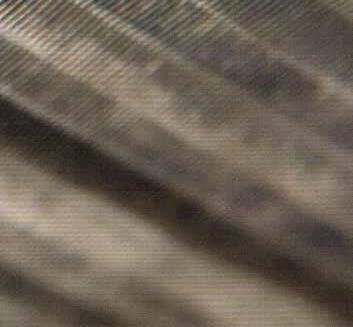
Member of Beppe Ploner Group wool2yarn china is used by wool and textile companies around the world to advertise their products and services to the textile industry in China.
‘This Chinese language publication is circulated to over 5000 major importers of wool and speciality fibres, wool processing and topmaking mills, spinners and weavers, carpet and garment manufacturers, manufactures of yarn and fabric, rugs carpet and government agencies and ministries in China’, says Victor Chesky, Editor. ‘It is circulated in China by Nanjing Wool Market.’ wool2yarn china is also distributed to all delegates (500+) attending the annual Nanjing Wool market Conference, the major conference for the wool and early wool processing industry in China. This magazine is also distributed to textile enterprises in Hong Kong and Taiwan. ‘wool2yarn china provides exporters from around the world the opportunity to reach buyers in China, communicating in Chinese, breaking down any language barrier,’ says Mr Chesky. ‘For companies seeking new customers, advertising in wool2yarn china will introduce their company to this targeted decision maker base in all sectors of the wool industry in China. For companies that have established customers in China, advertising in wool2yarn china will reinforce their position as a preferred supplier to these existing customers. ‘wool2yarn china is published in September each year and is used as a buyers’ guide by companies in China over the following 12 months.’ If your company is interested in advertising in the 2020 issue of wool2yarn china please contact us on victorch@bigpond.com or www.wool2yarnchina.com



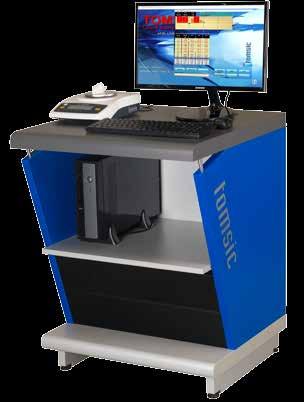
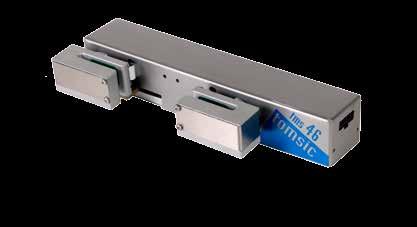
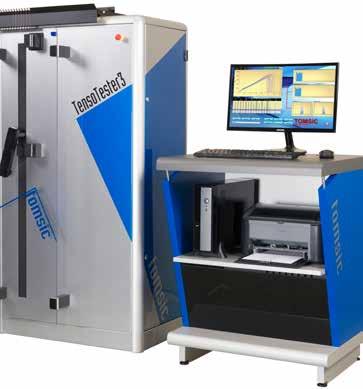
easy Evenness Tester
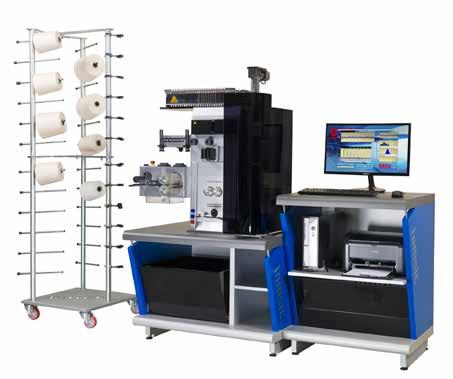
There are No Shortcuts to Quality
Tomsic has been designing and manufacturing complete laboratory equipment for wool and cotton spinning mills, as well as quality monitoring systems for sliver and roving, and autoleveller systems for cards and drawframes, from Gorizia Italy for more than 60 years. ‘Quality starts at the lab and using the right testing equipment
Ladi Tomsic ensures that consistency and quality can be monitored and costly mistakes avoided’, says Ladi Tomsic, sales manager at Tomsic. ‘Our testing and monitoring equipment is specifically well known within the wool industry, although the same machine can work just as well with cotton. Our equipment has been running successfully in many topmaking and spinning plants in Europe and around the world. We provide best quality control technology for the entire topmaking and spinning process’. Ladi Tomsic continues ‘our easy Evenness Tester is designed for combing and re-combing for both wool and cotton. It is specifically designed for testing and analysing the quality of sliver, roving, and yarn. There are no maintenance costs and it is very easy to operate from a standard PC monitor using Windows 10. It takes just 3 clicks and from 1 - 20 minutes depending on the evenness, hairiness, and mass. Multi-diagram windows provide for direct test comparisons. For export purposes printouts are available as multi-language reports. Data retrieval is easy to use and personalised search options are available, in many languages.’
All Tomsic machines are made in Italy and offer flexibility, low maintenance, and are very competitively priced compared to other manufacturers of similar equipment.
‘Where others manufacture a range of testing equipment our equipment is textile industry specific. We are familiar with wool and our advanced technologies
TMS45-Count Analyser
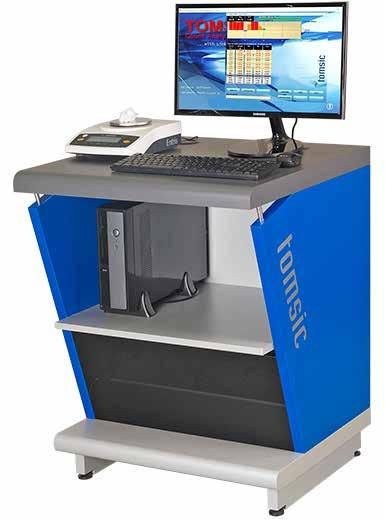
reflect the quality control needed for this fibre. Our technology runs successfully in plants in more than 30 countries. Our local agents have a particular focus on spare parts and after sales service’, says Ladi Tomsic.
‘Our Tenso Tester 3 automatic strength tester tests and analyses the elongation and force properties of staple-fibre spun yarns and filament yarns. Test length is from 100mm - 500mm, with a pre-tension value from 0.00cN/Tex - 10.00 cN/Tex. It can test yarns of all materials and counts. It provides for multi language software operation with test runs in just 3 clicks. It requires only one window for graphical and numerical display and multi diagram windows for direct test comparisons’, says Ladi Tomsic.
The TMS46-QM - digital system is for high accuracy sliver and roving quality monitoring. It is installed directly on to existing
Tenso Tester 3
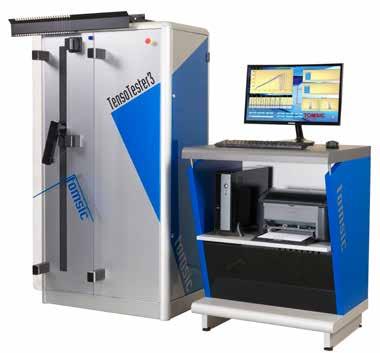
and new production machines with online measurement. It can be adapted to a wide range of counts. ‘We provide 3 versions: for carding machines producing long fibres, for finishing machines also for long fibres, and for roving machines producing short and long fibres, all are suitable for wool, silk, jute, acrylic and more’, he says.
The TMS45-Count Analyser measures yarn, roving, and sliver count. The main software technology is Microsoft compatible and provides for multi language use and report printing. At least 20 years of data, such as storage, is available and free retrieval of the stored data is also available via other software (for example: Excel). It is possible to change measuring units such as Nec, Nel, New, Nm, tex, Ktex, gr/yd, and Denier. Avg, and CV% graphs are displayed during the test. The Software Data View shows Min., Avg., Max, CV% Q95% data and it is possible to visualize up to 3 measuring units at the same time. The Link-Job Technology is simple to use and saves time. Ladi Tomsic added that ‘delivering quality and consistency in tops and yarn production is not an easy task but using our laboratory testing equipment will achieve the best outcome every single time. We welcome enquiries from topmakers, spinners, and weavers who wish to talk to us about how our technology can help them’. Ladi Tomsic can be contacted at ladi@tomsic.it
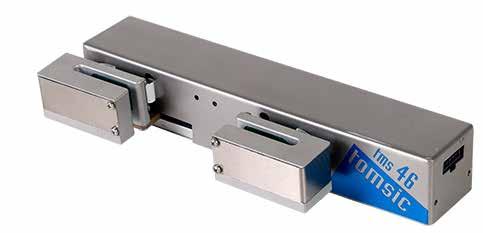
Weight and quality sliver control sensor at the output
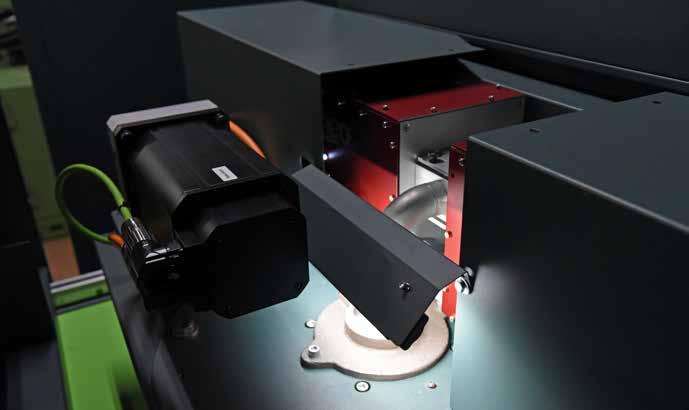
New generation drawing frames
‘At the dawn of the fourth industrial revolution, Sant’Andrea Novara is providing a breath of fresh air - its Elvo smart drawing frame monitors the quality of the entire production - a new generation machine able to collect data on production performance and organise in an Industry 4.0 way’.
‘All Italian know-how and innovation has always been part of our DNA’, says Marco Ploner, director at Sant Andrea. ‘Innovation is real and concrete, more than a novelty. Italian companies are revolutionising markets, turning the Made in Italy into a symbol of excellence all around the world.
‘Innovation meets the tangible needs of a precise target audience, improving worker performance and safety and focusing on research’, he says. For almost a century, Sant’Andrea Novara has been involved in technological research and the development of new products for the mechanical and textile sector. ‘Today, the Piedmontese brand is still a beacon of innovation - meeting the new and shifting needs of the modern industry’.
MECHATRONICS LEAD THE WAY
This is a very exciting period for the textile machinery industry. Companies in this sector - and Sant’Andrea Novara in particular - are taking a real technological leap, moving from mechanics to mechatronics. Such an important change not only revolutionises the conventional way of designing machines, and also prepares them to the interconnected world of Industry 4.0.
With this scenario in mind Mario and Marco Ploner, directors of Sant’Andrea Textile Machines Srl, have radically re-invented Sant’Andrea Novara’s production, as well as technology, and in communication and design. The new machines are named for the rivers in the wool
district around Piedmont. ‘It was like putting an Italian seal of approval on our new production line, highlighting the strong relationship between the company and the surrounding landscape’, says Marco Ploner. The new drawing machine has been updated in both its hardware and software: the drawing system has been mechatronically redesigned, while the machine layout has been designed with intuitive and coordinated user interfaces to mimic the anthropometry and gestures of the machine operator.
ELVO - A NEW GENERATION OF DRAWING MACHINES
Sant’Andrea Novara presented the prototype of its new ELVO drawing machine (with brand new design and colour) during ITMA 2019, an important signal marking a new era. The company exhibited Elvo’s innovative core: the quality control system RiverX, a technological device that controls and manages the quality of the entire production during fibre processing. The introduction of this new technology is important to replace manual control and the delivery weight through spot checks. Elvo enables monitoring adjustment of the outgoing sliver during the whole process, ensuring that the entire production complies with the desired weight standard. A “controlling eye” on the whole processed batch, analyses data, saving it, and making it remotely available.
Mechatronics makes machines “smart”, allowing them to improve auto-levelling performance as well
Mario Ploner (left) and Marco Ploner
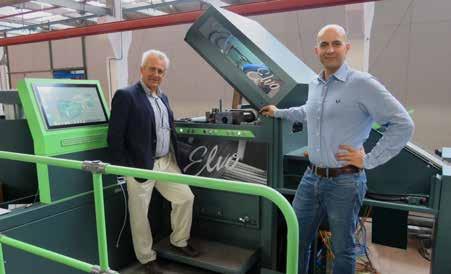
as axis rotation, if necessary, to ensure that the desired weight is as uniform as possible throughout the whole processed batch.
Sant’Andrea Novara has launches its first machine designed from an IoT (Internet of things) perspective, with a proprietary control panel (SanProMo: Sant’Andrea Production Monitor) able to create an ideal “dashboard” to manage the machine efficiency and to control quality. The “embedded” SanProMo software will help the operator/supervisor optimise production and keep fibre quality under control, even remotely. Maybe in the future it will be able to manage an entire line. ‘Elvo will allow us to provide our clients with a product that meets its value proposition as far as high quality and durability are concerned. We are even going to strengthen it by adding an IoT plus to measure the performance in terms of production, efficiency and quality’, says Silvio Givone, company sales manager.
AN EYE TO THE FUTURE
Elvo is the first step on a path leading to the modernisation of the entire production in Sant’Andrea Novara. The company will soon present Cervo (the vertical finisher already announced at ITMA 2019) and Sesia (a new multi-head drawing frame). This is only the beginning of an exciting journey dedicated to innovation. ‘The underlying idea is to one day offer our clients the chance of managing the whole fibre processing line from an IoT perspective, in order to support them in the performance of their tasks. For our clients, Sant’Andrea Novara will not only be a supplier but also a reliable partner, which will help make processes easier, faster, and smarter by means of state-of-the-art technological tools’, says Mario Ploner. Throughout its history the company production has been underpinned by new ideas and constant innovation and the current management continues this focus into the future.
Dr. Pietro Prosino

Best performance in spinning
The COVID-19 pandemic has had a devastating impact on the wool industry worldwide,’ says Dr Pietro Prosino, CEO PROSINO Borgosesia Rings from the company’s manufacturing base in Biella Italy. ‘Whether you are a wool grower, manufacturer or retailer the impact of this unprecedented situation has caused us all to revaluate our plans for the future’.
‘But when business returns to normal the fundamental values, such as quality output and efficiency in manufacturing will still be there. For spinners around the world running machinery at greater speed with no breakdowns and maintaining quality throughout the process will be as important as ever. ‘I have no doubt that the industry will come out of this stronger and more resilient. The changes in consumer behaviour will affect the retail and manufacturing sectors for years to come but demand for quality, and the necessity to be more competitive at manufacturing, will continue to be important factors for the industry,’ he said.
PROSINO supplies to Original Equipment Manufacturer (OEM) companies and its rings are preferred by Zinser, Cognetex, and Gaudino for spinning any fibre, whether long or short staple. The company supplies a complete range of ring holders and ring-rails, as well as sintered metal rings for technical textiles including carpet, fiber glass, and synthetic fibers. Prosino uses 100Cr6 ball bearing steel for all its rings.
It also supplies spinning rings to top end spinners such as Sudwolle-Safil, Zegna Baruffa, Reda, XinAo and many others.
‘Our business goal has always been to keep spinning frame performance at the highest level. Our steel canonical rings provide extra strength and speed and reduces yarn breakage and yarn hairiness, and provides a longer lasting life to customer machinery, a benefit in cost saving,’ says Pietro Prosino.
Saurer Group, manufacturer of the Zinser brand, commented that buyers of their new machines request Prosino Rings because they are known for their quality and durability. This sentiment is
also shared by Xinao, one of the biggest worsted yarn manufacturers in China, who has switched to using only Prosino Rings in all its processing. ‘We must ensure that our yarn is of the highest quality and we depend on our machinery to work with less breakage throughout the spinning process’, says Zhou Xiaotian, Xinao General Manager.
Longtime customer REDA, a world recognised manufacturer of luxury fabric, has relied on PROSINO rings for many years. ‘We have always opted for Prosino Rings because we need a stable and reliable supplier. Prosino has always demonstrated an ability to listen to the needs of yarn producers and develop high quality rings that meet their requirements’, says Francesco Botto Poala, REDA CEO. Pietro Prosino comments that ‘natural fibre such as wool, cashmere, and mohair will continue to be expensive fibres. Eliminating breakage and ensuring uninterrupted production runs is important to any spinner around the world. We have a long and established relationship with Michell Perù, the largest Alpaca textile group in Peru. Prosino has been supplying its Borgosesia Rings to this company since the 1980s.
Josè Valdivieso, Director of Michell Perù, comments that ‘the quality of the rings and personalised service and attention we receive from Prosino is excellent. We must have reliable machinery to ensure that we are able to deliver our products on time and to best quality. Prosino Rings are an important part of our ability to achieve this outcome’.
‘The exceptional performance of our rings is achieved because of the latest innovation in manufacturing,’ continues Pietro Prosino. ‘Best performance in manufacturing is our goal, and we have been working on it for over 70 years. We offer a continuously evolving range of products. Our client base appreciate the reliability, flexibility and innovation that our rings provide’, says Dr Prosino.
For more information Dr Prosino can be contact at pprosino@prosino.com
Dr. Pietro Prosino
Best performance in spinning
The Covid-19 pandemic has had a devastating impact on the wool industry worldwide,’ says Dr Pietro Prosino CEO PROSINO Borgosesia Rings from the company’s manufacturing base in Biella Italy. ‘Whether you are a wool grower, manufacturer or retailer the impact of this unprecedented situation has caused us all to revaluate our plans for the future’. ‘But when business returns to normal the fundamental values such as quality output and efficiency in manufacturing will still be there. For spinners around the world running machinery at greater speed with no breakdowns and maintaining quality throughout the process will be as important as ever.
104 | wool2yarnglobal 2020 ‘I have no doubt that the industry will come out of this stronger and more resilient. The changes in consumer behaviour will affect the retail and manufacturing sectors for years to come but demand for quality, and the necessity to be more competitive at manufacturing will continue to be important factors for the industry, ‘he said. PROSINO supplies to Original Equipment Manufacturer (OEM) companies and its rings are preferred by Zinser, Cognetex, and Gaudino for spinning any fibre, whether long or short staple. The company supplies a complete range of ring holders and ring-rails, as well as sintered metal rings for technical textiles including carpet, fiber glass, and synthetic fibers. Prosino uses 100Cr6 ball bearing steel for all its rings. It also supplies spinning rings to top end spinners such as Sudwolle-Safil, Zegna Baruffa, Reda, XinAo and many others.
‘Our business goal has always been to keep spinning frame performance at the highest level. Our steel canonical rings provide extra strength and speed and reduces yarn breakage and yarn hairiness, and provides a longer lasting life to customer machinery, a benefit in cost saving,’ says Pietro Prosino.
Saurer Group, manufacturer of the Zinser brand, commented that buyers of their new machines request Prosino Rings because they are known for their quality and durability. This sentiment is also shared by Xinao, one of the biggest worsted yarn manufacturers in China, who has switched to using only Prosino Rings in all its processing. ‘We must ensure that our yarn is of the highest quality and we depend on our machinery to work with less breakage throughout the spinning process’, says Zhou Xiaotian, Xinao General Manager. Longtime customer REDA, a world recognised manufacturer of luxury fabric, has relied on PROSINO rings for many years. ‘We have always opted for Prosino rings because we need a stable and reliable supplier. Prosino has always demonstrated an ability to listen to the needs of yarn producers and develop high quality rings that meet their requirements’, says Francesco Botto Poala, REDA CEO. Pietro Prosino comments that ‘natural fibre such as wool, cashmere, and mohair will continue to be expensive fibres. Eliminating breakage and ensuring uninterrupted production runs is important to any spinner around the world. We have a long and established relationship with Michell Perù, the largest Alpaca textile group in Peru. Prosino has been supplying its Borgosesia Rings to this company since the 1980s. Josè Valdivieso - Director of Michell Perù comments that ‘the quality of the rings and personalised service and attention we receive from Prosino is excellent. We must have reliable machinery to ensure that we are able to deliver our products on time and to best quality. Prosino Rings are an important part of our ability to achieve this outcome’.
‘The exceptional performance of our rings is achieved because of the latest innovation in manufacturing,’ continues Pietro Prosino. ‘Best performance in manufacturing is our goal, and we have been working on it for over 70 years. We offer a continuously evolving range of products. Our client base appreciate the reliability, flexibility and innovation that our rings provide’, says Dr Prosino.
For more information Dr Prosino can be contact at pprosino@prosino.com
We chat:
Whatsapp nr: +39 335 8361291 www.prosino.com - info@prosino.com
wool2yarnglobal 2020 | 105
Giacomo Meucci Regional Sales Director Autefa Solutions
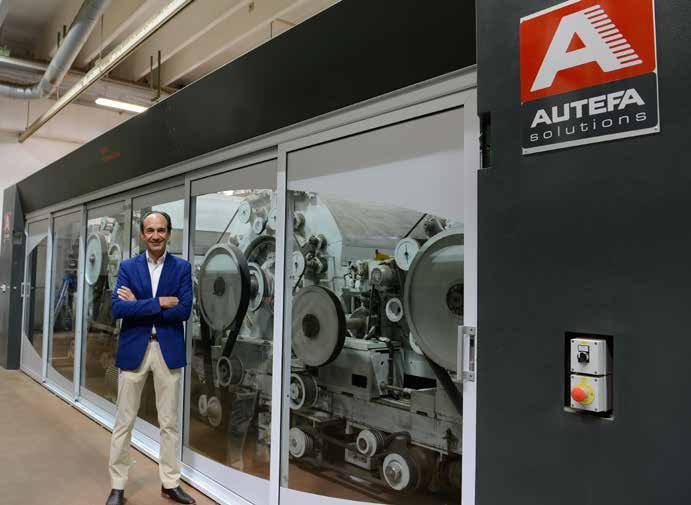
Cards for finer fibres
COVID-19 caused a micron wools corresponds with a cashmere woollen spinning are temporary slow-down of demand on the spinning sector to the preferred option. Ningbo some AUTEFA machinery manufacture yarn using finer fibre Consinee in Zhejiang province installations around the and to precise specifications. will operate the most automated world. ‘But as sites have been able and modern plant for processing to start up, we are seeing a way ‘Our machines deliver excellent cashmere, and Gobi, the biggest forward and our major installation quality outcomes in wool, alpaca, spinning mill in Mongolia, in China is back on track’, says and cashmere. They can run at uses our AUTEFA cards in its Giacomo Meucci, Regional Sales a precise speed, guaranteeing production’, he says. Director Autefa Solutions from Biella Italy. consistency and evenness in top and yarn production. Tops will be some 2-3mm longer the best yarn The OCTIR-Dragon Multitrave Worsted and Semi-worsted Cards ‘Today there is an increasing quality achievable’, says Giacomo guarantee high productivity focus on the use of natural without compromising the Meucci.fibres in manufacturing leisure, quality of the top. The result sportswear, and next-to-skin ‘In China and in Europe our is fibre fineness from 14.5 - 40 clothing. This focus on finer machinery installations for microns and fiber length from
40 - 220mm. AUTEFA woollen carding sets feature feeding cylinders that reduce to 108mm, enabling better fibre control, producing a yarn with greater evenness and better CV and Uster values. These cards provide a more simplified opening of the card cover and increased throughput and blending action. A control panel with touchscreen allows easy management of all functions including fault messages. Side doors without rails on the floor create quick and easy access to card parts for cleaning and maintenance.
OCTIR-Dragon Multitrave Woollen Carding Sets are available with a single or double tape condenser, as well as either a giant traversing creel or a tandem creel. Based on the OCTIR system, the synchronization between the two cards is mechanical (breaker and finisher) because this is the best way to reach the perfect synchronization by the various carding set cylinders.
‘COVID-19 and the travels restrictions it has imposed has shown us how important and useful online and remote problem solving and communication can be,’ says Jutta Soell, head of marketing. ‘We have been using remotely controlled troubleshooting equipment for some time. Now, it is even more important than ever.
‘Our machines and lines are known as very robust and reliable; however, customers with production lines older than 15-20 years, with no remote access, were unable to take advantage of our online troubleshooting services. Very early on in the pandemic and at the time of the first lockdown, we recognized the need for retrofits to those older production lines, to enable remote access and to upgrade these machines with the latest state- of- the- art- technology. Our supply chain has not been disrupted during COVID-19 and we continue to support users of our machines worldwide.’
For more information about AUTEFA cards and online servicing - www.autefa.com/ woolenworsted/
OCTIR. Woollen. Worsted. Semi worsted.

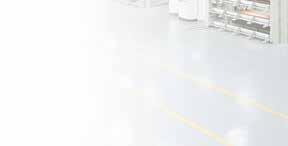
The best worsted, semi worsted, and woollen carding sets to process the fi nest fi bers.
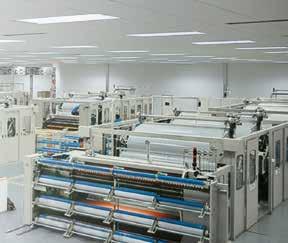

New insert grip machine provides greater accuracy
making tops, but are integral to the process. This is why the quality of combs is so important’, says Mario Ploner of Coppa, a member company of the Beppe Ploner Group. ‘We have been manufacturing high quality steel combs for over 50 years and are a preferred supplier for NSC, Sant’Andrea, OKK and Cognetex’. This Italian company has always been innovative, keeping pace with the technologies needed for todays’ production processes. ‘The experience and knowledge we have acquired over time, and our willingness to collaborate with leading textile machinery manufacturers, is beneficial to all. We guarantee that Coppa products provide longevity, durability, minimum maintenance, and simple needle replacement’, says Mario Ploner. at their plant. ‘We can make combs to specific order for individual machines’, says Mario Ploner. ‘And we deliver promptly all around the world’. Coppa’s new automated insertation technique for combs in textile machinery has made a reliable, high quality product even better. ‘If combs are not correctly installed or are too old, they can affect the quality and speed of the entire topmaking process. To meet customer need all over the world, we have designed a new insert grip machine. When the insert is worn-out and it is necessary to change it, the replacement operation has previously been done manually; now it can be done mechanically. This machine provides greater accuracy than the manual method and eliminates damage that can be made to the comb during manual insertion. The new machine inserts combs with greater accuracy and provides a safer installation process for the operator’, says Mario
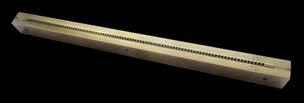
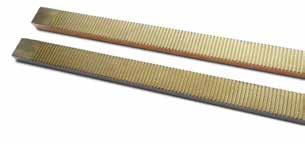
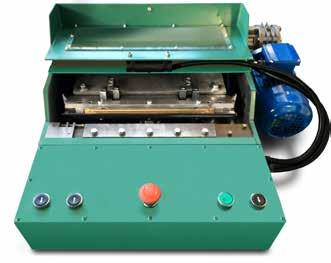
Combs are a very small component in the
Ploner.
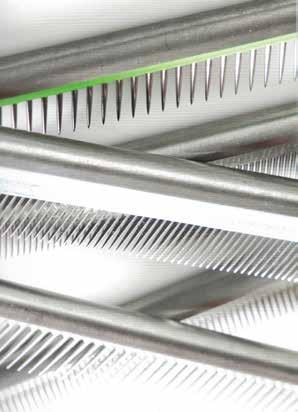
Always in fashion
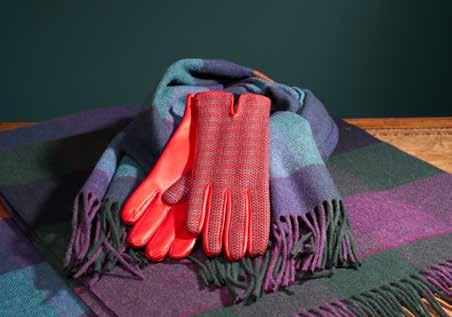
The buzz word in fashion today is casual casual casual, and this all the more so as a result of COVID-enforced working from home. Many might be leaving their formal suits firmly in the wardrobe but there is always a place for gloves! The Queen may be one of a very few to wear gloves as a sartorial standard but cold weather will always provide an opportunity to wear gloves to keep our hands and fingers warm. So why not make them fun and fashionable? Britain used to have a huge glove industry and being a glover was a sought after skill and Dashing Tweeds is taking up the mantra. ‘We have used our reflective fabric for men using our Navy Raver design, and our Red Raver for our womenswear gloves. These both feature our reflective threads woven with fine Merino wool and the gloves are made of the most lusciously soft leather and lined with cashmere.
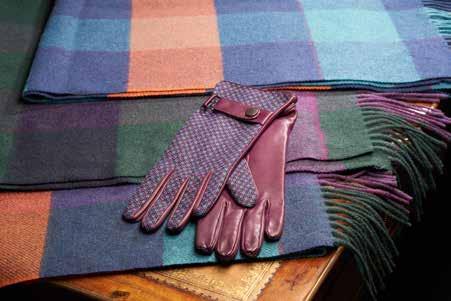
‘We have also turned two of the fabrics from our current autumn collection into really exquisite gloves. The Libertine design is matched to a rich purple leather and our sumptuous Verdant tweed to a rich green leather. We have all pairs in small, medium and large sizes.’

Why advertising works
When business is good it pays to advertise. When business is bad you must advertise.
One thing is for sure, if buyers have never textile companies in over 60 countries worldwide. It heard about your company they cannot is circulated by direct mail to all buy your product. You simply major importers and exporters of wool cannot contact 20,000 people. Advertising in woo2yarn magazines can. Advertising promotes wool2yarnSpeciality Fibres China 中国羊毛与纱线 and speciality fibre, wool carbonisers, topmakers, spinners, weavers and fabric, garments, and carpet manufacturers. your product to new markets and reassures your existing customers that buying from your company is the right choice.
Magazine advertising is targeted and builds product awareness. To get your message across you must have a profile that your customers and potential customers can see and easily access.
wool2yarn global and wool2yarn china magazines are published once each year and advertising in both of these publications will connect you to all major wool companies using wool and speciality fibres in their production. wool2yarn global is an English language publication, circulated to 5000 wool and
2020-2021年羊毛购买商指南
wool2yarnSpeciality Fibres Global wool2yarn china is circulated to over 5000 wool importers, wool processors (scouring and carbonising), topmaker, spinners and weavers, and fabric and carpet manufacturers in China by China by Nanjing Wool Market. wool2yarn china is also distributed to all delegates (500+) attending the annual Nanjing Wool Market
Conference, the major international conference for the wool and textile industry in China. Attendees include leading Chinese companies from greasy wool importers and processors to garment manufacturers.
BUYERS GUIDE TO WOOL 2020-2021 For more information visit us at
www.wool2yarnglobal.com
Who Reads Us
Garment / Carpet Retail
7% 21%
Yarn Manufacturers
Garment/Carpet Manufacturers
Government Agencies
11% 4%
17%
Exporters / Importers / Agents
16%
Fabric Manufacturers
24%
Wool & Top Processing
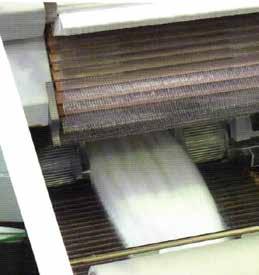
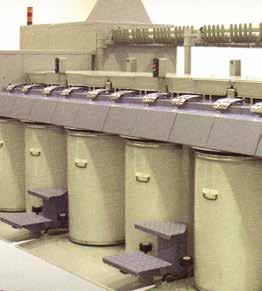
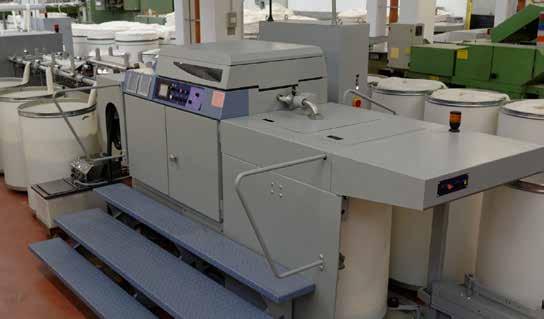
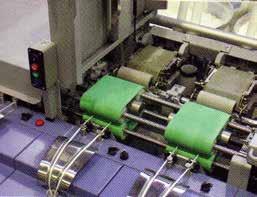
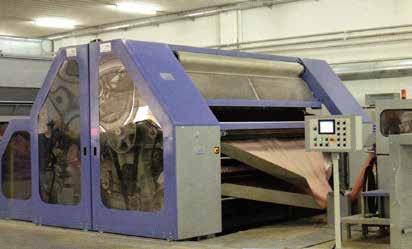
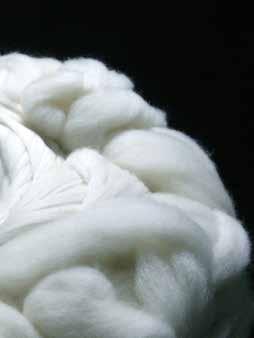

EXCELLENCE IN WOOL TOP B U L G A R I A
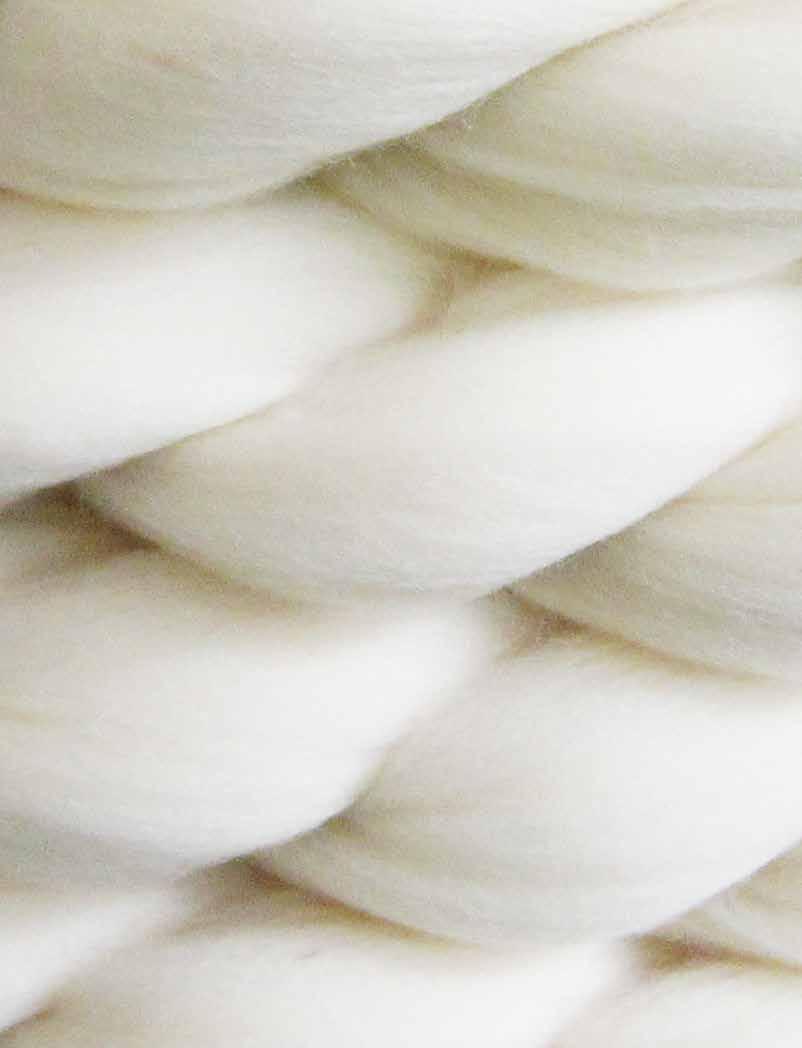