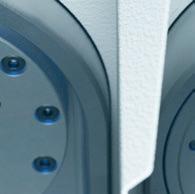
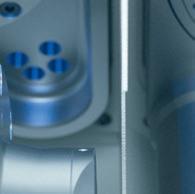
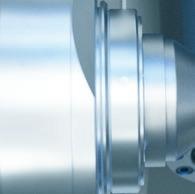
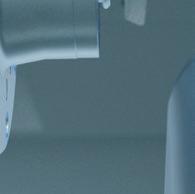
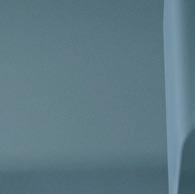



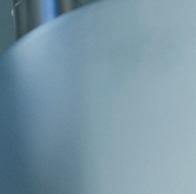


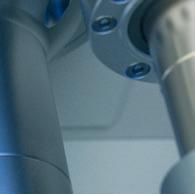
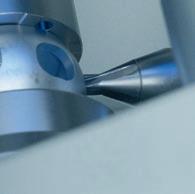
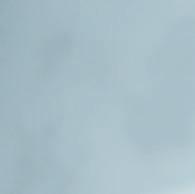

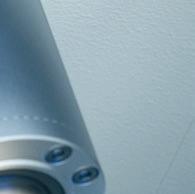
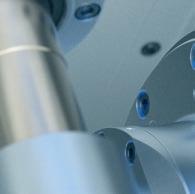
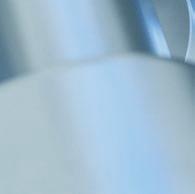
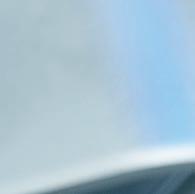


Double offset joints, ball cages, outer races and more in focus

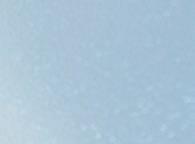
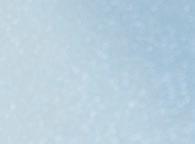

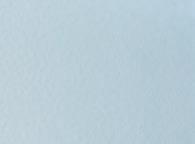


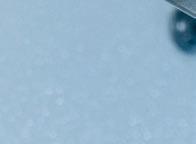
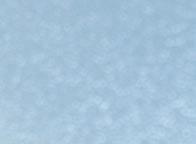


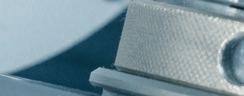
PACESETTER
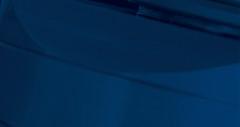
Double-spindle technology from EMAG ensures maximum productivity in the machining of constant velocity joints.

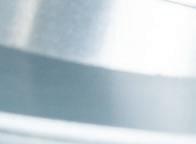
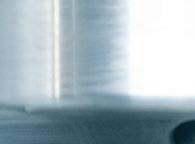

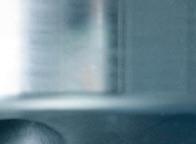

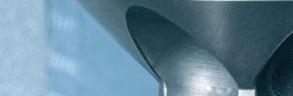




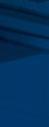




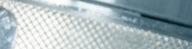




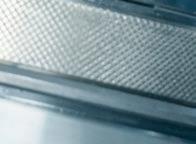





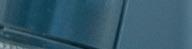


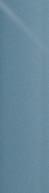

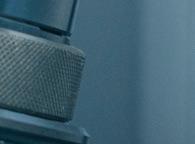

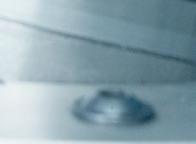
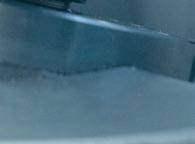
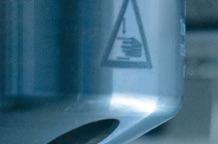

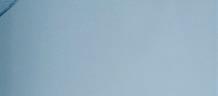








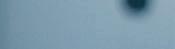

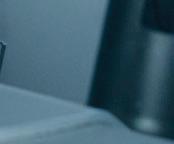

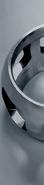
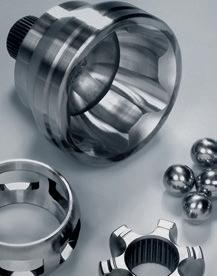


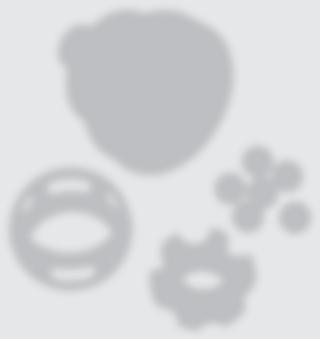
Double offset joints, ball cages, outer races and more in focus
Double-spindle technology from EMAG ensures maximum productivity in the machining of constant velocity joints.
How do you transfer forces between two axes that are at a specific angle to each other - and this angle also changes constantly? The automotive industry answers this question with the tripod joint and other constant-velocity joints. What’s interesting is that, given the success of electromobility, the design of these components is currently changing as well.
The reasons for this are easy to explain. The high torques of the electric motor ultimately ensure equally high forces inside the joint - including constant load changes, which are often noticeable after a while. The rollers of the tripod joint virtually "work" their way into the housing, resulting in greater play, which in turn causes annoying noises on bumpy surfaces or when cornering. With many combustion engines, this is an almost tolerable problem, as the engine drowns out the noise. However, this does not apply to the (much quieter) electric motors.
Remaining consistently important: homokinetic joints in automobiles.
As a result, many car constant-velocity joints are being designed increasingly larger and more robustly. Both their length and diameter are increasing. While homokinetic joints for cars previously had a maximum diameter of 120 millimeters, joints with diameters of up to 150 millimeters are already planned today.
We develop manufacturing solutions tailored specifically to the requirements for machining homokinetic joints. Not only the machine itself is in focus. The entire process - machining technology, NC programming, tools, automation, and energy consumption - is optimized specifically.
Tripod joints ensure uniform force transmission between the axle gearbox and the drive shaft, while simultaneously compensating for the vehicle’s suspension movement through length adjustment.
This is made possible by an ingenious design characterized by three recesses in the outer pot. It is located at the end of one shaft. On the other shaft, however, there are three pins with needle-bearing rollers that move in the recesses. Overall, based on this configuration, a maximum deflection angle of up to 30 degrees and a length compensation of 30 to 50 millimeters are achieved.
In the DO joint, balls ensure the flexible connection between two axes.
Due to their low manufacturing costs, tripod joints are (still) installed in many vehicles - including electric vehicles. However, the joint is not designed for the high torque of electric drives and thus deforms. The Double-Offset Joint (DO-Joint) - also known as Double-Offset-Joint (DOJ)is a long-established alternative:
» Inside it, balls move in precisely milled tracks. They are held in position by ball cages.
» The ball raceways have a very low manufacturing tolerance and a high surface quality. As a result, the balls can roll without play and smoothly - high precision of the milled ball tracks is therefore crucial.
» With its thicker wall thickness, the joint can also withstand high torques and has a long service life.
For the processing of angled and straight ball raceways in homokinetic joints, EMAG has special production solutions. After a modification these machines can now also be used to process larger housings, such as those used in e-mobility.
VSC 315 DUO KBU: DOUBLE-SPINDLE BALL
The VSC 315 DUO KBU is a flexible machine that is universally suitable for straight and inclined ball tracks - for hard and soft machining (always dry). It combines technologies such as soft turning, soft milling, hard turning and hard milling in a single clamping operation. This produces articulated housings and inner races with maximum precision.
The heart of the machine is the double spindle arrangement. Another impressive feature is the double-walled gantry design, in which the combination with a base body made of polymer concrete ensures maximum stability - for soft and hard machining at the highest level.
The machine's fully automated processes simplify the integration into comprehensive production systems.
» Milling spindle on an NC swivel unit (B-axis)
» Swivel angle from -30° to +90°
» Maintenance-free AC synchronous spindle motors for performance and durability
The VSC 315 KBU milling and turning center scores highly as a flexible machine for straight and angled ball tracks in articulated housings. During hard machining, one milling spindle is used, which is mounted on an NC swivel unit (B-axis). For soft machining, the machine can also be equipped with two milling spindles. Hard and soft machining are always carried out dry.
The machine has a total of five axes (X, Y, Z, B, C - plus additional axes in the automation), with high rapid traverse speeds ensuring short non-productive times when changing workpieces. In addition, the large distances between the pre-tensioned linear roller guides in the X-axis also ensure the necessary precision at high feed speeds and cutting forces.
The spindle unit is equipped with a dynamic AC synchronous spindle motor. In addition, a triple bearing arrangement - with optimized bearing distances and precision shoulder bearings in tandem O arrangement - ensures stiffness, good damping and excellent guiding quality.
» Milling spindle on an NC swivel unit (B-axis)
» Swivelangle from -30° to +90°
» Maintenance-free AC synchronous spindle motors
» Thermosymmetrical machine design
The VSC 315 TWIN KBG impresses with its high performance and accuracy in high-volume production. The simultaneous machining of two workpieces with two spindles also increases productivity. It is specifically used for straight ball tracks (in hubs and joint housings) in hard machining (dry).
The portal slides of the ball track milling machine are independent units. Each slide and each spindle has its own X- and Z-axis drives. In addition, there are separate measuring systems with linear scales in all axes. This guarantees high-precision machining, allowing diameter and length corrections to be made individually for each spindle.
Important: The developers at EMAG have increased the working stroke Z of the workpiece spindle by 48.5 millimeters.
*Longer workpieces and larger diameters on request
» Generously dimensioned ball screws and linear guides for perfect machining quality
» Machine bed made of Mineralit® for optimum damping properties and long tool lifCan
» Can be used for hard turning and hard milling
So-called ball cages hold the balls of the homokinetic joints in their orbit. Their “windows” require extreme precision. Different production processes are used depending on the components.
As a general rule, the number of windows corresponds to the number of ball tracks in the joint. There are alternatives for their manufacture:
If the geometry of the component allows, the windows are punched out first. After a hardening process, a suitable manufacturing process ensures the desired quality.
If the component geometry does not permit punching (e.g. with a high wall thickness), there is usually a two-stage milling process (roughing and finishing) during soft machining. Depending on the joint type, further fine machining - for example by hard milling - is required after hardening.
Geometry, wall thickness and number of windows vary depending on the cage. Solutions from EMAG can be configured flexibly for this purpose.
It requires highly flexible systems that can produce various components (with a varying number of windows). For example, EMAG offers the HCM 110 for this purpose (see following pages).
With the double-spindle HCM 110 machine, EMAG has a solution specifically for the production of ball cages - flexibly configurable for a different number of windows.
The machine is designed for soft milling and hard milling. Thanks to its accuracy, it can replace grinding processes. There is also another advantage: in the conventional sanding process, one spindle is used per window. Flexible conversion (from six to eight windows, for example) is, therefore, not possible. In contrast, the HCM offers a flexible production concept for all cage types and window numbers - for both soft and hard machining (dry).
In principle, users can choose between three operating modes (given the basic design with two main spindles) Select variants:
In this mode (hard machining), the left milling spindle only machines the cage on the left workpiece spindle and the right milling spindle only machines the cage on the right workpiece spindle.
In pendulum mode, the cage is processed in parallel from two sides.
With the pendulum principle (hard machining), both milling spindles machine a cage at the same timesometimes on one tool spindle, sometimes on the other. Meanwhile, the other tool spindle is loaded and unloaded. The pendulum principle is the processing method with the shortest cycle time.
A third operating mode is mostly used in soft machining. In OP 10, the windows are milled out of the ring (roughing). The subsequent OP 20 is a finishing process.
There is a stop on the base flange that is perfectly adapted to the window geometry - including raised areas that lie under the bars of the cage and do not affect the processing. In addition, there is a centering pin that holds the workpiece in the center without deforming it. The actual clamping takes place via the opposite tailstock with a stop plate. Conversion is very quick - only the bolt needs to be replaced if the number of windows remains the same.
There is a cross slide on the left and right with a milling spindle, while two main spindles, each with an electrically driven tailstock, are arranged in the center. The machine is completely hydraulic-free.
Here, the parts are still completely round (not deformed by hardening). Consequently, a normal mandrel is used for radial clamping within the diameter. Axial clamping is carried out using a tailstock. The solution works purely pneumatically.
The blanks are transported via a feed belt. An integrated sensor system checks the position and condition of the blanks. Faulty or incorrect parts are automatically ejected.
When converting, only the feed is adjusted. Quick adjustments are used for the height and width of the side guides and hold-down devices in the feed. The stopper/closer is also very easy and quick to adjust.
The gripper jaws of the robot can be changed through a small window in the machine door. For this purpose, the robot moves forward.
Outer race components place high demands on the machine and machining technology. It's all about quality of the ball raceways, tight tolerances in the turning operations and large quantities.
The VT 2/VT 4 and VTC 100/VTC 200 machines from EMAG are designed for this task. Here, the turning processes are performed externally - during soft or hard machining in a single clamping operation. The machines are individually designed and can be easily integrated into production systems. EMAG also develops customized solutions for internal turning. KBU machines, for example, are used for soft machining.
The machines have four axes and can process very different components with short cycle times from two sides.
Both machines perfect 4-axis vertical shaft machining. This is ensured, among other things, by a fully integrated and automated loading and unloading via the turret (with very short paths) as well as a powerful main spindle. There are differences in the workpiece size: The VT 2 is suitable for a maximum diameter of 100 mm and a maximum length of 400 mm. With the VT 4, 200 mm (diameter) and 630 mm (length) are possible.
The workpieces are clamped between the main spindle and tailstock and supported by a steady rest. Two turrets are available for machining. To the left and right of the work area are conveyor belts for stocking raw or finished parts.
The VTC machines from EMAG are similarly structured and process shafts with four axes or from two sides. This significantly reduces processing time. Additionally, the machines excel with short travel distances, a powerful main spindle, and two tool turrets, each with eleven tool positions.
The VTC 100 and VTC 200 differ in the maximum component size - the dimensions are identical to those of the VT 2 and VT 4 machines.
» Reduced main times thanks to four-axis machining
» Short set-up and changeover times
» Less manual intervention
» Shortert non-productive times due to time-parallel Loading and unloading parts
» Less space required
Maximum productivity in the smallest of spaces - the multi-spindle machines VL 3 DUO and VSC 250 DUO benefit from pick-up automation, a stable basic structure and powerful spindles in the separate work areas.
VL 3 DUO: MIRRORED POWER
The modular VL 3 DUO machine has mirrored workspaces with their own work spindles, each equipped with up to 17.9 kW of power and 144 Nm of torque - enough power for fast and precise machining in OP 10 and OP 20. In addition, each workspace has a tool turret with twelve tool positions that can be equipped with turning tools and driven tools.
Two separate work areas are available for OP 10 and OP 20. Each work area is equipped with a powerful pick-up spindle. This means that OP 10 and OP 20 or simultaneous processing OP 10/OP 10.
VL 3 DUO
» Compact design for OP 10 and OP 20
» 12-position tool turret from EMAG
» Simple interlinking with other EMAG machines via TrackMotion
VSC 250 DUO
» Multifunctional means of production
» Accuracy-determining assemblies are liquid-coole
» Hydrostatically mounted work spindle in the Z-axis
» Free chip fall (suitable for dry machining
» Short distances for loading and unloading 2.
VSC 250 DUO: INDEPENDENT
The VSC 250 DUO multi-spindle automatic lathe has two separate workspaces and independently programmable portal slides. In addition, each work area has an EMAG disc turret in the front wall. This means that both spindles can carry out both identical and different work sequences. Overall, the machine requires very little space.
For the production of outer races, ball cages, inner races and housings, EMAG develops highly flexible solutions that combine various operations in one machine and can also be perfectly integrated into complete manufacturing systems.
SIMPLY CONTACT US - WE SUPPLY THE ENTIRE SOLUTION FROM A SINGLE SOURCE.