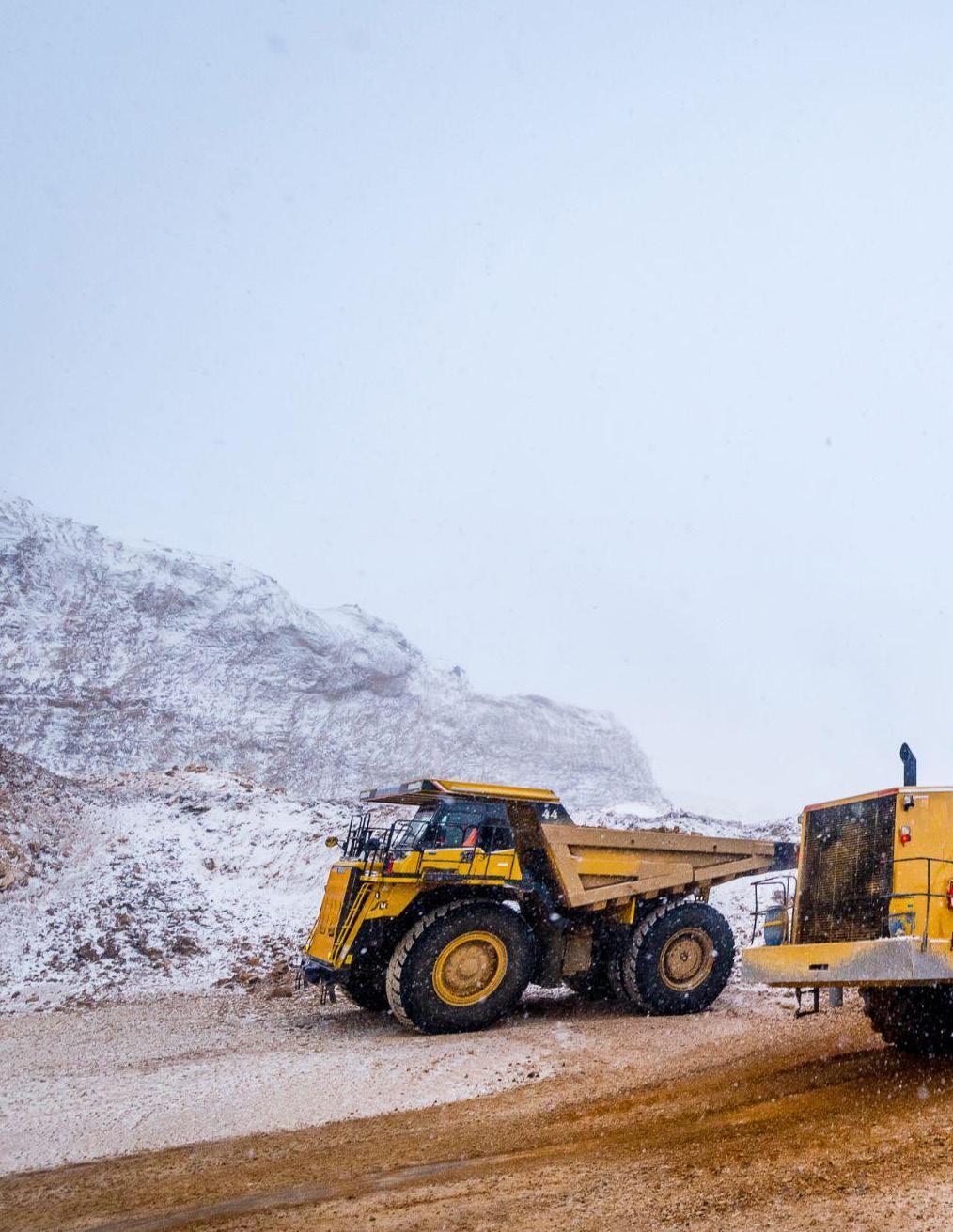
4 minute read
Pod 4: Towards zero emissions haulage

Slide from presentation by Scott Davis, Lead Innovation - Zero Emissions Material Movement, BHP
On the topic of zero emissions haulage, miners and OEMs were adamant that collaboration is the way forward. “Collaborating across different mining companies and suppliers is key. It is really important to onboard the suppliers early in the process, getting the team on site to be a part of the mine design,” recommended Mark Passi, Energy Manager at Glencore.
Advertisement
One example of this collaborative approach is the Charge On Innovation Challenge, led by BHP, Rio Tinto and Vale. With the goal of developing scalable, interoperable solutions for safely delivering electricity to 220-tonne haul trucks without adding time to the haul cycle, the challenge received 88 submissions from vendors, and shortlisted 21 proposals earlier this year. In his update on the challenge, Scott Davis, Lead Innovation, Zero Emissions Material Movement at BHP, told the audience that shortlisted vendors received feedback and one-on-one mentoring from the Challenge’s 21 mining patrons before submitting their final proposals in early November. Next year, OEMs will be invited to give their feedback on the final selection and a consortium will be formed to develop and commercialize the winning products.
While the ‘chicken and egg’ dilemma of the early days of zero-emissions haulage seems to have been resolved through collaboration, a mentality shift is still necessary for the mining sector to adopt new mobility business models. “Batteries are costly, but for total cost of ownership, we’re already equivalent or slightly better than diesel, because buying the battery is essentially buying all of your fuel in one go. That’s a shift that’s taking some getting used to,” said Brian Huff, VP of Technology, Battery and Hybrid Electric Vehicles at Sandvik.
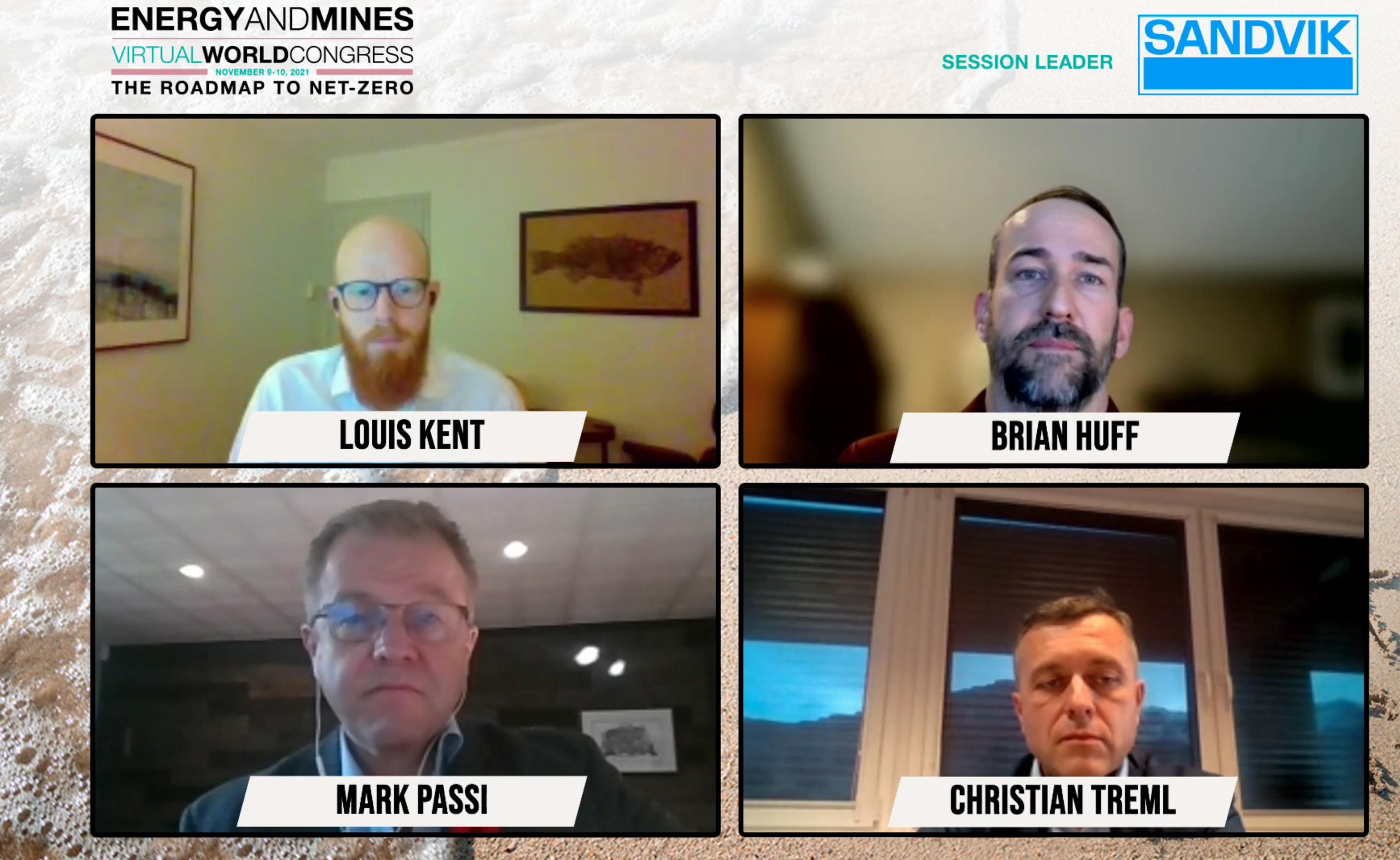
Louis Kent, Principal Carbon Management, BHP chairs the panel on the Fleet Technology Shift with Brian Huff, VP of Technology, Battery and Hybrid Electric Vehicles, Sandvik; Mark Passi, Manager, Energy, Glencore; Christian Treml, Managing Director, VA Erzberg
Several mining operators are already pursuing electrification solutions for their material movement. Pierre Joubert, Executive Vice President, Technical Services at Ivanhoe Mines, gave a presentation on the company’s plan to reach net-zero operational emissions at its African mines: the company is getting ready to test and implement electric equipment at the Platreef and Kamoa Kakula mines.
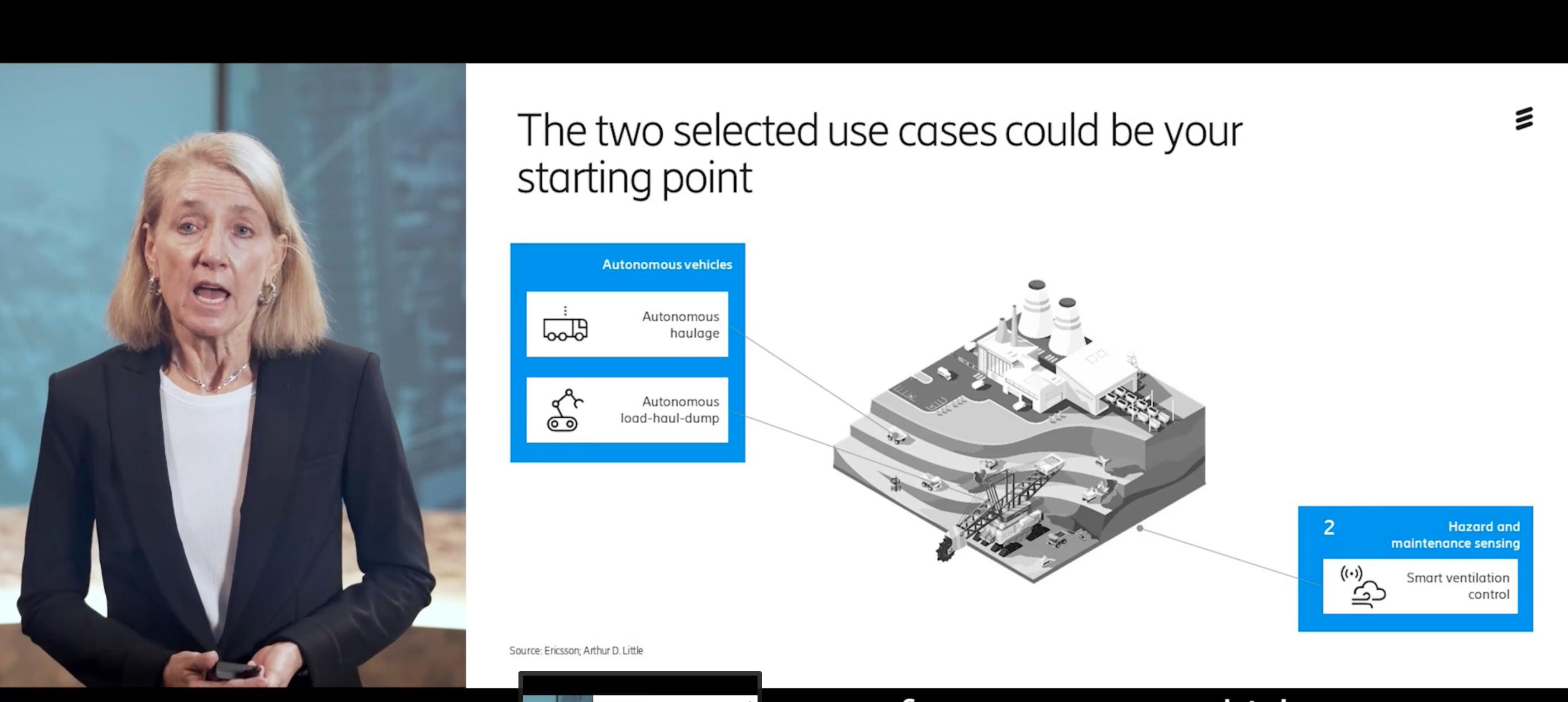
Kirstin Sym-Smith, Director of Business Development, Mining Industry, Ericsson North America presents on sustainable, smart and autonomous mining operations
In British Columbia, New Gold has begun deploying batteryelectric vehicles at its New Afton Mine. Peter Prochotsky, the mine’s Manager, noted that change management is challenging but crucial for the transition to battery-electric equipment. He recommended early planning to ensure buy-in from the entire organization, and paying particular attention to safety, occupational hygiene, human behaviour, maintenance, GHG emissions and energy requirements.
For both Ivanhoe and New Gold, battery swaps seem to be the preferred recharging solution. “It is easy for employees to adapt to charging that is timed with break cycles, so you should aim to select battery equipment that can last until breaks,” Prochotsky said.
Several speakers highlighted the importance of digitization and wireless communication in this transition, as operators, suppliers and experts need to be able to communicate seamlessly and solve issues that may come up. Kirstin SymSmith, Director of Business Development, Mining Industry, Ericsson North America, made the case for private wireless networks to enable autonomous vehicle haulage and smart ventilation control. “Private wireless networks can make this happen through limitless reliable connectivity and security, with benefits to workers and the environment,” she said.
Of course, miners should also consider the impact of an electric fleet on their overall energy requirements. While in underground mines, ventilation reductions are expected to offset the increase in electricity needs, surface mines will need to make significant adjustments to their power supply, and put buffering systems in place to protect generation from charging-related peaks. Ensuring that the electricity supply doesn’t counteract the emissions reductions achieved through electrification is also key — it is no coincidence that most of the mines that have already adopted the batteryelectric technology are connected to hydropower grids.