
6 minute read
Towards the all-electric mine
Mine electrification is a necessary step in achieving a net zero mining sector, but technological, infrastructure and cost hurdles remain. Bernard Norton, Country Managing Director, Hitachi Energy in Australia, shares the lessons learned from the company’s recent work in Australian mines.
Energy and Mines: What are the main challenges with managing the transition to electrification?
Advertisement
Bernard Norton: If we look at the specific challenges of the energy transition from an “on the ground” perspective several issues need to be considered. First, the current infrastructure may not be sufficient to support electrification, which will bring significant new load onto the network with battery electric dump trucks, electric excavators, etc. Additionally, a stable network where generation and load are matched with the necessary connectivity to ensure availability is a major consideration. Integrating new power generation assets, managing intermittency, maintaining power quality and ensuring energy availability as and when needed whilst maintaining operational efficiencies is key, and sustainable energy and digitalisation are inextricably linked. OT & IT will need to work seamlessly to optimize the operation and maintenance of the interconnected network. New skills will be required to operate and maintain a complex, interconnected energy network.
Miners are competing with other market sectors and global economies in the drive to transition to a sustainable energy future. Efforts to build a robust and resilient supply chain, recover from the pandemic, and rebuild logistics capacities are needed. Taking a collaborative approach which engages all stakeholders and focuses on an overall program of works rather than individual projects will be a key to the successful transition to electrification. Finally, governments need to implement supportive policies and regulations to encourage, support and drive the energy transition.
E&M: How can miners choose which electrification options are best suited for a site?
BN: Assuming the driver for electrification is the decarbonisation of operations, the most important factor to consider is an understanding of what parts of the operation contribute the most to the mine’s emissions profile. For example, in a large open cut iron ore mine, digging and in mine hauling of ore contributes between 50% and 70% of total emissions. The work Hitachi is doing as part of the Charge On Innovation Challenge has strong prospects of delivering a cost-effective battery electric dump truck that charges in minutes and minimizes impact on mine operational efficiency.
Depending on whether the mine operates its own generation assets or buys in electricity, another significant contributor to emissions is energy generation. BESS operating as Virtual Spinning Reserve such as Alinta’s Mt Newman project has continued to ensure supply reliability, reduced emissions and has already recouped the initial investment since being in operation from 2017.
Other factors that miners should consider when selecting electrification options include energy needs, resource availability, operational requirements, infrastructure and cost.
E&M: Greenfield vs. brownfield electrification - how do the approaches differ?
BN: With greenfield sites, mining engineers can be more proactive and design the power system and processes with the end goal in mind. Because they are starting with a “clean sheet of paper”, fleet electrification, microgrids, digitalisation, BESS and integration with other operational features such as autonomous haul can be addressed and implemented in an optimal way.
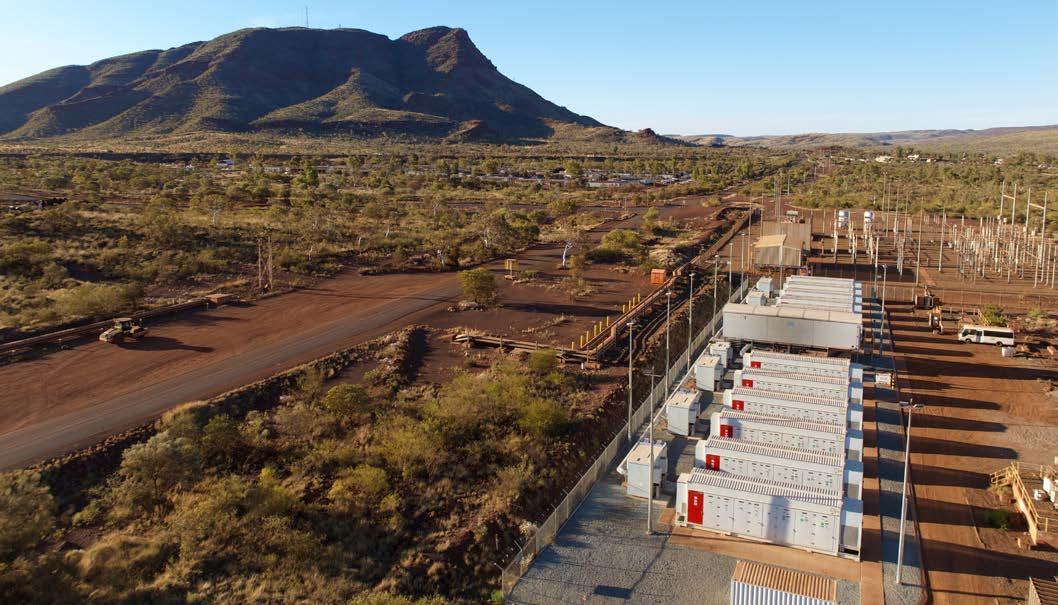
Rio Tinto Tom Price mine
Brownfield mines, on the other hand, often have legacy systems and require more staging and management of constraints through automation and scheduling. For brownfield sites, Hitachi Energy recommends incremental mine hybridisation, where projects are staged to build toward the transition while some benefits can still be realized early. For example, we have supported off-grid mines such as Roy Hill, Tom Price, Soloman, Northstar, and many others with virtual synchronous machines and battery energy storage for virtual spinning reserve. This typically provides a sub-fiveyear payback and lays a strong foundation to connect high levels of renewables over time while ensuring power system stability.
For both brownfield and greenfield sites the starting point of the electrification journey needs to be a clear understanding of the current and future energy needs of the mine, the level of automation and digitization that will be implemented, and sustainable energy resource availability for the site. Hitachi
Energy’s consulting team can assist with establishing this baseline for both greenfield and brownfield locations.
E&M: What is the best strategy for combining automation with electrification?
BN: It’s important to understand that digitalisation and automation of the energy network are fundamental to the shift to sustainable energy. Supply, distribution and consumption systems must be integrated to ensure a reliable and resilient energy system. Data is key to successful integration of these systems, and availability of quality data enables the opportunity to further automate operations.
Key issues to consider include:
• Determine which automation and electrification technologies are best suited for your mine’s needs and operations by evaluating the scalability, interoperability, and costeffectiveness of various options.
• Develop a phased implementation plan by identifying priority areas or operations for automation and electrification and building a timeline and budget for implementation.
• Prioritize data management by investing in systems and infrastructure to collect, store, and analyze data.
• Ensure system stability by implementing measures to maintain frequency and voltage levels, manage power quality and prevent power outages.
• Invest in training and upskilling employees to operate and maintain new technologies.
• Seek partnerships with experienced providers who can provide guidance and support for the implementation of new technologies.
E&M: How can mines estimate and prepare the energy system to make the leap to all-electric?
BN: The investment required to electrify is an investment in medium and long-term assets. As with any investment of this nature careful planning and assessment of future needs is required. In the case of the transition to all electric operations, a careful assessment of the adequacy and availability of generation, transmission and distribution assets is required as part of overall mine planning.
To enable this, a techno-economic assessment is needed, which requires collaboration between technology and mining experts. And this means bringing together and working collaboratively with the right industry partners with the requisite knowledge and experience is key. This team needs to focus on balancing technology solutions with customer needs and risks to achieve the optimal techno-economic outcome for the mining operation.
The pace of change is rapid, and traditional engineer-procureconstruct models that focus solely on lowest cost CAPEX investment can leave customers with stranded or obsolete infrastructure. An optimized outcome therefore needs to consider whole-of-life and systems / solutions that enable and support enhancements and innovations that adapt the system over time.
Along with our deep domain expertise in hardware and software, Hitachi Energy has significant expertise in energy consulting. We can support miners in their electrification journey from feasibility and planning right through to execution and ongoing maintenance.