
25 minute read
The Warren Report
Andrew Warren is chairman of the British Energy Efficiency Federation
04.21
Advertisement
Environmental taxes work – but we’re not sure how
A report from the National Audit Office acknowledges the benefits of taxation on organisations but questions what specific effects they achieve
The National Audit (NAO) has produced a fascinating report. Blandly entitled “Environmental Tax Measures”, it reveals that in 2019 eco taxes and charges - as defined by the Office for National Statistics - raised some £51.6bn. Threequarters of which came from energy use, and almost all the rest from transport taxes.
This report examines how HM Treasury and Her Majesty’s Revenue & Customs (HMRC) manage tax measures with environmental objectives, including the work undertaken to design, monitor and evaluate them.
The NAO looked in detail at the oldest of these taxes, the Climate Change Levy (CCL). First collected in 2001, it now costs business users and public sector organisations “around” £1bn a year. Together with the Carbon Price Support, introduced in 2013, the two taxes raise a very precise £2.091bn per annum.
The objective of the CCL is to “encourage businesses and the public sector to use energy more efficiently, and thus reduce greenhouse gas emissions.” Has it worked? Well, the amount of energy used by industry to produce a unit of output has fallen by two-thirds.
Curiously, little attention is paid to the 51 industrial sectors which have established Climate Change Agreements, whereby they commit to improving energy efficiency in exchange for receiving a discount on the levy, which costs the Exchequer £260m a year. Many earlier studies have concluded how effective these Agreements are.
But as the Treasury acknowledges, given its longevity, the CCL “has had most of the behavioural effect for many businesses” and thus “ongoing monitoring provides limited insight into the Levy’s effect.”
The NAO is rather scathing that neither they nor HMRC “hold data, or undertake analysis to help understand how the taxes effect business decisions.” It has now been agreed, to address potential compliance risks, that VAT-related visits should include data on the CCL, particularly “for larger suppliers.”
The NAO has even more question marks about quite why since 2014 highly energy-intensive sectors like the mineralogical and metallurgical industries have avoided paying the Levy altogether. This includes cement manufacture and operation of blast furnaces. Such reliefs cost the Exchequer approximately £210m each year.
Unclear future for support scheme The Carbon Price Support mechanism has coincided with a huge drop in coal-fired electricity generation. But other policies like emissions trading systems and renewables tax breaks have also contributed. So, as new coal generation will be illegal from 2024, the NAO pointedly concludes, the “future role of Carbon Price Support is unclear.”
It is the way in which differential tax rates are charged for similar activities that particularly concern the NAO. They highlight that by failing to levy the standard 20 per cent VAT rate on domestic fuel, the Exchequer forgoes £5bn each year. The reason given is “to
reduce fuel poverty”.
Reducing fuel poverty is also the policy reason given for the absence of fuel duty on the use of kerosene as a heating fuel (the Treasury forgoes £2.5bn). That is also apparently the justification for many energy-saving measures also being charged VAT at 5 per cent (costing the Exchequer £70m a year). Actually, the reason given by the then Chancellor was to ensure that energy conservation was taxed at the same rate as energy consumption.
Taxation of natural gas usage differs enormously, depending upon where it is used. Industry pays three times as much tax per gigajoule of energy use as do commerce or public services. But industry in turn pays just one-sixth of the amount levied for gas used in electricity generation.
Positive impact of taxes Overall, the NAO acknowledges there is some evidence of the positive impact that taxes do have upon the environment. But too little is known about their specific effects. The exchequer departments tend to focus more on the revenue that environmental taxes raise, rather than the environmental impact they achieve.
The NAO reckons there are other measures – both taxes and tax reliefs – which impact upon government’s wider environmental objectives but which are not recognised as “environmental” in nature. As such, the exchequer departments do little to identify these measures, or assess their relevance to government’s environmental goals, though the NAO concede they do consider environmental impact in some significant cases when advising ministers.
The scale of government’s environmental ambitions, particularly on net zero, means it must employ every tool at its disposal if it is to succeed. The exchequer departments need to fully understand the relationship between existing taxes and these ambitions, to ensure the taxes contribute as intended, and to learn lessons for any future taxes which may support wider environmental strategies.
Boilers & Burners
Hans Bahnsen is UK & Ireland sales manager for industrial boilers for Bosch Commercial & Industrial
When reliability is top priority
Maintaining process heat is crucial for many sectors. Hans Bahnsen discusses why having a reliable, efficient boiler is essential for your manufacturing plant
When we think of boilers we understandably think of heat and how boiler technology contributes to keeping us warm. However, in industry, boilers can have other important uses, which aren’t necessarily related to providing heat and hot water to buildings.
One such application is process heat. This is where industrialsized steam or hot water boilers, not dissimilar to the ones you see in district heating networks, are utilised in production lines within manufacturing plants and factories. It’s the application of heat for industrial processes.
Two obvious sectors are the food and beverage industries. However, some others not so obvious like a car manufacturer which may have a paint shop within their production line which requires hot air to fix the paint to the car. Boilers are used to generate that hot air through generating hot water and passing it through a heat exchanger. It is a similar process to heating a commercial building with a different end use.
So, with that in mind, boilers can be at the heart of any production facility that uses hot water or steam. So if the boiler shuts down the consequences can be catastrophic.
To emphasise the importance of the industrial boiler let’s look at the food and drink industry. Most industrial boiler applications are through generating steam, which is used as a means for transferring energy within a factory setting.
So, as an example, think of a dairy product company who pasteurises milk. When the factory opens the boilers are switched on and begin burning fuel to generate steam, creating a cycle of heat. This steam takes heat energy and transfers it to the area of the factory where the milk is pasteurised.
This is one part of the production process for the dairy company, but a critical one if this company has

The simplest way of preventing boiler downtime is to have back-up, also known as redundancy
millions of bottles of milk leaving the factory door each day. Let’s say that its industrial boiler breaks down and stops working. This will halt the production line and could result in tens of thousands of pounds of lost revenue per every hour of boiler downtime.
This situation can of course be prevented however, if the right steps and options are made to begin with.
More than one boiler installed
The simplest way of preventing boiler downtime is to have back-up, also known as redundancy. Many manufacturers have more than one boiler installed, which is a very sensible system to have. If a boiler fails, or has a service, then another can be switched on to take its place and ensure the production line isn’t affected.
However, there are more robust and efficient ways to prevent possible failures thanks to the technological advances in controls. Through smart controls facility managers can monitor a system’s use, identify any issues and even pre-plan boiler servicing and downtime.
There are other benefits, like boiler efficiency levels. So far we’ve discussed the loss of revenue if a production line stops. However a faulty, old or leaking system can have an adverse effect on energy bills in the long term.
You can have the most efficient heating system from day one but what if nobody looks or monitors it in over a year? There may be issues that have cropped up during that time or the overall efficiency has reduced. By opting for boiler systems which have robust, smart monitoring technology it is possible to identify and resolve any possible efficiency issues.
Another area to be aware of is how future policies and technologies related to heating and processed heating will come to the fore. The UK has set an ambitious target of net zero carbon emissions by 2050 and there are many steps that need to be taken for that to become reality.
As industrial process heat is one of the biggest contributors to the UK’s carbon footprint, policy and regulations are already being put in place, which favour the use of alternative fuel to gas, such as hydrogen.
To stay ahead of that curve, manufacturing plants could opt for hydrogen or bio fuel-ready boiler systems which burn 100 per cent hydrogen (once the fuel becomes available on the gas grid). With only a simple change required, the boiler doesn’t need to be replaced later down the line saving on doubling up on initial purchase cost of a boiler system.
Finally, when searching for a new boiler for your factory opt for companies that offer bespoke services and products. No industrial boiler should be available ‘off-theshelf’. Each and every manufacturing plant will have specific requirements so opt for a site visit where the boiler manufacturer can evaluate your needs, the space available and other technical points.
By taking the time to choose the best, most efficient boiler for the job will help save a lot of hassle down the line.
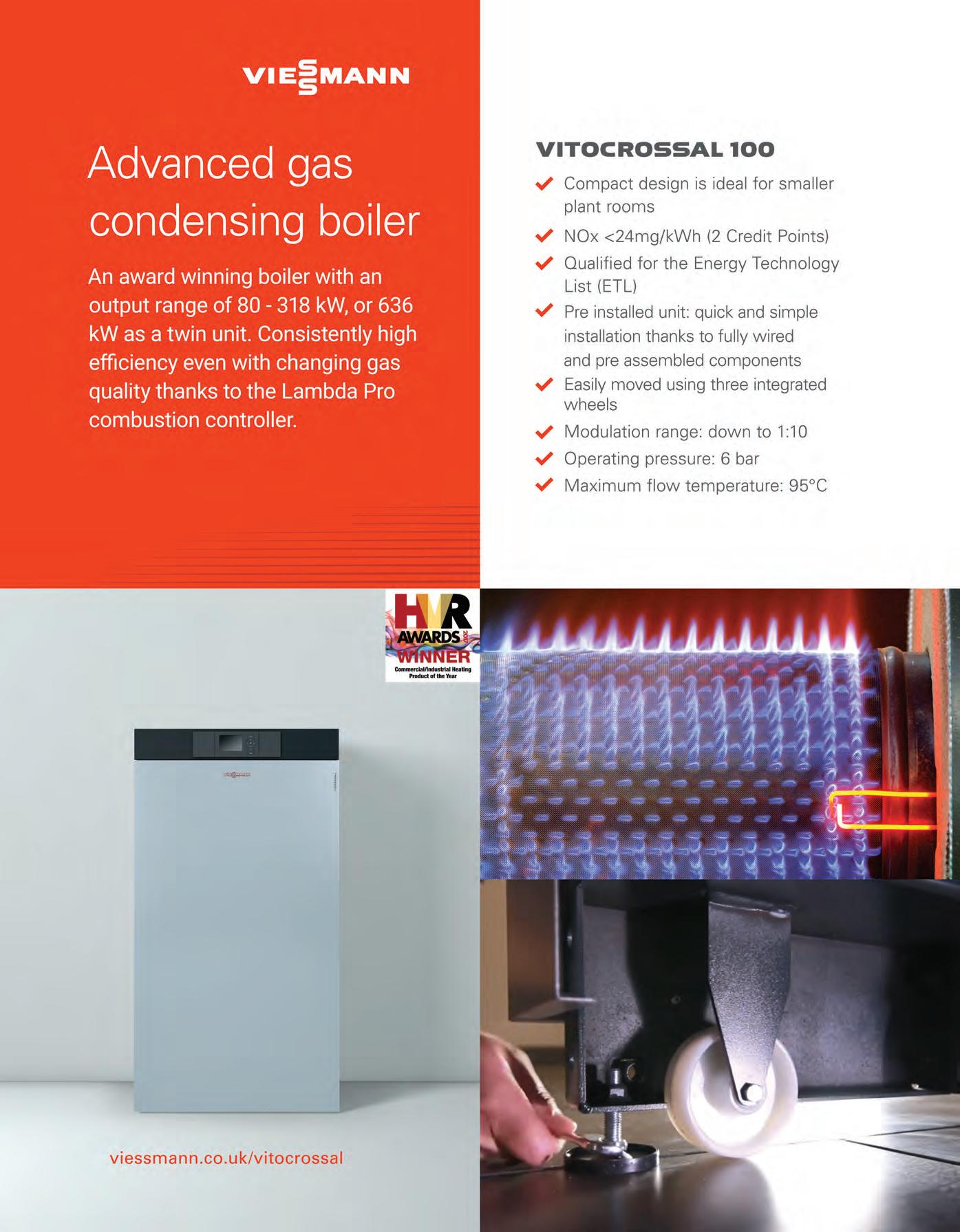
Boilers & Burners
Tom Murray is specification director at Baxi Heating
The challenge of future heat
Tom Murray looks at the opportunities ahead for energy managers to reduce emissions from heat and how the humble boiler is evolving to meet immediate and future requirements
As sustainability rises up the business agenda, heat, which accounts for 37 per cent of total UK emissions, is becoming an increasingly hot topic for energy managers. The Government has set decarbonising heat in buildings at the heart of its ten-point plan for a green industrial green evolution, with heat pumps and hydrogen highlighted as being pivotal to achieving its ambitious goals.
The focus to date has largely centred on the UK’s circa 28m homes but reducing demand in commercial buildings is clearly critical if we are to achieve our 2050 net zero target.
With that in mind, what feasible opportunities are available for energy managers? And what part will the boiler play in heating our commercial buildings – now and in the future?
Heating presents particular challenges as older, poorly insulated commercial properties will have very different requirements to thermally efficient new buildings, making a single ‘silver bullet’ approach to decarbonisation impossible.
Instead, applying a mix of different technologies and techniques – including heat networks, heat pumps and hydrogen – will offer a solution. Energy efficiency will also be key, as it’s the most cost-effective resource available to meet our energy needs.
A pragmatic approach for energy managers is to identify both longerterm measures and immediate actions that together will set their buildings on the path to net zero.
In well-insulated buildings that are designed to require less heat, the merits of applying heat pumps are well established. We view air source heat pumps (ASHPs) as the most popular and cost-effective choice of heat pump and will soon be offering them as part of our portfolio of cleaner, greener
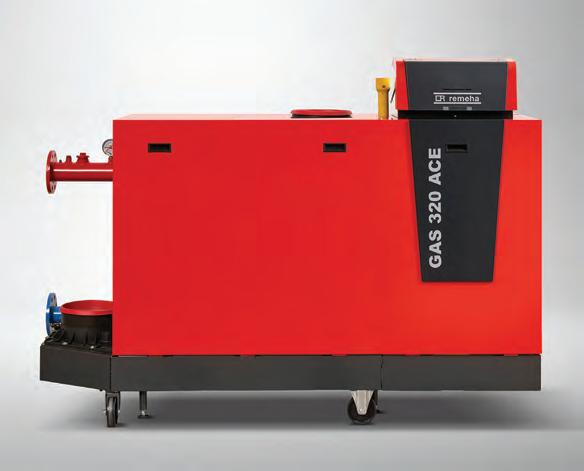
Operators of older commercial buildings are going to be using gas for many years to come, the trick is to use it as efficiently as possible
commercial heating and hot water solutions.
We also see multivalent heating systems that include both boilers and heat pumps as a natural next step to deliver an efficient and costeffective heating system all year round – at least until heat pump technology evolves.
But without funding, the technically and economically viable solutions in our older and less thermally efficient building stock are currently constrained. Retrofitting heat pumps, for example, may not be an option at present as heat pumps typically optimise their efficiency at low flow temperatures (around 30-55ºC).
So what alternatives are there for energy managers in these ‘hardto-tackle’ buildings? One low disruption, medium- to longerterm solution is to repurpose the gas grid to transport green gas – which leads us to hydrogen boilers.
As hydrogen is a gas, it can capitalise on existing infrastructure while transitioning us to a cleaner fuel source. Baxi Heating and BDR Thermea Group have been working with UK Government to trial hydrogen boilers in a number of projects. 20 per cent hydrogen blends are being demonstrated using current boilers at the HyDeploy project at Keele University. We are also demonstrating prototypes of 100 per cent hydrogen boilers through the UK government Hy4Heat programme, with larger scale trial projects in development.
The government has committed £81m investment from this year to develop hydrogen generation capacity. It is also pioneering hydrogen heating trials, starting with a hydrogen neighbourhood and scaling up to a potential hydrogen town by the end of the decade. It isn’t far-fetched to envisage businesses heating their buildings with hydrogen or hydrogen-ready boilers long before 2050.
But what about the here and now? With many businesses financially impacted by the COVID crisis, energy managers may struggle to balance environmental and economic concerns when the heating system needs upgrading.
This is supported by the findings of a recent survey of 1,000 organisations by the British Standards Institution (BSI) to understand how businesses are managing the transition to net zero by 2050. The ‘Net Zero Barometer’1 found that cost was named by 44 per cent as the largest barrier to achieving net zero. Additionally, 68 per cent said that their plans and progress had been set back by the COVID-19 pandemic.
When it comes to heating, many operators of older commercial buildings are likely to continue to use gas for heat for the next ten years or twelve years. The focus, therefore, must be on using this energy source as efficiently and effectively as possible. The cheapest and cleanest energy choice is, after all, not to waste it.
Upgrading any ageing or inefficient boilers to high efficiency condensing boilers will considerably reduce emissions associated with heat. At the same time, condensing boilers are a core component in hybrid heating systems and heat networks. For this reason, we are continuing to evolve condensing boiler design to enhance the heating systems of today, all the while we innovate with hydrogen boilers.
With advanced condensing boilers providing immediate, achievable opportunities for energy and emission savings and futureproofed hydrogen boilers leading businesses to net zero, boilers continue to have an important role to play in heating. Reference
Boilers & Burners
Hoval launches second generation UltraGas
Hoval has launched UltraGas® 2, the latest generation of gas condensing boilers, which brings even higher efficiency to the popular features of the first UltraGas® generation
The UltraGas® 2 is Hoval’s latest generation of gas condensing boilers for heating and hot water generation, available with output ratings from 125 kW to 1550 kW (250kW to 3,100kW as a double boiler). Based on the first generation of UltraGas® condensing boilers – which have been tried and tested for many years – the successor model boasts a patented Hoval TurboFer® heat exchanger for even greater efficiency, combined with a future-proof and compact design, setting the new benchmark in large-scale renovation and new-build projects.
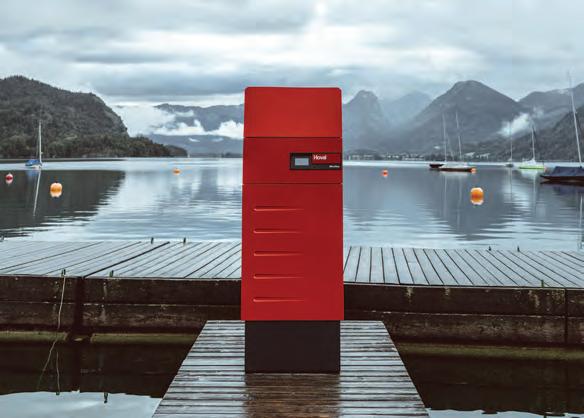
The UltraGas 2 boiler can operate on biomethane or hydrogen, equipping it for the energy transition
Patented heat exchanger
The TurboFer® heat exchanger is the brand-new, patented core component of the boiler. The unique design of the heat exchanger and its special injection technology generates turbulence on the heating gas side, increasing heat transfer and boosting efficiency. In combination with other UltraGas® features, such as high and low temperature return flow, a large water capacity, the Ultraclean® combustion system and the TopTronic® E system controller, the TurboFer® heat exchanger guarantees an optimum condensing performance.
Future ready
As well as natural gas, the UltraGas® 2 boiler can operate on biomethane and hydrogen, equipping it for the ongoing energy transition from gas to biomethane and for a hydrogen-powered future. Alternative, sustainable energy sources, such as solar, pellets and heat pumps, are easy to integrate into the new generation of system boilers.
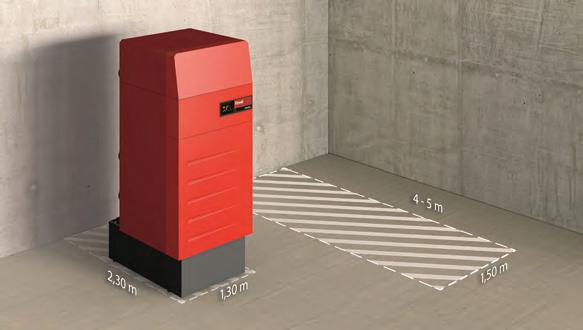
Key features of the UltraGas 2
New TurboFer® heat exchanger for an even more efficient performance and enhanced cost-efficiency Secure investment, equipped for future challenges or hybrid systems Compact and lightweight design for effortless installation and commissioning
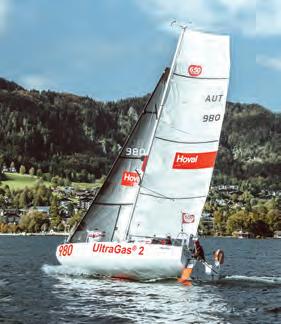
UltraGas 2 units are compact enough to fit through any standard door
System integration
Thanks to the standardised Hoval TopTronic® E controller, UltraGas® 2 boilers can be easily combined with any type of heat generator and solar energy system to create an integrated heating system where all the components work together to optimise efficiency.
TopTronic® E delivers a completely new level of simplicity, modularity, connectivity and user experience without compromising on control functionality. As such, it eliminates the inconvenience and risk of trying to work with different controllers for different appliances and system configurations.
Featuring ‘plug and play’ modular hardware, TopTronic® E allows easy extension of an existing system with additional Hoval components (e.g. solar thermal panels or an additional water heater). It can also operate alongside the new TopTronic® Supervisor within a fully scalable system for the real-time visualisation, monitoring and optimisation of district heating networks.
Built to last
Like all Hoval products, the UltraGas® 2 system boiler was built to last, with the motto “ready for future” in mind. Each individual component and material was designed and selected for a long service life – which is why we opted for highquality stainless steel on the hot water side. This promise is supported by an extended warranty on the boiler body. All of these factors make the UltraGas® 2 a future-proof investment.
Compact, lightweight and easy to install
When designing the new generation of boilers, ensuring that the UltraGas® 2 would be as easy as possible to install was high on the agenda. As a result, there is no need for system components such as a circulating pump or a hydraulic separator. We also reduced the amount of pipework in the TurboFer® heat exchanger to keep the weight down.
All of these measures produced a lightweight design that takes up significantly less space. UltraGas® 2 models up to 450kW are less than 800mm wide – compact enough to fit through any standard door. And a compact design means that less installation space is required, too. Larger models usually take up just half of the space of other gas condensing boilers. This makes the UltraGas® 2 the perfect choice for large-scale renovation and new-build projects. For more information: boilersales.uk@hoval.com
Boilers & Burners
Next generation gas condensing boiler range makes servicing easier
Viessmann has introduced the next-generation of its most popular gas-condensing boiler, the Vitodens 100-W.
The WiFi-integrated Vitodens 100-W’s new control platform makes commissioning and servicing the boiler easier. It is now possible to monitor and make adjustments to customers’ boilers remotely. No thirdparty controls are required, meaning a Vitodens boiler with ViCare Thermostat provides homeowners with a load-compensating smartphone-controlled heating system.
The mechanical design of the Vitodens 100-W has reduced the number of spare parts typically needed for routine maintenance by about 50 per cent, meaning Viessmann installers should be able to carry less stock.
At the same time as the new-generation Vitodens 100-W series goes on sale in April, Viessmann will also launch the new Vitodens 111-W wall-mounted combi boiler. Intended for family homes where there is high hot water demand, the 111-W features a cylinder loading system and 46-litre integrated stainless steel storage tank, allowing it to provide a flow rate of up to 181 litres in 10 minutes. Outputs range from 3.2kW to 32kW (and with an 11kW version now added to the range), the Vitodens 100-W series is suited to a much broader range of homes and ideal for installers searching for boilers to match heat loss calculations.
Two further versions of the Vitodens range will be introduced by September, in time for the 2021/2022 heating season: a heat-only 100-W, and the new Vitodens 050-W.

New warmth for Leeds offices
Six TRIGON XL boilers from ELCO are providing the office tenants of 7 & 8 Wellington Place in Leeds, with heating and hot water.
Home to the Leeds Government Hub, the new 35,000m2 commercial development is the biggest ever office pre-let in the area and is expected to bring over 6,000 civil servants to the city centre.
Developed by MEPC on behalf of the joint venture between Hermes Investment Management and Canada Pension Plan Investment Board (CPPIB), the buildings offer grade A office accommodation with an ‘Excellent’ BREEAM rating. To fulfil the development’s requirements, three 500kW ELCO TRIGON XL floor standing condensing gas boilers were specified and installed in a roof top plant room to supply 7 Wellington Place, prior to three additional 570kW models being fitted in building number 8. The whole process was undertaken and managed by construction, development and property services specialists Wates Group.
Matthew Bell, project engineer at Wates said: “This was a prestigious project and therefore required a carefully designed, high quality heating system. We selected ELCO boilers for a number of reasons, but one of the most important was the longevity of the units, as well as the guarantee that parts would be available for many years to come. We had already used ELCO on a previous part of the Wellington Place project, so were confident that their boilers would achieve the required BREEAM rating and NOx emission targets.”
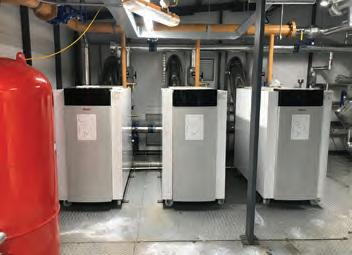
Low NOx steam process boilers
Industrial process heating equipment and solutions specialist Babcock Wanson has launched the SteamPack range of Fire Tube Steam Boilers, for steam outputs from 3,500kg/h to 8,000kg/h.
SteamPack boilers feature unique Babcock Wanson technology in the form of three-pass design and a water tube flue gas reversal chamber for operational flexibility, very high long-term efficiency and reliability and low operating costs. The chamber is welded outside the pressure part body, and does not require any furnace tie rods or reinforcement, giving exceptional flexibility to the shell and furnace expansion allowing large steam load changes with minimal operational stress. The dedicated burner combustion head design, linked to very high turndown ratios, provides accurate control of excess air and minimum start/stop cycles. This design reduces fuel consumption while ensuring excellent performance across a wide process operating range. It can be further enhanced with a Babcock Wanson flue gas heat recovery system adapted to the process at hand. A range of compatible flue gas heat recovery systems is available, including economisers and combustion air preheaters.
Also notably low with SteamPack boilers is emissions, including NOx. SteamPack boilers not only readily meet the latest European environmental legislation and when fitted with Babcock Wanson combustion equipment they exceed regulatory requirements.
All boilers in the range come with comprehensive instrumentation and controls as standard, including Babcock Wanson’s exclusive three- and seven-day unattended operation modes.
The SteamPack range includes options including a condensing economiser, combustion air pre-heater, dual and mixed fuel firing, O2 and CO trim.

Hoval Ltd says that its PowerBloc combined heat and power units meet all of the technical parameters and considerations relating to connection to the networks of licensed electricity distribution businesses throughout Great Britain.
The company has confirmed that its PowerBloc EG43 to EG530 units are now fully compliant with the latest Engineering Recommendation (EREC) G99 standard.
EREC G99, issued by the Energy Networks Association, ensures harmonised network standards (Requirements for Generators) are incorporated into Great Britain’s distribution and grid codes for CHP and other power generators with capacities between 0.8kW and 1MW.
Managing director, Ian Dagley commented: “Onsite power generation with CHP as part of the energy mix is set to make a major distribution to the ‘greening’ of the UK’s grid electricity. It will also help end users reduce their energy costs and dependence on the national grid.
“The assurance that G99 compliance brings, therefore, will make an essential contribution to meeting the UK’s carbon reduction targets.”
Mark Ferris is specification manager for ELCO Heating Solutions
Boilers & Burners
Specifying for hot water demands
Efficient production of bulk hot water is vital for many commercial buildings, but with so many options, what should specifiers look out for? Mark Ferris outlines the approaches available
From healthcare facilities to leisure centres, hotels to larger residential schemes, the efficient delivery of domestic hot water (DHW) is crucial for day-to-day operations.
There are, of course, a variety of tried and tested methods that can be taken to fulfil the requirements of a high demand for instantaneous hot water. However, as is so often the case in the commercial heating and hot water industry, there isn’t a ‘one product that fits all’ solution.
Before considering the different types of hot water units available, there are some fundamental aspects that need to be assessed in order to help identify the best product for the job. The first question should be on the building’s peak flow rate, its predicted demand and existing/predicted usage patterns.
Regardless of the size and scale of a commercial project, the equipment will need to deliver sufficient hot water during the building’s busiest periods – and these will differ widely depending on the application.
For example, a school is likely to have a fairly predictable pattern of usage; after all, it has set opening and closing times, with a defined timetable of activity where peak demands can be calculated, whether it is for a canteen during lunch or after-school sports clubs.
Conversely, when you consider a hotel, which is not only open 24/7, but can also have vast disparity in occupancy, DHW demand can vary from day to day. However, a hotel will always experience a peak in demand during the mornings when guests get up and have a shower, so the worst-case scenario for a fully occupied venue can be calculated.
Other information useful in determining the right product for the application includes how often peak delivery is repeated during a day and the average continuous
DHW demand in a 24-hour period.
Both these factors will give further

Before considering the different types of hot water units available there are some fundamental considerations to examine
evidence to the demand profile of a commercial building.
Referring to any existing or estimated patterns of usage from the outset will also help to narrow down the options and identify products that can cope with the peak demand. And this task shouldn’t be taken lightly, as under-sizing the system could result in not enough hot water being available for the building’s occupants, whereas oversizing can cause a vast amount of energy to be wasted. But, ultimately, occupants should never have to wait for the equipment to become operational.
Direct and indirect delivery
There are two distinctive appliance types for hot water delivery, direct and indirect. These two categories, and the products associated with them, will have their own pros and cons depending on the type of commercial building in which they are to be fitted. A direct unit has an integral heat generator, e.g. a gas burner, which directly heats the water flowing through it. Some products, such as ELCO’s new Tudor NHREC, will transfer heat into a stored volume of water that surrounds the firing tube, whereas other direct products will utilise a heat exchanger to the point of use.
The benefit of these types of unit relates to their design, which is dedicated to the efficient generation of hot water. This ensures they generally provide far quicker response times compared to indirect units, as well as reduce the potential for heat losses in pipework, such as that between a boiler and calorifier, for example.
Furthermore, the latest direct-fired gas water heaters are condensing appliances, incorporating a room sealed pre-mix combustion system. This ensures that much of the latent energy (present in water vapour discharged through the flue) is recovered and not lost to atmosphere, allowing for delivery of gross thermal efficiencies up to 96 per cent. In addition, this type of condensing water heater considerably reduces NOx emissions, making it ideal for new build properties.
When considering the demand for delivering DHW directly to the point of use, there are two different mechanisms. The first is instantaneous, whereby water is heated as it is being delivered; a good commercial example is a health club, which has a swimming pool that needs to maintain a set temperature. In this instance, the water is often heated directly and transferred straight to the point of use, which requires a direct fired unit, such as ELCO’s TRIGON XL Water Heater (model ZW) - which is specially designed for swimming pools and to deliver a high volume of DHW per hour. Although highly effective and often considered for this type of application, the capital costs of this approach are at the upper end of the scale, due to the size of unit required.
As a compromise in some projects, an alternative approach may use a combination of instantaneous DHW generation alongside a stored volume that is held at a set-point temperature. So, when there is high instantaneous demand occurring over a relatively short period of time; this is best met by using both the stored volume of DHW and that generated by the instantaneous hot water heater. Consequently, the plant can be suitably sized to recover the volume of stored DHW over an acceptable period of time, relative to the application.